Конструирование двухступенчатого редуктора




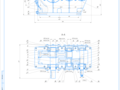
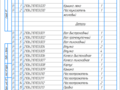
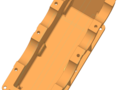
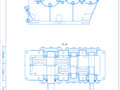
- Добавлен: 24.01.2023
- Размер: 7 MB
- Закачек: 0
Описание
Конструирование двухступенчатого редуктора
Состав проекта
![]() |
![]() |
![]() |
![]() ![]() ![]() ![]() |
![]() |
![]() ![]() ![]() |
![]() |
![]() |
![]() |
![]() |
![]() |
![]() |
![]() |
![]() |
![]() |
![]() |
![]() |
![]() |
![]() |
![]() ![]() ![]() |
![]() |
![]() |
![]() |
![]() |
![]() |
![]() ![]() ![]() |
![]() ![]() ![]() ![]() |
![]() |
![]() |
![]() ![]() ![]() ![]() |
![]() |
![]() |
![]() |
![]() |
![]() |
![]() |
![]() |
![]() |
![]() ![]() ![]() ![]() |
![]() |
![]() |
![]() |
![]() |
![]() |
![]() |
![]() |
![]() |
![]() ![]() ![]() ![]() |
![]() |
![]() |
![]() |
![]() |
![]() |
![]() |
![]() |
![]() |
![]() |
![]() |
![]() |
![]() |
![]() |
![]() |
![]() |
![]() |
![]() |
![]() ![]() ![]() ![]() |
![]() ![]() ![]() |
![]() |
![]() |
![]() |
![]() |
![]() |
![]() |
![]() |
Дополнительная информация
Редуктор.cdw

Титульник.docx
Российской Федерации
УФИМСКИЙ ГОСУДАРСТВЕННЫЙ АВИАЦИОННЫЙ
ТЕХНИЧЕСКИЙ УНИВЕРСИТЕТ
“ Прикладная механика ”
Расчет и проектирование двухступенчатого редуктора.
(подпись) (дата) (и. о. фамилия)
Ильяс.docx
Рабочим органом машины для которой проектируется привод служит стальной проволочный канат.
Определению подлежат диаметр каната диаметр барабана и величина крутящего момента а также частота вращения.
Для привода грузоподъемной машины:
По заданному рабочему усилию определим диаметр каната
Примем Канат 74-Г-В-Н-Т ГОСТ 3062-80
По найденному диаметру каната определяем диаметр барабана
Диаметр барабана округляем в большую сторону по ГОСТ 6636-69 нормальных линейных размеров
Определяем крутящий момент и частоту вращения
2. Выбор электродвигателя.
Для выбора электродвигателя определим потребную мощность и частоту вращения. Потребляемую мощность (кВт) привода (мощность на выходе) определим по формуле:
Тогда требуемая мощность электродвигателя:
Требуемая частота вращения вала электродвигателя:
где частота вращения приводного вала редуктора вычисляется по формуле:
Примем передаточные числа для вычисления из рекомендуемого диапазона для двух зубчатых передач (табл. 1.2 [1]):
По таблице 24.9 [1] выбираем электродвигатель 100L6950
3. Определение передаточных чисел.
После выбора определяем общее передаточное число привода
Полученное расчетом общее передаточное число распределяется между редуктором и отдельными ступенями редуктора
Передаточные числа быстроходной и тихоходной ступеней двухступенчатого редуктора определяем по соотношениям из таблицы 1.3. [1]:
4. Определение вращающих моментов и частот вращения циклов
Частота вращения вала колеса тихоходной ступени:
т.к. в заданной схеме отсутствует ременная и цепная передача.
Частота вращения вала шестерни тихоходной ступени (вала колеса быстроходной ступени):
Частота вращения вала шестерни быстроходной ступени:
Вращающий момент (Нм) на приводном валу:
Момент на валу колеса тихоходной ступени
Вращающий момент на валу шестерни тихоходной ступени
Момент на валу шестерни быстроходного вала
Расчёт зубчатой передачи.
В зависимости от вида изделия условий его эксплуатации и требований к габаритным размерам выбирают необходимую твердость колес и материалы для их изготовления. Для силовых передач чаще всего применяют стали. Передачи со стальными зубчатыми колесами имеют минимальную массу и габариты тем меньше чем выше твердость рабочих поверхностей зубьев которая в свою очередь зависит от марки стали и варианта термической обработки. По табл. 2.1 [1] выбираем вариант термической обработки:
- для колеса – улучшение твердость зубьев 235-262 НВ;
- для шестерни – улучшение твердость зубьев 269-302 НВ.
Марка стали для них одинакова – сталь 40ХН.
Получим средние значения для шестерен и для колёс
Рассчитаем для шестерней и колёс:
1. Расчёт допускаемых контактных напряжений.
Допускаемое контактное напряжение рассчитывают для каждого зубчатого колеса передачи по формуле
где - определяют по эмпирическим зависимостям
- коэффициент безопасности назначим для колёс и шестерен SH = 11 - коэффициент долговечности
Если то следует принимать
Расчет числа циклов перемены напряжений выполняют с учетом режима нагружения передачи. При постоянном режиме нагрузки расчетное число циклов напряжений
где с - число зацеплений зуба за один оборот (для проектируемого редуктора с=1);
n12 - частота вращения того зубчатого колеса по материалу которого определяют допускаемые напряжения обмин;
t - время работы передачи (ресурс) в часах; t = Lh.
-для шестерни первой ступени (быстроходной):
-для колеса первой ступени (быстроходной) и шестерни второй ступени(тихоходной):
для колеса второй ступени (тихоходной):
Рассчитаем для колёс и для шестерен по формуле :
Поскольку для всех шестерен и колёс то примем коэффициент долговечности
Вычислим допускаемые контактные напряжения:
- допускаемое контактное напряжение для шестерен
- допускаемое контактное напряжение для колес.
-для тихоходной ступени (прямозубая передача):
2. Допускаемые напряжения изгиба.
Расчет зубьев на изгибную выносливость выполняют отдельно для зубьев шестерни и колеса для которых вычисляют допускаемые напряжения изгиба по формуле
где - предел выносливости зубьев по напряжениям изгиба
SF - коэффициент безопасности рекомендуют SF= 15 175;
YA -коэффициент учитывающий влияние двустороннего приложения нагрузки (например реверсивные передачи) при односторонней нагрузке YA =1;
Yn) - коэффициент долговечности методика расчета которого аналогична расчету ZN (смотри выше).
При следует принимать . Рекомендуют принимать для всех сталей . При постоянном режиме нагружения передачи
Коэффициент безопасности примем SF=175;
Тогда допускаемые значения напряжений изгиба
- допускаемое напряжение изгиба для шестерен
- допускаемое напряжение изгиба для колес.
3. Проектный расчёт закрытой цилиндрической зубчатой передачи.
При проектном расчете прежде всего определяют главный параметр цилиндрической передачи - межосевое расстояние в мм. Расчёт производят по следующим формулам:
- для прямозубой передачи
- для косозубой передачи
В указанных формулах знак "+" принимают в расчетах переда внешнего зацепления а знак"-" - внутреннего зацепления.
Рекомендуется следующий порядок расчетов.
Назначают относительную ширину колес в соответствии со схемой расположения колес относительно опор и выбранной ранее твердостью поверхностей зубьев. Большие значения целесообразно принимать для передач с постоянными или близкими к ним нагрузками. В дальнейшем в расчетах может встретиться относительная ширина колес которую рассчитывают с учетом зависимости
Коэффициент неравномерности нагрузки по длине контакта в соответствии с расположением колёс относительно опор и твёрдостью рабочих поверхностей зубьев колёс.
Приведённый модуль упругости Епр в случае различных материалов колёс рассчитывают по соотношению
Если в передаче используется для изготовления колёс один материал (например сталь с Е=2.1·105 МПа или чугун с =0.9·105 МПа) тогда Епр=Е МПа.
Полученное значение межосевого расстояния aw (мм) для нестандартных передач рекомендуется округлить до ближайшего большего значения по ряду Ra20 нормальных линейных размеров.
Для быстроходной ступени (косозубая передача):
выберем и рассчитаем коэффициенты
и тогда примем Епр=Е=2·105 МПа получим
Для тихоходной ступени (прямозубая передача):
Полученное значение межосевого расстояния aw (мм) для нестандартных передач рекомендуется округлить до ближайшего большего значения по ряду Ra20 нормальных линейных размеров получим
4. Геометрический расчёт закрытой цилиндрической передачи.
Определяют модуль зацепления т (или тn для косозубой передачи) из соотношения т(тn) = (0.01 0.02)·aw.
Полученное значение модуля необходимо округлить до стандартного значения по 1-му ряду модулей: 10; 125; 15; 2; 25; 3; 4; 5; 6; 8; 10 мм. При этом для силовых передач рекомендуют принимать m(mn)15 мм.
Для косозубой передачи угол наклона линии зуба назначают в пределах = 8° 20°.
Далее определяют суммарное число зубьев шестерни и колеса:
для прямозубых колес
для косозубых колес
Полученное значение округляют до целого числа.
Число зубьев шестерни определяют из соотношения: где u - передаточное число передачи . Здесь знак "+" - для внешнего заципления знак "-" - для внутреннего зацепления.
Значение z1 следует округлить до целого числа. Из условия отсутствия подрезания зубьев необходимо назначать: для прямозубых и - для косозубых колёс. Зачастую для шума в быстроходных передачах принимают .
Рассчитывают число зубьев колеса передачи
Определяют фактическое значение передаточного числа передачи с точностью до двух знаков после запятой. Определяют фактическое межосевое расстояние. Для прямозубой передачи . Для косозубой передачи уточняют значение фактического угла наклона линии зуба
Рабочую ширину зубчатого венца колеса рассчитывают как и округляют до целого числа по ряду Ra20 нормальных линейных размеров (табл. 2.5). Тогда ширина зубчатого венца колеса ширина зуба шестерни мм.
Делительные диаметры рассчитывают по формулам:
- для прямозубых колес
и - для косозубых колес.
Начальный диаметр шестерни -
Начальный диаметр колеса передачи -
Диаметры вершин зубьев колес для прямозубых и - для косозубых колес. Диметры впадин зубьев колес - для прямозубых и - для косозубых колес. Точность вычислений диаметральных размеров колес должна быть выше 0001 мм. Угол зацепления передачи принимают равным углу профиля исходного контура:
Для быстроходной ступени (прямозубая передача):
Примем mn=2 и рассчитаем суммарное число зубьев
Для шестерни получим тогда для колеса
Рабочая ширина зубчатого венца колеса
Рабочая ширина зубчатого венца шестерни примем
-делительные диаметры:
- диаметры начальных окружностей:
-диаметры вершин зубьев
-диметры впадин зубьев колес
Примем m=3 рассчитаем суммарное число зубьев
Для шестерни получим тогда для колеса уточним передаточное число межосевое расстояние и угол наклона линии зуба
Проверочный расчёт закрытой цилиндрической передачи.
1.Проверка контактной выносливости рабочих поверхностей зубьев колёс.
Расчётом должна быть проверена справедливость соблюдения следующих неравенств:
- для прямозубых колёс
- для косозубых колёс
где - коэффициент повышения прочности косозубых передач по контактным напряжениям .
Все геометрические параметры рассчитываемых колёс определены в п.2.4. Для косозубой передачи дополнительно рассчитывают - коэффициент торцового перекрытия зубчатой передачи по формуле [1]:
Здесь также знак "+" относится к передачам внешнего зацепления а "-" внутреннего зацепления.
Для определения коэффициента внутренней динамической нагрузки KHV необходимо назначить степень точности передачи в зависимости от окружной скорости в зацеплении
Однако практически ошибки нарезания зубьев мог устранить двухпарное зацепление и при контакте одной пары между зубьями второй пары может быть небольшой зазор который устраняется под нагрузкой вследствие упругих деформаций зубьев. Это учитывают коэффициентом КН.
Если в результате проверки выявится существенная недогрузка (свыше 10 %) передачи то с целью более полного использования возможностей материалов зубчатых колёс возможна корректировка рабочей ширины зубчатого венца по соотношению .
Уточнённое значение рабочей ширины венца рекомендуется округлить до нормального линейного размера.
Проверочный расчёт первой ступени
Рассчитаем контактные напряжения для первой ступени:
Недогрузка составляет
Проверочный расчёт второй ступени:
Рассчитаем контактные напряжения для второй ступени
Перегруз составляет
2. Проверка прочности зубьев по напряжениям изгиба.
Расчёт выполняют отдельно для шестерни и для зубчатого колеса передачи после уточнения нагрузок на зубчатые колёса и их геометрических параметров.
Проверяют справедливость соотношения расчётных напряжений изгиба и допускаемых напряжений :
для прямозубых колёс
где - коэффициент повышения прочности косозубых передач по напряжениям изгиба . Здесь -коэффициент учитывающий повышение изгибной прочности вследствие наклона контактной линии на зубе к основанию зуба где подставляют в градусах. Коэффициент неравномерности распределения нагрузки между одновременно зацепляющимися зубьями . Окружное усилие в зацеплении колёс рассчитывают по формуле
Коэффициент неравномерности распределения нагрузки по длине линии контакта определяют по графикам аналогично рассмотренному выше определению значения коэффициента .
Коэффициент формы зуба для прямозубых колёс назначают в зависимости от фактического числа зубьев для прямозубых колёс и от числа зубьев эквивалентных колёс - для косозубых колес.
Если при проверочном расчёте рабочие напряжения изгиба в зубьях колёс оказываются значительно меньшей величины чем допускаемые напряжения то для закрытых передач это вполне допустимо так как нагрузочная способность таких передач ограничивается как правило контактной выносливостью зубьев.
Проверим на прочность зубьев по напряжениям изгиба шестерни обоих ступеней для этого рассчитаем окружные силы:
- для быстроходной ступени;
- для тихоходной ступени;
По аналогии с расчётом на контактную прочность выберем коэффициенты
-коэффициент неравномерности распределения нагрузки по длине линии контакта
-коэффициент формы зуба :
для прямозубой быстроходной передачи
для прямозубой тихоходной передачи передачи
- коэффициент внутренней динамической нагрузки KFV
для прямозубой передачи
Рассчитаем напряжения по изгибу:
Для первой ступени (косозубая передача):
Для второй ступени (прямозубая передача):
Условие прочности выполняется.
Разработка эскизного проекта.
Первым этапом конструирования редуктора является разработка эскизного проекта. При эскизном проектировании определяем расположение деталей передач расстояния между ними ориентировочные диаметры валов ступеней выбираем типы подшипников и схемы их установки.
1 Конструирование валов редуктора привода.
Для быстроходного вала:
учитывая что dэд = 28 мм примем d = dб = 28 мм;
диаметр цапфы вала под подшипником
dп = d + 2tцил = 28+222 = 324 мм
округляем до большего кратного пяти и принимаем dп = 35 мм.
диаметр буртика для упора кольца подшипника
dбп = dп + 3r = 40+32 = 41 мм
диаметр вал-шестерни
Для промежуточного вала:
Основной диаметр получим:
для стандартизации деталей редуктора с учетом малой разности цен на подшипники примем dк = 30 мм;
dп =d + 2tцил =30+222=344 мм
для стандартизации деталей редуктора с учетом малой разности цен на подшипники примем dп = 35 мм;
размер фаски при dк = 35 мм примем f = 12 мм;
размер радиуса закругления r = 2мм;
диаметр буртика для упора колеса
dбп = dп + 3r = 35 + 32 = 41 мм;
Подберем стандартное значение dбп = 42 мм;
диаметр шейки вала в месте установки зубчатых колес
диаметр буртика колеса
dбк = dк + 3f=42+312=456 мм
Для тихоходного вала:
dп =d + 2tцил =35+228=506 мм
округляем до большего кратного пяти и принимаем dп = 50 мм.
dбп = dп + 3r = 50+325 = 56 мм;
dбк = dк + 3f = 60 + 32 = 66 мм.
2 Определение усилий в зацеплении зубчатых передач.
На каждое из четырех зубчатых колес редуктора действуют три составляющих усилия в зацеплении: окружная сила Ft и радиальная сила Fr которые соответственно определяются по формулам:
для шестерни быстроходной передачи
Ft1Б = 22210336 = 1222 Н;
где W - начальный угол профиля или угол зацепления по ГОСТ 13755-81 W = 200;
Fr1Б = 1222tg 200 = 445 Н;
для колеса быстроходной передачи
Ft2Б = 2123103214 = 1150 Н;
Fr2Б = 1150tg 200= 418 Н;
для шестерни тихоходной передачи
Ft1Т = 212310357 =4316 Н;
Fr1Т = 4316 tg 200= 1570 Н;
для колеса тихоходной передачи
Ft2Т = 2545103264 = 4129 Н;
Fr2Т = 414672 tg 200= 1503Н;
3. Расчет валов на прочность.
Основными нагрузками на вал являются силы от передач. Силы на валы передают через насажанные на них детали.
При расчете примем что насажанные на вал детали передают силы и моменты на валу на середине своей ширины.
Под действием постоянных по значению и направлению сил во вращающихся валах возникают напряжения изменяющиеся по симметричному циклу.
Выберем материал для вала сталь 40ХН.
Выполним расчет вала (промежуточного) на статическую прочность и на сопротивление усталости.
Перед основными расчетами выполним следующее: по чертежу сборной единицы вала составим расчетную схему на которую нанесем все внешние силы нагружающие вал; затем определим реакции опор в горизонтальной и вертикальной плоскостях в этих же плоскостях построим эпюры изгибающих моментов и отдельно эпюру крутящего момента ; предварительно установим опасные сечения; проверим прочность вала в опасных сечениях.
В расчетной схеме длина от опоры А до опоры D равна:
Из рисунка параметры
Определяем реакции в опорах А и В в горизонтальной и вертикальной плоскостях.
Вертикальная плоскость:
Горизонтальная плоскость:
Перед построением эпюр изгибающих моментов и крутящего момента определим их значения на концах расчётных участков:
Крутящие моменты действуют на участке ВС =123 Нм
Найдём суммарный изгибающий момент:
-Получили опасное сечение С в котором действуют суммарный изгибающий момент и крутящий момент T=123 Н·м в котором концентрация напряжений обусловлена шпоночной канавкой
Определяют амплитуду симметричного цикла нормальных напряжений при изгибе вала в опасных сечениях: и амплитуду отнулевого цикла касательных напряжений при кручении вала
Wx и Wр – моменты сопротивления изгибу и кручению опасного сечения вала мм3.
для промежуточного вала
Wu=6450 мм3 Wр=13720 мм3 для сечения вала d=40 мм с пазом для призматической шпонки по ГОСТ 23360-78
Рассчитаем вал на статическую прочность:
Для стали 45 Т=540 МПа Т=270 МПа
где s и s коэффициенты запаса прочности по пределам текучести
Условие статической прочности выполняется.
Для опасных сечений определяют коэффициенты запаса усталостной прочности и сравнивают их с допускаемыми.
При совместном действии изгиба и кручения запас усталостной прочности определяют по формуле:
где - запас сопротивления усталости только по изгибу.
Коэффициент запаса сопротивления усталости только по кручению берется как меньшая величина из двух значений:
- запас сопротивления усталости только по кручению.
В предыдущих формулах и - амплитуды переменных составляющих циклов напряжений а и - постоянные составляющие; и - коэффициенты корректирующие влияние постоянной составляющей цикла напряжений на сопротивление усталости;
и - пределы выносливости материала вала при симметричном цикле нагружения. Их определяют по таблицам или по приближенным формулам:
где - предел прочности материала вала;
- предел текучести при сдвиге;
и - масштабный фактор и фактор шероховатости поверхности;
и - эффективные коэффициенты концентрации напряжений при изгибе и кручении.
Коэффициент концентрации напряжений с пазом под шпонку и . Значение масштабного фактора . Посадочную поверхность шлифуют коэффициент качества поверхности и - коэффициенты корректирующие влияние постоянной составляющей цикла напряжений на сопротивление усталости пределы выносливости материала вала при симметричном цикле нагружения
Сопротивление усталости можно существенно увеличить применяя тот или иной метод поверхностного упрочнения: поверхностную закалку токами высокой частоты дробеструйный наклёп обкатку роликами азотирование цементирование и т.д. Можно также существенно уменью концентрацию напряжений изменением формы соответствующих мест перехода.
Условие усталостной прочности выполнено.
Выбор типа подшипника.
Для промежуточного вала выбираем подшипник средней серии 307 ГОСТ 8338-75
1. Проверка правильности подбора подшипников качения.
Выбранный в ходе проектирования узла вала типоразмер подшипника должен быть проверен на работоспособность по динамической грузоподъёмности.
Проверка правильности выбора подшипников может быть проведена по сравнению требуемой Сr треб и паспортной Сr пасп динамической грузоподъемности подшипника когда должно выполняться условие Сr треб Сr пасп;
где а1 – коэффициент надежности обычно принимают а1=1 при 90% надежности;
а2 – обобщенный коэффициент совместного влияния качества металла деталей подшипника и условий его эксплуатации для обычных условий эксплуатации назначают а2=07 08 (для шарикоподшипников) и а2=06 (для роликоподшипников).
Величина эквивалентной динамической нагрузки на проверяемый подшипник рассчитывается в общем случае по формуле
где Fr и Fa – соответственно радиальная и осевая силы в опоре. V – коэффициент вращения зависящий от того какое кольцо подшипника вращается; при вращении внутреннего кольца V=1;
kб – коэффициент безопасности учитывающий характер нагрузки при умеренных толчках kб=13 15;
kt – температурный коэффициент для температуры подшипникового узла
X и Y – коэффициенты соответственно радиальной и осевой нагрузок на подшипник назначаются в зависимости от параметра осевого нагружения подшипника. При малой осевой силе действие осевой силы в расчет не принимается то есть X=1 и Y=0.
Для шариковых подшипников: .
Коэффициент надежности: .
Обобщенный коэффициент совместного влияния качества металла и условий эксплуатации .
Поскольку ни в одном подшипнике не действует осевых сил то примем X=1 и Y=0.
условие подбора подшипника выполняется.
Расчет соединения зубчатого колеса.
Призматические шпонки применяемые в проектируемом редукторе проверяем на смятие (См. рис.).
Условие прочности шпонки
где – окружная сила (T – крутящий момент; d – диаметр вала)
– площадь смятия (– рабочая длина шпонки со скругленными торцами).
При стальной ступице и спокойной нагрузке допускаемое напряжение .
Для промежуточного вала принимаем призматическую шпонку по ГОСТ 23360-78 с параметрами: .
Подберем длину шпонки по условию прочности:
Подставим числовые значения:
Принимаем длину шпонки аналогично для тихоходного вала
Конструирование основных соединений определение основных размеров корпусных деталей.
1. Расстояния между деталями.
Чтобы поверхности вращающих колес не задевали за внутренние поверхности корпуса между ними оставляют зазор мм
где – расстояние между внешними поверхностями деталей передач мм
Расстояние между дном корпуса и поверхностью колес примем:
Расстояние между торцевыми поверхностями колес примем:
2. Основные размеры корпуса редуктора.
Корпусные детали редукторов общего назначения имеют сложную форму при этом наиболее рациональной является технология их изготовления из отливок (чаще из чугуна марки СЧ15) с последующей механической обработкой. Корпус редуктора валы которого размещены в одной плоскости выполняют состоящим из основания корпуса и крышки с разъемом в плоскости валов.
Основные размеры определяющие внешние очертания корпуса находят в функции толщины стенки (мм) вычисляемой по формуле
Диаметр прилива для привертной крышки:
где диаметр фланца.
Для быстроходного и промежуточного вала
Диаметр d резьбы болта соединяющего крышку и основание корпуса:
Диаметр крепления редуктора к плите (раме)
3. Смазывание зубчатых передач.
Смазывание зубчатых передач применяют в целях защиты от коррозии снижения коэффициента трения уменьшения износа отвода тепла и продуктов от трущихся поверхностей снижения шума и вибраций.
Для редукторов общего назначения применяют непрерывное смазывание жидким маслом картерным непроточным способом (окунанием).
Сорт масла зависит от контактного напряжения н (МПа) и окружной скорости (мс).
Для зубчатой передачи при температуре 40оС с контактным напряжением н600 МПа рекомендуется кинематическая везкость:
-для тихоходной ступени: 34 мм2с
-для быстроходной ступени: 34 мм2с
По данным кинематическим вязкостям выбираем масло: И-Г-А-32
При в масло должны быть погружено колесо тихоходной передачи.
Определение количества масла.
При смазывании окунанием объем масляной ванны определяют из расчета 08 1 л на 1кВт передаваемой мощности.
Определение уровня масла.
При окунании в масляную ванну колеса уровень масла должен быть в пределах
где – модуль зацепления;
– диаметр делительной окружности тихоходного колеса.
– диаметр вершин зубьев быстроходного колеса
4 Контроль уровня масла.
Уровень масла находящегося в корпусе редуктора контролируют жезловыми указателями так как они удобны для осмотра; конструкция их проста и достаточно надежна.
При работе передач масло постепенно загрязняется продуктами износа деталей передач. С течением времени оно стареет свойства его ухудшаются. Поэтому масло налитое в корпус редуктора периодически меняют. Для этой цели в корпусе предусматривают сливное отверстие закрываемое пробкой с цилиндрической резьбой.
При длительной работе в связи с нагревом масла и воздуха повышается давление внутри корпуса. Это приводит к просачиванию масла через уплотнения и стыки. Чтобы избежать этого внутреннюю полость корпуса сообщают с внешней средой путем установки отдушины в его верхних точках.
Дунаев П.Ф. Леликов О.П. Конструирование узлов и деталей машин: Учеб. пособие для машиностроительных спец. вузов – 4-е изд. перераб. и доп.- М.: Высш. шк. 1985-416с. ил.
Иванов М.Н. Деталей машин: Учеб. для студентов втузов Под ред. В.А.Финогеева – 6-е изд. перераб.-М.: Высш. шк. 2000-383с. ил.
Дунаев П.Ф. Леликов О.П. Конструирование узлов и деталей машин: Учеб. пособие для техн. спец. вузов. – 7-е изд. исправ.-М.: Высш.шк. 2001-447с. ил.
Оглавление.docx
2. Выбор электродвигателя.4
3. Определение передаточных чисел.5
4. Определение вращающих моментов и частот вращения циклов
Расчёт зубчатой передачи.6
1. Расчёт допускаемых контактных напряжений.6
2. Допускаемые напряжения изгиба.7
3. Проектный расчёт закрытой цилиндрической зубчатой передачи.8
4. Геометрический расчёт закрытой цилиндрической передачи.9
Проверочный расчёт закрытой цилиндрической передачи.12
1.Проверка контактной выносливости рабочих поверхностей зубьев колёс.12
2. Проверка прочности зубьев по напряжениям изгиба.13
Разработка эскизного проекта.15
1 Конструирование валов редуктора привода.16
2 Определение усилий в зацеплении зубчатых передач.18
3. Расчет валов на прочность.19
Выбор типа подшипника.24
Расчет соединения зубчатого колеса.26
Конструирование основных соединений определение основных размеров корпусных деталей.27
1. Расстояния между деталями.27
2. Основные размеры корпуса редуктора.27
3. Смазывание зубчатых передач.28
4 Контроль уровня масла.29
Спецификация.spw

Редуктор 2.cdw

быстроходной ступени 5
тихоходной ступени 4
Вращающий момент на тихоходном валу. Нм 545
Частота вращения тихоходного
Основные параметры зацепления см. табл. 1
Обозначение в скобках для тихоходной ступени.
Технические требования
Перед сборкой необработанные наружние поверхности корпуса
редуктора покрыть 1 слоем грунтовки
Плоскость разъема корпуса редуктора покрыть тонким слоем
герметика ВКГ-18 №2 МРТУ 07-6012-63 при окончательной
В редуктор залить Масло И-Г-А-31. Уровень не должен превы-
шать максимальной отметки.
Редуктор обкатать без нагрузки при частоте вращения
быстроходного вала n=950 обмин в течении 2 часов
масло слить и проверить проворачиваемость.
Маслоуказатель.spw

Крышка люка.spw

Эпуры.cdw

Содержание 2.docx
2.Выбор электродвигателя4
3.Определение передаточных чисел5
4.Определение вращающих моментов и частот вращения циклов нагружения5
Расчет зубчатой передачи6
1.Расчет допускаемых контактных напряжений6
2.Допускаемые напряжения изгиба7
3.Проектный расчет закрытой цилиндрической передачи8
4.Геометрический расчет закрытой цилиндрической передачи9
Проверочный расчет закрытой цилиндрической передачи12
1.Проверка контактной выносливости рабочих поверхностей зубьев колёс12
2. Проверка прочности зубьев по напряжениям изгиба 13
Разработка искизного проекта 15
1.Конструирование валов редуктора привода16
2.Определение усилий в зацеплении зубчатых передач18
3.Расчет валов на прочность19
Выбор типа подшипника24
Расчет соединения зубчатого колеса26
Конструирование основных соединений определение основных размеров корпусных деталей27
1.Расстояния между деталями27
2.Основные размеры корпуса редуктора27
3.Смазывание зубчатых передач28
4.Контроль уровня масла29
Список литературы 31
Рекомендуемые чертежи
- 24.01.2023
- 24.01.2023
- 17.04.2018