Двухбалочный мостовой кран




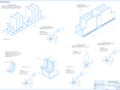
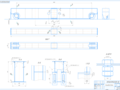
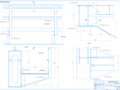
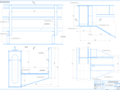
- Добавлен: 25.01.2023
- Размер: 471 KB
- Закачек: 0
Описание
Состав проекта
![]() |
![]() |
![]() |
![]() ![]() ![]() ![]() |
![]() ![]() ![]() ![]() |
![]() ![]() ![]() ![]() |
![]() ![]() ![]() ![]() |
![]() ![]() ![]() ![]() |
![]() ![]() ![]() ![]() |
![]() ![]() ![]() ![]() |
![]() ![]() ![]() |
![]() ![]() ![]() ![]() |
![]() ![]() ![]() ![]() |
![]() ![]() ![]() ![]() |
![]() ![]() ![]() ![]() |
![]() ![]() ![]() |
![]() ![]() ![]() ![]() |
![]() ![]() ![]() ![]() |
![]() ![]() ![]() ![]() |
![]() ![]() ![]() ![]() |
![]() ![]() ![]() ![]() |
![]() ![]() ![]() ![]() |
![]() ![]() ![]() ![]() |
![]() ![]() ![]() ![]() |
![]() ![]() ![]() ![]() |
![]() ![]() ![]() ![]() |
![]() ![]() ![]() ![]() |
![]() ![]() ![]() ![]() |
Дополнительная информация
рис.8.frw

при сочетании: а - эпюра изгибающих моментов от нагрузки q; б - эпюра
изгибающих моментов от силы Т при в - эпюра изгибающих моментов
рис.6.frw

а - в вертикальной плоскости; б - в горизонтальной плоскости.
рис.5.frw

а - со стороны механизма передвижения; б - со стороны площадки токоподвода.
рис.9.frw

рис.11.frw

рис.7.frw

конструкцию моста при сочетании 2а.
рис.3.frw

рис.4.frw

нагрузок; б - от распределенной инерционной нагрузки.
рис.11a.frw

рис.10.frw

соед.узлы.cdw

РПЗ.doc
университет им. Н.Э. Баумана
Расчетно-пояснительная записка к курсовому проекту
“Строительная механика и металлические конструкции”
Двухбалочный мостовой кран Q=15 т.
Задание на курсовое проектирование
Выбор основных геометрических параметров конструкции
Выбор геометрических параметров узлов конструкции
Определение расчетных нагрузок на узлы металлоконструкции и усилий в них
Расчет основных узлов металлоконструкции по методу предельных состояний
Расчет сварных соединений
Технологическая часть
Описание конструкции
Обоснование технических требований
Анализ технологичности конструкции
Разработка технологической схемы сборки
Разработка технологического процесса изготовления элементов балки
Выбор метода и режима сварки
Параметры линий влияния изгибающих моментов и поперечных сил в вертикальной плоскости главной балки.
Ординаты линий влияния
* Сечение 5 при сочетании нагрузок 2в.
Расчетные значения изгибающих моментов и поперечных сил в главной балке в вертикальной плоскости (сочетание 2):
Наименование силового фактора
От Gм.п.т и Gд.м.п.т
Суммарный силовой фактор
Изгибающие моменты М
Расчетные напряжения в главной балке МПа.
Нормальные (в середине пролета)
Касательные (в опорном сечении)
От вер-тикальных нагрузок
От гори-зонтальных нагрузок
Расчет поперечного сечения главной балки мостового крана:
- осевой момент сопротивления
- момент инерции сечения балки
Основное допускаемое напряжение для Ст3 равно 160 МПа следовательно для обеспечения прочности главной балки ее осевой момент сопротивления должен быть равен:
Максимальный изгибающий момент равен: Нм
Рекомендуемое соотношение толщины и высоты листа:
Используя данное соотношение получим:
Толщина листов стали составляет 12 мм значит выбираем листовой прока прокат толщиной 6 мм по ГОСТ 14012-80. Тогда высота листа по условию наименьшего веса и обеспечения достаточной жесткости конструкции получается равной:
Примем высоту главной балки моста равной 1200 мм.
Таким образом для металлоконструкции моста будем использовать листовой прокат толщиной 6 мм. Высота главной балки будет составлять 12м ширина 46 м для обеспечения необходимой прочности и устойчивости металлоконструкции мостового крана.
Мостовой кран предназначен для подъема и перемещения груза в вертикальной и горизонтальной плоскости.
Металлоконструкция концевой балки крана воспринимает нагрузки от веса груза главной балки механизмов подъема и передвижения кабины а также от собственного веса. Нагрузка через концевую балку передается с главной балки на буксы потом на колеса потом на рельсы.
Металлические конструкции в значительной степени определяют массу стоимость и эксплуатационную надежность подъемно-транспортных машин. Они работают под воздействием различных нагрузок окружающей среды и должны удовлетворять требованием жесткости прочности устойчивости и экономичности.
Концевая балка работает при средних условиях которые характеризуются работой с грузами различной массы со средними скоростями(vк=125 мс vт=063 мс vп=028 мс) средним числом включений в час(до 120 в час) средним значением относительной продолжительности включения(до ПВ=50%).
Концевая балка является опорным и соединительным элементом главной балки. Для установки ходовой части крана к концевым балкам приваривают посадочные платики с обработанными поверхностями к которым с помощью болтов крепят буксы с ходовыми колесами. На концевой балке установлены упругие предохранительные устройства – буферы которые срабатывают при положении крана в конечных точках пути взаимодействуя с упорами в конце кранового пути и смягчая удар крана об эти упоры.
Концевая балка представляет собой жесткую сварную металлическую конструкцию габаритные размеры которой 5750х570х450.Металлическая конструкция концевой балки состоит из двух поясов двух вертикальных стенок и диафрагм размещенных внутри балки. Так как длина балки невелика то она выполняется одноразъемной с целью разъединения моста после его изготовления на две половины для лучшего транспортирования по железной дороге. Разъемные части балки соединяют с помощью монтажных накладок на заводе-изготовителе с установкой 20 % чистых болтов от общего количества черных болтов. При монтаже крана на месте эксплуатации стыки балок с монтажными накладками соединяют заклепками или чистыми болтами. Основные параметры и элементы концевых балок унифицированы по группам грузоподъемности что позволило создать типовые технологические процессы их изготовления.
Материалом для элементов металлоконструкций концевых балок служит листовая сталь Ст3.сп. Толщина применяемых листов для поясов балки 10 мм вертикальных стенок и диафрагм 6 мм.
Сварка поясов со стенками выполняется снаружи. Стенки и пояса в балке являются очень тонкими элементами поэтому под действием внутренних сил нормальных и касательных напряжений (особенно при достижении критических значений) стенки и пояса могут потерять свою плоскую форму и выйти из плоскости что приведет к усталостным разрушениям.
Диафрагмы привариваются к сечению балки по трем сторонам. С растянутым поясом диафрагмы не свариваются. Между ними есть технологический зазор 10 мм. По длине балка имеет переменное сечение (переменная высота балка) для того чтобы она удовлетворяла условиям статической и динамической жесткости и времени затухания колебаний. Из условий местной устойчивости выполняются скосы длиной 75 мм.
Важным с точки зрения конструкции является узел соединения главных балок с концевыми. Это соединение должно быть достаточно жестким чтобы воспринимать изгибающие моменты в местах стыковки балок при действии горизонтальных нагрузок. От горизонтальной жесткости моста в значительной степени зависит величина перекоса крана при движении и степень износа ходовых колес. Поскольку балки работают на изгиб в горизонтальной плоскости они должны обладать в этом направлении достаточной жесткостью поэтому момент инерции их сечений относительно вертикальной оси принимается не меньшим чем момент инерции сечения главной балки в месте их соединения. Соединение главных балок с концевыми осуществляется сваркой внахлест что резко снижает трудоемкость изготовления металлоконструкций. Для улучшения качества сварного шва используют накладки что приводит к увеличению сварного шва следовательно к разделению конструктивного и технологического концентраторов а это повышает предел выносливости и усталостную прочность. Чтобы избежать концентраций напряжений а следовательно усталостных разрушений острые углы сварных швов необходимо скруглить. Такое исполнение шва является типовым. Он наиболее технологичный не требует больших денежных затрат и прост в изготовлении.
В месте соединения главной балки с концевой необходимо выполнять сопряжение: напротив внутренней диафрагмы концевой балки должны быть стенки главной балки. Накладки приваренные снизу повышают жесткость. Для присоединения ходовых колес на концевой балке выполняют планки под буксы.
Отклонения от перпендикулярности опорных поверхностей горизонтальных подбуксовых платиков к опорным поверхностям вертикальных подбуксовых платиков не более (ГОСТ 24378-80).
Отклонение от перпендикулярной вертикальной плоскости проходящей через опорные поверхности вертикальных подбуксовых платиков каждой стороны по отношению к вертикальной плоскости проходящей через ось подкранового рельса не более (ГОСТ 24378-80).
Габаритные размеры балки выполнены по 14-му квалитету (ГОСТ 24378-80).
Скручивание коробчатой концевой балки измеренное по крайним большим диафрагмам должно быть не больше (ГОСТ 24378-80).
Отклонение от прямолинейности концевой балки в горизонтальной плоскости измеренное по верхнему поясу допускается (ГОСТ 24378-80).
Отклонение от плоскостности в коробчатых балках на участке между соседними диафрагмами допускается: поясов в растянутой зоне в сжатой зоне ; вертикальных стенок (ГОСТ 24378-80).
Отклонение от вертикали боковых стенок по высоте балки замеренное по большим диафрагмам допускается (ГОСТ 24378-80).
В коробчатых балках стыки поясов должны быть смещены по отношению к стыкам стенок не менее чем на 300 мм и не должны располагаться в одном поперечном сечении и находиться от диафрагмы не менее чем на 100 мм (ГОСТ 24378-80).
Стыки стенок должны располагаться симметрично относительно середины балки (ГОСТ 24378-80).
Посадочные поверхности подбуксовых платиков должны быть обработаны по 11-му квалитету (h11) с параметрами шероховатости Rz=40мкм (ГОСТ 2789-73). Расстояние между ними также выполнено по 11-му квалитету (Н11) (ГОСТ 24378-80).
Монтажные отверстия под чистые болты должны быть развернуты под посадку (ГОСТ 24378-80).
Местная волнистость заготовок по плоскости не должна превышать (ГОСТ 24378-80).
При разметке листового проката следует учитывать усадку вызываемую наложением сварных швов.
Отклонение параллельности сторон листов допускается в пределах ±3 мм (ГОСТ 24378-80).
Косина реза при газовой резке по толщине кромок не должна превышать 3Rz (ГОСТ 24378-80).
В сильно нагруженных элементах металлоконструкций изготовленных из листа направление действующего усилия должно совпадать с направлением проката.
Не допускается изготовление элементов металлоконструкций из металла имеющего на поверхности следы маркировки стальными клеймами.
Прихватки поставленные при сборке должны быть не более 08 высоты основного шва длиной 30 – 60 мм и выполняться теми же электродами что и основная сварка.
При заварке стыков для обозначения начала и конца сварки необходима прихватка технологических планок которые удаляют после окончательной сварки стыков с обязательной обработкой концов стыка шлифовальным кругом.
При наложении нескольких швов каждый из них зачищается от брызг и шлака.
При окончании сварки кратер должен быть выведен на основной металл.
Не допускается в сварных швах подрезы основного листа толщиной до 8 мм более чем на 05 мм а листов толщиной свыше 8 мм – более 1 мм.
Сваривать металлоконструкции нужно на выверенных стеллажах или стендах обеспечивающих взаимное положение частей металлоконструкции в закрытых помещениях при температуре не ниже –10°С без ударных воздействий на свариваемые элементы при сварке.
В сварных швах не допускаются трещины непровары наплывы протоки не заделанные кратеры несимметричность расположения шва свищи несплавления между слоями в многослойных швах пористость шлаковые включения и подрезы.
Изготовление балок коробчатого сечения в отличие от других конструкций позволяет широко применять механизированные способы сварки что является технологичным. Недостатком балок коробчатого является сечения перед металлоконструкциями решетчатого типа большая масса конструкции и большая наветренная площадь. Применение механизированных способов сварки позволяет снизить стоимость металлоконструкции. Преимуществом балок коробчатого сечения является очень небольшое количество по сравнению с другими типами металлоконструкции элементов узлов мелких деталей резко повышающих трудоемкость изготовления; практически полное отсутствие пазух и недоступных мест для покраски снижающих коррозионную стойкость.
С точки зрения изготовления изделие является технологичным т.к. используются высокопроизводительные методы сварки: автоматическая и полуавтоматическая (в основном) а также ручная. Используются стандартные электроды.
При изготовлении концевой балки возможны следующие схемы технологической сборки и сварки:
последовательная сборка и сварка элементов сборочных единиц и конструкции в целом;
сборка и сварка сборочных единиц а затем сборка элементов сборочных единиц и конструкции из сборочных единиц.
Учитывая то что производство серийное конструкция крупногабаритная выбираем второй способ сборки. Применение узловой сборки определяется объемом выпуска ограниченностью грузоподъемных средств в цехе трудностью кантования изделия. Подсборочными единицами являются верхний и нижний пояса и вертикальные стенки которые состоят из двух соединяемых между собой листов (балка одноразъемная).
При разработке общей схемы сборки в качестве базового элемента учитывая удобство установки и снятия собираемого изделия надежность и удобство его закрепления возможность подвода присоединяемых деталей и сборочных инструментов с разных сторон принимаем верхний пояс. Базовую деталь изделия устанавливают на различные последовательно сменяемые базы. Сначала к верхнему поясу привариваются диафрагмы. Для необходимой устойчивости сечения балки требуется восемь диафрагм которые должны находится на одном уровне. Это достигается следующим образом: устанавливаются по выверке первая и последняя диафрагмы между ними натягивается леска по которой ставятся остальные диафрагмы. Чтобы передать полученную конструкцию на следующее рабочее место диафрагмы надо закрепить поэтому используются прихватки. Точность расстановки диафрагм требуется проконтролировать. Далее прихватывают накладки и вертикальные стенки далее собирают платики под буксы с угольниками которые прихватываются к крайней стенке в двух точках затем собирают балку и нижний пояс устанавливают буферы на верхний пояс.
В серийном производстве сборку изделий выполняют на плитных настилах с пазами снабженными упорами фиксаторами и различными зажимными устройствами. Для поворотов вращения и установки изделия в наиболее удобное для сварки положение применяют кантователи. Для стягивания поджима и выравнивания отдельных элементов концевой балки используются винтовые прижимы: струбцины.
Схемы базирования изделий при узловой и общей сборке выбирают с учетом обеспечения заданной точности сборки удобств ее выполнения сборщиками упрощения приспособлений оборудования и транспортных средств а также надежной собираемости деталей.
Разработка технологического процесса изготовления элементов балки.
Основные параметры и элементы концевых балок унифицированы и имеют типовые технологические процессы их изготовления.
В крановых конструкциях значительное применение имеет листовая горячекатаная сталь (ГОСТ 19903 – 74) широкополосная универсальная (ГОСТ 82 – 70) полосовая (ГОСТ 103 – 76). В качестве заготовки для изготовления концевой балки будем использовать широкополосную сталь толщиной 4 – 50 мм которая катается шириной 200 – 1050 мм при длине 3 – 10 м и является рациональной как готовый элемент конструкции. Пояса балки состоят только из листов. Количество поясных листов следует брать по возможности меньше (1 – 3). Наиболее целесообразна конструкция с одним поясным листом. Т. к. концевая балка является одноразъемной то заготовками для пояса служат два одинаковых листа толщиной 10 мм (во избежание хрупких разрушений рекомендуется толщины листов из низколегированных сталей назначать не выше 40 мм) длиной 3000 мм и шириной 700 мм а для стенок – четыре листа толщиной 6 мм длиной 3000 мм и шириной 700 мм.
С целью устранения волнистости выпучин назначается правка. Листы правят преимущественно в холодном состоянии путем местной пластической деформации. Для правки листового проката используются листоправильные многовалковые машины. Листы толщиной 5 – 40 мм правят на семивалковых вальцах многократным пропусканием листов между двумя рядами валков причем валки одного ряда размещены в шахматном порядке по отношению к валкам другого ряда. Рабочая скорость правки на листоправильных машинах зависит от толщины и ширины листов и ориентировочно составляет 6–3. Качество правки листов проверяют с помощью линейки. Волнистость опускается не более 2 мм на 1000мм.
При изготовлении концевых балок применяют поточную линию дробеметной очистки и фосфатирования (образование в результате химического процесса на поверхности стального листа тонкого слоя нерастворимой фосфорно-кислой соли железа и марганца обладающего высокими антикоррозионными свойствами) стальных листов под окраску с терморадиационной сушкой. Листовой металл очищают от окалины ржавчины масла и других загрязнений вызывающих дефекты в сварных швах.
В серийном производстве применяют разметку с помощью шаблонов. Все необходимые размеры переносят на заготовку с помощью разметочных игл.
Резка металла является одной из наиболее трудоемких и сложных операций. Наиболее распространенным методом резки металла при изготовлении элементов металлоконструкций на заводах подъемно-транспортного машиностроения является механическая и газопламенная резка. Механическую резку выполняют на ножницах: гильотинных дисковых вибрационных и пресс ножницах. Резка ножницами основана на разделении металла по линии реза под давлением верхнего подвижного ножа и нижнего неподвижного (у дисковых ножниц оба ножа являются ведущими). Газопламенная резка основана на интенсивном сгорании разрезаемого металла в струе кислорода сосредоточенного на узком участке и удалении жидких шлаков. Выбираем резку металла на гильотинных ножницах т.к. заготовки вырезанные на дисковых ножницах требуют правки заготовки после резки на пресс ножницах требуют обязательной правки и учета величины вмятины при последующей обработке вибрационные ножницы применяют при резке листового металла до 5 мм а в качестве заготовок для данной балки используются листы толщиной 6 и 10 мм после газопламенной резки необходима механическая обработка кромок. Гильотинные ножницы служат для продольной и поперечной резки листов толщиной до 40 мм и для обрезки фасок под сварку. Гильотинные ножницы допускают максимальную длину реза до 3200 мм точность резки соответствует 12 – 14-му квалитету. Они дают чистый рез заготовки меньше деформируются и более производительны.
Процесс сборки-сварки концевой балки производится на переменно-поточной стационарной линии состоящей из специализированных пяти рабочих мест оснащенных механизированными стендами сборочными стапелями кантователями и специальной переналаживаемой оснасткой что позволяет с минимальными затратами времени на переналадку быстро перейти на любого из типоразмеров концевых балок. Все оборудование цеха размещено вдоль пролета цеха. Для межоперационной передачи балок вдоль линии смонтирован подвесной монорельс с самоходными спаренными электротолкателями имеющими специальные захваты. Такой вид транспортирования балок очень прост удобен и безопасен т.к. при движении балка подвешенная на двух электротолкателях находится в устойчивом положении и не требует сопровождения рабочим. При этом значительно облегчилась установка балок в стапели и труд рабочего сведен к нажатию кнопок управления электроталью. Все рабочие места линии механизированы с широким использованием в сборочных стапелях стендах кантователях электрических гидравлических пневматических и магнитных устройств для закрепления и поджима деталей при сборке балок.
На первом рабочем месте собирают нижний и верхний пояса и вертикальные стенки с обработкой отверстий на радиально-сверлильном станке. На стыки установленных с помощью упоров и выверенных листов вручную подают одну накладку выдерживая установочные размеры. В накладках по шаблону намечают места для отверстий под установку болтов и с помощью пневмоподжимами листы и накладки закрепляют на столе. Радиально-сверлильным станком сверлят зенкеруют и развертывают отверстия под установку чистых болтов Мх42. В отверстия вставляют болты на них надевают шайбы и навертывают гайки.
На втором рабочем месте собирают корпус балки без нижнего пояса. Верхний пояс укладывают на стенд по упорам вниз накладками размечают его под установку диафрагм и накладок. Согласно разметке под угольник с помощью тележки устанавливают и прихватывают в 3-ех точках диафрагмы а на стыки накладки. Т.к. балка одноразъемная то накладки приваривают к одному из концевых листов. Далее на верхний пояс устанавливают вертикальные стенки по торцевым упорам. С помощью ручной сварки вертикальные стенки прихватывают к диафрагмам и верхнему поясу с внутренней стороны с одновременным прижимом их в процессе прихватки порталом с пневмоприжимами.
На третьем рабочем месте собирают платики под буксы с угольниками прихватывают угольники к корпусу балки и сваривают все внутренние швы балки. Буксу устанавливают углом вверх в пазы вставляются платики и на них устанавливаются угольник до совмещения отверстий в которые вводят болты крепления платиков. Прихватывают платики к угольникам и снимают их с дальнейшей их сваркой и установкой на специальные приспособления установленные на стенде под размер балки. Балку устанавливают на другие приспособления предназначенные для установки платиков в угольниках вырезами вертикальных стенок на угольники. Прижимами угольники поджимают к вертикальным стенкам и прихватывают их с наружной стороны стенок. Далее привариваются диафрагмы к внутренним вертикальным стенкам и угольники.
На четвертом рабочем месте собирают балку с нижним поясом и устанавливают буферы на верхний пояс. Балку крепят на стойках стола. С помощью гидроцилиндров нижний пояс поджимают к вертикальным стенкам и прихватывают. На верхний пояс по разметке устанавливают и прихватывают два корпуса буфера.
На пятом рабочем месте устанавливают балку угольниками на стойки и закрепляют с помощью ручных захватов. Поворачивая балку в удобное для сварки положение производят полуавтоматическую сварку в среде углекислого газа всех наружных поясных швов.
Выбор метода и режима сварки.
Трудоемкость сварочных работ в сварных конструкциях составляет около 30% общей трудоемкости ее изготовления. В подъемно-транспортном машиностроении по объему применения электродуговая сварка является основным видом сварки
По СНИП II-23-81* для стальных конструкций.
Для сварки стальных конструкций следует применять:
электроды для ручной дуговой сварки по ГОСТ 9467-75*;
сварочную проволоку по ГОСТ 2246-70*;
флюсы по ГОСТ 9078-81*;
углекислый газ по ГОСТ 8050-85.
Применяемые сварочные материалы и технология сварки должны обеспечивать значение временного сопротивления металла шва не ниже нормативного значения временного сопротивления Run основного металла а также значения твердости ударной вязкости и относительного удлинения металла свариваемых соединений установленные соответствующими нормативными документами.
В конструкциях со сварными соединениями следует:
предусматривать применение высокопроизводительных механизированных способов сварки;
обеспечивать свободный доступ к местам выполнения сварных соединений с учетом выбранного способа и технологии сварки.
Разделку кромок под сварку следует принимать по ГОСТ 8713-79* ГОСТ 11533-75 ГОСТ 14771-76* ГОСТ 23518-79 ГОСТ 5264-80 и ГОСТ 11534-75*.
Размеры и формы сварных угловых швов следует принимать с учетом следующих условий:
) катеты угловых швов kf должны быть не более 12t где t- наименьшая толщина соединяемых элементов;
) катеты угловых швов kf следует принимать по расчету но не менее указанных в таблице 38[1];
) расчетная длина углового сварного шва должна быть не менее 4kf и не менее 40 мм;
) расчетная длина флангового шва должна быть не более 85bf kf (bf-коэффициент принимаемый по таблице 34*[1]) за исключением швов в которых усилие действует на всем протяжении шва;
) размер нахлестки должен быть не менее 5 толщин наиболее тонкого из свариваемых элементов;
) соотношения размеров катетов угловых швов следует принимать как правило 1:1. При разных толщинах свариваемых элементов допускается принимать швы с неравными катетами при этом катет примыкающий к более тонкому должен соответствовать требованиям 1 а примыкающий к более толстому элементу – требованиям 2.
Для прикрепления ребер жесткости диафрагм и поясов сварных двутавров допускается применять односторонние угловые швы катеты которых kf следует принимать по расчету но не менее указанных в таблице 38 [1].
Необходимо обеспечить не только прочность сварных соединений но и позволить сварным швам воспринимать нагрузку что возможно когда прочностные свойства шва соответствуют свойствам материала т.е. швы должны быть однородными поэтому сварку ответственных швов надо выполнять при постоянной температуре и под слоем флюса который используется для защиты расплавленного металла от вредного влияния атмосферного воздуха и получения качественного сварного шва. Полуавтоматическая сварка металлическим электродом производится при горении дуги между сварочной проволокой и кромки свариваемого металла под слоем флюса засыпаемого через шланг в зону шва впереди дуги. Тепло дуги расплавляет свариваемый металл проволоку и часть флюса образуя сварочную ванну. Расплавленный флюс защищает жидкий металл от вредного влияния азота и кислорода воздуха одновременно раскисляет его и удаляет окисел в слой шлака. Флюс также концентрирует тепло в зоне сварки обеспечивая при этом глубокий провар основного металла правильно формирует сварной шов благодаря давлению на ванну жидкого металла и медленному его остыванию устраняя потери на угар и разбрызгивание расплавленного металла стабилизирует горение дуги легирует металлы шва и обеспечивает высокие механические свойства наплавленного металла. Флюс изготавливают путем сплавления нескольких компонентов и последующего их размельчения до определенной фракции. В качестве флюса для полуавтоматической сварки применяют флюс АН-348 (ГОСТ 9087-69). В качестве электродов применяют проволоку стальную сварочную диаметром 3 – 6 мм марки СВ-08А (ГОСТ 2246-76). Применяется полуавтомат типа ПШ-5 с постоянной скоростью подачи сварочной проволоки не зависящей от напряжения дуги. Сварку ведут на переменном токе т.к. меньше расходуется электроэнергии и применяют относительно простую аппаратуру.
Диафрагмы привариваются электродуговой сваркой в углекислом газе т.к. сварочные швы выполняются прерывистыми и их качество не важно. Сущность способа состоит в том что воздух оттесняется от зоны сварки струей углекислого газа а окисление самим углекислым газом переплавляемого дугой металла компенсируется повышенным содержанием элементов-раскислителей в электродной проволоке. Для сварки применяем полуавтомат А-537 предназначенный для сварки постоянным током 70–200А металла толщиной более 3 мм сварочной проволокой марки СВ-08Г2С (ГОСТ 2246-70) диаметром 16–2 мм. Напряжение дуги 17 – 21 В.
Предел текучести МПА
Минимальные катеты швов kf мм при толщине более толстого из свариваемых t мм
Тавровое с двусторонними угловыми швами; нахлесточное и угловое
Автоматическая и полуавтоматическая
Тавровое с односторонними угловыми швами
Вид сварки при диаметре сварочной проволоки d мм
Значение коэффициентов bf и bz при катетах швов мм
Автоматическая при d=3-5
Автоматическая и полуавтоматическая при d=14-2
Нижнее горизонтальное вертикальное
Ручная; полуавтоматическая проволокой сплошного сечения при d14 или порошковой проволокой
В лодочку нижнее горизонтальное вертикальное потолочное
Расчет на прочность деталей машин: Справочник Биргер И.А Иосилевич Г.Б. Шорр Б.Ф. 4-е изд. М. Машиностроение 1993 640 стр.
Мостовые краны общего назначения Шабашов А.П. Лысяков А.Г. 5-е изд. М. Машиностроение 1980 304 стр.
Справочник по кранам в 2-ух томах под общ. ред. Гохберга М.М. М. Машиностроение 1988.
Подъемно-транспортные машины: Атлас конструкций под ред. М.П. Александрова Д.Н. Решетова. Изд. 2-е. М. «Машиностроение» 1987 122стр
Основы конструирования в 3-ех томах. Орлов П.И. 2-ой том. М. «Машиностроение» 1988 574 стр.
Технология производства подъемно-транспортных машин Косилова А.Г. Сухов М.Ф. 2-е изд. М. Машиностроения 1982 301 стр.
Справочник технолога-машиностроителя в 2-ух т. Т.1 под ред. Косиловой А.Г. Мещерякова Р.К. 4-е изд. М. Машиностроение 1986 656стр.
Рыбаков В.М. Сварка и резка металлов: Учебник для сред.проф. - техн. училищ. – 2-е изд. испр. – М.: Высш. школа 1979 – 214с.
тех.кон.бал..cdw

Приварить диафрагмы к верхнему поясу
непрерывным сварным швом Т1-
0 Операция сборочная.
Установить крайние диафрагмы
по этой струне и угольнику установить
остальные диафрагмы в соответствии с эскизами.
5 Операция сборочная.
Установить вертикальные стенки
в соответствии с эскизом.
0 Операция сварочная.
Приварить вертикальные стенки к
верхнему поясу непрерывным сварным швом Т1-
Приварить диафрагмы к вертикальной стенке
0 Операция сборочно-сварочная.
Приварить платики под буксы с угольниками
швом по незамкнутой линии H1-
Приварить угольники к корпусу балки
непрерывным швом Т1-
Эскизы сборки-сварки
гл.cdw

соед.cdw

кон.cdw

соед.узлы2.cdw

общ.вид2.cdw

База грузовой тележки
Колея грузовой теллежки
Режим работы 6К (ГОСТ 25546-82)
Скорость передвижения крана
Скорость подъема груза
Скорость передвижения тележки
Материал конструкции Ст3
общ.cdw

База грузовой тележки
Колея грузовой теллежки
Режим работы 6К (ГОСТ 25546-82)
Скорость передвижения крана
Скорость подъема груза
Скорость передвижения тележки
Материал конструкции Ст3
гл.балка.cdw

кон.балка2.cdw

общ.вид.cdw

База грузовой тележки
Колея грузовой теллежки
Режим работы 6К (ГОСТ 25546-82)
Скорость передвижения крана
Скорость подъема груза
Скорость передвижения тележки
Материал конструкции Ст3
кон.балка.cdw

гл.балка1.cdw
