Проектирование червячного редуктора




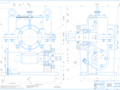
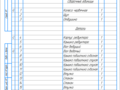
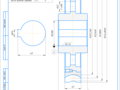
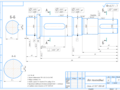
- Добавлен: 04.11.2022
- Размер: 297 KB
- Закачек: 1
Описание
Курсовой проект - Проектирование червячного редуктора
Состав проекта
![]() |
![]() ![]() ![]() ![]() |
![]() ![]() ![]() ![]() |
![]() ![]() ![]() |
![]() ![]() ![]() ![]() |
![]() ![]() ![]() ![]() |
![]() ![]() ![]() ![]() |
Дополнительная информация
Спецификация.spw

Крышка подшипника сквозная
Крышка подшипника глухая
Прокладка регулировочная
Болт М14х110 ГОСТ 7808-70
Болт М12 х 40 ГОСТ 7808-70
Болт М12х45 ГОСТ 7808-70
Болт10х35 ГОСТ 7808-70
Болт М8х10 ГОСТ 7808-70
Гайка М14 ГОСТ 5915-70
Гайка М10 ГОСТ 5915-70
Шайба 14 ГОСТ 11872-89
Шайба 12 ГОСТ 11872-89
Шайба 10 ГОСТ 11872-89
Шайба 8 ГОСТ 11872-89
Штфит 8х25 ГОСТ 9464-79
Манжета 1-45х70 ГОСТ 8752-79
Манжета 1-25х40 ГОСТ 8752-79
Шпонка 8х7х22 ГОСТ 23360-78
Шпонка 16х10х60 ГОСТ 23360-78
Шпонка 18х11х40 ГОСТ 23360-78
Роликоподшипник №7208 ГОСТ 27365-87
Роликоподшипник №7211 ГОСТ 27365-87
Корпус А2.cdw

Обработка мест под головки болтов (гаек) выполниь до чистоты поверхностей
с шероховатостью боковых поверхностей от зенковки
Резьбовые отверстия выполнить с фаской 1х45
Поверхность корпуса очистить и красить маслостойкой краской.
Пояснительная записка.doc
Частота вращения выходного вал nвых = 85 обмин
Коэффициент годового использования Кгод = 07;
Коэффициент суточного использования Ксут = 035
Срок службы Т = 7 лет.
Кинематический расчет4
1 Выбор электродвигателя5
2 Определение передаточных отношений6
3 Определение вращающих моментов и угловых скоростей на валах привода6
Проектировочный расчет передач редуктора9
1 Выбор материалов зубчатых колес и допускаемых напряжений9
2 Определение предварительных размеров колес10
3 Определение усилий в зацеплении13
4 Предварительный расчет валов13
5 Выбор подшипников14
6 Разработка компоновочного чертежа редуктора14
Проверочный расчет передач редуктора17
1 Расчет на контактную выносливость17
2 Расчет на выносливость при изгибе18
Расчет цепной передачи19
1 Расчет геометрических паарметров19
2 Усилия и направление в цепи21
Уточненный расчет валов23
1 Определение долговечности подшипников23
2 Проверка запаса прочности и выносливости30
Расчет шпоночных соединений34
Выбор способа смазки и сорта масла35
Порядок сборки редуктора36
Библиографический список37
В рамках данного проекта нам необходимо разработать привод цепного транспортёра состоящий из частей: электродвигатель муфта червячный редуктор цепная передача.
Цепной транспортёр - машина непрерывного транспорта для перемещения грузов.
Редуктором называют механизм состоящий из зубчатых или червячных передач выполненный в виде отдельного агрегата и служащий для передачи мощности от двигателя к рабочей машине. Назначение редуктора – понижение угловой скорости и повышение вращающего момента ведомого вала по сравнению с валом ведущим.
Кинематический расчет
Определяем срок службы привода. Принимаем сменность привода Lc = 2; длительность смены tc = 8. Ресурс привода определяем по формуле [4 стр. 36]:
Lh = 365 · Т · Кг · Кс · tc · Lc = 365 · 7 · 07 · 035 · 8 · 2 = 10016 ч(1)
Принимаем время простоя машинного агрегата 15% ресурса тогда срок общий ресурс привода Lh = 8514 ч.
1 Выбор электродвигателя
Определяем мощность на ведущем валу привода:
гдеР1 – расчетная мощность на ведущем валу привода кВт;
общ – коэффициент полезного действия привода равный произведению частных КПД.
Определяем общий КПД привода:
Частные КПД выбираем по таблице 2.2 [4 стр. 41]:
- КПД закрытой передачи;
4 - КПД открытой передачи;
9 - КПД пары подшипников качения;
Полученные частные КПД подставим в формулу и получим общее КПД привода:
Полученные значения подставим в формулу и найдем Р1:
Мощность на ведомом валу редуктора определяем по формуле:
Выбираем по табл. К9 [4 стр. 384] электродвигатель 4AМ132S4УЗ мощностью 75 кВт частотой вращения 1455 .
2 Определение передаточных отношений
Передаточное число привода определяем по формуле:
Из стандартного ряда передаточных чисел [4 стр. 43] принимаем передаточное число редуктора uр = 8.
Передаточное число открытой передачи определяем по формуле:
3 Определение вращающих моментов и угловых скоростей на валах привода
Определяем угловые скорости на валах привода радс
Угловая скорость на первом валу привода:
Угловая скорость на втором валу привода:
Угловая скорость на третьем валу привода:
Определяем частоту вращения валов привода .
на первом валу привода:
на втором валу привода:
на третьем валу привода:
Определяем вращающие моменты на валах привода Нм:
Таблица 1 – Результаты кинематического расчета привода.
Проектировочный расчет передач редуктора
1 Выбор материалов зубчатых колес и допускаемых напряжений
Выбор марки материала зависит от передаваемой мощности и скорости скольжения Ошибка! Закладка не определена.[4 стр. 54]:
При передаваемой мощности = 77 кВт и скорости скольжения Vs = 48мс принимаем по таблице 3.5 [4 стр. 54] из II группы материал для которого: Нмм² Нмм².
Определяем допускаемые напряжения для червячного колеса [4 стр. 55]:
где – коэффициент долговечности при расчете на изгиб определяемый по формуле [4 стр. 55]:
2 Определение предварительных размеров колес
Вычисляем межосевое расстояние мм – главный параметр передачи по формуле [4 стр. 71]:
где - коэффициент концентрации нагрузки. Принимаем = 11 [4 стр. 71].
Полученное значение межосевого расстояния округляем до стандартного значения = 140 мм [4 табл. 13.15]. Принимаем число витков червяка = 4. Принимаем архимедов тип червяка.
Определяем число зубьев червяка [4 стр. 71]:
Определяем модуль зацепления [4 стр. 71]:
Принимаем = 7 мм [4 стр. 72].
Определяем коэффициент диаметра червяка [4 стр. 72]:
Согласно ГОСТ 19372-74 принимаем = 8 [4 стр. 72].
Вычисляем коэффициент смещения инструмента [4 стр. 72]:
Фактическое передаточное число и его отклонение от заданного [4 стр. 73]:
Определяем фактическое межосевое расстояние мм [4 стр. 73]:
Определяем основные геометрические размеры червяка [4 стр. 73]:
Основные размеры червяка мм:
Диаметр вершин витков
Диаметр впадин витков
Длина нарезной части червяка
Делительный угол подъема линии витков
Определяем основные геометрические размеры колеса мм:
Диаметр вершин зубьев
Наибольший диаметр вершин
Диаметр впадин зубьев
Условный угол обхвата
3 Определение усилий в зацеплении
Определяем силы действующие в зацеплении [4 стр. 96-100].
Определяем окружную силу на колесе Н численно равную осевой силе на червяке :
Определяем окружную силу на червяке Н численно равную осевой силе на колесе :
Определяем окружную силу в зацеплении:
4 Предварительный расчет валов
Диаметр ведущего вала редуктора определяем по формуле [4 стр. 108]:
где[] – допускаемое напряжение кручения.
Диаметр выходного конца ведущего вала принимаем d1 = 25 мм;
Диаметр выходного конца ведомого вала принимаем d2 = 45 мм;
Остальные размеры назначаем в соответствии с рекомендациями [4 стр. 108] и на основе эскизной компоновки:
Диаметр вала под подшипник принимаем dп1 = 30 мм;
Диаметр вала в опасном сечении под шестерней принимаем dш1 = 45 мм;
Диаметр вала под подшипник принимаем dп2 = 55 мм;
Диаметр вала в опасном сечении под колесом принимаем dш2 = 63 мм.
Предварительно принимаем подшипники [4 стр. 414-417].
Таблица 2 - Типоразмеры подшипников качения.
6 Разработка компоновочного чертежа редуктора
Корпус конструируем по рекомендациям §10.5 [4 стр. 210-230]. Определяем длину ступицы и диаметр ступицы для ведомого вала:
Определяем минимальную толщину стенки:
Определяем расстояния от внутренней поверхности стенки редуктора до:
боковой поверхности вращающейся части:
боковой поверхности подшипника качения:
Радиальный зазор от поверхности вершин зубьев до:
внутренней поверхности стенки редуктора:
до внутренней нижней поверхности стенки корпуса:
Расстояние от боковых поверхностей элементов вращающихся вместе с валом до неподвижных частей редуктора:
Определяем диаметр болтов для фланцев:
Принимаем коэффициент k = 33.
Определяем ширину фланцев:
Толщина фланца боковой крышки:
Определяем высоту головки болта:
Определяем толщину фланца втулки:
Длина цилиндрической части крышки:
Проверочный расчет передач редуктора
1 Расчет на контактную выносливость
Уточняем КПД червячной передачи [4 стр. 74]:
По табл. 4.9 [4 стр. 74] в зависимости от скорости скольжения передачи принимаем угол трения = 34º
Проверяем контактные напряжения зубьев колес Нмм² [4 стр. 74]:
где – коэффициент нагрузки зависящий от окружной скорости колеса. При = 1 [4 стр. 74].
Определяем отклонение действительной нагрузки от заданной [4 стр. 74]:
Условие прочности выполняется т.к. действительная нагрузка находится в допустимом интервале (-15 + 5)% [4 стр. 74].
2 Расчет на выносливость при изгибе
Определяем напряжение изгиба зубьев колеса Нмм² [4 стр. 74]:
где - коэффициент формы зуба колеса принимаемый в зависимости от эквивалентного числа зубьев колеса ZV2 = 32. Принимаем по табл. 4.10 [4 стр. 74] = 177.
Условие прочности выполняется.
Расчет цепной передачи
1 Расчет геометрических параметров
Принимаем приводную роликовую цепь типа ПР. Определяем число зубьев меньшей звездочки цепной передачи [3 стр. 152]:
Определяем число зубьев ведомой звездочки [3 стр. 152]:
Условие соблюдается.
Определяем фактическое передаточное отношение цепной передачи:
Определяем отклонение фактического передаточного отношения от принятого:
Определяем коэффициент эксплуатации передачи [3 стр. 149]:
гдеКд = 1 - коэффициент учитывающий динамичность нагрузки [3 стр. 149];
Ка – коэффициент межосевого расстояния. Ка = 1 - для оптимального межосевого расстояния [3 стр. 150];
Кс – коэффициент способа смазывания. Принимаем Кс = 15 - при периодическом способе смазывания [3 стр. 150];
К – коэффициент наклона линии центров звездочек е горизонту. При угле наклона 60º принимаем К = 1 [3 стр. 150];
Креж – коэффициент режима работы. Принимаем Креж = 1 - при работе передачи в одну смену [3 стр. 150];
Кр – коэффициент способа регулирования натяжения цепи. Кр = 1 - при регулировании натяжения отжимными винтами [3 стр. 150].
Т.к. 3 то условия эксплуатации цепной передачи можно оставить без изменений.
Определяем шаг роликовой цепи по формуле 7.38 [3 стр. 149]:
гдеm – число рядов в цепи. Принимаем m = 1;
[pц] – допускаемое давление в шарнирах цепи. По таблице 7.18 [3 стр. 150] принимаем [pц] = 30.
По табл. 7.20 [3 стр. 156] принимаем цепь с шагом 254 мм разрушающая нагрузка Q = 60 кН вес 1 метра цепи q = 26 кгм.
Делительный диаметр ведущей звездочки
D1 = = = = 21878 мм(63)
Делительный диаметр ведомой звездочки
D2 = = = = 46115 мм(64)
Определяем ориентировочное межосевое расстояние по формуле [3 стр. 148]:
= 30 · 254 = 762 мм(65)
Вычисляем длину замкнутой цепи выраженную в шагах t:
Принимаем четное значение lt = 98 мм.
Уточняем межосевое расстояние по формуле 7.37 [3 стр. 149]:
Подставив данные в формулу получаем а = 76138 мм.
Принимаем монтажное межосевое расстояние:
= 0998 · 76138 = 760 мм(68)
Окончательно принимаем цепь ПР-254-166 ГОСТ 13568-75.
2 Усилия и направление в цепи
Скорость цепи [3 стр. 153]:
Определяем окружную силу на валу ведомой звездочки [3 стр. 153]:
Определяем центробежную силу [3 стр. 153]:
Fv = q · v² = 26 · 21² = 115 Н(71)
Определяем силу от провисания цепи [3 стр. 153]:
Ff = 981 · kf · q · a = 981 · 6 · 26 · 762 = 117 Н(72)
где kf – коэффициент учитывающий расположение цепи. При горизонтальном положении принимаем kf = 6 [3 стр. 151].
Расчетная нагрузка на валы [3 стр. 154]:
Fв = Ft + 2 · Ff = 3 + 2 · 117 = 237 Н(73)
Проверяем коэффициент запаса прочности по формуле [3 стр. 154]:
По таблице 7.19 при n1 = 382 обмин и шаге t = 254 мм нормативный коэффициент запас прочности [s] = 76. Т.к. s > [s] условие прочности выполняется.
Уточненный расчет валов
1 Определение долговечности подшипников
Принимаем из эскизной компоновки L1 = 113 мм L2 = 93 мм.
Вертикальная плоскость
Ошибка! Закладка не определена. Н
Горизонтальная плоскость
Суммарные радиальные реакции подшипников:
Строим эпюры моментов.
Крутящий момент Т = 51 Нм
Рисунок 1 – Расчетная схема ведущего вала.
Принимаем из эскизной компоновки l3 = l4 = 82 мм l5 = 95 мм Ма2 = 408 Нм
Консольная сила от цепной передачи Fm2 = 237 Н.
-2124 – (1613) + 3500 + 237 = 0
- 635 - 639 + 1274 = 0
Определяем суммарные реакции:
Строим эпюры моментов:
Вертикальная плоскость:
Крутящий момент Т = 392 Нм
Рисунок 2 - Расчетная схема ведомого вала.
Подшипник пригоден при условии:
Расчетную динамическую грузоподъемность определяем по формуле:
гдеRe – эквивалентная динамическая нагрузка Н;
m – показатель степени. = 333 - для роликовых подшипников;
Эквивалентную динамическую нагрузку определяем согласно формуле [4]:
гдеХ – коэффициент радиальной нагрузки. Принимаем X = 056 для радиальных шарикоподшипников;
V – коэффициент вращения принимаем V = 1 т.к. вращается внутреннее кольцо подшипника;
Rr – радиальное усилие в наиболее нагруженной опоре;
Кб – коэффициент безопасности. По таблице 32 в зависимости от характера нагрузки и вида машинного агрегата принимаем Кб = 11;
Кt – температурный коэффициент. При t ≤ 100º C принимаем Кt = 1.
Подшипник поменять один раз за период службы
2 Проверка запаса прочности и выносливости
Ведущий вал. Проверка жесткости вала
Приведённый момент инерции поперечного сечения червяка определяем по формуле [4]:
Таким образом жесткость обеспечена так как .
Ведомый вал. Сечение I-I. Концентрация напряжений обусловлена наличием шпоночного паза. Материал Сталь 45 термообработка – улучшение .
Определение запасов прочности вала для опасных сечений по нормальным напряжениям.
гдеK = 172 – эффективный коэффициент концентрации напряжений [4];
= 073 – коэффициент учитывающий влияние масштабных факторов;
- амплитуда нормальных напряжений.
где М – изгибающий момент действующий на вал колеса;
Wи – момент сопротивления сечения изгибу:
Суммарный изгибающий момент в горизонтальной и вертикальной плоскостях:
- среднее напряжение отнулевого цикла:
Проверка вала по касательным напряжениям
гдеK = 156 – эффективный коэффициент концентрации напряжений [4];
= 063 – коэффициент учитывающий влияние масштабных факторов;
- амплитуда касательных напряжений численно равная среднему напряжению цикла:
= 01 – коэффициент учитывающий влияние постоянной составляющей цикла на усталостную прочность.
Коэффициент запаса прочности по касательным напряжениям:
Результирующий коэффициент запаса прочности:
Условие прочности вала выполняется .
Согласовываем полученный диаметр выходного конца ведущего вала редуктора с посадочным диаметром муфты. При значении крутящего момента T = 51 Н принимаем МУВП ГОСТ 21424-93 [4 табл. К21] с номинальным вращающим моментом 63 Нм и посадочным диаметром . Радиальную силу действующую на вал определяем по формуле [4]:
Рисунок 3 – Муфта упругая втулочно-пальцевая.
Расчет шпоночных соединений
Производим расчет шпонок на смятие по формуле [4 стр. 251]:
где h - высота сечения шпонки мм;
t1- глубина паза вала мм;
b - ширина шпонки мм.
[см] - допускаемое напряжение на смятие [см] = 100 МПа - при стальной ступице.
Параметры шпонок принимаем из табл. К42 [4 стр. 427428]. Результаты расчета приведены в таблице 4.
Таблица 3 - Проверочный расчет шпоночных соединений.
Передаваемый момент Нм
Высота сечения шпонки мм
Напряжение на смятие МПа
Условие прочности для всех шпоночных соединений выполняется.
Выбор способа смазки и сорта масла
Смазка зубчатых колес
При скорости скольжения = 48 мс принимаем по табл. 12.29 [4 стр. 241] смазочное масло И-Т-Д-220 ГОСТ 17479.4-87. Это индустриальное масло для тяжело нагруженных узлов с присадками.
Объём масляной ванны V определяется из расчёта 025 дм³ масла на 1 кВт передаваемой мощности:
V = 025 · 77 = 193 дм³
Смазка подшипников осуществляем консталином УТ-1 ГОСТ 7957-73 [4 стр. 241-243]. Закладываемой в подшипниковые камеры примерно 23 объема камеры при сборке редуктора. В сквозные крышки подшипников устанавливаем манжетные уплотнения.
Порядок сборки редуктора
Перед сборкой внутреннюю поверхность корпуса редуктора тщательно очищают и покрывают маслостойкой краской.
Сборку производят в соответствии со сборочным чертежом редуктора начиная с узлов валов.
На ведущий вал насаживают маслоудерживающие кольца и роликоподшипники предварительно нагретые на масле до 90 ОС. В шпоночный паз ведомого вала закладывают шпонку и напрессовывают колесо до упора в бурт вала. Затем надевают распорную втулку мазеудерживающие кольца и устанавливают подшипники предварительно нагретые в масле.
Собранные валы устанавливают в корпус монтируют крышку корпуса покрывая предварительно поверхности стыка крышки и корпуса спиртовым лаком. Для центровки устанавливают крышку на корпус с помощью двух конических штифтов; затягивают болты крепящие крышку к корпусу.
В подшипниковые камеры закладывают пластическую смазку ставят крышки подшипников с комплектом регулировочных прокладок. Перед постановкой сквозных крышек в проточки закладывают войлочные уплотнения пропитанные горячим маслом. Проверяют проворачиванием валов отсутствие заклинивания подшипников (валы должны свободно проворачиваться от руки) и закрепляют крышки винтами.
В шпоночную канавку выходного конца ведомого вала закладывают шпонку. Затем ввертывают пробку маслосливного отверстия с прокладкой и жезловый указатель.
Заливают масло в объеме 15 л и закрывают смотровое окно крышкой с прокладкой изготовленной их технического картона. Крышку закрепляют винтами.
Собранный редуктор обкатывают без нагрузки в течение заданного времени по программе установленной техническими требованиями.
Библиографический список
Анурьев В. И. Справочник конструктора-машиностроителя. В 2 т. г. 2. М.: Машиностроение 1979.
Курмаз Л.В. Детали машин. Проектирование: Справочное учебно - методическое пособие Л.В.Курмаз А.Т.Скойбеда – 2 –е изд. исп. М Высшая школа 2005. – 309 с. ил.
Чернавский С. А.. Курсовое проектирование деталей машин 2-е изд. М.: Машиностроение 1988.
Шейнблит А. Е. Курсовое проектирование деталей машин. М.: Высшая школа 1991.
Сборка А1.cdw

Внутренние поверхности корпуса и крышки покрасить маслостойкой краской.
В редуктор залить 2 л. масла И-Т-Д-200 ГОСТ 17479.4-87.
Перед окончательной сборкой стыки фланцев корпуса покрыть пастой типа "Герметик".
Техническая характеристика
Номинальный момент на ведомом валу 392 Нм.
Частота вращения ведущего вала 1455 обмин.
Передаточное число U=8.
Модуль зацепления m=7.
Число витков червяка Z=4.
Вал тихоходный А3.cdw

Закалка поверхностей ТВЧ h 0
Радиусы галтелей 2 мм.
Канавки: ширина 5 мм
Неуказанные предельные отклонения размеров валов - t
t:2 среднего класса точности по ГОСТ 25670-83
Колесо А3.cdw

Направление линии зуба
Коэффициент диаметра червяка
Межосевое расстояние
Число витков червяка
Неуказанные предельные
отклонения размеров:
* Размер для справок.
Рекомендуемые чертежи
- 24.01.2023
- 24.01.2023