Сборка цилиндрического редуктора




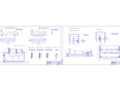
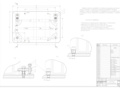
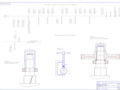
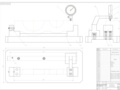
- Добавлен: 25.10.2022
- Размер: 2 MB
- Закачек: 0
Описание
Состав проекта
![]() |
![]() |
![]() ![]() ![]() ![]() |
![]() ![]() ![]() ![]() |
![]() ![]() ![]() ![]() |
![]() ![]() ![]() ![]() |
![]() ![]() ![]() ![]() |
![]() ![]() |
![]() ![]() ![]() |
![]() ![]() ![]() |
![]() ![]() |
![]() ![]() |
![]() ![]() ![]() |
![]() ![]() |
![]() ![]() |
![]() ![]() |
Дополнительная информация
1 - Маршрут сборки.dwg

МГТУ им. Н.Э.Баумана
Запрессовка подшипника на вал
мехнаического пресса
Установака дистанционного кольца и
плоскости соприкосновения корпуса и крышки
покрыть тонким слоем герметика
Прокрутить редуктор вручную
Контроль пятна контакта
Сборка промежуточного вала редуктора
Схема сборки цилиндрического двуступенчатого редуктора
3,4 - Операционная технология.dwg

МГТУ им. Н.Э.Баумана
Операция 070 . Вертикальносверлильная
Оборудование: станок вертикальносверлильный
Операция 15. Сверлильно-фрезерно-расточная с ЧПУ
Оборудование: Станок сверлильно-фрезерно-расточной с ЧПУ 630
Инструмент: Торцовая фреза
23-0156 ГОСТ 17026-71
Операция 10. Сверлильно-фрезерно-расточная с ЧПУ
Оборудование: станок сверлильно-фрезерно-расточной с ЧПУ 630
Инструмент: торцовая фреза 223-0156 ГОСТ 17026
Операция 035. Сборочная
. Сверлильно-фрезерно
Заведение оправки с инструментом
в корпус редуктора и регулироваине резцов
Станок: Станок сверлильно-фрезерно
Растачивание черновое
Инструмент: Сверло спиральное
01-3212 ГОСТ 12121-77
Инструмент: Зенкер цельный
23-0511 ГОСТ 12489-71
Инструмент: Развертка цельная
63-3429 ГОСТ 1672-80
Инструмент: Резец упорный
Инструмент: Молоток слесарный
5 - Станочное приспособление.dwg

МГТУ им. Н.Э.Баумана
Палец установочный 7030-0909
Палец установочный 7030-0929
Прихват передвижной 7011-0521
Обработка детали производится на сверлильно фрезерно-расточном
станке. Установка и закрепление заготовки производится во время
обработки. Корпус устанавливается последовательно на цилиндрический 7
и срезанный 8 пальцы. Закрепление производится прихватами 9 посредством
Технические требования:
Отклонение от параллельности поверхности Г относительно
поверхности Д не более 0
Отклонение от параллельности плоскости
через оси пальцев 7 и 8 относительно плоскости
проходящей через оси крепежных отверстий не более 0
2 - Маршрут обработки.dwg

Технология машиностроения
Обработка по размерам в квадратных
скобках проводится совместно с
Заготовительная. Литьё в ПФ
Операция 010. Сверлильно-фрезерно-расточная
Неуказанные предельные отклонения размеров
Операция 020. Сверлильно-фрезерно-расточная с ЧПУ
Операция 035. Сборочная
Операция 030. Слесарная
Операция 045. Сверлильно-фрезерно-расточная
Операция 015. Сверлильно-фрезерно-расточная
Операция 040. Сборочная
Операция 015. Контрольная
6 - Контрольно-измерительное приспособление.dwg

Технология машиностроения
Винт М6 х 10 ГОСТ 1409-80
Винт М8 х 40 ГОСТ 8878-93
Винт М8 х 45 ГОСТ 11738-84
Винт М10 х 30 ГОСТ 11738-84
Штифт 8 x 30 ГОСТ 3128-70
Маршрут Сборки.doc
Код наименование операции
Обозначение документа
Код наименование оборудования
Наименование детали сб. единицы или материала
Установить корпус редуктора 7 в сборе на место сборки
Установить тихоходный вал 2 в сборе в гнезда подшипников подъемником
Установить тихоходный вал 3 в сборе в гнезда подшипников подъемником
ГОСТ 3.1118-82 Форма 2б
Установить промежуточный вал 4 в сборе в гнезда подшипников подъемником
Установить крышку подшипника 11 в сборе в отверстие редуктора
Установить крышку подшипника 12 в сборе в отверстие редуктора
Установить крышку подшипника 9 в отверстие редуктора
Установить крышку подшипника 10 в отверстие редуктора
Плоскости соприкосновения редуктора и крышки редуктора покрыть тонким слоем герметика
Герметик УТ-34 ГОСТ 24285-80
Установить крышку редуктора 8 на редуктор
Запрессовать конический штифт 45 в отверстия крышки и корпуса редуктора
Надеть на винты 22 шайбы 37
Затянуть винты с шайбами до упора в редуктор 7
Шуруповёрт сетевой МЭСШ-0.55
Надеть на болты 21 шайбы 37
Прикрепить болтами с шайбами крышку в сборе 12 к редуктору 7
Надеть на болты 17 шайбы 36
Прикрепить болтами с шайбами крышку в сборе 11 к редуктору 7
Надеть на болты 19 шайбы 36
Прикрепить болтами с шайбами крышку 9 к редуктору 7
Завернуть конический винт 21 до упора в отверстие редуктора 7
Контроль пятна контакта
Установить крышку люка 4 в сборе на крышку редуктора 15
Закрутить до упора болты 18 в крышку люка 1 и крышку редуктора 7
Ручная слесарная отвертка
Прокрутить редуктор вручную за выходной вал
Обкатать редуктор в сборе
Маршрут Обработки.doc
Крышка подшипниковой опоры
Код наименование операции
Обозначение документа
Код наименование оборудования
Заготовительная (литьё в песчаную форму)
Сверлильно-фрезерно-расточная с ЧПУ
Сверлильно-фрезерно-расточной станок с ЧПУ модель 630VH
Фрезеровать плоскость выдержав размер 71+05
Торцовая фреза 2223-0156 ГОСТ 17026-71
ГОСТ 3.1118-82 Форма 1б
Фрезеровать плоскость выдержав размер 70+05
Торцовая фреза 2223-0156 ГОСТ 17026-71 пальцы установочные 7030-0905 ГОСТ 12200-66
Контрольно-измерительное приспособление
Контролировать плоскостность поверхности стыка крышки и корпуса
Сверлить 3 отверстия 15+012
Сверлить 2 отверстия 115+01
Сверла спиральные 2301-3212 2301-3244 ГОСТ 12121-77
Зачистить кромки отверстий 15+012 115+01
Надеть на винты 23 шайбы 37
Затянуть винты с шайбами до упора в редуктор 7
Шуруповёрт сетевой МЭСШ-0.55
Сверлить по 2 отверстиям в крышке отверстия 115+01 в корпусе выдержав размер 30+025
Сверло спиральное 2301-3212 ГОСТ 12121-77
Зенкеровать совместно с корпусом 2 отверстия 12+001 выдержав размер 100+025
Зенкер цельный 2323-0511 ГОСТ 12489-71
Развернуть совместно с корпусом 2 отверстия 12+005 выдержав размер 100+025
Развёртка машинная цельная 2363-3429 ГОСТ 1672-80
Запрессовать штифты конические поз 46
Молоток слесарный приспособление станочное
Запрессовать конический штифт 45 в отверстия крышки и корпуса редуктора
Надеть на винты 20 22 шайбы 37
Завести оправку с резцами в отверстие 115
Расточить отверстия 117+005147+030
Перенастроить резцы и расточить отдельно отверстия 119+005149+030
Перенастроить резцы и расточить отдельно отверстия 120+0035150+004
Расточить отверстия 77+00597+020
Перенастроить резцы и расточить отдельно отверстия 79+00599+010
Перенастроить резцы и расточить отдельно отверстия 80+003100+0035
Оправка расточная резцы упорные приспособление станочное
Записка.docx
Кафедра «Технология машиностроения»
РАСЧЕТНО-ПОЯСНИТЕЛЬНАЯ ЗАПИСКА
К КУРСОВОМУ ПРОЕКТУ
ПО ТЕХНОЛОГИИ МАШИНОСТРОЕНИЯ
Студент: Думчев Е.К. Дата: группа РК 4-101
Консультант: Большагин Н.П. Дата:
Проектирование технологического процесса сборки узла4
1.Назначение узла в машине и краткое описание его конструкции4
2.Анализ технических требований на сборку с разработкой схем проверки по заданным требованиям4
4.Технологический анализ конструкции узла с расчетом показателей технологичности9
5.Разработка технологической схемы сборки и пояснения к ней9
6.Разработка технологического процесса сборки с заполнением карт техническим нормированием времени по элементам и определением суммарной трудоемкости сборки узла11
Проектирование технологического процесса обработки14
1.Назначение детали в узле доработка чертежа по действующим ГОСТам анализ технических требований выявление технологических задач возникающих при изготовлении и разработка схем проверки по заданным требованиям14
2.Тип производства15
3.Отработка конструкции на технологичность для заданного типа производства16
4.Выбор метода изготовления заготовки и составление эскиза технико-экономическое обоснование при выборе эскиза [1]16
5.Разработка маршрута обработки основных поверхностей детали18
6.Выбор баз и анализ схем базирования для нескольких операций. Составление эскизов обработки19
7.Расчет припусков на обработку и составление расчетной таблицы27
8.Разработка операционной технологии с выбором моделей оборудования и типов режущих инструментов28
Конструирование и расчет приспособленияОшибка! Закладка не определена.
1.Описание конструкции и работы приспособления32
2.Анализ технических требований33
3.Составление схемы сил действующих на заготовку и расчет зажимного устройства.34
В данном курсовом проекте рассмотрено проектирование технологического процесса сборки цилиндрического редуктора с учетом анализа технических требований на сборку разработана технологическая схема сборки.
Разработан технологический процесс изготовления детали «Крышка подшипников» на основе анализа технических требований к данной детали технологичности конструкции составлен маршрут обработки поверхностей разработана операционная технология выбраны режимы обработки.
Так же разработаны контрольное приспособление для контроля плоскостности детали и станочное приспособление для сверлильно-фрезерно-расточной операции. Назначены технические требования на приспособления. Проведен расчет зажимного устройства.
Раздел А. Проектирование технологического процесса сборки узла
Назначение сборочной единицы в машине краткое описание его конструкции и доработка чертежей по соответствующим ГОСТам.
Двухступенчатый цилиндрический редуктор выполненный по соосной схеме с внутренним зацеплением узкий горизонтальный предназначен для передачи крутящего момента и движения от двигателя на барабан привода ленточного конвейера.
Техническая характеристика:
Номинальный крутящий момент на тихоходном валу:
Частота вращения выходного вала:
Передаточное число редуктора:
Межосевое расстояние:
Степень точности изготовления передач:
Редуктор состоит из литого чугунного корпуса в котором располагаются три сборочные единицы: быстроходный промежуточный и тихоходный вал.
При включении электродвигателя вал электродвигателя начинает вращаться. Через упругую муфту и шпонку поз.41 крутящий момент передается на входной вал редуктора. Шестерня быстроходной ступени вращается со скоростью равной скорости вращения быстроходного вала. Шестерня входит в зацепление с колесами поз.5. Поворот колеса приводит к вращению промежуточного вала. При вращении вала начинает вращаться шестерня на промежуточном валу. Шестерня находится в зацеплении с колесом 6. При вращении шестерни начинает вращаться и колесо. При вращении колеса начинает вращаться тихоходный вал на который передается крутящий момент с промежуточного вала. С помощью упругой муфты с лепестками крутящий момент с тихоходного вала передается на барабан. Барабан приводит в ленту конвейера.
Анализ технических требований на сборку с разработкой схем проверки по заданным требованиям.
Технические требования:
Необработанные поверхности литых деталей находящихся в масляной ванне красить маслостойкой красной эмалью.
Плоскость разъёма покрыть тонким слоем герметика УТ-34 ГОСТ 24285-80 при окончательной сборке
Радиальная консольная нагрузка:
на тихоходном валу:
на быстроходном валу:
Радиальное смещение валов:
Осевое смещение валов:
Проверить пятно контакта по ГОСТ 1643-81
При сборке залить маслом И-Г-А-32
Произвести обкатку редуктора
Разработка схем проверки по заданным требованиям.
Контроль качества сборки осуществляется проведением следующих операций:
Контроль точности зубчатых передач
Нормальную работу зубчатых передач обеспечивают нормы точности. ГОСТ 1643-81 устанавливает четыре нормы точности эвольвентных цилиндрических передач: кинематическую плавности работы пятна контакта зубьев бокового зазора. Стандартом предусмотрены 12 степеней точности зубчатых колес и передач обозначенных в порядке убывания точности цифрами 1 12. Наибольшее распространение имеют 6 7 8 и 9 степени точности.
Нормы контакта определяются относительными размерами пятна контакта в процентах (рис. 6). По длине зуба берется отношение расстояния а между крайними точками пятна за вычетом разрывов с превосходящих величину модуля к полной длине зуба.
По высоте зуба – отношение средней высоты пятна контакта hm к рабочей высоте зуба hp равной 2mn :
Степень точности по нормам контакта зубьев определяется по табл. 1
Рис.6. Пятно контакта
Определение мгновенного пятна контакта
Протереть зубья нанести на два зуба шестерни тонкий слой краски повернуть рукой вал и по отпечаткам на зубьях колеса замерить размеры а с hm.
Вычислить относительные размеры пятна контакта и по табл. 1 определить соответствующую степень точности по нормам контакта.
Нормы контакта зубьев цилиндрических зубчатых колес (ГОСТ 1643-81)
Назначить нормы кинематической точности и плавности работы по табл.2.
Допускаемая стандартами область комбинирования норм кинематической
точности плавности работы и контакта зубьев
Номер степени точности
Кинематическая точность
В технической характеристике редуктора проставить степень точности передачи в следующем порядке: кинематическая точность; плавность работы контакт зубьев; боковой зазор. Например: 7-8-8 ГОСТ 1643-81.
Проверка на статический момент
Проверку статического момента проводят путём проворачивания входного вала редуктора с одновременным контролем проворачивания выходного вала в прямом и реверсивном направлениях.
Проверка осевого смещения валов
Проверку осевого смещения валов осуществляют по схеме:
Провернув вал на один оборот необходимо проконтролировать максимальное значение показанное индикатором затем сравнить его с требуемым значением осевого биения.
Качественная и количественная оценка технологичности сборочной единицы.
В конструкции редуктора есть группы деталей которые собираются предварительно (тихоходный быстроходный и промежуточные валы). Для сборки разборки редуктора используется узкая номенклатура сборочных и регулировочных инструментов. В конструкции также предусмотрен элементы для транспортировки (проушины в крышке). Предусмотрена регулировка зазора в подшипниках (посредством прокладок 141516). Предусмотрены фаски для обеспечения возможности сборки. Редуктор содержит максимальное количество стандартных деталей что облегчает его изготовление и сборку.
К недостаткам данной конструкции можно отнести: необходимость установки крышки для промежуточных подшипниковых опор что усложняет процесс изготовления и сборки. Также к недостаткам можно отнести то что тихоходный вал является опорой подшипников быстроходного вала что снижает их ресурс.
Коэффициент стандартизации:
где - количество стандартных деталей и сборочных единиц; – общее количество деталей и сборочных единиц.
Проведя анализ и внеся необходимые дополнения конструкцию редуктора можно считать технологичной для данного типа производства.
Описание методов достижения точности сборки и составление размерной цепи
Для достижения заданной точности сборки редуктора используют метод неполной взаимозаменяемости. По принципу неполной взаимозаменяемости может производиться сборка редуктора только в условиях данного предприятия. Так как частичная взаимозаменяемость позволяет значительно расширить допуски на размерах деталей и тем самым уменьшить себестоимость их обработки это полностью компенсирует дополнительные затраты времени на регулировку при сборке редуктора. Следовательно метод регулировки это второй метод достижения точности сборки. В данном редукторе регулируется зазор в подшипниках с помощью прокладок 141516 между крышками подшипников и корпусом.
Разработка технологической схемы сборки и пояснений к ней.
Последовательность сборки с обоснованиями:
) За базовую деталь выбирается корпус редуктора поз. 7 т.к. данная деталь наилучшим образом определяет положение других деталей данного узла. Под наилучшим образом понимается минимальная погрешность базирования деталей.
) В корпус редуктора запрессовываются 2 установочных штифта поз. 45 которые необходимы для соблюдения соосности установочных отверстий в корпусе редуктора и крышки корпуса.
) Вал тихоходный поз. 2 в сборе. Т.к. вал в сборе по массе и габаритам наибольший среди других валов то ставим его первым.
) Вал промежуточный поз. 3 в сборе.
) Регулировка зацепления цилиндрической пары.
) Вал быстроходный поз. 4 в сборе. Т.к. вал в сборе по массе и габаритам наименьший других валов то ставим его последним.
) Крышка подшипника поз. 11 в сборе (с манжетой) ставится на посадку с зазором в редуктор.
) Крышка подшипника поз. 12 в сборе (с манжетой) ставится на посадку с зазором в редуктор.
) Крышка подшипника (глухая) поз. 9 ставится на посадку с зазором в редуктор.
) Крышка подшипника (глухая) поз. 10 ставится на посадку с зазором в редуктор.
) В корпус редуктора запрессовываются 2 установочных штифта поз. 36 которые необходимы для соблюдения соосности установочных отверстий в корпусе редуктора и крышки опор подшипников 13.
) Плоскости соприкосновения редуктора и крышки опор подшипников покрывают слоем герметика. После этого крышку редуктора по направляющим штифтам поз. 36 ставят на редуктор.
) Прикручиваются 3 винта поз.34 вместе с 3 шайбами поз.35 закрепляя тем самым крышку опор подшипников с корпусом редуктора.
) Плоскости соприкосновения редуктора и крышки редуктора покрывают слоем герметика. После этого крышку редуктора по направляющим штифтам поз. 21 ставят на редуктор.
) Прикручиваются 10 винтов поз.22 вместе с 10 шайбами поз.38 закрепляя тем самым крышку редуктора с корпусом редуктора.
) Прикручиваются 6 болтов поз.21 вместе с 6 шайбами поз.37 закрепляя тем самым крышку подшипника 11 с корпусом редуктора.
) Прикручиваются 4 болта поз.17 вместе с 4 шайбами поз.36 закрепляя тем самым крышку подшипника 12 с корпусом редуктора.
) Прикручиваются 4 болта поз.19 вместе с 4 шайбами поз.36 закрепляя тем самым крышку подшипника 9 с корпусом редуктора.
) Прикручиваются 4 болта поз.17 вместе с 4 шайбами поз.36 закрепляя тем самым крышку подшипника 10 с корпусом редуктора.
) Шпонка поз.41 запрессовывается на быстроходный вал в сборе
) Шпонка поз.43 запрессовывается на тихоходный вал в сборе
) Пробки поз. 37 завертывают в коническое резьбовое отверстие в редукторе до упора.
) Заливают масло И-Г-А-32 ГОСТ 20799-88 в количестве 155 л.
) С помощью верхней пробки поз. 37 контролируют уровень масла в редукторе.
) Закрывают отверстие для осмотра крышкой люка поз. 1
) Закручивают 4 винта поз. 18 прикручивая тем самым крышку люка к крышке редуктора.
) Прокручивают редуктор вручную за выходной вал (назначение см. технические требования).
) Обкатывают редуктор (назначение см. технические требования).
) Контролируют пятно контакта (назначение см. технические требования).
) Редуктор в сборе как сборочная единица собран.
Разработка технологического процесса сборки с заполнением карт техническим нормированием времени по элементам и определением суммарной трудоёмкости сборки узла.
Нормативное время на сборку редуктора.
Факторы влияющие на продолжительность сборки
Норма времени (мин.)
Установить корпус редуктора 7 на место сборки
Наибольший размер детали – 540 мм вес – 60 кг
Запрессовать конический штифт 45
Размер штифта - 12×40 мм. Количество 2 шт.
Установить тихоходный вал 2 в сборе в открытые гнезда подшипников подъемником
Наибольший размер детали – 300 мм вес – 80 кг
Установить промежуточный вал 3 в сборе в открытые гнезда подшипников подъемником
Наибольший размер детали – 148 мм вес – 60 кг
Отрегулировать зацепление цилиндрической пары и проверить легкость вращения
Диаметр вала – 45 мм. Длина вала 200 мм
Установить быстроходный вал 4 в сборе в открытые гнезда подшипников подъемником
Наибольший размер детали – 190 мм вес – 25 кг
Диаметр вала – 35 мм. Длина вала 190 мм
Установить крышку подшипника 12 в сборе в отверстие редуктора
Диаметр отверстия – 120 мм. Длина продвижения –30 мм. Вес – 44 кг.
Посадка – скользящая.
Установить крышку подшипника 11 в сборе в отверстие редуктора
Диаметр отверстия – 62 мм. Длина продвижения – 20 мм. Вес – 22 кг.
Установить крышку подшипника 9 в отверстие редуктора
Диаметр отверстия – 80 мм. Длина продвижения – 25 мм. Вес – 4 кг.
Посадка – скользящая.
Плоскости соприкосновения редуктора и крышки редуктора покрыть тонким слоем герметика
Площадь соприкосновения – 55000 мм2
Установить крышку редуктора 8 на редуктор
Наибольший размер детали – 592 мм. Вес – 55 кг
Надеть на винты 22 шайбы 37
Внутренний диаметр шайбы – 14 мм. Длина детали – 38 мм. Количество 4 шт.
Затянуть винты с шайбами до упора в редуктор поз. 7
Диаметр резьбы – 14 мм. Шаг резьбы – 175 мм. Длина завертывания винта – 38 мм. Количество 4 шт.
Надеть на винты 23 шайбы 37
Внутренний диаметр шайбы – 14 мм. Длина детали – 55 мм. Количество 6 шт.
Диаметр резьбы – 14 мм. Шаг резьбы – 175 мм. Длина завертывания винта – 55 мм. Количество 6 шт.
Надеть на болты 21 шайбы 37
Внутренний диаметр шайбы – 10 мм. Длина детали – 25 мм. Количество 4 шт.
Диаметр резьбы – 10 мм. Шаг резьбы – 15 мм. Длина завертывания винта – 25 мм. Количество 4 шт.
Надеть на болты 17 шайбы 37
Внутренний диаметр шайбы –8 мм. Длина детали – 25 мм. Количество 4 шт.
Диаметр резьбы –8 мм. Шаг резьбы – 1 мм. Длина завертывания винта – 25 мм. Количество 4 шт.
Надеть на болты 19 шайбы 37
Внутренний диаметр шайбы – 8 мм. Длина детали – 25 мм. Количество 4 шт.
Диаметр резьбы – 8 мм. Шаг резьбы – 175 мм. Длина завертывания винта – 25 мм. Количество 4 шт.
Завернуть конический винт 21 до упора в отверстие редуктора 7
Диаметр резьбы – 40 мм. Шаг резьбы – 15 мм. Длина ввертывания – 16 мм.
Установить маслоуказатель 7 в редуктор 15
Наибольший размер детали – 315 мм. Вес – 1 кг
Установить крышку люка 4 в сборе на крышку редуктора 15
Наибольший размер детали – 338 мм. Вес – 15 кг
Закрутить до упора винты 18 в крышку люка 4 и крышку редуктора 15
Диаметр резьбы – 5 мм. Шаг резьбы – 15 мм. Длина ввертывания – 23 мм. Количество винтов – 4Инструмент – ручная слесарная отвертка.
Выполнение работы удобное движение рабочего не стеснены установка деталей происходит сверху или сбоку. Значит поправочный коэффициент на изменение условия работы принимаем равным 1.
Время сборки редуктора: T = 2713 мин.
В данное время не включены прокрутка и обкатка редуктора контроль пятна контакта и время на нанесение на зубья пистолетом-дозатором смазки т.к. на данные операции не нормированы по времени.
Раздел Б. Проектирование технологического процесса обработки
Назначение детали в сборочной единице доработка чертежа по действующим ГОСТам анализ технических требований выявление технологических задач возникающих при изготовление и разработка схем проверки по заданным требованиям.
Корпуса соосных редукторов отличает наличие дополнительной стенки расположенной внутри корпуса и предназначенной для размещения опор соосных валов Проектируемая деталь – крышка шариковых однорядных подшипников выходного и промежуточного валов цилиндрического двухступенчатого соосного редуктора. Деталь служит для фиксации шариковых однорядных подшипников в промежуточной опоре выходного и промежуточного валов редуктора. Наличие такой крышки обусловлено необходимостью точного позиционирования подшипников служит для простоты изготовления опор выходного и промежуточного валов простоты сборки редуктора.
Описание конструкции.
Деталь сложной конфигурации. Крышка имеет восемь цилиндрических участков из них три внутренних (90мм 100мм 140мм и 150мм) и два внешних (200мм 160мм); две канавки на внутренних цилиндрических поверхностях 100 и 150 детали перед торцами выступов 90 и 140 соответственно (чтобы обеспечить сопряжение торцов выступа детали и торца подшипника по плоскости). Также в детали имеются пять отверстий два 12 под штифты и три 15 под крепежные болты М14.
Анализ технических требований.
При обработке детали решаются технологические задачи обеспечениям (допуски формы и расположения после их определения округляем до ближайшего целого числа из ряда предпочтительных [1] стр.380):
Допуск цилиндричности (для 150H7 0.5t20 мкм где t=40мкм для 100H7 0.5t18 мкм где t=35мкм ([1] стр.284 [2] стр.165 таб. П.1.1)) и следовательно дорожки качения наружного кольца подшипника.
Допуск цилиндричности задаём чтобы ограничить отклонения геометрической формы посадочной поверхности.
Допуск перпендикулярности (для 150H7 не более 50мкм для 100H7 не более 40мкм ([1] стр.451 таб.5 при степени точности допуска для шарикового подшипника - 8)).
Допуск параллельности торцов задаём т.к.по торцу базируем подшипник качения (для 150H7 не более 40мкм для 100H7 не более 30 мкм ([1] стр.360 таб.22.8 при степени точности допуска для шарикового подшипника - 8)).
Допуск на крепежные размеры принимают равным ± 0.1(d0-d)=100 мкм где d0=15мм – диаметр крепежного отверстия d=14мм – диаметр винта.
Предельное отклонение межосевого расстояния a=150мм крышки промежуточной опоры цилиндрической зубчатой передачи Δ= ±(0.6 0.7)fa=0.65·50= 32мкм где fa - предельное отклонения межосевого расстояния цилиндрической зубчатой передачи.
Допуски плоскостности по ГОСТ 16162-85 на плоскость разъема – 0.01100 мммм на торцевую плоскость– 0.03100 мммм ([1] стр.384)
Технологические задачи:
Выбор вида и метода получения заготовки.
Выбор методов обработки поверхностей детали.
Выбор схемы установки заготовки.
Определения структуры маршрутного процесса.
Выбор режима обработки.
Характеристика условий производства
Производство мелкосерийное. Серийное производство – производство продукции товаров сериями то есть отдельными партиями в значительном но не массовом количестве. Серийный тип производства характеризуется изготовлением ограниченной номенклатуры деталей партиями повторяющимися через определенный промежуток времени. Это позволяет использовать специальное оборудование наряду с универсальным.
Предметная специализация участков делает целесообразным обработку партии деталей параллельно на нескольких станках выполняющих следующие друг за другом операции. Как только на предыдущей операции заканчивается обработка нескольких первых штук они передаются на следующую операцию до окончания обработки всей партии. Таким образом в условиях серийного типа производства становится возможной параллельно-последовательная организация производственного процесса [2].
Так как производство мелкосерийное расчёт такта выпуска не производим.
Качественная оценка технологичности. Анализ конструкции детали
Конструкция детали состоит из большого количества поверхностей обусловленных ее функциональным назначением. Установленные допуски являются оправданными: допуски формы обусловлены степенью ответственности детали самую высокую размерную точность (6 квалитет) имеют цилиндрические поверхности базирования подшипников диаметров 100 и 150 мм. Все размеры поверхностей соответствуют нормальному ряду размеров. Система простановки размеров в целом обеспечивает удобство и производительность контроля. Для контроля параметров точности можно использовать простые измерительные средства и приспособления.
За счет небольшой протяженности обрабатываемых поверхностей снижается объём механообработки что приводит к снижению трудоемкости обработки детали.
Необходимость обработки цилиндрических поверхностей детали в которые устанавливаются подшипники выходного и промежуточного валов в сборе с редуктором значительно повышает трудоемкость.
Сложность геометрической формы изделия подразумевает применение технологий литья для изготовления данного изделия.
Простота расположения поверхностей друг относительно друга обеспечивает удобный подвод и свободный выход режущего инструмента.
На основе проведенного анализа считаем конструкцию данной детали нетехнологичной в условиях мелкосерийного производства.
Выбор метода изготовления заготовки и составление эскиза обоснование при выборе заготовки.
Заготовки необходимо подбирать таким образом чтобы обеспечить наиболее рациональное использование материала минимальную трудоемкость получения заготовок и возможность снижения трудоемкости изготовления самой детали.
При выборе заготовки учитывают:
- тип производства;
- материал заготовки;
Корпусные детали изготавливают из чугуна марок СЧ15 СЧ20.
Крышки опор подшипников изготавливаются с местами установки самих подшипников а также с крепёжными отверстиями для крепления крышки к корпусу опоры а в данном случае цилиндрического редуктора.
Заготовка получается отливкой в песчаную форму. Степень точности отливки для среднесерийного типа производства – вторая.
Заготовка для литья – прокат круглого поперечного сечения 50 мм длиной 400 мм.
Для выбора метода отливки для заготовки проанализируем два предлагаемых метода.
Габаритный размер отливки 340 мм. Тогда допустимые отклонения для второго класса точности составляют 1 мм.
Ручная формовка опоках
Степень точности отливки
Выбираем метод литься в песчаную форму со стержнями. Этот способ также подходит так как минимальная толщина стенки при этом способе литья 6 мм [1 с123] а стойкость формы составляет 100 отливок [1 с126].
Т.к. этот метод обеспечивает наибольшее приближение заготовки по форме к изделию и позволит оставить необрабатываемые поверхности.
Назначаем 14 квалитет отливки.
Операция 005. Заготовительная. Литьё в песчаную форму.
Рис. Эскиз заготовки крышки подшипниковой опоры
Разработка маршрута обработки основных поверхностей детали.
Выбор метода обработки поверхности заготовки производится на основе обеспечения наиболее рационального процесса обработки (с учетом выбора более короткого маршрута) служебного назначения детали функционального назначения поверхности требований точности.
Отверстия под штифты 12Н7 (Ra=1.6мкм)
-Сверление – IT11 Ra 25-0.8 мкм ([1] стр.11 табл.5).
-Зенкерование – IT8 Ra 16-2.5 мкм ([1] стр.11 табл.5).
-Развертывание точное – IT7 Ra 6.3-0.4 мкм ([1] стр.11 табл.5).
Отверстия под винты 15Н7 (Ra=16мкм)
-Сверление – IT10 Ra 25-0.8 мкм ([1] стр.11 табл.5).
Внутренняя цилиндрическая поверхность 100H7 (Ra=1.6мкм)
-заготовка IT14 Rz 40;
-Растачивание черновое – IT11 Ra 25-1.6 мкм ([1] стр.11 табл.5).
-Растачивание получистовое – IT8 Ra 16-2.5 мкм ([1] стр.11 табл.5).
-Растачивание чистовое – IT7 Ra 6.3-0.4 мкм ([1] стр.11 табл.5).
Внутренняя цилиндрическая 150H7 (Ra=1.6мкм)
Торцовая поверхность крепления к корпусу редуктора (Ra=3.2 мкм)
-фрезерование черновое – IT11 Ra 25-1.6 мкм ([1] стр.8 табл.4).
-фрезерование получистовое – IT8 Ra 16-2.5 мкм ([1] стр. 8 табл.4).
-фрезерование чистовое – IT7 Ra 6.3-0.4 мкм ([1] стр.8 табл.4).
Выбор баз составление маршрута обработки выбор вида оборудования. Составление эскизов обработки и контроля с упрощенными обозначениями по ГОСТу.
Заготовка детали должна занять и сохранять в течение всего времени обработки определенное положение относительно деталей станка и приспособления. Для этого необходимо исключить возможность трех прямолинейных движений ее в направлении выбранных координатных осей и трех вращательных движений вокруг параллельных им осей (то есть лишить заготовку детали 6 степеней свободы).
Выбираемые базы должны обеспечивать:
- удобство установки (базирования и закрепления) и снятия заготовки
- возможность беспрепятственного подвода инструмента к намеченным для обработки поверхностям
- исключение деформаций заготовки при установке и последующей обработке.
При выборе баз по возможности должны соблюдаться принципы:
- совмещение установочных и измерительных баз.
На первых двух-трёх операциях при базировании по черновым базам обрабатывают основные технологические базы [1 с.199]. Поэтому за черновую технологическую базу примем поверхность крышки параллельную плоскости разъема крышки и редуктора за основную технологическую – саму поверхность разъема.
Выбор вида оборудования.
Т.к. производство мелкосерийное то целесообразно применять универсальное оборудование. Соответственно оборудованием будут станки с ЧПУ. Деталь имеет сложную конфигурацию есть необходимость обрабатывать торцовые поверхности горизонтально расположенные внутренние цилиндрические поверхности вертикально расположенные отверстия. Используем универсальный вертикально-сверлильно-расточной станок с ЧПУ 630VH который может выполнять все требуемые операции.
Таблица. Основные технические характеристики станка
сверлильно-фрезерно-расточного с ЧПУ 630VH
Размер рабочей поверхности стола мм
Диаметр центрального отверстия мм
Диаметр крепежных отверстий мм
Наибольшая масса обрабатываемой детали кг
Число ступеней частот вращения шпинделя
Пределы частот вращения шпинделя обмин
Номинальный крутящий момент на шпинделе Нм
Мощность главного привода кВт
Наибольшее программируемое перемещение по координатам
- продольное перемещение стола (Х) мм
- поперечное перемещение колонны (Y) мм
- вертикальное перемещение шпиндельной бабки (Z) мм
- вращение шпинделя (А) град.
- вращение стола (С) град.
Точность позиционирования по осям Х Y Z мм
Дискретность задания перемещения мм
Число одновременно управляемых осей координат
Наибольшее усилие подачи по координатам Х Y Z Н
Пределы рабочих подач по координатам Х Y Z мммин
Число ступеней рабочих подач
Скорость быстрого перемещения по координатам Х Y Z ммин
Инструментальный магазин
Емкость инструментального магазина шт.
Время смены инструмента с
Наибольшая масса оправки устанавливаемой в магазине кг
SIEMENS SINUMERIK 840D
Прочие характеристики
Габаритные размеры мм
Далее составляем эскизы обработки и контроля.
Операция 010. Сверлильно-фрезерно-расточная.
На сверлильно-фрезерно-расточной операции 010 производится обработка поверхности параллельной поверхности В на сверлильно-фрезерно-расточном станке с ЧПУ с установкой заготовки по плоскости. В качестве базы используем необработанную поверхность В.
Операция 015. Сверлильно-фрезерно-расточная.
На сверлильно-фрезерно-расточной операции 010 производится обработка поверхности В сверлильно-фрезерно-расточном станке с ЧПУ с установкой заготовки по плоскости. В качестве базы используем поверхность обработанную в операции 010.
Операция 020. Контрольная.
Контролируется плоскостность поверхности стыка крышки и корпуса с использованием контрольно-измерительного приспособления. Схема контроля показана на листе «Контрольно-измерительное приспособление»
Операция 025. Сверлильно-фрезерно-расточная.
На сверлильно-фрезерно-расточной операции 015 производится сверление отверстий 3х15 и 2x12 на сверлильно-фрезерно-расточном станке с ЧПУ с установкой заготовки по плоскости. В качестве базы используем поверхность В.
Операция 030. Слесарная.
На слесарной операции 025 производится удаление стружки полученной на предыдущей операции при использовании напильника слесарного.
Операция 035. Сборочная.
На сборочной операции 030 производится установка детали на корпус и закреплении её на корпусе при помощи 3х винтов М14.
На сверлильно-фрезерно-расточной операции 035 производится сверление зенкерование и развёртывание отверстий 2х12 на сверлильно-фрезерно-расточном станке с ЧПУ с установкой заготовки по плоскости. В качестве базы используем поверхность В.
Операция 040. Сборочная.
На сборочной операции 040 производится запрессовка штифтов в отверстия в крышке и корпусе посредством 2х штифтов 12.
Операция 045. Сверлильно-фрезерно-расточная.
На установе 1 сверлильно-фрезерно-расточной операции 045 производится растачивание отверстия 150+004 на сверлильно-фрезерно-расточном станке с ЧПУ с установкой заготовки по плоскости. В качестве базы используем крепёжные отверстия в корпусе.
На установе 2 сверлильно-фрезерно-расточной операции 045 производится растачивание отверстия 100+0035 на сверлильно-фрезерно-расточном станке с ЧПУ с установкой заготовки по плоскости. В качестве базы используем крепёжные отверстия в корпусе.
Расчет припусков на обработку.
Рассчитаем припуски на обработку одной из самых ответственных поверхностей детали – внутренней цилиндрической поверхности А с диаметром 100Н7 мм и шероховатостью Ra = 16 мкм. Определение припусков производится расчетно-аналитическим методом.
Минимальный припуск для i-го перехода рассчитывается по следующей формуле:
ΔΣi – суммарное отклонение расположения поверхностей на предшествующем переходе:
где - местное отклонение оси детали от прямолинейности.
Для заготовки перед обработкой:
где Δк=1 мкммм – коробление корпуса на 1 мм .
На последующих переходах ΔΣ
i – погрешность установки заготовки на данном переходе. Радиальное смещение заготовки 10 мкм осевое 10 мкм. Суммарная погрешность установки для данного перехода . Погрешность закрепления для оправки: радиальная – 60 мкм осевая – 30 мкм. Тогда:
Расчетный максимальный диаметр определяется по следующей формуле:
Расчетный минимальный диаметр определяется по следующей формуле:
Результаты расчета представлены в таблице:
Черновое растачивание
Получистовое растачивание
Чистовое растачивание
Общие припуски определяем как сумму промежуточных припусков на обработку: 2Zоmax = 3142 мкм 2Zоmin = 2493 мкм. Рассчитанное значение припуска получилось меньше принятого по рекомендациям. Таким образом в качестве припуска принимаем припуск назначенный по рекомендациям.
Воспользуемся рекомендациями:
Технологический маршрут обработки детали
Точность поверхности
Припуск на обработку мм
Принятые размеры по переходам мм
Заготовка отливка (IT14)
) Черновое точение (IT11)
) Получистовое точение (IT8)
) Чистовое точение (IT7)
Разработка операционной технологии. Нормирование операций с учетом штучного времени.
Группу режущего инструмента устанавливают по виду обработки предусмотренному маршрутным технологическим процессом. По конфигурации обрабатываемой поверхности заготовки компоновки станка принятой схеме установки заготовки выявляют форму и расположение режущих лезвий определяющий вид режущего инструмента.
Режимы резания определяются глубиной резания t подачей S и скоростью резания V. Значения этих режимов влияют на точность и качество получаемой поверхности производительность и себестоимость обработки. Режимы резания определяют в порядке возрастания их влияния на стойкость режущих инструментов: tSV
Рассмотрим методику выбора режущего инструмента и расчет режимов резания на примере нескольких операций.
При черновой обработке глубину резания назначают равной всему припуску на обработку или его большей части [2 с. 261]. Выбор параметров режимов резания осуществляем по справочным таблицам [2 с. 262-269].
Операция 010. Сверлильно-фрезерно-расточная с ЧПУ.
Оборудование: сверлильно-фрезерно-расточной станок с ЧПУ модели 630VH.
Переход 1. Фрезеровать верхнюю плоскость.
Подача на один зуб: .
Стойкость инструмента: .
Скорость резания определяем по формуле:
где =41; q=025; m=02; y=04; u=015; p=0; B=34 мм – ширина фрезерования; – общий поправочный коэффициент на скорость резания учитывающий фактические условия резания.
где – коэффициент учитывающий качество обрабатываемого материала; – коэффициент учитывающий состояние поверхности заготовки; – коэффициент учитывающий материал инструмента.
где – коэффициент характеризующий группу стали по обрабатываемости; .
Определяем частоту вращения шпинделя:
Определим подачу на один оборот фрезы:
Определим минутную подачу:
Норма штучного времени: tшт = (То + Тв)(1 + Kобсл + Kотд).
Основное время: где – длина рабочего хода фрезы.
где – путь подвода фрезы и длина перебега на выходе фрезы; – длина заготовки; – величина врезания фрезы; – путь выхода фрезы.
ТВ – вспомогательное время согласно нормативам. Вспомогательное время Тв затрачивается на закрепление и снятие обрабатываемых заготовок пуск и останов станка смену режущего инструмента а также на его подвод и отвод на каждом переходе на измерение размеров заготовки и т. п.
Коэффициент Kобсл характеризует время на обслуживание станка. По нормативам для фрезерных станков Kобсл = 0035.
Коэффициент Kотд характеризует затраты времени на отдых и личные надобности рабочего. По нормативам Kотд = 006 при ручной смене заготовок массой до 50 кг. Поскольку за период стойкости обрабатывается Kз заготовок время на смену инструмента приходящееся на одну заготовку будет составлять где tсм — время затрачиваемое на смену инструмента т. е. вспомогательное время может быть выражено как . В слагаемом То с помощью коэффициента учитываются все временные вспомогательные затраты при обработке одной заготовки (исключая время на смену инструмента) в долях основного технологического времени То.
Время tсм на замену изношенной фрезы составляет 20 30 мин. Примем что tсм = 25 мин. Таким образом:
Раздел В. Конструирование и расчет приспособления
Разработка схемы приспособления.
Станочное приспособление конструируется для сверлильно-фрезерно-расточной операции. Оно необходимо для точного позиционирования и закрепления обрабатываемого изделия.
Станочное приспособление должно содержать установочные элементы для базирования корпуса и зажимные элементы для противодействия силам резания которые оказывают опрокидывающее воздействие на заготовку. Все элементы устанавливаются на плите. Плита в свою очередь крепится на столе сверлильно-фрезерно-расточного станка.
Выбор установочных зажимных и других элементов приспособления.
В качестве установочных элементов используем установочные пальцы:
палец установочный цилиндрический ГОСТ 12200-66
палец установочный срезанный ГОСТ 12210-66
Для того чтобы установка корпуса на пальцы была возможной используются сочетание срезанного и цилиндрического пальцев из-за наличия отклонения размера между осями крепёжных отверстий.
В качестве зажимных устройств используем прихваты поворотные ГОСТ 4734-69. Прижимное усилие создаётся завинчиванием болта.
Все элементы базируются на плите которая имеет необходимые крепёжные отверстия. Для крепления плиты на столе станка в ней есть установочные отверстия.
Схема приспособления показана на рисунке:
Выбор установочных зажимных и других элементов приспособлений с необходимыми расчётами.
В данном приспособлении применяем прихват поворотный [5 с.164]. Помимо трения в нарезке (наиболее характерного для зажима винтами со сферической пятой) учитываем и трение на торце гайки.
При зажиме болтом силу Q определяем исходя из следующих рассуждений.
Где средний диаметр резьбы винта
коэффициент учитывающий потери от трения в шарнире на оси прихвата
Опрокидывающий момент от резца:
Момент сопротивления опрокидыванию:
Момент создаваемый прихватом должен быть больше либо равен моменту силы резания:
Сила воздействия на корпус со стороны резца:
n – частота вращения резца обмин
Ср=682; х=086; y=072; u=01; q=086;w=0.
Усилие на одном винте:
– сила затяжки винта
Назначение технических требований на приспособление обеспечивающих заданную точность
Отклонение от параллельности поверхности Г относительно поверхности Д не более 001 мм на длине 100 мм.
Данное требование обеспечивает горизонтальное расположение обрабатываемых отверстий.
Отклонение от параллельности плоскости проходящей через оси пальцев 7 и 8 относительно плоскости проходящей через оси крепежных отверстий не более 001 мм на длине 100 мм.
Данное требование обеспечивает отсутствие перекоса обрабатываемых отверстий друг относительно друга.
Оформление чертежа приспособления составление спецификации основных деталей
Чертёж станочного приспособления и спецификации к нему представлен на чертежах (лист 5).
Описание конструкции и работы приспособления
Обработка детали производится на сверлильно-фрезерно-расточном станке. Установка и закрепление заготовки производится во время обработки. Корпус последовательно устанавливается на цилиндрический палец 7 и срезанный палец 8. Закрепление производится прихватами 9 посредством болта 4.
Конструирование контрольного приспособления
Чертёж приспособления для контроля плоскостности поверхности разъёма крышки подшипниковой опоры и корпуса со спецификацией на основные детали представлен на листе 6 «Контрольно-измерительное приспособление»
В данном курсовом проекте была выполнена разработка технологических процессов сборки двухступенчатого цилиндрического редуктора с внутренним зацеплением.
При проведении анализа технических требований на сборку было установлено что конструкция данной сборочной единицы является технологичной за исключением некоторых доработок. Была также выполнена разработка технологической схемы общей сборки и технологического процесса сборки.
Во второй части проекта был проведен анализ технических требований чертежа стакана и технологичности конструкции на основании этого можно сказать что деталь является технологичной только в условиях мелкосерийного производства. Был составлен маршрут обработки основных поверхностей выбраны базы проведена разработка маршрута изготовления детали.
В третьей части проекта сконструировано приспособление для растачивания отверстий в корпусе редуктора описана конструкция и работа приспособления рассчитана сила закрепления.
Справочник технолога-машиностроителя. В 2-х т. Т. 1Под ред. А.Г. Косиловой и Р.К. Мещерякова. – 4-е изд. перераб. и доп. – М.: Машиностроение 1986. 656 с.
Справочник технолога-машиностроителя. В 2-х т. Т. 2Под ред. А.Г. Косиловой и Р.К. Мещерякова. – 4-е изд. перераб. и доп. – М.: Машиностроение 1986. 496 с. ил.
Дунаев П.Ф. Леликов О.П. Детали машин. Курсовое проектирование: Учеб. пособие для машиностроит. спец. учреждений среднего профессионального образования. – 3-е издание перераб. и доп. – Машиностроение 2002. – 536 с. ил.
Анурьев В.И. Справочник конструктора-машиностроителя: в 3-х т.: Т.2. – 8-е изд. перераб. и доп. Под ред. И.Н. Жестковой. – М.: Машиностроение 2001. – 912 с.: ил.
Горошкин А.К. Приспособления для металлорежущих станков. Справочник. – 6-е издание исправленное и дополненное. – М.: Машиностроение 1971. – 384 с.
Вереина Л.И. Справочник токаря: учеб. Пособие для нач. проф. образованияЛ.И. Вереина – 2-е издание стер. – М.: Издательский центр «Академия» 2006. - 448с.
Рекомендуемые чертежи
- 29.04.2019