Интегрированное рабочее место на участке крепления каблука




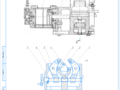
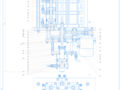
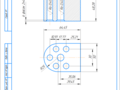
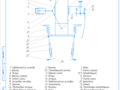
- Добавлен: 24.01.2023
- Размер: 42 MB
- Закачек: 0
Описание
Состав проекта
![]() |
![]() |
![]() |
![]() |
![]() ![]() ![]() |
![]() |
![]() ![]() ![]() |
![]() ![]() ![]() |
![]() ![]() ![]() |
![]() ![]() ![]() |
![]() |
![]() ![]() ![]() ![]() |
![]() ![]() ![]() ![]() |
![]() ![]() ![]() ![]() |
![]() |
![]() ![]() ![]() ![]() |
![]() ![]() ![]() ![]() |
![]() ![]() ![]() ![]() |
![]() ![]() ![]() ![]() |
![]() |
![]() ![]() ![]() ![]() |
![]() ![]() ![]() ![]() |
![]() ![]() ![]() ![]() |
![]() |
![]() |
![]() ![]() ![]() |
![]() |
![]() ![]() ![]() ![]() |
![]() ![]() ![]() ![]() |
![]() ![]() ![]() ![]() |
![]() |
![]() |
![]() |
![]() |
![]() ![]() ![]() ![]() |
![]() |
![]() |
![]() ![]() ![]() |
![]() |
![]() |
![]() ![]() ![]() ![]() |
![]() |
![]() |
![]() |
![]() ![]() ![]() ![]() |
![]() ![]() ![]() ![]() |
![]() ![]() ![]() ![]() |
![]() ![]() ![]() ![]() |
![]() |
![]() |
![]() ![]() ![]() ![]() |
![]() |
![]() ![]() ![]() ![]() |
![]() |
![]() ![]() ![]() ![]() |
![]() ![]() ![]() ![]() |
![]() ![]() ![]() ![]() |
![]() |
![]() ![]() ![]() ![]() |
![]() ![]() ![]() ![]() |
![]() |
![]() |
![]() |
![]() |
![]() |
![]() ![]() ![]() ![]() |
![]() |
![]() ![]() ![]() ![]() |
![]() ![]() ![]() ![]() |
![]() |
![]() ![]() ![]() ![]() |
![]() ![]() ![]() ![]() |
![]() |
![]() ![]() ![]() ![]() |
![]() ![]() ![]() ![]() |
![]() |
![]() |
![]() ![]() ![]() |
Дополнительная информация
Курсовой - Брызгалов.doc
Учреждение образования
«Витебский государственный технологический университет»
по дисциплине «Организация планирование и управление предприятием»
на тему: «Расчет цеховой себестоимости изготовления детали»
Исполнитель: студент гр. ЗМ-49
Характеристика возможных вариантов механической обработки детали
Расчет эффективного фонда времени работы оборудования
Расчет потребного количества оборудования для выполнения производственной программы
Расчет потребного количества рабочих по профессиям разрядам и фонда их заработной платы
Расчет потребности и стоимости основных материалов
Расчет расходов на содержание и эксплуатацию оборудования
Расчет производственных расходов
Определение цеховой себестоимости изготовления детали
Расчет годового экономического эффекта разработанного варианта технологического процесса механической обработки детали
Организация производственных процессов выбор методов подготовки планирования и контроля производства во многом определяются типом производства который решающим образом влияет на эффективность использования ресурсов предприятия. Использование групповых методов обработки автоматизация и электронизация производственных процессов дают возможность применять организационные формы массового производства в серийном а иногда даже в мелкосерийном производствах.
Устойчивое развитие предприятия определяется уровнем конкурентоспособности его продукции которая в свою очередь связана с качеством и уровнем цены. Уровень цены зависит от себестоимости изготовления продукции.
В связи с этим целью данной работы является определение цеховой себестоимости изготовление детали. Кроме того цеховая себестоимость детали определяется с учетом выбранного варианта технологического процесса обеспечивающего минимум приведенных затрат по сравнению с другим технологическим процессом изготовления детали. А также приобретение навыков по расчету цеховой себестоимости изготовления детали.
Заготовка представляет собой прямоугольную гкатаную полосу ГОСТ 103-76 (40х22х12) из стали 30 ГОСТ 1050-88. Получаемая деталь имеет три отверстия диаметром 5 мм а также две зенковки диаметром 8 мм. Для детали предъявляются особые требования по шероховатости обрабатываемых поверхностей а также требования по выдерживанию соответствующих размеров указанных на чертеже детали.
При механической обработке используются два станка: вертикально-фрезерный (6Р11) и вертикально-сверлильный (2Н118).
Разрабатываем два варианта технологического процесса механической обработки.
Для определения штучного времени используем следующие формулы:
Тшт=Топ +Тоб+Тот(1.1)
где Топ – оперативное время мин.;
Тоб – время на обслуживание рабочего места мин.;
Тот – время перерывов на отдых и личные надобности мин;
где То – основное время мин.;
Тв – вспомогательное время мин.
Тв=Тус+Тзо+Туп+Тиз(1.3)
где Тус – время на установку и снятие детали мин.;
Тзо – время на закрепление и открепление детали мин.;
Туп – время на приемы управления мин.;
Тиз – время на измерение детали мин;
k – поправочный коэффициент на вспомогательное время.
5 Предварительное фрезерование поверхности (В) торцевой фрезой со снятием припуска толщиной 05 мм;
0 Предварительное фрезерование поверхности (Б) торцевой фрезой со снятием припуска толщиной 05 мм;
5 Предварительное фрезерование поверхности (А) концевой фрезой со снятием припуска толщиной 08 мм;
0 Предварительное фрезерование поверхности (Г) концевой фрезой со снятием припуска толщиной 125 мм;
5 Предварительное фрезерование поверхности (Д) концевой фрезой со снятием припуска толщиной 08 мм;
0 Предварительное фрезерование поверхности (Е) концевой фрезой со снятием припуска толщиной 125 мм;
5 Чистовое фрезерование поверхности (А) концевой фрезой со снятием припуска толщиной 04 мм;
0 Чистовое фрезерование поверхности (В) торцевой фрезой со снятием припуска толщиной 05 мм;
5 Чистовое фрезерование поверхности (Б) торцевой фрезой со снятием припуска толщиной 05 мм;
0 Сверление отверстий диаметром 5 мм спиральным сверлом в кондукторе;
5 Зенкование отверстий под головку болта диаметром 8 мм.
5 Предварительное фрезерование поверхности (А) концевой фрезой со снятием припуска толщиной 08 мм пачки из 3-х деталей;
0 Предварительное фрезерование поверхности (Г) концевой фрезой со снятием припуска толщиной 125 мм пачки из 3-х деталей;
5 Предварительное фрезерование поверхности (Д) концевой фрезой со снятием припуска толщиной 08 мм пачки из 3-х деталей;
0 Предварительное фрезерование поверхности (Е) концевой фрезой со снятием припуска толщиной 125 мм пачки из 3-х деталей;
5 Чистовое фрезерование поверхности (А) концевой фрезой со снятием припуска толщиной 04 мм пачки из 3-х деталей;
0 Сверление отверстий в пачке из 3-х деталей диаметром 5 мм спиральным сверлом в кондукторе;
5 Предварительное фрезерование поверхности
TО = 6*L*10-3 = 6*40*10-3 = 024 мин;
ТВ = 0033 + 004 + 022 + 001 = 0303 мин;
ТОП = TО + TВ = 024 + 0303 = 0543 мин;
ТОБ = 0056*0543 = 00304 мин;
ТОТ = 004*0543 = 00217 мин;
ТШТ = ТОП + ТОБ + ТОТ = 0543 + 00304 + 00217 = 05951 мин.
0 Предварительное фрезерование поверхности
TО = 6*L*10-3 = 6*212*10-3 = 01272 мин;
ТОП = TО + TВ = 01272 + 0303 = 04302 мин;
ТОБ = 0056*04302 = 00241 мин;
ТОТ = 004*04302 = 00172 мин;
ТШТ = ТОП + ТОБ + ТОТ = 04302 + 00241 + 00172 = 04715 мин.
TО = 6*L*10-3 = 6*3875*10-3 = 02325 мин;
ТОП = TО + TВ = 02325 + 0303 = 05355 мин;
ТОБ = 0056*05355 = 00299 мин;
ТОТ = 004*05355 = 00214 мин;
ТШТ = ТОП + ТОБ + ТОТ = 05355 + 00299 + 00214 = 05868 мин.
TО = 6*L*10-3 = 6*204*10-3 = 01224 мин;
ТОП = TО + TВ = 01224 + 0303 = 04254 мин;
ТОБ = 0056*04254 = 00238 мин;
ТОТ = 004*04254 = 0017 мин;
ТШТ = ТОП + ТОБ + ТОТ = 04254 + 00238 + 0017 = 04662 мин.
5 Чистовое фрезерование поверхности
TО = 4*L*10-3 = 4*375*10-3 = 015 мин;
ТОП = TО + TВ = 015 + 0303 = 0453 мин;
ТОБ = 0056*0453 = 00254 мин;
ТОТ = 004*0453 = 00181 мин;
ТШТ = ТОП + ТОБ + ТОТ = 0453 + 00254 + 00181 = 04965 мин.
0 Чистовое фрезерование поверхности
0 Сверление отверстия
ТВ = 006 + 002 + 004 + 008 = 02 мин;
ТОП = 0026 + 02 = 0226 мин;
ТОБ = 005*0226 = 00113 мин.;
ТОТ = 004*0226 = 0009 мин.;
ТШТ = 0226 + 00113 + 0009 = 02463 мин.
5 Зенкование отверстия
ТОП = 00074 + 02 = 02074 мин;
ТОБ = 005*02074 = 00104 мин.;
ТОТ = 004*02074 = 00083 мин.;
ТШТ = 02074 + 00104 + 00083 = 02261 мин.
Штучное и оперативное время для первого варианта технологического процесса механической обработки детали:
ТШТ.СВ. = 3*02463+2*02261 = 11911 мин.
ТШТ.ФР. = 3*05951+04715+05868+04662+3*04965 = 47993 мин.
ТОП.СВ. = 3*0226+2*02074 = 10928 мин.
ТОП.ФР. = 3*0543+04302+05355+04254+3*0453 = 44191 мин.
5 Предварительное фрезерование поверхности в пачке
Для одной детали ТОП = 0181 мин;
Для одной детали ТШТ = 01984 мин;
0 Предварительное фрезерование поверхности в пачке
Для одной детали ТОП = 01434 мин;
Для одной детали ТШТ = 01572 мин;
Для одной детали ТОП = 01785 мин;
Для одной детали ТШТ = 01954 мин;
Для одной детали ТОП = 01418 мин;
Для одной детали ТШТ = 01554 мин;
Для одной детали ТОП = 0151 мин;
Для одной детали ТШТ = 01655 мин;
0 Сверление отверстия в пачке
Для одной детали ТОП = 00753 мин;
Для одной детали ТШТ = 00821 мин;
Штучное и оперативное время для второго варианта технологического процесса механической обработки детали:
ТШТ.СВ. = 3*00821+2*02261 = 06985 мин.
ТШТ.ФР. = 2*05951 + 01984 + 01572 + 01954 + 01554 + 01655 + 2*04965 = =30551 мин.
ТОП.СВ. = 3*00753+2*02074 = 06407 мин.
ТОП.ФР. = 2*0543+0181+01434+01785+01418+0151+2*0453 = 27877 мин.
Принимаем второй вариант технологического процесса механической обработки детали т.к. рассчитанное штучное время во втором варианте на 22368 минуты меньше чем в первом а значит при изготовлении партии деталей из 10000 единиц затраты времени и средств будут меньше.
Экономия времени изготовления всей партии деталей составляет 3728 часов.
Проектируемый вариант (технологический процесс №2)
Величина эффективного фонда времени работы оборудования зависит от режима работы участка и времени простоя оборудования в ремонте. Число дней на ремонт определяется на основе нормативов содержащихся в “Единой системе планово-предупредительного ремонта оборудования”.
На предприятиях с прерывным производством эффективный фонд времени одного станка рассчитывается следующим образом:
Тэф=(Тк-Тв)*а*с*Ки (1.4)
где Тк – календарное число дней в году Тк = 365 дней;
Тв – количество выходных и праздничных дней в году
Тв = Твых.+Тпр.= 6+104 = 110 дней;
а – продолжительность работы одной смены а = 8 часов;
с – количество смен с = 2 смены;
Ки – коэффициент использования оборудования.
Коэффициент использования оборудования можно определить следующим образом:
где Трем – количество дней простоя оборудования во всех видах ремонта в течение года;
Ттс – количество дней технологических остановок оборудования в течении года.
Т.к. отсутствуют необходимые данные принимаем коэффициент использования равным Ки = 095.
Тогда эффективный фонд времени одного станка будет равен:
Тэф = (365-110)*8*2*095 = 3876 час.
Количество смен выбираем равным двум т. к. при данном значении потребное количество оборудования и коэффициент загрузки уменьшится вдвое а значит уменьшатся расходы на содержание и эксплуатацию оборудования но увеличится фонд заработной платы за счет доплат за работу в вечернее и ночное время. Однако экономия средств на содержание и эксплуатацию оборудования превышает расходы на заработную плату поэтому количество смен выгоднее принять равным двум.
Расчет потребного количества оборудования производится по каждой операции по формуле:
где Чр – расчетное количество станков;
ТШТ – штучное время операции;
КН – планируемый коэффициент выполнения норм штучного времени Кн=12;
В – общий годовой выпуск деталей В = 10000 шт.
Для сверлильной операции:
Определяем коэффициент загрузки на данную программу по формуле:
Чп – принятое количество станков Чп = 1.
Для фрезерной операции:
На основании данных о нормах времени и годовой программе определяется потребность по каждому виду оборудования (табл. 1).
Таблица 1 – Ведомость потребности в оборудовании
Транспор-тировка и монтаж (20% от ст-ти станка)
Полная стоимость оборудования тыс. руб.
Вертикально-сверлильный
Вертикально-фрезерный
Для расчета потребного количества рабочих занятых на нормируемых работах составляем баланс рабочего времени одного рабочего (табл. 2).
Таблица 2 – Баланс рабочего времени одного среднесписочного рабочего на 2007г.
Состав рабочего времени
Календарный фонд времени
Число нерабочих дней всего
Номинальный фонд времени
Неявки на работу всего
в т.ч. а) очередные и дополнительные отпуска
б) отпуска по беременности и родам
г) выполнение государственных и общественных обязанностей
Полезный фонд времени
Номинальная продолжительность рабочего дня
Потери времени: всего
в т.ч. а) для занятых на вредных работах и в праздничные
Средняя продолжительность рабочего дня
Эффективный фонд рабочего времени одного рабочего
После составления баланса рабочего времени подсчитываем потребное количество основных производственных рабочих численность которых зависит от трудоемкости выполнения отдельных операций.
Для расчета численности основных производственных рабочих используем штучно-калькуляционное время которое определяется по формуле:
Содержание и продолжительность подготовительно-заключительного времени (Тпз) зависит от характера производственного процесса типа производства характера труда и участия работника в осуществлении производственного процесса организации труда и обслуживании рабочего места. Тпз берется в процентах от Топ.
Тшт.к.= Тшт + 34%*Топ = 07203 мин.
Тшт.к.= Тшт + 38%*Топ = 31610 мин.
Численность основных производственных рабочих определяется по формуле:
Чсд = = 00556 чел.(1.9)
Таблица 3 – Расчет численности рабочих занятых на нормируемых работах
годовой программы с учетом выполнения норм выработки час
Номиналь-ный фонд времени одного рабочего час
Явоч-ное число рабо-чих чел
Полезный фонд времени одного рабочего час
Списоч-ное число рабочих чел
После определения численности рабочих рассчитываем фонд заработной платы.
Определяем часовую тарифную ставку по формуле:
где МТС – минимальная тарифная ставка 1 разряда МТС=65000руб.;
Ктар – тарифный коэффициент;
Тмес – месячный фонд рабочего времени одного рабочего
Тмес = 22*8 = 176час.
Таблица 4 – Расчет заработной платы рабочих занятых на нормируемых работах
Наименование операции
Час. тарифная ставка
Трудоемкость произв. прог-
Тарифный фонд зар. платы руб.
Годовой фонд заработной платы
по премиальн. системам
за работу в вечерн. время
за работу в ночное время
Трудоемкость производственной программы:
Тарифный фонд заработной платы:
Размер доплат по премиальной системе (25% от тарифного фонда заработной платы):
ЗПДОП.СЛ=025*ТФСВ=025*59853128 = 14963282 руб;
ЗПДОП.ФР=025*ТФФР=025*305476683 = 76369171 руб;
Доплаты за работу в вечернее и ночное время соответственно равны (1 смена – 8.00 – 17.00; 2 смена – 17.00 – 01.00):
Оплата отпусков составляет 15% от тарифного фонда заработной платы:
ЗПОТ.СВ=015*ТФСВ=015*59853128 = 8977969 руб;
ЗПОТ.ФР=015*ТФФР=015*305476683 = 45821502 руб;
Годовой фонд заработной платы равен сумме тарифного фонда заработной платы и общей суммы доплат по премиальной системе за работу в ночное и вечернее время а также оплата отпусков.
При расчете потребностей и стоимости сырья и материалов учитываются все затраты на сырье и материалы необходимые для изготовления данной детали с учетом транспортно-заготовительных расходов (10% от стоимости материала).
В общем виде затраты по этой статье можно определить по формуле:
Зм = (Цм*Нм*Ктз – Цо*Но)*В(1.11)
где Зм – затраты на сырье и материалы;
Цм – оптовая цена материала за 1кг Цм = 2000 руб.;
Нм – норма расхода материала на единицу продукции Нм = mзаг= 00829 кг;
Ктз – коэффициент транспортно-заготовительных расходов Ктз = 11;
Цо – цена возвратных отходов на 1кг Цо = 01*Цм = 200 руб.;
Но – вес возвратных отходов на единицу продукции
Тогда затраты на сырье и материалы будут равны:
Зм = (2000*00829*11–200*00301)*10000 = 1763600 руб.
1 Амортизация оборудования и транспортных средств
Затраты на амортизацию оборудования транспортных средств и ценного инструмента определяем исходя из первоначальной их стоимости и действующих годовых норм амортизационных отчислений.
где Коб – полная первоначальная стоимость оборудования и транспортных средств;
НА – норма амортизационных отчислений НА=141% [2 c.10];
Кз – коэффициент загрузки оборудования.
Для сверлильного станка:
Ао = 12000000*0141*0025 = 42300 руб.
Для фрезерного станка:
Ао = 18000000*0141*0109 = 276642 руб.
2 Эксплуатация оборудования
2.1 Стоимость смазочных обтирочных материалов эмульсий для охлаждения и прочих вспомогательных материалов необходимых для ухода за оборудованием и содержанием его в исправном состоянии определяется его нормативом или по формуле:
См.в.=Нр*До*Цм.в(1.13)
где Нр – годовая норма расхода материала на единицу оборудования;
До – количество единиц оборудования;
Цм.в. – цена единицы вспомогательного материала.
При отсутствии необходимых данных ориентированно затраты на вспомогательные материалы вычисляются из расчета 3% стоимости станка (необходимо учесть коэффициент загрузки оборудования).
См.в.=10000000*0025*003 = 7500 руб.
См.в.=15000000*0109*003 = 49050 руб.
ΣСм.в. = 56550 рублей.
2.2 Основная и дополнительная заработная плата вспомогательных рабочих обслуживающих оборудование (наладчиков электромонтеров слесарей ремонтных рабочих и др.) зависит от численности рабочих и составляет 40% годового фонда заработной платы основных рабочих.
Для вертикально-сверлильного станка:
ФВ.Р = 04*92772349 = 3710894 руб.
Для вертикально-фрезерного станка:
ФВ.Р = 04* 473488858 = 189395543 руб.
Σ ФВ.Р = 226504483 рубля.
2.3 Годовые затраты на электроэнергию можно определить по формуле:
где Муст – суммарная мощность электродвигателей установленных на оборудовании;
Тэф – эффективный фонд времени работы оборудования Тэф = 3876 ч;
Цэ – плата за 1кВт-час электроэнергии Цэ = 150 руб;
Кр – коэффициент одновременной работы двигателя станка;
Кз – коэффициент загрузки оборудования;
Кп – коэффициент учитывающий потери в сети Кп=095;
Кд – КПД электродвигателей.
ΣСэ = 5508765 рублей.
3 Текущий ремонт оборудования
В затратах на текущий ремонт оборудования учитываются в основном расходы связанные с приобретением для текущего ремонта запасных частей и других материалов а также основная и дополнительная заработная плата с отчислениями на социальное страхование рабочих (40%) занятых ремонтом оборудования. При отсутствии необходимых данных затраты по этой статье можно ориентировочно принять 10% от стоимости оборудования включая транспортно-заготовительные расходы. Кроме того необходимо учесть коэффициент загрузки оборудования.
ЗРЕМ = 10%*Коб*Кз = 01*12000000*0025 = 30000 руб.
ЗРЕМ = 10%*Коб*Кз = 01*18000000*0109 = 196200 руб.
ΣЗрем = 226200 рублей.
4 Внутризаводское перемещение
Затраты по статье “Внутризаводское перемещение” вычисляются из грузооборота для перевозки деталей и стоимости перемещения 1 тонны груза принимаемой по данным предприятия по формуле:
где Нм – норма расхода материала на единицу продукции Нм = 00829кг;
В – годовая программа выпуска В = 10000 шт;
Кпер – коэффициент перемещения груза Кпер = количество станков+1=2;
Спер – стоимость перемещения одной тонны груза Спер = 30000 руб.
ЗПЕР = = 74610 рублей.
5 Износ малоценных и быстроизнашивающихся инструментов и приспособлений
Сумма износа малоценных и быстроизнашивающихся инструментов и приспособлений определяется по данным предприятия или приближенно – 5% стоимости станка. При расчете необходимо учесть коэффициент загрузки оборудования.
Ии = 5%*Коб*Кз = 005*10000000*0025 = 12500 руб.
Ии = 5%*Коб*Кз = 005*15000000*0109 = 81750 руб.
Итог по статье “Расходы на содержание и эксплуатацию оборудования” определяется как сумма затрат по пунктам 6.1 и 6.5. Результаты расчета сводим в таблицу 5.
Таблица 5 – Смета расходов на содержание и эксплуатацию оборудования
Наименование статей расходов
Амортизация оборудования и транспортных средств
Эксплуатация оборудования
Текущий ремонт оборудования
Внутризаводское перемещение грузов
Износ малоценных и быстроизнашивающихся инструментов и приспособлений
Сравниваемый вариант (технологический процесс №1)
Эффективный фонд времени одного станка будет равен:
Расчет потребного количества оборудования:
Таблица 6 – Ведомость потребности в оборудовании
Таблица 7 – Расчет численности рабочих занятых на нормируемых работах
Таблица 8 – Расчет заработной платы рабочих занятых на нормируемых работах
ЗПДОП.СВ=025*ТФСВ=025*10206382 = 25515955 руб;
ЗПДОП.ФР=025*ТФФР=025*480024046 = 120006012 руб;
ЗПОТ.СВ=015*ТФСВ=015*10206382 = 15309573 руб;
ЗПОТ.ФР=015*ТФФР=015*480024046 = 72003607 руб;
Амортизация оборудования и транспортных средств:
Ао = 12000000*0141*0043 = 72756 руб.
Ао = 18000000*0141*0172 = 436536 руб.
ΣАо = 509292 рублей.
Эксплуатация оборудования:
См.в.=10000000*0043*003 = 12900 руб.
См.в.=15000000*0172*003 = 77400 руб.
ΣСм.в. = 90300 рублей.
Основная и дополнительная заработная плата вспомогательных рабочих:
ФВ.Р = 04*158198921 = 63279568 руб.
ФВ.Р = 04*744037272 = 297614909 руб.
Σ ФВ.Р = 360894477 рублей.
Годовые затраты на электроэнергию:
ΣСэ = 8717175 рублей.
Текущий ремонт оборудования:
ЗРЕМ = 10%*Коб*Кз = 01*12000000*0043 = 51600 руб.
ЗРЕМ = 10%*Коб*Кз = 01*18000000*0172 = 309600 руб.
ΣЗрем = 135600 + 478800 = 361200 рублей.
Внутризаводское перемещение:
Износ инструментов и приспособлений:
Ии = 5%*Коб*Кз = 005*10000000*0043 = 21500 руб.
Ии = 5%*Коб*Кз = 005*15000000*0172 = 129000 руб.
Таблица 9 – Смета расходов на содержание и эксплуатацию оборудования
Общепроизводственные расходы включают следующие затраты:
Содержание аппарата управления цеха;
Содержание прочего цехового персонала;
Амортизация зданий сооружений и инвентаря;
Содержание зданий сооружений и инвентаря;
Текущий ремонт зданий сооружений и инвентаря;
Испытания опыты и исследования;
Износ малоценного и быстроизнашивающегося инвентаря;
В связи с большой номенклатурой изготовляемых в цехе изделий рассчитать общепроизподственные расходы приходящиеся на конкретную деталь сложно. Поэтому при определении этих затрат используем следующая формула:
где Спр.пр. – годовая сумма общепроизводственных расходов по проектируемому варианту руб;
Спр.ср. – годовая сумма общепроизводственных расходов по сравниваемому варианту руб;
Зпр.ср. – основная заработная плата производственных рабочих по сравниваемому варианту руб;
Зпр.пр. – основная заработная плата производственных рабочих по проектируемому варианту руб;
Следовательно Спр.пр2 = 185*365329811 = 6758602 руб.
Спр.пр1 = 185*582087866= 10768626 руб.
После определения всех расходов связанных с изготовлением детали составляем плановую калькуляцию. Плановая калькуляция составляется на годовой объем и на единицу продукции по форме приведенной в таблице 10. В ней приводим значения показателей разработанных вариантов что позволяет дать сравнительный анализ технологического процесса механической обработки детали.
Себестоимость единицы продукции вычисляем по статьям калькуляции путем деления суммы годового выпуска по каждой статье на количество изделий по плану. При определении отчислений на социальное страхование затраты рассчитываем от суммы основной и дополнительной заработной платы производственных рабочих (40%).
Таблица 10 – Плановая калькуляция единицы продукции
Наименование статей затрат
Сравниваемый вариант
Сырье и основные материалы
Возвратные отходы (вычитаются)
Топливо и энергия на технологические цели
Основная заработная плата производственных рабочих
Дополнительная заработная плата производственных рабочих
Налоги и отчисления исчисляемые от заработной платы
Расходы на содержание и эксплуатацию оборудования
Общепроизводственные расходы
Для определения экономического эффекта сопоставляем цеховую себестоимость разнообразных вариантов технологического процесса механической обработки детали.
Эс = (С1-С2)*В(1.18)
где С1 – себестоимость изготовления детали сравниваемого варианта
С2 – себестоимость изготовления детали проектируемого варианта.
Эс = (65221-478015)*10000 = 1741948377 руб.
ПРИЛОЖЕНИЯЛитература
Курсовое проектирование по технологии машиностроения. Горбацевич А.Ф. Шкред В.А. Мн.: Высшая школа. 1983 с. 256.
Дипломное проектирование по технологии машиностроения под общ.ред. В.В.Бабука. – Минск: Высшая школа 1979.
Организация производства и управление предприятием: методические указания по выполнению курсовой работы. Машков Н.М. УО «ВГТУ» 2006г.
Единый тарифно-квалификационный справочник работ и профессий рабочих. Выпуск 2. М. Экономика. 1990.
Курсовой - Брызгалов2.doc
Учреждение образования
«Витебский государственный технологический университет»
по дисциплине «Организация планирование и управление предприятием»
на тему: «Расчет цеховой себестоимости изготовления детали»
Исполнитель: студент гр. ЗМ-49
Характеристика возможных вариантов механической обработки детали
Расчет эффективного фонда времени работы оборудования
Расчет потребного количества оборудования для выполнения производственной программы
Расчет потребного количества рабочих по профессиям разрядам и фонда их заработной платы
Расчет потребности и стоимости основных материалов
Расчет расходов на содержание и эксплуатацию оборудования
Расчет производственных расходов
Определение цеховой себестоимости изготовления детали
Расчет годового экономического эффекта разработанного варианта технологического процесса механической обработки детали
Организация производственных процессов выбор методов подготовки планирования и контроля производства во многом определяются типом производства который решающим образом влияет на эффективность использования ресурсов предприятия. Использование групповых методов обработки автоматизация и электронизация производственных процессов дают возможность применять организационные формы массового производства в серийном а иногда даже в мелкосерийном производствах.
Устойчивое развитие предприятия определяется уровнем конкурентоспособности его продукции которая в свою очередь связана с качеством и уровнем цены. Уровень цены зависит от себестоимости изготовления продукции.
В связи с этим целью данной работы является определение цеховой себестоимости изготовление детали. Кроме того цеховая себестоимость детали определяется с учетом выбранного варианта технологического процесса обеспечивающего минимум приведенных затрат по сравнению с другим технологическим процессом изготовления детали. А также приобретение навыков по расчету цеховой себестоимости изготовления детали.
Заготовка представляет собой прямоугольную гкатаную полосу ГОСТ 103-76 (40х22х12) из стали 30 ГОСТ 1050-88. Получаемая деталь имеет три отверстия диаметром 5 мм а также две зенковки диаметром 8 мм. Для детали предъявляются особые требования по шероховатости обрабатываемых поверхностей а также требования по выдерживанию соответствующих размеров указанных на чертеже детали.
При механической обработке используются два станка: вертикально-фрезерный (6Р11) и вертикально-сверлильный (2Н118).
Разрабатываем два варианта технологического процесса механической обработки.
Для определения штучного времени используем следующие формулы:
Тшт=Топ +Тоб+Тот(1.1)
где Топ – оперативное время мин.;
Тоб – время на обслуживание рабочего места мин.;
Тот – время перерывов на отдых и личные надобности мин;
где То – основное время мин.;
Тв – вспомогательное время мин.
Тв=Тус+Тзо+Туп+Тиз(1.3)
где Тус – время на установку и снятие детали мин.;
Тзо – время на закрепление и открепление детали мин.;
Туп – время на приемы управления мин.;
Тиз – время на измерение детали мин;
k – поправочный коэффициент на вспомогательное время.
5 Предварительное фрезерование поверхности (В) торцевой фрезой со снятием припуска толщиной 05 мм;
0 Предварительное фрезерование поверхности (Б) торцевой фрезой со снятием припуска толщиной 05 мм;
5 Предварительное фрезерование поверхности (А) концевой фрезой со снятием припуска толщиной 08 мм;
0 Предварительное фрезерование поверхности (Г) концевой фрезой со снятием припуска толщиной 125 мм;
5 Предварительное фрезерование поверхности (Д) концевой фрезой со снятием припуска толщиной 08 мм;
0 Предварительное фрезерование поверхности (Е) концевой фрезой со снятием припуска толщиной 125 мм;
5 Чистовое фрезерование поверхности (А) концевой фрезой со снятием припуска толщиной 04 мм;
0 Чистовое фрезерование поверхности (В) торцевой фрезой со снятием припуска толщиной 05 мм;
5 Чистовое фрезерование поверхности (Б) торцевой фрезой со снятием припуска толщиной 05 мм;
0 Сверление отверстий диаметром 5 мм спиральным сверлом в кондукторе;
5 Зенкование отверстий под головку болта диаметром 8 мм.
5 Предварительное фрезерование поверхности (А) концевой фрезой со снятием припуска толщиной 08 мм пачки из 3-х деталей;
0 Предварительное фрезерование поверхности (Г) концевой фрезой со снятием припуска толщиной 125 мм пачки из 3-х деталей;
5 Предварительное фрезерование поверхности (Д) концевой фрезой со снятием припуска толщиной 08 мм пачки из 3-х деталей;
0 Предварительное фрезерование поверхности (Е) концевой фрезой со снятием припуска толщиной 125 мм пачки из 3-х деталей;
5 Чистовое фрезерование поверхности (А) концевой фрезой со снятием припуска толщиной 04 мм пачки из 3-х деталей;
0 Сверление отверстий в пачке из 3-х деталей диаметром 5 мм спиральным сверлом в кондукторе;
5 Предварительное фрезерование поверхности
TО = 6*L*10-3 = 6*40*10-3 = 024 мин;
ТВ = 0033 + 004 + 022 + 001 = 0303 мин;
ТОП = TО + TВ = 024 + 0303 = 0543 мин;
ТОБ = 0056*0543 = 00304 мин;
ТОТ = 004*0543 = 00217 мин;
ТШТ = ТОП + ТОБ + ТОТ = 0543 + 00304 + 00217 = 05951 мин.
0 Предварительное фрезерование поверхности
TО = 6*L*10-3 = 6*212*10-3 = 01272 мин;
ТОП = TО + TВ = 01272 + 0303 = 04302 мин;
ТОБ = 0056*04302 = 00241 мин;
ТОТ = 004*04302 = 00172 мин;
ТШТ = ТОП + ТОБ + ТОТ = 04302 + 00241 + 00172 = 04715 мин.
TО = 6*L*10-3 = 6*3875*10-3 = 02325 мин;
ТОП = TО + TВ = 02325 + 0303 = 05355 мин;
ТОБ = 0056*05355 = 00299 мин;
ТОТ = 004*05355 = 00214 мин;
ТШТ = ТОП + ТОБ + ТОТ = 05355 + 00299 + 00214 = 05868 мин.
TО = 6*L*10-3 = 6*204*10-3 = 01224 мин;
ТОП = TО + TВ = 01224 + 0303 = 04254 мин;
ТОБ = 0056*04254 = 00238 мин;
ТОТ = 004*04254 = 0017 мин;
ТШТ = ТОП + ТОБ + ТОТ = 04254 + 00238 + 0017 = 04662 мин.
5 Чистовое фрезерование поверхности
TО = 4*L*10-3 = 4*375*10-3 = 015 мин;
ТОП = TО + TВ = 015 + 0303 = 0453 мин;
ТОБ = 0056*0453 = 00254 мин;
ТОТ = 004*0453 = 00181 мин;
ТШТ = ТОП + ТОБ + ТОТ = 0453 + 00254 + 00181 = 04965 мин.
0 Чистовое фрезерование поверхности
0 Сверление отверстия
ТВ = 006 + 002 + 004 + 008 = 02 мин;
ТОП = 0026 + 02 = 0226 мин;
ТОБ = 005*0226 = 00113 мин.;
ТОТ = 004*0226 = 0009 мин.;
ТШТ = 0226 + 00113 + 0009 = 02463 мин.
5 Зенкование отверстия
ТОП = 00074 + 02 = 02074 мин;
ТОБ = 005*02074 = 00104 мин.;
ТОТ = 004*02074 = 00083 мин.;
ТШТ = 02074 + 00104 + 00083 = 02261 мин.
Штучное и оперативное время для первого варианта технологического процесса механической обработки детали:
ТШТ.СВ. = 3*02463+2*02261 = 11911 мин.
ТШТ.ФР. = 3*05951+04715+05868+04662+3*04965 = 47993 мин.
ТОП.СВ. = 3*0226+2*02074 = 10928 мин.
ТОП.ФР. = 3*0543+04302+05355+04254+3*0453 = 44191 мин.
5 Предварительное фрезерование поверхности в пачке
Для одной детали ТОП = 0181 мин;
Для одной детали ТШТ = 01984 мин;
0 Предварительное фрезерование поверхности в пачке
Для одной детали ТОП = 01434 мин;
Для одной детали ТШТ = 01572 мин;
Для одной детали ТОП = 01785 мин;
Для одной детали ТШТ = 01954 мин;
Для одной детали ТОП = 01418 мин;
Для одной детали ТШТ = 01554 мин;
Для одной детали ТОП = 0151 мин;
Для одной детали ТШТ = 01655 мин;
0 Сверление отверстия в пачке
Для одной детали ТОП = 00753 мин;
Для одной детали ТШТ = 00821 мин;
Штучное и оперативное время для второго варианта технологического процесса механической обработки детали:
ТШТ.СВ. = 3*00821+2*02261 = 06985 мин.
ТШТ.ФР. = 2*05951 + 01984 + 01572 + 01954 + 01554 + 01655 + 2*04965 = =30551 мин.
ТОП.СВ. = 3*00753+2*02074 = 06407 мин.
ТОП.ФР. = 2*0543+0181+01434+01785+01418+0151+2*0453 = 27877 мин.
Принимаем второй вариант технологического процесса механической обработки детали т.к. рассчитанное штучное время во втором варианте на 22368 минуты меньше чем в первом а значит при изготовлении партии деталей из 10000 единиц затраты времени и средств будут меньше.
Экономия времени изготовления всей партии деталей составляет 3728 часов.
Проектируемый вариант (технологический процесс №2)
Величина эффективного фонда времени работы оборудования зависит от режима работы участка и времени простоя оборудования в ремонте. Число дней на ремонт определяется на основе нормативов содержащихся в “Единой системе планово-предупредительного ремонта оборудования”.
На предприятиях с прерывным производством эффективный фонд времени одного станка рассчитывается следующим образом:
Тэф=(Тк-Тв)*а*с*Ки (1.4)
где Тк – календарное число дней в году Тк = 365 дней;
Тв – количество выходных и праздничных дней в году
Тв = Твых.+Тпр.= 6+104 = 110 дней;
а – продолжительность работы одной смены а = 8 часов;
с – количество смен с = 2 смены;
Ки – коэффициент использования оборудования.
Коэффициент использования оборудования можно определить следующим образом:
где Трем – количество дней простоя оборудования во всех видах ремонта в течение года;
Ттс – количество дней технологических остановок оборудования в течении года.
Т.к. отсутствуют необходимые данные принимаем коэффициент использования равным Ки = 095.
Тогда эффективный фонд времени одного станка будет равен:
Тэф = (365-110)*8*2*095 = 3876 час.
Количество смен выбираем равным двум т. к. при данном значении потребное количество оборудования и коэффициент загрузки уменьшится вдвое а значит уменьшатся расходы на содержание и эксплуатацию оборудования но увеличится фонд заработной платы за счет доплат за работу в вечернее и ночное время. Однако экономия средств на содержание и эксплуатацию оборудования превышает расходы на заработную плату поэтому количество смен выгоднее принять равным двум.
Расчет потребного количества оборудования производится по каждой операции по формуле:
где Чр – расчетное количество станков;
ТШТ – штучное время операции;
КН – планируемый коэффициент выполнения норм штучного времени Кн=12;
В – общий годовой выпуск деталей В = 10000 шт.
Для сверлильной операции:
Определяем коэффициент загрузки на данную программу по формуле:
Чп – принятое количество станков Чп = 1.
Для фрезерной операции:
На основании данных о нормах времени и годовой программе определяется потребность по каждому виду оборудования (табл. 1).
Таблица 1 – Ведомость потребности в оборудовании
Транспор-тировка и монтаж (20% от ст-ти станка)
Полная стоимость оборудования тыс. руб.
Вертикально-сверлильный
Вертикально-фрезерный
Для расчета потребного количества рабочих занятых на нормируемых работах составляем баланс рабочего времени одного рабочего (табл. 2).
Таблица 2 – Баланс рабочего времени одного среднесписочного рабочего на 2007г.
Состав рабочего времени
Календарный фонд времени
Число нерабочих дней всего
Номинальный фонд времени
Неявки на работу всего
в т.ч. а) очередные и дополнительные отпуска
б) отпуска по беременности и родам
г) выполнение государственных и общественных обязанностей
Полезный фонд времени
Номинальная продолжительность рабочего дня
Потери времени: всего
в т.ч. а) для занятых на вредных работах и в праздничные
Средняя продолжительность рабочего дня
Эффективный фонд рабочего времени одного рабочего
После составления баланса рабочего времени подсчитываем потребное количество основных производственных рабочих численность которых зависит от трудоемкости выполнения отдельных операций.
Для расчета численности основных производственных рабочих используем штучно-калькуляционное время которое определяется по формуле:
Содержание и продолжительность подготовительно-заключительного времени (Тпз) зависит от характера производственного процесса типа производства характера труда и участия работника в осуществлении производственного процесса организации труда и обслуживании рабочего места. Тпз берется в процентах от Топ.
Тшт.к.= Тшт + 34%*Топ = 07203 мин.
Тшт.к.= Тшт + 38%*Топ = 31610 мин.
Численность основных производственных рабочих определяется по формуле:
Чсд = = 00556 чел.(1.9)
Таблица 3 – Расчет численности рабочих занятых на нормируемых работах
годовой программы с учетом выполнения норм выработки час
Номиналь-ный фонд времени одного рабочего час
Явоч-ное число рабо-чих чел
Полезный фонд времени одного рабочего час
Списоч-ное число рабочих чел
После определения численности рабочих рассчитываем фонд заработной платы.
Определяем часовую тарифную ставку по формуле:
где МТС – минимальная тарифная ставка 1 разряда МТС=65000руб.;
Ктар – тарифный коэффициент;
Тмес – месячный фонд рабочего времени одного рабочего
Тмес = 22*8 = 176час.
Таблица 4 – Расчет заработной платы рабочих занятых на нормируемых работах
Наименование операции
Час. тарифная ставка
Трудоемкость произв. прог-
Тарифный фонд зар. платы руб.
Годовой фонд заработной платы
по премиальн. системам
за работу в вечерн. время
за работу в ночное время
Трудоемкость производственной программы:
Тарифный фонд заработной платы:
Размер доплат по премиальной системе (25% от тарифного фонда заработной платы):
ЗПДОП.СЛ=025*ТФСВ=025*59853128 = 14963282 руб;
ЗПДОП.ФР=025*ТФФР=025*305476683 = 76369171 руб;
Доплаты за работу в вечернее и ночное время соответственно равны (1 смена – 8.00 – 17.00; 2 смена – 17.00 – 01.00):
Оплата отпусков составляет 15% от тарифного фонда заработной платы:
ЗПОТ.СВ=015*ТФСВ=015*59853128 = 8977969 руб;
ЗПОТ.ФР=015*ТФФР=015*305476683 = 45821502 руб;
Годовой фонд заработной платы равен сумме тарифного фонда заработной платы и общей суммы доплат по премиальной системе за работу в ночное и вечернее время а также оплата отпусков.
При расчете потребностей и стоимости сырья и материалов учитываются все затраты на сырье и материалы необходимые для изготовления данной детали с учетом транспортно-заготовительных расходов (10% от стоимости материала).
В общем виде затраты по этой статье можно определить по формуле:
Зм = (Цм*Нм*Ктз – Цо*Но)*В(1.11)
где Зм – затраты на сырье и материалы;
Цм – оптовая цена материала за 1кг Цм = 2000 руб.;
Нм – норма расхода материала на единицу продукции Нм = mзаг= 00829 кг;
Ктз – коэффициент транспортно-заготовительных расходов Ктз = 11;
Цо – цена возвратных отходов на 1кг Цо = 01*Цм = 200 руб.;
Но – вес возвратных отходов на единицу продукции
Тогда затраты на сырье и материалы будут равны:
Зм = (2000*00829*11–200*00301)*10000 = 1763600 руб.
1 Амортизация оборудования и транспортных средств
Затраты на амортизацию оборудования транспортных средств и ценного инструмента определяем исходя из первоначальной их стоимости и действующих годовых норм амортизационных отчислений.
где Коб – полная первоначальная стоимость оборудования и транспортных средств;
НА – норма амортизационных отчислений НА=141% [2 c.10];
Кз – коэффициент загрузки оборудования.
Для сверлильного станка:
Ао = 12000000*0141*0025 = 42300 руб.
Для фрезерного станка:
Ао = 18000000*0141*0109 = 276642 руб.
2 Эксплуатация оборудования
2.1 Стоимость смазочных обтирочных материалов эмульсий для охлаждения и прочих вспомогательных материалов необходимых для ухода за оборудованием и содержанием его в исправном состоянии определяется его нормативом или по формуле:
См.в.=Нр*До*Цм.в(1.13)
где Нр – годовая норма расхода материала на единицу оборудования;
До – количество единиц оборудования;
Цм.в. – цена единицы вспомогательного материала.
При отсутствии необходимых данных ориентированно затраты на вспомогательные материалы вычисляются из расчета 3% стоимости станка (необходимо учесть коэффициент загрузки оборудования).
См.в.=10000000*0025*003 = 7500 руб.
См.в.=15000000*0109*003 = 49050 руб.
ΣСм.в. = 56550 рублей.
2.2 Основная и дополнительная заработная плата вспомогательных рабочих обслуживающих оборудование (наладчиков электромонтеров слесарей ремонтных рабочих и др.) зависит от численности рабочих и составляет 40% годового фонда заработной платы основных рабочих.
Для вертикально-сверлильного станка:
ФВ.Р = 04*92772349 = 3710894 руб.
Для вертикально-фрезерного станка:
ФВ.Р = 04* 473488858 = 189395543 руб.
Σ ФВ.Р = 226504483 рубля.
2.3 Годовые затраты на электроэнергию можно определить по формуле:
где Муст – суммарная мощность электродвигателей установленных на оборудовании;
Тэф – эффективный фонд времени работы оборудования Тэф = 3876 ч;
Цэ – плата за 1кВт-час электроэнергии Цэ = 150 руб;
Кр – коэффициент одновременной работы двигателя станка;
Кз – коэффициент загрузки оборудования;
Кп – коэффициент учитывающий потери в сети Кп=095;
Кд – КПД электродвигателей.
ΣСэ = 5508765 рублей.
3 Текущий ремонт оборудования
В затратах на текущий ремонт оборудования учитываются в основном расходы связанные с приобретением для текущего ремонта запасных частей и других материалов а также основная и дополнительная заработная плата с отчислениями на социальное страхование рабочих (40%) занятых ремонтом оборудования. При отсутствии необходимых данных затраты по этой статье можно ориентировочно принять 10% от стоимости оборудования включая транспортно-заготовительные расходы. Кроме того необходимо учесть коэффициент загрузки оборудования.
ЗРЕМ = 10%*Коб*Кз = 01*12000000*0025 = 30000 руб.
ЗРЕМ = 10%*Коб*Кз = 01*18000000*0109 = 196200 руб.
ΣЗрем = 226200 рублей.
4 Внутризаводское перемещение
Затраты по статье “Внутризаводское перемещение” вычисляются из грузооборота для перевозки деталей и стоимости перемещения 1 тонны груза принимаемой по данным предприятия по формуле:
где Нм – норма расхода материала на единицу продукции Нм = 00829кг;
В – годовая программа выпуска В = 10000 шт;
Кпер – коэффициент перемещения груза Кпер = количество станков+1=2;
Спер – стоимость перемещения одной тонны груза Спер = 30000 руб.
ЗПЕР = = 74610 рублей.
5 Износ малоценных и быстроизнашивающихся инструментов и приспособлений
Сумма износа малоценных и быстроизнашивающихся инструментов и приспособлений определяется по данным предприятия или приближенно – 5% стоимости станка. При расчете необходимо учесть коэффициент загрузки оборудования.
Ии = 5%*Коб*Кз = 005*10000000*0025 = 12500 руб.
Ии = 5%*Коб*Кз = 005*15000000*0109 = 81750 руб.
Итог по статье “Расходы на содержание и эксплуатацию оборудования” определяется как сумма затрат по пунктам 6.1 и 6.5. Результаты расчета сводим в таблицу 5.
Таблица 5 – Смета расходов на содержание и эксплуатацию оборудования
Наименование статей расходов
Амортизация оборудования и транспортных средств
Эксплуатация оборудования
Текущий ремонт оборудования
Внутризаводское перемещение грузов
Износ малоценных и быстроизнашивающихся инструментов и приспособлений
Сравниваемый вариант (технологический процесс №1)
Эффективный фонд времени одного станка будет равен:
Расчет потребного количества оборудования:
Таблица 6 – Ведомость потребности в оборудовании
Таблица 7 – Расчет численности рабочих занятых на нормируемых работах
Таблица 8 – Расчет заработной платы рабочих занятых на нормируемых работах
ЗПДОП.СВ=025*ТФСВ=025*10206382 = 25515955 руб;
ЗПДОП.ФР=025*ТФФР=025*480024046 = 120006012 руб;
ЗПОТ.СВ=015*ТФСВ=015*10206382 = 15309573 руб;
ЗПОТ.ФР=015*ТФФР=015*480024046 = 72003607 руб;
Амортизация оборудования и транспортных средств:
Ао = 12000000*0141*0043 = 72756 руб.
Ао = 18000000*0141*0172 = 436536 руб.
ΣАо = 509292 рублей.
Эксплуатация оборудования:
См.в.=10000000*0043*003 = 12900 руб.
См.в.=15000000*0172*003 = 77400 руб.
ΣСм.в. = 90300 рублей.
Основная и дополнительная заработная плата вспомогательных рабочих:
ФВ.Р = 04*158198921 = 63279568 руб.
ФВ.Р = 04*744037272 = 297614909 руб.
Σ ФВ.Р = 360894477 рублей.
Годовые затраты на электроэнергию:
ΣСэ = 8717175 рублей.
Текущий ремонт оборудования:
ЗРЕМ = 10%*Коб*Кз = 01*12000000*0043 = 51600 руб.
ЗРЕМ = 10%*Коб*Кз = 01*18000000*0172 = 309600 руб.
ΣЗрем = 135600 + 478800 = 361200 рублей.
Внутризаводское перемещение:
Износ инструментов и приспособлений:
Ии = 5%*Коб*Кз = 005*10000000*0043 = 21500 руб.
Ии = 5%*Коб*Кз = 005*15000000*0172 = 129000 руб.
Таблица 9 – Смета расходов на содержание и эксплуатацию оборудования
Общепроизводственные расходы включают следующие затраты:
Содержание аппарата управления цеха;
Содержание прочего цехового персонала;
Амортизация зданий сооружений и инвентаря;
Содержание зданий сооружений и инвентаря;
Текущий ремонт зданий сооружений и инвентаря;
Испытания опыты и исследования;
Износ малоценного и быстроизнашивающегося инвентаря;
В связи с большой номенклатурой изготовляемых в цехе изделий рассчитать общепроизподственные расходы приходящиеся на конкретную деталь сложно. Поэтому при определении этих затрат используем следующая формула:
где Спр.пр. – годовая сумма общепроизводственных расходов по проектируемому варианту руб;
Спр.ср. – годовая сумма общепроизводственных расходов по сравниваемому варианту руб;
Зпр.ср. – основная заработная плата производственных рабочих по сравниваемому варианту руб;
Зпр.пр. – основная заработная плата производственных рабочих по проектируемому варианту руб;
Следовательно Спр.пр2 = 185*365329811 = 6758602 руб.
Спр.пр1 = 185*582087866= 10768626 руб.
После определения всех расходов связанных с изготовлением детали составляем плановую калькуляцию. Плановая калькуляция составляется на годовой объем и на единицу продукции по форме приведенной в таблице 10. В ней приводим значения показателей разработанных вариантов что позволяет дать сравнительный анализ технологического процесса механической обработки детали.
Себестоимость единицы продукции вычисляем по статьям калькуляции путем деления суммы годового выпуска по каждой статье на количество изделий по плану. При определении отчислений на социальное страхование затраты рассчитываем от суммы основной и дополнительной заработной платы производственных рабочих (40%).
Таблица 10 – Плановая калькуляция единицы продукции
Наименование статей затрат
Сравниваемый вариант
Сырье и основные материалы
Возвратные отходы (вычитаются)
Топливо и энергия на технологические цели
Основная заработная плата производственных рабочих
Дополнительная заработная плата производственных рабочих
Налоги и отчисления исчисляемые от заработной платы
Расходы на содержание и эксплуатацию оборудования
Общепроизводственные расходы
Для определения экономического эффекта сопоставляем цеховую себестоимость разнообразных вариантов технологического процесса механической обработки детали.
Эс = (С1-С2)*В(1.18)
где С1 – себестоимость изготовления детали сравниваемого варианта
С2 – себестоимость изготовления детали проектируемого варианта.
Эс = (65221-478015)*10000 = 1741948377 руб.
Курсовое проектирование по технологии машиностроения. Горбацевич А.Ф. Шкред В.А. Мн.: Высшая школа. 1983 с. 256.
Дипломное проектирование по технологии машиностроения под общ.ред. В.В.Бабука. – Минск: Высшая школа 1979.
Организация производства и управление предприятием: методические указания по выполнению курсовой работы. Машков Н.М. УО «ВГТУ» 2006г.
Единый тарифно-квалификационный справочник работ и профессий рабочих. Выпуск 2. М. Экономика. 1990.
Телефоны ВГТУ.doc
Профком преподавателей и сотрудников
Миронович Евгений Григорьевич
ГУСАКОВА Лариса Николаевна
Силкин Евгений Владимирович
АДМИНИСТРАТИВНАЯ ЧАСТЬ
ПЕТУХОВ Виталий Викторович
АНДРЕЕВА Ирина Викторовна
Зав. производственной практикой
ГУЩЕНКО Александр Иванович
БАРКОВСКАЯ Эмма Николаевна
Социально-экономический отдел
КРЮКОВСКАЯ Алла Васильевна
МИХЛИНА Ирина Владимировна
Отдел воспитательной работы
Коженец Татьяна Николаевна
Ведущий социальный педагог
Драненко Тереса Викторовна
ШКРАБОВА Лилия Петровна
ТИТОВЕЦ Татьяна Александровна
ЛИПСКИЙ Александр Владимирович
БЫЦКАЯ Любовь Ивановна
РАДАЕВА Тамара Стапановна
НАУЧНО-ИССЛЕДОВАТЕЛЬСКИЙ СЕКТОР
БЕЛИКОВ Сергей Александрович
СКРОБОВА Алина Сергеевна
Испытательный центр
продукции текстильной
и легкой промышленности
ШЕВЕРИНОВА Лилия Николаевна
ЦЕНТР ИНФОРМАЦИОННЫХ ТЕХНОЛОГИЙ
МИРОНОВИЧ Евгений Григорьевич
Минаев Олег Анатольевич
ЛЕОНОВ Александр Владимирович
Сектор программирования
ЛЮБОЧКО Николай Сергеевич
РЕГИОНАЛЬНЫЙ ЦЕНТР ТЕСТИРОВАНИЯ
СУВОРОВ Александр Павлович
ДРЮКОВА Галина Николаевна
Механико-технологический
Дрюков Василий Васильевич
КОЖЕМСКАЯ Алевтина Степановна
Художественно-технологический
Рубаник Василий Васильевич
РЫБАЧЕНОК Галина Евгеньевна
Конструкторско-технологический
СМЕЛКОВ Виталий Константинович
Котикова Юлия Юрьевна
ШАРСТНЕВ Владимир Леонидович
САМУСЕНКО Лариса Степановна
ТИМОФЕЕВ Анатолий Михайлович
МАРШАЛКОВА Жанна Васильевна
Довузовской подготовки и профориетации
СТЕПАНОВА Елена Владиславовна
Повышения квалификации и переподготовки кадров
Семенчукова Ирина Юзефовна
ДИКУН Тамара Михайловна
Автоматизации технологических процессов и производств
Смелков Дмитрий Витальевич
БАТАЛКО Тамара Ивановна
КАЗАРНОВСКАЯ Галина Васильевна
СКОКОВ Павел Иванович
ПИОТУХ Анатолий Антонович
Кунцевич Сергей Петрович
Конструирования и технологии одежды
ТРУТЧЕНКО Любовь Ивановна
Машин и аппаратов легкой промышленности
СУНКУЕВ Борис Семенович
Машин и технологий высокоэффективных процессов обработки
КЛИМЕНКОВ Степан Степанович
Охраны труда и промэкологии
КОВЧУР Сергей Григорьевич
Прядения натуральныхи химических волокон
КОГАН Александр Григорьевич
Сопротивления материалов и деталей машин
ФЕДОСЕЕВ Гелий Николаевич
Теоретической и прикладной математики
ДЖЕЖОРА Александр Александрович
Теоретической механики и теории механизмов и машин
ЛОКТИОНОВ Анатолий Васильевич
Технологии и конструирования изделий из кожи
ГОРБАЧИК Владимир Евгеньевич
Технологии и оборудования машиностроительного производства
ОЛЬШАНСКИЙ Валерий Иосифович
Технологии трикотажного производства
ЧАРКОВСКИЙ Александр Владимирович
Иванова Татьяна Петровна
БУРКИН Александр Николаевич
КАСАЕВА Тамара Васильевна
Ванкевич Елена Васильевна
Коммерческой деятельности
ПРОКОФЬЕВА Нина Леонидовна
Экономической теории и маркетинга
ВЕДЕНИН Геннадий Александрович
ФЕДОРОВ Вениамин Владимирович
Чеснокова Ольга Ивановна
РУБАНИК Василий Васильевич
ПЛАТОНОВ Александр Петрович
ПРОЧИЕ ПОДРАЗДЕЛЕНИЯ
ЧЕПЕЛКИНА Тамара Александровна
БОДРОВА Людмила Дмитриевна
ЛЯТОХА Лидия Митрофановна
БЕЗБОЖНЫЙ Дмитрий Васильевич
ЕРШОВА Елена Николаевна
КОЗИК Татьяна Александровна
ХОРОШЕВА Нина Ивановна
КУНДЕР Мария Адамовна
Санаторий-профилакторий
КОЗАЧЕНКО Любовь Дмитриевна
САМУХИН Павел Михайлович
РКЦ «Белгазпромбанк»
ОРЛОВА Галина Петровна
Экспериментально-опытное предприятие УО «ВГТУ»
МАЩЕНКО Андрей Сергеевич
ДАДЕКО Тамара Михайловна
ЕФРЕМОВА Валентина Николаевна
БОРИСЕНКО Вячеслав Владимирович
Зам. директора по коммерческим вопросам
ИВАНОВСКАЯ Людмила Алексеевна
БАШМЕТОВ Валерий Степанович
МАЛАШЕНКОВ Сергей Иванович
ШВИЛО Лариса Георгиевна
Проректор по научной работе
Владислав Владимирович
Проректор по социально-экономическим вопросам и капит. строительству
РЫКЛИН Борис Ефимович
ШУТ Алексей Николаевич
Проректор по воспитательной работе
БЕЛОВ Анатолий Алексеевич
Титульник к АТТП.doc
Учреждение образования
«Витебский государственный технологический университет»
КОНТРОЛЬНАЯ РАБОТА №1
по дисциплине : «Автоматизация процессов производства»
Курсовой - Брызгалов_копия.doc
Учреждение образования
«Витебский государственный технологический университет»
по дисциплине «Организация планирование и управление предприятием»
на тему: «Расчет цеховой себестоимости изготовления детали»
Исполнитель: студент гр. ЗМ-49
Характеристика возможных вариантов механической обработки детали
Расчет эффективного фонда времени работы оборудования
Расчет потребного количества оборудования для выполнения производственной программы
Расчет потребного количества рабочих по профессиям разрядам и фонда их заработной платы
Расчет потребности и стоимости основных материалов
Расчет расходов на содержание и эксплуатацию оборудования
Расчет производственных расходов
Определение цеховой себестоимости изготовления детали
Расчет годового экономического эффекта разработанного варианта технологического процесса механической обработки детали
Организация производственных процессов выбор методов подготовки планирования и контроля производства во многом определяются типом производства который решающим образом влияет на эффективность использования ресурсов предприятия. Использование групповых методов обработки автоматизация и электронизация производственных процессов дают возможность применять организационные формы массового производства в серийном а иногда даже в мелкосерийном производствах.
Устойчивое развитие предприятия определяется уровнем конкурентоспособности его продукции которая в свою очередь связана с качеством и уровнем цены. Уровень цены зависит от себестоимости изготовления продукции.
В связи с этим целью данной работы является определение цеховой себестоимости изготовление детали. Кроме того цеховая себестоимость детали определяется с учетом выбранного варианта технологического процесса обеспечивающего минимум приведенных затрат по сравнению с другим технологическим процессом изготовления детали. А также приобретение навыков по расчету цеховой себестоимости изготовления детали.
Заготовка представляет собой прямоугольную гкатаную полосу ГОСТ 103-76 (40х22х12) из стали 30 ГОСТ 1050-88. Получаемая деталь имеет три отверстия диаметром 5 мм а также две зенковки диаметром 8 мм. Для детали предъявляются особые требования по шероховатости обрабатываемых поверхностей а также требования по выдерживанию соответствующих размеров указанных на чертеже детали.
При механической обработке используются два станка: вертикально-фрезерный (6Р11) и вертикально-сверлильный (2Н118).
Разрабатываем два варианта технологического процесса механической обработки.
Для определения штучного времени используем следующие формулы:
Тшт=Топ +Тоб+Тот(1.1)
где Топ – оперативное время мин.;
Тоб – время на обслуживание рабочего места мин.;
Тот – время перерывов на отдых и личные надобности мин;
где То – основное время мин.;
Тв – вспомогательное время мин.
Тв=Тус+Тзо+Туп+Тиз(1.3)
где Тус – время на установку и снятие детали мин.;
Тзо – время на закрепление и открепление детали мин.;
Туп – время на приемы управления мин.;
Тиз – время на измерение детали мин;
k – поправочный коэффициент на вспомогательное время.
5 Предварительное фрезерование поверхности (В) торцевой фрезой со снятием припуска толщиной 05 мм;
0 Предварительное фрезерование поверхности (Б) торцевой фрезой со снятием припуска толщиной 05 мм;
5 Предварительное фрезерование поверхности (А) концевой фрезой со снятием припуска толщиной 08 мм;
0 Предварительное фрезерование поверхности (Г) концевой фрезой со снятием припуска толщиной 125 мм;
5 Предварительное фрезерование поверхности (Д) концевой фрезой со снятием припуска толщиной 08 мм;
0 Предварительное фрезерование поверхности (Е) концевой фрезой со снятием припуска толщиной 125 мм;
5 Чистовое фрезерование поверхности (А) концевой фрезой со снятием припуска толщиной 04 мм;
0 Чистовое фрезерование поверхности (В) торцевой фрезой со снятием припуска толщиной 05 мм;
5 Чистовое фрезерование поверхности (Б) торцевой фрезой со снятием припуска толщиной 05 мм;
0 Сверление отверстий диаметром 5 мм спиральным сверлом в кондукторе;
5 Зенкование отверстий под головку болта диаметром 8 мм.
5 Предварительное фрезерование поверхности (А) концевой фрезой со снятием припуска толщиной 08 мм пачки из 3-х деталей;
0 Предварительное фрезерование поверхности (Г) концевой фрезой со снятием припуска толщиной 125 мм пачки из 3-х деталей;
5 Предварительное фрезерование поверхности (Д) концевой фрезой со снятием припуска толщиной 08 мм пачки из 3-х деталей;
0 Предварительное фрезерование поверхности (Е) концевой фрезой со снятием припуска толщиной 125 мм пачки из 3-х деталей;
5 Чистовое фрезерование поверхности (А) концевой фрезой со снятием припуска толщиной 04 мм пачки из 3-х деталей;
0 Сверление отверстий в пачке из 3-х деталей диаметром 5 мм спиральным сверлом в кондукторе;
5 Предварительное фрезерование поверхности
TО = 6*L*10-3 = 6*40*10-3 = 024 мин;
ТВ = 0033 + 004 + 022 + 001 = 0303 мин;
ТОП = TО + TВ = 024 + 0303 = 0543 мин;
ТОБ = 0056*0543 = 00304 мин;
ТОТ = 004*0543 = 00217 мин;
ТШТ = ТОП + ТОБ + ТОТ = 0543 + 00304 + 00217 = 05951 мин.
0 Предварительное фрезерование поверхности
TО = 6*L*10-3 = 6*212*10-3 = 01272 мин;
ТОП = TО + TВ = 01272 + 0303 = 04302 мин;
ТОБ = 0056*04302 = 00241 мин;
ТОТ = 004*04302 = 00172 мин;
ТШТ = ТОП + ТОБ + ТОТ = 04302 + 00241 + 00172 = 04715 мин.
TО = 6*L*10-3 = 6*3875*10-3 = 02325 мин;
ТОП = TО + TВ = 02325 + 0303 = 05355 мин;
ТОБ = 0056*05355 = 00299 мин;
ТОТ = 004*05355 = 00214 мин;
ТШТ = ТОП + ТОБ + ТОТ = 05355 + 00299 + 00214 = 05868 мин.
TО = 6*L*10-3 = 6*204*10-3 = 01224 мин;
ТОП = TО + TВ = 01224 + 0303 = 04254 мин;
ТОБ = 0056*04254 = 00238 мин;
ТОТ = 004*04254 = 0017 мин;
ТШТ = ТОП + ТОБ + ТОТ = 04254 + 00238 + 0017 = 04662 мин.
5 Чистовое фрезерование поверхности
TО = 4*L*10-3 = 4*375*10-3 = 015 мин;
ТОП = TО + TВ = 015 + 0303 = 0453 мин;
ТОБ = 0056*0453 = 00254 мин;
ТОТ = 004*0453 = 00181 мин;
ТШТ = ТОП + ТОБ + ТОТ = 0453 + 00254 + 00181 = 04965 мин.
0 Чистовое фрезерование поверхности
0 Сверление отверстия
ТВ = 006 + 002 + 004 + 008 = 02 мин;
ТОП = 0026 + 02 = 0226 мин;
ТОБ = 005*0226 = 00113 мин.;
ТОТ = 004*0226 = 0009 мин.;
ТШТ = 0226 + 00113 + 0009 = 02463 мин.
5 Зенкование отверстия
ТОП = 00074 + 02 = 02074 мин;
ТОБ = 005*02074 = 00104 мин.;
ТОТ = 004*02074 = 00083 мин.;
ТШТ = 02074 + 00104 + 00083 = 02261 мин.
Штучное и оперативное время для первого варианта технологического процесса механической обработки детали:
ТШТ.СВ. = 3*02463+2*02261 = 11911 мин.
ТШТ.ФР. = 3*05951+04715+05868+04662+3*04965 = 47993 мин.
ТОП.СВ. = 3*0226+2*02074 = 10928 мин.
ТОП.ФР. = 3*0543+04302+05355+04254+3*0453 = 44191 мин.
5 Предварительное фрезерование поверхности в пачке
Для одной детали ТОП = 0181 мин;
Для одной детали ТШТ = 01984 мин;
0 Предварительное фрезерование поверхности в пачке
Для одной детали ТОП = 01434 мин;
Для одной детали ТШТ = 01572 мин;
Для одной детали ТОП = 01785 мин;
Для одной детали ТШТ = 01954 мин;
Для одной детали ТОП = 01418 мин;
Для одной детали ТШТ = 01554 мин;
Для одной детали ТОП = 0151 мин;
Для одной детали ТШТ = 01655 мин;
0 Сверление отверстия в пачке
Для одной детали ТОП = 00753 мин;
Для одной детали ТШТ = 00821 мин;
Штучное и оперативное время для второго варианта технологического процесса механической обработки детали:
ТШТ.СВ. = 3*00821+2*02261 = 06985 мин.
ТШТ.ФР. = 2*05951 + 01984 + 01572 + 01954 + 01554 + 01655 + 2*04965 = =30551 мин.
ТОП.СВ. = 3*00753+2*02074 = 06407 мин.
ТОП.ФР. = 2*0543+0181+01434+01785+01418+0151+2*0453 = 27877 мин.
Принимаем второй вариант технологического процесса механической обработки детали т.к. рассчитанное штучное время во втором варианте на 22368 минуты меньше чем в первом а значит при изготовлении партии деталей из 10000 единиц затраты времени и средств будут меньше.
Экономия времени изготовления всей партии деталей составляет 3728 часов.
Проектируемый вариант (технологический процесс №2)
Величина эффективного фонда времени работы оборудования зависит от режима работы участка и времени простоя оборудования в ремонте. Число дней на ремонт определяется на основе нормативов содержащихся в “Единой системе планово-предупредительного ремонта оборудования”.
На предприятиях с прерывным производством эффективный фонд времени одного станка рассчитывается следующим образом:
Тэф=(Тк-Тв)*а*с*Ки (1.4)
где Тк – календарное число дней в году Тк = 365 дней;
Тв – количество выходных и праздничных дней в году
Тв = Твых.+Тпр.= 6+104 = 110 дней;
а – продолжительность работы одной смены а = 8 часов;
с – количество смен с = 2 смены;
Ки – коэффициент использования оборудования.
Коэффициент использования оборудования можно определить следующим образом:
где Трем – количество дней простоя оборудования во всех видах ремонта в течение года;
Ттс – количество дней технологических остановок оборудования в течении года.
Т.к. отсутствуют необходимые данные принимаем коэффициент использования равным Ки = 095.
Тогда эффективный фонд времени одного станка будет равен:
Тэф = (365-110)*8*2*095 = 3876 час.
Количество смен выбираем равным двум т. к. при данном значении потребное количество оборудования и коэффициент загрузки уменьшится вдвое а значит уменьшатся расходы на содержание и эксплуатацию оборудования но увеличится фонд заработной платы за счет доплат за работу в вечернее и ночное время. Однако экономия средств на содержание и эксплуатацию оборудования превышает расходы на заработную плату поэтому количество смен выгоднее принять равным двум.
Расчет потребного количества оборудования производится по каждой операции по формуле:
где Чр – расчетное количество станков;
ТШТ – штучное время операции;
КН – планируемый коэффициент выполнения норм штучного времени Кн=12;
В – общий годовой выпуск деталей В = 10000 шт.
Для сверлильной операции:
Определяем коэффициент загрузки на данную программу по формуле:
Чп – принятое количество станков Чп = 1.
Для фрезерной операции:
На основании данных о нормах времени и годовой программе определяется потребность по каждому виду оборудования (табл. 1).
Таблица 1 – Ведомость потребности в оборудовании
Транспор-тировка и монтаж (20% от ст-ти станка)
Полная стоимость оборудования тыс. руб.
Вертикально-сверлильный
Вертикально-фрезерный
Для расчета потребного количества рабочих занятых на нормируемых работах составляем баланс рабочего времени одного рабочего (табл. 2).
Таблица 2 – Баланс рабочего времени одного среднесписочного рабочего на 2007г.
Состав рабочего времени
Календарный фонд времени
Число нерабочих дней всего
Номинальный фонд времени
Неявки на работу всего
в т.ч. а) очередные и дополнительные отпуска
б) отпуска по беременности и родам
г) выполнение государственных и общественных обязанностей
Полезный фонд времени
Номинальная продолжительность рабочего дня
Потери времени: всего
в т.ч. а) для занятых на вредных работах и в праздничные
Средняя продолжительность рабочего дня
Эффективный фонд рабочего времени одного рабочего
После составления баланса рабочего времени подсчитываем потребное количество основных производственных рабочих численность которых зависит от трудоемкости выполнения отдельных операций.
Для расчета численности основных производственных рабочих используем штучно-калькуляционное время которое определяется по формуле:
Содержание и продолжительность подготовительно-заключительного времени (Тпз) зависит от характера производственного процесса типа производства характера труда и участия работника в осуществлении производственного процесса организации труда и обслуживании рабочего места. Тпз берется в процентах от Топ.
Тшт.к.= Тшт + 34%*Топ = 07203 мин.
Тшт.к.= Тшт + 38%*Топ = 31610 мин.
Численность основных производственных рабочих определяется по формуле:
Чсд = = 00556 чел.(1.9)
Таблица 3 – Расчет численности рабочих занятых на нормируемых работах
годовой программы с учетом выполнения норм выработки час
Номиналь-ный фонд времени одного рабочего час
Явоч-ное число рабо-чих чел
Полезный фонд времени одного рабочего час
Списоч-ное число рабочих чел
После определения численности рабочих рассчитываем фонд заработной платы.
Определяем часовую тарифную ставку по формуле:
где МТС – минимальная тарифная ставка 1 разряда МТС=65000руб.;
Ктар – тарифный коэффициент;
Тмес – месячный фонд рабочего времени одного рабочего
Тмес = 22*8 = 176час.
Таблица 4 – Расчет заработной платы рабочих занятых на нормируемых работах
Наименование операции
Час. тарифная ставка
Трудоемкость произв. прог-
Тарифный фонд зар. платы руб.
Годовой фонд заработной платы
по премиальн. системам
за работу в вечерн. время
за работу в ночное время
Трудоемкость производственной программы:
Тарифный фонд заработной платы:
Размер доплат по премиальной системе (25% от тарифного фонда заработной платы):
ЗПДОП.СЛ=025*ТФСВ=025*59853128 = 14963282 руб;
ЗПДОП.ФР=025*ТФФР=025*305476683 = 76369171 руб;
Доплаты за работу в вечернее и ночное время соответственно равны (1 смена – 8.00 – 17.00; 2 смена – 17.00 – 01.00):
Оплата отпусков составляет 15% от тарифного фонда заработной платы:
ЗПОТ.СВ=015*ТФСВ=015*59853128 = 8977969 руб;
ЗПОТ.ФР=015*ТФФР=015*305476683 = 45821502 руб;
Годовой фонд заработной платы равен сумме тарифного фонда заработной платы и общей суммы доплат по премиальной системе за работу в ночное и вечернее время а также оплата отпусков.
При расчете потребностей и стоимости сырья и материалов учитываются все затраты на сырье и материалы необходимые для изготовления данной детали с учетом транспортно-заготовительных расходов (10% от стоимости материала).
В общем виде затраты по этой статье можно определить по формуле:
Зм = (Цм*Нм*Ктз – Цо*Но)*В(1.11)
где Зм – затраты на сырье и материалы;
Цм – оптовая цена материала за 1кг Цм = 2000 руб.;
Нм – норма расхода материала на единицу продукции Нм = mзаг= 00829 кг;
Ктз – коэффициент транспортно-заготовительных расходов Ктз = 11;
Цо – цена возвратных отходов на 1кг Цо = 01*Цм = 200 руб.;
Но – вес возвратных отходов на единицу продукции
Тогда затраты на сырье и материалы будут равны:
Зм = (2000*00829*11–200*00301)*10000 = 1763600 руб.
1 Амортизация оборудования и транспортных средств
Затраты на амортизацию оборудования транспортных средств и ценного инструмента определяем исходя из первоначальной их стоимости и действующих годовых норм амортизационных отчислений.
где Коб – полная первоначальная стоимость оборудования и транспортных средств;
НА – норма амортизационных отчислений НА=141% [2 c.10];
Кз – коэффициент загрузки оборудования.
Для сверлильного станка:
Ао = 12000000*0141*0025 = 42300 руб.
Для фрезерного станка:
Ао = 18000000*0141*0109 = 276642 руб.
2 Эксплуатация оборудования
2.1 Стоимость смазочных обтирочных материалов эмульсий для охлаждения и прочих вспомогательных материалов необходимых для ухода за оборудованием и содержанием его в исправном состоянии определяется его нормативом или по формуле:
См.в.=Нр*До*Цм.в(1.13)
где Нр – годовая норма расхода материала на единицу оборудования;
До – количество единиц оборудования;
Цм.в. – цена единицы вспомогательного материала.
При отсутствии необходимых данных ориентированно затраты на вспомогательные материалы вычисляются из расчета 3% стоимости станка (необходимо учесть коэффициент загрузки оборудования).
См.в.=10000000*0025*003 = 7500 руб.
См.в.=15000000*0109*003 = 49050 руб.
ΣСм.в. = 56550 рублей.
2.2 Основная и дополнительная заработная плата вспомогательных рабочих обслуживающих оборудование (наладчиков электромонтеров слесарей ремонтных рабочих и др.) зависит от численности рабочих и составляет 40% годового фонда заработной платы основных рабочих.
Для вертикально-сверлильного станка:
ФВ.Р = 04*92772349 = 3710894 руб.
Для вертикально-фрезерного станка:
ФВ.Р = 04* 473488858 = 189395543 руб.
Σ ФВ.Р = 226504483 рубля.
2.3 Годовые затраты на электроэнергию можно определить по формуле:
где Муст – суммарная мощность электродвигателей установленных на оборудовании;
Тэф – эффективный фонд времени работы оборудования Тэф = 3876 ч;
Цэ – плата за 1кВт-час электроэнергии Цэ = 150 руб;
Кр – коэффициент одновременной работы двигателя станка;
Кз – коэффициент загрузки оборудования;
Кп – коэффициент учитывающий потери в сети Кп=095;
Кд – КПД электродвигателей.
ΣСэ = 5508765 рублей.
3 Текущий ремонт оборудования
В затратах на текущий ремонт оборудования учитываются в основном расходы связанные с приобретением для текущего ремонта запасных частей и других материалов а также основная и дополнительная заработная плата с отчислениями на социальное страхование рабочих (40%) занятых ремонтом оборудования. При отсутствии необходимых данных затраты по этой статье можно ориентировочно принять 10% от стоимости оборудования включая транспортно-заготовительные расходы. Кроме того необходимо учесть коэффициент загрузки оборудования.
ЗРЕМ = 10%*Коб*Кз = 01*12000000*0025 = 30000 руб.
ЗРЕМ = 10%*Коб*Кз = 01*18000000*0109 = 196200 руб.
ΣЗрем = 226200 рублей.
4 Внутризаводское перемещение
Затраты по статье “Внутризаводское перемещение” вычисляются из грузооборота для перевозки деталей и стоимости перемещения 1 тонны груза принимаемой по данным предприятия по формуле:
где Нм – норма расхода материала на единицу продукции Нм = 00829кг;
В – годовая программа выпуска В = 10000 шт;
Кпер – коэффициент перемещения груза Кпер = количество станков+1=2;
Спер – стоимость перемещения одной тонны груза Спер = 30000 руб.
ЗПЕР = = 74610 рублей.
5 Износ малоценных и быстроизнашивающихся инструментов и приспособлений
Сумма износа малоценных и быстроизнашивающихся инструментов и приспособлений определяется по данным предприятия или приближенно – 5% стоимости станка. При расчете необходимо учесть коэффициент загрузки оборудования.
Ии = 5%*Коб*Кз = 005*10000000*0025 = 12500 руб.
Ии = 5%*Коб*Кз = 005*15000000*0109 = 81750 руб.
Итог по статье “Расходы на содержание и эксплуатацию оборудования” определяется как сумма затрат по пунктам 6.1 и 6.5. Результаты расчета сводим в таблицу 5.
Таблица 5 – Смета расходов на содержание и эксплуатацию оборудования
Наименование статей расходов
Амортизация оборудования и транспортных средств
Эксплуатация оборудования
Текущий ремонт оборудования
Внутризаводское перемещение грузов
Износ малоценных и быстроизнашивающихся инструментов и приспособлений
Сравниваемый вариант (технологический процесс №1)
Эффективный фонд времени одного станка будет равен:
Расчет потребного количества оборудования:
Таблица 6 – Ведомость потребности в оборудовании
Таблица 7 – Расчет численности рабочих занятых на нормируемых работах
Таблица 8 – Расчет заработной платы рабочих занятых на нормируемых работах
ЗПДОП.СВ=025*ТФСВ=025*10206382 = 25515955 руб;
ЗПДОП.ФР=025*ТФФР=025*480024046 = 120006012 руб;
ЗПОТ.СВ=015*ТФСВ=015*10206382 = 15309573 руб;
ЗПОТ.ФР=015*ТФФР=015*480024046 = 72003607 руб;
Амортизация оборудования и транспортных средств:
Ао = 12000000*0141*0043 = 72756 руб.
Ао = 18000000*0141*0172 = 436536 руб.
ΣАо = 509292 рублей.
Эксплуатация оборудования:
См.в.=10000000*0043*003 = 12900 руб.
См.в.=15000000*0172*003 = 77400 руб.
ΣСм.в. = 90300 рублей.
Основная и дополнительная заработная плата вспомогательных рабочих:
ФВ.Р = 04*158198921 = 63279568 руб.
ФВ.Р = 04*744037272 = 297614909 руб.
Σ ФВ.Р = 360894477 рублей.
Годовые затраты на электроэнергию:
ΣСэ = 8717175 рублей.
Текущий ремонт оборудования:
ЗРЕМ = 10%*Коб*Кз = 01*12000000*0043 = 51600 руб.
ЗРЕМ = 10%*Коб*Кз = 01*18000000*0172 = 309600 руб.
ΣЗрем = 135600 + 478800 = 361200 рублей.
Внутризаводское перемещение:
Износ инструментов и приспособлений:
Ии = 5%*Коб*Кз = 005*10000000*0043 = 21500 руб.
Ии = 5%*Коб*Кз = 005*15000000*0172 = 129000 руб.
Таблица 9 – Смета расходов на содержание и эксплуатацию оборудования
Общепроизводственные расходы включают следующие затраты:
Содержание аппарата управления цеха;
Содержание прочего цехового персонала;
Амортизация зданий сооружений и инвентаря;
Содержание зданий сооружений и инвентаря;
Текущий ремонт зданий сооружений и инвентаря;
Испытания опыты и исследования;
Износ малоценного и быстроизнашивающегося инвентаря;
В связи с большой номенклатурой изготовляемых в цехе изделий рассчитать общепроизподственные расходы приходящиеся на конкретную деталь сложно. Поэтому при определении этих затрат используем следующая формула:
где Спр.пр. – годовая сумма общепроизводственных расходов по проектируемому варианту руб;
Спр.ср. – годовая сумма общепроизводственных расходов по сравниваемому варианту руб;
Зпр.ср. – основная заработная плата производственных рабочих по сравниваемому варианту руб;
Зпр.пр. – основная заработная плата производственных рабочих по проектируемому варианту руб;
Следовательно Спр.пр2 = 185*365329811 = 6758602 руб.
Спр.пр1 = 185*582087866= 10768626 руб.
После определения всех расходов связанных с изготовлением детали составляем плановую калькуляцию. Плановая калькуляция составляется на годовой объем и на единицу продукции по форме приведенной в таблице 10. В ней приводим значения показателей разработанных вариантов что позволяет дать сравнительный анализ технологического процесса механической обработки детали.
Себестоимость единицы продукции вычисляем по статьям калькуляции путем деления суммы годового выпуска по каждой статье на количество изделий по плану. При определении отчислений на социальное страхование затраты рассчитываем от суммы основной и дополнительной заработной платы производственных рабочих (40%).
Таблица 10 – Плановая калькуляция единицы продукции
Наименование статей затрат
Сравниваемый вариант
Сырье и основные материалы
Возвратные отходы (вычитаются)
Топливо и энергия на технологические цели
Основная заработная плата производственных рабочих
Дополнительная заработная плата производственных рабочих
Налоги и отчисления исчисляемые от заработной платы
Расходы на содержание и эксплуатацию оборудования
Общепроизводственные расходы
Для определения экономического эффекта сопоставляем цеховую себестоимость разнообразных вариантов технологического процесса механической обработки детали.
Эс = (С1-С2)*В(1.18)
где С1 – себестоимость изготовления детали сравниваемого варианта
С2 – себестоимость изготовления детали проектируемого варианта.
Эс = (65221-478015)*10000 = 1741948377 руб.
ПРИЛОЖЕНИЯЛитература
Курсовое проектирование по технологии машиностроения. Горбацевич А.Ф. Шкред В.А. Мн.: Высшая школа. 1983 с. 256.
Дипломное проектирование по технологии машиностроения под общ.ред. В.В.Бабука. – Минск: Высшая школа 1979.
Организация производства и управление предприятием: методические указания по выполнению курсовой работы. Машков Н.М. УО «ВГТУ» 2006г.
Единый тарифно-квалификационный справочник работ и профессий рабочих. Выпуск 2. М. Экономика. 1990.
Место.cdw

Машина для гвоздевого крепления деталей каблука.
Машина для крепления деталей каблука шурупом.
С - Тележка-стеллаж.
КС - Контрольный стол.
Молоткодержатель.cdw

Ось толкателя.cdw

Сборочный.cdw

Наружную поверхность корпуса поз. 1 красить эмалью ПФ-115 ГОСТ
При окончательной сборке поверхность разъёма корпуса и
толкателя покрыть тонким слоем смазки ГОСТ 24285-80.
Втулка.cdw

Молоток.cdw

Лапка.cdw

Толкатель.cdw

111.cdw

Наружную поверхность корпуса поз. 1 красить эмалью ПФ-115 ГОСТ
При окончательной сборке поверхность разъёма корпуса и
толкателя покрыть тонким слоем смазки ГОСТ 24285-80.
кинематика.cdw

Сламывающиеся рычаги; 7. Нижний шарнир;
Ползун; 9. Ударная плита; 10
Верхний шарнир; 13. Ползун. 14. Шпилька;
Стакан-гайка; 16. Ползуны; 17. Контр-гайка;
Уголковые накладки; 19. Пневматические цилиндры; 20. держатели;
Пружины; 22. Кронштейны; 23. Штыри;
Молотковые ползуны; 25. Молотки; 26. Молотковые направляющие;
Удерживающие пластины; 28. Гайка; 29. Регулировочный винт;
Каретка; 31. Направляющие каретки; 32. Упор.
Пояснительная записка.doc
Учреждение образования
«Витебский государственный технологический университет»
«МАШИНЫ И АППАРАТЫ ЛЁГКОЙ ПРОМЫШЛЕННОСТИ»
Анализ устройств и механизмов для крепления каблука
Разработка кинематической схемы модуля для крепления каблука
Разработка структурной схемы интегрированного рабочего места
Расчёт усилия молоткового механизма
Обувь – неотъемлемая часть нашего гардероба. Она всегда нужна людям и всегда при создании новых коллекций она связана с модой.
Дизайнеры стилисты художники обувного мира постоянно заняты мыслями: а что еще можно создать необычного? И вот появляются платформы различных видов и форм по высоте и ширине носочной части.
Казалось бы обычная конструкция «лодочка» что там особенного но оказывается и здесь художники создают удивительные формы каблуков носочной части выреза и различные украшения верха обуви.
Затем конструкторы по эскизам художника делают чертежи деталировку и потом изготавливают обувь обсуждают и принимают решения что эта модель должна быть внедрена в производство.
Специалисты: технологи химики мастера производства – все включаются в процесс изготовления обуви.
На конвейере рабочий должен каждую полупару взять в руки и правильно технологично выполнить свою операцию.
Обувь готова и попадает в магазин. И тут наступает следующий ответственный этап – реализация.
Подчас мы приходим в магазин и не можем выбрать ту или иную вещь теряемся и обращаемся к продавцу как к специалисту владеющему информацией. Да и психологически работник магазина должен чувствовать покупателя дать такие рекомендации чтобы покупатель ушел довольный и благодарный за ваш труд и внимание.
Так что же такое обувь и из чего она состоит?
Обувь – изделие для предохранения ног от внешних воздействий и несущее эстетические функции.
Размер обуви – длина стопы в миллиметрах.
Полнота обуви – условное обозначение обхвата стопы в пучках прямом взъеме в косом проходе.
Вид обуви – конструктивные особенности обуви определяемые степенью закрытия ноги деталями верха обуви.
Модель обуви – конкретное изделие с индивидуальными признаками конструкции материалов и внешнего оформления обуви.
Коллекция – совокупность моделей обуви.
Метод крепления – способ прикрепления низа обуви к верху.
По назначению различают:
Повседневная модельная обувь домашняя обувь обувь для активного отдыха и спорта. круглосезонная обувь летняя обувь зимняя обувь весенне-осенняя обувь обувь для пожилых детская обувь.
Обувь состоит из следующих частей:
Носочно-пучковая часть
Геленочная часть или перейменная
Пяточно-геленочная часть
По конструкции обувь делится на полуботинки туфли ботинки полусапоги сапоги открытая обувь бесподкладочная обувь мокасины обувь типа мокасин.
ЖЕНСКАЯ ОБУВЬ. МУЖСКАЯ ОБУВЬ.
ТУФЛИ ЛЕТНИЕ – ОТКРЫТЫЕ.
Детали верха обуви – комплект деталей верха обуви не скрепленных между собой такие как: союзка берцы носок задинк голенище овальная вставка обтяжка клапан.
Подкладка обуви – комплект внутренних деталей обуви для повышения гигиенических теплозащитных свойств формоустойчивости и изоляции ноги от швов наружных деталей верха. Так же выделяют такие внутренние детали верха обуви как: карман подблочник штаферка вкладная полустелька подпяточник задник простилка геленок или супинатор.
Детали низа обуви: основная стелька подошва подошва с язычком подошва с крокулем профилированная подошва формованная или монолитная подошва рант накладкакаблук.
Гвоздевой метод крепления подошв и каблуков.
В зависимости от вида и назначения обуви при креплении подошвы и каблука к заготовке верха применяют различные методы соединения деталей: гвоздевые прошивные клеевые и комбинированные.
Наиболее старым и надежным является гвоздевой метод крепления подошв и каблуков к заготовке верха обуви. Последнее время он больше распространен при производстве продукции специального назначения (рабочей и военной обуви). Но нужно отметить что методика соединения верха обуви с подошвами и каблуками при помощи гвоздей и сегодня применяется некоторыми фирмами выпускающими модельную обувь. Гвоздевым методом крепления подошв с давних пор пользуются на Руси. Обувь созданная по этой технологии обладает особой прочностью и износостойкостью. Многие производственные предприятия предпочитают покупать для своих работников именно такую обувь как наиболее надежную и дешевую.
Суть гвоздевого метода заключается в том что заготовка верха соединяется с подошвой и каблуком при помощи гвоздей. В некоторых моделях обуви количество гвоздей может достигать 100 - 150 штук. Для крепления применяют стальные и латунные гвозди различных размеров. Сейчас применяют внутренний и внешний гвоздевые методы крепления подошв. Выбор типа крепления зависит от вида материала из которого изготовлены подошвы и каблуки их толщины и высоты конструкции обуви. Подошвы и каблуки могут быть кожаными наборными или резиновыми формованными. Такие подошвы и каблуки прикрепляют гвоздями как изнутри так и снаружи. Изнутри каблук крепят со стороны стельки через нее и затяжную кромку задника и верха обуви. При креплении подошвы и каблука снаружи гвозди проходят через материал подошвенной части затяжную кромку верха обуви и задника и загибаются в стельку на 2-3 мм.
При производстве рабочей и специальной обуви как правило применяют внешний гвоздевой метод. Так как резиновые подошвы и каблуки имеют не очень высокое сопротивление вырыванию гвоздя они выполняются достаточно толстыми. Кожаные наборные каблуки в основном прикрепляют изнутри обуви гвоздями с конусными головками. При применении любого из двух методов гвозди скрывают в конструкции обуви так чтобы они не выступали над поверхностью стельки.
Анализ устройств и механизмов для крепления каблука.
Механизмы для скрепления деталей и изделий штучными крепителями широко используются в машинах обувного производства для временного прикрепления стелек к колодкам прикрепления подошв обуви соединения элементов (фликов и набоек) каблука вставки блочков а также в некоторых типах обтяжных и затяжных машин для фиксации обтянутой или затянутой заготовки на колодке. В качестве штучных крепителей используют шпильки винты гвозди полускобки скобки блочки и т. д. При скреплении двух или нескольких деталей их спрессовывают и перпендикулярно или под углом к плоскости их скрепления поступательным или поступательным с вращением движением вводят штучный крепитель.
Из машин для скрепления деталей и изделий штучными крепителями применяют гвоздевые скобочные и блочковые ограниченное применение находят шпилечные и винтовые машины. Из гвоздевых машин следует отметить: АСГ-19 — для прикрепления подошв стандартными гвоздями; ПДН-О — для прикрепления подошв гвоздями изготовляемыми машиной; МКН ПКВ и ПДК — для прикрепления каблука гвоздями; 04222Р.1 (ЧССР) — для прибивания каблуков к обуви гвоздями; ОМ-4М — для обтяжки заготовки на колодке пятью гвоздями; полуавтоматы 02038Р1 и 02038Р2 (ЧССР) —для затяжки пяточной части заготовки обуви 12—20 гвоздями; ЗВ-1 и ЗВ-2-О 02087Р1 и 02074Р2 (ЧССР) —для затяжки заготовки верха обуви на колодке и др. К скобочным относится машина ППС-С — для временного прикрепления стелек к колодкам и подошв к стелькам скобками. Для вставки и закрепления блочков широко применяется машина ВБ-1.
В зависимости от формы пяточной части подошвы высоты и материала каблука назначения обуви каблук можно крепить гвоздями шурупами или клеем. Для прикрепления каблуков применяют пресс ППГ-4-О машины 04222Р1 04222РЗ 04299Р1 04299Р2 04352Р1 (ЧССР) машины 947 РТ и 935 BLA фирмы «Сигма» (Италия).
Машины 04299Р1 и 04299Р2. Предназначены для крепле-ния изнутри разнообразных по форме пластмассовых каблуков металлическими шурупами с крестообразной канавкой на головке преимущественно к женской обуви. Машины пневматические.
На машине 04299Р2 в отличие от машины 04299Р1 можно прикреплять каблуки к женским сапожкам.
Технологический процесс на машине 04299Р1 выполняется следующим образом. Колодку с затянутой заготовкой верха и установленным каблуком надевают следом вверх на направляющий штуцер машины который входит во втулку пяточной части колодки. При включении машины каблук прижимается к обуви и винт входит через стельку в каблук после чего полупару вручную снимают с машины и цикл повторяется.
Машина 947 РТ фирмы «Сигма» (Италия). На машине прикрепляют каблуки гвоздями изнутри. Машина имеет гидропривод и механическое устройство для подачи гвоздей по одному из двух каналов что дает возможность использовать гвозди различной длины.
Машина 935 BLA фирмы «Сигма» (Италия). Предназначена для прикрепления каблуков изнутри к женской обуви одним шурупом.
Машина 04222Р1. Является универсальной и предназначена для прикрепления гвоздями различных каблуков к любому виду обуви как снаружи так и изнутри. Машина имеет электромеханический привод гидравлическое устройство прессования деталей и забивания гвоздей.
Рис 1. Машина 04222Р1 (а) схемы прикрепления каблуков изнутри (б)
снаружи (в) и движения гвоздеподающей кассеты (г)
кинематическая схема (д).
Техническая характеристика машины 04222Р1
Производительность пар обуви в час До 250
Усилие забивания гвоздей кН 5—40
Длина гвоздей мм 10—35
Мощность электродвигателя кВт 042
Габарит мм 550X800X1
При прибивании каблука изнутри обувь без колодки надевают следом вверх на головку 8 (рис. 1 а б) стойки 9 машины предварительно наполненную гвоздями и на пяточную часть обуви устанавливают каблук. При легком нажатии на педаль 12 верхний упор 7 опускается и прижимает каблук к обуви. При дальнейшем нажатии на педаль включают машину. Происходит дополнительное прижатие каблука после чего гвозди забиваются в него изнутри. Обработанную обувь снимают со стойки машины гвоздеподающая кассета автоматически наполняет головку 8 требуемым числом гвоздей и машина выключается.
Время между прибиванием каблука и переносом гвоздей в головку 8 можно регулировать рукояткой 11 изменяя этим продолжительность цикла работы машины.
При прибивании каблука снаружи на машине устанавливают отклоняющийся верхний упор 13 (рис. 1 б) и головку 14 с выемкой для каблука. После заполнения головки 14 гвоздями в ее выемку вкладывают каблук правой рукой за рукоятку отклоняют верхний упор на себя настолько чтобы на него можно было легко надеть обувь упор возвращают в первоначальное положение и слегка нажимают на педаль до тех пор пока обувь не будет плотно прижата к каблуку. Пальцами левой руки проверяют совпадение пяточной части обуви с каблуком и дальнейшим нажатием на педаль включают машину. Гвозди забиваются в каблук. Обработанную обувь снимают с верхнего упора головка автоматически наполняется гвоздями и цикл работы повторяется.
Машина имеет механизмы привода подачи гвоздей молотков и прессования деталей. Механизм подачи гвоздей 5 (см. рис. 1 а) расположен в верхней части машины и имеет бункер 6 для гвоздей. Гвозди от механизма подачи поступают в головку 8 с помощью кассеты З совершающей сложное движение по траектории АБВГ (рис. 1 г). Одновременно может подаваться от 1 до 20 гвоздей.
Усилие прессования деталей и забивания гвоздей зависит от материала каблука и числа гвоздей. Это усилие регулируют маховиком 2 (см. рис. 1 а).
Электрооборудование машины расположено в коробке 4. Машина имеет два рабочих столика 10 и выдвигающиеся колесики 1 для транспортирования машины.
Машина 04222РЗ. Отличается конструкцией рабочих органов (стойки и верхнего упора) и предназначена для прикрепления каблуков к сапогам гвоздями снаружи (рис. 2).
Машина ПДН-1-О предназначена для крепления деталей низа обуви: стелек полустелек геленков простилок гвоздями при сборке школьной женской и мужской обуви всех моделей.
Устройство и принцип работы. Машина (.рис. 3) состоит из станины 7 головки 2 гвоздевого барабана 3 электрооборудования 4.
Станина представляет собой сварную конструкцию на которой смонтированы все сборочные единицы машины.
Рис. 3. Общий вид машины
Головка (рис. 4) предназначена для забивания гвоздей.
От электродвигателя клиноременной 1 и зубчатой 2 передач вращение получает шестерня-полумуфта 3 свободно сидящая на главном валу головки. Главный вал приводится во вращение через полумуфту 6 закрепленную на нем.
Шестерня-полумуфта 3
Рис. 4. Кинематическая схема машины и полумуфта 6
подпружиненной скользящей шпонкой 4 имеющей конусообразный конец который входит в одно из шести отверстий шестёрни-полумуфты 3. Шпонка 4 расцепляется с полумуфтой 3 рычагом 5 при нажатии на педаль 16 через систему тяг и рычагов.
В верхней части головки смонтирован патрон 14 с ловителем гвоздя штанга 11 с молотком 13 пружина 12 сообщающая движение штанге для удара. Для смягчения удара в верхней части штанги установлены шайбы 9 удерживаемые чашечной гайкой. На конце главного вала смонтированы кулачки 8 и 10. От кулачка 8 прикрепленного к торцу кулачка 10 осуществляется подъем штанги 11. Кулачок 10 через двуплечий рычаг 17 сооб-щает возвратно-поступательное движение отсекателю 19 гвоздевого барабана.
Механизм нижнего упора представляет собой двуплечий рычаг 20 соединенный с наковальней 15 которая получает возвратно-поступательное движение от кулачка 7 жестко соединенного с шестерней-полумуфтой 6 через подпружиненную тягу 21.
Усилие прибивания материала гвоздями регулируют пружиной 12.
Гвоздевой барабан 22 предназначен для отделения гвоздя и подачи его в патрон по одному за каждый оборот главного вала. Корпус барабана закреплен на головке. Привод барабана состоит из конического и цилиндрического зубчатых колес.
От зубчатого конического колеса 2 (рис. 5) через зубчатое колесо 5 и предохранительную шариковую муфту 5 вращение передается валу 4. На валу 4 закреплена крышка 1 с совочками 6 захватывающими при вращении гвозди из корпуса барабана. Гвозди высыпаются на наклонный лоток 7 и далее поступают в наклонный канал 9 в конце которого смонтирован отсекатель10.
Рис. 5. Гвоздевой барабан машины Внутри барабана установлен
ПДН-1-О сбрасыватель 8 тех гвоздей которые легли поперек канала и препятствуют прохождению других гвоздей к отсекателю. Сбрасыватель гвоздей приводится в движение рычагом 11 который под воздействием пружины утапливается в прорезь выступающей части зубчатого колеса 5. За один оборот зубчатого колеса 5 сбрасыватель срабатывает дважды.
Положение отсекателя 19 (см. рис. 4) регулируют винтом 18.
Электрооборудование состоит из пульта управления расположенного на дверце станины 1 (см. рис. 3) со стороны обслуживания; панели управления находящейся с внутренней стороны дверцы станины электродвигателя 5; ламп местного освещения. Электродвигатель привода машины включается тумблером вместе с лампой местного освещения. Электрооборудование защищено от перегрузок и токов короткого замыкания автоматическими выключателями.
Машина подключается к цеховой сети с. помощью штепсельного разъема. Положение электродвигателя и натяжение клиновых ремней регулируют болтами 6 (см. рис. 3). Машину подключают к сети переменного тока так чтобы вал электродвигателя вращался по часовой стрелке (со стороны обслуживания) нанесенной на шкив электродвигателя.
До начала работы в гвоздевой аппарат засыпают 05 кг гвоздей. Проверяют работу механизмов пуска и останова: при включенном выключателе рабочие органы машины должны находиться в исходном состоянии.
Работа на машине осуществляется следующим образом. Детали низа накладывают друг на друга вводят между патроном и упором прижимают в скрепляемом месте к патрону. При нажатии на педаль гвоздь забивается.
При креплении деталей низа к колодке нижний упор снимают. Колодку с наложенной деталью подводят к патрону прижимают скрепляемым местом к отверстию в патроне нажимают на педаль и гвоздь забивается.
МОЛОТКОВЫЕ МЕХАНИЗМЫ.
Все приведённые выше машины имеют в своей конструкции молотковые механизмы. Молотковые механизмы предназначены для забивания штучных крепителей (шпилек гвоздей полускобок скобок и др.) в скрепляемые детали. Помимо введения крепителя нормально к плоскости скрепляемых деталей механизмы должны как правило обеспечивать загибку или расклепывание его острия. Молотковые механизмы можно классифицировать по характеру выполняемого скрепления по структуре по конструктивному оформлению и т. д.
По характеру выполняемого скрепления деталей механизмы могут быть предназначены для временного (ППС-С ОМ-4М и др.) и для постоянного скрепления деталей крепителями (НШВ — для шпилькования набоек ДШ — для прикрепления подошв к обуви деревянными шпильками ПДН-О АСГ-19 МКН ПКВ ЗВ-1 ЗВ-2-О полуавтоматы 02087Р1 02074Р2 и др.).
Молотковые механизмы могут быть плоскими и пространственными. По структуре их можно разделить на кулачковые (НШВ) и пружинно-кулачковые (большинство машин). Структурная схема и конструктивное оформление механизмов могут быть самыми разнообразными и во многом определяются величиной развиваемого усилия на рабочем инструменте работой сия сопротивления штучного крепителя при забивании назначением проектируемой машины общей компоновкой механизмов и узлов машины на станине и т. п.
Независимо от вида штучного крепителя сопротивление введению его в скрепляемые детали определяется в основном силами контактного взаимодействия крепителя и соединяемых им элементов.
Полная сила сопротивления Р введению крепителя в скрепляемые детали:
Рт — силы сопротивления контактного трения;
Рд — силы сопротивления отдельных контактных площадок упругим и
пластическим деформациям различного вида (смятию срезу
α — коэффициент показывающий соотношение слагаемых Рт и Рд.
На величины слагаемых Рт и Рд влияют вид крепителя материал из которого он изготовлен его геометрические параметры физико-механические свойства скрепляемых материалов и т. д. Средние значения коэффициента α (в %) для некоторых типов крепления составляют: гвоздевого (резина) 20 — 40 гвоздевого (кожа) 40 — 50 винтового (резина) 200 — 250 деревянно-шпилечного — стремится к .
Силы сопротивления контактного трения для различных креплений являются компонентами силы держания крепителей. Поэтому закономерности контактного трения в той или иной степени относятся ко всем типам крепления штучными крепителями и определяют их общие характеристики.
Рассмотрим упрощенную схему системы скрепляемым элементом которой является одиночная шпилька (рис. 6). После прокола шилом диаметром d0 скрепляемых материалов в них образуется отверстие диаметром d2 = d0 где — коэффициент зависящий от свойств скрепляемых материалов геометрии шила и т. п. Шпилька в свободном состоянии имеющая диаметр d1 после забивания сжимается и ее диаметр уменьшается до d. При этом создается посадочная контактная поверхность с общим для материалов и шпильки диаметром d. Сила сопротивления контактного трения при радиальном удельном давлении р по контактной поверхности коэффициенте трения f и высоте s шпильки будет:
Удельное контактное давление р можно определить приближенно по известному из теории сопротивления материалов уравнению для радиальных напряжений по контактной поверхности при соединении цилиндрических деталей с натягом:
s — диаметральный абсолютный натяг;
Е1 и Е2 — модули продольной упругости соответственно шпильки и
скрепляемых материалов;
и 2 — коэффициенты Пуассона материалов шпильки и скрепляемых
k1 и k2 — безразмерные геометрические параметры шпильки
(отношение диаметра шпильки к диаметру контактного
цилиндра) и скрепляемых деталей (отношение диаметра
контактного цилиндра к наружному диаметру проколотого
Для рассматриваемого случая:
Так как k1= 0 k2= 0 и Е1 >> E2 а поперечные размеры шпильки невелики то можно пренебречь поперечной деформацией шпильки и считать d1 = d. Тогда
Выражение (1) позволяет с достаточной для инженерных расчетов точностью определить силу сопротивления контактного трения одиночной цилиндрической шпильки. Для штучных крепителей другой геометрической формы выражение (1) с учетом анизотропности скрепляемых волокнистых материалов можно использовать лишь для общей аналитической характеристики силовых соотношений в системе скрепляемые детали — шпилька. Силовые соотношения при скреплении деталей другими штучными крепителями для которых характерно наличие не только сил сопротивления контактного трения Рт но и сил сопротивления РД отдельных контактных площадок упругим и пластическим деформациям рассмотрим на примере гвоздевого скрепления деталей.
В первом приближении будем считать что на гвоздь в процессе его внедрения в скрепляемые материалы действуют активная сила Р направленная в сторону острия гвоздя; сила сопротивления смятию Q скрепляемых материалов или сопротивление острия гвоздя загибке; реакция материалов N на коническую поверхность гвоздя; сила трения Т гвоздя о материал (рис. 5.2). Условия статики по проекциям всех сил на направление силы Р и перпендикулярно к ней примут вид
Для решения этой системы определим действующие на гвоздь силы.
Из геометрических соотношений для острия гвоздя (см. рис. 7) имеем:
dCT — диаметр стержня гвоздя;
d — переменный диаметр контактного конуса;
d3 — диаметр контактного конуса на выходе из стельки т. е. диаметр
загибаемого сечеция острия гвоздя;
s —толщина скрепляемых материалов;
L3 —длина загиба острия;
l —координата переменного сечения контактного конуса
(относительно конца острия до загибания);
— угол заострения острия;
r — переменный радцус контактного конуса.
Составим уравнение силы контактного трения для .элементарного усеченного конуса высотой dl и с радиусами круглых оснований r и (r + dr). При этом с учетом выражения (1) получим следующее значение элементарной силы контактного трения по образующей поверхности указанного элементарного усеченного конуса:
—коэффициент характеризующий геометрию гвоздя;
- параметр соединения который счи-
таем постоянным по толщине скрепляемых материалов;
f — коэффициент контактного трения.
Интегрируя это выражение в пределах l = L3 и l = L3 + s т. е. по всей толщине скрепляемых материалов получим полную силу контактного трения гвоздя
Очевидно реакция N скрепляемых материалов на коническую поверхность гвоздя будет:
При отсутствии загибки острия в случае забивания гвоздя в предварительно проколотое отверстие в уравнении (2) можно принять Q = 0. Тогда подстановка выражений (3) и (4) в уравнение (2) позволяет определить аналитически усилие Р забивания для любого положения гвоздя в скрепляемых материалах.
Для случая загибки острия гвоздя на стельку имеем:
где: — предел текучести материала гвоздя;
а — коэффициент зависящий от формы загибки острия;
W —момент пластического сопротивления загибке острия.
Основные вопросы проектирования и расчета рассмотрим на примере кулачковых и пружинно-кулачковых молотковых меха-низмов.
Конструкция кулачковых молотковых механизмов проста. Механизм (рис. 8) имеет кулачок 1 в пазу которого находится ролик 2 закрепленный на молотковой штанге 5 которая может перемещаться в направляющих 4. В механизме осуществлено кинематическое замыкание ролика с кулачком. В некоторых случаях целесообразно осуществлять силовое замыкание. Движениемолотка вверх и вниз производится кулачком в соответствии с циклограммой работы механизма и машины в целом. Профиль кулачка в этом механизме имеет резкие очертания вследствие чего значительно увеличиваются углы давления что приводит к быстрому изнашиванию кулачка. Для уменьшения углов давления обычно применяют
внецентренные кулачковые механизмы с положительным эксцентриситетом е.
При проектировании механизма следует иметь в виду что молоток должен обеспечить забивание различных по длине штучных крепителей. Ход s молотка зависит от длины забиваемых крепителей расположения молотка величины направляющих для крепителей и изделия. Очевидно:
—расстояние между молотком в исходном положении и
— расстояние между острием крепителя и изделием.
Обычно принимают s = klmax где k = 2-3 —коэффициент пропорциональности.
Например в машине НШВ lmах = 158 мм s = 32 мм.
Кулачковые молотковые механизмы нецелесообразно применять при скоростях больших 300—400 обмин и при больших s и размерах кулачка так как развиваются значительные ударные силы и контактные давления в паре кулачок—ролик.
Профиль паза кулачка или его рабочей поверхности в случае использования силового замыкания кулачка с роликом определяется по известному закону движения s (φ) толкателя. Этот закон выбирают таким чтобы на участке рабочего хода (забивание) скорость движения молотка была максимальной.
Пружинно-кулачковые молотковые механизмы можно разделить на плоские (машины ЗВ-1 АСГ-19 и др.) и пространственные (ОМ-4М полуавтомат 02038Р1 и др.). Кроме того они могут быть с поступательно-движущимся толкателем (машины ЗВ-1 АГС-19 полуавтомат 02038Р1 и др.) и коромыслового типа (машина ОМ-4М). Механизмы с поступательно-движущимся толкателем можно разделить на два типа —с центральным кулачковым механизмом и с внецентренным кулачковым механизмом.
Рис. 9. Схема пружинно-кулачкового Рис. 10. Схема пружинно-
механизма молотка машины ЗВ-1 кулачкового механизма
молотков машины ОМ-4М
Центральный пружинно-кулачковый механизм применяется в машинах АСГ-19 ЗВ-1 (рис. 5.4) и др. Механизм состоит из молотка 1 молотковой штанги 2 маятникового рычага 3 пружины кручения 4 кулачка 5 клина 6 пружины 7 маховичка 5 гайки 9 ползуна 10 и кронштейна 11. Молоток совершает сложное движение по траектории A BCD.
Основными элементами молоткового механизма коромыслового типа машины ОМ-4М (рис. 5.5) являются молотки 1 кулачок 2 пружины 3 рычаги 4 7 и 8 вал 5 ось 5 дуга 9 тяги К) ползуны И боковых клещей и ползун 12 средних клещей стержень 13 стойка 14 кожаные прокладки 15 гайка 16 крючки 17 и регулировочные гайки 18. Вставки 2а и 4а в случае износа заменяются.
Структурную схему механизма выбирают исходя из обеспечения основных требований предъявляемых к механизму его назначения возможностей размещения во вновь проектируемой машине и т. д.
Для пружинно-кулачкового механизма работа А затрачиваемая при каждом ударе молотка зависит от типа пружины ее размеров и размеров звеньев механизма. Эта работа должна быть значительно больше необходимой для введения штучного крепителя в скрепляемые детали т. е.
А1 — работа необходимая для введения
штучного крепителя в скрепляемые
k — коэффициент запаса.
Указанное требование может быть выполнено если усилие развиваемое механизмом достигает Рmах (рис. 11). Тогда при перемещении молотка по координате у и длине крепителя l работа А1 определяется из графика Р = f (у) величиной заштрихо ванной площади.
Большие значения коэффициента k приводят к увеличению шума повышают напряжения в деталях механизма снижая их долговечность. Рекомендуется при проектировании молотковых механизмов принимать k = 15-:-20.
Основные вопросы проектирования и расчета рассмотрим на примере гидравлических молотковых механизмов.
Конструкция гидравлических молотковых механизмов проста. Механизм (рис. 8) имеет:
Гидравлический цилиндр; 2.Поршень;
Сламывающиеся рычаги; 7. Нижний шарнир;
Верхний шарнир; 13. Ползун.
Уголковые накладки; 19. Пневматические цилиндры;
Кронштейны; 23. Штыри;
Молотковые ползуны; 25. Молотки; 26.Молотковые направляющие;
Удерживающие пластины;
Гайка; 29. Регулировочный винт; 30. Каретка;
Направляющие каретки; 32. Упор.
Разработка рабочего места
Необходимая часть организации труда — организация рабочих мест. Рабочее
место — это первичное звено производства зона трудовой деятельности
рабочего или группы рабочих (если рабочее место коллективное) оснащенная необходимыми средствами для выполнения производственного задания. Под организацией рабочего места понимается система его оснащения и планировки подчиненная целям производства. Эти решения в свою очередь зависят от характера и специализации рабочего места от его вида и роли в
производственном процессе.
В зависимости от специфики производства рабочие места могут быть специализированными и универсальными индивидуальными и коллективными стационарными и подвижными одностаночными и многостаночными постоянными и временными а также рабочими местами ручной работы механизированными автоматизированными аппаратными рабочими местами служащих и др.
Оснащение рабочего места складывается из совокупности средств необходимых для осуществления производственного процесса. К ним относятся:
а) основное технологическое и вспомогательное оборудование;
б) технологическая оснастка — рабочий и мерительный инструмент
приспособления запасные части;
в) организационная оснастка — средства связи и сигнализации
г) рабочая мебель тара; рабочая документация; средства
коммуникации для подачи на рабочее место сырья материалов
д) хозяйственный инвентарь для поддержания чистоты и порядка и
Полное и комплектное оснащение рабочего места позволяет наилучшим образом организовать процесс труда. Для этого необходима рациональная планировка средств оснащения — размещение их на рабочем месте так чтобы обеспечивалось удобство их обслуживания свободный доступ к механизмам и их отдельным узлам требующим регулирования и контроля экономия движений и перемещений работника удобная рабочая поза хороший обзор рабочей зоны безопасность труда экономия производственной площади наличие проходов подъездов и проездов для транспортных средств взаимосвязь со смежными рабочими местами и с местом бригадира мастера другого руководителя.
Проводимые аттестации рабочих мест позволяют выявлять отступления от нормативных требований к ним и совершенствовать организацию рабочих мест в соответствии с требованиями научной организации труда. По результатам аттестации малоэффективные рабочие места могут упраздняться при этом появляется возможность более рационального использования производственных площадей установки современного высокопроизводительного оборудования и
интенсификации производственного процесса.
Уровень организации труда на рабочем месте зависит также от совершенства системы его обслуживания. Организация обслуживания рабочих мест предполагает:
* своевременное обеспечение рабочих мест всем необходимым
включая техническое обслуживание — наладку смазку регулировку;
* ремонтное и межремонтное обслуживание; обеспечение сырьем
* полуфабрикатами комплектующими изделиями инструментом;
* подачу необходимых видов энергии — тепла электроэнергии
* межоперационный и финишный контроль качества продукции;
. * хозяйственное обслуживание — уборку чистку оборудования;
* транспортное обслуживание и т.д.
Чтобы организовать обслуживание рабочих мест необходимо решить следующие вопросы:
-определить в каких видах обслуживания нуждается каждое рабочее
-по каждому виду обслуживания установить его норму т.е. обосновать
объем обслуживания в смену месяц год;
-установить регламент обслуживания т.е. график периодичность и
-закрепить выполнение обязанностей по обслуживанию за строго
определенными исполнителями.
Эффективность обслуживания рабочих мест может быть достигнута лишь при соблюдении:
***принципа предупредительности обслуживания предусматривающего выполнение соответствующих работ до того как процесс производства прервется в силу несвоевременного их выполнения; принципа оперативности обслуживания — быстроты реагирования на возможные сбои производства;
***принципа комплексности выражающегося в обеспечении разностороннего обслуживания по всем его видам; принципа плановости заключающегося в проведении расчетов потребности в видах сроках и объемах обслуживания каждого рабочего места.
Прогресс в системах обслуживания рабочих мест состоит в переходе от дежурного обслуживания т.е. обслуживания по вызову с места остановки производства к стандартному обслуживанию основанному на расчетах норм обслуживания и реализации планово-предупредительного проведения обслуживающих работ.
Достижение эффективных решений по организации рабочих мест и систем их обслуживания облегчается использованием разработанных типовых проектов организации труда для массовых профессий рабочих и служащих. Типовой проект организации труда — это как правило средоточие передового опыта
организации труда в котором находят отражение все принципиальные вопросы организации труда в том числе вопросы оснащения и планировки рабочих мест организации их обслуживания.
На основании вышеизложенного построим структурную схему интегрированного рабочего места для креплении каблука:
Аппарат для прогрева деталей каблука.
Машина для гвоздевого крепления деталей каблука.
Машина для крепления деталей каблука шурупом.
КС - контрольный стол.
Построим схему для силового анализа кинематики гидрапривода данного молоткового механизма.
Расчет усилия на гидроцилиндре
Полезная сила гидростатического давления Рпол определяется из условий статического равновесия Толкателя молотка и гидроцилиндра молоткового механизма в начальный момент внедрения гвоздей в материал:
Где: f -коэффициент трения в направляющих;
Рпол -полезная сила гидростатического давления в гидроцилиндре
молоткового механизма;
Рзаб-усилие необходимое для забивания гвоздей в материал каблука (по заданию Рзаб=10 кН).
Определение диаметра гидроцилиндра забивания:
D– диаметр гидроцилиндра забивания [м];
k– коэффициент запаса (k=15 2); k=15
Pн – давление создаваемое насосом в магистрали. Из стандартного
ряда давлений выбираем Pн = 6.3 МПа. = 6.3*10 Па;
Рпол -полезная сила гидростатического давления в гидроцилиндре;
Уточненное значение в соответствии с ГОСТ 12447-80
Определение диаметра штока. Штоки гидроцилиндров работающие на сжатие при длине L 10d рассчитываются на продольный изгиб по формуле Эйлера. Для коротких штоков (L 10d ) справедлива упрощённая формула:
P-усилие сжатия штока;
что соответствует нормируемым значениям d = 20 мм.
Определение производительности насоса и выбор насоса
Требуемая производительность Qн насоса определяется из уравнения:
t3 – длительность периода забивания;
L2 – величина хода штока;
D -диаметр гидроцилиндра забивания;
В соответствии с ГОСТ 13825-80 принимаем Qн =135 лмин
Подбираем по каталогу насос марки Г13-32АМ
Определение толщины стенок гидроцилиндра.
Толщина стенок гидроцилиндра определяется из условий прочности.
т – предел текучести (значение т выбирается в соответствии с ь
материалом цилиндра например для стали 20Х т =638 Нмм²);
s – масштабный коэффициент (s =07);
n – коэффициент запаса (n=125);
D – диаметр гидроцилиндра;
Рн– максимальное давление на выходе насоса;
Определение наружного диаметра гидроцилиндра
Наружный диаметр гидроцилиндра Dн находится
Где: D – диаметр гидроцилиндра вырубания;
- толщина стенок гидроцилиндра.
Определение диаметров трубопроводов
Диаметры трубопроводов определяют по формуле
Где: dтр – диаметр трубопровода;
Vтр – допускаемая скорость движения масла;
Vтрвс=12 мс – для всасывания;
Vтр =2 мс – для слива;
Qн - производительность насоса
По ГОСТ 12447-80 dтрв=16 мм
По ГОСТ 12447-80 dтрс=12 мм
При Pн=63 МПа допускаемая скорость нагнетания Vтрн =32 мс
По ГОСТ 12447-80 dтрн=10 мм.
В данной работе был проведен анализ устройств и механизмов для прикрепления каблука были рассмотрены различные конструкции механизмов молотка.
Была разработана кинематическая схема молоткового механизма с гидроприводом. Также была разработана структурная схема интегрированного рабочего места для крепления каблука.
На основании расчета усилия необходимого для забивания определенного количества гвоздей произведен расчет гидропривода молоткового механизма.
В ходе выполнения работы сделан вывод что для повышения эффективности производства наряду с совершенствованием оборудования требуется уделять немаловажное внимание и рациональной организации рабочих мест так как рабочее место — это первичное звено производства зона трудовой деятельности рабочего или группы рабочих (если рабочее место коллективное) оснащенная необходимыми средствами для выполнения производственного задания. Под организацией рабочего места понимается система его оснащения и планировки подчиненная целям производства. Эти решения в свою очередь зависят от характера и специализации рабочего места от его вида и роли в производственном процессе.
Сироткин Г.П. Выбор типа привода маигн легкой промышленности: Учебное пособие.-П.: ИГИЛП I98I.-66 с
Анастасиев А.А. Архипов Н.Н. Жаров А.Н. Корнилов В.П. Сторожев В.В. Машины машины-автоматы и автоматические линии легкой промышленности. - М.
Длуогий В.А. Муха Т.И. Цупиков А.Н. Януш В.В. Приводы машин: Справочник. -Д.: Машиностроение 1962- 382с.
Колясин В.П. Оборудование сборочных цехов обувных фабрик М.:
Место.cdw

Машина для гвоздевого крепления деталей каблука.
Машина для крепления деталей каблука шурупом.
КС - контрольный стол.
Сборочный.cdw

Наружную поверхность корпуса поз. 1 красить эмалью ПФ-115 ГОСТ
При окончательной сборке поверхность разъёма корпуса и
толкателя покрыть тонким слоем смазки ГОСТ 24285-80.
кинематика.cdw

Сламывающиеся рычаги; 7. Нижний шарнир;
Ползун; 9. Ударная плита; 10
Верхний шарнир; 13. Ползун. 14. Шпилька;
Стакан-гайка; 16. Ползуны; 17. Контр-гайка;
Уголковые накладки; 19. Пневматические цилиндры; 20. держатели;
Пружины; 22. Кронштейны; 23. Штыри;
Молотковые ползуны; 25. Молотки; 26. Молотковые направляющие;
Удерживающие пластины; 28. Гайка; 29. Регулировочный винт;
Каретка; 31. Направляющие каретки; 32. Упор.
3. А4 Втулка.cdw

4. А4 Наконечник.cdw

5. А4 Кронштейн.cdw

2. А4 Молоткодержатель.cdw

6. А4 Вставка направляющая.cdw

1. А4 Молоток.cdw

Молоток Эскиз заготовки (А4) 5.cdw

Операция 05 переход 5 (А3) 2.cdw

Молоток Эскиз детали (А4) 4.cdw

Операция 05 переход 3 (А3) 1.cdw

Операция 15 (А3) 3.cdw

Операция 25 (А3).cdw

Приспособление (А2).cdw

6. Сб.ч. Привода.cdw

На поверхности А дефекты не допускаются.
Качество и толщину покрытия на поверхности Б не
Зубчатые колеса редуктора смазать смазкой ЦИАТИМ-201
Остальные технические требования по ОСТ 58324-78.
7. Гтдросхема.cdw

клапан высокого давления;
- двухпозиционный четырехходовой
распределитель с электромагнитным
управлением и возвратной пружиной;
- гидроцилиндр механизма
закручивания шурупа.
- обратный напорный клапан;
- переливной клапан прямого
действия с золотниковым
запорно-регулирующим элементом;
- регулируемый гидродроссель;
Схема и тактограмма гидропривода
5. Сб.ч. Молот. колонка.cdw

На поверхности А дефекты не допускаются.
Качество и толщину покрытия на поверхности Б не
Трущиеся поверхности В и Г смазать смазкой ЦИАТИМ-201
Остальные технические требования по ОСТ 58324-78.
4. Общий вид.cdw

Гвоздеотсекающий механизм.
Гвоздеподающий механизм.
Колонка молоткового
Рубильник включения-выключения
Спаренные рычаги пуска машины.
Педаль опускания прижимного
Педаль подъема прижимного
3. Кинем. схема.cdw

Шток гидроцилиндра.
Шток гидроцилиндра упора.
Поршень гидроцилиндра упора.
Колонка молоткового механизма.
Гидроцилиндр механизма для
Поршень механизма для
Подшипник скольжения.
Четырёхгранный шток.
Кинематическая схема
1. Раб. место.cdw

Машина для крепления деталей каблука гвоздём и (или) шурупом.
С - Тележка-стеллаж.
КС - Контрольный стол.
РМ00. 01 00 000. 000
2. Раб. место с конв..cdw

Машина для крепления деталей каблука гвоздями и (или) шурупом.
С - Тележка-стеллаж.
КС - Контрольный стол.
РМ00. 02 00 000. 000
Диплом - исправление.doc
Учреждение образования
«Витебский государственный технологический университет»
Кафедра «Машины и аппараты
Лёгкой промышленности»
РАСЧЁТНО-ПОЯСНИТЕЛЬНАЯ ЗАПИСКА
к дипломному проекту
Тема: «Интегрированное рабочее место на участке
Руководитель к.т.н. доц. Дрюков В. В.
Консультанты: к.т.н. доц. Белов Е. В.
к.э.н. доц. Машков Н. М.
Проект рассмотрен и допущен к защите
Зав. Кафедрой проф. Сункуев Б. С.
Введение и обоснование темы дипломного проекта
Обзор механизмов и устройств оборудования используемого на участке крепления каблуков
Описание компоновочной схемы интегрированного рабочего места
Описание кинематической схемы
Описание технологии крепления каблуков
Основные технические характеристики
Расчёт технологических режимов
Расчёт деталей на прочность
Технология машиностроения
Разработка технологического процесса изготовления детали
Уравнения размерных цепей
Расчет режимов резания
Технико-экономический расчёт
Охрана труда и промышленная экология
Характеристика машины для крепления каблука гвоздем и шурупом
Санитарно-гигиенические мероприятия. Вентиляция. Отопление
Санитарно-гигиенические мероприятия. Освещение
Мероприятия по пожарной безопасности
Компенсация профессиональных вредностей. Индивидуальная защита. Личная гигиена
Промышленная экология
Обувь – это изделие предназначенное для предохранения ног от внешних воздействий и несущее утилитарные и эстетические функции.
Обувная промышленность является важной отраслью производящей предметы народного потребления. Ее продукция составляет около 20% общего объема производства отраслей легкой промышленности.
Выпуск обуви в нашей стране непрерывно возрастает.
В массовом количестве выпускается обувь пользующаяся повышенным спросом (модельная женские сапожки зимние утепленные ботинки домашние туфли бесподкладочная обувь и др.). Значительно расширены ассортимент детской обуви и выпуск обуви для различных условий производственной деятельности.
В балансе сырья потребляемого обувной промышленностью все еще 70-80% занимает натуральная кожа увеличение выпуска которой отстает от роста объема производства обуви что обусловливает трудности в материальном обеспечении обувной промышленности.
Современное обувное производство использует технологию изготовления изделий основанную на чрезмерно глубоком разделении труда. Дифференциация технологического процесса на мелкие простые операции способствовала в свое время специализации рабочих механизации производства и труда внедрению конвейерно-поточной системы и следовательно росту производительности труда. Однако такое дробление производственного процесса в современных условиях не обусловливает дальнейший рост производительности труда и препятствует комплексной механизации и автоматизации производства обуви.
Потоки содержат большое число организационных учётных и транспортных операций выполняемых вручную и отвлекающих от 6 до 14% всех рабочих что значительно снижает уровень производительности труда. Применение несовершенных форм организации производства вызывает также значительные потери времени при смене ассортимента продукции. На многих обувных предприятиях низок уровень специализации цехов потоков участков и неэффективна производственная структура.
Анализируя тенденции развития и совершенствования конструкций машин обувного производства можно выделить следующие основные особенности этого процесса:
* агрегирование - объединение (концентрация) нескольких операций в одной машине (агрегате);
* передача непосредственно исполнительных трудовых функций от человека к машине - создание машин (и комплекса машин) полуавтоматического и автоматического действия;
* увеличение производительности машин путем внедрения приспособлений повышения частоты вращения и т.д.;
* повышение качества и точности обработки полуфабриката;
* максимальное приспособление машины к человеку посредством учета комплекса эргономических требований;
* улучшение экономических характеристик новой техники.
При создании новой техники для некоторых стадий обувного производства например для сборки заготовок обуви наряду с учетом перечисленных положений важное значение имеет дальнейшая специализация оборудования: создание машин для выполнения отдельных (или групп) операций для сборки заготовок определенных конструкций изготовления заготовок из различных материалов (искусственных кож тканей и др.).
Одним из принципов конструирования современного специализированного оборудования а так же полуавтоматических и автоматических линий является обеспечение их переналадки при смене изготовляемого вида изделия. Основное направление реализации этого принципа - создание оборудования из нормализованных сменных элементов и серийное производство таких элементов.
Указанное направление обеспечивает высокую производительность оборудования в результате его специализации и одновременно обеспечивает производству высокую маневренность ускоряет переналадку машин подготовку и освоение новых изделий снижает издержки производства. По данным машиностроения стоимость оборудования из нормализованных элементов в 2 раза ниже стоимости оборудования оригинальной необратимой конструкции.
Таким образом мы видим что существует множество различных материалов для изготовления деталей низа обуви к которым относится и каблук а так же есть много методов крепления деталей низа и их комбинаций. Возникает вопрос создания соответствующего оборудования чтобы реализовать выполнение нескольких операций на одной машине а так же рациональной организации рабочего места на участке крепления каблука чтобы максимально сократить норму времени на одну единицу продукции на данном участке так как повышение организационно-технического уровня высокое качество и разнообразный своевременно обновляемый ассортимент продукции четкое выполнение заказов торгующих организаций эффективное использование ресурсов и достижение лучших технико-экономических показателей являются основными задачами совершенствования современного обувного производства.
Обзор механизмов и устройств оборудования используемого на участке крепления каблуков
Механизмы для скрепления деталей и изделий штучными крепителями широко используются в машинах обувного производства для временного прикрепления стелек к колодкам прикрепления подошв обуви соединения элементов (фликов и набоек) каблука вставки блочков а также в некоторых типах обтяжных и затяжных машин для фиксации обтянутой или затянутой заготовки на колодке. В качестве штучных крепителей используют шпильки винты гвозди полускобки скобки блочки и т. д. При скреплении двух или нескольких деталей их спрессовывают и перпендикулярно или под углом к плоскости их скрепления поступательным или поступательным с вращением движением вводят штучный крепитель.
Из машин для скрепления деталей и изделий штучными крепителями применяют гвоздевые скобочные и блочковые ограниченное применение находят шпилечные и винтовые машины. Из гвоздевых машин следует отметить: АСГ-19 — для прикрепления подошв стандартными гвоздями; ПДН-О — для прикрепления подошв гвоздями изготовляемыми машиной; МКН ПКВ и ПДК — для прикрепления каблука гвоздями; 04222Р.1 (ЧССР) — для прибивания каблуков к обуви гвоздями; ОМ-4М — для обтяжки заготовки на колодке пятью гвоздями; полуавтоматы 02038Р1 и 02038Р2 (ЧССР) — для затяжки пяточной части заготовки обуви 12—20 гвоздями; ЗВ-1 и ЗВ-2-О 02087Р1 и 02074Р2 (ЧССР) — для затяжки заготовки верха обуви на колодке и др. К скобочным относится машина ППС-С — для временного прикрепления стелек к колодкам и подошв к стелькам скобками.
В зависимости от формы пяточной части подошвы высоты и материала каблука назначения обуви каблук можно крепить гвоздями шурупами или клеем. Для прикрепления каблуков применяют пресс ППГ-4-О машины 04222Р1 04222РЗ 04299Р1 04299Р2 04352Р1 (ЧССР) машины 947 РТ и 935 BLA фирмы «Сигма» (Италия).
Машины 04299Р1 и 04299Р2. Предназначены для крепления изнутри разнообразных по форме пластмассовых каблуков металлическими шурупами с крестообразной канавкой на головке преимущественно к женской обуви. Машины пневматические.
На машине 04299Р2 в отличие от машины 04299Р1 можно прикреплять каблуки к женским сапожкам.
Технологический процесс на машине 04299Р1 выполняется следующим образом. Колодку с затянутой заготовкой верха и установленным каблуком надевают следом вверх на направляющий штуцер машины который входит во втулку пяточной части колодки. При включении машины каблук прижимается к обуви и винт входит через стельку в каблук после чего полупару вручную снимают с машины и цикл повторяется.
Машина 947 РТ фирмы «Сигма» (Италия). На машине прикрепляют каблуки гвоздями изнутри. Машина имеет гидропривод и механическое устройство для подачи гвоздей по одному из двух каналов что дает возможность использовать гвозди различной длины.
Машина 935 BLA фирмы «Сигма» (Италия). Предназначена для прикрепления каблуков изнутри к женской обуви одним шурупом.
Машина 04222Р1. Является универсальной и предназначена для прикрепления гвоздями различных каблуков к любому виду обуви как снаружи так и изнутри. Машина имеет электромеханический привод гидравлическое устройство прессования деталей и забивания гвоздей.
Рисунок 1 - Машина 04222Р1 (а) схемы прикрепления каблуков изнутри (б)
снаружи (в) и движения гвоздеподающей кассеты (г)
кинематическая схема (д)
Техническая характеристика машины 04222Р1
Производительность пар обуви в час До 250
Усилие забивания гвоздей кН 5—40
Длина гвоздей мм 10—35
Мощность электродвигателя кВт 042
Габарит мм 550X800X1
При прибивании каблука изнутри обувь без колодки надевают следом вверх на головку 8 (рис. 1 а б) стойки 9 машины предварительно наполненную гвоздями и на пяточную часть обуви устанавливают каблук. При легком нажатии на педаль 12 верхний упор 7 опускается и прижимает каблук к обуви. При дальнейшем нажатии на педаль включают машину. Происходит дополнительное прижатие каблука после чего гвозди забиваются в него изнутри. Обработанную обувь снимают со стойки машины гвоздеподающая кассета автоматически наполняет головку 8 требуемым числом гвоздей и машина выключается.
Время между прибиванием каблука и переносом гвоздей в головку 8 можно регулировать рукояткой 11 изменяя этим продолжительность цикла работы машины.
При прибивании каблука снаружи на машине устанавливают отклоняющийся верхний упор 13 (рис. 1 б) и головку 14 с выемкой для каблука. После заполнения головки 14 гвоздями в ее выемку вкладывают каблук правой рукой за рукоятку отклоняют верхний упор на себя настолько чтобы на него можно было легко надеть обувь упор возвращают в первоначальное положение и слегка нажимают на педаль до тех пор пока обувь не будет плотно прижата к каблуку. Пальцами левой руки проверяют совпадение пяточной части обуви с каблуком и дальнейшим нажатием на педаль включают машину. Гвозди забиваются в каблук. Обработанную обувь снимают с верхнего упора головка автоматически наполняется гвоздями и цикл работы повторяется.
Машина имеет механизмы привода подачи гвоздей молотков и прессования деталей. Механизм подачи гвоздей 5 (см. рис. 1 а) расположен в верхней части машины и имеет бункер 6 для гвоздей. Гвозди от механизма подачи поступают в головку 8 с помощью кассеты З совершающей сложное движение по траектории АБВГ (рис. 1 г). Одновременно может подаваться от 1 до 20 гвоздей.
Усилие прессования деталей и забивания гвоздей зависит от материала каблука и числа гвоздей. Это усилие регулируют маховиком 2 (см. рис. 1 а).
Электрооборудование машины расположено в коробке 4. Машина имеет два рабочих столика 10 и выдвигающиеся колесики 1 для транспортирования машины.
Машина 04222РЗ. Отличается конструкцией рабочих органов (стойки и верхнего упора) и предназначена для прикрепления каблуков к сапогам гвоздями снаружи (рис. 2).
Машина ПДН-1-О предназначена для крепления деталей низа обуви: стелек полустелек геленков простилок гвоздями при сборке школьной женской и мужской обуви всех моделей.
Рисунок 3 - Общий вид машины ПДН-1-О
Устройство и принцип работы. Машина (рис. 3) состоит из станины 7 головки 2 гвоздевого барабана 3 электрооборудования 4.
Станина представляет собой сварную конструкцию на которой смонтированы все сборочные единицы машины.
Рисунок 4 - Кинематическая схема машины ПДН-1-О
Головка (рис. 4) предназначена для забивания гвоздей. От электродвигателя клиноременной 1 и зубчатой 2 передач вращение получает шестерня-полумуфта 3 свободно сидящая на главном валу головки. Главный вал приводится во вращение через полумуфту 6 закрепленную на нем. Шестерня-полумуфта 3 и полумуфта 6 соединены подпружиненной скользящей шпонкой 4 имеющей конусообразный конец который входит в одно из шести отверстий шестёрни-полумуфты 3. Шпонка 4 расцепляется с полумуфтой 3 рычагом 5 при нажатии на педаль 16 через систему тяг и рычагов.
В верхней части головки смонтирован патрон 14 с ловителем гвоздя штанга 11 с молотком 13 пружина 12 сообщающая движение штанге для удара. Для смягчения удара в верхней части штанги установлены шайбы 9 удерживаемые чашечной гайкой. На конце главного вала смонтированы кулачки 8 и 10. От кулачка 8 прикрепленного к торцу кулачка 10 осуществляется подъем штанги 11. Кулачок 10 через двуплечий рычаг 17 сооб-щает возвратно-поступательное движение отсекателю 19 гвоздевого барабана.
Механизм нижнего упора представляет собой двуплечий рычаг 20 соединенный с наковальней 15 которая получает возвратно-поступательное движение от кулачка 7 жестко соединенного с шестерней-полумуфтой 6 через подпружиненную тягу 21.
Усилие прибивания материала гвоздями регулируют пружиной 12.
Гвоздевой барабан 22 предназначен для отделения гвоздя и подачи его в патрон по одному за каждый оборот главного вала. Корпус барабана закреплен на головке. Привод барабана состоит из конического и цилиндрического зубчатых колес.
Рисунок 5 - Гвоздевой барабан машины ПДН-1-О
От зубчатого конического колеса 2 (рис. 5) через зубчатое колесо 5 и предохранительную шариковую муфту 5 вращение передается валу 4. На алу 4 закреплена крышка 1 с совочками 6 захватывающими при вращении гвозди из корпуса барабана. Гвозди высыпаются на наклонный лоток 7 и далее поступают в наклонный канал 9 в конце которого смонтирован отсекатель10.
Внутри барабана установлен сбрасыватель 8 тех гвоздей которые легли поперек канала и препятствуют прохождению других гвоздей к отсекателю. Сбрасыватель гвоздей приводится в движение рычагом 11 который под воздействием пружины утапливается в прорезь выступающей части зубчатого колеса 5. За один оборот зубчатого колеса 5 сбрасыватель срабатывает дважды. Положение отсекателя 19 (см. рис. 4) регулируют винтом 18.
Электрооборудование состоит из пульта управления расположенного на дверце станины 1 (см. рис. 3) со стороны обслуживания; панели управления находящейся с внутренней стороны дверцы станины электродвигателя 5; ламп местного освещения. Электродвигатель привода машины включается тумблером вместе с лампой местного освещения. Электрооборудование защищено от перегрузок и токов короткого замыкания автоматическими выключателями.
Машина подключается к цеховой сети с. помощью штепсельного разъема. Положение электродвигателя и натяжение клиновых ремней регулируют болтами 6 (см. рис. 3). Машину подключают к сети переменного тока так чтобы вал электродвигателя вращался по часовой стрелке (со стороны обслуживания) нанесенной на шкив электродвигателя.
До начала работы в гвоздевой аппарат засыпают 05 кг гвоздей. Проверяют работу механизмов пуска и останова: при включенном выключателе рабочие органы машины должны находиться в исходном состоянии.
Работа на машине осуществляется следующим образом. Детали низа накладывают друг на друга вводят между патроном и упором прижимают в скрепляемом месте к патрону. При нажатии на педаль гвоздь забивается.
При креплении деталей низа к колодке нижний упор снимают. Колодку с наложенной деталью подводят к патрону прижимают скрепляемым местом к отверстию в патроне нажимают на педаль и гвоздь забивается.
1 Описание компоновочной схемы интегрированного рабочего места
Огромное значение совершенствования организации труда для повышения эффективности производства объясняется тем что живому труду принадлежит наиболее активная функция в производстве.Разделение труда вызывает следующее расчленение производственного процесса: потоки участки и операции. Для бесперебойного и эффективного протекания производственного процесса необходимо установление целесообразной взаимосвязи между его отдельными частями и соответствующими им подразделениями. Это достигается разработкой рациональной производственной структуры предприятия представляющей собой наиболее общую форму организации производства - организацию производства в пространстве. Ее характер определяется уровнем организационно-технического развития производства степенью совершенствования техники технологии и уровнем специализации. От характера производственной структуры зависит техническое и организационное развитие производства слаженность работы всех звеньев предприятия экономичность аппарата управления уровень производительности труда и использования оборудования размер издержек производства.
Разделение труда в обувном производстве совершенствуется на основе следующих принципов:
- установления целесообразного расчленения технологического процесса на операции для устранения монотонности в работе;
- отделения вспомогательных работ от основных квалифицированных работ от неквалифицированных;
- достижения высокого качества обработки полуфабриката
обеспечения полной загрузки специализированных исполнителей и более высокого использования оборудования.
Согласно рекомендациям физиологов для устранения вредного влияния монотонности на организм человека продолжительность операции должна быть не менее 075 мин. Для этого создают многооперационные агрегаты полуавтоматического и автоматического действия. Частными средствами борьбы с монотонностью используемыми на обувных предприятиях являются: совмещение операций периодическая смена выполняемых исполнителем операций в течение рабочего дня установление скорости конвейера в соответствии с характером кривых изменения работоспособности введение перерывов для отдыха музыка и др.
Необходимая часть организации труда — организация рабочих мест. Рабочее
место — это первичное звено производства зона трудовой деятельности
рабочего или группы рабочих (если рабочее место коллективное) оснащенная необходимыми средствами для выполнения производственного задания. Под организацией рабочего места понимается система его оснащения и планировки подчиненная целям производства. Эти решения в свою очередь зависят от характера и специализации рабочего места от его вида и роли в производственном процессе.
В зависимости от специфики производства рабочие места могут быть специализированными и универсальными индивидуальными и коллективными стационарными и подвижными одностаночными и многостаночными постоянными и временными а также рабочими местами ручной работы механизированными автоматизированными аппаратными рабочими местами служащих и др.
Оснащение рабочего места складывается из совокупности средств необходимых для осуществления производственного процесса. К ним относятся:
а) основное технологическое и вспомогательное оборудование;
б) технологическая оснастка — рабочий и мерительный инструмент
приспособления запасные части;
в) организационная оснастка — средства связи и сигнализации
г) рабочая мебель тара; рабочая документация; средства
коммуникации для подачи на рабочее место сырья материалов
д) хозяйственный инвентарь для поддержания чистоты и порядка и
Полное и комплектное оснащение рабочего места позволяет наилучшим образом организовать процесс труда. Для этого необходима рациональная планировка средств оснащения — размещение их на рабочем месте так чтобы обеспечивалось удобство их обслуживания свободный доступ к механизмам и их отдельным узлам требующим регулирования и контроля экономия движений и перемещений работника удобная рабочая поза хороший обзор рабочей зоны безопасность труда экономия производственной площади наличие проходов подъездов и проездов для транспортных средств взаимосвязь со смежными рабочими местами и с местом бригадира мастера другого руководителя. Основные показатели экономии движений: уменьшение количества движений; повышение их скорости и снижение утомляемости за счет сокращения протяженности движения; выбор рациональных направлений повышение решительности естественности и привычности движений; совмещение и обеспечение симметричности движений и др.
Средством реализации принципов экономии движений является прогрессивная организация рабочего места включающая рациональную планировку обеспечение организационной оснасткой и четкую организацию обслуживания.
Планировка рабочего места заключается в установлении целесообразного расположения оборудования инструмента приспособлений полуфабрикатов и организационной оснастки. Все средства труда (инструменты приспособления и т.д.) должны располагаться с учетом антропометрических и физиологических данных человека (предела досягаемости рук и наиболее удобных зон движений углов видимости и т.д.).
При организации рабочего места должно учитываться следующее:
- для обеспечения симметричности предметы которые рабочий берет левой рукой должны находится слева а которые правой - справа;
- привычность движений достигается рациональным расположением инструментов приспособлений и т. п. всегда на одних и тех же местах;
- для сокращения протяженности движений инструменты полуфабрикаты оснастку которыми в течение смены пользуется часто следует располагать ближе к рабочему а которыми приходится пользоваться редко можно несколько удалить от рабочего (в пределах рабочей зоны) и др.
Рационально располагая инструменты и предметы труда нужно стремиться так же к обеспечению и ритмичности движений максимальному использованию обратных движений рук.
Научно-исследовательские организации и передовые обувные предприятия уже разработали ряд проектов рациональной планировки типовых рабочих мест обувного производства.
Необходимым условием реализации принципов экономии движений является также выбор рациональной конструкции организационной оснастки: производственных столов стульев тумбочек стеллажей подставок трапов и т.п.
При рациональной конструкции организационной оснастки исполнитель освобождается от лишних движений повышенных физических усилий и имеет удобную рабочую позу. Выбор рабочей позы зависит от величины физических усилий при обработке конструктивных особенностей оборудования и зоны обслуживания.
Физиологические исследования показали что если мышечное напряжение при правильной рабочей позе "сидя" принять за 100% то при удобной позе "стоя" оно возрастает на 16% а при неудобной (согнутой) на 98%.
В соответствии с этим рабочая поза "стоя" должна применяться только в тех случаях если при работе требуются значительные физические усилия (50-100 Н и выше) и при большой зоне обслуживания.
Наиболее рациональная рабочая поза - переменная позволяющая рабочему через определенные промежутки времени переходить от позы "стоя" к позе "сидя" и наоборот.
Важное значение имеет обеспечиваемая конструкцией рабочего стола высота рабочей зоны и правильное её соотношение с высотой несущей части конвейера. Оптимальной считается высота стола 850 мм при позе "сидя" и 1100 мм при позе "стоя". Уровень рабочей поверхности стола должен быть на 30-50 мм выше несущей части конвейера. При двухъярусном конвейере на пошивочном участке рациональной считается высота: верхнего яруса - 1000 мм нижнего — 700 мм.
На рабочих местах при позе "сидя" целесообразно применение стульев с полумягкими профилированными сиденьями и спинками. Высота сиденья и угол наклона спинки должны регулироваться.
Крепление каблуков чаще всего производится на рабочих местах при позе "стоя" поэтому в соответствии с ГОСТом 12.2.033-78 который устанавливает Общие эргономические требования на рабочем месте при выполнении работ стоя. Этот стандарт устанавливает общие эргономические требования к рабочим местам при выполнении работ в положении стоя при проектировании нового и модернизации действующего оборудования и производственных процессов.
Стандарт не устанавливает требования к рабочим местам транспортных средств машин и оборудования перемещающихся в процессе работы а также на рабочие места для учащихся проходящих производственную практику и военнослужащих.
Рабочее место для выполнения работ стоя организуют при физической работе средней тяжести и тяжёлой а также при технологически обусловленной величине рабочей зоны превышающей её параметры при работе сидя. Категория работ - по ГОСТ 12.1.005-76.
Конструкция взаимное расположение элементов рабочего места (органы управления средства отображения информации и т.д.) должны соответствовать антропометрическим физиологическим и психологическим требованиям а также характеру работы.
Рабочее место должно быть организовано в соответствии с требованиями стандартов технических условий и (или) методических указаний по безопасности труда.
Размерные характеристики рабочего места.
Рабочее место должно обеспечивать выполнение трудовых операций в пределах зоны досягаемости моторного поля. Зоны досягаемости моторного поля в вертикальной и горизонтальной плоскостях для средних размеров тела человека приведены на рис. 7 и 8.
Рисунок 7 – Зоны досягаемости моторного поля в вертикальной плоскости
Рисунок 8 – Зоны досягаемости моторного поля в вертикальной плоскости
Выполнение трудовых операций «часто» и «очень часто» должно быть обеспечено в пределах зоны лёгкой досягаемости и оптимальной зоны моторного поля (рис. 9 и 10).Частоту выполнения операций принимают: очень часто - две и более операций в 1 мин часто - менее двух операций в 1 мин но более двух операций в 1 ч; редко - не более двух операций в 1 ч.
При проектировании оборудования и организации рабочего места следует учитывать антропометрические показатели женщин (если работают только женщины) и мужчин (если работают только мужчины); если оборудования обслуживают мужчины и женщины - общие средние показатели мужчин и женщин.
Организация рабочего места и конструкция оборудования должны обеспечивать прямое и свободное положение корпуса тела работающего или наклон его вперёд не более чем на 15 град.
Конструкцией производственного оборудования и организацией рабочего места должно быть обеспечено оптимальное положение работающего которое достигается регулированием высоты рабочей поверхности. Регулируемые параметры в зависимости от тяжести труда и роста работающего следует выбирать по номограмме приведённой на рис. 11;
подставки для ног при нерегулируемой высоте рабочей поверхности . В этом случае высоту рабочей поверхности устанавливают по номограмме приведённой на рис. 11 для работающего ростом 1800 мм. Оптимальная рабочая поза для работающих более низкого роста достигается за счёт увеличения высоты подставки для ног на величину равную разности между высотой рабочей поверхности для работающего ростом 1800 мм и высотой рабочей поверхности оптимальной для роста данного работающего.
В тех случаях когда невозможно осуществить регулирование высоты рабочей поверхности и подставки для ног допускается проектировать и изготовлять оборудование с нерегулируемой высотой рабочей поверхности и подставки для лог. В этом случае числовые значения высоты рабочей поверхности определяют по табл. 1.
Таблица 1 - Высота рабочей поверхности мм
Требования к размещению органов управления.
Общие требования к размещению органов управления - по ГОСТ 22269-76.
При работе двумя руками органы управления размещают с таким расчётом чтобы не было перекрещивания рук.
При размещении органов управления следует руководствоваться данными табл. 1 и рис. 9-11. Органы управления на рабочей поверхности в горизонтальной и вертикальной плоскостях необходимо размещать с учётом следующих требований :
очень часто используемые и наиболее важные органы управления должны быть расположены в зоне 1 (рис. 9 и 10);
часто используемые и менее важные органы управления не допускается располагать за пределами зоны 2 а при тяжёлой работе - выше 1000 мм от площадки на которой стоит рабочий;
редко используемые органы управления не допускается располагать за пределами зоны 3.
Органы управления используемые до 5 раз в смену допускается располагать за пределами зоны досягаемости моторного поля .
Аварийные органы управления следует располагать в пределах зоны досягаемости моторного поля при этом следует предусмотреть специальные средства опознавания и предотвращения их непроизвольного и самопроизвольного включения в соответствии с ГОСТ 12.2.003-74.
При необходимости освобождения рук операции не требующие точности и быстроты выполнения могут быть переданы ножным органам управления.
Требования к размещению средств отображения информации.
Общие требования к размещению средств отображения информации - по ГОСТ 22269-76.
Средняя высота расположения средств отображения информации должна соответствовать значениям приведённым в табл. 2.
Таблица 2 – Средняя высота расположения средств отображения информации
Очень часто используемые средства отображения информации требующие точного и быстрого считывания показаний следует располагать в вертикальной плоскости под углом +-15 град. от нормальной линии взгляда и горизонтальной плоскости под углом +-15 град. от сагиттальной плоскости (рис. 12 и 13).
Часто используемые средства отображения информации требующие менее точного и быстрого считывания показаний допускается располагать в вертикальной плоскости под углом +-30 град от нормальной линии взгляда и в горизонтальной плоскости под углом +-30 град от сагиттальной плоскости.
Примечание . Для стрелочных индикаторов допускаемый угол отклонения от нормальной линии взгляда - не более 25 градусов.
Редко используемые средства отображения информации допускается располагать в вертикальной плоскости под углом +-60 град от нормальной линии взгляда и в горизонтальной плоскости под углом +-60 град от сагиттальной плоскости (при движении глаз и повороте головы).
Проводимые аттестации рабочих мест позволяют выявлять отступления от нормативных требований к ним и совершенствовать организацию рабочих мест в соответствии с требованиями научной организации труда. По результатам аттестации малоэффективные рабочие места могут упраздняться при этом появляется возможность более рационального использования производственных площадей установки современного высокопроизводительного оборудования и
интенсификации производственного процесса.
Уровень организации труда на рабочем месте зависит также от совершенства системы его обслуживания. Организация обслуживания рабочих мест предполагает:
* своевременное обеспечение рабочих мест всем необходимым
включая техническое обслуживание — наладку смазку регулировку;
* ремонтное и межремонтное обслуживание; обеспечение сырьем
* полуфабрикатами комплектующими изделиями инструментом;
* подачу необходимых видов энергии — тепла электроэнергии
* межоперационный и финишный контроль качества продукции;
. * хозяйственное обслуживание — уборку чистку оборудования;
* транспортное обслуживание и т.д.
Чтобы организовать обслуживание рабочих мест необходимо решить следующие вопросы:
-определить в каких видах обслуживания нуждается каждое рабочее
-по каждому виду обслуживания установить его норму т.е. обосновать
объем обслуживания в смену месяц год;
-установить регламент обслуживания т.е. график периодичность и
-закрепить выполнение обязанностей по обслуживанию за строго
определенными исполнителями.
Эффективность обслуживания рабочих мест может быть достигнута лишь при соблюдении:
***принципа предупредительности обслуживания предусматривающего выполнение соответствующих работ до того как процесс производства прервется в силу несвоевременного их выполнения; принципа оперативности обслуживания — быстроты реагирования на возможные сбои производства;
***принципа комплексности выражающегося в обеспечении разностороннего обслуживания по всем его видам; принципа плановости заключающегося в проведении расчетов потребности в видах сроках и объемах обслуживания каждого рабочего места.
Прогресс в системах обслуживания рабочих мест состоит в переходе от дежурного обслуживания т.е. обслуживания по вызову с места остановки производства к стандартному обслуживанию основанному на расчетах норм обслуживания и реализации планово-предупредительного проведения обслуживающих работ.
Достижение эффективных решений по организации рабочих мест и систем их обслуживания облегчается использованием разработанных типовых проектов организации труда для массовых профессий рабочих и служащих. Типовой проект организации труда — это как правило средоточие передового опыта
организации труда в котором находят отражение все принципиальные вопросы организации труда в том числе вопросы оснащения и планировки рабочих мест организации их обслуживания.
На основании вышеизложенного построим структурную схему интегрированного рабочего места для креплении каблука при ручном перемещении комплектующих и заготовок:
Рис 14 - Структурная схема интегрированного рабочего места на участке крепления каблука при ручной транспортировке
Последнее время на предприятиях получило широкое применение линий по производству обуви где междуоперационное перемещение заготовок осуществляется с помощью конвейера. Тогда компоновочная схема рабочего места для крепления каблука будет иметь вид:
Рисунок 15 - Структурная схема интегрированного рабочего места на участке крепления каблука при конвейерном транспортировании.
2 Описание кинематической схемы
Кинематическая схема машины для крепления каблука гвоздями и шурупами приведена на рисунке 16. На нем же приводится описание позиций звеньев входящих в схему.
Рисунок 16 - Кинематическая схема универсальной машины для крепления каблука гвоздями и (или) шурупом
На машине схема которой представлена на рис. 16 производится крепление каблука к подошве обуви с помощью гвоздей и (или) шурупов. Молотковый механизм рассмотрим на примере одного из пяти молотков установленных на машине которые приводятся в действие с помощью пневмопривода.
Трёхсекционный пневмоцилиндр 1 содержит три поршня 2 которые жёстко закреплены на общем штоке 3 на котором закреплена планка 4. Эта планка приводит в движение толкатель 5. Толкатель в свою очередь движет молоткодержатель 6 в котором подвижно установлен стержень-молоток 8 который и забивает гвоздь 9. Полупара обуви фиксируется на колонке молоткового механизма 14 с помощью механизма упора который состоит из гидроцилиндра упора 13 с поршнем 12 который движет шток на котором закреплён прижимной механизм 10.
Также машина оснащена механизмом для ввинчивания шурупа. Он состоит из гидроцилиндра 16 поршня 17 который через скользящий подшипник 18 передает поступательные перемещения четырёхгранному штоку 19 вращательное движение которому передаётся через редуктор 20 от электродвигателя 21. Шток проходит через станину 15 входит в колонку молоткового механизма 14 и соединяется со вставкой-отвёрткой 22 которая и ввинчивает шуруп 23.
3 Описание технологии крепления каблуков на предприятиях
Каблуки крепятся независимо от вида подошвы здесь метод крепления определяется материалом высотой фасоном и половозрастным
назначением обуви. В качестве крепителей используются каблучные гвозди втулки стержни и шурупы – для высоких и средних каблуков клеи и другие материалы. Все методы крепления в зависимости от вида крепителя разделяют на штифтовые клеевые комбинированные.
Резиновые каблуки из-за плохого держания крепителей малого сопротивления резины вырыванию гвоздя чаще прикрепляют снаружи. Число гвоздей (7-13) зависит от фасона каблука и от размера обуви. Гвозди должны быть равномерно распределены по поверхности каблука и располагаться на расстоянии 4-10 мм от края стельки.
Крепление гвоздями осуществляют снаружи и изнутри обуви. Клеи для крепления низких каблуков применяются в детской обуви. Комбинированные методы – клеевой вместе со штифтовым –применяются наиболее часто так как они дают наибольшую прочность.
Для модельной обуви в основном применяются кожаные наборные деревянные и пластмассовые (полиэтиленовые полипропиленовые капроновые) с обтяжкой из кожи или крашеные каблуки.
Кожаные наборные каблуки изготовляются вручную в мастерской из фликов. Пластмассовые и деревянные каблуки приобретаются согласно размеру фасону и виду. Завинчивание винтов-саморезов (шурупов) для крепления каблуков в малом ручном производстве осуществляется при помощи мощной ручной отвертки (простой или крестовой).
Забивание каблучных гвоздей производится сапожным молотком или при помощи специального приспособления описанного в разделе посвященном механизмам и оборудованию для гвоздевого крепления каблука.
Каблуки прикрепляются гвоздями винтами металлическими втулками (высокие каблуки) и клеями или одновременно тем и другим. Выбор крепителя определяется материалом и высотой каблука.
Прикрепление каблуков к следу обуви может производиться перед приклеиванием подошвы если язычок подошвы приклеивается к фронтальной части среднего или высокого каблуков или после приклеивания подошвы если язычок подошвы закрепляется в "замок" т. е. каблук накладывается на подошву.
Рисунок 17 – Виды гвоздей
Прикрепление каблуков гвоздями можно производить двумя способами: изнутри и снаружи. Первый способ является более распространенным.
В зависимости от способа крепления и материала каблука могут применяться различные каблучные гвозди рис. 17 отличающиеся диаметром формой стержня и шляпки формой и длиной острия. При прикреплении каблука изнутри длина гвоздя берется такой чтобы он
прошел через стельку затяжные кромки задника и верха обуви подошву и каблук но не доходил на 2-3 мм до ходовой поверхности набойки.
При прикреплении каблука снаружи гвоздь должен пройти через каблук подошву затяжные кромки верха обуви и задника стельку и загнуться на ее поверхности. По форме стержня гвозди бывают цилиндрические пирамидальные и навинтованные шляпки гвоздя могут быть круглые плоские или конусные. Диаметр шляпки гвоздя с плоской головкой колеблется от 17 до 33 мм; с потайной головкой — от 16 до 21 мм.
Острие каблучных гвоздей может быть четырехгранным пирамидальным длиной 15-25 мм для прикрепления каблуков изнутри и удлиненным овальным длиной 4-5 мм для прикрепления каблуков снаружи.
Рисунок 18 – Виды каблучных шурупов
Для прикрепления деревянных и капроновых каблуков применяются гвозди каблучные навинтованные рис. 18 Они должны иметь на стержне накатку и плоскую головку овальной формы. Гвозди могут быть с острием и без острия. В некоторых случаях применяются каблучные навинтованные гвозди с конусной головкой и четырехгранным пирамидальным острием длиной 25-35 мм. В настоящее время наиболее распространенным способом особенно для среднего и высокого каблуков является прикрепление их винтами. Для этого применяются винты № 12-18 различной длины с резьбой по всей длине.
Каблук предварительно окрашивают по всей поверхности в цвет верха обуви или обтягивают кожей гармонирующей с цветом заготовки. Обтяжка должна плотно облегать всю боковую поверхность каблука и не иметь складок или морщин.
В настоящее время стали широко применяться каблуки из различных пластмасс (ударопрочного полистирола полипропилена или капрона). Пластмассовые каблуки за исключением про-пиленовых можно легко окрашивать в различный цвет прямо в массе или после их отливки перед прикреплением т. е. их можно применять без кожаных обтяжек что значительно снижает себестоимость выпускаемойпродукции. Каблуки из пластмасс красятся в любой цвет путем нанесения красителя на боковую поверхность. Все больше получает распространение окраска с имитацией под наборный кожаный каблук. Это достигается нанесением на боковую поверхность поперечных полос более темного цвета чем основной цвет.
Прикрепление низких каблуков.
Прикрепление каблука снаружи гвоздями с различной формой головки и шляпки осуществляется двумя способами: без набойки или одновременно с набойкой. Гвоздь должен пройти через все скрепляемые материалы и загнуться на стельке.
Наиболее распространенным способом является прикрепление низких каблуков изнутри гвоздями. Для лучшего прижатия каблука по всему периметру пяточной части обуви ляпис каблука перед прибивкой тщательно промазывается наиритовым клеем.Сборный кожаный каблук состоящий из набойки поднабойки фликов и обводки (кранца) крепится изнутри каблучными гвоздями.
При ручном изготовлении обуви применяются два способа сборки и прикрепления кожаных каблуков. По способу наращивания кожаные флики последовательно склеивают друг с другом и одновременно прикрепляют их к пяточной части стельки и подошвы. По второму способу более распространенному кожаные флики предварительно скрепляют между собой получая сборный каблук. Перед прикреплением каблука пяточную часть подошвы обрезают по грани пятки причем урез должен быть строго вертикальным и ровным. Кранец предварительно увлажняют подшкуривают с бахтармы крепят к подошве клеем и деревянными шпильками. После этого с бахтармяной стороны кранец спускают по краям ножом обрабатывают рашпилем и промазывают тонким слоем резинового клея. Затем на него накладывают собранный каблук и крепят его деревянными шпильками или навинтованной проволокой. Расстояние шпилек от края каблука в обуви с рантом до пяточной части составляет 6-8 мм. Обрезанная боковая поверхность каблука должна быть ровной без выхватов и иметь вертикальное направление. После этого 5-7 гвоздями или шпильками прикрепляют поднабойку и набойку.
Резиновые формованные каблуки прикрепляют к обуви с предварительным приклеиванием их наиритовым клеем. Приклеивание предотвращает появление зазоров между каблуком и подошвой. Клей наносят один раз ровным слоем на отшлифованную верхнюю поверхность (ляпис) каблука и пяточную часть подошвы. Каблук может быть приклеен одновременно с подошвой.
Прикрепление средних каблуков.
Средний каблук для модельной обуви может быть деревянным сборным кожаным и пластмассовым. Сборный кожаный средний каблук крепится так же как низкий.
Средний пластмассовый каблук учитывая особенности материала каблука крепится несколько иначе чем кожаный и деревянный. Если материал каблука имеет необходимую вязкость и не очень хрупкий то он крепится специальными навинтованными гвоздями. Таким же способом могут быть прикреплены и каблуки имеющие специальные деревянные вкладыши в которые вбиваются навинтованные гвозди. Наиболее распространено прикрепление пластмассовых каблуков винтами. Эта операция выполняется на двухшпиндельной машине для винчения каблуков. Обувь предварительно снятая с колодок сверлится со стороны стельки в пяточной части сверлом закрепленным на одном из вращающихся шпинделей машины. Диаметр сверла должен быть несколько меньше диаметра винта. В полученные отверстия вручную вставляются винты головки которых поочередно прижимаются к торцу второго вращающегося шпинделя. Внутренняя часть торца этого шпинделя сделана на конус так что головка винта входит немного в него и при дальнейшем нажатии на подошву прижимается плотнее к конусу и за счет передачи вращательного движения от шпинделя винту происходит завинчивание последнего в тело стельки и каблука. Головка винта должна быть утоплена заподлицо в стельке. Каблук крепится 3 винтами № 12-18 длина которых зависит от толщины скрепляемых деталей.
Во всех случаях перед прикреплением кожаных деревянных и пластмассовых каблуков ляпис должен быть намазан наиритовым клеем.
Если подошва приклеивается на фронтальную часть среднего каблука то в этом случае он должен быть предварительно посажен на специальный (посадочный) гвоздь. Намазанный в ляписной части клеем каблук устанавливают в пяточной части полупары и прижимают посадочным гвоздем так чтобы он вошел в тело каблука на всю длину и верхней головкой коснулся упорной шайбы. Острие гвоздя должно войти в деревянную пробку колодки.
Крокуль подошвы приклеивают к фронту деревянного каблука и прикрепляют металлическими шпильками на машине или вручную под углом 7-10°. С каждой стороны среднего каблука должно быть забито 3-4 шпильки. Расстояние шпилек от грани каблука 25-30 мм между центрами шпилек 10-12 мм. Крокуль должен быть длиннее каблука на 4-5 мм и выступать за боковую грань его равномерно на 10-15 мм. В пластмассовых каблуках крокуль подошвы прикрепляется наиритовьм клеем.
После прикрепления крокуля подошвы удаляется посадочный гвоздь конец крокуля приклеивается к поднабоечной части каблука наиритовым клеем вбивается металлическая втулка венчик которой должен захватить конец крокуля подошвы и плотно прижать его к каблуку. Втулка должна пройти через каблук стельку и выступать над ней на 4-5 мм. После снятия обуви с колодок втулку расклепывают и окончательно прикрепляют каблук одним из способов описанных выше.
Прикрепление высоких каблуков.
Для модельной обуви применяются каблуки из пластмасс различных форм и высоты. Высокие каблуки крепятся в основном изнутри за исключением тех случаев когда они укрепляются металлическими втулками которые забиваются снаружи. Но в высоком каблуке в отличие от среднего каблука эта втулка играет роль не крепителя а специального стержня предохраняющего от переломов и изгибов. Прикрепление высокого каблука производится винтами или навинтованными гвоздями так же как и среднего каблука. Ляпис каблука перед прикреплением его к пяточной части обуви промазывается клеем.
Прикрепление набоек.
Во время эксплуатации обуви набойка испытывает большую нагрузку поэтому она должна быть изготовлена из материала высокой прочности. Такими материалами могут быть кожа и кожеподобная резина различные пластмассы (капрон полиамиды поливинилхлорид полиуретан) или сплавы металлов. Набойка должна хорошо работать на истирание не должна быть хрупкой ломкой и пластичной. Поэтому все меньше используют набойки из кожи и кожеподобной резины.
В зависимости от материала и формы набойки а также формы и строения каблука применяют различные способы прикрепления набоек.
Прикрепление набоек из кожи резины и искусственных кож в обуви на деревянном или гвоздимом капроновом каблуках производится каблучно-набоечными гвоздями с плоской или потайной (конусной) головкой № 12-24. Каблучно-набоечный гвоздь должен иметь гладкий цилиндрический стержень четырехгранное пирамидальное острие. На высокий каблук набойку прибивают тремя гвоздями на средний — пятью-семью. Расстояние от края набойки до центра гвоздя определяется величиной набойки. Гвозди забиваются вручную или на машине с наклоном внутрь каблука. Головки гвоздей должны быть забиты заподлицо с поверхностью набойки а острие гвоздя не должно выходить на боковую поверхность каблука.
В обуви с кожаной набойкой иногда применяют целлулоидную поднабойку которая предохраняет каблук от преждевременного износа.
Для прикрепления металлической набойки применяют гвозди с шестигранным стержнем длиной 22 мм предотвращающим поворачивание гвоздя и набойки вокруг своей оси и круглой конусной головкой со сферической поверхностью обоих оснований. Острие гвоздя четырехгранное пирамидальное. Гвоздь забивается вручную молотком так что головка его полностью утапливается в выемке металлической набойки. Для прикрепления пластмассовых набоек к каблукам применяется метод их запрессовки. Сущность этого метода заключается в том что для облегчения веса пластмассового каблука в его теле при отливке делаются углубления. С неходовой стороны набойки делают специальные приливы и выступы по своей форме копирующие углубления в каблуке. Набойка намазанная с неходовой стороны клеем несильным ударом запрессовывается в тело каблука так чтобы выступ ее прочно вошел в полую часть каблука. Держание набойки осуществляется силами трения возникающими между боковыми поверхностями набойки и каблука. Сила трения увеличивается в результате применения клея нанесенного на набойку. Запрессовка набойки выполняется вручную молотком и считается нормальной если между набойкой и каблуком нет расщелин и отверстий. Применение таких набоек удобно еще тем что изношенные легко заменить новыми.
4 Основные технические характеристики
* Каблуки в паре должны быть одинаковыми по высоте форме размеру и
Соответствовать номеру обуви.
* Количество гвоздей для прикрепления низкого кожаного каблука изнутри
Размер обуви Количество гвоздей шт.
* Расстояние от центра гвоздей до края стельки при прикреплении кожаного
каблука — 4-7 мм деревянного или пластмассового — 10-12 мм.
* Количество гвоздей для прикрепления среднего деревянного каблука
должно быть 5-7для всех размеров.
* Расстояние между центрами гвоздей при прикреплении изнутри
деревянных и пластмассовых каблуков 11-13 мм. Гвозди должны
вбиваться с наклоном внутрь головки гвоздей утапливают в подпяточник.
Острие гвоздя не должно доходить до ходовой поверхности набойки на 2-3
* Величина загибки острия гвоздя при прикреплении каблука снаружи
должна составлять 2-3 мм.
* Прикрепление деревянного и пластмассового каблуков снаружи и изнутри производят:
- втулкой (для высокого и среднего) или тремя гвоздями (для среднего
- прикрепление изнутри (высокого) 3 шурупами или 5 гвоздями
расстояние между их центрами 7-10 мм.
* При прикреплении каблука изнутри головки гвоздей и шурупов не должны
выступать над поверхностью стельки. Особенно надо следить за тем чтобы
головка шурупа не располагалась под углом к поверхности стельки.
* Каблук должен быть посажен ровно без перекосов. Кривизна ляписа
среднего и высокого каблуков должна совпадать с кривизной пяточной
части обуви во всех точках между ними не должно быть зазоров и
* Обтяжка должна плотно без морщин и складок прилегать к боковой
поверхности каблука цвет обтяжки должен гармонировать с цветом верха
* Краситель не должен осыпаться при использовании гладкокрашеных
каблуков или каблуков с имитацией наборного.
* На высокий деревянный или капроновый каблук набойки крепят одним
специальным шестигранным гвоздем или тремя каблучно-набоечными
гвоздями на средний 5-7 гвоздями или способом запрессовки.
1 Расчёт технологических режимов
Структурная схема и конструктивное оформление механизмов могут быть самыми разнообразными и во многом определяются величиной развиваемого усилия на рабочем инструменте работой сия сопротивления штучного крепителя при забивании назначением проектируемой машины общей компоновкой механизмов и узлов машины на станине и т. п.
Независимо от вида штучного крепителя сопротивление введению его в скрепляем+ые детали определяется в основном силами контактного взаимодействия крепителя и соединяемых им элементов.
Полная сила сопротивления Р введению крепителя в скрепляемые детали:
Рт — силы сопротивления контактного трения;
Рд — силы сопротивления отдельных контактных площадок упругим и
пластическим деформациям различного вида (смятию срезу
α — коэффициент показывающий соотношение слагаемых Рт и Рд.
На величины слагаемых Рт и Рд влияют вид крепителя материал из которого он изготовлен его геометрические параметры физико-механические свойства скрепляемых материалов и т. д. Средние значения коэффициента α (в %) для некоторых типов крепления составляют: гвоздевого (резина) 20 — 40 гвоздевого (кожа) 40 — 50 винтового (резина) 200 — 250 деревянно-шпилечного — стремится к .
Силы сопротивления контактного трения для различных креплений являются компонентами силы держания крепителей. Поэтому закономерности контактного трения в той или иной степени относятся ко всем типам крепления штучными крепителями и определяют их общие характеристики.
Рассмотрим упрощенную схему системы скрепляемым элементом которой является одиночная шпилька (рис. 19). После прокола шилом диаметром d0 скрепляемых материалов в них образуется отверстие диаметром d2 = d0 где — коэффициент зависящий от свойств скрепляемых материалов геометрии шила и т. п. Шпилька в свободном состоянии имеющая диаметр d1 после забивания сжимается и ее диаметр уменьшается до d. При этом создается посадочная контактная поверхность с общим для материалов и шпильки диаметром d. Сила сопротивления контактного трения при радиальном удельном давлении р по контактной поверхности коэффициенте трения f и высоте s шпильки будет:
Удельное контактное давление р можно определить приближенно по известному из теории сопротивления материалов уравнению для радиальных напряжений по контактной поверхности при соединении цилиндрических деталей с натягом:
s — диаметральный абсолютный натяг;
Е1 и Е2 — модули продольной упругости соответственно шпильки и
скрепляемых материалов;
и 2 — коэффициенты Пуассона материалов шпильки и скрепляемых
k1 и k2 — безразмерные геометрические параметры шпильки
(отношение диаметра шпильки к диаметру контактного
цилиндра) и скрепляемых деталей (отношение диаметра
контактного цилиндра к наружному диаметру проколотого
Для рассматриваемого случая:
Так как k1= 0 k2= 0 и Е1 >> E2 а поперечные размеры шпильки невелики то можно пренебречь поперечной деформацией шпильки и считать d1 = d. Тогда
Выражение (1) позволяет с достаточной для инженерных расчетов точностью определить силу сопротивления контактного трения одиночной цилиндрической шпильки. Для штучных крепителей другой геометрической формы выражение (1) с учетом анизотропности скрепляемых волокнистых материалов можно использовать лишь для общей аналитической характеристики силовых соотношений в системе скрепляемые детали — шпилька. Силовые соотношения при скреплении деталей другими штучными крепителями для которых характерно наличие не только сил сопротивления контактного трения Рт но и сил сопротивления РД отдельных контактных площадок упругим и пластическим деформациям рассмотрим на примере гвоздевого скрепления деталей.
В первом приближении будем считать что на гвоздь в процессе его внедрения в скрепляемые материалы действуют активная сила Р направленная в сторону острия гвоздя; сила сопротивления смятию Q скрепляемых материалов или сопротивление острия гвоздя загибке; реакция материалов N на коническую поверхность гвоздя; сила трения Т гвоздя о материал (рис. 20). Условия статики по проекциям всех сил на направление силы Р и перпендикулярно к ней примут вид
Для решения этой системы определим действующие на гвоздь силы.
Из геометрических соотношений для острия гвоздя (см. рис. 7) имеем:
dCT — диаметр стержня гвоздя;
d — переменный диаметр контактного конуса;
d3 — диаметр контактного конуса на выходе из стельки т. е. диаметр
загибаемого сечеция острия гвоздя;
s —толщина скрепляемых материалов;
L3 —длина загиба острия;
l —координата переменного сечения контактного конуса
(относительно конца острия до загибания);
— угол заострения острия;
r — переменный радцус контактного конуса.
Составим уравнение силы контактного трения для .элементарного усеченного конуса высотой dl и с радиусами круглых оснований r и (r + dr). При этом с учетом выражения (1) получим следующее значение элементарной силы контактного трения по образующей поверхности указанного элементарного усеченного конуса:
—коэффициент характеризующий геометрию гвоздя;
- параметр соединения который счи-
таем постоянным по толщине скрепляемых материалов;
f — коэффициент контактного трения.
Интегрируя это выражение в пределах l = L3 и l = L3 + s т. е. по всей толщине скрепляемых материалов получим полную силу контактного трения гвоздя
Очевидно реакция N скрепляемых материалов на коническую поверхность гвоздя будет:
При отсутствии загибки острия в случае забивания гвоздя в предварительно проколотое отверстие в уравнении (2) можно принять Q = 0. Тогда подстановка выражений (3) и (4) в уравнение (2) позволяет определить аналитически усилие Р забивания для любого положения гвоздя в скрепляемых материалах.
Для случая загибки острия гвоздя на стельку имеем:
где: — предел текучести материала гвоздя;
а — коэффициент зависящий от формы загибки острия;
W —момент пластического сопротивления загибке острия.
Для проектирования нам необходимы:
Схема гидропривода приведена на рис. 21.
Диаграммы состояний распределителей приведена на рис. 22.
Тактограммы исполнительных устройств .приведены на рис. 22.
Максимальное усилие прикладываемое к шурупу .. .1 кН.
Величина хода поршня в гидроцилиндре 002 м.
Длительность тактов t2 и t3 07 с.
Требуется в процессе проектирования определить:
Максимальное давление на выходе насоса . pн;
Производительность насоса Qн;
Внутренний диаметр гидроцилиндра ..D;
Диаметр штока поршня . . d;
Толщину стенок гидроцилиндра .. ;
Диаметр трубопровода ..dтр;
2.2Структура и работа гидропривода
Кинематика и динамика подвижных элементов гидравлических исполнительных устройств (ими могут быть поршни цилиндры роторы и др.) во многом определяется характером изменения расхода и давления масла в рабочих полостях (объемах) этих устройств. Характер же изменения расхода и давления зависит от вида источника гидростатической энергии. По этому признаку можно выделить два типа гидроприводов: насосные и насосно-аккумуляторные.
В насосных гидроприводах единственным источником гидростатической энергии является насос постоянной производительности который обеспечивает практически постоянный расход масла в рабочих полостях исполнительных устройств и развивает при этом давление масла необходимое для преодоления полезных и вредных нагрузок.
В заданной установке используется насосный гидропривод а исполнительным устройством является гидравлический цилиндр.
Гидравлическим цилиндром называется объемный гидродвигатель с возвратно-поступательным движением выходного звена. Гидроцилиндры широко применяются в качестве исполнительных механизмов различных машин. По конструкции и принципу действия гидроцилиндры очень разнообразны и классифицируются в соответствии с ГОСТ 17752-81.
Рисунок 21 Схема гидропривода механизма закручивания шурупа
– Регулируемый предохранительный клапан высокого давления;
- двухпозиционный четырехходовой распределитель с электромагнитным управлением и возвратной пружиной;
- гидроцилиндр механизма закручивания шурупа.
- обратный напорный клапан;
– переливной клапан прямого действия с золотниковым запорно-
регулирующим элементом;
– регулируемый гидродроссель;
Рисунок 22 – Цикл работы гидропривода
Описание работы гидропривода может быть дано посредством диаграммы состояний распределителя 5 и тактограммы исполнительного устройства 10.
Исполнительное устройство может находиться в трех состояниях: прямой ход остановка обратный ход. На рис. 21 за прямой ход поршня 10 принято его движение вверх. На тактограмме (рис. 22) прямому и обратному ходу исполнительного устройства соответствуют наклонные отрезки прямых (обозначены стрелками) а остановке - горизонтальные. На тактограмме длительности тактов условно принимаются одинаковыми. На диаграмме состояний распределителя условно показаны: состояние I в виде отрезков прямых совпадающих с осью абсцисс состояние II в виде отрезков горизонтальных прямых расположенных выше оси абсцисс. Цикл работы гидропривода (рис. 22) состоит из трёх тактов.
В первом такте поршень 10 неподвижен. Масло подаваемое насосом 2 проходит через фильтр 3 регулируемый предохранительный клапан высокого давления 4 и сливается в бак.
Во втором такте масло подаваемое насосом проходит через распределитель 5 находящийся в позиции II регулируемый гидродроссель 11 и поступает в нижнюю полость цилиндра 6 перемещая поршень 10 вверх в результате происходит прямой ход гидроцилиндра.
В третьем такте масло подаваемое насосом через распределитель 5 переключившийся обратно в позицию I поступает в верхнюю полость гидроцилиндра 6 в результате происходит обратный ход гидроцилиндра.
2.3 Проектирование и расчет гидропривода.
Из стандартного ряда давлений выбираем давление насоса:
Расчет усилия на гидроцилиндре.
Полезная сила гидростатического давления Рпол - определяется Из уравнения которое получено из рассмотрения условий статического равновесия штока (7) и гидроцилиндра механизма отвёртки (6) в момент в начальный момент внедрения шурупа в материал. Учитывая конструкцию заданного механизма получаем:
Рпол - полезная сила гидростатического давления в гидроцилиндре
молоткового механизма;
Рзаб - усилие необходимое для забивания гвоздей в материал каблука (по заданию Рзаб=1 кН).
Определение диаметра гидроцилиндра механизма отвёртки.
Задаются из конструктивных соображений соотношением
φ=dD между диаметрами D гидроцилиндра 6 и диаметром d штока 7
поришя 10 и коэффициентом запаса k в уравнении:
Для подобных прессов принимают φ= 03 05. Учитывая динамический характер работы данного механизма возрастание усилий на толкатель отвёртки за счет внедрения шурупа в каблук принимаем k=15.
Подставив в уравнение (2) выражение d= φ·D и выразив из него D определяем диаметр гидроцилиндра:
D – диаметр гидроцилиндра механизма отвёртки [м];
K – коэффициент запаса (k=15 2); k=15
Pн – давление создаваемое насосом в магистрали.
Из стандартного ряда давлений выбираем Pн = 6.3 МПа. =
Рпол -полезная сила гидростатического давления в гидроцилиндре;
Уточненное значение в соответствии с ГОСТ 12447-80
Определение диаметра штока.
Это значение уточняем в соответствии со стандартным рядом диаметров штоков гидроцилиндров. Оно соответствует:
Определение производительности насоса и выбор насоса.
Требуемая производительность Qн насоса определяется из уравнения:
t3 - длительность периода закручивания;
L - величина хода штока;
D - диаметр гидроцилиндра закручивания;
Но так как в рабочей нижней полости также расположен шток 7 поршня 10
то уравнение будет иметь вид:
- объём заполняемый рабочей жидкостью при работе гидроцилиндра.
В соответствии с ГОСТ 13825-80 принимаем Qн =55 лмин
Подбираем по каталогу насос марки Г13-32АМ;
Определение толщины стенок гидроцилиндра.
Толщина стенок гидроцилиндра определяется из условий прочности.
т – предел текучести (значение т выбирается в соответствии с
материалом цилиндра например для стали 20Х т =638 Нмм²);
s – масштабный коэффициент (s =07);
n – коэффициент запаса (n=125);
D – диаметр гидроцилиндра;
Рн– максимальное давление на выходе насоса;
Определение наружного диаметра гидроцилиндра.
Наружный диаметр гидроцилиндра Dн находится
Где: D – диаметр гидроцилиндра вырубания;
- толщина стенок гидроцилиндра.
Определение диаметров трубопроводов.
Диаметры трубопроводов определяют по формуле
где: dтр – диаметр трубопровода;
Vтр – допускаемая скорость движения масла;
Vтрвс=12 мс – для всасывания;
Vтр =2 мс – для слива;
Qн - производительность насоса
По ГОСТ 12447-80 dтрв=6 мм
По ГОСТ 12447-80 dтрс=6 мм
При Pн=63 МПа допускаемая скорость нагнетания Vтрн =35 мс;
По ГОСТ 12447-80 dтрн = 6 мм.
Поверочный расчёт давления насоса.
Достаточно ограничиться проверкой давления pн создаваемого насосом во втором такте рис. 22 в котором требуется иметь максимальное давление масла в гидроцилиндре 6 рис. 21.
Р2 – сила создаваемая пружиной возврата .. 30 Н;
М – масса звеньев привода отвёртки. 04 кг;
g – ускорение силы тяжести ..98 мс²
Ртр – сила трения в уплотнениях гидроцилиндра 20 Н;
Поверочный расчет длительности тактов.
где t2 – время закручивания шурупа;
t3 – время затрачиваемое на ход поршня вниз;
D - диаметр гидроцилиндра ;
L - длина хода поршня гидроцилиндра;
Qн - производительность насоса.
Структурная схема и конструктивное оформление механизмов могут быть самыми разнообразными и во многом определяются величиной развиваемого усилия на рабочем инструменте работой сил сопротивления штучного крепителя при вкручивании назначением проектируемой машины общей компоновкой механизмов и узлов машины на станине и т. п.
Независимо от вида штучного крепителя сопротивление введению его в скрепляемые детали определяется в основном силами контактного взаимодействия крепителя и соединяемых им элементов.
3 Расчёт деталей на прочность
Давление на шток со стороны гидроцилиндра p = 3МПа при его диаметре d1 = 60мм.
Площадь гидроцилиндра:
Определим силу P сжимающую шток:
P = p*F1 = 63×106×283×10-3 = 178×104Н.
Выясним какую формулу можно использовать для определения критической силы PКР.
Определим гибкость штока:
коэффициент приведения длины зависящий от вида закрепления концов штока.
– длина штока; = 80мм;
- радиус инерции поперечного сечения;
используем эмпирическую формулу Ясинского:
a b – эмпирические коэффициенты равные для стали:
кр = 32 – 011*747 = 238 ;
PКР =кр*F =кр* = 238* = 168кН.
Проверим условие устойчивости:
[ny] – допустимый коэффициент запаса устойчивости для грузовых винтов штоков принимаем равным:
Из произведенных нами расчетов мы можем сделать вывод:
Устойчивость штока обеспечена.
1.1Конструкция детали
Данная деталь относится к классу осей. Ее функция в узле механизма – молоток.
Эскиз детали представлен на рис. 23.
Рисунок 23 - Исходный эскиз детали
В соответствии с классификацией все обрабатываемые поверхности детали разбиваются в зависимости от формы направляющей линии на следующие классы:
- поверхности вращения;
- плоские поверхности;
- винтовые поверхности.
Данная деталь ограничена поверхностями из которых:
L1 L3 L4 L5 - принадлежат к классу плоских поверхностей;
K6 K7 - к поверхностям вращения.
поверхности L1 L5 - относятся к открытым плоским обрабатываемым; поверхности L3 L4 - к полуоткрытым плоским обрабатываемым; поверхностm K6 - к открытым цилиндрическим обрабатываемым; поверхность K7 – к полуоткрытым.
Габаритные размеры детали:
- наибольший диаметр – 5 мм.
Т. е. данную деталь можно отнести к «малогабаритным» деталям. Материал детали – углеродистая сталь У8.
Механические свойства данного материала
Сталь У8 относится к инструментальным сталям. Содержание углерода 08 %. После термической обработки твердость (HRC 60-62). Теплостойкость 200-250 градусов при этой температуре твердость стали резко уменьшается и детали изготовленные из этой стали не могут выполнять работу инструмента резания но вполне пригодны для изготовления деталей работающих в качестве молотка в заданной машине.
1.2 Размерный анализ чертежа
Выполняем эскиз детали по 2-м осям.
Рисунок 24 - Эскиз детали с указанием номеров поверхностей
Обработанные поверхности выделяем красным цветом. Каждая цилиндрическая поверхность имеет отдельную ось оси рассматриваются как отдельные поверхности.
Далее по 2-м осям строим исходные графы.
Рисунок 25 - Исходный граф по оси L
Рисунок 26 - Исходный граф по оси К
Вершины графа обозначаем окружностью с номером поверхности. Ребра графа обозначаем плавной линией с записью номера и допуска на него. Цвет вершин должен соответствовать их обозначению на эскизе.
Анализ недостающей информации:
- на графе не должно быть оторванных поверхностей и групп
поверхностей. Оторванные поверхности и группы поверхностей
указывают на недостающие размеры;
- на графе не должно быть замкнутых контуров. Это указывает на
наличие лишних размеров;
- на графе должна быть только одна связь между комплексом
обработанных и необрабатываемых поверхностей.
Согласно анализа исходного графа по оси L не выполняется требование 1.
Добавляем необходимый размер и строим исправленный граф по оси L
Рисунок 27 - Исправленный граф по оси L
По оси K выполняются все требования поэтому строим эскиз детали с исправленными размерами.
Рисунок 28 - Эскиз детали с исправленными размерами.
1.3Выбор заготовки для изготовления заданной детали
Заготовкой является калиброванный пруток диаметром 6 мм длинной 1 метр по ГОСТ 1435-74 из которого получается девять заготовок для изготовления заданных деталей.
Где sв – временное сопротивление (предел выносливости);
НВ=187– твердость по Бриннелю.
=21% - относительное удлинение.
2. Разработка технологического процесса обработки детали
2.1. Выбор маршрута обработки типовых поверхностей детали
Все обрабатываемые поверхности детали разбиваются в зависимости от формы и точности обработки на следующие группы
- плоскости с шероховатостью R a =63 мкм;
- плоскость с шероховатостью R a =08 мкм;
- вал 5 Н6 с шероховатостью R a =08 мкм;
- вал 4 мм с шероховатостью R a =63 мкм;
Для формообразования любой из поверхностей с заданной точностью при помощи механической обработки машиностроение располагает набором методов. В зависимости от точности и качества поверхности которые обеспечивает любой из методов последний подразделяется на предварительный (П) чистовой (Ч) тонкий (Т). Многие методы обеспечивают заданные параметры точности за счет режимов резания за одну обработку (однократная обработка О).
Для поверхностей данной детали:
- плоскости (торцы) L1 L3
- плоскость (торец)
- поверхности L2 К7;
ШЛФК – шлифование круглое.
2.2. Синтез маршрута обработки.
Технологический процесс изготовления детали разделяется на ряд последовательных этапов в каждый из которых включаются однородные по характеру и точности методы обработки различных поверхностей детали.
Т. о. маршрут обработки детали можно разбить на ряд этапов которые чередуясь с операциями термической обработки образуют принципиальную схему техпроцесса. Укрупненные этапы техпроцесса приведены в табл.4.
Таблица 4 – Этапы технологического процесса
Назначение и характеристики
Получение заготовки и ее термообработка
Съем напусков и большей части припусков
Хромирование нивелирование и т.д.
Состав и порядок этапов обработки детали т.е. принципиальную схему определяют виды точность и физические свойства главных поверхностей точность которых максимальна. Обработка второстепенных поверхностей проводится на этапе Э4 и не оказывает существенного влияния на характер принципиальной семы процесса. Т. к. деталь достаточно жесткая а требования точности ограничивается квалитетом. то можно этапы Э2 и Э4 объединить в один а этап Э3 выполнять сразу после Э1.
2.3. Выбор баз для первой операции.
При выборе технологических баз следует учитывать что наибольшую точность обеспечивает принцип совмещения технологической и конструкторской баз. Но соблюдение этого принципа часто приводит к удорожанию станочных приспособлений. Поэтому если позволяет требуемая точность лучше применять принцип постоянства баз т. е. на всех или большинстве операций использовать один и тот же комплект баз. Необходимо стремиться к тому чтобы выбранная схема базирования обуславливала более простую и надежную конструкцию приспособления удобство установки и снятия обрабатываемой заготовки.
Особенно важно правильно выбрать базу для первой операции. При этом решаются следующие задачи:
)обеспечить без использования операции разметки заданное
чертежом относительное расположение обработанных и
необрабатываемых поверхностей детали;
)обеспечить равномерное распределение припуска на точной и
точно скоординированной поверхности обрабатываемой
маложестким инструментом что позволяет сократить требуемое
количество проходов (или переходов) при ее обработке.
Если необходимо решить только первую задачу то в качестве базы для первой операции выбирается та необрабатываемая поверхность которая на графе размерных связей является единственной вершиной связанной размером с группой обработанных поверхностей. Если необходимо решить только вторую задачу то в качестве базы для первой операции принимается именно та поверхность на которой припуск должен быть равномерным.
На основании вышесказанного составим таблицу технологического процесса обработки.
Таблица 5 – Технологический процесс изготовления детали
Наименование операции
Точить поверхность D=51 мм на длину 119 мм
Точить канавку d=4 мм шириной 8мм
Шлифовать торец в размер 115 мм
Бесцентрошлифовальная
Шлифовать диаметр D=5h6
Построим размерный анализ техпроцесса по оси L.
Рисунок 29 - Размерный анализ техпроцесса по оси L
Построим исходный производный и совмещённый графы.
Рисунок 30 - Исходный граф
Рисунок 31 - Производный граф
Рисунок 32 - Совмещённый граф
3 Уравнения размерных цепей
Используя данные исходных и производных технологических графов составляем уравнения размерных цепей.
) 3-2-6-4-3 A2=S1-S2-
Решение данных уравнений.
Результаты вычислений сводим в таблицу 6.
Таблица 6 – Расчет операционных размеров
Номинальное значение
Построим размерную схему технологического процесса по оси K.
Рисунок 33 - Размерная схема технологического процесса по оси K.
Построим исходный технологический граф по оси K (рис. 34).
Рисунок 34 - Исходный технологический граф по оси K
Рисунок 35 - Производный технологический граф по оси K
Рисунок 36 - Совмещённый граф по оси K
) 7-6-1-5-2-6-7 P3=S1-S2+S5-
) S4=A2=4-0.1=3.9 мм;
S3min=S1min+S5min-S2ma
Результаты вычислений сводим в таблицу 7.
Таблица 7 – Расчет операционных размеров
4 Выбор оборудования
Операция 05. Токарно-винторезный станок 1603
Наибольший диаметр обрабатываемой детали
Наибольший диаметр прутка обрабатываемого в патроне
Расстояние между центрами
Число оборотов шпинделя
Продольная подача суппорта
Мощность главного электродвигателя
Операция 15. Круглошлифовальный станок ЗА10П
Наибольшая длинна обрабатываемых деталей
Наибольший диаметр шлифования
Наибольшая длинна шлифования
Диаметр шлифовального круга
Мощность электродвигателя
Операция 20. Бесцентрошлифовальный станок 3Д180
Диаметр обрабатываемой детали
Размеры шлифовального круга
Размеры ведущего круга
Число оборотов в минуту
а) шлифовального круга
5Расчет режимов резания
Расчет режимов резания для операции 0.5.
Точить поверхность.
Глубина резания t = 045 мм;
Подача по табл. 33 (стр. 283 [1]):
Где по табл.39 (стр.286-287[1])
Т = 120 мин – стойкость резца (табл. 40 (стр.290 [ 1 ]);
К v –поправочный коэффициент на скорость резания:
К v = К мv * К пv * К иv=1*06*1=06 ;
где К мv – коэффициент учитывающий качество обрабатываемой поверхности. По табл.1 (стр.261 [ 1 ]):
К пv – коэффициент учитывающий состояние поверхности заготовки. По табл.5 (стр.263 [ 1 ]) К пv =06
К иv – коэффициент учитывающий материал инструмента. По табл.6 (стр.263 [ 1 ])
Число оборотов шпинделя:
По паспортным данным станка принимаем n = 2800 обмин ;
S м = S о * n = 02 * 2800 =560 мм мин ;
L = L1 + L2 + L3 мм ;
где L1= 115 мм – рабочая длина;
L2 =5 мм – подвод инструмента;
L3 = 1 мм – перебег инструмента;
L = 115 + 5 +1 = 121 мм ;
Технико-экономический расчет
Определим эффективность совершенствования организации рабочих мест с целью полной ликвидации потерь рабочего времени ( в размере 35 минут в смену у каждого основного рабочего).
Таблица 9 – Экономические характеристик рабочего места
Количество основных рабочих на участке
Годовая программа деталей
Норма времени на 1 деталь
Выполнение норм выработки
Себестоимость годового выполнения
Удельный вес условно-постоянных расходов в структуре себестоимости
Годовой фонд рабочего времени одного рабочего
Стоимость оборудования на участке
Продолжительность смены
Определение годового экономического эффекта.
Определение эффективности совершенствования организации рабочих мест определяется на основе следующих показателей:
Условное высвобождение численности рабочих чел.:
Б1 и Б2 - потери рабочего времени до и после внедрения мероприятий %;
Ч- численность основных рабочих до внедрения мероприятий чел.
Пр - потери рабочего времени до внедрения мероприятий. мин.;
Тсм - продолжительность смены мин.
Расчет прироста производительности труда %:
Расчет экономии рабочего времени основных рабочих нормо-часов:
Ч - численность рабочих у которых сокращаются потери рабочего
Т - годовой фонд рабочего времени одного рабочего дн.;
Квн - коэффициент выполнения нормы выработки.
Расчет прироста объема производства.
Нвр - норма времени на 1 деталь час.
Ргод - годовая программа деталей шт.
Расчет экономии на условно-постоянных расходах руб.
С - себестоимость годового выпуска руб.;
У - удельный вес условно-постоянных расходов в структуре себестоимости (0.3).
Расчет экономии от снижения удельных капитальных вложений руб.
Фб - балансовая стоимость оборудования руб.
Ен - нормативный коэффициент экономической эффективности
внедряемых мероприятий. Ен = 015.
Годовой экономический эффект составит
Эг = Эпр + Эу.к=15120000+81900=15201900 руб.
После внедрения мероприятий по совершенствованию организации рабочего места в частности сокращения потерь рабочего времени пришли к следующим результатам:
Произошло условное высвобождение численности рабочих на 01458 чел.
Прирост производительности труда составил 786 % .
Экономия рабочего времени составила 168 нормо-часов.
Произошёл прирост объёма производства на 84 % .
При этом общий экономический эффект составил 15201900 рублей.
Рассчитаем экономический эффект за год службы усовершенствованной конструкции станка.
Таблица 10 – Экономические показатели использования станка
Годовой объем производства станков
Производительность станка
Себестоимость станка
Удельные капитальные вложения изготовителя обусловленные производством одного станка
Сопутствующие капитальные вложения потребителя на один станок
Годовые эксплутационные расходы потребителя при использовании одного станка (без отчислений на реновацию)
Нормативный коэффициент эффективности
Коэффициент отчислений от балансовой стоимости на полное восстановление (реновацию).
Определим годовой экономический эффект.
Экономический эффект от производства и использования новых средств труда долговременного применения с улучшенными качественными характеристиками за срок службы определяется по формуле.
и З2 - приведенные затраты базового и нового станка тыс. руб.;
В1 и В2 - производительность станка или годовые объемы продукции
производимые при использовании базового и нового станка штук;
К`1 и K`2 - сопутствующие капитальные вложения потребителя при
использовании базового и нового станка тыс. руб.;
И'1 и И'2- годовые эксплуатационные издержки потребителя при
использовании базового и нового станка тыс.руб.;
А2 - годовой объем производства станков усовершенствованной
З1= С1+ЕН*К1 =6400+015*9900=7885 тыс. руб.;
З2= С2+ЕН*К2=6500+015*8500=7775 тыс. руб.
С1 - себестоимость станка по базовому варианту тыс.руб.;
С2 - себестоимость по новому варианту тыс.руб.;
К1 - удельные капитальные вложения изготовителя обусловленные
производством одного станка по базовому варианту тыс.руб.;
К2 - удельные капитальные вложения изготовителя обусловленные
производством одного станка по новому варианту тыс.руб.
- коэффициент учитывающий рост производительности станка.
И1 - годовые эксплуатационные издержки потребителя при
использовании базового станка тыс.руб.;
И2 - годовые эксплуатационные издержки потребителя при
использовании нового станка тыс.руб.
=805629135 тыс. руб.
Таким образом мы видим что величина экономического эффекта от производства и использования новых средств труда долговременного применения с улучшенными качественными характеристиками за год составит 805629135 тыс. руб.
Тогда общий экономический эффект будет:
- экономический эффект от совершенствования организации
- экономический эффект от использования новых
средств труда долговременного применения с улучшенными
качественными характеристиками.
Охрана труда создание безопасных и здоровых условий на предприятии лёгкой промышленности способствует повышению эффективности труда и улучшению качества выпускаемой продукции. Поэтому на всех предприятиях необходимо внедрение современных средств техники безопасности и обеспечение санитарно-гигиенических условий устраняющих производственный травматизм и профессиональные заболевания. Особое внимание должно уделяться вопросам улучшений условий труда санитарно-оздоровительным мероприятиям. При проектировании оборудования используемого на предприятиях лёгкой промышленности следует учитывать соответствие создаваемых конструкций требованиям норм охраны и гигиены труда.
Предприятия лёгкой промышленности оснащены сложным технологическим оборудованием и к лицам обслуживающим это оборудование предъявляются высокие требования с точки зрения обеспечения эффективности надёжности и безопасности работы машин и аппаратов. Причина производственного травматизма или профессионального заболевания как правило определяется комплексом факторов зависящих от надёжности и безопасности машины или технологического процесса поведения человека управляющего ими его быстродействия точности надёжности влияния окружающей среды и других факторов. Причинами травматизма могут быть опасные и вредные производственные факторы которые подразделяются на следующие группы:
-по природе воздействия они могут быть физические химические биологические и психофизические;
-ошибки при изготовлении наладке и ремонте технологического оборудования;
-отказ в работе оборудования и систем обеспечивающих его работу;
-неправильная организация рабочего места и технологического процесса;
-ошибки в действиях человека управляющего технологическим процессом;
-недостатки в подборе обучении персонала.
Все планируемые мероприятия по охране труда должны обеспечить нормальные и безопасные условия труда обслуживающего персонала и должны разрабатываться исходя из конкретных особенностей проектируемого объекта.
Для поддержания высокой работоспособности и сохранения здоровья человека необходимо улучшать условия труда которые определяются:
* общим состоянием производственных помещений - площадь и объем помещения приходящиеся на одного работающего оформление интерьера планировка и окраска оборудования;
* санитарно-гигиеническим состоянием производственных помещений - воздушная среда (запыленность загазованность влажность температура) освещенность шум вибрация излучение и д. р.).
На основе изучения существующих условий труда разрабатываются организационно-технические мероприятия по их улучшению.
Эту работу целесообразно выполнять в два этапа: приведение условий труда в полное соответствие с санитарными нормами и создание наиболее благоприятной "комфортной" среды.
При шуме 70 - 85 дб сохраняются благоприятные условия труда при шуме от 85 до 120 дб создаются неблагоприятные условия труда а свыше 120 дб - недопустимые. Высокочастотный шум более вреден для здоровья чем низкочастотный.
Кроме того на повышение производительности труда и сохранение здоровья рабочих оказывают влияние некоторые другие факторы определяющие условия труда: температура освещенность производственная эстетика и т.д.
Практическим путем установлено что проведение комплекса мероприятий по производственной эстетике (интерьер цеха форма и конструкция рабочей мебели окраска оборудования и т.п.) способствует повышению производительности труда примерно на 10%.
При разработке мероприятий необходимо руководствоваться принципами технической эстетики. Например при окраске оборудования и рабочей мебели следует применять цвета отражающие не менее 40% падающего света ( белый цвет отражает 90% световых лучей светло-желтый - 75% салатовый - 70% светло-голубой - 45% бежевый - 38% желто-коричневый — 25% темно-зеленый — 16% темно-серый -15% темно-синий - 10% черный - 4%). Наиболее рациональными для окраски оборудования и рабочей мебели на обувных фабриках являются цвета: светло-серый светло-голубой и зелено-голубой.
Созданию эстетических условий способствует также постоянное поддержание чистоты и соблюдение общей культуры производства: ликвидация засоренности рабочих мест производственными отходами устранение "завалов" полуфабриката и т.п.
Охрана труда в Республике Беларусь обеспечивается системой законодательных актов социально-экономических организационных технических и лечебно-профилактических мероприятий и средств обеспечивающих безопасность сохранение здоровья и работоспособности человека в процессе труда. Основой законодательства о труде является Трудовой Кодекс РБ принятый Палатой представителей и одобренный Советом Республики 30 июня 1999 года. Часть трудового законодательства составляет действующее законодательство об охране труда которое заключено в главе 16 «Охрана труда» (статьи 221–232) раздел II – «Общие правила регулирования индивидуальных трудовых и связанных с ними отношений». Этот раздел регламентирует права работников на охрану труда гарантии этих прав права на компенсацию по условиям труда обязанности нанимателя по обеспечению охраны труда и т.д.
Кроме вышеперечисленного в систему законодательных актов регулирующих вопросы охраны труда в Республике Беларусь входят:
– Конституция РБ гарантирующая право граждан на здоровье и безопасные условия труда;
– Закон РБ «Об основах государственного социального страхования» в котором предусмотрены вопросы страхования граждан от несчастных случаев на производстве и профзаболеваний;
– Закон РБ «О санитарно-эпидемическом благополучии населения» направленный на предупреждение воздействия неблагоприятных факторов среды на здоровье населения и регламентирует действия органов государственной власти и управления предприятий и организаций должностных лиц и граждан по обеспечению санитарно-эпидемического благополучия;
– Закон РБ «О сертификации продукции работ услуг» который обеспечивает безопасность продукции для жизни здоровья и имущества населения а так же охрану окружающей среды;
– Закон РБ «О коллективных договорах и соглашениях» определяющий правовые основы заключения и исполнения коллективных договоров и соглашений для содействия регулированию трудовых отношений и согласованию социально-экономических интересов работников и нанимателей в частности в вопросах создания здоровых и безопасных условий труда улучшения охраны здоровья среды.
2 Характеристика машины для крепления каблука гвоздём и шурупом
Данная характеристика отражена в табл. 6.1.
На основе анализа данных даётся полная характеристика имеющихся на предприятии опасных вредных токсичных пожароопасных и взрывоопасных веществ отражены разработанные мероприятия по обеспечению безопасного труда обслуживающего персонала.
Все планируемые мероприятия по охране труда обеспечивают безопасные и здоровые условия труда обслуживающего персонала и разрабатываются исходя из проектируемого обувного производства. Анализ опасных и вредных факторов обувного производства и общая характеристика этого производства представлен в таблице 6.1.
Таблица 6.1 – Общая характеристика машины для крепления каблука штучными крепителями.
Характеристика параметра
Опасные и вредные факторы имеющиеся в конструкции изделия либо проявляющиеся при его эксплуатации
Наличие вредных опасных или токсичных веществ.
Наличие источников ионизирующего излучения
Наличие источников электромагнитных полей
Наличие возможности поражения человека электрическим током
Наличие опасностей при работе изделия на холостом ходу и при обработке изделий
Таблица 6.2 - Характеристика опасности поражения персонала электрическим током
Характеристика реализуемого параметра
Класс помещения по опасности поражения электрическим током.
С повышенной опасностью
Напряжение электрического тока питания электросистем изделия В
Электрический привод: 380
Тип исполнения электрооборудования
Класс электрооборудования по способу защиты человека от поражения электрическим током
Способ отключения электрооборудования от сети.
Общий рубильник кнопка «стоп»
Сопротивление изоляции токоведущих частей МОм
Удельное сопротивление Ом*м
Нормируемое значение сопротивления защитного заземления Ом
Индивидуальные средства защиты
Диэлектрический коврик
Рассчитаем схему заземления выполненную вертикальными стержнями d=6 см l=25 м грунт – суглинок ρ=100 Ом. Заземляющее устройство предполагается выполнить в виде прямоугольника 2030 м. Стержни соединены между собой стальной полосой 404 мм и зарыты на глубину t0=07 м. Коэффициент сезонности Кс=1.
Расчёт ведётся по методике изложенной в литературном источнике [ 9 ].
Сопротивление растеканию тока для одного вертикального стержневого заземлителя:
Расстояние между стержнями a принимаем равным 5 м.
Определяем предварительно число стержней. Длина соединительной полосы равна периметру прямоугольника =100 м.
Коэффициент использования заземлителей.
Необходимое число труб для системы заземления при Rзаз=4 Ом:
Сопротивление растеканию соединительной стальной полосы Ом:
d – эквивалентный диаметр d=004 м.
Требуемое сопротивление системы заземления
Таблица 6.3 - Характеристика опасностей при работе изделия на холостом ходу и при выполнении операций
Опасные зоны изделия
Прижимное устройство молотковый и гвоздеподающий механизм.
Средства защиты исключающие попадание человека в опасную зону
Защитный кожух два спаренных рычага включения молоткового механизма.
Способ крепления детали в изделии при её обработке
Верхнее прижимное устройство и нижний прижимной упор (молотковая колонка).
Средства механизации при установке крепления и снятия обрабатываемой детали
Масса обрабатываемой заготовки кг
Продолжение таблицы 6.3
Средства защиты человека от пыли при обработке заготовки
сухой вручную щёткой
Средства механизации используемые при монтаже ремонте и демонтаже изделия
3 Санитарно-гигиенические мероприятия. Вентиляция. Отопление
Таблица 6.4 - Метеорологические условия на участке. Вентиляция. Отопление
Наименование производственного помещения
Швейно-сборочный цех
Характеристика тяжести работы
Температура воздуха рабочей зоны С
Относительная влажность воздуха %
Скорость движения воздуха мс
Система вентиляции в помещении и на рабочем месте
Приточно–вытяжная естественная
Кратность обмена воздуха
Система отопления в помещении
теплоноситель и его параметры
4 Санитарно-гигиенические мероприятия. Освещение
Данные мероприятия сведены в таблице 6.5
Таблица 6.5 - Искусственное освещение на участке
Наименование помещения и рабочего места
Площадь помещения м2
Разряд зрительной работы
Освещенность при рабочем освещении лк
Комбинированное (общее + местное) –750
Освещенность при аварийном освещении: на рабочих местах %
на путях эвакуации лк
Источник питания аварийного освещения
Автономная сеть аварийного освещения
Люминесцентная лампа ЛБ-40-4
Исполнение светильников
Мощность лампы светильника Вт
Количество светильников шт.
Расчёт количества светильников ведём используя метод светового потока по методике изложенной в литературном источнике [ 9 ].
Рассчитаем общее люминесцентное освещение для цеха площадью 5030 м имеющего высоту 58 м. Напряжение осветительной сети 220 В.
Исходные данные: требуемая освещённость по нормам Ен = 300 лк.; коэффициенты использования светового потока п = 70% с = 50%; hр = 08 м hс = 05 м; отношение расстояния между светильниками к расчётной высоте подвеса = 15.
Принимаем светильник с люминесцентными лампами ЛБ–40–4 имеющими световой поток = 3120 лм.
Расчётная высота подвеса:
Оптимальное расстояние между светильниками при многорядном расположении:
Светильники размещают в три ряда вдоль помещения.
Индекс площади помещения:
А и В – длина и ширина помещения А = 50 м В = 30 м
Нр – высота подвеса светильника Нр = 45 м.
При i = 417 коэффициент использования светового потока 47 %.
N – количество светильников или количество ламп накаливания шт.;
Ен – нормируемая освещённость Ен = 300 лк.;
S – площадь помещения S = 1500 м2;
z – коэффициент неравномерности освещения z = 12;
k – коэффициент запаса. Выбирается в зависимости от атмосферы в
производственном помещении k = 15;
Fл – световой поток группы ламп в светильнике или лампы накалива
– коэффициент использования светового потока зависящий от ха
рактеристики источника света ограничивающих способностей
интерьера помещения кривой распределения света а так же ин
Число светильников в каждом ряду:
при двухламповых светильниках: шт.;
при трёхламповых светильниках: шт.
5Мероприятия по пожарной безопасности
Данные по пожарной безопасности и молниезащите предприятия а так же мероприятия по пожарной безопасности на предприятии приведены в таблице 6.6.
Таблица 6.6 – Пожарная безопасность. Молниезащита
Класс помещения по пожароопасности
Категория производства по пожароопасности
Характеристика материалов стен по сгораемости
Характеристика материалов перекрытий по сгораемости
Степень огнестойкости стен здания и их огнестойкость ч
Расстояние от рабочего места до Эвакуационного выхода м
Средства пожаротушения
Пожарный щит вода огнетушители углекислотные ОУ-4
Категория молниезащиты здания
Сопротивление заземляющего устройства Ом
6Компенсация профессиональных вредностей. Индивидуальная защита. Личная гигиена
Данные мероприятия сведены в таблицу 6.7
Таблица 6.7 – Компенсация профессиональных вредностей. Средства индивидуальной защиты. Личная гигиена
Продолжение таблицы 6.7
Продолжительность рабочей недели ч
Дополнительный отпуск дни
Пенсионный возраст лет
Обеспечение лечебно-профилактическим питанием
Халат (хлопчатобумажный)
Индивидуальные средства защиты органов зрения
Индивидуальные средства защиты головы
Средства обеззараживания кожи
Метод обеззараживания кожи
Вывод: основными требованиями к помещениям обувного предприятия являются: благоприятный микроклимат нормируемая температура воздуха чистота воздушной среды требуемая относительная влажность воздуха рациональное освещение и пожарная безопасность.
7 Промышленная экология
Наряду с охраной труда большое значение приобретает охрана окружающей среды – одна из важнейших задач современности. Выбросы промышленных предприятий энергетических систем и транспорта в атмосферу водоемы и недра на современном этапе развития достигли таких размеров что в ряде районов земного шара особенно в крупных промышленных центрах уровни загрязнения существенно превышают допустимые санитарные нормы.
Промышленная экология призвана на основе оценки степени вреда приносимого природе индустриализацией разрабатывать и совершенствовать инженерно-технические средства защиты окружающей среды повсеместно развивать основы создания замкнутых безотходных и малоотходных технологических циклов и производств.
На данной машине производится сборка заготовок низа обуви. Осуществление этой работы при автоматизированном производстве повышает производительность увеличивает качество выпускаемого изделия тем самым уменьшая брак при выпуске данной продукции что ведет к уменьшению отходов производства и засорению ими окружающей среды.
При работе на проектируемой машине используются различные виды сырья. Сырье недефицитное и доступное для предприятий республики. На все виды обрабатываемого сырья есть сертификаты качества. Что касается самой машины то для её производства используются черные и цветные металлы (в основном сталь 35 относится к доступным не токсичным) а также пластмассы которые также являются недефицитными и доступными материалами.
В процессе работы машины в воздух выделяется незначительное количество мелкодисперсной пыли. Её количество соответствует требованиям санитарным нормам. Поэтому дополнительные средства для пылеулавливания не предусматриваются. Достаточно естественной приточно-вытяжной вентиляции.
Вода в процессе не используется следовательно не загрязняются и водные ресурсы.
По окончанию срока службы машины все детали и узлы перерабатываются на месте их образования или на других предприятиях имеющих соответствующую технологию.
Учет отходов черных и цветных металлов ведется еженедельно и ежемесячно по форме 6СН (лом). Лом и отходы черных и цветных металлов отличаются от других видов отходов тем что они представляют собой особо дорогостоящее сырье. Образующийся при ликвидации швейных машин лом черных металлов сдается в организацию «Вторчермет». Лом цветных металлов сдается в организацию «Белцветмет». Требования к лому сдаваемому на утилизацию регламентируются ГОСТ 1639-78 «Лом и отходы металлов и сплавов».
В конструкции используется масло индустриальное И-20 Гост 20799-79. агрегатное состояние жидкое класс опасности 4 количество вещества в объекте 5 кг предельной допустимой концентрации не более 5 мгм2 группа взрывоопасности смеси Т3.
В соответствии с рядом принятых постановлений и директивных органов все предприятия и организации обязаны осуществлять сбор учет и сдачу отработанных нефтепродуктов. Отработанные масла перерабатываются с целью получения масляных компонентов. Наиболее перспективным и рациональным направлением использования отработанных масел является их переработка на масло перегонных заводах с получением отдельных компонентов для повторного использования. К методам обработки масел относятся отстаивание центрифугирование фильтрация вакуумная перегонка и т.д.
Остальные материалы такие как пластмассы также подлежат переработке либо утилизации.
При работе на полуавтомате используется оптимальное количество масла
пары которого не оказывают больших проблем загрязнения ими окружающей обстановки. Также идет определенный выброс пыли при обработке деталей. Количество которой зависит от используемого сырья и объемов работ. Но всегда соответствует нормам при этом достаточно общеобменной вентиляции.
Все детали и узлы полуавтомата и оснастки являются разборными и по истечению срока службы полностью подлежат утилизации. Что также в значительной степени является положительным фактором в отношении экологической обстановки за счет уменьшения отходов.
Вывод: экологическая экспертиза показывает что использование данного полуавтомата не только соответствует всем нормам в отношении промышленной экологии но способствует их снижению путем замены выполнения старых технологических процессов новыми с более лучшими показателями.
В данной работе был проведен анализ устройств и механизмов для прикрепления каблука были рассмотрены различные конструкции механизмов молотка.
Была разработана кинематическая схема молоткового механизма с пневмоприводом. Также была разработана структурная схема интегрированного рабочего места для крепления каблука.
На основании расчета усилия необходимого для закручивания шурупа произведен расчет гидропривода механизма подачи отвертки.
В разделе дипломного проекта «Технология машиностроения» составлен
технологический процесс изготовления детали входящей в конструкцию
механизма молотка проведены расчеты уравнений размерных цепей
режимов резания составлены операционные карты и операционные эскизы.
В «Экономической части» определен экономический эффект от
внедрения спроектированной установки на производство.
Раздел «Охрана труда и промышленная экология» связан с рассмотрением
вопросов касающихся отдела «Охраны труда и промышленной экологии»
предприятия с учетом использования в производстве проектной установки.
В ходе выполнения работы сделан вывод что для повышения эффективности производства наряду с совершенствованием оборудования требуется уделять немаловажное внимание и рациональной организации рабочих мест так как рабочее место — это первичное звено производства зона трудовой деятельности рабочего или группы рабочих (если рабочее место коллективное) оснащенная необходимыми средствами для выполнения производственного задания. Под организацией рабочего места понимается система его оснащения и планировки подчиненная целям производства. Эти решения в свою очередь зависят от характера и специализации рабочего места от оборудования используемого на нем от его вида и роли в производственном процессе.
Поддержание работоспособности человека на высоком уровне и недопущение его переутомления - одна из главных целей НОТ. Решающую роль в достижении этой цели играет научно-обоснованный режим труда и отдыха (порядок чередования периодов работы и отдыха).
Для предприятий наиболее важна разработка внутрисменного режима труда и отдыха.
Отдых должен назначаться в период начала снижения работоспособности который выявляют на основе результатов специальных исследований работоспособности исполнителя (измеряется системой показателей) в различные часы рабочего дня и построения кривых работоспособности.
Научно-исследовательские организации разработали общие правила назначения перерывов.
Основным временем отдыха в течение смены является обеденный перерыв. Он должен быть не менее 30-45 мин и делить смену примерно на две равные части. Встречающееся на практике назначение обеденного перерыва через 2 -25 ч после начала смены (характерно для цехов многих обувных фабрик) неправильно. В этом случае перерыв назначенный в часы наиболее высокой работоспособности нарушает трудовой ритм и приводит к повышенному утомлению рабочих во второй половине смены.
Периоды остального отдыха также устанавливают в характерных точках кривой работоспособности когда начинает нарастать утомление. Общая продолжительность отдыха зависит от условий и характера работы. В среднем для работ обувного производства отдых должен длиться примерно 20 мин в смену. В конвейерном потоке устанавливают одновременные организационные перерывы для всех рабочих.
Количество перерывов зависит от специфики работ. Перерывы на отдых должны устанавливаться тем чаше чем выше темп работы и больше ее монотонность. Для работ обувного производства не требующих значительных физических затрат но монотонных и выполняемых при высоком темпе увеличение числа перерывов дает больший эффект повышение продолжительности перерывов и их числа.
Данные исследований показали что в обувном производстве целесообразно устанавливать четыре перерыва продолжительностью по 5 мин через каждые 15-2 ч. работ два из них для производственной гимнастики и два для отдыха с легкой разминкой.
Введение производственной гимнастики способствует быстрому включению человека в работу и поддержанию высокой работоспособности.
Сироткин Г.П. Выбор типа привода маигн легкой промышленности: Учебное пособие.-П.: ИГИЛП I98I.-66 с
Анастасиев А.А. Архипов Н.Н. Жаров А.Н. Корнилов В.П. Сторожев В.В. Машины машины-автоматы и автоматические линии легкой промышленности. - М.
Длуогий В.А. Муха Т.И. Цупиков А.Н. Януш В.В. Приводы машин: Справочник. -Д.: Машиностроение 1962- 382с.
Колясин В.П. Оборудование сборочных цехов обувных фабрик М.:
Гавриленко В.А. Минин В.А. Рождественский С.В. Гидравлический привод.- М.: Машиностроение 1968- 502с.
Машина TAVOLA- 300.10V.5 (Италия).
Машина TAVOLA-300.10V.5 (Рис.6) предназначена для крепления каблуков гвоздями а так же шурупом изнутри к женской мужской и детской обуви.
Основные технические характеристики.
Напряжение питания (В) ..380
Частота тока (Гц) 50
Потребл. Мощность (КВт) 0100
Необходимое давление (Бар) .5
Габариты (М) .08х16х21
Каблук на данной машине прикрепляется семью гвоздями и шурупом. Машина имеет электронное управление для забивания гвоздей и шурупа последовательно в запрограммированном порядке или парами по несколько гвоздей одновременно. Машина имеет пневмопривод и подсоединяется к внутрицеховой пневмомагистрали.
Основные блоки устройства и механизмы машины.
Основными механизмами данной машины являются такие как:
) гвоздеотсекающий механизм
Механизм имеет два отделения для загрузки гвоздей и
винтов и предназначен для деления и распределения
штучных крепителей по каналам ведущим к
гвоздеподающему механизму.
) гвоздеподающий механизм
Предназначен для загрузки молоткового механизма штучными крепителями (гвозди и (или) шурупы).
) прижимное устройство-
-служит для фиксации и удержания деталей низа обуви и каблука в определенном положении при забивании гвоздей и шурупа.
) молотковый механизм.
Внутри данного механизма находятся втулки со штоками-молоточками которые непосредственно и забивают гвозди и шуруп.
) электронный блок управления
Данный блок оснащен микропроцессорами благодаря которым и осуществляется программирование порядка в котором и будут забиваться гвозди и шуруп а так же их количество.
Электрооборудование защищено от перегрузок и токов короткого замыкания автоматическими выключателями.
Машина подключается к цеховой сети переменного тока с помощью штепсельного разъема. До начала работы в соответствующее отделение гвоздевого аппарата засыпают 05 кг гвоздей а также 03 кг шурупов. Проверяют работу механизмов пуска и останова: при включенном выключателе рабочие органы машины должны находиться в исходном состоянии.
Работа на машине осуществляется следующим образом. Детали низа накладывают друг на друга и помещают на колонку молоткового механизма При нажатии на педаль верхнее прижимное устройство фиксирует соединяемые детали прижимая их к молотковому механизму. Затем рабочий нажимает одновременно на две рукоятки и происходит процесс прибивания каблука в заранее запрограммированном порядке.