Самопередвигающаяся вибрационная плита




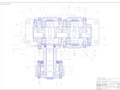
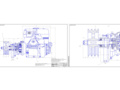
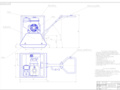
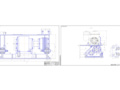
- Добавлен: 25.10.2022
- Размер: 12 MB
- Закачек: 0
Описание
Состав проекта
![]() |
![]() ![]() ![]() |
![]() ![]() ![]() |
![]() ![]() ![]() |
![]() |
![]() ![]() |
![]() |
![]() ![]() ![]() ![]() |
![]() |
![]() ![]() ![]() ![]() |
![]() ![]() |
![]() ![]() ![]() |
![]() ![]() ![]() |
![]() |
![]() |
![]() ![]() |
![]() ![]() ![]() |
![]() ![]() ![]() ![]() |
![]() |
![]() ![]() ![]() ![]() |
![]() ![]() |
Дополнительная информация
Ведомость.docx
Пояснительная записка
Самопередвигающаяся вибрационная плита
Расчет экономической эффективновсти
Ведомость объема дипломного проекта
Содержание мое.docx
Постановка задач по усовершенствованию существующих конструкций 26
Конструкторская часть .. 27
1 Расчет основных элементов вибрационной плиты . 27
2 Разработка конструкции 53
Технологическая часть . 58
1 Назначение детали и выбор заготовки . .. .. 58
2 Проектирование маршрута обработки. Выбор оборудования
3 Расчет режимов обработки и норм времени . 62
Экономическая часть . 78
1 Краткое описание машины . 78
2 Исходные конструктивно-эксплуатационные данные для оценки конкурентоспособности 79
3 Расчет затрат по сравниваемым вариантам технических решений 80
1 Разработка мероприятий по обеспечению безопасной эксплуатации разработанной вибрационной плиты .. .. 90
Список используемой литературы .. 98
пз моя.docx
ВИБРОПЛИТА ДВИГАТЕЛЬ ДЕБАЛАНС ВЫНУЖДАЮЩАЯ СИЛА ЗУБЧАТОЕ КОЛЕСО КОНСТРУКЦИЯ МУФТА.
Объектом разработки является вариант самопередвигающейся вибрационной плиты.
Цель проекта – проектирование самопередвигающейся вибрационной плиты с вынуждающей силой 28 кН.
В процессе работы проведен анализ литературных и патентных источников и разработан самопередвигающейся вибрационной плиты. Дано техническое обоснование использования данного решения.
Проведен расчет и разработаны чертежи мостового самопередвигающейся вибрационной плиты.
Разработана технологическая часть по изготовлению зубчатого колеса
Произведен расчет экономической эффективности внедрения новизны.
Разработаны мероприятия по охране труда.
Абсолютно все дорожно-строительные предприятия в своей деятельности сталкиваются с необходимостью применения уплотнительной техники [13]. История ее использования для построения качественного фундамента уходит корнями к истокам строительной деятельности человека. Даже самое совершенное здание не простоит долго без качественного фундамента это знали и этим пользовались еще в древности. В наши дни технологии обработки грунта существенно изменились в прошлом веке было изобретено совершенно уникальное оборудование которое применяется и доныне претерпев лишь некоторые технологические этапы усовершенствования. В данном случае речь идет о вибрационной плите которая по большей части применяется для уплотнения строительных смесей и материалов таких как песок бетон гравий асфальт тротуарная плитка и прочее. Максимальная производительность этого оборудования достигается за счет применения уникальных форм с закругленными углами рабочих поверхностей. Следует отметить что это оборудование легкое в эксплуатации и техническом обслуживании оно компактно и без особых сложностей работает в стесненных условиях[13]. А поскольку в производстве этого оборудования применяются самые совершенные технологии и качественные комплектующие то к его достоинствам можно добавить еще и надежность и долговечность.
На сегодня различают одноходные (или же прямоходные) и виброплиты реверсивные. Реверсивные модели отличаются способностью совершать движения и вперед и назад таким образом лишая оператора необходимостью производить маневры по развороту оборудования. Все подобное оборудование можно разделить и по типу привода. К наиболее популярным моделям стоит отнести бензиновые модели однако существуют еще достаточно хорошие модели дизельного и электрического привода. Современные дизельные модели обладают большим количеством достоинств по характеристикам маневренности и уровню уплотнения к достоинствам электрических моделей смело можно отнести самый низкий уровень шума и отсутствием каких-либо выхлопов что сохраняет чистоту воздуха. Электрические модели могут применяться только в закрытых помещениях так как нуждаются в источнике питания.
Виброплита (рис.1) – механизм повышенной мобильности экономичен занимает мало пространства не требует особых знаний и тщательной подготовки для работы с ним. Применение виброплит в случаях когда объемы работ по строительству дороги (уплотнение асфальта и грунта) относительно небольшие экономически выгодно.
Суть работы плиты заключается в подачи вибрации на грунт с помощью специальных механизмов (эксцентриков) которые крепятся к самой плите. Эксцентрики расположены таким образом что при вращении в противофазе можно изменять направление их действие (сдвигать фазу за счет чего меняется вибрационное усилие) и таким образом регулировать направление вибрационных колебаний. То есть виброплита может работать на месте в режиме поступательного движения или менять направление движения (вперед-назад).
Ход виброплиты регулируется специальным рычагом работающим с помощью гидравлического привода. Рукоятка расположения на панели управления. Двигатель плиты закрепляется штифтами на основании и обеспечивает работу вибрационного механизма. При запуске двигателя основную часть работу начинает выполнять центробежная муфта (закреплена на выходе момента двигателя и работает с помощью ремня передачи клиновидного типа который проходит на двух осях). Она передает вращение на вибрационный механизм. Муфта не функционирует на самых низких оборотах двигателя поэтому возможен запуск виброплиты на «холостом» ходу. Рычаг акселератора регулирует частоту оборотов двигателя (непосредственно во время работы желательно выставлять его на максимальный уровень чтоб плита не буксовала). Двигатель установлен на нижней части виброплиты и присоединен к амортизаторам с помощью которых убирается вибрация передаваемая на верхнюю часть
Рисунок 1 – Виброплита
2 Конструкция виброплит
Виброплита (рис.2) состоит из рабочей плиты поз.3 на которой монтируются все основные узлы виброплиты. Вибратор поз.4 имеет дебалансный вал установленный в подшипниковых опорах. Корпус вибратора выполнен в виде цилиндра. Вибратор устанавливается на рабочую плиту в гнездо повторяющее форму корпуса и фиксируется прижимными хомутами которые крепятся к рабочей плите болтами. Моторная рама поз.13 крепится к рабочей плите через резинометаллические элементы-амортизаторы. Двигатель поз.7 установлен на моторной раме. На валу двигателя установлена центробежная муфта сцепления поз.6 которая включается при частоте вращения 2200 обмин. От муфты к валу вибратора вращение передается через клиноременную передачу поз.5. Клиноременная передача имеет кожух поз.2 который крепится к моторной раме. Водило поз.9 через сайлентблоки крепится к моторной раме. На водиле установлен пластиковый бак для воды поз.8 смачивающей подошву рабочей плиты.
Виброплита комплектуется съемными транспортными колесами. [14]
2 Классификация виброплит
– разбрызгиватель; 2 – защитный кожух; 3 – рабочая плита; 4 - вибратор; 5 – клиноременная передача; 6 – центробежная муфта; 7 – двигатель; 8 - пластмассовый бак для воды; 9 – водило; 10 – блок крепления бака; 11 – устройство натяжения ремня; 12 – амортизатор водила; 13 – моторная рама; 14 – ручка.
Рисунок 2 – Конструкция виброплиты
Плиты подразделяют на следующие типы:
По эксплуатационной массе:
- сверхлегкие - до 100 кг;
- легкие - от 101 до 200 кг;
- средние - от 201 до 500 кг;
- тяжелые - массой свыше 500 кг.
По способу передвижения:
- самоходные нереверсивные (одноходовые) - (с перемещением в процессе уплотнения только вперед) ПВУСО;
- самоходные реверсивные (с перемещением в процессе уплотнения вперед и назад) ПВУСР;
По виду топлива и источника энергии:
- Виброплита бензиновая(рис. 3). Это наиболее простой вид виброплиты для уплотнения грунта. Данное оборудование оснащено бензиновым двигателем. Благодаря этому виброплита бензиновая с успехом применяется в местах где требуется автономная работа. Виброплита бензиновая очень проста в эксплуатации и использовании.
Рисунок 3 – Виброплита бензиновая
- Виброплита дизельная. Обеспечивает качественную утрамбовку сыпучего грунта. Виброплита дизельная используется при строительстве дорожных покрытий пандусов пешеходных дорожек. Виброплита дизельная не имеет привязки к постоянным источникам питания что расширяет сферу ее применения.
- Виброплиты электрические(рис.4). Обеспечивают удобное и комфортное применение в строительно-ремонтной области. Виброплиты электрические значительно дешевле чем другие аналоги виброплит для вибротрамбовки. Единственный минус – зависимость от источника питания.
Рисунок 4 – Виброплита электрическая
В нормативных документах на плиты конкретных моделей рекомендуется устанавливать:
- эксплуатационную массу;
- ширину уплотняющей поверхности;
- частоту вибрации или частоту вращения вибровозбудителя;
- скорость перемещения плиты;
- глубину уплотнения для различных видов уплотняемого материала;
- производительность плиты;
- габаритные размеры;
- вместимость бака для воды;
- мощность двигателя;
- время работы без дозаправки топливом.
В нормативных документах на плиты конкретных моделей должны быть указаны следующие показатели эргономики и охраны окружающей среды:
- параметры вибрации на органах управления плитой;
- выброс вредных веществ с отработавшими газами из системы выпуска двигателя в соответствии с ГОСТ 17.2.2.03 или ГОСТ Р 17.2.2.07 (по документации на двигатель).
Для плит конкретных моделей проектируемых после введения в действие настоящего стандарта рекомендуется следующая структура условного обозначения (индексации):
Пример условного обозначения вибрационной уплотняющей самоходной нереверсивной плиты эксплуатационной массой 114 кг с уплотняющей поверхностью шириной 400 мм третьей модели:
то же реверсивной плиты эксплуатационной массой 148 кг с уплотняющей поверхностью шириной 500 мм второй модели:
Обзор и анализ существующих конструкций вибрационных плит по литературе патентам отчетам по НИР и ОКР периодическим изданиям и интернету
Основными частями самопередвигающихся виброплит (рис. 5) являются рабочая плита вибратор подмоторная рама двигатель трансмиссия система подвески механизмы управления [2]. Плиты изготавливаются из стали литыми или сварными. На плите жестко закреплен вибровозбудитель. Привод его осуществляется клиноременной передачей от двигателя внутреннего сгорания установленного на подмоторной раме. На некоторых моделях виброплит применяются электродвигатели. Самопередвижение виброплиты происходит за счет наклона к вертикали суммарной вынуждающей силы вибратора.
Рисунок 5 – Самопередвигающаяся вибрационная плита Д-605 весом 250 кГ
Управление почти всеми плитами — ручное при помощи рукоятки. Выпускаются также виброплиты с механизированным управлением: механизация управления обеспечивается за счет применения вибровозбудителей специальной конструкции.
– ведомый шкив; 2 – крайний дебаланс; 3 – средний дебаланс; 4 - шестерня; 5 –
червячная передача; 6 – паразитная шестерня; 7 – корпус вибратора; 8 – вал.
Рисунок 6 – Схема вибратора самопередвигающейся виброплиты с механизированным управлением: а - с тремя дебалансами; б – с четырьмя дебалансами;
На рисунке 6а показана схема вибровозбудителя с тремя дебалансами расположенными в одном корпусе 7. Средний дебаланс 3 жестко закреплен на общем валу 8 возбудителя и по своему статическому моменту массы равен сумме статических моментов массы двух одинаковых крайних дебалансов 2 установленных на валу на подшипниках качения. Вал вибровозбудителя вращается на подшипниках качения установленных в боковых крышках корпуса. Корпус вибровозбудителя имеет цилиндрическую форму. К нижней части корпуса приварены лапы при помощи которых он прикрепляется к плите. Привод возбудителя осуществляется двумя клиноременными передачами . Изменение направления вращения правого или левого подвижных дебалансов оператор производит штурвалом при помощи червячных 5 и цилиндрических шестеренчатых 4 передач.
При вращении червячных шестерен вперед или назад цилиндрические шестерни будут поворачивать на необходимый угол крайние' дебалансы и этим изменять направление суммарной вынуждающей силы и следовательно направление движения виброплиты.
При положении всех трех дебалансов т. е. среднего и двух крайних под углом наклона около -30o к горизонтальной поверхности виброплита будет двигаться вперед при установке их под углом 90° виброплита будет работать на месте и совершать вертикально направленные колебания а при установке под углом — 30° к горизонтальной поверхности виброплита будет двигаться назад.
При изменении положения одного из крайних дебалансов виброплита будет поворачиваться соответственно вправо или влево а при положении одного дебаланса вперед а другого назад будет происходить разворот машины на одном месте.
Направление суммарной вынуждающей силы под углом близким к ±30° к горизонтальной поверхности является оптимальным как для уплотнения так и для передвижения.
На рисунке 6 б показана возможная схема вибровозбудителя самопередвигающейся виброплиты с механизированным управлением. На общем валу установлены четыре дебаланса (2 и 3). Крайние дебалансы 2 выполнены совместно с приводными шкивами 1 возбудителя установленными жестко на валу. Средние дебалансы 3 установлены на подшипниках качения и соединены посредством цилиндрических шестерен 4 с червячным колесом. Положение средних дебалансов оператор может изменять при помощи штурвала изменяя этим направление действия вынуждающей силы. В том случае когда горизонтальные составляющие средних дебалансов направлены в одну сторону т. е. совпадают происходит самопередвижение машины а в том случае когда между ними образуется некоторый угол происходит поворот плиты в сторону меньшей горизонтальной силы.
На некоторых моделях самопередвигающихся виброплит в передней части устанавливается кабестан предназначенный для самовытаскивания вибро.плиты при застревании канатом прикрепленным к грунтовому якорю. Вращается кабестан от общего двигателя при помощи цепной передачи.
Для увеличения производительности виброплит предусматривается устройство позволяющее производить сцепку от двух до шести штук установленных в один ряд которым управляет один оператор (рис. 7 а). Повороты производятся путем включения вибратора одной или двух крайних виброплит (рис. 7 б в). С целью увеличения ширины уплотняемой полосы на некоторых плитах устанавливают съемные боковые уширители. Для перевозки виброплит с одного строительного объекта на другой предусматриваются съемные транспортные колеса на пневматических шинах и дышло.
Рисунок 7 - Сцеп из четырех самопередвигающихся виброплит: а – общий вид; б в – схемы поворота.
Установка подмоторной плиты с двигателем на амортизаторах предохраняет двигатель и трансмиссию от колебаний создаваемых вибровозбудителем. В качестве амортизаторов в виброплитах широкое' применение получили спиральные пружины. На некоторых виброплитах предусматривается установка пружин в вертикальной и горизонтальной плоскостях (рис. 8).
– горизонтальная пружина; 2 – вертикальные пружины; 3 – подмоторная рама
Рисунок 8 – Конструкция подвески подмоторной рамы самопередвигающейся виброплиты
Существует конструкция вибротрамбующей машины представленной на рисунке 9 [12]. На опорной плите установлены вибраторы которые приводятся во вращение от двигателя через клиноременную передачу. Для амортизации двигателя служат пружины.
Рисунок 9 - Самопередвигающаяся вибрационная плита
Виброэлементы могут быть ненаправленного и направленного действия (рис. 10). В последнем случае виброэлемент состоит из двух вращающихся в разные стороны с одинаковой угловой скоростью эксцентриков расположенных таким образом что в каждый момент времени горизонтальные составляющие центробежных сил уравновешаны а вертикальные составляющие суммируются. При ненаправленных колебаниях опорная плита совершает круговые колебательные движения а в случае вибратора направленного действия колебания происходят только в напрвлении оси вибратора ОО (рис. 10 а).
Если корпус вибратора направленного действия повернуть относительно шарнирной оси его крепления (рис. 10 в) то его вертикальная ось ОО наклонится и перейдет в положение О1О1. При этом изменится направление суммарной возмущающей силы. За счет горизонтальной силы может происходить перемещение вибратора. На этом принципе и основано передвижение самопередвигающихся вибрационных плит.
Рисунок 10 – Схемы вибраторов: а – ненапрвленного действия; б – направленного действия; в – маятникового типа.
Известна конструкция виброплиты [9] включающая дебалансный механизм уплотняющую плиту и привод дебалансного механизма уплотняющая плита снабжена зубьями установленными на поверхности плиты предназначенной для контакта с уплотняемым материалом при этом площадь поверхности плиты на которой установлены зубья не превышает половины всей площади поверхности плиты предназначенной для контакта с уплотняемым материалом (рис. 11 и 12).
Недостатком этой виброплиты является то что для уплотнения связных грунтов необходимо производить несколько проходов виброплиты по одной и той же полосе уплотнения.
В основу изобретения поставлена задача усовершенствования конструкции виброплиты для снижения энерго- и трудоемкости процесса уплотнения связных грунтов путем уплотнения последних меньшим числом проходов виброплиты.
Предложенная конструкция виброплиты позволяет уплотнять связные грунты которые ранее не могли быть уплотнены до требуемой плотности существующими самопередвигающимися плитами.
Рисунок 11 – Общий вид виброплиты вид спереди
Рисунок 12 – Общий вид виброплиты вид сбоку и снизу
Известна конструкция виброплиты [10] содержащей дебалансный механизм ненаправленного действия уплотняющую плиту двигатель внутреннего сгорания клиноременную передачу амортизаторы рукоять управления дебалансный механизм ненаправленного действия установлен на уплотняющей плите с возможностью фиксированного перемещения в направляющих(рис. 13).
Недостатком этой виброплиты является то что в процессе уплотнения материала свойства среды изменяются и это требует изменения режимов работы виброплиты а конструкция виброплиты не позволяет изменять режим уплотнения. Основное правило уплотнения грунта это постепенное повышение давления на грунт. Это ведет к созданию призмы волочения перед передней кромкой виброплиты неравномерной плотности по глубине уплотнения появлению волнистой поверхности.
Эти явления присущи существующим самопередвигающимся виброплитам так как они имеют постоянные параметры и режимы работы соответствующие концу уплотнениия.
В связи с тем что дебалансный механизм ненаправленного действия установлен на виброплите с возможностью фиксированного перемещения обеспечивается регулировка контактных давлений и изменения скорости передвижения виброплиты.
Рисунок 13 – Общий вид виброплиты с горизонтальным фиксированным перемещением дебалансного механизма.
Известна трамбовочная виброплита [11] содержащая рабочую плиту на которой размещен вибратор с возбудителем колебаний в видевала центр массы которого смещен относительно оси вращения в радиальном направлении и несущую раму на которой размещен приводной двигатель вибратора причем вибратор и двигатель связаны между собой ременной передачей через шкивы закрепленные на валу вибратора и на валу приводного двигателя на котором также установлена центробежная муфта сцепления(рис. 14).
При работе этой виброплиты вызываемы вибратором изменения положения рабочей плиты относительно несущей рамы а следовательно пульсирующие изменения расстояния между осями вращения роторов двигателя и вибратора и силы натяжения приводного ремня приводят к преждевременному износу и разрушению ремня и к дополнительной нагрузке на опорные подшипники валов вибратора и приводного двигателя и как следствие выходу из строя виброплиты.
Задача изобретения решена в трамбовочной виброплите содержащей рабочую плиту на которой размещен по крайней мере один вибратор с возбудителями колебаний в виде вала центр массы которого смещен относительно оси вращения в радиальном направлении (рисунок 15) и несущую раму на которой размещен приводной двигатель вибратора причем вибратор и двигатель связаны между собой ременной передачей через шкивы закрепленные на валу вибратора и на валу приводного двигателя а расстояние от оси вращения шкива вибратора до внутренней образующей профиля рабочей поверхности шкива выполнено переменным в радиальном относительно оси вращения шкива совпадающей с осью вращения вала вибратора направлении(рисунок 16). Максимальное изменение расстояния от оси вращения шкива вибратора до внутренней образующей профиля его рабочей поверхности в радиальном направлении не превышает удвоенную величину максимального изменения расстояния между осями валов двигателя и вибратора при работе виброплиты.
Рисунок 14 – Общий вид виброплиты
Рисунок 15 - Схема выполнения вибратора
Рисунок 16 – Схема установки шкива вибратора
Постановка задач по усовершенствованию существующих конструкций
В данном дипломном проекте ставится задача усовершенствовать имеющуюся конструкцию виброплиты путем замены двигателя MOTOR JIKOV 1509 на менее мощный и более экономичный двигатель HONDA GX240(рис. 17).
Рисунок 17 – Двигатель HONDA GX240
Разработать новую конструкцию подмоторной рамы которая позволяет уменьшить действие вибрации на оператора и на двигатель за счет применения упругих элементов в виброопоре.
Усовершенствовать конструкцию ведомого шкива разгружающий вал от действия сил клиноременной передачи за счет передачи вращения на вал через фланец . Это позволит снизить нагрузки на подшипники и вал увеличить их долговечность.
Конструкторская часть
1 Расчет основных элементов вибрационной плиты
1.1 Статический расчет виброплиты [1]
К основным показателям виброплит относят: размеры рабочей площади вес частоту колебаний величину вынуждающей силы скорость передвижения и мощность двигателя. Их выбирают на основании данных найденных экспериментальным путем.
Вынуждающая сила - 28 кН;
Максимальная скорость передвижения – ma
Вес виброплиты 315 кг(3090 Н)
)Минимальный размер площади основания виброплиты должен быть больше толщины уплотняемого слоя т.е. B ≥ h
где В – размер основания плиты в направлении движения в м;
-скорость движения виброплиты в мсек;
t – время необходимое для полного уплотнения материала;
m – необходимое число проходов по одному месту обычно m=2..4
B= (t)n=(0416c3125)2=065 м
По рекомендациям [1] длина виброплиты L можно принять равной (1..115) от ширины B
Принимаем L=700 мм =07 м
)Необходимое время вибрирования можно определять по формуле:
где С – число повторностей приложения нагрузки необходимое для доведения грунта до требуемой плотности С=1500-15000;
n – частота колебаний вибратора в минуту
)Площадь основания плиты:
)Удельное статическое давление виброплиты:
p = Q F =3090 0455=6791 Па
где Q – вес виброплиты ;
F – площадь основания виброплиты.
)Средняя скорость передвижения плиты ориентировочно может быть определена по формуле
ср= (tg α) (√22+1) мс где
– частота вращения дебалансов за которое происходит один удар плиты =1;
α – угол наклона суммарной вынуждающей силы α=35о.
ср= (314107) (√314212+1)=067 ммин
)Производительность самопередвигающейся виброплиты:
П=3600 (B-02) в m м2ч где
(B-02) – ширина вибрационной плиты с учетом необходимого перекрытия следа предыдущего прохода в м.
в – коэффициент использования машины по времени с учетом поворотов в=07 08.
П=(B-02) в m =3600 ((065-02) 0416 075 ) 2=25272 м2 ч
Тяговый расчет виброплиты
)Мощность двигателя:
Nдв= Nпер + Nвд + Nтр =417+064+02=501кВт
где Nпер – мощность затрачиваемая на передвижение виброплиты;
Nвд – мощность необходимая для поддержания колебаний виброплиты; Nтр- мощность необходимая для преодоления трения в опорах вала вибратора.
Nпер= (WV) = (2400 0416)085=417 кВт
где – общий КПД передач от двигателя к вибратору =085;
W – суммарное сопротивление передвижению машины.
W=W1+W2+W3+W4 =2163+927+136+1312=2400 Н;
Входящие в эту формулу составляющие определяются следующим образом.
)Сопротивление передвижению виброплиты по поверхности грунта:
W1 =1Q =309007=2163 Н
где 1 – коэффициент сопротивления перемещению виброплиты 1=06 07 ;
)Сопротивление на преодоление подъема уплотняемой поверхности:
W2 = Qα = 3090003=927 Н
где α – подъем в процентах.
)Сопротивление призмы волочения уплотняемого материала перед площадкой виброплиты:
где 2 – коэффициент внутреннего трения уплотняемого материала для несвязных грунтов 2=06 08;
– коэффициент сопротивления перемещению призмы грунта по грунту 2=05 09;
Q3 – коэффициент сопротивления перемещению призмы грунта по грунту;
Q1 – вес призмы волочения.
Q1 =981ρ (05BH 2) tg φ1 =9811700(05065005 2) tg 45=136 Н
где B – ширина призмы волочения примерно равна ширине площадки плиты;
ρ=1700 кг м3 – плотность грунта;
H – высота призмы волочения можно принять (06 08) от высоты площадки плиты;
φ1 – угол естественного откоса грунта примерно равен φ1=45o
)Сопротивление от преодоления сил инерции:
W4= (Q ) (gt)= (3090 0416 ) (9811)=1312 Н
где g – ускорение свободного падения;
t - время разгона c.
) Мощность двигателя для поддержания вращения вибровальцов:
Nвд =((088 116) 10-8 (Gr)2n3) ( Qвв ) кВт где
Gr – статический момент дебалансов Gr=2S=201=02 Нм;
Qв – вес вибровальца Qв 40 Н;
Nвд =(116 10-8 02236003) ( 40085 )=064 кВт
) Мощность необходимая для преодоления трения в опорах вала вибратора:
Nтр=(057 10-8 dпGrn3) в кВт где
d – диаметр посадочного места вала под подшипник м;
п – приведенный коэффициент трения подшипника качения п=0006
Nтр=(05710-8 00500060236003) 085=002 кВт
1.2 Расчет фрикционной многодисковой муфты [23]
Расчет фрикционных муфт производится на износостойкость и ограничение давления на рабочих поверхностях.
) Расчетный момент определяется по уравнению:
где — коэффициент запаса сцепления учитывающий возрастание момента при перегрузках и вводимый с целью устранения буксования. Обычно принимается = 125 - 15 в зависимости от возможной величины перегрузки; Мк - номинальный крутящий момент.
) Номинальный крутящий момент:
Mк =(R 2-r2) Rсрi[p] f где
Rср - средний радиус поверхности трения; f - коэффициент трения f= 03-035 для асбестовых обкладок по стали или чугуну при работе всухую. Конструктивно примем радиусы диска:
r=46 мм; R=(15-25) d=59 мм;
Rср = (r+ R)2=(46+59)2=525 мм.
) Допускаемое удельное давление:
где [ р0 ]=2010-2 МПа – удельное давление асбестовых обкладок по стали или чугуну при работе всухую;
k1 - коэффициент в зависимости от средней окружной скорости поверхности трения k1=05;
k2 – коэффициент учитывающий число ведущих дисков при
k3 – коэффициент учитывающий количество включений муфты в час k3=1 при 90 и менее включений в час.
[р]= [р0] k1k2k3=2010-2050941=9410-2 МПа
Mк =(R 2-r2) Rсрi[p]f =314(0059 2-0046 2) 00525594104 0314=2266 Н м
Mр = Mк=142266=3172 Н м
Наибольший крутящий момент двигателя Honda GX240 153 Нм при 2500 обмин таким образом данная муфта нам подходит.
) Усилие для включения дисковой муфты приведенное к оси муфты определяется по уравнению:
Q= Mр ( Rсрif ) = 3172 (00525503)=40279 Н
) Давление на рабочую поверхность дисков:
p=(4Q) ((D 2-d 2))= (440279) (314(0118 2-0092 2))=00574 МПа
p ≤ [p]- по допускаемым удельным давлениям проходит
Конструктивно примем пружины со следующими параметрами:
G =75000 МПа – модуль сдвига;
n=7 – число рабочих витков;
d=25 мм – диаметр прутка;
D=125 мм – средний диаметр пружины;
Z=6 – количество пружин в муфте сцепления.
A=2700000 – напряжение соответствующее 1Н нагрузки приложенной к пружине;
B=187000 – жесткость одного витка;
) Осевая сила действующая на одну пружину:
Fпр = Q Z =40279 6=6713 Н
Из следующих зависимостей найдем другие параметры:
) Напряжения в пружине:
= AFпр =27000006713=18125 МПа
) Деформация пружины:
= (Fпрn) B=(67137)187000=00025 м =25 мм
) Жесткость пружины:
С= B n =187000 7 =26714 Н м = 267 Нмм
1.3 Расчёт клиноременной передачи [4]
Расчет клиноременной передачи заключается в определении размеров ремня в зависимости от заданных условий работы. В результате расчета клиноременной передачи устанавливаются нагрузки основные размеры деталей (шкивов валов опор и др.) определяется долговечность ремня.
Исходные данные для расчёта:
–передаваемая мощность — 59 кВт;
–частота вращения ведущего шкива — 3600 обмин;
–передаточное число ирем = 10.
) Выбираем тип сечения ремня:
Подходит ремень типа "Б".
Технические данные ремня:
мм; мм; мм; см2; мм (минимальный диаметр шкива)
Рис. 1 - Сечение клинового ремня
) Определяем диаметры шкивов:
Из стандартного ряда . Выбираем мм.
Диаметр ведомого шкива мм.
По ГОСТ 1284.3 - 80 принимаем мм.
) Уточняем передаточное отношение с учетом относительного скольжения S=001
Определяем относительную ошибку:
Останавливаемся на этом варианте.
) Определяем диапазон межосевого расстояния
Принимаем конструктивно значение равное:
) Определяем расчетную длину ремня
Ближайшее стандартное значение: мм
) Уточняем межосевое расстояние
) Определяем угол обхвата ремнем малого шкива
Что больше допускаемого значения т.е. условие удовлетворяется.
) Находим максимальную мощность передаваемую одним ремнем
Для типа сечения "Б" и длины ремня до 1120 мм берем Р0=576 кВт
) Определяем расчетную мощность на один ремень
где - коэффициент угла обхвата. С=1.
СL - коэффициент длины. СL=085.
СР - коэффициент динамической нагрузки - тип двигателя II 2 смена СР=15.
) Определяем число ремней
Предварительно принимаем Z=3 тогда по данным находим СZ=070-082.
Округляем расчетное число ремней до Z=3.
) Находим скорость ремней
) Число пробегов ремней
) Определяем полезную окружную силу:
Ft=P11000V=5910003391=17399 Н
) Касательные напряжения
t= Ft (zAp)=173993138=042 МПа
=12 МПа- начальное напряжение в ремне
) Нормальные напряжения в ведущей ветви:
n1=+2=12+0422=141 МПа
) Нормальные напряжения в ведомой ветви:
n2=-2=12-0422=099 МПа
) Примем E=80 МПа и определим напряжения изгибов в ремне:
ведущая ветвь: u=Ed1=60105180=35 МПа
ведомая ветвь: u=Ed2=60105180=35 МПа
) Напряжения в ремне от действия центробежных сил:
ρ=11-12 гсм; принимаем ρ=1100 кгм
= ρV10=1100339110=126 МПа
) Напряжения в ветвях:
= n1+u+=141+35+126=617 МПа
=n2+u+=099+35+126=575 МПа
==617 МПа (максимальное напряжение в ветви);
) Определяем силы действующие на валы:
F= zAp=1210313810=4968 Н
F=2Fsin(α2)=24968sin(1802)=9936 Н
)Определяем долговечность плоскоременной передачи:
-1=9 МПа N=10-базовое число циклов нагружений
Коэффициент учитывающий передаточное число ременной передачи:
Коэффициент учитывающий постоянство нагрузки: С=18;
Показатель степени m=8 (т.к. клиноременная передача);
L=( ) (N С С)(3600 i )=(9617)8 (107181)(360023027)=169272 часов
Уточняем частоту и крутящий момент на валу:
n3=n1Uрп=3600101 = 356436 обмин
P3 = P2 п.п з=5490099098=5326 Вт
T3=955P2n2=9555326356436 = 1427 Нм
1.4 Расчет зубчатой передачи быстроходной ступени [4]
При расчете необходимо определить минимальные размеры передачи которые обеспечивали бы ее работоспособность в течение заданного срока службы. Наиболее рациональное решением такой задачи возможно при проведении прочностного расчета с учетом влияния на нагрузочную способность передачи геометрических параметров зацепления термической и химико-термической обработкой. Из анализа работы зубчатой очевидно что зубья под действием нормальной силы и силы трения находятся в сложном напряженном состоянии.
Решающее влияние на работоспособность передачи оказывают контактные напряжения и напряжения изгиба . В современных методиках расчета основным критерием расчета зубчатых передач принята контактная усталость поверхности зубьев.
–передаваемая мощность — 549 кВт;
–частота вращения шестерни — 356436 обмин;
–передаточное число и = 1.
Выбираем материалы со средними механическими характеристиками по табл. 16.2.1 [1]:
Для шестерни и зубчатого колеса:
Термическая обработка: улучшение
а) Расчет допускаемых контактных напряжений при расчете на усталость:
)Определяем число часов работы передачи за весь срок службы:
L=L365K8Kсnсм =8365068204=112128 часа
)Определяем базовое число нагружений:
N=30 (HB1)=30 (240)=154710≤12010
N=30 (HB2)=30 (240)=154710≤12010
)Расчетное число циклов нагружений:
N=601356436112128=239810
Ci – число зацеплений зуба за один оборот
ni – число оборотов в минуту рассчитываемого колеса
Lh – число часов работы передачи за весь срок службы (в часах)
т.к. N N выбираем формулу расчет коэффициента долговечности:
)Предел контактной выносливости:
=2НВi + 70 МПа – для улучшенных колес
)Коэффициент контактной выносливости:
- предел контактной выносливости
ZNi – коэффициент долговечности
SHi – коэффициент запаса прочности (SHi=11)
=(55011) 090995=44775 МПа
=(55011) 090995=44775 МПа
)Допускаемые напряжения для передачи:
=min ( )=min =44775 МПа
б )Допускаемые напряжения изгиба:
=175НВ1=175240=420 МПа
=175НВ2=175240=420 Мпа
)Базовый предел выносливости (изгибной):
= YaYz – для улучшенных колес
причем Ya=1; Yz=1(поковка)
= YaYz=42011=420 МПа
Коэффициент запаса: SF1= SF2=17 и gF=6
)Расчетное эквивалентное число циклов нагружений:
NFE1=601356436112128=239810
NFE2=601356436112128=239810
)Коэффициент долговечности:
Поскольку NFEi > NFlimi принимаем YN1=YN2=1
И определяем напряжения изгиба (при расчете на усталость):
=(420 МПа 17) 1=24706 МПа
в) Определение кинематических параметров передачи:
)Определяем межосевое расстояние по формуле:
Ka – коэффициент равный 490 для прямозубых передач
U – передаточное число зуб. передачи («+» внешнее зацепление «–» внутреннее зацепление)
T2 – крутящий момент на ведомом колесе Нм
- коэффициент учитывающий неравномерность распределения нагрузки по длине контактной линии
- коэффициент ширины зубчатого колеса (венца)
По рекомендации приняли =0125
u=1 – передаточное отношение
T2=955P3n3=9555330356436=1428 Нм – крутящий момент на втором валу
=44775 МПа – допускаемое контактное напряжение
=05 (u+1)=050125 (1 +1)=0125
по определяем коэффициент
aw 490 (1 +1) =8183 мм
по ГОСТу конструктивно принимаем aw = 160 мм
)Определяем ширину зубчатого венца:
b= aw=0125160=200 мм
b= b+(2 4) = 20+2 = 22 мм
)Определяем модуль зацепления:
mn =(0015-003) aw = 0015160=25 мм
)Определяем суммарное число зубьев
)Определяем число зубьев меньшего (ведущего) колеса:
Z1= Z(u+1)=128(1+1) = 64
Z2= Z- Z1=128– 64 = 64
)уточняем передаточное отношение:
)Определяем геометрические параметры зубчатых колес:
dw1= mn Z1 = 2564= 160 мм
dw2= mn Z2 = 2564= 160 мм
)Уточняем межосевое расстояние:
aw = (dw1+ dw2) 2 = (160 +160) 2 = 160 мм
)Определяем диаметры вершин:
da1= dw1 + 2 mn = 160 + 225 = 165 мм
da2= dw2 + 2 mn = 160 + 225 = 165 мм
)Определяем диаметры впадин зубьев:
df1= dw1-25 mn =160 –2525 =15375 мм
df2= dw2-25 mn = 160 – 2525 = 15375 мм
)Определяем окружную скорость в зацеплении:
V = (dw1n1) (601000) = (314160356436) (601000) = 2985 мс
в зависимости от окружной скорости выбираем степень точности – 7-с
)Определяем усилия действующие в зацеплении:
окружная: Ft = (2T1) dw1 = (21471) (1605 10) = 18388 Н
радиальная: Fr = Ft tn(α) = 18388 10036397 = 6693 Н
n3=n1Upп=3564361 = 356436 обмин
T3=955P2n2=9555490356436 = 1471 Нм
г) Выполняем проверочный расчет на контактную усталость:
) Удельная расчетная окружная сила:
WHT=FTKHKHKHVKA b2=18388121021613520=243 Hмм
KA =135 (табл 4.2.9)[4]
KH=12 (табл 4.2.11)[4]
KHV=16(табл 4.2.8 [4])
) Контактные расчетные напряжения:
H=ZHZZE (WHT (U+1))(dw1 U)= 177 275 1 (243 2)(160 1)=
=26827≤44775 МПа –условие выполняется
д) Выполняем проверочный расчет на изгибную усталость:
WFT = FtKfαKfKfvKA b2 = 18388 2110101 20 = 195 Нмм
Kfv = 21 (табл 4.2.8 [4])
Kfα = 10 (табл 4.2.11)[4]
Kf = 101 (рис 4.2.3.(в)) [4]
)Эквивалентное число зубьев:
)Определяем коэффиценты YFSi :
YFS1 = 371; YFS2 = 371 (рис. 4.2.5) [4]
FP1 YFS1 = 24706371 = 6659
FP2 YFS2 = 24706371 = 6659
) Напряжения изгиба:
F= YFS1YYWFT mn = 3711119525 = 2894 Мпа ≤ 24706 Мпа где
Y = 1 – коэффициент учитывающий перекрытие зубьев;
- коэффициент учитывающий наклон зубьев.
1.5 Расчет дебаланса [1]
В соответствии с исходными данными Fвын=28 кН n2 =356436 обмин спроектируем необходимые размеры дебаланса.
)Центробежная сила от 1 дебаланса (В нашей схеме 2-ух вальный вибратор направленных колебаний):
Fц = Fвын 2 = 282 =14 кН
)Статический момент дебаланса найдем:
S= Fц 2=14000(37307)2=010059 Нм где -угловая скорость дебалансного вала;
=(n30)=(31435643630)=37307 с-1
)Конструктивно примем эксцентриситет дебаланса r = 15 мм угол α=30о тогда масса дебаланса равна:
mд=S r=010059(9811510-3)=0688 кг
Возьмем для изготовления дебалансов материал Сталь45 ГОСТ 1050-88 с объемной плотностью ρ=782 тм.3
С помощью ЭВМ сконструируем геометрическую форму дебаланса(рис.18) у которого площадь сечения F=527928 мм2.
)Ширина дебаланса тогда равна:
l= mд (F ρ)=(068852792810-6 782)=001668 м = 1688 мм
Рисунок 18 – Дебаланс
1.6 Расчет валов виброблока [4]
Для проектирования валов виброблока составим расчетные схемы нагружения валов с учетом действующих на них сил. Полученные результаты отразим в расчетах и эпюре.
Применим конструкцию разгружающую консоль вала от действия нагрузки от клиноременной передачи.
а) Первичный вал виброблока
Определяем реакции опор для этого составляем уравнения моментов относительно опор A и B в двух плоскостях: Плоскость H и Плоскость V
Fr69- Fad12 + RbH114=0;
RbH = - Fr69114 = - 669369114= - 4051 H
- RaH 114 – Fr45 =0;
RaH = - Fr45114 = -669345114= -2642 H
Проверка: RaH +Fr + RbH = -2642+6693-4051=0
Ft69- Fц 35+ RbV 114=0;
RbV = (Fц35 - Ft69)114=(1400035 – 1838869)114=418695 H
-RaV114 + Fц79 - Ft45=0;
RaV= (Fц79 - Ft45)114=(1400079 – 1838845)114=962917 H
RaV+Ft - Fц + RbV = 962917+18388-14000+418695=0
Определяем полные поперечные реакции Ra и Rb в опорах A и B :
Определяем изгибающие моменты в характерных точках вала с построением эпюры изгибающих моментов: в плоскости H – MИH; в плоскости V – MИV
Определяем суммарные изгибающие моменты MИЗ в характерных точках вала с построением эпюры изгибающих моментов MИ
Строим эпюру крутящих моментов T и изгибающих моментов Mэкв передаваемых валом
Вычисляем эквивалентные изгибающие моменты Mэкв в характерных точках вала построением эпюры
Мэкв1 = 02 +14712= 1471Нм
Определяем расчетные диаметры вала в характерных сечениях:
здесь где (табл. 16.2.1 [1])=5 . Материал вала: Сталь 5.
Конструктивно назначаем диаметр под шестерню и дебаланс d=60 мм под подшипники d=50 мм
а) Вторичный вал виброблока
1.7 Подбор подшипников виброблока [4]
Условное обозначение подшипника
Так как имеет место прогиб вала под действием центробежной силы дебаланса то применим сферический двухрядный самоустанавливающийся подшипник с внутренним диаметром d=50мм выбранный из таблицы 7.10 [1].Осевая нагрузка отсутствует так как передача зубчатая прямозубая. (X и Y - коэффициенты радиальной и осевой нагрузки)
Определяем отношение Fa Co=0 так как нет осевой составляющей силы
Определяем соотношение Fa (VFrб)=0e
Отсюда следует X=1; Y=0;
Определяем эквивалентную динамическую радиальную нагрузку по формуле:
Pr=[XVFrб+YFa] KДKТ где
KД – коэффициент учитывающий динамичность внешней нагрузки (табл. 7.5.3 [1])
KТ – коэффициент учитывающий влияние температуры подшипникового узла (табл. 7.5.4 [4])
V – коэффициент вращения (V=1)
Frб - наибольшая полная поперечная реакция
Pr=[XVFra+YFa] KДKТ=[11962921+0] 11=962921 Н
Определяем и сравниваем долговечность подшипника с долговечностью редуктора
n – частота вращения кольца
m – показатель степени (для шариковых m=3 )
C – динамическая грузоподъемность (табл. 7.10 [4] )
1.8 Проверка прочности шпоночных соединений [5]
Призматические шпонки выбранные для вибратора проверяем на смятие.
Проверку проводим для шпонки под дебалансом и шестерней:
см = 2T d Aсм =2Tdlр (h-k)≤ []cм
где T — момент на валу Нм
Acм— площадь смятия м2
lр = l – b — рабочая длина шпонки (lр = l – b=0063-0018=0045 м)
[]cм – допускаемые напряжения на смятия ([]cм= 180 МПа)
[]cм – допускаемые напряжения на смятия ([]cм= 100 МПа)
см = 214710060045 (0011-0007)=272МПа 180 МПа
ср = 2147100180045 006=061МПа 100 МПа
что удовлетворяет проверочному расчёту.
Проверку проводим для шпонки под дебалансом и зубчатым колесом:
см = 214270060045 (0011-0007)=264МПа 180 МПа
ср = 2142700180045 006=059 МПа 100 МПа
2 Разработка конструкции
Рисунок 19 – Общий вид двигателя HONDA GX240
Четырехтактный бензиновый двигатель Honda GX240 с верхним расположением клапана цилиндра (OHV) горизонтальным валом и воздушным охлаждением цилиндр расположен под углом 25°. Профессиональные двигатели GX рассчитаны на постоянную работу в течение длительного времени.
Модель двигателяGX240
Фирма производительHonda
Тип двигателя4-тактный OHV
Объём двигателя242 см. куб.
Мощность двигателя59 кВт (8 л.с.) 3.600 обмин
Полезная мощность5.3 кВт (7.1 л.с.) при 3.600 обмин
Мощность на валу4.4 кВт (5.9 л.с.) 3.000 обмин
1 кВт (6.8 л.с.) 3.600 обмин
Крутящий момент max.153 Нм 156 кгм 2.500 обмин
Диаметр x Ход поршня 73 x 58 мм
Расход топлива313 гкВт.ч - 230 гл.с.ч
Система зажиганиятранзисторная
Ёмкость топливного бака л5.3 л
Объём масла в картере л1.1 л
Запуск ручной (опция - электрический)
Базовые габариты380 x 430 x 410 мм
Размер вала: в зависимости от модификации
Топливо: бензин от АИ92
Масло (рекомендованное)10W30 10W40
ОСОБЕННОСТИ ДВИГАТЕЛЯ HONDA GX240
Самая высокая мощность для этого литража.
Все компоненты разработаны для длительного использования.
Все компоненты двигателя Honda GX240 высоконадежны.
Самое низкое потребление топлива в своей категории.
Уникальная технология Honda.
Легко найти запчасти и расходные материалы.
Рисунок 20 – Подмоторная рама
Рисунок 21 - Виброопора
Конструкция ведомого шкива разгружающая вал от действия сил клиноременной передачи за счет передачи вращения через фланец (рисунок 22).
Рисунок 22 – Ведомый шкив
Технологический процесс изготовления зубчатого колеса виброблока
1 Назначение детали и выбор заготовки [67]
Изготавливаемая деталь (рис. 23) – зубчатое колесо материал – Сталь 40Х ГОСТ 4543-75 служит для передачи вращения в виброблоке.
Рисунок 23 – Колесо зубчатое
В качестве заготовки для изготовления зубчатого колеса принимаем круг диаметром 170 мм.
2 Проектирование маршрута обработки. Выбор оборудования
Маршрут обработки выбранной заготовки включает следующие операции:
5 –Отрезная (Отрезать от круга заготовку длиной 52 мм);
Переход 1 (Сверлить отверстие диаметром 25 мм);
Переход 2 (Сверлить отверстие диаметром 45 мм);
Переход 3 (Расточить отверстие до диаметра 595 мм);
Переход 4 (Снять фаски);
5 – Токарная (Подрезать торцы);
Переход 1 (Точить наружные поверхности);
Переход 2 (Снять фаски);
5 – Зубофрезерная (Фрезеровать 64 зуба);
0 - Протяжная (Протянуть шпоночный паз);
5 – Термическая (Закалить заготовку);
0 – Шлифовальная (Шлифовать отверстие);
5 – Шлифовальная (Шлифовать зубья);
В таблице 1 сведен выбор оборудования и инструмента в соответствии с операциями.
Таблица 1 – Применяемое оборудование и инструмент при изготовлении зубчатого колеса
Станок токарный 1К625
Сверла 2301-0028 и 2301-0045 ГОСТ 10903-77
резец расточной 2145-0041 1 ВК6М ГОСТ 18063-72 резец 2112-0051 ВК8 ГОСТ 18880-73
Резец 2102-0073 ВК8 ГОСТ 18877-73
Резец 2102-0073 ВК8 ГОСТ 18877-73; резец 2112-0051 ВК8 ГОСТ 18880-73
Зубофрезерный станок
Фреза червячная модульная 2510-4037 ГОСТ 9324-80
Горизонтально-протяжной станок 7Б55
Протяжка 2405-1115.I ГОСТ 18217-90
Установка для закалки ТВЧ
Станок внутришлифовальный
Круг шлифовальный ПП 50x32x16 25А 25Н С2 7 К5 35мс А1 кл ГОСТ 2424-83
Зубошлифовальный полуавтомат 5В835
П 250x10x76 91А 16Н СМ1 7 К5 35мс А1 кл ГОСТ 3434-83
Штангенциркуль ШЦ-II- 250-630-01-1 ГОСТ 166-89
индикатор часового типа ИЧ02-0001 ГОСТ 577-68; штатив Ш-II Н ГОСТ 10197-70 нутромер 50-125-0001 ГОСТ 9244-75.
Комплект документов на технологический процесс изготовления зубчатого колеса представлен в Приложении Б.
3 Расчет режимов обработки и норм времени [6]
Расчет режимов обработки ведем по методике изложенной в [6]
Операция 010 – Токарная
Переход 1: Сверление отверстия 25 мм.
где D – диаметр отверстия
Подача выбирается по таблице 25 из [6] so=01ммоб.
По паспорту станка принимаем подачу s=01ммоб.
Скорость резания определяется по формуле:
где Сv - постоянный коэффициент (Сv=85);
Т - период стойкости мин ();
m y - показатели степени.
По таблицам из [6] m=02; y=05;
Кv - общий поправочный коэффициент на скорость резания учитывающий отличные от табличных условия резания.
где Кmv - коэффициент учитывающий марку обрабатываемого материала (Кmv=08);
Кuv - коэффициент на инструментальный материал (Кuv=09);
Расчет частоты вращения шпинделя станка:
Уточняем частоту вращения шпинделя по паспорту станка:
Произведем уточнение скорости резания по принятой частоте вращения:
Крутящий момент и рассчитываются по формуле из [7]:
Согласно таблице 32 из [7]: Cm=00345; y=08; q=2.
Необходимая мощность станка:
где - кпд станка ().
Мощность электродвигателя токарного станка 1К625 8 кВт следовательно условия резания выполняются.
Определяем длину рабочего хода суппорта
– длина резания мм (мм);
– величина подвода врезания перебега инструмента мм ();
–дополнительная длина хода инструмента вызванная особенностями наладки или конфигурации детали мм ();
Рассчитаем основное технологическое время
где L– длинa рабочего хода суппорта мм;
S- подача ммоб (ммоб);
n – частота вращения шпинделя обмин (обмин);
Переход 2: Сверление отверстия 50 мм.
Подача выбирается по таблице 25 из [6] so=05ммоб.
По паспорту станка принимаем подачу s=05ммоб.
s - подача ммоб (ммоб);
где Кmv - коэффициент учитывающий марку обрабатываемого материала (Кmv=122);
Кuv - коэффициент на инструментальный материал (Кuv=1);
Крутящий момент и рассчитываются по формуле из [6]:
Согласно таблице 32 из [6]: Cm=00345; y=08; q=2.
– длина резания мм ();
n – частота вращения шпинделя обмин ();
Растачиваем сквозное отверстие диаметром до диаметра длиной .
Глубина резания при снятии припуска за один рабочий проход
Назначаем период стойкости резца
где – скорость резания ммин ();
– коэффициент зависящий от обрабатываемого материала ();
– коэффициент зависящий от типа материала и стойкости инструмента ();
– коэффициент зависящий от диаметра прутка при его обработке ();
Рассчитываем число оборотов шпинделя станка
где – диаметр отверстия до которого нужно обработать поверхность детали мм ();
– скорость резания ммин (ммин).
Корректируем частоту вращения по данным станка и устанавливаем действительную частоту вращения .
Тогда уточним величины ммин по принятым значениям обмин
– величина подвода врезания перебега инструмента мм () ;
где – длинa рабочего хода суппорта мм ();
– частота вращения шпинделя обмин ();
где – осевая сила резания кН ();
– глубина резания мм ();
Необходимая мощность станка
где – сила резания кВт ();
– скорость резания ммин ();
Мощность токарного станка 1К625 8 кВт следовательно обработка возможна.
Операция 015 – токарная
Подрезаем торец детали с величину .
Назначаем подачу. По [6] .
Назначаем период стойкости резца в минутах основного времени .
где – диаметр обрабатываемой поверхности детали мм ();
– скорость резания ммин ().
Операция 020 – токарная
Протачиваем наружную поверхность детали с .
Назначаем подачу. по [6] .
– частота вращения шпинделя обмин ;
– глубина резания мм ;
Мощность токарного станка 16К20 8 кВт следовательно обработка возможна.
Операция 030 – протяжная
По таблице 3.19[6] находим подачу Sz =0075 мм на зуб.
По таблице 3.17[6] находим рабочую скорость резания Vрх = 4 ммин.
Обратная скорость протяжки по паспорту станка Vох = 20 ммин.
Необходимое усилие резания определяется по формуле:
где – усилие на 1 мм; (F=5 кгмм);
где – ход инструмента;
– количество одновременно обрабатываемых деталей;
где P– сила резания кВт ;
Vд – скорость резания ммин;
Мощность электродвигателя станка 7Б55 55 кВт следовательно условия резания выполняются.
Операция 040 – шлифовальная
Шлифуем отверстие до с .
Определим длину пути шлифовального круга по формуле
Подставив данные получим
Рекомендуемая скорость вращения шлифовального круга =25 мс [10].
Частоту вращения шлифовального круга определяем по формуле
Рекомендуемая скорость вращения детали =60 мс [6].
Частота вращения детали
Подставив значения в формулу получим
Принимаем по паспорту станка
Поперечная подача рассчитывается по формуле
При чистовом шлифовании поперечная подача на каждый ход стола t=001 мм.
Минутная подача определяется по формуле
Основное время определяем по формуле
Мощность затрачиваемая на вращение шлифовального круга
Потребная мощность электродвигателя
Для выполнения операции выбираем шлифовальный станок модели 3140 с мощностью двигателя N=4 кВт.
В дорожной отрасли довольно часто встречаются неудобные стесненные и относительно труднодоступные места для уплотнения грунтов щебеночных материалов и даже асфальтобетонных смесей. К таким местам относятся различного рода подземные прокладки труб коллекторов и кабелей в городских траншеях водопропускных труб и газовых пересечек на загородных дорогах места сопряжения мостов и путепроводов с дорожной конструкцией пазухи у колодцев опор и столбов откосы насыпей и конусов под мостами и путепроводами.
На выполнении уплотнительных работ в таких местах не могут быть использованы крупные грунтоуплотняющие средства применяемые при устройстве обычных насыпей выемок площадок или оснований. Их габариты и силовое воздействие зачастую не соответствуют размерам этих мест и условиям сохранности ответственных элементов и конструкций в них (трубы кабели опоры плиты балки и т. п.).
Во всем мире в том числе и в России грунты в стесненных неудобных и труднодоступных местах уплотняют как правило малогабаритными средствами ударного и виброударного типа – ручными вибротрамбовками виброплитами и виброкатками. Иногда используют также гидромолоты навешиваемые на стрелу одноковшового экскаватора или специализированной машины. Методы и средства статического уплотнения практически не применяются ввиду их малой эффективности.
1 Краткое описание машины
Конструкция виброплиты состоит из конструкционной рамы на которой размещен двигатель а в нижней части закреплена подошва. Управляющая ручка прикреплена с помощью амортизаторов часто бывает складной для удобства перемещения.
2 Исходные конструктивно-эксплуатационные данные для оценки конкурентоспособности
Исходные конструктивно-эксплуатационные данные для оценки конкурентоспособности проектируемой машины приведены в таблице 2:
Таблица 2 - Исходные данные
Варианты конструкции машины
Анулированные элемен-
Характеристика вводи-
мых элементов конст-
Удельный расход топлива
3 Расчет затрат по сравниваемым вариантам технических решений
Определим цену машины данную в долларах США (Ц=1000) по курсу НБ РБ в белорусских рублях по которому один доллар равен 8200 белорусских рублей. Тогда цена базовой машины 8200 тыс.руб.
Расчитаем налоги Нб (по белорусскому законодательству)
Отчисление в фонд поддержки производителей сх продукцииставка налога 2%
Осх=0028200=164тыс.руб
Отчисления в жилищный фонд ставка налога по Минску 075%
Ож=(Цр - Ож) 075100%
Ож=(8200-164) 00075=60тыс.руб
Налог на добавленную стоимость (НДС) ставка налога 20%
НДС = ДС20% 120% где ДС - добавленная стоимость;
ДС = Ц - Осх - Ож - МЗР МЗР - материальные затраты в цене продукциипринимаем на уровне 582% от цены 47724 тыс.руб. тогда
ДС =8200-164-60-47724=3203 тыс.руб
НДС =32036=534 тыс.руб
Прибыль балансовая Пбал
Пбал=Ц-Осх - Ож - НДС - ФЗП - Осс - Офз -А –МЗР
где ФЗП - фонд заработной платы средний по машиностроению 10% от цены изделия тыс.руб.
ФЗП=0108200=820 тыс.руб
Осс - отчисления на социальное страхование 35 % от ФЗП;
Осс =035820=287 тыс.руб
Офз - отчисления в фонд занятости 1% от ФЗП
Офз =001820=82 тыс.руб
А - амортизация среднюю норму амортизации примем на уровне 12% от стоимости капиталовложений;
А =0125740=6888 тыс. руб.
Пбал =8200-164-60-534-820-287-8-689-4772=865 тыс.руб
Налог на недвижимость
Ннб =5740100=57 тыс.руб
Налог на прибыль Нпр ставка 25%
Нпр = (Пбал-Нн) 25%100%
Нпр = 025 (865-57)=202 тыс.руб
Определим чистую прибыль Пч
Пч=865-57-202=606 тыс.руб
Рассчитаем налоги входящие в себестоимость
Отчисления в дорожный фонд Од ставка 1%
Од = (Ц - Осх - Ож - НДС) 1% 100%тыс.руб
Отчисления на содержание детских дошкольных учреждений 5% от ФЗП
Одду=005820=41 тыс.руб
Чрезвычайный налог на ликвидацию последствий аварии на Чернобыльской АЭС 4% от ФЗП
Одду=004820=328 тыс.руб
Полная себестоимость машины определим по формуле
С = МЗР +А+ ФЗП + Осс + Офз
С = МЗР +А+ 136 ФЗП где ФЗП - фонд заработной платы примем на среднем уровне по машиностроению 1% от Ц т.е. ФЗП=820тыс.руб А=689 тыс.руб
Осс - отчисления на социальное страхование 35% от ФЗП
Офз-отчисления в государственный фонд занятости1%от ФЗП
Сб =47724+689+136 820=6 576 тыс.руб
Найдем рентабельность по себестоимости Рс б
Найдем рентабельность по инвестициям Ри
Риб = 606100%5740=11 %
Полную себестоимость проектируемой машины определим методом удельных показателей по формуле
Cо = СбGоGб где Gб Gо - соответственно масса базовой и проектируемой машин т
Сб - полная себестоимость базовой машины тыс. руб.
Со =6 576031032=6 371тыс.руб
Рассчитаем прибыль при производстве проектируемой машины результаты сводим в таблицу 3
Таблица 3 - Результаты расчетов проектируемой машины.
Полная себестоимость
Фонд заработной платы
Отчисления на соцстрах и фонд занятости
Чрезвычайный налог и отчисления на ДДУ
Капитальные вложения Ко
Материальные затраты
Цена за вычитом Осх и Ож
Налог на недвижемость
Годовой экономический эффект полученный в результате инвестирования проектируемого технического решения за счет средств хранящихся на банковском счете определяется по формуле
Бр =Бнd где ΔП-годовая дополнительная прибыль остающаяся на нужды предприятия при инвестициях обеспечивающий реализацию проектируемого технического варианта; И - величина инвестиций в проектируемом техническом варианте.
КоКб - капитальные вложения соответственно по базовому и проектируемому вариантам тыс.руб.
Соотношение капвложений в производство и себестоимостьюдля базового варианта 07 а для проектируемого принимаем равным 071 в следствии малой сложности освоения новых технологий применяемых для изготовления изделия и невысокой предполагаемой серийности производства.
Бр - реальный банковский процент за пользование кредитом в десятичном виде;
Бн - номинальный банковский процент за пользование кредитом в десятичном виде Бн=080;
d - среднегодовой дефлятор d=2
Определим экономический эффект от выпуска одной машины для производства
Кб = 078200=5740 тыс.руб
Ко = 0717944=56400625 тыс.руб
Эп=(674-606)-(5 640-5 740) 1 0802=148 тыс.руб
Теперь найдем экономический эффект от выпуска одной машины для потребителя. Исходные данные таблица 4
Талица 4-Исходные данные
Наименование показателя
Цена продажи (Ц) тыс.руб.
Доставка (5% от цены) ( Т ) тыс.руб.
Производительность (Пр) у.е.ч
Расход топлива ( Q ) (тыс.рубч)
Стоимость ТОиР тыс.рубгод
Срок эксплуатации ( Г ) лет
Норма амартизации ( А ) %
Зарплата оператора виброплиты тыс.рубч
Зарплата рабочих на ТО и Р тыс.рубч
Количество маш-час работы в году ч
Цена продажи услуг (Цм) тыс.руб
Прямые затраты Сэк на годовую выработку определим по формуле:
Сэк=((Ц+T) А(100)+В(Сзп+Сэл)+Стор тыс.рубгод
где Сзт - затраты на зарплату основных и дополнительных рабочих тыс.рубч.
Сэн - затраты на электроэнергию тыс.рубч
Стор - затраты на ТО и ремонт млн.руб.год
Сзт =(Ко Сосн.+Кд Сдоп.)
Сосн и Сдоп - часовые соответственно тарифные ставкиосновных и дополнительных рабочих;
Результаты расчетов затрат сводим в таблицу 5 прибыли в таблицу 6
Таблица 5 - Результаты расчетов затрат .
Проектируемой машины
Таблица 6 - Результаты расчетов прибыли
Проектируемая машина
Объем выработки у.е.год
Полная себестоимость выработки
Выручка за вычетом Осх и Ож
Добавленная стоимость
Налог на недвижимость
Экономический эффект потребителя Ээ
Экономический эффект в народном хозяйстве
Энх =148+276=424 тыс.руб
Показатели эффективности проектируемой машины таблица 7
Показатель эффективности
Варианты конструкций изделия
Экономия(+) перерасход(-)
Себестоимасть изготовления одного изделия
в том числе по статьям затрат:
основная заработная плата
амортизация оборудования и зданий
Налоги не включаемые в себестоимость
Прибыль на одно изделие
Инвестиции на одно изделие
Экономический эффект на одно изделие
Текущие затраты на одно изделие
Суммарный эффект на одно изделие
1 Разработка мероприятий по обеспечению безопасной эксплуатации
При эксплуатации проектируемой вибрационной плиты основную опасность для персонала представляет локальная вибрация и шум.
Вибрация – это колебания тела около положения равновесия возникающие при неуравновешенности силовых воздействий. Вибрация относится к факторам обладающим высокой биологической активностью. Выраженность ответных реакций обусловливается главным образом силой энергетического воздействия и биомеханическими свойствами человеческого тела как сложной колебательной системы. Мощность колебательного процесса в зоне контакта и время этого контакта являются главными параметрами определяющими развитие вибрационных патологий структура которых зависит от частоты и амплитуды колебаний продолжительности воздействия места приложения и направления оси вибрационного воздействия демпфирующих свойств тканей явлений резонанса и других условий.
Параметр вибрации – физическая величина характеризующая механические колебания твердого тела (виброускорение виброскорость виброперемещение).
На рабочих местах где возможно вредное воздействие на человека вибрации необходимо чтобы ее уровень не превышал предельно допустимого значения для данного вида вибрации. В соответствии с нормативным документом [8] различают общую и локальную вибрацию.
Источники общей вибрации можно разбить на три категории: транспортные транспортно-технологические и технологические. Источниками транспортных вибраций служат дорожно-строительные машины – автогрейдеры бульдозеры скреперы грузовой автотранспорт и др. Технологическую вибрацию создают станки насосы вентиляторы электрические машины оборудование промышленности строительных материалов (камнедробильные машины грохоты и др.).
Источниками локальной вибрации являются ручные механизированные инструменты.
К работе с вибрирующими машинами и оборудованием допускаются липа не моложе 18 лет прошедшие предварительный медицинский осмотр имеющие соответствующую квалификацию сдавшие технический минимум по правилам техники безопасности и ознакомленные с характером воздействия локальной вибрации на организм.
К эксплуатации допускаются только исправные вибрирующие машины и оборудование отвечающее требованиям санитарных норм СанПин 2.2.42.1.8.10-32-2002.
Рукоятки ручных машин приспособлений а также органов управления должны иметь форму удобную для работы и не вызывать охлаждения рук Температура поверхности рукояток ручных машин должна находиться в пределах от 215 до 435°С. Оптимальным является диапазон от 25 до 32°С.
Не допускается использование вибрирующего оборудования не по назначению и в режимах отличающихся от паспортных.
Запрещается проведение сверхурочных работ с вибрирующим оборудованием.
Предельно допустимые значения локальной вибрации составляют:
виброускорение - 76 дБ;
виброскорость - 112 дБ.
Лица занятые на работах с вибрирующими машинами и оборудованием должны ежегодно проходить периодические медицинские осмотры.
В целях профилактики неблагоприятного воздействия локальной вибрации работникам выдаются средства индивидуальной защиты рук:
рукавицы антивибрационные;
сапоги антивибрационные;
Основными мерами по устранению вредных вибраций являются:
Проведение организационно-технических мероприятий обеспечивающих нормальный режим эксплуатации оборудования его предупредительный ремонт с сохранением паспортных характеристик выполнение требований технологического процесса и эффективные методы борьбы.
Выполнение инженерных мероприятий по активной виброизоляции оборудования и пассивной виброизоляции рабочих мест с повышенными общими вибрациями.
К методам защиты от вредного воздействия вибрации относятся:
- ослабление вибрации в источнике ее возникновения за счет уменьшения действующих в системе переменных сил;
- виброгашение достигается увеличением массы агрегата или повышением его жесткости;
- вибропоглощение осуществляется за счет увеличения потерь энергии в системе что достигается применением вязких смазочных материалов переводом механической колебательной энергии в другие виды энергии такие как энергия электромагнитного поля энергия токов Фуко тепловая энергия и др.;
- виброизоляция заключается во введении в колеблющуюся систему дополнительной упругой связи которая уменьшает долю вибрации передающейся от агрегата к основанию смежным конструкциям или к человеку.
При работе виброплиты на оператора действует общая и локальная вибрация которые превышают допустимые ПДУ. Длительное воздействие вибрации высоких уровней на организм человека приводит к развитию преждевременного утомления снижению производительности труда росту заболеваемости и нередко к возникновению профессиональной патологии - вибрационной болезни.
Между ответными реакциями организма и уровнем воздействующей вибрации нет линейной зависимости. При повышении частот колебаний более 07 Гц возможны резонансные колебания в органах человека. Резонанс человеческого тела отдельных его органов наступает под действием внешних сил при совпадении собственных частот колебаний внутренних органов с частотами внешних сил вызванных работой технологического оборудования. Особое значение резонанс приобретает по отношению к органу зрения. Расстройство зрительных восприятии проявляется в частотном диапазоне между 60 и 90 Гц что соответствует резонансу глазных яблок. Для органов расположенных в грудной клетке и брюшной полости резонансными являются частоты 3 3.5 Гц. Для всего тела в положении сидя резонанс наступает на частотах 4 6 Гц.
Гигиеническое нормирование вибраций регламентирует параметры производственной вибрации и правила работы с виброопасными механизмами и оборудованием ГОСТ 12.1.012-90 "ССБТ. Вибрационная безопасность. Общие требования". ГОСТ устанавливает предельно-допустимые уровни (ПДУ) которые не должны превышаться при передаче колебаний на тело человека.
Шум – это беспорядочное сочетание звуков различной частоты и интенсивности которые мешают воспринимать полезный сигнал. При работе оборудования звуки возникают при механических колебаниях в газообразной среде (воздухе). Колебательное движение воздушной упругой среды сопровождается перепадом давления этой среды и этот перепад воспринимается слуховым аппаратом человека. Воспринимаемые человеком звуковые волны характеризуются частотой и звуковым давлением которое прямо пропорционально амплитуде громкости интенсивности этой волны. Слуховой аппарат человека как слышимые воспринимает не все звуки а звуки определённой частоты и давления которые укладываются в слуховое поле.
При работе виброплиты персонал подвергается интенсивному шумовому воздействию которое неблагоприятно влияет на протекание нервных процессов способствует развитию утомления изменениям в сердечно-сосудистой системе и появлению шумовой патологии среди многообразных проявлений которой ведущим клиническим признаком является медленно прогрессирующее снижение слуха по типу кохлеарного неврита. Шум затрудняет своевременную реакцию работающих на предупредительные сигналы различных транспортирующих машин и механизмов (автопогрузчиков конвейеров) работающих на погрузочно-разгрузочных работах в зоне производства что может поспособствовать возникновению несчастных случаев на производстве. В биологическом отношении шум является заметным стрессовым фактором способным вызвать срыв приспособительных реакций рабочих. Акустический стресс может приводить к разным проявлениям: от функциональных нарушений регуляции ЦНС до морфологически обозначенных дегенеративных деструктивных процессов в разных органах и тканях. Степень шумовой патологии зависит от интенсивности и продолжительности воздействия функционального состояния ЦНС и что очень важно от индивидуальной чувствительности организма к акустическому раздражителю. Индивидуальная чувствительность к шуму составляет 4 17%. Высокая индивидуальная чувствительность может быть одной из причин повышенной утомляемости и развития различных неврозов.
Нормирование и классификация шумов на рабочих местах производится по двум нормативным документам:
ГОСТ 12.1.003-88 ССБТ “Шум. Общие правила безопасности”
СанПиН 2.2.42.1.8.10-32-2002 “Шум на рабочих местах в помещениях жилых и общественных зданий и на территории жилой застройки”
Эти нормы устанавливают классификацию шумов допустимые уровни шумов требования к измерению шума и основные меры профилактики при воздействии шума на человека. В качестве общей характеристики шума на рабочих местах применяется оценка уровня звука в дБА представляющая собой среднюю величину частотных характеристик звукового давления. Характеристикой непостоянного шума на рабочих местах является интегральный параметр - эквивалентный уровень звука в дБА.
Для постоянных рабочих мест и рабочей зоны в производственных помещениях и на территории предприятия допустимая норма шума составляет 80 дБА. Для тональных и импульсных шумов нормы уменьшаются на 5 дБА. Для диспетчерского персонала обслуживающего комплекс оборудования уровень шума не должен превышать 65 дБА (в кабине диспетчерской).
Основными мероприятия по борьбе с шумом на предприятии по переработке древесины на топливную щепу являются технические мероприятия которые проводятся по трем главным направлениям:
- устранение причин возникновения шума или снижение его в источнике;
- ослабление шума на путях передачи;
- непосредственная защита работающих.
Наиболее эффективным средством снижения шума является замена шумных технологических операций на малошумные или полностью бесшумные. Однако этот путь борьбы не возможен при данной технологической схеме поэтому большое значение имеет снижение шума в источнике. Снижение шума в источнике может быть достигнуто путем совершенствования конструкции или схемы той части оборудования которая производит шум использования в конструкции материалов с пониженными акустическими свойствами оборудования на источнике шума дополнительного звукоизолирующего устройства или ограждения расположенного по возможности ближе к источнику.
Одним из наиболее простых технических средств борьбы с шумом на пути передачи является применение звукоизолирующих кожухов которые могут закрывать отдельные шумные узлы машин комплекта оборудования по производству щепы. Также значительный эффект снижения шума от оборудования дает применение акустических экранов отгораживающих шумный механизм от рабочего места или зоны обслуживания машины.
Учитывая что с помощью технических средств в настоящее время не всегда удается решить проблему снижения уровня шума большое внимание должно уделяться применению средств индивидуальной защиты (антифоны заглушки и др.) а также проведению различных профилактических мероприятий с персоналом. Эффективность средств индивидуальной защиты может быть обеспечена их правильным подбором в зависимости от уровней и спектра шума а также контролем за условиями их эксплуатации. Персонал обслуживающий комплекс оборудования должен подвергаться предварительным и периодическим медосмотрам. Важным условием снижения воздействия шума на организм человека являются соблюдение режимов труда и отдыха контроль уровней шума и приём поливитаминов 2 раза в год.
В ходе дипломного проектирования были выполнены:
- анализ патентных источников вследствие которого была усовешенствована конструкция вибрационной плиты.
- расчеты по основной специальной и технологической частям дипломного проекта;
- расчет экономический эффективности который показал что эффект от внедрения нового технического решения составит 424 тыс. руб. в год;
- графическая часть дипломного проекта которая составила 8 листов формата А1;
- разработка мероприятий по охране труда при выполнении работ вибрационной плитой.
Список используемой литературы
Б.Ф. Бондаков И.П. Бордачев. Справочник конструктора дорожных машин. 2-е издание переработанное. Москва. «Машиностроение» 1973 г
В.А. Бауман И.И. Быховский Б.Г. Гольдштейн. Вибрационные машины в строительстве и производстве строительных материалов. Москва. «Машиностроение» 1970 г
А. Г. Казанцев К.Н. Падюков. Расчет и конструирование коробок скоростей и подач основного технологического оборудования механических производств. – Электронное учебное издание – Бийск: Изд-во АлтГТУ 2009
Л.В.Курмаз Скойбеда А.Т. Детали машин проектирование. Учебное пособие. Минск. «Технопринт». 2001г.
Чернавский. Курсовое проектирование деталей машин. Учебное пособие. Москва. «Машиностроение» 1988 г.
Ю.В. Барановский. Режимы резания металлов. 3-е издание переработанное и дополненное. Москва. «Машиностроение» 1972 г
А.А. Панов. Обработка металлов резанием. Справочник технолога. Москва. «Машиностроение» 1988 г.
ГОСТ 12.1.012-90 ССБТ «Вибрационная безопасность»
Виброплита: пат.2229551 РФ Точкин А.В. Артюх Н.В. Прошин В.В. Мазур Е.В. Российское агентство по патентам и товарным знакам.
Трамбовочная виброплита: пат.2231591 РФ Зиганшин И.Т. Российское агентство по патентам и товарным знакам.
Н.Я. Хархута М.И. Капустин В.П Семенов И.М. Эвентов. Дорожные машины. Ленинград. «Машиностроение» 1968 г
Руководство по эксплуатации виброплиты VS-244
Чертеж общего вида1.dwg

Назначение плиты вибрационной самопередвигающейся:
для механизации работ по уплотнению несвязных и связных
грунтов и материалов при благоустройстве прилегающих к зданию
территорий в стесненных условиях
Частота вращения двигателя
Максимальная скорость движения
Привод виброблока: клиноременная передача
Размеры рабочего органа плиты
Технические требования
Нормы затяжки резьбовых соединений по
При установке двигателя рукоятка пускового механизма должна быть
установлена как показана на главном виде.
В топливный бак залить бензин АИ - 92
В картер двигателя залить масло 10
в муфту сцепления М10 ГОСТ
Самопередвигающаяся
Плита в сборе.dwg

Спецификация виброблок.docx
Шайба 10 ГОСТ 11371-78
Манжеты ГОСТ 8752-78
Кольцо 160-170-58-2-4
Спецификация силовой агрегат.docx
Шайба 8 ГОСТ 11371-78
Гайка М20 ГОСТ 2528-73
Шайба 20 ГОСТ 11371-78
Двигатель Honda GX240
Pmax=59 кВт при n=3600
Силовой агрегат.dwg

При установке двигателя рукоятка пускового механизма должна быть
установлена как показана на главном виде.
В топливный бак залить бензин АИ - 92
В картер двигателя залить масло 10
в муфту сцепления М10 ГОСТ
Детали поз. 6 промыть и просушить сжатым воздухом
Напресовку подшипников поз.6 на вал производить безударным способом
Перед запресовкой в крышку
смазать Литолом ГОСТ 21150-75
Момент затяжки гайки поз. 11 100 150 Н м
виброблок.dwg

ТАП-15В ГОСТ 23659-79 в размере 4
и обкатать его в течение 2 часов