Разработка технологического процесса восстановления вилки включения сцепления трактора МТЗ-80/82




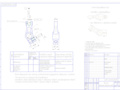
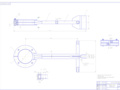
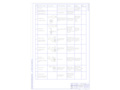
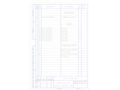
- Добавлен: 25.10.2022
- Размер: 522 KB
- Закачек: 0
Описание
Состав проекта
![]() |
![]() |
![]() ![]() |
![]() ![]() ![]() ![]() |
![]() ![]() ![]() ![]() |
![]() ![]() |
![]() ![]() |
![]() ![]() ![]() ![]() |
![]() ![]() |
![]() ![]() |
![]() ![]() ![]() ![]() |
![]() |
![]() ![]() ![]() |
![]() ![]() ![]() |
![]() ![]() ![]() |
![]() ![]() ![]() |
Дополнительная информация
Маршрутный процесс восстановления.dwg

Основное оборудование
Машина моечная ОМ-834М
Штангенциркуль ШЦ-1-
- наплавить зев вилки
Станок фрезерный 6К82Ш
- сверлить резьбовое
генциркуль ШЦ-1-125-01
генциркуль ШЦ-1-125-
- установить резьбовую
завинчивания резьбо-
- контролировать восста-
новленные поверхности
Установка для закалки
тошь 25 ГОСТ 5354-79
Маршрутный технологический
процесс восстановления
Чертеж.dwg

резьбу под резьбовую вставку
установить резьбовую вставку.
Наплавить в среде СО2
Наплавить в среде углекисло-
го газа проволокой Нп-30ХГСА
Технологический маршрут восстановления:
резьбонарезная (Деф.1)
слесарно-механическая (Деф.1)
Ремонтный сборочный чертеж
* Размеры для справок.
кроме мест обозначенных особо.
На боковых поверхностях зева допускаются риски глубиной до
мм и завалы от обоих торцев глубиной до 0.2 мм.
Ресурс восстановленной вилки должен быть не менее 80% от
ресурса новой детали.
Остальные ТТ по СТБ 1014-95.
Вилка бракуется при наличии усталостного разрушения
Схемы базирования при:
- наплавке и фрезеровании;
- при сверлении и нарезании резьбы.
Индуктор.dwg

Сварка по ГОСТ 14771-76 в среде защитных газов.
*Размеры для справок.
Маркировать материал режущей части
Остальные ТТ по СТБ 1022-96.
Спецификация к индуктору.dwg

Техпроцесс.DOC
Министерство образования Республики Беларусь
Белорусский национальный технический университет
Руководитель М.М Гарост
ТЕХНОЛОГИЧЕСКОГО ПРОЦЕССА ВОССТАНОВЛЕНИЯ ВИЛКИ
ГОСТ 3.118-82 форма 1
Код наименование операции
Обозначение документации
Код наименование оборудования
РМ 005 Моечная ИОТ №5
Машина моечная ОМ-834М 2-х % раствор кальцинированной соды ветошь щетка металлическая 1-2
РМ 010 Дефектовочная ИОТ №10
Стол дефектовщика штангенциркуль ШЦ-1-125-01 ГОСТ 165-80 линейка стальная 500 мм.
РМ015 Наплавочная ИОТ №15
Выпрямитель ВСГ-3 генератор НД наплавочная головка ГМВК-2 дроссель РСТЭ-34 штангенциркуль ШЦ-1-125-01 ГОСТ 166-80 линейка.
РМ020 Фрезерная ИОТ №20
Станок фрезерный 6К82Ш тиски фреза пальцевая 5 20 ГОСТ 2679-78штангенциркуль ШЦ-1-125-01 ГОСТ 166-80 линейка стальная.
РМ 025 Сверлильная ИОТ №25
Станок вертикально-сверлильный 2Т125 тиски сверло 2300-6411-А1 ГОСТ 10902-77 штангенциркуль ШЦ-1-125-01 ГОСТ 166-80 линейка.
Наименование детали сборочной единицы или материала
РМ030 Резьбонарезная ИОТ №30
Станок вертикально-сверлильный 2Т125 тиски метчик М12 15-6g ГОСТ 3266-81 штангенциркуль ШЦ-1-125-01 ГОСТ 166-80 линейка.
РМ 035 Термическая ИОТ №35
Установка для закалки деталей ТВЧ клещи пресс Роквелла индуктор штангенциркуль ШЦ-1-125-01 ГОСТ 166-80 линейка стальная.
РМ 040 Контрольная ИОТ №40
ПЗ.doc
Ежегодно в различных отраслях промышленности и в дорожном хозяйстве изымается из эксплуатации большое количество металла пластмасс древесины и т.д. из-за физического морального износа машин механизмов. При соответствующей переработке они могут быть повторно использованы.
Целью курсовой работы является разработка технологического процесса восстановления вилки включения сцепления трактора МТЗ-8082.
Анализ условий работы и дефектов вилки.
Вилка является частью трансмиссии трактора и предназначена для включения сцепления. Основные виды повреждений возникающие при работе: абразивный износ усталостные поломки и задиры [1].
Абразивный износ. На поверхности наблюдаются риски параллельные направлению трения. Причины разрушения - взаимодействие трущихся поверхностей с абразивными частицами.
Усталостный излом. Характер повреждений - образование трещин. Причина разрушения - понижение прочности металла действие знакопеременных нагрузок циклические термические напряжения наличие концентраторов напряжений.
Истирание металлических пар. Характер повреждений - постепенное изменение геометрических размеров деталей. Причина разрушения - длительное трение сопряженных деталей.
На ремонт вилка поступила со следующими дефектами:
Износ зева до размера более 155 мм;
Вилка изготовлена из стали 45Л-1 ГОСТ 977-75.
Ремонтный сборочный чертеж вилки с указанием дефектов номинальных размеров изношенных поверхностей и схем базирования при обработке приведен на листе [1].
Анализ научно-технической и патентной литературы по способам восстановления вилки.
В настоящее время восстановление тел вращения производится наплавкой и нанесением газотермических покрытий [2] [3].
Наплавка - нанесение слоя металла заданного состава на деталь или режущую часть инструмента методами сварки для образования поверхностного слоя обладающего заданными свойствами (повышенной прочностью износостойкостью кислотостойкостью и т.д.) а также для восстановления изношенной поверхности. Основные способы наплавки:
Дуговая под флюсом - наплавка деталей диаметром более 50 мм при повышенных требованиях к качеству наплавленного металла и толщине слоя наплавленного металла более 1 мм.
Дуговая в среде С02 - наплавка стальных деталей диаметром более 16 мм широкой номенклатуры.
Дуговая с газопламенной защитой - наплавка стальных и чугунных деталей работающих в различных условиях.
Вибродуговая - наплавка стальных деталей работающей в различных условиях при невысоких требованиях к сопротивлению усталости.
Дуговая порошковой проволокой или лентой - наплавка износостойких слоев на детали работающие в условиях интенсивного изнашивания ударных нагрузок в узлах трения.
Дуговая в среде аргона - наплавка алюминиевых деталей и деталей из коррозионностойких сталей.
Контактная - наплавка гладких цилиндрических деталей с износом не более 1мм.
Газовая - наплавка цилиндрических и профильных деталей с местным износом при повышенных требованиях к износостойкости.
Плазменная - наплавка ответственных деталей при повышенных требованиях к износостойкости и сопротивлению усталости.
Многоэлектродная под флюсом - наплавка деталей со значительным износом
по величине и площади
Лежачим электродом - наплавка плоских поверхностей и поверхностей со сложной конфигурацией со значительным износом.
Электроимпульсная - наплавка наружных цилиндрических поверхностей с износом до 05 мм с ограничением температуры нагрева детали.
Электроискровая - наращивание и упрочнение поверхности с износом до 02 мм при невысоких требованиях к сплошности покрытия.
Электрошлаковая - наплавка деталей с износом более 6 мм.
Жидким металлом - наплавка деталей со значительным износом (более 3 мм) при повышенных требованиях к износостойкости и невысоких требованиях к стойкости против ударных нагрузок.
С одновременным деформированием - наплавка деталей с наружным шлицевым профилем.
С одновременным резанием - наплавка и обработка износостойких материалов в нагретом состоянии обработка которых в холодном состоянии затруднена.
Лазерная - наплавка износостойких материалов на ответственные детали со сложным профилем.
Высокочастотная - наплавка износостойких материалов на рабочие органы и лезвия почвообрабатывающих и землеройных машин.
Высокочастотная в огнеупорной среде - наплавка проушин и цевок звеньев гусениц тракторов.
Нанесение газотермических покрытий:
Пламенное порошковыми материалами без оплавления (на ацетилене или пропан-бутановой смеси) - восстановление и упрочнение наружных и внутренних цилиндрических поверхностей неподвижных сопряжений при невысоких требованиях к прочности сцепления с основным материалом.
Пламенное порошковыми материалами с оплавлением - то же но при повышенных требованиях к износостойкости и сцеплению с основным материалом.
Плазменное порошковыми материалами - восстановление и упрочнение наружных и внутренних цилиндрических поверхностей
Плазменное проволокой сплошного сечения - то же.
Детонационное - нанесение износостойких покрытий с особыми свойствами.
Ионно-плазменное - нанесение износостойких и защитных покрытий с особыми свойствами толщиной не более 002 мм.
Дуговое - нанесение покрытий на наружные и внутренние цилиндрические поверхности при невысоких требованиях прочности сцепления с основным материалом.
Высокочастотное - то же.
При осуществлении того или иного процесса наплавки происходит оплавление поверхности металла - основы расплавление присадочного материала соединение их и кристаллизация образовавшейся смеси. Соотношение долей основного и присадочного металлов в наплавленном слое определяет его состав микроструктуру и свойства. При восстановительной наплавке нелегированным металлом доля основного металла не оказывает существенного влияния на свойства наплавленного слоя. Напротив при упрочняющей наплавке легированным металлом увеличение доли основного металла приводит к ухудшению свойств наплавленного слоя.
Ручную электродуговую наплавку выполняют на постоянном и переменном токе штучными неплавящимися или плавящимися электродами. В качестве неплавящегося электрода чаще всего используют графитовые (угольные) стержни. На наплавляемую поверхность наносят слой наплавочной смеси или пасты соответствующего состава и расплавляют теплом дуги. Толщина наплавленного слоя -1-3 мм. Угольным электродом по слою смеси чаще всего наплавляют плоские поверхности. Более распространена наплавка плавящимися покрытыми электродами. Достоинства способа: простота и маневренность; недостатки: низкая производительность (1-3 кгч) тяжелые условия труда снижение усталостной прочности наплавленных деталей.
Достоинствами механизированной наплавки являются: непрерывность процесса достигаемая в результате использования электродной проволоки или ленты в виде больших мотков; подвод тока к электроду на минимальном расстоянии от дуги позволяющий применять токи большой силы без перегрева электрода.
Из всех способов механизированной наплавки наибольшее распространение получила наплавка под флюсом. Схема этого способа показана на рисунке 1. Электродная проволока 1 непрерывно с постоянной скоростью подается в дуговой промежуток. Подвод тока к проволоке осуществляется в непосредственной близости от дуги при помощи втулки 2. В дуге 3 проволока плавится. Капли металла пройдя дуговой промежуток смешиваются с расплавленным металлом изделия 4 и образуют сварочную ванночку 5. После кристаллизации получается наплавленный валик 6 покрытый шлаковой коркой 7 и нерасплавившимся флюсом 8. Избыток флюса ссыпается а остывшая шлаковая корка удаляется. Формируется однородный наплавленный металл без пор и раковин. Производительность процесса одноэлектродной наплавки под слоем флюса невелика.
Рисунок 1 – Схема механизированной наплавки.
Поэтому наряду с одноэлектродной наплавкой применяют и другие разновидности этого способа: наплавку электродной лентой многоэлектродную и многодуговую наплавку наплавку с поперечным колебанием электрода (рисунок 2абвг)
Рисунок 2 – Схемы наплавки:
а- наплавка электродной лентой б- многоэлектродная наплавка в- многодуговая наплавка г- наплавка с поперечным колебанием электрода.
При наплавке электродной лентой (рисунок 2а) достигаются малая глубина проплавления основного металла и возможность наплавить за один проход валик шириной до 100 мм. При многоэлектродной наплавке (рисунок 2б) в зону дуги одновременно подаются несколько электродов подключенных к одному полюсу источника сварочного тока. Дуга периодически перемещается с одного электрода на другой; при этом образуется общая сварочная ванна формируется широкий валик. При многодуговой наплавке (рисунок 2 в) применяется несколько наплавочных аппаратов или один аппарат с изолированными друг от друга несколькими электродами каждый электрод питается от отдельного источника тока.
При наплавке деталей малого диаметра глубоких внутренних поверхностей и ряда высоколегированных сплавов затруднено удаление шлаковой корки. Этого недостатка лишена механизированная наплавка открытой дугой и наплавка в защитных газах. При наплавке открытой дугой в качестве электрода используется порошковая проволока. Для защиты металла от кислорода и азота воздуха в ее сердечник вводят кроме легирующих элементов газо- и шлакообразующие компоненты и раскислители (при наплавке крупных деталей используют не порошковую проволоку а ленту). Иногда используют голую легированную проволоку содержащую в небольших количествах РЗМ
Наплавку в защитных газах чаще выполняют плавящимся электродом. В качестве защитных газов используют углекислый газ аргон азот.
Электрошлаковая наплавка (ЭШН)
Схема процесса показана на рисунке 3.
Рисунок 3 – Схема электрошлаковой наплавки.
В пространстве образованном наплавляемой поверхностью 6 и формирующим устройством 5 создается ванна расплавленного флюса-шлака 2 в которую непрерывно подается металлический электрод 1. Ток проходя между электродом и наплавляемым изделием нагревает расплавленный шлак и поддерживает высокую температуру и электропроводность. Шлак расплавляет электрод и оплавляет поверхность изделия. Ниже шлаковой ванны образуется металлическая ванна 3 которая затвердевая дает слой 4 прочно сплавленный с металлом изделия. Процесс наплавки начинают на графитовых медных или стальных подкладках. Формирующее устройство в виде охлаждаемого водой медного ползуна медленно перемещается вверх с помощью специального механизма.
При электрошлаковой наплавке в качестве электродов используют проволоку литые стержни и пластины трубы в качестве шлака - флюс АН-25. Благодаря применению больших токов (несколько тысяч ампер) достигают очень высокой производительности - до 150 кг наплавленного металла в час. ЭШН плоских поверхностей может производиться при вертикальном нижнем и наклонном положениях наплавляемой поверхности.
Для торцовой наплавки деталей сложной формы используется прием стыкошлаковой наплавки (рисунок 4).
Рисунок 4 – Схема стыкошлаковой наплавки.
Процесс начинается наведением шлаковой ванны на дне водоохлаждаемой формы. Электродом служит хвостовик детали 1 с приваренной пластиной или прутком из легированного металла 2 которые расплавляются в первую очередь. В момент погружения хвостовика 1 в шлак происходит его разогрев а затем он погружается в металлическую ванну. Таким образом успешно восстанавливают зубья экскаваторов сверла и метчики большого диаметра и т.п.
Плазменную наплавку применяют в тех случаях когда необходимо наплавить слой толщиной от 05 до 50 мм при строго регламентированной доле основного металла. Применяют несколько разновидностей плазменной наплавки. Присадочный материал нужного состава подают в плазменную дугу или выделенную плазменную струю в виде проволоки ленты спрессованных металлокерамических колец пластин пасты или порошка. На рисунке 5 показана схема плазменной наплавки с токоведущей присадочной проволокой.
Рисунок 5 – Схема плазменной наплавки.
Источником тепла для расплавления присадочной проволоки является двухдуговой разряд. Одна дуга (маломощная) горит между вольфрамовым электродом 1 и соплом 2 вторая (основная) - между вольфрамовым электродом и проволокой 4. Через сопло 3 подается защитный газ. Основной металл разогревается теплом перегретого расплавленного металла проволоки и факелом плазменной струи. По этой схеме наплавляются: бронзы латуни нержавеющие стали и т.п.
На рисунке 6 показана схема плазменно-порошковой наплавки. Порошок нужного состава вдувают в дугу через специальные каналы в горелке. Во внутреннем рабочем сопле 2 формируется плазменная струя по соплу 3 подается присадочный порошок а по соплу 4 - защитный газ. Источник 5 служит для зажигания дуги между электродом 1 и соплом 2; в плазменной струе этой дуги плавится порошок. Источник 6 формирует плазменную дугу прямого действия которая оплавляет поверхность изделия и является дополнительным источником тепла для плавления присадочного порошка. Производительность указанных способов невелика (05-10 кг наплавленного металла в час). Более высокой производительностью (до 30 кгчас) обладает плазменная наплавка с подачей в ванну двух плавящихся электродов.
Рисунок 6 – Схема плазменно-порошковой наплавки.
При индукционной наплавке в качестве источника нагрева используются токи высокой частоты. Нагрев осуществляется с помощью индуктора присоединенного к машинному или ламповому генератору ТВЧ. Практическое применение нашли два способа индукционной наплавки: 1) с использованием твердого присадочного материала наносимого на наплавляемую поверхность в виде порошка пасты или прессованных брикетов; 2) с использованием жидкого присадочного материала расплавляемого в отдельной индукционной печи и определенными порциями подающегося на разогретую поверхность наплавляемой детали. Наплавку твердым присадочным материалом применяют для повышения износостойкости бил и молотков дробилок лап культиваторов лемехов плугов (рисунке 7). На рисунке: 1- деталь 2 - смесь порошков сплава и флюса 3 - индуктор. В качестве присадочного материала используют порошок сплава сормайт 1 а также композиции сормайт - релит сормайт - феррохром. Применяют также индукционную наплавку клапанов двигателей внутреннего сгорания. Присадочный материал в виде литых колец из сплава ВЗК или НХ15С2Р2 укладывают в предварительно проточенную канавку на тарелке клапана а затем расплавляют с помощью специальных индукторов.
Рисунок 7 – Схема индукционной наплавки.
Основа процесса газопламенного нанесения порошков заключается в пластификации порошка в высокотемпературном источнике тепла например ацетилено-кислородном пламени и нанесении его газовым потоком на предварительно подготовленную изношенную поверхность.
Преимущества данного способа восстановления: а) высокая производительность; б) локальность т.е. выборочное нанесение материала только на изношенную поверхность; в) незначительное воздействие на подложку; г) отсутствие ограничений на сочетание материалов.
В зависимости от назначения и материала детали условий ее эксплуатации используют следующие методы газопламенного нанесения порошковых материалов:
Газопламенное напыление порошка без последующего оплавления. Используется для восстановления износов более 2-х мм на сторону без деформации искажения или изменения структуры основного металла. Таким образом восстанавливают детали не подвергающиеся в процессе эксплуатации ударам знакопеременным нагрузкам сильному нагреву.
Газопламенное напыление порошка с одновременным оплавлением. Используется для восстановления износов 3-5 мм. Восстанавливаются детали работающие при знакопеременных нагрузках изготовленные из хромистых конструкционных сталей
Газопламенное напыление порошков с последующим оплавлением. Восстанавливают детали типа вала с износом до 25 мм на сторону из материалов устойчивых против коррозии работающие в условиях абразивного изнашивания действия повышенных температур.
Технологический процесс газопламенного напыления состоит из следующих этапов:
) нагрев поверхности детали до 200 - 250 °С
) нанесение подслоя;
)нанесение основных слоев с заданными физикомеханическими свойствами.
Для осуществления процесса используют сварочные горелки снабженные бункером для порошка. У инжекторного распылительного аппарата (рисунок 8) порошок через клапан размещенный в корпусе аппарата под влиянием всасывающего действия кислорода и горючего газа протекающего по каналу попадают в сопло а затем - в ядро пламени.
Рисунок 8- Схема газопламенного напыления.
Металлизация - это один из распространенных способов получения металлических покрытий поверхностей нанесением на эти поверхности расплавленного металла. Сущность метода заключается в том что металл расплавленный дугой (при электрометаллизации) или ацетиленокислородным пламенем и распыленный сжатым воздухом (давлением 06 МПа) покрывает поверхность восстанавливаемой детали.
Процесс дуговой металлизации осуществляется металлизатором. Аппарат (см. рисунок 9) действует
Рисунок 9- Схема дуговой металлизации.
следующим образом: с помощью протяжных роликов по направляющим наконечникам непрерывно подаются две проволоки (1) к которым подведен электрический ток. Дуга возникающая между проволоками расплавляет металл. Одновременно по воздушному соплу 5 в зону дуги подается сжатый воздух (давление 06 МПа). Скорость движения частиц металла в струе достигает 120 - 300 мс. Высокая скорость и малое время движения частиц не превышающее сотых долей секунды обусловливает пластическое деформирование частиц в момент удара их о твердую поверхность детали 6 и заполнение частицами неровностей и пор сцепление частиц между собой и поверхностью. Таким образом формируется сплошное покрытие толщиной от нескольких микрон до 10 мм (обычно для тугоплавких металлов толщина слоя от 1 до 15 мм а для легкоплавких - от 25 до 3 мм).
В зависимости от источника расплавления металла металлизацию разделяют на: 1 - газопламенную;
Наибольшее распространение на практике нашла дуговая металлизация.
В зависимости от цели восстановления и условий эксплуатации деталей для металлизации применяют проволоки различных марок (табл.1).
Таблица 1 - Марки проволок для дуговой металлизации
Восстановление поверхностей под неподвижные посадки
Получение износостойких покрытий
Стали: 45 У7 У8 У10. Проволоки марок Нп-40 Нп-ЗОХГСА Нп-ЗОХ13
Металлизация деталей работающих при высоких температурах
Хромоникелевые стали
Восстановление подшипников скольжения
Антифрикционные сплавы: 50 %А1+50 % Al
Заделка трещин раковин и нанесение антикоррозионных покрытий на чугунные детали
Заделка трещин в деталях из алюминиевых сплавов
Применяя разнородные материалы проволок можно получить композиционные покрытия. При нанесении слоя покрытия на деталь температура нагрева последней достигает 50 -70 °С что позволяет наносить металлические покрытия на любые материалы (металлы пластмассу дерево резину).
Недостатками процесса металлизации являются: 1. Металлизированный слой не повышает прочности детали. Поэтому металлизация не годится для восстановления деталей с ослабленным сечением. 2. Сцепляемость покрытия с деталью невысока. Поэтому не следует восстанавливать детали работающие в условиях: а) сухого трения; б) динамических нагрузок.
Перспективные способы восстановления.
Восстановление деталей наплавкой взрывом.Процесс заключается в следующем. На жесткое основание устанавливают изделие. Над ним располагают пластину присадочного металла поверх которой укладывают заряд гранулированного взрывчатого вещества. После взрыва детонатора взрывается основной заряд и возникает плоская детонационная волна. Взрыв вызывает соударение пластины присадочного металла с поверхностью изделия и на поверхности контакта возникает давление в десятки тысяч Паскалей. Металл течет деформируясь пластически. Оксидные пленки дробятся. Перемешивание основного и присадочного металлов отсутствует; тем не менее образуется металлическая связь дислокационного характера так как при взрыве протекает совместное пластическое деформирование основного и присадочного металлов.
Наплавку осуществляют на открытых полигонах в специальных производственных помещениях вакуумных камерах и др.
Детонационное нанесение порошковых покрытий. Способ основан на использовании энергии детонации в газах. При этом способе металлический или металлизированный порошок наносится взрывом кислородо-ацетиленовой смеси обеспечивающим скорость движения частиц 800 - 900 мс. Прочное соединение частиц с восстанавливаемой поверхностью обеспечивается микросваркой.
Образование газовопорошковой смеси ее взрыв осуществляется в специальной камере куда порошок доставляется струей азота.
В качестве материалов порошков применяют: а) карбиды - вольфрама и титана; б) оксиды - алюминия и хрома; в) металлы: хром кобальт титан вольфрам.
При каждом взрыве длящемся примерно 023 секунды образуется слой толщиной примерно 0007 мм. Многослойные покрытия толщиной 002 - 04 мм получают многократно повторяя взрывы.
Покрытие обладает высокой твердостью и износостойкостью малой пористостью (менее 1 %) высокой прочностью сцепления с основным металлом.
Преимуществом способа детонационного нанесения порошков является невысокая температура нагрева металла-основы (менее 250 °С) что позволяет наносить слой порошка на закаленную поверхность без риска ее отпуска.
Технологические возможности способа позволяют наносить покрытия на цилиндрические внешние поверхности диаметром до 1000 мм и внутренние диаметром более 15 мм а также на плоские поверхности сложной конфигурации.
Примером использования данного способа может служить восстановление детонационным покрытием порошком ВК - 15 закаленной поверхности гибочного штампа из стали Х12М имеющей твердость НRC -57 - 61.
При наплавке изношенных поверхностей зачастую нельзя получить восстановленную поверхность достаточной твердости. Для этого необходимо проводить термическую обработку. Наиболее выгодным является использование метода закалки токами высокой частоты (ТВЧ).
Метод разработан советским ученым Вологдиным В.П.[2].
Основан на том что если в переменное магнитное поле создаваемое проводником-индуктором поместить металлическую деталь то в ней будут индуцироваться вихревые токи вызывающие нагрев металла. Чем больше частота тока тем тоньше получается закаленный слой.
Обычно используются машинные генераторы с частотой 50 15000 Гц и ламповые генераторы с частотой больше 106 Гц. Глубина закаленного слоя – до 2 мм.
Высокая скорость нагрева смещает фазовые превращения в область более высоких температур. Температура закалки при нагреве токами высокой частоты должна быть выше чем при обычном нагреве.
При правильных режимах нагрева после охлаждения получается структура мелкоигольчатого мартенсита. Твердость повышается на 2 4 HRC по сравнению с обычной закалкой возрастает износостойкость и предел выносливости.
Перед закалкой ТВЧ изделие подвергают нормализации а после закалки низкому отпуску при температуре 150 200oС (самоотпуск).
Наиболее целесообразно использовать этот метод для изделий из сталей с содержанием углерода более 04 %.
Преимущества метода:
большая экономичность нет необходимости нагревать все изделие;
более высокие механические свойства;
отсутствие обезуглероживания и окисления поверхности детали;
снижение брака по короблению и образованию закалочных трещин;
возможность автоматизации процесса;
использование закалки ТВЧ позволяет заменить легированные стали на более дешевые углеродистые;
позволяет проводить закалку отдельных участков детали.
Основной недостаток метода – высокая стоимость индукционных установок и индукторов.
Целесообразно использовать в серийном и массовом производстве.
Выбор и обоснование способов восстановления вилки.
Выбор способа зависит от конструктивно-технологических особенностей детали условий ее работы величины износов характера дефектов и особенностей самих способов восстановления определяющих долговечность отремонтированных деталей и себестоимость ремонта.
Конструктивно-технологические особенности деталей определяются их формой размерами материалом видом термообработки точностью изготовления шероховатостью поверхности типом посадок видом трения и величиной допустимого и предельного износа при эксплуатации.
Зная конструктивно-технологические особенности детали и условия ее работы а также эксплуатационные свойства различных способов ремонта можно в первом приближении решить вопрос о применении того или иного способа восстановления для данной детали.
Восстановление зева вилки будем производить наплавкой в среде углекислого газа. Наплавку в защитных газах применяют в тех случаях когда невозможны или затруднены подача флюса и удаление шлаковой корки. Преимуществами данного вида наплавки являются визуальное наблюдение за процессом и возможность его широкой механизации и автоматизации с использованием серийного сварочного оборудования. Ее применяют при наплавке деталей в различных пространственных положениях внутренних поверхностей глубоких отверстий мелких деталей и сложных форм и т.п. Технология выполнения наплавки в защитных газах во многом сходна с технологией наплавки под флюсом отличие лишь в том что вместо флюсовой применяют газовую защиту зоны сварки. Помимо перечисленных преимуществ это освобождает сварщика от необходимости засыпки флюса и удаления шлака. С целью уменьшения разбрызгивания металла наплавка в защитном газе производится самой короткой дугой.
Наплавка может производиться в углекислом газе аргоне гелии и азоте. Высоколегированные стали а также сплавы на алюминиевой и магниевой основе наплавляются в аргоне или гелии. Наплавка меди и некоторых ее сплавов может производиться в азоте который ведет себя по отношению к ней нейтрально. При наплавке углеродистых и легированных сталей используют более дешевый углекислый газ. Наплавка может производиться как плавящимся так и неплавящимся электродами. Неплавящийся вольфрамовый электрод обычно применяют при наплавке в аргоне и гелии. Наибольшее распространение получила наплавка в углекислом газе плавящимся электродом на постоянном токе обратной полярности. Учитывая что углекислый газ окисляет расплавленный металл в наплавочную проволоку обязательно вводят раскислители (марганец кремний и др.). При наплавке применяют как проволоку сплошного сечения так и - порошковую. Для наплавки деталей из углеродистых и низколегированных сталей с целью восстановления их размеров применяют сварочные проволоки сплошного сечения Св-08ГС Св-08Г2С Св-12ГС а также наплавочные Нп-40 Нп-50 Нп-30ХГСА и др. При необходимости получения наплавленного слоя с особыми свойствами применяют порошковые проволоки.
Недостатком способа является то что в процессе наплавки в углекислом газе наблюдается сильное разбрызгивание жидкого металла приводящее к налипанию брызг на мундштук и засорению сопла горелки. Кроме того возможность сдувания газовой струи ветром затрудняет наплавку на открытом воздухе.После наплавки проводим механическую обработку и закалку ТВЧ.
Изношенную резьбу ремонтируем установкой стандартной резьбовой втулки. Для этого резьбу рассверливаем и нарезаем резьбу под наружную резьбу втулки. После этого вставим втулку на фиксатор резьбы.
Проектирование технологического процесса восстановления вилки.
С учетом имеющихся дефектов и выбранного способа восстановления технологический процесс восстановления вилки будет следующим:
5 Моечная операция (очистка вилки от грязи и смазки);
0 Дефектация (дефектовать вилку);
5 Наплавочная операция (наплавить зев вилки);
0 Фрезерная операция (фрезеровать зев);
5 Сверлильная операция (рассверлить резьбу);
0 Резьбонарезная операция (нарезать резьбу под ремонтную втулку);
5 Слесарно-механическая операция (установить ремонтную втулку);
0 Закалка (закалить зев ТВЧ);
5 Контрольная операция (контролировать восстановленные поверхности).
Подробный технологический маршрут восстановления вилки с указанием применяемого оборудования и режимов обработки представлен в Приложении и на листе [2] графической части.
Выбор оборудования и инструмента.
При выборе оборудования для каждой технологической операции необходимо учитывать назначение обработки габаритные размеры деталей размер партии обрабатываемых деталей расположение обрабатываемых поверхностей требования к точности и качеству обрабатываемых поверхностей.
Наплавку производим выпрямителем ВСГ-3 с генератором НД наплавочной головкой ГМВК-2 и дросселем РСТЭ-34 проволокой Нп-30ХГСА.
Зев фрезеруем на фрезерном станке 6К82Ш табл. 2 установив вилку в тиски. Фрезерование зева производим пальцевой фрезой ГОСТ 2679-78.
Широкоуниверсальный консольно-фрезерный станок 6К82Шпредназначен для выполнения всех видов фрезерных работ сверления зенкерования и растачивания отверстий на деталях из черных и цветных металлов их сплавов и пластмасс в условиях единичного мелкосерийного и серийного производства.
Уверенный привод главного движения и тщательно подобранные передаточные отношения обеспечивают оптимальные режимы обработки при различных условиях резания и полное использование возможностей режущего инструмента.
Простота обслуживания и быстрая переналадка приспособлений и инструмента представляют значительные удобства при использовании станка в мелкосерийном производстве. Автоматическая система смазки узлов обеспечивает неприхотливость и надежность станка в самых жестких условиях эксплуатации
Таблица 2 – Техническая характеристика фрезерного станка 6К82Ш.
Размеры рабочей поверхности стола мм
Наибольшее перемещение стола мм
Мощность электродвигателей приводов кВт
- вертикального шпинделя
- горизонтального шпинделя
Габаритные размеры станка мм
Сверление и нарезание резьбы производим на станке вертикально-сверлильный 2Т125 табл. 3 и табл. 4 сверлом ø 108 ГОСТ 10902-77 и метчиком М12×15 -7Н ГОСТ 3266-81.
Таблица 3 - Технические данные ихарактеристики 2Т125.
Наибольший условный диаметр сверления мм
Наибольший диаметр нарезаемой резьбы мм встали
Расстояние от оси шпинделя до образующей колонны (вылет) мм
Наибольшее перемещение шпинделя мм
Расстояние от торца шпинделя до стола мм
Расстояние от торца шпинделя до плиты мм
Размеры рабочей поверхности мм:
Количество скоростей шпинделя
Пределы частот вращения шпинделяобмин
Количество подач шпинделя
Величина подач шпинделя ммоб
Мощность привода главного движения кВт
Габариты станка (LxBxH) мм не более
Масса станка сохлаждением кг не более
Таблица 4 - Комплект поставки станка.
ВХОДИТ В КОМПЛЕКТ ИСТОИМОСТЬ СТАНКА ИНСТРУМЕНТ ИПРИНАДЛЕЖНОСТИ
Втулки ГОСТ 13598-85
— 6100-0142 (Морзе 3-1)
— 6100-0144 (Морзе 3-1)
Клин 7851-0012 ГОСТ 3025-78
ПОСТАВЛЯЕТСЯ ПО ТРЕБОВАНИЮ ЗАКАЗЧИКА ЗА ОТДЕЛЬНУЮ ПЛАТУ
Патрон сверлильный 6150-4020-03 ТУ РБ 022.3728.021-95
Тиски 7200-0215-02 ГОСТ 16518-96
Патрон резьбонарезной 045.0730.000
Головки ТУ2.035.0223723.001-90:
— 6251-4002-05 (М10)
— 6251-4002-06 (М12)
Закалку ТВЧ производим на универсальной установке для закалки деталей ТВЧ при помощи индуктора.
Контролирование восстановленных поверхностей производим штангенциркулем ШЦ – 1-150-01 ГОСТ 165-80 линейкой стальной 500мм.
Расчет режимов обработки и норм времени.
Расчет режимов обработки и норм времени производим по методике изложенной в [6].
Операция 015 – наплавочная
Для обеспечения стабильности процесса наплавки необходимо правильно установить индуктивность за счет изменения числа витков дросселя. Для выпрямителя ВСГ-3М величина индуктивности 05 мГ что соответствует 10 виткам дросселя РСТЭ-34.
Шаг наплавки должен быть в 1 3 раза больше диаметра наплавочной проволоки. Выбираем проволоку для наплавки в зависимости от диаметра вала: все восстанавливаемые поверхности имеют диаметры которые входят в диапазон размеров 60 80 мм поэтому проволока для наплавки – Нп-30ХГСА ГОСТ 10543-75 диаметром 10 мм. Тогда шаг наплавки будет равен
где - диаметр наплавочной проволоки мм ().
Амплитуда вибрации электродной проволоки равна
Скорость наплавки определяется в зависимости от требуемой толщины наплавленного слоя по формуле
где - диаметр проволоки мм ();
- скорость подачи проволоки ммин;
- толщина наплавляемого слоя мм;
- шаг наплавки мм ();
- коэффициент учитывающий угар ().
Скорость подачи проволоки
где - напряжение наплавки В ();
- ток наплавки А ().
Толщина наплавленного слоя
где - коэффициент формирования шва ().
Зная скорость подачи проволоки и толщину наплавляемого слоя находим скорость наплавки
Угол подачи проволоки к детали 45º расход охлаждающей жидкости 06 лмин.
Особенность нормирования при автоматической наплавке на специальной установке или приспособленном токарном станке состоит в необходимости учета как факторов сварочного процесса так и режимов используемых при токарной обработке.
Норма штучно-калькуляционного времени
где - основное время мин;
- вспомогательное время мин;
- время обслуживания рабочего места мин;
- подготовительно-заключительное время на одну деталь мин.
В зависимости от того какие параметры процесса автоматической наплавки известны определение нормы времени осуществляется по формуле:
- при известной скорости наплавки и шаге наплавки:
где - шаг наплавки мм ;
- скорость наплавки ммин ;
- общая длина наплавляемых поверхностей мм ;
- число проходов при наплавке ;
- толщина наплавляемого слоя за один проход мм ;
- коэффициент учитывающий время обслуживания рабочего места отдых и личные надобности рабочего;
- вспомогательное время на установку закрепление и снятие детали мин ;
- время на очистку и контроль погонного метра наплавленного валика минм ;
- подготовительно-заключительное время на ознакомление с работой наладку оборудования и сдачу наплавленных деталей и оснастки.
Тогда норма штучно-калькуляционного времени будет равно:
Операция 020 – фрезерная.
Фрезерование шпоночного паза под диск производим на широкоуниверсальном фрезерном станке марки 6К82Ш.
В зависимости от марки фрезеруемой стали назначаем подачу и глубину резания .
Мощность расходуемая на фрезерование равна:
Скорость резания при фрезеровании равна:
где - коэффициенты и показатели степеней которые характеризуют условия обработки
- диаметр фрезы мм ;
- поправочный коэффициент на скорость резания учитывающий фактические условия резания:
где - коэффициент учитывающий качество обрабатываемого материала ;
- коэффициент учитывающий состояние поверхности заготовки ;
- коэффициент учитывающий материал инструмента .
Скорость резания равна:
Частота вращения фрезы равна:
Так как частота вращения шпинделя устанавливается бесступенчато тогда .
Сила резания определяется по формуле:
Рассчитанная мощность менее мощности выбранного станка следовательно обработку производим на данном станке.
Конструкторская разработка индуктора.
Для проектирования станочного приспособления необходимо произвести анализ исходных данных который включает: последовательность и содержание операций; принятое базирование; используемое оборудование и инструмент; режимы резания; запроектированную производительность с учетом времени на установку закрепление и снятие обработанной детали; размеры допуски шероховатость обрабатываемых поверхностей деталей; марку и вид термической обработки материала [6].
Для закалки деталей ТВЧ применяются индукторы. Индуктор представляет собой дистанционный проводник токов высокой частоты. Индукторы изготавливаются из медных трубок внутри которых циркулирует вода благодаря чему они не нагреваются. Форма индуктора соответствует внешней форме изделия при этом необходимо постоянство зазора между индуктором и поверхностью изделия.
После нагрева в течение 3 5 с вилку зевом быстро перемещается в специальное охлаждающее устройство – спрейер через отверстия которого на нагретую поверхность разбрызгивается закалочная жидкость.
Сборочный чертеж индуктора приведен на листе [3] графической части курсовой работы.
В курсовой работе произведено проектирование технологического процесса восстановления вилки включения сцепления. Произведен анализ способов восстановления полуосей и выбран способ наплавки в среде углекислого газа. Основным достоинством являются визуальное наблюдение за процессом и возможность его широкой механизации и автоматизации с использованием серийного сварочного оборудования. Произведены расчеты режимов наплавки и механической обработки для каждой операции. Произведена конструкторская разработка индуктора для закалки ТВЧ.
Список использованных источников
Баранов Л.Ф. Техническое обслуживание и ремонт машин. Ростов нД: Феникс 2001. 416 с.
Воловик Е.Л. Справочник по восстановлению деталей. М.: Колос 1981. 351 с.
Есенберлин Р.Е. Восстановление деталей сваркой наплавкой и пайкой. М.:Транспорт 1994. 256 с.
Основы технологии производства и ремонта машин: Метод. указания.Сост. А.Д. Полканов ВоГТУ: - Вологда 1999 г.
Справочник технолога-машиностроителя. Т. 1Под редакцией А.Г. Косиловой и Р.К. Мещерякова. – М.: Машиностроение 1972 г.
Справочник технолога-машиностроителя. Т. 2Под редакцией А.Н. Малого. – М.: Машиностроение 1972 г.
ОК №20 - фрезеровка.doc
Наименование операции
Оборудование устройство с ЧПУ
Обозначение программы
Установить деталь и закрепить.
Фрезеровать зев фрезой пальцевой ГОСТ 2679-78
Снять деталь контролировать все обработанные поверхности: штангенциркулем ШЦ-1-150-01 ГОСТ165-80;
ОПЕРАЦИОННАЯ КАРТА МЕХАНИЧЕСКОЙ ОБРАБОТКИ
Фрезеровать зев вилки выдерживая размеры.
ОК №015 - Наплавка.doc
Обозначение документации
Код наименование оборудования
Наименование детали сборочной единицы или материала
Пl I U Vнап S ЧП dэ hэ lэ
Выпрямитель ВСГ-3 генератор НД наплавочная головка ГМВК-2 дроссель РСТЭ-34
Установить деталь и закрепить.
Наплавить поверхность выдерживая размеры
Снять деталь и контролировать наплавленные поверхности
Щетка металлическая напильник 2820-0018 ГОСТ 1465-80 штангельциркуль ШЦ-1-125-01 ГОСТ 165-80.
0А 25В 75мин 20 мм 10 мм 191 мм 46 мм
ОПЕРАЦИОННАЯ КАРТА НАПЛАВКИ
“Строительные и дорожные машины”
Наплавить зев вилки выдерживая размеры.
Рекомендуемые чертежи
- 22.07.2023
- 20.03.2015
- 24.01.2020
- 30.03.2018