Расчет конического редуктора




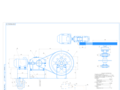
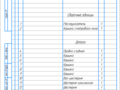
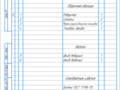
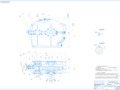
- Добавлен: 04.11.2022
- Размер: 4 MB
- Закачек: 0
Описание
Курсовой проект - Расчет конического редуктора
Состав проекта
![]() |
![]() |
![]() ![]() ![]() ![]() |
![]() |
![]() ![]() ![]() ![]() |
![]() ![]() ![]() ![]() |
![]() ![]() ![]() ![]() |
![]() ![]() ![]() ![]() |
![]() ![]() ![]() ![]() |
![]() ![]() ![]() ![]() |
![]() ![]() ![]() ![]() |
![]() |
![]() ![]() ![]() |
![]() |
![]() |
![]() |
![]() |
![]() ![]() ![]() |
![]() |
![]() |
![]() |
![]() |
![]() |
![]() |
![]() |
![]() |
![]() |
![]() |
![]() |
![]() |
![]() |
![]() |
![]() |
![]() |
![]() |
![]() |
![]() |
![]() |
![]() |
![]() |
![]() |
![]() |
![]() ![]() ![]() |
![]() ![]() ![]() |
![]() |
![]() |
![]() |
![]() |
![]() |
![]() |
![]() |
![]() |
![]() |
![]() |
![]() |
![]() |
![]() |
![]() ![]() ![]() ![]() |
Дополнительная информация
вал 3.frw

Редуктор.cdw

Техническиая характеристика
Тип редуктора коническо-цилиндрический
Передаточное число 48
Передаваемая мощность
Частота вращения выходного вала
Технические требования
Регулировка подшипников производить прокладками поз. 25
Плоскпсти разьемов покрыть пастой "Герметик"У-30М ГОСТ .
Масло в редуктор залить по верхнюю метку маслоуказателя
Подшипниковые камеры заполнить смазкой на 2 3 их объема
Спецификация к общему виду привода.spw

Шайбы 17 ГОСТ 10906-78
Шайба 16 ГОСТ 11371-78
Ремень Б-1600 ГОСТ 1284-80
Болт фундаментный изогнутый тип 1
Спецификация к редуктору.spw

Крышка смотрового окна
Винт М8х25 ГОСТ 1491-80
Болт М8х55 ГОСТ 7798-70
Болт М12х50 ГОСТ 7798-70
Болт М8х40 ГОСТ 7798-70
Болт М16х105 ГОСТ 7798-70
Гайка М12 ГОСТ 5915-70
Гайка М16 ГОСТ 5915-70
Шайба 8 Н ГОСТ 6402-70
Шайба 16 Н ГОСТ 6402-70
Шпонка 5х5х15 ГОСТ 23360-78
Шпонка16х9х52 ГОСТ 23360-78
Шпонка 14х8х48 ГОСТ 23360-78
Масло И-Г-А-46 ГОСТ 20799-88
Литол-24 ГОСТ 21150-87
Вал.cdw

После стуков вал должен проворачиваться свободно.
Технические характеристики
Общий вид привода.cdw

Частота вращения на выходе обмин 10.03
Крутящий момент на выходном валу редуктора
Передаточное число привода 48
- передаточное число 4
- передаточное число 11.5
Технические требования
Непараллельность осей шкивов не более 1мм ширины шкивов.
Смещение осей канавок шкивов не более 0.7 мм.
Покрытие рамы: эмаль ПФ-246 серая
колесо.cdw

Коеффициент смещения
Неуказанные предельные отклонения размеров
Данные для контроля зубчатого венца выбирают по ГОСТ 1643-81.
Неуказанные предельные отклонения размеров поверхностей
Данные для контроля зубчатого венца выбирают по ГОСТ
Технические характеристики
крышка.cdw

Технические характеристики.
Вал 2.frw

Эпюра.frw

Poyasnitelnaya_zapiska_k_KP_po_DMiOK.docx
Число деталей в сложных машинах достигает десятков тысяч. Выполнение машин из большого количества деталей вызвано необходимостью относительных движений частей. Однако неподвижные и взаимно неподвижные части машин (звенья) также делают из отдельно соединённых между собой деталей. Это позволяет применять оптимальные материалы восстанавливать работоспособность изношенных машин заменяя только простые и дешёвые детали облегчает их изготовление обеспечивает возможность и удобство сборки.
Детали машин как научная дисциплина рассматривает следующие основные функциональные группы:
) Корпусные детали несущие механизмы и другие узлы машин.
) Передачи – механизмы передающие механическую энергию на расстояние как правило с преобразованием скоростей и моментов иногда с преобразованием видов и законов движения.
) Валы и оси – для поддерживания вращающихся деталей.
) Вращающиеся валы или оси опираются на подшипники а поступательно перемещающиеся детали (столы суппорты и др.) движутся по направляющим.
) Муфты – для соединения валов. Эта функция может совмещаться с компенсацией погрешностей изготовления и сборки смягчением динамических воздействий управлением и т.д.
) Упругие элементы – предназначаются для виброизоляции и гашения энергии удара для выполнения функций двигателя (например часовые пружины) для создания зазоров и натяга в механизмах.
) Соединительные детали – являются отдельной функциональной группой. Различают неразъёмные и разъёмные соединения.
Кинематический расчёт привода.
1. Выбор электродвигателя.
Выбор электродвигателя по мощности.
Мощность на исполнительном органе привода:
где F и V – сила приложенная к исполнительному органу и линейная скорость исполнительного органа соответственно.
Потребная мощность двигателя:
где – мощность на выходе привода.
Среднеквадратичная мощность двигателя:
где – коэффициенты (из задания).
Выбор электродвигателя по частоте вращения.
Частота вращения вала исполнительного органа:
где – угловая скорость вала исполнительного органа. Находится по формуле:
где D – диаметр исполнительного органа. Находится по формуле:
z – количество зубьев.
Ориентировочное передаточное отношения привода:
Ориентировочная частота вращения электродвигателя:
Выбор электродвигателя.
По полученным характеристикам выбираем электродвигатель АИР 100L8 со следующими характеристиками:
Частота вращения: 750 обмин;
Ток при 380 В: 41 А;
Коэффициент мощности: 07;
Момент инерции: 00123 кгм2.
Рис.1.Основные размеры электродвигателя АИР 100L8.
Табл.1. Основные размеры электродвигателя АИР 100L8.
2. Определение передаточных отношений кинематических силовых и энергетических параметров элементов привода.
Перед началом расчёта производится корректировка передаточного отношения.
Действительное передаточное отношение привода:
Ступень корректировки – вторая прямозубая зубчатая передача.
Действительное передаточное отношение прямозубой зубчатой передачи:
В конце расчёта находим мощность угловую скорость крутящий момент и частоту вращения на каждом валу.
Угловая скорость вала:
Крутящий момент вала:
Частота вращения вала:
где – КПД элементов где происходят потери при переходе потока мощности с вала на вал.
где – передаточное отношение передачи.
Где действительное передаточное отношение зубчатой прямозубой передачи.
По полученным данным строим таблицу результатов.
Крутящий момент кН*м
Угловая скорость радс
Частота вращения обмин
Передаточное отношение
Табл.2.Результаты кинематического расчёта.
Расчёт и проектирование зубчатого редуктора.
1. Выбор материалов зубчатых колёс и определение допускаемых напряжений.
Материал зубчатых колёс.
Для шестерни выбираем сталь 40Х. Термообработка – закалка ТВЧ сквозная с охватом впадины. Твёрдость – 55 HRC ().
Для колеса выбираем сталь 35ХМ. Термообработка – закалка ТВЧ сквозная с охватом впадины. Твёрдость – 50 HRC ().
Определение допускаемых напряжений.
Допускаемые контактные напряжения.
Условия определения допускаемых напряжений:
Предельные допускаемые контактные напряжения для шестерни и колеса находятся по формулам:
Где– предел контактной выносливости (по табл. 3.2);
– коэффициент безопасности (по табл. 3.2);
– коэффициент долговечности:
– базовое количество циклов (по рис. 3.1);
– действительное количество циклов
Где n – частота вращения вала шестерни (колеса);
c – количество одновременных зацеплений;
– ресурс работы передачи
где – коэффициент суточного использования привода (из задания);
– коэффициент годового использования привода (из задания).
Проверка правильности выбора материала сводится к условию:
Учитывая полученное значение и погрешность вычислений условие правильности выбора материала можно считать выполненным.
Допускаемые изгибные напряжения.
Предельные допускаемые изгибные напряжения находятся по формуле:
где – предел изгибной выносливости (по табл. 3.2);
– коэффициент долговечности по напряжениям изгиба
– коэффициент учитывающий влияние двустороннего
приложения нагрузки (принимается равным 1).
2. Проектировочный расчёт зубчатой передачи.
Расчёт относительно межосевого расстояния a:
где U– передаточное отношение зубчатой передачи;
– приведённый модуль упругости;
– крутящий момент на колесе;
– меньшее допускаемое напряжение в зубчатой паре;
– коэффициент ширины зубчатого колеса относительно межосевого расстояния;
– коэффициент концентрации нагрузки (согласно рис. 3.2).
После расчёта проводится операция нормирования по ряду Ra40. Принимаем мм.
Далее уточняются основные геометрические параметры.
Коэффициент ширины относительно диаметра:
Ширина зубчатого колеса:
После получения модуля его значение приводится к ГОСТу по 1 ряду (табл. 3.5). Принимаем мм.
Коэффициент ширины колеса относительно модуля (по табл. 3.4):
Суммарное число зубьев передачи:
Число зубьев шестерни(при условии ):
Полученное значение числа зубьев округляется до ближайшего целого значения:
Число зубьев колеса:
Фактическое передаточное число:
Погрешность выбора передаточного числа:
После определения указанных параметров определяются остальные геометрические параметры (согласно табл. 3.7).
Межосевое расстояние:
Делительный диаметр шестерни ():
Делительный диаметр колеса ():
где – угол профиля исходного контура.
Диаметр вершин зубьев:
Диметр впадин зубчатых колёс:
2.1. Проектировочный расчёт валов.
Расчёт начинается с определения минимального диаметра концевого участка из условия прочности на кручение:
где T – крутящий момент на валу Н*м;
– допускаемые касательные напряжения для выбранного материала вала Па.
Округляем до ближайшего значения диаметра подшипника.
Для дальнейшего расчёта согласно полученным данным выбираем шариковый радиально-упорный однорядный подшипник 46305 со следующими характеристиками:
По имеющимся данным проектируем валы редуктора.
Рис. 2.2-ой вал редуктора.
Для дальнейшего расчёта согласно полученным данным выбираем шариковый радиально-упорный однорядный подшипник 46310 со следующими характеристиками:
А также выбираем уплотнение армированный резиновый манжет для валов со следующими характеристиками:
Рис. 3. 3-ий вал редуктора.
3. Проверочный расчёт зубчатой передачи.
Проверка по контактным напряжениям.
Расчёт действующих напряжений:
где – крутящий момент на валу шестерни;
– коэффициенты концентрации нагрузки (по рис. 3.2):
где – коэффициент динамической нагрузки (по табл. 3.8).
Скорость скольжения в зацеплении:
Назначается степень точности согласно табл. 3.9. Выбираем степень точности – 9.
Т.к. допускаемые контактные напряжения составляют МПа то получив МПа можно утверждать что материал выбран верно.
Проверка по изгибным напряжениям.
где – коэффициент формы зуба (по рис. 3.3).
– коэффициент концентрации нагрузки:
Расчёт выполняется для того из колёс зубчатой пары для которого отношение наименьшее:
Т.к. допускаемые изгибные напряжения составляют МПа то получив можно утверждать что материал выбран верно.
3.1. Расчёт зубчатой передачи в системе APMWinMachine.
Расчёт второй и третьей зубчатой передачи был произведён в системе APMWinMachine. Все полученные данные показаны на рис. 5 – 10.
Первая передача – коническая
Рис. 4. Основные параметры 1-ой передачи.
Рис.5. Параметры материалов 1-ой передачи.
Рис.6. Основные геометрические параметры 1-ой передачи
Третья передача – ременная (клиноременная).
Рис. 7. Результаты расчёта ременной 3-ей передачи.
Рис. 8. Результаты расчёта ременной 3-ей передачи.
Рис. 9. Результаты расчёта ременной 3-ей передачи.
Из предложенных вариантов выбираем вариант №0 с большим числом ремней но с меньшими диаметрами шкивов и небольшим осевым расстоянием.
4. Расчёт и выбор подшипников и уплотнений.
Проверочный расчёт подшипников.
Условие расчёта подшипников:
где – требуемый ресурс (из расчёта зубчатой передачи);
где – коэффициент надёжности (принимаем равным 1);
– коэффициент смазки материала (по табл. 3.43);
– динамическая грузоподъёмность подшипника (из справочника);
– показатель степени (принимаем равным 3);
– эквивалентная нагрузка на подшипник:
где V– коэффициент вращения;
– коэффициенты безопасности и температуры (принимаем равные 1);
X Y– коэффициенты учитывающие различные повреждающие действия радиальной и осевой нагрузок (принимаем равные 1 и 0 соответственно согласно табл. 3.44);
– радиальная и осевая нагрузки приведённые к подшипнику:
Требуемый ресурс передачи берётся из расчёта зубчатой передачи:
Согласно расчётам полученный ресурс передачи больше требуемого ресурса что доказывает правильность выбора подшипников.
5. Эскизная компоновка редуктора.
Рис. 10. Эскизная компоновка редуктора.
6. Проверочный расчёт валов на прочность жёсткость и колебания.
Составление расчётной схемы и определение расчётных нагрузок.
Для дальнейшего проверочного расчёта валов требуется построение эпюры изгибающих моментов. Для её построения находят действующие на вал силы:
При наличии всех необходимых сил производим построение эпюры изгибающих моментов.
Определение реакций опор.
Построение эпюры изгибающих моментов по оси 0yz.
Построение эпюры изгибающих моментов.
Рис. 11.Эпюра изгибающих моментов.
Согласно полученной эпюре находим максимальный изгибающий момент действующий на вал в опасном сечении которое будет проверяться на прочность:
Расчёт на прочность.
Так как для расчёта на прочность подшипник 46305 не подходит из-за низкого коэффициента запаса прочности принимаем для расчёта подшипник 36207К6 с внутренним диаметром мм внешним диаметром мм и шириной мм.
Условие расчёта на прочность:
где – действительный коэффициент запаса прочности;
– допускаемый коэффициент запаса прочности.
Допускаемый коэффициент запаса прочности принимаем равным 15.
Действительный коэффициент запаса прочности находится по формуле:
где – коэффициент запаса прочности по напряжениям изгиба;
– коэффициент запаса прочности по напряжениям кручения.
Коэффициент запаса прочности по напряжениям изгиба:
где – предел выносливости материала вала (из характеристики материала вала);
– переменная составляющая цикла напряжения;
– постоянная составляющая цикла напряжения (по формуле 3.119 );
– коэффициент корректирующий влияние постоянной составляющей цикла напряжений на усталостную прочность;
– эффективный коэффициент концентрации напряжения при изгибе (по табл. 3.41);
– масштабный фактор и фактор качества поверхности соответственно (по рис. 3.23).
Амплитудная составляющая напряжения:
где – максимальный изгибающий момент действующий на валу (с эпюры изгибающих моментов принимаем Н*м);
– момент сопротивления сечения относительно осей x и y:
Запас усталостной прочности по кручению:
где – предел усталостной выносливости (из характеристик материала вала);
– постоянная составляющая цикла напряжения:
– переменная составляющая цикла напряжений:
– (по формуле 3.120 ).
Учитывая полученный в ходе расчётов результат коэффициент запаса прочности в опасном сечении составляет 28. Это больше чем допускаемый коэффициент запаса прочности . Значит условие расчёта вала на прочность выполняется.
Расчёт на жёсткость.
Условия расчёта на жёсткость:
где – прогиб под зубчатым колесом;
– угол поворота вала в подшипнике.
– допускаемый прогиб под зубчатым колесом (принимаем = 001*m)
– допускаемый угол поворота вала в подшипнике (принимаем = 0.005 рад.).
Прогиб под зубчатым колесом определяется суммарным прогибом (по табл. 342):
где I – полярный момент инерции сечения вала:
Суммарный прогиб под зубчатым колесом:
Угол поворота вала в подшипнике (по табл. 3.42):
Согласно полученным данным условие расчёта на изгибную жёсткость выполняется.
Расчёт на виброустойчивость.
Критическая частота вращения:
где m– приведённая масса вала:
– изгибная жёсткость вала:
6.1. Проверочный расчёт валов в система APMWinMachine.
Рис. 12. Вал редуктора.
Рис. 13. Реакции в опорах проекции вала.
Рис. 14. Момент изгиба в вертикальной плоскости.
Рис. 15. Момент изгиба в горизонтальной плоскости.
Рис. 16. Усталостная прочность.
Рис. 17. Угол изгиба в вертикальной плоскости.
Рис. 18. Угол изгиба в горизонтальной плоскости.
Рис. 19. Перемещение вертикальное.
Рис. 20. Перемещение горизонтальное.
7. Расчёт и конструирование корпуса и крепёжных деталей.
По табл. 3.47 находят ориентировочные соотношения размеров основных элементов литого корпуса редуктора.
Толщина стенки корпуса:
где – крутящий момент на тихоходном валу редуктора.
Толщина стенки крышки:
Толщина ребра в сопряжении со стенкой корпуса:
Толщина ребра в сопряжении со стенкой крышки:
Диаметр фундаментных болтов:
Диаметр болтов соединения крышки с корпусом редуктора:
Толщина фундаментных лап:
Толщина фланца корпуса:
Толщина фланца крышки для болта с шестигранной головкой:
Толщина подъёмных ушей корпуса:
Толщина подъёмных ушей крышки:
Диаметр болтов крепления торцевых крышек подшипников и крышки смотрового отверстия:
Диаметр прилива подшипникового гнезда для торцевой крышки:
Расстояние между осями болтов для крепления крышки редуктора к корпусу:
Расстояние между осями болтов для крепления крышки редуктора к корпусу в месте приливов подшипниковых гнёзд:
8. Тепловой расчёт и смазка редуктора.
Линейная скорость зубчатого колеса на тихоходном валу:
По полученным значениям выбираем сорт масла.
Согласно табл. 3.49 определяем необходимую кинематическую вязкость масла. Она составила 60*10-6 м2с.
Далее по табл. 3.51. выбираем соответствующую имеющимся данным марку масла. Это индустриальное масло И-70А с промежутком кинематической вязкости 65*10-6 – 75*10-6 м2с.
Условие теплового расчёта:
Температура масла в корпусе редуктора при непрерывной работе без искусственного охлаждения составляет:
где – мощность на быстроходном валу редуктора (мощность электродвигателя);
– коэффициент теплопередачи (принимают равным 9 17 Вт(
– площадь теплоотдающей поверхности корпуса.
Для определения площади теплоотдающей поверхности корпуса редуктор вписывают в параллелепипед и определяют площадь его граней без площади днища:
где B – ширина корпуса редуктора;
H – высота корпуса редуктора;
L – длина корпуса редуктора.
Согласно полученным данным условие теплового расчёта выполняется.
Проверочный расчёт соединений.
Для проверки выбираем шпонку с сечением .
где B – ширина зубчатого колеса;
Напряжения смятия на шпонке:
где F – сила на смятие:
Aсм – площадь смятия:
где Аср– площадь среза:
Так как допускаемые напряжения смятия МПа а расчётное значение МПа то можно утверждать что шпонка выбрана верно.
В качестве муфты выбираем упругую втулочно-пальцевую муфту с внешним диаметром мм номинальным вращающим моментом Н*м частотой вращения с-1. Радиальное смещение валов не более 04 мм мм масса кг.
Рис. 21. Упругая втулочно-пальцевая муфта.
В данной пояснительной записке содержится расчет трёхступенчатого редуктора. На основе расчетов разработан сборочный чертёж редуктора и рабочие чертежи деталей редуктора.
При выполнении курсового проекта были использованы системы автоматизированного инженерного проектирования APM WinMachine Kompas-3D и MathCAD. Также были использованы различные текстовые материалы в виде книг методических указаний и справочников по деталям машин гидравлике сопротивлению материалов технологии конструкционных материалов материаловедению и электротехнике.
В ходе выполнения курсового проекта были получены навыки проектирования различных узлов машин в программе Kompas-3D и навыки расчёта узлов и деталей редуктора в системе APM WinMachine. Кроме того был закреплен учебный материал полученный в ходе изучения курса «Детали машин и основы конструирования».
Результатом выполнения курсового проекта является данная пояснительная записка в которой приводится пошаговый расчет привода и его основных узлов чертежи редуктора и рабочих деталей а также рабочая документация.
Список используемой литературы
Детали машин и основы конструирования. Курсовое проектирование Л. А. Савин Р. Н. Поляков А. В. Сытин и др. – Орёл: ФГОУ ВПО «Госуниверситет – УНПК» 2011. – 230 с.
Анурьев В. И. Справочник конструктора-машиностроителя: в 3-х т.: Т. 2. В. И. Анурьев; под ред. И. Н. Жестковой. – М.: Машиностроение 2001. – 912 с.
Анурьев В. И. Справочник конструктора-машиностроителя: в 3-х т.: Т. 3. В. И. Анурьев; под ред. И. Н. Жестковой. – М.: Машиностроение 2001. – 864 с.
Детали машин. Атлас конструкций: в двух частях под ред. Д.Н. Решетова. – Изд. 5-е. – М.: Машиностроение 1992.
Конструкционные материалы: справочник под общ. ред. Б. Н. Арзамасова. – М.: Машиностроение 1990. – 688 с.
Титульный лист и содержание к пояснительной записке для КП по ДМиОК.docx
ФЕДЕРАЛЬНОЕ ГОСУДАРСТВЕННОЕ БЮДЖЕТНОЕ ОБРАЗОВАТЕЛЬНОЕ
УЧРЕЖДЕНИЕ ВЫСШЕГО ПРОФЕССИОНАЛЬНОГО ОБРАЗОВАНИЯ
«ГОСУДАРСТВЕННЫЙ УНИВЕРСИТЕТ –
УЧЕБНО-НАУЧНО-ПРОИЗВОДСТВЕННЫЙ КОМПЛЕКС»
Кафедра «Мехатроника и международный инжиниринг»
ПОЯСНИТЕЛЬНАЯ ЗАПИСКА
к курсовому проекту по дисциплине:
«Детали машин и основы конструирования»
группы 21ЭТ:Шолохов В.Ю.
Руководитель курсового проекта:Поляков Р.Н.
Кинематический расчёт привода5
1. Выбор электродвигателя5
2. Определение передаточных отношений кинематических силовых и энергетических параметров элементов привода6
Расчёт и проектирование зубчатого редуктора9
1. Выбор материалов зубчатых колёс и определение допускаемых напряжений9
2. Проектировочный расчёт зубчатых передач10
2.1. Проектировочный расчёт валов13
3. Проверочный расчёт зубчатой передачи15
3.1. Расчёт зубчатой передачи в системе АPMWinMachine16
4. Расчёт и выбор подшипников и уплотнителей20
5. Эскизная компоновка редуктора21
6. Проверочный расчёт валов на прочность жёсткость и колебания21
6.1. Проверочный расчёт валов в системе APMWinMachine28
7. Расчёт и конструирование корпуса и крепёжных деталей32
8. Тепловой расчёт и смазка редуктора33
Проверочный расчёт соединений35
Список использованных источников38
эскиз редуктора.frw
