Расчет и выбор посадок для редуктора




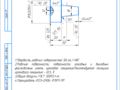
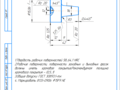
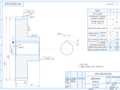
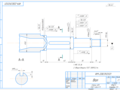
- Добавлен: 04.11.2022
- Размер: 850 KB
- Закачек: 0
Описание
Состав проекта
![]() |
![]() |
![]() ![]() ![]() |
![]() ![]() ![]() ![]() |
![]() ![]() ![]() ![]() |
![]() ![]() ![]() |
![]() ![]() ![]() |
Дополнительная информация
Kursovaya_po_metrologii.docx
ФГБОУ ВПО «Южно-Уральский государственный университет»
(Национальный исследовательский университет)
Кафедра «Технология машиностроения»
Пояснительная записка на курсовую работу по дисциплине
«Метрология стандартизация и сертификация»
Нормоконтролер Руководитель
Выбойщик А.В. Выбойщик А.В
студент группы ФМ – 208
Куколев Н.С. Расчёт точностных параметров и методов их контроля Челябинск: ЮУрГУ ФМ 2015 34 с. 15 илл. 2 табл. библиогр. список – 2наим.
В данной курсовой работе назначена посадка с натягом с зазором приведен расчет калибров деталей гладких цилиндрических соединений расчет калибра для резьбовой детали а так же разработаны рабочие чертежи вала зубчатого колеса и схемы контроля вала.
РАСЧЕТ ПОСАДКИ С НАТЯГОМ5
РАСЧЕТ ПЕРЕХОДНОЙ ПОСАДКИ 14
РАСЧЕТ ПОСАДКИ ПОДШИПНИКА КАЧЕНИЯ17
1 РАСЧЕТ ИСПОЛЬНИТЕЛЬНЫХ РАЗМЕРОВ ГЛАДКИХ КАЛИБРОВ – СКОБ20
2 РАСЧЕТ ИСПОЛЬНИТЕЛЬНЫХ РАЗМЕРОВ ГЛАДКИХ КАЛИБРОВ – ПРОБОК21
3 ПОСТРОИТЬ СХЕМЫ РАСПОЛОЖЕНИЯ ПОЛЕЙ ДОПУСКОВ РЕЗЬБОВЫХ СОЕДИНЕНИЙ24
4 РАСЧИТАТЬ ИСПОЛНИТЕЛЬНЫЙ РАЗМЕР ПР И НЕ РЕЗЬБОВЫХ КАЛИБРОВ ПРОБОК ДЛЯ ВНУТРЕННЕЙ РЕЗЬБЫ М30-7Н25
5 РАСЧИТАТЬ ИСПОЛНИТЕЛЬНЫЙ РАЗМЕР ПР И НЕ РЕЗЬБОВЫХ КАЛИБРОВ КОЛЕЦ ДЛЯ НАРУЖНЕЙ РЕЗЬБЫ М8-8g 28
РАСЧИТАТЬ ПАРАМЕТРЫ ЗУБЧАТОГО КОЛЕСА32
СПОСОБЫ КОНТРОЛЯ ВАЛА34
БИБЛИОГРАФИЧЕСКИЙ СПИСОК37
Основной задачей конструирования является создание новых и модернизация существующих машин и приборов подготовка чертежей и другой технической документации обеспечивающей высокий технический уровень качество необходимую технологичность изделий их конкурентоспособность. Решение этой задачи в значительной степени связано с выбором необходимой точности изготовления изделий в том числе допусков их размеров допусков формы и расположения шероховатости поверхностей назначением зазоров и натягов в соединении деталей (посадок) расчетом размерных цепей.
В решении задач совершенствования технологии машиностроения особое значение приобретает стандартизация и взаимозаменяемость. Созданы государственные стандарты регламентирующие допуски и посадки типовых деталей и соединений. Без этой стандартизации всевозможных изделий промышленности взаимозаменяемость в машиностроении была бы невозможна а следовательно сделалось бы невозможным и создание приборов и машин разнообразных деталей и прочих изделий обладающих желаемой технологичностью качеством и совершенством конструкции. Кроме того взаимозаменяемость – основной принцип конструирования изготовления контроля и эксплуатации машин позволяющий значительно ускорить проектно-конструкторские работы удешевить производство машин и их эксплуатацию.
Целью данной работы является ознакомление с основами стандартизации и взаимозаменяемости и обучение использованию разнообразных стандартов выбору оптимальных расчетных посадок и оптимальной точности размеров при расчете размерных цепей.
Для неподвижного соединения 67 рассчитать и подобрать посадки ручным способом.
Таблица 1 «Исходные данные»
Номинальный диаметр соединения
Внутренний диаметр вала
Наружный диаметр втулки d2
Модуль упругости материала втулки
Модуль упругости материала вала
Коэффициент Пуассона материала втулки
Коэффициент Пуассона материала вала
Предел текучести материала втулки.
Предел текучести материала вала
Среднеарифметическое отклонение профиля поверхности втулки
Среднеарифметическое отклонение профиля поверхности вала
При расчете определяем предельные (Nminф Nmaxф) величины натягов соединении.
Минимальный функциональный натяг определяем из условия обеспечения прочности соединения. При нагружении крутящим моментом.
CD и Cd - коэффициенты жесткости конструкции.
Максимальный функциональный натяг определяем из условия обеспечения прочности сопрягаемых деталей.
Nmax ф = pдопdн(CDED+ CdEd)
Где Pдоп – наибольшее допустимое давление на контактные поверхности при которой отсутствуют пластические деформации.
Определяем по формулам:
PDдоп 058 тD[1-(dнd2)2]
Pdдоп 058 тd[1-(d1dн)2]
где т - предел текучести материала детали при растяжении
PDдоп=05836107[1-(3060)2]=1566107 Па
Pdдоп=05836107[1-(2030)2]=1169107 Па
Меньшее из pдоп используем в расчете Nmax ф.
Из функционального допуска посадки определяем конструкторский допуск посадки по которым устанавливаем квалитеты вала и отверстия.
Где функциональный допуск посадки равен:
TNф= Nmax ф - Nmin ф = 743 – 299 = 7131мкм
Конструкторский допуск посадки
ITD - табличный допуск отверстия;
ITd - табличный допуск вала.
Эксплуатационный допуск посадки
Tэ=э+ сб где э - запас на эксплуатацию сб - запас на сборку.
Конструктивный допуск посадки TNк определяется на основании экономически приемлемой точности изготовления деталей соединения и рекомендаций по точности посадок с натягом (не менее IT6 и не грубее IT8). Эксплуатационный допуск посадки должен быть не менее 20% от TNф.
Определяем квалитет и отверстие вала. Из ГОСТ 25346-82 найдем допуски IT6 IT8 для
dн=40 мм IT6=13 мкм IT7=21 мкм IT8=33 мкм
Возможно несколько вариантов значение TNк и Tэ.
При TNк= ITD+ITd = IT7+ IT6=6+7=34 мкм
Tэ= TNф-TNк= 7131 - 34 = 3731 мкм что составляет 52% от TNф
При TNк= ITD+ITd = IT7+ IT7=21+21=42 мкм
Tэ= TNф-TNк= 7131 - 42= 3231 мкм что составляет 45% от TNф
Вариант TNк= IT7+ IT8=21+33=54 мкм
Tэ= TNф-TNк= 7131 - 54= 1731 мкм что составляет 24% от TNф
Все варианты дают удовлетворительный результат.
Учитывая предпочтительность посадок по ГОСТу 25347-82 примем для отверстия втулки допуск IT7 а для вала IT7 или IT8.
Для учета конкретных условий эксплуатации в расчетные предельные натяги необходимо ввести поправки.
) Поправка U - учитывает снятие неровностей контактных поверхностей соединяемых деталей.
где RaD и Rad - среднеарифметическое отклонение профиля соответственно отверстия и вала.
По условию: RaD = 25 мкм Rad = 125 мкм
Тогда U=5(25+125)=1875 мкм
) Поправка Ut - учитывает различия рабочей температуры и температуры сборки и коэффициента линейного расширения.
Принимаем Ut=0 так как рабочая температура близка к температуре сборке.
) Поправка Uц - учитывает деформацию детали от действия центробежных сил.
Uц принимается равной нулю так как скорость вращения не велика.
Определяем функциональные натяги с учетом поправок.
N min ф рас= N min ф + U = 299+1875=2175 мкм
N max ф рас= N max ф + U = 7131+1875=9006 мкм
Выбор посадок. Для обеспечения работоспособности стандартной посадки необходимо выполнить условия (неравенства).
N max т N max ф рас
N max ф рас - N max т = сб
N min т N min ф рас
N min т - N min ф рас =э
Проверим посадки с натягом из числа рекомендуемых ГОСТ 25346–89 «Единая система допусков и посадок. Общие положения ряды допусков и основных отклонений» комбинированная посадка.
Таблица 2 Анализ посадок
Из таблицы видим что рекомендуемая посадка удовлетворяет поставленным условиям. Поля допусков представлены на рис. 1. Выберем посадку
Рисунок 1 – Схема рекомендуемых посадок в системе отверстия2 ПЕРЕХОДНЫЕ ПОСАДКИ
Для сопряжения 1-6 подбираем стандартную посадку.
Для такого типа соединений применяются посадки с Smin =0
a также переходные посадки которые обеспечивают высокую точность центрирования и легкость сборки.
Такими посадками по ГОСТу 25347-82 являются
) 20 ; = 00275 мм; 2) 20 ; = 0019
) 20 ; = 0013 мм; 4) 20 ; = 0006
Для данного соединения наиболее подходит посадка 20 H7k6.
Посадка 20H7m6 обеспечит лучшее центрирование но трудоемкость сборки увеличится по сравнению с посадкой 20H7k6 так как относительный зазор 001920 > 001320.
Выбираем посадку 20H7k6.
Smax табл=0019 мм Nmax табл=0015 мм.
TD+Td=0021+0017= 0038
Средний размер отверстия.
Dc=(30021+20)2=300105 мм
Средний размер вала.
dc=(30015+30002)2=30008 мм
Так как Smax табл >Smax расч то надо определить вероятное предельное значение Smax в. Легкость сборки определяют вероятностью получения натягов в посадке. Принимаем что рассеяния размеров отверстия и вала а также зазора и натяга подчиняются закону нормального распределения и допуск равен величине поля рассеивания.
Тогда D=216=3.5; d=196=316.
При средних размерах отверстия и вала получается
Определяем вероятность зазоров от 0 до 2 мкм то есть х=2мкм.
По приложению значение функции Ф(Z) находим вероятность зазоров в пределах от 0 до 2 мкм. Ф(042)=01628.
Кривая вероятности натягов и зазоров посадки 20H7k6
=6NS=6.4.7=282 —диапазон рассеивания натягов и зазоров.
Вероятность получения зазоров и натягов в соединении:
2+01628=058 или 58%.
Вероятность получения натягов в соединении 1-0.58=042 или 42%.
Предельные значения зазоров и натягов.
NS - 35 = 3*4.7-2=121
NS + 35 = 3*4.7 + 2= 161
Рисунок 2 – Кривая вероятностей зазоров и натягов посадки 20H7k6
РАСЧЁТ ПОСАДОК ПОДШИПНИКОВ КАЧЕНИЯ
Выбор посадок зависит от вида нагружения колец подшипника. Определяем виды нагружения. По условиям работы узла внутреннее кольцо подшипника имеет циркуляционное нагружение нагружение – местное. Принимаем класс точности 0 по которой в зависимости от диаметра d = 15 мм D = 35 мм определяем ширину кольца B = 11 мм и r = 1 мм (ГОСТ 8338 – 75). Для циркуляционного нагруженного кольца подшипника посадку выбирают по интенсивности радиальной нагрузки на посадочной поверхности:
где R = 900 Н – приведенная радиальная реакция опоры на подшипник
b – рабочая ширина посадочной поверхности кольца подшипника за вычетом фасок: b = B - 2r = 11 - 2 1 = 9 мм
– динамический коэффициент посадки зависящий от характера нагрузки (при перегрузке до 150 % умеренных толчках и вибрации = 1)
– коэффициент учитывающий степень ослабления посадочного натяга при
полом вале или тонкостенном корпусе (при сплошном вале = 1)
– коэффициент неравномерности распределения радиальной нагрузки (в обычных условиях = 1).
Найденным значениям и d соответствует основное отклонение k.
Номер квалитета зависит от класса точности подшипника.
При посадке на вал если подшипник 0 класса то квалитет вала IT6 будет k6 ) поле допуска подшипника L0 ).
Для местного нагруженного кольца выбираем основное отклонение H а номер квалитета в зависимости от класса точности подшипника. Для 6 класса квалитет отверстия будет IT7. Поле допуска отверстия в соединении будет H7 ) поле допуска вала будет l0 ).
Схема расположения полей допусков подшипников представлена на рисунке 5 технические требования к посадочным поверхностям – на рисунке 6.
Рисунок 3 – Схема расположения полей допусков подшипника качения
Рисунок 4 – Технические требования к посадочным поверхностям подшипников качения: а) вала; б) корпуса
1 Расчёт исполнительных размеров гладких калибров – скоб
Контроль детали 1 по размеру 15 в массовом и серийном производствах осуществляется с помощью предельных калибров – скоб. Рассмотрим расчёт их исполнительных размеров.
По ГОСТ 25346 – 82 «Единая система допусков и посадок. Общие положения ряды допусков и основных отклонений» определяем верхнее и нижнее отклонение вала 15 :
верхнее отклонение вала es = 12 мкм;
нижнее отклонение вала ei = 1 мкм.
Определим наибольший и наименьший предельный диаметр вала:
= + es = 15 + 0.012 = 15.012 мм;
= + ei = 15 – 0001 = 15.001 мм.
По табл. 2 ГОСТ 24853 – 81 «Калибры гладкие для размеров до 500 мм. Допуски» определяем:
= 3 мкм – отклонение середины поля допуска на изготовление проходного калибра для вала относительно наибольшего предельного размера вала;
= 2 мкм – допуск на изготовление калибров для вала;
= 3 мкм – допустимый выход размера изношенного проходного калибра для вала за границу поля допуска изделия.
Строим схему расположения полей допусков вала ПР и НЕ сторон предельного калибра–скобы (рис. 1).
Рисунок 5 – Схема расположения полей допусков вала ПР и НЕ сторон предельного калибра – скобы
Считаем исполнительные размеры калибров – скоб.
В качестве исполнительного размера скобы берется наименьший предельный размер ее с положительным отклонением равным допуску на изготовление калибра.
Наименьший предельный размер ПР – проходного калибра – скобы:
= - - = 15 - 0003 - = 15.0075+0003 мм.
Наименьший предельный размер НЕ – непроходного калибра – скобы:
= - = 15.001 - = 14.9995 мм.
Исполнительный размер ПР стороны калибра – скобы который ставится на чертеже калибра равен 150075+0003 мм.
Исполнительный размер НЕ стороны калибра-скобы 14.9995+0003 мм.
2 Расчёт исполнительных размеров гладких калибров – пробок
Контроль отверстия 15 осуществляется с помощью предельных калибров – пробок. Произведём расчёт их исполнительных размеров.
По ГОСТ 25346 – 82 «Единая система допусков и посадок. Общие положения ряды допусков и основных отклонений» определяем верхнее и нижнее отклонение отверстия 15 :
верхнее отклонение отверстия es = + 59 мкм
нижнее отклонение отверстия ei = +16.
Находим наибольший размер отверстия:
= + es = 15 + 0059 = 15059 мм.
Наименьший предельный размер отверстия:
Z = 8 мкм – отклонение середины поля допуска на изготовление проходного калибра для вала относительно наибольшего предельного размера вала;
H = 3 мкм – допуск на изготовление калибров для вала;
Y = 0 мкм – допустимый выход размера изношенного проходного калибра для отверстия за границу поля допуска изделия.
Строим схему расположения полей допусков отверстия ПР и НЕ сторон предельного калибра – пробок (рис. 2).
Рисунок 6 – Схема расположения полей допусков отверстия ПР и НЕ сторон предельного калибра-пробки
Считаем исполнительные размеры калибров – пробок.
В качестве исполнительного размера калибра – пробки берется наибольший
предельный размер его с отрицательным отклонением равным допуску на изготовление калибра.
Наибольший предельный размер ПР – проходного калибра – пробки: = + Z + = 15.016 + 0008 + = 150255-0003 мм.
Наибольший предельный размер НЕ – проходного калибра – скобы:
= + = 15059 + = 7506-0003 мм.
Исполнительный размер проходного калибра – пробки 150075+0005 мм.
Исполнительный размер НЕ стороны калибра-скобы 1506-0003 мм.
3 ПОСТРОЕНИЕ СХЕМЫ РАСПОЛОЖЕНИЯ ПОЛЕЙ ДОПУСКОВ РЕЗЬБОВОГО СОЕДИНЕНИЯ
Для обеспечения требований взаимозаменяемости соединяемых изделий устанавливают предельные контуры резьбы болта и гайки. По ГОСТ 24705-81 определим основные размеры резьбового соединения М12 - .
Наружный диаметр резьбы общий для болта и гайки d = D = 12 мм средний диаметр болта и гайки d2 = D2 =11.026 мм внутренний диаметр болта и гайки d1 = D1 = 10.376 мм угол профиля метрической резьбы α = 60° .
Построим профиль резьбы на рис.3 он показан жирной линией
Рисунок 7 – Профиль резьбы
Точность резьбового соединения задана М12 -
М12 – 6Н – условное обозначение внутренней резьбы (гайки);
M12 – 6g – обозначение наружной резьбы (болта).
По ГОСТ 16093-81 находим предельные отклонения диаметров гайки:
нижние отклонения D; D1 EI = 0 мкм;
верхнее отклонение D2 ESD2 = 190 мкм;
верхнее отклонение D1 ESD1 = 300 мкм.
По ГОСТ 16093-81 находим предельные отклонения диаметров болта:
верхнее отклонение d d2 d1 es = -32 мкм;
нижнее отклонение d e
нижнее отклонение d2 ei = -172 мкм.
4 РАСЧЕТ ИСПОЛНИТЕЛЬНЫХ РАЗМЕРОВ ПР И НЕ РЕЗЬБОВЫХ КАЛИБРОВ-ПРОБОК ДЛЯ ВНУТРЕННЕЙ РЕЗЬБЫ М12 – 6Н
По ГОСТ 24705-81 определяем основные размеры резьбы
M12– 6H : наружный диаметр D = 12 мм; средний диаметр D2 = 11.026 мм; внутренний диаметр D1 = 10.376 мм.
По ГОСТ 16093-81 находим предельные отклонения диаметров резьбы:
нижнее отклонение DD2 D1EI = +0мкм;
верхнее отклонение D2 ESD2 = +190мкм;
верхнее отклонение D1ESD1 = +300мкм.
Строим схему расположения полей допусков резьбовых калибров-пробок.
Рисунок 8 – Отклонения и допуски калибров
Считаем исполнительные размеры резьбовых калибров-пробок. В соответствии с примечанием к табл. 7 приложения 13 определяем наименьшие предельные диаметры резьбы калибра.
Рисунок 9 – Схема расположения полей допусков ПР и НЕ сторон калибра – пробки
Для ПР резьбового калибра-пробки:
наибольший предельный наружный диаметр
наибольший предельный средний диаметр
Наибольший предельный внутренний диаметр (см. табл. 7 приложения 13)
Значение в табл. 1 приложения 13.
Допуски наружного диаметра ПР резьбового калибра-пробки
(TdПР) и среднего диаметра (Td2ПР):
TdПР = 2TPL = 20011 = 0022мм;
Td2ПР = TPL = 0011 мм.
Исполнительные размеры ПР резьбового калибра-пробки:
наружный диаметр 12.0230022 ;
средний диаметр 11.04350011 ;
внутренний диаметр 10.166 max по канавке или радиусу.
Размер изношенного резьбового калибра-пробки по среднему диаметру:
d2ПРизн = D2 + EID2 + ZPL WGO = 11.026 + 0 + 0012 0017 = 1102.
5 РАСЧЕТ ИСПОЛНИТЕЛЬНЫХ РАЗМЕРОВ ПР И НЕ РЕЗЬБОВЫХ КАЛИБРОВ-КОЛЕЦ ДЛЯ НАРУЖНОЙ РЕЗЬБЫ (БОЛТА) М12-6g.
Основные размеры резьбы: наружный диаметр d=12мм средний диаметр d2=11.026мм внутренний диаметр d1=10.376мм.
верхнее отклонение dd2 d1es = -32мкм;
нижнее отклонение d2eid2 = -172мкм.
Рисунок 10 – Отклонения и допуски калибров
Рисунок 11 – Схема расположения полей допусков ПР и НЕ сторон калибра – кольца
Для ПР резьбового калибра-кольца наименьший предельный наружный диаметр:
Dmin ПР= d+ esd+ TR+H12=12-0032+0018+0108=12.094
Значение Н12 в таблице 1 приложения 13.
Наименьший предельный средний размер.
D2minПР= d2+ esd2-ZR-TR2=11.026-0032-0008-0009=10.905
Наименьший предельный внутренний диаметр
D1min ПР= d1+ esd1- TR2=10.376-0032-0009=10.335
Допуск среднего диаметра ПР резьбового калибра-кольца
Допуск внутреннего диаметра ПР резьбового калибра-кольца
Исполнительные размеры ПР резьбового калибра-кольца:
наружный диаметр 12.094 min по канавке или радиусу
средний диаметр 10.905+0018
внутренний диаметр 10.335 +0018
Размер изношенного ПР резьбового калибра-кольца по среднему диаметру:
D2ПРизн=d2+esd2-ZR+WGO=11.026-0032-0008+0021=11.007
Для НЕ резьбового калибра-кольца:
наименьший предельный наружный диаметр
Dmin НЕ= d+ esd+ TR+H12=12-0032+0018+0108=12.094
наименьший предельный средний размер
D2min НЕ= d2+ eid2-TR=11.026-0172-0018=10.836
наименьший предельный внутренний диаметр
D1min НЕ= d1+ eid1-2F1 -TR 2- TR =10.376-0268-03-0009-0018=9.781
Допуски на изготовление калибра.
Допуск среднего диаметра НЕ резьбового колибра-кольца
Допуск внутреннего диаметра НЕ резьбового калибра-кольца
TD1ПР=2TR=2*0018=0036
Исполнительные размеры НЕ резьбового калибра-кольца:
наружный диаметр 808 min по канавке или радиусу
средний диаметр 6952+0018
внутренний диаметр 6152+0036
Размер изношенного НЕ резьбового калибра-кольца по среднему диаметру
D2НЕизн=d2+eid2-TR2+WNG=11.026-0172-0009-0015=10.83.
РАСЧЕТ ПАРАМЕТРОВ ЗУБЧАТОГО КОЛЕСА
Модуль m=3 мм число зубьев z=31 и диаметр делительной окружности мм.
Так как то это зубчатое колесо нарезается без смещения (x=0) при α=20 и высоте головки зуба ha=m=4.
По ГОСТ 1643-81 «Основные нормы взаимозаменяемости. Передачи зубчатые цилиндрические. Допуски» определяем точность зубчатого колеса принимаем степень точности 8-А.
При выборе параметров контроля необходимо использовать показатели ГОСТ 1643-81 характеризующие кинематическую точность плавность работы контакт зубьев и боковой зазор. Для норм кинематической точности по 8-й степени определяем по ГОСТ 1643-81 таблице 6:
– допуск на колебание измерительного межосевого расстояния за оборот зубчатого колеса F
По 8-й степени точности определяем показатель плавности работы колеса по ГОСТ 1643-8 таблице 8 :
– допуск на колебание измерительного межосевого расстояния на одном зубе f"i =28 мкм.
По 8-й степени находим показатель норм контакта зубьев в передаче по ГОСТ 1643-81 таблице 12:
– суммарное пятно контакта по длине зуба не менее 40 % по высоте не менее 30 %.
Сопряжению вида А соответствует вид допуска а на боковой зазор класс отклонений межосевого расстояния VI .
Показателем обеспечивающим гарантированный боковой зазор является среднее значение длины общей нормали с предельными отклонениями.
Номинальный размер длины общей нормали определяется по формуле
Wm = (1476(2n+1)+z*001387)*m = 4114мм;
где n = 011z+05 = 011*56+05 = 4 число зубьев захватываемых губками нормалемера (целое число).
По ГОСТ 1643-81 «Основные нормы взаимозаменяемости. Передачи зубчатые цилиндрические. Допуски» таблица 16: Наименьшее отклонение средней длины общей нормали (первое слагаемое) ЕWms=200 мкм наименьшее отклонение средней длины общей нормали (второе слагаемое) ЕWms=11 мм(при Fr=45мм по таблице 17). Таким образом ЕWms=200+11=211(мм).
По ГОСТ 1643-81 «Основные нормы взаимозаменяемости. Передачи зубчатые цилиндрические. Допуски» таблице 18: Допуск на среднюю длину общей нормали при сопряжении вида А ТWm=100мкм[1].
Наибольшее отклонение средней длины общей нормали:
ЕWms+ ТWm=211+100=311мкм.
Показатель бокового зазора:
Так как наружный диаметр заготовки не используется в качестве базовой поверхности при установке зубчатого колеса на зубообрабатывающем станке и при контроле толщины зубьев поэтому диаметр может считаться свободным размером поле допуска h 12.
Допуск на биение окружности вершин зубьев принимается равным 01m=01*3=03. Отклонение перпендикулярности базового торца заготовки к рабочей оси зубчатого колеса приводит к неточности обработки зубчатых колёс которая в наибольшей мере отражается на отклонении направления зубьев. Величина допустимого биения базового торца заготовки должна быть установлена на основе допусков на отклонение направления зуба F:
где ширина зубчатого венца b=20мм. По ГОСТ 1643-81 «Основные нормы взаимозаменяемости. Передачи зубчатые цилиндрические. Допуски» таблица 11: допуск на погрешность направления зуба F=0009 мм (для норм контакта зубьев 8-й степени точности).
Все данные наносятся на чертеж зубчатого колеса выполненного в соответствии с ГОСТ 2.403-75.
СПОСОБЫ КОНТРОЛЯ ВАЛА.
Отклонения и допуски посадочных размеров вала контролируются гладкими ПР и НЕ калибрами – скобами:
Рисунок 12 – Контроль отклонений размеров вала калибром-скобой
– контролируемая деталь.
Контроль шпоночного паза осуществляется специальными калибром.
Рисунок 13 – калибр для контроля шпоночного паза.
Контроль вала под подшипник .
Отклонения и допуски форм поверхностей можно произвести установкой вала в призму:
Рисунок 14 – Контроль формы посадочной поверхности вала в призме
– индикатор часового типа;
– контролируемая деталь;
– контрольная плита.
Контроль допуска торцового биения производится координатной измерительной машиной (КИМ):
Рисунок 15 – Контроль допуска торцового биения при помощи КИМ
– контрольная плита;
По завершении работы были изучены методики подбора и расчета посадок для различного типа соединений а также методы и средства контроля заданных точностей.
Библиографический список
Анухин В.И. Допуски и посадки. Учебное пособие. 4-е издание – СПб.: Питер 2008.
Анурьев В.И. Справочник конструктора – машиностроителя: В 3-х т.: Т.2. – 7-е изд. перераб. и доп. – М.: Машиностроение 1992.
Белкин И.М. Допуски и посадки: Учеб. Пособие для студентов машиностроительных специальностей технических заведений. – М.: Машиностроение 1992.
Метрология взаимозаменяемость и стандартизация: Учебное пособие по выполнению курсовой работы. Компьютерная версия. — 2-е изд. перер. Т.В. Столярова В.А. Кувшинова О.В. Ковалерова Т.А. Поляева; Под ред. к.т.н. В.Н. Выбойщика. — Челябинск: Изд-во ЮУрГУ 2005 — 110 с.
ГОСТ 1643-81. Основные нормы взаимозаменяемости. Передачи зубчатые цилиндрические. Допуски.
kalibr_NE.cdw

Твердость рабочих поверхностей 58 64
поверхности заходных и выходных фасок
должны иметь хромовое покрытие.Рекомендуемая толщина
хромового покрытия - (0
Общие допуски: ГОСТ 30893.1-m.к
Маркировать 8133-0906:
val.cdw

zubchatoe_koleso.cdw
Средняя длина общей нормали
Допуски на колебание
делительного межосевого расстояния
Колебание длины оющей нормали
Допуск на радиальное биение
Общие допуски ГОСТ 30893.2-m;
kalibr_PR.cdw
Твердость рабочих поверхностей 58 64
поверхности заходных и выходных
фасокдолжны иметь хромовое покрытие.Рекомендуемая толщина
хромового покрытия - (0
Общие допуски ГОСТ 30893.1-m
Маркировать 8133-0906: