Проект плавильного отделения со складом шихтовых материалов



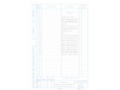
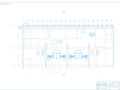
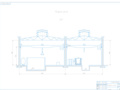
- Добавлен: 25.10.2022
- Размер: 937 KB
- Закачек: 1
Описание
Состав проекта
![]() |
![]() |
![]() ![]() ![]() ![]() |
![]() ![]() ![]() |
![]() ![]() ![]() |
![]() ![]() ![]() |
![]() |
![]() ![]() ![]() ![]() |
![]() |
![]() |
![]() ![]() ![]() ![]() |
![]() ![]() ![]() |
Дополнительная информация
спецификация.cdw

со складом шихтовых материалов
стенд для подогрева раздаточных ковшей
стенд для сушки и подогрева разливочных ковшей
индукционная тигельная печь
закром с молотым кварцевым песком
трансформатор промышленной частоты
закром с бентонитовыми глинами
закром с ломом чушковым М2
площадка с чушковым литейным чугуном Л2
закром с ломомом стальным 1А
площадка с чушковым литейным чугуном Л5
закром с отходами собственного производства
закрома с ферросплавами
общецеховая железная дорога
РПЗ.docx
Расчет годовой потребности цеха в литейном сплаве 4
Составление баланса металла и расчет количества плавильных печей 5
Выбор плавильного агрегата 7
Описание технологического процесса приготовления сплавов 9
Расчет оптимальной емкости ковша .13
Расчет полезной площади складов шихтовых материалов .16
Список использованных источников 21
Литейное производство является одной из основных заготовительных баз машиностроения. Широкое распространение литейного производства объясняется большими его преимуществами по сравнению с другими способами производства заготовок (ковка штамповка):
возможностью получения деталей с заданными физико-механическими свойствами;
универсальностью и экономичностью методов формообразования сложных металлических изделий
максимальным приближением отливок по конфигурации и размерам к готовой детали;
снижением цикла изготовления;
отходы в стружку при изготовлении специальными способами литья сведены до минимума;
изготовлением деталей из сплавов которые трудно поддаются механической обработке;
безвозвратные потери у отливок составляют 7 – 9 % у деталей из сварных соединений около 11 – 12 % у поковок 13 – 14.
Примерно около 70 % (по массе) заготовок получают литьем а в некоторых отраслях машиностроения например в станкостроении 90 – 95 %. Литьем можно получить заготовки практически любой сложности с минимальными припусками на механическую обработку. Это очень важное преимущество так как сокращение затрат на обработку резанием снижает себестоимость изделий и уменьшает расход металла. Кроме того производство литых заготовок значительно дешевле чем например производство поковок.
В последнее время большое развитие получили специальные методы литья. К ним относятся:
литье по выплавляемым моделям;
литье в оболочковые формы;
литье под давлением;
литье под низким давлением;
центробежное литье и т.д.
Отливки получаемые специальными методами литья по конфигурации и размерной точности приближаются к готовым деталям и объем их обработки резанием невелик.
Выход годного литья увеличивается для кокильного литья до 40 – 60 %.
При литье специальными способами увеличивается производительность процесса снижается трудоемкость изготовления деталей возможно получение тонкостенных отливок широко используются средства механизации и автоматизации.
Литье в кокиль является одним из самых экономичных способов литья который нашел широкое применение во многих отраслях промышленности особенно в машиностроении.
Сущность процесса литья в кокиль заключается в заливке жидкого сплава в металлическую форму в которой благодаря высокой теплопроводности материала формы происходит быстрое затвердевание и охлаждение отливки. Металлическая форма применяется многократно и имеет высокую стойкость. С целью регулирования скорости затвердевания отливок рабочие поверхности кокилей облицовывают и окрашивают теплоизоляционными красками. Покрытие наносят также и для защиты формы от воздействия жидкого металла.
Область применения литья в кокиль в значительной степени определяется технологическими возможностями и экономической целесообразностью производства отливок этим способом.
Литье в кокиль дает следующие качественные и количественные преимущества:
повышение физико-механических и эксплуатационных свойств отливок;
увеличение выхода использованного для изготовления отливок металла т.е. отношения массы полученной отливки к залитому в форму расплаву;
повышение размерной точности и качества поверхностей отливок;
уменьшение допусков и припусков на механическую обработку;
частичное или полное исключение формовочных материалов из производства;
увеличение производительности труда и съема отливок с производственной площади;
улучшение санитарно-гигиенических условий труда.
Недостатки литья в кокиль – высокие трудоемкость изготовления и стоимость металлической формы повышенная склонность к возникновению внутренних напряжений в отливке вследствие затрудненной усадки и более узкого по сравнению с литьем в песчаную форму интервала оптимальных режимов литья обеспечивающих получение качественной отливки. [ЦЛ]
Литьем под низким давлением изготавливают отливки подвергаемые испытаниям на герметичность сложной конфигурации с тонкими и толстыми стенками крупногабаритные с несколькими массивными тепловыми узлами.
Основные преимущества литья под низким давлением: большой выход годного (80-98 %) повышенная плотность отливок высокий уровень автоматизации процесса.
Литье под низким давлением состоит в вытеснении газом жидкого металла из раздаточной печи в литейную форму. Помимо принудительного заполнения литейной формы в этом методе литья эффективно используют питание затвердевающей отливки жидким металлом из естественной прибыли – металлопровода.
В целом цехи специальные виды литья: ЛНД ЛПД литье в кокиль являются более производительными и экономичными по сравнению с традиционными видами литья (литье в песчаные формы) в этих цехах гораздо выше уровень автоматизации процессов и культура производства.
Исходные данные для проектирования
Согласно заданию на проектирование необходимо спроектировать плавильное отделения со складом шихтовых материалов сталелитейный цех мощностью 12000 тонн литья в год с развесом отливок до 1000 кг.
По характеру производства проектируемый цех относится к цехам с серийным характером производства [1].
В цехе принимаем двухсменный параллельный режим работы.
Для выполнения проектных расчетов принимаем 10 отливок – представителей параметры которых приведены в таблице 1.1.
Расчет цеха выполнен по приведенной программе. Форма приведения – по массе. Исходные данные по проектируемому цеху после приведения к заданной мощности 12000 тонн годного литья представлены в таблице 1.5.
Пояснения к таблице 1.5:
Годовой выпуск в тоннах (т) базового цеха определяется как:
Годовой выпуск = ( вес 1 отливки (т) годовой выпуск (шт)) т.
Переводной коэффициент = мощность проектируемого цеха
Программа проектируемого цеха рассчитана как:
Годовой выпуск отливок (шт) = переводной коэффициент годовой выпуск (шт) базового цеха.
Годовой выпуск отливок (т) = годовой выпуск отливок (шт) проектируемого цеха вес 1 отливки (т).
Расчет годовой потребности цеха в литейном сплаве
В проектируемом цехе предполагается изготавливать отливки из стали марок Ст20 и Ст25 механические свойства которых приведены в таблице 1.3 химический состав чугунов в таблице 1.4
Получение жидкого металла (стали) предполагается в электрических индукционных печах.
Исходные данные для расчета плавильного отделения представлены в таблице 1.5
Брак литья принят равным 3% сливы 1% угар и безвозвратные потери 2%.
Результаты расчета потребности цеха в жидком металле и металлической шихте представлены в таблице
Составление баланса металла и расчет количества
Принятый в цехе среднегодовой состав шихты и ведомость баланса металла представлены в таблице 1.9
Так как в проектируемом цехе предполагается изготавливать отливки из сталей марок Ст20 и Ст25 то в качестве плавильных агрегатов принимаем электрические индукционные печи. Количество печей необходимое для обеспечения формовочного отделения жидким чугуном может быть определено по формуле:
где: - количество вагранок;
- годовая потребность цеха в жидком металле т;
- коэффициент неравномерности работы отделения (10-12) =12 [1];
- действительный годовой фонд времени работы вагранок = 3890 часов [ 1 ];
- производительность вагранок (тчас). = 158тч [ 1 ].
К установке принимаем 4 индукционные печи модели ИЧТ-6 технологические параметры которых представлены в таблице 1.7.
Программа базового цеха
Группа отливок по массе
Наименование отливки
Механические свойства сталей Ст20 и Ст25
Механические свойства
прочности при растяжении
Химический состав сталей Ст20 и Ст25
Исходные данные для расчета потребности цеха в литейных сплавах
Литники и прибыли тонн
Нижняя крышка подшипника
Алгоритм расчета потребности цеха в жидком металле и металлической шихте следующий:
Годное литье = вес 1 отливки(т) годовой выпуск(шт);
Вес ЛПС (т) = вес ЛПС на 1отливку(т) годовой выпуск(шт);
Брак литья(т) = годное литье(т) 3100 где 3 – принятый процент брака;
Сливы(т) = годное литье(т) 1100; где 1 – принятый процент сливов остатков металла из ковша;
Жидкий металл(т) = годное литье(т) + вес ЛПС(т) + брак(т) + сливы(т);
Металлозавалка(т) = жидкий металл(т) 10095; где: 100 – 95 = 5 – это угар плюс безвозвратные потери;
Угар и бв потери(т) = металлозавалка(т) – жидкий металл(т);
% годного литья = годное литье(т) 100металлозавалка(т);
% ЛПС = ЛПС(т) 100 металлозавалка(т);
% брака = брак(т) 100 металлозавалка(т);
% сливов = сливы(т) 100 металлозавалка(т);
Выбор плавильного агрегата
В настоящее время в литейном производстве для плавки стали следующие печи:
пламенные отражательные печи;
индукционные канальные и тигельные печи;
электропечи сопротивления.
Для производства вторичных литейных алюминиевых сплавов применяют пламенные отражательные печи емкостью от 10 до 30 тонн и тигельные индукционные печи емкостью от 25 до 6 тонн. В пламенных отражательных печах имеет место повышенный угар металла низкая производительность и насыщение расплава газами. В результате этих недостатков широкого применения данные печи не находят.
Плавка в индукционных печах вследствие меньшей удельной площади сопровождается меньшей газонасыщенностью расплава меньшей его окисляемостью и более низкими безвозвратными потерями.
В последнее время широкое применение получили индукционные печи промышленной частоты с сердечником. Эти печи имеют низкий удельный расход электроэнергии порядка 305 большую производительность и высокий коэффициент полезного действия (КПД) (до 75%). Однако данные печи имеют ряд существенных недостатков таких как:
зарастание каналов печи окисью алюминия а также флюсами и шлаками;
низкая стойкость футеровки (2-3 месяца).
Свободными от данных недостатков и более удобными в эксплуатации являются тигельные индукционные печи. Индукционный нагрев металла получил в настоящее время широкое распространение. При индукционном нагреве теплота выделяется непосредственно в металле нагреваемом в тигле благодаря чему использование тепла оказывается более совершенным и обеспечивается значительно большая скорость нагрева.
Индукционные тигельные печи промышленной частоты просты по своей конструкции. Они представляют собой тигель помещенный в индуктор питаемый переменным током. После слива каждой плавки можно легко осмотреть и очистить а затем если это необходимо загрузить в него шихту другого по композиции сплава.
Тигельные индукционные печи применяются главным образом для плавки высококачественных сплавов сталей и алюминиевых сплавов требующих особой частоты однородности и точности химического состава. Эти печи имеют ряд несомненных преимуществ перед другими печами. При малом зеркале металла и большой скорости нагрева плавка характеризуется малым угаром (05 – 10 %). Благодаря тому что атмосфера эл.печей не содержит продуктов сгорания топлива возможно получение сплавов со значительно меньшим чем в пламенных печах уровнем загрязнения неметаллическими примесями (водородом и оксидами) и отказаться например в ряде случаев от применения эффективных но дорогостоящих методов дегазации расплава либо при их применении получить особо высокое качество металла. Пониженнаягазонасыщенность дает отливки с высокими механическими свойствами.
Печи дают более высокую производительность (в 2-3 раза по сравнению с пламенными и в 5-6 раз по сравнению с электропечами сопротивления).
Затраты на получение тонны расплава литейных алюминиевых сплавов в индукционных тигельных печах значительно ниже чем в пламенных отражательных печах. Меньший расход энергии обусловлен отсутствием потери тепла из рабочего пространства печи продуктами сгорания топлива. Также необходимо отметить еще несколько преимуществ данных печей:
более легкие условия труда;
простое и широкое регулирование мощности и температуры;
сокращение производственной площади из-за малых габаритов печи;
получение чистого расплава благодаря отсутствию источников загрязнения; поглощение водорода на 40% меньше чем в других печах из-за более совершенных условий нагрева;
стойкость тигля более 6 месяцев.
Основным недостатком индукционных печей по сравнению с канальными печами является повышенный расход электроэнергии.
Хорошо зарекомендовали себя для плавки алюминия и его сплавов печи емкостью до 25 тонн. Такие печи снабжены механизированной крышкой шихту можно загружать как вручную так и механизированным способом например мостовым краном. При непрерывной работе с одним сплавом рекомендуется оставлять на дне тигля определенный переходящий остаток и в него загружать свежую шихту.
Расплавленный металл сливается через сливной носок путем наклона печи гидравлическим приводом.
Описание технологического процесса приготовления сплавов
В первую очередь в плавильную печь загружается порция возврата производства. По мере расплавления возврата в отключенную печь загружаются порции свежих материалов в следующей последовательности: марганец ковшом затем чушки алюминия первичного и силумина. Далее производится расплавление шихты в плавильной печи под крышкой.
С целью снижения потерь металла в шлаке производится его обработка рафинирующим флюсом в следующем порядке:
В отключенную плавильную печь на зеркало сплава ковшом засыпается флюс в количестве не менее 02 % от массы сплава в печи.
Производится выдержка сплава под слоем флюса в течение от 8 до 10 минут.
Флюс замешивается в сплав на глубину шумовки шлак снимается с поверхности сплава шумовкой в шлаковню.
После операции обработки сплава при помощи шумовки вводится в сплав навеска магния печь включается на ступень быстрого нагрева.
Не менее чем через 10 минут после ввода магния заливается образец для анализа химического состава сплава образец передается в спектральную лабораторию. Результат анализа передается на плавильный участок телефонограммой. При необходимости производится действия по корректировке химического состава. Сплав сливается из плавильной печи только при положительном результате анализа.
Затем сплав нагревается в плавильной печи до температуры свыше температуры плавления. Готовый и годный по химическому составу металл сливается в ковш. При технологическом переливе жидкого металла из плавильной печи в ковш а из него в раздаточную печь происходит рафинирование жидким флюсом
Расчет потребности цеха в жидком металле
Основные технические характеристики индукционной печи ИЧТ-6 [1]
Плавильное оборудование
Индукционная тигельная печь
Мощность трансформатора кВ*А
Потребляемая мощность кВт
Производительность тч
Продолжительность плавки на твердой шихте (полный цикл) ч
Рабочая температура °С
Расход охлаждающей воды м3ч
Общий вес печи сжидким металлом т
Для проведения химического анализа выплавляемого металла и контроля за его механическими свойствами предусмотрена экспресс – лаборатория площадью 50м2.
В таблице 1.8 приведен состав шихты для сталей Ст25 и Ст20 и расчет годовой потребности проектируемого цеха в шихтовых материалах
Ведомость шихт и баланса металла
Чугун литейный чушковый Л5
Чугун литейный чушковый Л2
Лом чушковый покупной М2
Лом стальной покупной 1А
Отходы собственного производства
Расчет оптимальной емкости ковша
Вместимость заливочного ковша определяется максимальнойметаллоемкостью формы и может быть равна или кратна ей.
Формы заливаем с помощью поворотного ковша емкостью 2 т.
Число ковшей необходимых для обеспечения металлом данного потока определяется по формуле: [3]
где nк– число ковшей определенной металлоемкости находящихся одновременно в работе шт;
gМе – потребность в металле для заполнения готовых форм из такого ковша тч;
ц.к. – время оборота работающего ковша ч;
gк – металлоемкость ковша используемая для заполнения литейных форм т;
Ккн – коэффициент неравномерности потребления металла ковшом.
Потребность в металле будет определяться производительностью литейной формовочной линии и если в цехе один формовочный поток то она будет равна часовой потребности цеха в металле т. е.
Рассчитываем часовую потребность цеха в металле:
Время оборота ковша складывается из времени заполнения ковша металлом транспортировки его до места заливки времени разливки металла возвращения ковша под новое заполнение слива остатка и ожидания заполнения ковша. Принимаем ц.к.= 02 ч.
Коэффициент неравномерности потребления металла ковшом будет больше чем при расчете количества плавильных печей и его можно брать в пределах 13–17. Принимаем Ккн=14.
Подставляя в формулу (8) найденные значения получим:
Работающий ковш постепенно выходит из строя из-за механического разрушения футеровки носка краев а также разъедания внутренней футеровки металлом и шлаком. Поэтому периодически ковш возвращается на перефутеровку или ремонт.
Число ковшей постоянно находящихся в ремонте в течении года устанавливается формулой: [3]
где nк.р.– число ковшей находящихся в ремонте в течении года шт.;
nк– число ковшей находящихся одновременно в работе шт.;
рем.к.– длительность ремонтного цикла ковша ч;
nр– число ремонтов ковша в год;
Кнк.рем– коэффициент неравномерности поступления ковшей в ремонт;
Фр– фонд рабочего времени ремонтных рабочих ч.
Длительность ремонтного цикла ковша невелика и связана с вместимостью методом восстановления футеровки длительностью сушки и разогрева ковша а также зависит от вида заливаемого сплава. Принимаем рем.к.= 16 ч.[3]
Рабочий цикл ковша от ремонта до ремонта складывается из оборота ковша и числа наливов которые выдерживает его футеровка. Стойкость ковшей для разливки углеродистой стали составляет 05 месяца или 24 ремонта в год. Принимаем nр= 24.
Подставляя в формулу (10) найденные данные находим
Вместимость раздаточного ковша определяется максимальнойметаллоемкостью печи и должна быть ей.
Расплав из печи сливаем в ковш емкостью 6 т.
gк – металлоемкость ковша используемая для заполнения форм т;
Рабочий цикл ковша от ремонта до ремонта складывается из оборота ковша и числа наливов которые выдерживает его футеровка. Стойкость ковшей для разливки углеродистой стали составляет 1 месяц или 12 ремонтов в год. Принимаем nр= 12.
Рассчитана необходимость в двух разливочных ковшах емкостью 2 тонны.и в одном раздаточном ковше емкостью 6 тонн. В ремонте постоянно один разливочный ковш и один раздаточный ковш.
Расчет полезной площади складов шихтовыхматериалов
На складе осуществляется приемка складирование подготовка шихтовых и формовочных материалов огнеупорных изделий флюсов и т.д. При определении площади закромов необходимых для хранения материалов используются данные расчетов плавильного и смесеприготовительного отделений являющихся основными потребителями исходных материалов.
Площадь занимаемую материалом на месте хранения определяют по формуле
где Q – масса соответствующего материала хранимого на складе т;
Н – высота хранения материала м;
– насыпная массы материала тм3;
к – коэффициент использования емкости склада (не более 08).
Данные для расчета площадей хранения по формуле (16) берутся из ведомости расчета площадей складов представленной в табл. 10. также в эту ведомость вносятся рассчитанные площади хранения.
Расчетные площади хранения округляют в соответствии с удобством механизированной загрузки и разгрузки материала.
При определении площади складов учитываются также площади занятые приемными приямками разгрузочными площадками эстакадами приемными устройствами для подачи материалов в цех оборудованием для подготовки материалов а также проходами и проездами.
Общая площадь склада равна
где FМ – сумма округленных площадей хранения каждого материала на складе м2; FЭ – площадь занимаемая эстакадами м2;
FР – площадь разгрузочных площадок м2;
К – коэффициент учитывающий площади занимаемые приемными устройствами для подачи материалов в цех оборудованием для подготовки материалов а также проходами и проездами К =12–14.
Площадь разгрузочных площадок определяется по формуле:
где n – число разгрузочных площадок шт.;
L – протяженность железнодорожного пути находящегося в цехе м;
W – ширина фронта разгрузки по всей протяженности железнодорожного пути (L) W = 6–8 м.
FР = 1·48·6= 288 м2.
Подставляя в формулу найденные значения получим:
При расчете площадей складов руководствуемся следующими положениями:
а) количество материалов поступающих на склад должно равняться расчетным величинам с учетом потерь на складе и при транспортировании в цех – 4%.
б) на складе должен храниться минимальный но обеспечивающий бесперебойную работу цеха запас регламентированный нормами хранения [1].
Карта технологического процесса подготовки шихтовых материалов представлена в таблице 1.
Технологический процесс подготовки шихтовых материалов
Разгрузка шихтовых материалов из вагонов
Мостовой кран с магнитной шайбой
Дробление ферросплавов и известняка на куски массой 3 – 5 кг.
Очистка отходов производства (ЛПС) от формовочной смеси и пригара
Расход с учетом потерь(т) = расход на годовую программу(т) × 100(100- потери на складе(%);
Запас на складе всего(т) = расход с учетом потерь(т) × нормы хранения (сутки)365;
Запас на складе всего(м3) = запас на складе всего(т) объемная масса (тм3 );
Запас на складе в том числе в закромах(т) = запас на складе всего(т) × 09
Запас на складе в том числе в закромах(м3) = Запас на складе в том числе в закромах(т) объемная масса (тм3)
Запас на складе в том числе на площадке(т) = запас на складе всего(т) - запас на складе в том числе в закромах(т);
Потребная площадь закрома(м2) = запас на складе в том числе в закромах(м3) высота хранения(м);
Потребная площадь площадки(м2) = расход с учетом потерь(т) Нагрузка на площадку(тм2).
Таблица 1.10 Расчет площадей складов шихтовых материалов
Наименование материалов
Расход на годовую программу т
Расход с учетом потерь т
Нормы хранения (сутки)
Запас на складе всего
Отходы собственного производства
Огнеупорные материалы
Кварцевый песок молотый
Таблица 1.11 Расчет площадей складов шихтовых материалов (продолжение)
Запас на складе в том числе
Нагрузка на площадку тм2
Потребная площадь м2
Список использованных источников
литейный цех расчет проектирование
Мостовой Н. И. Методические указания к курсовой работе по дисциплине «Проектирование новых и реконструкция действующих литейных цехов» для студентов специальности 100400 – Литейное производство черных и цветных металлов специализация 110405 – Художественное и прецизионное литье (ювелирные изделия). – Хабаровск изд. ХГТУ 2000. – 32 с.
Основы проектирования литейных цехов и заводов Под ред. Б. В. Кнорре. – М.: Машиностроение 1979. – 376 с.
Проектирование машиностроительных цехов и заводов Под ред. В. М. Шестопала. – М. Машиностроение 1977. – 294 с.
Логинов И. З. Проектирование литейных цехов. – Минск: Высш. Школа 1975. – 320 с.
Аксенов П. Н. Оборудование литейных цехов. – М. Машиностроение 1977. – 294 с.
Типаж технологического оборудования для литейного производства на 1981 – 1985 гг. – М.: ВНИИМаш 1980. – 131 с.
План.cdw

Разрез цеха.cdw

спецификация.dwg
со складом шихтовых материалов
стенд для подогрева раздаточных ковшей
стенд для сушки и подогрева разливочных ковшей
индукционная тигельная печь
закром с молотым кварцевым песком
трансформатор промышленной частоты
закром с бентонитовыми глинами
закром с ломом чушковым М2
площадка с чушковым литейным чугуном Л2
закром с ломомом стальным 1А
площадка с чушковым литейным чугуном Л5
закром с отходами собственного производства
закрома с ферросплавами
общецеховая железная дорога
Рекомендуемые чертежи
- 29.07.2014
- 24.10.2015
- 03.07.2014