Кран башенный на гусеничном ходу




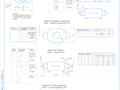
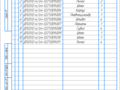
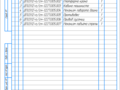
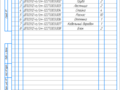
- Добавлен: 25.01.2023
- Размер: 5 MB
- Закачек: 0
Описание
Кран башенный на гусеничном ходу
Состав проекта
![]() |
![]() |
![]() |
![]() ![]() ![]() ![]() |
![]() ![]() ![]() |
![]() ![]() ![]() |
![]() ![]() |
![]() ![]() ![]() ![]() |
![]() |
![]() ![]() ![]() ![]() |
![]() ![]() ![]() ![]() |
![]() |
![]() ![]() ![]() ![]() |
![]() ![]() ![]() ![]() |
![]() ![]() ![]() ![]() |
![]() ![]() ![]() ![]() |
![]() ![]() ![]() ![]() |
![]() ![]() ![]() ![]() |
![]() ![]() ![]() ![]() |
![]() ![]() ![]() ![]() |
![]() ![]() ![]() ![]() |
![]() ![]() ![]() ![]() |
![]() ![]() ![]() ![]() |
![]() |
![]() ![]() ![]() |
![]() ![]() ![]() |
![]() ![]() ![]() |
![]() ![]() ![]() |
![]() ![]() ![]() |
![]() ![]() ![]() |
![]() ![]() ![]() |
![]() ![]() ![]() |
![]() ![]() ![]() |
![]() ![]() ![]() |
![]() ![]() ![]() |
![]() ![]() ![]() |
Дополнительная информация
2.1. Стрела .cdw

Канат механизма подъема
ДП.0312-псм-1227.002.000.СБ
ДП.0312-псм-1227.002.001
ДП.0312-псм-1227.002.002
ДП.0312-псм-1227.002.003
ДП.0312-псм-1227.002.004
ДП.0312-псм-1227.002.005
ДП.0312-псм-1227.002.006
5.2. Технол2.cdw

ДП.0312-псм-1227.009.000.СБ
ДП.0312-псм-1227.009.001
ДП.0312-псм-1227.009.002
ДП.0312-псм-1227.009.003
ДП.0312-псм-1227.009.004
ДП.0312-псм-1227.009.005
ДП.0312-псм-1227.009.006
ДП.0312-псм-1227.009.007
ДП.0312-псм-1227.009.008
ДП.0312-псм-1227.009.009
ДП.0312-псм-1227.009.010
ДП.0312-псм-1227.009.011
2.2. Портал.cdw

ДП.0312-псм-1227.003.000.СБ
ДП.0312-псм-1227.003.001
ДП.0312-псм-1227.003.002
ДП.0312-псм-1227.003.003
ДП.0312-псм-1227.003.004
ДП.0312-псм-1227.003.005
ДП.0312-псм-1227.003.006
ДП.0312-псм-1227.003.007
ДП.0312-псм-1227.003.008
2.4. Тележка гусеничная.cdw

Механизм поворота башни
Механизм подъёма стрелы
ДП.0312-псм-1227.005.000.СБ
ДП.0312-псм-1227.005.001
ДП.0312-псм-1227.005.002
ДП.0312-псм-1227.005.003
ДП.0312-псм-1227.005.004
ДП.0312-псм-1227.005.005
ДП.0312-псм-1227.005.006
ДП.0312-псм-1227.005.007
5.1. Технол1.cdw

пов-ти инструмента и ГОСТ
Операция 015 Продольно-строгальная
Станок продольно-строгальный 7110
0 Операция Сверлильно-центровальная
Станок: Горизонтально-расточной 2М615
Операция 020 Продольно-строгальная
прямой с пластинами
Операция 025 Токарная
Станок токарный 1Е140
Операция 030 Токарно-карусельная
Станок токарно-карусельный 1512
Неуказанные предельные отклонения
размеров отверстий по Н14
остальных t2 по классу точности
ДП.0312-псм-1227.008.000.
2.3. Кондор.cdw

ДП.0312-псм-1227.004.000.
Барабаны условно не показаны
2.cdw

2.ыыыcdw.cdw

1.Выдвижение башни.cdw

1.cdw

3. Установка.cdw

5.2. Технол2.cdw

воздуха в пневмосети 0.4 МПа.
* размеры для справок.
ДП.0312-псм-1227.009.000.Сб
2.1. Стрела.cdw

Сварные швы второго класса по ОСТ 4
ДП.0312-псм-1227.002.000.
Горизонтальная стрела
Техническая характеристика:
2.2. Портал.cdw

ДП.0312-псм-1227.003.000.
Технические требования:
1. Общий вид.cdw

Группа режима работы крана
при мах грузоподъемности 15
передвижения крана 12
передвижения тележки 7
Диаметр поворотной части
крана без противовеса
Диаметр ходового колеса
Тип подкранового рельса
ДП.0312-псм-1227.001.000.
Запасовка стрелового крана
Запасовка грузового каната
ТЕХНИЧЕСКАЯ ХАРАКТЕРИСТИКА
Высота подъема крюка
4. Элсхема.cdw

электропривода с контроллером К
ДП.0312-псм-1227.007.000.
Схема магнитного крнтроллера ТСА
Схема магнитного контроллера К
Механичесские характеристики электропривода с контроллером ТСА
2.4. Тележка гусеничная.cdw

Материал разъёмных колец Сталь45
Ролики сталь ШХ15 или ШХ15СГ
Прочие параметры по НП 4819-83
ДП.0312-псм-1227.005.000.
Барабаны условно не показаны
Техническая характеристика:
1. Введение.doc
Подавляющее большинство строительных объектов – это многоэтажные сооружения возводимые в стесненных городских условиях. Строящееся здание занимает большую часть строительной площадки. Башенный кран в свою очередь занимает минимальную площадь вблизи строящегося здания позволяет обеспечить большую высоту подъема широкую зону обслуживания и кроме того в транспортном состоянии имеет приемлемый габарит.
Проектируемый кран должен быть простым по конструкции легко и быстро монтируемым мобильным и доступным в цене для небольшой организации или частного лица. В процессе разработки необходимо обеспечить взаимозаменяемость деталей и узлов а это значит что кран должен быть собран из возможно большего числа стандартных изделий.
При изготовлении и эксплуатации крана необходимо соблюдать требования охраны труда и защиты окружающей среды.
2. Аналитический обзор.doc
Башенные краны имеют значительные размеры зон обслуживания строительной площадки большую высоту подъема груза с возможностью горизонтального его перемещения при неподвижно стоящем кране несложность перебазировки с одного объекта на другой автомобильным и железнодорожным транспортом общего назначения.
Башенные краны различаются между собой по характеру установки способу обслуживания изменению вылета груза конструктивному исполнению башни способу соединения стрелы с башней. По характеру установки башенные краны делят на наземные и устанавливаемые на строящемся объекте (самоподъемные). Наиболее универсальны первые вторые применяют на особо высоких (выше 45 м) объектах строительства.
По способу обслуживания мостостроительного объекта башенные краны разделяют на: стационарные обслуживающие объект с одной установки; передвижные работающие в зоне обусловленной расположением рельсовых или других путей. В частности при строительстве высоких но небольших по сечению сборных опор мостов могут с успехом применяться стационарные башенные краны в том числе и приставные (крепящиеся к возводимому объекту).
По характеру ходовых частей способу перемещений применяются башенные краны на рельсовом ходу (в основном) и безрельсовом. Возможности рельсового хода расширились с появлением устройств для перемещения ходовой части по криволинейным путям.
По способу изменения вылета крюка башенные краны бывают со стрелой балочной подъемной сочлененной. Наиболее удобными в эксплуатации и обеспечивающими наибольшую точность монтажа являются краны с балочной стрелой по которой перемещается грузовая каретка. Такая конструкция удобна в случаях когда с одной стоянки кран должен выполнять значительное число подъемов. Однако балочные стрелы по сравнению с другими конструкциями тяжелы снижают грузоподъемность крана поэтому большее распространение получили подъемные решетчатые стрелы эффективные в случаях когда работа крана связана с его частой передвижкой. Для удобства транспортирования эти стрелы часто выполняют сочлененными.
Башни кранов бывают: постоянной длины составные секционно наращиваемые с центральным или боковым расположением секций; складывающиеся.
По способу сочленения стрелы с башней различают краны с неповоротной башней на верхней части которой монтируется поворотная стрела на опорно-поворотном устройстве и с башней поворачивающейся совместно с подвешенной к ней стрелой. В первом случае это будет кран с нагруженной изгибающим моментом башней во втором — с разгруженной башней (более легкой конструкции).
Башенные краны имеют многодвигательный электропривод с отдельными двигателями для каждой операции.
Наиболее целесообразными для использования из отечественных кранов являются башенные краны унифицированной серии КБ. Это краны КБ-303 (КБк-100.1) КБ-306 (С-981) С-981Б КБ-401 (КБ-160.2) КБ-674.
В настоящее время в России распространены краны следующих производителей:
Краны отечественного производства (а также СНГ)
КБ-474 выпускают в двух базовых вариантах – передвижной полноповоротный и приставной стационарный с неповоротной башней и полноповоротной балочной стрелой. Оба варианта выпускают в пяти исполнениях по грузоподъемности – от 12 до 38 т. КБ-474 остается самым высоким отечественным краном. Высота подъема при двукратной запасовке грузового каната составляет 222 м. В передвижном и стационарном исполнениях производят также кран КБ-571Б гп 26 120 т при вылете стрелы 208 700 м. В производственной программе завода – мобильные башенные краны КБМ-401П КБМ-401П-41 КБ-405 мобильные самомонтирующиеся краны РБК-2.20 РБК-3.40 РБК-5.60 стреловые краны серии КЛ-3 грузовые и пассажирские лифты ПП и ПГ для промышленных зданий и сооружений строительные подъемники вышки связи ВС-60 крановые электродвигатели блоки резисторов и др.
КБ-403Б предназначен для механизации строительных и монтажных работ в жилищном и гражданском строительстве сооружений высотой до 547 м с массой монтируемых элементов до 8 т.
КБ-408.21 используют на строительных и монтажных работах производимых на высоте до 727 м с массой монтируемых элементов до 10 т. Кран-погрузчик
КБ-578 по своим характеристикам не имеет аналогов в России и странах СНГ. Он предназначен для погрузочно-разгрузочных работ в промышленности на складах и при различных технологических операциях в строительном комплексе.
Передвижной башенный кран КБ-515 на рельсовом ходу выпускаемый с 2003 года на Одинцовском механическом заводе предназначен для строительства 25-этажных зданий (грузоподъемность 10 т вылет стрелы 50 м высота подъема 96 м). Глубина опускания груза у КБ-515 – 5 м что позволяет применять его для котлованных работ. Наращивание башни производится сверху монтажной обоймой с гидравлическим механизмом наращивания.
Недавно завод освоил выпуск 10-тонного крана КБМ-401ХЛ с балочной стрелой и высотой подъема груза 47 м при максимальном вылете стрелы (при поднятой на 30° стреле максимальный подъем – 60 м).
Никопольское ПО «Краностроительный завод» (старейшее в СНГ предприятие выпускающее башенные краны Украина) в этом году отмечает свое 120-летие. В его производственной программе – кран-лесопогрузчик башенного типа КБ-572Б на рельсовом ходу с балочной стрелой и грузовой тележкой (возможно передвижение под порталом железнодорожных вагонов допускается использование в качестве строительного крана).
Краны зарубежных производителей:
Компания Potain представлена в России двумя сериями: гидравлические компактные самомонтирующиеся башенные краны HD для работы в стесненных условиях и рельсовые или фундаментные высотные башенные краны серии MD которые оснащены системой координатной защиты и управления для работы в пересекающихся рабочих зонах. Грузоподъемность кранов – 6 12 т. При вылете стрелы 60 м высота свободностоящих кранов достигает 75 м а с пристежкой к зданию – до 200 м и выше.
Liebherr. В модельный ряд немецкой фирмы Liebherr входит семь серий башенных кранов (HC LC LD EL EC-H EC-H Litronic и EC-HM FR.Litronic) три серии специальных кранов (EC-B HC-K HC-L) и пять серий компактных монтажных кранов (H HM TT K и R) управляемых с пульта на земле. При этом краны серии R (32 TTR и 42 KR.1) грузоподъемностью 4 т (высота подъема груза 24 м и 26 м соответственно) изготовлены на гусеничном ходу что делает их незаменимыми на грунтах с пониженной несущей способностью. Для работы в городских условиях производят башенные краны на автомобильном шасси (8-тонные Liebherr МК 80 и Liebherr МК 100) и на шасси прицепа (12- и 20-тонные Liebherr 13 HM и Liebherr 20 HM).
Компания Comedil TEREX экспортирует в Россию новейшую модель крана CTT Flat top используемую строителями США и Европы. Существует 21 модификация этой модели для решения задач любого масштаба и любой сложности – от небольшой реконструкции до возведения кварталов высотных домов или больших мостов. В зависимости от модификации грузоподъемность кранов CTT изменяется от 25 до 40 т максимальный вылет стрелы – от 41 до 85 м а высота – от 18 до 106 м без крепления к стене и до 285 м в случае крепления к строительному объекту.
Кроме этого на рынке России широко представлены башенные краны IHI Jaso Linden-Comansa Ogawa PPM Raimondi и Zeppelin (серия ZBS).
3. Исследовательский раздел.doc
Провести анализ дефектов возникающих на автомобильных кранах эксплуатирующихся в Калужской области. Разработать систему классификации и кодирования дефектов автомобильных кранов.
Подробная классификация дает возможность найти наиболее распространенные дефекты характерные для каждого типа кранов. А анализ полученных результатов дает возможность разработать методы по предупреждению возникновения дефектов по диагностике крана во время его эксплуатации.
После проведения классификации полученные дефекты подвергаем кодировке. Кодировка дефектов облегчает создание электронного банка данных. Банка данных позволяет рационально организовать компактно хранить и оперативно использовать разнообразную информацию обо всех рассмотренных кранах.
В процессе эксплуатации кранов их металлические конструкции подвергаются интенсивному воздействию различных физико-химических процессов приводящих к физическому износу коррозии образованию трещин остаточным деформациям. Физический износ стимулирует рост динамических нагрузок. Их интенсивность определяет величину и скорость накопления повреждений приводящих к частичной а затем и к полной утрате работоспособности конструкций. Особо остро эта проблема касается грузоподъемных машин отработавших свой срок службы.
Грузоподъемные машины отработавшие нормативный срок службы подвергаются экспертному обследованию (диагностированию) проводимому специализированными организациями в соответствии с нормативными документами. По результатам обследования оформляется акт обследования с заключением комиссии и приложениями включающими информацию об объекте обследования его владельце о комиссии проводящей обследование о фактических условиях использования ГПМ их общем состоянии и состоянии отдельных узлов на момент обследования о количестве дефектов с их классификацией о характере работ выполняемых ГПМ результатах статических и динамических испытаний и т.д.
Из этой ведомости можно узнать паспортные данные крана а также что важнее наименование узла (элемента) в котором был обнаружен дефект; описание самого дефекта и еще дается заключение о необходимости и сроках устранения дефектов.
3. ст.Исследовательский раздел.doc
Актуальность исследования
Универсальным рабочим органом грузоподъемных кранов является грузовой крюк. Размеры крюков стандартизованы: для механизмов с ручным и машинным приводом – однорогие по ГОСТ 6627 для механизмов с машинным приводом – двурогие по ГОСТ 6628. Стандартные крюки подбираются для соответствующей номинальной грузоподъемности кранов и расчет их сечений в данном случае не проводят.
В ГОСТе 6627 регламентированы параметры 26-и типоразмеров однорогих грузовых крюков грузоподъемностью от 025 до 100 тонн с промежутками в стандартном ряде производительности от 007 до 20 тонн. Такой диапазон типоразмеров не может удовлетворять всему многообразию эксплуатационных требований в каждом конкретном случае при создании специальных грузоподъемных машин и грузозахватных приспособлений с грузовыми крюками. Часто возникает необходимость в крюках нестандартной грузоподъемности отличающихся от стандартных размерами или формой с увеличенной (уменьшенной) шириной зева и т.д. Так в последнее время широкое распространение получили грузоподъемные краны грузоподъемность которых значительно превышает 100 тонн. В перечисленных и других подобных случаях при проектировании крюка форма размеры или грузоподъемность которого не соответствуют стандартным необходимо обосновывать оптимальные геометрические параметры и проводить расчет его прочности [6].
Расчет крюка оптимизированной формы
Расчет крюка выполнен в среде MathCAD.
Поперечное сечение крюка описывается частями линий окружности y(x) h2(x) optim1(x) прямой optim2(x) и параболы optim(x).
Уравнение окружности y(x) имеет вид:
где Ry – радиус окружности y(x).
Уравнение окружности h2(x):
где R2 – радиус окружности h2(x) x2 y2 – координаты центра окружности.
Уравнение окружности optim1(x):
где Rh – радиус окружности optim1(x) H–ширина поперечного сечения.
Уравнение параболы optim(x):
где xo yo – координаты вершины параболы [14].
Уравнение прямой optim2(x):
С использованием функции Given Find(x) получим координаты граничных точек:
Сечение описывается с помощь встроенного языка программирования:
Площадь поперечного сечения и статический момент:
где Н – ширина поперечного сечения.
Координата центра масс:
где S – статический момент F – площадь поперечного сечения.
Координаты крайних точек поперечного сечения:
Коэффициент формы поперечного сечения:
Напряжение в крайних волокнах сечения:
Напряжения в промежуточных точках поперечного сечения:
)От центральной линии в сторону зева крюка:
)От центральной линии в сторону противоположную зеву крюка:
Сравнение крюков со стандартным и нестандартным профилем поперечного сечения. Сравнение допускаемых напряжений.
Для сравнения использовался крюк рассчитанный по ГОСТ. Расчет произведен в среде MathCAD.
Определение допускаемых напряжений:
где [n]=12 для режимов работы М1-М6
[n]=15 для режимов работы М7-М8
Как видно из расчетов напряжения меньше допустимых но если крюк выполненный с трапециевидным сечением с трудом укладывается в отведенные рамки то крюк с тавровым сечение имеет большой запас по напряжениям. В литературе в качестве рекомендованного значения независимо от режима работы нестандартных крюков принимается запас прочности равный 15.
Этому условию может удовлетворять только крюк с тавровым сечением. К тому же масса крюка с оптимизированным сечением меньше стандартизованного при сохранении всех геометрических параметров кроме профиля поперечного сечения.
Список литературы.doc
Невзоров Л.А. Пазельский Г.Н. Романюха В.А. Строительные башенные краны: Учебник для сред. ПТУ. – М.: Высш. школа 1986. – 176 с.
Невзоров Л.А. Башенные строительные краны:
Справочник Невзоров Л.А. Пазельский Г.Н. Певзнер Е.М. - М.: Машиностроение 1992. -320 с.
Безопасности жизнедеятельности под ред. C.В. Белова. М.: Высш. школа 2001.
Ланин В.А. Кукин П.П. Понамарев Н.Л. Безопасности технологических процессов и производств: Учебник. М.: Высш. школа 2001. – 306 с.
Невзоров Л.А. Зарецкий А.А. Волин Л.М. и др. Башенные краны:
М.: Машиностроение 1979. – 296 с.
Вергазов В.С. В помощь крановщикам и стропальщикам:
М.: Моск. рабочий 1982. – 347 с.
Крановое электрооборудование: Справочник Под ред. А.А. Рабиновича. М.: Энергия 1979. – 238 с.
Невзоров Л.А. и др. Современное состояние и перспективы развития механизмов и приводов башенных кранов отечественного и зарубежного производства: ЦНИИТЭстройдормаш 1987. Сер. 1 Вып. 2. 52 с.
Невзоров Л.А. и др. Справочник молодого машиниста башенных кранов: Справочник М.: Высш. школа. 1985. – 192 с.
Справочник по кранам. Т. 1 и 2 Под ред. М.М. Гохберга. Л.: Машиностроение 1988. Т. 1. 536 с. Т. 2. 560 с.
Строительные машины. Т. 1 и 2 Т. 1 под ред. Э.Н. Кузина и т.2 под ред. М.Н. Горобца. М.: Машиностроение 1991.
Яуре А.Г. Певзнер Е.М. Крановые электроприводы:
Справочник. М.: Энергоатомиздат 1988. 344 с.
Промышленное и строительное оборудование. Под ред. Игошев Д.
Сборник № 4 Зарегистрирован Комитетом РФ по печати. Рег. Свид. №014909 2003. – 170 с.
Навроцкий Д.И. Расчет сварных соединений с учетом концентрации напряжений. – Л.: Машиностроение 1968. – 170 с.
Николаев Г.А. Куркин С.А. Винокуров В.А. Сварные конструкции. Прочность сварных соединений и деформаций конструкций: Учеб. Пособие. – М.: Высш. школа. 1982. – 272 с.
Faltus F. Joints with fillet welds - Prague: Academia 1985. – 300 р.
Махненко В.И. Рябчук Т.Г. Концентрация напряжений у концов фланговых швов Применение математических методов в сварке. – Киев: ИЭС им. Е.О. Патона 1988. – C. 61 – 67.
Тимошенко С.П. Курс теории упругости. – Киев: Наук. Думка 1972. – 107 с.
Махненко В.И. Рябчук Т.Г. Компьютеризация расчета сварных соединений с угловыми швами Fdnjvfn cdfhrf - 1991. - №11 – C. 1-6.
Прочности сварных соединений при переменных нагрузках
Под ред. В.И. Труфякова. – Киев: Наук. Думка 1990. – 256 с.
4. Конструкторский раздел.doc
1. Расчет металлоконструкции стрелы
Металлоконструкция выполняется сварной из стали марки Ст3ПС. Определение расчетных усилий в стержнях в данном случае производим исходя из двух возможных случаев работы крана:
при мгновенном торможении опускаемого груза и неподвижном кране
при резком торможении вращающегося крана с подвешенным грузом
Первый расчетный случай.
При определении динамического коэффициента исходим из статического удлинения грузовых канатов деформацию самой конструкции в данном случае не учитываем что идет в запас прочности.
В рассчитываемом кране груз подвешен на одинарном полиспасте с передаточным числом n= 2 принятый диаметр грузового каната d = 11мм. площадь сечения его проволок к=0.47см². расчетная длинна вертикального участка lк=11.5м. горизонтального – l1 = 10 м..
Статическое удлинение вертикального участка каната:
λ 1 = ––––––––––––––––– = ––––––––––––––– = 3.06 см.;
n ·к· Ек2 · 047 ·1 ·106
Ек = 1·106 - модуль упругости каната;
Для горизонтального участка каната:
λ 2 = –––––––––––––––––––– = –––––––––––––––––– = 1.33 см.;
·к· n· Ек 2· 0.47· 2 ·1· 106
Суммарное удлинение каната:
λ ст = λ 1 + λ 2 = 3.06 + 1.33 = 4.39 см.;
Скорость подъема груза:
Динамический коэффициент:
g = 1 + ––––––– = 1+ –––––––––– = 1.5;
Расчетная нагрузка от массы поднимаемого груза:
Qp = g ·Q = 1.5 · 2500 = 3750 кг = 36800 Н;
Нагрузка от напряжения грузового каната:
Sк = –––––––––––––– · g = –––––––––––––– ·1.5 = 1913 кг = 18800 Н;
Размеры сечения стрелы:
––––– = 0.02 ÷ 0.04 ; [4]
hПринимаем h = 0.4 м. в = 03 м.
Точку крепления оттяжки к стреле выбираем исходя из равенства моментов от веса груза в середине пролета М2 и на конце стрелы М1.
Gгр (L - C) = Gгр · –––––––– ; с = –––––––– ;
При длине стрелы L = 9.2 м с = 7.36 м;
Нагрузки от поднимаемого груза.
Sp = 36800·9.2 2 = 169280 Н;
R = 169280 + 36800 = 206080 H;
Методом поперечных сечений находим усилия в поясах и раскосах.
Qp · 0.92 + Sк · 0.4 + (F 7-8 + F 7-9) cos 20° · 0.61 = 0;
(- F 5-8 – F 6-9) · 0.4 + Qp · 1.38 = 0;
Qp · 1.84 + Sк · 0.4 + F7-10 · 0.4 = 0;
F5-8 = F6-9 = 5526 H;
F7-8 = F7-9 = 26678 H;
F8-9 = F 8-7 · 2 · s
F8-9 = 26678 · 2 · s
Второй расчетный случай.
Горизонтальная сила от веса груза и грузовой подвески:
Pг = 0.1· (Q +G подв) = 0.1· (14500 + 357) = 1485 H;
F1-4 = ––––––––– = –––––––––––– = 76206 H;
Pг · 8.28 – F 1-4 · 0.3 + F 4-2 · 0.3 = 0;
-1485 · 8.28 + 76206 · 0.3
F4-2 = –––––––––––––––––––– = 7620 H;
Нагрузки от собственной массы металлоконструкции.
Sp R g2 = 400 кг g1 = 100 кг
Принимаем массу стрелы 500 кг.;
g2 · 3.68 + g1 · 8.28
Sp = –––––––––––––––––––– = 1150 кг. = 11280 Н.;
М мах = М2 – М1' = 7220 – 450 = 6770 Н·м;
Нагрузки в верхних поясах:
Fвп = ––––––––––––––––––– = –––––––––––––––––– = 9002
· 0.4 ·cos 20° 2 · 0.4 cos 20°
Расчет нагрузок в нижнем поясе и раскосах определяем аналогично приведенному выше расчету:
Усилие в стойке верхнего пояса аналогично F 8-9:
Горизонтальная нагрузка
gг = 0.1g = 0.1 · 533 = 53 Hм.
g = 533 Hм - принятая распределенная нагрузка;
Pг = 9.2 · g= 9.253 = 488
F1-4 = ––––––– = ––––––––– = 7482
Нагрузки в вертикальной и горизонтальной распорках
Sp = 1692080 + 11280 = 180560
Sp sin 37°+Spsin 11°
F = –––––––––––––––––––– = 71890 2 cos 11°2
Sp sin 53 ° 18056 sin 53°
F= –––––––––––– = –––––––––––––––––––– = 72434
cos 17 °2 2 cos 17 ° 2
Найденные усилия в стержнях сводим в таблицу. Стержни металлоконструкции стрелы выполнены из труб что дает выигрыш в весе по сравнению с металлоконструкцией из уголков или швеллеров. Нижний пояс стрелы выполнен из двутавра.
Нагрузки в стержнях выбираем по наибольшему значению с учетом знака.
Усилия в стержнях фермы рассчитываемого башенного крана для металлоконструкции стрелы.
Нагрузки в стержнях с учетом знака
От поднимаемого груза
От собственной массы
Принимаем двутавр №12 с площадью поперечного сечения А = 17.8 см² моментом инерции Jm
При расчетах на прочность допускаемое напряжение
n = 1.4 – коэффициент запаса прочности для металлоконструкций из стали;
пр = т =255 МПа – предел текучести для Ст 3;
[] = 2251.4 = 160 MПа;
Коэффициент соответствующий этой гибкости φ= 0.87;
Напряжение в стержне = F φ ·А;
F – нагрузка на стержень к
= –––––––––– = 11.6 кH см² [] = 16 кH см² ;
Из условия прочности подходит двутавр № 12 но т.к. диаметр колеса грузовой каретки 100 мм принимаем в качестве нижнего пояса двутавт № 14.
Двутавр = –––––––––––––––––––– ; [4]
Принимаем трубу 30 мм толщиной стрелы S = 3 мм площадью поперечного сечения А = 2.5 см² r = 1 см.
Для растянутых стержней:
= ––– = ––––––– = 11.5 кH см² 16 кH см² ;
Условие прочности удовлетворено.
Труба 30 · 3 – Ст 3 ГОСТ8734-78-г.
Принимаем трубу 60 мм S = 6 мм А = 10.1 см² r = 3.7 см.;
Гибкость λ = 92 3.7 = 25;
= ––– = ––––––– = 8.7 кH см² [] = 16 кH см² ;
Труба 60· 6– Ст 3 ГОСТ 8734-78-г.
Принимаем трубу 12 мм S = 2 мм А = 0.2 мм А = 0.6 см²;
= –––––– = 15.1 кH см² [] = 16 кH см² ;
Труба 12 · 2– Ст 3 ГОСТ 8732-78-г.;
Принимаем трубу 20 мм S = 2.5 мм А = 1.4 см² r = 0.6 см.
λ = 300.6 = 50 φ= 0.89;
= –––––– = 11.1 кH см² 16 кH см² ;
Труба 20 · 2.5– Ст 3 ГОСТ 8732-78-г.
Принимаем трубу 60 мм S = 6 мм А = 101 см r = 1.92 см.
λ = 2101.92 = 109 φ= 0.53;
= –––––– = 14.4 кH см² 16 кH см² ;
Труба 60 · 6 – Ст 3 ГОСТ 8734 -78-г.
Принимаем трубу 60 мм S = 5 мм А = 86 см² r = 2.0 см.
λ = 1502 = 75 φ= 0.84;
= –––––– = 10.5 кH см² 16 кH см² ;
Труба 60 · 5– Ст 3 ГОСТ 8734-78-г.
Усилие в растяжке от веса поднимаемого груза и собственной массы металлоконструкции Sp = 180.6 кH.
Выбираем канат ЛК-Р 6 19 + 1о.с. диаметром 21 мм.
Разрывное усилие Sразр = 194.5 кH.
1.1.Расчет массы металлоконструкции стрелы
Масса 1м трубы в кг м = 0.02466 S(Д - S);
S – толщина стенки трубы мм.;
Д – диаметр трубы мм;
Для определения массы стрелы составляем таблицу:
Определение массы стрелы
Общая масса металлоконструкции 397.8 400 кг.;
Крюковая подвеска 364 кг.;
С учетом канатных блоков и роликов принимаем массу стрелы 450 кг.
1.2. Расчет сварных швов
Соединение раскосов с нижним поясом.
Напряжение для шва на растяжение :
F = 28.8 кH = 28.810³H;
[p] – допускаемое напряжение на растяжении мПа.;
[p] = 0.9[p] = 0.9 160 = 144 мПа:
[p]o - допускаемое напряжение для основного материала конструкции мПа;
p = –––––––––– = 68 мПа [p] = 144 мПа;
Для сжатых стержней:
с = ––––– = [с]; [3]
[с] – допускаемое напряжение на сжатие для шва мПа;
[с] = [р] = 160 мПа;
с = –––––––––– = 68 мПа [с] = 160 мПа;
Условия прочности для сварных швов работающих на растяжение и сжатие выполнено.
Cоединение растяжки с верхним поясом.
Крепление растяжки к стреле осуществляется за оба верхних пояса.
Усилие в каждом канате Sp = 90 кH = 30 10³
Принимаем длину сварного шва = 200 мм.;
катет шва к = 7 мм.;
Проверку сварного шва производим как работающего на срез.
c = Sp 0.7 к = [c];
c – допускаемое напряжение на срез для шва мПа.;
[c] = 0.6 [p]. = 96 мПа;
c = 90 · 10³ 0.7 · 7 · 200 = 80 мПа [c] = 96 мПа;
Условие прочности выполнено.
1.3. Расчет шарнирных соединений
Диаметр оси в соединении стрелы с башней;
P – поперечная сила действующая на ось H
[c] – допускаемое напряжение на срез мПа;
[c] = 0.25 · 225 = 60 мПа
d = 1.13 √(179 · 10³) 60 = 62 мм.;
Принимаем d = 65 мм.
Проведем проверку прочности оси на стяжке
h – длина наиболее сжимаемой части мм;
[см] – допускаемое напряжение на стяжке для соединения мПа;
[см] = 0.8 · 225 = 180 мПа;
см = ––––––––– = 37 мПа [см] = 180 мПа;
Диаметр болта в соединении оттяжки со стрелой:
Р = 90 кН = 90 · 10³Н;
d = 1.13 √(90 · 10³) 60 = 45 мм.;
Принимаем d = 46 мм.
Проведем проверку прочности на сжатие;
см = ––––––––– = 130 мПа 180 мПа;
Диаметр болта для крепления грузового каната;
d = 1.13 √18800 60 = 20 мм.;
Принимаем болт d = 22 мм;
см = ––––––––– = 170 мПа [см] 180 мПа;
1.4. Определение прогиба стрелы
М – эпюра моментов от веса груза;
М1 – эпюра моментов от единичной силы;
Е = 0.2 10 мПа – модуль упругости стали;
Jх – момент инерции сечения стрелы м ;
S – площадь эпюры моментов М кН м ²;
Δ – ордината соответствующая центру тяжести эпюры М у эпюры М1 м ²;
Y = 1 Е Jх (45 3.68 1.2+453.681.2) = 199 кН м4 Е Jх;
2 ; Jх = 0.08 cм 4860 ; Jх = 37.5 cм
Определяем положение центра тяжести сечения. Статический момент относительно оси Х2
А – площади элементов сечения см²;
У – ордината элементов относительно оси Х2 см;
Sх = 10.1 20 + 10.1 20+0.6 20 – 17.8 20 = 60 cм ³;
Общая площадь сечения:
А = А = 10.1+10.1 + 0.6+17.8+2.5+2.5=44 cм ²;
Ордината центра тяжести:
Ух = (37.5+10.1 18.6²)2 + 0.08+0.618.6² +(2.6+2.51.4²)2+436+17.821.4²=15875 cм4;
У= –––––––––––– = 0.1 м;
2. Расчет жесткой оттяжки
В качестве жесткой оттяжки принимаем сварную конструкцию из четырех труб квадратного сечения.
Нагрузка на каждую оттяжку составляет 41 кН. Нагрузка на каждую трубу
В целях унификации конструкции крана принимаем трубу 60 мм. толщиной стенки S = 5 мм. площадью сечения А = 8.6 cм2 радиусом инерции r = 2.0 cм.
Гибкость каждой трубы:
l = 245 см. – длина участка трубы между узлами.
Коэффициент снижения напряжений
= Rφ·A = 10.30.45·8.6 = 3 кНсм2 [] = 16 кНсм2;
[] – допускаемое напряжение для материала трубы.
3. Подбор размеров поворотной платформы
Для передачи нагрузки от поворотной части платформы на неповоротную на проектируемом кране устанавливаем нормализованное роликовое опорно-поворотное устройство.
Опорно-поворотное устройство состоит из внутреннего кольца верхнего и нижнего наружных колец и роликов. Внутреннее кольцо имеет зубчатый венец с которым входит в зацепление выходная инерция механизма поворота.
Внутреннее кольцо крепим на ходовой (неповоротной) раме крана а наружные к поворотной. Кольца крепим к ходовой и поворотной рамам болтами. При эксплуатации крана необходимо следить за затяжкой болтов.
Ролики расположенные между кольцами опорно-поворотного устройства имеют взаимно перпендикулярные оси и воспринимают нагрузки действующие вниз а так же удерживают поворотную раму от опрокидывания.
Периодическая смазка опорно-поворотного устройства производится спринцеванием через пресс-масленки расположенные в верхнем наружном кольце.
Выбор опорно-поворотного устройства производим по вертикальной нагрузке составляющей 121 кН.
Принимаем опорно-поворотное устройство наружным диаметром Д = 2700мм.
Выбор роликового опорно-поворотного устройства обусловлен большой эксплуатационной надежностью долговечностью равномерностью передаваемой нагрузки и по сравнению с другими устройствами большей грузоподъемностью
(т.е. меньшей массой и габаритами) и меньшей трудоемкостью технического обслуживания.
3.1. Расчет металлоконструкции поворотной
Металлоконструкция поворотной платформы представляет собой плоское основание на котором монтируется пространственная конструкция из труб для крепления монтажного винта жестких оттяжек и противовеса.
Gк - вес стрелы башни и размещенных на них механизмов;
Gn = 78.5 кН – вес противовеса;
Gм = 7.8 кН – вес механизмов размещенных на поворотной платформе;
Наибольшие нагрузки будут возникать в стержне ВК для их определения рассмотрим узел В.
Запишем уравнение равновесия сил в проекции на ось У;
Fвк ·cos 25° - Rжо· sin 55° - Gn = 0
Подставляя значения и решая уравнение получим:
Так как общая нагрузка воспринимается двумя стержнями то для каждого:
Fвк = 1612 = 80.5 кН;
Изгибающий момент на основание поворотной платформы от суммы внешних нагрузок.
При работе элементов металлоконструкции на изгиб условие прочности:
W – момент сопротивления см3;
[u] – допустимое напряжение элемента при изгибе мПа;
[u] = 1.2 ти = 1.2 225 = 270 мПа;
В качестве основания поворотной платформы принимаем четыре швеллера №8.
u = 114004152.2 = 19 кНcм2 27 кНcм2;
Подбор труб для металлоконструкции производим по максимальному сжимающему усилию 80.5 кН.
Принимаем трубу 60 мм. с толщиной стенки S = 6 мм радиусом инерции
r = 1.9 cм площадью A = 10.1 cм2.
Действительная гибкость:
Коэффициент уменьшения допускаемых напряжений:
Проверим правильность подбора сечения по устойчивости:
= F φA = 80.5 0.8610.1 = 9.3 кН cм2 16 кНcм2;
Условие устойчивости выполнено.
3.2. Подвеска противовеса
В качестве противовеса приняты два груза массой 4 тонны каждый. Противовес крепится к задней части поворотной платформы с помощью четырех проушин.
Нагрузка на каждую проушину:
Принимаем длину сварного шва l = 94 мм толщину принимаем S = 10 мм.
Проверим сварной шов на растяжение:
= Р Sl = 19.6103 10 94 = 21мПа [p] = 144 мПа
Сварной шов условию прочности удовлетворяет.
Диаметр стержня входящего в отверстие проушин:
d = 1.13 √P c = 1.13 √19.6 103 60 = 20 мм;
4. Опорно – поворотное устройство и механизм
Принимаем опорно-поворотное устройство наружным диаметром Д = 1000 мм.
4.1. Расчет механизма поворота
Момент сопротивления вращению опорного круга.
025 Мхк +0.05Ркр·Д кр
Ркр – суммарная вертикальная нагрузка на опорный круг тс;
Д кр – диаметр опорного круга м;
Мхк – угол наклона к горизонтали сил действующих на ролики опорного круга град.;
Мхк – момент действующий на опорный круг в плоскости подвеса стрелы;
Мхк = 14тсм = 140 кНм;
Мтр = = 1.4 тсм = 14 кНм;
Маховой момент крана при положении тележки с грузом на наибольшем вылете:
GД2кр = 4 (2500 102+170102+1274222+80001.62);
GД2кр = 1182832 кгсм2 =11.6 кНм2;
Gгр - масса груза кг.;
Gт- масса грузовой тележки кг.;
G – масса металлоконструкции крана кг.;
L – расстояние от оси вращения крана до центра тяжести металлоконструкции м;
Gn- масса противовеса кг.;
Ln- расстояние от оси вращения крана до центра тяжести противовеса м;
Мu = –––––––––––– = 946 кгс м = 9.3 кН м;
nкр – частота вращения крана мин;
tn = 5 с время пуска механизма поворота;
Суммарный пусковой момент:
М1 = 1400 + 1.1 946 = 2141 кгс м = 21 кН м;
Необходимая поисковая мощность двигателя:
Nп = –––––––––– = 5.0 кВт;
= 0.75 – КПД механизма поворота;
Принятая продолжительность включения двигателя при заданном легком режиме работы согласно ПВ = 15 %;
Необходимая поворотная мощность двигателя при среднем коэффициенте пусковой перегрузки
Nк = Nп ср = 5.0 1.5 = 3.3 кВт;
Мощность двигателя при установившемся движении механизма;
Ny = –––––––––– = 2.9 кВт ;
Исходя из мощности Nк в рассчитываемом башенном кране устанавливаем двигатель типа МТF 111 – 6.
Мощность двигателя Ng = 4.5 кВт при ПВ = 15 %;
Чистота вращения ng = 850 мин -1;
Маховой момент ротора GД р2 = 0.20 кгс м2;
Наибольший (предельный) момент Mma
Маховой момент крана при положении тележки с грузом на наибольшем вылете подсчитанный выше:
GДкр2 = 1182832 кгс м2;
Этот момент приведенный к валу двигателя:
GД2г = GДкр2 nкр2ng2 = 1182832 1.52 8502 =3.7 кгс м2 =36.3 Н м2;
Принятый диаметр тормозного шкива:
Маховой момент муфты:
Общий маховой момент механизма:
GДо2 = (GДр2 + GДт2 ) 1.2 +GДг2;
GДо2 = (0.202+0.52) 1.2+3.72 = 4.5 кгс м2 = 44.1 H м2;
Момент сил инерции при положении тележки на наибольшем вылете:
Mu= 975 Ng n g - 975 Ny n g = 975 (4.5850) – 975(2.9850);
Мu = 1.8 кгс м =17.7 H м;
Наибольшее время пуска при положении тележки на наибольшем вылете:
tn = 4.5 850 375 1.8 = 5.6 c
Допускается превышение номинального времени пуска в пределах 20 %.
Передаточное число механизма.
Необходимое передаточное число при частоте вращения крана nкр = 1.5 мин -1;
В рассчитываемом механизме принимаем трехступенчатую передачу с передаточными числами:
Где U1 - червячная передача U2 U3 - передачи цилиндрически зубчатыми колесами.
4.2. Определение расчетных нагрузок деталей механизма поворота
За расчетный режим работы механизма поворота принят - легкий.
Расчет производим по двум случаям нагрузки:
рабочей (первый расчетный случай);
предельной (второй расчетный случай);
При расчете деталей на усталостную прочность при изгибе по первому расчетному
случаю исходим из среднего пускового момента двигателя. Этот момент на первом
М1 = Мс+1.1 Мu GДг2 GДо2 ;
М1 = 3.3 + 1.1 1.8 3.74.5 = 4.9 кгс м = 48.3 Н м;
М1 – рабочий момент кгс м;
Мu – момент сил инерции приведенный к валу редуктора кгс м;
GДг2 GДо2 - маховые моменты подсчитанные выше.
Маховой момент на втором валу редуктора:
М1 = 4.9 20 0.75 = 73.5 кгс м = 721.0 Н м;
U1 – передаточное число червячной передачи ;
– КПД червячной передачи;
Момент на третьем валу:
М3 = М2 U2 2 = 73.5 4.7 0.95 = 328.2 кгс м = 3219.4 Н м;
U1 1 – передаточное число и КПД цилиндрической передачи;
Расчет валов на кручение и проверку на статическую прочность на изгиб и кручение для первого расчетного случая производим исходя из наибольшего пускового момента двигателя
Mu = 8.7 – 3.3 = 5.4 кгс м =53.0 Н м;
Расчетный момент на первом валу редуктора при проверке на усталостную прочность:
М1 = Мс+1.1 Мu GДг2 GДо2;
М1 = 3.3+1.1 5.4 3.74.5 = 8.2 кгс м = 80.3 Н м;
Расчетный момент на первом валу при проверке на статическую прочность по первому расчетному случаю:
М1р = 8.2 1.2 = 9.8 кгс м = 96.5 Н м;
Кд=1.2 – динамический коэффициент.
Расчетный момент на втором валу при проверке на усталостную прочность:
М2 = 8.2 20 0.75 = 123 кгс м = 1206 Н м;
Расчетный момент на втором валу при проверке на статическую прочность:
М2р = 9.8 20 0.75 =147 кгс м = 1442 Н м;
Аналогично находим моменты на третьем валу
М2р = 701 кгс м = 6877 Н м;
М2р = 838 кгс м = 8221 Н м;
Первый вал редуктора.
Определение нагрузок при расчете вала на изгиб производим исходя из момента:
М2 = 7350 кгссм = 721 Н ·м - действующего на червячном колесе при среднем пусковом моменте двигателя.
Основная нагрузка на вал при диаметре колеса:
Р = 2М2 d2 = 2 ·7350 32.0 = 459 кгс = 4503 Н;
Принятый угол подъема витков червяка λ = 11°.
Окружное усилие на червяке
Po = 459 tg (11° + 6°) = 140 кгс = Н;
ρ = 6° - угол трения;
Радиальное усилие на червяке:
Рр = Р · tgα cos (λ+ρ) = 459 tg20° cos (11° + 6°) = 175 кгс = 1714 Н;
α – угол зацепления град.;
Нагрузки Р и Рр действуют в вертикальной плоскости. Опорные давления от этих нагрузок :
Нагрузка на опоры от силы Ро в горизонтальной плоскости:
RA = RB = Po 2 = 140 2 = 70 кгс = 686 Н;
Наибольшие изгибающие моменты в среднем сечении вала:
В вертикальной плоскости:
В горизонтальной плоскости:
Равнодействующий момент:
Мu = √( Мu)2 +√( Мu )2 = √22202+10502 = 2455 кгс·см = 240 Н·м;
Дополнительно к валу приложим крутящий момент:
Мкр = 820 кгс·см = 80 Н·м;
Мпр = √ Мu2 +α Мкр2 = √24552+(1·820)2 = 2588 кгс·см = 254 Н·м;
α – коэффициент учитывающий разницу в характере циклов изменения напряжения на изгиб и кручение;
Для предварительного выбора размеров вала допускаемые напряжения для материала сталь 45 с поверхностной закалкой до твердости НRС 45-50:
[u ] = -1 [n] · Ко = 26001.2·2.1 = 1032 кгс·см2 100 мПа;
[n] – допускаемый запас прочности для механизма поворота;
-1 – предел выносливости материала сердцевины вала;
Ко - коэффициент учитывающий концентрацию напряжений и влияние размеров рассчитываемого сечения на предел выносливости.
Необходимый диаметр вала в среднем сечении:
d = 3√10 Мпр [u] = 3√10·2588 1032 = 2.9 см 29 мм.;
Второй вал редуктора.
Аналогично расчету приведенному выше получаем:
Мпр = 7524 кгс·см = 738 Н· м;
В качестве материала вала принимаем углеродистую конструкционную сталь 45:
[u] = 1032 кгссм2 = 100 мПа;
Для вала работающего на сложное сопротивление необходимый диаметр в среднем сечении:
d = 3√10 Мпр [u] = 3√10·7524 1032 = 4.2 см 42 мм.;
Рассчитанный приведенный момент:
Мпр = 33272 кгс·см = 3264 Н·м
Материал вала – углеродистая конструкционная сталь 65 с пределом выносливости - -1 = 31 кгс мм2.
Допускаемые напряжения:
[u] = -1 [n] ·Ко = 3100 1.2·2.1 = 1230 кгссм2 = 120 мПа;
Необходимый диаметр вала в среднем сечении:
d = 3√10·33272 1230 = 6.4 см = 64 мм..
Для механизма поворота рассчитываемого крана выбираем колодочный тормоз. Необходимый момент тормоза определяем исходя из среднего замедления:
Необходимое время торможения при равнозамедленном движении груза:
tт = 60· Аср = п·L·n 30· Аср = п ·10·1.5 30·0.6 = 2.6
– линейная скорость конца стрелы м мин.;
Избыточный момент (момент сил инерции):
Мu = G ·Д2o ng 375·t = 4.5·850 375·2.6 = 3.9 кгс·м = 38.3 Н·м.;
Момент необходимый для поворота крана при установившемся движении приведенный к тормозному валу (первый вал редуктора) Мс = 3.3 кгс·м = 32.4 Н·м..
Необходимый тормозной момент:
Мт = Мu - Мc = 3.9 – 3.3 = 0.6 кгс·м = 5.9 Н·м;
Во избежание проскальзывания фрикциона при торможении тормозной момент приведенный к валу фрикциона не должен быть больше:
Мгр = 8820 кгс·см = 865 Н·м;
Тормозной момент приведенный у валу фрикциона:
Мт = Мт· U1·1 = 0.6·20·0.75 = 9 кгс·м = 88.3 Н·м;
U1 и 1 – КПД и передаточное число червячной передачи;
Запас по отношению к расчетному моменту фрикциона:
= Мф Мт = 865 88.3 = 9.7;
что вполне допустимо.
По рассчитанному тормозному моменту выбираем тормоз ТКТ 200 100 с тормозным моментом Мт = 40 Н·м..
Тип хода - гусеничный гусениц - две. Ходовая часть крана состоит из рамы с опорно-поворотным устройством и ходового механизма с приводами.
5.1. Ходовой механизм с приводами
Ходовая тележка включает две продольные балки с опорными катками (по пять катков с каждой стороны) левую и правую приводные звездочки 8 натяжные катки 9 поддерживающие катки 10 гусеничные цепи 11 механизмы натяжения гусеничных цепей и приводы.
Два параллельных ряда шарнирно соединенных между собой траков гусеничной цепи образуют дорожки качения опорных катков. Одновременно с помощью приводной звездочки гусеничная цепь передает тяговое усилие. Опорные и поддерживающие катки на бронзовых втулка вращаются на неподвижных осях закрепленных на балке. Натяжение катки на бронзовых втулка посажены на хвостовиках общей оси которая может перемещаться по направляющим балкам.
Приводные звездочки посажены на ведущих полуосях. После натяжения гусеничной цепи ось фиксируется распорной трубой и набором прокладок относительно специального упора расположенного внутри балки.
В целя повышения маневренности машины каждая ветвь гусеничной цепи снабжена отдельным приводом.
Каждый привод цепи включает редуктор типа РМ-650 с приводным электродвигателем 13 (марки 4А250М4УЗ мощностью - 90 кВт) и две зубчатые пары 15 16 (выходная пара сдвоенная). Электродвигатель тормоз и зубчатые пары закрываются кожухами. Электродвигатель с редуктором соединяются посредством кулачковой муфты. В приводе применен тормоз ТКТ-300.
Общее передаточное число трансмиссии гусеничного привода составляет 36225.
5.2. Тяговый расчет механизма передвижения крана
Условие передвижения крана:
где Тс max максимальная сила тяги
Wn сопротивление передвижению
где G сила тяжести = 150т =1500 кН
Vx = 5 м мин - скорость крана = 008 мс
tр = 4с время разгона
Wпод - сопротивление подъему
где α = 5° угол подъема
Wk сопротивление качению по грунту
где к = 15 коэффициент конструкции гусеницы
п = 2 число гусениц;
b = 1 м ширина гусеницы
L = 35 длина гусеницы
Рф фактическое давление на грунт
h глубина продавливания грунта гусеницами
Ро коэффициент сопротивления грунта =13
D = 096 м диаметр колеса
Тяговое условие выполняется.
Максимальная мощность привода хода:
Для обеспечения мощности выбираем 2 двигателя марки 4А250М4УЗ
8.Заключение.doc
Малогабаритный башенный кран более прост в управлении и не требует отдельной штатной единицы - крановщик – водитель. Это в свою очередь позволит сэкономить на затраты по заработной плате.
Механизмы автомобильного крана рассчитаны на грузоподъемность до 2.5 тонн однако ввиду его небольшой грузовой устойчивости более 10 м. на минимальном вылете стрелы не рекомендуется использовать его для подъема грузов более 1.5 т. При необходимости строительства коттеджа высотой 14 метров автомобильному крану приходится удлинять стрелу не менее чем до 20 метров. При этом грузоподъемность падает до 15 тонн у башенного крана грузоподъемность не меняется в зависимости от вылета стрелы и остается постоянной 2 тонны что вполне хватается для подъема любых строительных элементов.
У гидравлических стреловых самоходных кранов типа К – 35715 КС- 3575 А удельные энергозатраты на подъем 1тонны почти в два раза выше чем у бешенного малогабаритного крана использующего для подъеме электропривод.
Помимо разницы в цене кранов автомобильного и проектируемого башенного малогабаритного крана которая составляет 43236 руб. в пользу проектируемого произведенный выше расчет эксплуатационных затрат которые составляют 42303 руб. говорит о том что они полностью окупятся.
Таким образом мы убедились что для малоэтажного строительства и строительства коттеджей экономически целесообразно применять малогабаритный башенный кран грузоподъемностью 2 тонны.
7. Экономический раздел.doc
1. Технико-экономические показатели рентабельности
производства крана на гусенечном ходу в условиях
серийного производства
Определение себестоимости в условиях серийного производства.
Планируемая годовая программ выпуска кранов на гусенечном ходу 60 штук в производственных условиях предприятия таким образом месячная программа составляет 5 штук. Себестоимость проектируемого крана определим по формуле:
С = (М + Зпл. + Зпл. доп + Сн + Нр + Э) К; (1)
М - затраты ан материалы покупные и комплектующие изделия;
Зпл - затраты на заработную плату;
Зпл. доп - расходы на дополнительную затраты на заработную плату;
Сн - социальный налог с основной и дополнительной заработной
Нр - накладные расходы содержащие: транспортно – заготовительные расходы цеховые и общецеховые расходы расходы на содержание и эксплуатацию оборудования;
Э – затраты на энергоносители на технологические цели;
К – количество кранов выпускаемых в месяц;
Затраты на материалы покупные и комплектующие изделия.
М = М1 + М2 + М3 ; (1)
М1 – затраты на металлопрокат;
М2 – затраты на покупные и комплектующие изделия;
М3 – затраты на изготовление деталей и узлов на заводе;
2 Расчет затрат на металлопрокат
Общий вес металлоконструкции крана 12.5 тонн. Для изготовления опытного образца крана потребовалось с учетом неделовых расходов – 8% закупить 13.5 тонн проката. Однако при серийном производстве отходы металла уменьшатся в 4 раза благодаря более рациональному использованию и составляет примерно 2%. Тогда требуется закупить на один кран 12.75 тонн. Средняя цена одной тонны проката на 1 марта 2009 года составляет при оптовой закупке учитывая скидку 10% около 8000 рубт.:
М1 = 12.75 8000 = 102000 руб.;
2.2. Затраты на покупные и комплектующие изделия
Эта величина практически не изменяется как при изготовлении опытного образца и для всех механизмов может быть рассчитана по формуле:
М2 = Рз + Мпг + Мп + М ив + Мгс + Мки ;
Рз - стоимость рамы стрелового крана на базе ЭРГ-250 после капитального ремонта - 25700 руб.;
Мпг - стоимость механизма подъема груза – 7220 руб.;
Мп -стоимость механизма поворота - 4860 руб.;
М ив - стоимость механизма изменения вылета - 4140 руб.;
Мгс – стоимость гидросистемы – 5785 руб.;
Мки - стоимость комплектующих изделий 5265 руб.;
М2 = 25700 + 7220 + 4860 + 4140 + 5785 + 5265 = 52970 руб.;
Затраты на изготовление деталей и узлов на заводе
При изготовлении опытного образца затраты составили – 5150 руб. Учитывая чти при серийном производстве эти затраты уменьшаются согласно заводского норматива на 10% получим величину затрат 4635 руб.
Таким образом получим затраты на материалы покупные и комплектующие изделия:
М = 102000 + 52970 + 4635 = 159605 руб.;
Расчет затрат на заработную плату.
Для изготовления крана принимаем следующий состав ИТР и производственных рабочих:
- 2 инженера технолога для сопровождения производства с заработной платой 5900 руб.;
Производственные рабочие:
- 2 токаря с заработной платой 3000 руб.;
- 1 фрезеровщик с заработной платой 3500 руб.;
- 2 формовщика с заработной платой 3800 руб.;
- 5 сварщиков с заработной платой 3100 руб.;
- 4 слесаря с работной платой 2500 руб.;
- 2 наладчика гидросистемы 3300 руб.;
- сборщик электрооборудования 4000 руб.;
Итого: 2 человека ИТР и 17 человек рабочих. Месячные расходы на заработную плату составляют: 65000 руб.;
Зпл = 11800 + 53200 = 65000 руб. (3);
Расчет дополнительной заработной платы.
Зпл. доп – составляет 15% от основной заработной платы:
Зпл. доп = 65000 15 % = 9750 руб.; (4);
Единый социальный налог.
Сн – составляет 26 % от основной и дополнительной заработной платы;
Сн доп.ЗП = 2535 руб.;
Сн осн.ЗП = 16900 руб.;
Сн = 2535 + 16900 = 19435 руб.;
3.1. Затраты на изготовление опытного образца
При расчете учтем следующие статьи затрат:
Статьи затрат на изготовление опытного образца
Наименование статей затрат
б) гусеничная тележка ЭРГ-250
Затраты на покупные и комплектующие изделия:
а) механизм подъема груза:
б) механизм поворота:
в) механизм изменения вылета:
г) электрооборудование:
3.2. Затраты на заработную плату производственных рабочих
Для изготовления комплектующих изделий и сборки крана необходимо следующее количество производственных рабочих: 2 токаря 1 фрезеровщик 4 сварщика 2 слесаря сборщика 2 наладчика 1 формовщик - литейщик всего 12 человек. Принимаем срок выполнения работы 1 месяц. Для упрощения расчетов принимаем среднюю заработную плату 3000 рублей. Дополнительная заработная плата составляет 15% от среднемесячной заработной платы. Учитывая что социальный налог составляет 26% получим затраты на заработную плату производственных рабочих:
Ппр = (3000 + 450 + 897)121 = 52164 руб.;
Накладные расходы включающие в себя: расходы на подготовку и освоение производства; топливо и электроэнергию; на технологические цели; износ инструмента и приспособлений; содержание оборудования ; транспортные расходы на перемещение сырья и материалов; цеховые и общезаводские расходы внепроизводственные коммерческие расходы; все это составляет - 500% от расходов на заработную плату производственных рабочих таким образом получаем:
3.3. Статьи затрат производственных расходов
Проанализировав затраты на изготовление опытного образца и затраты на заработную плату производственных рабочих можем свезти в таблицу статьи затрат производственных расходов что позволит нам произвести подсчет общей себестоимости крана.
Общие производственные расходы
Механизм подъема груза
Механизм изменения вылета
Заработная плата производственных рабочих
3.4. Расчет затрат на энергоносители
Расход электроэнергии от сварочных работ составит - 5600 кВтч. Время работы 8- ми сварочных аппаратов средней мощностью - 14 кВт каждый с учетом технологических простоев составляет - 400 часов. Примем затраты на электроэнергию от ручных электрических машин - 400 кВтч. Освещая цеха люминесцентными лампами в среднем в месяц - 300 кВтч. Станки затрачивают на изготовление деталей - 200 кВтч. Сжатый воздух для технологических целей от компрессора – 150 кВтч. Таким образом не сложно подсчитать общие затраты электроэнергии – 6650 кВтч. Стоимость одного киловатта для завода составит 1.68 руб. Получим затраты на электроэнергию:
Э = 6650 168 = 11172 руб.;
3.5. Накладные расходы
Из произведенных выше подсчетов можем рассчитать накладные расходы по формуле:
Нр = (Зпл + Зпл. доп + Сн) 5;
Нр = (65000 + 9750 + 19435) 5 = 470925 руб.;
Исходя из всех произведенных выше расчетов получаем производственную себестоимость одного крана:
С = (159605 + 65000 + 9750 + 19435 + 470925 + 11172) 5 = 147177 руб.;
3.6. Полная себестоимость крана. Цена проектируемого крана
Затраты на проектирование крана составили П = 559469 руб. Тогда на один кран приходится 9324 руб. Подсчитаем полную себестоимость проектируемого крана :
Спол = 147177 + 9325 = 156502 руб.;
Отпускная цена крана с учетом НДС это 20% от полной себестоимости равна:
Заказчику малогабаритный башенный кран с учетом генератора будет стоить:
Цотп = 187803 + 57581 = 245384 руб.;
4. Расчет эксплуатационных затрат
4.1. Технологическая себестоимость
При расчете экономической эффективности крана под эксплуатационными затратами понимается себестоимость транспортировки одной тонны груза. Так как большинство затрат по составляемым вариантам подъемно – транспортных средств остается без изменений то расчет эксплуатационных затрат ограничивается технологической себестоимостью.
Формула технологической себестоимости имеет вид:
С = Сз + Сэл. эн + Ср + Са + С всп; (1);
Сз – заработная плата транспортных рабочих включая дополнительную и отчисления на соцстрах руб.;
Сэл.эн. – затраты на электроэнергию;
Ср ем – затраты на текущий ремонт;
Са – амортизационные отчисления
Свсп – затраты на вспомогательные материалы;
Сз = к1 к2 Fэф ч тар N сп ; (2)
к1–коэффициент учитывающий дополнительную заработную плату равен 1.15;
к2–коэффициент учитывающий отчисления на социальное страхование равен 1.14;
Fэф - эффективный годовой фонд рабочего времени одного рабочего;
Fэф = d · s·tcм· (1 – W) (3)
d – количество рабочих дней в год – d = 250;
S – сменность работы машины S = 1;
tcм – продолжительность рабочей смены tсм = 8 часов;
W – потери рабочего времени на ремонт и простой под погрузкой и выгрузкой принимаем равный - 30 %;
Fэф = 250 ·8·1· (1 – 30100) = 1400 ч.;
чтар – часовая тарифная ставка рабочего руб.;
Nсп - численность рабочих;
Получим заработную плату транспортных рабочих (2);
Сз = 1.15 · 1.14·1400 · 8 · 2 = 29366 руб.;
Сэл.эн. - затраты на электроэнергию определяются по формуле:
Сэл.эн. = Ц Эл. эн. Nу w1 w2 Fд А; (4)
Ц Эл. эн. – тариф за 1 кВт · ч электроэнергии равен 1.68 руб.;
Nу - установочная мощность двигателей кВт в нашем случае 13.3 кВт;
w1 - коэффициент использования двигателя по времени 1.3;
w2 – коэффициент использования двигателя по мощности 1.3448; Fд – годовой действительный фонд работы машины 143 ч.;
А – количество установленных двигателей – 2 шт.;
Сэл.эн = 1.68 ·13.3· 1.3·1.3448·143·2 = 11172 кВт ;
R – категория ремонтной сложности – R = 2.3;
НR – норматив затрат на единицу ремонтной сложности равно 12;
Срем = 2.3 ·12 = 27.6;
Амортизационные отчисления определим по формуле:
Са = (Но · Кз ) 100 ; (6)
Но – общая норма амортизации 12.4 %;
Са = (12.4 · 5000) 100 = 620 ;
Затраты на вспомогательные материалы определяются но нормативам. При укрупненных расчетах принимаются в размере 10% от затрат на электроэнергию в нашем случае эта сумма составит С всп = 1117.2 руб.;
Произведя все необходимые расчеты элементов технологической себестоимости по проектируемому крану сведем в таблицу.
Расчет технологической себестоимости
заработная плата транспортных рабочих
стоимость потребляемой электроэнергии
затраты на текущий и средний ремонт на единицу ремонтной сложности
амортизационные отчисления
затраты на вспомогательные материалы
Полученные данные сведем в формулу (1) и получим технологическую себестоимость сумму эксплуатационных затрат:
С = 29366 + 11172 + 27.6 + 620 + 1117.2 = 42303 руб.;
Экономический эффект при внедрении проектируемого крана определяем как разницу в цене существующего автомобильного крана МАЗ - 3537 и проектируемого малогабаритного башенного крана:
Ээф = Цмаз – Цотп = 288620 – 245384 = 43236 руб.;
3. н. Исследовательский раздел.doc
В кранах с поворотной башней по сравнению с кранами с поворотной головкой масса высокорасположенных элементов меньше а следовательно и ниже расположен общий центр масс что способствует уменьшению общей массы крана повышению удобства его транспортирования и монтажа а также уменьшению раскачивания груза поскольку башня меньше деформируется. У такого крана трубчатая башня 1 крепится к поворотной платформе 2 с противовесами 8 и механизмами 9—11 платформа через опорно-поворотное устройство 3 роликового или шарикового типа опирается на неповоротную раму 5. К раме 5 присоединены поводковые размещенные диагонально под прямыми углами друг к другу двухшарнирные кронштейны 4 позволяющие крану передвигаться как по прямым так и по криволинейным путям. Неповоротная рама 5 через кронштейны 4 соединяется с ходовыми приводными и неприводными тележками б. В рабочем положении тележки 6 удерживаются тягами 7.
На поворотной платформе 2 установлен противовес и смонтированы стреловая и грузовая лебедки и механизмы вращения. К верхнему концу башни шарнирно прикреплены консоль-распорка 12 с направляющими блоками стрела 13 и кабина управления 14. Изменение вылета производится изменением наклона стрелы.
Рис.1. Схема монтажа и демонтажа крана
Стреловая лебедка на барабан которой наматывается хвостовая ветвь грузового полиспаста в направлении обратном направлению наматывания ветви стрелового полиспаста обеспечивает при изменении вылета перемещение грузового крюка приблизительно по горизонтали.
Платформу 1 и неповоротную раму 3 выполняют кольцевыми по контуру роликового или шарикового ОПУ. Для повышения жесткости рам и улучшения работы ОПУ они могут выполняться коническими сужающимися.
В транспортном положении кронштейны 2 вместе с тележками 4 поворачиваются вдоль продольной оси уменьшая этим ширину неповоротной части крана.
Монтаж и демонтаж башенных кранов с поворотной башней вращающейся на ОПУ осуществляются следующим образом. При демонтаже крана стрелу опустить в крайнее нижнее положение и разъединить стык между средней и крайней секциями а сами секции прикрепляют к башне. После этого разъединить стык крепления башни к основанию и опустить башню в горизонтальное положение. Тележку стрелоподъемным полиспастом приподнять и под нее подводят автомобильные колеса на специальной оси в таком виде переместить кран к новому месту установки. Монтаж производится в обратном порядке.
Для нашего крана характерно несимметричное расположение башни относительно основания. Башня размещена на стороне направленной к возводимому объекту а на противоположной стороне находится бетонный противовес. В кранах с горизонтальной стрелой в которых вылет изменяется передвижением каретки по стреле высота подъема на малых вылетах меньше той которую можно получить при подъемной стреле. Чтобы увеличить высоту подъема на малых вылетах (что важно при достройке высоких зданий) каретку закрепляют жестко на конце стрелы установленной под необходимым углом. Имеются краны в которых возможно и передвижение каретки с грузом по наклонной стреле. При такой схеме кран обычно работает при постоянном наклоне стрелы и маневренность его несколько снижается.
Кран выполнен с подращиваемой башней. Основанием крана является портал со свободным проемом с одной стороны. Башня состоящая из секций может вертикально перемещаться внутри портала при помощи монтажной лебедки установленной на портале. Для подращивания крана башню поднимают относительно портала и в образовавшийся зазор вводят новую секцию после чего башню опускают и производят ее стыковку с секцией. Так продолжается до получения нужной высоты крана. Прикрепление к возводимому объекту осуществляется также при помощи кронштейнов.
Увеличение высоты крана методом подращивания несколько проще чем методом наращивания но требует более мощной монтажной лебедки из-за необходимости подъема всей башни.
Для соединения секций между собой применяют быстро собираемые и разбираемые соединения. Соединительным элементом является палец соединяемый с трубами стоек башни пальцами закрепленными от сдвига скобами.
Монтаж представляет собой совокупность всех работ по установке и сборке машины на месте ее эксплуатации. Это относится к машинам перевозимым в разобранном виде. В состав монтажных работ входят организация монтажной площадки и обеспечение ее техническими средствами необходимыми для производства работ (домкратами мачтами сварочной аппаратурой и т. п.) выгрузка и хранение прибывающего и подлежащего монтажу оборудования проверка сборка и соединение отдельных частей оборудования на рабочем месте и приведение их в рабочее состояние испытание и сдача машин в эксплуатацию. В процессе проведения монтажных работ необходимо выполнять сборку а иногда и сварку металлических конструкций и их подъем (установку) в рабочее положение; установку и соединение механических узлов и их регулировку; прокладку проводов и соединение электрооборудования; монтаж трубопроводов гидро- и пневмооборудования и другие работы.
При монтаже для проведения подъемных работ в ряде случаев можно использовать подъемные механизмы самих монтируемых объектов (для башенных кранов). Правильность и качество проведенного монтажа характеризуется соответствием полученных (после монтажа) осевых и габаритных размеров проектным бесшумной работой соответствующих механизмов и отсутствием нагрева узлов трения выше допустимых норм нормальной работой силового оборудования и системы управления механизмами.
Для проведения монтажа допускаются лица не моложе 18 лет прошедшие курс обучения по соответствующей программе и аттестованные квалификационной комиссией с участием представителей Ростехнадзора. При допуске к работе им выдается производственная инструкция. Проверка знаний персонала проводится не реже одного раза в год. Ответственность за правильность проведения монтажных и последующих погрузочно-разгрузочных работ возлагается на представителя технической администрации данные о котором заносятся в паспорт машины.
6. Техника безопасности и охрана труда.doc
1.Защита окружающей среды при
конструкторской разработке башенного крана
Грузоподъемные машины как таковые не загрязняют окружающую среду. Непосредственное отношение к этому имеют машиностроительные предприятия на которых производятся данного вида машины. Эти предприятия имеют цеха по обработке различных металлов например такие как литейный цех кузнечно – прессовый и др. В процессе производства машин используется большое количество сварочных работ переработка неметаллических материалов лакокрасочные операции что пагубно влияет на окружающую среду.
Твердые отходы машиностроительного производства содержат амортизационный лом стружки и опилки металлов пластмасс и др. Количества амортизационного лома зависит от намеченного списания в лом изношенного оборудования и имущества а также от замены отдельных деталей в ППР.
Анализ состава загрязнения выбрасываемых в атмосферу машиностроительными предприятиями вредных веществ показывает что кроме основных примесей атмосферы пыль гарь в выбросах содержатся другие токсические вещества которые пагубно влияют на окружающую среду.
2. Опасные и вредные производственные факторы при эксплуатации грузоподъемных машин
Согласно ГОСТ 12.0.003-74 Опасные и вредные производственные факторы делят на физические химические биологические и психофизиологические.
Из числа опасных и вредных физических факторов при эксплуатации грузоподъемных машин выделяют:
движущиеся машины и механизмы;
незащищенные подвижные элементы механизмов;
разрушающиеся конструкции;
повышенный уровень шума на рабочем месте;
повышенное напряжение в электрической сети замыкание которой может произойти через тело человека;
отсутствие или недостаточность естественного освещения;
острые кромки заусенцы и шероховатость поверхностей изделий и оборудования;
расположение рабочего места на значительной высоте относительно поверхности земли (пола);
Химически опасные и вредные производственные факторы не связаны с работой грузоподъемных машин а определяются окружающими условиями в которых находится машина. Исключение составляют грузоподъемные машины с приводом от двигателя внутреннего сгорания.
Биологически опасные и вредные производственные факторы при эксплуатации грузоподъемных машин отсутствуют.
Психофизиологические опасные и вредные производственные факторы по характеру действия делят на физические и нервно-психологические перегрузки. Физические нагрузки делят на: статические и динамические; нервно – психологические: умственное перенапряжение перенапряжение анализаторов монотонность труда. Незащищенные движущиеся машины и механизмы:
поворотная платформа;
валы электродвигателей и редукторов;
зубчатые колеса при попадании в опасную зону работающего могут привести к травме или смертельному случаю;
Для исключения контакта человека с опасной зоной применяются оградительные средства защиты: кожухи щиты решетки сетки на жестком каркасе корпуса электродвигателей и редукторов а также предупреждающие и указывающие плакаты.
Повышенный уровень шума при работе зубчатых передач подшипников качения вращении неуравновешенных частей машины вызывает общее утомление приводит к ухудшению слуха ослабляет внимание замедляет психические реакции. Уменьшение шума достигается совершенствованием технологических процессов изготовления деталей своевременной заменой изношенных применение принудительной смазки балансировкой вращающихся элементов использованием звукоизолирующих кожухов экранов кабин. По ГОСТ 12.1.003-83 «Уровень звукового давления на рабочем месте при умеренно напряженном труде и легкой категории работ 70 дБА». [4]
Повышенное напряжение в электрической цепи замыкание которой может произойти через тело человека при случайном прикосновении к токоведущим частям машины неизолированному тоководу приводит к местным (электрические ожоги механические повреждения электроофтальмия) и общим электротравмам (электрическим ударам). Мерами защиты от поражения электрическим током являются: ограждение неизолированных токоведущих частей защитное заземление зануление двойная изоляция защитное отключение применение предупреждающих и запрещающих плакатов.
Недостаточная освещенность на рабочем месте приводит к ухудшению зрения снижению безопасности работ. При недостаточности естественного освещения применяются источники искусственного света: лампы прожектора специальные осветительные установки. По ГОСТ 24378-80Е [5] освещенность на погрузо-разгрузочных площадках в зоне работы крана и на грузозахватном устройстве на любом уровне его подъема и перемещение в горизонтальной плоскости должна быть не менее Ен = 10 лк от наружной осветительной установки. Освещенность от внешних осветительных установок 0.9 ·(Ен ·К) [К - коэффициент запаса].
Физические и нервно – психологические перегрузки приводят к быстрому утомлению ослаблению внимания замедлению реакций. Для уменьшения перегрузок необходимо: повышать комфортность мест операторов; применение вентиляции (кондиционирования). Освещенность на рабочих поверхностях пульта и рычагах управления должна быть на менее 20лк (ГОСТ 24378-80Е [5].
3. Правила Ростехнадзора
Грузоподъемные машины относятся к оборудованию повышенной опасности. Для обеспечения безопасных условий их эксплуатации установлен государственный технический надзор осуществляемый Ростехнадзором. Главными задачами Ростехнадзора являются контроль за выполнением установленных требований по безопасному ведению работ и проведением профилактических мер по предупреждению аварий и производственного травматизма а также обеспечение единства требований к мероприятиям по технике безопасности на предприятиях независимо от их территориального расположения и ведомственного подчинения.
При проектировании и эксплуатации грузоподъемных машин особое внимание обращается на повышение их надежности и соблюдение требований техники безопасности. Соблюдение норм и правил Ростехнадзора является обязательным при проектировании расчете и эксплуатации грузоподъемных машин.
В соответствие с правилами все вновь устанавливаемые грузоподъемные машины на которые распространяются эти правила а также съемные грузозахватные устройства до пуска в работу подлежат техническому освидетельствованию при проведении которого необходимо убедиться что машина находится в исправном состоянии обеспечивающем ее безопасную эксплуатацию. Различают полное и частичное освидетельствование. Полное техническое освидетельствование состоит из осмотра машины а также статического и динамического испытания под нагрузкой. При частичном техническом освидетельствовании производится только осмотр машины без испытания ее под нагрузкой.
Полному техническому освидетельствованию подвергаются грузоподъемные машины перед вводом их в работу (первичное техническое освидетельствование) и в процессе эксплуатации не реже одного раза в 3 года. Редко используемые краны должны подвергаться полному техническому освидетельствованию через каждые 5 лет. Первичное освидетельствование кранов транспортируемых с завода-изготовителя на место эксплуатации в собранном состоянии производится отделом технического контроля завода-изготовителя перед их отправкой. Грузоподъемные машины находящиеся в эксплуатации должны подвергаться техническому освидетельствованию через каждые 12 месяцев.
Контроль за содержанием и безопасной эксплуатацией грузоподъемных машин осуществляется инспекцией Ростехнадзора и инженером по техническому надзору назначаемым администрацией предприятия эксплуатирующего машины. Помимо инженерно-технического работника по надзору руководство предприятия назначает также ответственного за содержание грузоподъемных машин в исправном состоянии. В его подчинении находится персонал обслуживающий краны (за исключением стропальщиков).
Работы по закреплению грузов проводят стропальщики (такелажники зацепщики) прошедшие специальное обучение и аттестованные квалификационной комиссией.
В особо опасных случаях (работа под линией электропередачи работа у котлована или у траншеи подъем груза двумя кранами и т. п.) подъемно-транспортные операции могут производиться только под непосредственным руководством и наблюдением лица ответственного за безопасное перемещение грузов кранами.
4. Проверка устойчивости крана
Башенный кран является свободно стоящим краном устойчивость которого против опрокидывания обеспечивается только его собственным весом.
Грузовая устойчивость.
Рассматриваем положение когда груз находится на максимальном витке. Ветровую нагрузку принимаем способствующей опрокидыванию крана.
Коэффициент грузовой устойчивости.
К1 = МG - МUU – МВ МГР > = 1.15;
МГР = Gгр· а – момент создаваемый весом номинального груза относительно ребра опрокидывания кгс·м;
а – расстояние от плоскости проходящей через ребро опрокидывания до центра тяжести подвешенного максимально допустимого рабочего груза при установке крана на горизонтальной плоскости м.;
МG = G · с – момент создаваемый силой тяжести частей крана и противовеса относительно ребра опрокидывания кгс·м.;
с- расстояние от вертикальной плоскости проходящей через ребро опрокидывания до центра тяжести крана м.;
МВ – момент создаваемый ветровой нагрузкой рабочего состояния действующий на наветренную площадь крана и груза перпендикулярно ребру опрокидывания и параллельно плоскости на которой установлен кран кгс·м.;
МUU - суммарный момент сил инерции элементов крана и груза возникающих в процессе пуска и торможения механизмов крана и центробежной силы при вращении крана кгс·м.;
МГР = 2500·8 = 20000 кгс·м;
МG = Gп ·3.6+Gпл ·2.4+Gб ·1.4 - Gт ·0.1 - Gс·3.2;
МG = 8000·3.6+1800·2.4+664·1.4 - 160·0.1 - 450·3.2 = 32594 кгс ·м.;
Gп – масса противовеса кг.;
Gпл – масса поворотной и неподвижной платформы и механизмов размещенных на поворотной платформе кг.;
Gб – масса башни кг.;
Gт – масса механизма передвижения грузовой тележки кг.;
Gс – масса стрелы кг.;
Мв = W·d = 68.2·6 = 409 кгс ·м.;
W – сила давления ветра действующего перпендикулярно ребру опрокидывания и параллельно плоскости на которой установлен кран при давлении ветра рабочего состояния: g = 11 кгсм2.;
d – расстояние от плоскости проходящей через точки опорного контура до центра положения ветровой нагрузки м.;
Опрокидывающий момент от центробежной силы возникающей во время поворота крана с грузом:
Мц = F·H = 10 · Gгр·n2·L·H 900 – n2·H
Мц = 10·2500·1.52·10·12 900 – 1.52·12 = 7031 кгс·м.;
n – частота вращения стрелы мин.- 1;
L – вылет стрелы м.;
H – высота подъема груза м.;
Опрокидывающий момент от силы инерции поднимаемого (опускаемого груза)
Мuuгр = Gгр ··в t = 2500 ·0.33 ·8 3.3 = 2000 кгс ·м.;
- установившееся значение скорости поднимаемого (опускаемого) груза мc;
в=а-расстояние от плоскости проходящей через ребро опрокидывания до центра тяжести подвешенного максимально допустимого рабочего груза при установке крана на горизонтальной плоскости м.;
t - время разгона при торможении груза с;
Тогда коэффициент грузовой устойчивости:
К1 = 32594 – 7031 – 2000 – 409 20000 = 1.16;
По правилам Госгортехнадзора необходимо определить значение коэффициента грузовой устойчивости без учета дополнительных нагрузок:
К1 = МG МГР > = 1.4;
К1 =32594 20000 = 1.6 > 1.4;
Грузовая устойчивость крана обеспечена.
5. Собственная устойчивость.
При проверке собственной устойчивости рассматриваем кран при минимальном вылете и снятом грузе при ветровой нагрузке неработающего состояния действующей в сторону опрокидывания.
Коэффициент собственной устойчивости:
К2 = МG МB > = 1.15 ;
МB – момент ветровой нагрузки нерабочего состояния действующей на наветренную площадь перпендикулярно ребру опрокидывания и параллельно плоскости на которой установлен кран;
МG – момент создаваемый силой тяжести частей крана и противовеса
относительно ребра опрокидывания кгс·м.;
МG = Gс ·7.2 +Gт · 4.1 + Gб ·2.6 + Gпл ·1.6+Gп· 0.4;
МG = 450·7.2+160·4.1+664·2.6+1800·1.6+8000·0.4 = 11702 кгс·м;
МВ = WВ·d = 99·6 = 594 кгс ·м;
WВ – сила давления ветра действующего перпендикулярно ребру опрокидывания и параллельно плоскости на которой установлен кран при давлении ветра нерабочего состояния gвн = 45 кгс м2;
К2 = 11702 594 = 19.7 > 1.15;
Собственная устойчивость крана обеспечена.
Устойчивость крана при монтаже.
Перед началом монтажа крана его необходимо установить на выносные опоры.
При этом центр тяжести неподвижных частей крана G1 и центр тяжести поднимаемых частей G2 находятся внутри опорного контура что обеспечивает устойчивость крана при монтаже.
5. Технологический раздел.doc
1 Технологический процесс изготовления траверсы
Деталь «Траверса» располагается в закрылке в его передней точке крепления. Траверса соединяет сам закрылок с подвижной частью механизации – кареткой.
2. Выбор типа производства
Тип производства характеризуется коэффициентом закрепления операций КЗ.О..
Условно различают три основных типа производства: массовое серийное и единичное.
Приняты следующие коэффициенты серийности:
для массового производства - ;
для крупносерийного - ;
для среднесерийного - ;
для мелкосерийного - ;
На базовом предприятии в цехе 251 имеется 300 рабочих мест. Он изготавливает 1500 наименований деталей и на одну деталь в среднем приходится по 8 операций то есть
Таким образом производство является мелкосерийным.
Разработка маршрута механической обработки.
Эта задача так же как и проектирование маршрута для отдельной поверхности является многовариантной. Маршрут обработки детали представляет собой определенную последовательность выполнения операций. При установление общей последовательности выполнения операций необходимо:
Определить подготовительные базы.
Установить поверхности в последовательности обрабатываемой их точности.
Последняя обрабатывается наиболее точная поверхность.
Не совмещать черновые и чистовые переходы.
Если деталь подвергается термообработки то маршрут разбивается на 2 части: до термообработки и после так как возможны деформации.
Для деталей массового производства необходимо чтобы длительность операций была равна или кратна такту выпуска.
Выбранный маршрут подвергают экономическим расчетам.
При разработки операций решаются две основные задачи.
Обеспечение точности и качества обрабатываемой поверхности. 2.Получение высокой производительности (за счет уменьшения штучного времени)
Маршрут обработки траверсы
0. Заготовительная (заготовку получить).
0. Расточная (Зацентровка с двух сторон по разметке с переустановкой заготовки).
5. Продольно-строгальная (точить поверхности 1).
0. Продольно-строгальная (точить поверхности 1).
5. Токарная(точить поверхность с 1 по 6).
5. Сверлильная (сверлим отверстие под крюк)
0. Токарно-карусельная.
Расчет операционных припусков и межоперационных размеров
расчетно — аналитическим методом.
Этот метод заключается в том что промежуточный припуск на каждом технологическом переходе должен быть таким чтобы при его снятие устранялись погрешности обработки и дефекты поверхностного слоя полученные на предшествующих переходах а также для исключения погрешности установки заготовки.
Определение минимального припуска для поверхности вращения.
Rzi-1 высота неровностей профиля на предыдущем переходе.
Hi-1 глубина дефектного слоя возникающего на предшествующем
- суммарное отклонение расположения поверхности на
предшествующем переходе рассчитывается по формуле:
k- отклонение оси детали от прямолинейности.
- длина заготовки до зажима.
Х - длина обрабатываемой части заготовки.
Максимальный припуск на обработку поверхности вала рассчитывается по формуле:
Z max =2Zmin+Tdi-1+Tdi
Tdi-1 - допуск размеров на предшествующем переходе
Tdi - допуск размеров на выполнимом переходе.
Минимальный диаметр с учетом припуска рассчитывается по формуле:
- минимальный диаметр полученный на выполняемом переходе.
Максимальный диаметр с учетом припуска рассчитывается по
3. Выбор метода получения заготовки и его обоснование
Расчет произведен по методике изложенной в [9 120].
Рассмотрим два варианта изготовления данной детали: кованая штамповка и поковка. Так как у нас производство мелкосерийное то выбираем метод свободной ковки.
Коэффициент использования материала:
Трудоемкость изготовления детали для нового варианта:
- трудоемкость по базовому варианту мин;
- масса заготовки кг при новом и базовом варианте.
Снижение материалоемкости кг:
- годовой объем выпуска детали шт;
Себестоимость изготовления детали:
Стоимость основных материалов:
- масса заготовки по варианту ;
- стоимость материала заготовки ;
- коэффициент транспортных расходов ( для черных металлов и для других);
- масса отходов на одну деталь ;
Заработная плата основных рабочих:
- коэффициент выполнения норм;
- коэффициент учитывающий премирование;
- коэффициент отчисления по социальному страхованию;
- штучное время на операцию;
- часовая тарифная ставка ;
Экономия по себестоимости:
Вывод: проведя данный анализ можно сделать вывод что штампованная заготовка по экономическим затратам менее выгодна заготовки полученной методом свободной ковки.
Расчет режимов резания выбор оборудования и режущего инструмента.
Операция 010 Расточная
Скорость резания [м мин] при сверлении:
Т = 25 [мин] - среднее значение стойкости инструмента (том 2 стр. 277).
t = 80 [мм] - глубина резания
s = 02 [мм] - подача (том 2 стр. 277 т - 13)
Cv = 70 - коэффициент скорости (том 2 стр. 278 т - 17)
m = 055 - показатель степени (том 2 стр. 278 т - 17)
х = 015 - показатель степени (том 2 стр. 278 т - 17)
у = 02 - показатель степени (том 2 стр. 278 т - 17)
kv- поправочный коэффициент рассчитывается по формуле:
Kv = KmvКт Kuv = 131 09 = 117.
Kmv = 13 - коэффициент учитывающий влияние материала заготовки
Kuv =1 - коэффициент учитывающий влияние материала инструмента
Knv = 09 - коэффициент состояния поверхности.
Крутящий момент Нм и осевую стлу Н рассчитываем по формулам
Мкр=10СмDqSyKp=100.03451620.215=120 Н*м
Po=10CpDqSyKp=2000 Н.
Глубина резания t=0.5D=0516=8 мм.
Подача: При сверлении выбираем максимально допустимую по прочности сверла подачу S=0.2 ммоб
Выбор станка: Станок горизонтально расточной 2М615.
Операция 015 Продольно-строгальная
При всех видах строгания глубину резания назначают так же как и при точении.
Подача: При обдирочном и черновом строгании подачу S ммдв.ход выбирают максимальной из допустимых значений по табл.1113 (том 2 стр.266) в соответствии с глубиной резания сечением державки прочностью пластинки.
Скорость резания: При строгании плоскостей проходными резцами скорость резания рассчитывается по формулам для точения с введением дополнительного поправочного коэффициента Kyu учитывающего ударную нагрузку.
T = 45 [мин] - среднее значение стойкости инструмента (том 2 стр. 268).
t = 25 [мм] - глубина резания
s = 09 [мм] - подача (том 2 стр. 268 т - 13)
Cv = 420 - коэффициент скорости (том 2 стр. 269 т - 17)
m = 02 - показатель степени (том 2 стр. 269 т - 17)
х = 015 - показатель степени (том 2 стр. 269 т - 17)
у = 02 - показатель степени (том 2 стр. 269 т - 17)
Kv- поправочный коэффициент рассчитывается по формуле:
Ky=Kmv-Knv-Kuv = 13 -1-09 = 117.
Kиv = 13 - коэффициент учитывающий ударную нагрузку.
Силу резания принято раскладывать на составляющие силы направленные по осям координат станка: тангенсальную Pz радиальную Ру осевую Рх. При наружном продольном точение эти силы рассчитываются по формуле:
Постоянная Ср и показатели степени для конкретных условий обработки для каждой из составляющих сил резания берем из (том 2 стр. 273 т-22).
Поправочные коэффициенты учитывающие влияние геометрические параметры режущей части инструмента на составляющие сил резания берем из ( том 2 стр. 275 т - 23) для углов
φ° = 45° γ° =0° λ0 = 0° г = 2 [мм].
Pz =103008.510.30.7589.6-0.151.1=5722.48[H]
Ру = 102438.50.90.30.689.6-0.31.1=2337.33[H]
Рх =103398.510.30.589.6-0.41.1=2337.33[H]
Станок: продольно-строгальный 7110
Операция 020 Продольно-строгальная
Скорость резания: При строгании плоскостей проходными резцами скорость резания рассчитывается по формулам для точения с введением дополнительного поправочного коэффициента Ky учитывающего ударную нагрузку.
Kиv = 13-коэффициент учитывающий ударную нагрузку (том 2 стр. 263 т-1)
Операция О25 Токарная
На данной операции мною обрабатывается шесть поверхностей.
Глубина резания t: при черновом точении и отсутствии ограничений по мощности оборудования жёсткости системы СПИД принимаем равной припуску на обработку; при чистовом точении припуск срезается за два прохода и более. На каждом последующем проходе назначаю меньшую глубину резания чем на предшествующем.
Подача s: Подачу назначаем в соответствии с табл.1112 том2 стр.266.
Скорость резания [м мин] при наружном продольном точение рассчитываем по эмпирической формуле:
-обработана пов-ть№1 при первом проходе.
t = 10 [мм] - глубина резания
s = 07 [мм] - подача (том 2 стр. 268 т - 13)
Kmv = 13 - коэффициент учитывающий влияние материала заготовки (том 2 стр. 263 т - 1)
Kuv =1 - коэффициент учитывающий влияние материала инструмента ( том 2 стр. 263 т - 6)
Knv = 09 - коэффициент состояния поверхности ( том 2 стр. 263 т -5).
Число оборотов n [обмин] заготовки определяется по формуле:
D = 105 [мм] - диаметр заготовки
V = 07 [ммин] - скорость резания.
Стандартное значение nст=100 [обмин].
Pz =103841010.70.7507-0.151.1=4468[H]
Ру = 1034510.90.70.607-0.31.1=2787.33[H]
Рх =102411010.70.507-0.41.1=2787.33[H]
Сводная таблица по всем переходам осуществляемым на данной опирации
Станок: токарный 1Е140
Орерация 030 Разметочная
Производится разметка поверхности под рассверливание центрального отверстия под крюк.
Операция 35 Сверлильная.
s = 1[мм] - подача (том 2 стр. 277 т - 13)
Cv = 98 - коэффициент скорости (том 2 стр. 278 т - 17)
Kv = KmvКт Kuv = 13 1 09 = 117.
Kmv = 13 - коэффициент учитывающий влияние материала заготовки (том 2 стр. 263т-1)
Kuv =1 - коэффициент учитывающий влияние материала инструмента (том 2 стр.263 т-6)
Knv = 09 - коэффициент состояния поверхности (том 2 стр. 277 т - 5).
Крутящий момент Нм и осевую силу Н рассчитываем по формулам
Мкр=10СмDqSyKp=100.03451620.215=120 Нм
Глубина резания t=0.5D=0550=25мм.
Подача: При сверлении выбираем максимально допустимую по прочности сверла подачу S=1ммоб
Операция 040 Токарно-карусельная
Т = 45 [мин] - среднее значение стойкости инструмента (том 2 стр. 268).
t = 85 [мм] - глубина резания
s = 02[мм] - подача (том 2 стр. 268 т - 13)
Cv = 350 - коэффициент скорости (том 2 стр. 269 т - 17)
m = 055 - показатель степени (том 2 стр. 269 т - 17)
Knv = 09 - коэффициент состояния поверхности (том 2 стр. 263 т - 5)
Число оборотов n[обмин] заготовки определяется по формуле:
Силу резания принято раскладывать на составляющие силы направленные по осям координат станка: тангенциальную Pz радиальную Ру осевую Рх. При наружном продольном точение эти силы рассчитываются по формуле:
Поправочные коэффициенты учитывающие влияние геометрические параметры режущей части инструмента на составляющие сил резания берем из ( том 2 стр. 275 т - 23) для углов φ° = 45° γ0 =0° λ° = 0° г = 2 [мм].
Pz = 1030085 03075896-015 11 = 572248[Н]
Pr = 10243 8509 0306 896-03 11 = 233733[Н]
Px =10339850305896-0411 = 233733[Н]
Станок: токарно-карусельный 1512.
Расчет станочного приспособления
При фрезеровании принимаем усилие зажима равным 4000Н. Определяем необходимое давление в цилиндре.
где QШТ=400 Н осевая сила на штоке;
Ду= 130 мм. диаметр пневмоцилиндра;
γ =085÷090 - кПд пневмоцилиндра.
Вследствие того что в магистрали давление воздуха 4-5 атм. то перед приспособлением должен быть понижающий редуктор.
4. Конструкция станочного приспособления.
При разработке технологического процесса необходимо правильно выбрать приспособление которое должно способствовать повышению производительности точности обработки улучшению условий труда.
Для данного техпроцесса были выбраны тиски пневматические универсальные.
В отверстие неподвижной оси 8 тисков встроен пневмоцилиндр 11 с которым винтами соединен полый поворотный корпус 12. К корпусу прикреплен распределительный кран 6 с рукояткой 7 для переключения золотника при поочередном выпуске сжатого воздуха в верхнюю или нижнюю полость пневмоцилиндра 11 и выпуска воздуха в атмосферу. На верней части поворотного корпуса 12 закреплена плита 5.
Сжатый воздух поступает в верхнюю полость пневмоцилиндра 11 и перемещает поршень 10 со штоком вниз при этом длинное плечо рычага 2 находящееся в пазу штока опускается а короткое перемещает подвитую губку вправо и деталь зажимается.
Во время поворота рукояти 7 завиток крана 6 пропускает воздух в нижнюю полость пневмоцилиндра 11. Сжатый воздух действуя на поршень 10 перемещает его со штоком 9 вверх. При этом длинное плечо рычага 2 поднимается вверх а короткое отводит губку 1 влево и деталь разжимается.