Листопрокатный стан 5000 Ижорских заводов




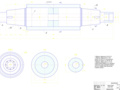
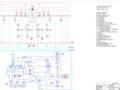
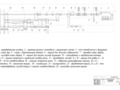
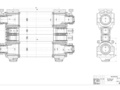
- Добавлен: 25.01.2023
- Размер: 8 MB
- Закачек: 1
Описание
Состав проекта
![]() |
![]() |
![]() |
![]() ![]() ![]() ![]() |
![]() ![]() ![]() ![]() |
![]() ![]() ![]() ![]() |
![]() ![]() ![]() ![]() |
![]() ![]() ![]() ![]() |
![]() |
![]() ![]() ![]() ![]() |
![]() ![]() ![]() ![]() |
![]() ![]() ![]() ![]() |
![]() |
![]() ![]() ![]() ![]() |
![]() ![]() ![]() ![]() |
![]() |
![]() |
![]() |
![]() |
![]() ![]() |
![]() |
![]() |
![]() |
![]() |
![]() |
![]() |
![]() |
![]() |
![]() |
![]() |
![]() |
![]() |
![]() |
![]() |
![]() |
![]() |
![]() |
![]() |
![]() |
![]() |
![]() |
![]() ![]() ![]() |
![]() ![]() ![]() ![]() |
![]() |
![]() ![]() ![]() |
![]() ![]() ![]() |
![]() ![]() ![]() |
![]() ![]() ![]() |
![]() |
![]() |
![]() |
![]() |
![]() |
![]() ![]() ![]() |
![]() ![]() ![]() |
![]() ![]() ![]() |
![]() |
![]() |
![]() |
![]() |
![]() ![]() |
![]() |
![]() |
![]() |
![]() ![]() ![]() |
![]() ![]() ![]() ![]() |
![]() |
![]() |
![]() ![]() ![]() |
![]() |
![]() ![]() ![]() ![]() |
![]() ![]() ![]() |
![]() ![]() ![]() |
![]() ![]() ![]() |
![]() ![]() ![]() |
Дополнительная информация
Графики.dwg

Стан 5000 (разрез) 1_25 Рамка.dwg

мс 3. Максимальная масса слитков до 60 тонн 4. Максимальный рабочий момент на валке 300 тм 5. Отключающий момент 360 тм 6. Диаметр рабочих валков: максимальный 1120 мм минимальный 1050 мм 7. Длина бочки рабочих валков 5000 мм 8. Диаметр опорных валков: максимальный 2360 мм минимальный 2200 мм 9. Длина бочки опорных валков 4800 мм 10. Максимальная ширина раската 4800 мм 11. Максимальный растор валков 1100 мм 12. Скорость нажимных винтов: максимальная 54 ммс минимальный 0
ммс 13. Диаметр резьбы нажимных винтов 800x64 14. Цена деления шкалы циферблата: грубого отсчёта 10 мм точного отсчёта 0
мм 15. Скорость перемещения при перевалке: рабочих валков 0
мс 16. Давление воды в системе гидросбива 180 кгссм 17. Уравновешивание верхних валков гидравлич. 18. Давление масла в системе уравновешивания валков 188 196 кгссм 19. Диаметр поршня разгрузочного устройства 1500 мм 20. Ход поршня 25 мм 21. Давление масла в цилиндре разгрузочного устройства 255 кгссм
ТЭП.dwg

Энергосиловые F.dwg

План отделения 1_250.dwg

Помещение электрических вакуумных
Насосно-аккумуляторная станция №1
План листопрокатного
отделения стана 5000
Стан 5000 Разрез цеха.dwg

Цементная стяжка h=50
Утеплитель (полистироловые
Сборные железобетонные плиты
Схема расположения оборудования.dwg

Автоматизация А1.dwg

М2-двигатели главного привода М-двигатели рольганга с коническими роликами М1-Мп-двигатели рольганга FA1
FA2-силовые трансформаторы Т1
Т2-силовые трансформаторы UZ1
UZ2-реверсивный тиристорный преобразователь цепи якоря двигателя UZ3-преобразователь цепи обмотки возбуждения SE-задатчик РЭ-регулятор э.д.с. РТ-регулятор тока якоря РТВ-регулятор тока возбуждения РС-реулятор скорости ФВУ-фазовыпрямительное устройство Ф-фильтр ЭС-элемент сравнения РВН-регулятор выравнивания нагрузки ЗИ-задатчик интенсивности СИФУ-система импульсно-фазового управления
К системе управления двигаталем М2 через МП
главный электропривод
Скорость прокатки: до 4
Температура прокатки: 1050 - 800 С
Толщина листа: 100 - 10 мм
Стан 5000 Опорный валок А1.dwg

после упрочнения накаткой до глубины 5 мм 250-320 HB. 3.Твёрдость поверхностей Б и Е 50 HS. 4.Перед посадкой бандажа на ось произвести контрольные замеры диаметров посадочных мест оси и бандажа. Натяг должен быть в пределах размера Г.
Ось валка: сталь 45ХНМ
Бандаж валка: сталь 90ХФ
Стан 5000 валковый узел A1.dwg

Расчёт валков на прочность.doc
Диаметр рабочих валков стана: мм
Диаметр опорных валков стана: мм
Диаметр подшипников рабочих валков: мм
Диаметр подшипников опорных валков: мм
Длина бочки рабочего валка: мм
Длина бочки опорного валка: мм
Ширина прокатываемого листа: мм
Определение распределения усилия между рабочими опорными валками:
Усилия на рабочих валках:
Усилия на опорных валках:
Рабочие валки воспринимают % от общего давления на валки при прокатке.
Определение опорных реакций.
Распределённая нагрузка на бочки валков при прокатке:
опорные валки воспринимают нагрузку через рабочие по всей длине бочки валка.
Принимаем валок в виде балки покоящейся на двух опорах испытывающей нагрузку приложенную посередине длины. Тогда реакции опор составят:
Находим напряжения в рабочем валке
Максимальный изгибающий момент посередине бочки рабочего валка от вертикального усилия P.
расстояние между точками приложения силы мм
Максимальное напряжение изгиба посередине бочки рабочего валка
Напряжение на шейке ведущего валка
Диаметр шейки валка: dШРВ = 710 мм
Длина шейки валка: lШРВ = 1700 мм
коэффициент концентрации напряжений для шпоночного паза
Результирующее напряжение
МПа условие прочности выполняется
Находим напряжения в опорном валке
Максимальный изгибающий момент посередине бочки опорного валка от вертикального усилия P передаваемого через рабочий валок.
Максимальное напряжение изгиба посередине бочки опорного валка
Напряжение на шейке опорного валка в сечении 1-1
Диаметр шейки валка в данном сечении мм
расстояние от точки приложения равнодействующей реакции подшипника до края бочки мм
Напряжение на шейке опорного валка в сечении 2-2
Допустимые напряжения для валков из углеродистой стали
Коэффициенты запаса прочности от предела текучести
шейки опорного валка
шейки рабочего валка
Минимальный требуемый запас прочности n = 4. В данном случае валки полностью ему удовлетворяют расчёт на усталостною прочность не производим.
Рассчитываем контактное напряжение в поверхностном слое валков.
Определяем приведённый радиус валков
Модуль упругости для стальных валков: МПа
Модуль упругости для чугунных валков: МПа
Приведённый модуль упругости для стальных опорных и чугунных рабочих валков: МПа
кНмм - усилие на 1 мм ширины листа
Для валков с твёрдостью > 55 HRC []конт = 4400 МПа.
Определяем прогиб опорного валка.
Определяем момент инерции бочки валка
Определяем момент инерции шейки валка
Модуль сдвига для стальных валков: МПа
Модуль сдвига для чугунных валков: МПа
Приведённый модуль сдвига для стальных опорных и чугунных рабочих валков: МПа
расстояние от бочки валка до середины шейки с = 800 мм.
определяем прогиба в результате действия изгибающих моментов:
Определяем прогиба в результате действия поперечных сил:
Определяем разность прогибов в середине бочки валка и у края прокатываемого листа:
Определяем суммарный прогиб:
Расчёт на циклическую прочность.
Предел выносливости при изгибе:
Предел выносливости при кручении:
Масштабные факторы для валков диаметром > 500 мм:
Амплитуда цикла напряжений при изгибе:
Амплитуда цикла напряжений при кручении:
Коэффициент обработки поверхности:
Коэффициент характеризующий чувствительность материала к ассиметрии цикла напряжений:
Эффективный коэффициент концентрации при изгибе:
Эффективный коэффициент концентрации при кручении:
Коэффициент запаса прочности при изгибе:
Коэффициент запаса прочности при кручении:
Совместное действие кручения и изгиба:
условие прочности выполняется.
Валок.dwg

Режим прокатки+ vD.doc
Продольная протяжка до заданной ширины кантовка
Продольная протяжка до заданной ширины кантовка Прокатка во второй клети
Энергосиловые.doc
Диаметр рабочих валков стан:
Диаметр опорных валков стана:
Диаметр подшипников:
Мощность электродвигателей:
частота вращения электродвигателей:
угловая скорость электродвигателей:
Параметры прокатываемого листа:
Толщина листа до прокатки:
Толщина листа после прокатки:
Средняя толщина листа:
Абсолютное обжатие:
Относительное обжатие:
Отношение длины дуги захвата к средней толщине листа:
Коэффициент контактного трения:
Коэффициент наличия зон отставания и прилипания:
Проверяем наличие зоны прилипания на дуге захвата
значит зона прилипания имеется и её протяжённость при составляет:
участки скольжения на дуге захвата:
Определяем отношение pср по длине контакта l
Определяем скорость деформации металла
При температуре прокатки 1070 °C и скорости деформации СР = 8.9 1с предел текучести стали составляет: Д = 138 МПа. Удвоенная константа пластичности
Определяем среднее давление металла на валки и полное усилие прокатки.
усилие на 1 мм ширины прокатываемого толстого листа:
при максимальной ширине листа b = 4600 мм полное усилие прокатки:
Определяем момент прокатки.
определяем коэффициент плеча приложения равнодействующей давления
Определяем момент прокатки
плечо приложения силы a
Определяем момент трения.
Валки вращаются в подшипниках жидкостного трения поэтому принимаем
где P -усилие прокатки
dП- диаметр подшипников
DР- диаметр рабочего валка
DОП - диаметр опорного валка
Определяем статический момент.
(Момент на валу электродвигателя от статической нагрузки)
где i - передаточное число шестерённой клети
Проверка двигателя по моменту.
Коэффициент перегрузки по двигателю
Определение мощности прокатки.
Угловая скорость вращения валков
Мощность при прокатке
Мощность электродвигателей
Двигатели допускают кратковременную трёхкратную перегрузку по мощности.
Суммарная допустимая мощность двух двигателей стана:МВт что меньше мощности прокатки.
Определение времени прокатки.
Площадь поперечного сечения до прохода
Площадь поперечного сечения после прохода
Время нахождения полосы в клети составляет
Энергосиловые 1 проход.doc
Диаметр рабочих валков стан:
Диаметр опорных валков стана:
Диаметр подшипников:
Мощность электродвигателей:
частота вращения электродвигателей:
угловая скорость электродвигателей:
Скорость прокатки в 1 проходе:
Параметры прокатываемого листа:
Толщина листа до прокатки:
Толщина листа после прокатки:
Средняя толщина листа:
Абсолютное обжатие:
Относительное обжатие:
Отношение длины дуги захвата к средней толщине листа:
Коэффициент контактного трения при горячей прокатке:
Коэффициент наличия зон отставания и прилипания:
Проверяем наличие зоны прилипания на дуге захвата
значит зона прилипания не возникает (по всей дуге захвата имеется только скольжение).
Определяем коэффициент напряжённого состояния n=pср
Определяем скорость деформации металла:
При температуре прокатки 1200 °C и скорости деформации СР = 1.63 1с предел текучести стали составляет: МПа. Удвоенная константа пластичности:
Определяем среднее давление металла на валки и полное усилие прокатки:
Усилие на 1 мм ширины прокатываемого толстого листа:
При максимальной ширине листа мм полное усилие прокатки:
Определяем момент прокатки.
Определяем коэффициент плеча приложения равнодействующей давления
Плечо приложения силы a:
Определяем момент трения.
Валки вращаются в подшипниках жидкостного трения поэтому принимаем коэффициент трения в подшипниках:
где P -усилие прокатки
dП- диаметр подшипников
DР- диаметр рабочего валка
DОП - диаметр опорного валка
Определяем статический момент
(Момент на валу электродвигателя от статической нагрузки):
Проверка двигателя по моменту:
Коэффициент перегрузки по двигателю:
Определение мощности прокатки.
Угловая скорость вращения валков
Мощность при прокатке:
Мощность электродвигателей:
Двигатели допускают кратковременную трёхкратную перегрузку по мощности.
Суммарная допустимая мощность двух двигателей стана:МВт что меньше мощности прокатки.
Определение времени прокатки.
Площадь поперечного сечения до прохода:
Площадь поперечного сечения после прохода:
Длина после прохода:
Время нахождения полосы в клети составляет:
Станина.doc
Усилие прокатки P = 45.05 МН. Усилие прокатки воздействующее на станину для листовых станов составляет половину усилия прокатки:
Материал станины: углеродистая литая сталь со следующими
механическими характеристиками:
предел прочности МПа
модуль упругости МПа
Геометрические параметры сечения верхней поперечены:
Определение площади поперечного сечения верхней поперечены:
Определение положения центра масс верхней поперечены:
Определение момента инерции:
Определение момента сопротивления:
Геометрические параметры сечения стойки:
Определение положения центра масс стойки:
Определение площади поперечного сечения стойки
Геометрические параметры сечения нижней поперечины:
Определение площади поперечного сечения нижней поперечены:
Максимальный момент изгиба верхней и нижней поперечин силой Y:
Статистически неопределимые моменты в углах жёсткой рамы:
Отношение статистически неопределимых моментов:
При J1 = J3 и n = 1 получим:
Напряжения растяжения в середине верхней и нижней поперечин:
Напряжения растяжения в стойке станины:
Запас прочности станины для нижней поперечины при пределе прочности углеродистой литой стали МПа:
Прогиб среднего сечения от изгиба и поперечных сил
Упругое растяжение стойки станины:
Суммарная деформация станины по вертикали:
Жесткость станины по вертикали (в направлении действия силы Y):
Прогиб стоек станины по горизонтали:
Задание Дипломный Проект.doc
Государственное образовательное учреждение высшего профессионального образования
(ТЕХНОЛОГИЧЕСКОГО УНИВЕРСИТЕТА)
Факультет ММТ «УТВЕРЖДАЮ»
Кафедра Т и О П П Зав. кафедрой Ахмедшин Р.И.
Тема дипломного проекта _Реконструкция толстолистового стана горячей прокатки 5000_Ижорского металлургического завода
Исходные данные (в том числе проектная и технологическая документация и основная литература) _1._Материалы_преддипломной_практики_2._Материалы_КНИР_и_курсовых_работ
Перечень подлежащих разработке вопросов:
2. По технике производства1. Исходные материалы и нагрев их перед
4. По экономике и управлению производством _1._Расчёт_производительности_стана_5000_2._Расчёт_штата_рабочих_и_фондов
заработной_платы_3.Система_управления_качеством_готовой_продукции_4._Капитальные_вложения_в_реконструкцию_5._Расчёт_основных_фондов_6._Расчёт_себестоимости
Согласовано:Консультант по экономике и управлению производством
5. По безопасности жизнедеятельности _1._Географическое_и_территориальное_расположение_цеха_2._Технические_решения_по_производственной_санитарии_3._Анализ_потенциально_опасных_производственных
факторов_4._Разработка_мер_защиты_5._Безопасность_жизнедеятельности_при
Согласовано:Консультант по безопасности жизнедеятельности
6. По охране окружающей среды _1._Оценка_загрязнения_воздушного_бассейна
Оценка загрязнения водного бассейна 3. Утилизация отходов производства
Согласовано:Консультант по охране окружающей среды
Использование ЭВМ _1._Расчёт_энергосиловых_параметров (MathCad)
Выполнение пояснительной записки (Word Excel) 3. Выполнение графической части (AutoCad)
Перечень графического и иллюстрированного материала (с указанием обязательных чертежей) _1._План_листопрокатного_отделения_2._Поперечный_разрез_здания_цеха_3._Рабочая
клеть_4._Валковый_узел_5._Опорный_валок_6._Энергосиловые_параметры_7._Схема
Срок сдачи проекта руководителю 25.05.2009
Консультанты по проекту (с указанием относящихся к ним разделов)
Дата выдачи задания 23.03.2009
Руководитель проекта
Задание принял к исполнению студент
Список литературы.doc
П. И. Полухин Н. М. Федосов А. А. Королев Ю. М. Матвеев. Прокатное производство. М.: Металлургия1982. 696 с.
А. А. Королёв. Конструкция и расчёт машин и механизмов прокатных станов.
М.: Металлургия 1985. 375 с.
Сафьян М. М. Прокатка широкополосной стали. М.: Металлургия 1969. 460 с.
А. И. Целиков П. И. Полухин В. М. Хребенник и др. Машины и агрегаты
металлургических заводов. В Зх томах Т.З Машины и агрегаты для производства и
отделки проката. М.: Металлургия 1989. 576 с.
П.И. Полухин Г.Я. Гунн А.М. Галкин. Сопротивление пластической деформации металлов и сплавов. М.: Металлургия 1983. 352 с.
Антипин В.Г. Савчук А.А. О производстве толстого листа и труб большого диаметра для магистральных газопроводов Черная металлургия. Бюллетень. – 2001. - №3. – С. 3-6.
Технология трубного производства. В.Н. Данченко А.П. Коликов. Б.А. Романцев С.В. Самусев - М. "Интермет-Инжиниринг"2002. 650 с.
Охрана труда в металлургии. Б.М. Злобинский. М.: Металлургия 1975. 536 с.
Охрана труда в машиностроении. Под редакцией Е.Я Юдина С.В. Белова. М.: Металлургия 1983. 432 с.
Журнал «Сталь» №12 2007 г.
ГОСТ 19903-74 Прокат листовой горячекатаный. Сортамент.
ГОСТ 12.1.005-88 Система стандартов безопасности труда.
ГОСТ 2789-73 Шероховатость поверхности. Параметры и характеристики.
ГОСТ 7634-75 Подшипники радиальные роликовые многорядные с короткими цилиндрическими роликами
Методические указания по дипломному проектированию для специальности 11060 «Обработка металлов давлением». В.Т. Торшин С.Б. Чеканова. Электросталь 2005 56 с.
ВЕДОМОСТЬ ОБЪЕМА ДИПЛОМНОГО ПРОЕКТА.doc
Пояснительная записка
План расположения оборудования в ЛПЦ-3
Разрез клети стана 5000
Энергосиловые параметры
График работы стана во времени
Технико-экономические
ЭПИ МИСиС г.Электросталь
Подшипник рабочего валка
Гидроциллиндр системы уравновешивания верхнего рабочего валка
Гидроциллиндр системы уравновешивания верхнего опорного валка
Подушка верхнего опорного валка
Подушка верхнего рабочего валка
Электродвигатель станинных роликов
План листопрокатного отделения стана 5000
Двухвалковая горизонтальная клеть
Двухвалковая вертикальная клеть
Машина огневой зачистки
Черновая клеть кварто
Чистовая клеть кварто
План листопрокатного отделения
валок.dwg

План цеха 2.dwg

Заземление.dwg

соединяющие оборудование с заземляющим контуром и контурными заземлителями; 5-внешний контур заземления."
Записка.doc
1. Экономическая целесообразность проекта
Прямошовные и спиральношовные трубы большого диаметра предназначены для магистральных трубопроводов газа нефти нефтепродуктов а также для водо- и паропроводов низкого давления.
Сварные трубы для магистральных трубопроводов изготавливают прямошовными и спиральношовными диаметром 529—2560 с толщиной стенки 8—35 мм Основной сортамент используемых труб большого диаметра приведён в таблице 1.1.
Таблица 1.1 - Сортамент и механические свойства труб для трубопроводов
Применяемая марка стали
Допускаемые отклонения
Ударная вязкость а* кДжм2
Прямошовные горячетравленые трубы
Прямошовные горячетравленые экспандированные трубы
Спиральношовные трубы с локальной термообработкой
То же термоупрочненные
* в числителе — для основного металла в знаменателе — для металла шва. Температура испытаний —40 °С 7.
Главным потребителем труб большого диаметра является нефтегазовая отрасль промышленности. Трубы большого диаметра применяются при строительстве магистральных газо- и нефтепроводов. Что особенно актуально для нашей страны в связи с большой протяжённостью территорий. Данные о протяжённости газотранспортной системы нашей страны приведены в таблице 1.2.
Таблица 1.2 - Данные о протяженности газопроводов в России
Увеличение добычи углеводородов приводит к необходимости увеличивать объёмы трубного производства. Производство труб сварных большого диаметра в 2001 - 2006 гг. выросло в 22 раза. Так потребность в трубах диаметром 1420 мм в 2001 г. составила около 900 тыс. т. а к 2010 г. возрастет до 1000-1200 тыс. т. Что несомненно потребует увеличения производства заготовок. В среднесрочной перспективе ежегодно потребуется около 600 тыс. т толстого листа и 900-1000 тыс. т труб диаметром 1420 мм.
За 50 лет строительства магистральных нефтегазопроводов (1956 - 2006 гг.) было смонтировано труб СБД более 80 млн.т. Даже при увеличении сроков службы труб до 50 лет (над этой задачей работает Газпром) потребность в них на реконструкцию возрастёт в ближайшие 10 лет до 16 – 2 млн. т в год. Реальная потребность может возрасти до 4 млн. т в год. 6
Заготовки под одношовные трубы диаметром 1420 мм в нашей стране на данный момент может производить только толстолистовой реверсивный стан 5000. В настоящее время стан Ижорского металлургического завода оборудован одной реверсивной клетью кварто. При этом его максимальная производительность составляет порядка 850 тыс. т. Следует так же учесть что стан 5000 Ижорского металлургического завода производит прокат для всей промышленности нашей страны а не только нефтегазовой. В частности на стане прокатываются листы броневой стали и из титановых сплавов потребление которых тоже возрастает. На стане проводились модернизации в виде установки более производительных печей замены отдельных узлов на более совершенные (например система гидросбива окалины установленная на стане в данный момент является второй по мощности в Европе) однако установка второй клети позволить значительно повысить производительность стана в целом.
При установке второй клети изменится технологический процесс: существующая клеть кварто станет черновой и будет производить подкат для проектируемой чистовой клети. Подобные схемы технологического процесса уже существуют например на толстолистовом реверсивном стане 3600 завода «Азовсталь».
Таблица 1.3 - Основной сортамент стана 5000
Листовой прокат классов прочности К52 К55 производится по
ТУ 14-1-1950-89. Предназначен для изготовления электросварных прямошовных труб для магистральных газо- и нефтепроводов.
Механические свойства
Временное сопротивление Нмм2 (кгсмм2)
Предел текучести Нмм2 (кгсмм2)
Односительное удлинение %
Ударная вязкость Джсм2
Листовой прокат класса прочности К52. Производится по ТУ 14-1-1921-76. Предназначен для изготовления электросварных прямошовных газопроводных труб.
Продолжение таблицы 1.3
Временное сопротивление Нмм2
Предел текучести Нмм2
Прокат листовой применяется для изготовления электросварных прямошовных труб магистральных газо- нефтепроводов. Производится по ТУ 14-1-4034-96. Сортамент
Толщина – 12-22 мм определенной мерной длины от 11500 до 11800 мм. Предельные отклонения по длине листов – по ГОСТ 19903-74.
Временное сопротивление Нмм2
Предел текучести Нмм2
Прокат производится по ТУ 14-1-4627-96 и используется для изготовления:
электросварных спиральношовных труб диаметром 530-1420 мм (листовой и рулонный)
электросварных труб диаметром 530-1020 мм (толстолистовой прокат).
Прокат толстолистовой производится по ТУ 14-1-5246-94 предназначен для изготовления газопроводных труб северного исполнения.
Листовой и рулонный прокат из конструкционных марок стали производится по ТУ 14-1-4358-87 предназначен для изготовления электросварных прямошовных труб и труб свариеваемых токами высокой частоты (ТВЧ) диаметр труб - до 530 мм.
Техника производства
1. Исходные материалы и нагрев их перед прокаткой
Исходным материалом при прокатке толстолистовой стали на толстолистовом стане 5000 являются слябы прокатываемые на слябингах и блюмингах либо полученные на машинах непрерывного литья заготовок (МНЛЗ). Листовые слитки применяют только при прокатке толстолистовой стали толщиной более 60 мм. Массу слитков в этом случае определяют исходя из размеров готового проката и расхода металла (фабрикационного коэффициента). Листовые слитки обычно плоские: они характеризуются отношением ширины к толщине высоты к толщине или ширине и конусности. При выборе толщины слитка следует принимать такое суммарное обжатие которое обеспечивает получение необходимого качества листовой стали. На основании практических данных принимают минимальную толщину слитка равную не меньше 15—20-кратной толщины готового листа; конусность слитков должна быть минимальной.
Прокатка листовой стали из слябов более рациональна так как при этом повышается качество листовой стали и снижаются отходы. Размеры и массу слябов при прокатке толстолистовой стали выбирают в зависимости от размеров листов. Однако наиболее рациональными являются слябы имеющие наименьшую толщину и наибольшую ширину. Благодаря этому число проходов уменьшается что способствует значительному увеличению производительности стана. Длина слябов для прокатки на толстолистовых станах часто ограничивается длиной бочки валков так как слябы с длиной больше длины бочки валков не позволяют вести прокатку поперек для разбивки ширины листа.
Если разбивку ширины листа не производят длина сляба ограничивается допустимыми температурой конца прокатки и разницей температур переднего и заднего концов полосы.
При выборе размеров сляба необходимо учитывать также условия работы блюминга или слябинга на данном заводе. Слябы являются исходным материалом и при прокатке универсальной стали. Ширину слябов в этом случае принимают больше ширины полосы на 20—50 мм. Толщину и длину слябов определяют исходя из длины прокатываемой полосы. Следовательно и в этом случае чем меньше толщина сляба тем меньше число проходов.14
Осуществляют в методических печах с проходными тележками и с выкатным подом. Топливом является смесь доменного и коксового газов или природный газ.
Нагревательные печи для нагрева слябов оборудованы загрузочным рольгангом и реечными толкателями. Нагретые слябы от печи к стану поступают по подводящему рольгангу. При горячей прокатке листовой стали происходит значительное снижение температуры. Чтобы закончить прокатку при необходимой температуре слябы следует нагревать до максимально допустимой температуры так как при этом значительно снижается сопротивление деформации.
Температура нагрева слябов зависит от химического состава стали и составляет 1150—1280 °С. Продолжительность нагрева зависит от толщины слябов химического состава стали и температуры при их посадке. Общее падение температуры дымовых газов весьма значительно. Температура газов держится на уровне 1300—1400 °С в зоне высоких температур в конце методической зоны она находится в пределах 850—1100°С.
Ограничение скорости нагрева холодного металла в интервале температур от 0 до 500 °С распространяется в основном на качественные и высоколегированные стали. 3
2 Технологический процесс прокатки на стане 5000
На толстолистовом стане 5000 предусмотрены следующие основные технологические потоки:
прокатка плит из слитков с обрезкой горячей головной части и последующей противофлокенной обработкой (окончательную обработку плиты проходят в термическом цехе);
прокатка и термоупрочнение плит толщиной до 160 мм с прокатного нагрева;
прокатка и термоупрочнение листов толщиной 10-50 мм с прокатного нагрева с последующим отпуском и полной отделкой в потоке стана;
прокатка листов с последующей противофлокенной обработкой вне потока возвратом в поток для закалки с отпуском и полной отделки;
прокатка листов с последующей нормализацией охлаждением отпуском и отделкой в потоке;
прокатка листов с последующей аустенизацией правкой и порезкой в потоке окончательная отделка листов - в травильно-зачистном отделении;
прокатка листов с последующим отжигом вне потока возвратом в поток для правки с температурой отжига охлаждением правкой порезкой передачей в травильно-зачистное отделение для окончательной обработки;
прокатка и отделка листов в потоке стана без их термической обработки.
Расположение оборудования стана которое используется при прокатке приведено на рисунке 1.
Слитки и слябы подаются в пролет нагревательных печей железнодорожным транспортом на специальных платформах и загружаются краном в нагревательные колодцы или печи с выкатным подом. Температура нагрева составляет 1180—1280° С. После нагрева слитки транспортируются и укладываются клещевым краном или слитковозом на рабочий рольганг центрируются по оси прокатки манипулятором головной частью вперед взвешиваются и при помощи поворотного устройства поворачиваются на 180° и узким концом (донной частью) по рольгангу подают к двухвалковой клети с горизонтальными валками. Сюда же поступают нагретые в печах (3) слябы.
Чтобы уменьшить действие динамических нагрузок на подшипниковые опоры роликов рольгангов и фундаменты при прокатке тяжелых слитков массой до 60 т рабочие рольганги перед и за клетями установлены на амортизаторах. Для этого применяются железнодорожные серийные взаимозаменяемые поглощающие аппараты ЦНИИ-Нб или Р-2П. Рольганг состоит из десяти цельнокованых конических роликов смонтированных в стаканах на двухрядных сферических подшипниках качения.
Затем происходит прокатка в клети с вертикальными валками в которой снимается конусность боковых граней слитка разрушается слой окалины удаляемой затем гидросбивом под давлением 15-18 МПа. При реверсивной прокатке сляба в двухвалковых вертикальной и горизонтальной клетях так же происходит интенсивное взрыхление окалины облегчающее её дальнейшее удаление устройствами гидросбива. Непосредственно за вертикальной клетью расположена машина огневой зачистки. Она предназначена для улучшения поверхности сляба в частности для удаления поверхностных дефектов. Далее заготовка на максимальной скорости для уменьшения времени остывания по рольгангу передаётся к черновой четырёхвалковой клети.
В черновой четырехвалковой клети слиток центрируется манипулятором и задаётся в валки. При прокатке слитка сначала снимается конусность широких граней слитка затем на рольганге с коническими роликами слиток (имеющий высоту менее 3000 мм) поворачивается на 90° и прокатывается поперек своей оси с целью увеличения ширины слитка (до требуемой ширины толстого листа). При этом боковые грани могут периодически обжимаются в клети с вертикальными валками для получения плиты требуемой ширины. Таким образом формируется подкат для чистовой клети. Температура начала прокатки обычно составляет 1250 – 1200 °С. Толщина раската получаемого в черновой клети составляет не более 100 мм. Скорость прокатки обычно составляет порядка 2-3 мс. Относительно невысокая скорость прокатки применяется для согласования тактов прокатки черновой и чистовой клетей.
Рис 1. Схема расположения оборудования толстолистового стана 5000
Далее уширенный слиток снова поворачивается коническими роликами рольганга на 90° головной частью вперед и передаётся в чистовую клеть где центрируется линейками манипулятора и прокатывается до требуемого размера по толщине. В процессе прокатки окалина с поверхности листа удаляется устройством гидросбива. Температура начала прокатки в чистовой клети составляет не ниже 1050 °С; температура конца прокатки порядка 830 °С в зависимости от марки стали. Скорость прокатки составляет до 45 мс. Скорость прокатки выше чем в черновой клети т.к. длина раската в последних проходах может достигать 15 м а его толщина всего 10 мм то происходит интенсивное охлаждение металла более высокая скорость позволяет сократить время прокати.
После прокатки листы передаются к правильным машинам. Цех оборудован двумя подобными агрегатами:
листы толщиной до 25 мм с коробоватой поверхностью подвергают горячей правке при температуре около 500° С (для упрочнения листов) на роликовой— правильной машине (РПМ № 1) и далее по рольгангу направляют на дальнейшую отделку;
листы толщиной 25—50 мм частично охлаждают на передаточном шлеппере и правят на правильной машине (РПМ №2); в этом случае правильная машина (РПМ № 1) сдвигается с линии рольганга и заменяется передвижной секцией рольганга; далее листы охлаждают до 100—200° С на холодильнике и до 50—100° С водой в охлаждающем устройстве.
При подаче слитков в рабочую клеть оба привода рольганга работают в одну сторону. При развороте подката на 90° для прокатки по ширине левый и правый приводы рабочего рольганга вращаются в разные стороны.
В процессе прокатки в клети периодически осуществляется гидросбив окалины водой под давлением 18-20 МПа После предварительного обжатия на 40-50% раскаты подаются к машине огневой зачистки (6) для поочередной зачистки верхней и нижней поверхностей при этом раскат кантуется кантователем на 180°. Для этого раскат задается рольгангом в зону кантователя так что его передний конец находится над рабочей поверхностью стола-шабота. Включением левого гидропривода левая кантующая плита ставится в вертикальное положение. Правый гидропривод поднимает правую кантующую плиту и вместе с раскатом и прижимает его к левой плите. Плиты с зажатым раскатом совместно отклоняются от вертикали на угол 15° после чего правая плита возвращается в исходное положение а левая укладывает раскат на рольганг.
После зачистки раскат возвращается к клети кварто для дальнейшей прокатки до заданных размеров. Во время прокатки раскат периодически центрируется по оси манипуляторами.
Все прокатанные листы и плиты проходят правку в листоправильных машинах (14 или 15) и клеймение в установленном над рольгангом клеймителе (18).
При необходимости после прокатки лист и плиты толщиной до 160 мм массой до 30 т проходят термоупрочнение с прокатного нагрева в закалочной машине (9) для чего горячие листы и плиты после прокатки в вертикальном положении опускают в ванну с водой и затем плавно укладывают их обратно на рольганг. После чего раскат центрируется но оси рольганга и клеймится. Клеймитель рычажного типа с приводом от пневмоцилиндра предназначен для клеймления листов и плит в горячем и холодном состоянии после термоупрочнения.
По другой технологии прокатанные листы и плиты поступают на рольганг с подъемным устройством и передаются сталкивателем на передаточное устройство для транспортировки в пролет склада.
Подъемное устройство с рольгангом (10) представляет собой шарнирный четырехзвенник паралелограммного типа состоящий из подъемных балок рычагов и трансмиссионного вала с приводом от двух гидроцилиндров. В исходном положении балки опущены и ролики балок находятся ниже верхних образующих бочек роликов рольганга на 80 мм В крайнем верхнем положении балок подъемного устройства между нижней поверхностью балки и бочкой роликов рольганга образуется зазор 200 мм позволяющий транспортировать по рольгангу листы толщиной до 50 мм к листоправильным машинам.
Сталкиватель плит (10) предназначенный для сталкивания плит с балок подъемного устройства на тележки передаточного устройства реечного типа с приводом от электродвигателя через редуктор.
Передаточное устройство плит (10) для транспортировки плит из станового пролета цеха в пролет склада состоит из двух самоходныхте лежек перемещающихся каждая по своему рельсовому пути. В зависимости от габаритов транспортируемых плит тележки могут работать совместно и раздельно. Сцепляются и расцепляются тележки с помощью специальных выдвигающихся упоров. Мостовой кран с помощью траверсы с управляемыми подхватами снимает плиты с тележки и передает на линию резки
На складе концы и боковые кромки листов обрезаются на машинах газовой резки (11 12). В этом же пролете расположен кантователь листов и плит (13) для контроля качества поверхности. После обрезки листы и плиты направляются для термической обработки и отделки в соответствующие цеха.
Еще одним технологическим потоком предусматривается транспортирование проката после правки (14 или 15) клеймения (18) и обрезки переднего и заднего концов и боковых кромок на ножницах (16 и 17) на холодильник (20). Далее листы проходят термообработку (нагрев закалку и отпуск) в закалочных машинах (19 или 26).
3. Контролируемая прокатка
Для повышения качества готовой продукции на стане 5000 освоено применение контролируемой прокатки. Это горячая прокатка преимущественно конструкционных феррито-перлитных сталей по регламентируемым температурно-деформационным режимам для формирования в готовом прокате мелкозернистой структуры с упорядоченным распределением дефектов кристаллической решетки обеспечиваищей повышение предела текучести снижение температуры вязко-хрупкого перехода и улучшение свариваемости. Применяются две основные технологические схемы контролируемой прокатки: низко- (НТКП) и высокотемпературная (или «рекристаллизационная») контролируемая прокатка (ВТКП).
НТКП была разработана в 1970-х гг. и внедрена на многих металлургических фирмах Германии Японии и США при производстве толстолистового проката для магистральных газопроводов большого диаметра. В 1980-х гг. НТКП толстолистового проката была освоена на ряде металлургических заводов России и Украины. НТКП осуществляется как правило на реверсивных станах и включает три стадии многопроходной горячей деформации с регламентируемыми разовыми и суммарными обжатиями: выше температуры рекристаллизации аустенита когда при повторной рекристаллизации происходит измельчение зерна аустенита с последующим охлаждением со скоростью до 15—20 °Сс. Причем для НТКП были разработаны специальные малоперлитные микролегированные Mb Ti иили V стали (типа 10Г2ФБ или 10Г2ФБТ). В результате было достигнуто резкое повышение (на 100—150 МПа) прочности и особенно вязкости горячекатаного проката при отрицательных температурах (при испытании DWTT при -20 ºС доля вязкой составляющей > 80 %). Основные структурные факторы упрочнения таких сталей после НТКП: измельчение зерна феррита и дисперсное упрочнение вследствие выделения мелкодисперсных карбидных частиц которое интенсифицируется низкотемпературной конечной горячей деформацией. Однако необходимость значительных разовых обжатий (до 20 %) при пониженных температурах окончания горячей деформации (700—780 °С) обусловливает большие нагрузки на валки чистовых клетей что требует применения для НТКП специализированных прокатных станов и соответственно сужает области применения этой технологии в частности для сортового и фасонного проката.
Структурно-технологические принципы ВТКП в условиях горячей прокатки с окончанием деформации при режимах близких к режимам прокатки на серийных непрерывных листовых и сортовых станах горячей прокатки были разработаны в России и в зарубежных странах (США Японии др.) в 1980-х гг. Эти принципы базируются на фундаментальных положении фазовых превращениях в Fe-C сплавах о том что мелкозернистую ферритно-перлитную структуру в горячедеформированной стали можно получить в результате γ-α-превращения как перекристаллизованного деформированного (наклепанного) аустенита так и повторно рекристаллизованного аустенита если в нем сохраняется достаточно мелкое зерно. Это условие обеспечивает карбонитридное микролегирование (Ti V Al N) стали при котором в
горячедеформированном аустените выделяются дисперсные карбонитридные фазы препятствующие росту зерна при повторной рекристаллизации преимущественно по «барьерному» механизму. 11
4. Назначение и состав оборудования стана 5000
Толстолистовой стан 5000 горячей прокатки предназначен для прокатки крупногабаритных листов толщиной 10 - 50 мм шириной 1500 - 4800 мм и длиной до 15 м а также плит толщиной 50 - 300 мм из углеродистых легированных и специальных сталей и сплавов в том числе с применением термомеханической обработки (прокатка при пониженной температуре раската).
В качестве исходной заготовки для прокатки используют кованые слябы и слитки массой 5 - 60 и 5 - 40 т соответственно.
Техническая характеристика стана 5000
ширина (без обрезки кромокс обрезкой)48004600 мм
длина мерных листовдо 15 м
Максимальная длина раската:до 30 м
Толщина плит:50 - 300 мм
Максимальная масса сляба:60 т
Максимальная масса слитка:40 т
в клети дуо и в вертикальной клетидо 3 мс
в чистовой клети квартодо 45 мс
Диаметры минмакс (длина) бочки валков клетей:
дуо12001350(4000) мм
вертикальной10001100(1100) мм
рабочих10701150(5000)мм
опорных20002200(4800)мм
Мощностьмомент номинальный привода валков:
клети дуо2×6700кВт145МНм
вертикальной2×2000 кВт
кварто черновая2×6700кВт145МНм
кварто чистовая2×6700кВт145МНм
Масса механического оборудования:51600 т
Установленная мощность электрооборудования:95000 кВт
Площадь цеха:98684 м2
Состав технологического оборудования стана и схема его расположения представлены на рисунке 1.
В состав технологического оборудования полного комплекса стана 5000 входит: оборудование участка нагрева слитков и слябов - нагревательные колодцы (1) и печи (3) слитковоз и приемное устройство (2). Участок рабочих клетей включает черновую клеть дуо (4) клеть с вертикальными валками (5) Черновую клеть кварто (7) чистовую клеть кварто (8) а также машину огневой зачистки (6) и транспортные рольганги с центрирующими и кантующими устройствами.
Большой объем оборудования отделки и термообработки вызван сложным марочным сортаментом и большим количество типоразмеров прокатываемых листов.
В состав отделочного оборудования входят машины поперечной и сдвоенные машины продольной огневой резки (11 и 12) ножницы поперечной резки (16) сдвоенные кромкообрезные ножницы (17) клеймители (18 и 23) листоправильные машины для листов толщиной 8 - 24 и 25 - 50 мм (14 и 15)листоукладчик (21) дробеметная машина (22) и транспортные средства (кантователь (13) рольганги сталкиватели передаточные тележки (10) и др.).
Средства для термообработки (закалка отжиг отпуск) включают машину для закалки листов окунанием (9) закалочные машины (19 и 26) печи для отпуска (24) и закалки (25) листов.
Для обеспечения работы оборудования предусмотрены смазочные системы расположенные в маслоподвалах и гидравлические системы размещенные в гидроподвалах насосно-аккумуляторной станции стана.
Завод отличает удобная логистика: близкое расположение морского порта (30 км) речного порта (прилегает к территории) железной дороги (на территории промышленной площадки).
5. Чистовая клеть кварто толстолистового стана 5000
Особенностью конструкции клети стана 5000 по сравнению с существующими отечественными станами является ее большие габаритные размеры что вызвано необходимостью воспринимать конструктивными элементами клети большие технологические нагрузки. Это обстоятельство затрудняет применение в конструкции клети традиционных решении.
Примерно можно считать что при прочих равных условиях усилия и моменты прокатки пропорциональны ширине прокатываемых листов. Тогда как показывает анализ с учетом прокатки высокопрочных марок сталей с пределом прочности до 1200 МПа против 700 МПа освоенных в настоящее время на толстолистовых станах максимальное усилие прокатки составит 90 МН и максимальный момент на рабочем валке - 3 МН м.
Конструкция опорных валков определена из условий прочности при нагрузках необходимых для прокатки раската максимальной ширины (4800 мм) и допустимой погонной нагрузки в межвалковом контакте рабочего и опорного валков с одной стороны и техническими возможностями для изготовления таких крупногабаритных деталей с другой:
Техническая характеристика клети кварто стана 5000
Длина бочки опорныхрабочих валков:48005000 мм
Максимальная ширина листа:4800 мм
Максимальная масса сляба:до 60000 кг
Диаметр рабочих валков минмакс:1050-1120 мм
Диаметр опорных валков минмакс:2200-2360 мм
Оптимальная глубина слоя переточки опорного валка: 50-100 мм
Максимальное усилие прокатки:90 Мн
Максимальный момент на рабочем валке:3 Мнм
Отключающий момент на рабочем валке:36 Мнм
Максимальная скорость прокатки:45 мс
Нажимное устройство:2 шт.
профиль резьбы нажимных винтов:спец. УП 80064 мм
мощность электродвигателя:2×630 кВт
скорость вращения:750 обмин
передаточное число редуктора:1978
цена деления циферблата:0110 мм
скорость перемещения верхнего валка:095- 54 ммс
скорость перемещения при перевалке:
рабочих валков150 ммс
опорных валков50 ммс
Максимальный рабочий раствор валков:1100 мм
Максимальное перемещение при перевалке:
комплекта рабочих валков13200 мм
комплекта опорных валков13760 мм
поддона с прокладками15440 мм
Станинные ролики:6 шт.
мощность электродвигателя315 кВт
скорость вращения315 обмин
Давление воды в системе гидросбива:18 МПа
диаметрдлина18001600 мм
максимальное усилие45 МН
Подшипники качения рабочих валков:12 шт.
Уравновешивание верхнего рабочего валка:2 цилиндра
диаметр плунжера цилиндра 420 мм
давление рабочей жидкости188-196 МПа
Уравновешивание верхнего опорного валка:2 цилиндра
диаметр плунжера цилиндра360 мм
Уравновешивание нижнего опорного валка:4 цилиндра
диаметр штокапоршня цилиндра280320 мм
Прижим нижнего рабочего валка к опорному:4 цилиндра
диаметр плунжера цилиндра180 мм
Разгрузочное устройство:
диаметр поршня1500 мм
давление масла в цилиндре255 МПа
Модуль жесткости рабочей клети:65 МНмм
Грузоподъемность крана для термообработки оси валка:185 т
Максимальная грузоподъемность вальцетокарного станка:210 т
Максимальная масса слитка:
для заготовки бандажа225 т
При этом конструктивно принята длина бочки опорного валка 4800 мм и из условий прочности минимальный диаметр бочки валка 2200 мм. Диаметр и длина шеек опорных валков выбраны с учетом размеров конической посадочной поверхности втулок-цапф ПЖТ 1800 грузоподъемность которых составляет 45 МН каждого.
Рабочие и опорные валки
Для уменьшения массы отдельных составляющих принят вариант сборно-сварной конструкции опорного валка (рисунок 2) Валок состоит из полой оси сваренной из двух полуосей (шов - по оси прокатки) и посаженного на нее по горячей посадке бандажа. Конструкция валка не разборная сборка производится на заводе-изготовителе. Для сварки половинок осей применяется электрошлаковая сварка. Материал оси: сталь 45ХНМ бандажа: 90ХФ. Различные марки стали выбраны для обеспечения прочностных качеств валка: бандаж из более твёрдой стали надет на упругую ось подобная конструкция позволяет валку испытывать высокие напряжения сохраняя при этом высокую твёрдость поверхности. Необходимая твёрдость рабочей поверхности валка (50-60 HS) достигается накаткой.
Рисунок 2. Схема опорного валка стана 5000
Рабочие валки клети - чугунные с отбеленной поверхностью бочки твердостью 69-70 HS диаметр бочки валка 11201050 мм масса - 52 т. По краям бочки расположены цилиндрические шейки диаметром 750 мм предназначенные для опор под люнеты вальцешлифовального станка. При перешлифовках валок устанавливается на вальцешлифовальный станок в сборе с подушками. Это уменьшает объем работ и время на перешлифовку. Поверхность валков имеет напыление из быстрорежущей инструментальной стали выполненное по технологиям фирм “Nippon Steel” и “Hitachi metals”. Это позволяет повысить износостойкость валков более чем в пять раз.
Валки вращаются в радиальных роликовых многорядных подшипниках с короткими цилиндрическими роликами для восприятия радиальной нагрузки при прокатке и усилия поджима рабочих валков к опорным. Для восприятия осевой составляющей усилия прокатки (с одной стороны клети) и фиксации плавающей подушки на шейке валка (с другой) применены двухрядные упорные подшипники качения. Внутренние кольца этих подшипников выполнены гладкими и установлены на шейке валка по посадке с натягом.
Подушки рабочих валков выполнены коваными из стали 38ХНЗМФА. В расточке подушки между радиальными роликовыми многорядными подшипниками с короткими цилиндрическими роликам расположен центральный массивный кольцевой бурт который повышает жесткость подушки уменьшает деформацию расточки под подшипники обеспечивает более равномерное распределение нагрузки между роликами подшипника.
Подушки нижнего рабочего валка снабжены катками на которых по направляющим комплект рабочих валков перемещается из клети при перевалке.
Подшипники опор рабочих валков смазываются масляным туманом с рабочим давлением 003-004 МПа (расход масла на одну опору 92 гч воздуха 184 м3ч).
Привод рабочих валков клети - индивидуальный редукторный.
Система уравновешивания валков
Конструкция системы уравновешивания валков имеет свои особенности (рисунок 3). Большая масса подвижных деталей перемещаемых при изменении межвалкового зазора (800 т - верхняя валковая группа 460 т - нижняя) требует больших усилий в системе А большая инерционность вращающихся масс опорных валков и увеличенные потери на трение в ПЖТ из-за отсутствия достаточной толщины слоя масла при пуске электродвигателя главного привода валков требуют больших усилий прижатия приводного рабочего валка к холостому опорному чтобы исключить проскальзывание валков относительно друг друга при реверсе с большими ускорениями (замедлениями). В конструкции также целесообразно исключить подвод трубопроводов высокого давления к подвижным элементам клети: подушкам верхних рабочего и опорного валков траверзе и другим чтобы избежать применения уплотнении деталей перемещаемых друг относительно друга т.е. гидроцилиндры желательно размещать на неподвижных элементах клети - станинах.
Система уравновешивания верхнего рабочего валка состоит из двух гидроцилиндров плунжерного типа диаметром 420 мм установленных на верхних поперечинах станин клети коромысел тяг четырех крюков и двух балок уравновешивания расположенных в окнах станин по бокам валка. Балки одновременно выполняют роль проводковых брусьев и при перевалках остаются в клети на приливах стоек станин. Давление рабочей жидкости в гидроцилиндрах 188-196 МПа.
Кроме массы верхнего рабочего валка балок уравновешивания и крюков гидроцилиндры уравновешивают верхний опорный валок путем поджатая бочки рабочего
Рисунок 3. Система уравновешивания
валка к опорному с усилием 2890-2620 кН что обеспечивает реверс опорного валка без проскальзывания. Усилие передаваемое от шейки опорного валка через ПЖТ к подушке при реверсе составляет 900 -1500 кН.
Масса верхнего опорного валка его подушек балок уравновешивания двух месдоз нажимных винтов с подпятниками и коромыслами уравновешивается усилиями двух гидроцилиндров плунжерного типа диаметром 360 мм установленных в верхней части клети рядом с гидроцилиндрами уравновешивания массы верхнего рабочего валка. Усилие уравновешивания через коромысла и тяги передается на балку затем на концевые корпуса установленные рядом с подушками на шейках верхнего опорного валка. В корпусах установлены подшипники качения. Система обеспечивает гарантированный поджим втулки-цапфы к втулке-обойме ПЖТ и подушке и исключает проскальзывание рабочего валка относительно опорного.
При перевалках верхнего рабочего валка полость гидроцилиндров уравновешивания верхнего опорного валка запирается и последний зависает на тягах в окне станины на заданной высоте.
При перевалках верхнего опорного валка гидроцилиндры опускают его на перевалочную балку балка уравновешивания зависает на упорах тяг и полость гидроцилиндров подключается на слив.
Поджим нижнего рабочего валка к опорному осуществляется четырьмя стационарными цилиндрами плунжерного типа диаметром 180 мм расположенными в приливах станин и работающими на сжатом азоте при давлении 188-196 МПа. Применение газообразной среды (азота) вместо жидкой снижает ударные нагрузки в трубопроводах при задаче проката в валки. Усилие поджима между валками 2920-2800 кН что обеспечивает реверс опорного валка без проскальзывания.
Для уменьшения усилия поджима втулки-цапфы ПЖТ к втулке-обойме и подушке опорного валка при работе стана и в паузах между пропусками до 460-800 кН подвижная масса нижнего рабочего и опорного валков частично уравновешена четырьмя гидроцилиндрами поршневого типа диаметром 280320 мм. Штоки гидроцилиндров упираются в концевые корпуса установленные рядом с подушками на шейках нижнего опорного валка.
При работе стана рабочая жидкость под давлением подается одновременно в штоковую и поршневую полости. При перевалке штоковые полости переключаются на слив и нижняя валковая группа поднимается гидроцилиндрами вверх до упора лап подушек нижнего рабочего валка в приливы станин. Снижается давление азота в гидроцилиндрах поджима нижнего рабочего валка к опорному. После удаления поддона с прокладками нижний опорный валок опускается гидроцилиндрами на тележку с катками. Нижний рабочий валок опускается на направляющие и между бочками нижних рабочего и опорного валков образуется зазор.
В перевалочной яме расположена одна тележка а не две как на аналогичных станах для раздельной перевалки рабочих и опорных валков с подушками и поддонов с прокладками для регулирования высотной отметки бочки нижнего рабочего валка. Особенностью тележки является наличие отдельных сцепных устройств: для перевалки нижнего опорного валка передвижного настила нижнего рабочего валка и поддона. Из-за большого хода валков при перевалке в качестве привода перемещения тележек применяют реечный механизм.
Клеть кварто снабжена приспособлениями для замены вышедших из строя узлов и деталей доступ к которым краном затруднен что сокращает время простоев стана и облегчает процесс замены. После удаления из клети узла валков на направляющие краном устанавливают тележку.
С помощью устройства для перевалки валков тележку с приспособлением перемещают по направляющим в проем станин. После опускания на тележку изношенного узла ее обратно перемещают на сторону перевалки в зону обслуживания краном. Таким образом производится демонтаж нажимных винтов с гайками месдоз с подпятниками балок уравновешивания верхних валков гидроцилиндров уравновешивания нижнего опорного валка и поджима нижнего рабочего валка к опорному.
Еще одной особенностью стана 5000 является совмещение технологий прокатки в одной клети толстых плит и листов предъявляющих различные требования к конструкции нажимных механизмов перемещения валков. При реверсивной горячей прокатке слитков и толстых слябов с целью сокращения времени пауз между пропусками и соответственно сохранения температуры раската необходима высокая скорость перемещения верхнего валка при его установке. Точность же установки валка в первых проходах относительно невелика. Регулирование толщины по длине раската в этих проходах не требуется.
В последних проходах когда величина перемещения валков между проходами определяющая обжатие за проход становится относительно небольшой в связи с уменьшением толщины раската более важным параметром нажимного механизма становится не скорость перемещения а точность установки валков определяющая точность толщины листов.
Удовлетворить эти противоречивые требования можно путем установки двух типов нажимных устройств: высокоскоростного механического и высокоточного гидравлического (ГНУ). Первое - установочное предназначено для установки межвалкового зазора в паузах между пропусками с помощью двух нажимных винтов с приводом вращения через цилиндрические зубчатые передачи смонтированные в стальном литом корпусе ГНУ используется при достижении раскатом определенной длины когда требуется регулирование толщины по длине раската в процессе прокатки.
Конструктивно электромеханические нажимные устройства расположены на верхних поперечинах станин а гидравлические - внизу на нижних поперечинах станин. В связи с тем что ход плунжера ГНУ небольшой а уровень линии прокатки необходимо обеспечить с достаточно высокой точностью изменение диаметров нижних валков при переточках компенсируется набором прокладок при перевалках валков.
На первом этапе строительства стана вместо ГНУ установлены разгрузочные устройства. Гидроцилиндры разгрузочного устройства расположены на нижних поперечинах станин. Цилиндры состоят из неподвижного корпуса подвижного в вертикальном направлении плунжера и нижней гайки. Внутри гидроцилиндра поддерживается постоянное давление рабочей жидкости (25-50 МПа). При работе стана плунжер занимает верхнее положение и упирается в кольцевой бурт корпуса Между плунжером и гайкой - слой рабочей жидкости толщиной 25 мм. При застревании проката в валках рабочая жидкость из гидроцилиндра сливается и плунжер опускается вниз вместе с нижней валковой группой. Диаметр плунжера 1600 мм.
В рабочей клети установлены станинные ролики обеспечивающие транспортировку сляба к рабочим валкам. Три станинных ролика перед клетью объединены в качающийся амортизированный блок. Первый ролик со стороны валка - гладкий диаметром 600 мм второй и третий - с ребристой бочкой диаметром 900650 мм. Амортизация всего блока роликов осуществляется за счет поглощающих аппаратов автосцепки для железнодорожного транспорта которые установлены в ряд в гнездах качающейся рамы. Станинные ролики приводятся во вращение электродвигателями через промежуточные валы и роликовые муфты. Станинные ролики за клетью устроены аналогично.
Узел станин состоит из двух станин закрытого типа двух плитовин с клиновыми прижимами лап двух верхних траверз для соединения между собой станин в верхней части и других узлов и деталей.
В связи с невозможностью отливки цельной станины массой около 400 тонн принята сварная конструкция станины. Каждая станина состоит из верхней и нижней литых поперечин и двух литых стоек (рисунок 4).станины после чистовой механической обработки 332 т до чистовой обработки - 382 т. Станина стана 5000 отличается более рациональным распределением металла между стойками и поперечинами. При этом обеспечивается равнопрочность во всех сечениях станины за счет введения наклонных скосов в местах
Рисунок 4. Схема станины рабочей клети кварто стана 5000
перехода наружных поверхностей верхней и нижней поперечин в стойках вместо более металлоемких переходов по дуге окружности.
Применено клиновое крепление лап станины к плитовинам. Плитовины стянуты со станинами горизонтальными болтами с гайками что позволяет исключить применение поперечных балок для стягивания левой и правой плитовин между собой. Схема станины приведена на рисунке 4.
Клеть оборудована необходимыми системами смазки и охлаждения а также исполнительными механизмами и информационными датчиками обеспечивающими работу автоматических систем регулирования параметров рабочей клети и технологического процесса прокатки.
Конструкция рабочей клети кварто 5000 с диаметром бочки опорного валка 2360 мм и максимальным усилием прокатки 90 МН для прокатки крупногабаритных листов и плит шириной до 4800 мм из слитков массой до 60 т из углеродистых легированных и специальных марок сталей и сплавов была разработана и изготовлена впервые в отечественной практике.
6. Возможные дефекты горячекатаных листов
Часть продукции современных толстолистовых станов подвергают отделке в цехе горячей прокатки другую часть горячекатаных рулонов направляют в цехи холодной прокатки для дальнейшего передела. Горячекатаная листовая сталь может являться товарной продукцией в виде рулонов или в виде отдельных листов.
Для отделки листовой продукции в цехе горячей прокатки установлены агрегаты резки термической обработки травления правки дрессировки и промасливания где листы проходят соответствующую отделку в зависимости от требований предъявляемых к готовой продукции.
Термической обработке подвергают листы прочностные характеристики которых строго регламентированы техническими условиями. Горячая прокатка полос толщиной 30 мм и выше заканчивается выше критической точки Аr3 поэтому такие листы порезанные и охлажденные на рольгангах практически находятся в нормализованном состоянии. Так как прочностные характеристики готовых листов (предел прочности предел текучести твердость) зависят от марки стали температуры конца прокатки условий охлаждения полосы после выхода из стана то для некоторых партий листов возникает необходимость нормализации или смягчающего отжига.
Нормализации подвергают листы при заниженных значениях предела текучести или предела прочности с целью повышения значений этих характеристик. При малом относительном удлинении завышенных значениях предела прочности и твердости и при неудовлетворительной пробе на загиб в холодном состоянии применяют смягчающий отжиг. Листы прокатываемые из легированных сталей проходят термическую обработку; некоторые легированные стали подвергаются закалке.
Для нормализации и смягчающего отжига в пролетах отделки листового стана установлены термические печи непрерывного действия с роликовым подом и газовым обогревом. Газовые горелки размещают с каждой стороны печи в один ряд. Скорости передвижения листов в печи регулируют в пределах 2—16 ммин. За нормализационной печью располагают рольганг состоящий из нескольких секций в линии которого устанавливают правильную машину. Рольганг заканчивают механизированным карманом подачу листов в который осуществляют с помощью фрикционных роликов. При нормализации листов толщиной до 2 мм загрузку в печь производят пакетами; при смягчающем отжиге листы загружают по одному. С целью предохранения от царапин получаемых от соприкосновения мягких нагретых листов с роликами подового конвейера металл подвергаемый термообработке укладывают на подкладки из листов.
Для создания замедленного охлаждения листов при смягчающем отжиге отводящий рольганг за печью перекрывают съемными крышками футерованными огнеупорным кирпичом.
Листы из легированных сталей при необходимости проходят закалку в специальных термических печах которые состоят из камер нагрева и охлаждения. Обогрев печи как правило производят газом. Охлаждение верхней и нижней поверхности листов производят в камере охлаждения водой из брызгал. Листы в печи перемещаются охлаждаемым роликовым конвейером со скоростью до 12 ммин. Для равномерного прогрева металла и равномерного его охлаждения в камерах нагрева листы совершают возвратно-поступательное движение. Перед печью устанавливают приводной загрузочный рольганг с укладывателем. За печью расположены холостой гравитационный рольганг правильная машина укладыватель.
Для окончательной отделки поверхности листов уменьшения разнотолщинности устранения незначительной волнистости и коробоватости а также создания поверхностного наклепа препятствующего образованию линий сдвига при штамповке листовой металл подвергают дрессировке т. е. прокатке с небольшими обжатиями. Дрессировочный стан оборудован спереди подающим ленточным конвейером а позади отводящим ленточным конвейером и правильной машиной с подающими роликами.
Дрессировку листов ведут следующим образом. Пачку листов укладывают перед станом и листы по одному сбрасывают на подающий конвейер который задает лист в рабочие валки стана. Дрессировка производится за один проход с максимальным обжатием до 3—4%. По выходе из валков листы падают на отводящий конвейер который задает их в правильную машину. С помощью роликов выдачи листы по выходе из правильной машины укладывают в пачки. Для дополнительной правки промасливания листов а также продольной резки в отделочных пролетах устанавливают соответствующие агрегаты.
По техническим условиям часть заказов горячекатаных или термически обработанных листов поставляют травлеными. Для удаления окалины с поверхности листа в пролетах отделки устанавливают машины периодического травления в которые листы загружают пачками. Эти машины представляют собой вертикальный паровой цилиндр в котором плунжер имеет возвратно-поступательное движение. На верхнем конце плунжера укреплены четыре консоли к которым на цепях подвешивают корзины выполняемые из кислотоупорного металла. Вокруг парового цилиндра по окружности радиус которой равен вылету консолей располагают три прямоугольные ванны выложенные из кислотоупорного кирпича на кислотоупорном цементе. Размеры ванн определяют по максимальным размерам листов подвергаемых травлению. В две ванны залит раствор серной кислоты (в первой ванне концентрацией 8—12% во второй 5—8%) в третью — проточная вода. Кислотный раствор и воду подогревают паром до 95° С. Плунжер паровой машины имеет рабочий ход до 500 мм и максимальный ход обеспечивающий подъем корзин с металлом из травильных ванн. При возвратно-поступательном движении плунжер перемещает корзины с металлом в ваннах с растворами. Консоли с корзинами можно поворачивать в горизонтальной плоскости. Листы в травильных корзинах устанавливают вертикально.
Для равномерного омывания листов растворов их отделяют друг от друга навесными крючками. Цикл травления состоит из следующих операций: прицепка корзины к консоли поворот консолей на 90° в горизонтальной плоскости травление в первой ванне поворот консолей на такой же угол травление во второй ванне поворот консолей промывка листов в третьей ванне снятие корзины с консоли. Интенсивность травления регулируют концентрацией температурой кислотных растворов и временем травления.
Вся товарная продукция проходит контроль для определения соответствия металла требованиям ГОСТа и технических условий. Листы с неустраненными дефектами переводят в соответствии с ГОСТом в пониженные сорта или на другие заказы или списывают как окончательный брак. Все основные дефекты горячекатаных листов можно разбить на следующие группы: по вине металла по вине нагрева и по вине прокатного производства.
К наиболее распространенным порокам первой группы относятся плена рванины волосовины неметаллические включения дыры рваные кромки расслой. Плена является языкообразной окисленной пластинкой металла образовавшейся на поверхности полосы в результате неудаленных с поверхности слябов плен. В отдельных случаях плены могут быть удалены с поверхности листа зачисткой. Рванины представляют собой изогнутые поперечные трещины на поверхности листа вытянутые в направлении прокатки. Кроме низкого качества металла рванины возникают в результате перегрева или пережога металла в нагревательных печах. Если в прокатку поступают слябы с поверхности которых не удалены волосовины на поверхности готовых листов появляются мелкие трещины направление которых совпадает с направлением прокатки. Волосовины могут быть удалены с поверхности листа зачисткой.
При наличии неметаллических включений на плоскостях слябов на стане эти включения раскатываются по поверхности листа. Зачисткой они могут быть удалены только при условии очень мелкого залегания.
Если в слябах остаются следы усадочной раковины то при прокатке в этих местах на поверхности листов образуются разрывы которые называют дырами причем листы с дырами являются окончательным браком. Рваные кромки возникают при незаварившихся сотовых пузырях в результате пониженного содержания марганца в стали 08кп плохого раскисления стали наличия на узких гранях слябов неудаленных дефектов и при нагреве металла.
Лист с расслоем получают если не удален расслой на слябах.
При слишком высокой температуре нагрева слябов в методических печах с окислительной атмосферой металл частично оплавляется с окислением по границам зерен в результате чего на плоскостях раската образуются крупные рванины. Этот вид брака называют пережогом и он исправлению не подлежит. Причиной рванин на раскате может быть также прокатка слябов которые продолжительное время нагревались в печи при высокой температуре. Такие слябы не должны поступать в прокатку. Их следует охладить и вновь нагреть без перегрева.
По причинам прокатного производства можно назвать следующие основные виды дефектов: серповидность коробоватость волнистость смятие вмятины закат окалина недокаты несоответствие заказу геометрических размеров.
Серповидность листов и полос возникает в результате непараллельной установки валков в вертикальной плоскости неравномерного нагрева слябов или неправильной установки направляющих линеек перед станом. В этих случаях одна из сторон раската больше обжимается и следовательно больше удлиняется. Серповидность может быть устранена обрезкой кромок листа если после обрезки ширина полученного листа будет удовлетворять заказу.
Малые обжатия в последних клетях чистовой группы при большой выпуклости валков вызывают за счет большей вытяжки посредине полосы образование поперечных волн не доходящих до кромки листов. Этот вид дефекта называют коробоватостью. Небольшую коробоватость устраняют правкой на правильной машине и дрессировкой.
Если поперечные волны расположены по кромкам листа или по одной из них то такой дефект называют волнистостью. В этом случае вытяжка листа у кромок или у одной из них больше чем у середины листа. Волнистость может быть вызвана чрезмерным обжатием в последних двух клетях чистовой группы прокаткой на одних и тех же валках широкого листа после прокатки более узких листов или прокаткой листов на валках с большой выработкой посредине.
Небольшую волнистость листов устраняют правкой и дрессировкой.
Неправильный режим охлаждения валков по их длине может вызвать коробоватость или волнистость.
При неправильной укладке листов в стопы застревании полос в межроликовых рольгангах неправильной транспортировке одновременно нескольких полос шлепперными дорожками на холодильнике металл изгибается в различных направлениях. Такие листы называют смятыми. Этот вид дефектов устраняют правкой на роликоправильных машинах и в отдельных случаях дрессировкой а при значительной смятости подобные полосы бракуют.
При прокатке наблюдаются случаи когда частицы металла от кромок попадают на поверхность полосы и оставляют отпечатки — вмятины. Вмятины часто получают при выкрашивании валков наварах на валках или наварах на валиках роликоправильных машин. Мелкие вмятины могут быть устранены при дрессировке листов. Прокатка слябов с неудаленными закатами на боковой кромке листов в направлении прокатки вызывает образование прямой складки в виде трещины. На листах с закатами боковую кромку обрезают. Если в этом случае ширина обрезного листа не соответствует заказанной ширине то эти листы поставляют по другому заказу.
Остатки неудаленной окалины дают на поверхности листов темные пятна и точки. Этот дефект является результатом недостаточного обжатия раската на окалиноломателях засорения сопел для воды высокого давления большой выработки рабочих валков и недостаточного давления воды для полного удаления окалины с поверхности раскатов. В большинстве случаев окалину можно устранить зачисткой.
Несоответствие размеров листа по заказу получается при неправильной настройке стана или вспомогательного оборудования например летучих ножниц. Неравномерная толщина листов по сечению возникает в результате неудовлетворительного режима обжатий или неправильно выбранной профилировки валков. При получении листов равномерной толщины необходимо изменить размеры выпуклости рабочих валков или перераспределить обжатия между клетями.
При травлении листов в травильной машине периодического действия возникают черные пятна на поверхности листов — «недотрав». Этот дефект получается в результате недостаточной продолжительности травления и при выработанном или недостаточно подогретом кислотном растворе или при неправильной установке листов в травильных корзинах.
При чрезмерно высокой концентрации кислотных растворов высокой температуре подогрева растворов или излишне продолжительном времени травления поверхность листов получается шероховатой — разъеденной кислотой. Этот дефект называют «перетравом».
Плохая промывка листов после травильных ванн вызывает на поверхности появление желтых пятен — ржавчины. Промытые листы после травления необходимо промасливать.
Сравнительно большую долю в общем количестве брака при прокатке полос и листов составляют недокаты возникающие в результате подачи в стан для прокатки недостаточно нагретых слябов захолаживания в процессе прокатки на одной из клетей концов раската получения после уширительной клети раската ширина которого больше заданной чрезмерного загиба переднего конца раската после выхода из клети остановки раската в чистовой группе клетей в результате неправильной настройки раствора валков или неверного выбора скорости прокатки по клетям неправильной установки направляющих линеек между клетями и других нарушений технологии прокатки. 13
7. Автоматизация процесса прокатки в чистовой клети
В комплекс реверсивного стана горячей прокатки кроме рабочих клетей входит целый ряд других механизмов: рольганги ножницы слитковозы кантователи и др.
Перед каждым пропуском реверсивный стан разгоняется вхолостую. При определённой скорости; которую называют скоростью захвата в валки поступает прокатываемый металл. Скорость захвата сравнительно невелика и составляет 15-30% от максимальной скорости в данном пропуске.
Сравнительно небольшая скорость при захвате металла валками объясняется условиями надежного безударного захвата. После захвата стан снова разгоняется с металлом в валках. Перед концом прокатки скорость снижается с таким расчетом чтобы слиток не был выброшен на большое расстояние от клети. Второй пропуск происходит в обратном направлении после реверса. После второго пропуска слиток обычно кантуется и вновь рольгангом; направляется к рабочим валкам для следующего пропуска. Общее количество пропусков от 9 до 20.
В последующем пропуске слиток выбрасывается с максимальной скоростью поскольку в этом случае металл не возвращается обратно в клеть.
Требуемый по технологии диапазон регулирования скорости (от ползучей до максимальной) составляет (10-25):1. Требования касающиеся точности регулирования скорости невысоки и составляют 1-2%.
Ввиду частых включений важным требованием к приводу является минимизация длительности переходных процессов - пуска торможения реверса а также потерь энергии при переходных процессах. Привод должен обладать большой перегрузочной способностью. Индивидуальный электропривод стана должен регулировать соотношение скоростей верхнего и нижнего валков до захвата металла и выравнивания нагрузки двигателей при прокатке.
Указанным требованиям удовлетворяет в основном индивидуальный электропривод постоянного тока выполненный по системе: реверсивный тиристорный преобразователь - двигатель с системой подчиненного управления на базе УБСР с двухзонным регулированием скорости.
Особенностью является наличие регулятора выравнивания нагрузок РВН который является общим для систем регулирования напряжения якоря и тока возбуждения двигателя. Сигнал с датчика тока якоря ИА1 поступает на элемент сравнения ЭС на выходе которого сигнал ДI равен разности токов двигателей Ml и М2 ДI = I1- I2. При равномерной загрузке двигателей Ml и М2 сигнал ДI = 0 и выходной сигнал РВН также равен нулю. При перегрузке например двигателя М2 на выходе РВН появится сигнал. При этом выходные сигналы РВН будут уменьшать задание на скорость двигателя М2 и увеличивать задание на скорость двигателя Ml на входе регулятора скорости PC. Соответственно уменьшается напряжение тиристорного преобразователя UZ2 скорость и ток двигателя М2. В то же время напряжение другого преобразователя UZI скорость и ток двигателя Ml увеличатся. В приводе используются реверсивные прокатные электродвигатели специального металлургического
исполнения с повышенной механической и электрической прочностью (усиленные подшипники и крепление обмоток якоря теплостойкая изоляция и т.п.) Погрузочная способность составляет 25-3; станины двигателей выполняются разъемными для удобства
монтажа и ремонта. Мощность главного привода горизонтальных валков достигает 126 МВт
поэтому современные мощные обжимные станы имеют только индивидуальный привод валков.
Рисунок 5 . Схема автоматизации процесса прокатки в чистовой клети.
Напряжение двигателей 6-10 кВ частота вращения 32-80 обмин и максимальная при ослабленном поле до 120 обмин.
Для электроприводов выпускаются тиристорные агрегаты в реверсивном исполнении мощностью до 16 МВт на номинальные напряжения 600 8251050 В.
После прокатки до нужной толщины в черновой клети уширенный слиток снова поворачивается коническими роликами рольганга на 90° головной частью вперед и передаётся в чистовую реверсивную клеть где центрируется линейками манипулятора и прокатывается до требуемого размера по толщине. В процессе прокатки окалина с поверхности листа удаляется устройством гидросбива. Температура начала прокатки в чистовой клети составляет не ниже 1050 °С; температура конца прокатки порядка 830 °С в зависимости от марки стали. Скорость прокатки составляет до 45 мс. Скорость прокатки выше чем в черновой клети т.к. длина раската в последних проходах может достигать 15 м а его толщина всего 10 мм то происходит интенсивное охлаждение металла более высокая скорость позволяет сократить время прокатки.
Все сигналы от датчиков (ДП ДТ Дт ДУ) после и при прохождении металла через валки чистовой клети поступающей на информационную промышленную сеть Profibus далее на МП и ПО которые отрабатывающей все технологические режимы как вручную (наладка) так и автоматически и полуавтоматически.
8. Объёмно-планировочные решения цеха
В соответствии с инженерно- геологическим заключением расчетное сопротивление грунта 02 МПа. За условную отмету ±0000 принимается отметка чистого пола . Планировочная отметка –015мм.
Внешние метеорологические условия :
-снеговая нормативная нагрузка –50МПа
-средняя скорость ветра –7мс
-средняя температура воздуха зимняя - 120С
-глубина промерзания грунта ниже собственное поверхности – 12м
-глубина залегания грунтовых вод - 5-7м
Производственное здание по степени пожароопасности относится к категории Г в
соответствии со СНИП II-80 а по санитарной характеристике к группе 2Б в соответствии с
Помещение цеха отапливается. Здание каркасного типа прямоугольной формы. Каркасом здания являются металлические колонны металлические фермы подкрановые балки сварные железобетонные покрытия. Основной шаг колонн – 12м.
Фундаменты колонн – монолитный железобетон.
Фундаменты под несущие стены – ленточные сборные из крупных железобетонных блоков.
Фундаменты под оборудование - монолитные железобетонные ступенчатые. фундаменты имеют каналы для электропроводки трубопроводов для смазки воды и сжатого воздуха. Так же в фундаментах имеются каналы для слива окалины. Фундаменты изготовлены из бетона марки М-300 арматура из Ст.З. Глубина заложения фундамента определяется конструкцией оборудования. В фундаментах также размещаются маслоподвалы для подачи смазки.
Колонны сплошностенчатые двутаврового сечения привариваются к металлической плите фундаментных башмаков. Шаг основных колонн-12 м в местах установки оборудования значительного размера - 24 м.
Стены выполнены из стеновых панелей ПМС-6 высотой 1200мм. Нижняя панель устанавливается на фундаментные балки верхние друг на друга. Панели крепятся к колоннам с помощью анкеров приваренных к закладным деталям в плитах. Между ними оставлены проемы для окон.
Полы выполнены из рифленых металлических плит уложенные на бетонное основание толщиной 150мм. Бетон марки М-300. под бетонным основанием укладывается слой песка и гравия толщиной 100 мм.
Подземные сооружения
В цехе имеются приемники для сбора окалины расположенные ниже уровня пола и
футерованные огнеупорным кирпичом. Пол приямка кроме того выложен чугунными
Светоаэрационный фонарь
Для верхнего освещения производственной площади и естественной вентиляции предусмотрен светоаэрационный фонарь. Все пролеты здания склада оборудованы светоаэрационными фонарями.
Несущий каркас из металлических ферм стоек и каркасов для увеличения жесткости. Для заполнения фонарных проемов применены металлические остекленные фрамуги. Открывание и закрывание фрамуг механизировано. Управление осуществляется с пола цеха.
Форма крыши – двухскатная для настила крыши применены железобетонные плиты. В качестве утеплителя используется газобетон. Влагостойкое покрытие состоит из трех слоев рубероида на битумной мастике и цементной стяжки.
1. Свойства стали 10Г2ФБ
Сталь 10Г2ФБ относится к конструкционным низколегированной сталям. Прокат листовой применяется для изготовления электросварных прямошовных труб магистральных газо- нефтепроводов. Производится по ТУ 14-1-4034-96. Сортамент:
Толщина – 12-22 мм определенной мерной длины от 11500 до 11800 мм. Предельные отклонения по длине листов – по ГОСТ 19903-74. Отклонения от плоскостности на 1 м длины должны соответствовать нормам улучшенной плоскостности по ГОСТ 19903-74. По согласованию с потребителем допускается поставка листов нормальной плоскостности по ГОСТ 19903-74. Серповидность листов не должна превышать 1 мм на 1 м длины но не более 12 мм по всей длине. Данные о стали представлены в таблицах 3.1 – 3.4.
Таблица 3.1 - Предельные отклонения по толщине листов
Отклонения по толщине листов при ширине мм
Свыше 1500 до 2000 вкл.
Свыше 2000 до 2500 вкл.
Свыше 2500 до 3000 вкл.
Максимальные минусовые отклонения по толщине листов от номинальной не превышают 5% нормальной толщины а для листов толщиной 16 мм и более – не должны превышать минус 08 мм.
Таблица 3.2 - Предельные отклонения по ширине листов
Таблица 3.3 - Химический состав по плавочному анализ
Массовая доля элементов %
Допускается массовая доля в стали остаточного хрома никеля и меди не более 03% каждого азота – не более 0010%;
Допускается до 15% плавок стали с массовой долей азота не более 0012%;
Сталь обрабатывается модификатором содержащим кальций кальций иили редкоземельные элементы в количестве 05-202 кгт. Массовая доля кальция кальция иили редкоземельных элементов факультативна и не является браковочным признаком;
Углеродный эквивалент стали должен быть не более 043.
Листы поставляются (режимы прокатки выбирает предпритиятие-изготовитель и ЦНИИЧермет):
после контролируемой прокатки
после контролируемой прокатки с ускоренным охлаждением
после дополнительной термической обработки
после диффузионного рафинирования по водороду в холодной (ниже 150°С) или теплой (150-600°С) стопе.
Листы подвергаются 100-процентному ультразвуковому контролю.
Качество поверхности листов должно соответствовать требованиям ГОСТ 14637-89.
Таблица 3.4 - Механические свойства
Относительное удлинение 5" % не менее
Относительное удлинение 2" % не менее
Ударная вязкость Джсм2 и доля вязкой составляющей В в изломе образцов ДВТТ % при температуре испытания не ниже 20°С
KCV(образцы типа II)-20°С
KCU(образцы типа I)-20°С
B(образцы ДВТТ)-20°С
Отношения фактических значений предела текучести и временного сопротивления должно быть не более 09;
Ударную вязкость и долю составляющей в изломе образцом при всех температурах испытания определяют как среднее арифметическое значение по результатам испытаний трех и двух образцов соответственно. На одном из испытанных образцов допускается снижение ударной вязкости на 10 Джсм2 (кгсмм2) вязкой составляющей – на 10%.
Рис 5. Изменение предела текучести стали 10Г2ФБ
2. Расчёт энергосиловых параметров
В качестве исходной заготовки был взят сляб размерами 260x1700x2700 мм массой 9.4 т из стали 10Г2ФБ полученный на МНЛЗ Данная заготовка наиболее подходит для производства готового изделия. Готовый штрипс имеет следующие размеры: 22x4600x12300 мм. Температура начала прокатки составляла 1200 °С конца прокатки 850 °С. Получение штрипса производилось с помощью контролируемой прокатки что обеспечило необходимые механические свойства проката.
Расчёт энергосиловых параметров производился по методике приведённой в [2].
Произведён расчёт первого прохода. Расчёт остальных проходов осуществлялся по аналогичной методике. Расчёты выполнялись в среде “Mathsoft Mathcad”. Результаты расчётов энергосиловых параметров приведены в таблице прокатки (таблица 8).
Таблица 3.5 - Результаты расчётов энергосиловых параметров
Разбивка ширины кантовка
Продольная протяжка до заданной ширины кантовка
Техническая характеристика стана:
Диаметр рабочих валков стан:мм
Диаметр опорных валков стана:мм
Диаметр подшипников:мм
Мощность электродвигателей:кВт
частота вращения электродвигателей:обмин
угловая скорость электродвигателей:
Скорость прокатки в 1 проходе:
Параметры прокатываемого листа:
Толщина листа до прокатки:
Толщина листа после прокатки:
Средняя толщина листа:
Абсолютное обжатие:
Относительное обжатие:
Отношение длины дуги захвата к средней толщине листа:
Коэффициент контактного трения при горячей прокатке:
Коэффициент наличия зон отставания и прилипания:
Проверяем наличие зоны прилипания на дуге захвата
значит зона прилипания не возникает (по всей дуге захвата имеется только скольжение).
Определяем отношение pср по длине контакта l
Определяем скорость деформации металла:
При температуре прокатки 1200 °C и скорости деформации СР = 1.63 1с предел текучести стали составляет: МПа. (рисунок 5).
Удвоенная константа пластичности:
Определяем среднее давление металла на валки и полное усилие прокатки:
Усилие на 1 мм ширины прокатываемого толстого листа:
При максимальной ширине листа мм полное усилие прокатки:
Определяем момент прокатки.
Определяем коэффициент плеча приложения равнодействующей давления
Плечо приложения силы a:
Определяем момент трения.
Валки вращаются в подшипниках жидкостного трения поэтому принимаем коэффициент трения в подшипниках:
где P -усилие прокатки
dП- диаметр подшипников
DР- диаметр рабочего валка
DОП - диаметр опорного валка
Определяем статический момент
(Момент на валу электродвигателя от статической нагрузки):
Проверка двигателя по моменту:
Коэффициент перегрузки по двигателю:
Определение мощности прокатки.
Угловая скорость вращения валков
Мощность при прокатке:
Мощность электродвигателей:
На стане используются двигатели МП 6300 32У4. Двигатели допускают кратковременную трёхкратную перегрузку по мощности. Суммарная допустимая мощность двух двигателей стана:МВт что меньше затрачиваемой мощности прокатки.
Определение времени прокатки.
Площадь поперечного сечения до прохода:
Площадь поперечного сечения после прохода:
Длина после прохода:
Время нахождения полосы в клети составляет:
3. Расчёт оборудования на прочность
При расчёте оборудования на прочность использовались значения энергосиловых параметров полученные при прокатке металла в 9 проходе чистовой клети т.к. нагрузка на оборудование при этом была максимальной.
Скорость прокатки: мс
Расчёт валков на прочность
Диаметр рабочих валков стана:мм
Диаметр опорных валков стана:мм
Диаметр подшипников рабочих валков:мм
Диаметр подшипников опорных валков:мм
Длина бочки рабочего валка:мм
Длина бочки опорного валка:мм
Ширина прокатываемого листа:мм
Материал опорных валков:
Материал рабочих валков:отбеленный чугун
Определение распределения усилия между рабочими опорными валками:
Усилия на рабочих валках:
Усилия на опорных валках:
Рабочие валки воспринимают % от общего давления на валки при прокатке.
Определение опорных реакций
Распределённая нагрузка на бочки валков при прокатке:
опорные валки воспринимают нагрузку через рабочие по всей длине бочки валка.
Принимаем валок в виде балки покоящейся на двух опорах испытывающей нагрузку приложенную посередине длины. Тогда реакции опор составят:
Находим напряжения в рабочем валке
Максимальный изгибающий момент посередине бочки рабочего валка от вертикального усилия P.
расстояние между точками приложения силы мм
Максимальное напряжение изгиба посередине бочки рабочего валка
Напряжение на шейке ведущего валка
Диаметр шейки валка: dШРВ = 710 мм
Длина шейки валка: lШРВ = 1700 мм
коэффициент концентрации напряжений для шпоночного паза
Результирующее напряжение:
МПа условие прочности выполняется.
Находим напряжения в опорном валке
Максимальный изгибающий момент посередине бочки опорного валка от вертикального усилия P передаваемого через рабочий валок.
Максимальное напряжение изгиба посередине бочки опорного валка:
Напряжение на шейке опорного валка в сечении 1-1
Диаметр шейки валка в данном сечении мм
расстояние от точки приложения равнодействующей реакции подшипника до края бочки мм
Напряжение на шейке опорного валка в сечении 2-2
Допустимые напряжения для валков из углеродистой стали
Коэффициенты запаса прочности от предела текучести
шейки опорного валка:
шейки рабочего валка:
Минимальный требуемый запас прочности n = 4. В данном случае валки полностью ему удовлетворяют.
Рассчитываем контактное напряжение в поверхностном слое валков
Опорные валки стальные рабочие чугунные.
Определяем приведённый радиус валков:
Модуль упругости для стальных валков: МПа
Модуль упругости для чугунных валков: МПа
Приведённый модуль упругости для стальных опорных и чугунных рабочих валков: МПа
кНмм - усилие на 1 мм ширины листа
Для валков с твёрдостью > 55 HRC []конт = 4400 МПа.
Определяем прогиб опорного валка
Определяем момент инерции бочки валка:
Определяем момент инерции шейки валка:
Модуль сдвига для стальных валков: МПа
Модуль сдвига для чугунных валков: МПа
Приведённый модуль сдвига для стальных опорных и чугунных рабочих валков: МПа
расстояние от бочки валка до середины шейки с = 800 мм.
Определяем прогиба в результате действия изгибающих моментов:
Определяем прогиба в результате действия поперечных сил:
Определяем разность прогибов в середине бочки валка и у края прокатываемого листа:
Определяем суммарный прогиб:
Расчёт на циклическую прочность
Предел выносливости при изгибе:
Предел выносливости при кручении:
Масштабные факторы для валков диаметром > 500 мм:
Амплитуда цикла напряжений при изгибе:
Амплитуда цикла напряжений при кручении:
Коэффициент обработки поверхности:
Коэффициент характеризующий чувствительность материала к ассиметрии цикла напряжений:
Эффективный коэффициент концентрации при изгибе:
Эффективный коэффициент концентрации при кручении:
Коэффициент запаса прочности при изгибе:
Коэффициент запаса прочности при кручении:
Совместное действие кручения и изгиба:
условие прочности выполняется.
Рис 6. Эпюры напряжений
Расчёт подшипников опорных валков
Опорные валки расположены в подшипниках жидкостного трения ПЖТ 1800-1600.
Максимальная нагрузка на подшипник при прокатке:
Диаметр цапфы подшипника:
Длина цапфы подшипника:
Отношение длины цапфы к её диаметру:
Смазка – масло МК-22.
Рабочая температура подшипника tраб = 40 °С вязкость масла при этой температуре:
Угловая частота вращения валков:
Окружная скорость вращения цапфы:
Определяем среднее давление в подшипнике (по проекции его диаметра):
Для подшипника скольжения с заливкой из высокооловянистого баббита Б83 допустимо
Определяем коэффициент грузоподъёмности масляного клина:
Чтобы работа подшипника была более устойчивой (без вибраций цапфы) принимаем относительный эксцентриситет при котором . По кривым находим
При изготовлении подшипника допустимы предельные допуски по диаметру:
втулки-вкладыша +24 мкм и втулки-цапфы - 18 мкм. Суммарный предельный допуск 42 мкм. Возможный радиальный зазормкм. При этом зазоре требуемая грузоподъёмность масляного клина У будет достигнута при мкм.
Определим критическую минимальную толщину масляного слоя при которой может возникнуть полужидкое трение.
Средняя суммарная высота микронеровностей цапфы и втулки согласно ГОСТ 2789-73 равна мкм. Учтём также прогиб конической цапфы (при изгибе валка) равный около и возможную максимальную непрямолинейность (овальность) цилиндрических образующих рабочих поверхностей допускаемую в пределах до 2 мкм тогда мкм.
Определим коэффициент запаса ПЖТ по толщине масляного слоя при заданной нагрузке:
а) при номинальном радиальном зазоре:
б) при максимальном радиальном зазоре:
Таким образом при заданных условиях подшипник будет работать с большим запасом по толщине масляного слоя.
Определим коэффициент трения подшипника:
Определим расход масла Q необходимый для прокачки через подшипник и поддержания постоянной его рабочей температуры °С
температура входа масла в подшипник °С
разность температур на входе и выходе из подшипника °С
объёмная удельная теплоёмкость масла Дж(м3°С).
расход масла на четыре подшипника клети составит: лс.
Расчёт подшипников рабочих валков
Рабочие валки расположены в радиальных роликовых многорядных подшипниках с короткими цилиндрическими роликами №41629710 с внешним диаметром мм и внутренним мм грузоподъёмностью Н.
Число оборотов в минуту составляет:
коэффициент учитывающий неравномерность распределения нагрузки на подшипники:
реакция опоры составляет:
На каждой шейке валка установлено три подшипника каждый из которых воспринимают часть реакции опоры т.е. 380.87 кН.
Эквивалентная нагрузка на подшипник составит:
степенной показатель для роликоподшипников
Количество часов работы подшипника составляет:
Долговечность подшипников достаточна.
Расчёт нажимного винта и гайки
Максимальное осевое усилие на нажимной винт при прокатке составляет половину усилия прокатки:
Максимальная скорость перемещения нажимного винта по вертикали:
Нажимной винт имеет упорную (одностороннюю трапецеидальную) резьбу УП 800 мм с шагом мм
Коэффициент трения:
Материал винта - сталь 45Х МПа.
Модуль упругости: МПа
Нажимная гайка высотой мм с наружным диаметром мм.
Число витков резьбы
Материал гайки - БР.АЖ9-4Л
Определяем напряжение сжатия в сечении нижнего опорного конца винта имеющего наименьший диаметр мм
Проверка винта на продольный изгиб:
Определяем напряжение смятия между витками винта и гайки
Определяем напряжение смятия по площади соприкосновения гайки со станиной
внутренний диаметр гайки мм
Напряжение смятия конца гайки:
Определим упругую деформацию нажимного винта:
наибольшая деформируемая длина винта от подпятника до нажимной гайки мм
Определим упругую деформацию нажимной гайки:
Определим суммарную деформацию системы нажимной винт - гайка:
учтём деформацию подпятника (10%)
Расчёт станины на прочность
Станину представляем в виде жёсткой прямоугольной рамы состоящей из двух одинаковых вертикальных стоек (длиной l2) и двух горизонтальных поперечин
Усилие прокатки P = 45.05 МН. Усилие прокатки воздействующее на станину для листовых станов составляет половину усилия прокатки:
Материал станины: углеродистая литая сталь со следующими механическими характеристиками:
Предел прочности МПа
Модуль упругости МПа
Геометрические параметры сечения верхней поперечены:
Определение площади поперечного сечения верхней поперечены:
Определение положения центра масс верхней поперечены:
Определение момента инерции:
Определение момента сопротивления:
Геометрические параметры сечения стойки:
Определение положения центра масс стойки:
Определение площади поперечного сечения стойки
Геометрические параметры сечения нижней поперечины:
Определение площади поперечного сечения нижней поперечены:
Максимальный момент изгиба верхней и нижней поперечин силой Y:
Статистически неопределимые моменты в углах жёсткой рамы:
Отношение статистически неопределимых моментов:
При J1 = J3 и n = 1 получим:
Напряжения растяжения в середине верхней и нижней поперечин:
Напряжения растяжения в стойке станины:
Запас прочности станины для нижней поперечины при пределе прочности углеродистой литой стали МПа:
Прогиб среднего сечения от изгиба и поперечных сил верхней поперечины:
Упругое растяжение стойки станины:
Суммарная деформация станины по вертикали:
Жесткость станины по вертикали (в направлении действия силы Y):
Прогиб стоек станины по горизонтали:
Суммарная деформация клети составит сумму деформаций валков нажимного винта и гайки станины:
Жёсткость клети при данной нагрузке:
МНмм.4. Безопасность жизнедеятельности
1. Географическое и территориальное расположение цеха
Рассматриваемый цех является источником шума и запылённости кроме того в цехе имеются источники загрязнения воды. В соответствии с требованиями СанПиН 2.2.12.1.1.1031-01 для проектируемого помещения предусматриваются мероприятия по защите окружающей среды и обслуживающего персонала. В соответствии с нормами санитарно-защитная зона составляет 500 м.
Цех расположен с подветренной стороны по отношению к жилому району и с наветренной стороны по отношению к другим цехам.
Продольные оси аэрационных фонарей и стены здания с проемами используемых для аэрации ориентируются перпендикулярно к преобладающему направлению ветров в теплый период года.
Высота пролета где расположен стан составляет 23600 мм. Основной шаг колонн равен 12000 мм по наружным и внутренним рядам. В цехе предусмотрены переходные дорожки переходы и эстакады.
Здание листопрокатного цеха №3 представляет собой помещение общей площадью 98684 м2 и объемом 2328942 м3. С учетом того что в цехе работает примерно 575 человек то на одного работающего приходится 172 м2 производственной площади и 4050 м3 объема здания что удовлетворяет санитарным нормам СНиП 245-71 .
2.Технические решения по производственной санитарии
Вентиляция и отопление
В рассматриваемом помещении воздухообмен происходит естественным образом (аэрация). Температура воздуха поддерживается благодаря тепловым выделениям от технологического оборудования и горячего металла. Учитывая время года предусмотрено резервное отопление позволяющее в холодный период года поддерживать температуру не менее 5 ºС при проведении ремонтных работ.
В производственном помещении предусматривается приточная вентиляция обеспечивающая подачу свежего воздуха.
Машинные залы а также санитарно-бытовые и подсобные помещения оборудованы центральной водной системой отопления.
Согласно СНиП 2.4.90-81 производственное помещение стана по удельному тепловыделению относятся к разряду горячих цехов. Для удаления избыточного тепла в летний период времени на перекрытии цеха имеется световые фонари с открывающимися створками посредством которых интенсифицируется процесс вентиляции помещения.
Оптимальные и допустимые температуры относительная влажность и скорость движения воздуха устанавливаются для рабочей зоны производственных помещений с учетом тяжести выполняемой работы и должны соответствовать нормам указанным в таблице согласно ГОСТ 12.1.005-88. Метеорологические условия проектируемого участка стана создаются путем естественного воздухообмена через аэрационные фонари. 8
Рис 7. Схема аэрации
В многозонных методических печах применяемых для нагрева заготовок направление потока пламени горелок и продуктов сгорания противоположно направлению движению металла. При недостатке воздуха для горения топлива возникает подсос воздуха через окно и загрузочное отверстие в случае избыточного давления в печи происходит сгорание газа вне рабочего пространства и выбивание пламени из под крышек окон. Конструктивные особенности нагревательных печей исключают вероятность взрыва газа в рабочем пространстве печи.
Для защиты от взрывов дополнительно производится:
-герметизация печи за счет использования уплотняющих крышек смотровых окон;
-проветривание вокруг газопроводов и у печи (естественное проветривание и продувка сжатым воздухом с кратностью 6 ед. в час);
-автоматический контроль за состоянием газовой атмосферы методической печи;
-индивидуальные меры защиты ( спец. костюм рукавицы противогаз).
Тепловая изоляция печей (облицовка печи металлическими теплоотражательными щитами) понижает температуру до 50°С. Печи подвергают также герметизации (уплотнение зазоров между крышками и кладкой камеры печи путем засыпки песка).
С целью более интенсивного снижения температуры стен печей применяют охлаждение их водой. Охлаждение электродвигателей принудительное – воздушное.
На участке горячей прокатки листа большинство технологических операций механизированы и автоматизированы. Дистанционное наблюдение и управление технологическим процессом прокатки имеет большое значение для защиты от теплового излучения так как позволяет избежать необходимости пребывания рабочего персонала в непосредственной близости с опасными агрегатами.
Для защиты о тепловых выделений предусмотрена надежная изоляция двухслойным оргстеклом кабин электромостовых кранов и пультов управления (ПУ). В кабинах и на ПУ установлены кондиционеры.
Для защиты рабочих мест от избыточного выделения тепла на участке установлены отражательные экраны (материал с небольшой степенью черноты – полированный алюминий белая жесть оцинкованное железо).
Для индивидуальных мер защиты предусмотрены:
Специальная одежда. Изготавливается из сукна брезента либо льняных тканей;
Для защиты головы от механических повреждений применяют каски.
Для защиты ног применяют специальную обувь. Материал обуви должен быть стойким к повышенной температуре облучению искрам обладать малой теплопроводностью и воздухонепроницаемостью;
Брезентовые рукавицы;
Для защиты глаз используют очки .
Предусмотрен питьевой режим.
Продукты неполного сгорания топлива.
СО нейтрализуется термическим методом то есть проводится высокотемпературное дожигание: . Так как выбросные газы имеют высокую температуру процесс дожигания происходит в камере с подмешиванием свежего воздуха.
Нейтрализация SО2 производится методом адсорбции. В качестве адсорбента используется активированный уголь который поглощает вредные примеси SО2 . процесс происходит в адсорбционных установках.
Помещение цеха по степени загрязнения воздушной среды относится к 4 классу – малоопасное. Содержание в воздухе окислов не превышает предельно допустимых значений:
По ГОСТ 12.1.005-7 окись углерода 20 мгм³;
окись железа 6 мгм³.
Дистанционное управление станом 5000 с пультов управления позволяет защитить работающий персонал от вредных выделений.
Большое значение для предотвращения загрязнения воздуха вредными выделениями имеет своевременное и качественное проведение планово-предупредительных ремонтов основного производственного оборудования и в первую очередь методических печей с целью поддержания необходимой герметичности.
При работе с вредными веществами необходимо использовать индивидуальные средства защиты: халаты из плотной ткани с завязками на рукавах резиновые фартуки рукавицы очки.
Для защиты органов дыхания применяются фильтрующие маски (лепестки). 9 Данные о параметрах воздушной среды представлены в таблице 4.1.
Таблица 4.1 - Значения допустимых параметров воздушной среды в рабочей зоне помещения в тёплый (холодный) период года.
Категория работ по тяжести
Допустимые значения на постоянных рабочих местах
относительная влажность %
скорость движения воздуха мс
Производственное освещение
Естественное освещение
Производственное освещение обеспечивает необходимые условия для осуществления работающими своих функциональных обязанностей. Рациональное освещение производственных помещений позволяет сохранять зрение человека обеспечивать безопасность на производстве и повысить уровень труда.
Требуемое естественное освещение в цехе обеспечивается за счет аэрационных фонарей и световых проемов в стенах производственных помещений с учётом требований СНиП 23.05-95. Параметры естественного освещения приведены в таблице 4.2. 8
Таблица 4.2 - Параметры естественного освещения
Разряд зрительной работы
Нормируемое значение КЕО %
Номер района по ресурсам светового климата
Коэффициент светового климата
Искусственное освещение
В качестве источников искусственного освещения в цехе применяются лампы ДРЛ-700. Для административных корпусов и других помещений применяются люминесцентные лампы ЛД-40. В цехе предусматривается комбинированное освещение. Параметры искусственного освещения представлены в таблице 4.3.
Количество светильников для общего освещения в цехе определяется по методу коэффициента использования светового потока по формуле:
где - количество светильников в помещении шт.;
- нормированное значение освещённости лк;
- площадь освещаемого помещения м2;
- коэффициент запаса;
- коэффициент минимальной освещённости;
- световой поток одной лампы лм;
- коэффициент использования светового потока.
Таблица 4.3 - Параметры искусственного освещения
Характеристика зрительной работы
Показатель освещённости Р
Коэффициент пульсации %
Работа со светящимися материалами и изделиями в горячих цехах
Для газоразрядных ламп коэффициент запаса равен 18. Коэффициент минимальной освещённости в расчётах принимается равным 12.
Мощность потребляемая светильниками рассчитывается по формуле:
где - мощность потребляемая светильниками Вт;
- мощность одного светильника Вт.
Расчёт площади световых проёмов при боковом освещении производится по формуле:
где - площадь оконного светового проёма м2;
- нормируемое значение КЕО;
- площадь пола освещаемого помещения м2;
- cветовая характеристика окон;
- общий коэффициент светопропускания;
- коэффициент учитывающий повышение КЕО при
боковом освещении благодаря свету отражённому от
поверхностей помещения.
Площадь световых проёмов при верхнем освещении:
- cветовая характеристика фонаря зависящая от
количества пролётов длины ширины и высоты
освещаемого помещения;
верхнем освещении благодаря свету отражённому от
поверхностей помещения;
- коэффициент учитывающий тип фонаря.
Площадь верхних световых проёмов составляет 53 % от площади боковых оконных проёмов.
3. Анализ потенциально опасных и вредных производственных факторов при выполнении основных операций
Результаты анализа потенциально опасных и вредных производственных факторов при производстве проката из высоколегированных сталей и сплавов на стане приведены в таблице 4.4 на основании ГОСТ 12.0.003-74. 9
Таблица 4.4 - Потенциально опасные и вредные производственные факторы при прокатке.
Операция тех. процесса
Оборудование на котором выполняется операция
Опасные и вредные факторы (по ГОСТ 12.0.003-74)
Нормированные значения параметра
Возможные преимущественные воздействия
Нагрев и подогрев заготовок
Повышенная температура воздуха рабочей зоны ºС
Повышенная температура воздуха на рабочем месте ºС
Повышенный уровень шума на рабочем месте дБ по шкале А
Воздействие на органы слуха
Повышенная температура поверхности оборудования ºС
Ожог кожного покрова
Опасный уровень напряжения в электрической цепи замыкание которого может пройти через тело человека A B кB Гц
Электрические удары нагрев тканей кожи металлизация
Транспортирование и складирование
Рольганг манипуляторы
Движущиеся механизмы
Возможность получения травм
4. Разработка мер защиты от выявленных потенциально опасных и вредных производственных факторов
Работа прокатного стана и вспомогательного оборудования сопровождается шумом среднечастотного спектра и уровнем звукового давления порядка 95 дБ что превышает требования ГОСТ 12.0.003-74.
Для ослабления шума в редукторах шестерённых клетях и муфтах предусмотрено применение шевронных передач вместо прямозубых. Для снижения трения поверхностей и вибраций зубья цилиндрических и других зацеплений выполнены по 8 классу точности. Шум трения ослабляется смазкой заключением вибрирующих деталей в жидкостные ванны. Двигатели заключены в звукоизолирующие кожухи снижающие уровень шума на 5-10 дБ.
Ослабление вибраций достигнуто упругой подвеской агрегатов и амортизацией. Для ограничения передачи вибраций от фундамента к окружающему грунту вокруг фундамента прокатного стана предусмотрены акустические швы. Вибрация также ослабляется уравновешиванием деталей и применением динамических гасителей. 8
В отношении опасности поражения электрическим током помещение цеха относится к помещениям с повышенным уровнем опасности из-за электроустановок высокого напряжения. По доступности электрооборудования и по квалификации персонала отделение относится к производственным помещениям т.к к электрооборудованию имеют доступ помимо обслуживающего персонала и другие рабочие.
Главные электродвигатели питаются от сети с напряжением 6-10 кВ с промышленной частотой 50 Гц.
Что бы исключить возможность поражения электрическим током в цеху предусмотрено:
а) защитное заземление металлических корпусов электромашин и электродвигателей; сопротивление заземления свыше 4 Ом т.к. применяемое напряжение выше 1 кВ;
б) щиты управления оборудованы плавкими предохранителями рубильники с блокировкой и предохранительными кожухами;
в) для сети общего напряжения 220В; в помещениях с повышенной опасностью напряжение для светильников местного освещения 36В в особоопасных местах (маслоподвал) 12В;
г) для защиты от прикосновения предусмотрена изоляция токоведущих частей а также недоступное их расположение;
д) при напряжениях свыше 250В цепи силового питания помещены в экранированные магнитомягким материалом и диэлектриком трубы; двигатели привода прокатного стана оборудованы системой электродинамического торможения с аварийным выключением с пульта управления и с рабочих мест; ограждениями и блокировкой;
е) электрооборудование окрашивается в установленные цвета это имеет кроме эстетического и опознавательного значения и защитную роль благодаря изолирующим свойствам лаков и красок;
ж) для предупреждения об опасности используют предупредительные плакаты и сигнализацию;
з) использование персоналом индивидуальных средств защиты (основные – инструмент с изолированными рукоятками указатели направления; дополнительные – резиновые коврики изолирующие подставки). 8
Рис. 8. Схема заземления
Меры защиты от основных опасных и вредных производственных факторов представлены в таблице 4.6.
Таблица 4.6 - Технические меры защиты от опасных и вредных производственных факторов
Опасные и вредные производственные факторы
Проектируемое устройство
Параметры защитного устройства и его характеристика
Место установки защитного устройства
Повышенная температура воздуха рабочей зоны
Площадь приточных проёмов 217 м2 площадь вытяжных 244 м2
Повышенная температура воздуха на рабочем месте
Защитное ограждение теплозащитный экран
Повышенный уровень шума на рабочем месте
Звукоизоляционные кабины экраны с коэффициентом звукопоглощения - 05
Посты управления стана
Повышенная температура поверхности оборудования
Опасный уровень напряжения в электрической цепи замыкание которого может пройти через тело человека A B Гц
Рабочая клеть электрические устройства
Установка кожухов и ограждений
Кожух ограждения из стали 3 мм
Все движущиеся (вращающиеся) механизмы стана
5. Безопасность жизнедеятельности при чрезвычайных ситуациях
В соответствии с НПБ 107-97 по взрывопожарной и пожарной опасности проектируемый участок стана можно отнести к категории Г.
В цехе предусматривается водяное пенное и газовое пожаротушение а также пожароохранная сигнализация помещений и сооружений цеха. Водяное пожаротушение предусматривается в кабельных тоннелях и этажах. Пенное пожаротушение предусматривается в маслотоннелях газовое - в помещениях машинных залов и вычислительном центре. Возле электрических машин в цехе устанавливаются углекислотные огнетушители. Со всех сторон цеха предусмотрены пожарные въезды.
Для оповещения рабочих и служащих о возникновении пожара в цехе имеется сирена и сигнализация для вызова пожарной команды.
Установки автоматического водяного газового и пенного пожаротушения и пожарно-охранной сигнализации выполнены согласно нормативным документам по строительству техники безопасности и пожарной безопасности.
По степени огнестойкости здание в котором расположен стан в соответствии со СНиП 21.07-97 относится ко II степени.
Чрезвычайная ситуация возникает в результате реализации потенциальной опасности при определённых параметрах и масштабах её проявления.
Прогнозирование чрезвычайных ситуаций должно включать оценку вероятности опасного события последствий и возможного времени его возникновения или хотя бы темпов изменения вероятности возникновения со временем и сравнительного влияния отдельных факторов трудового и технологического процесса и производственной обстановки и тенденций их изменения на вероятность события.
Мероприятия по ликвидации аварий и катастроф на производстве включают комплекс организационных и технических мероприятий направленных на выявление и устранение их причин максимальное снижение возможных разрушений и потерь в случае если эти причины не удаётся полностью устранить а также на создание безопасных условий для создания и проведения спасательных и неотложных аварийно-восстановительных работ. 9
Охрана окружающей среды
Листопрокатный цех №3 потребляет большое количество воды для охлаждения элементов нагревательных печей интенсивного охлаждения валков гидросбива и смывания окалины термической обработки металла приготовления травильных растворов и смазочно-охлаждающих жидкостей. Для охлаждения рабочих валков в процессе прокатки на стане применяется вода. На одну тонну готовой продукции используется 105 м3 воды. Сточные воды после охлаждения рабочих валков стана проходят через отстойник и по трубопроводам самотеком отводятся в наружную сеть промканализации и подвергаются очистке на существующих очистных сооружениях.
Вода используемая для охлаждения тиристорных преобразователей частоты тока включена в общезаводской водооборот и в окружающую среду не попадает. Общий расход воды предприятия 1009 м3 на 1 т готовой продукции.
Так же воздействие прокатного цеха на окружающую среду проявляется не только в результате образования загрязнённых сточных вод но и в выделении пыли и газов в атмосферу.
При сжигании топлива в нагревательных печах образуется дым состоящий из газов (окись и двуокись азота окись и двуокись углерода сернистый ангидрид) и твердых частиц (зола сажа). Для нагрева заготовок в качестве топлива используется природный газ поэтому продукты сгорания очистке не подвергаются так как твердые частицы в них почти отсутствуют.
В процессе нагрева заготовок в печах образуются твердые промышленные отходы в виде окалины. Отходы являются невзрывоопасными класс опасности 4. Отходы собираются в специально отведённом месте и помещаются в маркированную тару. Маркировка тары: “Отходы класс опасности – 4”. По мере заполнения тары отходы автотранспортом вывозятся за пределы цеха в специальный цех по переработке.
В процессе производства прутков образуются такие виды отходов как обрезь металлическая стружка и пыль а также маслоотходы.
Обрезь и металлическая стружка собираются и направляются на переработку также как окалина.
Металлическая пыль улавливается в рукавных фильтрах мокрых пылеуловителях и циклонах. Собранная пыль может быть использована в качестве составляющей для изготовления экзотермических смесей.
Маслоотходы очищаются и сдаются на регенерацию. Сброс в канализацию маслоотходов образующихся при промывке смазочных и гидравлических систем исключен.
В прокатном цехе действует система оборотного водоснабжения. Это рационально и очень важно с точки зрения защиты окружающей среды. Добавка свежей воды из природных источников в такую систему (для компенсации испарения) составляет 3-5 % от общего потребляемого объема.
Задачей этого раздела является описание мероприятий по предотвращению утечки в окружающую среду вредных веществ с вентиляционными газами сточными водами различными твердыми и жидкими отходами и поступление в неё токсичных веществ в концентрациях и количествах превышающих предельно допустимую концентрацию (ПДК). 9
1. Оценка загрязнения воздушного бассейна
Основные источники технологических выбросов - листопрокатный стан машины огневой зачистки и правильные отделения цеха.
При производстве листового проката наблюдается загрязнение воздуха такими ингредиентами как оксиды железа диоксиды кремния оксиды марганца угарный газ фтористый водород углеводороды масляный туман гидрооксид натрия сероводород сернистый газ.
Пылеобразование в сортопрокатных цехах связано с разрушением в процессе прокатки листа образующихся на поверхности плёнок оксидов (окалины).
Регламентирование выбросов вредных веществ в атмосферу через те или иные источники осуществляется на основе установления ПДВ (выбросов).
Для очистки воздуха эффективна местная вытяжная вентиляция особенно при расположении пылегазоприёмника в непосредственной близости к источнику пылевыделения - зоне валков применение вытяжных зонтов над клетями прокатных агрегатов менее эффективно. Снижению поступления в воздух прокатных цехов масляного аэрозоля способствует установка глушителей выхлопа отработанного воздуха (на пневмонических приводах) являющихся одновременно маслосборниками и имеющих устройство для спуска масла.
Широкое применение для сухой очистки газов получили циклоны разных типов и электрофильтры (рисунок 9). 8
Рисунок 9 - Схема процесса фильтрования.
Перед выбросом очищенные воздушные массы проходят контроль по ПДК.
2. Защита водного бассейна
Производственное водоснабжение цехов в состав которого входит проектируемый участок осуществляется по двум системам:
- система производственного водопровода речной воды прямоточная с очисткой нагретой воды в специальных отстойниках;
- система грязного оборота воды (оборотного цикла). В системе грязного оборотного цикла образуется маслоэмульсионные стоки и окалиносодержащий шлак. От стана эмульсию сбрасывают периодически через двое - трое суток в количестве 100 - 150 м3. Разложение маслоэмульсионных стоков производят в частности отработавшим травильным раствором имеющимся в цеху. На обработку 1 м3 эмульсий необходимо около 100 л отработавшего травильного раствора.
Система очистки стоков выглядит следующим образом: маслоэмульсионные стоки поступают сначала в сборник (смеситель плюс контактный резервуар) куда подается реагент. Затем стоки поступают в отстойник-маслоуловитель. Всплывшие масла направляют в емкость а осветлённая вода в резервуар. Для улучшения всплывания в отстойник подают пар температура в отстойнике около 50 ºС. В отстойнике предусмотрена и флотация для чего в него подают воздух. Для создания требуемой РН в сточные воды подают известковое молоко. Такую воду можно направлять в общезаводской пруд-осветлитель.
Пребывание воды в сборнике 1 принимают 30 мин в отстойнике 2- 15-2 часа. Осадок из отстойника направляют в шлаконакопитель или на обезвоживающие площадки. 9
3. Утилизация отходов производства
Основными производственными отходами в листопрокатных цехах являются: окалина; стружка и обрезь; маслоотходы; отработанная эмульсия; производственный мусор (обвязочная проволока обрывки тросов металлическая лента деревянные промасленные опилки ветошь и др.).
Окалина поступает на установку по переработке железосодержащих шлаков и металлоотходов. Маслоотходы от установки очистки поступают на установку по переработке маслоотходов. Производственный мусор вывозится на заводской отвал.
Тепло отходящих газов утилизируется в металлических рекуператорах петлевого типа и используется для подогрева воздуха подаваемого к горелкам печи. Также оно может быть использовано для отопления бытовых помещений цеха в зимнее время. 8
Экономика и управление производством
1. Расчет производительности стана 5000
Толстолистовой стан 5000 предназначен для прокатки крупногабаритных листов и плит из углеродистых легированных и специальных сталей и сплавов.
Схема технологического процесса до реконструкции.
Подогрев и нагрев слябов.
Прокатка слябов в двухвалковой клети с горизонтальными валками.
Прокатка слябов в двухвалковой клети с вертикальными валками..
Обработка поверхности сляба на машине огневой зачистки.
Прокатка в четырёхвалковой клети.
Правки листа на листоправильных машинах
Охлаждение и резка листов.
Схема технологического процесса после реконструкции.
Прокатка слябов в двухвалковой клети с вертикальными валками.
Прокатка в черновой четырёхвалковой клети.
Прокатка в чистовой четырёхвалковой клети.
Все агрегаты цеха работают в непрерывном режиме в 3 смены по 4-х бригадному графику при рабочем дне продолжительностью 8 часов.
Организация ремонтной службы
Ремонтное хозяйство нужно для обеспечения постоянной работоспособности оборудования с высокой производительностью и экономичностью.
Эта задача может быть выполнена в результате проведения систематических профилактических работ и различных видов ремонтов.
Для предотвращения прогрессирующего износа оборудования внеплановых ремонтов аварий и поддержания оборудования в работоспособном состоянии в цехе применяется система планово-предупредительного ремонта (ППР).
Система ППР предусматривает следующие виды обслуживания и ремонтов машин:
-межремонтное обслуживание (уход и надзор);
-периодические осмотры и ревизии;
-периодические текущие ремонты;
-капитальные ремонты.
Основным видом ремонта является текущий.Текущие ремонты проводятся в дни плановых остановок оборудования в соответствии с годовым графиком.
Для выполнения текущих ремонтов на основе данных осмотров и ревизий составляют ведомости дефектов оборудования в которых указывают планируемую дату остановки агрегата на ремонт перечень работ и сроки ремонта.
Текущие ремонты выполняют цеховые ремонтные бригады под руководством механика.
Периодические осмотры необходимы для проверки состояния деталей и узлов недоступных для непосредственного наблюдения при ежесменном обслуживании.
При капитальном ремонте проводят полную разборку машины очистку и промывку всех деталей замену или исправление основных деталей и узлов изношенных деталей ремонт фундаментов при необходимости реконструируют отдельные узлы и модернизируют детали. После чего машину регулируют испытывают и красят. Капитальные ремонты выполняют на основании данных обследования ревизии и текущих ремонтов оборудования и ведомостей дефектов оборудования составляемых за 6 месяцев до остановки агрегата на капитальный ремонт.
За 2 месяца до начала ремонта исполнитель ремонта составляет оперативный график в котором перечисляет виды работ сроки и необходимое число рабочих.
Производительность стана
Производственная мощность стана – это максимальное количество продукции которое может быть получено на нем в течение года.
Годовая производительность стана рассчитывается по формуле:
Fф- фактический годовой фонд времени работы стана в течение года час.
Фактический годовой фонд времени определим по формуле:
FНОМ – номинальный годовой фонд времени работы стана;
КТ – процент текущих простоев (по заводским данным составляет 15).
Причины текущих простоев:
-отсутствие ресурсов (материалов электроэнергии и т.д.);
-замена сменного оборудования
-ремонт механической части оборудования;
-ремонт электрической части оборудования;
-замена оборудования по износу.
Уменьшение текущих простоев достигается в виду:
-улучшения снабжения ресурсами;
-повышение качества проводимых профилактических плановых работ т.е. ремонт оборудования;
-повышение долговечности сменного оборудования путем выбора лучших марок стали для инструмента и методов его обработки.
Номинальный годовой фонд рабочего времени для стана работающего по 3-х сменному непрерывному графику:
где FК- календарный фонд времени 365 дней;
tК -продолжительность капитального ремонта капитальный ремонт
проводят один раз в год продолжительностью 10 суток;
tППР -продолжительность планового предупредительного ремонта
принимаем 10 сутгод;
tПД –праздничные и выходные дни (tПД =0 т.к. график работы стана непрерывный).
Фактический годовой фонд времени стана до реконструкции:
Фактический годовой фонд рабочего времени стана 5000 после реконструкции не изменится.
Таблица 6.1 - Данные времени работы стана
Число и продолжительность смен
Планово-предупредительные ремонты
Часовая производительность стана
Масса используемого сляба:
- соответственно длина высота и ширина сляба.
Часовая производительность стана:
где: r- плотность стали = 785 тм3
Т – время такта такт прокатки берётся для четырёхвалковой клети т.к. именно она является узким местом в процессе прокатки (рисунок 10);
KИСП – коэффициент использования из заводских расчётов = 087;
КР – расходный коэффициент метала = 12;
Рисунок 10. График работы стана во времени
Время такта прокатки до реконструкции составило 300 сек.
После реконструкции:
Время такта прокатки после реконструкции составил 170 сек.
Годовая производительность стана:
FФ - фактическое время работы стана.
Повышение производительности стана составило:
2.Расчет штатов рабочих и фонда заработной платы
Расчет штата рабочих
В условиях цеха предусматривается непрерывный 3-х сменный 4-х бригадный график работы (таблица 6.2).
Расчет штатов рабочих проводится следующим образом. Сначала определим расстановочный штат т.е. минимальную численность рабочих обеспечивающих бесперебойное функционирование оборудования цеха.
При составлении штатного расписания учитывалось необходимое число рабочих при принятом графике работы. Суточный расстановочный штат определен умножением односменного расстановочного штата на 4.
Списочный штат предусматривает резерв на подмену к полному расстановочному штату. Для его определения составляют плановый баланс использования рабочего времени в году для каждой категории рабочих по продолжительности отпуска и графику невыходов. Полная резервная численность рабочих определяется умножением полного расстановочного штата на коэффициент списочности. Списочный штат равен сумме полного расстановочного штата и полного резерва на подмену (таблица 6.3).
Таблица 6.2 - Баланс рабочего времени одного трудящегося в днях.
Выполнение общественных обязанностей:
Коэффициент списочности:
Процент невыходов по отношению к фактическому времени:
По болезни и обязанностям:
Разряды и тарифные ставки рабочих выбирались с целью обеспечения высококвалифицированной эксплуатации оборудования и получения качественного металла.
Коэффициент списочности:
Таблица 6.3 - Списочный штат рабочих
Вспомогательные рабочие
Мастер электрообору-
Общее количество работающих:
Расстановочный штат т.е. минимальная численность рабочих необходимая для обеспечения бесперебойного функционирования производства в одну смену составляет 128 человек. Полный расстановочный штат при 4-х бригадном графике работы в 3 смены составляет 128 человек.
Списочный штат рабочих в котором дополнительно к полному расстановочному штату предусматривается резерв на подмену 9 человек составляет 137 человек.
Расчет фонда заработной платы
Время работы оборудования в течение года и общее количество выходов на одного рабочего определяется из баланса использования рабочего времени составленного в предыдущем подразделе. Отдельные элементы фонда заработной платы рассчитываются следующим образом.
Расчёт приведем для оператора ПУ 6 разряда. Расчет для остальных специальностей выполняется аналогичным способом. Результаты расчета представлены в таблице 12.
Распределение рабочих часов:
Праздничных часов ч.
Вечерних часов: 730 ч.
Часов переработки графика: 65 ч.
Заработная плата рабочих после реконструкции не меняется.
Заработная плата по тарифу определяется умножением часовой тарифной ставки на количество часов работы в год и на полный расстановочный штат соответствующей группы рабочих.
– количество отрабатываемых часов за год.
Размер премии для каждой группы рабочих принимается в процентах от суммы сдельного заработка на основе действующих на предприятии положений о премировании (в данном случае – 100%).
Расчет премий за выполнение плана
За каждый час работы в ночное время производится доплата в размере 40% часовой тарифной ставки
Доплата за работу в ночное время определяется умножением на 04 (40%) часовой тарифной ставки на количество ночных часов и на полный расстановочный штат.
За каждый час работы в вечернее время производится доплата в размере 20% часовой тарифной ставки.
Доплата за работу в праздничные и выходные дни определяется умножением на 2 (100%) отработанных часов в праздничные и выходные дни на часовую тарифную ставку и на полный расстановочный штат.
Доплата за переработку графика составляет 50% от часовой тарифной ставки.
Сумма основной заработной платы определяется суммированием оплаты по тарифу премии и суммы доплат.
Дополнительная заработная плата:
Дополнительная заработная плата определяется с помощью процента невыходов по отношению к фактическому времени за вычетом резерва в связи с невыходом по болезни так как оплата больничных листов проводится из фонда социального страхования. Дополнительная заработная плата рассчитывается путем умножения основной заработной платы на процент невыходов в связи с отпуском или выполнением государственных и общественных обязанностей.
Весь фонд заработной платы определяется суммированием основной и дополнительной заработной плат.
Среднемесячная заработная плата одного рабочего определяется делением общей суммы выплат соответственно на списочное количество рабочих и на число месяцев в году.
Среднемесячная заработная плата одного работника по фонду зарплаты:
Расчёт заработной платы на остальных работников представлен в таблицах 6.4 и 6.5.
Таблица 6.4 - Заработная плата основных рабочих
аработная плата по тарифу руб.
Доплата за работу в вечер руб.
Доплата за работу в ночь руб.
Доплата за работу в выходные руб.
Таблица 6.5 - Заработная плата вспомогательных рабочих
Мастер электрообору-дования
3.Система управления качеством готовой продукции
-контроль качества и устранение дефектов;
При производстве проката в понятие качества входит:
-соблюдение точных геометрических размеров (готовое изделие должно соответствовать установленным технологической схемой размерам);
-хорошее состояние поверхности;
-получение заданных механических свойств готового проката.
Функция организация в отношении качества продукции осуществляется путем обоснованного выбора необходимого оборудования а также использования специальных узлов устройств и конструктивных решений которые гарантируют или способствуют достижению оговоренных параметров качества на запланированном уровне.
Установленная на стане клеть удовлетворяет всем требованиям качества.
Предельные допуска на продукцию при прокатке на стане 5000 указаны в
Таблица 6.6 - Допуски по ширине
Ширина листа: 1700-4800 мм
Таблица 6.7 - Предельные допуски по толщине при прокатке на стане 5000 (ГОСТ 19903-74)
4. Капитальные вложения в реконструкцию
Капитальные затраты на возведение зданий
где Sп — площадь производственного здания
Цп — цена 1 м2 производственного здания (10600 руб.)
Сведения о капитальных вложениях в здание показаны в таблице 6.8.
Таблица 6.8 - Капитальные вложения в здания.
Капитальные вложения на установку чистовой клети кварто стана 5000 составят 1598420690 рублей.
Капитальные вложения в производственное оборудование:
ЦОБ — цена оборудования 1598420690 руб.
bТ — коэффициент учитывающий транспортно-заготовительные расходы
связанные с приобретением оборудования bT=005.
bM — коэффициент учитывающий затраты на устройство фундаментов монтаж
Капитальные вложения в производственный инвентарь:
Капитальные вложения в санитарно-технические устройства:
Капитальные вложения в неучтенное оборудование:
5. Расчёт основных фондов
Стоимость основных фондов составит:
Кп- капитальные затраты на эксплуатацию производственного здания руб.
Коб- капитальные вложения руб.
Кп.ин- капитальные вложения в производственный инвентарь руб.
Кс.у--капитальные вложения в санитарно-технические устройства руб.
Кн.о- капитальные вложения в неучтенное оборудование руб.
Данные о амортизационных отчислениях приведены в таблице 6.9.
Таблица 6.9 - Амортизационные отчисления
Амортизационные отчисления
Производственное здание
Производственное оборудование
Производственный инвентарь
Санитарно-технические устройства
Неучтённое 41оборудование
6. Расчёт себестоимости продукции
Основная заработная плата рабочих:
- фонд основной заработной платы руб.
-базовая годовая производительность стана
-проектная годовая производительность стана
Дополнительная заработная плата рабочих:
- фонд дополнительной заработной платы руб.
Отчисления во внебюджетные фонды:
Амортизация основных фондов:
Величина амортизации: 40918497949 руб.
Внутрицеховые перемещения:
Расходы на подготовку и освоение:
Итоговые расходы по переделу:
Общезаводские расходы составляют 10% от итоговых расходов по переделу:
Прочие производственные расходы составляют 7% от итоговых расходов по переделу:
Передел за вычетом отходов:
Сталь 10Г2ФБ принимаем:
Цена на передел: 36290 руб.
Цена отходов: 11790 руб.
Металла в передел задано: 12 т
Заводская себестоимость:
7. Расчёт технико-экономических показателей
коэффициент расхода металла для толстолистовых станов:
Удельная производительность оборудования:
Производительность труда рабочих:
Для основных рабочих:
До реконструкции(человек):
После реконструкции(человек):
Для вспомогательных рабочих (человека):
До реконструкции (человек):
После реконструкции (человек):
Рентабельность продукции:
Годовой экономический эффект:
Сравнительные значения технико – экономических показателей приведены в таблице 6.10.
В данной дипломной работе были рассчитаны технико-экономические показатели до реконструкции производства а затем с учетом изменений после реконструкции производства.
В проектном варианте себестоимость продукции снизилась повысилась рентабельность производства с 15% до 1674%.
Производительность стана увеличилась на 7647%.
Годовой экономический эффект составил 401 млн. руб. Капитальные вложения должны окупиться за 284 года что меньше нормативного (3 года) следовательно реконструкция экономически эффективна.
Таблица 6.10 - Сравнительные технико-экономические показатели
Наименование показателей
Годовой объем производства
Часовая производительность
Годовой фонд фактического времени
Численность трудящихся
Производительность труда одного работающего
Среднемесячная заработная плата одного работающего
Капитальные вложения в реконструкцию
Рентабельность продукции
Годовой экономический эффект
Дипломный Проект_титульный лист.doc
ФАКУЛЬТЕТ Металлургических и машиностроительных технологий
КАФЕДРА Технологии и оборудования прокатного производства
СПЕЦИАЛЬНОСТЬ 150106 «Обработка металлов давлением»
ПОЯСНИТЕЛЬНАЯ ЗАПИСКА
К ДИПЛОМНОМУ ПРОЕКТУ
на тему: Реконструкция толстолистового стана горячей прокатки 5000
Ижорского металлургического завода
Руководитель работы( )
по экономике и управлению производством( )
по безопасности жизнедеятельности( )
по охране окружающей природной среды( )
Работа рассмотрена кафедрой и допущена к защите в ГАК
Электросталь июнь г.
Содержание.doc
1. Экономическая целесообразность проекта
Техника производства
1. Исходные материалы и нагрев их перед прокаткой
3. Технологический процесс прокатки на стане 5000
4. Контролируемая прокатка
5. Назначение и состав оборудования стана 5000
6. Чистовая клеть кварто толстолистового стана 5000
7. Возможные дефекты горячекатаных листов
8. Автоматизация процесса прокатки
9. Объёмно-планировочные решения цеха
1. Свойства стали 10Г2ФБ
2. Расчёт энергосиловых параметров
3. Расчёт оборудования на прочность
Безопасность жизнедеятельности
1. Географическое и территориальное расположение цеха
2.Технические решения по производственной санитарии
3. Анализ потенциально опасных и вредных производственных
факторов при выполнении основных операций
4. Разработка мер защиты от выявленных потенциально опасных и вредных
производственных факторов
5. Безопасность жизнедеятельности при чрезвычайных ситуациях
Охрана окружающей среды
1. Оценка загрязнения воздушного бассейна
2. Защита водного бассейна
3. Утилизация отходов производства
Экономика и управление производством
1. Расчет производительности стана 5000
2.Расчет штатов рабочих и фонда заработной платы
3.Система управления качеством готовой продукции
4. Капитальные вложения в реконструкцию
5. Расчёт основных фондов
6. Расчёт себестоимости продукции
7. Расчёт технико – экономических показателей
Список использованных источников
Введение.doc
Расположение главных районов добычи нефти и газа на Севере а основных потребителей — в Центре и на Западе России и за границей обусловливает необходимость сооружения сети мощных подземных и надземных магистральных трубопроводов большой протяженности. Наша страна обладает крупнейшей в мире сетью газопроводов протяжённостью более 150 тыс. км. При этом потребность в трубах большого диаметра только за последние 7 лет увеличилась почти в 25 раза. Так лишь для строительства газопровода «Северный поток» прокладываемого по дну Балтийского моря потребуется 1220 км труб большого диаметра. Кроме того планируется расширение сети существующих газопроводов. Широкие листы из высокопрочных сталей потребляет и оборонная промышленность где они используются в качестве корабельной брони и материала для корпусов подводных лодок. Это вынуждает нашу промышленность в данный момент закупать часть потребляемых широких листов за границей.
Современные проектируемые станы 5000 имеют годовую производительность порядка 15 млн. тонн проката в год. Годовая производительность стана 5000 Ижорского металлургического завода составляет порядка 850 тыс. тонн. Этого явно недостаточно для обеспечения нефтегазовой промышленности. Реконструкция позволит существенно увеличить производительность стана. Следует отметить что установка двух клетей кварто предусматривалась на стане ещё на стадии проектирования однако в силу различных причин уже на стадии строительства было решено ограничится одной. Однако место под вторую клеть было зарезервировано что при данной модернизации позволяет затратить меньше средств на строительную часть проекта. Кроме того непосредственно рядом со станом 5000 был построен новый цех предназначенный для производства сварных труб большого диаметра. Увеличение производительности после реконструкции позволит так же обеспечить загрузкой и его.