Стреловой кран гп 10 т.



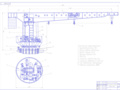
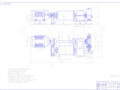
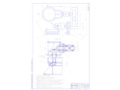
- Добавлен: 25.10.2022
- Размер: 828 KB
- Закачек: 1
Описание
Состав проекта
![]() |
![]() ![]() ![]() ![]() |
![]() ![]() |
![]() ![]() ![]() ![]() |
![]() ![]() ![]() |
![]() ![]() |
![]() ![]() |
![]() ![]() ![]() ![]() |
Дополнительная информация
rrsrrrerr-ryirrssrr-2.dwg

Грузоподъемность 10т.
Скорость подъема груза 8ммин
Мощность двигателя 13кВт
Передаточное число редуктора 32
Диаметр барабана 300мм
*Размеры для справок.
rrssrr-rrsrrr-rrerr-2.dwg

Грузоподъемность 10т
Режим работы 3М(легкий)
Скорость подъема 8ммин
Скорость поворота 07 обмин
Рабочее напряжение 380В
Кран на колонне с тележко
КП ГПМ 12.01.00.000.
rrssrresrrsrrs-rrryiresryer.doc
Федеральное государственное бюджетное образовательное
учреждение высшего профессионального образования
«Тульский государственный университет»
Кафедра Подъемно-транспортные машины и оборудование
ГРУЗОПОДЪЕМНЫЕ МАШИНЫ
РАСЧЕТ МЕХАНИЗМА ПОДЪЕМА3
1 Определение кратности полиспаста3
2 Определение усилия в канате набегающем на барабан3
4 Определение требуемого диаметра блоков и барабана4
5 Выбор крюковой подвески5
6 Определение размеров барабана5
8 Определение передаточного числа привода7
10 Выбор муфты быстроходного вала8
11 Выбор муфты тихоходного вала8
12 Определение пусковых характеристик механизма9
13 Расчет электромагнитного колодочного тормоза10
14 Определение тормозных характеристик механизма11
15 Проверка двигателя на нагрев12
РАСЧЕТ МЕХАНИЗМА ПОВОРОТА15
1 Схема настенного стрелового консольно-поворотного крана15
2 Определение размеров крана15
3 Определение масс крана16
4 Определение реакций в опорах16
5 Определение сопротивления вращению от сил трения в опорах16
6 Определение сопротивления от ветровой нагрузки17
7 Определение сопротивления от уклона колонны18
8 Определение передаточного числа привода19
9 Выбор цилиндрического и конического редукторов. Выбор открытой зубчатой передачи.19
10. Определение крутящих моментов и частот вращения на валах привода20
11 Определение фактической частоты вращения стрелы крана21
12 Выбор муфт быстроходного и промежуточного валов21
13 Проверка пусковых характеристик механизма21
14 Определение тормозных моментов и расчёт колодочного тормоза22
15 Проверка тормозных характеристик23
СПИСОК ИСПОЛЬЗОВАННЫХ ИСТОЧНИКОВ24
РАСЧЕТ МЕХАНИЗМА ПОДЪЕМА
В качестве исходных данных для расчета механизма подъема используем следующие данные:
- тип крана – стреловой на колонне;
- грузоподъемность Q = 10 т;
- скорость подъема груза Vпод = 8 ммин = 013 мс;
- высота подъема Н = 35 м;
- режим работы крана 3М (легкий);
- продолжительность включения механизма подъема ПВ = 25%.
1 Определение кратности полиспаста
Кратность полиспаста механизма подъема груза выбираем в зависимости от грузоподъемности механизма. Принимаем Uп = 4 для простого полиспаста в соответствии с рекомендациями [1 c. 55 табл. 2.2].
Рис. 1 Схема простого полиспаста
2 Определение усилия в канате набегающем на барабан
где Q – номинальная грузоподъемность крана кг;
z – число простых полиспастов в системе;
Un – кратность полиспаста;
– общий КПД полиспаста и обводных блоков ().
где бл – КПД одного блока принимаем бл = 098 для подшипников качения.
где – количество обводных блоков (см. рис. 1).
Выбираем канат по расчетному разрывному усилию в канате:
где k – коэффициент запаса прочности принимаемый в зависимости от назначения
и режима работы крана принимаем k = 5 согласно [1 c. 55 табл. 2.3].
В соответствии с рекомендациями [1 c. 277 табл. III.1.1] принимаем канат двойной свивки типа ЛК-Р 6×19 (1 + 6 + 66) + 1о.с. диаметром d = 180 мм имеющий при маркировочной группе проволок 1764 МПа с разрывным усилием F = 137000 H.
Обозначение каната: Канат 15 – Г – I – Н – 1960 ГОСТ 2688 – 80
– название изделия: ”канат”;
– диаметр наружного каната: d = 15 мм;
– назначение каната: Г – грузовой;
– марка проволок материала: I – первая;
– способ свивки: Н – нераскручивающийся;
– маркировочная группа прочности проволок: 1960 МПа;
Проверка фактического коэффициента запаса прочности каната:
4 Определение требуемого диаметра блоков и барабана
Допускаемый диаметр блока и барабана по средней линии навитого стального каната определяется по формуле:
где d – диаметр стального каната мм;
e – коэффициент зависящий от типа крана типа привода и режима работы
механизма принимаем e = 16 согласно [1 c. 59 табл. 2.7].
принимаем Dб = 300 мм.
5 Выбор крюковой подвески
Из атласа «Грузоподъемные машины» и в соответствии с принятой схемой (см. рис. 1) принимаем подвеску крановую с двумя блоками.
D = 500 мм; dк = 14 17 мм; режим работы легкий; грузоподъемность 10 т;
6 Определение размеров барабана
Длина каната навиваемого на барабан с одного полиспаста определяется по формуле:
где H – высота подъёма груза м;
Dб – диаметр барабана м;
z1 – число запасных (неиспользуемых) витков на барабане до места крепления:
z1 = 15 2 согласно [1 c. 60];
z 2 – число витков каната находящихся под зажимным устройством на барабане
z2 = 3 4 согласно [1 c. 60].
Так как полиспаст в системе сдвоенный и z = 2 то общая длина всего каната будет вдвое больше.
Рабочая длина барабана для навивки каната с одного полиспаста определяется по формуле:
где Lк – длина каната навиваемого на барабан м;
t – шаг витка (см. рис. 2) принимается в зависимости от диаметра каната: при
d = 150 мм тогда t = 18 мм = 0018 м в соответствии с рекомендациями
[1 c. 60 табл. 2.8];
Рис. 2 Профиль канавок на барабане
m – число слоев навивки (для нарезного барабана m = 1);
d – диаметр каната м;
Dб – диаметр барабана по средней линии навитого каната м;
φ – коэффициент неплотности навивки: φ = 1 для нарезных барабанов
Определяем минимальную толщину стенок литого чугунного барабана по формуле:
где Dдна – диаметр дна барабана м.
Произведем проверку прочности стенки барабана т.е. определим напряжения сжатия стенки барабана по формуле:
где Fб – усилие в канате H;
Принимаем для среднего режима работы механизма материал для барабана чугун марки СЧ 15 с допускаемым напряжением [сж ] = 130 МПа.
Статическая мощность двигателя механизма подъёма определяется по формуле:
где Q – номинальная грузоподъемность крана т;
g = 981 мс2 – ускорение свободного падения;
Vпод – скорость подъема груза мс;
– КПД механизма в целом (от крюка до двигателя) принимаем согласно [1 c. 23 табл. 1.18] для подшипников качения = 085.
Номинальную мощность двигателя необходимо принимать равной или несколько меньшей статической мощности на 30 35%.
Двигатель выбираем с учетом ПВ в % и мощности.
Принимаем электродвигатель MTF 311-6-13кВт согласно [6 с. 35 табл. 2]:
– мощность Pэл = 13 кВт;
– частота вращения nэл = 935 мин-1;
– момент инерции ротора Ip = 0225 кг · м2;
– максимальный крутящий момент 320 Н · м
8 Определение передаточного числа привода
Частота вращения барабана определяется по формуле:
где Vпод – скорость подъема груза мс;
Dб – диаметр барабана м.
Требуемое передаточное число привода определяем по формуле:
Расчетную мощность редуктора находим по формуле:
Где Pc – статическая мощность двигателя
- коэффициент зависящий от типа механизма – для механизма подъема – 1.
Выбираем из каталога редуктор Ц2 - 300 с передаточным числом – 3242 межосевое расстояние 300 мм мощность на быстроходном валу Р = 18 кВт n = 1000
10 Выбор муфты быстроходного вала
Момент статических сопротивлений на валу двигателя с общим КПД всего механизма согласно [1 c. 23]:
где z – число простых полиспастов в системе;
Uр – фактическое передаточное число привода;
– КПД механизма в целом = 085.
Расчетный момент для выбора соединительной муфты с учетом ответственности и режима работы механизма определяется по формуле:
где k1 – коэффициент учитывающий степень ответственности механизма;
k2 – коэффициент учитывающий режим работы механизма.
Тогда согласно [1 c. 42 табл. 1.35] для механизмов подъёма: k1 = 13; k2 = 11 легкий режим.
Принимаем втулочно-пальцевую муфту по ГОСТ 24246 – 80 согласно [3 с. 142 табл. 6.1]:
– диаметр шкива Dшкива=200 мм;
– момент инерции Jм= 024 кгм2.
– номинальный тормозной момент 250 Н · м
11 Выбор муфты тихоходного вала
Момент статических сопротивлений на валу барабана с КПД барабана согласно [1 c. 23]:
где б – КПД барабана (б = 095 096).
Расчетный момент для выбора соединительной муфты с учетом ответственности и режима работы механизма определяется по формуле аналогично (п. 1.10):
Из каталога (стр. 333) принимаем втулочно-пальцевую муфту №5:
– крутящий момент Tмуф. =8000 Н·м;
– допускаемая частота вращения муфты nmax = 2800 мин-1.
12 Определение пусковых характеристик механизма
Фактическая частота вращения барабана определяется по формуле:
где nэл. – частота вращения электродвигателя мин-1;
Uр – фактическое передаточное число привода.
Фактическая скорость подъёма груза определяется по формуле:
где Dб – диаметр барабана м;
Un – кратность полиспаста.
Время пуска при подъёме груза определяется по формуле:
где – коэффициент учитывающий влияние вращающихся масс привода
механизма за исключением ротора двигателя и тормозного шкива
установленного на быстроходном валу: = 11 125;
I – момент инерции ротора двигателя и тормозного шкива установленного
на быстроходном валу:
Ip – момент инерции ротора двигателя кг · м2;
Iм – момент инерции муфты кг · м2;
Tср.п. – средний пусковой момент двигателя определяем по формуле:
Tном. – номинальный момент двигателя определяем по формуле:
Максимальная кратность пускового момента двигателя:
Минимальная кратность пускового момента двигателяопределяется по каталогу или приближенно = 11 14
Tс – момент статических сопротивлений на валу двигателя (см. п. 1.10) Н·м;
Q – номинальная грузоподъемность крана кг;
V – фактическая скорость подъёма груза мс;
Ускорение при пуске определяется по формуле:
Таблица 1 – Проверка полученных значений пусковых характеристик на
соответствие рекомендуемым значениям для механизма подъёма
Допускаемое значение
±10% от заданной 013 мс
для массовых грузов
с некоторыми допущениями
13 Расчет электромагнитного колодочного тормоза
Момент статического сопротивления на валу двигателя при торможении механизма определяется по формуле:
– КПД механизма в целом = 085;
Необходимый по нормам Ростехнадзора момент развиваемый тормозом определяется по формуле:
где KТ – коэффициент запаса торможения принимаем KТ = 15 – для легкого режима работы механизма.
Выбираем тормоз (стр. 340) ТКГ-200 с Тт=250 Н*м
14 Определение тормозных характеристик механизма
Время торможения при опускании груза определяется по формуле:
где TТ – необходимый момент развиваемый тормозом (см. п. 1.13) Н·м;
TсТ – момент статического сопротивления на валу двигателя при торможении
механизма (см. п. 1.13) Н·м.
Наибольшее допускаемое время торможения в соответствии с рекомендациями [4 с. 397]: tTmax = 1 2 с.
Замедление при торможении определяется по формуле:
Таблица 2 – Проверка полученных значений тормозных характеристик на
Замедление при торможении
15 Проверка двигателя на нагрев
Во избежание перегрева двигателя необходимо чтобы развиваемая им среднеквадратическая мощность удовлетворяла условию:
Средняя квадратичная мощность электродвигателя определяется по формуле:
где Tср – средний квадратичный момент преодолеваемый электродвигателем Н·м;
nэл. – частота вращения электродвигателя мин-1.
где tп – общее время пуска при подъёме и опускании груза с;
tу – время установившегося движения с;
t – общее время работы электродвигателя с;
Tср.п. – средний пусковой момент двигателя (см. п. 1.12) Н·м;
Tс – момент статических сопротивлений на валу двигателя при подъёме Н·м;
TсТ – момент статических сопротивлений на валу двигателя при торможении
механизма т.е. при опускании груза (см. п. 1.13) Н·м.
В качестве исходных данных для расчета используем график загрузки механизма в соответствии с рекомендациями [1 с. 16 рис. 1.1]. Соответственно для легкого режима работы механизма подъёма график будет иметь следующий вид (см. рис. 3):
Рис. 3 Усредненный график загрузки механизма подъёма
козлового крана (для легкого режима режима работы)
Согласно графику за время цикла (подъём и опускание груза) механизм будет работать с номинальным грузом Q = 10000 кг – 4 раза с грузом 01·Q = 1000 кг – 3 раза с грузом 005·Q = 500 кг – 3 раза.
Сведем результаты расчетов с различными грузами в таблицу 3.
Таблица 3 – Результаты расчетов
Результаты расчета при Q кг
(см. [1 с.24 рис.1.2])
Время пуска при подъёме
Момент при опускании груза
Время пуска при опускании (по формуле из п.1.12
Общее время пуска при подъёме и опускании груза определяется по формуле:
где ni – число подъёмов i-го груза.
Время установившегося движения определяется по формуле:
где Hср – средняя высота подъёма груза: Hср = 08·H м;
V – фактическая скорость подъёма груза мс.
Определим общее время работы средний квадратичный момент и среднюю квадратичную мощность электродвигателя:
Pср = 481 кВт Pном = 13 кВт – следовательно условие выполняется.
РАСЧЕТ МЕХАНИЗМА ПОВОРОТА
В качестве исходных данных для расчета механизма поворота используем следующие данные:
- тип крана – настенный стреловой консольно-поворотный кран;
- частота вращения стрелы ппов. = 07 обмин;
- вылет стрелы R = 104 м;
- высота подъёма груза Н = 35 м;
- возможное отклонение оси колонны от вертикали α = 1°;
- режим работы крана 2К (легкий);
- режим работы механизма 3М (легкий);
- продолжительность включения механизма поворота ПВ = 25%.
1 Схема настенного стрелового консольно-поворотного крана
Рис. 4. Расчётная схема крана с поворотной колонной
где Qg –масса груза т;
mc– масса вращающейся части крана т;
h – расстояние между верхней и нижней опорами м;
FC – реакции в опорах Н.
2 Определение размеров крана
Расстояние от центра тяжести поворотной части крана до оси его вращения:
Расстояние между верхней и нижней опорами выбираем по крану-аналогу:
3 Определение масс крана
По ГОСТу 19811-90 выбираем кран аналог и принимаем его массу:
Массу вращающейся части крана определяем по формуле:
коэффициент использования крана по грузоподъемности
4 Определение реакций в опорах
По справочнику Анурьева по полученной нагрузки выбираем упорный однорядный шарикоподшипник 8217 ГОСТ 7872-89 с допускаемой осевой нагрузкой Соа = 2344 кН внутренним диаметром: d = 85 мм и наружным диаметром: D = 125 мм.
Конструкция нижней опоры А в данном настенном стреловом кране подшипникового типа.
Для опор А и С выбираем упорный однорядный шарикоподшипник 8310 ГОСТ 7872-89 с допускаемой осевой нагрузкой Соа = 146 кН внутренним диаметром: d = 50 мм и наружным диаметром: D = 95 мм.
5 Определение сопротивления вращению от сил трения в опорах
Моменты сопротивления вращению:
где ТA; ТB; ТC – моменты трения в соответствующих опорах.
Для подшипниковых опор:
где f = 0015 – коэффициент трения подшипниках опор; FC – реакции в опорах Н; dB и dC – средние диаметры опор определяются как половина суммы внутреннего и наружного диаметров подшипников.
Суммарный момент от трения в опорах:
6 Определение сопротивления от ветровой нагрузки
Ветровая нагрузка определяется по формуле:
Где коэффициент сплошности для ферм ;
Р – распределенная ветровая нагрузка Па;
А – расчетная площадь элемента конструкции;
- ветровая нагрузка для крана;
Где q – динамическое давление ветра для кранов общего назначения при ;
k – коэффициент учитывающий высоту конструкции при ;
c – коэффициент аэродинамической силы зависит от типа конструкции для плоской фермы для груза ;
n – коэффициент перегрузки; ;
- ветровая нагрузка для груза;
Площадь конструкции крана определяется по площади контуров элементов крана ( габаритная площадь)
Площадь груза выбираем из справочника. Для грузоподъемности 10 т. площадь груза составляет:
Ветровая нагрузка на стрелу:
Ветровая нагрузка на противовесную сторону:
Момент от ветровой нагрузки на кран:
Момент от ветра на груз:
Суммарный момент от ветровой нагрузки:
7 Определение сопротивления от уклона колонны
Момент сопротивления вращению крана от уклона колонны
где α — возможный угол наклона колонны α = 1°;
mпов— масса поворотной части крана ;
lпов — центр тяжести поворотной части крана
Суммарный момент сопротивлений вращению крана:
где Fтр. – сопротивление от трения в опорах;
Fукл. – сопротивление от уклона колонны;
Fв – сопротивление от ветровой нагрузки;
Статическая мощность двигателя механизма поворота определяется по формуле:
где Тпов. – суммарный момент сопротивлений вращению крана Нм;
ппов. – частота вращения стрелы крана обмин;
– КПД механизма поворота крана
Номинальную мощность двигателя механизма поворота необходимо принимать равной или несколько большей статической мощности. Двигатель выбираем с учетом ПВ в % а также с учетом частоты вращения ротора.
Принимаем электродвигатель MTF111-6 согласно [с.313 табл.3.5]:
– мощность Pэл = 41 кВт;
– частота вращения nэл = 870 мин-1;
– момент инерции ротора Ip = 0048 кг · м2;
Требуемое передаточное число одного привода определяем по формуле:
где пэл и ппов — частота вращения электродвигателя и стрелы крана при повороте.
9 Выбор цилиндрического и конического редукторов. Выбор открытой зубчатой передачи.
Расчетная мощность одного редуктора определяется по формуле:
где kр – коэффициент учитывающий условие работы редуктора принимаем
kр = 15 – для легкого режима работы [1 с. 40 табл. 1.34].
При выборе редуктора учитываем передаточное число расчетную мощность режим работы частоту вращения быстроходного вала (равно частоте вращения электродвигателя).
Из каталога [с.318 табл. III.4.2] выбираем цилиндрический редуктор с меньшим расчетным передаточным числом из-за наличия открытой зубчатой передачи и конического редуктора:
– передаточное число Uрред.= 5094;
– частота вращения быстроходного вала nр = 1000 мин-1;
– мощность на быстроходном валу 82 кВт ;
Определение передаточного числа конического редуктора по формуле:
где z1 и z2 – число зубьев шестерни и колеса.
Определение передаточного числа открытой зубчатой передачи:
10. Определение крутящих моментов и частот вращения на валах привода
Определяем крутящие моменты начиная с выходного открытой зубчатой передачи в соответствии с рекомендациями [3 с.13]:
где Uо.з. – передаточное число открытой зубчатой передачи привода;
о.з. – КПД в открытой зубчатой передаче привода
Тогда согласно о.з. = 096.
Момент на валу конического редуктора (цилиндрического редуктора):
где . – передаточное число открытой зубчатой передачи привода;
. – КПД конического редуктора.
Тогда согласно [3 с. 11 табл. 1.2]:
Момент на валу электродвигателя (цилиндрического редуктора):
. – передаточное цилиндрического редуктора;
. – КПД цилиндрического редуктора.
Тогда согласно [с. 23 табл. 1.18]
Таким же образом находим частоты вращения валов:
11 Определение фактической частоты вращения стрелы крана
12 Выбор муфт быстроходного и промежуточного валов
Номинальный момент представляемой муфты:
Выбираем муфту с тормозным шкивом с диаметром отверстия для вала 200мм.
Для промежуточного вала выбираем муфту по заранее вычисленному моменту на промежуточном валу:
Выбираем зубчатую муфту с диаметром отверстия для вала 50мм.
13 Проверка пусковых характеристик механизма
Требуемая мощность двигателя поворота при пуске:
где nэл. – частота вращения электродвигателя nэл = 870 мин-1;
Тпуск – момент сопротивления на валу двигателя при пуске.
где U – фактическое передаточное число привода U = 1243;
– КПД механизма поворота крана = 05;
Тин – момент сил инерции при пуске.
механизма за исключением ротора двигателя и муфты быстроходного вала
I – момент инерции ротора двигателя и тормозного шкива на быстроходном валу:
Iш – момент инерции тормозного шкива на быстроходном валу:
Iвр – момент инерции поворотной части крана:
tп – время пуска (торможения) механизма поворота принимаем согласно [1 с. 28 табл. 1.21] в зависимости от вылета стрелы: tп = 8 с.
Тогда момент сопротивления на валу двигателя при пуске:
Номинальная мощность выбранного двигателя должна удовлетворять условию:
условие выполняется – двигатель выбран верно.
14 Определение тормозных моментов и расчёт колодочного тормоза
Момент сопротивления на валу тормоза:
где – момент сил инерции при торможении механизма поворота:
По тормозному моменту выбираем тормоз (по большему моменту) ТКТ-200100 с диаметром тормозного шкива 200мм итормозным моментом 40 и регулируем его до 198
15 Проверка тормозных характеристик
Проверка времени пуска (торможения) по допускаемому углу поворота стрелы
где – наибольший допускаемый угол поворота поворотной части крана при пуске (торможении). Согласно [1 с.31 табл.1.24] для лёгкого режима работы тогда
Эта величина соответствует требованиям [1 с.28 табл.1.21] так как 77 с > 3 c
и фактический угол поворота поворотной части крана при пуске (торможении) меньше чем наибольший допускаемый: – верно.
16 Проверка двигателя на нагрев.
Так как выбранный двигатель по мощности превосходит номинальную мощность проверка на нагрев не требуется.
СПИСОК ИСПОЛЬЗОВАННЫХ ИСТОЧНИКОВ
А.В. Кузьмин Ф.Л. Марон Справочник по расчетам механизмов подъёмно-транспортных машин. Изд. 2-е. перераб. – Минск: Высш. шк.1983.
Курсовое проектирование грузоподъёмных машин: Учеб. Пособие для вузов под ред. С.А. Казака. – М.: Высш. шк.1989. – 319 с.: ил.
Курсовое проектирование деталей машин: учеб. пособие В.Д. Соловьёв В.И. Фатеев. – Тула: Изд-во ТулГУ 2007.- 324 с.
Справочник по кранам Т2 Под ред. М.М.Гохберга. Л.: Машиностроение 1988. 559 с.
Вайснон А.А. Атлас конструкций. Подъёмно-транспортные машины строительной промышленности. - 2-е изд. перераб. – М.: Машиностроение 1976.
Подъёмно-транспортные машины. Атлас конструкций. Под. ред. М.П. Александрова Д.Н. Решетова. - 2-е изд. перераб. и доп. – М.: Машиностроение 1987. – 122 с.: ил.
Грузоподъёмные машины: Атлас конструкций: учеб. пособие для вузов В. А. Голутвин В. Д. Соловьёв Ю. Е. Семёнов; под ред. Г.Г.Дубенского; ТулГУ.— Тула: Изд-во ТулГУ 2012 . — 123 с.
rrsrrrerr-ryirrrsrsr-2.dwg

Частота вращения стрелы 0
Общее передаточное число 1243
Передаточное число открытой зубчатой передачи 15
Передаточное число конического редуктора 1
Передачтоное число цилиндрического редуктора 50
Момент сопротивлений на валу тормоза 19
Мощность двигателя 4
Частота вращения быстроходного вала 870 обмин