Установка по наплавке колесных пар думпкаров в условиях карьеров




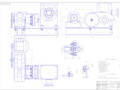
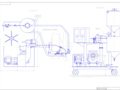
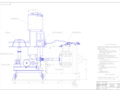
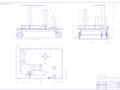
- Добавлен: 25.10.2022
- Размер: 2 MB
- Закачек: 0
Описание
Состав проекта
![]() |
![]() |
![]() |
![]() |
![]() |
![]() ![]() |
![]() ![]() |
![]() ![]() |
![]() ![]() ![]() ![]() |
![]() ![]() ![]() ![]() |
![]() ![]() |
![]() |
![]() ![]() ![]() ![]() |
![]() ![]() ![]() |
![]() ![]() ![]() ![]() |
![]() ![]() |
![]() |
![]() ![]() |
Дополнительная информация
Тележка в сборе.dwg

Неуказанные предельные отклонения размеров: H12
Сварные швы по ГОСТ 5264-80-У3 электродами Э46 ГОСТ9466-75
Вид общий Установка наплавки колес (Лист 1) А1 при открытии нажимайте игнорировать.dwg

Техническая характеристика
Назначение-Стенд предназначен для производства наплавки
гребней колесных пар диаметром 1250 мм без выкатки из под
Сварочный автомат: тип
-минимальный сварочный ток при ПВ=100%
-рабочее напряжение при номинальном токе
-диаметр сварочной проволоки
Направление вращения наплавляемого колеса
Регулировка угла наклона электрода
Частота вращения наплавляемого объекта
- емкость флюсобункера
- давление воздуха в питающей магистрали
- высота всасывания флюса
электродная проволока)
Обслуживающий персонал
Технические требования
Неуказанные предельные отклонения H12
На виде Б Лист2 кардан условно не показан.
Установка наплавки колес (Лист 2) А1.dwg

Пояснительная записка.DOC
1 Краткая характеристика района и месторождения
2 Физико–механические свойства пород
3 Способ вскрытия карьерного поля и рабочей зоны
Сарбайского месторождения
4 Система разработки Сарбайского карьера
5Буровзрывные работы
6 Выемочно–погрузочные работы
8 Транспортные машины и оборудование карьера
9 Стационарные машины
Электроснабжение горного предприятия
2 Расчет электрических нагрузок
3 Выбор числа и мощности трансформаторов
4 Расчет и выбор линии питающей ГПП
5 Расчет и выбор наиболее загруженной линии карьера
Ремонт технологического оборудования
1 Организация технического обслуживания и ремонта
4 Виды технических обслуживаний и ремонтов
5 Ремонтные нормативы
6 Планирование ремонтов
7 Расчет и выбор ремонтного оборудования для РММ
8 Проектирование РММ
1 Установка для наплавки гребней колесных пар
2 Расчет привода наплавляемого объекта
3 Расчет режима сварки под флюсом и выбор сварочного
4 Выбор соединительных муфт
Охрана труда и техника безопасности
1 Организация работ по охране труда
2Обеспечение безопасности производства
3 Общие санитарные правила
4 Ответственность за нарушение правил безопасности
5 Пожарная профилактика
6 Правила техники безопасности при эксплуатации
установки по наплавке колесных пар думпкаров
Промышленная экология
Экономическое обоснование
Список использованной литературы
Дальнейшее развитие технического прогресса в горнорудной промышленности рост экономической эффективности производства и повышение производительности труда возможны при наличии новой техники и прогрессивной технологии.
Современные горные предприятия ведущие разработку открытым способом (карьеры) представляют собой мощные механизированные промышленные предприятия насыщенные разнообразными машинами и оборудованием. Ритмичная и бесперебойная работа таких предприятий в значительной степени зависит от технического состояния оборудования.
Надежная высокопроизводительная работа оборудования предприятия может быть обеспечена только при хорошем знании их назначения устройства принципа действия условий их рационального применения правил технической эксплуатации и других условий.
Одна из главных задач стоящих перед ремонтными службами карьера - дальнейшее повышение качества работы и снижение продолжительности простоев оборудования в ремонте путем более широкого внедрения индустриальных методов ремонта и всемерного развития специализированных ремонтных мощностей особенно по производству деталей в износостойком исполнении.
Многочисленность технологических способов используемых при восстановлении деталей объясняется разнообразием производственных условий и дефектов для устранения которых они применяются. В зависимости от характера устраняемых дефектов все процессы восстановления деталей группируются в две основные группы: восстановление деталей с механическими повреждениями и восстановление деталей с изношенными поверхностями (с изменением размеров рабочих поверхностей). К первой группе относят способы восстановления деталей имеющих трещины пробоины изломы деформации а также коррозионные повреждения; ко второй – с измененными размерами и геометрической формой рабочей поверхности в виде овальности конусообразности корсетности и др.
Наиболее распространенные способы восстановления деталей – сварка и наплавка. Этими способами восстанавливают около 60 % деталей. Широкое применение сварки и наплавки обусловлено простотой технологического процесса и используемого оборудования возможностью восстановления деталей из большинства используемых деталей и сплавов высокой производительностью и низкой себестоимостью.
При восстановлении деталей применяют следующие виды и способы сварки и наплавки: ручная дуговая сварка газовая сварка полуавтоматическая сварка в углекислом газе полуавтоматическая сварка проволокой вибродуговая наплавка автоматическая наплавка под слоем флюса электроконтактная сварка.
Автоматическая наплавка под слоем флюса обеспечивает наиболее высокое качество наплавляемого металла так как сварочная дуга и ванна жидкого металла полностью защищены от вредного влияния кислорода воздуха а медленное охлаждение способствует наиболее полному удалению из наплавленного металла газов и шлаковых включений. При автоматической наплавке заданный режим почти не изменяется.
При наплавке под слоем флюса электрическая сварочная дуга горит в закрытой полости из расплавленного минерального вещества (флюса). Флюс предотвращает разбрызгивание жидкого металла обеспечивает формирование нормального сварного шва защищает расплавленный металл от воздействия кислорода и азота воздуха влияющих отрицательно на свойства наплавленного металла. Электродная проволока из кассеты к месту наплавки подается автоматической головкой.
Применение флюса позволяет использовать голую (без покрытия) электродную проволоку. Ток к проволоке подводится по скользящему контакту на небольшом расстоянии от дуги что уменьшает длину электрода по которому протекает сварочный ток. Плотность тока при этом увеличивается в несколько раз следовательно и возрастает производительность наплавки. Питание дуги чаще всего осуществляется током от сварочных генераторов и выпрямителей.
Наплавкой под слоем флюса восстанавливают изношенные плоские цилиндрические резьбовые и другие поверхности деталей. Цилиндрические поверхности деталей наплавляемых под слоем флюса должны иметь наружный диаметр свыше 50 мм так как на меньших сечениях расплавленный флюс и шлак из-за большого разогрева не успевают затвердевать и стекают с деталей. Механизированной наплавкой под флюсом восстанавливают катки колеса башмаки валы ролики барабаны.
Целью данного проекта является разработка конструкции установки наплавки гребней колесных пар думпкаров. Установка представляет собой стенд для обслуживания колесных пар диаметром 950 мм.
Сарбайское месторождение железных руд находится в Костанайской области Республики Казахстан в 45 км к юго–западу от областного центра города Костаная в 9км к северу от города Рудного.
Месторождение разрабатывается с 1956 года открытым способом. Район месторождения характеризуется слаборасчлененным равнинным рельефом с абсолютными отметками 170–200 метров.
Основная водная артерия – река Тобол. Сарбайское месторождение пространственно приурочено к Западному крылу Соколовско–Сарбайской антиклинали являющейся одной из составных частей Валерьяновской синклинальной зоны.
В геологическом строении месторождения принимают участие палеозойские образования складчатого фундамента и мезокайнозойские горизонтально залегающие отложения преимущественно рыхлые.
Палеозойские породы представлены вулканогенно–осадочной толщей интрузиями диоритового состава контактово–метасоматическими и контактово–метаморфическими образованиями.
Все эти породы в верхней части подверглись значительной переработке с образованием коры выветривания мощностью от 0 до 47 метров.
Вулканогенно–осадочная толща сложена андезитовыми порфиритами альбинтофирами и их туфами песчаниками известняками и глинисто–карбонатными сланцами. Породы этой толщи имеют меридиональное простирание и Западное падение от 40 до 60 градусов. Мощность пород колеблется от 35 до 100 метров. Метаморфические и скарновые образования представлены различного рода роговинами скарнами пироксенового гранатового и смешанного состава эпидот–антиколитовыми и хлоритизированными породами а так же магнетитовыми и сульфидными рудами. Эти образования приурочены к контакту интрузий диорит–порфиритов с породами вулканогенно–осадочной толщи. Мощность их колеблется от 20 до 100 метров.
Мезокайнозойские породы представлены (от молодых к старым ) глинами пестроцветными (1–27м) сланцеватыми–чеганской свиты (7–27м) опоками (4–35м) песчаниками кварц–глауконитовыми (0–10м) песками кварц–глауконитовыми (5–32м) песками кварцевыми (0–35м)среди которых залегают оолитовые бурые железняки мощностью (2–3м) глинами лигнитовыми (0–24м) встречаются базальный конгломерат до 5 метров.
На Сарбайском месторождении выделяется три рудных залежи – Восточная Западная и Юго–Восточная имеющие меридиональное простирание и западное падение. Рудные залежи выдержаны по падению и по простиранию. Наибольших размеров достигает Восточное рудное тело промежуточное положение занимает Западное и на третьем месте стоит Юго–Восточное.
Восточное рудное тело прослежено по простиранию 1700 м и на глубину 1300 метров. Истинная мощность рудного тела фиксируется в южной части по мере продвижения с юга на север мощность рудного тела постепенно уменьшается.
Восточное рудное тело представлено пластообразной залежью имеющей почти меридианальное простирание и западное падение причем угол падения уменьшается при движении с севера на юг с 55 до 45 градусов. Восточное рудное тело буровыми скважинами до полного выклинивания на глубину не прослежено. Максимально возможное распространение рудного тела на глубину по геологическим данным равно 1500–1800 метров.
Западное рудное тело прослежено по простиранию на протяжении 1000 м и представляет собой пластообразную залежь имеющую близкое к меридиональному простиранию и западное падение. В северной части рудного тела руды падают под углом 65 градусов в центральной части под углом 550 и в южной под углом 450 к Западу.
Истинная мощность рудного тела колеблется от 50 до 185 метров. Максимальная глубина распространения руд в северной части составляет 1100–1300 м в южной части 350–400 метров.
Первичные магнетитовые руды на месторождении занимают господствующее положение они составляют 991% от общих запасов балансовых руд месторождения.
Богатые магнетитовые руды располагаются в основной части рудных тел а бедные и убогие руды локализуются в лежачих и висячих рудных залежах. Окисленные руды на месторождении имеют ограниченное распространение. Они составляют 09% от общей цифры балансовых запасов. Окисленные руды встречены на верхних горизонтах Восточного Западного и Юго–Восточного рудных телах.
Колчеданные руды представлены вкраплениями и прожилками пирита и пирротина в рудных и безрудных скарнах.
Залежи образованны первичными окисленными рудами которые слагают практически все запасы месторождения. Окисленные руды имеют подчиненное значение и значительная часть их уже выработана.
По содержанию серы первичные руды делятся на магнетитовые (серы меньше 10%) и сульфидные (серы больше 10%). Все сульфидные руды отнесены к забалансовым.
К основным свойствам горных пород относятся [1]: твердость вязкость хрупкость упругость плотность устойчивость трещиноватость слоистость разрыхляемость пористость выветриваемость водоносность.
Каждая горная порода характеризуется также углом естественного откоса и объемным весом.
Трещиноватость пород – 3 категория. Коэффициент разрыхления для одной и той же породы может быть различным в зависимости от условий в которых находится разрыхленная порода. Например: при экскаваторных работах порода имеет наибольшее разрыхление в момент ее добычи – в ковше экскаватора. При погрузке породы в вагон происходит ее уплотнение и коэффициент разрыхления имеет некоторое уменьшение. Наименьшее значение коэффициент разрыхления имеет для пород помещенных в отвал (см. табл. 1.1)
Коэффициент разрыхления пород при экскаваторных работах
Коэффициенты разрыхления
Физико–механические свойства пород приводятся в таблице 1.2.
Физико–механические свойства руд и пород
Наименование руд и пород
3 Способ вскрытия карьерного поля и рабочей зоны Сарбайского месторождения
В соответствии с проектом Сарбайское месторождение вскрыто двумя капитальными железнодорожными выездными траншеями внешнего заложения – Юго–Восточный до отметки +125 м (глубиной 70 м) и Северной на глубину 15 м. Юго–Восточная траншея предназначена для вскрытия горизонтов рыхлых и скальных пород и руды имеет внешнее заложение до кровли скальных пород Северная траншея предназначена для вскрытия верхних горизонтов покрывной толщи и имеет внешнее заложение до отметки +189 м и внутреннее до отметки +125 м.
Юго–Восточная траншея Сарбайского карьера примыкающая к середине Восточного борта является основной ж.д. магистралью для транспортировки руды и скальный пород. Внешняя часть траншеи имеет прямолинейную трассу с руководящим уклоном 40000. Все шесть проектных ж.д. путей Юго–Восточной траншеи используются для грузового и порожнякового движения.
Юго – Восточная траншея имеет внешнее заложение до отметки гор.+134м а затем переходит во внутреннею. В месте перехода внешней траншеи во внутреннюю ж.д. пути уложенные в траншее разделяются – часть путей уложено по Восточному борту часть по Юго – Восточному.
Ж.д. пути уложенные по Восточному борту на гор.+115 м примыкают к ж.д. станции гор.+115 м. Ж.д.станция гор.+115 м имеет двухпутный тупиковый заезд на гор.+80 м где построена станция гор.+80 м. Станция гор.+80 м со стороны Северной горловины соединена двух путным перегоном с станции гор.+49 м расположенной по Восточному борту карьера.
Со стороны Южной горловины станция гор.+80 м через пост №1 соединена тупиковым двух путным заездом со станцией гор.+36 м Восточного борта. Со станцией гор.+115 м гор.+49 м и гор.+36 м по Восточному Северному и Северо – Западному бортам карьера вскрыты гор.+112 м +95 м +80 м +60 м +40 м +20 м 0 м.
Ж.д. пути уложенные по Юго–Восточному и Южному борту карьера на гор. +93м примыкают к ж.д. станции гор.+93 м. К станции гор.+93 м примыкает пост гор.+80 м Южного борта. Со станции гор.+93 м и поста гор.+80 м и Западного борта вскрыты гор.+95 м+80 м+60 м+40 м+20 м и кроме того на ж.д.путях примыкающих к посту гор.+80 м работают четыре перегрузочных склада. Таким образом постоянная транспортная схема развития ж.д. путей начиная со станции +115 м имеет тупиковые развития.
Северная траншея предназначена в основном для вскрытия горизонтов рыхлой толщи. Два ж.д. пути уложенные в Северной траншее на гор.+189 м примыкают к ж.д. посту ''Единый “. С поста “ Единый” по Западному борту уложены ж.д. пути на гор.+174 м+161 м+151 м+138 м и +125 м. Два других ж.д. пути Северной траншее уложены по Восточному капитальному борту до гор.+151 м где примыкают к ж.д. посту гор.+151 м. С поста гор.+151 м обратными заездами вскрыты гор.+174 м +161 м +151 м +138 м +125 м и +118 м по Северному и Северо – Западному бортами карьера. Пост гор.+115 м имеет двух путную телескопную связь со станцией гор.+151 м что позволяет транспортировать скальную вскрышу с нижних горизонтов на Северный отвал. При этом расстояние транспортирования сокращается на два – три км в среднем с Юго – Восточным направлением.
Горизонты по Юго – Западному борту карьера и все нижележащие горизонты не вскрытые на ж.д. транспорт отрабатываются на автомобильный внутрикарьерный транспорт и вскрытый временными автомобильными съездами.
Низшие горизонты вскрыты ж.д. тоннелями по тупиковой схеме гор.0 м–80 м (первая очередь тоннелей находящаяся в эксплуатации) и гор.–40 м–120 м (вторая очередь тоннелей строящаяся).
Параметры Юго – Восточной траншеи Сарбайского карьера.
В траншее шесть ж.д. путей и две автодороги (с Восточной стороны технологическая шириной 16 –18 м с Западной стороны хозяйственная шириной 12 м).
Глубина траншеи в устье – 60 м длина траншеи – 1.5 км ширина по низу – 75 – 100 м ширина по верху – 370 м объем траншеи – 15 млн.м3 [1]
Система разработки Сарбайского карьера – транспортная с внешним отвалообразованием.
Структура системы разработки имеет вид:
-одноковшовые экскаваторы на погрузке
-автомобильный транспорт на дне карьера
-железнодороджный транспорт на транспортировке горной массы из карьера на поверхность
-одноковшовые экскаваторы на отвале.
Выемка и погрузка руды и вскрышных пород осуществляется экскаваторами типа ЭКГ–8УС на карьере используется ж.д. транспорт – на верхних горизонтах и комбинированный транспорт – автомобильно – железнодорожный. С нижних горизонтах вывоз породы и руды осуществляется автомобильным транспортом на промежуточные концентрационные горизонты (внутрикарьерные склады) а затем электрифицированным ж.д. транспортом на поверхность: руда – на фабрики порода – в отвал. Основные показатели по системе разработки приводятся в таблице 1.3.
5Буровзрывные работы
Разработка руд и вмещающих скальных пород предусматривается полностью с предварительным рыхлением их буровзрывным способом [2]. Полускальные породы ввиду их незначительной крепости разрабатываются с рыхлением буровзрывным способом на встряхивание.
Бурение скважин осуществляется станками типа СБШ–250 МНА–32.
В качестве взрывчатых веществ для скважин рекомендуется гранулит Э. В качестве промежуточного детонатора предусматривается применение тротиловой шашки типа Т–400 а замедлителя – пиротехническое реле КЗДШ–69.
Принятые в проекте параметры системы разработки позволяют применять многорядное короткозамедленное взрывание скважин.
Массовые взрывы предусматривается производить один раз в неделю. Подготовка массового взрыва производится три дня по две смены в сутки в светлое время.
Проектом предусматривается механизированная зарядка и забойка скважин. Для механизированной зарядки скважин предусматривается зарядная машина типа МЗ–4 а для забойки скважин – забойные машины типа ЗС–1М.
Буримость пород характеризуется показателем трудности бурения
гдеsсж – сопротивление пород сжатию МПа: для руды – 140 МПа
для породы – 120 МПа;
sсдв – сопротивление пород сдвигу МПа: для руды – 296 МПа для породы – 28 МПа;
j – объемный вес тм3: для руды – 35 тм3 для породы – 26 тм3;
g – ускорение свободного падения g=98 мс2.
Для руды по формуле (1.1)
Для породы по формуле (1.1)
Принимается для бурения скальных пород и руды станок типа СБШ–250МНА–32 с диаметром долота D=2445 мм.[3]
Для принятого типа бурового станка определяется рациональный режим бурения характеризующийся оптимальной осевой нагрузкой – P0 кН и частотой вращения – nв обсек.
где D – диаметр долота D=02445 м;
f – крепость породы по шкале профессора М.И. Протодьяконова.
Ведение горных работ по Сарбайскому карьеру
Параметры системы разработки
Размеры карьера по поверхности:
Глубина карьера (проектная)
б) по породе: – рыхлой
Ширина рабочей площадки:
в рыхлых породах (ЭКГ–8И)
в скальной вскрыше и руде (ж.д. трансп.)
в скальной вскрыше и руде (атрансп.)
Ширина заходки (ЭКГ–63УС)
Угол постоянного откоса борта карьера:
Средний коэффициент вскрыши
Угол рабочего откоса борта карьера
а) в постоянном положении
б) в рабочем положении
Ширина транспортной бермы:
а) при ж.д. транспорте
б) при автотранспорте
Размеры карьера по поверхности достигли проектных контуров
Рыхлая вскрыша закончилась в 1990 году
По формуле (1.2) для руды и породы соответственно:
Рациональная частота вращения бурового инструмента для СБШ–250 МНА –32 составляет – nВ=1518 обс.[2].
По выбранному рациональному режиму бурения устанавливаем техническую скорость бурения
По формуле (1.3) для руды и породы соответственно:
По установленной технической скорости бурения устанавливаем сменную и годовую производительность станка.
Сменная производительность мсмена
где ТСМ – продолжительность смены ТСМ =12 час.
tВ – вспомогательное время на бурение одного метра скважины tВ=007 час.[2]
TПЗ+ТРП+Тпр – соответственно продолжительность подготовительно–заключительных операций регламентированных перерывов внутрисменных простоев TПЗ+ТРП+Тпр=1 час.
По полезному ископаемому по формуле (1.4)
Годовая производительность мгод
гдеNСМ – количество смен в год при двухсменной работе в день и 260 рабочих днях получаем 520 смен.
Годовая производительность станка по полезным ископаемым по формуле (1.5)
QГОД ПИ=926×520=48152
По породе по формуле (1.5)
QГОД П=797×520=41444
Рабочий парк буровых станков:
гдеWб – годовой объем бурения мгод:
гдеA – годовая производительность м3год по полезному ископаемому – AПИ=10 млн. тгод по вскрыше – AВП =21×106 м3год.
g – выход горной массы с одного погонного метра скважины по полезному ископаемому: gПИ=39 м3м; по вскрыше: gВП =496 м3м [3]
По полезным ископаемым по формуле (1.7)
По вскрыше по формуле (1.7)
Рабочий парк буровых станков по полезным ископаемым по формуле (1.6)
Рабочий парк буровых станков по вскрыше по формуле (1.6)
Принимаем 12 станков СБШ–250МНА–32. Общий парк станков – 14 штук.
Определяем сменную производительность экскаваторов [1]
где ТСМ=12 – продолжительность смены час;
ТПЗ+ТРП – время подготовительно заключительных операций и регламентированных перерывов ТПЗ+ТРП=1 час;
КН – коэффициент наполнения ковша КН=09;
КТВ –коэффициент технологии выемки (при трех рядном взрыве) КТВ=093;
КТР – коэффициент учитывающий простои из–за отсутствия транспорта КТР=07;
КИ – коэффициент использования экскаватора КИ=08;
КУ –коэффициент управления КУ=095;
КП – коэффициент потерь КП=08;
ТЦ – продолжительность цикла экскавации:
где tР – продолжительность разгрузки tР=3 сек;
tЧ – продолжительность черпания сек:
где ПЭП–паспортный показатель трудоемкости экскавации пород ПЭП=5;
tЧП–паспортная продолжительность черпания tЧП=12 [2].
Продолжительность черпания по полезному ископаемому и вскрыше соответственно по формуле (1.10)
tП – продолжительность поворота при угле 900 сек:
где tПП – паспортная продолжительность операции поворота tПП=17 сек [1];
b – действительный угол поворота экскаватора b=115°.
Продолжительность цикла экскавации по полезному ископаемому и вскрыше соответственно по формуле (1.10)
Подставляем все данные в формулу (1.8) и подсчитаем сменную производительность экскаваторов по полезному ископаемому и вскрыше соответственно:
Годовая производительность определяется по формуле млн. м3год
где N– число рабочих дней в году N=260;
n – число смен в сутки n=2.
Годовая производительность по полезному ископаемому и вскрыше соответственно по формуле (1.12):
где А – проектная производительность карьера м3год;
QГОД – расчетная годовая производительность м3год.
Число экскаваторов по полезному ископаемому по формуле (1.13):
Число экскаваторов по скале (автомобили):
Число экскаваторов по скале (железнодорожный транспорт):
Общее число экскаваторов
Инвентарный парк экскаваторов:
Скальные породы из Сарбайского карьера транспортируются в Восточный отвал.
Прием пород на отвалах производится при железнодорожном транспорте экскаваторами типа ЭКГ–8И.
Высота отвальных уступов при применении экскаваторов ЭКГ–8и составляет в среднем 20–22 метра.
Технология отвалообразования экскаватором ЭКГ–8и заключается в следующем. Порода из железнодорожных вагонов (думпкаров) разгружается на площадку (приямок) длинной 20–25 метров по фронту разгрузки подготовленную экскаватором. Глубина приямка от уровня железнодорожных путей 6 метров угол откоса 60°. Приемная емкость равна емкости состава.
Отвальный уступ разделяется на два подступа на кровле нижнего подступа который располагается на пять метров ниже железнодорожного пути устанавливается экскаватор. Экскаватор перемещает породу разгружаемую из думпкаров в приямок [5].
Из приямка порода перемещается вперед по ходу экскаватора в нижний подступ сбоку под откос отвала сзади экскаватора в нижний подступ. Отсыпав одновременно нижний и верхний подступы в пределах радиуса своего действия экскаватор перемещается вдоль фронта разгрузки на расстояние определяемое его линейным параметром вновь сооружает приемный бункер и производит переэкскавацию породы. После отсыпки по всей длине тупика обоих подступов на ширину отвальной заходки железнодорожный путь перекладывают на новую трассу и экскаватор приступает к отсыпке новой заходки.
8.1 Расчет автомобильного транспорта
8.1.1 Выбор типа самосвала
Соотношение ёмкости кузова автосамосвала и ковша экскаватора должно удовлетворять условию
Из данного выражения следует ёмкость кузова автосамосвала м3:
Vкуз=( 4 8 ) × Vков (1.17)
Vкуз= ( 4 8 ) · 8 = 32 64
В данных пределах выбираем автомобиль и проверяем по коэффициенту использования ёмкости и грузоподъёмности.
Количество ковшей экскаватора необходимых для загрузки кузова автосамосвала по ёмкости
и по грузоподъёмности
где V –– объём кузова автосамосвалам3;
Vэ– объём горной массы в ковше экскаваторам3;
Е – объём ковша экскаваторам3;
kн – коэффициент наполнения ковша kн = 08 [3];
kу – коэффициент уплотнения горной массы kу = 08[7];
q – грузоподъёмность автосамосвала;
qэ – масса горной массы в ковше экскаватора;
kр – коэффициент разрыхления горной массы в ковше экскаватора kр = 13;
g – плотность горной массы g = 35 тм3 .
Из полученного значения количества ковшей nv и nq принимаем меньшее и округляется до целого (n).
Коэффициент использования кузова автомобиля по ёмкости и грузоподъёмности определяем по формулам
Нормальный тип автосамосвала характеризуется коэффициентами kу и kq близкими к единице. На основании опытных данных допустимыми значениями коэффициентов являются значения: kу=0911 и kq=0711.
Принимаем автосамосвал БЕЛАЗ–7512: объём кузова V=47 м3 грузоподъёмность q = 120 т.
По формулам (1.18) и (1.20):
Принимаем n3 = 7 ковшей.
По формулам (1.20) и (1.21):
8.1.2 Тяговые расчёты автосамосвалов
Определение скорости движения автомобиля кмч производим по формуле
где N – мощность двигателя кВт [3];
Р – масса автомобиля т [3];
h – КПД трансмиссии для электромеханической КПД=07[3];
КV – переходной коэффициент скорости КV=088 [7];
i – уклон автодорог для автосамосвала Б–7512 принимаем i=70000.
Скорость движения груженого автомобиля на подъем по формуле (1.22):
Скорость движения порожнего автомобиля на спуск по условиям техники безопасности скорость спуска принимаем V=20 кмчас.
Скорость движения груженого автомобиля по горизонтальному участку по формуле (1.22):
По условиям техники безопасности скорость ограничивается до V=25 кмчас.
Скорость движения автомобиля в порожнем направлении на криволинейных участках постоянных дорог ограничивается по условиям техники безопасности до VR2=25 кмчас.
Тормозной путь автомобиля рассчитывается по формуле
где tР – время реакции водителя tР=05 с;
j – коэффициент инерции вращающихся частей j=002 [3];
V – скорость автомобиля на заданном участке кмчас;
yТ – коэффициент сцепления колес автомобиля с дорогой yТ=025 [3];
w0 – удельное основное сопротивление движению автомобилю w0=30 НкН.
Тормозной путь автомобиля БелАз должен быть меньше расстояния видимости в данной местности не менее чем на длину машины т.е. при LВ=50 м [7] Lm=978 м: LTLB–Lm=50–978=4122 м
Тормозной путь автомобиля при движении по горизонтальному участку в грузовом и порожнем направлениях по формуле (1.23):
Тормозной путь автомобиля при движении на спуск по формуле (1.23)
8.1.3 Эксплуатационные расчёты автосамосвалов
Время движения автомобиля определяем по длине транспортирования и скорости движения на каждом участке трассы:
гдеtГР и tПОР – соответственно время движения груженного и порожнего автомобиля tГР=0167 ч. и tПОР=0081 ч.;
SГР; VГР; SПОР; VПОР – расстояние транспортирования и скорость движения соответственно груженного и порожнего автомобиля.
Длину трассы в грузовом и порожнем направлениях складывают из длины наклонных и горизонтальных участков длины поворотов и петлевых заездов под погрузку и разгрузку. Подъём дороги от самого дальнего экскаватора составляет П=90м. Тогда длина участка подъёма l=1000×9070=1285м
Время движения автосамосвалов по формуле (1.24):
tДВ=60×(0167+0081)=1488
Расчетный расход топлива кг определяем по формуле
гдеtТР –расстояние транспортирования км;
Н – высота подъема горной массы м;
w0 – удельное сопротивление движению w0=30 НкН;[7]
kТ –коэффициент тары kТ=09.
Фактический расход топлива
гдеkК – коэффициент учитывающий повышение расхода в зимнее время kК=11[7];
kВ – коэффициент учитывающий расход на внутрикарьерные нужды kВ=106;
kМ – коэффициент учитывающий расход на маневры kМ=11.
Расход смазочных материалов составляет 5–8% от расхода топлива
Продолжительность рейса автомобиля определяем по формуле
где tП – соответственно время погрузки автомобиля мин;
где tЦ – продолжительность цикла tЦ=394 с (раздел 1.6).
tГР и tПОР – соответственно время движения груженым и порожним;
tР – время разгрузки кузова на ПП мин [7];
tДОП – дополнительное время связанное с простоями машины.
Подставляем все данные в формулу (1.28) получаем
Сменную производительность тсмену определяем по формуле:
где qф – фактическая грузоподъемность самосвала т;
ТСМ – время смены ТСМ=660 мин;
kq – коэффициент использования грузоподъемности kq=11;
Количество рейсов автомобиля за смену
Среднее количество автомобилей обслуживающих нижние горизонты Сарбайского карьера определяем по формуле
где QСМ – сменная производительность экскаватора по руде тсм (см раздел 1.6)
QCМ – сменная производительность самосвала тсм;
fГН – коэффициент неравномерности грузопотока fГН=115;
Так как продолжительность смены экскаватора и самосвала не совпадают то расчет производим по часовой эксплуатационной производительности. По формуле (1.32)
Произведем аналогичные расчёты получим для двух других экскаваторов работающих на вышележащих уступах.
Количество экскаваторов
Общее число автосамосвалов на руде
Для самого дальнего экскаватора работающего на скале расчёты сведём в таблицу 1.5.
Расчёт автотранспорта по скале
Количество загружаемых ковшей
Коэффициент использования ёмкости
Коэффициент использования грузоподъёмности
Производительность автосамосвала в смену
Общее количество необходимых автосамосвалов для трёх экскаваторов на скале – 6 штук.
Тогда необходимый рабочий парк машин БелАЗ – 16 штук.
8.2 Карьерный железнодорожный транспорт
8.2.1 Расчет транспорта
Учитывая срок существования карьера и производительность принимаем материалы для дорог первой категории: рельсы Р – 65 шпалы деревянные пропитанные – 1А число шпал – 18402000 на 1 км. балласт – щебеночный. Толщина балластного слоя 045 м – щебень на постоянных путях и 30–40 см отходов СМС на передвижных путях.
С учетом напряжения контактной сети карьера (33 кВ – постоянное) и как наиболее прогрессивный и экономичный выбирается тяговый агрегат ПЭ–2М.
Для перевозки скальных пород руды и рыхлой вскрыши применяем вагоны–самосвалы 2ВС–105.
Весовая норма поезда определяем из условия равномерного движения по руководящему подъему с полным использованием сцепных сил локомотива Q и по условию трогания на приведенном уклоне Q по формулам
где Рсц – сцепной вес локомотива Рсц = 368 т;
w’0 и w0’’ – удельное основное сопротивление движению соответственно локомотива и вагона НкН:
w’0 = 297+0048V+000079V2 (1.34)
где V=30 кмч – скорость тягового агрегата.
w’’0 = 36+0015V (1.35)
где а – ускорение поезда при пуске а=0025005 мс2;
тр – удельное сопротивление при трогании поезда с места тр = 4НкН [7] ;
– коэффициент сцепления колес при трогании локомотива [3].
w’0 = 2.97+0048×30+000079×302 = 501
w’’0 = 36+0015×30 = 403
Окончательно принимаем вес прицепной части поезда 1453 тонн.
Количество вагонов определяем по формуле
где qT – вес тары вагона qT=485 т [3];
q – грузоподъемность вагона q = 105т.
Принимаем 9 вагонов в составе.
Вес прицепной части поезда
Сила тяги Н определяем по формуле
При горизонтальном движении сила тяги по формуле (1.39)
Сила тяги при движении состава на подъем по формуле (1.39):
Fп=368×(501+40)+13815(403+40)=77391125
Определяем время рейса состава мин:
Тр=tп+tгр+tр+tпор+tож (1.40)
где tп – время погрузки состава мин;
где VВ – емкость вагона VВ=50м3;
ПВ – количество вагонов ПВ=9;
VК – емкость ковша VК=8 м3.
tгр – время движения груженого состава мин;
tр – время разгрузки состава tр =27 мин;
tпор – время движения порожнего состава мин;
tож – время ожидания tож=10 мин.
Tр=301+19+27+18+10=1041
Таким образом время рейса от самого дальнего экскаватора ЭКГ–8УС до отвала составляет 1041 мин.
Необходимое число рейсов локомотивов для вывоза суточного объема горной массы
где f – коэффициент неравномерности движения f=1112 [3];
Qсут – суточная производительность карьера Qсут=47945 м3смену;
Qсост – ёмкость состава Qсост=4365 м3.
Количество рейсов в сутки одной машины
где Тсут– время работы локомотива в сутки час;
Тр – среднее время рейса Тр=181 час.
Количество тяговых агрегатов:
Принимаем 10 тяговых агрегатов типа ПЭ–2М.
Инвентарный парк локомотивов определяем по формуле
Nинв.=Nраб+Nрем+Nрез+Nхоз (1.47)
где Nрем –количество локомотивов находящихся в ремонте;
Nрем=015×Nраб (1.48)
Nрез –количество резервных локомотивов
Nрез=(00501)Nраб (1.49)
Nхоз – число локомотивов на хозяйственных работах Nхоз=1;
9 Стационарные машины
В настоящее время воды проскока и атмосферные осадки по дренажным канавкам стекаются в три водосборника которые оборудуются:
зумпф – расположен на горизонте –2765 м. Водоприток составляет 305 м3час.
зумпф – расположен на горизонте –279 м. Водоприток 337 м3час.
зумпф – расположен на горизонте –2963 м. Водоприток 318 м3час.
Вода с третьего зумпфа подается по трубопроводу во второй зумпф откуда выкачивается насосной установкой.
Вода насосами поднимается до горизонта +40 м и сбрасывается в подземную дренажную систему карьера (рисунок 1.1).
Производится расчет насосной установки второго зумпфа. Требуемая расчетная подача насоса. Минимальная подача насоса – это откачка нормального суточного притока за 20 час.
где QПР – номинальный суточный приток м3ч .
– нагнетательный трубопровод 2 – всасывающий трубопровод
– насос 4 – зумпф 5 – подземный дренажный комплекс
– водосбросная скважина.
Рисунок 1.1. Схема открытого водоотлива Сарбайского карьера.
Геометрический напор
Ориентировочный напор насоса м
Предусматриваем установку на уступе одного работающего основного насоса типа ЦНС–850 имеющего в оптимальном режиме подачу QОПТ =850 м3час при напоре на одно рабочее колесо НК =360 м. Напор одного рабочего колеса при нулевой подаче НК0 =400 м а также одного резервного насоса [5].
Необходимое число последовательно соединенных рабочих колес насоса
Предусматриваем установку на понтоне двух работающих вспомогательных насосов типа К 200-150-400а имеющего в оптимальном режиме подачу QОПТ =400 м3час и напор НОПТ =40 м и одного резервного.
Техническая характеристика насоса К 200-150-400а:
Частота вращения обмин1500
Мощность электродвигателя кВт 75
Диаметр рабочего колеса мм 400
Схема трубопровода приведена на рисунке 3.2. Количество уступов:
где НГ – геометрическая высота подъема м;
НУСТ – высота уступа м.
Трубопровод для насоса К 200-150-400а (всасывающий трубопровод).
Внутренний диаметр всасывающего трубопровода определяем по формуле
гдеQ – подача насоса м3час;
V – скорость движения жидкости во всасывающем трубопроводе V=15 мс.
Рисунок 1.2. Схема трубопровода.
По рассчитанному внутреннему диаметру всасывающего трубопровода выбираем трубы бесшовные горячекатаные (ГОСТ 8731–74)
имеющие следующие технические данные:
Наружный диаметр DВС мм426
Внутренний диаметр dВС мм 406
Толщина стенки dВС мм 10
Длину всасывающего трубопровода принимаем равной один метр.
Нагнетательный трубопровод.
гдеV – скорость движения жидкости в нагнетательном трубопроводе V=25 мс.
По рассчитанному внутреннему диаметру нагнетательного трубопровода выбирается резиновый шланг.
Длина резинового шланга для насоса принимаем равной пяти метрам.
Также по рассчитанному внутреннему диаметру нагнетательного трубопровода выбираем трубы стальные бесшовные горячекатаные ГОСТ 8731–74 имеющие следующие технические данные:
Наружный диаметр DН мм377
Внутренний диаметр dН мм 357
Толщина стенки dН мм 10
Проверяем полученные результаты по условию: d dВЫБ
где d – необходимая толщина стенки трубы мм;
d0 – толщина стенки определяемая прочностью материала труб мм;
dК – коэффициент учитывающий коррозионный износ мм;
КС – коэффициент учитывающий минусовой допуск толщины %.
где К1 – для стали 3 К1=252;
D – наружный диаметр выбранной трубы м;
Р – максимальное давление в трубах МПа.
Давление в трубах на 20 м это 22 м вод.столба или 022 МПа
где a1 – скорость коррозионного износа наружной поверхности трубы (при наличии взрывных работ) a1=025 ммгод;
a2 – коррозионный износ внутренней поверхности a2=01ммгод;
Т – срок службы трубопровода Т=10лет.
Выбранная труба для нагнетательного трубопровода насоса К 200-150-400а удовлетворяет условиям.
Длину общего нагнетательного трубопровода принимаем равной двадцать метров.
Нагнетательный трубопровод для насоса ЦНС–850.
Внутренний диаметр нагнетательного трубопровода определяем по формуле (1.55).
По рассчитанному внутреннему диаметру нагнетательного трубопровода выбираем трубу бесшовную горячекатаную ГОСТ 8731–74 имеющую следующие технические данные:
Проверяется полученный результат по выше приведенным формулам (1.56–1.58) для высоты 315 м 346 м. водн. столба это 339 МПа.
Выбранная труба для нагнетательного трубопровода насоса ЦНС–850 удовлетворяет условиям. Длину общего нагнетательного трубопровода складываем из длины по дну карьера (lПО ДНУ м) по борту карьера (lПО БОРТУ м) по площадке уступа до водосбросной скважины (lПО ПЛ.УСТ. м).
l = lПО ДНУ+lПО БОРТУ+lПО ПЛ.УСТ. (1.59)
l = 50+950+647+20=1667 м
Построение характеристики нагнетательного трубопровода работающего вспомогательного насоса К 200-150-400а
гдеR – постоянная трубопровода ч2м5;
гдеh – потери напора в трубопроводе м
Потери напора в трубопроводе складываем из потерь на прямолинейном участке (hПРЯМ м) и потерь на местных сопротивлениях (hМЕСТ м).
d– внутренний диаметр общего нагнетательного трубопровода d=0357 м;
V – фактическая скорость воды в нагнетательном трубопроводе мс:
гдеx – суммарный коэффициент местных сопротивлений.
В зависимости от типа арматуры и фасонных частей трубопровода значения коэффициента x приведены в таблице 1.6.
Коэффициент местных сопротивлений
Приемная сетка с клапаном
Клапан обратный поворотный
Колено под углом 135°
По формулам (1.65) и (1.63):
По формулам (1.61) и (1.60):
Результаты расчета внешней сети приводятся в таблице 1.7.
Внешняя сеть насоса К 200-150-400а
Построение характеристики нагнетательного трубопровода работающего основного насоса ЦНС–850.
Характеристика нагнетательного трубопровода работающего основного насоса ЦНС-850 рассчитывается по формулам (1.60)–(1.65). d=0357 – внутренний диаметр общего нагнетательного трубопровода м.
В зависимости от типа арматуры и фасонных частей трубопровода значения коэффициента x приведены в таблице 1.8.
Характеристики внешней сети насоса ЦНС 850
Определение мощности приводного двигателя насоса К 200-150-400а
Согласно построенным характеристикам насос К 200-150-400а
имеет следующий рабочий режим (т. Е):
QE=480 м3час ; НЕ=200081 м ; hЕ=80%
Расчетную мощность двигателя кВт определяем по формуле:
Принимаем электродвигатель А–81–4 имеющий следующие технические характеристики:
Частота вращения обмин1460
Коэффициент запаса мощности двигателя:
Определение мощности и расхода энергии для приводного двигателя насоса ЦНС–850.
Согласно построенным характеристикам насос ЦНС–300420 имеет следующий рабочий режим (т. А):
QА=950 м3час; НА=315798 м; hА=72%
Расчетную мощность двигателя определяем по формуле 3.16
Принимаем электродвигатель А 13–59–4УХЛ имеющий следующие технические характеристики:
Частота вращения обмин1480
Число часов работы в сутки при откачивании нормального притока
Годовой расход электроэнергии кВт·час определяем по формуле:
гдеhС – КПД сети hС=095;
hДВ– КПД двигателя hДВ=092;
h – КПД насоса h=072;
nДН – количество дней ожидаемого притока nДН=365;
Расход энергии в течение года при работе насосов по откачке притока по формуле (1.69):
Годовой нормальный приток воды
Удельный расход электроэнергии
Вместимость водосборника м3 определяем по формуле
Для насоса Д31571 мощность двигателя составляет 110 кВт принимаем двигатель 4А280S2У3.
Для общего освещения карьера используем лампы типа ДКсТ (дуговые ксеноновые лампы)[6].
Минимальная освещенность карьера 05 люкс. Расчет освещенности производится методом светового потока Лм:
где ЕMIN – минимальная освещенность ЕMIN =05 люкс;
S – площадь карьера м2;
kЗ – коэффициент запаса kЗ=12;
KП – коэффициент потерь KП=11.
Принимаем лампу ДКсТ–20000 с параметрами [7]:
Номинальное напряжение В 380
Номинальная освещенность Лк 600000
Выбор числа прожекторов которые устанавливаются на борту карьера определяем по формуле
Высота установки прожекторов
Из условия безопасности принимаем Н=20 метров [8].
Определяем мощность трансформатора:
где n – число светильников в группе n=3 шт.
Требуемая мощность Вт:
где hС– КПД светильника hС=076;
hОС – КПД осветительной сети hОС=095;
cosjC – коэффициент мощности лампы cosjC=09.
Принимаем трансформатор ТМ–1006 [9]. Его техническая характеристика приводится в таблице 2.1.
Техническая характеристика трансформатора ТМ–1006
Выбор кабеля для осветительной установки.
Минимальное сечение проводника мм2:
gПР – удельная проводимость меди gПР=0057 Амм2 [10];
DU% – допустимая потеря напряжения DU%=25 [10].
Принимаем кабель КГ–350+116 с IДОП=165 А [11].
Расчет электрических нагрузок производим с целью последующего выбора трансформатора ГПП сечения проводов питающих линию и т.д. расчет сводим в таблицу 2.2.
Активная мощность определяем по формуле
Где PP – суммарная мощность кВт ;
КС – коэффициент спроса.
Реактивная мощность (кВАр)
Расчет электрических нагрузок
Главный насос карьера
Перекачивающий насос
В целях рационального распределения электроэнергии экономии материалов и электрооборудования уменьшения трудозатрат ЛЭП рудника проектируем на один ГПП.
ГПП получает питание от двух независимых друг от друга ЛЭП напряжением U=110 кВ.
Принимаем трансформатор ТДН–16000110 [78] технические данные которого сведены в таблицу 2.3.
Техническая характеристика трансформатора
Тип марка трансформатора
Выбранный трансформатор проверяем по загрузке в номинальном режиме коэффициент загрузки определяем по формуле:
Коэффициент загрузки сравниваем с экономическим коэффициентом
где Р х.х. – потери мощности холостого хода кВт;
Р к.з. – потери мощности короткого замыкания кВт;
К пп. – коэффициент повышения потерь К пп = 002 – 013 кВтквар.
Реактивная мощность определяем по формуле
где Qх.х. – реактивная мощность трансформатора холостого хода квар;
Qк.з. – реактивная мощность трансформатора при коротком замыкании квар;
Iх.х. – ток холостого хода %;
Uк.з. – напряжение короткого замыкания трансформатора %.
По формулам (2.14) (2.15):
Производим проверку по перегрузочной способности трансформатора при аварийном отключении одного из них если условия проверки выполняются то выбранный трансформатор принимаем к установке при этом он не должен превышать коэффициент [Кп]= 14 [11].
где SP– полная мощность кВ×А;
Предварительный выбор сечения провода по экономической плотности тока
Выбираем 2 провода провод АС–75.
Проверка на потерю напряжения
R0– удельное активное сопротивление R0=027 Омкм;
Х0 – удельное индуктивное сопротивление Х0=008 Омкм.
По формуле (2.20) условие выполняется 019% 5%.
Наиболее загруженной линией карьера является линия питающая два экскаватора ЭКГ–8УС и СБШ–250.
где КС1 – для ЭКГ–8УС КС1=061;
КС2 – для СБШ КС2=07;
Принимаем провод А–35: IДЛДОП=170 А
Проверяем на потерю напряжения:
где r0 – удельное активное сопротивление r0=089 Омкм;
х0 – удельное индуктивное сопротивление х0=008 Омкм
Условие выполняется 32% 5%.
Рассчитываем кабельную линию питающую ЭКГ–8УС.
Определяем расчетный ток нагрузки А:
Выбираем кабель по длительному допустимому току КГЭ–325+110 [12]: IДЛ.ДОП=105 А
Кабель удовлетворяет требованию 022% 5%
Расчет кабельной линии бурового станка
Для подключения бурового станка используем два кабеля включенные параллельно. Принимаем кабель КГ–395+125 [12].
Длительный допустимый ток для двух кабелей: IДЛ.ДОП=265 А
где где r0 – удельное активное сопротивление r0=026 Омкм;
х0 – удельное индуктивное сопротивление х0=0194 Омкм
cosjC – коэффициент мощности сosj=075
Кабель удовлетворяет требованию 373% 5%.
Для условий Сарбайского карьера проектируем смешанную форму управления электромеханической службой. Смешанной формой электромеханической службы называется такая форма при которой часть ремонтных сил и средств сосредоточена в ведении главного механика которым выполняются капитальные ремонты основного технологического оборудования а другая часть сконцентрирована в ведении цеховых механиков предприятия выполняющих текущие ремонты Т1 Т2 Т3 и технические обслуживания То.
Организация проведения ремонтов
Примечание СС – собственные силы цехового подразделения;
СП – специализированные ремонтно–механические заводы.
Достоинством смешанной формы управления является то что она позволяет распределить ремонтные силы и средства как на специализированных так и на собственных ремонтных службах что позволяет своевременно и качественно производить плановые ремонты (К Т1 Т2 Т3) и технические обслуживания То [13].
Электромеханическое оборудование Сарбайского карьера проектируем выполнять по системе ТОиР.
Системой ТОиР называется совокупность взаимосвязанных средств документации технического обслуживания ремонта и исполнителей необходимых для поддержания и восстановления качества изделий и их составных частей.
Сущность системы ТОиР – профилактическая заключающаяся в проведении работ по мойке чистке креплению подтягиванию регулировке и смазке а также по замене рабочего инструмента осмотре основных базовых деталей и узлов и оценке их технического ресурса по степени изнашивания.
Система ТОиР развивается в следующих направлениях:
Широкого внедрения средств технического диагностирования горного оборудования в процессе эксплуатации;
Разработке и внедрения современных технологических процессов изготовления ремонта и восстановления деталей узлов;
Централизации концентрации и специализации горных предприятий (РМЗ ЦММ).
Для ремонта электромеханического оборудования карьера проектируем агрегатно–узловой метод ремонта рисунок 3.1.
Рисунок 3.1. Схема агрегатно–узлового метода ремонта.
При агрегатно–узловом методе машина разбираем на узлы и агрегаты и собираем из ранее отремонтированных узлов и агрегатов из однотипной предшествующих машин находящихся в оборотном фонде.
За счет этого сокращается нахождение машин в ремонте т.к. в процессе ремонта выполняются только разборочно–сборочные работы по узлам и агрегатам и ремонт их осуществляется в межремонтный период [14].
Для горного оборудования карьера проектируем выполнять следующие виды обслуживаний и ремонтов:
Технические обслуживания:
-ежесменное обслуживание ЕО
-ежесуточная проверка правильности эксплуатации ЕПП
-наладка и ревизия полугодовая НРП наладка и ревизия годовая НРГ [13].
Для горного оборудования карьера согласно "Положения о ТОиР" принимаем следующие ремонтные нормативы таблица 3.2. [13]
Наименование оборудования
Межремонтный период м
Структура ремонтного цикла
К–2Т1–Т2–2Т1–Т3–2Т1–Т2– –2Т1–Т3–2Т1–Т2–2Т1–Т3–2Т1–Т2–2Т1–Т3–2Т1–Т2–2Т1– –Т3–2Т1–Т2–2Т1–К
Буровой станок СБШ–250МНА–32
К–2ТО–Т1–2ТО–Т2–2ТО–Т1– –2ТО–К
К–2Т1–Т2–2Т1–Т3–2Т1–Т2–2Т1–К
Продолжение таблицы 3.2
Электродвигатели 630 кВт
К– 11Т1–Т2–11Т1– Т2–11Т1–К
Электродвигатели 110 кВт
Электродвигатель – 40 кВт
6.1 Расчет годового количества ремонтов
Расчет годового количества ремонтов оборудования карьера выполняем расчетно–аналитическим методом по выражениям [14]:
где Тгк– календарное плановое время Тгк=12 мес;
ТТ1Т2Т3ТО – календарное время ремонтов и ТО.
Результаты расчетов сводим в таблицу 3.3
6.2 Определение годового объема ремонтных работ
Годовой объем ремонтных работ электромеханического оборудования карьера определяем по методу трудоемкости по выражению [15]:
Tpi – трудоемкость i–го ремонта или ТО.
Результаты расчета сводим в таблицу 3.3.
Объём работ силами специальных организаций – 92952 час в том числе
Слесарные работы – 46476 часов
Сварочные работы – 4648 часов
Кузнечные работы – 2778 часов
Электроремонтные работы – 16667 часов
Механические работы – 18518 часов
Термические работы – 463 часа
Гальванические работы – 463 часа
Окрасочные работы – 1389 часов
Прочие работы – 1389 часов
Определение трудоемкости ремонтных работ
Годовое количество ТОиР
Трудоемкость ремонтов
Годовой объём ремонтных работ
Электродвигатель – 630 кВт
Электродвигатель – 110 кВт
Объём работ своими силами – 1479143 часов в том числе
Слесарные работы – 76915 часов
Сварочные работы – 7396 часов
Кузнечные работы –4437 часов
Электроремонтные работы – 26624 часа
Механические работы – 29582 часа
Термические работы – 0 часов
Гальванические работы – 0 часов
Окрасочные работы – 2219 часов
Прочие работы – 740 часов
7.1 Расчет потребного количества ремонтного оборудования
Необходимое число ремонтного оборудования определяем по формуле
где Фoi – годовой фонд рабочего времени одной единицы ремонтного оборудования.
где Дк– число календарных дней в году Дк=365;
Дв – выходные Дв=104;
Дп – праздничные дни Дп=9.
Фо=(365–104–9)·8·2·095=37848
Количество станков в РММ
Из них 30% – 13 токарных 20% – 9 сверлильных 3% – 2 заточных 10% – 5 строгальных 12% – 6 фрезерных 10% – 5 намоточных 2% – 1 кузнечных 2% – 1 балансировочных 1% – 1 окрасочных [15].
Количество оборудования на РМЗ
7.2 Расчет численности ремонтных рабочих
Явочный штат ремонтных рабочих рассчитываем по выражению:
Фр – годовой фонд рабочего времени одного ремонтника.
где t'см – время на которое сокращается продолжительность смены в предпраздничные дни - 1 час;[14]
Списочный штат ремонтных рабочих:
Фр=(365–9–104) ·8 – (9+104) ·1=1903
Число работающих на РММ
Число работающих на РМЗ
С учетом коэффициента списочного состава kсп=118 [14] списочное количество работающих составит для РММ – 90 человек.
Количество ИТР принимается 6% от явочной численности – 5 человек.
В соответствии с технологическим процессом ремонта электромеханического оборудования в состав РММ включаем следующие ремонтные отделения[14]:
-разборочно–сборочное
-кузнечно–термическо–гальваническое
-складские и бытовые помещения
Производственная площадь ремонтных отделений определяем по удельной площади приходящейся на одного рабочего:
где Np – кол–во работающих в смену;
Sуд – удельная норма площади на 1–го работника [15]
Общая площадь ремонтного подразделения:
Общая площадь РММ составит 1956 м2.
Установка для наплавки гребней колесных пар (рисунок 4.1) состоит из следующих частей: тележки привода вращения колесной пары карданного вала тормоза ручного флюсосборника флюсобункера флюсораздатчика насадки флюсосборника катушки механизма подачи наплавочной проволоки приспособления для дуговой наплавки пульта управления.
Рисунок 4.1. Общий вид установки.
Сварочный трансформатор устанавливается стационарно и на рисунке не показан. Установка перемещается вручную по специальному рельсовому пути.
Тележка состоит из платформы в нижней части которой на кронштейнах смонтированы четыре независимых одноребордчатых колеса установленных в опорах на подшипниках качения. Одно колесо имеет стояночный тормоз состоящий из фрикционной накладки закрепленной на выдвижной оси пружины рукоятки и корпуса закрепленного на тележке. Торможение колеса осуществляется поворотом рукоятки которая поджимает фрикционную накладку к цилиндрической поверхности колеса.
На платформе сверху установлена стойка для крепления шкафа управления механизма подачи проволоки сварочного аппарата А-1416. Кроме стойки на платформе установлена рама с приводом вращения колесной пары состоящим из электродвигателя ременной передачей связанным с входным валом цилиндрического редуктора выходной вал которого через муфту соединен с входным валом червячного редуктора. Вращение от выходного вала червячного редуктора передается на наплавляемую колесную пару через карданный вал который с одной стороны имеет фланцевое соединение и крепится на выходном валу редуктора через промежуточный фланец а со второй стороны имеет форму накидного ключа который входит в зацепление с гайкой находящейся на оси колесной пары тягового двигателя.
Для проведения наплавки требуется подключать установку к вытяжной вентиляции воздушной напорной магистрали электрической сети переменного тока и низкой стороне сварочного трансформатора.
Наплавка производится электрической дугой возникающей между электродом (к нему подключается отрицательный провод с выхода сварочного трансформатора) и гребнем колесной пары (к ней подключается положительный провод с выхода сварочного трансформатора)
При горении электрической дуги между электродом и гребнем колесной пары вследствие высокой температуры происходит плавление поверхностного слоя гребня колесной пары и электрода. Так как поперечное сечение электрода меньше чем сечение гребня колесной пары быстрее происходит плавление металла электрода которое необходимо компенсировать скоростью подачи электродной проволоки при этом происходит сплавление расплавленного металла электрода и расплавленного металла гребня. При этом способе в зону горения дуги непрерывно подают гранулированный флюс. Часть флюса плавится под действием высокой температуры дуги образуя вокруг нее эластичную оболочку надежно защищающую наплавленный металл от действия воздуха и препятствующую выгоранию углерода и других элементов.
При медленном вращении детали жидкий металл выйдя из зоны горения дуги затвердевает. Флюс так же затвердевает покрывая наплавленный слой плотной коркой.
Скорость горения дуги (скорость наплавки или расплавления электрода) подбирается экспериментально изменением тока сварочного трансформатора скорости подачи электродной проволоки положения сварочной головки относительно реборды колесной пары частотой вращения колесной пары (регулируется передаточным отношением ременной передачи) и величиной слоя флюса в зависимости от степени износа и как следствие количества наплавляемого металла.
Флюс в зону наплавки подается по пневмопроводу из флюсобункера за счет разряжения сжатым воздухом под давлением 25 - 6 кгсм2. Остатки нерасплавившегося флюса с места сварки отсасываются эжектором во флюсосборник за счет разряжения.
2.1 Выбор электродвигателя
Реакции в подшипниковых опорах колесной пары Н находим по формуле:
где mK – масса колесной пары (для колесной пары думпкара mK =2850 кг).
Момент сопротивления от трения в подшипниковых опорах колесной пары Нм:
где f – коэффициент трения в подшипниковой опоре;
d – средний диаметр подшипника.
Для колесных пар с подшипниками скольжения принимаем f =01; d =02 м. По формуле (4.2):
При частоте вращения наплавляемого объекта n=0173 обмин потребная мощность на колесной паре кВт:
Требуемая номинальная мощность электродвигателя кВт:
где – общий КПД привода.
Согласно принятой кинематической схеме привода общий КПД равен:
где 1 – КПД ременной передачи;
– КПД зубчатой передачи;
– КПД червячной передачи;
– КПД подшипниковых опор колесной пары.
Согласно [16] примем 1 =095; 2 =097; 3 =075; 4 =096.
Из [16] выбираем асинхронный электродвигатель переменного тока серии 4А (по ГОСТ 19523-81) имеющий следующие характеристики: типоразмер 4А71В4УЗ; мощность 075 кВт; частота вращения 1495 обмин.
2.2 Кинематический расчет привода.
Общее передаточное число привода находим по формуле:
Производим разбивку общего передаточного числа по отдельным ступеням:
где U1 – передаточное число ременной передачи;
U2 – передаточное число цилиндрического редуктора;
U3 – передаточное число червячного редуктора.
Ориентируясь на рекомендации [16] назначаем U1=3.6 U2=40 U3=60.
2.3 Выбор редуктора.
По величине передаточного числа U2=40 из [17] выбираем цилиндрический двухступенчатый редуктор типа Ц2У имеющий следующие характеристики: типоразмер Ц2У-125; номинальное передаточное число 40; номинальный крутящий момент на тихоходном валу 500 Нм; КПД не менее 097; номинальная радиальная нагрузка на выходном валу 1000 Н; масса не более 53 кг.
По величине передаточного числа U3=60 из [18] выбираем червячный одноступенчатый редуктор типа Ч имеющий следующие характеристики: типоразмер Ч-125; номинальное передаточное число 60; номинальный крутящий момент на тихоходном валу 610 Нм; КПД не менее 076; масса 88 кг.
2.4 Расчет ременной передачи.
Исходные данные для расчета: в кинематической схеме привода ременная передача расположена между электродвигателем и цилиндрическим редуктором. Номинальная передаваемая мощность 075 кВт передаточное отношение 36. Электродвигатель переменного тока с частотой вращения 1495 обмин. Режим работы тяжелый.
Для уменьшения габаритов ременной передачи выбираем клиновый ремень [19]. Расчет начинаем с выбора сечения ремня.
По номограмме [19] для заданных условий подходит ремень сечением «О». Из [19] выписываем технические данные ремня: W=10 мм; ТО=6 мм; А(площадь сечения)=047 см2; масса 1 метра ремня m=006 кг; расчетная длина LР=400÷2500 мм; ΔL=LP-LВ=25 мм; минимальный диаметр меньшего шкива d1min (не менее)=63 мм.
Определяем диаметры шкивов: для повышения ресурса передачи рекомендуется устанавливать меньший шкив с расчетным диаметром d1> d1m из стандартного ряда значений [19] принимаем ближайший диаметр d1=80 мм.
Диаметр ведомого шкива определяется по формуле:
Принимаем ближайшее значение из стандартного ряда 280 мм. Уточним передаточное отношение с учетом относительного скольжения S=001:
Определяем межосевое расстояние по формуле:
где Т0 – высота сечения ремня мм.
Принимаем промежуточное значение 300 мм.
Определяем расчетную длину ремней по формуле:
Принимаем ближайшее стандартное значение 1120 мм.
Уточняем межосевое расстояние по формуле:
где w и y – величины определяемые по приведенным ниже зависимостям:
Определяем угол обхвата ремнями малого шкива по формуле:
Определяем коэффициенты: угла обхвата Сα=052 [19]; длины ремняСL=095 [19]; режима работы СР=12; числа ремней СZ=095 [19] предварительно задавшись числом ремней 2.
Находим [19] номинальную мощность N0: для ремня сечением «О» с расчетной длиной 1120 мм при d1=80 мм U=36 и n=1495 обмин имеем N0=082 кВт.
Определяем расчетную мощность по формуле:
Находим число ремней:
Окончательно принимаем z=1.
Находим скорость ремня мс:
Значение коэффициента учитывающего влияние центробежных сил =006 [20].
Натяжение ветви ремня Н:
Усилие действующее на валы на которых установлены подшипники Н:
Определяем рабочий ресурс ч рассчитанной клиноременной передачи:
где NОЦ – число циклов выдерживаемых ремнем (нормативный ресурс).
Для клиновых ремней сечением «О» имеем NОЦ=46106 по формуле (4.19):
Так как для тяжелого режима работы средний ресурс установлен 2000 часов то заключаем что вычисленный ресурс удовлетворяет нармативному.
3 Расчет режима сварки под флюсом и выбор сварочного оборудования
Режим автоматической сварки под флюсом назначаем в следующей последовательности. Устанавливаем требуемую глубину проплавления =10 мм.
Далее выбираем величину сварочного тока [7] из расчета 80÷100 А на 1 мм глубины проплавления:
Напряжение на дуги назначаем в диапазоне 30÷40 В.
Диаметр электродной проволоки для требуемой глубины проплавления =10 мм согласно [7] d=2÷5 мм.
Скорость сварки (мс) определяется из выражения:
где аН – коэффициент наплавки г(А·ч);
γ – плотность металла гсм3;
FНМ – площадь поперечного сечения наплавленного металла см2.
Диаметр колесной пары по границе гребня равен D=910 мм (после износа) а после наплавки D1=930 (толщина наплавленного слоя равна по 10 мм с каждой стороны колесной пары).
Коэффициент наплавки под флюсом в среднем составляет аН=14÷16 г(А·ч). Плотность наплавленного металла примем 18 гсм3.
Вычисляем скорость сварки по формуле (4.21):
Из [7] выбираем сварочное оборудование имеющее следующие параметры:
Сварочный автомат: типА-1416 УХЛ4
-номинальный сварочный ток при ПВ=100 % 1000
-напряжение питающей сети трехфазного переменного тока
при частоте 50 Гц В380
-количество электродов шт.1
-диаметр электродной проволоки мм2
-способ защиты дугифлюс
-скорость подачи электродной проволоки мч от 47 ± 7 до 509 ±76
-скорость сварки мч от 12-2 до 120 +12
-регулировка скорости подачи электродаступенчатая
-регулировка скорости сваркиступенчатая
-регулировка угла наклона электрода град±45
-расход воздуха не более м3ч30
-давление воздуха в питающей магистрали кгсм25
-высота всасывания флюса не менее м2
Далее определяем массу наплавленного на изделие металла г:
где GHM – масса наплавленного металла;
FHM – площадь наплавленного шва см2;
L – длина сварного шва см;
γ – плотность металла гсм3.
Длина сварного шва: =см2. По формуле (4.23):
Для определения расхода электродной проволоки следует [7] учесть потери на угар и разбрызгивание (не весь металл проволоки переходит в шов). Эти потери для сварки под флюсом составляют от 2÷5 %.
Окончательно принимаем1700 г. Расход флюса принимаем равным массе наплавленного металла то есть 16505 г.
Для соединения выходного вала цилиндрического редуктора с входным валом червячного редуктора используем втулочно-пальцевую муфту по ГОСТ 21424-75. Согласно [21] для соединяемых диаметров концов валов 45 мм и 32 мм (исполнение коническое) выбираем муфту с номинальным крутящим моментом М=710 Н·м.
Требуемый крутящий момент Н·м определяется по формуле:
где МНОМ – номинальный момент на валу двигателя Н·м.
где NДВ – номинальная мощность двигателя кВт;
nДВ – частота вращения вала двигателя обмин.
По формулам (4.25) и (4.26):
Так как М=710 Н·м > МК=61666 Н·м следовательно подобранная муфта удовлетворяет условию проверки.
Организация безопасных условий труда на производстве возложена на административно – технический персонал предприятия. Директор главный инженер главный механик главный энергетик начальники цехов и сменные мастера обеспечивают на своих участках безопасные условия труда. Они должны принимать все необходимые меры к устранению или уменьшению опасностей на производстве предупреждению несчастных случаев и содержанию рабочих мест в надлежащем санитарно – гигиеническом состоянии.
Большая организаторская роль в создании и поддержании нормальных и безопасных условий труда на предприятиях принадлежит отделу технической безопасности который находится в непосредственном подчинении главного инженера предприятия.
Различают следующие виды инструктажа рабочих:
)вводный или предварительный
)инструктаж на рабочем месте
)инструктаж рабочих переводимых с одной работы на другую
)повторный инструктаж проводимый периодически.
Вводный инструктаж проводится работниками отдела техники безопасности предприятия а все остальные – техническим персоналом цеха.
К управлению горными и транспортными машинами допускаются лица прошедшие обучение и имеющие удостоверение на право управления соответствующей машиной. Машинист и помощники машинистов машин управление которыми связано с оперативным включением и отключением высоковольтных установок должны иметь квалификацию по знанию правил техники безопасности при эксплуатации электротехнических установок промышленных предприятий: машинисты – не ниже IV группы а помощники машинистов – не ниже III группы.
К техническому руководству на открытых разработках допускаются лица имеющие законченное высшее и среднее горнотехническое образование или право ответственности ведения горных работ [23].
Рабочие поступающие на горное предприятие (в том числе на сезонную работу) должны пройти с отрывом от производства предварительное обучение по технике безопасности в течение 3 дней (ранее работающие в горнодобывающей промышленности и рабочие переводимые на работу по другой профессии – в течение 2 дней) и сдать экзамен по утверждённой программе комиссии под председательством главного инженера предприятия или его заместителя.
Помимо предварительного обучения рабочие должны пройти обучение по профессии в объёме и в сроки установленные программой и сдать экзамен. Лица не прошедшие обучение и не сдавшие экзамен к самостоятельной работе не допускаются. Всем рабочим выдержавшим экзамены выдаются удостоверения установленной формы.
Студенты высших и учащиеся средних технических учебных заведениях до начала первой производственной практики должны пройти обучение в течение двух дней и сдать экзамены по технике безопасности экзаменационной комиссии предприятия [24].
Всем рабочим под личную расписку должны быть выданы администрацией инструкции по безопасным методам ведения работ по их профессии.
2.1Основные определения
Несчастным случаем или травмой называется повреждение тела человека или нарушение функций его органов в результате внезапного внешнего воздействия. Несчастные случаи подразделяются на травмы связанные с производством; травмы связанные с работой и на бытовые травмы. В основу такого деления положены место и время получения травмы работающим и связь выполняемой работы с производством [25].
Несчастные случаи по характеру связи с работой можно разбить на три группы:
Первая группа – несчастные случаи имеющие непосредственную связь с работой.
Вторую группу составляют несчастные случаи которые лишь косвенно связаны с выполняемой работой.
К третьей группе относятся несчастные случаи которые произошли при выполнении государственных или общественных обязанностей.
К несчастным случаям связанным с производством относятся те из них которые произошли на территории предприятия; вне территории предприятия при выполнении работы по заданию предприятия; на территории предприятия с обслуживающими его лицами а так же с рабочими и служащими доставленными на место работы и с работы на транспорте предприятия.
В зависимости от исхода несчастные случаи делятся на следующие группы:
Лёгкие несчастные случаи отличительной особенностью которых является полное восстановление трудоспособности пострадавшего.
Тяжёлые случаи с повреждением крупных кровеносных сосудов и нервов костей сотрясение мозга переломы костей проникающие ранения живота и др. нередко заканчивающиеся продолжительной потерей трудоспособности (пострадавшему устанавливается инвалидность I II III группы).
Несчастные случаи со смертельным исходом.
По числу пострадавших несчастные случаи разделяются на одиночные и групповые.
К материально – техническим причинам несчастных случаев на открытых горных работах относят повреждения механизмами обвалы обрушения падение кусков руды или породы действие взрыва при взрывных работах действие электрического тока отсутствие оградительных или предохранительных устройств у машин и механизмов несовершенство средств индивидуальной защиты и др.
Из организационно – технических причин наиболее важными являются: плохая обученность пострадавшего неправильный приём работы отсутствие средств индивидуальной защиты отсутствие технического надзора за ведением работ неудовлетворённое состояние трудовой дисциплины и др. К несчастным случаям по санитарно – гигиеническим причинам относятся те из них которые произошли из–за неблагоприятных метеорологических условий труда или в следствии недостаточной освещенности сильного шума и др [26].
2.2Производственные вредности как причина профессиональных заболеваний
Профессиональным заболеванием называется постоянное ухудшение здоровья работающего вызванного неблагоприятными условиями труда или систематическим воздействием на организм вредных веществ. Неблагоприятные условия труда и вредные вещества называются производственными вредностями. К производственным вредностям относятся определённые факторы трудового процесса (положение тела при работе мышечное или нервно – психическое напряжение отдельных органов и систем) и неблагоприятные санитарно – гигиенические условия труда на рабочих местах (загрязнение воздуха пылью и ядовитыми газами недостаточное освещение значительный шум недопустимые параметры вибраций и др.).
К наиболее распространённым профессиональным заболеваниям для условий открытых работ относятся:
пневмокониозы (силикозы силикатозы антракозы другие пылевые фиброзы в чистом виде или в сочетании с туберкулёзом лёгких или смешанные формы) вызванные длительным вдыханием пыли.
отравления (острые или хронические и их последствия) вызванные действием на организм веществ обладающих токсическим действием (окислы азота окись углерода альдегиды и др.).
антоневрозы и ангиотрофоневрозы вызванные вибрацией при работе с вибрирующим инструментом (вибрационная болезнь).
прогрессирующее понижение слуха в следствии систематического воздействия сильного шума или резкого звука.
3.1 Санитарно–бытовые помещения
При каждом карьере или для нескольких карьеров должны быть оборудованы административно–бытовые помещения. Бытовые помещения должны иметь отделения для мужчин и женщин и рассчитываться на число рабочих проектируемое ко времени полного освоения карьера.
В состав бытовых помещений должны входить: гардеробы для рабочей и верхней одежды помещения для сушки и обеспыливания рабочей одежды душевые уборные прачечная мастерские по ремонту спецодежды и спецобуви помещения для чистки и мойки обуви кипятильная станция для питьевой воды фляговое помещение респираторная помещение для личной гигиены женщин здравпункт [23].
Административно–бытовые помещения столовые здравпункт должны располагаться с наветренной стороны на расстоянии не менее 50 метров от открытых складов угля руды дробильно–сортировочных фабрик эстакад и других пылящих участков но не далее 500 метров от основных производственных зданий. Все эти здания следует окружать полосой древесных насаждений.
Раздевалки и душевые должны иметь такую пропускную способность чтобы работающие в наиболее многочисленной смене затрачивали на мытье и переодевание не более 45 минут.
Душевые или бани должны быть обеспечены горячей и холодной водой из расчета 500 литров на одну душевую сетку в час и иметь смесительные устройства с регулирующими кранами.
Регулирующие краны должны иметь указатели холодной и горячей воды. Трубы подводящие пар и горячую воду должны быть изолированы или ограждены на высоту 2 метра от пола.
Качество воды используемой для мытья в обязательном порядке согласуется с органами государственной санитарной инспекции.
В душевой и помещениях для раздевания с отделениями для хранения одежды полы должны быть влагостойкими и с нескользкой поверхностью стены и перегородки – облицованы на высоту не менее 25 метров влагостойкими материалами допускающими легкую очистку и мытье горячей водой. В этих помещениях обязательно наличие кранов со шлангом для обмывания пола и стен.
Все санитарно–бытовые помещения должны иметь приточно–вытяжную вентиляцию обеспечивающую содержание вредных примесей в воздухе этих помещений в пределах норм.
3.2 Медицинская помощь
На каждом карьере или для группы близко расположенных карьеров должен быть организован пункт первой медицинской помощи. Организация и оборудование пункта согласовываются с местными органами здравохранения.
Пункт первой медицинской помощи обязательно оборудуется телефонной связью.
3.3 Производственно–бытовые помещения
Кабины экскаваторов буровых станков и других механизмов должны быть утеплены и оборудованы безопасными отопительными приборами.
На открытых разработках должны быть оборудованы в соответствии с общими санитарными правилами закрытые туалеты в удобных для пользования местах.
На каждом предприятии должна быть организована стирка спецодежды а также починка обуви и спецодежды.
Каждое предприятие обязано обеспечить всех работающих питьевой водой.
Пользование водой из источников карьера для хозяйственно–питьевых нужд допускается после специального разрешения на это органов государственной санитарной инспекции.
Водонапорные сооружения поверхностных источников воды а также скважины и устройства для сбора воды должны быть ограждены от загрязнения. Для источников предназначенных для питьевого водоснабжения обязательно устанавливается зона санитарной охраны.
Персонал обслуживающий местные установки по приготовлению питьевой воды должен проходить медицинский осмотр и обследование в соответствии с действующими санитарными нормами.
Сосуды для питьевой воды должны изготовляться из оцинкованного железа или по согласованию с Государственной санитарной инспекцией из других материалов легко очищаемых и дезинфицируемых.
Сосуды для питьевой воды должны быть снабжены кранами фонтанного типа защищены от загрязнений крышками запертыми на замок и не реже одного раза в неделю промываться горячей водой или дезинфицироваться.
Должностные лица предприятий и организаций ведущих разработку полезных ископаемых открытым способом а также инженерно–технические работники учреждений осуществляющих проектирование конструирование исследования и другие работы для этих предприятий и организаций виновные в нарушении настоящих Правил несут личную ответственность независимо от того привело или не привело это нарушение к аварии или несчастному случаю.
Выдача должностными лицами указаний или распоряжений принуждающих подчиненных нарушать настоящие Правила безопасности и инструкции к ним самовольное возобновление работ остановленных органами госгортехнадзора или технической инспекцией труда а также непринятие этими лицами мер по устранению нарушений которые допускаются в их присутствии подчиненными должностными лицами или рабочими являются грубейшими нарушениями Правил.
В зависимости от характера допущенных нарушений и их последствий руководители специалисты и рабочие привлекаются к дисциплинарной административной материальной или уголовной ответственности в порядке установленном законодательством.
5.1 Мероприятия безопасности и устройства препятствующие возникновению пожаров
Противопожарная профилактика – это комплекс мероприятий направленных на предупреждение пожаров предотвращения распространения огня устройства путей эвакуации людей и материальных ценностей и создание условий для быстрой ликвидации пожара в случае его возникновения. Пожарно – профилактические мероприятия делятся на строительные осуществляемые при проектировании и строительстве предприятия и режимные выполняемые в процессе эксплуатации этих объектов [27].
На случае возникновении пожара в производственных и вспомогательных зданиях должна быть обеспечена возможность эвакуации людей путем устройства достаточного количества выходов.
Эвакуационными выходами могут быть проходы двери ворота если они ведут:
–из помещений первого этажа непосредственно наружу;
–из помещений в лестничную клетку с выходом наружу непосредственно или через вестибюль;
–из помещений в проход или коридор с непосредственным выходом наружу или выходом в лестничную клетку.
Количество выходов наружу и на лестницы определяется исходя из предельного расстояния от любого рабочего места в здании до одного из выходов считая по линии свободных проходов Эти расстояния устанавливаются в зависимости от категории производств по пожароопасности степени огнестойкости и этажности здания и принимаются в пределах от 25 до 75м.
Из каждого производственного вспомогательного и общественного здания должны быть не менее двух выходов.
Все эвакуационные двери ворота и люки должны открываться в сторону выхода наружу.
Суммарная ширина лестничных клеток а также дверей или проходов многоэтажных производственных или вспомогательных зданий на путях эвакуации должна приниматься в зависимости от числа людей находящихся в наиболее населенном этаже здания из расчета:
– для двух – и одноэтажных зданий – 125 человек на 1м ширина марша двери или прохода;
– для трехэтажных – 100 человек на 1м ширины марша двери прохода;
– для зданий высотой более трех этажей – 80 человек на 1м ширины марша двери или прохода.
При строительстве зданий и сооружений предусматриваются также специальные конструктивные элементы называемые противопожарными преградами. Различают основные и вспомогательные противопожарные преграды. Все основные преграды выполняются из несгораемых материалов. К ним относятся противопожарные несгораемые стены (брандмауэры) с пределом огнестойкости не менее 4 часов противопожарные зоны с пределом огнестойкости их несущих конструкций (стен или колон) не менее 4 часов тамбуры шлюзы (1ч) перекрытия и перегородки (1ч).
К вспомогательным противопожарным преградам относятся все несгораемые или трудносгораемые ограждающие и несущие конструкции с пределом огнестойкости не менее 025 ч.
Запрещается курение внутри горной техники и хранение в ней легко воспламеняемых материалов.
5.2 Средства пожаротушения
Для тушения пожаров применяют воду водные эмульсии химическую и воздушно–химическую пену водяной пар углекислый газ порошки и сжатый воздух [28].
В виде компактных и распыленных струй воды применяется для тушения большинства твердых горючих веществ тяжелых нефтепродуктов для создания водяных завес и охлаждания объектов находящихся в близи пожара.
5.3 Ручные огнетушители
В огнетушителя ОП–3ОП–5 и ОП–М кислотная часть состоит из водного раствора серной кислоты и железного дубителя. При тушении пожара пена покрывая поверхности изолирует их от окружающего воздуха а углекислый газ разбавляет концентрацию кислорода.
Воздушно–механическая пена обычной кратности применяется для тушения нефтепродуктов твердых горючих веществ. Пену высокой кратности применяют для тушения пожаров в подвалах шахтах и других закрытых объектах а также разлитых жидкостей.
Порошковые огнетушители применяют для тушения металлов и других твердых и жидких горючих веществ и материалов.
Сжатый воздух используют для тушения пожаров горючих жидкостей методом их перемешивания.
Для обеспечения карьеров водой должен устраиваться противопожарный трубопровод.
В систему производственно – противопожарного водопровода входят водосборные сооружения наружная водопроводная сеть прокладываемая на территории предприятия и внутренняя сеть прокладывания в зданиях.
Пожарные гидранты должны устанавливаться на кольцевых водопроводных линиях диаметром не менее 100 мм вдоль дороги на расстоянии один от другого не более 150м и вблизи перекрестков не ближе 5 м от стен зданий [28].
6 Правила техники безопасности при эксплуатации установки по наплавке колесных пар думпкаров
Перед началом работы установки следует провести следующие подготовительные мероприятия:
-осмотреть металлоконструкцию установки на предмет обнаружения повреждений;
-проверить крепление редукторов и наличие в них масла;
-проверить наличие чистого флюса во флюсобункере и плотность закрытия крышки.
При необходимости произвести досыпку флюса из тары или из флюсосборника (окалина и крупные спекшиеся куски флюса – удаляются);
-проверить надежность крепления наплавочной головки;
-проверить надежность заземления тележки и основных составных ее частей;
-проверить целостность манометра;
-в случае отсутствия наплавочной проволоки на кассете (бухту установить с помощью грузоподъемного механизма);
-проверить работу и наличие воздушных присоединительных рукавов и патрубков;
-проверить исправность сварочного аппарата – при необходимости подтянуть гайки крепления сварочных проводов на балластных сопротивлениях наплавочной тележке и сварочном аппарате;
-проверить исправность штепсельных соединений для сварочного провода в случае необходимости устранить неисправность.
К работе на установке наплавки гребней колесных пар допускаются лица не моложе 18-ти лет прошедшие инструктаж по ТБ изучившие руководство по эксплуатации и получившие практические навыки по ее эксплуатации имеющие удостоверение электросварщика стропальщика и квалификационную группу по электробезопасности не ниже 2.
При работе на установке выполнять «Правила техники безопасности при эксплуатации электроустановок промышленных предприятий» общие требования безопасности электросварочных работ по ГОСТ 12.3003-86 «Правила пожарной безопасности при производстве строительно-монтажных и огневых работ» (ППБС-01-94 от 14.04.1994г.) и «Правила пожарной безопасности в Республике Казахстан. Основные требования» (ППБ РК от 20.03.2006г №4126)
Работа на установке разрешается только при наличии надежного заземления сварочного источника шкафа питания и собственно установки.
Запрещается производить заземление отдельных частей аппаратуры последовательно. Каждая точка подлежащая заземлению должна быть присоединена непосредственно к контуру заземления.
Запрещается использовать контур заземления в качестве обратного провода сварочной цепи.
Запрещается наличие около установки легко воспламеняющихся материалов.
Обслуживающий персонал должен иметь рукавицы спецодежду каску ботинки на резиновой подошве и защитные очки.
Запрещается работа обслуживающего персонала без защитных очков.
Запрещается вскрывать и производить регулировку и ремонт механизмов во время работы установки.
Запрещается оставлять работающую установку без надзора. Не допускается нахождение посторонних лиц в рабочей зоне работающей установки.
Запрещается работа установки без укрытия привода.
К проведению технического обслуживания (ТО) установки допускаются лица из числа обслуживающего или ремонтного персонала не моложе 18-ти лет ознакомленные с конструкцией технической документацией и работой изделия получившие инструктаж согласно установленному порядку (порядок проведения и объем инструктажей определяет подразделение которое эксплуатирует установку).
Перед тем как приступить к работе по ТО – изделие обесточить. На главном рубильнике убрать предохранительные вставки и вывесить плакат «Не включать – работают люди».
Отключить подачу рабочего давления воздуха к установке на кран вывесить плакат «Не включать – работают люди»;
При проведении ТО изделия – пользоваться исправным инструментом и приспособлениями.
При использовании ударного инструмента – использовать защитные очки или маску.
Промышленная экология– прикладная наука о взаимодействии промышленности (как отдельных предприятий так и техносферы) и окружающей среды и наоборот – влияние условий природной среды на функционирование предприятий их комплексов [29].
В окружающей среде выделяют следующие зоны влияния промышленности:
Воздух (атмосферный воздух).
Вода (грунтовые поверхностные).
Энергетические воздействия:
Процессы окисления и выщелачивания токсичных элементов значительно активизируются под влиянием техногенных факторов возникающих при отработке рудных месторождений. В этой связи большое значение с точки зрения влияния на окружающую среду имеет способ отработки месторождения - открытый карьерный или подземный шахтный.
Наиболее неблагоприятным является открытый способ при котором забалансовые руды и минерализованные вскрышные породы в огромных количествах складируются на поверхности превращаясь в мощный источник загрязнения почв и воды на десятки и сотни лет. Накапливающаяся в теле отвала атмосферная влага превращается в насыщенную металлами серную кислоту самотеком сбрасывающуюся с дренажными водами в подстилающие отвалы почвы грунтовые воды и далее в ручьи и реки.
Большую опасность для окружающей среды и прежде всего для водных ресурсов районов размещения месторождений и горнодобывающих предприятий представляют откачиваемые из шахт и карьеров рудничные воды дренажные и сбросные воды хвостохранилищ. Для их обезвреживания и очистки требуется строительство специальных очистных сооружений.
Применение очистки сточных вод основано на использовании физических химических биологических физико-химических и биологических методов. Очистка сточных вод широко применяется в самых различных отраслях промышленности и тех или иных модификациях используется фактически в любых технологических циклах. Весьма перспективным представляется использование этих методов и в горнорудной промышленности (пруды-отстойники флотационные системы очистки системы аэрации и биологической очистки).
Сброс воды откачиваемой из водопонизительных устройств и горных выработок на поверхность земли не допускается. Допускается предусматривать сброс воды на неиспользуемые земли если при этом исключаются возможность попадания их в водные объекты загрязнение подземных вод эрозия почвы заболачивание местности и другие виды ущерба окружающей природной среде.
Для снижения концентрации взвешенных веществ предусмотрено отстаивание рудничных вод в отстойниках. Вместимость отстойника определяется с учетом объема откачиваемых рудничных вод требуемого времени отстоя и допускаемого сброса осветленных вод в водный объект.
Также для снижения концентрации загрязняющих веществ предусмотрено применение соответствующих физико-химических и биологических методов очистки рудничных вод. При необходимости очистка рудничных вод может быть заменена сбросом их в накопители-испарители.
Интенсивное пылеобразование в карьере создают многочисленные источники:
- экскаваторные работы;
- движение технологического транспорта.
Основной мерой борьбы с пылью при карьерных работах является использование пылеуловительных установок на станках. При погрузочных работах борьба с пылью ведется методом орошения забоя и взорванной массы при помощи гидромониторов оборудованных на передвижных установках. На автодорогах борьба с пылью проводится специальными машинами при помощи полива водой и специальными растворами.
Состав атмосферы карьеров должен отвечать установленным нормативам по содержанию основных составных частей воздуха и вредных примесей (пыль газы) с учетом действующих ГОСТов.
Воздух рабочей зоны должен содержать по объему 20 % кислорода и не более 05% углекислого газа: содержание других вредных газов не должно превышать величин ПДК.
В карьере имеющем источники выделения ядовитых газов (от работы автомобилей из пожарных участков из дренируемых в карьер вод от взрывных работ и др.) проводится на рабочих местах отбор проб для анализа воздуха на содержание вредных газов не реже одного раза в квартал.
Для интенсификации естественного воздухообмена в плохо проветриваемых и застойных зонах карьера организована искусственная вентиляция с помощью вентиляционных установок.
В карьере отмечается выделение вредных примесей поэтому применяются средства подавления или улавливания пыли ядовитых газов и агрессивных вод непосредственно в местах их выделения.
В случае когда применяемые средства не обеспечивают необходимого снижения запыленности воздуха в карьере осуществляется изоляция кабин экскаваторов и буровых станков с подачей в них очищенного воздуха.
Для снижения пылеобразования при экскавации горной массы в теплые периоды года проводят систематическое орошение взорванной горной массы водой.
Карьер и терриконы занимают огромные площади выводя из хозяйственного оборота миллионы гектаров земель большинство из которых были когда-то плодородны. Свойством карьеров является разрастание его со временем что ещё более усугубляет ситуацию по рациональному использованию земельных ресурсов.
Терриконы - горы из отвалов пустой породы или промышленных "хвостов". Они содержат вредные вещества некоторые из них издают неприятный запах при ветре они раздуваются и возникают пыльные бури при осадках размываются в результате мало- и непродуктивными становятся земли на территории в 10 - 15 раз превышающей по площади сами терриконы.
Для решения проблемы карьеров и терриконов необходима рекультивация - возвращение землям утраченной продуктивности либо конструирование нового эстетически наполненного ландшафта.
Оптимальный вариант - не допустить образования карьеров и терриконов. Для этого нужно пустую породу перемещать в отработанную часть карьера застилая сверху почвой аккуратно снятой с места предполагаемой разработки. Таким образом и карьер не будет разрастаться и пустая порода возвращаться на место а не образовывать терриконы.
Универсальный путь решения уже имеющейся проблемы - засыпать карьеры терриконами. Однако это не всегда выполнимо т.к. "хвосты" порой образуются довольно далеко от мест добычи и экономически очень невыгодно их перевозить обратно.
Можно использовать такой метод когда почвенный слой складируют в ленточный отвал на дно в центре карьерного поля по мере его отработки. Вскрышные породы складируют у границ карьерного поля на нерабочих бортах карьера в ленточные отвалы затем по мере отработки карьерного поля вскрышные породы перемещают на выположенную поверхность бортов и дна карьера прямым ходом планировочного оборудования до отвала почвенного слоя. После этого почвенный слой укладывают на вскрышные породы обратным ходом планировочного оборудования.
Проблема карьеров решается главным образом превращением их в водоёмы и дальнейшим использованием в рыбном хозяйстве или в качестве зоны отдыха. Местами допустимо выполаживание склонов и засаживание их деревьями или кустарниками.
Проблема терриконов требует более безотлагательного решения т.к. вред приносимый терриконами намного значительнее. Но и вариантов здесь гораздо больше: использование в стройиндустрии (хорошо применимо для "хвостов"); создание аттракционов и прочих объектов для отдыха и развлечений (главное чтобы терриконы были нетоксичны); произведение лесопосадок или разбивка садов; в крайнем случае можно произвести высев сорных трав из-за их неприхотливости.
Экономическое обоснование
Установка наплавки гребней колесных пар тяговых агрегатов предназначена для электродуговой наплавки на постоянном токе плавящимся электродом под слоем флюса колесных пар диаметром 950 мм без выкатки их из под думпкаров.
В дипломном проекте рассматривается разработка передвижная установка для наплавки гребней колесных пар с последующей заменой стационарной установки в технологическом цикле на передвижную установку что позволит сократить продолжительность времени технологического цикла как следствие уменьшатся расходы на обслуживание и эксплуатацию оборудования и при этом увеличится производительность труда.
Техническая характеристика проектируемой установки для наплавки колесных пар представлена в таблице 7.1 [30].
Техническая характеристика установки для наплавки
) Напряжение питающей сети трехфазного переменного тока
) Скорость подачи электродной проволоки
) Группа режима работы
) установки для наплавки
) Мощность электродвигателя
) Нормативный срок службы
) Категория ремонтной сложности
Расчет продолжительности технологического цикла установки для наплавки
Продолжительность технологического цикла установки для наплавки
) Время подъема колесной пары
) Время установки подставок под буксы
) Время монтажа установки
) Подготовительные операции перед наплавкой
) Время наплавки гребня колеса
) Время технологического цикла
Эффективный фонд времени работы установки для наплавки
) Число календарных дней в году
) Число праздничных дней
) Число выходных дней
) Номинальный фонд работы установки
) Процент потерь времени из-за
) Количество смен работы установки в сутки
) Продолжительность рабочей смены
) Эффективный фонд работы установки
Расчет годовой производительности установки
Годовая производительность установки для наплавки
) Эффективный фонд времени работы
) Производительность
Расчет стоимости установки для наплавки представлен в таблице 7.5.
Первоначальная стоимость установки для наплавки
) Цена проектирования и создания установки для наплавки
) Затраты на транспортировку
) Затраты на складирование
) Затраты на монтаж
) Полная первоначальная стоимость
Расчет годовых амортизационных отчислений производим по формулам:
Амортизационный фонд
) Полная первоначальная стоимость установки для наплавки
) Амортизационные отчисления
Расчет годовых затрат на текущий ремонт установки для наплавки гребней представлен в таблице 7.7.
Показатели системы ТО и Р установки для наплавки гребней
) Структура ремонтного хозяйства
1 текущий ремонт № 1
2 текущий ремонт № 2
3 капитальный ремонт
) Трудоёмкость ремонтов
Расчет продолжительности межремонтного периода представлен в таблице 7.8
Продолжительность межремонтного периода
) Нормативный ремонтный цикл
) Коэффициент учитывающий тип производства
) Коэффициент учитывающий условия производства
) Коэффициент учитывающий условия эксплуатации
) Количество ремонтов
) Межремонтный период
Расчет графика планово-предупредительных ремонтов представлен в таблице 7.9.
График планово-предупредительных ремонтов
дата последнего ремонта
Расчет затрат на текущий ремонт установки для наплавки гребней
Затраты на текущий ремонт установки для наплавки гребней
) Трудоёмкость ремонтных работ
) Средний разряд ремонтных работ
) Часовая тарифная ставка среднего разряда ремонтных рабочих
) Затраты на заработную плату
3 дополнительная заработная плата
Продолжение таблицы 7.10
) Начисления на заработную плату
) Затраты на материалы
) Затраты на социальный налог
) Затраты на социальные отчисления
) Итого затрат на текущий ремонт
Расчет затрат на электроэнергию представлен в таблице 7.11.
Затраты на электроэнергию
) Цена силовой электроэнергии 1 кВт·час
) Эффективный фонд работы
) Суммарная мощность электродвигателей
) Коэффициент использования установленной мощности электродвигателей
) Годовой расход силовой электроэнергии (Fэф·Nу·kМ)
) Затраты на силовую электроэнергию (ЦС·ЗС)
) Цена осветительной электроэнергии 1 кВт·час
) Коэффициент учитывающий время включения освещения
) Удельная мощность освещения 1 м2 площади
) Осветительная площадь
) Годовой расход осветительной энергии (Fэф·k· Ум· Sк)
) Затраты на освещение (ЦО· ЗО)
) Всего затрат на электроэнергию
Баланс рабочего времени представлен в таблице 7.12.
Баланс рабочего времени
) Номинальный фонд рабочего времени
3 выполнение государственных обязанностей
) Эффективный фонд рабочего времени
) Коэффициент списочного состава ДнFэф
Расчет численности рабочих представлен в таблице 7.13.
Расчет численности рабочих
Кол-во оборудова-ния ед.
Норма обслужива-ния чел.
Явочная числен-ность
Списочная численность
Расчет заработной платы для слесаря обслуживающего установку для наплавки гребней колеса представлен в таблице 7.14.
Расчет затрат на вспомогательные материалы и охрану труда приведены в таблице 7.15.
Сменная тарифная ставка
Система оплаты труда
Явочное количество рабочих человек
Списочная численность человек
Рабочий фонд времени челдни
Основная заработная плата тыс. тенге
Дополнительная заработная плата тыс. тенге
Эффективный фонд рабочего времени
Всего (гр. 7 * гр. 8)
ночные (гр. 9 гр. 3)
по тарифу (гр. 3 * гр. 9)
ночные (гр. 3 * гр. 10*05)
праздничные (гр. 3 * гр. 11)
итого (гр. 12+13+14+15)
Социальный налог ( гр. 16*011)
Всего фонд заработной платы(гр. 6+гр.17+гр.18+гр.19)
Среднемесячная заработная плата 1рабочего
Расчет фонда заработной платы слесаря обслуживающего установку для наплавки гребней колеса
Затраты на вспомогательные материалы и охрану труда
) Затраты на электроэнергию
) Расходы на вспомогательные материалы
) Фонд заработной платы рабочих
Продолжение таблицы 7.15
) Норматив отчислений
) Расход на охрану труда
Смета затрат на содержание и эксплуатацию установки для наплавки гребней колесных пар представлена в таблице 7.16.
Смета затрат на содержание и эксплуатацию установки для наплавки
) Заработная плата рабочих
) Вспомогательные материалы
Расчет срока окупаемости установки для наплавки гребней колесных пар представлен в таблице 7.17.
Срок окупаемости лет:
где Кб - полная первоначальная стоимость тенге
ЗЭ - затрат на содержание и эксплуатацию установки для наплавки тенге
П - общая прибыль тенге
Срок окупаемости установки для наплавки
) Стоимость наплавки гребня колеса на стационарной установке
) Процент от стоимости замены колесной пары затрачиваемый на оплату различный налогов и содержание вспомогательный служб
Продолжение таблицы 7.17
) Средние затраты на непосредственное обслуживание ремонт материалы электроэнергию приходящиеся на одну наплавку гребня
) Налог с прибыли (30%)
) Чистая прибыль получаемая с наплавки колесной пары
) Общая прибыль с обслуживания 1778 единиц для наплавки гребней
) Экономический эффект (общая прибыль - сумма затрат содержание и эксплуатацию установки для наплавки)
В первом разделе приводится краткая техническая характеристика Сарбайского карьера и на основании заданной производительности производится выбор буровых станков СБШ–250МНА–32 и экскаваторов ЭКГ–8УС в карьере расчет комбинированного карьерного транспорта. Для автомобильного транспорта на основании сравнения выбирается самосвал БЕЛаз–7512 и производится его тяговый и эксплуатационный расчет. Вывозку горной массы из карьера производим тяговыми агрегатами ПЭ–2м с девятью думпкарами 2ВС–105 также в разделе производится выбор комплекса оборудования карьерного водоотлива Сарбайского карьера.
В разделе «Электроснабжение горного предприятия» производится расчет освещения карьера в ночное время. Также производится расчет электрических нагрузок и по полученным данным выбирается силовые трансформаторы. Кроме того рассчитали и выбрали воздушные ЛЭП кабельные линии. На основании токов короткого замыкания произведен выбор защитной аппаратуры ГПП.
Раздел «Ремонт технологического оборудования» заключает в себе расчет трудоемкости количества и сил на ремонт основного технологического оборудования. Расчет выполнен с использованием программы ЭВМ.
Специальная часть проекта рассматривает проектирование установки для наплавки гребней колесных пар думпкаров. Описывается установка её основные составляющие произведен расчет привода наплавляемого объекта расчет режима сварки под флюсом и выбор сварочного оборудования выбор соединительных муфт расчет карданного вала.
В разделе «Охрана труда и техника безопасности» рассматриваются вопросы организации работ по охране труда обеспечения безопасности производства общие санитарные правила ответственность за нарушение правил безопасности пожарная профилактика и правила техники безопасности при эксплуатации установки по наплавке колесных пар думпкаров.
Раздел «Промышленная экология» посвящен вопросам связанным с охраной окружающей среды в условиях функционирования карьера.
Диплом также содержит экономическое обоснование спроектированной установки по наплавке гребней колесных пар думпкаров.
Ржевский В.В. Открытые горные работы:учебник для вузовВ.В.Ржевский ч.1 – М.: Недра 1985 – 509 с.
Томаков П. И. Технология механизация и организация открытых горных работ:учебник для вузовП.И.Томаков И.К. Наумов. — 2-е изд. перераб. н доп.— M.: Недра 1986 – 312 с.
Мельников Н.В. Краткий справочник по открытым горным работам: справочное пособиеН.В.Мельников. – М.: Недра 1982 – 414 с.
Хохряков B.C. Проектирование карьеров:учебник для вуховВ.С.Хохряков. – М.: Недра 1980 – 335 с.
Попов В.М. Водоотливные установки:справочное пособиеВ.М.Попов. – М.; «Недра» 1990 - 304 с
Справочник по электрическим машинам Под общ. ред. И.А. Копылова Б.К. Клокова. Т.1 - М.: Энергоатомиздат 1989 – 456 с.
Справочник по электрическим машинам Под общ. ред. И.А. Копылова Б.К. Клокова. Т.2 - М.: Энергоатомиздат 1989 – 688 с.
Самохин Ф.И. Электрооборудование и электроснабжение открытых горных работ:учебное пособиеФ.И. Самохин А.М. Маврицкий - М.: Недра1979 – 399с.
Справочник по электроснабжению и электрооборудованию: в 2т.Под общ. ред. Федорова А.А.Т. 1.Электроснабжение. – М.: Энергоатомиздат1978 – 540 с.
Справочник по электроснабжению и электрооборудованию: в 2т.Под общ. ред. Федорова А.А.Т. 2.Электрооборудование. – М.: Энергоатомиздат1978 - 592 с.
Чулков Н.Н. Электрификация карьеров в задачах и примерах. – М.: Недра 1972 – 256 с.
Справочник энергетика карьера Под ред. В.А. Голубева – М.: Недра 1984 – 420 с.
Временное положение технического обслуживания и ремонта механического оборудования предприятия системы министерства черной металлургии СССР – Харьков 1983.
Замышляев В.Ф. Эксплуатация и ремонт карьерного оборудования:учебник В.Ф. Замышляев В.И. Русихин Е.Е. Шешко - М.: Недра 1991 - 285 с.
Справочник механика открытых работ. Экскавационно-транспортные машины циклического действияПод ред. М.И. Щадова Р.Ю. Подэрни. – М.:Недра1989. – 374 с.
Зенков Р.Л. Машины непрерывного транспорта:учебник для вузов.Р.Л.Зенков И.И. Ивашкин П.Н. Колобов - М.: Машиностроение 1980 – 430 с.
Кузьмин А.В. Справочник по расчетам механизмов подъемно – транспортных машин:справочное пособие А.В. Кузьмин Ф.Л. Марон – Минск.: Высшая школа 1983 – 350 с.
Конвейеры: справочникпод ред. Р.А. Волкова Л.: Машиностроение 1984 – 367 с.
Спиваковский А.О. Транспортирующие машины:учебное пособиеА.О. Спиваковский В.К. Дъячков - М.: Машиностроение 1983 – 487 с.
Иванченко Ф.К. Конструкция и расчет подъемно – транспортных машин: учебник для вузов Ф.К. Иванченко – Киев.: «Вища школа» 1983 – 351 с.
Редукторы муфты тормоза. Каталог оборудования. - Л.: ВНИИ механобр. 1983 – 215 с.
Денисенко Г.Ф. Охрана труда: учебное пособие инженерных специальностей вузовГ.Ф. Денисенко. – М.: Высшая школа 1985. – 320 с.
Правила безопасности при разработке месторождений открытым способом 2002.
Правила эксплуатации электроустановок. М. 2001
ГОСТ 12.3.003-86 Система стандартов безопасности труда. Работы электросварочные. Требования безопасности – Введ. 1988–01–01. – М.: Изд–во стандартов 1988. – 10 с.
Правила техники безопасности при эксплуатации электроустановок. РД 34 РК.03.202-04
Правила пожарной безопасности при производстве строительно-монтажных и огневых работ. ППБС-01-94 Алматы 1994 г.
Правила пожарной безопасности в Республике Казахстан. Основные требования» от 20.03.2006г №4126
Экология и охрана природы при открытых горных работахПод редакцией П.И. Томакова – Москва Издательство Московского Государсвтенного Горного Университета 2000 – 417 с.
Рахимов З.Р. Методические указания по выполнению курсовой работы по дисциплине «Организация планирование и управление предприятием» и экономической части дипломного проекта для студентов специальности 140240 – «Горные машины и оборудование»З.Р.Рахимов. – Рудный: Изд-во РИИ 2002.
Привод вращения колеса.dwg

Редуктор цилиндрический
- передаточное число
Технические требования
* Размер для справок.
Неуказанные предельные отклонения размеров :14
Рекомендуемые чертежи
- 04.06.2022