Расчет щековой дробилки ЩДП 900х1200


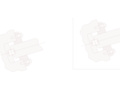
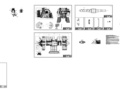
- Добавлен: 25.10.2022
- Размер: 2 MB
- Закачек: 2
Описание
Состав проекта
![]() |
![]() |
![]() |
![]() ![]() ![]() |
![]() ![]() ![]() ![]() |
![]() ![]() ![]() |
![]() ![]() |
![]() ![]() ![]() |
Дополнительная информация
Пояснительная записка.docx
1.Обоснование и описание выбранной технологической схемы5
2.Технические характеристики щековых дробилок.8
1.Назначение область применения конструкция принцип действия щековой дробилки с простым движением щеки ЩДП 900х1200.9
2.Проведение патентных исследований и анализ их результатов.13
3.Сущность модернизации щековой дробилки с простым движением щеки ЩДП 900х1200.21
4.Расчет кинематических параметров щековой дробилки.22
4.1.Определение угла захвата.22
4.2.Определение производительности.22
4.3.Определение мощности электродвигателя.23
5.Определение усилий и расчет деталей на прочность.25
5.1.Расчет клиноременной передачи.25
5.3.Расчет распорных плит.28
5.4.Расчет подвижной щеки30
5.5.Расчет маховика33
5.6.Расчет шпоночных соединений34
Техника безопасности при эксплуатации ЩДП 900х120036
1.Анализ производственных условий работы дробилки36
2.Мероприятия исключающие травматизм и заболевания.37
3.Пожарная безопасность38
4.Мероприятия по охране окружающей среды39
Развитие народного хозяйства предполагает увеличение добычи и переработки сырья. Достигается это путем строительства новых и реконструкции существующих предприятий промышленности строительных материалов где сырье являясь необходимым продуктом подвергается дроблению.
Предусмотренное снижение себестоимости продукции при одновременном повышение ее качества увеличение рентабельности производства основывается на широком внедрении новой техники и повышением эффективности использования существующего оборудования. Особое внимание при этом должно быть уделено совершенствованию широко используемого дробильного оборудования эксплуатационные расходы от которого составляют значительную часть общих расходов на переработку сырья.
Дробление является основным процессом при производстве таких важных строительных материалов как цемент щебень.
В ряде случаев дробильные машины стоят во главе крупных технологических линиях где особенно важно обеспечить их беспрерывную надежную работу так как простои по каким либо причинам вызывают простой всей линии и приносят значительные убытки предприятию. В связи с различными характеристиками перерабатываемого материала а так же различными требованиями к конечному продукту машиностроительные заводы должны выпускать самые разнообразные по типу и размерам дробильные машины причем наряду с созданием новых непрерывно применить и совершенствовать существующие конструкции машин и увеличивать объем их выпуска.
При выборе дробильной машины или комплекта машин обязательно учитывают физико-механические свойства исходного продукта: прочность хрупкость образивность крупность кусков исходного материала крупность кусков исходного продукта. В зависимости от этих факторов существует несколько типов дробления: крупное мелкое средние первичное вторичное что проводит к применению машин определенных типов. Для крупного дробления в промышленности строительных материалов широко используется щековые дробилки с простым движением подвижной щеки так как при крупном дроблении в щековых дробилках со сложным движением щеки эксцентриковый вал точнее его подшипники испытывают огромные нагрузки.
В дробилках с простым движением цепи отсутствует механизм истирания а материал измельчается только раздавливанием поэтому эти дробилки широко применяются для дробления высокопрочных пород типа гранитов базальтов кварцев.
Технологическая часть
1.Обоснование и описание выбранной технологической схемы
Щебень получают из естественного камня дроблением взорванных пород. Добыча пород ведется открытым способом в три уступа. Высота первых двух уступов 10 м высота третьего 8 м. При увеличении площадей карьера ведутся взрывные работы на глубину до 8 м при этом плодородный слой почвы глубиной 50 м снимается и складируется в склад чернозема. Прочность породы -115 мПа. Взорванные породы грузятся экскаватором в автомобили и доставляется на дробильно-обогатительную фабрику. Качество щебня характеризуется как прочностью так и количеством засоряющих примесей. Содержание в щебне пылевидных и глинистых частиц для известковых пород не должно превышать 07% по массе поэтому при температуре выше -5 оС щебень промывают чтобы улучшить качество строительного материала. В зимнее время при более низких температурах щебень не промывают при этом качество не снижается. На рисунке 1.1 показана технологическая схема производства щебня. При данной технологии получают щебень двух фракций: 5-20 мм фракция 20-70 мм и бутовый камень который используется для бетонных работ. Исходная горная масса размером 0-700 мм выгружается в приемный бункер объемом 20 м3. Из бункера горная масса пластинчатым питателем подается в зево щековой дробилки ЩДП-900х1200 где происходит измельчение известняка от 0 до 180 мм. Пройдя первую стадию измельчения ленточным транспортиром с шириной ленты 1200 мм горная порода подается на колосниковый грохот где происходит разделение на фракции 0-70 мм и 70-180 мм. Фракция 70-180 мм ленточным транспортиром №3 и №6 подается в конусную дробилку КСД-1650 также эта фракция транспортиром с шириной ленты 900 мм может транспортироваться в склад бутого камня. Пройдя вторую стадию измельчения материал размером 0-70 мм подается ленточным транспортиром №4 на грохот ГУП-2К где происходит отделение фракций 0-5 мм
Рисунок 1.1. Технологическая схема производства.
от основной массы и отгрузка этой фракции ленточным транспортиром в автомобили. В тоже время фракция 5-70 мм ленточным транспортиром №5 и №7 подается на второй грохот ГУП-2К где также происходит разделение на фракции 0-5 мм и 5-70 мм. Фракция 0-5 мм идет в отходы а фракция 5-70 мм подается в корытную мойку где происходит обогащение горной массы. Шлак-пульпа из корытной мойки поступает в станцию шлакоудаления откуда насосами пульпа по трубопроводу транспортируется в отстойник. В отстойнике происходит осаждение твердых частиц. Очищенная вода по трубопроводу с помощью насосов подается в корытную мойку. Из корытной мойки транспортирами №9 и №10 измельченный материал подается на грохот СН-60 где происходит окончательное обезвоживание и разделение на фракции 5-20 мм и 20-70 мм. Фракция 5-20 мм транспортером №12 подается на склад щебня откуда транспортером №13 щебень загружается в вагоны. Фракция 20-70 мм. транспортерами №11 и №11а подается на склад щебня откуда ленточным транспортером №14 грузится в вагоны. В зимнее время при температуре ниже –
оС корытные мойки не работают. Обогащение материала происходит на грохотах ГУП-2К и СМ-60 качество выпускаемого щебня при этом не изменяется потому что глинистые включения и другие мелкие частицы при более низких температурах отсеиваются лучше чем в летнее время.
2.Технические характеристики щековых дробилок.
Анализируя таблицу можно сделать вывод что дробилки с простым движением щеки имеют большую производительность используется более крупный исходный материал но это приводит к большим энергозатратам следовательно использование дробилок со сложным движением щеки представляется целесообразнее
1. Назначение область применения конструкция принцип действия щековой дробилки с простым движением щеки ЩДП 900х1200.
В дробилках с простым движением щеки (ЩДП) 1 (рис. 1 а) последняя подвешена на оси 2. Щека совершает качательные движения по дуге окружности которые ей сообщает вращающийся эксцентриковый вал 3 через шатун 4 и распорные плиты 5.
Рисунок 1. Схема ЩДП
Материал дробится при сближении щек а при удалении их друг от друга куски материала опускаются вниз и если их размеры меньше ширины выходной щели выпадают из камеры. Затем цикл повторяется. В ЩДП материал измельчается раздавливанием и частично изломом и раскалыванием поскольку на обеих щеках установлены дробящие плиты с рифлениями в продольном направлении.
Кинематическая схема ЩДП позволяет создавать относительно бОльшие нагрузки на измельчаемый материал чем в ЩДС при одинаковых вращательных моментах на приводных валах. Это особенно важно при дроблении больших кусков прочных материалов. Существенным недостатком ЩДП (рис. 1 а) является малый ход сжатия в верхней части камеры дробления. Для ЩДС характерен значительный износ дробящих плит. Однако конструкция ЩДС в целом более проста и менее металлоемка.
В зависимости отконструкции механизма приводящего вдвижение щеку различают дробилки срычажным икулачковым механизмами атакже сгидравлическим передаточным механизмом.
Рисунок 2. Схема щековой дробилки с простым движением щеки.
Типовая конструкция щековой дробилки для крупного дробления с простым движением щеки показана на рис. 2. Подвижная щека 3 ось 4 которой установлена в подшипниках скольжения закрепленных на боковых стенках станины 7 получает качательные движения через распорные плиты 10 и 11 от шатуна 6 подвешенного на эксцентричной части вала 5 приводимого во вращение от электродвигателя через клиноременную передачу. Рабочие поверхности щек футеруют сменными дробящими плитами 12 и 13 изготавливаемыми из износостойкой стали Ст110Г13Л. Боковые стенки камеры дробления также облицованы сменными плитами 2. Рабочую поверхность дробящей плиты как правило изготавливают рифленой и реже (для первичного дробления) гладкой. От продольного профиля плит зависят условия захвата кусков и гранулометрический состав материала.
Циклический характер работы щековых дробилок максимальное нагружение при сближении щек и холостой ход при их расхождении создает неравномерную нагрузку на двигатель. Для выравнивания нагрузки на приводном валу устанавливают маховик и шкив-маховик. Маховики «аккумулируют» энергию при холостом ходе и отдают ее при ходе сжатия.
В процессе эксплуатации возникает необходимость регулировать ширину выходной щели камеры дробления. В крупных дробилках для этого устанавливают разные по толщине прокладки между упором 9 и задней стенкой станины. Гарантированное замыкание звеньев механизма привода подвижной щеки осуществляется пружиной 7 и тягой 8.
В конструкциях современных дробилок предусматривается установка самовосстанавливающихся после срабатывания устройств предохраняющих элементы машины от поломок при попадании в них «недробимых» предметов. На практике применяют следующие варианты предохранительных устройств: подпружиненный рычаг шарнирно соединенный с подвижной щекой; пружина в сочетании с распорной плитой; пружина в сочетании с рычагом и распорной плитой и т.д.
2. Проведение патентных исследований и анализ их результатов.
3. Сущность модернизации щековой дробилки с простым движением щеки ЩДП 900х1200.
В проведенном анализе конструкции щёковой дробилки с простым движением подвижной щеки был выявлен следущий недостаток: распорная плита в узлах крепления имеет линейный контакт с ответственными деталями а сами узлы крепления выполнены без соединительных элементов. Во время работы в этом устройстве происходит повышенный износ опорных поверхностей плит и ответственных деталей вследствие их взаимного проскальзывания во время работы.
С целью упрощения сборки узла крепления распорной плиты что позволяет снизить затраты на её изготовление и проведение ремонтно- наладочных операций можно применить следующий патент: Авторы изобретения Г.А.Сперанский Б.И.Коновалов Заявлено 07.01.77(21) 244162829-33
В данной модернизации с целью упрощения конструкции и сборки узлов крепления распорной плиты предлагается соединительные элементы выполнить сферическими вмонтировать без зазоров в цилиндрические гнёзда расположенные в распорной плите и ответных деталях причём ось каждого цилиндрического гнезда перпендикулярна касательной к опорным поверхностям распорной плиты а диаметр равен максимальному диаметру сферы соединительных элементов. С целью установки распорной плиты без люфтов между соединительными элементами и дном каждого цилиндрического гнезда предлогается установить шайбы из упруго- пластичного материала например меди.
4. Расчет кинематических параметров щековой дробилки.
4.1.Определение угла захвата.
Дробление материала в щековой дробилке возможно в том случае когда угол между щеками не превышает определенной величины. Как только величина угла переходит этот предел дробильный материал не будет захватываться и начнет выталкиваться вверх. С другой стороны при малых значениях угла степень измельчения материала будет малой что отрицательно сказывается на производительности.
Угол захвата определяется по формуле:
f - коэффициент трения каменных материалов f = 03.
После подстановки найденного значения в формулу (2.1) получим:
Практически угол захвата принимают от 15о до 25о. Для щековой дробилки принимают .
4.2.Определение производительности.
Производительность дробилки определяется по формуле [2]:
где - коэффициент учитывающий размер дробилки и зависящий от размеров загрузочного отверстия K= 11;
C - коэффициент кинематики учитывающий характер траектории движения подвижной щеки C=084;
Scp - величина среднего хода щеки м;
L - длина загрузочного отверстия L=12м;
d - наибольшая величина ширины разгрузочного отверстия м;
n- число оборотов вала дробилкиС-1;
B - ширина загрузочного отверстия B=09м;
Величина среднего хода:
где Sm - ход сжатия в нижней точке мм;
Sb - ход сжатия в верхней точке мм;
где m - размер выходной щели b= 130мм.
Sm= 8+ 026130=418 мм
Ход сжатия в верхней точке:
После подстановки найденных значений в формулу (2.3) получим:
После подстановки найденных значений в формулу (2.2) получим:
4.3.Определение мощности электродвигателя.
Мощность электродвигателя определяем по формуле
где пр - коэффициент пропорциональности учитывающий изменение прочности материала с изменением размера кусков Кпр=0698;
сж - предел прочности дробимого материала на сжатие Есж=115мПа
В - поправочный коэффициент учитывающий число кусков укладывающихся по длине камеры
Е -модуль упругости материала Е=35·1010
- коэффициент полезного действия привода =085
Dср - средневзвешенный размер куска исходного материала Dср=0350м
dср - средневзвешенный размер куска выходящего из дробилки м.
Поправочный коэффициент учитывающий число кусков для дробилки 900*1200 длиной камеры 1200 а Dср =0350 при этом
Фактически может уложиться три куска следовательно
Средневзвешенный размер куска выходящего из дробилки:
После подстановки найденных значений в формулу (2.6) получим:
Выбираем электродвигатель мощностью 100кВт и n=750обмин 4 А 500 MS ГОСТ 19523 -81
5.Определение усилий и расчет деталей на прочность.
5.1.Расчет клиноременной передачи.
Определяем передаточное число по формуле:
где nэл.д - частота вращения вала электродвигателя nэл.д=750обмин;
nэл.в - частота вращения вала nэл.в=180обмин.
Из таблицы 7.6 для сечения при минимальном диаметре шкива d1=500мм передаточном числе U=416 и частоте вращения n1- nэл.дв=750обмин находим номинальную мощность передаваемую одним ремнем:
Находим диаметр ведомого шкива по формуле:
d2= d1·(1- )·U (2.9)
где - относительное в передаче = 002.
d2=05·(1-002)·416=2034м.
Принимаем стандартный размер шкива d2=2040м.
Расчетную длину ремня определим по формуле:
где а - межосевое расстояние а = 1500мм.
Из стандартного ряда предпочтительных расчетных длин выбираем Lр=7100мм.
Определяем окончательное межосевое расстояние по формуле:
где =05··( d1+ d2) (2.12)
=05·314·(500+2040) =39898мм.
y=025·(d2-d1)2 (2.13)
y=025·(2040-500)2=385мм.
После подстановки найденных значений в формулу (2.11) получим:
Найдем угол обхвата ремнем шкива по формуле:
=180-573·(d2-d1)а (2.14)
=180-573·(2040-500)1555=123о.
Найдем скорость ремня мс:
Скорость ремня находится между 15 мс и 20 мс что соотве6тствует правильному выбору ремня.
Определим мощность передачи одним ремнем кВт:
где Cα - коэффициент угла обхвата Cα = 082;
СL - коэффициент учитывающий длину ремня СL = 104;
Cp - коэффициент динамичности и режима работы Cp = 17.
Определим число ремней по формуле
где N- мощность двигателя N=100;
Np-мощность передачи одним ремнем;
Определим вращающий момент по формуле Н·м
где - угловая скорость с-1.
Угловая скорость муфты
= (314·750)30 = 785с-1.
После подстановки найденного параметра в формулу (2.18) получим:
Определим расчетный момент Н·м
где Кр- коэффициент режима работы дробилки Кр=25.
Мр=12739·25=318475 Н·м
По таблице для валов диаметром 90 и 100мм находим муфту с наружным диаметром D=500мм и допускаемым расчетным моментом Мр=8000Н*м.
Проверяем пальцы на изгиб по формуле:
D0 - диаметр окружности на которой расположены пальца мм;
Z - количество пальцев Z=10;
dп - диаметр пальца мм;
[п] - допускаемое напряжение при изгибе пальцев.
Проверим втулки на сжатие мПа
5.3.Расчет распорных плит.
Рисунок 2.7 Схема к расчету распорной плиты.
Усилия Т (рисунок 2.8) действующие вдоль распорных плит достигают максимальной величины когда плиты находятся в крайнем верхнем положении.
С увеличением угла возрастает усилие Т а при =900 cos900=0 т. Е. при горизонтальном положении распорных плит усилие Т неограниченно возрастает. Следовательно в щековой дробилке распорные плиты не должны располагаться в одну линию. Угол принимаем равным 120.
Усилие действующее вдоль распорных плит определяем по формуле:
Определяем площадь поперечного сечения плиты по формуле:
где [сж] – допустимое напряжение на сжатие [сж] = 685 мПа
При ширине распорной плиты b1=1100мм толщина ее составляет:
Принимаем толщину передней распорной плиты равной 45 мм.
Заднюю распорную плиту изготавливаем стальной из двух частей скрепляемых предохранительными болтами. Болты изготовляют из ст.3 и пределом прочности Еb=390мПа. Предел прочности на срез
Запас прочности для материала берем тогда допускаемое напряжение
Число болтов принимаем равным 12.
Диаметр болтов определим по следующей формуле
где i –число болтов i = 12.
Принимаем болты диаметром 40 мм.
5.4.Расчет подвижной щеки
Рисунок 2.8 Схема к расчету подвижной щеки
На щеку действует сила Трасч. которую можно разложить на две составляющие Т1 и Т2.
Определим силу Т1 по формуле
Силу Т2 изгибающую ось подвижной щеки определим по формуле
Определим силу Qmax которая приложена в точке соприкосновения щеки с дробимым куском небольшего размера
d1 – расстояние от оси подвижной щеки до линии действия силы Qmax d1 = 700 мм.
Подвижная щека должна иметь небольшую массу и быть достаточно прочной поэтому она изготовлена с ребрами жесткости.
При небольших размерах кусков материалов Qmax будет максимальной. Если щеку дробилки рассматривать как балку на двух опорах опорах со средоточенной нагрузкой (рисунок 2.9) М4 будет равен.
Рисунок 2.9 Расчетная схема
Напряжение в опасном сечении подвижной щеки определим по формуле
где W – момент сопротивления опасного сечения м3;
[л] - допустимое сопротивление для стального литья
h - толщина профиля м;
y – координата центра тяжести м.
Рисунок 2.10. Схема к расчету щеки
Возьмем оси Y1 X1 как показано (рисунок 2.10) тогда координаты центра тяжести Y определим по формуле
где Fл = b1 ·h1 (2.34)
Fл =0080·040=0032 м2
F2 = 115 ·008=0092 м2
Найденные значения подставим в формулу (2.37) и получим
Момент индукции поперечного сечения относительно оси XX определим по формуле
После подстановки найденных значений в формулу (2.36) получим
Определив момент сопротивления опасного сечения определим напряжение в сечении
Так как допустимое напряжение [п] для стального литья берется равным 115-130 мПА то напряжение 8858 мПа вполне допустимо так как п [п].
Размеры маховика определим из уравнения махового момента
где m – масса маховика кг;
D - диаметр маховика м;
N – мощность потребляемая щекой дробилкой кВт;
– угловая скорость диcцентринового вала радс;
– коэффициент неравномерности = 001.
Диаметр маховика определим из формулы
Принимаем = 19 мс и находим диаметр маховика
Из стандартного ряда диаметров маховика принимаем D = 204 м.
Массу обода маховика определим по формуле
Массу маховика с учетом спиц определим по формуле
На эксцентриковом валу установлено два маховика. Площадь сечений обода каждого из маховиков найдем из уравнения
где ρ – плотность материала ρ = 7100 кгм3.
Ширину шкива маховика берем равной 598 мм.
5.6.Расчет шпоночных соединений
Принимаем что нагрузка со стороны втулки на шпонку равномерно распределена как по высоте так и по длине шпонки. Из условия прочности по снятию рассчитаем по формуле
где [] – допустимое напряжение на смятие;
d – диаметр вала мм;
h – высота шпонки мм.
После подстановки найденных значений параметров в формулу (2.42) получаем
Напряжение на срез определим по формуле
где [] - допустимое напряжение на срез [] = 90 Нмм2
Рисунок 2.18 Шпоночное соединение
Рассчитаем шпоночное соединение на ведущем шкиве
гдеlP = 180-36=144 мм
Техника безопасности при эксплуатации ЩДП 900х1200
1. Анализ производственных условий работы дробилки
Работа дробилки связана с разрушением материала осуществляемого при помощи разбивания и раскалывания при котором происходит большое выделение пыли. Отсос пыли происходит у разгрузочного отверстия. Работа дробилки сопровождается среднечастотным шумом. Уровень шума составляет 100 Дб. Для снижения уровня шума дробилки обслуживающий персонал должен следить за интенсивностью смазки трущихся деталей.
Следующим аспектом обеспечения безопасности является предупреждение поражения персонала электрическим током. Привод ротора щековой дробилки работает от электродвигателя переменного тока. Для обеспечения необходимой защиты людей от поражения электрическим током все металлические части дробилки а также его электропривода должны быть заземлены. Защитное заземление в системе с изолированной нейтралью обеспечит электрическое соединение металлических частей оборудования с землей.
Из соображений безопасности данное заземление необходимо выполнять с малым сопротивлением что обеспечит полную безопасность в случае случайного прикосновения человека к оборудованию находящимся под напряжением.
Величина сопротивления заземляющего устройства для электрических установок данного типа не должна превышать 4 Ом.
На людей обслуживающий дробильное оборудование воздействует вибрация и шум. Щековую дробилку обслуживает один человек который следит за его исправной работой.
Существует ряд показателей определяющих факторы условий труда которые перечислены в таблице 3.1.
Допустимые значения
Фактические значение
Таблица 3.1 Факторы условий труда
2.Мероприятия исключающие травматизм и заболевания.
С целью уменьшения случаев травматизма при эксплуатации и ремонте щековой дробилки ночью рабочие места освещены согласно СНиП 2-007-79 не менее 50 Лк гирляндным освещением и персональными светильниками напряжением 12 В а в особо опасных местах подключаются прожекторы.
Для исключения допуска к вращающимся частям привода дробилки
предусмотрена установка защитных кожухов и различных ограждений.
Для уменьшения запыленности воздуха и охраны окружающей среды предусмотрена система пылеулавливания.
Определенная часть несчастных случаев приходится на электротравматизм. Все оборудование работает под высоким напряжением что является большой опасностью для человека поэтому произведем расчет заземления электрооборудования сырьевого цеха. Установленная мощность электрооборудования в цехе более 400 кВт. По требованиям утвержденным Минэнерго РФ при установленной мощности более 230-380 Вт сопротивление заземления допускается не более 4 Ом. Грунт в который закладывают заземление имеет сопротивление 1000 Омсм3. В качестве заземления приняты перфорированные трубы диаметром 53 см и длиной 200 см. Глубина заземления принимается равной 180 см. Расстояние между трубами равно 400 см а соединительная полоса имеет сечение 404 см.
Сопротивление точки одного сопротивления зависит от удельного сопротивления грунта глубины закладки труб размера сечения заземления.
3.Пожарная безопасность
В соответствии со СНиП 3-90-81 по не сгораемости данный цех относится к категории «Д» так как все основные конструкции здания выполнены из несгораемого материала: железобетона кирпича металлоконструкций. Территория завода асфальтирована и к каждому зданию обеспечен беспрепятственный подъезд.
На случай пожара цеха имеют достаточное количество выходов кроме того цеха завода имеют средства пожаротушения такие как пожарные щиты огнетушители гидранты из расчета один рукав на сто метров.
Склад ГСМ находится за пределами цеха. На видном месте установлены щиты с пожарным инвентарем таким как огнетушители багры лопаты ведра асбестовым полотном. Рядом со щитом установлен ящик с песком. Для тушения электрооборудования предусмотрены углекислотные огнетушители.
Тушение пожаров на заводе водой производится из водопроводной сети подсоединение к которой производится при помощи пожарных кранов. Связь с постом пожарной охраны обеспечивается через внутренние телефоны.
Соблюдение всех вышеперечисленных норм и правил обеспечит сокращение случаев пожара на производстве а в случае его возникновения при минимальных временных затратах локализовать очаг возгорания не допустив распространения огня.
4. Мероприятия по охране окружающей среды
Некоторые комбинаты строительных материалов выбрасывают в атмосферу много пыли которая вредно действует на здоровье людей вызывает различные заболевания. Кроме всего этого выбросы предприятий в своем масштабе нарушают структуру почв уменьшая их плодородие.
В настоящее время для обеспечения охраны окружающей среды в промышленности строительных материалов наметились два основных направления:
- борьба с загрязнением воздуха воды и почвы путем улавливания и обезвреживания пылегазовыделений и сточных вод;
- совершенствование существующих технологий производства строительных материалов.
Одним из таких является переход к замкнутым технологическим процессам малоотходной и безотходной технологии.
Для снижения выброса пыли в атмосферу предусмотрено применение новых осадительных электрофильтров «интеграл» в комплекте с трубчатыми коронирующими электродами.
Практика показала что при эксплуатации таких электродов степень очистки газов выросла с 96 % до 97%. Отсюда можно сделать вывод что пыле унос снизился на один процент.
В целях охраны окружающей среды от загрязнения сточными водами на предприятии предусмотрены отстойники для очистки воды после чего она выбрасывается в окружающую среду не принося урон природе и человеку.
В данном курсовом проекте произведен анализ конструкции научной и патентной информации о щековых дробилках осуществлен расчет модернизированной щековой дробилки ЩДП 900х1200. Определены основные параметры дробилки и приняты размеры рабочих органов. Для обеспечения работоспособности конструкции были проведены расчеты элементов дробилки на прочность.
Проведен патентный поиск с целью выявления наиболее прогрессивных технических решений в области создания щековых дробилок.
Распорная плита в узлах крепления имеет линейный контакт с ответственными деталями а сами узлы крепления выполнены без соединительных элементов. И целью модернизации является упрощенная конструкция крепления распорной плиты соединительные элементы сделать сферическими вмонтировать без зазоров в цилиндрические гнёзда расположенные в распорной плите и ответных деталях ось каждого цилиндрического гнезда перпендикулярна касательной к опорным поверхностям распорной плиты а диаметр равен максимальному диаметру сферы соединительных элементов.
Сапожников М.Я. Механическое оборудование предприятий строительных материалов изделий и конструкций. –М.: Высшая школа 1971. –382с.
Бауман В.А. Механическое оборудование предприятий строительных материалов изделий и конструкций. –М.: Машиностроение 1981. –324с.
Подэрни Р.Ю. Механическое оборудование карьеров. Учебник для вузов.
–М.: Горное дело 2007. –627с.
Клушанцев Б.В.Косарев А.И.Муйземнек Ю.А. Дробилки. Конструкция расчет особенности эксплуатации.-М.: Машиностроение 1990 г. 320 с
Пронин Б.А. Ревков Т.А. Бесступенчатые клиноременные и фрикцион-ные передачи Б.А. Пронин Т.А. Ревков. – М. : Машиностроение 1984. – 183 с.
gotovaya_schekovaya_drobilka_dwg.dwg

КР МО (ОК)-18084000000СБ
Мощность электродвигателя
Предел регулирования загрузочной щели
и впадиной) в открытом состоянии
Ширина загрузочной щели (между зубцом
Наибольший размер заегружаемых кусков
Ширина загрузочного отверстия
Техническая характеристика
*Размеры для справок
При сборке сегменты поз.29 установить в нижнем положении. 2. При сборке смазочные каналы маховика поз.1 и шкива поз.23 заполнить густой смазкой. 3. Отверстия в болтах поз.35
под шлицы поз.49 выполнить при сборке. 4. Фрикционные диски поз.24 и 25 и проволочную поверхность крышки поз.4 перед сборкой обезжирить
промыть в бензине и просушить. 5. Шлицевые соединения проверить на краску
величина бокового зазора должна быть в пределах 0
мм. В одновременном касании должно находиться не менее 75% зубьев. 6. Муфты после сборки отрегулировать на передачу момента в пределах 7
-8 т.м. Регулировку производить путем подтягивания или ослабления пружин. Разница величины осадки пружин должна быть в пределах ±1 мм. Для экспорта: Консервацию выполнить по ГОСТ 13168-69 группа II категория ОЖ. Срок хранения до переконсервации 3 года. Детали по стандартам предприятия изготовить согласно рабочим чертежам
указанным в графе "Примечание" спецификации. Покрытие по ГОСТ 9032-74-поз.19- эмаль ПФ-115 серо-голубая ГОСТ 6465-76
других поверхностей эмаль ПФ-115 красная ГОСТ 6465-76
покрытия которых производятся по входящим чертежам. Консервацию произвести по ГОСТ 13158-69
категория условий хранения и транспортирования Ж. Срок без переконсервации 3 года. Для экспорта: 1. Покрытие в районы умеренного климата по ГОСТ 9032-74 поз.19- эмаль АС-182 желтая VI Ж2; других поверхностей- эмаль ПФ-115 красная ГОСТ 6465-76 VI Ж2
покрытия которых производятся по входящим чертежам. 2. Покрытие в районы тропического климата по ГОСТ 9.032-74
поз.10 эмаль ХВ-110 желтая ГОСТ 12374-73. VI ОЖ2; других поверхностей- эмаль ПФ-115 красная ГОСТ 6465-76 VI ОЖ2; кроме поверхностей
покрытие которых производится по входящим чертежам.
Вал эксцентриковый в сборе
rrrrsrrerrsres-rr.dwg

Расчет кинематических параметров.doc
4.1. Определение угла захвата.
Дробление материала в щековой дробилке возможно в том случае когда угол между щеками не превышает определенной величины. Как только величина угла переходит этот предел дробильный материал не будет захватываться и начнет выталкиваться вверх. С другой стороны при малых значениях угла степень измельчения материала будет малой что отрицательно сказывается на производительности.
Угол захвата определяется по формуле:
f - коэффициент трения каменных материалов f = 03.
После подстановки найденного значения в формулу (2.1) получим:
Практически угол захвата принимают от 15о до 25о. Для щековой дробилки принимают .
4.2. Определение производительности.
Производительность дробилки определяется по формуле [2]:
где - коэффициент учитывающий размер дробилки и зависящий от размеров загрузочного отверстия K= 11;
C - коэффициент кинематики учитывающий характер траектории движения подвижной щеки C=084;
Scp - величина среднего хода щеки м;
L - длина загрузочного отверстия L=12м;
d - наибольшая величина ширины разгрузочного отверстия м;
n- число оборотов вала дробилкиС-1;
B - ширина загрузочного отверстия B=09м;
Величина среднего хода:
где Sm - ход сжатия в нижней точке мм;
Sb - ход сжатия в верхней точке мм;
где m - размер выходной щели b= 130мм.
Sm= 8+ 026130=418 мм
Ход сжатия в верхней точке:
После подстановки найденных значений в формулу (2.3) получим:
После подстановки найденных значений в формулу (2.2) получим:
4.3.Определение мощности электродвигателя.
Мощность электродвигателя определяем по формуле
где пр - коэффициент пропорциональности учитывающий изменение прочности материала с изменением размера кусков Кпр=0698;
сж - предел прочности дробимого материала на сжатие Есж=115мПа
В - поправочный коэффициент учитывающий число кусков укладывающихся по длине камеры
Е -модуль упругости материала Е=35·1010
- коэффициент полезного действия привода =085
Dср - средневзвешенный размер куска исходного материала Dср=0350м
dср - средневзвешенный размер куска выходящего из дробилки м.
Поправочный коэффициент учитывающий число кусков для дробилки 900*1200 длиной камеры 1200 а Dср =0350 при этом
Фактически может уложиться три куска следовательно
Средневзвешенный размер куска выходящего из дробилки:
После подстановки найденных значений в формулу (2.6) получим:
Выбираем электродвигатель мощностью 100кВт и n=750обмин 4 А 500 MS ГОСТ 19523 -81
5 Определение усилий и расчет деталей на прочность.
5.1. Расчет клиноременной передачи.
Определяем передаточное число по формуле:
где nэл.д - частота вращения вала электродвигателя nэл.д=750обмин;
nэл.в - частота вращения вала nэл.в=180обмин.
Из таблицы 7.6 для сечения при минимальном диаметре шкива d1=500мм передаточном числе U=416 и частоте вращения n1- nэл.дв=750обмин находим номинальную мощность передаваемую одним ремнем:
Находим диаметр ведомого шкива по формуле:
d2= d1·(1- )·U (2.9)
где - относительное в передаче = 002.
d2=05·(1-002)·416=2034м.
Принимаем стандартный размер шкива d2=2040м.
Расчетную длину ремня определим по формуле:
где а - межосевое расстояние а = 1500мм.
Из стандартного ряда предпочтительных расчетных длин выбираем Lр=7100мм.
Определяем окончательное межосевое расстояние по формуле:
где =05··( d1+ d2) (2.12)
=05·314·(500+2040) =39898мм.
y=025·(d2-d1)2 (2.13)
y=025·(2040-500)2=385мм.
После подстановки найденных значений в формулу (2.11) получим:
Найдем угол обхвата ремнем шкива по формуле:
=180-573·(d2-d1)а (2.14)
=180-573·(2040-500)1555=123о.
Найдем скорость ремня мс:
Скорость ремня находится между 15 мс и 20 мс что соотве6тствует правильному выбору ремня.
Определим мощность передачи одним ремнем кВт:
где Cα - коэффициент угла обхвата Cα = 082;
СL - коэффициент учитывающий длину ремня СL = 104;
Cp - коэффициент динамичности и режима работы Cp = 17.
Определим число ремней по формуле
где N- мощность двигателя N=100;
Np-мощность передачи одним ремнем;
Определим вращающий момент по формуле Н·м
где - угловая скорость с-1.
Угловая скорость муфты
= (314·750)30 = 785с-1.
После подстановки найденного параметра в формулу (2.18) получим:
Определим расчетный момент Н·м
где Кр- коэффициент режима работы дробилки Кр=25.
Мр=12739·25=318475 Н·м
По таблице для валов диаметром 90 и 100мм находим муфту с наружным диаметром D=500мм и допускаемым расчетным моментом Мр=8000Н*м.
Проверяем пальцы на изгиб по формуле:
D0 - диаметр окружности на которой расположены пальца мм;
Z - количество пальцев Z=10;
dп - диаметр пальца мм;
[п] - допускаемое напряжение при изгибе пальцев.
Проверим втулки на сжатие мПа
При переходе шатуна из нижнего положения в верхнее когда подвижная щека оказывает давление на дробильный материал в шатуне возникает растягивающее усилие Р. Это усилие изменяется от нуля при нижнем положении до максимального значения Рmax в верхнем положении.
Определим наибольшее усилие в шатуне по формуле Н
где l – эксцентриситет вала l = 003 м.
Учитывая ударный характер нагрузки и возможность попадания в дробилку не дробимых предметов принимаем величину расчетного усилия для шатуна в 3 раза больше чем Рmax.
Ррасч =3·Рmax (2.23)
Ррасч= 3·0472=1416 мН
Чтобы уменьшить неуравновешенность дробилки вес шатуна должен быть как можно меньше. Для изготовления шатуна берем высококачественную сталь.
Площадь поперечного сечения шатуна определяем по формуле:
где [p] – допустимое напряжение на растяжение [p] = 110 мПа.
По конструктивным соображениям принимаем шатун с поперечным сечением 1400см2.
Длину головки шатуна принимаем 100см. крышку подшипника охватывающую эксцентриковую часть вала крепим к шатуну восемью болтами из стали СТБ.
Диаметр болтов определяем по формуле
где 1 - коэффициент учитывающий наличие напряжения от затяжки болтов 1=135;
- коэффициент учитывающий неравномерность распределения нагрузки на болты 2=15;
5.4 Расчет распорных плит.
Рисунок 2.7 Схема к расчету распорной плиты.
Усилия Т (рисунок 2.8) действующие вдоль распорных плит достигают максимальной величины когда плиты находятся в крайнем верхнем положении.
С увеличением угла возрастает усилие Т а при =900 cos900=0 т. Е. при горизонтальном положении распорных плит усилие Т неограниченно возрастает. Следовательно в щековой дробилке распорные плиты не должны располагаться в одну линию. Угол принимаем равным 120.
Усилие действующее вдоль распорных плит определяем по формуле:
Определяем площадь поперечного сечения плиты по формуле:
где [сж] – допустимое напряжение на сжатие [сж] = 685 мПа
При ширине распорной плиты b1=1100мм толщина ее составляет:
Принимаем толщину передней распорной плиты равной 45 мм.
Заднюю распорную плиту изготавливаем стальной из двух частей скрепляемых предохранительными болтами. Болты изготовляют из ст.3 и пределом прочности Еb=390мПа. Предел прочности на срез
Запас прочности для материала берем тогда допускаемое напряжение
Число болтов принимаем равным 12.
Диаметр болтов определим по следующей формуле
где i –число болтов i = 12.
Принимаем болты диаметром 40 мм.
5.5 Расчет подвижной щеки
Рисунок 2.8 Схема к расчету подвижной щеки
На щеку действует сила Трасч. которую можно разложить на две составляющие Т1 и Т2.
Определим силу Т1 по формуле
Силу Т2 изгибающую ось подвижной щеки определим по формуле
Определим силу Qmax которая приложена в точке соприкосновения щеки с дробимым куском небольшего размера
d1 – расстояние от оси подвижной щеки до линии действия силы Qmax d1 = 700 мм.
Подвижная щека должна иметь небольшую массу и быть достаточно прочной поэтому она изготовлена с ребрами жесткости.
При небольших размерах кусков материалов Qmax будет максимальной. Если щеку дробилки рассматривать как балку на двух опорах опорах со средоточенной нагрузкой (рисунок 2.9) М4 будет равен.
Рисунок 2.9 Расчетная схема
Напряжение в опасном сечении подвижной щеки определим по формуле
где W – момент сопротивления опасного сечения м3;
[л] - допустимое сопротивление для стального литья
h - толщина профиля м;
y – координата центра тяжести м.
Рисунок 2.10. Схема к расчету щеки
Возьмем оси Y1 X1 как показано (рисунок 2.10) тогда координаты центра тяжести Y определим по формуле
где Fл = b1 ·h1 (2.38)
Fл =0080·040=0032 м2
F2 = 115 ·008=0092 м2
Найденные значения подставим в формулу (2.37) и получим
Момент индукции поперечного сечения относительно оси XX определим по формуле
После подстановки найденных значений в формулу (2.36) получим
Определив момент сопротивления опасного сечения определим напряжение в сечении
Так как допустимое напряжение [п] для стального литья берется равным 115-130 мПА то напряжение 8858 мПа вполне допустимо так как п [п].
Размеры маховика определим из уравнения махового момента
где m – масса маховика кг;
D - диаметр маховика м;
N – мощность потребляемая щекой дробилкой кВт;
– угловая скорость диcцентринового вала радс;
– коэффициент неравномерности = 001.
Диаметр маховика определим из формулы
Принимаем = 19 мс и находим диаметр маховика
Из стандартного ряда диаметров маховика принимаем D = 204 м.
Массу обода маховика определим по формуле
Массу маховика с учетом спиц определим по формуле
На эксцентриковом валу установлено два маховика. Площадь сечений обода каждого из маховиков найдем из уравнения
где ρ – плотность материала ρ = 7100 кгм3.
Ширину шкива маховика берем равной 598 мм.
5.8 Расчет эксцентрикового вала
Рисунок 2.12 Схема распределения нагрузок на эксцентриковый вал
Найдем реакции опор в вертикальной плоскости
Рисунок 2.13 Схема реакций опор в вертикальной плоскости.
Определим изгибающий момент в вертикальной плоскости
x1 =0925 M1X =236111·0925=218403 Н·м
x2 =0925 M2X =-218403 Н·м
Находим реакции опор в горизонтальной плоскости
Рисунок 2.14 Схема реакций опор в горизонтальной плоскости
Определим изгибающий момент в горизонтальной плоскости
y1 =185 M1Y =85522 Н·м
y2 =0525 M2Y =-8552 Н·м
Опасным сечение эксцентрикового вала является точка приложения силы Qнаиб. Определим одинарный изгибающий момент в опасном сечении по формуле
Эквивалентный момент в этом сечении определим по формуле
Диаметр вала под шатуном определим по формуле
где [1] – допустимое тангенсальное напряжение [1] = 10 – 30 мПа
Принимаем d = 380 мм.
Определим диаметр выходного конца эксцентрикового вала по формуле
где М1 – крутящий момент на выходном конце вала
Учитывая ослабляющие сечения поточенной канавкой и ударные нагрузки которые могут возрастать в 3 раза принимаем dк = 300 мм.
Можно считать что нормальные напряжения возникающие в поперечном сечении вала от изгиба изгибаются по симметричному циклу
где W – момент сопротивления вала
После подстановки найденного значения в формулу (2.60) получим
Касательные напряжения от нулевого цикла для сечения под шатунов определим по формуле
После подстановки найденного значения в формулу (2.62) получим
Коэффициент запаса прочности по нормальным напряжениям определим по формуле
где -1 – предел выносливости при изгибе Нмм2;
– эффективный коэффициент напряжений при изгибе =25;
– максимальных фактор для нормальных напряжений = 042;
– коэффициент учитывающий влияние постоянной составляющей цикла на усталостную прочность;
m – среднее напряжения циклов нормальных напряжений m =0.
Предел выносливости при изгибе
где - предел прочности для стали 40хН = 740 Нмм2
После подстановки найденных значений параметров в формулу (2.69) получим
Коэффициент запаса прочности по касательным напряжениям определим по формуле
где -1 – предел выносливости при кручении Нмм2;
– эффективный коэффициент концентрации напряжений при кручении =18;
–коэффициент учитывающий влияние постоянной составляющей цикла на усталостную прочность = 015;
m – амплитуда и средние напряжения циклов касательных напряжений.
Определим предел выносливости при кручении по формуле
После подстановки найденных значений параметров в формулу (2.71) получим
Общий коэффициент запаса прочности определим по формуле
Таким образом прочность и жесткость эксцентрикового вала в месте посадки шатуна обеспечена.
Эксцентриковый вал работает в очень трудных условиях поэтому рассчитаем коэффициент запаса прочности при двукратных нагрузках.
Коэффициент запаса прочности по сопротивлению пластическим деформациям определим по формуле
где r – предел тягучести r = 550 Нмм2;
и - максимальные напряжения при двукратных нагрузках.
Этот коэффициент запаса прочности также достаточен.
5.10 Проверка станины на прочность
Станина изготовлена из отдельных деталей удерживаемых замками и скрепленных болтами. Передняя и задняя стенки станины работающие на изгиб отлитые из стали а боковые стенки работающие на растяжение выполнены из листовой стали. Принимаем что передняя и задняя стенки станины работают как балки лежащие на двух опорах нагруженных сосредоточенным грузом Qmax = 83 мН. Поперечное сечение этих стенок показано на рисунке 2.13.
Рисунок 2.17 Поперечное сечение задней стенки
Определим координату центра тяжести сечения относительно оси X1Y1.
Момент инерции поперечного сечения
Момент сопротивления определим по формуле
Максимальное напряжение в стенке
Данное напряжение вполне допустимо для стального литья
5.11 Расчет шпоночных соединений
Принимаем что нагрузка со стороны втулки на шпонку равномерно распределена как по высоте так и по длине шпонки. Из условия прочности по снятию рассчитаем по формуле
где [] – допустимое напряжение на смятие;
d – диаметр вала мм;
h – высота шпонки мм.
После подстановки найденных значений параметров в формулу (2.95) получаем
Напряжение на срез определим по формуле
где [] - допустимое напряжение на срез [] = 90 Нмм2
Рисунок 2.18 Шпоночное соединение
Рассчитаем шпоночное соединение на ведущем шкиве
гдеlP = 180-36=144 мм
Рекомендуемые чертежи
- 24.01.2023