Проектирование технологического процесса механической обработки корпуса редуктора




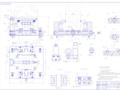
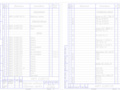
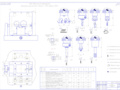
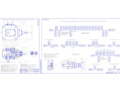
- Добавлен: 25.10.2022
- Размер: 7 MB
- Закачек: 0
Описание
Состав проекта
![]() |
![]() |
![]() ![]() ![]() ![]() |
![]() ![]() ![]() ![]() |
![]() ![]() ![]() ![]() |
![]() ![]() ![]() ![]() |
![]() ![]() ![]() ![]() |
![]() ![]() ![]() ![]() |
![]() ![]() ![]() |
![]() ![]() ![]() |
![]() ![]() ![]() |
![]() ![]() ![]() |
![]() ![]() ![]() |
![]() ![]() ![]() |
![]() ![]() ![]() |
![]() |
![]() ![]() |
![]() ![]() |
![]() ![]() |
![]() ![]() |
![]() ![]() |
![]() ![]() |
![]() ![]() ![]() |
![]() ![]() ![]() |
![]() ![]() ![]() |
Дополнительная информация
Наладка для 005 Операции.dwg

Установить. снять деталь
с образованием фаски 1
размеры на плоскости
Центровать 10 отв. выдерживая размеры
Фрезеровать резьбу М8-7Н
выдерживая размеры на плоскости
5 Сверлильно-фрезерная
Фрезерно-расточной станок с ЧПУ модели 500V
- Вспомогательный ход по оси Х
- Вспомогательный ход по оси Y
- Вспомогательный ход по оси Z
- Включение вращение шпинделя
- Обработка по контуру
- Остановка вращения шпинделя
10-00.dwg

Отливка 3-ой группы ГОСТ 977-88.
Точность отливки 10-5-14-11
точность необрабатываемых
стенок и рёбер 14 ГОСТ 26645-85. Расположение допусков
Неуказанные литейные радиусы скруглений 5 15 мм.
Прибыльные остатки удалить заподлицо с основной
шероховатость мест удаления
Маслопроницаемость корпуса редуктора не допускается
проверить методом керосиновой пробы.
*Размеры для справок.
Покрытие внутренних необработанных поверхностей Эмаль
НЦ-5123 красно-коричневая (2 слоя) ГОСТ 7462-73.
Формовочные уклоны по ГОСТ 3212-92.
Внутренние механически необрабатываемые поверхности
очистить по технологии предприятия-изготовителя
обеспечивающей вторую степень очистки поверхности по
00-00CБ.dwg

Обеспечить осевой люфт дет. поз. 9 в пределах 0
стопорением дет. поз. 20.
Обеспечить боковой зазор конической зубчатой передачи в
мм за счет пригонки дет. поз. 16 и 17.
Обеспечить осевой люфт дет. поз. 11 в пределах 0
счет пригонки дет. поз. 16 и 17.
Обеспечить осевой люфт дет. поз. 12 в пределах 0
счет пригонки дет. поз. 18 и 19..
и 15 ставить на герметике У-30М или УТ-31 ГОСТ
Проверить на герметичность полости редуктора гидравлическим
давлением масляного столба (масло ТАП-15В ГОСТ 23652-79)
высотой 2м с выдержкой 1 час. Течь не допускается.
В полость редуктора залить масло ТАП-15В с добавлением
10% концентрата присадки КП-2 ТУ 38-1019-80.
Обеспечить боковой зазор
конической зубчатой передачи
мм и осевой люфт дет.
Обеспечить пригонкой
Смазать тонким слоем смазкой ЦИАТИМ201
кольцо поз. 49 и место
установки: канавку сапуна поз. 3
Установить уплотнительное кольцо
Завинтить болт поз.72
Редуктор конвейера SM130K.M37D002821-00-00А
Схема сборки редуктора конвейера SM130K.M37D002821-00-00А
Вал-шестерня в сборе
Маслоуказатель в сборе
Схема узловой сборки СБ 1
Схема узловой сборки СБ 2
Схема узловой сборки СБ 3
Схема узловой сборки СБ 6
Схема узловой сборки СБ 7
Схема узловой сборки СБ 5
Схема узловой сборки СБ 4
Наладка для 015 Операции.dwg

Фрезерно расточной станок с ЧПУ модели 650Н
Фрезеровать карман 1 в размер 19
выдерживая размеры 82
с образованием радиусов R45
Фрезеровать четыре уступа 2 в размер 19
с образованием радиуса R25
Установить. снять деталь
Сверлить 10 отв. пр
размеры на плоскости 169
Центровать 14 отв. выдерживая размеры 24
Фрезеровать резьбу М8-7Н
Фрезеровать 2 отв. в размер
Фрезеровать 2 фаски 2
Фрезеровать карман 1 в размер 165
Фрезеровать четыре уступа 2 в размер 165
с образованием фаски 1
выдерживая размеры на плоскости24
выдерживая размеры 38
Фрезеровать плоскость 1 по
Центровать 4 отв. по
и 4 отв. выдерживая размеры 4
Фрезеровать резьбу М12-7Н
размеры на плоскости
Фрезеровать отв. в размер
00-00 Спецификация.dwg

Кольца ГОСТ 18829-73
Подшипники ГОСТ 333-59
Шпонки ГОСТ 23360-78
Приспособление для 005 Операции.dwg

Техническая характеристика
Усилие зажима 20000
Технические требоваия
* Размеры для справок.
Рзмеры для аттестации и поверки.
Испытать на функционирование путем врашения винта
движение сухорей и рычагов должно быть плавным без рывков и
Маркировать шрифтом 5-Пр3 ГОСТ 26008-85.
Маркировать массу М=93 кг шрифтом 10-Пр3 ГОСТ 26008-85
красная ГОСТ 8292-85.
Остальные ТТ по ОСТ 92-3829-89.
2. Формулировка проектной задачи.doc
1 Наименование и область применения разработки
Тема представленного курсового проекта «Проектирование технологического процесса механической обработки корпуса редуктора M37D002821-10-00» в условиях среднесерийного производства.
2 Основание для разработки
Основанием для разработки данного курсового проекта послужило то обстоятельство что в условиях рыночной экономики от внедрения технологических процессов требуется прогрессивность повышенная производительность при изготовлении выпускаемого изделия повышение качества выпускаемого изделия. Кроме того требуется разработка технологических процессов в кратчайшие сроки что не может быть достигнуто без применения ЭВМ.
Внедрение новых технологий покупка нового оборудования приводят к значительным материальным затратам. Но повышение качества выпускаемого изделия приводит к увеличению конкурентоспособности предприятия на рынке сбыта продукции что в свою очередь в дальнейшем приводит к повышению прибыли.
3 Цель проектирования
Целью проектирования является разработка технологического процесса механической обработки корпуса в условиях среднесерийного производства в котором должны быть устранены все недостатки выявленные в процессе анализа базового технологического процесса с применением оборудования соответствующего типу производства. Разрабатываемый технологический процесс должен обеспечить требуемую по чертежу точность изготовления при минимальной себестоимости изготовления изделия.
Технологический процесс – это последовательное изменение формы и размеров свойств материала или полуфабриката в целях получения детали или изделия в соответствии с заданными техническими требованиями.
Одной из главных задач при проектировании нового технологического процесса является оптимальный выбор оборудования в соответствии с годовой программой выпуска заготовки обеспечивающей при минимальных затратах на ее изготовление минимальный объем механической обработки.
4 Источники разработки
Источниками для разработки данного курсового проекта являются:
Действующий технологический процесс;
Методические указания по выполнению курсового проекта;
Паспортные данные металлорежущего оборудования;
Справочные издания по технологии машиностроения проектированию технологической оснастки и металлорежущего инструмента список которых приложен в конце расчётно-пояснительной записки разработанного курсового процесса.
5 Введение.doc
Технический процесс в машиностроении характеризуется разработанной
оптимальной конструкцией машины и совершенствованием технологии их производства. Сейчас важно качественно и дешево в короткие сроки с минимальными затратами изготовить машину применив наиболее прогрессивную технологию. От технологии производства во многом зависят долговечность и надежность выпускаемых машин. Совершенство конструкции машин характеризуется ее соответствием современному уровню техники экономичностью эксплуатации а так же тем в какой мере учтены возможности использования наиболее экономичных и производительных технологий ее изготовления применительно к данным условиям производства. Весьма актуальна проблема повышения и технологического обеспечения точности в машиностроении.
Актуальность курсового проекта заключается в улучшении существующего технологического процесса уменьшения времени на механическую обработку увеличении коэффициента использования материала и загрузки оборудования.
При разработке курсового проекта решаются следующие задачи: отработка конструкции изделия и детали на технологичность выбор средств технологического оснащения нормирование технологических механосборочных процессов разработка технологических операций сборки выбор рационального способа получения заготовки определение баз составление технологического маршрута обработки детали расчет припусков и режимов резания расчет потребного количества оборудования и коэффициентов его загрузки конструирование приспособления на операцию оценка экономической эффективности разработанного и базового технологических процессов.
1. Аналитическая часть.doc
1Служебное назначение и технические характеристики корпуса M37D002821-10-00А.
Корпус редуктора M37D002821-10-00А служит для размещения и координации деталей передачи защиты их от загрязнения организации системы смазки а также восприятия сил возникающих в зацеплении зубчатых колесных парах подшипниках открытой передачи.
РедукторM37D002821-00-00А.
Редуктор служит для передачи крутящего момента от электродвигателя к звездочке скребкового конвейера. Этот редуктор является частью привода проходческого комбайна применяемого в горно-шахтной промышленности. Также редуктор применяется для привода ведущего барабана ленточных конвейеров типа ПЛК800 ПЛШ800 ПЛШ600 изготавливаемых на предприятии.
Детали представляют собой отливки из легированной стали 12ДН2ФЛ ГОСТ 977-88.
Химический состав 12ДН2ФЛ ГОСТ 977-88:
Физико-механические свойства 12ДН2ФЛ ГОСТ 977-88:
Плотность р [кгм³] 786*10³;
Линейная усадка [%]12;
Модуль упругости при растяжении Е [МПа] (850 1100)*10;
Удельная теплоемкость C от 20 до 200°C [Дж]480;
Коэффициент линейного расширения
от 20 до 200 °C [1°C] 95*10-6 ;
Теплопроводность при 20°C [Вт] 54;
Временное сопротивление при растяжении [МПа]650;
Твёрдость HB 170..229.
2Производственная программа выпуска. Определение типа производства.
Для каждого типа производства характерны свои маршруты изготовления деталей. Поэтому прежде чем приступить к проектированию технологического процесса механической обработки детали необходимо исходя из заданной производственной программы и характера надлежащей обработки детали установить тип производства и соответствующую ему форму организации выполнения технологического процесса.
По заданию на курсовой проект устанавливаем тип производства – среднесерийное. После разработки технологического процесса механической обработки и числа основного оборудования тип производства подлежит уточнению по коэффициенту закрепления операций (ГОСТ 14.004-83).
где: ПО – количество операции в технологическом маршруте;
С – расчетное количество рабочих мест необходимых для выполнения годовой программы;
Fd – действительный годовой фонд времени работы оборудования час;
N – годовая программа шт.;
Тшт.к. – среднее штучно-калькуляционное время выполнения операции.
В таблице 1.1 представлена годовая производственная программа выпуска корпуса. M37D002821-00-00
Таблица 1.1 Годовая программа выпуска
Характеристика модель
Число изделий на программу
Процент на запасные части
На годовую программу
Согласно табл. 4 [1] при массе обрабатываемой заготовки 60 кг годовая программа выпуска деталей 5000
Рассчитываем размер партии запуска:
гдеN–годовая программа выпуска изделия;
F=252–число рабочих дней в году;
а=361224-периодичность запуска в днях.
3 Анализ базового технологического процесса
Технологический процесс механической обработки корпуса таблица 1.2
Технологический маршрут обработки корпуса КПЮ-50.04.10.000 имеет следующий вид:
5 Фрезерная. Продольно-фрезерный станок модели 6620.
0 Слесарная. Верстак.
0 Фрезерная. Вертикально-фрезерный станок с крестовым столом
5 Слесарная. Верстак..
0 Фрезерная. Фрезерно-расточной станок модели 2Н637.
5 Слесарная. Верстак.
0 Расточная. Горизонтально-расточной станок KCU 1501 CNC 840D фирмы UNION.
5 Вертикально-фрезерный станок с крестовым столом
5 Расточная. Горизонтально-расточной станок KCU 1501 CNC 840D фирмы UNION.
5 Контрольная. Плита контрольная.№
Болты планки подкладки
Тиски 7827–0332 ГОСТ 4045–75;
Напильник 2820–0018 ГОСТ 1465–80;
СТП 406-1451-79 Сверло 2243 СТП 406–1001–73;
ЩЦ–125–01 ГОСТ 166–80;
ЩЦ–250–0005 ГОСТ 166–80;
Пробка 2243+030 100–1609;
Тиски 7827–0332 ГОСТ 4045–75; Вороток 20 СТП 406–2522–80;
Метчик М24х15 2620–17193 ГОСТ 3266–80;
Пробка ПР М24х15–6Н 8221–0082 ГОСТ 17756–72;
Пробка НЕ М24х15–7Н 8221–1082 ГОСТ 17757–72;
Пробка Двн. М24х15–7Н СТП 406–4307–82;
KCU 1501 CNC 840D фирмы UNION.
Резец 20х20х80 СТП 406–1043–75;
Сверло 22 СТП 406–1001–73;
Сверло 40 СТП 406–1001–73;
Сверло 60 СТП 406–1001–73;
Оправка 6039–0008 ГОСТ 2682–86
Башмак при станке 220-392.
Штангенглубиномер ШГ 250 ГОСТ 162–80;
Пробка 206Н12 СТП 406–4307–82;
Пробка 176Н12 СТП 406–4307–82;
Пробка 160 СТП 406–4307–82;
Пробка 136Н12 СТП 406–4307–82;
Резец 16х16х60 СТП 406–1043–75;
Резец 25х25х170 СТП 406–1043–75;
Пробка 2097+01 СТП 406–4307–82;
Пробка 1797+01 СТП 406–4307–82;
Пробка 1397+01 СТП 406–4307–82;
Пробка 1197+01 СТП 406–4307–82;
Пробка 1297+01 СТП 406–4307–82;
Пробка 1497+01 СТП 406–4307–82;
Микрометрическая расточная головка TRM 6363 2шт. Планка PS 1230 4шт.
Фреза ВК8 СТП 406-1451-79
Микрометрическая расточная головка TRM 8080 2шт. Планка PS 1140 2шт.
Микрометрическая расточная головка TRM 80125 2шт.
Державка DIN69871-AD+B50 MHD’63150 2шт.
Удлинитель PR 63125 2шт.
Удлинитель PR 80 160 2шт
Пробка 210Н9 СТП 406–4307–82;
Пробка 180Н7 СТП 406–4307–82;
Пробка 140Н7 СТП 406–4307–82;
Пробка 120Н7 СТП 406–4307–82;
Пробка 130Н7 СТП 406–4307–82;
Пробка 150Н7 СТП 406–4307–82;
Калибр перпендикулярности 152–2748;
Сверло ø102 покупное (при станке)
Зенковка 20 ГОСТ 14953-80
Сверло ø14 покупное (при станке)
Сверло ø18 ГОСТ 10903-77
Сверло ø175 ГОСТ 10903-77.
Метчик М12 покупной (при станке)
Метчик М16 покупной (при станке)
Метчик М20 покупной (при станке)
Патрон сверлильный покупной (при станке)
Патрон резьбонарезной покупной (при станке)
Втулка Морзе 2222-630
Пробка ПР М12–7Н 8221–0082 ГОСТ 17756–72;
Пробка НЕ М12–7Н 8221–1082 ГОСТ 17757–72;
Пробка Двн. М12–7Н СТП 406–4307–82;
Пробка ПР М16–7Н 8221–0082 ГОСТ 17756–72;
Пробка НЕ М16–7Н 8221–1082 ГОСТ 17757–72;
Пробка Двн. М16–7Н СТП 406–4307–82;
Пробка ПР М20–7Н 8221–0082 ГОСТ 17756–72;
Пробка НЕ М20–7Н 8221–1082 ГОСТ 17757–72;
Пробка Двн. М20–7Н СТП 406–4307–82;
Нутромер НИ 18–50 ГОСТ 868–72;
Метчик М12 покупной (при станке)
Сверло ø22 ГОСТ 10903-77
Пробка 22+052 СТП 406–4307–82;
Очки О ГОСТ 12.4.013-85
Образцы шероховатости
Операционные эскизы базового технологического процесса
Операция 005 Фрезерная
Операция 015 Фрезерная
Операция 025 Фрезерная
Операция 035 Разметочная
Операция 040 Фрезерная
Операция 050 Фрезерная
Маршрут обработки детали пооперационный разработан для мелкосерийного производства. В ходе проектирования его необходимо частично изменить. Существующие оборудование и технологическая оснастка соответствуют мелкосерийному типу производства. Для среднесерийного типа производства необходимо оборудование имеющее высокую производительность обеспечивающее необходимую точность и качество поверхностей и соответствующая типу производства технологическая оснастка позволяющая механизировать процессы установки и закрепления заготовок уменьшить вспомогательное время. По ходу выполнения курсовой работы необходимо разработать свой технологический процесс механической обработки детали на основе базового.
Титульный и задание.doc
Государственное образовательное учреждение высшего профессионального образования
ТОМСКОГО ПОЛИТЕХНИЧЕСКОГО УНИВЕРСИТЕТА
Кафедра Технологии машиностроения
по дисциплине технология машиностроения
Тема: Разработка технологического процесса механической обработки корпуса M37D002821-10-00
гр. В-10340 (подпись) (И.О.Фамилия)
(подпись) (И.О.Фамилия)
ФЕДЕРАЛЬНОЕ АГЕНТСТВО ПО ОБРАЗОВАНИЮ
на выполнение курсового проекта
Студенту VI курса группы В-10340 Садовскому М.В.
Тема курсового проекта «Разработка технологического процесса механической обработки корпуса M37D002821-10-00»
Исходные данные к проекту:
Чертеж корпуса M37D002821-10-00
Базовый технологический процесс механической обработки корпуса M37D002821-10-00
Содержание пояснительной записки
ФОРМУЛИРОВКА ПРОЕКТНОЙ ЗАДАЧИ
ТЕХНОЛОГИЧЕСКАЯ ЧАСТЬ
КОНСТРУКТОРСКАЯ ЧАСТЬ
ОРГАНИЗАЦИОННАЯ ЧАСТЬ
КВАЛИМЕТРИЧЕСКАЯ ОЦЕНКА
Перечень графического материала
Рабочий чертеж детали
Общий вид станочного приспособления
5 Организационная частиь.doc
1 Определение необходимого количества оборудования и коэффициентов его загрузки
Расчетное количество станков для обработки годовой программы деталей определяется по формуле[13]:
где Ср – расчётное количество станков данного типа шт;
Fд – действительный годовой фонд времени работы оборудования час:
где Fн – номинальный годовой фонд времени работы оборудования час;
Кн =097– коэффициент учитывающий потери времени при ремонте оборудования.
Коэффициент загрузки оборудования:
где СП – принятое число станков.
Результаты расчёта приведены в таблице 5.1:
Таблица 5.1- Определение необходимого количества оборудования и коэффициентов его загрузки
Средний коэффициент загрузки Кзо. ср. =6475%.
Коэффициент загрузки оборудования получился небольшим поэтому следует произвести дозагрузку оборудования за счёт изготовления изделий другой номенклатуры. На Рис 5.1 приведён график загрузки оборудования:
Рис.5.1 График загрузки оборудования
2 Определение численности рабочих
Число основных производственных рабочих в серийном производстве можем определить как по общей трудоемкости так и по станкоемкости оборудования:
где С - количество станков.
Принимаем число станочников. На всех операциях принимаем многостаночное обслуживание т.к. коэффициент загрузки оборудования является небольшим:
На операции 005 Р1= 1 чел.;
На операции 015 Р2=1 чел;
Число основных рабочих работающих а одну смену Р=2чел.
Квалиметрическая оценка проекта
В ходе выполнения данного курсового проекта был разработан техпроцесс механической обработки корпуса ФЮРА.340087.001 для среднесерийного производства на основе реально существующего технологического процесса механической обработки данной детали.
При разработке данного техпроцесса был проведен сравнительный анализ способов получения заготовки анализ был проведен по технологической себестоимости заготовки:
При выполнении курсового проекта технологичность изделия была повышена а именно: применен более производительный метод получения заготовки уменьшены припуски на механическую обработку (увеличен Ки.м) более рационально построен маршрут обработки детали для условий мелкосерийного производства с применением более производительного оборудования оснастки и инструмента а также применен метод концентрации операций:
- базовый ТП – 37 операция
- спроектированный ТП – 5 операции
Концентрация операций позволила сократить время на изготовление детали:
- базовый ТП – 3285 мин
- спроектированный 974мин
Для базирования заготовки на сверлильно-фрезерной операции спроектировано самоцентрирующее сверлильно-фрезерное приспособление которое предназначено для фрезерования сверления корпуса на вертикально-фрезерном станке с ЧПУ. Спроектированное приспособление обеспечивает необходимую силу зажима и удовлетворяет требованиям точности.
Ансеров М.А. Гущин В.Ф. Приспособления для сверлильных станков. Конструкции и наладки. – Л.: Машгиз 1950 – 300 с.
Горбацевич А.Ф. Шкред В.А. Курсовое проектирование по технологии машиностроения: Учебное пособие для машиностроительных специальностей ВУЗов. – Минск: Высшая школа 1983. – 256 с.
Добрыднев И. С. Курсовое проектирование по предмету «Технология машиностроения»: Учебн. пособие для техникумов по специальности «Обработка металлов резанием». – М.: Машиностроение 1985. – 184 с.
Маликов Ф.П. Патроны для металлорежущих инструментов. Справочник. – М. Машгиз 1963. – 104 с.
Металлорежущий инструмент. Каталог-справочник. Часть 1. Резцы и фрезы. – М.: Машиностроение 1976. – 448 с.
Металлорежущий инструмент. Каталог-справочник. Часть 3. Резьбообрабатывающий трубо- и муфтообрабатывающий и зуборезный инструмент. – М.: НИИМАШ 1971. – 476 с.
Мягков В.Д Палей М.А. Романов А.Б.. Допуски и посадки: Справочник. В 2-х ч. Ч. 1. – Л.: Машиностроение 1982. – 543 с.
Мягков В.Д. Палей М.А. Романов А.Б.. Допуски и посадки: Справочник. В 2-х ч. Ч. 2. – Л.: Машиностроение 1978. – 545 с.
Общемашиностроительные нормативы времени вспомогательного на обслуживание рабочего места и подготовительно-заключительное для технического нормирования станочных работ. Серийное производство. – М.: Машиностроение 1974. – 422 с.
Общемашиностроительные нормативы времени и режимов резания для нормирования работ выполняемых на универсальных и многоцелевых станках с ЧПУ. Часть 1. Нормативы времени. – М.: Экономика 1990. – 208 с.
Общемашиностроительные нормативы режимов резания для технического нормирования работ на металлорежущих станках. В 3-х частях. Часть 1. Токарные сверлильные станки.– М.: Машиностроение 1974. – 416 с.
Общемашиностроительные нормативы режимов резания для технического нормирования работ на металлорежущих станках. В 3-х частях. Часть 2. Зуборезные горизонтально-расточные резьбонакатные и отрезные станки. – М.: Машиностроение 1974. – 200 с.
Справочник технолога-машиностроителя. В 2-х т. Т. 1 Под ред. А.Г.Косиловой и Р.К.Мещерякова. – М.: Машиностроение 1986. – 656 с.
Справочник технолога-машиностроителя. В 2-х т. Т. 2 Под ред. А.Г.Косиловой и Р.К.Мещерякова. – М.: Машиностроение 1985. – 596 с.
Станочные приспособления: Справочник в 2-х томах. Т. 1 под общ ред. Б.Н.Вардашкина. – М.: Машиностроение 1984. – 592 с.
Станочные приспособления: Справочник в 2-х томах. Т. 2 под общ ред. Б.Н.Вардашкина. – М.: Машиностроение 1984. – 656 с.
Технология машиностроения: Методические указания по выполнению курсового проекта для студентов специальности 120100 «Технология машиностроения» дневной и вечерней формы обучения. – Юрга: ИПЛ ЮФ ТПУ 1999. – 39 с.
3.Технологическая часть.doc
1 Анализ технологичности детали
Технологичность по ГОСТ 18831-73 рассматривается как совокупность свойств конструкции изделия проявляемых в возможности оптимальных затрат труда средств материалов времени при технологической подготовке производства изготовлении эксплуатации и ремонте по сравнению с соответствующими показателями однотипных конструкций изделий того же назначения при обеспечении установленных значений показателей качества в принятых условиях изготовления эксплуатации и ремонта.
Технологичность конструкции детали обуславливается рациональным выбором исходной заготовки технологичностью формы детали рациональной постановкой размеров назначением оптимальной точности размеров форм и взаимного расположения поверхностей параметров шероховатости и технических требований. Технологичность детали зависит от типа производства выбранного технологического процесса оборудования и оснастки организации производства а также условий работы детали сборочной единицы в изделии и условий ремонта.
Технологичность детали оценивается с точки зрения применения простых инструментов методов обработки доступности поверхности для обработки и измерения удобства и надежности базирования детали при обработке.
Технологичность конструкции оценивается качественно и количественно по ГОСТам 14.201 – 83 и 14.202-83.
1.1 Качественная оценка технологичности.
В качестве заготовки принята отливка. Необходимо пересмотреть способ получения заготовки и выбрать оптимальный для данного типа производства.
- Материал корпуса M37D002821-10-00 позволяет применять высокопроизводительные методы обработки;
- Конструкция корпуса M37D002821-10-00 допускает как обработку плоскостей на проход так и обработку карманов обработку карманов возможно заменить на обработку плоскостей но тогда увеличивается объем лишнего снимаемого металла по этому признаку корпус является технологичным;
- Форма внутренних отверстий позволяет произвести их обработку как с двух сторон так и на проход. По этому признаку корпус технологичен.
- Имеется свободный доступ инструмента к обрабатываем поверхностям По этому признаку корпус технологичен;
- В корпусе имеются только резьбовые глухие отверстия заменять на сквозные их не целесообразно так необходимо будет обеспечивать герметизацию резьбы остальные отверстия сквозные. По этому признаку корпус технологичен;
- Корпус не имеется отверстий и плоскостей расположенных не под прямым углом к плоскости входа инструмента. По этому признаку корпус технологичен;
- В конструкции корпуса имеются достаточные по размером и расстоянию базовые поверхности. По этому признаку корпус технологичен;
- Имеется возможность обработки наружных поверхностей и отверстий в корпусе на станках с ЧПУ с одной установки. По этому признаку корпус технологичен;
- Жесткость корпуса позволяет применить высокопроизводительные режимы резания. По этому признаку корпус технологичен;
- Размеры на чертеже поставлены рационально от торца корпуса до оси отверстий. Шероховатость технические требование и погрешность механической обработки обоснованы служебным назначением и технические характеристики корпуса M37D002821-10-00.
По качественным показателям деталь технологична.
1.1 Анализ технологичности конструкции изделия SM130K.M37D002821-00-00А СБ.
Конструкция редуктора позволяет производить его сборку из предварительно собранных узлов.
Возможно осуществление параллельной сборки одновременное и независимое присоединение составных частей.
Возможно механизация сборочных работ (применение гайковертов).
Крепление производится болтами не предусмотрено применение сварки и склеивания.
Конструкция изделия не представляет сложность при захвате и транспортировке.
На основании выше изложенного можно сказать что конструкция изделия в целом технологична и что сборку можно производить высокопроизводительным оборудованием а также произвести её автоматизацию.
1.2 Схема сборки изделия
Составляем схему сборки изделия при этом стремимся разбивать технологический процесс на большее количество узловых сборок. При составлении схемы учитываем удобство соединения изделий и возможности механизации сборки.
1.3 Выбор гайковерта
Для выбора находим момент затяжки гайки.
где φ – угол трения в резьбе град;
– угол подъёма винтовой линии град;
d2 – средний диаметр резьбы d2=10863 мм;
D1 – диаметр вписанной окружности шестигранника головки гайки мм;
d1 – внутренний диаметр резьбы d1= 10106 мм;
f – коэффициент трения в резьбе;
F – усилие прилагаемое к гайке.
Из условия прочности гайки:
Болт с резьбой М12 параметры выбираем [10].
Для затяжки болта М12 выбираем электрическую резьбозавёртывающую машину (гайковерт) ИЭ – 3121.
2 Выбор заготовки и метода ее изготовления
Одно из основных направлений современной технологии машиностроения – совершенствование заготовительных процессов с целью снижения припусков на механическую обработку снижение количества операций окончательной обработки а в ряде случаев полного исключения некоторых из них т.е. обеспечение малоотходной и безотходной технологии.
Метод получения заготовок в значительной мере определяется размерами программного задания и техническими возможностями заготовительных цехов предприятия материалом детали назначением и техническими требованиями на изготовление формой поверхности и размерами.
Выбор метода заготовки существенно зависит от времени подготовки технологической оснастки наличия соответствующего технологического оборудования и желаемой степени автоматизации процесса.
Следует иметь в виду что себестоимость изготовления детали определяется суммой затрат на исходную заготовку и её механическую обработку поэтому в конечном счёте важно обеспечить снижение всей суммы а не одной её составляющих. Метод получения заготовок для деталей машин определяется назначением и конструкцией детали материалом серийностью производства а также экономичностью изготовления.
Исходя из необходимости максимального приближения формы и размеров заготовки к параметрам готовой детали следует (приближать) применять прогрессивные методы и способы получения заготовок.
По своей конфигурации корпус является сложной деталью а материал сталь 12ДН2ФЛ ГОСТ 977-88 обладает хорошими литейными свойствами. В связи с этим проведём технико-экономический расчет вариантов изготовления заготовок полученных:
a.литьем в песчано-глинистые сырые формы из низковлажных (до 28%) высокопрочных (более 160 кПа) смесей с высоким и однородным уплотнением до твердости не ниже 90 единиц;
b.литье в вакуумно-пленочные песчаные формы.
2.1 Расчет заготовки получаемой литьем в песчано-глинистые сырые формы из низковлажных (до 28%) высокопрочных (более 160 кПа) смесей с высоким и однородным уплотнением до твердости не ниже 90 единиц.
По ГОСТ 26645-85 “Отливки из металлов и сплавов”. Номинальный размер отливки следует принимать равным номинальному размеру детали для необрабатываемых поверхностей и сумме среднего размера детали и общего припуска на обработку – для обрабатываемых поверхностей. При определении номинальных размеров отливок учитывают технологические напуски. Номинальную массу отливки следует принимать равной массе отливки с номинальными размерами.
Нормы точности устанавливают на отливку в целом её отдельные поверхности и размеры. Точность отливки в целом характеризуют классом размерной точности отливки степенью коробления степенью точности поверхности и классом точности поверхности и классом точности массы.
Общие припуски на механическую обработку регламентируются ГОСТ 1855-75 и их размеры зависят от класса точности литья наибольшего габаритного размера отливки положения рассматриваемой поверхности в форме при заливке металла.
Под номинальным размером понимают наибольшее расстояние между противоположными обрабатываемыми поверхностями или расстояние между базовой поверхностью и осью обрабатываемого отверстия.
Определение размеров заготовки и их допусков производят суммируя размеры детали и припуски на механическую обработку:
Для наружных поверхностей:
Для внутренних поверхностей:
Материал – сталь 12ДН2ФЛ ГОСТ 977-88;
Класс размерной точности – 10;
Степень коробления элементов отливки – 5;
Степень точности поверхности – 14;
Шероховатость поверхности отливки – Ra 32;
Класс точности массы отливки – 11;
Масса детали – 58 кг.
Таблица 3.1Допуски формы и общие допуски
Таблица 3.2 Основной припуск
Таблица 3.3 Размеры детали и отливки
С помощью ПК рассчитываем массу заготовки.
Определяем коэффициент использования материала и себестоимость:
где mД – масса детали кг;
mз.факт – фактическая масса заготовки кг;
Сзаг= 82 руб – стоимость 1 кг стали 12ДН2ФЛ ГОСТ 977-88.
руб – стоимость срезания 1 кг стружки стали 12ДН2ФЛ при механической обработке в среднем по машиностроению.
Полученные данные сводим в таблицу 3.7.
2.2 Расчет заготовки получаемой литьем в вакуумно-пленочные песчаные формы
Класс размерной точности –12;
Степень коробления элементов отливки – 7;
Степень точности поверхности – 13;
Класс точности массы отливки – 13;
Таблица 3.4Допуски формы и общие допуски
Таблица 3.5 Основной припуск
Таблица 3.6 Размеры детали и отливки
mП.факт – фактическая масса поковки кг;
Сзаг= 78 руб – стоимость 1 кг стали 12ДН2ФЛ ГОСТ 977-88.
Методы получения заготовок
Фактическая масса заготовки mП.факт кг
Стоимость 1 кг материала заготовки Сзаг руб
Коэффициент использования материала КИМ
Стоимость заготовки SТ руб.
2.3 Оценка экономической эффективности заготовки
Таким образом для изготовления детали принимаем отливку полученную литьем в песчано-глинистые сырые формы т.к. она экономически более выгодна чем отливка полученная литье в вакуумно-пленочные песчаные формы. Примерную экономическую прибыль от получения отливки выбранного способа получения определяем по формуле:
где N=5250– годовая программа выпуска.
3 Составление технологического маршрута обработки
На основе анализа базового технологического процесса изготовления корпуса разрабатываем проектный технологический процесс.
Таблица 3.8 Технологический маршрут обработки детали
Наименование и содержание операции
Сверлильно-фрезерная
Фрезеровать поверхность выдерживая размер 312-1;
Центровать 10 отв. выдерживая размеры 78 156 73 146 196 с образование 6+05 на плоскости;
Сверлить 8 отв. под резьбу 685 на глубину 20+3 с образованием фаски 16х450 выдерживая размеры на плоскости 78 156 73 и 146
Фрезеровать резьбу М8-7Н 8 мест;
Сверлить 2 отв. 138Н11 выдерживая размеры 146 196;
Зенковать 2 фаски 11х450
Развернуть 2 отверстия 14Н9 на глубину 15+1
Станок фрезерно-расточный с ЧПУ модели 500V
Сверлильно-фрезерно-расточная с ЧПУ
Фрезеровать карман 1 в размер 195-025 выдерживая размеры 82-05 13+05 198+1 150+1 с образованием радиусов R45+2;
Фрезеровать четыре уступа 2 в размер 195±03 выдерживая размер 2-05 265-05 198-05 49+05 с образованием радиуса
Центровать 14 отв. выдерживая размеры 245±02 27±02 250 265 1695±02 192±02 11 415 84 157 168 110 70 с образование 6+05 на плоскости;
Сверлить 8 отв. под резьбу 685 на глубину 20+3 с образованием фаски 16х450 выдерживая размеры на плоскости 1695±02 192±02 11 415 84 157 168 110 70
Фрезеровать резьбу М8-7Н 10 отверстий;
Сверлить 4 отв. 18+027 выдерживая размеры 245±02 27±02 250 265;
Фрезеровать 2 отв. в размер 709+019 889+019 выдерживая размеры 38±02 157±05 90±002;
Фрезеровать 2 фаски 26х450 выдерживая размеры 38±02 157±05 90±002;
Станок фрезерно-расточный с ЧПУ модели 650Н
Поворот стола на 900
Фрезеровать плоскость 1 по 268+1 в размер 55±02;
Центровать 4 отв. по 150 и 4 отв. выдерживая размеры 45±02 77±02 155 160
с образование 6+05 на плоскости;
Сверлить 8 отв. под резьбу 103 на глубину 20+3 с образованием фаски 16х450 выдерживая размеры 155 160 150 450;
Фрезеровать резьбу М12-7Н 8 отверстий;
Фрезеровать отв. в размер 1189+019 выдерживая размеры 955±02 157±001;
Фрезеровать фаску 26х450 выдерживая размеры 955±02 157±001;
Расточить отв. 1196+0087 предварительно;
Расточить отв. 120+0035 окончательно;
Центровать 14 отв. выдерживая размеры 245±02 27±02 250 265 1695±02 192±02 11 415 84 157 168 110 70 с образование;
Фрезеровать 2 фаски 26х450 выдерживая размеры 38±02 157±05 90±002;
Центровать 14 отв. 8Н14 выдерживая размеры 12± 1 50 105 210 237 80 220 360 500 640 128 256 384 512 640 717 187 и отв. выдерживая размеры 145 и 15+2;
Сверлить 15 отв. 102Н14 на глубину 25+21
Расточить отв. 716+0087 предварительно;
Расточить отв. 72+0035 окончательно;
Расточить отв. 896+0087 предварительно;
Расточить отв. 90+0035 окончательно;
Зачистить заусенцы притупить острые кромки;
Маркировать шрифтом 8-ПР3 ГОСТ 26.008-85 на глубину 06 1 мм;
Маркировать индекс изделия и обозначение детали на бирке.
Проверить размеры по чертежу и техпроцессу.
Для получения высокого качества и точности обработки большое значение имеет правильное базирование детали. При базировании детали следует придерживаться трех принципов базирования а именно:
При выборе баз следует иметь в виду что наибольшая точность обработки достигается при условии использования на всех операциях механической обработки одних и тех же базовых поверхностей т.е. при соблюдении принципа постоянства баз.
При чистовой обработке рекомендуется также соблюдать принцип совмещения баз согласно которому в качестве технологических базовых поверхностей используются конструкторские и измерительные базы. При совмещении технологической и измерительной баз погрешность базирования равна нулю.
Базы для окончательной обработки должны иметь наибольшую точность размеров и геометрической формы а также наименьшую шероховатость поверхности. Они не должны деформироваться под действием сил резания зажима и собственной массы.
Кроме того выбранные базы должны обеспечить надежное закрепление детали и наиболее простую конструкцию приспособления.
Операция 005. Сверлильно-фрезерная
Деталь базируется в специальном приспособлении.
Рисунок 3.1 Схема базирования
Операция 015. Сверлильно-фрезерно-расточная
Рисунок 3.2 Схема базирования. Позиция 1
Рисунок 3.3 Схема базирования. Позиция 2
Рисунок 3.4 Схема базирования. Позиция 3
5 Разработка технологических операций
5.1 Выбор оборудования и средств технологического оснащения
Оборудование: Станок фрезерно-расточный с ЧПУ модели 500V (ОАО «Стерлитамак – М.Т.Е.»).
Станок фрезерно-расточный с автоматической сменой инструмента (АСИ) и числовым программным управлением (ЧПУ) модели 500V предназначен для комплексной обработки деталей из различных конструкционных материалов в условиях единичного мелкосерийного и серийного производства. Неподвижный рабочий стол обеспечивает высокую точность обработки. Выполняет операции сверления зенкерования развертывания получистового и чистового растачивания отверстий нарезания резьбы метчиками и фрезами фрезерования.
Размер рабочей поверхности стола мм
Ширина направляющего паза мм
Количество Т-образных пазов мм
Наибольшее расстояние от торца шпинделя до плоскости планшайбы мм
Наибольшая масса обрабатываемой детали кг
Конус шпинделя (DIN 69871)
Пределы частот вращения шпинделя обмин
Номинальный крутящий момент на шпинделе Нм
Наибольшие перемещения по осям мм
- продольное перемещениеX-салазок (Х)
- поперечное перемещениеY-колонны (Y)
- вертикальное перемещение шпиндельной бабки (Z)
Точность позиционирования мм
Диапазон рабочих подач по координатам мммин
Ускоренные хода по всем осям
Инструментальный магазин
Емкость инструментального магазина шт.
Время смены инструмента сек .
Наибольший диаметр инструмента устанавливаемого в магазине[без пропуска гнезд] мм
Наибольшая длина инструмента устанавливаемого в шпинделе станка мм
Наибольшая масса оправки устанавливаемой в магазине кг
Характеристика электрооборудования
Мощность двигателя главного привода кВт
Номинальная частота вращения обмин
Максимальная частота вращения обмин
Суммарная мощность установленных на станке электродвигателей кВт
Прочие характеристики
Габаритные размеры мм
Общая площадь станка в плане кв.м. не более (с учетом открытых дверей шкафа)
Перемещение по осямё
Ось Х- продольное перемещение
Ось Y- поперечное перемещение
Ось Z- вертикальное перемещение шпиндельной бабки
Оборудование: Станок фрезерно-расточный с ЧПУ модели 650H (ОАО «Стерлитамак – М.Т.Е.»).
Станок фрезерно-расточный с автоматической сменой инструмента (АСИ) с автоматической уборкой стружки и числовым программным управлением (ЧПУ) модели 650Н предназначен для комплексной обработки деталей из различных конструкционных материалов с 4-х сторон без переустановки в условиях единичного мелкосерийного и серийного производства. Выполняет операции сверления зенкерования развертывания получистового и чистового растачивания отверстий нарезания резьбы метчиками и фрезами фрезерования.
Размер рабочей поверхности стола мм
Диаметр центрального отверстия мм
Диаметр крепежных отверстий мм
Наибольшая масса обрабатываемой детали кг
Количество фиксируемых отверстий
Количество крепежных отверстий
Наибольшее расстояние от оси шпинделя до плоскости паллетымм
Наибольшее расстояние от торца шпинделя до оси вращения палетымм
Конус шпинделя (DIN 69871)
Наибольший конус в отверстии инструментальной оправки по ГОСТ25557-82
Пределы частот вращения шпинделя обмин
Степень точности конуса шпинделя
Число ступеней частот вращения шпинделя
Регулирование бесступенчатое
Номинальный крутящий момент на шпинделе Нм
Наибольшие перемещения по осям мм не более
- продольное перемещение стола (Х)
- вертикальное перемещение шпиндел.бабки (Y)
- поперечное перемещение колонны ( Z )
Поворот стола (ось В) град.
Наибольшая частота вращения стола (ось B) мин-1
Точность углового положения стола град.
Дискретность задания перемещения мм
Число управляемых осей координат
Наибольшее усилие подачи по координатам Н - X Y Z
Предельные рабочие подачи по осям X Y Z ммин
Число ступеней рабочих подач
Ускоренные хода по осям X Y W ммин
Инструментальный магазин
Емкость инструментального магазина
Время смены инструмента с
Наибольший диаметр инструмента устанавливаемого в магазине [без пропуска гнезд] мм
Наибольшая длина инструмента устанавливаемого в шпинделе станка мм
Наибольшая масса оправки устанавливаемой в магазине кг
Характеристика электрооборудования
Мощность главного привода кВт
Номинальная частота вращения обмин
Перемещение по осям
Ось Х - продольное перемещение стола
Ось Y - вертикальное перемещение шпиндельной бабки
Ось Z - поперечное перемещение колонны
Ось B - поворот стола с вертикальной осью вращения
Приспособления и инструменты:
Оборудование: Станок фрезерно-расточный с ЧПУ модели 500V (ОАО «Стерлитамак – М.Т.Е.»)
Приспособление специальное ФЮРА.340087.040 СБ;
Патрон для насадных фрез A1B05-40 27035 (SANDVIK Coromant);
Фреза R290-080Q27-12H (SANDVIK Coromant);
Высокоточный патрон HydroGr
Цанга393.CG-20 12 52 (SANDVIK Coromant);
Сверло центровочное специальное ;
Патрон цанговый A1B14-40 20070 (SANDVIK Coromant);
Цанга 393.14-20100 (SANDVIK Coromant);
Сверло комбинированное 685 с обработкой фаски под резьбу М8-7Н R841-0685-30-A1A 1220 (SANDVIK Coromant);
Цанга393.CG-20 14 52 (SANDVIK Coromant);
Сверло R840-1400-30-A0A 1220 (SANDVIK Coromant);
Патрон цанговый A1B14-40 16070 (SANDVIK Coromant);
Цанга 393.14-16 0600 (SANDVIK Coromant);
Фреза резьбовая R217.14C060125AK17N 1630 (SANDVIK Coromant);
ШЦ-2-125-01 ГОСТ 166-80;
Калибр-пробка резьбовой М8-7Н
Очки О ГОСТ 12.4.013-85;
Кран-укосина - 05 т.
Операция 010. Слесарная
Оборудование: Верстак;
Тиски 7827–0332 ГОСТ 4045–75;
Напильник 2820–0018 ГОСТ 1465–80;
Очки О ГОСТ 12.4.013-85.
Оборудование: Станок фрезерно-расточный с ЧПУ модели 650H (ОАО «Стерлитамак – М.Т.Е.»);
Приспособление специальное ФЮРА.340087.050 СБ;
Фреза R390-080Q27-11H (SANDVIK Coromant)
Патрон для насадных фрез A1B05-40 22035 (SANDVIK Coromant);
Фреза R290-050Q22-12L (SANDVIK Coromant)
Сверло комбинированное 685 с обработкой фаски под резьбу М8-7Н R841-0685-30-A1A 1220 (SANDVIK Coromant);
Цанга 393.18-20100 (SANDVIK Coromant);
Сверло R840-1800-30-A0A 1220 (SANDVIK Coromant);
Фреза R390-044Q22-51 (SANDVIK Coromant)
Патрон для насадных фрез A1B05-40 22035 (SANDVIK Coromant);
Инструмент для снятия фасок специальный;
Патрон цанговый A1B05-12 20070 (SANDVIK Coromant);
Цанга 393.10-12100 (SANDVIK Coromant);
Сверло комбинированное 103 с обработкой фаски под резьбу М12-7Н R841-1030-30-A1A 1220 (SANDVIK Coromant);
Головка для чернового растачивания BHR MB80-90
Головка для чистового растачивания BHF MB50-50
Головка для чернового растачивания BHR MB80-60
Калибр-пробка резьбовой М8-7Н;
Калибр-пробка резьбовой М12-7Н;
Калибр перпендикулярности;
Операция 020. Слесарная
5.2 Расчет припусков
Расчет припусков на обработку обуславливает оптимальные промежуточные размеры от заготовки до готовой детали минимальное число технологических переходов рациональный выбор установочных баз и методов обработки.
Для наиболее точной и важной поверхности расчет припусков проведем аналитическим способом.
Рассмотрим данный метод на расчете размера детали: 90Н7 Ra 16:
Качество поверхности отливки:
Отклонение расположения поверхностей отливки:
Расположение отверстия относительно технологической базы – 05 12 мм;
От параллельности плоскости на 1 мм – 42 54 мкм;
Перекос отверстия на 1мм – 3 10 мкм.
Точность и качество поверхности после механической обработки:
Обдирочное фрезерование по контуру:
Получистовом точение:
где мкм – смещение стержня в горизонтальной или вертикальной плоскости.
где L=40 мм – длина знака отливки;
- коробление на 1 мм;
При обдирочном фрезеровании по контуру:
где Ку=008 – коэффициент уточнения;
При получистовом точении:
где Ку=006 – коэффициент уточнения;
При чистовом точении:
где: Ку=004 – коэффициент уточнения;
На основе проведенных расчетов производим расчет минимальных значений межоперационных припусков пользуясь основной формулой:
На обдирочное фрезерование по контуру:
На получистовое точение:
На чистовое точение:
Определяем минимальный расчетный размер:
Чистовое точение (размер m
Получистовое точение: мм;
Обдирочное фрезерование :
Получистовое точение
5.3 Расчет режимов резания
Расчет режимов резания представлен в таблице 3.10.
4.3 Расчет режимов резания
Переход 1: Фрезеровать плоскость с обеспечением размера на проход.
Инструмент: Фреза R290-080Q27-12H (SANDVIK Coromant) D=80 z=8.
Материал режущей части твердый сплав с покрытием 4030.
Черновое фрезерование
Глубина фрезерования:t = 25 мм;
Ширина фрезерования:В = 40 мм;
Диаметр фрезы: D = 80 мм.
Подача на один зуб фрезы:
Сv = 332; q = 02; y = 04; u = 02; p = 0; m = 02;
T = 180 мин. – период стойкости инструмента;
Общий поправочный коэффициент на скорость резания учитывающий фактические условия резания:
где – коэффициент на обрабатываемый материал; (22)
– коэффициент учитывающий состояние поверхности заготовки;
– коэффициент на инструментальный материал;
Следуя рекомендациям производителя инструмента при принятых режимах резания скорость резания должна составлять 180-205ммин следовательно принимаем скорость резания V=195 ммин
Принимаем ncт = 780 обмин.
Cp = 825; y = 075; u = 11; q = 13; w = 02
z = 8 – число зубьев фрезы.
Проверка на достаточность привода станка:
где Nшп – мощность привода станка;
Nшп=Nст×h Nст=7 кВт h=09 – КПД привода;(28)
Sм = Sz z nст = 01 8 780 = 624 мммин.(29)
Lр.х = Lрез + Lвр + Lпер(31)
Lвр + Lпер=85+85=170
Lр.х = 170 + 302*3(прохода)*2(раза) = 1982 мм.
Переход 2: Центровать 10 отверстий.
Инструмент: центровочное сверло 8; Р6М5.
Глубина резания: t = 3 мм.
Подача: S = 015 ммоб
Скорость резания: Vтабл. = 29 ммин
V = VтаблКмv·КlvКuv = 24·10·10·10= 29 ммин
Кмv – коэффициент зависящий от обрабатываемого материала;
Кuv – коэффициент учитывающий марку инструмента.
Частота вращения шпинделя:
Принимаем частоту вращения шпинделя станка (с учетом уменьшения числа переключений частоты вращения): nст = 780обмин.
Sм = S nст = 015 780 = 117 мммин.
Действительная скорость резания:
Мощность резания: Nе = 1кВт
где L = l+l1 – длина обработки
Для 10-ти отверстий: Т0=004·10=04 мин.
Переход 5: Сверлить 2 отверстия 138+036 .
Инструмент: сверло 138; твердый справ с покрытием 1220.
Глубина резания: t=05D=05·138=69мм.
Скорость резания: Vтабл. = 70ммин
V = VтаблКмv·КlvКuv = 70·10·10·10= 70 ммин
Принимаем частоту вращения шпинделя станка nст = 1600 обмин.
Sм = S nст = 021600 = 320 мммин.
Мощность резания: Nе = 18 кВт
Переход 7: Развернуть 2 отверстия 14Н9 .
Инструмент: Развертка 14; Р6М5.
Глубина резания: t=05=05=01 мм.
Подача: Sтабл. = 09ммоб
Коs = 07 – поправочный коэффициент на достижение более высокого качества;
S = Sтабл.Коs = 0907 = 063ммоб
где Т=30мин – период стойкости развертки
Cv = 105; q = 03; y = 065; m = 04; х = 02;
Принимаем частоту вращения станка nст = 305 обмин.
Sм = Snст = 063 305 = 192 мммин.
где L=l+l1 – длина обработки
Переход 27: Расточить отв. 7160087 предварительно
Инструмент: Головка для чернового растачивания BHR MB80-8
Получистовое точение:
Глубина точения:t=05=05=035 мм;
Сv = 420; y = 02; m = 02;
Следуя рекомендациям производителя инструмента при принятых режимах резания скорость резания должна составлять 130-170ммин следовательно принимаем скорость резания V=150 ммин
Принимаем ncт = 680 обмин.
Cp =300; y = 075; n =-015
Nшп=Nст×h Nст=11 кВт h=09 – КПД привода;(28)
Sм = Sz z nст = 02 2 680 = 272 мммин.(29)
Lр.х = 185 + 10 = 195 мм.
Переход 28: Расточить отв. 720035 окончательно.
Инструмент: Головка для чистового растачивания BHF MB50-58
Глубина точения: t=05=05=02 мм;
Sм = Sz z nст = 01 680 =68 мммин.(29)
Расчет режимов резания для операции 005 сводим в таблицу 3.10
Расчет режимов резания для операции 015 сводим в таблицы 3.11 3.12 3.13
Для 015 операции позиция 2
5.4 Нормирование технологического процесса
где ТШТ-К – штучно-калькуляционное время выполнения работ на станках мин;
ТШТ – норма штучного времени мин;
ТП-З – норма подготовительно-заключительного времени мин.
где ТО – основное время на обработку одной детали мин;
ТВ – вспомогательное время мин;
КtВ – поправочный коэффициент вспомогательного времени;
АОБС – время на обслуживание рабочего места %;
АОТД – время на отдых и личные надобности %.
где ТВУ – время на установку и снятие детали мин;
ТВ.ПЕР – время связанное с переходом мин;
ТВ.ИЗМ – время на измерение мин.
где ТП-З1 – время на организационную подготовку мин;
ТП-З2 – время на наладку станка мин;
ТП-З.ОБР – нормы времени на пробную обработку мин.
Штучное время для станков ЧПУ:
где ТПУ – время цикла автоматической работы станка по программе мин.
где ТО – основное технологическое время на обработку одной детали мин.
ТМВ – машинно-вспомогательное время по программе мин.
Результаты нормирования времени приведены в таблице 3.11.
Таблица 3.11 Нормирование технологического процесса
Вспомогательное время:
Время связанное операцией
- время на установку и снятия детали
- время связанное с операцией
- время на измерения
- машинно-вспомогательное время по программе
смена инструмента подвод детали время технологических пауз изменение режимов.
Коэффициент вспомогательного времени
Суммарное вспомогательное время
Время технического организационного обслуживания рабочего места и на отдых и личные надобности
Подготовительно-заключительное время
- организационная подготовка
- установить приспособление и снять
-переместить стол в позицию удобную для наладки
-установить инструментальные блоки
-установить программоноситель в считывающее устройство и снять
-ввести программу в память системы ЧПУ
-установить исходные координаты
-произвести пробную обработку
Время цикла автоматической работы станка по программе
Штучно-калькуляционное время
Сверлильно-фрезерная-расточная
Содержание.doc
1Служебное назначение и технические характеристики
корпуса M37D002821-10-00А5
2 Производственная программа выпуска. Определение
3 Анализ базового технологического процесса7
ФОРМУЛИРОВКА ПРОЕКТНОЙ ЗАДАЧИ23
ТЕХНОЛОГИЧЕСКАЯ ЧАСТЬ26
1 Анализ технологичности детали27
2 Выбор заготовки и метода ее изготовления30
3 Составление технологического маршрута обработки36
5 Разработка технологических операций46
КОНСТРУКТОРСКАЯ ЧАСТЬ72
1 Проектирование фрезерно-сверлильного приспособления на станок 500V73
ОРГАНИЗАЦИОННАЯ ЧАСТЬ91
1 Расчёт потребного количества оборудования и коэффициентов его загрузки92
2 Определение численности рабочих работающих на участке93
КВАЛИМЕТРИЧЕСКАЯ ОЦЕНКА94
Доклад.doc
Чертеж детали представлен на первом листе графической части. Корпус изготавливается из Стали 12ДН2ФЛ. основные поверхности в корпусе это 2 отверстия под подшипники 1 отверстие под стакан с жестким допуском на круглость параллельность и перпендикулярность между ними.
В аналитической части производился анализ различных методов получения заготовки. Анализ показал что наиболее оптимальным вариантом получения заготовки для рассматриваемой детали в условии среднесерийного производства является литьем в песчано-глинистые сырые формы . Чертеж заготовки совмещен с чертежом детали.
В технологической части был разработан технологический процесс обработки корпуса.
5 операция Сверлильно-фрезерная представлена на 2 листе графической части (показать лист). Операция выполняется на фрезерно-расточном станке 500V. Деталь базируется в специальном самоцентрирующем приспособлении. Базирование корпуса в приспособлении производится по плоскости двум прижимным рычагам и упору. Обрабатываются плоскость резьбовые отверстия и два технологических отверстия диметром 14Н9 предназначенные для бозирования корпуса на последующей операции (показать).
0 операция слесарная в графической части не представлена.
5 операция представлена на 3-5 листе графической части (показать лист). Операция выполняется на станке модели 650Н. Деталь базируется в специальном приспособлении по плоскости двум пальцам цилиндрическому и срезанному закрепление осуществляется при помощи прижима. Заготовка обрабатывается за 3 позиции.
позиция: обрабатывается плоскость под крышку 4 уступа4 крепежных отверстия и 10 резьбовых отверстий а также черновое фрезерование отверстий под подшипники (показать);
позиция: производится поворот стола на 90 градусов – обрабатывается плоскость и отверстие под стакан и переходной кожух 8 резьбовых отверстий фаска;
позиция: производится поворот стола на 90 градусов – обрабатывается плоскость под крышку 4 уступа4 крепежных отверстий и 10 резьбовых отверстий а также черновое фрезерование получистовое и чистовое растачивание отверстий под подшипники (показать).
0 операция слесарная.
В конструкторской части выпускной квалификационной работы спроектированы приспособления на 005.
Базирование детали в приспособлении производится по плоскости двум прижимным рычагам и упору. Три точки несёт главная базирующая плоскость выполненная в виде четырех опор две из которых являются плавающими самоустанавливающими две точки образованы самоцентрирующими рычагами одна точка – упором. Заготовка фиксируется двумя рычагами. Для базирования и закрепления приспособления на столе станка предусмотрены четыре специальные втулки.
Приспособление состоит из литого корпуса. В нем установлен винт с правой и левой резьбой гайки рычаг. Винт от осевого перемещения фиксирует шайба поз. 9 шайба в свою очередь фиксируется шплинтом. Также в корпус устанавливается две постоянные опоры и две самоустанавливающие опоры. Зажим детали производится вручную путем затяжки винта. Был произведен силовой расчет и расчет приспособления на точность приспособления. Заданная точность обработки на данном приспособлении обеспечивается.
Корпус редуктора M37D002821-10-00А является базовой деталью редуктора конвейера служит для размещения и координации деталей передачи защиты их от загрязнения организации системы смазки а также восприятия сил возникающих в зацеплении зубчатых колесных парах подшипниках открытой передачи.
РедукторM37D002821-00-00А.
Редуктор служит для передачи крутящего момента от электродвигателя к звездочке скребкового конвейера. Этот редуктор является частью привода скребкового конвейера проходческого комбайна применяемого в горно-шахтной промышленности. Также редуктор применяется для привода ведущего барабана ленточных конвейеров типа ПЛК800 ПЛШ800 ПЛШ600 изготавливаемых на предприятии.
Для редуктора был разработан технологический процесс сборки конструкция изделия позволяет производить его сборку из предварительно собранных узлов схемы узловых сборок представлены также представлены 2 позиции сборочного процесса 1 одевания резинового кольца на сапун завинчивание болта.
В организационной части произведен расчет потребного количества оборудования коэффициентов его загрузки. Расчет необходимой численности основных рабочих.
При разработки технологического процесса максимально увеличена концентрация операций применены специальные приспособления выбрано современное оборудование это позволило сократить количество операций с 37 до 5 применение современного инструмент с СМП позволило применять обработки с интерполяцией что сократило площадь обрабатываемых поверхностей и номенклатуру инструмента все это позволяет обеспечит большую производительность и меньшую себестоимость изделия по сравнению с базовым технологическим процессом.
Спасибо за внимание доклад окончен
4. Конструкторская часть.doc
1 Проектирование фрезерно-сверлильного приспособления на фрезерно-расточный станок с ЧПУ модели 500V (ОАО «Стерлитамак – М.Т.Е.»).
Приспособление предназначено для закрепления заготовки при обработке на сверлильно-фрезерном станке 500V.
Базирование детали в приспособлении производится по плоскости двум прижимным рычагам и упору. Три точки несёт главная базирующая плоскость выполненная в виде четырех опор две из которых являются плавающими самоустанавливающими две точки образованы самоцентрирующими рычагами одна точка – упором. Заготовка фиксируется двумя рычагами. Для базирования и закрепления приспособления на столе станка предусмотрены четыре специальные втулки.
Приспособление состоит из литого корпуса с установленным на нем опорными и зажимными элементами. Зажим детали производится вручную путем затяжки винта.
Рисунок 4.1 Расчетная схема
Сила резания Pv направлена в сторону опор. Этой силе препятствует сила трения возникающая в местах закрепления Qf где Q-сила зажима винтового прижима f-коэффициент трения.
Из расчета режимов резания максимальной является составляющая окружной силы возникающая при фрезеровании поверхности Pv=085Pz .
Для упрощения расчета примем допущения что:
По [9 Т2 с.80] определяем коэффициент трения f=08.
Коэффициент запаса определяется по формуле:
К = К0К1К2К3К4К5К6(4.2)
где К0 – коэффициент гарантированного запаса К0 = 15
К1 = 12 - коэффициент неровностей;
К2 = 16 – характеризует Рz;
К3 = 12 – характеризует постоянство Рз;
К4 = 13 – т. к. зажим ручной;
К5 = 12 – т. к. приспособление ручное;
К6 = 15 поправочный коэффициент.
К=15·12·16·12·13·12·15=612
Определим требуемую силу зажима:
Рисунок 4.2 Расчетная схема усилия зажима
Усилие зажима изделия передаваемое рычагами составляет:
Отсюда необходимое усилие передаваемое винтом равно:
Усилие создаваемое гайкой спроектированным приспособлением равно:
где dср – средний диаметр резьбы;
α – угол подъёма резьбы
φпр – приведённый коэффициент трения для заданного профиля резьбы (4.5)
– половина угла при вершине профиля витка резьбы.
Для треугольной резьбы (ГОСТ 9150–59) =30.
Длина гаечного ключа L=450мм.
Максимально допустимая сила зажима на рукоятке для приспособлений с ручным зажимом 250Н следовательно ручной зажим для данного приспособления может быть применён и приспособление обеспечивает необходимое усилие зажима.
2 Расчет приспособления на точность
Для определения точности спроектированного приспособления необходимо суммировать все составляющие погрешности влияющие на точность приспособления.
где К – коэффициент учитывающий возможность отступления от нормального распределения отдельных составляющих К = 12;
К1 – принимается если присутствует погрешность базирования К1= 1; б – погрешность базирования:
погрешность базирование равна зазору между центрирующей шайбой и корпусом приспособления 0021+0041=0062
з – погрешность закрепления принимаем по [16 с. 82] з = 002;
уст – погрешность установки приспособления на станке уст = 002;
п – погрешность смещения режущего инструмента п = 0 т. к. отсутствуют направляющие элементы приспособления;
изн – погрешность возникающая в результате износа составных частей изн = 004;
Δу – погрешность возникающая в результате упругих деформаций;
Δи – погрешность вызываемая размерным износом инструмента;
Δн – погрешность возникающая в результате настройки станка;
ΣΔф – погрешность возникающая в результате геометрической неточности станка;
Δт – погрешность возникающая в результате температурных деформаций.
Составляющие Δу Δи Δн ΣΔф Δт рассчитываются затруднительно но известно что их влияние на точность приспособления невелико поэтому в расчёте их учитывать не будем.
Заданная точность обработки на данном приспособлении обеспечивается.
Приложение выбор инструмента.docx
Фреза R290-080Q27-12H (SANDVIK Coromant);
Высокоточный патрон HydroGr
Цанга393.CG-20 12 52 (SANDVIK Coromant);
Сверло R840-1090-30-A0A 1220 (SANDVIK Coromant);
Патрон цанговый A1B14-40 20070 (SANDVIK Coromant);
Цанга 393.14-20100 (SANDVIK Coromant);
Сверло комбинированное 685 с обработкой фаски под резьбу М8-7Н R841-0685-30-A1A 1220 (SANDVIK Coromant);
Цанга393.CG-20 14 52 (SANDVIK Coromant);
Сверло R840-1400-30-A0A 1220 (SANDVIK Coromant);
Патрон цанговый A1B14-40 16070 (SANDVIK Coromant);
Цанга 393.14-16 0600 (SANDVIK Coromant);
Фреза резьбовая R217.14C060125AK17N 1630 (SANDVIK Coromant);
Рекомендуемые чертежи
- 24.01.2023
- 30.08.2014
- 23.04.2016
- 09.04.2021
- 24.01.2023
- 05.01.2022
- 20.12.2021