Проектирование цилиндрического резервуара




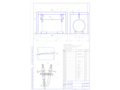
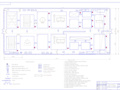
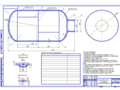
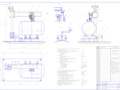
- Добавлен: 25.10.2022
- Размер: 1 MB
- Закачек: 4
Описание
Состав проекта
![]() |
![]() |
![]() |
![]() ![]() ![]() ![]() |
![]() ![]() ![]() ![]() |
![]() ![]() ![]() ![]() |
![]() ![]() ![]() ![]() |
![]() ![]() ![]() ![]() |
![]() ![]() ![]() ![]() |
![]() ![]() ![]() ![]() |
![]() ![]() ![]() ![]() |
![]() ![]() ![]() ![]() |
![]() |
![]() ![]() ![]() |
![]() ![]() ![]() |
![]() ![]() ![]() |
![]() ![]() ![]() |
![]() ![]() ![]() |
![]() ![]() ![]() ![]() |
![]() |
![]() ![]() ![]() |
![]() ![]() ![]() |
Дополнительная информация
4лист.cdw

-Участок подготовки днищ под сварку и сварку;
покрытыми электродами.
-Установка АСФ для сварки кольцевых и продольныхь швов;
-Подвод трехфазного напряжения;
-Подвод сжатого воздуха давлением 3 Атм;
-Подвод холодной воды с отводом в канализацию;
-Направление движения грузопотока;
-Место складирования листового проката под обечайки;
-Установка плазменной резки ;
-Установка для вальцовки обечаек;
-Участок резки заготовок опор
-Участок заготовки патрубков;
-Участок сбоки и сварки опор;
-Участок сборки и сварки патрубков;
-Установка плазменной резки;
-Участок сборки заготовок днищ под штамповку;
-Источник питания для сварки
-Капитальная стена здания
Условные обозначения:
-Кран мостовой;Q=30т
-Участок сбоки и сварки обечайки опоры;
-Место складирования загогтовок крепежных деталей резервуара;
-Участок окончатльной сборки и сварки деталей крепежа;
-Участок завершающей сборки и сварки резервуара;.
-Кладовая вспомогательных материалов;
-Кладовая электродов
электродной проволоки и флюсов;
-Источник питания для машины
2лист.cdw

Сварку производить электродом Э46Р ГОСТ9467-75
Предельные отклонения размеров
*Размеры для справок.
спецификация.cdw

лист1.cdw

Для корпуса резервуара
Давление пробное при гидроиспытании
Температура рабочей среды
Температура расчетная стенки
Минимально допустимая температура
Группа аппарата для контроля
Прибавка для компенсации коррозии
Расчетный срок службы
Число циклов нагружения за весь срок
Масса аппарата при гидроиспытании
Технические требования
*Размеры для справок.
Неуказанные предельные отклонения размеров
Изготовление и приемку резервуара произвести в соответствии
с требованиями ГОСТ Р 52630-2012.
Неуказанные сварные швы по ГОСТ 14771-76.
Произвести гидроиспытание корпуса аппарата на прочность и
герметичность пробным давлением 0
МПа в течении не менее 10
После гидроиспытаний воду слить и просушить воздухом резервуар.
Покрытие наружной поверхности: эмаль ПФ-115
Маркировать знак "Место строповки" по ГОСТ 14192-96.
Произвести консервацию резервуара по ГОСТ 9.014-78.
Условия транспортировки и хранения по ГОСТ 380-2005.
Основной конструкционный материал корпуса 09Г2С.
Таблица1-Техническая характеристика
3лист.cdw

Допускаемая нагрузка на одну роликовую опору
Скорость вращения изделий :
свариваемых изделий
Мощность электродвигателей привода
сварочной скорости 0
Габаритные размеры узлов стенда
Т5-5А редукторной 654
Технические характеристики сварочной установки
Диаметр обрабатываемого изделия
Вес изделия при сварке
Вес изделия при сборке
Скорость вращения изделия
Точное обеспечение заданной скорости
Скорость осевого перемещения изделия
Скорость перемещения каретки манипулятора
Высота манипулятора от поверхности пола
Диаметр проволоки при сварке
Напряжение питающей сети
Напряжение на кнопках упраыления
Датчик ультрозвуковой
4лист.cdw

-Участок подготовки днищ под сварку и сварку;
покрытыми электродами.
-Установка АСФ для сварки кольцевых и продольныхь швов;
-Подвод трехфазного напряжения;
-Подвод сжатого воздуха давлением 3 Атм;
-Подвод холодной воды с отводом в канализацию;
-Направление движения грузопотока;
-Место складирования листового проката под обечайки;
-Установка плазменной резки ;
-Установка для вальцовки обечаек;
-Участок резки заготовок опор
-Участок заготовки патрубков;
-Участок сбоки и сварки опор;
-Участок сборки и сварки патрубков;
-Установка плазменной резки;
-Участок сборки заготовок днищ под штамповку;
-Источник питания для сварки
-Капитальная стена здания
Условные обозначения:
-Кран мостовой;Q=30т
-Участок сбоки и сварки обечайки опоры;
-Место складирования загогтовок крепежных деталей резервуара;
-Участок окончатльной сборки и сварки деталей крепежа;
-Участок завершающей сборки и сварки резервуара;.
-Кладовая вспомогательных материалов;
-Кладовая электродов
электродной проволоки и флюсов;
-Источник питания для машины
2лист.cdw

Сварку производить электродом Э46Р ГОСТ9467-75
Предельные отклонения размеров
*Размеры для справок.
спецификация.cdw

лист1.cdw

Для корпуса резервуара
Давление пробное при гидроиспытании
Температура рабочей среды
Температура расчетная стенки
Минимально допустимая температура
Группа аппарата для контроля
Прибавка для компенсации коррозии
Расчетный срок службы
Число циклов нагружения за весь срок
Масса аппарата при гидроиспытании
Технические требования
*Размеры для справок.
Неуказанные предельные отклонения размеров
Изготовление и приемку резервуара произвести в соответствии
с требованиями ГОСТ Р 52630-2012.
Неуказанные сварные швы по ГОСТ 14771-76.
Произвести гидроиспытание корпуса аппарата на прочность и
герметичность пробным давлением 0
МПа в течении не менее 10
После гидроиспытаний воду слить и просушить воздухом резервуар.
Покрытие наружной поверхности: эмаль ПФ-115
Маркировать знак "Место строповки" по ГОСТ 14192-96.
Произвести консервацию резервуара по ГОСТ 9.014-78.
Условия транспортировки и хранения по ГОСТ 380-2005.
Основной конструкционный материал корпуса 09Г2С.
Таблица1-Техническая характеристика
лист1.dwg
Для корпуса резервуара
Давление пробное при гидроиспытании
Температура рабочей среды
Температура расчетная стенки
Минимально допустимая температура
Группа аппарата для контроля
Прибавка для компенсации коррозии
Расчетный срок службы
Число циклов нагружения за весь срок
Масса аппарата при гидроиспытании
Технические требования
*Размеры для справок.
Неуказанные предельные отклонения размеров
Изготовление и приемку резервуара произвести в соответствии
с требованиями ГОСТ Р 52630-2012.
Неуказанные сварные швы по ГОСТ 14771-76.
Произвести гидроиспытание корпуса аппарата на прочность и
герметичность пробным давлением 0
МПа в течении не менее 10
После гидроиспытаний воду слить и просушить воздухом резервуар.
Покрытие наружной поверхности: эмаль ПФ-115
Маркировать знак "Место строповки" по ГОСТ 14192-96.
Произвести консервацию резервуара по ГОСТ 9.014-78.
Условия транспортировки и хранения по ГОСТ 380-2005.
Основной конструкционный материал корпуса 09Г2С.
Таблица1-Техническая характеристика
3лист.dwg
Допускаемая нагрузка на одну роликовую опору
Скорость вращения изделий :
свариваемых изделий
Мощность электродвигателей привода
сварочной скорости 0
Габаритные размеры узлов стенда
Т5-5А редукторной 654
Технические характеристики сварочной установки
Диаметр обрабатываемого изделия
Вес изделия при сварке
Вес изделия при сборке
Скорость вращения изделия
Точное обеспечение заданной скорости
Скорость осевого перемещения изделия
Скорость перемещения каретки манипулятора
Высота манипулятора от поверхности пола
Диаметр проволоки при сварке
Напряжение питающей сети
Напряжение на кнопках упраыления
Датчик ультрозвуковой
2лист.dwg
Сварку производить электродом Э46Р ГОСТ9467-75
Предельные отклонения размеров
*Размеры для справок.
4лист.dwg
-Участок подготовки днищ под сварку и сварку;
покрытыми электродами.
-Установка АСФ для сварки кольцевых и продольныхь швов;
-Подвод трехфазного напряжения;
-Подвод сжатого воздуха давлением 3 Атм;
-Подвод холодной воды с отводом в канализацию;
-Направление движения грузопотока;
-Место складирования листового проката под обечайки;
-Установка плазменной резки ;
-Установка для вальцовки обечаек;
-Участок резки заготовок опор
-Участок заготовки патрубков;
-Участок сбоки и сварки опор;
-Участок сборки и сварки патрубков;
-Установка плазменной резки;
-Участок сборки заготовок днищ под штамповку;
-Источник питания для сварки
-Капитальная стена здания
Условные обозначения:
-Кран мостовой;Q=30т
-Участок сбоки и сварки обечайки опоры;
-Место складирования загогтовок крепежных деталей резервуара;
-Участок окончатльной сборки и сварки деталей крепежа;
-Участок завершающей сборки и сварки резервуара;.
-Кладовая вспомогательных материалов;
-Кладовая электродов
электродной проволоки и флюсов;
-Источник питания для машины
3лист.cdw

Допускаемая нагрузка на одну роликовую опору
Скорость вращения изделий :
свариваемых изделий
Мощность электродвигателей привода
сварочной скорости 0
Габаритные размеры узлов стенда
Т5-5А редукторной 654
Технические характеристики сварочной установки
Диаметр обрабатываемого изделия
Вес изделия при сварке
Вес изделия при сборке
Скорость вращения изделия
Точное обеспечение заданной скорости
Скорость осевого перемещения изделия
Скорость перемещения каретки манипулятора
Высота манипулятора от поверхности пола
Диаметр проволоки при сварке
Напряжение питающей сети
Напряжение на кнопках упраыления
Датчик ультрозвуковой
Записка.doc
-показано описание проектируемой конструкции резервуара условия его работы;
- приведено наглядное описание технологии изготовления резервуара режимов сварки;
-рассмотрено применяемое оборудование при изготовлении резервуара и приведены технические характеристики;
-приведены планово-технологические расчеты;
-спроектирован план участка сборки и сварки резервуара.
Данный дипломный проект состоит из графической части на листах формата А1 расчетно-пояснительной записки.
Актуальной целью курсового проекта является проектирование участка сборки и сварки резервуара цилиндрического. Для реализации поставленной цели необходимо было решить следующие задачи:
- провести анализ конструкции резервуара;
- подобрать материал для изготовления резервуара;
- подобрать сварочные материалы;
- разработать технологию изготовления конструкции;
- выбрать современное оборудование для сборки и сварки;
- разработать планировку цеха сборки и сварки.
В качестве исходных данных использовано:
- конструкторская документация;
- нормативно-техническая документация;
ИСХОДНЫЕ ДАННЫЕ ДЛЯ ПРОЕКТИРОВАНИЯ
1 Назначение конструкция и условия работы резервуара
Резервуар предназначен для работы в нефтехимической промышленности
2 Описание конструкции
Резервуар состоит из корпуса днища и патрубка. Общий вид резервуара представлен в графической части
3 Выбор конструкционного материала
3.1 Выбор основных материала
Произведем сравнительный анализ стали ВСт3сп и стали 09Г2С. Вместо среднеуглеродистых сталей при изготовлении сварных конструкций в машиностроении целесообразно использовать низколегированные стали что обеспечивает снижение массы конструкций и позволяет повысить надежность сварных деталей и узлов. Низколегированные стали (09Г2С) повышают прочность при положительных температурах отличаются от низкоуглеродистых (ВСт3сп) сталей отсутствием склонности к старению их можно применять при пониженных до –70ОС и повышенных температурах.
Исходя из вышеприведенного анализа принимаем для производства резервуара сталь 09Г2С.
Химический состав и механические свойства сталей приведены в таблицах 1.2 – 1.5.
Таблица 1.2 - Механические свойства стали 09Г2С 1
Листы после закалки отпуска (образцы поперечные).
от 10 до 32 вкл. от 32 до 60 вкл.
Таблица 1.3 - Предел текучести (ГОСТ 5520-79)
Таблица 1.4 - Температура критических точек ОС
Таблица 1.5 - Химический состав %
КОНСТРУКТИВНАЯ ДОРАБОТКА
1 Расчет толщины стенки днища
Днище ослаблено отверстием под патрубок.
Рисунок 2.1 – Расчетная схема днища
p = 01 МПа – расчетное давление
D = 2300 мм – расчетный диаметр
SНОМ = 8 мм – номинальная толщина стенки
здесь: С1=1-минусовой допуск на толщину стенки
[s]=[s]Т = 156 МПа – допускаемое напряжение материала при расчетной температуре
d = 800 мм – максимальный диаметр отверстия
j =0915 – коэффициент снижения прочности
Расчетная толщина стенки днища
Проектная толщина стенки днища равна 8мм
Условие прочности выполняется.
2 Расчет толщины стенки обечайки
Обечайка ослаблена отверстиями под патрубки.
Расчетная схема представлена на рисунке 2.2
Рисунок 2.2 – Расчетная схема обечайки
D = 1200 мм – внутренний диаметр
SНОМ = 8мм – номинальная толщина стенки
С=С1+С2 – суммарная прибавка к толщине стенки.
ТЕХНОЛОГИЯ ИЗГОТОВЛЕНИЯ
1 Технологический процесс изготовления обечаек
Обечайки Dвн=2300мм стыкуемые с днищем изготавливаем из листового проката=8мм.
Сначала осуществляют входной контроль заготовок. Затем заготовку из стали марки 09Г2С укладывают на настил плитный. Проверяют маркировку листа. Плазменной резкой вырезают из листа заготовку 7272×1500. Проводят зачистку мест реза контроль ВИК. Полученную заготовку вальцуют на четырехвалковой листогибочной машине. Затем осуществляют контроль ВИК вальцованной заготовки и отправляют её на сборку для дальнейшей сварки. Сборка под сварку продольного шва обечайки проводится в следующем порядке. Обечайку устанавливают роликоопору в горизонтальном положении. С помощью технологических скоб устанавливают зазор в стыке мм смещение кромок не более 2 мм. Устанавливают выводные планки на торце обечайки прихватывают каждую в 2-3 местах. С внутренней стороны устанавливают керамическую подкладку для формирования обратного валика с помощью гибкой ленты. Контролируют сборку. Заваривают швы выводных планок па и зачищают. Выполняют сварку АСФ продольного шва. После окончания сварки термической резкой срезаются выводные планки зачищаются места их срезки заподлицо с основным металлом. Снимают усиление сварного шва зачищают и проводят контроль (внешним осмотром и измерениями в объёме 100%). Затем обечайку калибруют на вальцах. Далее производят контроль ВИК и УЗК в объёме 100%.
Обечайки патрубков (ВГ) изготавливаем аналогично.
2 Технологический процесс изготовления днищ
Сначала осуществляют входной контроль материала. Затем лист из стали марки 09Г2С (толщиной 8мм) укладывают на раскройный стол машины плазменной резки «Термит». Плазменной резкой вырезают из листа 2860×2860 заготовку 2-х днища диаметром 2854мм. Осуществляют зачистку мест реза контроль ВИК. Осуществляют с помощью пресса гибку в горячем состоянии по матрице днища с последующей зачисткой механической обработкой и контролем ВИК.
3 Сборка-сварка днища с обечайкой
Установить обечайку в горизонтальное положение на подставки. Затем установить и приварить направляющие планки (шесть штук равномерно по периметру обечайки). Застропить днище за проушины и установить на обечайку по направляющим планкам выдержав зазор в стыке мм. Прихватить па кольцевой стык в 8 – 10 местах длина прихватки 40-50 мм. Застропить полученное соединение и кантовать в горизонтальное положение. Удалить технологические детали слесарным способом. Переместить на установку для сварки кольцевых швов. С внутренней стороны устанавливают керамическую подкладку для формирования обратного валика с помощью гибкой ленты. Установить сборку на роликоопорный стенд и произвести полуавтоматическую сварку кольцевого шва снаружи с последующей зачисткой металла шва после прохода). Контролировать сборку по ОСТ 26291-94: внешним осмотром измерениями сварку УЗК в объёме 100%.
4 Приварка патрубков к обечайке
Патрубки вставляют в отверстия. Прихватывают в 2-3 местах па контролируют сборку. Осуществляют па сварку с обеих сторон. Далее снимается усиление шва и обеспечивается плавный переход к патрубку (при помощи шлифовальной машинки). Производят контроль геометрических размеров и контроль сварных соединений ВО измерениями и УЗК.
5 Обоснование выбора способов сварки
Исходя из условий работы назначения материала используемого при изготовлении резервуараи допускается использовать для сварки конструкции следующие виды сварки: ручная дуговая сварка (РДС) автоматическая сварка под флюсом (АСФ) автоматическая и полуавтоматическая сварка в среде СО2 и его смесях с О2 (кислородом) .
Ручная дуговая сварка
Этим способом сваривают конструкции во всех пространственных положениях из разных марок сталей в случаях когда применение автоматической и полуавтоматической сварок не возможно например при отсутствии требуемого оборудования. К преимуществам РДС относятся также:
- возможность сварки в любом пространственном положении;
- возможность устойчивого горения дуги и плавление электрода на постоянном и переменном токе;
- достаточная защита расплавленного металла;
- возможность получения хорошо сформированных валиков;
К недостаткам можно отнести большую вероятность получения дефектов в сварном соединении малую производительность процесса большой расход сварочных материалов плохие санитарные условия сварки большое тепловложение в свариваемое изделие что приводит к послесварочным деформациям изделия. Регулирование скорости подачи и скорости сварки осуществляется сварщиком вручную следовательно качество сварного шва будет зависеть от практических навыков сварщика.
Сварка в СО2 и его смесях
По сравнению с РДС сварка в защитных газах имеет следующие преимущества:
а) возможность механизации сварочных работ при выполнении коротких швов;
б) уменьшение коробления изделий за счет повышенной теплоотдачи охлаждающего действия защитной среды и увеличения скорости кристаллизации расплавленного металла;
в) простота процесса и техники сварки (сварщики осваивают этот способ за 3-5 смен);
г) более высокая производительность труда за счет автоматической подачи проволоки при удовлетворительном качестве сварных швов;
д) малая чувствительность к образованию пор по сравнению с процессом сварки электродами с фтористо-кальциевым покрытием и сваркой под флюсом ОСЦ-45 и АН-348А металла покрытого окалиной ржавчиной и другими загрязнениями;
е) уменьшенное содержание газов в шве;
ж) возможность непосредственного наблюдения за процессом сварки и местом положения швов;
з) возможность сварки в труднодоступных местах;
и) дешевизна процесса.
Недостатки: в связи с повышенным содержанием кислорода в атмосфере дуги необходимо раскислять в процессе сварки металл шва. Элементы раскислители вводятся в сварочную ванну через электродную проволоку.
Таким образом выбираем для сварки протяженных продольных швов более 3000мм и для поперечных коротких швов АСФ патрубков - способ полуавтоматической сварки в среде защитного газа СО2 для сборочных работ РДС.
6 Выбор сварочных материалов
Сварочные материалы должны удовлетворять следующим требованиям:
а) должны соответствовать требованиям стандартов технических условий и паспортов и иметь сертификаты;
б) сварочные материалы следует хранить рассортированными по партиям. На поверхности сварочной проволоки не должно быть следов ржавчины масла и других загрязнений;
в) электроды перед использованием должны быть прокалены.
Сварочные проволоки и электроды должны иметь химический состав близкий к составу основного металла иметь низкое содержание C S P.
Для ручной дуговой сварки низко- и среднеуглеродистых сталей рекомендуют использовать покрытые электроды УОНИИ 1355. Эти электроды обеспечивают высокую пластичность ударную вязкость металла шва и стойкость против образования трещин.
Выбираем сварочные материалы:
- РДС – электроды УОНИИ-1355 (3 – 5 мм).
- РДС – электроды ОЗС-312 (4 мм) – переходные электроды для приварки лотка к корпусу;
- па в СО2 – проволоку Св-08Г2С(О) ( 12 мм);
- газовая защита – смесь «Аргомикс» СО2 20% Ar 80%;
- АСФ – флюс АН-348А;
- проволоку Св-08ГА ( 3 мм);
- самоклеющаяся керамическая подкладка с возможностью изгиба
Таблица 3.1 - Химический состав электродов УОНИИ-1355 %
Таблица 3.2 - Химический состав электродов ОЗС-312 %
Таблица 3.3 - Химический состав сварочной проволоки Св-08Г2С(О)
Таблица 3.4 - Состав сварочного флюса
Таблица 3.5 - Химический состав сварочной проволоки Св-08А
Углекислый газ или углекислота (СО2) – бесцветный газ с едва ощутимым запахом; при растворении в воде придает ей слабый кисловатый вкус. При 0° Си давлении 760 мм рт. ст. плотность 197686 гл плотность по отношению к воздуху 1524.
Жидкую углекислоту транспортируют в стальных баллонах или в специальных контейнерах.
7 Расчет параметров режимов
Рисунок 3.1 Сварное соединение
S = 8; e = 120; e1 = 8; h =25;
а) Определение площадь наплавленного металла (FН).
Для упрощения расчета проводим разбивку общей площади на простые фигуры как представлено на рис. 1 соответственно обозначив их как F1 F2 F3 F4 по формулам :
б) Определение площади поперечного сечения корневого и подварочного валиков (FK) по формуле :
Принимаем FК = 20мм (для одного шва).
в) Определение ориентировочно площади поперечного сечения последующих валиков (FС1) по формуле :
Принимаем FС1 = 42мм
г) Определение ориентировочно число проходов (n1) по формуле:
д) Расчет сварочного напряжения и силу сварочного тока.
Так как покрытие электрода основное то силу сварочного тока будем вычислять по формуле (10); где Кп. – коэффициент учитывающий положение сварки. В нашем случае Кп.=1 так как сварку ведем в нижнем положении.
Производим расчет режима сварки корневого шва для наружной части стыка.
Определяем глубину проплавления принимаем
е) Определяем диаметр электродной проволоки принимаем dЭ1 = 3[мм].
ж) Определяем силу тока по формуле :
где: Кд – коэффициент зависящий от марки флюса диаметра электродной проволоки и полярности тока.
Принимаем IСВ К =480[А].
з) Определяем напряжение на дуге по формуле .
Принимаем UСВ К =34[В].
и) Определение скорости сварки. Скорость сварки [мчас] определяется по формуле:
где: А – табличный коэффициент зависящий от диаметра электрода.
Принимаем VСВ К = 42. [мчас] причем число должно быть целым.
к) Проверяем выбранные параметры.
Определение величины погонной энергии.
Погонная энергия [Джсм] определяется по формуле :
где: = 08 ..085 – эффективный КПД нагрева изделия дугой при АСФ; VСВ К – скорость сварки смс.
Определение коэффициента формы провара.
Коэффициент формы провара определяется по формуле:
k = 0367 j0.1925=0367 310.1925=071
При плотности тока j ≥ 120 Амм2 k = 092 (сварка на постоянном токе обратной полярности) k = 112 (сварка на постоянном токе прямой полярности). При j 120 Амм2 k = 0367 j0.1925 (сварка на постоянном токе обратной полярности) при сварке на прямой полярности k = 282 j0.1929. При сварке на переменном токе во всех диапазонах плотностей тока k = 1.
Определяем глубину проплавления gП [см] при рассчитанных выше параметрах режима:
Полученные значения глубины проплавления gП=58 сравнивают с исходным gП=6. Погрешность не превышает 5%.
л) Определяем коэффициент наплавки [ГАчас].
При скорости сварки от 20 до 100 мч (при сварке на переменном токе) действует следующая форма зависимости от dЭ К и IСВ К:
αН = 00065 IСВ + 915= 00065 480 + 915=1227гАчас
м) Определяем вылет электродной проволоки.
Это величина определяется по формуле :
н) Определяем время сварки.
При симметричной разделке кромок обычно используют средний диаметр обечайки. тогда время сварки определяется по формуле:
о) Вычисляем массу наплавленного металла mН по формуле:
п) Определение расхода электродной проволоки (GЭ) по формуле:
где Кр = 11 – коэффициент расхода учитывающий неизбежные потери электродов на угар разбрызгивание .
р) Определим расход флюса
Определим силу тока (IСВ) для электродов с основным покрытием (УОНИИ-1355) по формуле 7:
IСВ=(6 dЭЛ+20) dЭЛ КП (3.15)
где КП – коэффициент положения электрода в пространстве для нижнего положения КП = 10.
IСВ = (6×3+20) ×3×1=114 А
Определим напряжение по формуле 7:
Определим скорость сварки шва по формуле 7:
где: αн - коэффициент наплавки αН = 95 г(А×час) для УОНИИ-1355
g = 78 гсм3 – плотность металла; FH[см2].
ОБОРУДОВАНИЕ ДЛЯ СБОРКИ И СВАРКИ
1 Сварочный полуавтомат
Полуавтомат Speedtec 400S - инверторный сварочный аппарат предназначенный для полуавтоматической сварки в среде защитного газа (MIGMAG) с возможностью ручной дуговой сварки покрытыми электродами (ММА) а также полуавтоматической сварки порошковой проволокой (FCAW) .
Рисунок 4.1 – Сварочный полуавтомат Speedtec 400S
Технические данные полуавтомата Speedtec 400S приведены в таблице 4.1
Таблица 4.1 – Технические характеристики Speedtec 400S
Частота питающей сети
Потребляемая мощность
Диапазон регулирования сварочного тока
Сварочный ток MIGММА
Диапазон рабочего напряжения
Напряжение холостого хода
Скорость подачи проволоки
Диаметр сварочной проволоки
Допустимый вес катушки
Вид подающего устройства
Для проведения сварочных работ РДС используем отечественный инвертор марки МС-315 «Эллой» Нижний Новгород – представляет собой аппарат выполненный в однокорпусном исполнении и предназначенный для РДС покрытыми электродами (ММА) постоянным током на прямой или обратной полярности во всех пространственных положениях .
Рисунок 4.2 – Общий вид МС-315
Технические данные инверторного сварочного источника питания МС-315 приведены в таблице 4.2.
Таблица 4.2 – Технические характеристики МС-315
Температура окружающей среды °С
Диапазон регулирования сварочного тока А
Потребляемая мощность кВа
Напряжение холостого хода В
Время горячего старта сек.
Сварочный ток А при ПВ 60%
Сварочный ток А при ПВ 100%
Габаритные размеры мм
3 Оборудование для АСФ
Для выполнения кольцевых швов корпуса методом АСФ предлагается использовать сварочную установку скомплектованную из велосипедной тележки ВТ-2 сварочной головки А-1401 и роликоопорного стенда 60СД.
Технические характеристики сварочной установки:
Расстояние от оси колонны до оси электрода при
установке автомата А1401
Тип сварного автомата А1401
Диаметр свариваемых швов мм 500-3000
Длина свариваемых швов мм .. не ограничена
Скорость перемещения тележки:
рабочая (сварочная)мч 19-77
Регулировка рабочей скорости перемещения тележки
.плавная бесступенчатая
Скорость подъема и опускания каретки ммин 2
Электродвигатель механизма перемещения тележки:
частота вращения обмин ..1420
Габарит мм ..4650×3900×5900
Роликовый стенд модель HGK-10
Рисунок 4.2- Роликовый вращатель
Предназначен для вращения цилиндрических изделий со сварочной скоростью при ручной полу автоматической и автоматической сварке внутренних и наружных кольцевых швов а также для установки изделий в положение удобное для сварки. На нем можно производить работы требующие поворота изделия.
Сварка может проводиться под слоем флюса и в защитной среде инертных газов.
Технические характеристики роликового стенда:
Наибольший крутящий момент на выходном валу Н·м 1000
Грузоподъемность кг 20000
Частота вращения ролика обмин 006-39
Рекомендуемые свариваемые диаметры круговых швов мм .500-3200
Наружный диаметр роликов мм 300
частота вращения обмин 1500
Масса стенда(без электрошкафа) кг 3197
Масса электрошкафа кг 75
Сварочный автомат А-1401:
Автомат А1401 предназначен для дуговой сварки плавящимся электродом под флюсом или в защит ном газе (углекислом или аргоне) изделий из углеродистых сталей на переменном или постоянном токе
Автомат рассчитан на длительную работу и может быть использован в составе обычных или высокопроизводительных установок в поточных и автоматических линиях.
Основные особенности автоматов унифицированной серии — универсальность применения для дуговой сварки швов различных типов широкий диапазон настройки и регулирования режимов сварки.
В сварочной установке флюсоотсос находился на значительном расстоянии от сварочной головки. Из-за небольшого диаметра свариваемого изделия возникала опасность высыпания флюса. Поэтому было принято решение максимально близко расположить флюсоотсос от сварочной головки.
Технические характеристики сварочной головки А-1401:
Диаметр электродной проволоки мм 2-5
Скорость подачи электродной проволоки мч 53-532
Скорость сварки мч 12-120
Число электродов шт 1
Ход сварочной головки мм:
Вместимость флюсобункера м 0055
Масса электродной проволоки в катушке кг 80
Номинальный сварочный ток при ПВ = 100%А 1000
Номинальное напряжение питающей трехфазной сети
частотой 50 Гц В 380
1 Исходные данные для предлагаемого расчета
Таблица 5.1 - Геометрические параметры сварных швов
2 Нормирование автоматической сварки
Основное время при автоматической сварке под флюсом:
где VСВ – скорость сварки (задается режимом сварки) мчас
n – количество проходов.
Количество проходов при автоматической сварке рассчитывается по формуле:
где F – площадь поперечного сечения наплавленного металла шва мм2;
F1 – площадь поперечного сечения первого прохода шва мм2;
Fn – площадь поперечного сечения одного последующего прохода мм2.
Примерные площади поперечного сечения швов для первого и последующих проходов даны в таблице 4.1.
Таблица 5.2 – Площади поперечного сечения для первого и последующих проходов
Площадь поперечного сечения мм2
Углеродистые и низколегированные стали
Высоколегированные стали
Алюминий и алюминиевые сплавы
Медь и медно-никелевые сплавы
Вспомогательное время tв1 при автоматической сварке включает время на зачистку свариваемых кромок от ржавчины зачистку шва от шлака после каждого прохода осмотр измерение и клеймение шва смену кассет с электродной проволокой. В зависимости от толщины свариваемого металла вида соединений и сварных швов tв1 изменяется в широких пределах. Принимаем tв1 =2 мин на 1 метр одного прохода.
Вспомогательное время tв2 затрачивается на установку поворот и снятие изделий закрепление и открепление деталей перемещение сварщика.
tВ1 =2×1703=3406 мин.
tВ2=tУП+tПЕР=22×2+02×9=62мин.
Время вспомогательное:
tВ =34064+62=402 мин.
tоп = t0 + tВ=193+402=5952мин.
Таблица 5.3 – Время обслуживания отдых и личные надобности
В % от оперативного времени
Стационарные установки
Переносные автоматы полуавтоматы
Время обслуживания рабочего места:
tобс=006×595=35 мин.
Время на отдых и личные надобности:
tотд=005×595=209 мин.
Подготовительно-заключительное время tпз как правило составляет 4% от оперативного времени:
Определим норму штучного времени tшт на изготовление сварных конструкций:
где a=6% - процент составляющий tобс к оперативному времени;
b=5% - процент составляющий tотд к оперативному времени.
Рассчитаем штучно-калькуляционное время на каждый шов
tшк= tшт+ tпз=595+295 =624мин
Нормирование полуавтоматической сварки
Основное время при полуавтоматической в среде защитных газов рассчитывается по формуле:
tоп = t0 + tВ=78+2647=342мин.
tотд=005×342=17 мин.
tшк= tшт+ tпз=13+343=356мин
3 Планово-экономические расчеты сборочно-сварочного участка
Расчет стоимости основных производственных фондов участка
В данном разделе проекта рассчитывается стоимость только тех основных фондов которые непосредственно связаны с работой участка стоимость оборудования Фоб стоимость производственных площадей Фпл стоимость оснастки Фос и производственных площадей Фпл; стоимость оснастки Фос и производственно-хозяйственного инвентаря Фин. Общая сумма основных фондов участка Фуч:
Фуч =Фоб+Фпл+Фос+Фин
Стоимость оборудования определяется количеством каждого вида оборудования Кмi и затратами на приобретение и монтаж единицы оборудования Цбi :
=3800000+130000+50000=3980000 руб.
Стоимость технологической оснастки принимаем 8% а производственно-хозяйственного инвентаря 1% от стоимости оборудовании участка :
Стоимость производственных помещений (площадей) Фпл зависит от кубатуры V и стоимости 1 м3 здания Цзд :
Фпл=V Цзд=Fпр h kд Цзд
где Fпр – производственная площадь участка м2 (Fпр=2040 м2);
h – высота пролетов (принимается h= 18 м.);
kд – коэффициент учитывающий дополнительную площадь (принимается kд = 15)
Фпл=2040×18×15×1000=55080000 руб.
Определим общую сумму основных фондов участка:
Фуч =55080000+39800+3184+3980000=59102984руб.
4 Расчет фондов заработной платы участка
Фонды заработной платы рассчитываются отдельно по каждой категории работников.
Основная и дополнительная заработная плата сварщиков приходящаяся на одно изделие рассчитывается по формуле:
– штучно-калькуляционное время на каждый сварной шов мин.;
Kзд=13 – коэффициент учитывающий дополнительную заработную плату
Фонд заработной платы сварщиков рассчитаем по формуле:
где: Nг – годовая программа выпуска изделий (принимаем 2000) шт.
=5308×2000=1061600 руб.
Фонд заработной платы вспомогательных рабочих повременщиков рассчитывается по формуле:
где Фдр – действительный фонд времени одного рабочего ч. принимается равным 1780 ч.;
kвспi- численность вспомогательных рабочих чел.
=1780×115×13×1=266110руб.
Заработная плата вспомогательных рабочих приходящаяся на i-е изделие:
=2661102000×2=266 руб.
Фонд заработной платы инженерно-технических работников (ИТР) руководства участка:
Мг – число месяцев работы в году (принимается Мг =112);
lокi – месячный оклад i-й категории работников руб.
Lитр=112×28000×1=313600 руб.
Заработная плата ИТР и руководителей приходящаяся на i-е изделие:
=3136002000×1=1568 руб.
5 Определение себестоимости изделий
По мере отнесения затрат на единицу продукции различают технологическую Ст цеховую Сц производственную Спр и полную Спол себестоимости. В экономической части дипломного проекта расчет ведется по изделиям изготавливаемым на сборочно-сварочном участке.
Технологическая себестоимость сварочных работ включает затраты на основные материалы См сварочные материалы Ссв технологическую электроэнергию Сэ заработную плату Сзп расходы по содержанию и эксплуатации оборудования Со6 расходы на технологическое оснащение и инструмент целевого назначения Сос :
где Nг – производственная программа выпуска изделий шт.
Затраты на основные материалы рассчитываются по формуле:
kтз – коэффициент учитывающий транспортно-заготовительные расходы (можно принять kтз =105);
Цоi – цена 1 т отходов Цoj=7000 руб.
См=(24×40000×105)–1176=99624руб.
Затраты на сварочные материалы включают стоимость электродов Сэл сварочной проволоки Ссвп защитного газа и флюса Сг.
Затраты на электроды при ручной дуговой сварке и на сварочную проволоку при автоматической и сварке определяются по формуле:
где Qн – масса наплавленного металла кг;
qэл – расход электродов или сварочной проволоки на 1кг наплавленного металла (для РДС принимаем равным 15) кг;
Цэл – цена 1 кг электродов или сварочной проволоки руб.
Затраты на электроды при РДС и сварочную проволоку:
Масса наплавленного металла рассчитывается по формуле:
Ссв пр=10×15×110=1650 руб.
Затраты на флюс рассчитывается по формуле:
Ссв= Спр+Сфлюса =1650+680=2330 руб.
Затраты на защитный газ рассчитывается по формуле:
где Цг - цена на м³ газовой смеси К-2 руб (принимаем Цг=600);
Vг - объем необходимого газа.
Объем необходимого газа рассчитывается по формуле:
Затраты на технологическую электроэнергию определяются по формуле:
где qэ – удельный расход электроэнергии на 1 кг наплавленного металла кВт×чкг;
Цэ – цена 1 кВт×ч электроэнергии для предприятий
Удельный расход электроэнергии при дуговых способах сварки определяется двумя методами
где U – напряжение на дуге В (согласно расчетам Uсв=28 В);
aн – коэффициент наплавки гА×ч (aн=95).
hустРДС – КПД источника питания для ручной дуговой сварки покрытыми электродами (принимаем 07);
При автоматической сварке:
где hуст – КПД сварочной установки (принимается равным 085);
Vсв – скорость сварки (Vсв=10 мч);
Wд – мощность сварочной дуги (определяется по режиму).
СЭ1=40×42×423=711 руб.
СЭ2=14×611×423=3612 руб.
СЭ=711+3612=4323руб.
Расходы по содержанию и эксплуатации оборудования включают амортизационные отчисления Са затраты на текущий ремонт и обслуживание оборудования Со и прочие расходы Спр :
Амортизационные отчисления определяются по формуле:
hзi – коэффициент загрузки оборудования (принять 08).
Затраты на текущий ремонт и обслуживание оборудования можно принять в размере 20% от стоимости оборудования тогда:
Со=02×3980000=796000 руб.
Прочие расходы связанные с содержанием и эксплуатацией оборудования как правило составляют 6– 7 % от всех предыдущих затрат т.е.:
Спрч=007(1963+1020000)=71534 руб.
Соб = Са+Со+Спр=1963+1020000+71534=1093497 руб.
Расходы на оснастку и инструмент целевого назначения в сварном производстве составляют 12–15 % от стоимости производственного оборудования участка Фоб:
Сос=015×3980000=597500 руб.
Определим технологическую себестоимость сварочных работ:
Ст=(См+Ссв+Сэ+Сзп)N+Соб+Сос
Ст= (179550+8861+4323+26663)30+1093497+765000=8440407руб.
Таблица 5.3 – Сравнение вариантов
Затраты на основные материалы
Затраты на сварочные материалы
Затраты на технологическую электроэнергию
Основная и дополнительная заработная плата
В зависимости от объема выполняемых сборочно-сварочных работ числа работающих а также производственной площади различают сборочно-сварочный цех отделение или участок.
В зависимости от массы сварочных узлов годового выпуска их (тыс. шт.) указанные подразделения сварочного производства могут быть мелкосерийным и единичным серийным и крупносерийным.
По указанным признакам проектируемый участок (годовая программа 2000шт. изделий; масса изделия 2048 кг.) сборки и сварки резервуара можно отнести к массовому производству.
Расчет площади сборочно-сварочного участка производим по укрупненным нормам в соответствии с рекомендациями.
Площадь участка по своему назначению подразделяется на производственную вспомогательную и служебно-бытовую. Под общей площадью участка в расчетах понимают сумму производственной и вспомогательной площадей.
Производственной называют площадь участков непосредственно предназначенных для осуществления технологического процесса.
В состав производственной площади включают площади занимаемые:
– производственными оборудованием – установками для сборки и сварки печами и местами рабочих у оборудования;
– рабочими местами ручного труда и верстаками;
– шкафами для инструмента;
– складскими площадками для деталей узлов;
– рабочими местами у оборудования для технического контроля деталей узлов (кроме площади выгороженных помещений ОТК).
– проходами и проездами между станками установками и тому подобное (кроме магистральных проездов).
К вспомогательной площади относят:
- площади занятые участками для ремонта оборудования и оснастки мастерские для ремонта приспособлений мастерская энергетика;
- площади участков для дежурных электромонтеров слесарей;
- выгороженные помещения для службы ОТК;
- помещения для трансформаторных подстанций вентиляционных камер;
- площади магистральных проездов;
- складскую площадь и кладовые для хранения и выдачи основных и вспомогательных материалов.
На бытовой площади участка размещаются конторские помещения.
К конторской относят площадь занятую административно-конторскими службами участка: кабинетами начальника его заместителей и др руководящими работниками помещениями отдела технического контроля технического бюро бухгалтерами и др 8.
К бытовой относят площадь помещений предназначенных для обслуживания санитарно-технических и социально-бытовых нужд работников участка: гардеробы туалеты умывальники душевые и т.п.
Допускаемые расстояния между элементами зданий оборудования (рабочим местам) и местами складирования показаны в таблице 6.1.
Таблица 6.1- Допускаемые расстояния между элементами
От колон до: боковой стороны оборудования
Тыльной стороны оборудования
От фронта оборудования до места складирования
Между тыльной стороной оборудования и местом складирования
Между боковой стороной оборудования и местом складирования
Обоснованно выбраны способы сварки формы разделок кромок сварочные материалы.
Выбраны параметры режима сварки позволяющие обеспечить высокую технологическую прочность сварных соединений.
Показано что разработанная технология изготовления может быть реализована с использованием современного существующего оборудования для сборки и сварки. Произведен обоснованный выбор оборудования соответствующий требованиям сварочного производства.
Разработан план участка сборки и сварки резервуара на основе норм технологического проектирования сварочных цехов и норм и правил БЖД обеспечивающий максимально возможную степень загрузки оборудования и использования производственных площадей. На участке обеспечено прямоточное безвозвратное движение грузопотока.
Марочник сталей и сплавов. Под ред. В.Г. Сорокина. - М.: Машиностроение 1989 г. – 640 с.
ОСТ 26-291-94. Сосуды и аппараты стальные сварные. Общие технические условия. Москва: НПО ОБТ 1994 г.
ГОСТ 2246-70. Проволока стальная сварочная. Технические условия. - М.: Издательство стандартов 1983.
Петров Г.Л. Тумарев А.С. Теория сварочных процессов. Учебник для вузов. – М.: Высшая школа 1977.
Волченко В.Н. Контроль качества сварных конструкций. Учебник для техникумов. – М.: Машиностроение 1986. – 512 с ил.
Браткова О.Н. Источники питания сварочной дуги. Учебник для ВУЗов. – М.: Высшая школа 1982. – 182 с. ил.
Гитлевич А.Д. Этингоф Л.А. Механизация и автоматизация сварочного производства. М.: Машиностроение 1979. - 280 с.
Нормы технологического проектирования сварочных цехов
Сосуды и аппараты стальные сварные. ГОСТ Р52630-2006.
Содержание.doc
1 Назначение конструкция и условия работы резервуара. 5
2 Описание конструкции 5
3 Выбор конструкционного материала 5
3.1 Выбор основных материалов 5
3.2 Оценка свариваемости .. 5
КОНСТРУКТИВНАЯ ДОРАБОТКА РЕЗЕРВУАРА
1 Расчет толщины стенки днища .7
2 Расчет толщины стенки обечайки .8
ТЕХНОЛОГИЯ ИЗГОТОВЛЕНИЯ РЕЗЕРВУАРА
1 Технологический процесс изготовления обечаек.. .. .10
2 Технологический процесс изготовления днищ 11
3 Сборка-сварка днищ с обечайкой и фланцами ..11
4 Приварка патрубков к корпусу резервуара 12
5 Обоснование выбора способов сварки 12
6 Выбор сварочных материалов .14
7 Расчет параметров режимов сварки АСФ РДС фланцев .16
ОБОРУДОВАНИЕ ДЛЯ СБОРКИ И СВАРКИ
1 Оборудование для па 22
2 Оборудование для РДС . 23
3 Оборудование для АСФ . ..24
1 Исходные данные для расчета .. 28
2 Нормирование сварочных работ на участке 28
3 Планово-экономические расчеты участка 32
4 Расчет фондов заработной платы участка 33
5 Определение себестоимости изделий ..35
РАСЧЕТ УЧАСТКА .. 41
СПИСОК ЛИТЕРАТУРЫ 44
Рекомендуемые чертежи
- 04.11.2022
- 13.06.2021
- 09.12.2016
- 09.12.2016