Деталь стакан сверление 4-х отверстий


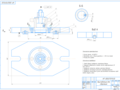
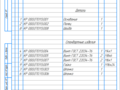
- Добавлен: 25.01.2023
- Размер: 133 KB
- Закачек: 0
Узнать, как скачать этот материал
Подписаться на ежедневные обновления каталога:
Описание
Деталь стакан сверление 4-х отверстий
Состав проекта
![]() |
![]() |
![]() ![]() ![]() |
![]() ![]() ![]() ![]() |
![]() ![]() ![]() ![]() |
Дополнительная информация
Контент чертежей
к.р прис чистовик 1.doc
Севастопольский национальный технический университет
«ПРОЕКТИРОВАНИЕ СТАНОЧНЫХ ПРИСПОСОБЛЕНИЙ »
Определение типа производства 3
Разработка маршрутного технологического процесса механической обработки детали . 6
Проектирование операционного технологического процесса обработки заданной поверхности расчет сил резания и нормы времени на операцию 7
.Расчёт норм времени на сверлильную операцию 10
Расчёт производительности приспособлений 11
Определение схемы установки заготовки в приспособлении
Выбор баз и разработка схем базирования 12
Расчёт погрешности базирования детали 14
Разработка схемы сил действующих на деталь определение точки приложения и направления действия зажимной силы 15
Разработка схемы сил действующих на деталь определение точки приложения и направления действия зажимной силы. . 17
Точностной расчет приспособления 18
Описание конструкции и работы спроектированного приспособления 19
Определение типа производства
Выбор того или иного производства а также присущих ему технологических и организационных форм на первоначальной разработки контрольной работы производится исходя из данной годовой программы выпуски ориентировочной трудоемкости изготовления детали и ее массы этот предварительный выбор производства осуществляется путем сравнения с данными имеющимися в литературных справочниках или путем сравнения с заводской деталью.
Тип производства по ГОСТ 3.1108-74 характеризуется коэффициентом закрепления операций Кз.о. который показывает отношение всех различных технологических операций выполненных или подлежащих выполнению подразделениям в течении месяца к числу рабочих мест. Так как Кз.о. отражает периодичность обслуживания рабочего всей необходимой информацией то Кз.о. оценивается применительно к явочному числу рабочих подразделения из расчета на одну смену:
где - суммарное число операций.
РЯ- число рабочих мест на которых выполняются эти операции.
Годовая программа изделий – 500 шт.
Количество деталей на изделие m=1.
Режим работы предприятия – 2 смены в сутки.
Кз.о. 4 следовательно массовое
Такт выпуска продукции равен
При Тв= 20 40 производство среднесерийное.
Тип производства определяется по коэффициенту закрепления операций (ГОСТ 3.1119-83)
где SПоi- суммарное число различных операций за месяц (по участку из расчета на одного сменного мастера)
SPi - явочное число рабочих участка выполняющих различные операции при работе в одну смену.
При учебном технологическом проектировании рекомендуется определять условное число однотипных операций выполняемых на одном станке в течение одного месяца при работе в одну смену
где hн - планируемый нормативный коэффициент загрузки станка всеми закрепленными за ним операциями принимается для крупно- средне- и мелкосерийного производства соответственно равным 075; 08; 09;
hз - коэффициент загрузки станка проектируемой операцией:
hз = ТшкNм (60FмКв)
где Тшк - штучно-калькуляционное время необходимое для выполнения проектируемой операции;
Кв - коэффициент перевыполнения норм принимается равным 13;
Nм - месячная программа при работе в одну смену: Nм = N(2×12)=5000024=20833;
N =50000- годовой объем выпуска заданной детали штук;
Fм - месячный фонд времени работы оборудования в одну смену ч;
Fм = 4055(2×12) = 169 ч
Поi = 13182hз(Тшк Nм)
Количество операций выполняемых в течение месяца на участке определяется по формуле:
SПoi = П01 + П02 + ..+ Пon = (шт) .
Условное число явочных рабочих необходимых для обслуживания одного станка определяется по зависимости
Явочное число рабочих участка определяется суммированием Рi
SРi = Р1 + Р2 + .. + Рn =34 (раб).
Если Кзо = 1 производство - массовое;
Кзо 10 - крупносерийное; 10 Кзо 20- серийное; 20 Кзо 40 - мелкосерийное.
При отсутствии базового технологического процесса тип производства предварительно может быть по таблице. Он уточняется по рассмотренной методике после выполнения нормирования технологических операций.
Программа выпуска N =50000штгод производство серийное.
Таблица 1 Ориентировочная программа выпуска при различных типах производства в механических и ремонтных цехах
Максимальная масса обрабатываемой детали кг.
Тип производства при программе выпуска
Вывод: Исходя из расчетов производство является серийным что подтверждает выбранные значения из таблицы.
Разработка маршрутного технологического процесса механической обработки детали
Операционный тех. процесс обработки заданной поверхности
Оборудование: Вертикально- сверлильный станок модели 2Р135Ф2
Техническая характеристика станка
Наибольший диаметр сверления в мм 35
Расстояние от оси шпинделя до лицевой стороны станины в мм 300
Наибольшее расстояние от торца шпинделя до стола в мм 600
Наибольший ход шпинделя в мм 225
Наибольшее установочное перемещение шпиндельной бабки в мм 200
Размеры рабочей поверхности стола в мм:
Наибольшее вертикальное перемещение стола в мм . 560
Число скоростей вращения шпинделя 12
Наибольшее число оборотов шпинделя в минуту 2000
Наименьшее число оборотов шпинделя в минуту . 45
Число подач шпинделя (револьверной головки ) 18 Наибольшая величина подачи в ммоб 10
Наименьшая величина подачи в ммоб 0115
Мощность главного электродвигателя в квт 37
Сверлильная операция.
Сверление будет производиться на сверлильном станке 2Р135Ф3.
Заготовка устанавливается при помощи приспособления «072».
Сверлятся 4 отверстия диаметром 11 мм выдерживая диаметр 125±001 мм.
При обработке используется спиральное сверло из быстрорежущей стали
диаметром 11 мм с коническим хвостовиком ГОСТ 10903 – 77.
Диаметр сверла D = 11 мм
Длина сверла L = 60 мм
Длина рабочей части l = 30 мм
Материал режущей части: P6М5
Геометрические параметры:
α=12º ; = 40º ; 2φ = 118º ;
Измерительный инструмент: штангенциркуль ШЦ–I–01–125 ГОСТ 160–80
Режущий инструмент: сверло диаметром 11 мм ГОСТ 10902-77
Операция 025 сверлильная:
Время на установку и снятие детали – 065 мин [карта 5 стр 31 2]
Время связанное с переходом – 049 мин [карта 20 стр 66 2]
Время на контрольные измерения – 020 мин [карта 87 стр 183 2]
Время связанное с переходом – 014 мин [карта 20 стр 67 2]
Время на изменение величины подачи – 007 мин [карта 20 стр 69 2]
Время на изменение числа оборотов – 008 мин [карта 20 стр 69 2]
Время связанное с подводом и отводом задней бабки –
0 мин [карта 20 стр 66 2]
Время на установку и снятие щитка – 003 мин [карта 20 стр 69 2]
Время на контрольные измерения – 011 мин [карта 87 стр 183 2]
Сверление отверстия чистовая операция.
В результате обработки получаем D= 11 мм глубина L=15
Глубина резания при сверлении t=05D.
Подача S (ммоб) при сверлении отверстий без ограничивающих факторов выбираем максимально допустимую по прочности сверла подачу(S=019ммоб)
Скорость резания ммин при сверлении:
Значения коэффициента Сv и показателей степени приведены для сверления в табл.28 стр.278.
Общий поправочный коэффициент на скорость резания учитывающий фактические условия резания Кv=KmvKиvKlv
где Кмv =10 коэффициент на обрабатываемый материал (табл.1-4 стр.261-263)
Киv =10 (Р18) коэффициент на инструментальный материал (табл.6 стр.263) Klv =10 коэффициент учитывающий глубину сверления (табл.31 стр.280).
Крутящий момент Н·м и осевую силу Н рассчитывают по формулам:
Значения коэффициентов См и Ср и показатели степени приведены в (табл.32 стр.281.) и равны 003 и 68 соответственно.(q=04; y=02).
Коэффициент учитывающий фактические условия обработки в данном случае зависит только от материала обрабатываемой заготовки и определяется выражением Кр=Кмр.
Значения коэффициента Кмр =10 приведены для стали и чугуна в (табл.9 стр.264.)
Мощность резания кВт определяется по формуле:
где частота вращения инструмента или заготовки обмин
Скорректируем полученное значение по паспорту станка:
Тогда скорость будет равна:
Корректируем по станку nд =1000обмин
Штучное время вычисляется по формуле:
Расчёт норм времени на сверлильную операцию
Вспомогательное время включает в себя:
Время на установку и снятие детали
Время связанное с первым переходом
Время связанное со вторым переходом
Так как производство серийное штучно-калькуляционное время равно:
Подготовительно-заключительное время на получение и сдачу инструмента 9 мин;
Подготовительно-заключительное время на наладку станка 10 мин;
Расчёт производительности приспособлений
Для определения производительности приспособления т.е. расчёта приспособления необходимо определить:
- минутную производительность
- часовую производительность
- сменную производительность
где: f – продолжительность смены ч.
Анализируя ритм выпуска и годовую программу выпуска устанавливаем зависимость:
- потребное время на изготовление годовой программы в часах.
Выбор баз и разработка схем базирования
Каждое приспособление должно обеспечивать выполнение всех функций обусловленных операцией. Среди них главной является базирование заготовки. После базирования заготовку необходимо закрепить чтобы она сохранила при обработке неподвижность относительно приспособления
Базирование и закрепление – это два разных элемента установки заготовки. Они выполняются последовательно. Базирование нельзя заменить закреплением. Если из шести опорных точек отсутствует одна или несколько то у заготовки остается одна или несколько степеней свободы. Это значит что в направлении отсутствующих опорных точек положение заготовки не определено и заменить отсутствующие опорные точки закреплением с целью базирования нельзя.
Опорные элементы разделяются на основные и вспомогательные опоры. Кроме того опоры бывают неподвижными подвижными плавающими и регулируемыми.
Установка – это процесс базирования и закрепления заготовки.
Оптимизация и выбор рациональной схемы базирования основан на определении минимальной погрешности базирования. .
Погрешность закрепления заготовки =100 мкм. При установке в зажимное приспособление с винтовым зажимным устройством.
Схема базирования заготовки выбираем.
где У – установочная база лишающая заготовку 3-х степеней свободы; Н – направляющая база лишающая заготовку 2-х степеней свободы; О –
опорная база лишающая заготовку 1-й степеней свободы; ДО – двойная опорная база лишающая заготовку 2-х степеней свободы;
Расчёт погрешности базирования детали
Погрешностью базирования называется разность предельных расстояний измерительной базы относительно установленного на размер инструмента возникающая при не совмещении инструмента установочной базы в результате неточности формы и размеров.
Погрешность базирования возникает в результате несовпадения конструкторских и установочных баз в данном случае измерительной базой является деталь в которой и производится упор детали во время обработки.
Где Smin – минимальный радиальный зазор посадки на палец определяется по формуле
Do-диаметр отверстия Do=37H6=37+0.016 =37016
dп-диаметр пальца dп=37ef7=37-0.089 -0.050 =36911
-допуск на диаметр отверстия мм.
- допуск на диаметр пальца мм.
Разработка схемы сил действующих на деталь определение точки приложения и направления действия зажимной силы.
Мпр=хРt1= Рt2==> Рt1=12 – 13Рt2=13
Рt1*(R+rотв)- Рt2*(R-rотв)- W*f*Rш.с=0
Rш.с =185 мм=00185 м
rотв 55 мм = 00055 м
Определение наиболее нагруженного элемента приспособления и его прочностной
Наиболее нагруженными в данном приспособлении будет винтовая пара за счет которой и производится преобразование вращательного движения в возвратно-поступательное и на которую будут действовать основные нагрузки.
Расчет ведется определение среднего диаметра резьбы которая выдержит необходимую нагрузку силу закрепления. Резьба рассчитывается на смятие.
Ксм=W(d2*H)≤[] (МПа)
[]=0.9*=09*640=576 МПа
d2- средний диаметр резьбы;
Н – высота профиля резьбы Н=0866*р;
р- шаг резьбы р=1 тогда Н=0866*1=0866мм
d2 = d - 2Н=16-(19*0866)8=119432 мм;
[] что удовлетворяет заданному условию и значит данная резьбовая пара будет удовлетворять требованиям приспособления по прочности.
Точностной расчёт приспособления.
На точность обработки влияет ряд технологических факторов вызывающих общую погрешность обработки которая не должна превышать допуск выполняемого размера при обработке заготовок т.е. ≤
Погрешность изготовления приспособления
Кт – коэффициент учитывающий отклонения составляющей этой от нормального распределения 11;
К1 – коэффициент учитывающий уменьшение погрешности базирования при работе на настроенном станке; К1=08-085 станок настроенный;
б – погрешность базирования 0032 мм;
з – погрешность закрепления учитывается только в условиях прецизионной обработки 0;
у – погрешность установки приспособления на станке
у= msL=00311118=00089 мм
S – зазор между шпонкой и пазом стола 003мм;
L – расстояние между шпонками 118 мм;
m – обрабатываемый размер ø11 мм;
и – износ установочных элементов приспособления 0;
п – погрешность связанная с перекосом инструмента (кондуктор) 0;
К2 – коэффициент учитывающий долю погрешности обработки в суммарной погрешности вызываемая факторами независящими от приспособления 06-08;
- экономическая точность обработки точность затрат для обеспечения которой для данного способа обработки будут меньше чем при других 016.
Допуск на заданный диаметр 11H9+0.043составляет 0043 мм т.е. выполняется требование
Описание конструкции и работы спроектированного приспособления.
Приспособление применяется для сверления 4-х отверстий диаметром 11 мм. Приспособление состоит из основания 1-270*160*25 которое центрируется двумя шпонками 6 с винтами 7 в котором установлен центрирующий палец2- крепится двумя винтами 5- М8*20 в палец установлена шпонка 3-8*65*15 закреплена винтом 4–М4*8. Заготовка устанавливается на палец и прижимается шайбой 8 - затем заготовка зажимается гайкой 9 –М16*24.
Горохов В.А. Проектирование и расчет приспособлений: Учеб. пособие для студентов вузов машиностроительных спец.- Мн.: Высшая школа 1986.- 238.: ил.
Горошкин А.К. Приспособления для металлорежущих станков: Справочник. – 7-е изд. переработан и доп. – М.: Машиностроение 1979. – 303 с. ил.
Справочник технолога-машиностроителя т.2 под редакцией А.Г.Косиловой и Р.К.Мещерякова . – М.: Машиностроение 1985. – 496 с. ил.
Конспект лекций по курсу: «проектирование приспособлений».
Адеев Р.В. Методические указания для выполнения курсовой работы по дисциплине: «проектирование приспособлений». – Сев.: СевНТУ 2004. – 21 с.
Горбацевич А.Ф. Шкред В.А. Курсовое проектирование по технологии машиностроения. – 4-е издание перераб. и доп. – Мн.: Выш. Школа 1983.- 256 с. ил.
Иванов М.Н. Детали машин. - М.: Высшая школа 1991. – 383 с. ил.
Справочник технолога-машиностроителя т.1 под редакцией А.Г.Косиловой и Р.К.Мещерякова. – М.: Машиностроение 1985.
.прис .spw

Чертеж Присп норм А-2-9 ремонт99.cdw

Усилие зажима W=3689 Н
Применять ключ с длиной рукоятки L= 120 мм не менее
*Размер для справок.
Технические требования.
Перед сборкой проверить сопрягаемые детали
Трущиеся поверхности смазать маслом индустриальным 30
Проверить плотность затяжки крепления деталей.
Проверить отклонения плоскости
Проверить отсутствие в узлах приспособления посторонних пред-
Рекомендуемые чертежи
Свободное скачивание на сегодня
Обновление через: 52 минуты