Производство аэродромных плит гладких 1ПАГ – 14 АIV


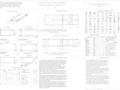
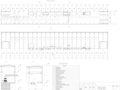
- Добавлен: 25.10.2022
- Размер: 800 KB
- Закачек: 1
Узнать, как скачать этот материал
Подписаться на ежедневные обновления каталога:
Описание
Производство аэродромных плит гладких 1ПАГ – 14 АIV
Состав проекта
![]() |
![]() ![]() ![]() |
![]() |
![]() ![]() ![]() ![]() |
![]() ![]() ![]() ![]() |
![]() ![]() |
![]() ![]() |
![]() ![]() |
![]() ![]() |
Дополнительная информация
Контент чертежей
1ПАГ-14АIV.doc
Список литературы – 10 наименования.
Данный курсовой проект посвящен разработке производства железобетонных преднапряженных плит для аэродромных покрытий 1ПАГ – 14 АIV.
Рассмотрены и рассчитаны производственный процесс способ производства тепловая обработка площадь технологической линии; Произведены подбор типовых складов расчеты и подбор необходимого оборудования компоновка технологических линий.
НОМЕНКЛАТУРА ПРОДУКЦИИ5
ВЫБОР СПОСОБА ПРОИЗВОДСТВА19
СОСТАВЛЕНИЕ И ОПИСАНИЕ ТЕХНОЛОГИЧЕСКОЙ СХЕМЫ ПРОИЗВОДСТВА21
РАЗРАБОТКА СТРУКТУРЫ ПРОИЗВОДСТВЕННОГО ПРОЦЕССА29
ТЕХНОЛОГИЧЕСКИЕ РАСЧЕТЫ31
1Режим работы предприятия31
2Технологические расчеты при конвейерном способе производства железобетонных изделий31
3Подбор и обоснование режима тепловой обработки32
4Определение и подбор технологического оборудования34
5Определение количества технологических постов на поточных технологических линиях39
6Определение площади технологической линии41
7Определение числа работающих42
КОМПОНОВКА ТЕХНОЛОГИЧЕСКИХ ЛИНИЙ В ЦЕХЕ45
ПРОЕКТИРОВАНИЕ СКЛАДА ГОТОВОЙ ПРОДУКЦИИ46
КОНТРОЛЬ ТЕХНООГИЧЕСКИХ ОПЕРАЦИЙ И ГОТОВОЙ ПРОДУКЦИИ47
ОХРАНА ТРУДА И ТЕХНИКА БЕЗОПАСНОСТИ49
ТЕХНИКО-ЭКОНОМИЧЕСКАЯ ОЦЕНКА ПРОИЗВОДСТВА ЖЕЛЕЗОБЕТОННЫХ ИЗДЕЛИЙ52
НОМЕНКЛАТУРА ПРОДУКЦИИ
Планируется производить предварительно напряженные железобетонные плиты 1ПАГ – 14АIV размерами 6х2 м изготовляемые из тяжелого бетона и предназначенные для устройства сборных аэродромных покрытий.
Таблица 1 – Расходы бетона и стали на плиту
Напрягаемая продольная арматура на плиту
Класс бетона по прочности
Объем бетона на плиту м3
Расход арматуры на плиту кг
на растяжение при изгибе
Технические требования
1. Плиты изготовляют в соответствии с требованиями ГОСТ 25912.1 и утвержденной в установленном порядке технологической документации содержащей требования к изготовлению плит на всех стадиях производственного процесса по чертежам приведенным в ГОСТ 25912.1
2. Плиты подлежат изготовлению в формах обеспечивающих соблюдение установленных ГОСТ 25912.1 требований к качеству и точности изготовления плит.
3. Основные параметры и размеры
3.1. Форма и основные размеры плит должны соответствовать указанным на рисунке 1.
На продольных гранях плит допускается устройство углублений размерами 20х100х200 мм для обеспечения возможности подъема плит с применением автоматических захватов.
В плитах с наклонными продольными гранями монтажно-стыковые изделия М1 (рисунок 1) устанавливают заподлицо с плоскостью определяющей габаритный размер ширины плиты — 2000 мм.
3.2. По согласованию с потребителем допускается изготовление плит с размерами проемов для монтажно-стыковых изделий отличающимися от приведенных на рисунке 1 и с монтажно-стыковыми изделиями другой конструкции при условии обеспечения эксплуатационных свойств аэродромного покрытия.
Рисунок 1 – Плита 1ПАГ-14
3.3. Плиты изготовляют рабочей поверхностью (верхняя поверхность аэродромного покрытия) «вверх». Допускается по согласованию с потребителем изготовление плит рабочей поверхностью «вниз».
Рабочая поверхность плит изготовляемых этой поверхностью «вверх» должна быть шероховатой. Шероховатость поверхности получают обработкой этой поверхности капроновыми щетками или брезентовой лентой (после уплотнения бетонной смеси).
Рабочая поверхность плит изготовляемых этой поверхностью «вниз» должна иметь рифление. Рифление поверхности образуют путем применения в качестве днища поддона формы стального листа с ромбическим рифлением по ГОСТ 8568.на поддоне располагают так чтобы большая диагональ ромба была перпендикулярна к продольной оси плиты (рисунок 2).
Рисунок 2 – Рифление рабочей поверхности плиты
Глубина рифления должна быть не менее 15 мм. По согласованию с потребителем допускается изготовлять плиты с глубиной рифления 12 мм.
3.4. Армирование плит производят:
в продольном направлении — напрягаемой арматурой;
в поперечном направлении — ненапрягаемой арматурой.
3.5. В качестве напрягаемой арматуры плит применяют стержневую арматурную сталь классов. Ат-V А-V Ат-IV Ат-IVС и А-IV. Напрягаемую арматуру следует применять в виде целых стержней без стыков.
Ненапрягаемая арматура — из стержневой арматурной стали классов А-III Ат-IIIС А-II и арматурной проволоки класса Вр-1 [7].
3.6. Конструкция плит приведена в графической части курсового проекта.
4. Требования к бетону
4.1. Плиты следует изготовлять из тяжелого бетона средней плотности более 2200 до 2500 кгм3 включительно удовлетворяющего требованиям ГОСТ 26633.
4.2. Фактическая прочность бетона должна соответствовать требуемой назначаемой по ГОСТ 18105 в зависимости от нормируемой прочности бетона (класс по прочности на растяжение при изгибе и класс по прочности на сжатие передаточная и отпускная прочность) и от характеристики фактической однородности прочности бетона.
4.3. Плиты должны изготовляться из бетона класса по прочности на растяжение при изгибе Вbtb 36 и класса по прочности на сжатие В25. При этом фактическая прочность бетона на сжатие (п. 1.4.2) не должна быть ниже 294 МПа (300 кгссм2).
4.4. Нормируемая передаточная прочность бетона — 70 % класса бетона по прочности на сжатие.
4.5. Значение нормируемой отпускной прочности бетона принимают равным значению нормируемой передаточной прочности и не ниже 70 % класса бетона по прочности на растяжение при изгибе.
Поставка плит с отпускной прочностью бетона ниже прочности соответствующей его классу по прочности на растяжение при изгибе и классу по прочности на сжатие производится при условии если изготовитель гарантирует достижение бетоном конструкции требуемой прочности определяемой по результатам испытания контрольных образцов изготовленных из бетонной смеси рабочего состава хранившихся в условиях согласно ГОСТ 18105 и испытанных в возрасте 28 сут (ГОСТ 13015.0).
4.6. Морозостойкость бетона плит должна соответствовать установленной проектной документацией конкретного сооружения или указанной в заказе плит марке бетона по морозостойкости.
Марку бетона по морозостойкости принимают для плит предназначенных для применения в районах с расчетной среднемесячной температурой воздуха наиболее холодного месяца (согласно СНиП 2.01.01) не ниже:
до минус 5°С включ. —
ниже минус 5°С до минус 15°С включ. —
ниже минус 15°С — F200.
4.7. Бетонная смесь применяемая для изготовления плит должна иметь водоцементное отношение не более 05.
В уплотненной бетонной смеси объем вовлеченного воздуха (при применении воздухововлекающих добавок) должен быть в пределах 5—6 %.
4.8. Для регулирования и улучшения свойств бетонной смеси и бетона при изготовлении плит следует применять пластифицирующие и воздухововлекающие (газообразующие) химические добавки по ГОСТ 24211.
4.9. Качество материалов применяемых для приготовления бетона должно обеспечивать выполнение технических требований установленных настоящим стандартом к бетону плит.
4.10. В качестве вяжущего следует применять портландцемент по ГОСТ 10178 предназначенный для бетона аэродромных покрытий [7].
4.11. Крупный и мелкий заполнители — по ГОСТ 10268 (крупность зерен крупного заполнителя — не более 20 мм).
Применение гравия в качестве крупного заполнителя допускается по согласованию с потребителем при соответствующем технико-экономическом обосновании.
4.12. В качестве крупных заполнителей для тяжелых бетонов используют щебень из природного камня по ГОСТ 8267 щебень из гравия по ГОСТ 10260 щебень из попутно добываемых пород и отходов горно-обогатительных предприятий по ГОСТ 23254 гравий по ГОСТ 8268 а также щебень из шлаков ТЭЦ по ГОСТ 26644.
В качестве мелких заполнителей для бетонов используют природный песок и песок из отсевов дробления и их смеси удовлетворяющие требованиям ГОСТ 8736 а также золошлаковые смеси по ГОСТ 25592.
4.12.1. В случае необходимости применения заполнителей с показателями качества ниже требований государственных стандартов а также требований настоящего стандарта предварительно должно быть проведено их исследование в бетонах в специализированных центрах для подтверждения возможности и технико-экономической целесообразности получения бетонов с нормируемыми показателями качества.
4.12.2. Крупный заполнитель в зависимости от предъявляемых к бетону требований выбирают по следующим показателям: зерновому составу и наибольшей крупности содержанию пылевидных и глинистых частиц вредных примесей форме зерен прочности содержанию зерен слабых пород петрографическому составу и радиационно-гигиенической характеристике. При подборе состава бетона учитывают также плотность пористость водопоглощение пустотность. Крупные заполнители должны иметь среднюю плотность от 2000 до 2800 кг м3.
4.12.3. Крупный заполнитель следует применять в виде раздельно дозируемых фракций при приготовлении бетонной смеси. Наибольшая крупность заполнителя должна быть установлена в стандартах технических условиях или рабочих чертежах бетонных и железобетонных конструкций.
4.12.4. Содержание пылевидных и глинистых частиц в щебне из изверженных и метаморфических пород щебне из гравия и в гравии не должно превышать для бетонов всех классов 1% по массе.
Содержание пылевидных и глинистых частиц в щебне из осадочных пород не должно превышать для бетонов класса В225 и выше 2% по массе; класса В20 и ниже - 3% по массе.
4.12.5. Содержание зерен пластинчатой (лещадной) и игловатой формы в крупном заполнителе не должно превышать 35% по массе.
4.12.6. Марка щебня из изверженных пород должна быть не ниже 800 щебня из метаморфических пород - не ниже 600 и осадочных пород - не ниже 300 гравия и щебня из гравия - не ниже Др16.
Содержание зерен слабых пород в гравии и щебне из гравия не должно превышать 10% по массе для бетонов всех классов.
4.12.7. Морозостойкость крупных заполнителей должна быть не ниже нормированной марки бетона по морозостойкости.
4.12.8. Мелкий заполнитель для бетона выбирают по зерновому составу содержанию пылевидных и глинистых частиц петрографическому составу радиационно-гигиенической характеристике. При подборе состава бетона учитывают плотность водопоглощение (для песков из отсевов дробления) пустотность а также прочность исходной горной породы на сжатие в насыщенном водой состоянии (для песков из отсевов дробления).
Мелкие заполнители должны иметь среднюю плотность зерен от 2000 до 2800 кг м3.
Допустимое содержание пород и минералов отнесенных к вредным примесям в заполнителях:
слоистые силикаты (слюды гидрослюды хлориты и др. являющиеся породообразующими минералами) - не более 15% по объему для крупного заполнителя и 2% по массе - для мелкого заполнителя;
магнетит гидроксиды железа (гетит и др.) апатит нефелин фосфорит являющиеся породообразующими минералами - каждый в отдельности не более 10% а в сумме - не более 15% по объему;
галоиды (галит сильвин и др.) включающие водорастворимые хлориды в пересчете на ион хлора - не более 01% по массе для крупного заполнителя и 015% по массе - для мелкого заполнителя;
свободное волокно асбеста - не более 025% по массе;
уголь - не более 1% по массе.
4.13. Пластифицирующие и воздухововлекающие (газообразующие) химические добавки применяемые при приготовлении бетона должны удовлетворять требованиям нормативно-технической документации утвержденной в установленном порядке.
4.14. Требования к воде
4.14.1. Содержание в воде органических поверхностно-активных веществ сахаров или фенолов каждого не должно быть более 10 мгл.
4.14.2. Вода не должна содержать пленки нефтепродуктов жиров масел.
4.14.4. Содержание в воде растворимых солей ионов SO -2 4 Cl -1 и взвешенных частиц не должно превышать предельных величин.
4.14.5. Окисляемость воды не должна быть более 15 мгл.
4.14.6. Водородный показатель воды (pH) не должен быть менее 4 и более 125.
4.14.7. Вода не должна содержать также примесей в количествах нарушающих сроки схватывания и твердения цементного теста и бетона снижающих прочность и морозостойкость бетона.
4.14.8. Допускается применение технических и природных вод загрязненных стоками содержащими примеси в количествах превышающих установленные в таблице кроме примесей ионов Cl -1 при условии обязательного соответствия качества бетона показателям заданным проектом [11].
5. Требования к арматурным и монтажно-стыковым изделиям
5.3. Марки арматурной стали классов А-III А-II и А-I а также марки углеродистой стали обыкновенного качества применяемые для изготовления монтажно-стыковых изделий должны соответствовать маркам установленным проектной документацией конкретного сооружения или указанным при заказе плит [7].
5.4. Арматурная сталь должна удовлетворять требованиям:
стержневая арматурная сталь классов:
Ат-V Ат-IVС Ат-IV и Ат-IIIС — ГОСТ 10884;
А-V А-IV А-III А-II и А-I — ГОСТ 5781;
арматурная проволока класса Вр-1 — ГОСТ 6727.
6. Натяжение напрягаемой арматуры
6.1. Натяжение напрягаемой продольной арматуры плиты следует осуществлять механическим или электротермическим способом.
6.2. Температура нагрева напрягаемой арматуры при электротермическом способе ее натяжения не должна превышать 450 °С.
6.3. Значения напряжений в напрягаемой арматуре контролируемые по окончании ее натяжения на упоры для арматурной стали классов:
Ат-V и А-V — 590 МПа (6000 кгссм2);
Ат-IV Ат-IVС и А-IV — 530 МПа (5400 кгссм2).
Отклонения значений напряжений в напрягаемой арматуре не должны превышать ±10 %.
7. Применяемые для смазки форм материалы не должны оказывать вредного воздействия на бетон.
Смазку форм следует наносить тонким слоем равномерно по всей поверхности поддона формы с удалением образовавшихся в отдельных местах излишков смазки [7].
9. Режим тепловой обработки плит должен соответствовать установленному технологической документацией согласно указаниям СНиП 3.09.01.
Температура изотермического прогрева не должна превышать 70°С.
Относительная влажность среды в период изотермического прогрева плит в камерах ямного типа должна быть не ниже 98%; в камерах тоннельного типа — не ниже 96 %.
10. Передача усилия обжатия на бетон (отпуск натяжения напрягаемой арматуры) должна производиться после достижения бетоном плиты требуемой передаточной прочности (п. 1.4.2).
11. Требования к точности изготовления плит
11.1. Действительные отклонения геометрических параметров плит не должны превышать предельных указанных в табл. 2 [7].
В плитах высшей категории качества действительные отклонения размеров плит в миллиметрах не должны превышать:
Таблица 2 - Действительные отклонения геометрических параметров плит
Вид отклонения геометрического параметра
Геометрический параметр
Предельное отклонение мм
Отклонение от линейного размера
Размер определяющий положение выемок у монтажно-стыковых изделий
Размеры выемок у монтажно-стыковых изделий
Смещение монтажно-стыковых изделий:
перпендикулярно к грани плиты
Отклонение от прямолинейности
Прямолинейность профиля поверхности и боковых граней:
в любом сечении на длине 2 м
Отклонение от плоскостности
Плоскостность рабочей поверхности плиты (при измерении от условной плоскости проходящей через три крайние точки)
Отклонение от равенства длин диагоналей
Разность длин диагоналей рабочей поверхности плиты
Отклонение от перпендикулярности
Перпендикулярность смежных торцевых граней плит на участке длиной мм:
11.2. Действительные отклонения толщины защитного слоя бетона до арматуры от номинального его значения указанного в чертежах не должны превышать ±3 мм.
11.3. Концы напрягаемой арматуры не должны выступать за торцевые поверхности плит более чем на 5 мм.
12. Требования к качеству поверхностей и внешнему виду плит
12.1. Рабочая поверхность плит (п. 1.3.3.) не должна иметь трещин.
На нерабочей поверхности и боковых гранях плит не допускаются усадочные и технологические трещины шириной более 005 мм и длиной более 50 мм.
Рифленая поверхность плиты должна иметь четкий рисунок рифления без околов граней канавок.
12.2. На рабочей поверхности плит не допускается шелушений бетона.
12.3. Размеры раковин местных наплывов и впадин на бетонной поверхности и околов бетона ребер плит не должны превышать значений указанных в таблице 3.
Таблица 3. – Размеры дефектов
Предельные размеры мм
наплывы (высота) и впадины (глубина)
суммарная длина на 1м ребра
Нерабочая и боковые грани
12.4. Исправление дефектов на рабочей поверхности и заделка околов ребер плит не допускается.
12.5. Боковые грани у нижней и верхней поверхностей плит а также открытые поверхности монтажно-стыковых изделий должны быть очищены от наплывов бетона.
13.1. Маркировка плит должна соответствовать требованиям ГОСТ 13015.2 и настоящего стандарта.
13.2. Маркировочные надписи наносят на боковой продольной грани плиты.
Маркировочные надписи должны содержать:
товарный знак или краткое наименование предприятия-изготовителя;
штамп технического контроля;
дату изготовления плиты.
13.3. На продольных гранях плиты на расстоянии 1 м от ее торца наносят монтажный знак «Место опирания».
13.4. На рабочей поверхности плиты должен быть нанесен знак предприятия-изготовителя обозначение и метод нанесения которого согласовывается с заказчиком и указывается в договоре на поставку плит.
1. Приемку плит осуществляют партиями в соответствии с требованиями ГОСТ 13015.1 и настоящего стандарта.
В партию включают плиты одного типа изготовленные предприятием по одной технологии из материалов одного вида и качества в течение не более одних суток.
Объем партии не должен превышать 200
2. Приемку плит производят по результатам:
приемосдаточных испытаний – по показателям прочности бетона (классам по прочности на растяжение при изгибе и по прочности на сжатие передаточной и отпускной прочности) водоцементному отношению бетонной смеси соответствию арматурных и монтажно-стыковых изделий толщины защитного слоя бетона до арматуры точности геометрических параметров качества поверхности и внешнего вида плит по трещиностойкости нижней и верхней зон плиты;
периодических испытаний - по показателям морозостойкости бетона по объему вовлеченного воздуха в уплотненной бетонной смеси.
3. Партию плит по показателям их прочности и жесткости принимают если удовлетворяются установленные настоящим стандартом требования по комплексу нормируемых и проектных показателей характеризующих прочность бетона толщину плиты диаметр и расположение арматуры толщину защитного слоя бетона до арматуры основные параметры арматурных и монтажно-стыковых изделий натяжение напрягаемой арматуры физико-механические свойства арматурной стали которые проверяются в процессе входного операционного и приемочного контроля в соответствии с ГОСТ 13015.1.
4. Приемочный контроль прочности бетона (на основе результатов испытаний образцов бетона либо неразрушающих методов) осуществляют в соответствии с ГОСТ 18105.
Определение прочности бетона на растяжение при изгибе а также прочности бетона на сжатие в проектном возрасте (п. 1.4.3) производят только по образцам.
4.1. Для контроля передаточной и отпускной прочности бетона на сжатие неразрушающими методами от партии отбирают три плиты.
Контроль прочности бетона проводят по пяти участкам любой поверхности плиты – по одному в середине плиты и в каждом углу на расстоянии 30 – 40 см от его вершины по биссектрисе.
4.2. В случаях если при контроле будет установлено что отпускная прочность бетона плит не удовлетворяет требованиям указанным в п. 1.4.5 поставка таких плит потребителю должна производиться только после достижения бетоном плит прочности соответствующей классам по прочности на растяжение при изгибе и по прочности на сжатие (п. 1.4.3).
5. Периодические испытания по показателям морозостойкости бетона плит а также по объему вовлеченного воздуха в уплотненной бетонной смеси проводят не реже одного раз в 6 мес. а также при изменении технологии изготовления плит изменении исходных материалов и состава бетонной смеси используемых для приготовления бетона.
6. Контроль водоцементного отношения в бетонной смеси осуществляют для каждой партии бетона плит.
7. Приемку арматурных и монтажно-стыковых изделий проводят до установки их в форму в соответствии с ГОСТ 10922 и ГОСТ 23858.
8. Приемку плит по показателям точности геометрических параметров толщины защитного слоя бетона до арматуры качества поверхности контролируемых путем измерений следует осуществлять по результатам выборочного одноступенчатого контроля.
Приемку плит по наличию монтажно-стыковых изделий по очистке их открытых поверхностей и ребер плит от наплывов бетона наличию шелушения бетона и жировых пятен на рабочей поверхности плиты правильности нанесения маркировочных надписей и знаков осуществляют по результатам сплошного контроля.
9. При приемке плит по показателям трещиностойкости их нижней и верхней зон от каждой партии плит отбирают для испытаний одну плиту удовлетворяющую по другим показателям требованиям настоящего стандарта.
Допускается использовать для испытаний плиту имеющую раковины местные наплывы и околы бетона размеры которых превышают допускаемые настоящим стандартом (п. 1.12.3) не более чем в два раза и другие дефекты не влияющие на прочность плит.
Плита считается выдержавшей испытание если при контрольной нагрузке указанной в п. 3.8.4 на поверхности испытуемой зоны и боковых гранях не будут обнаружены трещины при тщательном осмотре через лупу с четырехкратным увеличением.
При неудовлетворительных результатах испытания на трещиностойкость хотя бы по одной зоне производится дополнительное испытание двух плит данной партии. Если из двух плит хотя бы одна не выдерживает испытания то все плиты этой партии подвергают испытанию.
По согласованию с потребителем испытание плит на трещиностойкость допускается проводить не от каждой партии а от большего числа плит и в другие сроки в зависимости от объема их выпуска но не реже одного раза в месяц.
10. По результатам приемки составляют документ о качестве поставляемых плит в соответствии с ГОСТ 13015.3.
Дополнительно в документе о качестве должны быть приведены:
марка бетона по морозостойкости;
класс арматурной стали примененной в качестве продольной напрягаемой арматуры (Ат-V А-V Ат-IVС Ат-IV А-IV);
марки арматурной стали классов А-I — А-III и марки углеродистой стали обыкновенного качества из которой изготовлены монтажно-стыковые изделия плит.
1. Прочность бетона при ее контроле по образцам определяют по ГОСТ 10180 на серии образцов изготовленных из бетонной смеси рабочего состава и хранившихся в условиях согласно ГОСТ 10105.
Определение фактической передаточной и отпускной прочности бетона на сжатие при их контроле неразрушающими методами в плитах (п. 2.4.) производят ультразвуковым методом по ГОСТ 17624 приборами механического действия или методом отрыва со скалыванием по ГОСТ 22690.
2. Морозостойкость бетона плит следует определять в соответствии с ГОСТ 10060 для бетона аэродромных покрытий.
3. Проверку нормируемых показателей качества бетонной смеси производят по ГОСТ 10181.0 - ГОСТ 10181.4.
4. Методы контроля арматурных и монтажно-стыковых изделий – по ГОСТ 10922 и ГОСТ 23858.
5. Методы контроля исходных сырьевых материалов применяемых для изготовления плит должны соответствовать установленным стандартами или техническими условиями на эти материалы.
6. Измерение контролируемого напряжения в напрягаемой продольной арматуре - по ГОСТ 22362.
7. Размеры отклонения от прямолинейности профиля от плоскостности плиты от перпендикулярности смежных граней толщину защитного слоя бетона до арматуры положение монтажно-стыковых изделий а также качество бетонных поверхностей и внешний вид плит проверяют методами установленными ГОСТ 26433.0 и ГОСТ 26433.1.
8. Контроль трещиностойкости плит
Рисунок 3 – Контроль трещиностойкости плит
— испытуемая плита; 2 — нагрузка на всю ширину плиты; 3 — деревянные брусья сечением 10Х10 см; 4 — пригрузочный балласт
8.1. Испытание плит по трещиностойкости нижней зоны следует проводить по схеме А приведенной на рисунке 3. Испытание плит по трещиностойкости верхней зоны проводят по схеме А или Б приведенным на рисунке 3.
8.2. Испытание плит после термообработки (с отпускной прочностью бетона) следует проводить не ранее 4 ч и не позднее 2 сут.
8.3. Вначале проводят испытание плиты по трещиностойкости нижней зоны а затем испытание этой же плиты по трещиностойкости верхней зоны. При испытании плиты по трещиностойкости верхней зоны по схеме А приведенной на рисунке 3 плиту после испытания нижней зоны кантуют.
Загружение плиты при испытании проводят ступенями. Доля нагрузки каждой ступени должна составлять не более 10 % контрольной нагрузки а двух последних ступеней — не более 5 %.
После приложения каждой ступени контрольной нагрузки плиту выдерживают под нагрузкой не менее 10 мин а после приложения полной контрольной нагрузки — не менее 30 мин [7].
8.4. Значения контрольной нагрузки по испытанию трещиностойкости плиты приведены в таблице 4.
Таблица 4 - Значения контрольной нагрузки
Контрольная нагрузка кН (кгс) по испытанию трещиностойкости плиты с прочностью бетона соответствующей
отпускной прочности (п. 1.4.5) при испытании по схеме
классам бетона по прочности на растяжение при изгибе и по прочности на сжатие при испытании по схеме
Транспортирование и хранение
1. Транспортирование и хранение плит следует производить в соответствии с требованиями ГОСТ 13015.4 и ГОСТ 25912.1.
2. Транспортировать и хранить плиты следует в горизонтальном положении.
3. Высоту штабеля плит при их транспортировании устанавливают в зависимости от грузоподъемности транспортных средств и допускаемых габаритов погрузки но не более высоты штабеля плит при их хранении (п. 4.8).
4. Погрузку плит и их крепление при транспортировании на открытом железнодорожном подвижном составе (полувагоны платформы) следует осуществлять в соответствии с требованиями Правил перевозки грузов и Технических условий погрузки и крепления грузов утвержденных Министерством путей сообщения РФ.
Ориентировочный расход проволоки диаметром 6 мм для крепления плит на железнодорожном составе составляет 12 кг на 1 м3 перевозимых плит.
Транспортная маркировка — по ГОСТ 14192.
5. Погрузку транспортирование разгрузку и хранение плит следует производить с соблюдением мер исключающих возможность повреждения плит.
Плиты следует транспортировать с надежным закреплением на транспортных средствах исключающим продольное и поперечное смещение плит а также их взаимное столкновение и трение в процессе перевозки.
6. При транспортировании и хранении нижние плиты следует опирать на деревянные подкладки а между плитами по высоте штабеля необходимо укладывать прокладки. Подкладки и прокладки следует располагать на расстоянии 1 м от торца плиты перпендикулярно к ее длинной стороне и по вертикали одна над другой.
Толщина деревянных подкладок при жестком основании должна быть не менее 50 мм а при грунтовом основании — не менее 100 мм. Толщина прокладок — не менее 20 мм.
7. Погрузочно-разгрузочные операции с захватом за монтажно-стыковые изделия следует производить по одной плите. Запрещается подъем двух и более плит с захватом за монтажно-стыковые изделия нижней плиты.
При использовании специальных такелажных устройств работающих без захвата за монтажно-стыковые изделия число плит в поднимаемом пакете не должно превышать трех.
8. Плиты следует хранить на складах в штабелях рассортированными по маркам и партиям. В штабеле допускается укладывать по высоте не более 10 плит [7].
ВЫБОР СПОСОБА ПРОИЗВОДСТВА
На предприятиях сборного железобетона используются два способа изготовления изделий: стендовый – для массивных крупногабаритных изделий производимых в неперемещаемых формах и поточный при котором отдельные технологические операции осуществляются в перемещаемых формах на специализированных постах.
Способ производства железобетонных изделий определенного типа выбирается в соответствии с требованиями СНиП 3.09.01-85 и других инструктивных документов.[8]
Согласно СНиП 3.09.01-85 преднапряженные плиты для аэродромных покрытий следует формовать как правило на агрегатно-поточных полуконвейерных и конвейерных линиях.
Для выбора оптимального способа производства следует дать краткую характеристику каждого технологического способа.
При агрегатном способе производства изделия формуют на виброплощадке или на специально оборудованных установках — агрегатах состоящих из формовочной машины (обычно виброплощадки) машины для распределения бетонной смеси по форме (бетоноукладчика).
Отформованные изделия в формах мостовым краном перемещают в камеры тепловой обработки бетона для твердения.
Завершающая стадия – выдача изделий из камеры и их распалубка на специальном посту. После приемки готовых изделий ОТК их направляют на склад а освободившиеся формы подготавливают к очередному технологическому циклу и возвращают на формовочный пост.
Некоторые операции выполняют параллельно (распалубку осмотр изделий и подготовку форм совмещают по времени с формованием). При расчленении технологического процесса и соблюдении единого ритма возможна поточная организация производства. Для осуществления непрерывного производства технологическую линию оборудуют необходимыми транспортными средствами.
Конвейерный способ – усовершенствованный агрегатно-поточный способ формования железобетонных изделий. При конвейерном способе технологический процесс расчленяется на элементные процессы которые выполняются одновременно на отдельных рабочих постах.
Формы с изделиями перемещаются от одного поста к другому специальными транспортными устройствами каждое рабочее место обслуживается закрепленным за ним звеном. Для конвейера характерен принудительный ритм работы то есть одновременное перемещение всех форм по замкнутому технологическому кольцу с заданной скоростью. Весь процесс изготовления изделий разделяется на технологические операции причем одна или несколько из них выполняются на определенном посту. Тепловые агрегаты (термоформы туннельные щелевые и вертикальные камеры непрерывного действия) являются частью конвейерного кольца и работают в его системе также в принудительном ритме. Это обуславливает одинаковые или кратные расстояния между технологическими постами (шаг конвейера) одинаковые габариты форм и развернутую длину тепловых агрегатов.
Конвейерные линии по характеру работы могут быть периодического и непрерывного действия по способу транспортирования – с формами передвигающимися по рельсам или роликовым конвейерам с формами образуемыми стальной непрерывной лентой или составленными из ряда элементов и бортовой оснастки; по расположению тепловых агрегатов – параллельно конвейеру в вертикальной или горизонтальной плоскости а также в створе формовочной части.
Наибольшее распространение получили конвейеры периодического действия с формами передвигающимися по рельсам и образующими непрерывную конвейерную лилию из 6 15 постов оборудованных машинами для выполнения операций технологического процесса. Изделия изготовляют с ритмом 12 15 минут; скорость перемещения 09 013 мс; после выполнения одного элементного цикла вся цепь тележек-поддонов перемещается на длину одного поста для формования изделий используют современные машины и оборудование при необходимости выделяют посты для укладки отделочного слоя; ко всем постам подают материалы и полуфабрикаты.
Рациональной областью применения конвейерной технологии следует считать специализированное производство изделий одного вида и типа.[1]
Достоинства конвейерной линии:
-непрерывность потока и четкость ритма одновременного выполнения всех операций способствуют предотвращению простоев;
-пооперационное расчленение технологического процесса по стандартным специализированным постам и узкая специализация обеспечивает высокую производительность труда и создает предпосылки для комплексной механизации и автоматизации контроля пооперационных процессов;
-непрерывность процессов повышает коэффициент использования технологического оборудования формовочной оснастки и так далее.
Недостатки конвейерной технологии:
-повышенные капитальные вложения в результате обслуживания механизмов и оборудования;
-снижение гибкости технологии что ведет при переходе на новую номенклатуру к значительной реконструкции линии.[10]
Исходя из выше перечисленного с учетом всех достоинств и недостатков принимаем конвейерный способ производства.
СОСТАВЛЕНИЕ И ОПИСАНИЕ ТЕХНОЛОГИЧЕСКОЙ СХЕМЫ ПРОИЗВОДСТВА
Технологическая схема производства предварительно напряженных плит для аэродромных покрытий 1ПАГ-14АIV приведена на рисунке 4.
Процесс формования изделий – важнейшая стадия их изготовления на заводах сборного железобетона. Процесс формования изделий состоит из следующих операций: сборка очистка и смазка форм и бортовой оснастки установка и фиксация арматурного каркаса в форме натяжение арматуры на упоры формы укладка распределение и уплотнение бетонной смеси в форме отделка открытой поверхности изделия и извлечение готового изделия из формы после тепловой обработки.
Качество формования и качество готового изделия определяется:
-точностью размеров форм;
-качеством рабочих поверхностей форм;
-полным соответствием реологических свойств бетонных смесей принятому виду формовочного оборудования и режиму его работы.
Рисунок 4 – Технологическая схема производства плит 1ПАГ – 14АIV
Для производства плит 1ПАГ – 14АIV применяется одноместная сварная металлическая форма из профилированной и листовой стали. В качестве днища формы применяют листовую рифленую сталь с ромбическим рифлением по ГОСТ 8568-77. Для снижения металлоемкости форм а также для уменьшения скручивания и коробления форм из-за некачественной рихтовки рельсовых путей используем формы с трехточечным опиранием.[8]
Для обеспечения высокого качества изготовляемых изделий и для продления срока эксплуатации форм и формовочного оборудования необходимо содержать формы в чистоте. Для очистки форм и поддонов применяют машины рабочими органами которых являются цилиндрические щетки из стальной проволоки абразивные круги и инерционная фреза из металлических колец. Машины с относительно мягкими металлическими щетками применяют после каждого цикла формования. Остатки бетона убираются приспособлениями пылесосного типа.
На качество железобетонных изделий влияет сцепление бетона с поверхностью форм. Один из способов уменьшения сцепления – использование смазок. Правильно выбранная и хорошо нанесенная смазка облегчает распалубку изделия и способствует получению его ровной и гладкой поверхности. Смазка должна удовлетворять следующим требованиям: иметь консистенцию позволяющую наносить ее распылителем или кистью на холодные и горячие (до 40 50°С) поверхности сплошным тонким слоем (01 03 мм); обладать достаточной адгезией с металлом форм; быть достаточно водостойкой и не смешиваться с бетоном; не оказывать вредного действия на твердеющий бетон; не оставлять пятен на поверхности изделий; не вызывать коррозии рабочей поверхности формы; не создавать антисанитарных условий в цехах и быть безопасной в пожарном отношении. На заводах применяют три вида смазок: водные и водно-масляные суспензии водно-масляные и водно-мыльные эмульсии машинные масла нефтепродукты и их смеси. Смазку на поверхность форм наносят обычно различными распылителями а в тех местах где неудобно их использовать применяют специальные механизмы. Более тонкое распыление может получиться если применить для нанесения смазки сжатый воздух. Расход эмульсионной смазки при механизированном распылении сжатым воздухом составляет 200 300 гм2.
Откидные борта к поддонам крепят при помощи трубчатых или пластинчатых шарниров. Продольные и поперечные борта форм соединяют между собой замками натяжного типа так как они обеспечивают плотное соединение бортов и не раскрываются при действии вибрации. Борта имеют прорези для установки монтажно-стыковых изделий. Торцевые борта имеют прорези для пропускания напрягаемых арматурных стержней. Эти прорези прикрываются рубероидом во избежание утечки цементного молока. Для закрепления напрягаемой арматуры устраивают упоры которые должны обеспечивать легкую установку арматурных элементов. Обычно это вилочные упоры со специальными накладками из листовой стали которые позволяют продлить срок службы упора так как ремонт его состоит только в замене стальных накладок истираемых и деформируемых напрягаемой арматурой.
Собранная форма толкателем перемещается на пост армирования.
Схема армирования должна соответствовать приведенной на рисунке 5.
Рисунок 5.- Армирование плит 1ПАГ14-АIV
От положения арматурных элементов в форме зависят прочностные показатели железобетонных изделий и их долговечность.
Расстояние между арматурными изделиями и арматурными элементами а также между стенками формы и арматурными изделиями должно обеспечивать проход бетонной смеси кроме того необходимо соблюдать требуемую величину защитного слоя бетона.
Для продольной несущей напрягаемой арматуры в плитах ПАГ толщина защитного слоя должна составлять не менее 15 мм.
Для обеспечения толщины защитного слоя широко используют различные фиксаторы арматурных изделий. Сетки можно фиксировать путем разреза в нескольких местах арматуры и изгиба ее концов так чтобы они упирались в форму. Фиксаторы из цементно-песчаного раствора применяют в виде подкладок без прикрепления к арматуре.
Согласно рисунку 3 армирование производят следующим образом:
–на фиксаторы поддона укладываются 2 сетки С-1 и 1 сетка С-2;
–монтажно-стыковые петли М-1 М-2 вставляются в соответствующие прорези бортов;
–укладываются 5 напряженных стержней с предварительно установленными на каждом конце стержня спиралями;
–предварительно-напряженные стержни и сетки связываются между собой проволокой;
–производится укладка остальных 5 предварительно напряженных стержней аналогичным образом;
–устанавливаются 2 сетки С-1 и 1 сетка С-2;
–сетки и предварительно напряженные стержни фиксируются между собой проволокой.
Арматурные сетки следует привязывать к напрягаемой арматуре следующим образом:
–крайние стержни нижней и верхней сеток С-1 к среднему и крайним стержням напрягаемой арматуры;
–стержни нижней сетки С-2 к каждому стержню напрягаемой арматуры через 500 мм стержни верхней сетки С-2 – через 1000 мм.
Спецификация арматурных и монтажно-стыковых изделий а также выборка арматурной стали на плиту приведены в таблице 5.
Таблица 5 – Спецификация арматурных и монтажно-стыковых изделий
Арматурные и монтажно-стыковые изделия
Число изделий на плиту
Выборка стали на плиту
Напрягаемый стержень
Монтажно-стыковые изделия
Хранение арматурной стали поступившей на завод необходимо осуществлять в закрытых складах по профилям классам диаметрам и партиям на стеллажах в штабелях со свободными проходами. Допускается хранить арматурную сталь под навесом при условии защиты ее от влаги. Не допускается хранить арматурную сталь на земляном полу а также в условиях ведущих к возникновению коррозионных явлений (вблизи агрессивных сред повышенная влажность и так далее).
Арматурные изделия изготавливаются в арматурных цехах на специализированных комплексно-механизированных и автоматизированных линиях.
Механическая обработка арматурной стали включает правку отмеривание и резку а также гнутье стержней и сеток и изготовление монтажных петель.
Готовые арматурные изделия и стержни для предварительного напряжения транспортируют внутри арматурного цеха а также подают в формовочные цеха посредством специальных контейнеров самоходных передаточных тележек подвесных конвейеров.
Предварительное натяжение арматуры можно выполнять несколькими способами: механическим; электротермическим; электротермомеханическим и способом самонапряжения с использованием энергии расширяющегося цемента при его твердении.
Механическое натяжение арматуры осуществляется натяжными машинами и гидродомкратами а также различными винтовыми и рычажными устройствами.
Электротермомеханический способ напряжения арматуры применяется при непрерывном армировании проволочной арматурой намоточными машинами.
Электротермическое натяжение заключается в том что заготовленные стержни с анкерами на концах нагревают электрическим током до требуемого удлинения и фиксируют в жестких упорах форм или поддонов. По мере остывания зафиксированные стержни стремятся уменьшить свою длину соответственно в них возникает напряжение.
Натяжение стержневой арматуры класса AIV диаметром 8 22 мм целесообразно осуществлять электротермическим способом.
Для восприятия усилия натяжения и сохранения его на всех стадиях технологического процесса а в некоторых видах конструкций и при эксплуатации служат анкерные устройства являющиеся временной или постоянной частью арматурного элемента или специальные зажимы для временного закрепления арматуры на упорах.
Конструкция зажима или анкера зависит от принятой технологии изготовления изделия и способа натяжения арматурного элемента. Это могут быть высаженные в холодном или горячем состоянии головки опрессованные шайбы или спирали инвентарные зажимы НИИЖБа и так далее. Принимаем анкера в виде высаженных головок.
Контроль натяжения арматуры – важная технологическая операция. Необходимо контролировать равномерность натяжения арматуры степень натяжения арматуры перед бетонированием и надежность заанкеривания арматуры в бетоне перед отпуском натяжения.
При электротермическом напряжении необходимо обеспечить равномерный нагрев стержней по длине что достигается хорошим контактом токоподводящих электродов со стержнями. Хороший контакт обеспечивается при прижиме с определенным усилием и при хорошем качестве поверхностей. Таким образом следует контролировать не только удлинение и температуру нагрева арматурных элементов но также усилие прижима и качество поверхности контактов. Необходимо учитывать охлаждение преднапрягаемой арматуры при ее переносе в форму и осуществление установки арматуры на двух разных постах в два этапа.[9]
После установки всех арматурных элементов форма перемещается на резервный пост где она простаивает некоторое время для остывания арматуры.
Процесс формования включает следующие операции:
–установку форм и формообразующих элементов
–укладку распределение уплотнение в форме бетонной смеси
–заглаживание открытой поверхности свежезаформованного изделия.
Качественное выполнение процесса формования обеспечивается при соблюдении требований к бетонным смесям формующим установкам.
В соответствии с данными СНиП 3.09.01-85 был выбран поверхностный метод уплотнения смеси так как подвижность смеси для ПАГ при использовании поверхностных вибраторов составляет 1 4 см.
Поверхностное виброуплотнение получило широкое распространение в промышленности сборного железобетона поскольку позволяет полностью механизировать процесс формования изделий. Вибратор прикрепляется к бетоноукладчику и передает колебания бетонной смеси через рабочую площадку вибратора устанавливаемую на открытую поверхность бетона.
Бетонная смесь обладает рыхлой нестабильной структурой с высокой пористостью и большим объемом вовлеченного воздуха. Необходимое условие получения однородного по плотности и прочности бетона – уплотнение смеси на стадии формования изделий. Бетонная смесь из бетоносмесительного цеха транспортируется ленточным конвейером в бункер-накопитель. Затем к бункеру-накопителю перемещается бетоноукладчик. Затвор бункера-накопителя открывается и бетонная смесь попадает в бункер бетоноукладчика. После этого бетоноукладчик подъезжает к форме которая заполняется смесью за один проход.
Укладка и равномерное распределение бетонной смеси внутри форм осуществляются бункерами бетонораздатчиками и бетоноукладчиками.
Бункера и бетонораздатчики выдают смесь в форму без разравнивания. Бетоноукладчики имеют бункера стационарно установленные на раме и иногда перемещающиеся в ней в поперечном направлении их оснащают дополнительными устройствами распределяющими смесь в форме. Бетоноукладчики уплотняют и заглаживают поверхность свежеотформованного изделия.
После укладки уплотнения и заглаживания поверхности изделия его необходимо выдержать в течение не менее 30 минут.
Тепловая обработка изделий осуществляется в щелевой пропарочной камере непрерывного действия и состоит из следующих этапов:
-зона изотермического прогрева;
В качестве теплоносителя используется острый пар.
Изделия на поддонах расположены в один ряд и передвигаются с помощью толкателя следующим образом: при поступлении одной формы в камеру с противоположного конца камеры одна форма выталкивается.
Режим тепловлажностной обработки для изделия толщиной 14 см из тяжелого бетона с классом прочности на сжатие В25 составляет 9 часов (3ч+4ч+2ч).[9]
После тепловлажностной обработки форма с изделием подается на подъемник-снижатель который подводит форму к конвейерной линии. Толкатель выталкивает форму с рельс подъемника-снижателя на рельсы конвейерной линии.
Форма подается на пост обрезки арматуры.
Форма с изделием закрепляется с помощью фиксатора. Обрезка напряженной арматуры производится с помощью газокислородной горелки.
После того как стержни напрягаемой арматуры были обрезаны форма с изделием поступает на пост распалубки.
Рабочий открывает замки формы а борта открываются устройством для открывания и закрывания бортов.
Распалубленное изделие переворачивается кантователем рабочей поверхностью вверх и краном перевозится на промежуточный склад готовых изделий.
Далее осуществляется контроль и последующая маркировка изделий. По результатам приемочного контроля принимается решение о пригодности продукции к поставке потребителю. Кроме того его результаты используются для выявления недостатков технологического процесса и внесения необходимых изменений. Маркировка изделий способствует улучшению контроля готовой продукции и организации ее отпуска потребителю.
Изделия прошедшие контроль ОТК транспортируются на открытый склад готовой продукции с помощью самоходной тележки.
РАЗРАБОТКА СТРУКТУРЫ ПРОИЗВОДСТВЕННОГО ПРОЦЕССА
Таблица 7 – Оборудование для выполнения технологического процесса
Наименование выполняемой операции
Необходимое оборудование
Чистка формы и элементов бортоснастки
Машина для чистки с металлическими щетками
Приготовление смазки
Механический эмульгатор
Смазка формы и элементов бортоснастки
Закрытие бортов формы
Устройство для закрывания бортов
Закрытие замков формы
Установка сеток монтажных петель спиралей
Нагрев и установка напряженной арматуры
Автоматизированная линия ДМ-2
Соединение напрягаемой арматуры и сеток
Доставка арматурных изделий
Самоходная тележка мостовой кран
Укладка и равномерное распределение бетонной смеси внутри формы
Уплотнение бетонной смеси
Поверхностный вибратор закрепленный на бетоноукладчике
Перемещение формы на подъемник-снижатель
Перемещение формы до камеры тепловой обработки
Тепловлажностная обработка изделий
Перемещение формы в камеру тепловой обработки
Тепловлажностная обработка
Подъем формы на конвейерную линию
Перемещение формы на линию конвейера
Толкатель подъемника-снижателя
Обрезка предварительно-напряженных стержней
Газокислородная горелка
Устройство для раскрытия бортов
Траверса мостовой кран привод конвейера
Перемещение изделий на промежуточный склад
Контроль и маркировка изделий
Доставка готовых изделий на склад готовой продукции
Перемещение изделий на складе готовой продукции
Перемещение формы от одного поста конвейера к другому
ТЕХНОЛОГИЧЕСКИЕ РАСЧЕТЫ
1Режим работы предприятия
Режим работы предприятия принимается по ОНТП 07-85. Расчетное количество рабочих суток в году назначается исходя из 260 номинальных рабочих суток и длительности плановых остановок на ремонт которая составляет для конвейерных линий 13 суток.[8]
Таким образом расчетное количество рабочих суток в году для агрегатно-поточных линий составляет 247.
При определении режима работы предприятия следует принимать номинальное количество рабочих суток в году по выгрузке сырья и материалов с железнодорожного транспорта - 365; количество рабочих смен в сутки (без тепловой обработки) – 2 или 3; количество рабочих смен в сутки для тепловой обработки – 3; количество рабочих смен в сутки по приему сырья и материалов железнодорожным транспортом - 3; продолжительность рабочей смены – 8 ч. Таким образом принимаем 3 рабочих смены в сутки.
Также при проектировании формовочных цехов используют следующие требования ОНТП 07 – 85:
-запас в формовочном цехе арматурных сеток каркасов и других арматурных изделий создается на 4 часа;
-усредненная масса арматурных изделий размещаемых горизонтально на 1 м2 площади при хранении в формовочном цехе (с учетом проходов) из стали диаметром 14 22 мм составляет 005 т;
-объем в бетоне железобетонных изделий приходящихся на 1 м2 площади в период остывания выдержки контроля и доводки в формовочном цехе при хранении плоских беспустотных плит в горизонтальном положении составляет 035 м2.[8]
2Технологические расчеты при конвейерном способе производства железобетонных изделий
При конвейерном способе производства формы с изделиями перемещаются от поста к посту специальными транспортными устройствами – цепными конвейерами рольгангами и другими устройствами. Для конвейеров характерен принудительный ритм работы – одновременное движение всех форм по замкнутому технологическому кольцу с заданной периодичностью или скоростью. Тепловые агрегаты непрерывного действия являются частью конвейерного кольца.
Число постов на конвейерах составляет от 6 до 15 скорость перемещения 09 13 мс ритм работы конвейера не должен превышать максимальную продолжительность по ОНТП 07 – 85. Для плит 1ПАГ – 14АIV ритм работы конвейера ограничивается 12 минутами.
Годовая производительность конвейера периодического действия определяется по формуле (1):
где Bp – число рабочих дней в году Bp = 247 суток;
h – число рабочих часов в сутки h = 23 ч;
V – объем одновременно формуемых изделий V = 168 м3;
r – ритм работы конвейера по наиболее загруженному посту 02 часа.
P = 2472316802 = 477204 (м3).
Длина конвейерной линии периодического действия вычисляется по формуле (2):
Lпк=m1*lср+lp*(p+1) (2)
где m1 – число постов конвейерной линии m1=12
p – число разрывов p=13.
Lпк = 12*65+05*(13+1) = 85 (м).
Число форм на конвейерной линии с учетом 5% запаса на ремонт определяют из формулы (3):
где S – продолжительность тепловой обработки изделий S = 9 ч.
N=105*(12+902)=598»60 (шт.).
Число форм находящихся в агрегатах тепловой обработки непрерывного действия находится по формуле (4):
где Ткф – средняя продолжительность пребывания формы в камере тепловой обработки непрерывного действия.
Ткф в данном случае составляет 10 ч.
Nто = 1002 = 50 (шт.).
Рабочую длину щелевых камер определяют по формуле (5):
Lp = Ткф*(lср+l)r-l+2lo (5)
l- расстояние между двумя вагонетками l=05 м.
Lp = 10*(65+05)02 - 05+2*03=3501 (м).
Для того чтобы сократить длину камеры принимаем что она содержит 4 яруса тогда
Lp = 3501 4 = 875 (м).
3Подбор и обоснование режима тепловой обработки
Эффективность применения бетона в современном строительстве в значительной мере определяется темпами производства железобетонных изделий. Решающим средством ускорения твердения бетона в условиях заводской технологии сборного железобетона является тепловая обработка. Процесс тепловой обработки занимает 70 80% времени всего цикла изготовления изделий.
Тепловая обработка сборных железобетонных изделий производится до достижения ими требуемой отпускной (передаточной распалубочной) прочности. При этом должна обеспечиваться необходимая прочность в возрасте 28 суток после пропаривания то есть заданная проектная марка бетона.
Тепловая обработка сборных бетонных и железобетонных конструкций и изделий производится с применением режимов обеспечивающих минимальный расход топливно-энергетических ресурсов и ускоренное достижение бетоном заданных значений прочности.
Режимы тепловлажностной обработки характеризуются длительностью отдельных стадий процесса пропаривания и температурой изотермического прогрева. С режимом тепловлажностной обработки бетона тесно связаны его строительно-технические свойства расход цемента и тепловой энергии.
Общий цикл пропаривания разделяют на 4 периода: предварительное выдерживание – время от момента окончания формования изделия до начала повышения температуры среды камеры; подъем температуры среды в камере; изотермический прогрев – выдерживание при наивысшей заданной температуре; охлаждение – понижение температуры среды камеры.
Предварительное выдерживание изделий до начала тепловой обработки способствует формированию начальной структуры бетона необходимой для восприятия им теплового воздействия. Длительность предварительного выдерживания зависит от всех факторов которые определяют темп начального твердения бетона. Чем выше темп начального твердения бетона тем может быть короче время предварительного выдерживания. Предварительное выдерживание проводится как правило не менее 1 часа а для бетона конструкций с повышенными требованиями по морозостойкости водонепроницаемости – не менее 3 часов. Принимаем продолжительность предварительного выдерживания изделий 3 часа так как аэродромные плиты являются изделиями с повышенными требованиями по морозостойкости (до F600). За время выдерживания бетон приобретает начальную прочность до 05 МПа что позволяет повысить скорость подъема температуры без стимулирования деструкции.
Скорость подъема температуры для изделий с повышенной морозостойкостью бетона должна составлять не более 15°Сч а скорость охлаждения камер после изотермического прогрева при повышенных требованиях к бетону по морозостойкости не должна превышать 20°Сч.
Оптимальной температурой изотермического прогрева при применении портландцемента и его разновидностей является 80 85°С. При пропаривании изделий к которым предъявляются повышенные требования по морозостойкости изотермическое выдерживание осуществляется при температуре не выше 70°С до достижения бетоном максимальной прочности. Относительная влажность воздуха в камерах тепловой обработки в период изотермического прогрева изделий должна быть не менее 90%.
Продолжительность выдерживания распалубленных изделий в цехе при температуре наружного воздуха ниже 0°С после окончания тепловой обработки следует принимать 12 часов.[9]
4Определение и подбор технологического оборудования
Транспортное оборудование
) Формы-вагонетки перемещаются по конвейерной линии посредством привода конвейера СМЖ – 790 – 01 имеющего следующие технические характеристики:
Скорость перемещения115 мс;
Установленная мощность 57 кВт;
Тяговое усилие 36 кН;
Габаритные размеры (длинаширинавысота) м1562421111;
) Подъемник СМЖ – 789 служит для подъема и опускания на требуемый ярус передаточной тележки с формой применяется на конвейерных линиях с подземными щелевыми камерами тепловой обработки и обладает следующими техническими характеристиками:
Грузоподъемность25 т;
Скорость подъема 3 ммин;
Скорость опускания 35 ммин;
Установленная мощность2055 кВт;
Габаритные размеры (длинаширинавысота) м79855816;
) Автоматическая грузоподъемная траверса СМЖ – 630 предназначена для работы с мостовым краном выполнена в виде балки с подвесками подвешиваемой к крюку крана и имеет следующие технические характеристики:
Грузоподъемность6 т;
Габаритные размеры (длинаширинавысота) м803016;
) Самоходная тележка СМЖ – 151А предназначена для вывоза готовых изделий на склад готовой продукции и обладает следующими техническими параметрами:
Скорость передвижения40 ммин;
Грузоподъемность20 т;
Установленная мощность67 кВт;
Габаритные размеры (длинаширинавысота) м74925144;
Оборудование для распалубки изделий и подготовки форм
) На посту распалубки форма-вагонетка закрепляется с помощью фиксатора СМЖ – 788 со следующими техническими характеристиками:
Установленная мощность5 кВт;
Усилие толкания28 кН;
Габаритные размеры (длинаширинавысота) м 1140406;
) Для открывания и закрывания бортов формы устройство СМЖ–793:
Усилие открывания – закрывания продольных бортов495 кН;
Усилие открывания – закрывания поперечных бортов262 кН;
Число механизмов для продольных бортов4 шт.;
Число механизмов для поперечных бортов2 шт.;
Наибольшее время открывания – закрывания бортов90 с;
Габаритные размеры механизмов для продольного борта171065123м;
Габаритные размеры механизмов для поперечного борта128211061м;
) Кантователь СМЖ – 3333А предназначен для поворота форм с изделиями представляет собой платформу с устройствами для закрепления форм или изделий которая с помощью гидроцилиндров поворачивается около неподвижных шарнирных осей. СМЖ – 3333А имеет следующие технические характеристики:
Продолжительность цикла120 с;
Грузоподъемность13 т;
Установленная мощность75 кВт;
Габаритные размеры (длинаширинавысота) м 555456528;
) Для очистки формы от остатков бетона применяется машина СМЖ–112. Технические характеристики:
Частота вращения350 мин – 1;
Установленная мощность22 кВт;
Габаритные размеры (длинаширинавысота) м 9354155;
) Для смазки форм применяется установка СМЖ – 114:
Число форсунок7 шт.;
Вместимость расходного бака100 л;
Давление в сифоне05 МПа;
Габаритные размеры (длинаширинавысота) м .9354132;
Оборудование для формования.
) Для укладки и равномерного распределения бетонной смеси в формы используется бетоноукладчик 65631М с ленточным питателем обладающий следующими техническими характеристиками:
Количество бункеров1 шт.;
Ширина формуемых изделий2 м;
Установленная мощность73 кВт;
Габаритные размеры (длинаширинавысота) м 3213825;
) Для уплотнения бетонной смеси применяется поверхностный вибратор С – 489Б представляющий собой металлическую рейку с электродвигателем на валу которого установлены дебалансы. Техническая характеристика:
Производительность 80 100 м3ч;
Установленная мощность40 кВт;
Габаритные размеры (длинаширинавысота) м181839;
Оборудование для заготовки и натяжения арматуры.
ДМ – 2 выполняет следующие операции:
-поштучный отбор стержней из пачки;
-ориентирование и фиксирование формы;
-измерение расстояния между упорами с точностью до ±1 мм;
-высаживание анкерных головок при температуре 900±5°С;
-электронагрев стержней при температуре 400±20°С;
-установка разогретых стержней в форму.
Производительность ДМ – 2 до 100 шт.ч;
количество стержней одновременно загружаемых в бункер питателя250 шт.;
время нагрева стержня15 30 с.
Подсчет загрузки кранов.
Для определения времени использования мостовых и других кранов подсчитывается их загруженность с учетом норм расчета крановых операций по ОНТП 07 – 85 и технических характеристик мостовых кранов[5] в табличной форме (таблица 6).
Коэффициент использования крана во времени определяют по формуле (6):
где ti – время выполнения краном i – той операции мин.
Кв не должен превышать 08 при одном кране в пролете и 07 при двух и более кранах. Но как правило более трех кранов в одном пролете не устанавливают.[8]
Таблица 8 – Подсчет загрузки кранов
Наименование крановой операции
Время на одну операцию мин
Количество операций в смену
Продолжительность операций в смену мин
Доставка арматурных стержней
Загрузка самоходной тележки
Согласно полученному значению принимаем 1 мостовой кран на одной технологической линии.
Грузоподъемность крана определяется по формуле (7):
Qk = N1 + N2 + N3 (7)
гдеN1 – масса груза или изделия N1 = 42 т;
N2 = [70S0 + 5 N*(L + 2b) + 16h*4*(L + b) + N*L]a (8)
где a - средний конструктивный показатель a = 039;
S0 – опалубливаемая поверхность изделия S0 = 1424 м2;
L – длина изделия L = 6 м;
b – ширина изделия b = 2 м;
h – высота изделия h = 014 м;
N – передаваемое на форму усилие натяжения арматуры т:
где S – площадь поперечного сечения стержня
S = 314*1424 = 154 см2;
n – количество стержней n = 10 шт.;
sp = 65 кг см2 – величина предварительного натяжения;
N3 – масса траверсы строп и так далее:
N3 = 01(N1 + N2). (10)
Определим передаваемое на форму усилие N по формуле (9):
N = 154*10*65 =1001 кг =1001 т.
Определим массу формы по формуле (8):
N2 = [70*1424 + 5*1001*(6 + 2*2) + 16*014*4*(6 + 2) + 1001*6]039 = 29 т.
Массу строп вычислим из формулы (10):
N3 = 01*(42 + 29) = 071 т.
Таким образом грузоподъемность крана Qk = 42 + 29 + 071 = 781 т.
В соответствии с полученной грузоподъемностью принимаем мостовой кран со следующими техническими характеристиками:
Грузоподъемность10 т
Скорость перемещения крюка8 ммин
Стоимость с электрооборудованием8310 руб.
Так как три технологических линии принимаем три мостовых крана.
Количество самоходных тележек для вывоза готовых изделий на склад определяется по формуле (11):
nт = m*tц60Р*Ки (11)
где Р – число часов работы в смену
Ки – коэффициент использования оборудования Ки = 085[8];
m – количество транспортных циклов за смену;
tц – продолжительность цикла мин.
nт = 8*3960*8*085 = 076 » 1 шт.
Таблица 9 – Сводная таблица оборудования формовочного цеха
Наименование оборудования
Общая потребляемая мощность кВт
Автомати-ческая траверса
Устройство для открывания-акрывания бортов
Машина для чистки формы
Машина для смазки формы
Вибратор поверхностный
Установка для электрона-грева стержней
Газокисло-родная горелка
5Определение количества технологических постов на поточных технологических линиях
Таблица 10 – Продолжительность элементных процессов.
Наименование элементного процесса
Наименование операций переходов
Трудо-емк. ручной опера-ции чел- мин
Количест-во рабочих на данной операции чел.
Продолжи-тельность выполне-ния операции мин
Длитель-ность перехода мин
Продолжи-тельность каждого элементно-го процесса мин
Перемещение формы на пост
Подготовка и сборка форм
Установка сеток и их связка
Укладка ненапрягаемой арматуры
Подготовка бетоноукладчика
Заглаживание поверхности
Подъезд подъемника – снижателя к конвейерной линии
Подъезд к щелевой камере
Установка на подъемник-снижатель
Подъезд подъемника к линии
Перемещение формы на линию
Перемещение изделия на пост контроля
Складирование изделий
Установка на самоходную тележку
Вывоз на открытый склад
Таким образом окончательно определим количество постов:
Распалубка изделия осуществляется на 1 посту; подготовка формы к формованию на 2 посту; 3 и 4 пост – пост армирования; 5-формование; 678910-посты выдержки перед ТВО; 11- пост охлаждения; 12- резервный пост.
6Определение площади технологической линии.
При определении площади технологической линии учитывают ширину проходов и проездов в соответствии с требованиями:
-основных проходов в цехах не менее 15 м;
-проходов между оборудованием не менее 12 м;
-проходов между строительными конструкциями и оборудованием не менее 10 м;
-вокруг оборудования для его обслуживания и ремонта не менее 07 м;
-ширина проходов у рабочих мест должна быть увеличена на 075 м при одностороннем расположении рабочих мест и не менее чем на 15 м при двухстороннем.
Площадь занятая технологической линией определяется из формулы (12):
Sтл = (hл + 2hп + hк + hз)*(m*lср + p*lр + 2(lпод + hп)) (12)
где hл – ширина конвейерной линии м; hл =2 5м;
hп – ширина проходов у рабочих мест м hп = 2 м;
hк – расстояние между строительными конструкциями и оборудованием м hк = 2 м;
hз – ширина для запаса сеток м hз = 3 м;
m – число постов конвейера m = 12;
p – число разрывов p = 13;
lпод – длина подъемника lпод = 79 м.
Sтл = (25+2*2+2+3)*(12*65+13*05+2*(79+2)) = 11995 (м2).
В площадь технологической линии также входят площади на которых размещаются:
-площадка для выдерживания распалубленных изделий в цехе при температуре наружного воздуха ниже 0°С после окончания тепловой обработки для размещения изделий – S1 = 44 (м2);
-участок текущего ремонта форм – на каждые 100 т форм находящихся в эксплуатации 30 м2 – S2 = 70 (м2);
-участок складирования форм и оснастки – на каждые 100 т форм находящихся в эксплуатации предусматривается площадка 20 м2 – S3 =50 (м2);
-участок для ремонта изделий на котором размещается 5% суточного выпуска изделий S4 =80 (м2);
-площадъ занятая транспортными средствами (самоходная тележка) – S5 = 50 (м2);
-площадь под запас арматурных изделий – S6 =20 (м2);
-площадь бытовых помещений S7 = 2*18*6 = 216 (м2).
Площадь для размещения ехнологической линии рассчитывается как сумма всех участков входящих в технологическую линию:
Sобщ = 11995+70+44+50+50+80+20+216 = 17295 (м2).
Как правило технологические линии размещаются в унифицированном типовом пролете – УТП –1 размером 14418 м. Площадь одного типового пролета составляет 2592 м2.
Количество технологических линий размещаемых в одном типовом пролете определяется по формуле (14):
N = 259217295 = 149.
Согласно результатам вычислений в цехе размещается одна технологическая линия.
7Определение числа работающих
В состав производственной бригады технологической линии входят рабочие непосредственно выполняющие технологические операции а также машинисты и операторы всех видов технологического оборудования включая мостовые краны и передаточные тележки.
Суточное число рабочих в бригаде определяется суммированием по всем сменам.
Выработка в год на одного рабочего (м3чел) определяется по формуле:
где Р – годовая производительность линии Р = 477204м3;
б – суточное число рабочих в бригаде.
Средний тарифный разряд рабочих бригады определяется как средневзвешенная величина тарифных разрядов членов бригады:
рi – величина i – того разряда.
Затраты труда (трудоемкость) на единицу изготавливаемой продукции (чел*час м3) устанавливаются исходя из состава производственной бригады:
где R – явочное число рабочих в бригаде в сутки чел;
с – число рабочих суток в году;
h – число рабочих часов в сутки;
nc – число смен в сутки.
Полная заработная плата на 1 м3 изделий с учетом дополнительной зарплаты в размере 10% от основной отчисления на социальное страхование – 61% от суммы основной и дополнительной заработной платы коэффициента 12 учитывающего премии за выполнение плана и коэффициента 1331 учитывающего налоги на заработную плату составляет:
Z = r*ф*11*1061*1331*12 = 1656*ф*r (18)
где ф – часовая ставка рабочего-сдельщика среднего тарифного разряда; определяется интерполяцией из приложения 1 [8].
Профессии и тарифные разряды рабочих занятых на технологической линии по изготовлению плит 1ПАГ – 14AIV занесены в таблицу 8.
Таблица 11 – Состав производственной бригады
Технологический пост операция
Наименование профессии
Установка нижнего ряда сеток монтажных петель
Связывание напрягаемых стержней и установленных сеток
Установка верхнего ряда сеток
Связка сеток с верхним рядом напрягаемых стержней
Укладка и уплотнение смеси
Машинист бетоноукладчика
Заглаживание и уплотнение
Формовщики отделочники
Подача формы на подъемник перемещение и подача формы в камеру
Оператор конвейерной линии
Вывоз изделий на склад готовой продукции
Машинист самоходной тележки
Склад готовой продукции
Съем изделий с тележки и укладка их в штабель
Согласно данным таблицы 11 определим параметры В Тр r и Z:
В = 47720416 = 29825 (м3чел);
Тр= (3*5 + 11*4)16 = 37;
r = 16*247*23477204 =19 (чел*час м3);
Z = 1656*19*062 =195 (руб.м3).
КОМПОНОВКА ТЕХНОЛОГИЧЕСКИХ ЛИНИЙ В ЦЕХЕ
Для размещения технологической линии принимается унифицированный типовой пролет 18144 м при высоте подкрановых путей 785 м. Строительные конструкции УТП – 1 рассчитаны на мостовые краны грузоподъемностью до 30 т.
Арматурные изделия поступают из арматурного цеха на самоходной тележке а затем транспортируются к месту складирования мостовым краном. Проезд из арматурного цеха в формовочный устроен напротив поста армирования.
Подача бетонной смеси в бетоноукладчик осуществляется ленточным конвейером. Подача бетонной смеси – адресная.
В последней торцевой 6м зоне располагаются бытовые помещения а над ними – вентиляционные площадки для создания воздушной завесы на воротах через которые вывозится готовая продукция.
Для вывоза готовых изделий на открытый склад используют самоходную тележку. Склад готовой продукции располагается у торца формовочного цеха через который вывозится продукция с разрывом 5 10 м для аварийного проезда.[8]
ПРОЕКТИРОВАНИЕ СКЛАДА ГОТОВОЙ ПРОДУКЦИИ
Склады готовой продукции заводов железобетонных изделий проектируются в соответствии с ОНТП 07 – 85. Для хранения изделий и конструкций из тяжелого бетона применяют открытые склады представляющие собой площадку с твердым покрытием с небольшим уклоном для стока атмосферных осадков. При использовании мостовых кранов площадка оборудуется железобетонной рельсовой эстакадой а также дорогами для подъезда транспортных средств и площадкой для их загрузки. Готовые изделия складируются в штабели. Между изделиями укладываются деревянные прокладки точно друг над другом чтобы избежать повреждения изделий. Хранятся изделия и конструкции в рабочем положении.
Площадь склада готовой продукции (м2) определяется по формуле (19):
А = Гсут*Тхр*К1*К2Ги (19)
где Гсут – суточное поступление изделий на склад м3;
Гсут =115*168=1932 м3;
Тхр – продолжительность хранения изделий на складе сут. в данном случае 10 14 сут.; Т хр =12сут.;
К1 – коэффициент учитывающий увеличение площади склада на проходы между штабелями изделий К1= 15;
К2 – коэффициент учитывающий увеличение площади склада в зависимости от типа грузоподъемного механизма для мостовых кранов К2 = 13;
Ги – объем изделий хранящихся на 1 м2 площади склада Ги = 18 м3 для линейных элементов простой формы.
А =1932*12*15*1318 = 25116 (м2).
Высота штабелирования изделий при хранении в горизонтальном положении допускается не более 25 м минимальная ширина проходов между штабелями изделий – 08 м. К изделиям на складе должны быть свободные подходы.
КОНТРОЛЬ ТЕХНООГИЧЕСКИХ ОПЕРАЦИЙ И ГОТОВОЙ ПРОДУКЦИИ
При производстве сборных железобетонных изделий технический контроль осуществляют на различных стадиях технологического процесса. В зависимости от этого контроль различают входной операционный и приемочный. Контроль производства осуществляет цеховой технический персонал он отвечает за соблюдение технологических требований к изделиям. Отдел технического контроля (ОТК) контролирует качество и производит прием готовой продукции проверяет соответствие технологии техническим условиям производства изделий. Контроль может быть сплошным и выборочным. В производстве железобетонных изделий находит применение статический приемочный контроль качества – выборочный контроль с использованием статистических методов для обоснования плана контроля или корректировка этого плана по накопленной информации. При соответствующем качестве материалов и правильно организованном операционном контроле создаются условия выполнения технологического процесса гарантирующие выход продукции высокого качества.
Таблица 12 – Производственный контроль
Вид марка наличие паспорта физико-механические свойства
Вид наличие паспорта физико-механические свойства влажность
Сталь арматурная и для закладных деталей
Вид класс марка стали наличие сертификатов физико-механические свойства
Приготовление бетонной смеси
Дозирование перемешивание и удобоукладываемость
Лаборатория работники бсц
Изготовление арматурных изделий
Применение стали заданного класса и диаметра. Размеры и конструкция изделий и деталей
ОТК работники арматурного цеха
Правильность сборки форм и равномерность их смазки
Работники формовочного цеха
Окончание таблицы 12.- Производственный контроль.
Формование железобетонных изделий
Правильность положения арматурных элементов и качество их фиксации в форме
ОТК работники формовочного цеха
Степень напряжения арматуры заанкеривание концов арматуры; степень уплотнения бетонной смеси; качество открытых поверхностей изделий
Контроль температуры влажности и продолжительности процесса
Размеры формы и качество изделий
Внешний осмотр изделий проверка размеров и качества поверхности изделий
Марка бетона водонепроницаемость морозостойкость
Испытание контрольных кубов на удовлетворение требованиям нормативной документации
Отпускная и марочная прочность бетона и другие физико-механические свойства; прочность жесткость трещиностойкость определение защитного слоя бетона
Правильность укладки изделий
Проверка положения изделий и прокладок в штабеле маркировка изделий
К периодическим испытаниям относятся:
-прочность жесткость и трещиностойкость изделий по ГОСТ 8829;
-марка бетона по морозостойкости водонепроницаемости;
-истираемость теплопроводность водопоглощение плотность тяжелого бетона.
Сплошной контроль осуществляют по наличию закладных и комплектующих изделий монтажных петель и строповочных отверстий правильности нанесения маркировки.
Для выборочного контроля из потока изделий в процессе их выпуска или после изготовления всей партии отбирают определенное количество изделий и определяют количество дефектных изделий в ней по каждому показателю. Для партии изделий не принятой в результате выборочного контроля допускается применять сплошной контроль при этом изделия контролируются только по тем показателям по которым партия не была принята.
Результаты входного операционного и приемочного контроля должны быть зафиксированы в соответствующих журналах ОТК заводской лаборатории и других документах.
ОХРАНА ТРУДА И ТЕХНИКА БЕЗОПАСНОСТИ
Заводы сборного железобетона относятся к числу предприятий на которых санитарно-гигиенические условия труда и техника безопасности являются не только важнейшими критериями для повышения производительности труда они обеспечивают сохранение здоровья каждого работающего на предприятии. Вопросы обеспечения нормальных санитарно-гигиенических условий труда на предприятиях сборного железобетона закладываются еще при проектировании завода и должны строго соблюдаться при его эксплуатации. Таким образом для обеспечения безопасных и нормальных санитарно-гигиенических условий труда необходимо строго руководствоваться правилами техники безопасности и производственной санитарии действующими на каждом заводе.
Все работы связанные с производством сборного железобетона должны соответствовать требованиям СНиП 12 – 03 – 99. Способы безопасного производства погрузо-разгрузочных работ и складских операций должны соответствовать требованиям ГОСТ 12.3.009. Противопожарные нормы приведены в СНиП 2.01.02 – 85.
К внутрицеховым работам допускаются лица достигшие 18 лет и прошедшие инструктаж по технике безопасности.
На посту распалубки в момент открывания замков запрещено стоять на форме. После того как замки формы открыты рабочий предварительно отойдя от формы должен включить устройство для раскрытия бортов. При обрезке напрягаемой арматуры во избежание пожароопасной и других аварийных ситуаций необходимо на рабочее место укладывать резиновые коврики а также ограждать данный пост защитными экранами. Рабочего снабжают защитными очками и рукавицами.
В момент строповки изделия запрещено находиться под траверсой.
Машина для чистки форм должна быть оборудована защитным кожухом во избежание повышенной запыленности.
В арматурном цехе при ведении сварочных работ необходимо: заземлять сварочные аппараты применять очки и щитки со светофильтрами на рабочие места укладывать резиновые коврики ограждать сварочные посты защитными экранами а при работе правильно-отрезных станков их кожух подключать к местной системе аспирации.
Особые меры предосторожности следует соблюдать при изготовлении преднапряженных изделий. Необходимо предусмотреть и строго соблюдать меры безопасности на случай обрыва напрягаемой арматуры. В данном случае формы для изделий изготовлены с учетом выполнения мер безопасности на случай обрыва напрягаемой арматуры. Конструкция формы и описание ее характеристик приведено в разделе 3 данного курсового проекта. В частности на случай обрыва напрягаемой арматуры упоры снабжаются защитными козырьками.
На посту армирования рабочих снабжают специальными рукавицами.
При приготовлении бетонной смеси необходимо следить за исправной работой вентиляции герметизацией кабин пультов управления дозаторами и смесителями системой сигнализации и автоматизации.
Для формовочных цехов характерно большое звуковое давление превышающее допустимое. Для уменьшения вредного влияния используют следующие средства:
-индивидуальные средства защиты (обувь на толстой подошве из губчатой резины антифоны рукавицы с прокладкой пенопласта);
-конструктивные средства (использование различных изоляторов звукоотражающих щитов дистанционное управление процессом уплотнения смеси ).
Кроме того для снижения вредного влияния вибрации следует производить своевременный профилактический осмотр ремонт и наладку вибрационного оборудования.
Лица моложе 18 лет и женщины не допускаются к работе с вибрационным оборудованием.
Температура нагретых поверхностей оборудования и ограждений тепловых агрегатов на рабочих местах не должна превышать 35°С. При тепловой обработке изделий следует избегать утечки пара из камер тепловлажностной обработки. Для этого с торцов камеры устраивают воздушные завесы и резиновые шторы. Стены камеры обеспечивают теплоизоляцией во избежание больших теплопотерь.
При установке в цехе мостовых кранов необходимо учитывать требования «Правил устройства безопасной эксплуатации грузоподъемных кранов». Кабина должна быть подвешена со стороны противоположной расположению токоподводящих троллей. При этом вход в кабину располагается с фронтальной стороны. Для безопасной работы оператора посадочные площадки должны быть обнесены сплошным ограждением от пола площадки до конструкции крана с зазором между ними не более 100 мм.
Предупреждение возникновения вредного влияния вибрации на работающих обеспечивается ее локализацией в сфере «машина – фундамент».
Управление перемещением конвейера осуществляется оператором линии с пульта управления из звукоизолированной кабины обеспечивающей хороший обзор всей линии.
Запрещается переходить через конвейер во время его движения переход осуществляется через специальные мостики.
Температура относительная влажность и подвижность воздуха рабочей зоны должна быть в пределах установленных ГОСТ 12.1.005. Концентрация вредных веществ в воздухе рабочей зоны должна быть не выше ПДК. Участки чистки смазки распалубки обрезки напрягаемой арматуры должны иметь вытяжную вентиляцию.
Все площадки расположенные выше 11 м от уровня пола лестницы переходные мостики и переходы открытые люки должны быть ограждены перилами высотой не менее 1 м.
Угол наклона постоянно эксплуатируемых лестниц не более 45°.
Оборудование требующее обслуживания на высоте 11 м и более от пола должно быть снабжено специальными площадками с ограждением.
Естественное и искусственное освещение должно соответствовать требованиям СНиП 23-05-95.
При производстве железобетонных изделий следует предусматривать природоохранные мероприятия. Запыленный воздух перед выбросом в атмосферу должен подвергаться очистке с эффективностью не менее 99%.
Вода используемая в производстве изделий а также конденсат пропарочных камер должны подвергаться очистке в локальных очистных сооружениях до концентраций при которых она снова может поступать на технологические нужды.
ТЕХНИКО-ЭКОНОМИЧЕСКАЯ ОЦЕНКА ПРОИЗВОДСТВА ЖЕЛЕЗО-БЕТОННЫХ ИЗДЕЛИЙ
При экономической оценке проектных решений определяется заводская себестоимость продукции которая складывается из стоимости материалов и себестоимости их переработки с учетом затрат на амортизацию здания спецсооружений и оборудования. Себестоимость изготовления 1 м3 железобетонных изделий определяется по формуле (34):
Си = Сб +SЦст +SСа + SСн + Сд + Су + Сна + Сф + Со + Сп + Сзг + Сэ + Соб + Ц + О + Z (20)
где Сб – себестоимость 1 м3 бетонной смеси руб. Сб = 2009 руб.;
SЦст – суммарная цена всех видов арматурной стали расходуемой на 1 м3 изделий руб.;
Таблица 13 – Расход арматуры на одну плиту
Цена руб. арматурной стали приходящейся на 1 м3
Таким образом SЦст = 15805 (руб.)
SСа – суммарные затраты на изготовление ненапрягаемой арматуры на 1 м3 изделий руб.:
SСа=SВа*Ца(1000*168) (21)
SВа – масса каждого вида арматурных изделий;
Ца – себестоимость изготовления 1 т ненапрягаемой арматуры;
SСа= (1972*20+ 3534*1105+ 764*66+ 252*66+ 13*8435)(1000*168) = 057 (руб.);
SСн - суммарные затраты на изготовление напрягаемой арматуры на 1 м3 изделий руб.;
SСн = 00726*299168 = 129 (руб.);
Сд - себестоимость изготовления закладных деталей на 1 м3 изделий руб.; в данном случае закладные изделия не изготавливаются Сд = 0;
Су - себестоимость укладки ненапрягаемой арматуры и закладных деталей в форму на 1 м3 изделий руб.:
Су = Ва*Цу(1000*168) (21)
Цу – себестоимость укладки ненапрягаемой арматуры руб.;
Су = 6652*65(1000*168) = 026 (руб.);
Сна - себестоимость работ по натяжению арматуры в расчете на 1 м3 изделий руб.;
Сна = 726*204(1000*168) = 088 (руб.)
Сф - себестоимость формования 1 м3 изделий руб.; Сф = 7 руб.;
Со - затраты на содержание и эксплуатацию форм руб. на 1 м3 бетона конструкций руб.:
SАф – сумма отчислений на амортизацию форм;
SАф = 311*640*46*033 = 302143 (руб.);
Со = 16*302143477204=101 (руб.);
Сп - себестоимость пара для тепловлажностной обработки 1 м3 изделий острым паром руб.; для щелевых камер
Сп = 017*6 = 102 (руб.);
Сзг - себестоимость повышения заводской готовности изделий; Сзг =0;
Сэ - себестоимость электроэнергии расходуемой на 1 м3 изделий руб.:
где Э - удельный расход силовой электроэнергии кВт*чм3:
где F – суммарная мощность токоприемников (кВт) кроме установок для электронагрева арматуры;
Bp – число рабочих суток в году;
Р – годовая производительность м3;
Э = 03*1407*23*247477204= 5025 (кВт*чм3);
Цэ – стоимость электроэнергии Цэ = 0025 руб. за 1 кВт*ч;
Сэ = 5025*0025 = 0125 (руб.);
Соб - расходы на содержание и эксплуатацию оборудования руб.:
где SАоб – сумма отчислений на амортизацию технологического и транспортного оборудования формовочного цеха (без формы). Расчет амортизационных отчислений проводится в табличной форме (таблица 14).
Ц – удельные цеховые расходы на 1 м3 изделий для формовочного цеха:
Ц = (Дц + 35Азд + 125SАсс)Р + 02*Z (26)
гдеДц - годовой фонд заработной платы цехового персонала
Z – полная заработная плата рабочих на 1 м3 изделий Z = 195руб.;
Азд - сумма отчислений на амортизацию здания и склада готовой продукции руб.; определяется из стоимости 1 м2 площади основного цеха – 160 руб. склада – 55 руб. и нормативов амортизационных отчислений;
Азд = 160*144*18*0024+55*25116*001 = 1133466 (руб.);
SАсс – сумма отчислений на амортизацию спецсооружений руб. К спецсооружениям относятся фундаменты под оборудование рельсовые пути камеры тепловой обработки с системами теплоснабжения и автоматики эстакады и так далее. Стоимость спецсооружений при конвейерном способе производства 140 150 тыс. руб.; норматив амортизационных отчислений для спецсооружений при конвейерном способе производства составляет 6%;
SАсс = 006*145000 = 8700 (руб.).
Ц = (17000+35*1133466+125*8700)477204 + 02*195 = 18(руб.);
О – общезаводские расходы (руб.) на 1 м3 продукции формовочного цеха:
О = 80(50 + Р1) + 03*Z (27)
где Р1 – годовая производительность формовочного цеха в тыс. м3.
О = 80(50 + 477204) + 03*195 =1404 (руб.).
Тогда Соб = 32*12837477204 = 0861 (руб.).
Таблица 14 – Амортизационные отчисления на оборудование
Норма амортизационных отчислений
Устройство для открывания-закрывания бортов
Машина для чистки форм
Машина для смазки форм
Продолжение таблицы 11
Установка для нагрева арматуры
Поверхностный вибратор
Автоматическая траверса
Таким образом определим заводскую себестоимость с учетом требуемых вычислений.
Си = 1404 + 18 + 195 + 0861 + 0125 + 102+101+7+088+026+129+057+ +15805+2009=5407 (руб.)
Помимо себестоимости изготовления изделий одним из основных критериев оценки проектных решений являются приведенные затраты:
где SК – удельные капитальные вложения руб. включают стоимость здания склада готовой продукции спецсооружений технологического и транспортного оборудования форм и оснастки формовочного цеха отнесенную к 1 м3 изделий:
SК = (25116*55+18*144*160+141745)477204 = 1456 (руб.).
П = 5407+1456*015 = 5625 (руб.).
Годовая прибыль определяется из формулы (29):
где Ц1 – цена 1 м3 железобетонных конструкций руб. Ц1 = 7140 руб.
Согласно формуле (29)
Пр= (714 – 5407)*477204 = 8269945(руб.).
Срок окупаемости рассчитывается по формуле (44):
Таким образом Т = 084 (год).
Так как для рентабельных предприятий срок окупаемости должен быть не более 65 лет и в данном случае он составляет 084 года то проектируемое предприятие можно отнести к группе рентабельных.
Таблица 15 – Технико-экономические показатели
Наименование показателей
Годовой выпуск продукции
Годовая выработка на одного рабочего
Трудоемкость 1 м3 изделий
Себестоимость 1 м3 изделий
Баженов Ю.М. Комар А.Г. Технология бетонных и железобетонных изделий: Учебник для вузов. – М.: Стройиздат 1984. – 672 с.
ГОСТ 25912-83 Плиты железобетонные предварительно напряженные для аэродромных покрытий.
Домбровский В.Д. Корнгольд Е.А. Проектирование предприятий сборного железобетона. – Киев: Будивельник 1978 – 144 с.
Лямин В.Н. Оборудование для производства строительных материалов и изделий. – М.: Машиностроение 1991. – 89с.
Рекомендации по определению расчетной стоимости и трудоемкости изготовления сборных железобетонных конструкций на стадии проектирования.-М.: Стройиздат 1987-144с.
СНиП 3.09.01 – 85 Производство сборных железобетонных конструкций и изделий.
Справочник по производству сборных железобетонных изделий Под ред. К.В. Михайлова А.А. Фоломеева. – М.: Стройиздат 1982. – 440 с.
Трофимов Б.Я. Технология бетона строительных изделий и конструкций. – Челябинск: Изд. ЮУрГУ 2002. – 68 с.
Трофимов Б.Я. Вальт А.Б. Технология бетона строительных изделий и конструкций: Учебное пособие к курсовой работе. – Челябинск Изд. ЮУрГУ 2000. – 34 с.
Цителаури Г.И. Проектирование предприятий сборного железобетона: Учебник для вузов. – М.: Высшая школа 1986. – 312 с.
План цеха.dwg

Производство железобетоных
преднапряженных аэродромных
изделий и конструкций
Промежуточный склад готовой продукции
Участок ремонта готовых изделий
Участок текущего ремонта форм
Склад форм и оснастки
Щелевая тунельная камера ТВО
Ленточный конвейер подачи бетонной смеси
Рельсы самоходной тележки
Машина для чистки форм
Устройство для обрезания арматуры
Устройство для открывания и закрывания бортов формы
Машина для смазки форм
Машина для нагрева арматуры
Привод конвейерной линии
Подъемник-снижатель самоходный
преднапряженных аэродромных
Производство железобетоных
Кафедра строительных
Тех-карта.dwg

Технологическая карта на изготовление предварительно
напряженных железобетонных аэродромных плит 1ПАГ -
ГОСТ 25912.0-25912.3-83. Класс бетона В25. Морозостойкость F200. Трудоемкость изготовления
изделия 1.55 чел*часкуб.м. Состав производственной бригады в смену: машинист крана 4 разряда
- 2чел.; арматурщик 4 разряда - 5чел.; такелажник - 2чел.; оператор линии 4 разряда - 1чел.;
машинист тележки 4 разряда - 1чел.; оператор подъемника-снижателя 4 разряда - 2чел.;
пропарщик 3 разряда - 1чел.; машинист бетоноукладчика 4 разряда - 1чел.; контролер ОТК 4
Соответствие рабочим
Лица ответственные за
технического контроля
Устройство для открывания и
Приемку железобетонных плит осуществляют партиями. В состав партии включают плиты одного типа
изготовленные по одной технологии из материалов одного вида и качества в течении не более одних суток
этом размер партии не должен превышать 200Приемо-сдаточные испытания проводятся для каждой партии
изделий по результатам испытания не менее одной серии образцов
изготовленных из одной пробы бетонной смеси
не реже одного раза в смену. Сплошной контроль осуществляется по наличию закладных и комплектующих
монтажных петель и строповочных отверстий
правильности нанесения маркировки.
При приемке плит по показателям точности геометрических параметров
толщины защитного слоя бетона до
арматуры и качества поверхностей
контролируемым путем измерений
следует применять выборочный
одноступенчатый контроль. Партия изделий принимается
если при одноступечатом контроле в выборке нет
деффектных изделий или их количество не превышает браковочное число.
Приемку плит по показателям прочности и морозостойкости бетона следует проводить по результатам
периодических испытаний. В случаях если
если отпускная прочность бетона плит не удовлетворяет требованиям
(п.2.10 ГОСТ 25912.0)
поставка плит потребителю не должна производиться до достижения бетоном плит
соотвествующей классу бетона по прочности на сжатие и марке по прочности на растяжение при
При приемке плит необходимо производить испытание трещиностойкости их нижней и верхней зон. От каждой партии
для испытания отбирается одна плита
удовлетворяющая по другим показателям требованиям стандарта. Плита
считается выдержавшей испытание
если при контрольной нагрузке 33
кН (для нижней зоны) и 27
верхней зоны) на поверхности испытуемой зоны и боковым граням не будут обнаружены трещины при тщательном
осмотре через лупу с четырехкратным увеличением. Если более двух плит не выдерживают испытания
плиты данной партии подвергают испытанию.
Рабочая поверхность плит не должна иметь трещин. Рифленая поверхность плиты должна иметь четкий рисунок
рифления без околов граней канавок. Глубина рифа должна быть не менее 1
мм. На поверхностях плит не
допускается шелушений бетона. Размеры раковин
местных наплывов и впадин на бетонной поверхности и околов
бетона ребер плит не должны превышать значений указанных в ГОСТ 25.912.0-83. На любом участке бетонной
поверхности плиты площадью 1кв. м. должно быть не более трех раковин и местных наплывов или впадин.
Боковые грани у нижней и верхней поверхностей плит
а также открытые поверхности монтажно-стыковых изделий
должны быть очищены от наплывов бетона.
Запрещается производить какие либо работы с формами во время движения
конвейера. Запрещается переходить через конвейер в неустановленных местах или
через формы. Переходить через конвейер только по мостикам. Рабочие посты
должны быть оборудованы средствами звуковой и световой сигнализации. На
постах запрещается курить во избежании пожароопасной ситуации. В цехе
оборудуются несколько мест с огнетушителями.
На посту распалубки на дисковой пиле следует устанавливать искроотбойник
во время работы с пилой одевать наушники. Во время раскрытия бортов отойти от
формы. При перемещении готового изделия краном с траверсой
расстроповке необходимо отойти на безопасное расстояние.
При укладке горячей арматуры в упоры следует использовать специальные
Упоры формы должны быть снабжены защитными кожухами для предотвращения
несчастных случаев. Машина для чистки форм должна быть оборудована защитным
кожухом и пылевсасывающим устройством. При укладке ненапрягаемой арматуры во
избежании порезов и ранений нелбхлдимо использовать рукавицы.
На пост формования лица моложе 18 лет и женьщины не допускаются к работе
(в условиях вибрации). Запрещается находится рядом с виброплощадкой во время
уплотнения бетонной смеси. Кабина формовщика оборудуется амортизаторами.
Параметры напрягаемой
занимаемая конвейером; 2 - промежуточный склад готовой продукции; 3 - ремонт
изделий; 4 - участок текущего ремонта форм; 5 - склад форм и оснастки; 6 - бытовые помещения;
- основной проход; 8 - рельсовые пути.
- мостовой кран; 2 - рельсы для тележки; 3 - дороги для проезда и загрузки
машин; 4 - места стока атмосферных осадков.
Режим ТВО для железобетонных предварительно напряженных
аэродромных плит 1ПАГ - 14AV из тяжелого бетона с классом по
прочности на сжатие В25 составляет 9 часов.
часа - нагрев изделия; 4 - изотермическая выдержка; 2 -
- пульт управления; 2 - рабочее место; 3 - устройство
открывания бортов; 4 - пила трения; 5 - форма
- пульт управления; 2 - рабочее место; 3 - машина для смазки
формы; 4 - форма; 5 - машина для чистки формы
- установка нагрева арматуры; 2 - рабочее место;
- форма; 4 - запас арматурных элементов
- пульт управления; 2 - рабочее место; 3 - форма;
- бетоноукладчик; 5 - бункер бетоноукладчика
Диаметр напрягаемой
Режим работы предприятия принимается по ОНТП
-85. Количество рабочих суток в году составляет
7. Длительность плановых остановок на ремонт
составляет 13 суток для конвейерной линии.
Количество рабочих смен в сутки - 3. Количество
рабочих часов в сутки 23.
Расчетное количество рабочих суток в году
назначается исходя из 260 номинальных рабочих суток
и длительности плановых остановок на ремонт.
Проектное напряжение
Число напрягаемых стержней
- рабочее место; 2 - форма
- запасы арматурных элементов; 2 - рабочее место
Порядок выходного контроля
План склада готовой продукции
План формовочного цеха
Режим труда и отдыха
Характеристика армирования
Пост чистки и смазки
Общий вид изделия (с допусками)
Технологическую карту составила студентка группы
Техника безопасности
Поверхностный вибратор
Установка для электронагрева
Автоматическая траверса
Машина для смазки формы
Машина для чистки формы
Оборудование и инструмент
Пооперационный контроль качества
уплотнения бетонной смеси. Кабина формовщика оборудуется амортизаторами.
(в условиях вибрации). Запрещается находится рядом с виброплощадкой во время
На пост формования лица моложе 18 лет и женьщины не допускаются к работе
избежании порезов и ранений нелбхлдимо использовать рукавицы.
кожухом и пылевсасывающим устройством. При укладке ненапрягаемой арматуры во
несчастных случаев. Машина для чистки форм должна быть оборудована защитным
Упоры формы должны быть снабжены защитными кожухами для предотвращения
При укладке горячей арматуры в упоры следует использовать специальные
расстроповке необходимо отойти на безопасное расстояние.
во время работы с пилой одевать наушники. Во время раскрытия бортов отойти от
постах запрещается курить во избежании пожароопасной ситуации. В цехе
должны быть оборудованы средствами звуковой и световой сигнализации. На
через формы. Переходить через конвейер только по мостикам. Рабочие посты
конвейера. Запрещается переходить через конвейер в неустановленных местах или
Запрещается производить какие либо работы с формами во время движения
часа - нагрев изделия; 4 - изотермическая выдержка; 2 -
аэродромных плит 1ПАГ - 14AV из тяжелого бетона с классом по
Режим ТВО для железобетонных предварительно напряженных
назначается исходя из 260 номинальных рабочих суток
Расчетное количество рабочих суток в году
Количество рабочих смен в сутки - 3. Количество
7. Длительность плановых остановок на ремонт
-85. Количество рабочих суток в году составляет
Режим работы предприятия принимается по ОНТП
бетона ребер плит не должны превышать значений указанных в ГОСТ 25.912.0-83. На любом участке бетонной
мм. На поверхностях плит не
местных наплывов и впадин на бетонной поверхности и околов
Рабочая поверхность плит не должна иметь трещин. Рифленая поверхность плиты должна иметь четкий рисунок
а также открытые поверхности монтажно-стыковых изделий
При приемке плит необходимо производить испытание трещиностойкости их нижней и верхней зон. От каждой партии
верхней зоны) на поверхности испытуемой зоны и боковым граням не будут обнаружены трещины при тщательном
соотвествующей классу бетона по прочности на сжатие и марке по прочности на растяжение при
Приемку плит по показателям прочности и морозостойкости бетона следует проводить по результатам
удовлетворяющая по другим показателям требованиям стандарта. Плита
поставка плит потребителю не должна производиться до достижения бетоном плит
следует применять выборочный
если отпускная прочность бетона плит не удовлетворяет требованиям
если при одноступечатом контроле в выборке нет
толщины защитного слоя бетона до
этом размер партии не должен превышать 200Приемо-сдаточные испытания проводятся для каждой партии
не реже одного раза в смену. Сплошной контроль осуществляется по наличию закладных и комплектующих
- мостовой кран; 2 - рельсы для тележки; 3 - дороги для проезда и загрузки
Устройство для открывания и
пропарщик 3 разряда - 1чел.; машинист бетоноукладчика 4 разряда - 1чел.; контролер ОТК 4
машинист тележки 4 разряда - 1чел.; оператор подъемника-снижателя 4 разряда - 2чел.;
- 2чел.; арматурщик 4 разряда - 5чел.; такелажник - 2чел.; оператор линии 4 разряда - 1чел.;
изделия 1.55 чел*часкуб.м. Состав производственной бригады в смену: машинист крана 4 разряда
ГОСТ 25912.0-25912.3-83. Класс бетона В25. Морозостойкость F200. Трудоемкость изготовления
напряженных железобетонных аэродромных плит 1ПАГ -
Технологическая карта на изготовление предварительно
изделий; 4 - участок текущего ремонта форм; 5 - склад форм и оснастки; 6 - бытовые помещения;
занимаемая конвейером; 2 - промежуточный склад готовой продукции; 3 - ремонт
- пульт управления; 2 - рабочее место; 3 - устройство
- пульт управления; 2 - рабочее место; 3 - машина для смазки
- пульт управления; 2 - рабочее место; 3 - форма;
Параметры напрягаемой
Лица ответственные за
Соответствие рабочим
Рекомендуемые чертежи
- 01.04.2024
Свободное скачивание на сегодня
Обновление через: 6 часов 51 минуту