Редуктор одноступенчатый цилиндрический




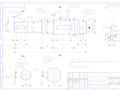

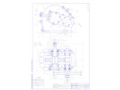
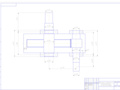
- Добавлен: 25.10.2022
- Размер: 2 MB
- Закачек: 0
Описание
Состав проекта
![]() |
![]() |
![]() ![]() |
![]() ![]() |
![]() ![]() ![]() ![]() |
![]() ![]() ![]() ![]() |
![]() ![]() ![]() ![]() |
![]() ![]() |
![]() ![]() |
![]() ![]() |
![]() ![]() ![]() ![]() |
![]() ![]() |
![]() ![]() |
![]() ![]() |
![]() ![]() |
![]() ![]() |
![]() ![]() ![]() ![]() |
![]() |
![]() ![]() ![]() |
Дополнительная информация
Вал ведомый.dwg

Неуказанные предельные отклонения по ГОСТ 30893.1: h14
* Разм. обеспеч. инстр.
Зубчатое колесо.dwg

Неуказанные предельные отклонения по ГОСТ 30893.1: h14
Сборочный редуктор.dwg

Техническая характеристика
Редуктор одноступенчатый
Поверхности соединения "корпус-крышка" перед сборкой покрыть
уплотнительной пастой типа "Герметик".
После сборки валы редуктора должны проворачиваться свободно
без заеданий и стука.
Редуктор обкатать по 10 15 мин на всех режимах нагрузки.
Спецификация.dwg

Крышка подшипника глухая
Крышка подшипника сквозная
Болт М6-8gх38.66.029
Болт М8-8gх28.66.029
Болт М10-8gх38.66.029
Штифт 4х20 ГОСТ 3128-70
Гайка М20 ГОСТ 5915-70
Шайба 20.01.016 ГОСТ13463-71
Эскизная компановка.dwg

Пояснительная записка №3_13_.doc
Выбор двигателя и кинематический расчет5
Расчет зубчатой передачи9
Расчет клиноременной передачи 17
Нагрузки валов редуктора22
Конструирование зубчатых колес35
Посадки зубчатых колес подшипников37
Конструктивные размеры корпуса редуктора38
Расчет и подбор муфты40
Смазывание редуктора39
Проверочный расчет шпонок 43
Проверочный расчет стяжных винтов45
Проверочный расчет валов 46
Список литературы 53
Цель проекта – проектирование привода к ленточному конвейеру. Приводная установка включает: электродвигатель клиноременную передачу цепную муфту косозубый цилиндрический редуктор. Вращательное движение от электродвигателя посредствомм клиноременной передачи сообщается ведущему валу редуктора а затем через цилиндрическую передачу (редуктор) на выходной вал редуктора. Далее через муфту передается на вал приводного барабана ленточного конвейера.
Ленточный конвейер- транспортирующее устройство непрерывного действия с рабочим органом в виде.
Ленточный конвейер является наиболее распространённым типом транспортирующих машин он служит для перемещения насыпных или штучных грузов. Применяется на промышленных производствах врудниках и шахтах в сельском хозяйстве. Груз перемещается по ленте в горизонтальной плоскости или под углом до 30° к горизонту.
Редуктором называют механизм состоящий из зубчатых или червячных передач выполненный в виде отдельного агрегата и служащий для передачи вращения от вала двигателя к валу рабочей машины. Кинематическая схема привода может включать помимо редуктора открытые зубчатые передачи цепные или ременные.
Назначение редуктора – понижение угловой скорости и соответственно повышение вращающего момента ведомого вала по сравнению с ведущим.
Редуктор состоит из корпуса в котором размещают элементы передачи – вал-шестерни зубчатые колеса валы подшипники и т.д.
Редукторы классифицируются по следующим основным признакам:
- типу передачи (зубчатые червячные);
- числу ступеней (одноступенчатые двухступенчатые);
- типу зубчатых колес (цилиндрические конические коническо-цилиндрические);
- относительному расположению валов редуктора в пространстве (горизонтальные вертикальные);
В данном проекте проводятся следующие вычисления:
- кинематический расчет и выбор электродвигателя;
- расчет валов редуктора;
- расчет цилиндрической передачи;
- расчет клиноременной передачи;
- проверка долговечности подшипников;
- проверка шпоночных соединений;
- уточненный расчет валов.
На основании выполненных расчетов выполняются сборочный чертеж редуктора а также рабочие чертежи деталей.
Срок службы приводного устройства
Местом установки конвейера принимается на транспортном агрегате применяемом в сельском хозяйстве – зернопогрузчик. Работает в течение 6 лет. Режим работы привода нереверсивный. При этом нагрузка спокойная. Работа в 1 смену продолжительность смены 8 часов.
Срок службы определяется по формуле ч:
где - срок службы привода (по заданию);
- продолжительность смены ;
Принимается время простоя машинного агрегата 20% следовательно:
Выбор двигателя и кинематический расчет
Общий КПД определим по формуле которая включает в себя произведение КПД всех передач муфты опор подшипников [1 стр.39]:
где - коэффициент учитывающий потери в клиноременной передаче [1 стр.40 табл. 2.2];
- коэффициент учитывающий потери цилиндрической зубчатой пары [1 стр.40 табл. 2.2];
- коэффициент учитывающий потери в муфте [1 стр.40 табл. 2.2];
- коэффициент учитывающий потери пары подшипников качения [1 стр.40 табл. 2.2];
- коэффициент учитывающий потери пары подшипников скольжения [1 стр.40 табл. 2.2];
Требуемая мощность рабочей машины определим по формуле:
где - тяговая сила ленты (по заданию);
-скорость тяговой цепи (по заданию);
Требуемая мощность электродвигателя:
где - общий КПД привода ;
- требуемая мощность рабочей машины ;
Номинальную частоту электродвигателя определим согласно [1 стр.384 табл.К9]:
Выберем тип электродвигателя соответствующей номинальной мощности из следующего ряда:
Таблица 2. Варианты выбора эдектродвигателя
Определим частоту вращения приводного вала машины:
где -скорость ленты (по заданию);
-димаетр барабана (по заданию);
Находим передаточное число привода для каждого типа двигателя:
Определим передаточные числа ступеней привода задавшись стандартным передаточным числом из первого ряда для закрытой передачи (цилиндрической) примем :
Таблица 3. Передаточные числа
цилиндрического редуктора
Очевидно что предпочтительным вариантом будет третий: .
Определяем максимально допустимое отклонение частоты вращения приводного вала конвейера:
где - частота вращения приводного вала машины;
- допускаемое отклонение скорости ленты
Определяем допускаемую частоту вращения приводного вала конвейера приняв обмин:
Определим фактическое передаточное число привода:
Уточним передаточное число открытой передачи:
Таблица 4. Определение силовых и кинематических параметров привода
Последовательность соединения элементов привода по кинематической схеме
Расчёт зубчатой передачи
Техническим заданием предусмотрено проектирование нестандартных одноступенчатых закрытых передач индивидуального производства.
Расчет зубчатой закрытой передачи производится в два этапа: первый расчет - проектный второй - проверочный.
Проектный расчет выполняется по допускаемым контактным напряжениям с целью определения геометрических параметров редукторной пары. В процессе проектного расчета задаются целым рядом табличных величин и коэффициентов; результаты некоторых расчетных величин округляют до целых или стандартных значений; в поиске оптимальных решений приходится неоднократно делать пересчеты. Поэтому после окончательного определения параметров зацепления выполняют проверочный расчет. Он должен подтвердить правильность выбора табличных величин коэффициентов и полученных результатов в проектном расчете а также определить соотношения между расчетными и допускаемыми напряжениями изгибной и контактной выносливости. При неудовлетворительных результатах проверочного расчета нужно изменить параметры передачи и повторить проверку.
При всем конструктивном разнообразии общепромышленных редукторов они мало различаются по технико-экономическим характеристикам и для них типичны средние требования к техническому уровню критерием которого является отношение массы редуктора к моменту тихоходном валу. В эскизном проектировании предварительно можно принять
Согласно [1 с.58 табл. 4.1] для цилиндрических редукторов получаем предварительные данные
Масса: Межосевое расстояние:
1Выбор материала и расчёт допускаемых контактных напряжений
Выбираем для колеса и шестерни сталь 45 с различной термообработкой [1с.49 табл. 3.1 3.2]:
- для колеса нормализация поковки с твердостью 179 207НВ2 (~200НВ2ср) в=600 Нмм2 при диаметре и толщине заготовки любой;
- для шестерни улучшение поковки 235..262 НВ1 (248НВ1ср) при диаметре заготовки и в=780 Нмм2.
2 Определение допускаемых контактных напряжений []H
Коэффициент долговечности принимаем КНL1(2)=1 т.к. N>NH0 передача является длительно работающей
Число циклов перемены напряжений за весь срок службы (наработка):
Число циклов перемены напряжений соответствующее пределу выносливости определяем согласно [1 стр. 51 табл. 3.3]:
Определяем допускаемое контактное напряжение []Н02 и []Н02 соответствующее пределу контактной выносливости при числе циклов перемены напряжений NH01 и NH02 согласно [1 стр. 49 табл. 3.1]:
Определим допускаемые контактные напряжения для зубьев шестерни []H2 и колеса []H2 Нмм2:
Так как для косозубой передачи разница твердостей зубьев шестерни и колеса НВ1ср-НВ2ср=248-200=48≤70 то расчетное среднее допускаемое напряжение принимается меньшее из следовательно .
3 Определение допускаемых напряжений изгиба []F
Коэффициент долговечности для зубьев шестерни KFL1 и колеса KFL2:
где – число циклов перемены напряжений для всех сталей соответ-ствующее пределу выносливости;
и циклов перемены напряжений за весь срок службы привода (наработка)
Принимаем KFL1=1 КFL2=1 т.к. N1>NF0
Определяем допускаемое напряжение изгиба []F01 и []F02 соответствующее пределу изгибной выносливости при числе циклов перемены напряжений NF0 согласно [1 стр. 49 табл. 3.1]:
Определяем допускаемые напряжения изгиба для зубьев шестерни []F1 и колеса []F2:
Расчет будем вести по меньшему значению т.е. по менее прочным зубьям колеса []F2=[]F=206МПа.
4 Проектный расчет цилиндрической передачи
Межосевое расстояние из условия контактной выносливости активных поверхностей зубьев:
где - коэффициент неравномерности нагрузки по длине зуба при прирабатывающихся зубьях принимается [1 с.59];
- коэффициент ширины венцов по межосевому расстоянию для косозубых цилиндрических колес выбирается из интервала 028 ÷063 принимается =028 [1 с.58];
– передаточное число зубчатой цилиндрической пары
– крутящий момент на валу колеса;
– допускаемое контактное напряжение;
=43 - коэффициент межосевого расстояния для косозубых передач [1 с.59];
Значение межосевого расстояния округляем до ближайшего значения по ГОСТ 2185-66 из первого ряда [1 с.58 табл. 4.1] .
Модуль зацепления принимаем по следующей рекомендации [1 с.59]:
где - вспомогательный коэфициент для косозубых передач;
- делительный диаметр:
- ширина венца колеса:
-допускаемое напряжение изгибу
Принимаем по ГОСТ 9563-60 из первого ряда ;
Определим угол наклона зубьев :
Определим суммарное число зубьев шестерни и колеса:
Уточним действительную величину угла наклона зубьев:
Определим число зубьев шестерни при условии что z1 ≥18:
Определим число зубьев колеса:
Определим фактическое передаточное число проверим его отклонение от заданного :
Отклонение от расчетного передаточного числа составляет 1% что допустимо.
Определим фактические геометрические параметры передачи:
Таблица 5. Геометрические параметры передачи
5 Проверочный расчет передачи
Проверим межосевое расстояние передачи:
Проверим пригодность заготовок колес по условию пригодности заготовок:
Диаметр заготовки шестерни:
Толщина диска заготовки колеса:
таким образом параметры заготовок колеса и шестерни по условию пригодны .
Проверим контактные напряжения :
где - вспомогательный коэффициент для косозубых передач
– коэффициент учитывающий распределение нагрузки между зубьями. Для косозубых определяется по графику [1с. 63 рис.4.2] в зависимости от окружной скорости колес:
и степени точности соответствующей передачи степень точности 8-ая [1с. 63 рис.4.2] тем самым ;
– коэффициент динамической нагрузки определяют [1с. 63 табл.4.3]
недогрузка до 10% что допустимо [1с. 62].
Проверяем напряжения изгиба зубьев шестерни и колеса :
где - модуль зацепления;
- ширина венца колеса;
для прирабатывающихся зубьев колес;
и – коэффициенты формы зуба шестерни и колеса. Определяются согласно [1с. 63 табл.4.4] интерполированием.
и допускаемые напряжения изгиба ;
Таблица 6. Параметры зубчатой цилиндрической передачи
Межосевое расстояние аw
Угол наклона зубьев °
Ширина зубчатого венца:
Диаметр окружности вершин:
Диаметр окружности впадин:
Расчет клиноременной передачи
-передаваемая мощность
-частота вращения ведущего вала (вала электродвигателя)
-предварительно принятое передаточное отношение
-коэффициент скольжения клинового ремня = 001
-угол наклона клиноременной передачи = 0º.
По номограмме [1 c.83] в зависимости от передаваемой мощности и частоты вращения ведущего вала принимаем тип сечения клинового ремня А по ГОСТ 1284.3-96.
Минимальный диаметр малого шкива [1 c.84]
Принимаем диаметр малого шкива на 1 2 размера больше .
Диаметр большего шкива по формуле [1 с. 84]:
где - диаметр меньшего шкива;
- передаточное отношение ременной передачи;
- относительное скольжение ремня [1 с.84]
Принимается d2 = 280 мм по ГОСТ 20889-88.
Уточняем передаточное отношение [1 с. 85]:
d2=280мм - диаметр большего шкива;
- относительное скольжение ремня [1 с. 120]
Отклонение составит
Определяем ориентировочное межосевое расстояние :
где d1 =100мм - диаметр меньшего шкива;
h =8 мм (высота сечения ремня) [2 с. 130 табл.7.7]
Расчетная длина ремня по формуле [1 с. 87]:
где aw=217мм – предварительное значение межосевого расстояния;
d1 =100мм - диаметр меньшего шкива;
Выбираем значение по ГОСТ 1384.1-89 [1 с. 418 К31] L=1060 мм.
Уточнённое значение межосевого расстояния aw с учетом стандартной длины ремня L[1 с. 87]:
где - коэффициент[1 с. 130];
-коэффициент [1 с. 130];
При монтаже передачи необходимо обеспечить возможность уменьшения межосевого расстояния на 001 x L =106 мм для облегчения надевания ремней на
шкивы и возможность увеличения его на 0025 x L = 265 мм для увеличения натяжения ремней. Это обеспечивается возможностью регулировки положения электродвигателя на раме.
Угол обхвата меньшего шкива по формуле [1 с.130]:
где d2=280мм - диаметр большего шкива;
- уточнённое значение межосевого расстояния
Линейная скорость ремня [1 с.332]:
Допускаемая мощность передаваемая одним ремнем:
где Р0 =095кВт - мощность передаваемая одним клиновым ремнем кВт [1 с.88 табл.5.5];
CP = 10- коэффициент режима работы учитывающий условия эксплуатации передачи [1 стр.82 табл.5.2]
CL = 10 - коэффициент учитывающий влияние длины ремня [1 с.86 табл.5.2]
- коэффициент учитывающий влияние угла обхвата [1 с.86];
Сz = 095 - коэффициент учитывающий число ремней в передаче [1 с.131] предполагая что ремней в передаче будет 2-3
Нажатие ветви клинового ремня по [1 стр. 88]:
где - требуемая мощность ;
z =2 – число ремней;
- линейная скорость ремня;
Определим окружную силу Ft передаваемую ремнем:
где Рном– номинальная мощность двигателя
Определим силы натяжения ведущей и ведомой ветвей:
Определим силу давления ремня на вал Fоп:
где α1 – угол обхвата ремнем ведущего шкива
2 Проверочный расчет
Проверим прочность ремня по максимальным напряжениям в сечении ведущей ветви :
где – напряжение растяжения;
где A = 81мм2 - площадь поперечного сечения ремня;
- нажатие ветви клинового ремня.
– напряжения изгиба:
где ЕИ=80 100мм2 – модуль продольной упругости при изгибе для прорезиненных ремней;
– напряжения от центробежных сил:
где ρ=1000 1200 кгмм3 – плотность материала ремня.
=10 Нмм2 – расчетное напряжение для клиновых ремней
Таблица 7. Параметры клиноременной передачи мм
Частота пробегов ремня
Межосевое расстояние а
Диаметр ведущего шкива d1
Диаметр ведомого шкива d2
Максимальное напряжение
Предварительное напряжение
Угол обхвата ведущего
Сила давления ремня на вал
Нагрузки валов редуктора
1 Определение сил в зацеплении закрытых передач
Таблица 8. Силы в зацеплении закрытой передачи
где Т2 – вращающий моменты на тихоходном вале редуктора ;
d2 – делительный диаметр колес;
– угол наклона зубьев цилиндрических колес ;
α – угол зацепления;
2 Определение консольных сил
Таблица 9. Консольные силы
Муфта тихо-ходного вала
где α1 – угол обхвата ремнем ведущего шкива;
F0 – сила предварительного натяжения ремня.
3 Выбор материала валов
В виду технологичности произведен выбор материала зубчатого зацепления одинаковым для колеса и шестерни. Быстроходный вал выполнен заодно с шестерней тем самым вал-шестерня имеет тот же материал который выбирался для зубчатого зацепления.
С целью уменьшения себестоимости редуктора и компенсации затрат производства на дорогие средства и различную технологию принимаем сталь 45
как материал тихоходного вала (под колесо).
Таблица 10. Характеристики материала валов
3 Выбор допускаемых напряжений на кручение
Допускаемые напряжения принимаем скомпенсированными то есть заниженными не учитывая напряжения изгиба концентрации напряжений и переменность во времени (циклы напряжений).
- допускаемые напряжения на кручение.
При этом меньшие значения для быстроходного вала а большие для тихоходного вала.
4 Определение геометрических параметров ступеней валов
- ступень под ведомый шкив:
где – крутящий момент в поперечном сечении ведущего вала ;
- допускаемое напряжение;
Диаметр вала принимается из стандартного ряда .
Длина ступени под шкив:
- 2-ая ступень под уплотнение крышки с отверстием и подшипник
по стандарту d2=30мм; t=22мм – высота буртика;
- 3-я ступень под шестерню
по стандарту - выбрано конструктивно; r–координаты фаски подшипника;
- 4-я ступень под подшипник
- 1-я ступень по муфту
где – крутящий момент в поперечном сечении тихоходного вала;
Принимается ближайшее значение из стандартного ряда
Принимается по стандартному ряду
- 2-я ступень под уплотнение крышки с отверстием и подшипник
где t–высота буртика; Принимается
- 3-я ступень под колесо
Принимаем по стандарту d3=48мм;
выбрано конструктивно; r–координаты фаски подшипника;
-я ступень упорная или под резьбу заменяем распорной втулкой.
5 Предварительный выбор подшипников качения
Предварительно намечаются однорядные радиальные шарикоподшипники по ГОСТ 8338-75 габариты выбираются по диаметру вала в месте посадки подшипников: и . Согласно ГОСТ 8338-75 выбираются подшипник 206 для ведущего вала и 308 для ведомого вала характеристики подшипников сведены в табл.9.
Таблица 11. Размеры ступеней. Характеристика подшипников
5 Эскизная компоновка редуктора
Эскизная компоновка служит для приближенного определения положения зубчатых колес для последующего определения опорных реакций.
Примерно посередине листа параллельно его длинной стороне проводим вертикальную линию затем две горизонтальные – оси валов на расстоянии
Вычерчиваем упрощенно шестерню и колесо в виде прямоугольников шестерня выполнена заодно с валом. Ступица колеса выполняется симметрично относительно диска.
Очерчивается внутренняя стенка корпуса редуктора принимая зазор между торцом ступицы колеса и стенкой 10 мм и принимая что зазор от внутренней стенки до торца подшипника 10 мм.
Зазор от внутренней стенки корпуса до окружности вершин зубчатых колес принимается равным .
Замерами определяются расстояния:
- на ведущем валу: ; ; .
- на ведомом валу: ; ; .
6 Проверочный расчет валов на выносливость
Силы действующие в зацеплении:
- радиальная сила: ;
- - расстояние между точками приложения реакций подшипников ведущего вала;
- - расстояние от реакции подшипника до середины выходного конца вала;
На ведущий вал (на выходной конец вала) действует нагрузка от ременной передачи .
Определяются реакции опор:
Определение реакций опор в плоскости XZ:
где– окружная сила в зацеплении цилиндрической передачи;
- нагрузка от ременной передачи;
- расстояние между линиями реакции подшипников быстроходного вала;
- расстояние от реакции подшипника до осевой линии ведомого шкива;
где– радиальная сила в зацеплении цилиндрической передачи;
- осевая сила в зацеплении цилиндрической передачи;
- средний делительный диаметр шестерни.
Определяются суммарные реакции:
- реакция опоры в плоскости
Выбираются подшипники по наиболее нагруженной опоре – опоре 1.
Отношение этой величине соответствует
Отношение следовательно осевую нагрузку учитываем
где - осевая расчетная нагрузка на подшипник;
- суммарная реакция в опоре 1
Эквивалентная нагрузка определяется:
где - суммарная реакция в опоре 1;
- коэффициенты радиальной и осевой нагрузки х=056 ;
- коэффициент при вращении внутреннего кольца ;
- коэффициент зависящий от характера нагрузки на подшипник принимаем ;
- температурный коэффициент принимается
6.2 Определение динамической грузоподъемности и расчетной долговечности
Динамическая грузоподъемность
следовательно грузоподъемность подшиников обеспечена.
Расчетная долговечность в млн. об.:
где С=195кН – динамическая грузоподъемность подшипника;
- эквивалентная нагрузка в опоре 1;
Расчетная долговечность в часах [1 стр.211]:
где - частота вращения ведущего вала;
- расчетная долговечность в млн. об.
- -консольная нагрузка на вал от муфты;
- - средний делительный диаметр колеса цилиндрической передачи
- - расстояние между точками приложения реакций подшипников ведомого вала;
- - расстояние от линии реакции ближайшего подшипника до средней линии муфты
- нагрузка на вал от муфты;
- расстояние между точками приложения реакций подшипников ведомого вала;
- средний делительный диаметр колеса.
Выбираются подшипники по наиболее нагруженной опоре – опоре 4.
Отношение следовательно осевую нагрузку не учитываем.
Эквивалентная нагрузка:
- коэффициент зависящий от того какое кольцо подшипника вращается при вращении внутреннего кольца
- коэффициент безопасности учитывающий характер нагрузки ;
- температурный коэффициент [1 стр.213 табл. 9.20];
6.4 Определение динамической грузоподъемности и расчетной долговечности
Расчетная долговечность млн. об
Расчетная долговечность подшипника ч:
Конструирование зубчатых колес
Шестерня выполняется заодно с валом её размеры.
- средний делительный диаметр
- диаметр вершин зубьев
- диаметр окружности впадин
- ширина шестерни b=40мм;
Основные размеры определены в разделе 3 данного проекта табл.4
- делительные диаметры ;
- диаметр вершин зубьев ;
- диаметр окружности впадин: ;
Способ получения заготовки для колеса выбираем поковку согласно [1 с.152 табл.10.2] определяем следующие геометрические параметры:
Диаметр ступицы колеса при шпоночном соединении:
где диаметр вала под колесом ;
Длина ступицы колеса:
Принимается длина ступицы колеса
Толщина ступицы колеса:
Толщина обода цилиндрического колеса:
где - модуль зацепления цилиндрической ступени ;
- ширина венца колеса ;
Посадки зубчатых колес подшипников
Посадки назначаем в соответствии с указаниями данными в таблице [2 табл. 10.13]
Посадка зубчатого колеса цилиндрической передачи на вал - по ГОСТ 25346-89
Шейки валов под подшипники выполняем с отклонением вала отклонения отверстий в корпусе под наружные кольца по Н7.
Остальные посадки назначаем пользуясь данными таблице.
Крышки торцовые узлов на подшипники качения .
Конструктивные размеры корпуса редуктора
Толщина стенок корпуса:
где - межосевое расстояние цилиндрической передачи ;
Так как согласно [2 с. 57 табл. 8.3] не менее 8 мм то принимается
Толщина стенок крышки:
Толщина фланцев (поясов) корпуса и крышки:
- верхнего пояса корпуса:
где – толщина стенок корпуса;
где – толщина стенок крышки;
- нижнего пояса корпуса без бобышки
Принимаются фундаментные болты с резьбой по ГОСТ 24379.1-80.
Болтов крепящих крышку к корпусу у подшипника:
где - диаметр фундаментных болтов;
Принимаются болты с резьбой М12 по ГОСТ 7798-80.
Болтов соединяющих крышку с корпусом:
Принимаем болты с резьбой М10 по ГОСТ 7798-80
Подбор и расчёт муфты
Муфтами называют устройства с помощью которых соединяют между собой валы или валы с находящимися на них деталями для передачи вращающего момента. В таких соединениях муфты как правило должны обеспечить не только передачу крутящего момента но и иметь возможность компенсировать различного рода смещения геометрических осей соединяемых валов. Осевые и радиальные смещения валов а также их угловой перекос возникают в результате упругих деформаций деталей под нагрузкой и в результате неточностей изготовления и сборки узлов. В реальных соединениях валов все эти виды смещений наблюдаются одновременно.
В данном случае применяется цепная муфта. Достоинства цепной муфты следующие: простота конструкции и обслуживания; надежность в работе; технологичность изготовления и сравнительно малые габариты и вес; удобный монтаж и демонтаж; способность компенсировать радиальные и угловые смещения за счет относительной податливости деталей цепи и их деформации.
Недостатком является наличие угловых зазоров и метрового хода вследствие чего они могут не применяться в реверсивных передачах а также при наличии больших динамических нагрузок.
На работу муфты существенно влияют толчки удары и колебания обусловленные характером работы приводимой в движение машины. Поэтому выбор муфты производят не по номинальному моменту на валу машины а по расчетному:
гдеТ - номинальный вращающий момент на валу
- коэффициент режима работы = 115.
Кроме того при выборе муфты учитываются диаметры концов сопрягаемых валов.
Принимаем цепную муфту 250-1-34-1-У3 ГОСТ 20742-93
Габаритные размеры: =140мм; =222 мм;
Для соединения полумуфт установленных на соединяемых валах используется приводная роликовая цепь типа ПР-254-6000 ГОСТ 13568-75:
Материал звездочек: сталь 45 ГОСТ 1050-88; твердость зубьев HRC 40 45.
Смазывание редуктора
Смазывание зубчатого зацепления производится окунанием зубчатого колеса в масло заливаемое внутрь корпуса до уровня обеспечивающего погружение колеса примерно на 10 мм. Объем масляной ванны V из расчета 04 08 л на 1 кВт передаваемой мощности: V=163·(04 08)=065 13 дм3
По таблице 10.29 [ 1с.241] устанавливаем вязкость масла. При контактных напряжениях НР=427 МПа и скорости =092 мс рекомендуемая вязкость масла должна быть примерно равна 34· 10-6 м2с. По таблице 10.29 [1.с.241] принимаем сорт масла И-Г-С-100
(индустриальное- для гидравлических систем – масло с антиокислительными присадками – класс кинематической вязкости 32 по ГОСТ 17479.4-87).
Определение уровня масла.
При окунании в масляную ванну колеса
Камеры подшипников заполняем вручную смазочным материалом при снятой крышке подшипникового узла на несколько лет. Смену смазочного пластинчатого материала производят при ремонте. Принимаем смазочный пластинчатый материал УТ -1.
Проверочный расчет шпонок
где – площадь смятия мм2;
–окружная сила на колесе или шестерне Н.
Проверим шпонку 3-й ступени тихоходного вала под колесом
Призматическая шпонка: h=9мм b=14мм t1 =55мм l=50мм.
– рабочая длина шпонки;
–интервал допускаемого напряжения на смятие Нмм2.
Снижаем значение допускаемого напряжения на 20 25% вследствие колебаний нагрузки.
Тогда шпонка пригодна.
Проверяем шпонку 1-й ступени тихоходного вала под муфтой: h=8мм b=10мм t1=50мм l=35мм.
Рассчитаем шпонку быстроходного вала 1-й ступени под шкивом
h=7мм b=7мм t1=4мм l=30мм.
Допускаемые напряжения уменьшаем в два раза в виду неоднородности материалов соединяемых деталей ступица чугунная.
Проверочный расчет стяжных винтов подшипниковых узлов
Стяжные винты подшипниковых узлов класса точности 5.6 стали 35 предел прочности – предел текучести – .
Стяжные винты рассчитывают на прочность по эквивалентным напряжениям на совместное действие растяжения и кручения :
где – расчетная сила затяжки обеспечивающая не раскрытие стыка под нагрузкой Н;
– сила воспринимаемая одним стяжным винтом Н где Ry самая большая из реакций в вертикальной плоскости в опорах подшипников быстроходного и тихоходного вала;
– коэффициент затяжки при переменной нагрузке;
x=02 03 – для соединения стальных и чугунных деталей без прокладок.
– площадь опасного сечения винта;
– расчетный диаметр винта; – наружный диаметр винта;
р – шаг резьбы (см. табл. К5 [1]).
– допускаемое напряжение при неконтролируемой затяжке для винтов с наружным диаметром до 16мм Нмм2.
Проверим прочность стяжных винтов узлов тихоходного вала:
Проверочный расчет валов
Цель расчета – определить коэффициенты запаса прочности в опасных сечениях вала и сравнить их с допускаемыми значениями:
После проведенного уточненного вычисления суммарных реакций в опорах подшипников увеличение оказалось незначительным.
Наиболее опасными сечениями являются сечение посадки подшипников со стороны консольной силы и 3-ей ступени под колесом (шестерней).
Источниками концентрации напряжений сечения 2-ой ступени считаются – ступенчатый переход галтелью или канавкой и посадка подшипника с натягом;
Концентрацию напряжений на 3-ей ступени определяют: посадка колеса с
натягом и шпоночный паз. Вал-шестерня – концентратор напряжений –
Материал вала-шестерни соответствует материалу выбранного в зубчатом зацеплении (см. 3.1) а для вала колеса применяем сталь 45 (см. табл. 7.1)
Определим напряжения в опасных сечениях быстроходного вала:
Сечение 3 (шестеренка)
где М – суммарный изгибающий момент;
Wнетто – осевой момент сопротивления сечения вала мм3 [1 табл. 11.1].
где Mk – крутящий момент;
Wρнетто – полярный момент инерции сопротивления сечения валамм3.
Сечение 2 (ступенчатый переход)
Определим коэффициент концентрации нормальных и касательных напряжений для вала без поверхностного упрочнения:
где – эффективный коэффициент концентрации;
– коэффициент влияния абсолютных размеров;
– коэффициент влияния шероховатости.
Расчет велся по наибольшему значению отношения – значение посадки с натягом [1 табл. 11.2–11.4].
Определим пределы выносливости в расчетном сечении вала:
где Нмм2 [1 табл. 7.1].
Определим коэффициент запаса прочности по нормальным и касательным напряжениям:
Определим общий коэффициент запаса прочности в опасном сечении:
Проверяем на прочность тихоходный вал опасные сечения: 2 (ступенчатый переход) и 3 (под колесом)
Определим напряжения в опасных сечениях вала:
– коэффициент влияния шероховатости;
Поэтому расчет ведутся по концентратору напряжений посадки с натягом:
– коэффициент концентрации напряжений посадки с натягом ;
отношение – расчет ведется по коэффициенту посадки с натягом.
Определим общий коэффициент запаса прочности в опасных сечениях:
Сопротивление усталости вала обеспечено во всех опасных сечениях вала.
Перед сборкой внутреннюю полость корпуса редуктора тщательно очищают и покрывают маслостойкой краской.
Сборку производят в соответствии со сборочным чертежом редуктора начиная с узлов валов:
на ведущий вал насаживают мазеудерживающие кольца и шарикоподшипники предварительно нагретые в масле до 80 - 100С;
в ведомый вал закладывают шпонку и напрессовывают зубчатое колесо до упора в бурт вала; затем надевают распорную втулку мазеудерживающие кольца и устанавливают шарикоподшипники предварительно нагретые в масле.
Собранные валы укладывают в основание корпуса редуктора и надевают крышку корпуса покрывая предварительно поверхности стыка крышки и корпуса спиртовым лаком. Для центровки устанавливают крышку на корпус с помощью двух конических штифтов; затягивают болты крепящие крышку к корпусу.
После этого на ведомый вал надевают распорное кольцо в подшипниковые камеры закладывают пластичную смазку ставят крышки подшипников с комплектом металлических прокладок для регулировки.
Перед постановкой сквозных крышек в проточки закладывают манжеты пропитанные горячим маслом. Проверяют проворачиванием валов отсутствие заклинивания подшипников (валы должны проворачиваться от руки) и закрепляют крышки винтами.
Далее на конец ведомого вала в шпоночную канавку закладывают шпонку устанавливают полумуфту и закрепляют ее торцовым креплением; винт торцового крепления стопорят специальной планкой.
Затем ввертывают пробку маслопускного отверстия с прокладкой и жезловый маслоуказатель.
Заливают в корпус масло и закрывают смотровое отверстие крышкой с прокладкой из технического картона; закрепляют крышку болтами.
Собранный редуктор обкатывают и подвергают испытанию на стенде по программе устанавливаемой техническими условиями.
А.Е. Шейнблит «Курсовое проектирование деталей машин» М. «Высшая школа» 1991.
С.А. Чернавский К.Н. Боков И.М. Чернин Г.М. Ицкович В.П. Козинцов
Курсовое проектирование деталей машин". М.: Машиностроение 1988.
П.Ф. Дунаев О.П. Леликов “ Конструирование узлов и деталей машин “.М.: «Академия» 2006.
Л.В. Курмаз А.В. Скойбеда; Детали машин. Проектирование – М. 2004г.
П.Ф. Дунаев «Конструирование деталей и узлов машин» Москва «Высшая школа»2001