Вакуумный ленточный пресс




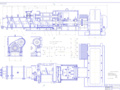
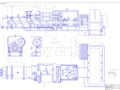
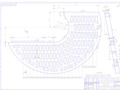
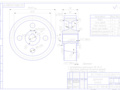
- Добавлен: 25.10.2022
- Размер: 3 MB
- Закачек: 2
Описание
Состав проекта
![]() |
![]() ![]() ![]() |
![]() |
![]() ![]() ![]() ![]() |
![]() ![]() |
![]() ![]() ![]() ![]() |
![]() ![]() |
![]() ![]() ![]() |
![]() ![]() ![]() |
![]() ![]() |
![]() ![]() ![]() |
![]() ![]() |
![]() ![]() |
![]() ![]() ![]() |
![]() ![]() ![]() ![]() |
![]() ![]() |
![]() ![]() |
![]() ![]() ![]() |
![]() ![]() ![]() |
![]() ![]() ![]() |
![]() |
![]() ![]() |
![]() ![]() ![]() ![]() |
![]() ![]() |
![]() ![]() ![]() ![]() |
![]() |
![]() ![]() |
![]() ![]() ![]() ![]() |
![]() ![]() ![]() ![]() |
![]() ![]() ![]() ![]() |
![]() ![]() |
![]() ![]() ![]() ![]() |
![]() ![]() |
![]() ![]() ![]() ![]() |
![]() ![]() |
![]() ![]() |
![]() ![]() ![]() ![]() |
![]() ![]() |
![]() ![]() |
![]() ![]() ![]() ![]() |
![]() |
![]() ![]() ![]() ![]() |
![]() ![]() ![]() ![]() |
![]() ![]() |
![]() ![]() |
Дополнительная информация
ЗАКЛЮЧЕНИЕ-3.docx
В результате модернизации сокращается время на проведение ремонта облегчается обслуживание и ремонт пресса.
В конструкторской части проекта произведен: кинематический и силовой расчет привода расчет зубьев цилиндрических колес на выносливость при изгибе расчет валов редуктора проверочный расчет подшипников обоснование основных технических характеристик пресса.
В технико – экономическом обосновании проекта произведен расчет изменения затрат на ремонт продолжительность и трудоемкость ремонта расчет заработной платы рабочих. Смета затрат на ремонт составила 761796 руб. при балансовой стоимости 18881000 руб. Смета затрат на ремонт до модернизации составляла 11355142 руб.
В разделе «Безопасность жизнедеятельности» предусмотрены технологические и организационные мероприятия исключающие или сводящие к минимуму несчастные случаи и чрезвычайные ситуации. Обеспечиваются оптимальные условия труда. Так же в проекте произведен расчет местной вытяжной вентиляции.
Опираясь на данные дипломного проекта можно сделать вывод о том что рассмотренная модернизация может быть рекомендована к практическому применению на предприятии.
спец.загр.вор.2.dwg

Спец. Шнек. вал.dwg

Шнековый вал в сборе
Нож питательной камеры
Перфорированная решетка
ДП 270101.41.25.02.04.01
ДП 270101.41.25.02.04.02
ДП 270101.41.25.02.04.03
ДП 270101.41.25.02.04.04
ДП 270101.41.25.02.04.05
ДП 270101.41.25.02.04.06
спецификация загр. вор.1.dwg

Стенка 110х20: l=200
ДП 270101.41.25.02.01.01
ДП 270101.41.25.02.01.02
ДП 270101.41.25.02.01.03
ДП 270101.41.25.02.01.04
ДП 270101.41.25.02.01.05
ДП 270101.41.25.02.01.06
ДП 270101.41.25.02.01.07
ДП 270101.41.25.02.01.08
ДП 270101.41.25.02.01.09
ДП 270101.41.25.02.01.10
ДП 270101.41.25.02.01.11
ДП 270101.41.25.02.01.12
ДП 270101.41.25.02.01.13
ДП 270101.41.25.02.01.14
ДП 270101.41.25.02.01.15
ДП 270101.41.25.02.01.16
ДП 270101.41.25.02.01.17
ДП 270101.41.25.02.01.18
ДП 270101.41.25.02.01.19
ДП 270101.41.25.02.01.20
ДП 270101.41.25.02.01.21
ДП 270101.41.25.02.01.22
ДП 270101.41.25.02.01.23
спец узла питательного вальца.dwg

ДП 270101.41.25.02.03.01
ДП 270101.41.25.02.03.02
ДП 270101.41.25.02.03.03
ДП 270101.41.25.02.03.04
Вал питательного вальца
Спец. Общ.вид сборка-01 (2).dwg

ДП 270101.41.25.02.01.00
ДП 270101.41.25.02.02.00
ДП 270101.41.25.02.03.00
ДП 270101.41.25.02.04.00
ДП 270101.41.25.02.05.00
ДП 270101.41.25.02.06.00
ДП 270101.41.25.02.07.00
ДП 270101.41.25.02.08.00
Спец. Общ.вид сборка-01.dwg

ДП 270101.41.25.01.01.00
ДП 270101.41.25.01.02.00
ДП 270101.41.25.01.03.00
ДП 270101.41.25.01.04.00
ДП 270101.41.25.01.05.00
ДП 270101.41.25.01.06.00
ДП 270101.41.25.01.07.00
ДП 270101.41.25.01.08.00
Спецификация.кожух.dwg

Крышка быстроходного
ДП 270101.41.25.02.09.01
ДП 270101.41.25.02.09.02
ДП 270101.41.25.02.09.03
ДП 270101.41.25.02.09.04
ДП 270101.41.25.02.09.05
ДП 270101.41.25.02.09.06
ДП 270101.41.25.02.09.07
ДП 270101.41.25.02.09.08
ДП 270101.41.25.02.09.09
Р.П.З.-3.docx
Вакуумный ленточный пресс загрузочная воронка валец питательный кожух звукоизолирующий решетка перфорированная скребок массоотражательный.
Проектом предусмотрена замена отражательного вальца отражательным скребком из износостойкого материала. Эта замена приводит к уменьшению количества деталей (редуктора подшипников вала) и снижению нагрузки на вал питательного вальца облегчению обслуживания и уменьшению ремонтных работ.
Для улучшения процесса вакуумирования проектом предусмотрен наклон перфорированной решетки.
Для снижения шума у редуктора проектом предусмотрены:
-увеличение числа и угла наклона зубьев быстроходной ступени редуктора;
-установка звукоизолирующего кожуха.
ПЕРЕЧЕНЬ УСЛОВНЫХ ОБОЗНАЧЕНИЙ
n - частота оборотов двигателя
Рдв - мощность двигателя
П - производительность
Т - вращающий момент
Uкп – передаточное число клиноременной передачи
Uоп – передаточное число зубчатой передачи
КHL – коэффициент долговечности
n н – коэффициент безопасности
н - допускаемое контактное напряжение колеса
Кн – коэффициент нагрузки
Кн - коэффициент неравномерности по ширине венца
КHL– коэффициент неравномерности между зубьями
Кнv – динамический коэффициент
Т2 – вращающий момент на колесе
в-ширина зубчатого венца
Rе– внешнее конусное расстояние
[] F-допускаемое напряжение на выносливость
d- средний делительный диаметр колеса
YF - коэффициент формы зубьев
Мв3 – изгибающий момент
Wнетто – осевой момент сопротивления вала
Ткр – крутящий момент
ПЕРЕЧЕНЬ ЛИСТОВ ГРАФИЧЕСКИХ ДОКУМЕНТОВ
Обозначение документа
Вакуумный ленточный пресс
0101.41.25.01.00.00 СБ
0101.41.25.02.00.00 СБ
0101.41.25.02.01.00 СБ
Кожух звукоизолирующий
0101.41.25.02.09.00 СБ
Шнековый вал в сборе с
перфорированной решеткой
0101.41.25.02.04.00 СБ
Узел питательного вальца
0101.41.25.02.03.00 СБ
0101.41.25.02.03.01 РЧ
Перфорированная решетка
0101.41.25.02.04.06 РЧ
0101.41.25.02.08.01 РЧ
0101.41.25.02.08.02 РЧ
Скребок отражательный
0101.41.25.02.06.01 РЧ
ТЕХНОЛОГИЧЕСКАЯ ЧАСТЬ
1 Краткое описание технологического процесса
Технологическим процессом предусмотрены следующие последовательности операций:
)Подача с дозированной шихты с транспортерной ленты в двухвальный лопастной смеситель непрерывного действия где первоначально смешивается в сухом виде затем увлажняется водой подогретой до 70 - 80° С и интенсивно перемешивается.
)Из смесителя масса поступает в загрузочную коробку ленточного пресса оборудованного мундштуком для выпуска бруса нормального сечения. Питание ленточного пресса должно быть непрерывным и равномерным. Из ленточного пресса лента (брус) должна выходить без трещин пустот расслоений и «драконового зуба».
)По выходу из мундштука ленточного пресса лента разрезается на заготовке в соответствии с размером прессуемого кирпича. Толщина заготовки должна обеспечивать выход сырца нормальных размеров.
)При формовке сифонных изделий и стопорных трубок выпущенная из ленточного пресса масса через мундштук нормального кирпича подается на вакуумный ленточный пресс для переработки под вакуумом.
)Из вакуумного ленточного пресса брус разрезается с помощью пневматического резательного станка наопределенного размера кирпичи.
)По люлечному подвесному конвейеру кирпичи поступают на допрессовочные пресса после этого кирпичи слаживаются на вагонетку и поступают в туннельные сушила для сушки и последующего обжига [3].
)На рисунке 1.1 показана технологическая схема.
)В таблице 1.1 дана техническая характеристика оборудования.
2 Технологическая схема
Рисунок 1.1. Технологическая схема пластического формования.
3 Технологическая характеристика оборудования
Таблица 1.1-технические характеристики оборудования.
Наименование параметра
Тарельчатый питатель
Число оборотов тарелки
Мощность электродвигателя
(без электродвигателя)
Ленточный транспортер
Частота вращения вала приводного барабана
Продолжение таблицы 1.1
Погрешность взвешивания
Двухвальный смеситель
Наружный диаметр лопастей
Частота вращения валов
Установленная мощность
Диаметр корпуса приемной коробки
Диаметр корпуса головки пресса
Частота вращения шнекового вала
Потребляемая мощность
Диаметр прессующего винта
Мощность электродвигателя
Окружная скорость транспортера
Давление сжатого воздуха в сети
Допрессовочный пресс
Число ударов в минуту
полуфабриката (сырца)
Температура теплоносителя начальная
Температура теплоносителя конечная
Продолжительность сушки
Влажность полуфабриката после сушки
вагонетки (без полуфабриката)
Количество вагонеток в печи
Продолжительность обжига
Скорость передвижения
4 Электрооборудование
Для работы вакуумлентпресса проектом предусмотрено подключение элекродвигателя и цепи управления к трёхфазной переменной сети напряжение 380В частота 50Гц.
Для привода вакуумлентпресса предусмотрен 3-х фазный эл. двигатель с короткозамкнутым ротором серии 4А.
В качестве коммутирующего аппарата для дистанционного управления двигателем предусмотрен эл. магнитный пускатель серии КМИ.
Основными командными аппаратами предусмотрены кнопки управления серии КЕ выключатели конечные типа ВК.
Защита эл. двигателя от короткого замыкания и перегрузок предусматривается автоматическим выключателем серии ВА и тепловым реле серии РТИ.
На рисунке 1.2 изображена электрическая принципиальная схема.
Схема электрическая принципиальная.
Рисунок 1.2 схема электрическая принципиальная.
Схемой предусмотрен один режим работы.
Перед запуском вакуумлентпресса в работу необходимо включить автоматический выключатель QF. Повернуть ключ-бирку SA в замке в положение «Вкл.».
Конечный выключатель SQ1 замыкает цепь при закрытии решётки загрузочного люка вакуумлентпресса.
Конечный выключатель SQ2 замыкает цепь при закрытии вакуумкамеры вакуумлентпресса.
Кнопкой SB2 производится включение привода пресса при этом происходит включение эл. магнитного пускателя КМ. Пускатель само блокируется а главные его контакты замыкают цепь питания эл. двигателя М.
Прекращение работы вакуумлентпресса осуществляется кнопкой управления SB1 при этом отключается питание цепи управления пресса. Двигатель М отключается.
Выключением ключ-бирки исключается возможность включения пресса посторонним персоналом.
В электрооборудовании вакуумлентпресса проектом предусмотрены следующие блокировки безопасности:
-блокировка решётки загрузочного люка вакуумлентпресса конечным выключателем SQ1.
-блокировка вакуумкамеры вакуумлентпресса конечным выключателем SQ2.
5 Литературный и патентный обзор
Особенности движения массы в ленточных прессах зависящие от конструкции пресса и свойств масс являются причиной неравномерного уплотнения массы выходящей из пресса. Эти особенности заключаются в следующем: под действием винтовых лопастей пресса масса совершает вращательное и поступательное движение. При этом скорость перемещения периферийных слоев массы соприкасающихся с внутренней поверхностью корпуса пресса меньше за счет возникающих сил трения. Местное торможение предопределяет различие скорости вращательного движения для периферийных и центрального слоев массы.
Собственно прессование (уплотнение) массы происходит между последним (нажимным) витком и материалом введенным в прессовую головку за предыдущий оборот винта; при этом масса наслаивается по спирали. Слои массы затем
деформируются и приобретают параболическую форму. Описанное движение массы в ленточном прессе и обусловливает образование дефектной структуры в изделиях – возникновение эллиптических и S-образных трещин.
В некоторых конструкциях прессов перед головкой имеется виброрешетка; под влиянием вибрации пластическая масса разжижается и слоистая структура разрушается. Величина прессового давления в ленточных прессах зависит от реологических свойств массы и в первую очередь от ее влажности пластичности связки и степени отощения. С увеличением влажности и пластичности всей массы величина прессового давления уменьшается. Прессовое давление зависит также от диаметра корпуса пресса длины прессовой головки и мундштука. С увеличением размеров этих частей пресса давление возрастает. Прессовое давление в ленточных прессах при переработке шамотных масс в зависимости от конструкции пресса и свойств массы равно 1-15 МПа.
Формование изделий выдавливанием пластичной массы через мундштук заданного сечения с последующим разрезанием получаемого непрерывного бруса на отдельные изделия широко используются в производстве строительной керамики и некоторой другой керамической продукции.
Прессы применяемые для пластического формования подразделяются по принципу действия на две основные группы: шнековые или винтовые и поршневые.
По направлению выхода формируемого бруса и по конструкции прессы подразделяются на горизонтальные и вертикальные.
По методу подготовке формируемой массы различают прессы вакуумные и прессы формирующие изделия без предварительного вакууммирования массы.
За последние годы наибольшее распространение получили горизонтальные вакуумные прессы в производстве строительного кирпича пустотелых керамических блоков ленточной черепицы дренажных и безраструбных канализационных труб тонкой технической керамики а также заготовок (валюшек) в производстве некоторых огнеупорных изделий.
Вертикальные вакуум-прессы применяются в производстве раструбных керамических труб и тому подобных фасонных изделий. Поршневые прессы получили широкое распространение в Соединённых Штатах Америки для формования канализационных труб и на некоторых огнеупорных заводах для прессования заготовок которые окончательно допрессовываются штемпельными прессами различных конструкций.
Формовкой называется процесс получения из огнеупорной массы изделий определённой формы и размеров. В зависимости от влажности масс различают два способа механизированного формования огнеупорных изделий: пластичное или мокрое прессование когда влажность масс составляет 15-20% и полусухое и сухое прессование когда влажность масс не превышает 10% и масса не обладает свойствами пластичности.
Менее экономичный пластичный метод формования интенсивно вытесняется более прогрессивным полусухим методом. Пластичным методом формуют не более 15 % всех изделий изготовляемых огнеупорной промышленностью. Процесс замены его полусухим методом продолжается.
Формовкой изделий предопределяется выполнение заводом заказа на выпуск продукции а потому прессы осуществляющие формование изделий являются
основными агрегатами предприятия. Формовку огнеупорных изделий осуществляют и другими способами – вибрационным пневматическим трамбованием литьём. Однако эти способы широкого распространения не получили.
Механическую формовку изделий при пластичном методе осуществляют обычно в два этапа на последовательно используемых прессах двух типов: на основном получают заготовки по форме и размерам напоминающие изделие а затем на дополнительном (допрессовочном) изделию придают окончательную форму и размеры. Заготовка производится на ленточных прессах окончательная формовка достигается на допрессовочных прессах.
Работа прессов основана на способности пластичных масс принимать требуемую форму под давлением внешних усилий и сохранять её после прекращения действия этих усилий. Для использования этих свойств пластичных масс оказывается достаточным при формировании приложить сравнительно небольшие удельные давления не превышающие 1-12Мнм2 (10-12кГсм2) при работе ленточных прессов и 12-35 Мнм2 (12-35 кгсм2) при работе допрессовочных прессов.
Назначение и принцип работы ленточных прессов. Ленточные прессы служат для формования пластичной массы уплотнением её и непрерывным выжиманием её через мундштук в виде ленты или бруса заданного поперечного сечения. При выходе из пресса лента массы разрезается на отдельные части заготовки определённых размеров и формы. Принцип работы ленточного пресса следующий: бесформенная масса через приёмную воронку поступает в цилиндр захватывается вращающимся шнеком и проталкивается им вдоль оси цилиндра по направлению к головке пресса. В головке масса несколько уплотняется и под давлением шнека проталкивается дальше к мундштуку через отверстие которого масса в виде непрерывного бруса или ленты выдавливается наружу. Отверстие мундштука по форме и размерам должно соответствовать поперечному сечению требующейся заготовки.
Формование на шнековых прессах глиняного кирпича пустотелых блоков облицовочной керамики ленточной черепицы дренажных труб а также заготовок (валюшек) для последующего прессования фасонных огнеупоров или ленточной черепицы на штемпельных прессах заканчивается отрезкой от непрерывно выходящего бруса отдельных изделий с заданными размерами. Этот процесс выполняется на современных заводах преимущественно резательными автоматами различных конструкций. Отрезка изделий ручными станками при высокой производительности шнековых прессов связана с напряжённым ритмом физического труда и поэтому применяется лишь при небольшом объёме производства или частой смене ассортимента изделий.
Большое разнообразие резательных автоматов работающих в керамической промышленности обусловлено различным сопротивлением резанию масс с разным содержанием влаги и отощающих материалов производительностью шнековых прессов комбинированием резательных автоматов с автоматами для укладки отрезаемых изделий на сушильные вагонетки различных типов а за рубежом – и конкуренцией машиностроительных фирм. Режущим элементом во всех аппаратах подобного типа является стальная струна выдерживающая высокие скорости резания при массах малой и средней плотности. При брусе высокой плотности который получают в современных мощных вакуумных прессах возникает необходимость снижения скорости резания. Поэтому для обеспечения высокой производительности при высокой плотности бруса используются автоматы с несколькими параллельно натянутыми струнами что дает возможность снизить скорость резания и обеспечить более благоприятные условия работы резательных автоматов.
Существует много конструкций резательных аппаратов которые не вполне удовлетворяют условиям производства поэтому продолжаются интенсивные поиски создания новых более совершенных конструкций. Все конструкции резательных аппаратов могут быть разделены на две группы:
а)ручные резательные станки
б) автоматические резательные автоматы.
Последние следует подразделить на полуавтоматические и автоматические. В каждой из указанных групп имеются конструкции станков предназначенных для отрезания одного или нескольких изделий одновременно.
Станок состоит из двух основных узлов: станины с приводом транспортера и резака с рамкой в форме скобы на которой натянута струна (рояльной проволоки) для резки ленты переработанной массы. Число струн может быть от одной до нескольких – зависит от количества одновременно отрезаемых заготовок.
В огнеупорной промышленности рядовые шамотные изделия прямоугольной конфигурации пластическим способом не изготавливают производство их переведено на полусухой способ формования в связи с чем в настоящее время применяют резательные аппараты с одной струной. Автоматические резательные станки широко применяют при пластическом формовании в шамотных цехах для получения заготовок толщиной 45-260мм. Их недостатками являются сложность конструкции и большая ремонтоемкость.
ЦЕЛИ И ЗАДАЧИ ПРОЕКТА
Проектом предлагается замена или модернизация быстроизнашивающихся деталей с минимальными затратами для производства. В частности на вакуум-камере предлагается замена отражательного валка отражательным скребком. Отражательный скребок по своей конструкции намного прост в изготовлении и в его обслуживании а также при его замене или ремонтетребуется меньше затрат.
При установке отражательного скребка отпадает необходимость в редукторе который передавал вращение с питательного валка на отражательный валок. А так как редуктор проектом не предусмотрен то в свою очередь отпадает необходимость в обслуживании ремонте редуктора.
Еще одна модернизация предусмотренная данным проектом – это модернизация узла питательного вальца.
)изменение конструкции питательного вальца а именно в первоначальном варианте питательный валец был изготовлен литьем и заказывался на специализированном предприятии. В данном проекте питательный валец изготавливается из нескольких деталей и заказывается на своем предприятии в механическом цехе;
)замена подшипникового узла который был в первоначальном варианте и подшипников на подшипники роликовые радиальные сферические двухрядные. Новая конструкция подшипникового узла и подшипники №3619 упрощают демонтаж и монтаж этого узла в процессе ремонта а также сокращает время на проведение этого ремонта.
) проектом предусмотрено изменение расположения перфорированной решетки вакуум-камеры. В частности у решетки установлен уклон в 10° для лучшего вакуумирования.
Недостатками работы традиционных конструкций узла перехода глиномассы из смесителя в вакуумную камеру являются:
невысокая эффективность процесса вакуумированияглиномассы из-за наложения жгутов верхних слоев на нижние;
загрузка заборной части шнека из узла перфорированной решетки осуществляется по длине приемного отверстия и скапливается непосредственно под решеткой;
отсутствие возможности регулирования давления глиномассы перед решеткой и толщины жгутов поступающих в вакуумную камеру;
как правило в нижней части пространства перед перфорированной решеткой требуется меньшая толщина глиняной пробки чем в верхней где прорыв воздуха наиболее вероятен что приводит к лишнему расходу электроэнергии на продавливание глиномассы в нижней части.
Анализ недостатков конуса и узла перфорированной решетки позволяет прогнозировать дальнейшие поиски путей их совершенствования. В этой связи представляет интерес конструкция узла перфорированной решетки.
Отличительной особенностью приведенной конструкции является то что перфорированная решетка выполнена составной и установлена под углом 10° к вертикали при чем одна часть решетки выполнена неподвижной а другая – с возможностью перемещаться относительно неподвижной массы.
Также задачей проекта является разработать методы снижения уровня шума превышающего ПДК у редуктора РМ-1000 привода пресса.
В процессе разработки дипломного проекта необходимо сделать следующие расчеты:
Кинематический и силовой расчет привода.
Расчет цилиндрической зубчатой передачи.
Расчет промежуточного быстроходного вала на прочность.
Проверочный расчет подшипников.
Обоснование основных технических характеристик пресса после модернизации.
Произвести сравнительный расчет затрат на себестоимость единицы продукции до и после проведения модернизации. Рассчитать экономический эффект и срок окупаемости проекта.
Предусмотреть и рассчитать мероприятия по безопасности жизнедеятельности проекта.
Составить вывод по целесообразности проведения данной модернизации.
1 Исходные данные для проектирования
В таблице 3.1 указанны исходные данные для проектирования.
Таблица 3.1-данные для проектирования.
2 Расчет основных параметров
2.1 Расчет производительности пресса
Производительность пресса рассчитывается по формуле (3.1)
где Д – диаметр прессующего винта м; (Д=0445м.);
d – диаметр ступицы винта м; (d=0150 м.)
- толщина лопастей м; (=0015 м.)
n – число оборотов винта м;
к – коэффициент использования пресса. (к =03 м.)
S = (065 ÷ 078) 0445 = 0325м
2.2 Расчет мощности электродвигателя
Мощность электродвигателя рассчитывается по формуле (3.2).
где Ртр. – мощность на преодоление сил трения между массой и поверхностью винта кВт;
Р1 – мощность на проталкивание массы через головку и мундштук кВт;
Р2 – мощность на транспортировку массы от приемной коробки к выпорной лопасти кВт;
Р3 – мощность на уплотнение массы;
Мощность на преодоление сил трения рассчитываем по формуле (3.3)
где - среднее удельное давление прессования кгсм²;
f – коэффициент трения;
R – радиус винта см;
r – радиус ступицы винта см ;
n – число оборотов винта обмин.
Среднее удельное давление прессования рассчитываем по формуле (3.4)
р = К1 · К2(0215W² - 1002W + 1905 + 108Д²) (3.4)
где К1 – коэффициент зависящий от длины головки К1 = 0988;
К2 – коэффициент зависящий от длины мундштука К2 = 091;
W – влажность массы %;
Д – диаметр лопастного вала м.
Р = 0988 091(0215 18² - 1062 – 18 + 1305 + 108 ·0445²) = 10 кгсм³
Мощность на проталкивание массы через головку и мундштук рассчитываем по формуле (3.5)
где - удельное давление кгсм²;
r – радиус ступицы винта м;
Мощность на транспортировку массы от приемной коробки к выпорной лопасти рассчитываем по формуле (3.6)
где Q – производительность м³ч;
X – плотность массы X = 16 т м³;
L – длина лопатного винта без выпорной лопасти м;
Кпр – коэффициент сопротивления продвижения массы Кпр = 40÷55.
Мощность на уплотнение массы рассчитываем по формуле (3.7)
- угол подъема винтовой лопасти рад;
Q – производительность м³ч.
Выбираем двигатель типа 4А250М6x3 Р = 55 кВт nдв = 985 обмин
3 Кинематический и силовой расчет привода
На рисунке 3.1 изображена кинематическая схема редуктора.
3.1 Расчет параметров редуктора
Рисунок 3.1. Кинематическая схема редуктора.
Мощность на быстроходном валу редуктора рассчитываем по формуле (3.8)
где -КПД клиноременной передачи = 096.
Скорость вращения быстроходного вала рассчитываем по формуле (3.9)
где - передаточное отношение клиноременной передачи.
Передаточное отношение клиноременной передачи рассчитываем по формуле (3.10)
где - диаметр шкива на электродвигателе =355 мм;
- диаметр шкива на быстроходном валу редуктора = 630 мм.
Мощность на промежуточном валу редуктора рассчитываем по формуле (3.8)
= 099 – КПД подшипников качения;
= 096 – КПД закрытой зубчатой передачи.
Скорость вращения промежуточного вала рассчитываем по формуле (3.9)
где - передаточное отношение 1-й ступени редуктора.
где =24- количество зубьев на шестерне;
=108- количество зубьев на колесе.
Мощность на тихоходном валу редуктора рассчитываем по формуле (3.8)
Скорость вращения тихоходного вала рассчитываем по формуле (3.9)
где - передаточное отношение 2-й ступени редуктора.
где =16- количество зубьев на шестерне;
=104- количество зубьев на колесе.
3.2 Расчет зубчатой передачи быстроходной ступени
Определяем число зубьев шестерни по формуле (3.10)
где =132 - суммарное количество зубьев колеса и шестерни;
=45 - передаточное отношение ступени.
Определяем число зубьев колеса по формуле (3.11)
Определяем фактическое передаточное отношение по формуле (3.12)
И проверяем отклонение от заданного передаточного отношения по формуле (3.13)
Проверяем фактическое межосевое расстояние по формуле (3.14)
где =6 - модуль зацепления зуба;
= - угол наклона зубьев.
Определяем фактические основные геометрические параметры передачи
делительный диаметр шестерни определяем по формуле (3.15)
Определяем диаметр вершин зубьев по формуле (3.16)
Определяем диаметр впадин по формуле (3.17)
3.3 Проверка зубьев шестерни и колеса на прочность
Выбираем материал для изготовления шестерни и колеса:
Шестерня – сталь 40Х термообработка – улучшение 240НВ
Колесо – сталь 45 термообработка – нормализация 200НВ.
Допускаемое напряжение определяем по формуле (3.18)
где=1 – коэффициент долговечности.
Допускаемое напряжение на изгиб определяем по формуле (3.19)
где=1 – табличный коэффициент.
Проверка прочности зубьев по контактным напряжениям рассчитывается по формуле (3.20)
где К =376 – вспомогательный коэффициент для косозубых передач.
-окружная сила в зацеплении рассчитывается по формуле (3.21)
где - диаметр делительной окружности колеса;
- крутящий момент на валу колеса.
=160 мм. – ширина обода колеса;
=108 - коэффициент распределения нагрузки между зубьями;
= 1 – коэффициент неравномерности распределения нагрузки по длине зуба для прирабатывающихся колёс;
=коэффициент динамической нагрузки зависит от окружной скорости и степени точности передачи рассчитывается по формуле (3.22).
=104- при =42мс 8 степень точности.
Условия прочности соблюдены.
Контактная прочность зуба обеспечена.
Проверка зубьев на прочность по напряжениям изгиба проверяется по формуле (3.23)
где m – модуль зацепления m = 6 мм;
b2- ширина венца зубчатого колеса b2 = 160 мм;
Ft – окружная сила зацепления;
KFα – коэффициент учитывающий распределение нагрузки между зубьями;
KF – коэффициент учитывающий приработку зубьев;
KFU – коэффициент учитывающий динамическую нагрузку;
YF2 – коэффициент учитывающий форму зуба;
Y – коэффициент учитывающий угол наклона зубарассчитывается по формуле (3.24).
Вывод: прочность зубьев по напряжениям изгиба обеспечена с большим запасом так как редуктор работает в тяжёлых условиях.
4 Расчет быстроходного вала редуктора на прочность
4.1 На рисунке 3.2 показаны силы действующие на быстроходный вал и нагрузки в вертикальной плоскости.
Определение усилий в зацеплении
Ft1 = Ft2 = = 16112 H.
Fr1 = Fr2 = Ft2 = 5936 H.
Fa1 = Fa2 = Ft2 = 16112 = 2555 H.
Рисунок 3.2 Схема нагрузок действующих на быстроходный вал в вертикальной
4.2 Определение реакций в опорах в вертикальной плоскости.
- Ft1 018 + R 056 = 0.
R = Ft1 - R = 16112 – 5179 = 10933 H.
4.3 Построение эпюры Q
Q1 = - R = - 10933 H.
Q = Q + Ft1 = - 10933 + 16112 = +5179 H.
4.4 Построение эпюры изгибающих моментов Мизг. (Н м).
Мн = - R 018 = - 10933 018 = 1968 Н м
На рисунке 3.3 показаны нагрузки действующие на быстроходный вал в горизонтальной плоскости.
Горизонтальная плоскость
Рисунок 3.3 Схема нагрузок действующих на быстроходный вал в горизонтальной
4.5 Определение реакций в опорах в горизонтальной плоскости.
+ Qк.п. 021 - Fr1 018 - Fa1 00713 – R 056 = 0
+ Qк.п. – R1+ Fr1 + R2 = 0
R = 7563 + 5963 + 603 = 14129 H.
4.6 Построение эпюры Q (Н.).
Q3 = + Qк.п. = 7563 H.
Q = Q - R1 = + 7563 – 14129 = - 6566 H.
Q = Q + Fr1 = - 6566 + 5936 = - 603 H.
Q2 = -R2 = - 603 H.
4.7 Построение эпюры изгибающих моментов Мизг. (Н м).
M1 = + Qк.п. 021 = 7563 021 = 1588 Нм
M = + R2 038 = + 603 038 = 229 Нм
M = M + Fd1 00713 = 229 + 2555 00713 = 411 Н м.
Анализируя эпюры М изгибающих моментов опасным сечением вала является сечение в точке “н”
Мн – суммарный изгибающий момент в точке “н”.
Приближенный расчет вала на прочность проводится по третьей теории прочности (теории наибольших касательных напряжений). По формуле (3.25)
Где Mu = Mн = 2010 Н м;
W = 01 1003 = 100000 мм3.
Допускаемое напряжение
=500 Мпа – для стали Ст.5;
Таким образом прочность вала при приближенном расчете обеспечена.
Уточненный расчет быстроходного вала редуктора на прочность
где [S] – допускаемый запас прочности;
[S] = 16 21 – при менее точной расчетной схеме.
Нормальные напряжения для валов применяются по симметричному циклу при котором амплитуда напряжений рассчитывается по формуле (3.26)
Касательные напряжений изменяются по нулевому циклу и рассчитываются по формуле (3.27)
где =02d3=0.21003=200000 мм3.
Коэффициенты концентрации нормальных и касательных напряжений без поверхностного упрочнения определяются по формулам (3.28 3.29)
где - табличные эффективные коэффициенты концентрации напряжений ;
- табличный коэффициент влияния абсолютных размеров
- коэффициент влияния шероховатости;
Определение предела выносливости рассчитывается по формулам (3.30 3.31)
Коэффициенты запаса прочности по нормальным и касательным напряжениям рассчитываем по формулам (3.32 3.33)
Определение общего запаса прочности рассчитывается по формуле (3.34)
Условия прочности соблюдены S = 37; [S] = 21;
Таким образом окончательно убеждаемся в результате уточненного расчета прочность вала обеспечена так как S> [S].
5 Расчет промежуточного вала редуктора на прочность
На рисунке 3.4 показаны силы действующие на промежуточный вал.
Рисунок 3.4 Схема нагрузок действующих на промежуточный вал.
5.1 Определение нагрузок действующих на промежуточный вал редуктора.
Вертикальная плоскость.
На рисунке 3.5 изображены нагрузки действующие на промежуточный вал в вертикальной плоскости.
5.2 Определяем реакций в опорах:
+ Ft2 018 + Ft3 038 - R 056 = 0.
+ R - Ft2 - Ft3 + R = 0.
R = 16112 + 64600 - 49014 = 31698 H.
Рисунок 3.5 Схема нагрузок действующих на промежуточный вал в вертикальной
5.3 Построение эпюры Q (н)
Q1 = - R = + 31698 H.
Q = Q - Ft2 = 31698 - 16112 = 15586 H.
Q2 = - R = - 49014 H.
5.4 Построение эпюры Мизг. (Н м)
Мн = + R 018 = 31698 018 = 5706 Н м
М3 = + R 018 = 49014 018 = 8822 Н м
На рисунке 3.6 изображены нагрузки действующие на промежуточный вал в горизонтальной плоскости.
5.5Определение реакций промежуточного вала в горизонтальной плоскости:
- Fa2 032 + Fr2 018 - Fa3 008 + R 018 = 0;
- R - Fr2 + Fr3 - R = 0.
R = - Fr2 - R + Fr3 = - 5936 – 17164 + 23798 = + 698 H.
Горизонтальная плоскость.
Рисунок 3.6 Схема нагрузок действующих на промежуточный вал в горизонтальной
5.6Построение эпюры Q (н)
Q = Q - Fr2 = - 698 - 5936 = - 6634 H.
Q2 = + R = + 17164 H.
5.7 Построение эпюры Мизг. (Н м).
М = - R 018 = - 17164 018 = -3090 Н м
М = М + М = - 3090 + 820 = - 2270 Н м
М = Fa3 008 = 10245 008 = 820 Н м
М = - R 018 = - 698 018 = - 126 Н м
М = Fa2 032 = 2555 032 = 818 Н м
М = М - М = - 126 – 818 = - 944 Н м.
Анализируя эпюры изгибающих моментов для промежуточного вала редуктора приходим к выводу что опасным сечением вала является сечение в т. «3»
5.8 Приближенный расчет вала на прочность производим по третьей теории прочности по формуле (3.25)
где М4 = М3 = 9347 Нм;
=700 Мпа – для стали Ст.40 термообработка улучшение;
Условия прочности соблюдены т.к. прочность вала при приближенном расчете обеспечена.
5.9 Уточненный расчет промежуточного вала редуктора на прочность.
где = 02 130³ = 439400 мм³.
- табличный коэффициент влияния абсолютных размеров ;
Определение предела выносливости в расчетном сечении вала рассчитывается по формулам (3.30 3.31)
Условия прочности соблюдены S = 22; [S] = 21;
6 Расчет шпоночных соединений
На промежуточном валу под зубчатым колесом первой ступени шпоночное соединение рассчитываем по формуле (3.35)
Условие прочности шпоночного соединения на промежуточном валу редуктора соблюдено
Прочность шпонки под клиновым шкивом на быстроходном валу рассчитываем по формуле (3.35)
= (094h – t1) lр = (094 14 – 9) 95 = 3952 мм²
Условие прочности шпоночного соединения на быстроходном валу редуктора соблюдено
7 Расчет подшипников качения
Исходные данные для расчета подшипника:
На быстроходном валу редуктора установлены подшипники № 7318 работает с легкими толчками.
Угловая скорость вала – W2 = 59 1с.
Осевая сила в зацеплении – Fа1 = 2555 Н.
Характеристика подшипника:
Требуемая долговечность подшипника Lh = 10000 часов.
Подшипники установлены по схеме враспор.
Реакции в подшипниках определяем по формуле (3.36)
Определяем осевые составляющие радиальных реакций по формуле (3.37)
Определение осевых нагрузок подшипников
Rа2 = 474 + 256 = 73 кН.
Определяем эквивалентную нагрузку
В зависимости от отношения и выбираем соответствующие формулы(3.38 и 3.39) для определения
Определяем динамическую грузоподъемность по большему значению эквивалентной нагрузки по формуле (3.40)
Предполагаемое количество отработанных часов рассчитываем по формуле (3.41)
Вывод: прочность подшипников установленных на быстроходном валу редуктора по динамической грузоподъёмности обеспечена.
На промежуточном валу редуктора установлены радиально – упорные роликовые конические подшипники № 7528.
Работает с легкими толчками угловая скорость вала – W3 = 131 1с
Осевая сила в зацеплении
Fа = Fа3 – Fа2 = 10245 – 2555 = 7690 Н = 769 кН
Реакции в подшипникахопределяем по формуле (3.36)
Определяем осевые нагрузки подшипников
Rа2 = Rs2 =14200 Н=142 кН
Rа1 = Rs2 – Fа = 142 – 769 = 65 кН
Вывод: прочность подшипников установленных на промежуточном валу редуктора по динамической грузоподъёмности обеспечена.
ТЕХНИКО-ЭКОНОМИЧЕСКОЕ ОБОСНОВАНИЕ ПРОЕКТА
1 Расчет технико-экономических показателей технической модернизации на участке производства
В проекте выполнена модернизация вакуумного ленточного пресса для пластической формовки керамических изделий прессо-формовочного цеха
Богдановичского огнеупорного завода.
Это позволит снизить себестоимость выпускаемой продукции в связи с уменьшением числа и стоимости ремонтов; времени текущих простоев оборудования.
2 Расчет проектно-производственных мощностей
и проектного объема производства
Планируется техническое перевооружение участка направленное на снижение себестоимости продукции.
Прессо-формовочный цех с непрерывным процессом производства продукции работающий по три смены в сутки с 8 часовой сменой включая праздничные и выходные дни. Следовательно календарный фонд работы оборудования принимается 365 суток. (8760 ч.)
3 Смета затрат на капитальный ремонт вакуумлентпресса
Годы эксплуатации – 48 лет
Метод ремонта – децентрализованный
Т1 = 308; Т2 = 9032; К = 4144
Категория ремонтной сложности – 22
К1 = 10 ; К2 = 115 ; К3 = 08
3.1 Периодичность и трудоёмкость ремонта
В таблице 4.1 указаны периодичность и трудоемкость ремонта вакуумлентпресса в таблице 4.2 график ППР.
Таблица 4.1-периодичность и трудоемкость ремонта.
Название оборудования
Количество часов на ремонты
Структура ремонтного цикла
Категории ремонтной сложности
Периодичность в сутках
Продолжительность простоя
Где: Т1 - текущее обслуживание (один раз в месяц по 40 минут);
Т2 – текущий ремонт оборудования (один раз в квартал по 8 часов до модернизации и один раз в квартал по 4 часа после модернизации);
К- капитальный ремонт (один раз в 4 года по 144 часа до модернизации и 72 часа после модернизации).
Плановый фонд рабочего времени после модернизации увеличится на 88 часов.
Таблица 4.2-график ППР.
Баланс времени работы вакуумлентпресса.
Таблица 4.3-баланс времени работы вакуумлентпресса
Календарный фонд времени оборудования (24 часа)
Режимный фонд времени (23 часа)
Расчет планового фонда времени оборудования.
Таблица 4.4-расчет планового фонда времени
Продолжительность в часах
Продолжительность 1 смены (Пс)
Плановые простои: в т.ч.
Подготовительно-заключительное время в т.ч. уборка рабочего места
Отдых и личные надобности
Настройка оборудования
Всего плановых простоев (ПРпл):
Чистое время работы оборудования на 1 смену (В)
Плановый коэффициент использования оборудования К=ВПс
3.2 Расчёт численности ремонтных рабочих
Численность ремонтных рабочих рассчитываем по формуле (4.1);
где R – категория ремонтной сложности ( таблица4.1 );
N – норматив единицы ремонтной сложности;
К1 – коэффициент учитывающий подготовительные работы К1 = 10;
К2 – коэффициент учитывающий годы эксплуатации оборудования К2 = 115;
К3 - коэффициент учитывающий степень механизации слесарных работ К3 = 08;
Тр – продолжительность капитального ремонта в часах ( таблица4 .1).
Продолжительность капитального ремонта в сутках:
Ремонт организован в 3 смены поэтому количество требуемых суток для ремонта рассчитываем по формуле (4.2);
где Тр- продолжительность капитального ремонта в часах ( таблица4.1 );
– количество часов в сутках.
3.3 Создание ремонтной бригады
Создаётся одна бригада из 6 человек. Работающие в 3 смены по скользящему графику. Бригада сквозная специализированная. Руководит бригадой 1 бригадир. В ночные смены назначается старший слесарь. В таблице 4.4 показан состав ремонтной бригады.
График работы: 1 смена – с 1-00 до 8-00 (продолжительность 7 часов)
смена – с 8-00 до 16-00 (продолжительность 8 часов)
смена – с 16-30 до 1-00 (продолжительность 8 часов)
Состав бригады и количество отработанных человеко-смен.
Таблица 4.5-состав бригады.
трудоемкость чел-час
слесарь-ремонтник (бригадир)
4 Расчёт фонда заработной платы ( ФЗП ).
Таблица 4.6-тарифные ставки
Тариф за ночную смену руб.
Тариф за дневную смену руб.
разряд+доплата за сварщика 15%
а) Прямая заработная плата ( 3 пр.) рассчитывается по формуле (4.3).
пр. = С час. N час. ( руб. ) (4.3)
где С час. – часовая тарифная ставка;
Nчас. – количество отработанных часов.
ЗПР. бр. = 388348 = 186384 руб.
ЗПР. сл. = 346790=31203 руб.
ЗПР. сл - св. = 399138=53585 руб.
Всего Зпр: 1049034 руб.
б) Доплата за ночное время работы ( Н )
Работа производится в 3 смены:
Nчас. н – количество отработанных ночных часов час.
Н=((346742)+(39942))04=125278 руб.
в) Доплата за вечернее время работы ( В )
Nчас. в – количество отработанных вечерних часов час.
Н=((346748)+(39948))02=71587 руб.
г) Доплата за бригадирство ( ) рассчитываем по формуле (4.6);
где ЗПР – прямая заработная плата руб.;
%бр. – премия за бригадирство = 10%.
д) Премия из ФЗП 40% ( П ) рассчитываем по формуле (4.7);
Н - доплата за ночное время работы руб.;
В-доплата за вечернее время работы руб.;
ЗБР -доплата за бригадирство руб.;
П = (1049034+125278+71587+18638)40%=505815 руб.
д) Основная заработная плата ( 3осн. ) рассчитывается по формуле (4.8);
осн. = 3пр. + Н + П +В+ 3бр. руб. (4.8)
ЗБР -доплата за бригадирство руб.
осн = 1049034+125278+71587+18638+505815=1770352 руб.
е) Общая заработная плата (.) рассчитывается по формуле (4.9)
. = 3 осн. Кр. руб. (4.9)
где Кр. – уральский коэффициент Кр. = 115.
= 1770352115 = 2035905
з) Страховые взносы с фонда оплаты труда (Н.ф.о.т ) насчитываются по формуле (4.10)
где % ф.о.т. – процент начислений 356%(34% страховые отчисления+16% страхование от несчастных случаев):
Результаты расчетов сведены в таблицу 4.7
Таблица 4.7-расчет заработной платы на ремонт до модернизации.
Сводная таблица расчёта заработной платы
Отработано человеко – час N час
Тарифная ставка Счас руб.
Заработная плата прямая Зпр руб
Заработная плата (руб)
За работу в ночное время
За работу в вечернее время
Расчет заработной платы на ремонт после модернизации.
На капитальный ремонт необходимо 3 суток(7224часа)
Состав бригады для ремонта после модернизации.
Таблица 4.8-состав бригады для ремонта после модернизации.
Расчет фонда оплаты труда после модернизации.
Таблица 4.9-расчет фонда оплаты труда после модернизации.
Страховые взносы составят 1017950356=36239 рублей.
5 Затраты на разборочно - сборочные работы до и после модернизации
Затраты на разборочные и сборочные работы до и после модернизации сведены в таблицы 4.10 и 4.11.
Таблица 4.10-затраты на разборочные и сборочные работы до модернизации.
Состав работы (последовательность выполнения) разборка.
Количество нормо-часов
Общая стоимость руб.
Подготовка ремонтной площадки
Продолжение таблицы 4.10
Демонтаж ремней клино-ременной передачи
Демонтаж головки мундштука
Демонтаж вала коренного
Демонтаж подшипников питателя
Разборка редуктора питателя
Разборка редуктора привода
Демонтаж всех подшипников
Итого разборочных работ (Т разб)
Монтаж подшипников питателя
Монтаж всех подшипников
Ревизия редуктора питателя
Ревизия электродвигателя
Ревизия редуктора привода
Ревизия вспомогательного оборудования
Ревизия предохранительного устройства
Ревизия питательного вальца
Сборка редуктора питателя
Сборка редуктора привода
Монтаж вала коренного
Монтаж загрузочного устройства
Монтаж прессующей головки
Монтаж ремней клино-ременной передачи
Монтаж кожуха клино-ременной передачи
Пробный пуск и сдача в эксплуатацию
Итого сборочных работ (Тсб)
Всего затрат (Зск) (Траз +Тсб)
Таблица 4.11-затраты на разборочные и сборочные работы после модернизации.
Стоимость нормо-часа Снч руб.
Демонтаж кожуха клино-ременной передачи
Демонтаж загрузочного устройства
Демонтаж прессующей головки
Демонтаж пластины вакуумкамеры
Монтаж пластины вакуумкамеры
Продолжение таблицы 4.11
Всего затрат ( Траз + Тсб)
6 Расчет стоимости запасных частей для ремонта до и после модернизации
В таблицах 4.12 и 4.13 рассчитана стоимость запасных частей до и после модернизации.
Таблица 4.12-стоимость запасных частей до модернизации.
Наименование деталей
Трудоемкость по операциям нормочасы
Стои-мость 1 нормо-часа руб.
Трудоемкость 1 детали
Клинореме-нная передача
Продолжение таблицы 4.12
Затраты на вспомогательные материалы
где Сбал – балансовая стоимость вакуумлентпресса
Прочие неучтенные затраты
где Тсб- итого сборочных работ из таблицы 4.5
Таблица 4.13-стоимость запасных частей после модернизации.
Клиноремен-ная передача
где Тсб- итого сборочных работ из таблицы 46
Затраты на вспомогательные материалы и приспособления (буферные тросы траверсы чалки пиломатериал для лесов и подмостей электроды уголки прутковый материал проволоку кислород ацетилен бензин и керосин для резаков и т.д.) принимать 0.5 от стоимости оборудования (Сбал) рассчитываем по формуле (4.11).
Прочие неучтенные затраты на ремонт (болты гайки метизы шплинты прокладочный материал дизтопливо для мойки деталей обтирочный материал и т.д.) принимать 2% от трудоемкости сборки узла машины (Тсб) умноженной на стоимость одного материала рассчитываем по формуле (4.12).
где - стоимость одного нормо-часа.
Трудоемкость сборки принимать из таблиц нормативов на ремонт за № 1396 графы 5.
Данные принимать из таблиц нормативов на ремонт за № 1396.
7 Смета затрат на капитальный ремонт вакуумлентпресса
В таблице 4.14 составлена смета затрат па капитальный ремонт вакуумлентпресса.
Таблица 4.14-смета затрат на капитальный ремонт.
Базовый вариант руб.
Проектируемый вариант руб.
отклонение (проектбаза) руб.
Услуги механического цеха
7.1 Расчет затрат на модернизацию
В целях экономии времени и средств проектом предусмотрено провести модернизацию совместно с капитальным ремонтом. В таблице 4.15 указаны затраты на модернизацию.
Таблица 4.15-затраты на модернизацию.
Наименование материала
Количество материалов
Стоимость единицы руб.
Быстроходная передача
Разборочные работы Тразб. (табл 4.9)
Монтаж скребка (Зрс)
Сборочные работы Тсб. (табл 4.10)
Заработная плата (табл.4.8)
Продолжение таблицы 4.15
Страховые отчисления
Затраты на вспомогательные материалы Звсп=(Смат 0.05)
Прочие неучтенные затраты Зпроч=(Смат 002)
ИТОГО затрат Змод = Смат+Тразб+Зрс+ Тсб+З+Отч
7.2 Обоснование объемов производства товарной продукции.
Средняя производительность вакуумлентпресса составляет 119 тонн в час. Годовой выпуск продукции вакуумлентпресса составляет 7500 тонн в год.
Время отведенное на ремонты оборудования составляет:
до реконструкции в соответствии графику Рд = 184 чгод
после реконструкции Рп = 96 чгод
Соответственно плановый фонд рабочего времени условно увеличится на 88 часа.
Тпр = 750062966384=7605 тн.
Где: 6296-плановый фонд времени до модернизации час;
84- проектный плановый фонд времени после модернизации час.
Расчет товарной продукции
Таблица 4.16-расчет товарной продукции
Годовой выпуск продукции
Проектируемый вариант
Стоимость тыс. руб.
Прирост товарной продукции
(4.13) где: ТПпроек - товарная продукция по проекту руб.год;
ТПбаз – товарная продукция до модернизации руб.год.
8 Расчет затрат на производство продукции
Расчет произведен с учетом разницы времени на текущие и капитальные ремонты до и после модернизации.
Таблица 4.17-расчет затрат на производство продукции.
Затраты на электроэнергию.
Где Р- потребляемая мощность= 75кВт
z- стоимость 1 кВт часа = 26руб.
Затраты на ремонт оборудования согласно смете
Амортизационные отчисления
Са1тн=1888107500=252 рубтн
Где Р- потребляемая мощность= 55кВт
Са1тн=19021437605=25 рубтн
Расчет заработной платы рабочих
Фт=СчN где Фт- прямая заработная плата Сч-часовая тарифная ставка прессовщика 5 разряда (3883 руб.час)съемщик-укладчик3 разряда(4 человека) N-кол-во отработанных часов в году.
Фт=142846296=8993206
Доплата за работу в ночное время 40%
Н=Фт40%3 где Н – ночные
Н=(899320604)3=1199094 руб.
Доплата за работу в вечернее время 20%.
В=Фт20%3 где В – вечерние
В=(899320602)3=599547 руб.
Приработок за выполнение норм:
Пр=Фт03 где Пр-приработок за выполнение норм выработки.
Пр=899320603=2697962
Фдоп=1199094+599547+2697962=4496603
Фонд заработной платы общий с учетом районного коэффициента 15%
Фонд заработной платы общий на 1тн.
Страховые отчисления 356%от ФЗП.
Остр=217185930356=7731819 руб.
Остр 1тн=77318197500=1031 рубтн
Накладные расходы 1% от ФЗПоб
Накладные расходы на 1тн
Н=(911890604)3=1215854 руб.
В=(911890602)3=607927 руб
Пр=911890603=2735672
Фдоп=607927+1215854+2735672=4559453
Остр=220221570356=7839889 руб.
Остр 1тн=78398897605=1031 рубтн
Затраты на объём производства
Затраты общие на 1тн
Изменение себестоимости годового выпуска
где: Спроек – себестоимость товарного выпуска по проекту руб.год;
Сбаз - себестоимость товарного выпуска до модернизации руб.год.
Свод затрат на годовой объем и на 1 тонну изделий.
Таблица 4.18-себестоимость технологического передела
Затраты до модернизации
Затраты после модернизации
9 Основные технико-экономические показатели проекта
Основные технико-экономические показатели проекта сведены в таблицу 4.19.
Таблица 4.19-технико-экономические показатели проекта.
Наименование показателя
Объем производства тн.
Производительность тн.
Себестоимость прессования 1 тонны полуфабриката руб. в.т.ч.
Смета на капитальный ремонт
Средняя заработная плата руб.
Затраты на модернизацию тыс.руб.
Условно-годовая экономия тыс.руб.
Срок окупаемости лет
Условно годовая экономия составляет:
ΔСед=(Сед до-Сед после)Q (4.15)
ΔСед = (5996-5506)7605 =372645 тыс. руб.
Срок окупаемости проекта:
Вывод: Проведение модернизации целесообразно т.к. при той же численности рабочих годовой объем выпускаемой продукции вырос на 14% себестоимость 1 тонны продукции снизилась на 82% фонд оплаты труда увеличился на 14% условно годовая экономия составляет 3726 тыс. рублей.
БЕЗОПАСНОСТЬ ЖИЗНЕДЕЯТЕЛЬНОСТИ
Промышленная площадка Богдановичского огнеупорного завода расположена на восточной окраине города на расстоянии 1 км от станции Богданович Свердловской железной дороги. Территория площадки с запада и юга ограничена городской застройкой с севера – железнодорожными путями МПС с юго-востока – площадкой базы стройиндустрии с северо-востока – свободная от застройки территория. Рельеф площадки спокойный с незначительными перепадами высот с запада на восток где находятся заболоченные участки и пруд. Для расчета рассеивания загрязняющих веществ в атмосфере и определения приземных концентраций принимается поправочный коэффициент на рельеф равный 1.
В районе размещения рассматриваемого производства преобладают ветры западного и юго-западного направлений. Скорость ветра вероятность превышения которой в данной местности 5 % равна 7 мс.
Средняя температура самого жаркого месяца +176 град.С наиболее холодного – -168 град.С.
Производственная площадка Богдановичского огнеупорного завода (в дальнейшем БОЗ) на территории которой находится прессо-формовочный цех (в дальнейшем ПФЦ) относится к II классу опасности с нормативным размером санитарно-защитной зоны 500 м.
1 Обеспечение безопасности работающих
1.1 Характеристика условий труда
Площадь(S) основного помещения прессо-формовочного цеха составляет 540 м2 объем(V) 3240 м3.
Размеры вспомогательных помещений:
сварочный пост S=19.5 м2 V=60 м3 ;
слесарная мастерская S= 10.0 м2 V=30 м3
Производственная среда в помещениях участка полусухого прессования прессо-формовочного цеха достаточно однородна так как все основные технологические процессы по приготовлению сырья производятся в других цехах.
Повышенный уровень шума и вибрации наблюдаются на рабочих местах прессовщика и бегунщика. Так же на эти рабочих местах наблюдается повышенная запылённость.
На всех технологических участках прессо-формовочного цеха опасным фактором производства является электрический ток опасность возгорания а также опасность травмирования.
Опасные и вредные факторы производства увеличивают степень риска получить травму на данном производстве.
Оценка риска получить травму ( R ) проводится по формуле (5.1);
где Сn - число несчастных случаев на производстве за год ;
Np - общее число работающих в сфере производства.
Np в 2010 г. составляло 3000 человек
2 Обеспечение безопасности труда
2.1 Мероприятия по электробезопасности
Помещение прессо-формовочного цеха по опасности поражения электрическим током относится к категории особо опасных.
В ПФЦ используется переменный электрический ток напряжением 380 В частотой 50 Гц.
Для обеспечения безопасности людейпроектом предусмотрено:
- недоступность токоведущих частей;
- заземление (Rз не выше 4 Ом) ГОСТ 12.1.030-81. [17];
- зануление электрооборудования;
- закрытие защитными оболочками токоведущих частей электродвигателей и их надежное изолирование;
- разделение электрических сетей; - использование малых напряжений на управляющих цепях.
2.2Пожарная безопасность
I. Помещениепрессо-формовочного цеха относится к категории производств по пожарной безопасности «Д» НПБ 105-03 и степени огнестойкости 3. СНИП 21-01-97[22 ]
II. Возможные причины возгорания:
-короткое замыкание в электропроводах и электрооборудовании;
-перегрев оборудования от перегрузок;
-неосторожное обращение с огнем при проведении электрогазосварочных работ.
Проектом предусмотрены следующие средства пожаротушения:
оборудованиевсех помещений цеха водопроводами и гидрантами. - обеспечение производственного помещения первичными средствами пожаротушения ГОСТ 12.1.004-85. [15] ;
-оборудование противопожарного щита ведрами асбестовым полотном ящиком с песком двумя воздухопенными огнетушителями ОХП-10 и одним углекислотным ОУ-5 ГОСТ 12.1.004-85. [15].
IV. Предусмотрены два эвакуационных выхода ГОСТ 12.1.004-85.
Размеры эвакуационных проходов:
к восточному выходу- 25 м
к западному выходу - 25 м
Размеры эвакуационных выходов:
Ширина восточный выход - 25 м
западный выход - 25 м
Максимальное удаление рабочих мест от ближайшего выхода – 15 м.
Источником повышенного шума в ПФЦ являются движущиеся и вращающиеся металлические части прессов бегунов питателей и другого оборудования.
Фактический уровень шума в цехе 80 ДБА. Нормированный уровень звукового давления 80 ДБА. ГОСТ 12.1.003-83 [26]
- замена цилиндрической прямозубой передачи на косозубую;
- установка звукоизолирующего кожуха.
2.4 Защита от вибрации
Источниками общей и локальной вибрации в ПФЦ являются вращающиеся механизмы прессов бегунов питателей и другого оборудования.
Различают общую и локальную вибрацию.
Фактический уровень вибрации в цехе 84 ДБ. Нормированный уровень локальной вибрации 109 ДБ общей 92 ДБ. ГОСТ 12.1.003-83. [17]
Для снижения вибрации проектом предусмотрено жесткое крепление оборудования к фундаменту.
2.5 Защита от механического травмирования
Источником механического травмирования в ПФЦ являются движущиеся и вращающиеся металлические части прессов бегунов питателей и другого оборудования.
Проектом предусмотрено:
- движущиеся и вращающиеся части прессов смесительных бегунов питателей элементы привода и передачи оборудовать надежно закрепленными ограждениями исключающие доступ к данным частям во время работы ГОСТ 12.2.062-81 [21];
- оснастить оборудование предпусковой звуковой сигнализацией ГОСТ 12.2.022-81
- устройства для предотвращения самопроизвольного включения Эл.двигателей конечные выключатели блокировки ГОСТ 12.4.155-85. [16]
2.6 Обеспечение рационального освещения
Проектом предусмотрена система естественного искусственного и совмещённого освещения:
Характеристика зрительных работ грубая.
Разряд зрительных работ V
-прессовщик – Е=200Лк
-слесарь-ремонтник – Е=200Лк
-естественное освещение боковое одностороннее через оконные проемы
-рабочее освещение предусмотрено во всех помещениях
-эвакуационное освещение.
ГОСТ 12.1.019-79 [16]
2.7 Категория тяжести работ
Категория тяжести работ предусмотрена ГОСТом 12.1.005-88 и показана в таблице 5.1.
Таблица5.1 . Категории тяжести работ.
Для притока свежего воздуха удаления вредных веществ и поддержания параметров микроклимата проектом предусмотрена механическая приточно-вытяжная и естественная вентиляция. ГОСТ 12.2.003-91 [22] .Местная вытяжная вентиляция предусмотрена в местах сосредоточения и выделения вредных веществ.
3.1Расчет местной вытяжной вентиляции
На рисунке 5.1 изображена схема местной вытяжной вентиляции ПФЦс забором воздуха из мест сосредоточения и выделения вредных веществ.
Для того что бы частицы пыли находились во взвешенном состоянии Рассчитываем оптимальную скорость воздушно-пылевого потока U по формуле (5.2)
где плотность глины 2400.
Рисунок 5.1. Схема местной вытяжной вентиляции ПФЦ.
Определяем диаметры труб от пылезаборников по формуле (5.3);
где Q1-рекомендуемый поток воздуха для оптимального пылеудаления через один пылезаборник
-оптимальная скорость воздушно пылевого потока.
Принимаем диаметр трубопроводов от заборников до коллектора d1=300мм.
Определяем суммарный расход воздуха по формуле (5.4);
где n-количество пылезаборников n=7.
Определяем диаметр коллектора и всасывающего трубопровода перед циклоном по формуле (53);
где 2-20 т.к. при этой скорости движения воздушно-пылевого потока наиболее эффективно работает циклон.
Принимаем диаметр коллектора и всасывающего трубопровода перед циклоном d2=560мм.
Определяем диаметр трубопровода на выходе из циклона и перед вентилятором по формуле (5.3);
где3=10рекомендуемая скорость очищенного воздуха на выходе из циклона
Принимаем диаметр трубопровода d=800мм.
Общие потери давления в трубопроводах рассчитываем по формуле (5.5);
где - сопротивление во всасывающих и нагнетательных трубопроводах;
- местные сопротивления;
- сопротивление циклона;
- сопротивление вытяжной трубы.
Сопротивление во всасывающих и нагнетательных трубопроводах рассчитываем по формуле (5.6);
где - табличный коэффициент трения по длине трубы;
= 0056 при 1=18; d1=300мм;
= 0024 при 2-20; d2=560мм;
=0017 при 3-10; d3=800мм;
- длинна трубопровода м;
- плотность запыленного воздуха ;
= 135 по данным О.А.О. «Огнеупоры» г. Богданович;
- скорость движения запыленного воздуха.
Сопротивление во всасывающих и нагнетательных трубопроводах рассчитываем как сумму сопротивлений на участках с учетом их длин и диаметров.
Местные сопротивления рассчитываем по формуле (5.7);
где -коэффициент местных сопротивлений зависит от угла и определяется по таблице
Сопротивление на участке вытяжной трубы рассчитываем по формуле (5.8);
где =0017 при 3-10; d3=800мм.;
Сопротивление в циклоне находим из справочника для циклонов НИИОГАЗ ;
По общему гидравлическому сопротивлению и по суммарному расходу воздуха подбираем вентилятор типа ВР-86-77-8; давление .
Диаметр ротора вентилятора Д=800мм.
Мощность электродвигателя определяем по формуле (5.9);
где- коэффициент запаса мощности;
Для меньших мощностей =13 14;
Подбираем ближайший по мощности электродвигатель ;
Показатели условий труда в рабочей зоне сведены в таблицу 5.2.
Таблица 5.2.Показатели условий труда в рабочей зоне
Наименование профессии
Категория тяжести работы
Параметры микроклимата
Освещённость фактнорм лк
Наименование вредного вещества на рабочем месте
Концентрация вредного вещества фактнорм*. мгм3
Наименование энергетического воздействия на среду
Уровень энергетического воздействия
Площадь приходящаяся на одного работающего фактнорм**. м2
приходящегося на одного работающего фактнорм**. м3
Относительная влажность %
Диоксид кремния кристаллический при содержании его в пыли от 20 до 70 %
*ГОСТ 12.1.005-88 [15]
**СП 2.2.1.1312-03[31]
4 Природопользование и охрана окружающей среды
При транспортировке к вакуумлентпрессу при прессовании глино-шамотной массы и придальнейшей резке массы на заготовки и ее дальнейшей транспортировке к допрессовочному прессу в воздух выбрасывается некоторое количество загрязняющих веществ. В основном это кремний-содержащая пыль которая отрицательно влияет на окружающую среду и на здоровье человека.
В связи с этим проектом предусмотрена установка в ПФЦ пылеочистных сооружений (циклонов).
4.1Перечень загрязняющих веществ выбрасываемых в атмосферу
В таблице 5.3 указаны загрязняющие вещества выбрасываемые в атмосферу прессо-формовочным цехом.
Таблица 5.3. Загрязняющие вещества.
Наименование вещества
КОП вещества значение вещества
Пыль неорганическая 70-20% двуокиси кремния (шамот цемент и т.д.)
Хром шестивалентный (в пересчете на 3х окись хрома)
Свинец и его соединения
* ГН 2.1.6.1338 - 03.
Объем выполняемой работы по контролю состояния воздушной среды определяется категорией опасности производства ( КОП ) вычисляемой
- относительный коэффициент опасности принимается в зависимости от класса опасности вещества.
КОП 104 значит предприятие относится ко 2-й категории опасности и для него необходимы следующий перечень основных разделов и подразделов входящих в состав проекта ПДВ:
-карта-схема предприятия;
-ситуационная карта-схема района размещения предприятия;
-краткая характеристика предприятия как источника загрязнения атмосферы(технология очистное оборудование перспективы развития);
-сведения о залповых выбросах;
-сведения об ущербе который причиняют выбросы предприятия окружающей среде;
-параметры выбросов загрязняющих веществ;
-расчеты и анализ уровня загрязнения атмосферы;
-предложения по достижению нормативов ПДВ;
-план мероприятий по достижению нормативов ПДВ;
-мероприятия по регулированию выбросов при НМУ;
-контроль над соблюдением нормативов ПДВ;
4.2 Чрезвычайные ситуации
Урал является зоной неопределённой сейсмичности аномальных осадков и температур. Причинами техногенных чрезвычайных ситуаций могут быть:
- прорывы и разрушения газо и водопроводов
- прекращение функционирования ливневых стоков и канализации
- обрушение фасадов и перекрытий зданий
- разлив технических жидкостей
В случае возникновения чрезвычайной ситуации (пожара)
-дежурный электрик отключает эл.питание оборудования цеха и включает аварийную светозвуковую сигнализацию. В случае отсутствия электрика в цехе в период ЧС эти функции выполняет заранее проинструктированное замещающее лицо из персонала цеха.(слесарь бегунщик сварщик прессовщик лафетчик). После чего сообщает о произошедшем администрации цеха и приступает совместно с другим персоналом цеха к локализации очага возгорания первичными средствами пожаротушения.
Мастер цеха после вызова пожарных организует тушение очага возгорания силами персонала цеха. Если потушить не удается проводит эвакуацию людей из опасной зоны. Начальник цеха сообщив о происшествии руководству завода направляет человека для встречи пожарной бригады после чего помогает разместить эвакуированных оказывает необходимую помощь пострадавшим. По прибытии пожарного подразделения обязан проинформировать руководителя тушения пожара о конструктивных и технологических особенностях объекта прилегающих строениях и сооружениях о количестве и о пожароопасных свойствах хранимых и применяемых веществах изделиях и других сведениях необходимых для успешной ликвидации и предупреждения развития пожара.
Вывод: Разработанное в данном проекте оборудование обеспечивает достаточную безопасность обслуживающего персонала и минимальное воздействие на окружающую среду.
БИБЛИОГРАФИЧЕСКИЙ СПИСОК
Василевский П.А. Технология и оборудование шамотного производства. П.А. Василевский. С.: Научно-техническое издательство 1956 386с.
Ильевич А.П. Машины и оборудование для заводов по производству керамики и огнеупоров. А.П. Ильевич. М.: Машиностроение 1975
Сапожников М.Я. Механическое оборудование для производства строительных материалов и изделий. М.Я Сапожников. М.: Государственное научно-техническое издательство машиностроительной литературы. 1962
Краузе Г.Н. Редукторы. Справочное пособие. Г.Н. Краузе Н.Д. Кутилин С.А. Сыцко. М.: Машиностроение 1965 638с.
Королев П.Г. Сопротивление материалов. К.: Высшая школа 1974 322с.
Шейнблит А.Е. Курсовое проектирование деталей машин. К.: Янтарный сказ 1999 455с.
Чернавский С.А. Курсовое проектирование деталей машин. 2-е изд. дополн. иперераб. С.А. Чернавский К.Н. Боков И.М. Чернин М.: Машиностроение 1988 414с.
Горфинкель В.Я. Экономика предприятий. Учебник. В.Я. Горфинкель В.А. Швандара. М:. Юнити 1998 742с.
Справочник по технике безопасности противопожарной технике и производственной санитарии. Том 2. Директивные материалы общие положения правила нормы инструкции. А.И. Игнатка. Л:. Судостроение 1971 662с.
Перель А.Е. Подшипники качения. Справочник. М.: Машиностроение 1991 424с.
Юдин Е.Я. Борьба с шумом на производстве. М.: Машиностроение 1985 362с.
Бринза В.Н. Охрана труда в черной металлургии. В.Н. Бринза М.Н. Зиньковский. М.: Металлургия 1982 328с.
Каменев П.Н. Отопление и вентиляция. Часть . Вентиляция. П.Н. Каменев. М:.Стройиздат 1964 470с.
Калинушкин М.П. Вентиляторные установки. М.: Высшая школа 1979 223с.
Оборудование для получения изделий методом пластического прессования. Методические указания по курсовому и дипломному проектированию. сост:. Ю.П. Канусник А.В. Говоров. Екатеринбург : ГОУ ВПОУГТУ-УПИ 1993г 32с.
Безопасность и экологичность проекта. Методические указания к дипломному проекту. сост:. А.Н. Фетисов Е.В. Сафронов Г.В. Тягунов. Екатеринбург УГТУ-УПИ 2008 18с.
ГОСТ 12.1.005-88 ССБТ. Общие санитарно-гигиенические требования к воздуху в рабочей зоне.
ГН 2.1.6.695-98 Гигиенические нормативы. ПДК вредных веществ в воздухе рабочей зоны.
ГОСТ 12.1.030-81 ССБТ. Электробезопасность. Защитное заземление. Зануление.
ГОСТ 24940-97 Здания и сооружения. Методы измерения освещенности.
ГОСТ 12.1.012-90 Вибрационная безопасность.
СаНПиН 2.2.1.2.1.1. 1031-01 Санитарно-защитная зона и санитарная классификация предприятий сооружений и иных объектов.
ГОСТ 12.2.062-81 ССБТ. Оборудование производственное. Ограждения защитные.
СНиП 2.04.05-91 (2001) Отопление вентиляция кондиционирование.
ГН 2.2.5.1313-03 ПДК вредных веществ в воздухе рабочей зоны.
ГОСТ 17.2.3.02-78 Охрана природы. Атмосфера. Правила установления допустимых выбросов вредных веществ промышленных предприятий.
СНиП 23-05-95. Строительные нормы и правила. Нормы проектирования. Естественное и искусственное освещение.
НПБ 105-95 Определение категорий помещений и зданий по взрывоопасной пожарной опасности.
СНиП 21-01-97 Определение зданий по степени огнестойкости конструктивной и функциональной пожарной опасности.
ГОСТ 12.1.036-81 ССБТ. Шум. Допустимые уровни шума в жилых и общественных зданиях.
СП 2.2.1.1312-03 Санитарно-эпидемиологические правила.
ВВЕДЕНИЕ-3.docx
Вакуумлентпресс используется на заводе для выпуска сифонных заготовок. Хотя эти прессы предназначены для обработки тонких керамических масс они удовлетворительно работают и на пластичных шамотных массах.
Для работы ленточных прессов характерным является то что глиняная масса в процессе переработки обогащается воздухом. Он проникает в массу не только во время продвижения ее в прессе но и другими путями. До 25% растворенного воздуха содержится в почвенной воде. Перемешивание массы в смесителях также связано с дополнительным захватом и запрессовкой воздуха.
Часть воздуха находится в комьях глиняной массы и при неудовлетворительном замесе он не в состоянии выйти на поверхность и поступает также в пресс. В общем в выходящем брусе может оказаться до 10% воздуха который резко ухудшает качество получаемой ленты. Для восстановления ценных свойств массы прибегают к процессу обезвоздушивания (деаэрации) массы.
Вакуумирование массы позволяет: повысить плотность и пластичность формуемой массы уменьшить деформацию резательной проволоки изделия получаются с острыми краями повысить прочность пластичность и однородность обжигаемых изделий.
Производительность пресса и качество формуемых изделий в большей степени зависят от износа рабочих деталей и зазора между ними. Нужно регулярно поверять следующие зазоры: зазор между кромками лопастей глиномешалки и накладками корыта (не более 15мм) зазор между нагнетательным валком и лопастью шнеки (не более 10мм) зазор между лопастями шнека и рубашкой (не более 5мм).
Для облегчения условий обслуживания и ремонта не влияя на производственный процесс проектом предлагается замена или модернизация быстроизнашивающихся деталей с минимальными затратами для производства. То есть на вакуум-камере предлагается замена отражательного валка отражательным скребком. Отражательный скребок по своей конструкции более прост в изготовлении и в его обслуживании а также при его замене или ремонте меньше требует затрат.
При установке отражательного скребка отпадает необходимость в редукторе который передавал вращение с питательного валка на отражательный валок. А так как редуктор проектом не предусмотрен то в свою очередь отпадает необходимость в обслуживании ремонте редуктора.
Проектом предусмотрено изменение перфорированной решетки вакуум-камеры. В частности решетку наклонили на 10 для лучшего вакуумирования.
Недостатками работы традиционных конструкций узла перехода глиномассы из смесителя в вакуумную камеру являются:
-невысокая эффективность процесса вакуумированияглиномассы из-за наложения жгутов верхних слоев на нижние;
-загрузка заборной части шнека из-за узла перфорированной решетки осуществляется неравномерно по длине приемного отверстия и скапливается непосредственно под решеткой;
-отсутствие возможности регулирования давления глиномассы перед перфорированной решеткой и толщины жгутов поступающих в вакуумную камеру;
-как правило в нижней части пространства перед перфорированной решеткой требуется меньшая толщина глиняной пробки чем в верхней где прорыв воздуха наиболее вероятен что приводит к лишнему расходу электроэнергии на продавливание глиномассы в нижней части.
Анализ недостатков конуса и узла перфорированной решетки позволяет прогнозировать дальнейшие поиски путей их совершенствования. В этой связи представляет интерес конструкция узла перфорированной решетки. Отличительной особенностью приведенной конструкции является то что перфорированная решетка выполнена составной.
В двухступенчатых редукторах типа РМ имеющих до сего времени широкое применение в промышленности принята для всех межцентровых расстояний и передаточных чисел одна сумма зубьев – 99. Эти редукторы первоначально проектировались для использования в крановых механизмах для которых характерным являются переменные высокие нагрузки и перерывы в работе. Поэтому с целью повысить изгибную прочность зубьев указанных передачи была принята относительно малая сумма зубьев с относительно большими модулями.
Малая сумма чисел зубьев имеет следующие недостатки: более низкий коэффициент перекрытия большие потери на трение в зацеплении большая скорость скольжения а отсюда меньшая сопротивляемость поверхностей зубьев заеданию и износу и большой вес зубчатых колес из-за увеличения их диаметра и толщины обода. Кроме того в редукторах типа РМ приzс = 99 тн = 002А = 04 и угле наклона зубьев д = 8634 не обеспечивается установленное ГОСТ 1643 – 56 для косозубых зубчатых колес соотношение между шириной колеса и осевым шагом зацепления.
В этих редукторах хотя и используют косозубые зубчатые колеса но в силу принятых параметров зацепления они посвоим кинематическим свойствам фактически не отличаются от прямозубых что снижает плавность и бесшумность работы редукторов.
Остальные типы редукторов имеют суммы чисел зубьев от 131 до 198. Передачи с такими суммами чисел зубьев не имеют вышеуказанных недостатков но недостаточно прочны (при том же диаметре) по изгибу при высоких переменных нагрузках.
Для снижения уровня шума превышающего предельно допустимую норму проектом предусмотрено: на быстроходной ступени редуктора увеличение суммы числа зубьев до 132 уменьшение модуля и увеличение угла наклона зуба.
СОДЕРЖАНИЕ-3.docx
ПЕРЕЧЕНЬ ЛИСТОВ ГРАФИЧЕСКИХ ДОКУМЕНТОВ
ТЕХНОЛОГИЧЕСКАЯ ЧАСТЬ
1Краткое описание технологического процесса
2 Технологическая схема
3 Технологическая характеристика оборудования
4 Литературный и патентный обзор
ЦЕЛЬ И ЗАДАЧИ ПРОЕКТА
1 Исходные данные для проектирования
2 Расчет основных параметров
2.1Расчет производительности пресса
2.2Расчет мощности электродвигателя
3 Кинематический и силовой расчет привода
3.1Расчет параметров редуктора
3.2 Расчет зубчатой передачи быстроходной ступени
3.3 Проверка зубьев шестерни и колеса на прочность
4 Расчет быстроходного вала редуктора на прочность
5 Расчет промежуточного вала редуктора на прочность
6 Расчет шпоночных соединений
7 Расчет подшипников качения
ТЕХНИКО-ЭКОНОМИЧЕСКОЕ ОБОСНОВАНИЕ ПРОЕКТА
1 Расчет технико-экономических показателей технической модернизации на участке производства
2 Расчет проектно-производственных мощностей
и проектного объема производства
3 Смета затрат на капитальный ремонт вакуумлентпресса
3.1 Периодичность и трудоёмкость ремонта.
3.2 Расчёт численности ремонтных рабочих
3.3 Создание ремонтной бригады
4 Расчёт фонда заработной платы ( ФЗП )
5 Затраты на разборочно - сборочные работы до и после модернизации
6 Расчет стоимости запасных частей для ремонта до и после модернизации
7 Смета затрат на капитальный ремонт вакуумлентпресса
7.1 Расчет затрат на модернизацию
7.2 Обоснование объёмов производства товарной продукции
8 Расчет затрат на производство продукции
9 Основные технико-экономические показатели проекта
БЕЗОПАСНОСТЬ ЖИЗНЕДЕЯТЕЛЬНОСТИ
1 Обеспечение безопасности работающих
1.1 Характеристика условий труда
2 Обеспечение безопасности труда
2.1 Мероприятия по электробезопасности
2.2 Пожарная безопасность
2.4 Защита от вибрации
2.5 Защита от механического травмирования
2.6 Обеспечение рационального освещения
2.7 Категория тяжести работ
3.1 Расчет местной вытяжной вентиляции
4 Природопользование и охрана окружающей среды
4.1 Перечень загрязняющих веществ выбрасываемых в
4.2 Чрезвычайные ситуации
БИБЛИОГРАФИЧЕСКИЙ СПИСОК
быстроходный вал.dwg

Неуказанные предельные отклонения размеров: отверстия Н15
ДП 270101.41.25.02.08.01. РЧ
Сталь 40Х ГОСТ 4543-71
кожух.dwg

электродом МР-3 или ОЗС по ГОСТ 5264-80.
Вместо гнутого профиля допускается
использовать швеллер N 5.
Косынки поз. 6 варить в шахмотном
порядке 200х200 мм.
ДП 270101.41.25.02.09.00 СБ
шнековый вал в сборе.dwg

скребок.dwg

ДП 270101.41.25.02.06.01 РЧ
Сталь Г13Л ГОСТ 977-88
Узел питат. вальца (2).dwg

варить сплошным швом
по всему периметру прилегания деталей.
Сварка ручная электродуговая
сварочные швы по ГОСТ 5264-80.
ДП 270101.41.25.02.03.00 СБ
питательный валец.dwg

по всему периметру прилегания деталей.
Использовать электроды марки МР-3 или ОЗС.
Неуказанные предельные отклонения размеров
ДП 270101.41.25.02.03.01 РЧ
Сталь 35Л ГОСТ 1050-88
общий вид сборка.dwg

станины и рамы привода.
Производительность 10тчас
Диаметр прессующего винта 445mm
Мощность электродвигателя 55кВт
Габаритные рамеры (без привода)
Масса (без привода) 4200кг
ДП 270101.41.25.02.00.00 СБ
Ось вакуумлентпресса
Техническая характеристика
Колесо.dwg

Термообработка-улучшение
Термообработка нормализация
Неуказанные предельные отклонения размеров
ДП 270101.41.25.02.08.02 РЧ
Сталь 45 ГОСТ 1050-88
общий вид до модернизации.dwg

станины и рамы привода.
Техническая характеристика
Призводительность 10тч
Диаметр прессующего винта 445мм
Мощность электродвигателя 75кВт
Габаритные размеры (без привода)
Масса (без привода) 4200кг
ДП 270101.41.25.01.00.00 СБ
Ось вакуумлентпресса
решетка.dwg

ДП 270101.41.25.02.04.06 РЧ
загрузочная воронка.dwg

сварка ручная электродуговая
варить непрерывным швом.