Автоматизированная установка вихретокового контроля детали типа вал




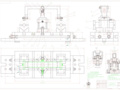
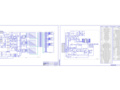
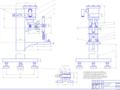
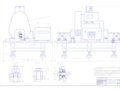
- Добавлен: 24.01.2023
- Размер: 3 MB
- Закачек: 0
Описание
Состав проекта
![]() |
![]() |
![]() |
![]() ![]() ![]() |
![]() |
![]() ![]() ![]() |
![]() |
![]() ![]() ![]() |
![]() |
![]() ![]() ![]() |
![]() |
![]() ![]() ![]() |
![]() |
![]() ![]() ![]() |
![]() |
![]() ![]() ![]() |
![]() |
![]() ![]() ![]() |
![]() ![]() ![]() |
![]() |
![]() |
![]() ![]() ![]() ![]() |
![]() |
![]() ![]() ![]() ![]() |
![]() |
![]() ![]() ![]() ![]() |
![]() ![]() ![]() ![]() |
![]() |
![]() ![]() ![]() ![]() |
![]() |
![]() ![]() ![]() ![]() |
![]() |
![]() ![]() ![]() ![]() |
![]() |
![]() ![]() ![]() ![]() |
![]() |
![]() ![]() ![]() ![]() |
![]() |
![]() ![]() ![]() |
![]() |
![]() ![]() ![]() ![]() |
![]() ![]() ![]() ![]() |
![]() |
![]() |
![]() |
![]() |
![]() |
![]() |
![]() ![]() ![]() |
![]() |
![]() ![]() ![]() |
![]() |
![]() ![]() ![]() |
![]() |
![]() ![]() ![]() |
![]() ![]() ![]() |
![]() |
![]() ![]() ![]() |
![]() |
![]() ![]() ![]() |
Дополнительная информация
АНОТАЦИЯ.doc
Целесообразность внедрения спроетированной системы подтверждена экономическим расчетом. Разработаны мероприятия по организации и охране труда. Рассмотрены вопросы гражданской обороны.
In the degree project according to the task are resulted: a substantiation of the functional and basic scheme power calculation and design system engineering of quality assurance of the wires differing from known analogues by simplicity and universality.
Еngineering of automated management by a marker ink (paints).The expediency of introduction of system is confirmed by economic calculation.Actions for the organisation and labour safety are developed. Civil defence questions are considered.
ЛИТЕРАТУРА .doc
Анурьев В. И. Справочник технолога-машиностроителя В. И.
Анурьев - в 3-х т. - М. 2001.
Визуализация в CoDeSys. Дополнение к руководству пользователя по программированию ПЛК в CoDeSys v 2.3 – Смоленск: ПК Пролог 2008. – 88 с.
Воскобоев В.Ф. Надежность технических систем и техногенный риск.
Часть 1. Надежность технических систем М.: Альянс 2008 – 200с.
Герасимов В.Г. Неразрушающий контроль качества изделий электромагнитными методами : монография В.Г. Герасимов Ю.Я. Останин А.Д. Покровский [и др.]. - М.: Энергия 1978. - 216 с.: ил.
Гжиров Р.И. Краткий справочник конструктора. Р. И. Гжиров
- Л.: Машиностроение 1984г.
Горохов В.А. Проектирование и расчет приспособлений. В.
А.Горохов - Минск 1986г.
ГОСТ 24.601–1992 Автоматизированные системы стадии создания. – М: ИПК Изд-во стандартов 1992. – 6 с.
ГОСТ 24.003–1992 Автоматизированные системы. Термины и определения. М: ИПК Изд-во стандартов 1992. – 16 с.
ГОСТ Р 27.002-2009 (ГОСТ Р 53480–2009) - "Надежность в технике.
Термины и определения".
Дьяконов В. Круглов В. Математические пакеты расширения MATLAB. Специальный справочник. – СПб.: ПИТЕР 2001. – 480 с.
Клюев В.В. Неразрушающий контроль и диагностика : Справочник В. В Клюев Ф. Р Соснин А.В. Ковалев и др.; Под. ред.В. В. Клюева.2-е изд. испр. и доп. - М.: Машиностроение 2003.656 с.: ил.
Корсаков В.С. Основы конструирования приспособлений. В. С.
Корсаков - в 2-х т. - М.: Машиностроение 1983г.
Краузе В. Конструирование приборов В. Краузе - в 2-х т. -
М.: Машиностроение 1987.
Лахтин Ю. М. Леонтьева В. П. Материаловедение Ю. М.
Лахтин В. П. Леонтьева - М.: Машиностроение 1990
Машиностроение. Энциклопедия.Надежность машин Т. IV-3 : Под общ. ред. В.В. Клюева М.: Машиностроение 2003- 592с.
Надежность электрорадиоизделий.Спаравочник.М.:МО РФ2004
Ненашев А.П. Конструирование РЭС: Учебник для радиотехнических спец. вузов. М.: Высшая школа 1990. 432 с.
Острейковский В. А. Теория надежности М.: Высшая школа 2003 - 463 с.
Половко А. М. Гуров С. В Основы теории надежности. Практикум.
СПб.: БХВ-Петербург2006- 560 с
Практическое пособие по учебному конструированию РЭА В.Т.Белинский В.П.Гондол А.Б.Грозин и др.; Под ред. К.Б.Круковского-Синевича Ю.Л.Мазора.- К: Вища школа 1992. – 494с.; ил.
Руководство пользователя по программированию ПЛК в CoDeSys v 2.3 – Смоленск: ПК Пролог 2008. – 166 с.
Сабинин Ю. А. Основы элетропривода Ю. А. Сабинин - М.:
Госэнергоиздат 1963.
Сабинин Ю. А. Теория элетропривода Ю. А. Сабинин - С.-Пб.:
Энергоатомиздат 1994.
Система реального времени CoDeSys для Windows NT2000XP. Руководство для OEM – Смоленск: ПК Пролог 2006. – 36 с.
Справочник по полупроводниковым диодам транзисторам и интегральным схемам Под ред. Н.Н. Горюнова. – М.: Энергия 1979. – 831 с
Справочник техника-конструктора Я.А. Самохвалов М.Я. Левицкий В.Д. и др. 3-е изд. перераб. и доп. К.: Техника1997 592 с.
Сухоруков В.В. Неразрушающий контроль: в 5 кн. Кн.3. Электромагнитный контроль: Практ. пособие В.Г. Герасимов А.Д. Покровский В.В. Сухоруков; Под ред.В. В. Сухорукова. - М.: Высш. шк. 1992. - 312 с.: ил.
Технические характеристики двухканального дозирующего устройства Гатчина: Конструкторское бюро 2009. – 10 с.
Технические характеристики контроллера универсального «КАСКАД» – Железногорск: Издательство ГХК 2000. – 30 с.
Федотов А.В. Основы теории надежности и технической диагностики
Шишмарев В.Ю.Надежность технических систем М.: Академия 2010 – 304с.
Ямпурин Н. П. Баранова А. В. Основы надежности электронных средств.
М.:Академия 2010-240с.
Яншин А.А. Теоретические основы конструирования технологии и надежности ЭВА: Учеб. пособие для вузов. – М.: Радио и связь 1983.- 312с.
Гузеев В. И. Режимы резания для токарных и сверлильно-фрезерно-расточных станков с числовым программным управлением: : справочник В. И. Гузеев В. А. Батуев И. В. Сурков. – 2-е изд. Под ред. В. И. Гузеева. М: Машиностроение 2007. – 368 с.
Режимы резания на работы выполняемые на шлифовальных и доводочных станках с ручным управлением и полуавтоматах : справочник Д. В. Ардашев [и др.]. – Челябинск: АТОКСО 2007. – 384 с.
Справочник технолога-машиностроителя. В 2-х т. Т. 1 Под ред. А. Г. Косиловой и Р. К. Мещерякова. – 4-е изд. перераб. и доп. – М.: Машиностроение 1986. – 656 с.: ил.
Справочник технолога-машиностроителя. В 2-х т. Т. 2 Под ред. А. Г. Косиловой и Р. К. Мещерякова. – 4-е изд. перераб. и доп. – М.: Машиностроение 1986. – 496 с.: ил.
Общемашиностроительные нормативы времени и режимов резания для нормирования работ выполняемых на универсальных и многоцелевых станках с числовым программным управлением: в 2 т. под общ. ред. С.Ю.Романова – М.: Экономика 1990. – Т.1. - 207с.
Общемашиностроительные нормативы времени и режимов резания для нормирования работ выполняемых на универсальных и многоцелевых станках с числовым программным управлением: в 2 т. под общ. ред. С.Ю.Романова – М.: Экономика 1990. – Т.2. - 472с.
Обработка металлов резаньем : Справочник технолога А.А. Панов [и др.]; под общ. ред. А.А. Панова – М.: Машиностроение 1988. – 736 с.: ил.
Кузнецов Ю. И. Оснастка для станков с ЧПУ : справочник Ю. И. Кузнецов А. Р. Маслов А. Н. Бойков. – 2-е изд. перераб. и доп. – М.: Машиностроение 1990. – 512 с.: ил.
Терликова Т.Ф. Основы конструирования приспособлений: учебное пособие для машиностроительных вузов. Т.Ф. Терликова А.С. Мельников В.И. Баталов. – М.: Машиностроение 1980. – 119с.: ил.
Доклад .doc
В проекте представлена разработка установки для контроля качества изоляции проводов с маркировкой поврежденного места что должно наиболее оптимизировать процесс контроля и обеспечить максимальную точность и надежность процесса контроля. Такой способ контроля позволяет исключить субъективный фактор измерения что значительно увеличило точность и производительность.
В качестве метода контроля мест повреждения изоляции вихретоковый метод
контроля. Данный метод позволяет проводить контроль с необходимой точностью большим КПД возможно применение бесконтактного способ контроля более дешево в обслуживании более компактно в отношении габаритов но более дорого в отношении покупки датчика (данный недостаток перекрывается стоимостью обслуживания альтернативного химического метода контроля).
В проекте используется схема где контролируемый вал :проволокакатанный пруток протягивают через вихретоковый датчик данные о повреждении передаются на счетчик который отправляет сигнал на маркировщик (краскоотметчик).
ЛИСТ 1 ДП (Функциональная схема системы контроля). ЛИСТ 4 ДП (Схема принципиальная).
Вихретоковые датчики – это современные контроллеры работающие по принципу изменения индуктивности электромагнитного поля. Вихретоковые датчики представляют собой систему состоящую из : держателей катушек предназначенных в нашем случае для контроля круглого материала из металлов с подобранные под диаметр направляющими втулки сделанные из диэлектрика(пластика) с несколько меньшим диаметром обеспечивающим защиту для катушки. На точность контроля влияет зазор между объектом контроля и катушкой. В проекте произведен выбор конструкции датчика (катушки) и произведен расчет параметров датчика (катушки) и выбор оптимального зазора исходя и максимально контролируемого диаметра. Кроме того произведен точностной расчет для вихретокового датчика.
Полезный сигнал снимаемый с измерительных обмоток катушки вихретокового датчика поступает на предварительный усилитель платы усиливается и передается на вход платы аналого цифрового преобразователя (АЦП) где преобразуется в 12-ти разрядный цифровой код.
В проекте проведена разработка электронного блока и рассмотрены основные его компонентыпроведен расчет надежности электронного блока узла контроля.ЛИСТ 5 ДП ЛИСТ 6 ДП Счетчик дефектов схема электрическая принципиальная.
По сигналу центрального процессора (ЦП) генератор вырабатывает синусоидальное напряжение которое подается на возбуждающую обмотку ВТП. Под действием электромагнитного поля вихревых токов наведенных в металле в измерительных обмотках преобразователя возникает электродвижущая сила (ЭДС) параметры которой соответствуют состоянию металла. Выходное напряжение ВТП после предварительного усиления подвергается детектированию и поступает на вход усилителя коэффициент усиления которого задается ЦП. Усиленный электрический сигнал фильтруется частотным фильтром и подается на вход аналого-цифрового преобразователя (АЦП). С выхода АЦП цифровой сигнал поступает в ЦП для дальнейшей обработки и отображения на дисплее. Схема электрическая условно разбита на субблоки:
Плата счета А1 ; 2.Плата управления А2; 3. Плата индикации А3;
Плата коммутации и отображения информации.
Плата счета А1 : В плате счета используется микросхема 176ИЕ4 которая представляет собой двоичный счетчик по модулю 10 с дешифратором в 7-сегментный код. Взаимодействие между аналоговой частью системы и цифровой (преобразование информации из аналоговой формы в цифровую и обратно) обеспечивают цифроаналоговые (ЦАП) и аналого-цифровые преобразователи (АЦП).Очень важную роль при аналого-цифровом преобразовании играют компараторы. В плате счета используется два компаратора на микросхеме К521 СА3. Компаратором называют устройство предназначенное для сравнения изменяющегося аналогового входного сигнала с опорным напряжением. При этом в зависимости от того больше входной сигнал опорного или меньше (на доли милливольт) на выходе компаратора должно установиться напряжение «логический нуль» (лог. 0) или «логическая единица» (лог. 1).
Плата управления А2:Построена на базе однокристальныго 8-разрядныго FLASH CMOS микроконтроллер компании Microchip Technology Incorporated
с RISC структуру процессорного ядра- PIC16F628 А. Две логические микросхемы К561ЛА7 которые в своем составе имеют 4 элемента 2И-НЕ.Две логические микросхемы К561ЛН2 которые в своем составе имеют 6 элементов НЕ. Узел триггера собран по классической схеме на логической микросхеме DDI К561ТМ2.Микросхема КР142ЕН5А трехвыводный стабилизатор с фиксированным выходным напряжением 5 .
Узел контроля представлен на ЛИСТЕ 2 ДП (Узел контроля.Общий вид.) Дополнительно для узла контроля произведен выбор материала направляющих роликов в технологической части дипломного проекта и рассмотрена конструкция дополнительных роликовых направляющих в узле датчика контроля при неблагоприятных условиях на линии : провис проволоки и т.п.
Для контроля необходимо протягивать контролируемую проволоку или пруток через датчик для этого необходимо к бабине ЛИСТ 4 ДП (Схема принципиальная)на которую закручивают проверенная проволока или пруток присоединить двигатель с редуктором которые обеспечат плавный ход проволоки и не подвергнут её возможности разрыва. В проекте произведен расчет характеристик и выбор двигателя. Выбран шаговый двигатель ДШИ – 200.
Основным элементом платы индикации является семи сегментный цифровой индикатор АЛС333Акоторой отображает информацию сформированную платой счета А1.
Плата коммутации и отображения информации обеспечивает подключение элементов системы контроля к блоку контроля через розеткигнезда клеммы.А также при наличии брака подается световой и звуковой сигналы
оператору.Световой сигнал обеспечивает светодиодный индикатор АЛ307Б
на лицевой панели блока контроля.Звуковой сигнал подается генератором звука SCO715BLLF SONITRON.
На ЛИСТе 3 ДП представле Узел маркировки .Общий вид.который является частью системы контроля качества и должен обеспечить точную маркировку поврежденного места с минимальными затратами средств и времени.В дипломном проекте решался вопрос управления расходом краски и типом маркировки (точечная или протяженная).Проведено рассмотрение маркерно-дозирующих устройств прерывистого действия и произведена разработка собственной конструкции маркера дозатора. В основе работы разработанного дозатора лежит закон Архимеда: погруженное в жидкость тело вытеснит объем равный объему тела. В зависимости от скорости опускания поршня меняется расход. Поршень приводится в движение посредством шагового двигателя (выбор шагового двигателя произведен в пояснительной записке) которым в свою очередь управляет контроллер. Меняя частоту вращения двигателя изменяется скорость опускания поршня. Плюс данного маркера-дозатора в том что не имеет значение плотность вещества и он прост в конструкции. Для данной конструкции в пояснительной записке разработана функциональная схема автоматизации. и система управления. На основе системы управления в пояснительной записке была разработана структурная схема дозатора маркирующих чернил. Оператор задаёт расход литров в час затем контроллер преобразует этот расход в 32 битный код который отправляется на генератор частоты. Контроллер переводит расход в код по определенным формулам.
(В пояснительной записке произведен выбор промышленно разработанного
контроллерного устройства «Каскад» на базе контроллера PIC 8616 )
Сложность управления состоит в том что расход не всегда соответствует частоте которая задается целым числом а подать на генератор можно только целое число. Поэтому применено программное управление. программа управления вычисляет два соседних кода соответствующих большему и меньшему расходу и поддерживает определенное время один расход затем другой что бы в среднем получался заданный оператором расход.
В пояснительной записке произведено моделирование в приложении Simulink пакета MatLab 6.5 расхода для оценки точности маркерного дозирования. Модель приведена в приложении к пояснительной записке . Разработан алгоритм управления установкой дозирования и маркировки брака вала Алгоритм привенен в приложении к пояснительной записке.
Разработано программное обеспечение для маркера –дозатора Программа написана в программном комплексе CoDeSys v2.3.
Программное обеспечение маркера –дозатора описание его применения и руководство системного программиста привенено в приложении к пояснительной записке. Также приведено в приложение Результаты работы программы при рабочей частоте и результаты работы программы управления при разгоне двигателя.
На ЛИСТЕ 7 приведен Алгоритм проведения контроля :где рассмотрены как операция контроля так и операция маркировки.
В Технологической части Дипломного проекта Разработан маршрут изготовления ролика направляющего являющейся частью системы крепления
вихретокового датчика.Направляю щий ролик технологически представляет собой втулку.
Для которой ; выбраны режимы резания по справочнику и произведен их перерасчет ; выбор станков и приспособлений; расчет технической нормы времени; разработано ТЗ на изготовление специального фрезрного приспособления для того чтобы рационально использовать стангочный парк и экономить межстаночное время. Произведен расчет силы зажима; расчет точности приспособления; разработан Единый Технологический Процесс на изготовление втулки.8 Приспособление для сверления отверстия и фрезерования паза; на Листе 9. представлена Технология обработки детали
В Экономическом разделе ЛИСТ 10.Экономика. проведен расчет себестоимости и цены автоматизированной установки. Кроме того в пояснительной записке представлен раздел Охраны труда и Гражданской обороны.
Данная установка разрабатывалась под контроль детали типа вал с диаметром от 2до 5 мм с возможностью контроля до 20мм. И исходя из данного задания и экономической целесообразности затрат выбран проходной круглый проходной вихретоковый датчик. Возможно модернизация данной установки под валы с диаметром большего размера.
Тогда возможными конструктивными решениями могут быть:
сочетание проходного и сканирующего датчика ;
применение в приборах вращающихся датчиков когда объект контроля перемещается в продольном направлении относительно вращающихся датчиков в результате чего осуществляется сканирование объекта по спиральной линии. Когда датчик проходит над дефектом он регистрирует изменения в распространении вихревых токов. Минимальная длина дефекта который можно уверенно выявить зависит от скорости вращения датчиков и скорости перемещения объекта контроля.
Для валов больших диаметров потребуется маркирование сложных дефектов (протяженных продольно-поперечных) тогда маркер- дозатор должен работать как система многосоплового дозирования.Тогда и система управления дозированием должна быть доработана.
Отдельные недочеты в логике построения расчетно-пояснительной записки.
При построения ПЗ использовалось логика Задагния на ДП.
Использование в качестве вихретокового датчика зарубежного
образца при наличии множества отечественных разработок.
1.Российское Федеральное агентство по техническому регулированию и метрологии требования к техническим характеристикам (диапазон измерения чувствительность нелинейность шум и др.) вихретоковых датчиков не конкретизирует. Существуют только рекомендации по метрологическому обеспечению и методам поверки. Поэтому вихретоковые датчики от различных отечественных производителей зачастую существенно отличаются друг от друга техническими параметрами.
2.У российских производителей преобразователи вихретоковые проходные изготавливаются под конкретное изделие по индивидуальному заказу.Это еще один довод в пользу выбора импортного датчика
Доклад закончен. Спасибо за внимание.
А что нового внесли вы?
Для узла контроля : произведен выбор конструкции датчика (катушки) и произведен расчет параметров датчика (катушки) и выбор оптимального зазора исходя и максимально контролируемого диаметра.
Для узла маркировки : Решен вопрос управления расходом краски и типом маркировки (точечная или протяженная).Разработана собственной конструкции маркера дозатора на основе закона Архимеда.
Разработана Программно-апаратная система управления маркером дозатором на базе универсального контроллера «Каскад».
Зачем усложнять узел маркировки?
Для точечного и протяженного дефекта нужно во первых разное количество красящего вещества; второе: скорость срабатывания узла маркировки естественно должна быть разная.
Справочно :(Ранее для узла маркировки производился лишь расчет узла открытия клапана а вопрос маркерного дозирования вообще не рассматривался.)
Содержание .doc
Конструкторская часть
1.Разработка функциональной и принципиальной схемы
2 Выбор основных элементов конструкции .
3.Выбор элементов конструкции для узла контроля ..
3.1.Выбор вихретокового датчика .. .
3.2.Расчет вихретокового датчика ..
3.3.Выбор электродвигателя и подводящего провода .
3.4.Точностной расчет узла контроля
3.5.Энергетический расчет узла контроля. ..
4.Выбор элементов конструкции для узла маркировки
4.1.Описание возможных конструкторских решений. .
4.2. Обзор маркерно- дозирующих устройств ..
4.4.Разработка маркерно –дозирующего устройства
4.5.Информационная структура объекта управления
4.6. Функциональная схема автоматизации узла маркировки . .
4.7.Система управления узла маркировки. ..
4.8. Структурная схема маркерно-дозирующего устройства ..
5. Выбор элементной базы маркерно-дозирующего устройства .
5.1 Контроллер универсальный «Каскад» .
5.2. Программа управления маркера-дозатора ..
5.3.Автоматические клапаны .
5.4.Расчет элементов конструкции узла маркировки
6.Расчет параметров надежности системы . ..
Технологическая часть
Экономическая часть ..
Охрана труда и техника безопасности ..
Гражданская оборона .
Список использованной литературы .
Приложение 1.Модель маркерно-дозирующего устройства ..
Приложение 2. Алгоритм управления установкой дозирования и маркировки брака детали типа «вал» . .
Приложение 3. Технические характеристики модулей входящих в состав КУ «Каскад»
Приложение 4. Программное обеспечение для маркера –дозатора
Приложение 5. Программное обеспечение маркера –дозатора. Описание при-менения ..
Приложение 6. Руководство системного программиста
Приложение 7. Результаты работы программы при рабочей частоте .
Приложение 8.Результаты работы программы управления при разгоне
Приложение 9.Спецификация к общему виду узла контроля .
Приложение 10.Спецификация к общему виду узла маркировки ..
Приложение 11.Технологическая карта изготовления направляющего ролика
ЗАДАНИЕ.doc
Государственное бюджетное образовательное учреждение
высшего профессионального образования
«Ковровская государственная технологическая академия
имени В.А.Дегтярева»
СТУДЕНТУ Фуфаеву Олегу Константиновичу
Тема проекта « Автоматизированная установка вихретокового контроля детали типа «вал»
Срок сдачи студентом законченного проекта .
Исходные данные к проекту см. техническое задание.
Содержание расчётно-пояснительной записки (перечень подлежащих разработке вопросов)
1Патентные исследования
2Конструкторская часть
2.1.Описание работы установки .
2.2.Разработка функциональной схемы.
2.3.Выбор основных элементов конструкции.
2.4.Выбор исполнительных элементов.
2.5.Выбор датчиковой аппаратуры.
2.6.Расчет элементов конструкции
2.7.Разработка элементов конструкции маркерно-индикаторного устройства.
2.8.Разработка блока управления установкой.
2.8.1.Разработка схемы электрической принципиальной блока управления.
2.8.2.Разработка алгоритма работы управления.
2.9.Расчет надежности.
3.Технологическая часть
3.1.Правила приемки готовых изделий.
3.2.Методика контроля установки
3.3.Требования к условиям обеспечению и проведению испытаний
4.Экономическая часть.
6.Гражданская оборона.
Перечень графического материала (с указанием обязательных чертежей)
1.Функциональная схема системы контроля-1лист.
2. Узел контроля.Общий вид-1лист.
3.Узел маркировки.Общий вид-1лист.
4.Портал контроля.Общий вид –1лист.
5.Счетчик дефектов схема электрическая принципиальная-2листа
6.Алгоритм проведения контроля –1лист
7.Технологический чертеж-2листа
8. Калькуляция себестоимости –1лист
Консультанты по проекту (с указанием относящихся к ним разделов проекта)
Дата выдачи задания .
Задание принял к исполнению .
02.КОНСТРУКТОРСКАЯ ЧАСТЬ.doc
Увеличение выпуска продукции и повышение качества выпускаемых изделий предъявляет особые требования к технологии изготовления продукции и как следствие к процессу контроля изготовления на всех этапах. Для освобождения работника от ручного малоквалифицированного труда а так же для повышения объективности контроля необходимо применение системы автоматического контроля основных параметров продукции. Современный этап научно-технического развития неразрывно связан с ускоренным развитием техники измерений. Одной из объективных особенностей развития современного промышленного производства является увеличение доли затрат всего общественного труда на выполнение различных измерений на всех стадиях создания контроля и эксплуатации изделий составляющих в среднем около 10 % а для наиболее сложных изделий 50 60 % от общих затрат на разработку организацию серийного производства и эксплуатацию изделий.
В дипломном проекте представлена разработка автоматизированной установки для контроля детали типа «вал» с маркировкой поврежденного места что должно наиболее оптимизировать процесс контроля и обеспечить максимальную
точность и надежность процесса контроля. Такой способ контроля позволяет
икслючить субъективный фактор измерения то есть человека что значительно увеличило точность и производительность.
1.Разработка функциональной и принципиальной схемы
Разработка принципиальной схемы.
Разрабатываемый прибор предназначен для увеличения скорости проверки качества детали типа «вал»: контроль прутков стержней труб проволоки.
Конструкция установки состоит из: двигателя который наматывает проверяемую проволоку тем самым протаскивая его через чувствительный элемент.
Задача контроля состоит в обнаружении поверхностные и подповерхностные дефектов в проволоке и прутках.(выявление дефектов типа волосовин в холоднотянутой проволоке или в прутковых заготовках).
В рассматриваемом варианте возможно использовать два принципа обнаружения возможных повреждений и использовать два варианта датчиков: химический вихретоковый. Химический метод состоит из применения электролита (водного раствора сульфата натрия) проверяемая проволока протягивается через раствор а счетчик подсчитывает количество локальных мест на проверяемом проводе с сопротивлением изоляции 250 кОм или менее. Способ дает возможность обнаружения повреждений размеров менее 1 мкм но обладает рядом недостатков: низкое КПД (по сравнению с вихретоковым методом) высокая стоимость обслуживания значительные габариты.
Вихретоковый метод основан на анализе взаимодействия внешнего электромагнитного поля с электромагнитным полем вихревых токов наводимых
возбуждающей катушкой в электропроводящем объекте контроля этим полем то есть вихревые токи могут появляться только в поврежденных местах. Данный метод позволяет проводить контроль с необходимой точностью большим КПД возможно применение бесконтактного способ контроля более дешево в обслуживании более компактно в отношении габаритов но более дорого в
отношении покупки датчика (данный недостаток перекрывается стоимостью обслуживания химического метода). Вихретоковые методы традиционно охватывают полосу частот примерно до 10 МГЦ - с дифференциальными катушками - обычно используются для контроля дефектов поверхности. Полуфабрикаты типа проволоки прутков и труб контролируются на местные дефекты в форме трещин и отверстий с помощью проходных катушек.(Рис.2.1)
Рис. 2.1 Контроль с помощью проходной катушки вихретокового датчика.
В приборах с проходными датчиками контролируемая продукция проходит через индуктивную катушку датчика возбуждаемую переменным током заданной частоты. В результате этого в материале объекта контроля наводятся вихревые токи. Несплошность или дефект вызывают изменения в распространении вихревых токов которые выявляются прибором и демонстрируются пользователю. Используются абсолютные или дифференциальные датчики а также их комбинация. Как правило приборы с проходными датчиками применяются для выявления поверхностных и подповерхностных дефектов в продукции с постоянным сечением в том числе для выявления дефектов сварных швов. Эти дефекты аналогичным образом могут выявляться с помощью накладных или сегментных датчиков зона контроля которых ограничивается частью окружности например зоной сварного шва.
Сегментный датчик реализует метод вихретокового сканирования
Рис.2.2 Сканирование полуфабриката вихретоковым методом.
В дипломном проекте используется схема где контролируемый «вал» протягивают через вихретоковый датчик данные о повреждении передаются на счетчик который отправляет сигнал на маркировщик (краскоотметчик). (Рис.2.3)
Рис.2.3. Структурная схема системы контроля
На рисунке цифрами обозначены:1-Блок контроля ; 2-Принтер распечатки протоколов контроля ; 3-Бабины с проволокой ; 4-Вихретоковый датчик с проходной катушкой; 5-Маркер(краскоотметчик). На рисунке также отображены поддерживающие и центрирующие ролики. Краскоотметчик используется для автоматической маркировки выявленных дефектов материала.
Подобная схема контроля реализована например в дефектоскопе ERIC VI фирмы
Magnetic Analysis Corporation (Рис. 2.4)
Дефектоскоп ERIC VI установленный в линии контроля прутков из нержавеющей стали. На переднем плане показаны датчики механизм транспортировки и катушка для намагничивания. Над дефектоскопом ERIC установлен прибор для сортировки продукции.
Вихретоковые дефектоскопы ERIC VI отображают сигналы контроля и пороговые уровни обеспечивающие регулировку в широких пределах частоты фазы и фильтрации позволяющие легко сохранять и вызывать из памяти неограниченное количество настроек.
Рис. 2.4 Дефектоскоп ERIC VI фирмы Magnetic Analysis Corporation
Предлагаются стандартные датчики от 32 мм до 191 мм различной конфигурации включая квадратные прямоугольные шестигранные и накладные (секторные) катушки. В зависимости от выбора датчика скорость контроля может быть в переделах 03-1 500 ммин. С помощью специальных датчиков можно контролировать объекты с высокой температурой.
Вихретоковые датчики – это современные контроллеры работающие по принципу изменения индуктивности электромагнитного поля. Вихретоковые датчики представляют собой систему состоящую из следующих компонентов:
-держатели датчика в виде катушек предназначены для контроля круглого материала из неферромагнитных металлов с подобранные под диаметр направляющими втулки сделанные из диэлектрика(пластика) с несколько меньшим диаметром обеспечивают защиту для катушки;
-удлинительный кабель ;
-электронный драйвер который генерирует магнитное поле и фиксирует необходимые показатели .
При неблагоприятных условиях на линии : провис проволоки прутка и т.п. возможно применение дополнительных роликовых направляющих в узле датчика контроля.(Рис.2.5)
Рис.2.5. Держатель датчиков с роликовыми направляющими
Драйвер (от английского driver в данном контексте — возбудитель колебаний выходной формирователь и т. п.) вихретокового преобразователя представляет собой электронный блок который вырабатывает сигнал возбуждения пробника и осуществляет выделение информативного параметра.
Вихретоковый преобразователь проходного типа
Вихретоковые датчики можно использовать автономно но чаще всего эти приборы являются компонентами систем контроля (Рис.2.6).
Рис.2.6 Структурная схема вихретоковый дефектоскопа построенного на базе промышленного компьютера.
На рисунке 2.6 ВТП- вихретоковый преобразователь проходного типа.
Плата формирователя импульсов ( рис.2.6) обеспечивает питание возбуждающей обмотки ВТП импульсами напряжения необходимой формы и амплитуды. Полезный сигнал снимаемый с измерительных обмоток ВТП поступает на предварительный усилитель платы усиливается и передается на вход платы АЦП где преобразуется в 12-ти разрядный цифровой код.
Результирующее поле зависит от электромагнитных свойств контролируемого объекта и расстояния между преобразователем и объектом (от зазора) поскольку распределение плотности вихревых токов зависит от этих факторов. В измерительной обмотке наводится эдс определяемая потокосцеплением. Эта эдс служит сигналом передающим информацию об объекте в блок измерения.ЭДС преобразователя зависит от многих параметров объектов контроля т.е. его информация многопараметровая. Это определяет преимущества и трудности реализации метода вихревых токов (МВТ). С одной стороны МВТ позволяет осуществлять многопараметровый контроль с другой - требуются специальные приёмы для разделения информации об отдельных параметрах объекта. При контроле одного из параметров влияние остальных на сигнал преобразователя становится мешающим и это влияние необходимо уменьшать.Другая особенность электромагнитного контроля состоит в том что его можно проводить без контакта преобразователя и объекта. Их взаимодействие происходит обычно на расстояниях небольших но достаточных для свободного движения преобразователя относительно объекта (от долей миллиметра до нескольких миллиметров). Поэтому этим методом можно получать хорошие результаты при высоких скоростях движения объектов контроля.Одна из особенностей МВТ состоит в том что на сигналы практически не влияет влажность давление и загрязнённость газовой среды радиоактивные излучения загрязнённость поверхности объекта контроля непроводящими веществами.
Автоматизированная установка вихретокового контроля детали типа «вал»
состоит из двух основных узлов: из стола контроля и стола маркировки. Для проектируемой системы установлен диапазон диаметра контролируемого проволоки от 2 до 5 мм и минимального размера дефекта от 1 мкм необходимо так же использовать систему не только для контроля проволоки и прутков данного диаметра но и для контроля качества поверхности труб диаметром до 20 мм проволоки и катанных прутков диа метром до 20 мм. Так система становиться универсальной то для обеспечения центрирования и поддержки контролируемого объекта в системе используется консольные ролики которые возможно быстро сменить при возникновении такой необходимости и которые эффективно выполняют предъявляемые к ним требования. Весь блок контроля установлен на столе с изменяющимся уровнем пола то есть на каждой из трех ножек установлена система регулирования позволяющая выровнять столешницу в устойчивое положение что важно при использовании направляющих роликов. Так же в блоке используется счетчик как элемент подсчета числа дефектов а так же как связующее звено с блоком маркировки так как при появлении дефекта происходит отправка сигнала включения на маркировщик.
2 Выбор основных элементов конструкции
Выбор элементов конструкции для узла контроля. Конструктивно разрабатываемая установка состоит из двух столов стол контроля и стол маркировки (позиция 5 и 8 Листа 5 ДП) со столешницей с закреплёнными на них приводом датчиком (позиция 4 Листа 5 ДП) счётчиком числа повреждений маркировщиком (позиция 6 Листа 5 ДП) роликами для поддержки и центрирования провода и стойкой. На стойке закреплены направляющий и натяжной ролики (позиция 2 Листа 5 ДП). Катушка для проверенной проволоки устанавливается на выходном конце привода и поджимается гайкой (позиция 7 Листа 5 ДП). Такой вид конструкции обеспечивает экономию места и простоту контроля а так же дает возможность видоизменять установку в любом месте всего процесса контроля.
Выбрав определенный вариант конструкции необходимо подобрать элементы которые составят единую композицию системы.
3.Выбор элементов конструкции для узла контроля
3.1.Выбор вихретокового датчика
Для контроля необходимо подобрать соответствующий датчик .На мировом рынке существует несколько производителей вихретоковых датчиков: американская корпорация Bent американская Metri шведская SKF датская Bruel & Kjaerнемецкая Foerster.
Российское Федеральное агентство по техническому регулированию и метрологии требования к техническим характеристикам (диапазон измерения чувствительность нелинейность шум и др.) вихретоковых датчиков не конкретизирует. Существуют только рекомендации по метрологическому обеспечению и методам поверки. Поэтому вихретоковые датчики от различных отечественных производителей зачастую существенно отличаются друг от друга техническими параметрами. Если же конечным продуктом является собственно вихретоковый датчик его технические характеристики должны быть стандартизованы.Поэтому выбор производится из импортных датчиков производство которых ориентировано на американский стандарт API 670 который практически стал международным. В зависимости от расположения ВТП по отношению к объекту контроля (ОК) их делят на проходные накладные и комбинированные.По способу соединения катушек (обмоток) различают абсолютные и дифференциальные ВТП. Абсолютным называют ВТП (рис.2.7 а) выходной сигнал которого определяется абсолютными значениями параметров ОК в зоне контроля. Дифференциальным ВТП принято называть по существу совокупность двух ВТП обмотки которых соединены таким образом (рис.2.7 б) что выходной сигнал определяется разностью параметров ОК соответствующих зон контроля.
Рис. 2.7. Абсолютный (а) и дифференциальный (б) параметрический ВТП: 1 - возбуждающие обмотки; 2 - объект контроля
Рис.2.8 Датчик Foerster –LMD 2.91.30
Вихретоковые датчики Таблица 2.1
Диапазон измерения 2-10мм
Габариты 120х116х 92
Диапазон измерения 2-4мм
Габариты 100х1006х80
Диапазон измерения 2-20мм
Foerster –LMD 2.91.30
Диапазон измерения 12-44мм
Просмотрев различные варианты датчиков от разных производителей можно сказать что наиболее подходящими характеристиками обладает вариант под номером 4 обладающий наилучшим диапазоном измерения средними габаритами и стоимостью.
В отличие от анологичных датчиков где элемент катушки составляет единое целое с кожухом и заполнен составом из смолы для герметизации датчик имеет модульную конструкцию. (Рис.2.8)
Датчик ремонтопригоден . Производитель предоставляет необходимые части для ремонта: элемент катушки ;центрирующие диски разъем.
Выбран проходной круглый дифференциальный ВТП.
У российских производителей преобразователи вихретоковые проходные изготавливаются под конкретное изделие по индивидуальному заказу.Это еще один довод в пользу выбора импортного датчика.
Рис.2.9.Проверка дефектов изоляции проходной катушкой.
Трещина прерывает распространение вихревых токов в материале контроля и соответствующий сигнал дефекта выдается катушкой.
3.2.Расчет вихретокового датчика
Расчет проведен по методике изложенной в источнике [4].
Рассчитаем радиус возбуждающей катушки. По техническому заданию максимальный диаметр зоны контроля 20 мм
где - диаметр зоны контроля - диаметр возбуждающей катушки. Подставляя значения в (1) получим
где rкат - толщина катушки Lкат - длина катушки Dкат - диаметр катушки D - диаметр трубы h - зазор T - толщина покрытия T = (1. .2) мм d - толщина стенки трубы d = 1 мм t - толщина протектора.
Каркасы катушек изготавливают из изоляционных материалов (капролон гетинакс оргстекло эбонит и др.) . Диаметр проводов обмоток возбуждения от 0.01 до 0.3 мм. [4].Из этого условия выберем диаметр провода возбуждающей катушки dпр равным 02 мм.
Рис.2.10. Схема расчетная вихретокового датчика
Количество витков в одном слое возбуждающей обмотки определяется по формуле: (2.2);
где Lкат - длина катушки dпр - диаметр провода обмотки.
Находим высоту возбуждающей катушки
В нашем случае толщину катушки r можно выбрать равной длине то есть мм. (2.4)
Подставляя (2.3) в (2.2) находим количество витков в одном слое возбуждающей катушке
Исходя из (2.4) находим число слоев в катушке
Получаем катушку из пяти слоев в каждом слое пять витков т.е. всего витков в возбуждающей обмотке:
Находим длину и площадь провода соответственно по формулам
Исходя из полученных геометрических параметров катушки выбираем толщину протектора равной t2 = 05 мм.
Подставляя полученные значения найдем значение обобщенного зазора по формуле:
Получаем h = (2. .3) мм.
Рассчитаем относительные значения зазоров по формуле:
Получаем h = (0.4 0.5 0.6).
При контроле зазора параметр выбирается >20 то есть выбирают высокую рабочую частоту.
Значение обобщенного параметра контроля .
Рабочую частоту fраб рассчитаем из формулы для нахождения обобщенного параметра контроля
где b - обобщенный параметр
Rкат - радиус возбуждающей катушки м
- круговая частота радс
а = 0m - относительная магнитная проницаемость m = 1;
m0 -магнитная постоянная 0 = 4p10-7 Гнм.
В тоже время при граничная частота равна Гц.
В зависимости от заданного диапазона температуры Т = 0. .40 ºС определим диапазон изменения УЭП. Изменение температуры ΔТ = ±20 ºС.
= ΔТ = 200428% = 856%
где α - температурный коэффициент удельного сопротивления для меди он равен α = 42810-3 1 ºС.
Δ = = 580856 = 49648 МСмм.
Получили диапазон изменения
УЭП ±Δ = (58±5) МСмм т.е.
при Т = 0 ºС = 63106 Смм
при Т = 20 ºС = 58106 Смм
при Т = 40 ºС = 53106 Смм.
Ток протекающий по возбуждающей катушке Imax А вычислим по формуле
где j - плотность тока в медном проводнике для многослойной катушки плотность тока j= (3. .4) берем j = 4 А; Sпр - площадь поперечного сечения провода.
Напряженность магнитного поля внутри возбуждающей катушки :
Рассчитаем индуктивность L0 Гн катушек:
где W - число витков катушки Dкат - ее диаметр - величина значения которой даны в таблице [4 стр.248] в зависимости от отношения
Сопротивление катушки R0 Ом:
где s - удельная электрическая проводимость основания МСмм.
Найдем комплексное сопротивление:
Определим напряжение холостого хода Uxx В на ВТП без ОК:
мВ - падение напряжение на ВТП.
Добавочное сопротивление Rд выбираем приблизительно в 10 раз меньше z0 Rд = 50 мОм также задаем С1 = 100 мкФ чтобы емкостное сопротивление было маленьким.
3.3 Выбор электродвигателя и подводящего провода
Для контроля необходимо протягивать контролируемый «вал» через датчик для этого необходимо к бабине на которую закручивают проверенную проволоку присоединить двигатель с редуктором которые обеспечат плавный ход проволоки и не подвергнут его возможности разрыва. Так как установка может контролировать проволоку с диаметром сечения от 2 до 5 мм то необходимо подобрать провод который наиболее подойдет по мощности для этого зададимся номинальной и максимальной массой контролируемого провода:
Мmin = 20 кг = 200 Н - для провода диаметром d = 2 мм
Мmax = 50 кг = 500 Н - для провода диаметром d = 5 мм.
Угловая скорость вращения двигателя = 110 угл.мин. = 680 обмин
(по техническому заданию).
Pmin = Mmin = 200 680 2 3.1460 = 1453.5 Вт
Pmax = Mmax = 500 680 2 3.1460 = 3558.6 Вт
Минимально возможная мощность двигателя составила Pmin =
кВт а максимально возможная Pmax = 36 кВт. Проверим
правильность определения мощности двигателя для этого определим максимальное и минимальное натяжение провода и сравним с табличным значением максимальной нагрузки медных проводов для соответствующих сечений:
min = Mmin S где S - площадь сечения провода
Smin = D2 4 = 3.14 10-6 4 = 3.14 10-6 м2
Smax = D2 4 = 3.14 2510-6 4 = 19.625 10-6 м2
min = 200 3.14 10-6 = 6.4 10-6 Н м2
справочное 1 = 8.1 10-6 Н м2
max = Mmax S = 500 19.625 10-6 = 2.55 10-6 Н м2
справочное 2 = 8.8 10-6 Н м2
Таким образом можно сделать вывод что выбор двигателя по мощности произведен правильно так как min справочное 1 а max справочное 2 [1].
Для данной установки наиболее благоприятно применить шаговый двигатель который не даст проволоке возможности оборваться так как протягивает её небольшими прерывистыми порциями а так же благоприятно для используемого датчика давая возможность точечной проверки .
Шаговые двигатели (ШД) применяются в качестве исполнительных элементов в системах с дискретным приводом. Частота вращения и суммарный угол поворота вала ШД пропорциональны соответственно частоте и числу поданных импульсов управления. При отсутствии управляющих импульсов ШД находится в режиме фиксированной стоянки и сохраняет конечные результаты предыдущих перемещений. Привод с ШД сочетает возможности глубокого регулирования частоты вращения с возможностью числового задания и надежной фиксации конечных координат. Для питания ШД применяются специальные блоки управления которые обеспечивают преобразование унитарной последовательности импульсов в m- разную систему напряжений питающих обмотки ШД через усилители мощности. Параметры блока управления определяются числом и порядном коммуникации обмоток ШД. Технический уровень блока управления определяется в основном примененной в них элементной базой.
Напряжение питания ШД задается на входе блока управления. Но минимальный момент ШД составляет обычно (0405)Мст мах. Номинальный момент инерции нагрузки выбирается обычно в пределах Jн=(12)Jр. Такое соотношение моментов инерции нагрузки и ротора позволяет наиболее полно использовать динамические качества ШД и обеспечить устойчивость его работы. Разрешающая способность ШД по углу определяется статической и динамической погрешностями которые характеризуют точность отработки шага. Основными характеристиками ШД являются предельная динамическая и предельная механическая характеристики. Рассмотрим два варианта двигателей: IM 1001 - Р = 3.7 кВТ и ДШИ - 200 Р = 4 кВт. Оба двигателя представлены в минимальном размерном исполнении но во избежании возможных колебаний массы протягиваемого провода которая может зависеть от массы различных факторов как природных так и человеческих выбираем двигатель ДШИ - 200 имеющий большее значение мощности что возможно при наличии значительного запаса по нагрузке натяжения провода[1].
3.4.Разработка схемы электронного блока
Структурная схема электронного блока приведена на рисунке 2.11.
По сигналу центрального процессора (ЦП) генератор вырабатывает синусоидальное напряжение которое подается на возбуждающую обмотку ВТП. Под действием электромагнитного поля вихревых токов наведенных в металле в измерительных обмотках преобразователя возникает электродвижущая сила (ЭДС) параметры которой соответствуют состоянию металла. Выходное напряжение ВТП после предварительного усиления подвергается детектированию и поступает на вход усилителя коэффициент усиления которого задается ЦП. Усиленный электрический сигнал фильтруется частотным фильтром и подается на вход аналого-цифрового преобразователя (АЦП). С выхода АЦП цифровой сигнал поступает в ЦП для дальнейшей обработки и отображения на дисплее
Рис.2.11 Структурная схема электронного блока
Схема электрическая условно разбита на субблоки:
Плата счета А1 ; 2.Плата управления А2; 3. Плата индикации А3;
Плата коммутации и отображения информации.
Плата коммутации и отображения информации
Плата коммутации и отображения информации обеспечивает подключение элементов системы контроля к блоку контроля через розеткигнезда клеммы.А также при наличии брака изоляции провода подается световой и звуковой сигналы
оператору.Световой сигнал обеспечивает светодиодный индикатор АЛ307Б
на лицевой панели блока контроля.Звуковой сигнал подается генератором звука SCO715BLLF SONITRON.
Плата счета А1 построена на базе операционного дифференциального усилителя
К544УД1 с высоким входным сопротивлением и низким уровнем входных токов с внутренней частотной коррекцией обеспечивающей устойчивую работу при любых режимах отрицательной обратной связи включая режимы интеграторов и повторителей напряжения. . Малые значения шумового тока и хорошие спектральные характеристики напряжения шума высокие динамические параметры дают преимущества при использовании их в качестве схем выборки и хранения.
В плате счета используется два компаратора на микросхеме К521 СА3
Взаимодействие между аналоговой частью системы и цифровой (преобразование информации из аналоговой формы в цифровую и обратно) обеспечивают цифроаналоговые (ЦАП) и аналого-цифровые преобразователи (АЦП).
Очень важную роль при аналого-цифровом преобразовании играют компараторы. Компаратором называют устройство предназначенное для сравнения изменяющегося аналогового входного сигнала с опорным напряжением. При этом в зависимости от того больше входной сигнал опорного или меньше (на доли милливольт) на выходе компаратора должно установиться напряжение «логический нуль» (лог. 0) или «логическая единица» (лог. 1).
В плате счета используется микросхема 176ИЕ4 (Рис.2.12)которая представляет собой двоичный счетчик по модулю 10 с дешифратором в 7-сегментный код.
Исходное состояние схемы устанавливается подачей сигнала H на вход Cl (5)Входная частота подается на вход Ck (4) а выходная частота (в 10 раз меньше) появляется на выводе Y10 (2) После каждого второго входного импульса на выводе Y4 (3) формируется сигнал который используется для выработки команды сброс в разрядах индикатора "Часы". В случаях использования жидкокристаллических индикаторов в схеме предусмотрено получение на выходе прямого и инверсного кода (относительно входа Ck) путем подачи на вывод 6 (M) сигнала с частотой 32 или 64 Гц. При применении индикаторов не требующих знакопеременного питающего напряжения на вывод M подается постоянное напряжение L
Рис. 2.12 Микросхема 176ИЕ4
Построена на следующих основных элементах:
PIC16F628 А однокристальный 8-разрядный FLASH CMOS микроконтроллер компании Microchip Technology Incorporated. Все микроконтроллеры PIC1617 используют RISC структуру процессорного ядра. Семейство микроконтроллеров PIC1617 имеет расширенные возможности ядра стек глубиной восемь уровней и множество внутренних и внешних прерываний. Гарвардская архитектура с отдельными шинами команд и данных позволяет одновременно передавать 14 разрядные команды и 8 разрядные данные. Двух командный конвейер позволяет выполнять все команды за один машинный цикл кроме команд ветвления программы которые выполняются за два цикла. Уменьшенная система команд (всего 35 команд). Высокая эффективность достигается использованием новшеств архитектуры и большого набора дополнительных регистров.
Микроконтроллеры семейства PIC16 по сравнению с другими 8 разрядными микроконтроллерами такого же класса позволяют уменьшить программу 2:1 и увеличить быстродействие 4:1.Две логические микросхемы К561ЛА7 которые в своем составе имеют 4 элемента 2И-НЕ.Две логические микросхемы К561ЛН2 которые в своем составе имеют 6 элементов НЕ. Узел триггера собран по классической схеме на логической микросхеме DDI К561ТМ2.Микросхема КР142ЕН5А трехвыводный стабилизатор с фиксированным выходным напряжением 5 вольт могут найти применение в широком спектре радиоэлектронных устройств в качестве источниках питания логических систем измерительной технике. Компоненты могут быть использованны для ускорения переходных процессов. Входной конденсатор необходим только в том случае если регулятор находиться на растоянии более 5 см от фильтрующего конденсатора источника питания.
Основным элементом платы индикации является семи сегментный цифровой индикатор АЛС333Акоторой отображает информацию сформированную платой счета А1.
3.5.Точностной расчет узла контроля
Точностной анализ проектируемой системы основан на определении возможных погрешностей при определении дефектов.
Рассмотрим каждый дефект в отдельности: – расстояние между контролируемым объектом и контролируемыми обкладками. В проектируемой системе данное расстояние не изменяется так как контролируемый датчик имеет две вращающиеся контрольные обкладки которые не дают возможности возникновения данной погрешности. - диаметр контролируемого «вала» и его возможное отклонение. По стандарту изготовления проволоки диаметром от 2 до 5 мм оклонение внешнего диаметра составит от 50 до 100 мкм. - проводимость среды в рассматриваемом случае воздуха. Данное значение составляет 1 000038 и может изменяться в зависимости от условий внешней среды от 0999937 до 10034.
- частота питающей сети и её изменение. По стандарту РФ данное значение составляет 50 2 Гц. – значение энергии излучаемой контролируемой обкладкой и её изменение. Данное значение определяется по закону Ома:
где U - напряжение питающей сети; I - сила тока. По стандарту откланение обоих значений составляет не более 5 % соответственно откланение значения энергии Е составит не более 5%[24].
3.6 Энергетический расчет
Каждый элемент проектируемой системы требует определенных
затрат электроэнергии которые рассчитываются по формуле:
ЗЭ = Мx Кx Тx Ц (2.18)
где ЗЭ - затраты на электроэнергию;
М - паспортная мощность кВт;
К - коэффициент использования мощности (07-09);
Т - время работы прибора час.;
Ц - цена 1 кВтчас. электроэнергии Ц = 232 руб.
Затраты на электроэнергию для проектируемой системы
приведены в таблице 2.2:
То есть за восьми часовую смену система контроли качествам изоляции проводов потребит электроэнергии на 23386 рублей.
4.Выбор элементов конструкции для узла маркировки
4.1.Описание возможных конструкторских решений
Проектируемая система маркировки является частью системы контроля качества изоляции проводов и должна обеспечить точную маркировку поврежденного места провода с минимальными затратами средств и времени.
Конструктивное решение №1.
На двигатель приходит сигнал включения при появлении дефекта изоляции провода. Двигатель раскручиваетролик или ролики (в различных модификациях используют два ролика для двусторонней окраски провода). На ролике нанесено специальное покрытие для равномерного распределения красещего фермента который поступает из дозирующей установки после начала раскрутки красящего ролика. Данная схема имеет ряд существенных недостатков: сложность системы маркеровки требующей значительных габаритных затрат; дороговизна осуществления системы; появление сил трения при отсутствии сигнала питания на двигателе данный
недостаток может вызвать дефект изоляции провода после проверки а так же быстрый износ ролика.
Конструктивное решение №2.
Конструктивное решение представляет собой механическую систему маркеровки. Сигнал включения поступает на электромагнит который
примагничевает крепление "качели" которые удерживают маркер предназначенный для отметки места повреждения изоляции провода. Противовесом в данной системе является пружина предназначенная для удержания крепления во время отсутствия сигнала о дефекте. Данный вариант схемы не является наиболее простыма сточки зрения надежности является самым ненадежным вариантом решения с точки зрения ремонта[12].
Конструктивное решение №3.
Сигнал питания подается на насоскоторый перекачивает красящий фермент из резервуара в дозирующую установку которая дозирует подаваемую краску. Такой вариант схемы изрядно упрощает систему
маркировки но требует наиболее точного расположения
маркирующего устройства та как маркеровка ведется точечным путем.
Необходимо решить вопрос управления расходом краски и шириной
4.2. Обзор маркерно- дозирующих устройств
4.2.1.Маркерно-дозирующие устройства прерывистого действия
Наибольшее распространение нашли следующие дозирующие устройства: поршневые переливные контактные отсечные мембранные и дроссельные. В качестве дозирующих устройств применяют поршневые мембранные плунжерные перистальтические и некоторые другие насосы с постоянной или переменной производительностью а также различного вида дроссельные устройства.
В дипломном проекте рассмотрены маркерно-дозирующие устройства в которых возможно применить максимальную степень автоматизации процесса дозирования.
4.2.2.Мембранные дозирующие устройства.
Рис.2.13 Поворотно-мембранное устройство.
В корпусе устройства расположены два одинаковых поворотных распределительных хлапана 2 и 3 приводимых в действие синхронными электродвигателями. Левый и правый клапаны соединены системами каналов соответствено с левой и правой половинами чечевицеобразной погости а также со входным 4 и 5 и сливными б и 7 штуцерами. Дозирующее устройство работает следующим образом о том положении распределительных клапанов которое показано на рис. 1 жидкость под напором поступает через штуцер 4 в левую половину чечевицеобразной полости при этом мембрана выталкивает Жидкость из правой половины полости через штуцер 7. После одновременного поворота распределительных Клапанов на 180° жидкость поступает через штуцер 5 в правую половину чечевицеобразной полости а мембрана выдавливает жидкость из левой полости через штуцер 6.
4.2.3.Дроссельные дозирующие устройства
Среди дроссельных дозирующих устройств нашли наибольшее распространение устройства со стабилизируемым напором столба жидкости. Стабилизация напора столба жидкости осуществляется либо с помощью поплавкового регулятора уровня либо с помощью сосуда Мариотта.
Рис.2 .14 Дроссельное дозирующее устройство со стабилизацией
Существенной частью устройств является капилляр Л создающий дросселирование потока жидкости. При постоянстве напора столба жидкости Н поддерживаемого поплавковым регулятором 2 или сосудом Мариотта 3 и неизменной вязкости жидкости ее расход за время определяемое временем открытия электромагнитного клапана 4 будет постоянным. Так как вязкость жидкости протекающей через капилляр меняется с температурой точность подобных устройств невелика около 4—5% однако точность может быть значительно улучшена при термостатированни жидкости протекающей через капилляр.
Рис.2.15. – Структурная схема одного канала дозирующего устройства
4.2.4.Двухканальное дозирующее устройство переливного типа
Двухканальное дозирующее устройство состоит из двух идентичных каналов. Структурная схема канала показана на рисунке 2.15.
Канал дозирующего устройства включает в себя:
– расходную емкость;
– тензометрический датчик веса емкости;
– электромагнитный клапан для раствора;
– электромагнитный клапан для воздуха;
– линии растворов и монтажные элементы;
– датчик температуры (общий для двух каналов).
Устройством осуществляется порционное дозирование раствора из весовой емкости которая с помощью тяги подвешена на тензометрическом датчике. Полиэтиленовые линии для раствора и воздуха соединяющие весовую емкость с монтажными элементами выполнены в виде пружинящих спиралей и практически не влияют на результаты измерений веса емкости. В зависимости от величины заданного расхода и измеренного веса емкости по командам контроллера периодически открывается электромагнитный клапан для раствора
и в аппарат поступает очередная порция раствора. Когда количество раствора в весовой емкости станет меньше заданного нижнего предела откроется электромагнитный клапан для воздуха в расходной емкости будет создано избыточное давление и раствор начнет поступать из расходной в весовую емкость. После того как количество раствора в весовой емкости увеличится до заданного верхнего предела электромагнитный клапан для воздуха выключится давление воздуха в расходной емкости сравняется со сдувкой раствор перестанет поступать в весовую емкость.
Главная проблема данного дозатора в том что чувствительным элементом являются тензометрические датчики которые очень чувствительны к вибрациям. А в цеху где большая вибрация эти датчики дают большую погрешность и быстро выходят из строя. Поэтому данный тип дозатора не может применяться по техническому заданию.
4.2.5. Пневматический маркер-дозатор
Фирма Foerster применяет для автоматической маркировки дефектов выявленных неразрушающим контролем материала пневматический маркер-дозатор (краскоотметчик) . Первоначально с помощью разрежения создаваемого регулятором либо другим способом заполняется расходная емкость. Контроль заполнения ведется по дискретному уровнемеру . Величина разрежения не может превышать по абсолютной величине давления создаваемого столбом чернил (краски) в гидрозатворе. Передача раствора из расходной емкости в измерительную емкость производится при избыточном давление в расходной емкости. Избыточное давление должно превышать по величине сумму давления в принимающей измерительной емкости и давления. Дозирование раствора заключается в поочередных выдаче и приеме раствора измерительными емкостями. Попеременная выдача раствора из измерительных емкостей происходит за счет линейного нарастания давления в дозирующей емкости. Скорость нарастания рассчитывается системой управления исходя из плотности раствора заданного расхода и площади основания измерительной емкости. Линейное изменение давления до заданной величины осуществляется контроллером регуляторов автономно только по первоначальной команде пульта оператора определяющей направление и конечное значение давления – разрежения. После окончания дозирования из очередной емкости давление в ней снижается плавно чтобы минимизировать возмущения вносимые в давление газовой фазы второй емкости. Для данного дозатора необходимо точно знать плотность раствора а измерять ее постоянно затруднительно. Он является одноканальной версией и позволяет маркировать дефекты одним цветом. Если вы хотите различать разные типы дефектов (например продольные и поперечные дефекты внешние и внутренние дефекты дефекты различных размеров) придется использовать комбинацию нескольких краскоотметчиков и заправить их различной краской. У данного дозатора сложная конструкция и высокая цена а так как по техническому заданию дозатор не подлежит ремонту и восстановлению то его применение экономически не выгодно.
4.3.Разработка маркерно –дозирующего устройства
Схема дозатора представлена на рисунке 2.16 .За прототип данной конструкции был взят поршневой дозатор постоянного давления .Недостатком его является непрерывность дозирования и необходимость регулирования постоянного давления в зависимости от плотности и расхода применяемых маркирующих чернил. В основе работы разработанного дозатора лежит закон Архимеда: погруженное в жидкость тело вытеснит объем равный объему тела. В зависимости от скорости опускания поршня меняется расход. Поршень приводится в движение посредством шагового двигателя (далее – ШД) которым в свою очередь управляет контроллер. Меняя частоту вращения двигателя изменяется скорость опускания поршня. Плюс данного дозатора в том что не имеет значение плотность вещества и прост в конструкции.
Рис. 2.16 – Поршневой маркер-дозатороснованный на законе Архимеда
4.4.Информационная структура объекта управления
На рисунке 2.17 представлена информационная структура маркера как объекта управления
Рис. 2.17 – Схема информационной структуры маркера как объекта управления
Информационная структура представляет собой объект управления с входными и выходными сигналами. На ОУ поступают три дискретных сигнала: DIH – сигнал ограничителя верхнего уровня хода штока; DIL – ограничитель нижнего уровня хода штока; DIU – уровень чернил в дозирующем устройстве; и один аналоговый сигнал: AIT – температура чернил в дозирующем устройстве.
На выходе сигнал расхода маркирующих чернил .
4.5. Функциональная схема автоматизации узла маркировки
Рис. 2.18 – Функциональная схема автоматизации узла маркировки
Что бы не заходить за пределы установлены два концевых выключателя верхнего и нижнего положения по сигналам от которых будет останавливаться шаговый двигатель. По сигналу с пульта будет открываться запорный клапан через который в дозирующее устройство будет подаваться чернила. Уровень заполнения дозатора контролируется датчиком уровня. Генерировать необходимую частоту вращения шагового двигателя будет частотный генератор которым будет управлять микроконтроллер.
4.6.Система управления узла маркировки
На рисунке 2.19 представлена блок схема системы управления .
Рис. 2.19 – Блок-схема системы управления
Система управления состоит из трех уровней:
– первый уровень – это персональный компьютер он обрабатывает данные полученные со второго уровня. С помощью PC оператор управляет процессом вводит необходимые константы и переменные задает требуемые границы. Так же он отвечает за архивирование данных вывод соответствующих сигнальных сообщений при возникновении аварийной ситуации;
– второй уровень – это шкаф контроля управления (ШКУ). Он производит сбор и первичную обработку сигналов с датчиков и выдачу информации на PC. По сигналам от оператора ШКУ выдает сигналы на исполнительные механизмы;
– третий уровень – это непосредственно датчики и исполнительные механизмы.
На основе системы управления была разработана структурная схема дозатора маркирующих чернил.
4.8. Структурная схема маркерно-дозирующего устройства
На рисунке 2.20 представлена структурная схема маркернодозирующего устройства.
Рис. 2.20 – Структурная схема маркерно-дозирующего устройства
Оператор задаёт расход литров в час затем контроллер преобразует этот расход в 32 битный код который отправляется на генератор частоты. Необходимость преобразования расхода в код вызвана тем что частотный генератор который управляет скоростью шагового двигателя сделан в программном комплексе MPlab на языке Assembler. Данный генератор формирует частоту в зависимости от кода поданного на вход данный код представляет собой целое число от 1 до 65535 наименьшее значение кода соответствует максимальной частоте равной 35084 Гц. Контроллер переводит расход в код по формулам:
где x – это полученный код.
На рисунке 2.21 представлена диаграмма зависимости кода от расхода.
Рис. 2.21 – Зависимость кода от расхода технологического раствора
В зависимости от этого кода генерируется частота подаваемая на вход драйвера ШД. Драйвер ШД делит входную частоту на 10 и полученная частота подается на ШД который в свою очередь связан с редуктором двигающем поршень. От скорости ввода поршня зависти получаемый расход. Отсюда следует что управлять расходом можно изменяя частоту ШД. Сложность управления состоит в том что расход не всегда соответствует частоте которая задается целым числом а подать на генератор можно только целое число. Поэтому программа управления вычисляет два соседних кода соответствующих большему и меньшему расходу и поддерживает определенное время один расход затем другой что бы в среднем получался заданный оператором расход. В соответствии со структурной схемой и математическим описанием была собрана модель в приложении Simulink пакета MatLab 6.5 . Модель представлена в приложении № 1.
Данные о заданном и полученном расходе приведены в таблице 1
По техническому заданию относительная погрешность не должна превышать 1 %. Из таблицы .1 видно что полученная модель удовлетворяет требованиям технического задания. На рисунке 2.22 представлена диаграмма зависимости расхода от относительной погрешности. Из этой диаграммы видно что погрешность растет с увеличением расхода. Это связано с тем что чем больше заданный расход тем больше частота которую необходимо подать на двигатель.
А на больших частотах у генератора большая дискретность шага следовательно и соседние расходы сильно отличаются поэтому при смешивании увеличивается погрешность. На основе математического описания и собранной модели был разработан алгоритм управления дозатором технологических растворов. Полное описание алгоритма приведено в приложении № 2
Результаты работы модели Таблица 2.3
Заданный расход (лч)
Полученный расход (лч)
Относительная погрешность (%)
Продолжение Таблицы 2.3
Рис. 2.22 – Диаграмма зависимости относительной погрешности от расхода
5. Выбор элементной базы маркерно-дозирующего устройства
На основе алгоритма управления и функциональной схемы были выбраны управляющие элементы. В качестве привода был выбран шаговый двигатель (ШД) FL86STH65–2808A который производит НПФ «Электропривод» .
Шаговые двигатели (ШД) применяются в качестве исполнительных элементов в системах с дискретным приводом. Частота вращения и суммарный угол поворота вала ШД пропорциональны соответственно частоте и числу поданных импульсов управления. При отсутствии управляющих импульсов ШД находится в режиме фиксированной стоянки и сохраняет конечные результаты предыдущих перемещений. Привод с ШД сочетает возможности глубокого регулирования частоты вращения с возможностью числового задания и надежной фиксации конечных координат.
Для питания ШД применяются специальные блоки управления которые обеспечивают преобразование унитарной последовательности импульсов в m- разную систему напряжений питающих обмотки ШД через усилители мощности. Параметры блока управления определяются числом и порядном коммуникации обмоток ШД. Технический уровень блока управления определяется в основном примененной в них элементной базой.
Напряжение питания ШД задается на входе блока управления. Но минимальный момент ШД составляет обычно (0405)Мст мах. Номинальный момент инерции нагрузки выбирается обычно в пределах Jн=(12)Jр. Такое соотношение моментов инерции нагрузки и ротора позволяет наиболее полно использовать динамические качества ШД и обеспечить устойчивость его работы. Разрешающая способность ШД по углу определяется статической и динамической погрешностями которые характеризуют точность отработки шага. Основными характеристиками ШД являются предельная динамическая и предельная механическая характеристики.Данный ШД имеет следующие характеристики:
– сопротивлениефаза – 14 Ом;
– индуктивностьфаза – 39 мГн;
– крутящий момент – 34 кг·см;
– момент инерции ротора – 1000 г·см2;
Рис. 2.23 – Электрическая схема ШД FL86STH65-2808A
Шаговые двигатели этой серии имеют основной угловой шаг 18° частоту приемистости до 2000 Гц и скорость вращения вала до 1500 обмин. Так же к двигателям этой серии идет устройство управления.
В качестве устройства управления был выбран программируемый блок управления ШД SMSD-3.0 . Он предназначен для управления работой четырехфазных либо двухфазных ШД с током фазы 3 A. Блок объединяет в себе управляющий микропроцессор и высококачественный драйвер ШД. Управление осуществляется по заданной программе в ручном режиме или в режиме драйвера. Блок SMSD может работать в режиме целого шага или осуществлять дробление на 12 14 18 116 и 132 блок может задавать направление скорость ускорение движения а также работать по сложным алгоритмам записываемым в энергонезависимую память. Блок работает автономно от компьютера (LPT или COM-порт) или от внешнего задающего контроллера. Блок имеет возможность получать сигналы от внешних устройств и датчиков а также подавать сигналы внешним устройствам. Блок имеет радиатор и не требует дополнительного охлаждения. Этот блок имеет одну особенность – он уменьшает входную частоту в 10 раз.
Основные характеристики блока SMSD-3.0:
–максимальный выходной ток – 3 А;
– напряжение питания – 18-40 В;
– диапазон частот отработки шагов – от 1 до 10000 Гц;
– точность установки скорости – не ниже 02%;
– обмен с ПК – RS232.
В качестве привода который будет двигать поршень дозирующего устройства выбран электромеханизм МП-100М с ходом штока 80 ± 15 мм. Нагрузка на шток: номинальная – 980 Н (100 кгс) максимальная – 1470 Н (150 кгс).
Так как рассмотренные частотные генераторы не позволяют работать в частотах от 200 Гц до 25000 Гц с возможностью подстройки частоты в 1 Гц то генерация частоты будет производиться от программного генератора. Генератор написан в программном пакете MPLAB IDEv 8.10 на языке ассемблер.
Данный генератор генерирует частоту в зависимости от полученного кода код задается с контроллера код – это значение от 1 до 65535 (32 бита). Частота поступает на блок управления ШД он делит ее на 10 и полученную частоту отправляет на ШД. В зависимости от поданного кода мы меняем скорость вращения двигателя и следовательно меняем расход технологического раствора.
5.1 Контроллер универсальный «Каскад»
КУ «Каскад» – промышленный программируемый контроллер предназначен для работы в системах автоматизированного управления производственными технологическими процессами [30].
КУ «Каскад» имеет открытую модульную архитектуру построения. Это позволяет наращивать и конфигурировать контроллер для решения конкретных задач. Для связи и обмена данными КУ «Каскад» с персональным компьютером используется стандартный протокол связи MODBUS.
Состав и технические характеристики
КУ «Каскад» объединяет в своем составе следующие модули (рисунок 2.24):
– микропроцессорный модуль;
– модуль преобразования напряжения;
– модули ввода-вывода.
Модульный принцип построения позволяет осуществлять наращивание и конфигурирование контроллера «Каскад» для решения конкретной задачи.
Контроллер «Каскад» включает в себя:
– базовый блок в состав которого входят базовый модуль и устанавливаемые в плату базового модуля микропроцессорный модуль модуль преобразования напряжения и один из модулей ввода-вывода;
– блок расширения в состав которого входят базовый модуль и устанавливаемые в плату базового модуля три модуля ввода-вывода.
Для базового блока и блока расширения используются одинаковые корпуса.
Основу контроллера составляет базовый блок в котором установлен микропроцессорный модуль. Этот блок обеспечивает реализацию программ управления обмен данными между блоками. К одному базовому блоку допускается подключать до четырех блоков расширения.
Рис.2.24 – Состав КУ «Каскад»
Технические характеристики модулей входящих в состав КУ «Каскад» приведены в приложении № 3.
Функциональная схема КУ «Каскад» представлена на рисунке 2.5
Обмен данными внутри контроллера осуществляется по шине SPI по технологии «главныйподчиненный». Главным является микроконтроллер установленный на плате микропроцессорного модуля подчиненные на платах базовых модулей. «Подчиненные» микроконтроллеры обеспечивают передачу управляющих сигналов для модулей дискретных выходов прием данных от модулей дискретных и аналоговых входов. Инициировать передачу данных может только главное устройство.
Рис.2.25 Функциональная схема КУ «Каскад»
5.2. Программа управления маркера-дозатора
На основе алгоритма управления и с учетом выбранной элементной базы была написана программа управления дозатора технологического раствора. Программа написана в программном комплексе CoDeSys v2.3. Тест программы представлен в приложении №4 описание применения программного обеспечения (далее по тексту ПО) представлено в приложении №5 руководство системного программиста ПО представлено в приложении № 6 Результаты работы программы при рабочей частоте представлены в приложении №7 а при разгоне двигателя в приложении №8 .
Данная программа должна генерировать код на устройство управления ШД в зависимости от расхода заданного оператором.
5.3Автоматические клапаны
В полуавтоматических и автоматических маркерах-дозаторах прерывистого действия все перепускные операции с растворами совершаются с помощью автоматических клапанов различного типа которые определяют надежность работы прибора. Конструкция автоматических клапанов должна обеспечивать их длительную работу в условиях технологических сред надежность запирания и быстроту действия. Этим требованиям удовлетворяют электромагнитные и поворотные клапаны которые н получили наибольшее распространение. Среди электромагнитных клапанов следует выделить конструкции: первая — с плоской запорной мембраной прижимаемой к плоскости; вторая — использует пары поверхностей различных форм.
Принцип действия клапана первого вида показан па рис. 2.26 а. Основание клапана имеет входной и выходной каналы выходящие на внутреннюю поверхность основания под мембраной 2. Под действием пружины 3 мембрана и скрепленный с ней сердечник 4 электромагнита 5 прижаты к плоской поверхности основания перекрывая оба или один из каналов. При включении электромагнита сердечник и мембрана поднимаются — запорное действие клапана прекращается. В клапане имеется подвижный стоп 6 с помощью которого регулируют величину воздушного зазора электромагнита.Эта конструкция чрезвычайно надежна в работе и нашла преобладающее распространение в автоматических и полуавтоматических дозаторах.На рис.2.26 б показан клапан с конусным плунжером и седлом. В этом клапане внутри плунжера находится железный сердечник 2 благодаря которому электромагнит 3 Может поднимать плунжер тем самым открывая путь жидкости через клапан. При обесточенной катушке плунжер клапана под действием своего веса опускается на седло 4 закрывая клапан. Обычно запорные поверхности таких клапанов тщательно притирают. Надежность работы этих клапанов довольно низкая поэтому они были вытеснены из мембранными клапанами и нашли применение лишь в полуавтоматических дозаторах.
Рис.2.26 Конструкции запорных клапанов
В полуавтоматических дозаторах иногда применяют и автоматические клапаны работающие по принципу пережимания резиновой трубки.(Рис 2.26 в). Резиновая трубка прижимается к основанию 2 фигурной скобой 3 с помощью пружины 4. В этом положении клапан закрыт. При срабатывании электромагнита 5 трубка освобождается и благодаря упругости резины восстанавливает проходимость своего сечения — клапан открывается.
Достоинствами клапанов с пережимом трубкой является их простота. Однако из-за усталости резины необходимо периодически передвигать трубку вдоль своей оси подставляя под зажимную скобу свежий участок трубки либо заменять ее новой.
Поворотные переключающие клапаны получившие наряду с электромагнитными мембранными клапанами широкое применение в автоматических маркерах-дозаторах чаще всего изготовляются двух видов: плоскоцилиндрические и конусные (Рис.2.27).
Рис.2.27 Поворотно-переключающие клапана
Плоскоцилиидрический переключающий клапан состоит из неподвижного цилиндрического основания 1 с каналами 2 по которым подводится и уводится жидкость и подвижного цилиндра 3 прижатого к торцу основания пружиной 4. В подвижном диске имеются переключающие каналы 5. Подвижной цилиндр вращается с помощью электродвигателя все время в одну сторону и при своем движении перекоммутирует направление потоков жидкости. Одностороннее вращение подвижной части клапана и высокая точность обработки соприкасающихся поверхностей обеспечивают высокую надежность работы клапана.
На рис.2.27 показан конический переключающий клапан. Клапан имеет неподвижную коническую втулку 1 и вращающийся переключающий конус 2 плотно посаженный на вал 3. Конус прижат к втулке пружиной 4. Во втулке имеются штуцера по которым подводится жидкость и штуцера 6 по которым она уводится а в конусе— переключающие каналы 7. При вращении конуса происходит попеременное подключение входных штуцеров к тому или другому выходному штуцеру. В промежуточных положениях конуса поток жидкости через штуцера перекрывается.
Переключающие клапаны применяются в автоматических маркерах-дозаторах как прерывистого так и непрерывного действия.
Основной частью автоматического клапана является электромагниткоторый подобран исходя из стоимости удобства закрепления и мощности. На другом из концов крепления установлена пружина предназначенная и рассчитаная для возврата всей системы в исходное положение.
5.4.Расчет элементов конструкции узла маркировки
Следующим шагом выбора элементов конструкции являетсявыбор электромагнита.
Расчет электромагнита
Расчетное усиление электромагнита
Для выбора данного устройства необходимо знать поднимаемый вес балки и усилие сопротивления пружины которая крепит балку так как данные
значения достоверно не известны примим необходимое усилие равным 70 Н а во избежании ошибок усилие электромагнита возьмем равным 90 Н.
Qp = 11·Q [н] (2.23)
где Q = 70 н – усилие одного электромагнита;
Напряжение сети питания катушки электромагнита
Расчетное эффективное напряжение сети при котором должно быть обеспечено расчетное усиление электромагнита
Up = kи · U [В] (2.24)
где kи = 075 – коэффициент учитывающий возможное изменение напряжения сети;
Up = 075 · 220 = 165В
Амплитуда колебаний в направлении установки электромагнита
Конструктивный фактор электромагнита
где S = А+01 =05+01=06 мм
Максимальное значение индукции Вт (Вбсм²) определяем в зависимости от значения конструктивного фактора Кф по графику Рис.14
Таблица 2.4 Характеристики электромагнитов
Электромагнит КВМ 36
Потребляемая мощность 34Вт
Номинальное тяговое усилие 80Н
Рабочее напряжение 125 В
Время срабатывания 004с
Потребляемая мощность 35Вт
Номинальное тяговое усилие 90Н
Рабочее напряжение 220 В
Время срабатывания 002с
Номинальное тяговое усилие 70Н
Рабочее напряжение 110В
Время срабатывания 003с
Электромагнит ЭМПУ 45.1
Время срабатывания 005с
Основным показателем для выбора электромагнита является номинальное тяговое усилие и только №2 обладает искомым усилием но данный электромагнит уступает по габарито-массовым показателям однако напряжение питающейсети в установке предусмотрено 220 В что даетвозможность на прямую подключить прибор не прибегая к использованию дополнительных устройств а так же данный вариант обладает самым наименьшим временем срабатывания
что важно для точной отметки места дефекта в следствии чего можно сделать вывод об оптимальном выборе электромагнита ПЭ - 10.
Для корректного расчета пружины необходимо задаться силой которая будет воздействовать на нее в данном случае пружина должна растягиваться при воздействии на нее силы в 90 Н (данное усилие соответствует силе электромагнита выбранного в предыдущей части работы). Сила пружины при рабочей деформации: F1 = 90 Н.Сила пружины при максимальной деформации:
F2 = F1 1 - = 90 1 - 0.25 = 120 Н. (2.26)
- относительный инерционный зазор пружины (для пружин
растяжения составляет 025).
Сила предварительного напряжения: F0 = 0.25 120 = 30 Н.
В соответствии с предварительным расчетом пружины выберем
по ГОСТ 13764 - 86 соответствующие значения диаметров:
диаметр проволоки d = 3 мм; средний диаметр пружины D = 14
мм; жесткость одного витка с = 9083 Нмм; максимальная
деформация пружины s = 5 мм.
Рассчитаем общую жесткость пружины:
с1 = F2-F0 s = 120-30 5 = 18 Нмм. (2.27)
Определим рабочее число витков:
n = c1c = 90.83018 = 5 (2.28)
Определим общее количество витков пружины:
N = n + n1 = 5 + 2 = 7. (2.29)
n1 - опорные витки для пружины растяжения с d = 2 мм
Определим длину пружины растяжения без зацепов в спокойном
l = (n1 + 1) d = (7 + 1) 2 = 16 см. (2.30)
В соответствии с полученными данными расчета выбираем
пружину по ГОСТ 13766 - 86 под номером 372.
6.Расчет параметров надежности установки.
6.1 Математические модели для расчета интенсивностей
отказов основных комплектующих изделий.
6.1.1. Математическая модель для расчета интенсивностей отказов резисторов конденсаторов полупроводниковых элементов трансформаторов и моточных изделий:
λЭ= λ0αiK1K2K3K4 (2.31)
где λ0 – номинальное значение интенсивности отказов перечисленных КИ соответствующее коэффициенту электрической нагрузки Kн = 1 и температуре окружающей среды T0C = +200C.
Значения λ0 выбираются из соответствующих таблиц:
αi=f(Kн T0C) – поправочные коэффициенты значения которых выбираются из соответствующих таблиц:
α1 – поправочный коэффициент для определения λЭ резисторов выбирается из таблицы;
α2 – поправочный коэффициент для определения λЭ конденсаторов выбирается из таблицы;
α3 – поправочный коэффициент для определения λЭ полупроводниковых приборов выбирается из таблицы;
α4 – поправочный коэффициент для определения λЭ трансформаторов и моточных изделий (дросселей катушек индуктивности) выбирается из таблицы.
Ki – поправочный коэффициент учитывающий действия внешних воздействующих факторов и выбирается из соответствующих таблиц:
K1K2 – поправочные коэффициенты учитывающие воздействия соответственно вибрациям и ударных нагрузок на неамортизированную аппаратуру значения данных коэффициентов выбираются из таблицы;
K3 – поправочный коэффициент учитывающий влажность и температуру окружающей среды выбирается из таблицы;
K4 – поправочный коэффициент учитывающий изменение λЭ в зависимости от высоты над уровнем моря выбирается из таблицы.
6.1.2. Математическая модель для расчета интенсивностей отказов реле:
λЭ= λ’0 KFK1K2K3K4 (2.32)
где λ’0 – базовое значение интенсивности отказов реле которое вычисляется по формуле:
Формула (2.33) используется для реле с диаметром провода обмотки d ≥ 035 мм; формула (2.34) используется для реле с диаметром провода обмотки d 035 мм.
N – общее число контактных пар;
n – число задействованных контактных пар;
λ0 – номинальное значение интенсивности отказов реле выбираемое из таблицы.
Ki – поправочный коэффициент учитывающий воздействие внешних факторов (i = 1234). Значения коэффициентов Ki (i = 1234) выбираются соответственно из таблиц.
KF – коэффициент учитывающий частоту коммутации реле при работе в изделии значения данного коэффициента выбираются из таблицы.
6.1.3. Математическая модель для расчета интенсивности отказов интегральных микросхем:
λЭ= λис0 K1K2K3K4 (2.35)
где λис0 – базовое значение интенсивности отказов интегральных микросхем вычисляется по следующей формуле:
λис0 = 08 λтр0+ (2.36)
где λтр0 – базовое значение интенсивности отказов маломощных транзисторов определяется предварительно (как дискретного элемента);
n – количество внешних задействованных выводов микросхемы;
Ki – (i = 1234) выбираются соответственно из таблиц.
6.1.4. Математическая модель для расчета интенсивности отказов коммутационных элементов (тумблеры переключатели кнопки):
λЭ= λ0Kf K1K2K3K4 (2.37)
где λ0 – номинальное значение интенсивности отказов выбирается из таблицы;
Kf - коэффициент зависящий от частоты включения значения данного коэффициенты выбираются из таблицы;
6.1.5.Математическая модель для расчета интенсивности разъемов:
λЭ= λ0KксKккK1K2K3K4 (2.38)
где λ0 - номинальное значение интенсивности отказов разъемов выбирается из таблицы;
Kкс – коэффициент зависящий от количества сочленений-расчленений выбирается из таблицы;
Kкк – коэффициент зависящий от количества задействованных контактов значения данного коэффициента вычисляется по формуле:
где N – количество задействованных контактов;
6.1.6. Математическая модель для расчета интенсивности отказов электрических кабелей проводов шнуров:
λЭ= λ0KФLK1K2K3K4 (2.40)
где λ0 [] - номинальное значение интенсивности отказов разъемов выбирается из таблицы;
L – суммарная длина кабеля (провода шнура); для изделий с L ≤ 3 м допускается принимать L = 1 м;
KФ – функциональный коэффициент значение данного коэффициента вычисляется по формуле:
где Eа – условная энергия активации кДжгрмоль;
RГ = 83144 – универсальная газовая постоянная джградгмоль;
Kt – температурный коэффициент зависящий от рабочей температуры окружающей среды в аппаратуре; оределяется по формуле:
где tб – базовая температура равная 250С или 1000С (по типу кабеля);
tp – рабочая максимальная температура в аппаратуре (изделии);
Как правило максимальная температура изделия с учетом перегрева находится в диапазоне 700С – 800С.
Величина условной энергии активации (в среднем) в достаточно широком диапазоне имеет уровень Eа 85 кДжгмоль. С учетом указанных ограничений для практических расчетов в формуле (10) рекомендуется использовать значения KФ = 90 (при tб = 250C).
6.1.7. Математическая модель для расчета интенсивности отказов соединений (паек):
λЭ= λ0nK1K2K3K4 (2.43)
где λ0 - номинальное значение интенсивности отказов паек;
n – количество паек в изделии;
6.1.8. Математическая модель для расчета интенсивности отказов предохранителей:
λЭ= λ0KTK1K2K3K4 (2.44)
где λ0 - номинальное значение интенсивности отказов предохранителей;
KT – тепловой коэффициент зависящий от температуры окружающей среды для предохранителей; значения данного коэффициента выбираются из таблицы ;
Расчет показателей надежности.
Расчет интенсивности отказов.
Предохранитель: λЭ= λ0KTK1K2K3K4
λЭ= 05 2 1 1 2 13 = 104 10-6 1час
λЭобщ= λЭ N = 104 5 = 52 10-6 1час
Генератор звука: λЭ= λ0αiK1K2K3K4
λЭ = 1 08 1 1 2 13 = 208 10-6 1час
λЭобщ= λЭ N = 208 1 = 208 10-6 1час
Индикатор: λЭ= λ0αiK1K2K3K4
λЭ = 204 089 1 1 2 13 = 47205610-6 1час
λЭобщ= λЭ N = 472056 1 = 47205610-6 1час
λЭ =204 089 1 1 2 13 = 47205610-6 1час
Резистор: λЭ= λ0αiK1K2K3K4
λЭ= 08 067 1 1 2 13 = 13936 10-6 1час
λЭобщ= λЭ N = 13936 1 = 13936 10-6 1час
λЭ= 07 067 1 1 2 13 = 12194 10-6 1час
λЭобщ= λЭ N = 12194 1 = 12194 10-6 1час
Выключатель: λЭ= λ0Kf K1K2K3K4
λЭ= 06 1 1 1 2 13 = 156 10-6 1час
λЭобщ= λЭ N = 156 1 = 156 10-6 1час
Трансформатор: λЭ= λ0αiK1K2K3K4
λЭ = 5 08 1 1 2 13 = 10410-6 1час
λЭобщ= λЭ N = 104 1 = 10410-6 1час
Вилка: λЭ= λ0Kf K1K2K3K4
λЭ = 05 1 1 1 2 13 = 13 10-6 1час
λЭобщ= λЭ N = 13 1 = 13 10-6 1час
Розетка: λЭ= λ0KксKккK1K2K3K4
λЭ = 025 039 055 1 1 2 13 = 014 10-6 1час
λЭобщ= λЭ N = 014 1 = 01410-6 1час
λЭ = 025 039 055 1 1 2 13 = 01410-6 1час
λЭ = 03 039 055 1 1 2 13 = 018 10-6 1час
λЭобщ= λЭ N = 018 1 = 018 10-6 1час
Гнездо: λЭ= λ0KксKккK1K2K3K4
λЭобщ= λЭ N = 014 2 = 02810-6 1час
Клемма: λЭ= λ0Kf K1K2K3K4
λЭ = 00005 1 1 1 2 13 = 00013 10-6 1час
λЭобщ= λЭ N = 00013 1 = 00013 10-6 1час
Фильтр сетевой: λЭ= λ0αiK1K2K3K4
λЭ= 09 08 1 1 2 13 = 1872 10-6 1час
λЭобщ= λЭ N = 1872 1 = 1872 10-6 1час
Провода: λЭ= λ0KФLK1K2K3K4
λЭ = 0015 90 1 1 1 2 13 = 35110-6 1час
Пайки: λЭ= λ0nK1K2K3K4
λЭ = 0015 55 1 1 2 13 = 214510-6 1час
Общее значение λ1= Σ λ1-20 = 4136242 10-6 1час
Конденсатор: λЭ= λ0αiK1K2K3K4
λЭ = 14 025 1 1 2 13 = 09110-6 1час
λЭобщ= λЭ N = 091 2 = 182 10-6 1час
λЭобщ= λЭ N = 091 1 = 091 10-6 1час
λЭобщ= λЭ N = 091 2 = 273 10-6 1час
λЭ = 20 025 1 1 2 13 = 1310-6 1час
λЭобщ= λЭ N = 13 3 = 39 10-6 1час
Микросхема: λЭ= λис0 K1K2K3K4
λЭ = 017 1 2 13 = 044210-6 1час
λЭобщ= λЭ N = 0442 1 = 044210-6 1час
λЭ = 0204 1 1 2 13 = 0530410-6 1час
λЭобщ= λЭ N = 05304 2 = 1060810-6 1час
λЭ = 036 1 1 2 13 = 093610-6 1час
λЭобщ= λЭ N = 0936 1 = 093610-6 1час
λЭ = 017 1 1 2 13 = 044210-6 1час
λЭобщ= λЭ N = 0442 3 = 132610-6 1час
Резистор: λЭ= λ0αiK1K2K3K4
λЭ = 06 067 1 1 2 13 = 1045210-6 1час
λЭобщ= λЭ N = 10452 3 = 31356 10-6 1час
λЭобщ= λЭ N = 10452 1 = 10452 10-6 1час
λЭ = 06 067 1 1 2 13 = 10452 10-6 1час
λЭ = 05 067 1 1 2 13 = 087110-6 1час
λЭобщ= λЭ N = 0871 1 = 087110-6 1час
λЭобщ= λЭ N = 0871 3 = 2613 10-6 1час
λЭобщ= λЭ N = 10452 2 = 20904 10-6 1час
λЭ = 1306711213 = 22646 10-6 1час
λЭобщ= λЭ N = 226462 = 4529210-6 1час
λЭ = 07 067 1 1 2 13 = 1219410-6 1час
λЭобщ= λЭ N = 12194 1 = 1219410-6 1час
λЭ = 06 067 11 2 13 = 1045210-6 1час
λЭобщ= λЭ N = 10452 1 = 1045210-6 1час
λЭ= 08 067 1 1 2 13 = 1393610-6 1час
λЭобщ= λЭ N = 13936 1 = 1393610-6 1час
λЭ= 07 067 1 1 2 13 = 1219410-6 1час
λЭобщ= λЭ N = 121941 = 1219410-6 1час
Мост выпрямительный: λЭ= λ0αiK1K2K3K4
λЭ = 12 08 1 1 2 13 = 249610-6 1час
λЭобщ= λЭ N = 2496 1 = 2496 10-6 1час
λЭ= 12 08 1 1 2 13 = 249610-6 1час
λЭобщ= λЭ N = 2496 2 = 499210-6 1час
Стабилитрон: λЭ= λ0αiK1K2K3K4
λЭ= 23 08 1 1 2 13 = 478410-6 1час
λЭобщ= λЭ N = 4784 1 = 478410-6 1час
Транзистор: λЭ= λ0αiK1K2K3K4
λЭ= 034 065 1 1 2 13 = 0574610-6 1час
λЭобщ= λЭ N = 05746 1 = 05746 10-6 1час
λЭ = 021 065 1 1 2 13 = 0354910-6 1час
λЭобщ= λЭ N = 03549 1 = 0354910-6 1час
λЭ= 025 065 1 1 2 13 = 0422510-6 1час
λЭобщ= λЭ N = 04225 21 = 88725 10-6 1час
λЭ = 05 1 1 1 2 13 = 1310-6 1час
λЭобщ= λЭ N = 13 1 = 1310-6 1час
λЭ= 025 1 1 1 2 13 = 06510-6 1час
λЭобщ= λЭ N = 065 1 = 06510-6 1час
λЭ = 0015 152 1 1 2 13 = 592810-6 1час
Общее значение λ2= Σ λ21-54 = 7221510-6 1час
Конденсатор: λЭ= λ0αiK1K2K3K4
λЭ= 14 025 1 1 2 13 = 09110-6 1час
λЭобщ= λЭ N = 091 2 = 18210-6 1час
λЭобщ= λЭ N = 091 3 = 27310-6 1час
λЭобщ= λЭ N = 091 1 = 09110-6 1час
λЭ=14 025 1 1 2 13 = 09110-6 1час
λЭобщ= λЭ N = 0911 = 09110-6 1час
λЭ = 20025 1 1 2 13 = 1310-6 1час
λЭобщ= λЭ N = 13 4 = 5210-6 1час
λЭ= 017 1 1 2 13 = 044210-6 1час
λЭ= 014 1 1 2 13 = 036410-6 1час
λЭобщ= λЭ N = 0364 2 = 072810-6 1час
λЭобщ= λЭ N = 0364 1 = 0364 10-6 1час
λЭ= 021 1 1 2 13 = 054610-6 1час
λЭобщ= λЭ N = 0546 1 = 0546 10-6 1час
Светодиод: λЭ= λ0αiK1K2K3K4
λЭ= 30 092 1 1 2 13 = 717610-6 1час
λЭобщ= λЭ N=7176 1 = 717610-6 1час
λЭ= 20 067 1 1 2 13 = 348410-6 1час
λЭобщ= λЭ N = 3484 1 = 348410-6 1час
λЭобщ= λЭ N = 12194 3 = 3658210-6 1час
λЭобщ= λЭ N = 13936 2 = 27872 10-6 1час
λЭобщ= λЭ N = 12194 2 = 2434810-6 1час
λЭ= 13 067 1 1 2 13 = 2264610-6 1час
λЭобщ= λЭ N = 22646 1 = 2264610-6 1час
λЭ= 04 067 1 1 2 13 = 0696810-6 1час
λЭобщ= λЭ N = 06968 1 = 0696810-6 1час
λЭобщ= λЭ N = 06968 1 = 06968 10-6 1час
λЭ= 04 067 1 1 2 13 = 06968 10-6 1час
λЭ= 16 067 1 1 2 13 = 2787210-6 1час
λЭобщ= λЭ N = 27872 1 = 0696810-6 1час
λЭ= 06 06711213 = 1045210-6 1час
λЭобщ= λЭ N = 10452 12 = 12542410-6 1час
λЭ= 06 067 1 1 2 13 = 1045210-6 1час
λЭобщ= λЭ N = 10452 4 = 4180810-6 1час
Диод: λЭ= λ0αiK1K2K3K4
λЭ= 07 089 1 1 2 13 = 1619810-6 1час
λЭобщ= λЭ N = 16198 6 = 9718810-6 1час
λЭ= 07 089 1 1 213 = 1619810-6 1час
λЭобщ= λЭ N = 16198 2 = 32396 10-6 1час
Стабилитрон: λЭ= λ0αiK1K2K3K4
λЭ= 17 08 1 1 2 13 = 353610-6 1час
λЭобщ= λЭ N = 3536 1 = 353610-6 1час
λЭ= 19 08 1 1 2 13 = 395210-6 1час
λЭобщ= λЭ N = 3952 1 = 395210-6 1час
Транзистор: λЭ= λ0αiK1K2K3K4
λЭ= 025065112 13 = 0422510-6 1час
λЭобщ= λЭ N = 04225 4 = 16910-6 1час
λЭ= 021 06511213 = 0354910-6 1час
λЭобщ= λЭ N = 03549 2 = 0709810-6 1час
λЭ= 03 065 1 1 2 13 = 0507 10-6 1час
λЭобщ= λЭ N = 0507 1 = 050710-6 1час
λЭ= 03 065 1 1 2 13 = 050710-6 1час
λЭобщ= λЭ N = 0507 1 = 0507 10-6 1час
λЭобщ= λЭ N = 05071 = 050710-6 1час
λЭ= 05111213 = 1310-6 1час
λЭ= 0015 90 1 1 1 2 13 = 35110-6 1час
λЭ = 0015 120112 3 = 468 10-6 1час
Общее значение λ3= Σ λ55-95 = 1027624 10-6 1час
λЭ= 1508911213 = 347110-6 1час
λЭобщ= λЭ N = 3471 3 = 1041310-6 1час
λЭ= 06 067 1 1 2 13 = 1045210-6 1час
λЭобщ= λЭ N = 10452 21 = 21949210-6 1час
λЭ= 05111213 = 1310-6 1час
λЭобщ= λЭ N = 131 = 1310-6 1час
λЭ= 001590111213 = 35110-6 1час
0.λЭ = 00156411213 = 249610-6 1час
Общее значение λ4= Σ λ96-100 = 396682 10-6 1час
Значение интенсивности отказов: λ = λ1+λ 2+ λ3+ λ4= 413624210-6
+ 7221510-6 + 102762410-6 + 39668210-6 =2560080210-6 1час
Расчет наработки до отказа.
Величина средней наработки на отказ изделия в целом в активном режиме определяется по следующей формуле:
где λj = - параметр потока отказов j-ой сборочной единицы.
λj – интенсивность отказов
n= 12 - количество элементов в j-ой сборочной единице.
Шаговый двигатель FL86STH65–2808A
Преобразователь температуры
Микропроцессорный модуль
Модуль преобразования напряжения
Системный блок Р-III
8 Mb RAM HDD 30Gb RW CDROM FDD
Жгуты технологические
Величина средней наработки на отказ в основном режиме составляет: Т0=4825 часа.
Величина средней наработки до отказа проектируемой системы
определяется по формуле:
То = 1 Ni = 1 2560080210-6 1час = 3900 час.
Расчет вероятности безотказной работы в зависимости от
времени работы прибора.
Для структурной схемы надежности вероятность безотказной
работы проектируемой системы в течение времени с учетом
принятых выше допущений определяется по следующей
Pc (t) = exp (- cNi t)
За восьмичасовую смену вероятность безотказной работы
Pc (8) = exp (- cNi t) = exp (-2560080210-6 1час1008) = 091
За десять лет службы вероятность безотказной работы
Pc (20000) = exp (- cNi t) = exp (-25600802 10-6 1час100 20000) = 0257
Таким образо проектируемая система обладает значительной
надежностью и способна работать длительное время.
03.ТЕХНОЛОГИЧЕСКАЯ ЧАСТЬ.doc
Разработан маршрут изготовления втулки ; выбраны режимы резания по справочнику и произведен их перерасчет ; выбор станков и приспособлений; расчет технической нормы времени; разработано ТЗ на изготовление специального приспособления расчет силы зажима; расчет точности приспособления; разработан ЕТП на изготовление втулки.
На форматах А1 спроектировано приспособление для сверления отверстия и фрезерования паза выполнен чертёж графической технологии обработки детали. Разработка наиболее рационального с точки зрения экономичности и технологичности технологического процесса обеспечивающего получение годной детали при минимальных затратах труда времени материалов (т.е выбраны оптимальные условия труда) и минимальной стоимости получения детали. Главной задачей изготовления втулки является правильно составленная технология изготовления. От технологии зависит производительность и экономичность процесса.
1. Метод изготовления втулки
Таблица 3.1 Квалитеты размеров
Таблица 3.2 Метод изготовления втулки
Методы ступеней обработки поверхностей
Квалитет достигаемой точности (IT)
Получистовая токарная
Черновое растачивание
Получистовое растачивание
Чистовое растачивание
Черновое фрезерование
Черновое развертывание
2 Выбор моделей станков
Токарные (точение растачивание зенкерование развертывание) операции
выполняем на токарном станке модели ТПК–125А1.
На станке установлена инструментальная головка ВТР-63 и инструментальный диск TD-VDI-S-63-8-20-240
Станок токарный с ЧПУ и автоматической сменой инструмента ТПК-125А1 предназначен для патронной обработки с высокой точностью малогабаритных деталей с большим количеством проходов и сложного профиля из различных конструкционных сталей и сплавов. На станке можно производить все виды токарной обработки. В конструкции станка ТПК-125А1 применены: базовые детали повышенной жесткости шпиндель выполнен на радиально-упорных подшипниках линейные роликовые направляющие с арочным профилем револьверная головка с пневмо-отжимом асинхронный двигатель с частотным регулированием в качестве привода главного движения сервоприводы Maxsine в качестве приводов координат. Наличие на станке револьверной головки и сервоприводов позволяет значительно расширить технологические возможности станка увеличить производительность повысить качество обрабатываемых деталей.
Фрезерно–сверлильную операцию выполняем на станке 6Р13РФ3.
Станок вертикальный консольно-фрезерный с ЧПУ и револьверной головкой предназначен для многооперационной обработки деталей сложной конфигурации из стали чугуна цветных и легких металлов а также других материалов. Наряду с фрезерными операциями на станке можно производить точное сверление растачивание зенкерование и развертывание отверстий.
Резец проходной подрезной с трехгранной пластиной ()из твердого сплава с :
Резец MWLNR1616Н06 ВК8 ТУ 2-035-892 – 82
Резец расточной с трехгранной пластиной из твердого сплава:
Резец К.01.4980.000-06 ВК8 ТУ 2-035-1040–86
Резец К.01.4980.000-06 ВК4 ТУ 2-035-1040–86
Резец проходной с с ромбической пластиной () из твердого сплава:
Резец MTGNR-1616K16 ВК8 ТУ 19-4206-96–83
Резец MTGNR-1616K16 ВК4 ТУ 19-4206-96–83
Фреза дисковая трехгранная с радиусом закругления 016мм с предельным отклонением для паза по Р9:
Фреза 2240-0371 Р6М5 ГОСТ 3755–78
Сверло спиральное с коническим хвостовиком с 2φ = 118° и = 55°
Сверло 035-2300-1225 Р6М5 ОСТ 2И20-1–80
Развертка машинная с цилиндрическим хвостовиком и
Развертка 2363-0062 Р6М5 Гост 1672-80 тип 1
2 Расчет режимов резания
Произведем расчет режимов резания для обработки двух поверхностей (токарная обработка сверление) остальные назначим по справочнику с учетом поправочных коэффициентов.
Черновое точение цилиндрической поверхности 3
Токарная обработка: черновое точение. Резец проходной правый с трехгранной пластиной из твердого сплава ВК8 с φ=90º. Сечение державки 16 х 16 радиус скругления режущей кромки 0025 мм радиус вершины резца 10 мм. Стойкость Т = 45 мин.
Глубина резания [39]
Скорость резания ммин
где КV = Кmv·Кnv ·Кuv =10·085·083=0481 - коэффициент учитывающий качество обрабатываемого материала.
- поправочный коэффициент учитывающий влияние материала заготовки [39]
HB=150 MПа - предел прочности обрабатываемого материала при растяжении;
Кпv = 085 - поправочный коэффициент учитывающий состояние поверхностного слоя заготовки [39];
Кuv = 083 - поправочный коэффициент учитывающий влияние инструментального материала на скорость резания[5].
среднее значение стойкости инструмента;
поправочный коэффициент [5]
Постоянная СР и показатели степеней x y z для каждой составляющей силы резания приведены в таблице [39]
Таблица 3.3 Коэфиценты и показатели степеней
Коэффициент и показатели степеней
КР =КМР·Кφр·Кλр·Кγр·Кrp - поправочный коэффициент учитывающий фактические условия резания
Поправочные коэффициенты (КМРКφрКλрКγрКrp) учитывающие влияние геометрических параметров на условия резания заносим в таблицу 3.4 [36]
- поправочный коэффициент учитывающий влияние качества обрабатываемого материала на силовые зависимости [36]
Таблица 3.2 Поправочные коэффиценты
Материал режущей части
Поправочные коэффициенты
Величина коэффициентов
Главный угол в плане
Радиус при вершине мм
Мощность резания (эффективная):
Расчет режимов резания на поверхность 8
Сверление отверстия
Инструмент: Сверло спиральное с коническим хвостовиком с 2φ = 118° и = 55°
Сверло 035-2300-1234 Р6М5 ОСТ 2И20-1–80
При сверлении глубина резания t = 05* D = 05*51 = 255 мм; где D – диаметр получаемого отверстия.
При сверлении отверстий без ограничивающих факторов берём максимально допустимую по прочности сверла подачу (табл. 25 стр 277[38])
Скорость резания. При сверлении скорость резания ммин равна:
Где С - поправочный коэффициент на скорость; Т – период стойкости; g m y – оказатели степени;
Кv= Кmv Кnv Кuv Kov=1*083*10*0.5=0415– общий поправочный коэффициент;
Км =1 – коэффициент на обрабатываемый материал;
Ки = 083 – коэффициент на инструментальный материал;
К = 10 – коэффициент учитывающий глубину сверления.
Где значения коэффициента Cv и показателей степени из таблицы 28 стр 278[39] а период стойкости Т- из таблицы 30 стр 279-280[35]
Cv=21.8; g=025; y=0125; m=055 Т=35мин;
Главная составляющая силы резания при сверлении - осевая сила Н
Где: Cр- поправочный коэффициент; Кр – коэффициент учитывающий фактические условия обработки.
Значение коэффициента Cр и показателей степени из табл. 32 поправочный коэффициент из табл. 9[39] .Cр=43.3; y=08; g=10; Кр=06
Мкр=10=10*0.021*5.10.2*013508*06=036 Н м
где См =0021– поправочный коэффициент; Кр =06– коэффициент учитывающий фактические условия обработки.
Мощность резания (эффективная) кВт
Режимы резания на остальные поверхности выбираем по справочнику [41]
Расчет режимов резания на поверхность 14
Содержание операции и стадии обработки: 1) черновая подрезка торца получистовая подрезка торца для поверхности 1 4.
Глубина резания для черновой стадии обработки на оби поверхности составляет ; для получистовой стадии обработки .
Для I стадии обработки глубина резания
Для черновой стадии обработки при подрезке терцев подачу выбирают по карте 3[36]. При глубине резания t до 2мм и диаметре детали до 180мм Для получистовой стадии обработки значения подач для данных поверхностей определяют по карте 4[36] аналогичным образом: при диаметре детали до 180мм и глубине резания до 15мм –
Выбранные значения подач корректируют по карте 5[36] для измененных условий в зависимости от:
инструментального материала ;
сечения державки резца;
прочности режущей части;
механических свойств обрабатываемого материала ;
схемы установи заготовки ;
состояния поверхности заготовки
геометрических параметров режущей части инструмента;
при получистовой обработке ковкого чугуна значение подачи умножаем на Ks=09
Окончательно значения подач для черновой и получистовой стадий обработки определяют по формуле
С учетом поправочных коэффициентов подачи принимают следующие значения:
для черновой стадии:
для поверхности 14 ;
для получистовой стадии :
для поверхности 14 .
Выбор скорости резания
Скорость резания для черновой и получистовой стадий обработки для поверхностей 1 4 выбирают по карте 21[36]. Черновой стадии обработке соответствует скорость резания для поверхностей 14 получистовой стадии обработки соответствует скорость резания для поверхности 14 .
По карте 23[2] выбирают поправочные коэффициенты на скорость резания для черновой и получистовой стадий обработки для измененных условий в зависимости от:
группы обрабатываемости материала
механических свойств обрабатываемого материала
геометрических параметров резца
периода стойкости (Т=30 мин) режущей части
Значение скорости для черновой и получистовой стадий обработки определяют по форме
С учетом поправочных коэффициентов у скоростей следующие значения:
На получистовой стадии
Частоту вращения шпинделя определяют по формуле .
Для черновой стадии обработки:
Принимаем частоту вращения для поверхности 14 тогда скорость резания
Для получистовой стадии обработки
Принимаем частоту для поверхности 14 .
Тогда скорость резания
Проверка выбранных режимов резания по мощности привода главного движения
Для черновой и получистовой стадий обработки мощность резания определяют по карте 21[36] аналогично выбору скорости и корректируют в зависимости от твердости обрабатываемого материала для черновой стадии обработки (карта 24[36]).
На черновой стадии обработки
На получистовой стадии обработки
Расчет режимов резания на поверхность 23
Базирование в патроне. Содержание операции – точить поверхность 23.
Выбор стадий обработки
Ведем в три стадии: черновое получистовое и чистовое точение.
Выбор глубины резания
По карте 2[36] определяют минимально необходимую глубину резания для получистовой стадии обработки.
При чистовой стадии обработки: для поверхности 23 диаметр которой соответствует интервалу размеров 50 80мм рекомендуется .
При получистовой стадии обработкидля поверхности 23 диаметр которой соответствует интервалу размеров 50 80мм рекомендуется .
Глубину резания на черновой операции определяют следующим образом
Для черновой стадии обработки подачу выбирают по карте 3[36Для поверхности 23 рекомендуется . По карте 3[36] определяют поправочные коэффициенты на подачу в зависимости от инструментального материала для поверхности .
Для получистовой стадии обработки значения подач определяют по карте 4[36] аналогично. Для поверхности 23 . Поправочные коэффициенты на подачу в зависимости от инструментального материала .
По карте 5 определяют поправочные коэффициенты на подачу для черновой и получистовой стадий обработки для измененных условий обработки в зависимости от:
для поверхности 23 ;
для поверхности 23 .
Расчетные подачи для черновой стадии обработки проверяют по осевой и радиальной составляющим силы резания допустимым прочностью механизма подач станка.
Табличные значения составляющих силы резания при обработке поверхности 23 с глубиной резания 27мм и подачей определяют по карте 32[36]
для поверхности 23 . По карте 33[36] определяют поправочные коэффициенты на силы резания для измененных условий в зависимости от:
главного угла в плане
угла наклона режущей кромки
Значение составляющих силы резания определяют по формулам
Для поверхности 2 3 ;
Рассчитанные значения составляющих силы резания меньше допустимых механизмом подач станка в соответствующем направлении.
Для чистовой стадии обработки рекомендуемые значения подач выбираем по карте 6[36]. Для поверхности 23.
По карте 8 определяют поправочные коэффициенты на подачу для чистовой стадий обработки для измененных условий обработки в зависимости от:
Скорость резания для черновой и получистовой стадий обработки для поверхностей 2 3 выбирают по карте 21[36] для чистовой стадии по карте 22[36]. Черновой стадии обработке соответствует скорость резания для поверхностей 2 3 ; получистовой стадии обработки соответствует скорость резания для поверхности 2 3 ; чистовой стадии для поверхности 23 .
По карте 23[36] выбирают поправочные коэффициенты на скорость резания для черновой и получистовой стадий обработки для измененных условий в зависимости от:
для поверхности 2 3 ;
Для черновой стадии обработки:
Принимаем частоту вращения для поверхности 23 тогда скорость резания
для поверхности 23 Принимаем частоту для поверхности23 .
Для чистовой стадии обработки
Принимаем частоту для поверхности 23 .
Расчет режимов резания на поверхность 6
Содержание операции: обработать отверстие 25+0052(Н9) мм длиной 40 мм с параметром шероховатости поверхности Ra=25 мкм.
Вариант маршрута обработки
Маршрут обработки включает в себя черновое растачивание получистовое растачивание чистовое растачивание.
Для поверхности 6 (25Н9) диаметр детали входит в интервал размеров 18 30мм. Глубина резания для получистовой стадии обработки мм; для чистовой стадии обработки мм.
Для черновой стадии обработки глубина резания
Для черновой стадии обработки подачу выбирают по карте 9[36]. При растачивании резцом круглого сечения d=16мм для поверхности 6 при глубине резания 19мм . Для получистовой стадии обработки значения подач для поверхности 6 определяют по карте 10[36] аналогичным образом: .
Выбранные значения подач корректируют по карте 11[36] для измененных условий в зависимости от:
инструментального материала
геометрических параметров резца
Принятое значение подачи на черновой стадии обработки проверяют по осевой и радиальной составляющим силы резания допустимым прочностью механизма подач.
Табличные значения составляющих силы резания при обработке поверхности 6 с глубиной резания 19мм и подачей определяют по карте 32[36]
По карте 33[36] определяют поправочные коэффициенты на силы резания для измененных условий в зависимости от:
Рекомендуемые значения подач для чистовой стадии обработки выбирают по карте 12[36]:
По карте 14[36] определяют поправочные коэффициенты на подачу для чистовой стадий обработки для изменений условий в зависимости от:
радиуса вершины резца;
квалитета обрабатываемой детали на чистовой стадии для;
Окончательно значения подач для чистовой и отделочной стадий обработки определяют по формуле
С учетом поправочных коэффициентов подачи принимают следующие значения ;
Скорость резания для черновой и получистовой стадий обработки для поверхности 6 выбирают по карте 21[36]. Черновой стадии обработке соответствует скорость резания ; получистовой стадии обработки соответствует скорость резания . Скорость резания для чистовой стадии обработки выбирают по карте 22[36]. Чистовой стадии обработки соответствует скорость резания .
Принимаем частоту тогда скорость резания
Принимаем частоту тогда скорость резания
Для чистовой стадии обработки
Расчет режимов резания на поверхность 7
Содержание операции: фрезеровать паз выдерживая размеры h=3мм l=5мм (Н14) с параметром шероховатости поверхности Rz=40 мкм.
Охлаждение – эмульсия.
Глубина резания на фрезерование равна глубине паза 3мм t=3мм.
Фрезу выбирают по выбирают по ГОСТ3755–78. Форма заточки инструмента нормальная.
При фрезеровании дисковыми фрезами размеры зависят от геометрических параметров режущего инструмента.
При фрезеровании дисковыми двух-и трехсторонними фрезами подачу на зуб выбирают по карте 95[36] исходя из группы обрабатываемого материала диметра и числа зубьев фрезы глубины и ширины фрезерования.
Полученное значение подачи умножают на поправочные коэффициенты в зависимости от:
твердости обрабатываемого материала
отношение вылета оправки к диаметру оправки
фактического числа зубьев фрезы
формы обрабатываемой поверхности
Скорость и мощность резания выбирают по картам 96-98[36] исходя из диаметра фрезы глубны и ширины фрезерования подачу на зуб фрезы.
Полученные значения скорости и мощности резания умножают на поправочные коэффициенты в зависимости от:
твердости обрабатываемого материала;
материала режущей части фрезы;
периода стойкости режущей части фрезы ;
отношение фактической ширены фрезы к нормальной ;
отношения вылета оправки к диаметру оправки ;
формы обрабатываемой поверхности .
Частоту вращения шпинделя определяют п формуле
По паспорту станка принимают ближайшее значение
Фактическая скорость резания .
Содержание операции: обработать отверстие 6Н10 мм длиной 75 мм с параметром шероховатости поверхности Rz=40 мкм.
Маршрут обработки включает в себя сверление развертывание черновое.
Глубина резания на переходах развертывания определяют по карте 45[2] и корректируют с учетом последовательности переходов маршрута (поправочный коэффициент Кti).
Черновое развертывание t=018; Кti=24 окончательно t=018·24=043
Расчет диаметров обрабатываемого отверстия по переходам маршрута и выбор инструмента
Диаметры обрабатываемого отверстия по переходам находят по формуле
C учетом ранее определенных глубин резания диаметры отверстия находят для:
сверления D=6-2·043=514
С учетом округления принимают следующие размеры инструментов:
Сверло выбирают по ОСТ 2И20-1–80. Форма заточки инструмента нормальная.
Выбор подачи скорости мощности и осевой силы резания осуществляют по картам 46 51 [36] для ближайшего большего табличного значения диаметра инструмента.
В данном случае значения этих величин выбирают для:
сверления при диаметре D=51 мм отношения длины рабочей части сверла к диаметру lD=3. Для этих значений по карте 46 лист2 [36] определяют
чернового развертывания диаметру D=6мм соответствует ближайшее табличное значение DT=12мм; по карте [36 карта 49 лист1] определяют:
Значение частот вращения шпинделя для табличных значений скорости резания определяют по формуле
Табличные значения режимов резания корректируют в зависимости от измененных условий работы по формулам корректировки приведенным в карте 52[36]. Значения поправочных коэффициентов выбирают из карты 53[36].
В данном случаи для переходов:
Подачу корректируют по формуле (карта 52[36]).
Коэффициент выбирают по карте 53 лист 1[36].
Для ковкого чугуна (150 НВ)
С учетом коэффициента
Скорость редактируется по формуле
По карте 53 [36] выбирают коэффициенты:
( Для ковкого чугуна 150 НВ);
(для нормальной формы заточки инструмента);
(обработка с охлаждением);
(состояние обрабатываемой поверхности отливка без корки);
(материал инструмента – быстрорежущая сталь);
(сверло по ОСТ 2И20-1–80)
(инструментальный материал без покрытия)
Скорректированную частоту вращения шпинделя рассчитываем по формуле
Скорость резания определяется по формуле
По паспортным данным станка выбирают ближайшую имеющуюся у станка частоту вращения .
Окончательно принимают мин-1 мммин ммоб.
Фактическую скорость резания определяют по формуле
Чернового развертывания.
Подачу корректируем по формуле (карта 52)[36].
Скорость корректируем по формуле
По карте 53 [36] выбирают: ;
( обрабатываемая поверхность без корки);
( предшествующий переход был сверление);
(инструментальный материал без покрытия).
С учетом поправочных коэффициентов определяют значения подачи
скорости частоты вращения шпинделя и скорости подачи :
для чернового развертывания
С учетом паспортных данных станка фактические режимы резания выбирают: мин-1 мммин ммоб ;
Фактическая скорость резания
Корректировка табличных значений мощности резания и осевой силы
По карте 52[36] формулы для корректировки мощности резания и осевой силы имеют вид:
По карте 53[36] выбирают поправочные коэффициенты
С учетом определенных коэффициентов скорректированные значения мощности и осевой силы определяют по формулам:
для развертывания ; ;
Установленные режимы резания осуществимы на данном станке так как максимальная осевая сила максимальная мощность не превосходят допустимых значений станка.
Таблица 3.5.Режимы резания
3 Техническое задание на проектирование специального приспособления
Таблица 3.6 - Техническое задание на проектирование специального приспособления.
Наименование и область применения
Приспособление для сверления отверстия 6H10мм и фрезерования паза шириной 3мм глубиной 5мм.
Основания для разработки
Операционная карта технологического процесса механической обработки втулки.
Цель и назначение разработки
Проектируемое приспособление должно обеспечить:
точную установку и надежное закрепление заготовки втулки а также постоянное во времени положение заготовки относительно положения станка и режущего инструмента с целью получения необходимой точности размеров и их положения относительно поперечного паза; удобство установки закрепления и снятия заготовки.
Технические (тактико-технические требования)
Тип производства–единичное; программа выпуска-150год.
Регулирования конструкции приспособления не допускается. Время закрепления заготовки не более 069мин. Уровень унификации и стандартизации деталей приспособления 75%. Входные данные о заготовке: диаметр заготовки: 50-010 мм Rz 20 мкм;
Длина заготовки 60-040 мм шероховатость торцов заготовки Ra =2.5мкм.
Выходные данные операции:
Диаметр отверстия 6+0048мм; Глубина отверстия на проход; ширина паза 3+025мм; глубина паза 5+03мм. Характеристика режущих инструментов:
Сверло 035-2300-1225 Р6М5 ОСТ 2И20-1–80
Режимы резания штучное время на операцию приведены в операционной карте.
ЭЧ .doc
Разрабатываемая система предназначена для увеличения скорости проверки качества деталей типа «вал» (круглый стальной прокат различного диаметра).
Преимущество установки в синхронизации работы системы подачи контроля и маркировки дефектных зон. Когда скорость подачи регулируется системой чтобы не влиять на точность контроля а краскоотметчик успевает точно пометить зону дефекта.
К моменту расчета мы обладаем следующими исходными данными:
-схема электрическая принципиальная
-рабочий технологический процесс
Поэтому для определения себестоимости проектируемого изделия должен быть использован точный метод расчета.
Целью расчета является определение оптовой цены прибора и экономического эффекта.
1. Определение стоимости основных материалов
Общая стоимость материалов в проектируемых приборах:
661руб.х 107=124773руб.
CМ - затраты на сырье и материалы;
n – количество типов изделий;
НТЗ – транспортно-заготовительные расходы составляют 7% от стоимости материалов.
Результаты расчет стоимости основных материалов на изготовление сведены в таблице 4.1.
Результаты расчет стоимости основных материалов на изготовление
Сталь конструкционная углеродистая
Сталь конструкционная легированная
2 Определение стоимости покупных изделий.
Общая стоимость покупных изделий рассчитывается по формуле:
СП – общая стоимость покупных изделий руб.;
НТЗ – транспортно-заготовительные расходы 7% от стоимости покупных изделий
Результат расчета стоимости покупных материалов и изделий для проектируемого прибора представлен в таблице 4.2.
Результат расчета стоимости покупных материалов и изделий
Продолжение таблицы 4.2
К10-17в-М1500-2200пФ
К10-17в-М1500-5600пФ
Мост выпрямительный М2 ТПК-125-1
Трансформатор ТИМ-187В
3 Определение основной заработной платы производственных рабочих.
Расчет основной заработной платы (ЗО) сведен таблицу 4.3.
Размер прямой заработной платы определяется исходя из суммарной трудоемкости изготовления прибора по каждой операции и тарифной ставке данной операции.
Расшифровка трудовых затрат на изготовление одного образца
Суммарная трудоемкость в норма часах
Тарифная ставка руб.
Тарифная заработная плата руб.
4 Определение дополнительной заработной платы.
Дополнительная заработная плата составляет 15% от размера основной заработной платы .
НД – норма дополнительной заработной платы (НД).
5 Определение величины отчислений на социальные нужды.
Отчисления на социальные нужды принимаются равным 302% от суммы основной и дополнительной заработной платы:
Отчисления делаются в: а) в пенсионный фонд РФ -22% ; б) фонд социального страхования (29%)-отчисления в фонт временной нетрудоспособность материнства и детства; 02 – страховые отчисления на риск профессиональных заболеваний (проектная деятельность);
в) фонд обязательного медицинского страхования (5.1% в федеральный бюджет).
Отчисления на социальное страхование рассчитывается по формуле:
где НСС – норматив отчислений на социальные нужды (НСС=302%).
6 Определение величины накладных расходов.
Данная статья является комплексной и включает в себя расходы связанные с эксплуатацией оборудования; с использованием электроэнергии; с выплатой заработной платы работникам заводоуправления; вспомогательным и обслуживающим рабочим; со стоимость различных заводских работ; с текущим ремонтом оборудования и транспортных средств и др.
Величина накладных расходов берется в размере 212% от основной заработной платы производственных рабочих.
Величину накладных расходов определяется по формуле:
РОП– величина накладных расходов;
НОП– норматив накладных расходов НОП=212%.
7 Определение производственной себестоимости.
Величина производственной себестоимости рассчитывается путем суммирования всех вышеизложенных пунктов:
СПр=СМ+СП+ЗО+ЗД+ ЗСС +РОП
Для проектируемой системы
СПр=137250+2849495+528230+79235 +183454+1119848=4897512руб.
8 Определение коммерческих расходов.
Коммерческие расходы составляют 5% от производственной себестоимости:
9 Определение полной себестоимости.
Полная себестоимость рассчитывается как сумма производственной себестоимости и коммерческие расходы:
С= СПр+РК= 4897512+ 244876руб.=5142388 руб.
10 Определение прибыли
Прибыль составляет 20% от полной себестоимости:
П=5142388 * 02=1028478 руб.
11 Определение оптовой цены приборов.
Оптовая цена рассчитывается как сумма себестоимости и планируемой прибыли:
Для проектируемой системы:
ЦО=5142388 +1028478=6170866руб
Калькуляция себестоимости изготовления системы
Наименование калькуляционных статей
Покупные комплектующие изделия
Основная заработная плата производственных рабочих
Дополнительная заработная плата
Отчисления на соцстрахование
Итого: производственная себестоимость
Коммерческие расходы
Итого: полная себестоимость
Таким образом себестоимость изготовления опытного образца
составляет : 48975рублей а расчетная оптовая цена 6170866 рублей.
При этом максимальную долю расходов в цене и себестоимости прибора составляют покупные комплектующие изделия 4617 % далее идут накладные расходы 1815 %далее идет основная заработная плата 856%.
Снижение производственной себестоимости возможно по следующим напра-лениям:
-поиска более дешевых комплектующих изделий ;
-совершенствование конструктивных решений;
-совершенствование технологии изготовления.
ПЛАКАТ.doc
Покупные комплектующие изделия
Основная заработная плата производственных рабочих
Дополнительная заработная плата
Отчисления на соцстрахование
Производственная себестоимость
Коммерческие расходы
Полная себестоимость
Приспособление для фрезерного станка.dwg

Технические характеристики
Усилие зажима на плунжере 12600
Неуказанные предельные отклонения IT14(it14)
Острые кромки притупить.
Трущиеся поверхности смазать смазкой ЭРА.
гидравлическом цилиндре - 10 МПа.
Номинальное рабочее давление гидропласта в
Объем заполняемый гидропластом в гидравлическом
для фрезерного станка
Технология механообработки ролика.dwg

Резец К.01.4980.000-02 ВК8 ТУ-035-1040-86
Резец К.01.4980.000-02 ВК4 ТУ-035-1040-86
Резец 035-2126-1177 ВК8 ОСТ 2И10-7-84
Сверло 035-2300-1225 Р6М5 ОСТ 2И20-1-80
Развертка 2363-0062 Р6М5 ГОСТ 1672-80
Фреза 2240-0374 Р6М5 ГОСТ 3755-78
механической обработки
Графическая технология
Резец MWLNR1616Н06 ВК8 ТУ 2-035-892-82
Резец MTGNR-1616K16 ВК8 ТУ 19-4206-96-83
Резец К.01.4981.000-02 ВК8 ТУ 2-035-1040-86
Резец MTGNR-1616K16 ВК4 ТУ 19-4206-96-83
Спецификация Узел контроля.dwg

Узел контроля - Общий вид.dwg

Подключение электрической аппаратуры проводить
в соответствии с монтажной электрической схемой.
Не параллельность осей направляющих роликов
обеспечить не более 20
Алгоритм проведения контроля.dwg

Программа и методика
На основании полученных данных принять
решение о годности контролируемого объекта
или проведении дополнительных мероприятий.
качества поверхности
Протянуть контролируемую
проволоку через датчик и закрепить
её конец на приемной бабине
маркировщик и датчик
Включить все элементы
и начать процесс контроля
Протянуть контролируемый
провод через датчик и закрепить
его конец на приемной бабине
Перед началом контроля
произвести исследование
подать питание к системе
Контроль работоспособности
и точности показаний
Принципиальная схема.dwg

- Бабина с контролируемым валом
- Направляющие ролики
- Центрирующие ролики
- Контролирующий датчик
- Бабина с проконтролированным валом
Электрическая схема.dwg

Вилка ГРПМШ1-45ШУ2-В НЩО.364.016 ТУ
Конденсаторы К50-24В ОЖО.464.137ТУ К50-24В-16В-47 мкФ
Конденсаторы К50-24В ОЖО.464.137ТУ К50-24В-63В-220 мкФ
Конденсаторы К50-24В ОЖО.464.137ТУ К10-17а-Н90-0
Конденсаторы К50-24В ОЖО.464.137ТУ К10-17а-Н50-0
Конденсатор КМ-6б-Н90-2
Микросхема КР142ЕН5А бКО.348.107 ТУ-77
Микросхема К561ЛА7 бКО.347.314-01 ТУ
Микросхема К561ТМ2 бКО.347.314-01 ТУ
Микросхема К561ЛН2 бКО.348.457ТУ12
Микросхема PIC 16F628A фирмы Microchip
Светодиод АЛ307Г аАО.336.076ТУ СП5-14-2
Резистор С5-35В ОЖО.467.551 ТУ С2-33Н-0
Резистор С5-35В ОЖО.467.551 ТУ С5-35В-10-2 Ом
Резистор С5-35В ОЖО.467.551 ТУ МЛТ-0
Резистор С5-35В ОЖО.467.551 ТУ МЛТ-2-220 Ом
Резистор С5-35В ОЖО.467.551 ТУ МЛТ-2-120 Ом
Резистор С5-35В ОЖО.467.551 ТУ С5-16МВ-5-0
Резистор С5-35В ОЖО.467.551 ТУ МЛТ-2-180 Ом
Диод 2Д202В УЖ3.362.036ТУ
Диод 2Д206А 3.362.113 ТУ
Диод КД510А ТТЗ.362.100 ТУ
Стабилитрон КС447А аАО.336.001 ТУ
Стабилитрон Д818Е СМЗ.362.045 ТУ
Транзистор КТ972Б аАО.336.453 ТУ
Транзистор КТ503А аАО.336.183 ТУ
Транзистор КТ809А аАО.365.003 ТУ
Транзистор КТ816Г аАО.336.186 ТУ
Транзистор КТ817Г аАО.336.187 ТУ
Вилка ГРПМ9-18ШУ2-В КеО.364.009 ТУ
Индикатор цифровой АЛС333А
Вилка ГРПМ9-30ШУ2-В КеО.364.009 ТУ
Предохранитель ВП1-1-1А ОЮО.480.003 ТУ
Генератор звука SCO715BLLF фирмы SONITRON
Индикатор АЛ307Б аАО.336.07602 ТУ
Индикатор АЛ307Г аАО.336.07602 ТУ
Выключатель ВК33Н19Б20 181-20 УХЛ4
Кнопка КМ2-1 ОЮО.360.011 ТУ
Трансформатор ТАН69-220-50
Вилка ВД1-1 ГАО.364.010 ТУ
Розетка 2РМД18Б4Г5В1 ГЕО.364.126 ТУ
Розетка ШР20П5ЭГ10 ГЕО.364.107 ТУ
Розетка РС-4ТВ АВО.364.047 ТУ
Розетка ГРПМШ1-45ГО2-В НЩО.364.016 ТУ
Розетка ГРПМ9-18ГО2-В КеО.364.009 ТУ
Розетка ГРПМ9-30ГО2-В КеО.364.009 ТУ
Клемма КП-1а ГаО.483.002 ТУ
Конденсатор К50-24В-63В-470 мкФ
Конденсатор К50-12-160 В-100 мкФ
Конденсаторы К10-17б ОЖО.460.107 ТУ К10-17б-Н50-300 пФ
Конденсаторы К10-17б ОЖО.460.107 ТУ К50-35-16В-100 мкФ
Конденсаторы К10-17б ОЖО.460.107 ТУ К10-17б-Н50-0
Конденсаторы К10-17б ОЖО.460.107 ТУ К10-17б-Н50-3300 пФ
Конденсаторы К10-17б ОЖО.460.107 ТУ К53-4А-16В-47 мкФ
Конденсатор КМ-6б-Н90-0
8 мкФ ОЖО.460.161 ТУ
Микросхема К544УД1 бКО.347.040 ТУ
Микросхема К521СА3 бКО.347.015 ТУ
Микросхема К176ИЕ4 бКО.348.047 ТУ
Резисторы С2-33 ОЖО.467.093 ТУ C2-33-0
Резисторы С2-33 ОЖО.467.093 ТУ CП5-22-1-10 кОм
Мост выпрямительный КЦ405Г УФО.336.006 ТУ
Мост выпрямительный КЦ407А ТТЗ.362.146 ТУ
Стабилитрон 2С530А СМ3.362.823 ТУ
Транзистор КТ805БМ аАО.336.341 ТУ
Транзистор КТ815Г аАО.336.185 ТУ
Транзистор КТ315А ЖКЗ.365.200 ТУ
Вилка РС-4ТВ АВО.364.047 ТУ
Стол контроля - Общий вид.dwg

Подключение электрической аппаратуры проводить
в соответствии с монтажной электрической схемой.
Не параллельность осей направляющих роликов
обеспечить не более 20
Функциональная схема .dwg

ПЛАКАТ2.doc
Покупные комплектующие изделия
Основная заработная плата производственных рабочих
Дополнительная заработная плата
Отчисления на соцстрахование
Производственная себестоимость
Коммерческие расходы
Полная себестоимость
Спецификация Узел маркировки.dwg

Маркировщик - Общий вид.dwg

ролика маркеровщика и осей роликов стола контроля не более 20
Регулировка положения маркера осуществлять при настройке
системы с помощью специализированного винта крепления.
Предварительное натяжение пружины обеспечить путем подбора
и регулировкой хода якоря электромагнита
позиция 9 (смотри документацию на электромагнит).
ПРИЛОЖЕНИЯ.doc
Алгоритм управления установкой дозирования и маркировки брака вала
1 Назначение алгоритма
Алгоритм управления предназначен для осуществления автоматизированного управления технологическим процессом дозирования чернильного маркирующего раствора и маркировки брака вала в составе системы автоматизированного контроля качества изготовления изоляции
кабельной продукции.
Алгоритм управления должен обеспечивать устойчивое ведение процесса дозирования и маркировки путем поддержания переменных процесса в регламентных границах в течение работы промышленной установки контроля качества вала. (за исключением пускового режима и остановки).
Главной целью автоматизированного управления является повышение технико-экономических показателей качества продукта и снижение влияния человеческого фактора на параметры технологического процесса. Снижение влияния человеческого фактора на технологический процесс обеспечивается выводом человека из непосредственных контуров управления технологическими переменными.
2Общие требования к входным и выходным данным
Для совместимости решаемых задач предусмотрена кодировка технологических участков (блоков) входныхвыходных сигналов контроллера технологического оборудования и исполнительных механизмов.
Погрешность измерения технологических переменных используемых в алгоритме не должна превышать 1%.
Используемая информация
1.Массивы информации сформированные из входных сообщений
Перечень необходимых сигналов для работы алгоритма приведена в таблице П2.1.
Таблица П2.1 - Перечень входных сигналов алгоритма
Сигнал верхнего ограничителя хода поршня
Сигнал нижнего ограничителя хода поршня
Уровень технологического раствора в дозирующем устройстве
Температура технологического раствора в дозирующем устройстве
2.Массивы информации сформированные на выходе алгоритма
Перечень выходных сигналов алгоритма приведен в таблице 2.2.
Таблица П2.2 - Перечень выходных сигналов алгоритма
Направление вращения шагового двигателя
Математическое описание
Оператор задаёт расход литры в час затем контроллер преобразует этот расход в 32 битный код который отправляется на генератор частоты. Необходимость преобразования расхода в код вызвана тем что частотный генератор который управляет скоростью шагового двигателя сделан в программном комплексе MPlab на языке Assembler. Данный генератор формирует частоту в зависимости от кода поданного на вход данный код представляет собой целое число от 1 до 65535 наименьшее значение кода соответствует максимальной частоте равной 35084 Гц. Контроллер переводит расход в код по формулам:
где x - это полученный код.
На рисунке П2.1 представлена диаграмма зависимости кода от расхода.
Рис. П2.1 Диаграмма зависимости кода от расхода.
1.Описание логики алгоритма
Алгоритм управления маркерно-дозирующим устройством входит в состав системы управления контроля качества вала.
Алгоритм работает в циклическом режиме и включает следующие модули:
- расчет частоты вращения двигателя;
- обеспечение необходимого расхода маркирующих чернил;
- поддержание температуры маркирующих чернил в заданном пределе;
2.Точность вычисления
Точность производимых вычислений по формулам раздела 4 должна соответствовать операциям с плавающей точкой формата «float32».
3 Связи между частями и операциями алгоритма
На рисунке П.2.2 представлена обобщенная схема алгоритма управления маркерно-дозирующим устройством. В начале алгоритма основные входные переменные (смотрите таблицу П.1) проверяются на достоверность (попадание в допустимые диапазоны изменения). Если входные данные не достоверны то алгоритм отключается.Следующим шагом выполняется разгон двигателя (из-за особенностей ШД перед началом работы его необходимо разогнать).
Рис П.2.2 Обобщенная схема алгоритма управления маркерно-дозирующим устройством.
Затем выполняется расчет необходимой частоты вращения ШД в зависимости от необходимого расхода маркировочных чернил.
Следующим шагом включается модуль управления ШД который по сигналу с контроллера задает частоту и направление вращения ШД.
Когда маркировочные чернила закончились открываются клапаны подачи маркировочных чернил.
Далее алгоритм циклично запускается на следующем такте работы системы.
Технические характеристики модулей входящих в состав КУ «Каскад»
Технические характеристики
Количество мест для установки сменных моду лей ввода- вывода (слотов)
Тип микроконтроллера
Внутренний интерфейс (шина данных)
Разъемы для подключения внешних цепей
Напряжение питания не более
Потребляемая мощность не более
Микропроцессорный модуль
Интерфейс для связи с внешним компьютером
Потребляемый ток не более
Модуль дискретных входов
Количество входных дискретных каналов
Входной ток не более
Задержка включения не менее
Задержка выключения не менее
Напряжение гальванического разделения между группами каналов между каналами и корпусом не менее
Сопротивление изоляции между группами каналов и корпусом не менее
Модуль дискретных выходов
Количество выходных дискретных каналов
Сопротивление подключаемой нагрузки не более
Напряжение на выходе
Задержка времени включения (активная нагрузка)
Задержка времени выключения (активная нагрузка)
Выход в состоянии ON: в системе фиксируется «0»
Выход в состоянии OFF: в системе фиксируется «1»
Каналы после сброса: OFF
Модуль преобразования напряжения
Потребляемая мощность
Сопротивление изоляции между входными цепями и корпусом между выходными цепями и корпусом не менее
Степень защиты корпуса IP20
Габаритные размеры устройства
Для крепления на DIN рельс. 110х116х85 мм
Программное обеспечение
Программное обеспечение для маркера –дозатора.
Программа разработана для микроконтроллера PIC 8616 1.Описание переменных программы управления дозатором
PROGRAM PLC_PRGVAR_INPUT
(*Входные величины*)
f_rab f_raz1f_raz2t_raz:
(*Выходные величины*)
o_ako_kbgranagranbt_razS:
Основное тело программы управления установкой дозированияttemp:=1(*время импульса при макс частоте*)
tconst:=(*время половины импульса*)
t(*время полученное в зависимости от частоты заданной оператором*)
IF f_razgon=FALSE THEN
IF f_razgon=TRUE THEN
IF f_raz1=0 AND f_raz2=0 THEN (*Остановка программы*)
f_raz1:=0; f_raz2:=0; f:=0; m:=0; c:=0; c_out:=0; t_raz:=0;
b:=a+1;(*Полученное значение*)
grana:=INT_TO_REAL(a);
granb:=INT_TO_REAL(b);
o_ak:=(k-grana)*100000; (*Вычисление границы A*)
o_kb:=(granb-k)*100000; (*Вычисление границы B*)
t_ak:=REAL_TO_TIME(o_ak);
t_kb:=REAL_TO_TIME(o_kb);
IF a=k AND finput>0.0 THEN
TONInst(IN:=TRUEPT:=t
IF TONInst.PT=tim AND TONInst.ET=TONInst.PT THEN
IF d=0 AND finput>0 AND a>k AND l=TRUE THEN (*Переход на
действие поддержания границы А*)
IF d=1 AND finput>0 AND a>k AND l=TRUE THEN (*Переход на
действие поддержание границы В*)
Действие первое - разгон двигателя
IF f_raz1>0 THEN (*Проверка условия перехода на это действие*)
t_razt:=REAL_TO_TIME(t_razS); (*Определение временного интервала для разгона*)
IF f=0 THEN (*Присвоение выходу начального кода*)
TPInst(IN:=TRUEPT:=t_razt);
IF TPInst.ET=TPInst.PT AND c>m THEN (*Уменьшение кода если разгон*)
IF TPInst.ET=TPInst.PT AND cm THEN (*Увеличение кода если торможение*)
(Выход из действия*)
f_raz1:=0;f_raz2:=0;f:=0;TPInst(IN:=FALSE);
Действие второе - поддержание первого кода
IF finput>0.0 AND d=0 THEN (*Присвоение выходу первого кода*)
TONInst(IN:=TRUEPT:=t_kb);
IF TONInst.ET=t_kb AND TONInst.ET=TONInst.PT THEN (*Проверка условия выхода действия*)
Действие третье - поддержание второго кода
IF finput>0.0 AND d=1 THEN (*Присвоение выходу второго кода*)
TONInst(IN:=TRUEPT:=t_ak);
IF TONInst.ET=t_ak AND TONInst.ET=TONInst.PT THEN (*Проверка условия выхода из действия*)
Программное обеспечение маркера –дозатора.
Описание применения
Система управления предназначена для управления приводами дозирующих устройств и клапанами заполнения по информации с концевых контактов и датчиков уровня установленных на дозирующих устройствах.
Ограничивают ход поршня концевые контакты верхнего и нижнего положения. При срабатывании концевых контактов система управления формирует команду остановки шагового двигателя.
Изменение параметров настройки программы управления дозатором производится по интерфейсу RS-232 с протоколом «ModBus».
Для работы программного обеспечения необходим быстродействующий однокристальный микроконтроллер со встроенной периферией. Требования к микроконтроллеру:
процессор с архитектурой «ARM7TDMI»: 32-разрядная RISC-архитектура поддержка 16-разрядных инструкций;
объем FLASH-памяти (перепрограммируемого ПЗУ): не менее 256 кб;
объем ОЗУ: не менее 32 кб;
встроенная периферия: 16 канальный АЦП 3 канальный 16-разрядный таймер интерфейс UART.
Системное программное обеспечение должно выполнять следующие функции:
вводвывод данных по дискретным и аналоговым линиям;
обмен данными по протоколу «ModBus RTU» через интерфейс RS-232;
формирование заданных временных интервалов;
управление задачами включая задачи пользователя;
Взаимодействие программы алгоритма управления дозатора с системным обеспечением должно выполняться по механизму «общая память» - обмен данными между задачами должен выполняться через глобальные переменные.
Программа алгоритма управления дозатора должна решать следующие задачи:
обеспечение заданного расхода маркировочных чернил;
осуществлять защиту от противоречивых команд;
реализация алгоритмов управления дозирующими устройствами в автоматическом и ручном режиме;
осуществлять управления приводами дозаторов и клапанами заполнения по информации с концевых контактов и датчиков уровня;
выполнять контроль температуры маркировочных чернил и отключать дозаторы при аварийной ситуации.
Поставленные задачи выполнены с использованием следующих решений:
концевые датчики необходимые для ограничения хода поршня датчики температуры маркировочных чернил;
использование режима реального времени - управляющая программа запускается с постоянным периодом;
формирование управляющих сигналов для шаговых двигателей и клапанов заполнения.
ВХОДНЫЕ И ВЫХОДНЫЕ ПЕРЕМЕННЫЕ
Входными переменными программы алгоритма управления дозатором являются:
дискретные сигналы сигнализатора уровня концевых контактов верхнего и нижнего положения;
управляющая частота;
аналоговый сигнал контроля температуры.
Выходными переменными программы алгоритма являются:
код рассчитанный в зависимости от расхода;
логические переменные управления работой шагового двигателя (пускстоп).
Руководство системного программиста
Общие сведения о программе
Программа предназначена для автоматизированного управления дозатором маркировочных чернил.
Программа обеспечивает выполнение следующих функций:
формирование управляющих сигналов для шагового двигателя;
реализация защиты устройства от противоречивых команд;
формирование сигнализации о некорректной работе устройства.
Для работы программного обеспечения необходим быстродействующий однокристальный микроконтроллер со встроенной периферией. Требования к микроконтроллеру: процессор с архитектурой «PIC» объем FLASH-памяти (перепрограммируемого ПЗУ) не менее 256 кб объем ОЗУ: не менее 32 кб встроенная периферия (16-канальный АЦП 3 канальный 16-разрядный таймер интерфейс UART).
Системное программное обеспечение должно выполнять следующие функции: вводвывод данных по дискретным и аналоговым линиям фильтрацию входных сигналов обмен данными по протоколу «ModBus RTU» через интерфейс RS-232 формирование заданных временных интервалов управление задачами включая задачи пользователя управление модулем шагового двигателя управление драйвером шагового двигателя. Взаимодействие программы алгоритма управления дозатора с системным обеспечением должно выполняться по механизму «общая память» – обмен данными между задачами должен выполняться через переменные.
На рисунке П6.1 представлена структура программы.
Рисунок П6.1 – Структура программы
Программное обеспечение дозирующего устройства состоит из двух подсистем:
Микроконтроллер «PIC»;
программа пользователя – программа алгоритма управления дозатором.
Обмен данными между этими модулями осуществляется через переменные расположенные в общей памяти системы «PIC». Программа алгоритма дозатора получает входные переменные из общей памяти и записывает результаты расчетов в переменные общей памяти.
Микроконтроллер выполняет функции: вводвывод данных по дискретным и аналоговым линиям фильтрацию входных сигналов обмен данными по протоколу «ModBus RTU» через интерфейс RS-232 формирование заданных временных интервалов управление задачами включая задачи пользователя Управление модулем шагового двигателя.
Программа пользователя состоит из модулей (блоков программы):
контроль температуры (технологического раствора);
контроль уровня (технологического раствора);
блок контроля хода (поршня);
блок открытия закрытия клапанов заполнения.
Модуль контроля температуры и уровня выполнен на датчиках установленных внутри дозатора. Блок входов представляет логическую схему реализованную с помощью логических операций «И» «ИЛИ» «НЕ» с использованием операций сравнения и триггеров. Блок контроля хода выполнен на концевых датчиках верхнего и нижнего положения.
Переменные расположенные в общей памяти доступны для чтения и изменения по интерфейсу RS-232 с протоколом «ModBus RTU».
Исходный текст программы алгоритма управления дозатором должен быть включен в проект сборки программного обеспечения системного ядра «PIC». Входныевыходные переменные должны быть согласованы с соответствующими переменными для процессоров PIC.
Компиляция и сборка исходного текста программы осуществляется с помощью среды разработки «CoDeSys v.2.3» функционирующей под операционной системой «Windows 2kXP2k3». Программирование микроконтроллера осуществляется из среды «CoDeSys v.2.3» через программатор подключенный к персональному компьютеру с интерфейсом «JTAG».
Для проведения настроек управления отладки и тестирования используется программа «CoDeSys v.2.3» функционирующая под операционной системой «Windows 2kXP2k3». В настройках проекта программы «CoDeSys v.2.3».
После запуска программного обеспечения дозатора необходимо записать в контроллер параметры настройки дозатора доступные по протоколу «ModBus» с помощью «CoDeSys v.2.3». Настройки должны быть рассчитаны в соответствии с параметрами подключенного к устройству шагового двигателя.
Проверка программы алгоритма устройства управления дозатора осуществляется с помощью программы «CoDeSys v.2.3 при пустом баке дозатора:
)после запуска устройства управления дозатора необходимо скорректировать параметры настройки модуля по мере необходимости;
)ввести поочередно команды управления – открытие закрытие регулирующего органа стоп;
)при правильной работе алгоритма т.е при начале движения поршня можно заливать технологический раствор;
)при неправильной работе программы необходимо необходимо проверить и при необходимости изменить алгоритм устройства управления дозатора.
Сообщения системному программисту
Настройка программы не предусматривает выдачу сообщений системному программисту. Настройка программы выполняется в соответствии с п.п. 3 и 4.
Логические переменные информирующие о превышении температуры и уровня технологического раствора доступны по интерфейсу RS-232 с протоколом «ModBus». Сигнализацию о режиме работы устройства управления дозатора необходимо выполнять на автоматизированном рабочем месте оператора с применение мнемосхем SCADA-системы.
Результаты работы программы управления при рабочей частоте
Результаты работы программы управления при разгоне двигателя
001.П А Т Е Н Т Ы .doc
о патентных исследованиях по дипломному проект
« Автоматизированная установка вихретокового контроля детали типа «вал»
Задача патентных исследований – исследование технического уровня .
Цель поиска информации: получение информации об устройствах вихретокового контроля
Задание на проведение патентного поиска
Студент Фуфаев О.К.
Название предмета поиска подлежащего патентной проработке:
Устройства и способы вихретокового контроля
Страны и глубина поиска: РФ Великобритания Франция
Германия СШАЯпония с 2012 по 2007 г.
Подпись руководителя проекта Белов С.А.
Подпись консультанта Тараскина Н.Н.
Подпись студента Фуфаев О.К.
Результаты проведения патентно-информационных исследований
1 По источникам патентной информации
которым проводился поиск
(изобретения модели).
Библиографические данные достаточные для их нахождения
Вихретоковый дефектоскоп и способ его настройки.
Патент № 2073232 2007г.
Способ вихретокового контроля и устройство для его осуществления.
Патент № 2365910 2009г.
Вихретоковый дефектоскоп для контроля длинномерных проводящих изделий
Патент № 23974862010
Цифровой вихретоковый дефектоскоп
Патент № 2411517 2011
Аналогов не обнаружено
Аналогов не обнаружено.
рефераты заявок на изобретения на английском языке
2 По источникам научно-технической информации
2.1. Кучинский К. И. Патерикин В. И. Плотников С. В. Вихретоковый
датчик для обнаружения дефектов поверхности катания колесных пар [Текст] К. И. Кучинский В. И. Патерикин С. В.Плотников Датчики и системы. - 2009 - №1. - С. 22-25.
2.2.Грошков Е.А. Кирпичев А.А. Клюшев А.В. Интеллектуальные вихрето-ковые датчиковые системы [Текст] Грошков Е.А. Кирпичев А.А. Клюшев А.В.Компоненты и технологии-2009-№1.-С.23-24.
2.3.Янгиров И. Ф. Математическая модель датчика неразрушающего
контроля [Текст] И. Ф. Янгиров Приборы и системы.
Управление контроль диагностика. - 2011 - №2. - С. 21-22.
Сравнительный анализ
Известен «Способ вихретокового контроля и устройство для его осуществления» (Пат. 2365910 )основан на использовании вихретокового преобразователя в виде параллельного колебательного контура который устанавливают в зоне контроля и периодически формируют в колебательном контуре собственные затухающие колебания по величине затухания судят об изменениях физико-механических параметров контролируемого объекта при этом колебательный контур периодически подключают к заряженному разрядному конденсатору для формирования в параллельном колебательном контуре собственных затухающих колебаний величину затухания переходного процесса измеряют путем детектирования фильтрации и интегрирования сигнала переходного процесса возникающего в контуре после каждого подключения его к разрядному конденсатору после окончания переходного процесса колебательный контур отключают от разрядного конденсатора после чего разрядный конденсатор подключают через зарядный резистор к источнику стабильного постоянного напряжения и вновь медленно заряжают разрядный конденсатор до напряжения источника.
Достоинство: повышение чувствительности и точности уменьшение потребляемой электрической мощности и более простая реализация схемы.
Недостатки: контроль исключительно малых объектов.
Известен «Вихретоковый дефектоскоп для контроля длинномерных проводящих изделий» (Пат. 2397486)который содержит последовательно соединенные генератор переменного тока вихретоковый дифференциальный преобразователь (ВТП) проходного типа компенсатор начальной ЭДС усилитель высокой частоты амплитудно-фазовый детектор фильтр нижних частот предварительный усилитель низкой частоты фильтр верхних частот регулируемый усилитель низкой частоты пороговое устройство блок управления сортировкой фазовращатель источник постоянного тока и соленоид причем генератор связан со вторым входом компенсатора напрямую а со вторым входом амплитудно-фазового детектора через фазовращатель при этом дефектоскоп дополнительно снабжен второй дифференциальной парой измерительных обмоток смещенной по оси ВТП на заданное расстояние аналого-цифровым преобразователем (АЦП) с помощью которого производится измерение выходных сигналов программно-управляемым микропроцессором вторым измерительным каналом состоящим из последовательно соединенных компенсатора начальной ЭДС усилителя высокой частоты амплитудно-фазового детектора фильтра нижних частот предварительного усилителя низкой частоты фильтра верхних частот регулируемого усилителя низкой частоты фазовращателя включенного между вторым выходом генератора и вторым входом дополнительного амплитудно-фазового детектора микропроцессор также связан по адресным шинам и шинам данных с генератором двумя фазовращателями двумя фильтрами верхних частот двумя регулируемыми усилителями низкой частоты АЦП пороговым устройством и блоком управления сортировкой.
Достоинство: повышение помехозащищенности дефектоскопа.
Недостатком такой системы является является её повышенная сложность и как следствие недостаточная надежность.
Известен «Цифровой вихретоковый дефектоскоп» (Пат. 2411517) содержит последовательно соединенные генератор и вихретоковый преобразователь подключенный к каналам измерения амплитуды и фазы выходного напряжения вихретокового преобразователя два преобразователя аналог-код подключенные к выходам каналов измерения амплитуды и фазы выходы преобразователей аналог-код присоединены ко входам логической схемы. Цифровой вихретоковый дефектоскоп снабжен переключателем соединенным входами с выходами логической схемы а выходами - с запоминающим устройством и сравнивающим устройством причем выходы сравнивающего устройства соединены с входами дисплея.
Достоинства: обеспечивает повышение точности и достоверности контроля сварных соединений за счет создания условий для проведения градуировки цифрового вихретокового дефектоскопа по эталонным образцам качественных и дефектных точечных сварных соединений изделий из немагнитных металлов
Недостаток :Не может быть использован для дефектоскопии длинномерных деталей типа «вал»т.к. предназначен для для дефектоскопии точечных сварных соединений из немагнитных металлов.
Известна статья Янгирова И. Ф. "Математическая модель датчика неразрушающего контроля". В работе описывается оригинальная конструкция электромагнитного преобразователя для неразрушающего контроля с повышенной избирательностью и разрешающей способностью к дефектам ферромагнитного
изделия. Разработана математическая модель датчика дефектоскопии с аналитическим расширением что позволяет создать инженерную методику расчета. Достоинством описываемого датчика является значительная точность контроля дефектов но данный датчик может использоваться исключительно в узкой области контролируемых материалов что не достаточно для проектируемой системы.
Из всех выявленных технических решений лучшим является
«Вихретоковый дефектоскоп и способ его настройки» (Пат.2073232) состоящий из последовательно соединенных автогенератора параллельный колебательный контур которого содержит вихретоковый преобразователь и конденсатор детектора и индикатораотличающийся тем что в него введены переменный резистор и катушка индукционности причем первая ветвь параллельного колебательного контура образована параллельно соединенными вихретоковым преобразователем и переменным резистором последовательно которым подключен конденсатор а вторая етвь состоит из катушки индуктивности. Обе ветви находятся в контролирующих элементах которые при помощи двигателя совершают в процессе контроля вращения на 360 . Основным преимуществом датчика является высокаячувствительность к небольшим поверхностным продольным дефектам. Это происходит за счет уменьшения размеров датчика и зоны контроля. Таким образом увеличивается относительный сигнал от дефекта. Следовательно вращающиеся датчики обнаруживают дефекты которые не могут обнаружить проходные датчики даже на пределе своей чувствительности. Так же данная система обладает значительной скоростью контроля до 50 ммин и возможностью вести контроль за длинномерными объектами типа «вал».
Данное техническое решение может быть использовано при проектировании Автоматизированной установки вихретокового контроля детали типа «вал» с учетом требований технического задания на дипломный проект.
6 ГО.doc
Чрезвычайная ситуация (ЧС) - состояние при котором в результате возникновения источника чрезвычайной ситуации на объекте определенной территории или акватории нарушаются нормальные условия жизни и деятельности людей возникает угроза их жизни и здоровью наносится ущерб имуществу населения народному хозяйству и окружающей природной среде.
Чрезвычайные ситуации могут быть классифицированы по значительному числу признаков. Так по происхождению ЧС можно подразделять на ситуации техногенного антропогенного и природного характера. ЧС также можно классифицировать по типам и видам событий лежащих в основе этих ситуаций по масштабу распространения по сложности обстановки тяжести последствий.
С каждым годом чрезвычайные ситуации порождаемые производственными и транспортными авариями катастрофами и стихийными бедствиями становятся все более частыми масштабными и опасными сопровождаются все большими человеческими жертвами материальным ущербом и деградацией природной среды.
Как свидетельствует анализ статистических данных большая часть чрезвычайных ситуаций в Российской Федерации возникает в регионах с высокой концентрацией промышленных предприятий с развитой сетью автомобильных и железных дорог. В основном это чрезвычайные ситуации техногенного характера (свыше 70% от общего числа).
Для решения задач предотвращения и ликвидации чрезвычайных ситуаций снижения возможных потерь населения и ущерба экономике в случае их возникновения в РФ создана и действует Единая государственная система предупреждения и ликвидации чрезвычайных ситуаций (РСЧС).
Правовая основа действия РСЧС регулируется Федеральным законом
“О защите населения и территорий от чрезвычайных ситуаций природного и техногенного характера” принятым Государственной Думой 11 ноября 1994 г.
Действие закона распространяется также на отношения возникающие в процессе деятельности предприятий учреждений и организаций независимо от их организационно-правовой формы в том числе и объектов промышленности. Таким образом планирование мероприятий по предупреждению и ликвидации чрезвычайных ситуаций является обязательным условием функционирования предприятия.
Создание структур ГО и ЧС на промышленном объекте подготовка Служб и формирований планирование и проведение мероприятий осуществляются на основании федеральных и областных Законов Постановлений Положений руководящих указаний городских органов ГО и ЧС приказов начальника ГО объекта.
Являясь составной частью городского звена (областной подсистемы единой государственной системы предупреждения и ликвидации чрезвычайных ситуаций РСЧС) объектовые органы ГО и ЧС имеют своей главной задачей: предупреждение возникновения ЧС защиту людей и снижение воздействия от ЧС техногенного природного и иного характера.
В настоящее время существуют два основных направления минимизации вероятности возникновения и последствий ЧС на промышленных объектах. Первое направление заключается в разработке технических и организационных мероприятий уменьшающих вероятность реализации опасного поражающего потенциала современных технических систем. В рамках этого направления технические системы снабжают защитными устройствами – средствами взрыво- и пожарозащиты технологического оборудования электро- и молниезащиты локализации и тушения пожаров и т.д.
Второе направление заключается в подготовке объекта обслуживающего персонала служб гражданской обороны и населения к действиям в условиях ЧС. Основой второго направления является формирование планов действий в ЧС для создания которых нужны детальные разработки сценариев возможных аварий и катастроф на конкретных объектах.
1 Краткая характеристика объекта и оценка обстановки.
На работоспособность промышленного объекта в условиях ЧС непосредственное влияние оказывает район его расположения характер застройки территории (структура тип плотность застройки) окружающие объект смежные предприятия транспортные магистрали естественные условия прилегающей местности и т.д.
Город Ковров — крупный промышленный центр расположен в северо-восточной части Владимирской области на правом берегу р. Клязьма в 64 км от города Владимира.
Предприятие расположено в юго-западной части города (в 2 км от центра) не является потенциально опасным продолжает работу в особый период.
Аварии в энергетических и водоканализационных сетях возгорание горюче-смазочных материалов и вылив химических веществ на гальваноучастке могут оказать локальное воздействие не выходящее за пределы объекта.
Кроме внутренних источников химических поражающих факторов имеются соседние объекты использующие в технологических процессах СДЯВ. Такими являются: молококомбинат (аммиак-2т) мясокомбинат (аммиак-5т) КЭМЗ ЗИД КМЗ городские очистные сооружения (хлор-10т) сыродельный цех молококомбината железнодорожная станция.
сильнодействующие вещества – яды (хлор и другие компоненты) – 15 тонн
лакокрасочные материалы – 16000 тонн различные пластмассы и полимерные соединения.
К числу СДЯВ и используемых в технологических процессах завода относятся: аммиак концентрированные кислоты (соляная серная азотная и фтористо-водородная) дихлорэтан толуол и перекись водорода. Наличие кислот на складе в среднем составляет:
соляная кислота – 63 тонны (эквивалент – 2 тонны хлора)
аккумуляторная – 59 тонн
фтористо-водородная – 1 тонна серная – 240 тонн.
На заводской АЗС и парке РВС хранятся:
горючие и легковоспламеняющиеся жидкости (ГЛВЖ): бензин керосин
дизельное топливо – 800 тонн
масла растворители – 220 тонн
обезводнееный мазут – 18 тонн.
В случае аварии (крушения) на железной дороге (станции) – удаление 15 км – при юго-западном ветре (со стороны КЭМЗ и прилегающей площади) сильно действующие ядовитые вещества (СДЯВ) через 3-10 минут могут достигнуть территории промышленной площадки и привести к чрезвычайной ситуации.
Наводнение (половодье) и дождевые паводки могут привести к подтоплению (затоплению) территории и подвалов зданий.
Сильный снегопад (град ураган смерч шквал) может быть причиной обрушения крыш зданий и других сооружений на промышленной площадке.
2 Сигналы оповещения
Своевременное оповещение и информирование персонала и населения о чрезвычайных ситуациях угрозе нападения противника и о необходимости принятия мер защиты является гарантией спасения возможно большего числа людей. Осуществляется оповещение с помощью сигналов ГО:
)«ВНИМАНИЕ ВСЕМ» - звучание сирен и теле- радио- речевое сообщение о ЧС;
)«ОБЪЯВЛЕН СБОР» («ПРОВЕРКА ВЫЗОВА») – по Стойке Циркулярного Вызова;
)«ВАС ВЫЗЫВАЕТ 225» - сигнал ОГВК (с информацией по Таблице сигналов).
Экстренная информация о ЧС передается с «паролем» срочности:
-по телефону – «БЕДСТВИЕ» и далее экстренное речевое сообщение;
-по телеграфу – «ШТОРМ» и далее соответствующая информация.
3 Режимы функционирования системы ГО и ЧС
В зависимости от прогнозирования и возникновения чрезвычайных ситуаций в мирное время установлены следующие режимы и действия по настоящему «Плану »:
) Режим ПОВСЕДНЕВНОЙ ДЕЯТЕЛЬНОСТИ (режим ПД);
)Режим ПОВЫШЕННОЙ ГОТОВНОСТИ (режим ПГ);
)Режим ЧРЕЗВЫЧАЙНОЙ СИТУАЦИИ (режим ЧС).
Порядок действий определяется приказом Начальника ГО промышленного объекта.
4 Действия объектовых органов ГО и ЧС
по предупреждению и ликвидации чрезвычайной ситуации
В отсутствии ЧС органы ГО работают в «Режиме ПОВСЕДНЕВНОЙ ДЕЯТЕЛЬНОСТИ».
При этом планируются и осуществляются мероприятия по предупреждению ЧС такие как: перспективное и текущее планирование мероприятий по ГО и ЧС расчет и выделение (резервирование) финансово-материальных ресурсов.
Проводится исследование возможности (вероятности) возникновения и развития ЧС анализ и оценка защищенности сотрудников и неработающего населения.
Так же осуществляется выработка мер по повышению устойчивости функционирования объекта и обеспечению надежности (дублирование) систем жизнеобеспечения; подготовка планово-распорядительных отчетных оперативных и других (в т. ч. формализованных) документов – в рабочих папках исполнителей.
Ответственными должностными лицами определяются необходимые мероприятия по ГО и ЧС.
Создание и подготовка сил и средств ГО и ЧС является неотъемлемой частью повседневной деятельности штаба ГО И ЧС предприятия.
Проводится обучение руководящего и командно-начальствующего состава (РКНС) комплектование оснащение и подготовка служб и формирований.
Контролируется содержание (строительство) коллективных средств защиты (убежищ) накопление и освежение средств индивидуальной защиты (СИЗ).
Осуществляется обслуживание (ремонт) коммунально-энергетических сетей поддержание исправности средств сигнализации и пожаротушения.
Проводятся командно-штабные и тактико-специальные учения тренировки рекогносцировка районов и маршрутов рассредоточения и эвакуации.
Наблюдение и прогнозирование обстановки осуществляется путем постоянного (круглосуточного) дежурства на участке связи (АТС) поддержания исправности и готовности средств связи и оповещения наблюдения и прогнозирования опасности снежных завалов половодья дождевых паводков загрязнения атмосферы почвы воды и т.п.
Кроме этого проводится периодическое измерение уровня радиоактивного излучения.
При угрозе возникновения производственных аварий катастроф и стихийных бедствий начальником ГО или председателем Комиссии по чрезвычайным ситуациям (КЧС) города начальником ГО или председателем КЧС предприятия вводится «Режим ПОВЫШЕННОЙ ГОТОВНОСТИ».
С позиции управления:
После приема сигнала об угрозе возникновения ЧС проводится оповещение и сбор руководящего состава оценка возможных масштабов ЧС комиссией по устойчивости и ЧС (КУЧС).
Управление переводится на председателя КЧС (Руководителя ликвидацией чрезвычайной ситуации) и начинается подготовка к действиям по «Плану » при возможной (конкретной) чрезвычайной ситуации.
Организуется информирование сотрудников об опасности возникновения ЧС и правилах поведения и защиты.
C точки зрения подготовки сил и средств:
При возникновении на предприятии АВАРИИ (КАТАСТРОФЫ ПОЖАРА ).
Проводятся работы по предотвращению возникновения локализации снижению воздействия чрезвычайной ситуации;
Организуется подготовка (отправка) отряда оперативного реагирования (ООР) развертывание доукомплектовывание дооснащение служб и формирований.
Осуществляется подготовка (выдача) снаряжения и имущества проверка техники защита энергосетей подготовка средств водозабора и пожаротушения.
При возникновении ЧС природного характера таких как БЕДСТВИЕ (НАВОДНЕНИЕ ПОЛОВОДЬЕ ПАВОДОК ).
Проводятся мероприятия по повышению устойчивости функционирования объекта (безаварийная остановка) защите подвальных помещений от затопления (обваловка зданий ) защите (сохранение перемещение) оборудования документации продовольствия.
При ВЫЛИВЕ (ЗАРАЖЕНИЕ СДЯВ РВ ).
Проводятся оборудование (приспособление) коллективных средств защиты людей и подготовка СИЗ и медицинских препаратов к применению (выдача формированиям);
Проверяются средства спецобработки (дегазации дезактивации и дезинфекции)
Осуществляется подготовка к эвакуационным мероприятиям (укрытие вывод маршруты указатели) и проверка готовности транспорта к массовой перевозке людей и грузов.
Необходимым этапом действий в режиме повышенной готовности являются разведка и оценка обстановки.
На этом этапе вводится оперативное дежурство руководящего состава (штаб ПУ ЗПУ) развертывается пост радиационно-химического наблюдения (ПРХН).
Проводится разведка в зоне вероятной ЧС оценка общей и метео- обстановки.
При возникновении и во время ликвидации чрезвычайной ситуации вводится «Режим ЧРЕЗВЫЧАЙНОЙ СИТУАЦИИ».
Функционирование объекта в режиме чрезвычайной ситуации регламентируется Таблицей 6.1.
Исполнители (службы)
Руководство ликвидацией ЧС
Прием сигнала и оповещение (по СЦВ) принятие предварительного решения по защите людей
Дежурный начальник СОС начальник ГО НШГО
Сбор руководящего и командно-начальствующего состава (РКНС) оценка масштабов ЧС
Начальник СОС председатель КУЧС
Ускоренное развертывание сил и средств определение порядка ликвидации ЧС
Все начальники Служб Руководитель ликвидацией ЧС
Действия сил и средств
А) Авария (катастрофа пожар )
От(под)ключение электропитания и воды спасение людей первая помощь пострадавшим
Тушение пожара (вызов пожарных машин) вынос и охрана имущества и документации
Аварийно-спасательные работы (АСР) и восстановление функционирования объекта
Б) Бедствие (наводнение )
Вывод (эвакуация) людей из опасных зон сохранение оборудования и продовольствия
СООП СУУ ТС СМТО СКОН
Ликвидация последствий стихийного бедствия (ураган смерч снег град гололед )
СОС СООП ТС СМТО СКОН
В) Вылив (заражение СДЯВ РВ )
Укрытие (вывод) и защита людей СИЗ продуктов воды спецобработка
Все службы и формирования
Первая медицинская помощь пострадавшим и восстановление систем жизнеобеспечения
Разведка контроль доклады
Общая (радиационно-химическая) разведка и токсо-дозиметрический контроль
ООР СРХЗ МС СООП СУУ
Контроль обстановки в зоне ЧС (охрана оцепление комендантская служба)
Взаимодействие со штабом ГО и ЧС города (связь доклады донесения информация)
НГО руководитель ликвидацией ЧС председатель КУЧС
Приведенный план действий по предупреждению и ликвидации ЧС в мирное время регламентирует действия руководящего состава служб и формирований ГО рабочих и служащих объекта в случае угрозы и возникновения ЧС а также профилактические меры в режиме нормальной обстановки.
Осуществление предложенного плана минимизирует людские и материальные потери в любой обстановке носящей чрезвычайный характер.
ОТ.doc
Основными носителями травмирующих и вредных факторов возникающих при эксплуатации установки могут являться конструктивные особенности промышленной установки повышенные уровни шума и вибраций электромагнитных излучений источники электроэнергии нерегламентированные действия работающих нарушения режимов и организации деятельности а также отклонения от допустимых параметров микроклимата рабочей зоны.
Рассмотрим каждый вариант нарушения с точки зрения требований стандартов.
1. Конструктивные особенности установки
В связи с конструктивными особенностями установки (наличие зоны автоматического перемещения высокие скорости перемещения исполнительных устройств) при её работе возможно воздействие на работающих физических опасных производственных факторов: подвижных частей (исполнительных устройств) установки; передвигающихся инструментов и материалов.
Основными причинами воздействия опасных производственных факторов при эксплуатации установки являются: непредусмотренные движения исполнительных устройств установки при наладке ремонте во время обучения и исполнения работы; внезапный отказ в работе установки; ошибочные (непреднамеренные) действия оператора или наладчика во время наладки и ремонта при работе в
автоматическом режиме; нарушение условий эксплуатации; нарушение требований безопасности труда при работе оборудования.
2.Электробезопасность
Основными причинами электротравм являются: прикосновение к конструктивным частям электросети и электрооборудования оказавшимся под напряжением при повреждении изоляции (например к корпусу электродвигателяимеющему замыкание на корпус или к электромагниту); нахождение вблизи места замыкания на землю (например вблизи оборванного электропровода упавшего на зем-
лю или касающегося земли); прикосновение к металлическим предметам случайно оказавшимся под напряжением; прикосновение к электрически заряженному электрооборудованию (конденсаторам кабелям);различные явления замыкания на землю короткие замыкания связанные с образованием электрической дуги.
3. Обеспечение безопасности при эксплуатации установки.
3.1. Электробезопасность
Электрооборудование установки должно удовлетворять требованиям безопасности по ГОСТ 12.1.038-82. То есть так как при работе приборов используется переменный ток с частотой в 50 Гц то предельно допустимые значения напряжений прикосновения и токов установлены в размере: U = не более 2 В I = не более 03 мА. Электрооборудование установки должно быть оснащено
пусковой аппаратурой исключающей самопроизвольное включение оборудования при восстановлении внезапно исчезнувшего напряжения.
Шумовые характеристики установки должны удовлетворять требованиям ГОСТ 12.1.003-83(1999). Так как установка будет установлена в производственном цехе то уровень шума составит не более 80 дБ что является максимальным допустимым значением шумовых помех.
3.3. Уровни вибрации
Уровни вибрации возникающей на рабочем месте оператора обслуживающего установку регламентируются по ГОСТ 12.1.012-90. Данный стандарт допускает повышение вибрационной нагрузки на оператора не более чем в 4 раза то есть не более 12 дБ. Так как установка расположена в чехе по производству и изолировании проводов то уровень вибрационной нагрузки составит не более чем 4 дБ с учетом возникновения возможных вибрационных нагрузок самой установки.
3.4 Пожаробезопасность
Установка должна удовлетворять требованиям пожарной безопасности по ГОСТ 12.1.044-89. В соответствии со стандартом так как в конструкции не применяются огнеопасные материалы и вещества а сама конструкция состоит из металлических частей работающая под напряжением то при пожаротушении необходимо применять порошковый огнетушитель и при возникновении опасной ситуации необходимо немедленно отключить питание прибора.
3.5. Освещенность рабочего места
Характеристики освещения рабочего места должны удовлетворять требованиям ГОСТ ИСО 8995-2002.
3.6. Микроклимат на рабочем месте
Уровень микроклимата на рабочем месте оператора обслуживающего установку регламентируется по ГОСТ 12.1.005-88. Данный вид работ подпадает под значение работ средней тяжести II а для которых определены характеристики: для холодного времени года Т = 18-20 °С относительная влажность 40-60% v движения воздушных масс 01 мс; для теплого времени года Т = 21-23 °С относительная влажность 40-60% v движения воздушных масс 03 мс.
3.7. Автоматика управления и безопасности установки
Система управления установкой должна иметь устройство аварийной остановки срабатывающее по команде оператора при нарушении работоспособности могущем привести к возникновению опасных факторов независимо от режима работы. При срабатывании устройства аварийной остановки должно прекратиться любое движение независимо от режима его работы как это предусмотрено при конструировании. Повторное включение после аварийной остановки должно осуществляться только после приведения всех исполнительных
органов в исходное положение и только по команде оператора.
4.Обязанности обслуживающего персонала
Перед началом работы должен быть произведен пробный цикл работы комплекса на холостом ходу. Оператор или наладчик должен убедиться в исправном состоянии установки и средств защиты и обеспечить устранение всех обнаруженных неполадок. Перед началом работы должна быть проведена тестовая проверка функционирования частей комплекса. При этом блокировочные устройства должны срабатывать в соответствии с электрической схемой. Неполадки и аварийные ситуации возникающие в процессе эксплуатации установки должны ежесменно регистрироваться оператором или наладчиком в специальном журнале форму которого устанавливает предприятие и утверждает главный инженер.
5.Безопасные приемы и методы работы при обучении
Запрещается выполнять ремонтные работы связанные с обслуживанием промышленной установки а также по присоединению и отсоединению рабочего органа без отключения питания. При выполнении работ в рабочем пространстве в месте включения питания должен быть вывешен плакат с предупреждающей надписью «Не включать. В рабочем пространстве проводится работа». Обучение и (или) наладка промышленной установки должны осуществляться в присутствии второго лица имеющего удостоверение на право обслуживания наблюдающего за безопасностью производства работ.
6.Расчет искусственного освещения
Важным вопросом охраны труда является освещение рабочего места. Правильно устроенное освещение обеспечивает хорошую видимость и создает благоприятные условия труда. Искусственное освещение по способу расположения источников света делятся на: общее местное и комбинированное.
Светотехнические расчеты являются основополагающими при проектировании осветительных установок. Задачей расчета обычно является определение числа и мощности светильников необходимых для получения заданной освещенности. Реже производятся проверочные расчеты т.е. определяется освещенность в определенных точках при заданных параметрах осветительной установки. При работе операторов установки используется общее освещение для расчета которого в условиях эксплуатации наиболее удобным и приемлемым является метод коэффициента использования светового потока.
6.1.Обеспечение требуемой освещенности.
Для обеспечения требуемой освещенности предусмотрена общая система искусственного освещения при которой светильники располагаются в верхней зоне помещения равномерно. Работа операторов связана с прочтением машинного текста и текста светящегося на экране.
Наименьший размер объекта различения 1-5 мм. поэтому предусматриваются следующие нормированные значения коэффициента естественной освещенности.
Характеристика зрительной работы высокой точности.
Разряд зрительной работы IIIб.
Контраст различения с фоном – средний.
Освещенность при общем освещении – 200 лк.
При верхнем освещении коэффициент естественной освещенности –5 %.
Нормирование значений освещенности коэффициента естественной освещенности на рабочих поверхностях при естственном и совместном освещении по указана в таблице 5.1
Разряд зрительной работы
Порядок расчета освещения по методу коэффициента использования светового потока сводится к следующему:
Определяется нормированное значение освещенности для общего освещения (E0).
Выбирается тип источника и светильника согласно требованиям.
Определяется высота подвеса светильников.
Находится расстояние между рядами светильников (L) крайним радом и стеной (I).определяется необходимое количество светильников N.
Требуется рассчитать освещение помещения по следующим данным:
Длина помещения А – 6 м.
Ширина помещения В = 4 м.
Потолок покрашен белой краской стены - светлой краской.
Нормативная освещенность для такого помещения составляет 600 лк для газоразрядных ламп и 300 лк для ламп накаливания. В общественных административных и подобных им зданиях из числа газоразрядных ламп должны применяться только люминесцентные лампы.
Люминесцентные лампы неизбежно применяются при повышенных требованиях к цветопередаче независимо от разряда работ.
Согласно этому для освещения берем люминесцентные лампы которые имеют ряд существенных преимуществ в числе которых:
Высокая световая отдача достигающая 75 лмВт.
Большой срок службы доходящий до 10.000 часов.
Возможность иметь источники света различного спектрального состава при лучшей для большинства типов цветопередачи чем лампы накаливания.
Относительно малая (хотя и создающая ослепленность) яркость что в ряде случаев является достоинством.
Так как условия среды нормальные то исходя из этого выбираем светильники с люминесцентными лампами (ЛБ-40) серии ЛСП02 условный номер группы 3.
Высоту свеса светильников принимаем равной hс = 0.25 м высота рабочей поверхности hр = 0.8 м (столы) тогда высота подвеса светильников:
h = H - hс – hр =3 –0.25 – 0.8 = 1.95 м.
Расстояние между рядами светильников по ширине здания:
где lc - светотехнические наивыгоднейшее расположение рядов светильников (находится по таблице).
Расстояние l между светильниками и стеной обычно принимается равным (025 03)L если рабочие места расположены у стен.
Число рядов светильников по ширине помещения:
М=(В – 2I)L+1=(4 – 2*0?68)273+1=1967
Определим коэффициент использования светового потока h характеризующий отношение потока падающего на расчетную поверхность к суммарному потоку всех ламп в функции индекса помещения и коэффициентов отражения стен рс и потолка рп рабочего оборудования ро по таблицам.
Индекс помещения вычисляется по формуле:
I=S[h*(A+B)] где S – площадь помещения.
l=4*6[195*(6+4)]=123
По таблице находим коэффициент использования светового потока
Для лампы ЛБ-40 (мощностью 40 Вт) световой поток составляет Фл = 2850 лм (данные берутся из таблицы «Технические данные люминесцентных ламп»).
Необходимое число светильников N=Ko*K*S*Zh*n*Ф
где К – коэффициент запаса характеризующий снижение освещенности при эксплуатации (данные из таблицы) для помещений с нормальной воздушной средой при газоразрядных лампах К = 15;
Z – коэффициент неравномерности характеризующий отношение средней освещенности к минимальнойZ=1.
n – число ламп в светильнике n = 2 шт.
Размещение светильников:
)Число светильников в ряду:
)Общая длина светильников в ряду Iобщ:
где lc – длина одного светильника по справочнику.
) Расстояние между светильниками в ряду ln (в том числе расстояние между столбом и крайним светильником в ряду)
ln=(A – lобщ)nn=(6-3711)4=057 м
где nn - число всех промежутков в ряду nn=4.
В результате проведенных расчетов получим что для требуемой освещенности вычислительного центра размерами 6*4*3 требуется 6 светильников ЛСП02 с лампами ЛБ-40 (в каждом светильнике 2 лампы) расположены в два ряда (рис. 5.1).
Рис.5.1 План расположения светильников.
ТЗ.doc
Государственное бюджетное образовательное учреждение
высшего профессионального образования
«КОВРОВСКАЯ ГОСУДАРСТВЕННАЯ ТЕХНОЛОГИЧЕСКАЯ АКАДЕМИЯ
имени В.А. Дегтярева»
Основание для разработки.
Учебный план по выполнению дипломного проектирования.
Цель разработки и проектирования.
Разработка автоматизированной установки для неразрушающего контроля (НК) широкого спектра деталей за счет универсальных возможностей быстрой перенастройки и адаптации к объектам различных форм и типоразмеров.
Технические требования.
1. Автоматизированная установка должна обеспечивать:
автоматическую стыковкурасстыковку необходимого преобразователя;
сканирование поверхности детали по заданной траектории;
отслеживание текущих координат рабочих преобразователей в реальном времени;
включение автоматической сигнализации дефекта (АСД);
анализ результатов контроля и запись в архив.
2. Технические параметры вихретокового режима:
Рабочий диапазон - 50кГц-5МГц;
Чувствительность контроля- Обнаружение трещин протяженностью не менее 3 мм с раскрытием в пределах от 005 до 1 мм
Удельная электропроводность: Вихретоковый контроль материалов с удельной электропроводностью (04-40)*106 Смм
Визуализация : Цветовая индикация дефектных участков контроля;
Управление: Наличие звуковой и световой сигнализации при обнаружении дефекта(ов) электропроводностью (04-40)*106 СМм.
3.Время непрерывной работы – неограниченно.
Конструктивные требования.
1. Массогабаритные характеристики составных частей автоматизированной установки должны быть минимальны.
2. Конструкция составных частей автоматизированной установки должна быть пыле-брызгозащищенной.
3. Конструктивно предусмотрено два варианта исполнения автоматизированной установки:
Настольный или встраиваемый - применяется для объектов контроля в поточно-серийном цикле с малыми геометрическими параметрами до 1000 мм3;
Портал - с дополнительными механизмами перемещения по высоте и ширине (система рассчитана на НК крупногабаритных объектов 2500х3000мм);
4.Требования по эргономичности в соответствии с ГОСТ 2300-78.
Требования к сырью и исходным материалам.
1. В конструкции автоматизированной установки должны максимально применяться материалы смазки краски в соответствии с ОСТ 83-3793-77 ОСТ 383-5688-74 ОСТ 3-1928-73 ОСТ 3-942-80 ОСТ 3-3368-76.
2. Номенклатура применяемых сортов и типов материалов должна быть минимальной.
Требования к прочности устойчивости устройства к воздействию внешних факторов.
1. Автоматизированная установка должна функционировать и сохранять свои параметры при воздействии:
1.1. изменения температуры окружающей среды от минус 400С до +400С при относительной влажности воздуха не более 95%;
1.2. вибрации частотой 50 Гц и 250 Гц с максимальным ускорением 50 мс2.
1.3. ударов многократного действия с максимальным ускорением 100 мс2 при длительности воздействия 5-20 мс. Количеством ударов – 10000.
1.4. влажной тепловой среды в течении 4 суток при температуре (40±2)°C и относительной влажности воздуха (95±3) %.
Требования к надёжности и долговечности.
1. Вероятность безотказной работы 095 за 1000 часов.
2. Назначенный срок службы – 10 лет.
3. Изделие в упаковке должно допускать транспортирование всеми видами транспорта.
Технико-экономические показатели.
1. Автоматизированная установка должна разрабатываться с максимальным применением стандартизованных и унифицированных сборочных единиц деталей и т.п.
Порядок разработки. Испытаний. Приёмки и окончания работ.
1. Еженедельное выполнение графика разработки дипломного проекта.
2. Стадия разработки КД – дипломное проектирование.
3. Окончание работ – защита дипломного проекта.
Титульник на ДП.doc
Государственное образовательное учреждение высшего профессионального образования
КОВРОВСКАЯ ГОСУДАРСТВЕННАЯ ТЕХНОЛОГИЧЕСКАЯ АКАДЕМИЯ
имени В.А. Дегтярева
ТЕМА ДИПЛОМНОГО ПРОЕКТА:
Автоматизированная установка вихретокового контроля детали типа «вал»
Допустить дипломный проект к защите в
Государственной экзаменационной комиссии
Рекомендуемые чертежи
- 18.08.2016
- 26.04.2016