Привод цепного конвейера




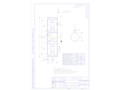
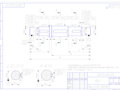
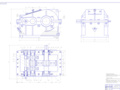
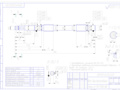
- Добавлен: 25.10.2022
- Размер: 2 MB
- Закачек: 0
Описание
Состав проекта
![]() |
![]() |
![]() ![]() ![]() ![]() |
![]() ![]() ![]() ![]() |
![]() |
![]() ![]() ![]() ![]() |
![]() ![]() ![]() ![]() |
![]() ![]() ![]() ![]() |
![]() ![]() ![]() ![]() |
![]() ![]() ![]() ![]() |
![]() ![]() ![]() ![]() |
![]() ![]() ![]() ![]() |
![]() |
![]() ![]() ![]() |
![]() ![]() ![]() |
![]() ![]() ![]() |
![]() ![]() ![]() |
![]() ![]() ![]() |
![]() ![]() ![]() |
![]() ![]() ![]() |
![]() ![]() ![]() ![]() |
![]() ![]() ![]() ![]() |
![]() ![]() ![]() ![]() |
![]() ![]() ![]() ![]() |
![]() ![]() ![]() ![]() |
![]() |
![]() ![]() ![]() |
Дополнительная информация
эскизная компоновка.cdw

Вал быстроходный.cdw

Нормальный исходный контур
Коэффициент смещения
Степень точности по ГОСТ1643-81
Сталь 45 ГОСТ1050-88
Термообработка- улучшение НВ 220 240.
Неуказанные предельные отклонения размеров: отверстий -
валов - остальных IT142.
Неуказанные радиусы 0
эскизная компоновка.cdw

Вал быстроходный.cdw

Нормальный исходный контур
Коэффициент смещения
Степень точности по ГОСТ1643-81
Сталь 45 ГОСТ1050-88
Термообработка- улучшение НВ 220 240.
Неуказанные предельные отклонения размеров: отверстий -
валов - остальных IT142.
Неуказанные радиусы 0
Спецификация.spw

Кольцо мазеудерживающее
Болт М10х40 ГОСТ7798-70
Болт М12х85 ГОСТ7798-70
Болт М12х100 ГОСТ7798-70
Гайка М10 ГОСТ11871-80
Гайка М12 ГОСТ11871-80
Манжета 1-15-32 ГОСТ8752-79
Манжета 1-32-52 ГОСТ8752-79
Подшипник 203 ГОСТ8338-75
Подшипник 105 ГОСТ8338-75
Подшипник 207 ГОСТ8338-75
Шайба 10 ГОСТ6402-70
Шайба 12 ГОСТ6402-70
Шпонка 5х5х14 ГОСТ23360-78
Шпонка 8х7х28 ГОСТ23360-78
Шпонка 8х7х36 ГОСТ23360-78
Шпонка 10х8х45 ГОСТ23360-78
Шпонка 12х8х40 ГОСТ23360-78
Штифт 10х25 ГОСТ9464-79
Сборочный чертеж редуктора.cdw

Передаточное число редуктора U = 7
Передаваемая мощность Р = 1
вращения быстроходного вала 950 обмин.
Размеры для справок.
Плоскость разъема покрыть герметиком при окончательной
Необработанные поверхности красить - внутри маслостойкой
снаружи - серой нитроэмалью.
В редуктор залить масло индустриальное И-20А ГОСТ 21743-76.
Редуктор обкатать в течение 3 часов.
Вал промежуточный.cdw

Термообработка- улучшение НВ 220 240.
Неуказанные предельные отклонения размеров: отверстий -
валов - остальных IT142.
Крышка подшипника промежуточного вала.cdw

Шестерня тихоходного вала.cdw

Cталь 45 ГОСТ 1050-74
Неуказанные радиусы 1 2 мм.
Термообработка улучшение НВ 200.
Неуказанные предельные отклонения размеров
Сборочный чертеж редуктора.dwg
Передаточное число редуктора U = 7
Передаваемая мощность Р = 1
вращения быстроходного вала 950 обмин.
Размеры для справок.
Плоскость разъема покрыть герметиком при окончательной
Необработанные поверхности красить - внутри маслостойкой
снаружи - серой нитроэмалью.
В редуктор залить масло индустриальное И-20А ГОСТ 21743-76.
Редуктор обкатать в течение 3 часов.
Вал быстроходный.dwg
Нормальный исходный контур
Коэффициент смещения
Степень точности по ГОСТ1643-81
Сталь 45 ГОСТ1050-88
Термообработка- улучшение НВ 220 240.
Неуказанные предельные отклонения размеров: отверстий -
валов - остальных IT142.
Неуказанные радиусы 0
Спецификация.dwg
Кольцо мазеудерживающее
Болт М10х40 ГОСТ7798-70
Болт М12х85 ГОСТ7798-70
Болт М12х100 ГОСТ7798-70
Гайка М10 ГОСТ11871-80
Гайка М12 ГОСТ11871-80
Манжета 1-15-32 ГОСТ8752-79
Манжета 1-32-52 ГОСТ8752-79
Подшипник 203 ГОСТ8338-75
Подшипник 105 ГОСТ8338-75
Подшипник 207 ГОСТ8338-75
Шайба 10 ГОСТ6402-70
Шайба 12 ГОСТ6402-70
Шпонка 5х5х14 ГОСТ23360-78
Шпонка 8х7х28 ГОСТ23360-78
Шпонка 8х7х36 ГОСТ23360-78
Шпонка 10х8х45 ГОСТ23360-78
Шпонка 12х8х40 ГОСТ23360-78
Штифт 10х25 ГОСТ9464-79
Вал промежуточный.dwg
Термообработка- улучшение НВ 220 240.
Неуказанные предельные отклонения размеров: отверстий -
валов - остальных IT142.
Шестерня тихоходного вала.dwg
Cталь 45 ГОСТ 1050-74
Неуказанные радиусы 1 2 мм.
Термообработка улучшение НВ 200.
Неуказанные предельные отклонения размеров
Спецификация.spw

Кольцо мазеудерживающее
Болт М10х40 ГОСТ7798-70
Болт М12х85 ГОСТ7798-70
Болт М12х100 ГОСТ7798-70
Гайка М10 ГОСТ11871-80
Гайка М12 ГОСТ11871-80
Манжета 1-15-32 ГОСТ8752-79
Манжета 1-32-52 ГОСТ8752-79
Подшипник 203 ГОСТ8338-75
Подшипник 105 ГОСТ8338-75
Подшипник 207 ГОСТ8338-75
Шайба 10 ГОСТ6402-70
Шайба 12 ГОСТ6402-70
Шпонка 5х5х14 ГОСТ23360-78
Шпонка 8х7х28 ГОСТ23360-78
Шпонка 8х7х36 ГОСТ23360-78
Шпонка 10х8х45 ГОСТ23360-78
Шпонка 12х8х40 ГОСТ23360-78
Штифт 10х25 ГОСТ9464-79
Сборочный чертеж редуктора.cdw

Передаточное число редуктора U = 7
Передаваемая мощность Р = 1
вращения быстроходного вала 950 обмин.
Размеры для справок.
Плоскость разъема покрыть герметиком при окончательной
Необработанные поверхности красить - внутри маслостойкой
снаружи - серой нитроэмалью.
В редуктор залить масло индустриальное И-20А ГОСТ 21743-76.
Редуктор обкатать в течение 3 часов.
Вал промежуточный.cdw

Термообработка- улучшение НВ 220 240.
Неуказанные предельные отклонения размеров: отверстий -
валов - остальных IT142.
Крышка подшипника промежуточного вала.cdw

Шестерня тихоходного вала.cdw

Cталь 45 ГОСТ 1050-74
Неуказанные радиусы 1 2 мм.
Термообработка улучшение НВ 200.
Неуказанные предельные отклонения размеров
Пояснительная записка.doc
РАСЧЕТ ГРАФИКА НАГРУЗОК6
1. Расчет цилиндрической передачи редуктора (быстроходная ступень)7
2. Расчет цилиндрической передачи редуктора (тихоходная ступень)12
3. Расчет цепной передачи17
ПРЕДВАРИТЕЛЬНЫЙ РАСЧЕТ ВАЛОВ 20
ПРЕДВАРИТЕЛЬНЫЙ ВЫБОР ПОДШИПНИКОВ22
ОПРЕДЕЛЕНИЕ КОНСТРУКТИВНЫХ РАЗМЕРОВ ЗУБЧАТЫХ КОЛЕС
ЗВЕЗДОЧЕК КОРПУСА И КРЫШКИ РЕДУКТОРА22
ЭСКИЗНАЯ КОМПОНОВКА ОСНОВНОГО ВИДА РЕДУКТОРА24
РАСЧЕТ ШПОНОЧНЫХ СОЕДИНЕНИЙ25
ПРОВЕРОЧНЫЙ РАСЧЕТ ПОДШИПНИКОВ 27
ОПРЕДЕЛЕНИЕ ДОЛГОВЕЧНОСТИ ПОДШИПНИКОВ 31
ПРОВЕРОЧНЫЙ РАСЧЕТ ВАЛОВ33
ВЫБОР ПОСАДОК СОПРЯЖЕННЫХ ДЕТАЛЕЙ37
Выбор электродвигателя и кинематический расчет привода
Определим предварительный общий коэффициент полезного действия (КПД) привода конвейера:
где * цепи = 092 – КПД открытой цепной передачи (090..095)
* Т = 097 – КПД тихоходной степени редуктора
* М = 098 – КПД муфты
* П = 099 – КПД одной пары подшипников
* Б = 097 – КПД быстроходной ступени редуктора для цилиндрической
Определим требуемую мощность на валу конвейера:
где =300 Нм-номинальный крутящий момент на выходном валу привода
= = = 523 с-1 – угловая скорость приводного вала
n1 = 50 мин -1 – частота вращения приводного вала
Выбор электродвигателя:
Определим требуемую мощность электродвигателя:
Выбираем тип двигателя с учетом Р ном ³ Рдв
По ГОСТ 19523-74 выбираем двигатель типа 4А100L6УЗ
Рном = 22 кВт – номинальная мощность двигателя
n1 = 950 мин-1 – частота вращения вала двигателя и ведущего вала
dдв = 28 мм – диаметр хвостовика двигателя.
Общее передаточное число конвейера:
Общее передаточное число двухступенчатого цилиндрического редуктора:
Разбивка общего передаточного числа двухступенчатого редуктора:
Передаточное отношение на каждой передаче:
Общее передаточное число редуктора:
Отклонение от ранее принятого значения:
Погрешность меньше 5% следовательно принимаем полученные значения.
Определения частоты вращения валов редуктора:
Определения угловых скоростей валов редуктора:
Определения крутящих моментов на валах редуктора:
промежуточного вала:
Расчет графика нагрузок
При выполнении расчетов зубчатых передач необходимо учесть график нагрузок приведенный в задании.
Интенсивность износа зубьев находится в непосредственной зависимости от сил взаимодействия между зубьями длительности и частоты этих взаимодействий.
Допустимый суммарный износ зубьев в соответствии с требованием задания должен наступить не ранее заданного ресурса (в нашем примере 20000 ч).
Поэтому при расчете зубчатых передач с учетом режима нагрузок вычисляется количество нагружений каждого зуба соответствующей нагрузкой за полное время ресурса. И затем исходя из максимального допустимого износа вычисляется коэффициент концентрации нагрузки KH значение которого учитывается при определении межосевого расстояния зубчатой передачи.
Определение KH производится следующим образом:
Для переменной нагрузки KH определяется по формуле:
где - начальный коэффициент концентрации нагрузки; Х – коэффициент режима нагрузки.
Начальный коэффициент концентрации нагрузки принимаем в зависимости от коэффициента d =b2d1.
Так как ширина колеса b2 и диаметр шестерни d1 еще не определены коэффициент d определяют ориентировочно по формуле:
При ступенчатом графике режима нагружения (см. график нагрузок в задании) коэффициент Х вычисляют по формуле:
где T T – наибольший из числа длительно действующим моментов обычно номинальный; N N=N n2 nз – число зацеплений колеса; ti – время работы передачи (ч) при i-м режиме.
При одинаковом значении n2
где t - время работы передачи ч.
1. Расчет цилиндрической передачи редуктора
Выбираем для колеса и шестерни материал сталь 45 термообработка – улучшение; твердость поверхности зуба шестерни HB230 твердость поверхности зуба колеса HB200.
Допускаемые контактные напряжения:
где – базовый предел контактной выносливости соответствующий базовому числу циклов.
Для стали 45 с термообработкой (улучшением)
– коэффициент долговечности; принимаем ; коэффициент безопасности .
Для косозубых колес расчетное допускаемое контактное напряжение
Тогда расчетное допускаемое контактное напряжение
Требуемое условие выполнено.
Принимаем для косозубых колес коэффициент ширины венца по межосевому расстоянию :.
где kН = 111 – коэффициент учитывающий неравномерность нагрузки по длине контактной линии (зависящий от твердости рабочей поверхности зубьев расположения опор и коэффициента bд)
Межосевое расстояние из условия контактной выносливости активных поверхностей зубьев:
где для косозубых колес Ка=43.
Ближайшее значение межосевого расстояния по ГОСТ 2185-66 .
Нормальный модуль зацепления:
принимаем по ГОСТ 9563-60 .
Примем предварительно угол наклона зубьев и определим числа зубьев шестерни и колеса:
Уточняем передаточное отношение
Отклонение от принятого ранее
Отклонение от ранее принятого значения не должно превышать 4%
Уточненное значение угла наклона зубьев
Основные размеры шестерни и колеса:
диаметры делительные:
Диаметры вершин зубьев:
ширина колеса ; принимаем ;
Определяем коэффициент ширины шестерни по диаметру:
Окружная скорость колес и степень точности передачи
При такой скорости для косозубых колес принимаем 8-ю степень точности.
Коэффициент нагрузки
где11 – коэффициент учитывающий неравномерность распределения
нагрузки между зубьями;
1 – коэффициент учитывающий неравномерность распределения нагруз
ки по длине контактных линий связанную с деформацией валов и самих зубьев
– коэффициент учитывающий динамическую нагрузку возникающую в зацеплении.
Проверка контактных напряжений:
Силы действующие в зацеплении:
Проверяем зубья на выносливость по напряжениям изгиба:
где – коэффициент нагрузки при проверке на изгибную выносливость:
– коэффициент учитывающий неравномерность распределения нагрузки между зубьями зависящий от степени точности изготовления;
4 – коэффициент учитывающий неравномерность распределения нагрузки по длине зубьев;
2 – коэффициент учитывающий динамическую нагрузку возникающую в зацеплении.
- коэффициент учитывающий форму зуба и зависящий от эквивалентного числа зубьев zv:
Согласно ГОСТ 21354-75 принимаем и .
Допускаемое напряжение:
Для стали 45 улучшенной при твердости НВ350 .
Коэффициент запаса прочности . ; для поковок и штамповок . Следовательно .
Допускаемые напряжения:
Для шестерни отношение ;
Определяем коэффициенты и :
Проверяем прочность зуба колеса:
Проверяем прочность зуба шестерни:
Условие прочности выполнено.
2. Расчет цилиндрической передачи редуктора (тихоходная ступень)
Выбираем для колеса и шестерни материал сталь 45 термообработка – улучшение; твердость поверхности зуба шестерни HB300 твердость поверхности зуба колеса HB260.
Принимаем для косозубых колес коэффициент ширины венца по межосевому расстоянию .
Учитывая диаметр выходного вала (см. п.5) принимаем по ГОСТ 2185-66 .
– коэффициент учитывающий динамическую нагрузку возникающую в зацеплении Таким образом .
3.Расчет цепной передачи
Выбираем приводную роликовую однорядную цепь(ПР)(табл. 7.15):
Вращающий момент на ведущей звездочке Т3 =158·103 Н·мм
Передаточное число: = 25
Число зубьев ведущей звездочки:
Число зубьев ведомой звездочки:
Тогда фактическое передаточное число :
Расчетный коэффициент нагрузки:
где kд= 1 - динамический коэффициент при спокойной нагрузке;
ka= 1 - коэффициент учитывающий влияние межосевого расстояния при aц=(30 50) · t;
kн= 1 - коэффициент учитывающий влияние угла наклона линии центров к горизонту при наклоне до 600 kН = 1;
kр = 125 - коэффициент учитывающий способ регулирования натяжения цепи в нашем случае при периодическом регулировании;
Kсм = 1- коэффициент учитывающий способ смазки;
Кп = 1- коэффициент учитывающий периодичность работы передачи в нашем случае - 1 смена.
Для определения шага цепи по формуле 7.38 надо знать допускаемое давление [p] в шарнирах цепи. В таблице 7.18 допускаемое давление [p] задано в зависимости от частоты вращения ведущей звездочки и шага t. Поэтому для расчета по формуле 7.38 величиной [p] следует задаваться ориентировочно. Ведущая звездочка имеет частоту вращения n3=121 обмин. Среднее значение
допускаемого давления примем [p]=28 МПа.
Подбираем по табл. 7.15 цепь ПР-1905-318 по ГОСТ 13568-75 имеющую t=1905 мм; разрушающую нагрузку Q=318 кН; массу q=19 кгм; F=1058 мм2.
Давление в шарнире проверяем по формуле:
Уточняем по табл 7.18 допускаемое давление:
Условие p [p] выполнено : 2573052
Определяем число звеньев цепи по формуле 7.36[9]:
Округляем до четного числа:
Суммарное число зубьев передачи:
Уточняем межосевое расстояние цепной передачи по формуле (7.37):
Принимаем межосевое расстояние:
Для свободного провисания цепи предусматриваем возможность уменьшения межосевого расстояния на 04% то естьпримернона 764x0004=3.мм
Определяем диаметры делительных окружностей звездочек:
Определяем диаметры наружных окружностей звездочек:
где d1 = 1191 мм – диаметр ролика цепи (по таб.7.15)
Силы действующие на цепь:
Окружная: Ft= 2176 Н - определена выше;
где масса одного метра цепи q=19 кгм по табл. 7.15;
От провисания цепи:
где =6 – коэф учитывающий расположение цепи: при горизонтальном расположении цепи =6
Расчетная нагрузка на валы:
Проверяем коэффициент запаса прочности цепи по формуле (7.40) :
Нормативный коэффициент запаса прочности по табл. 7.19: [s]=78; условие прочности n>[n] выполнено.
Толщина диска звездочки: 093 x ВВН = 093 x 1588 = 14768 = 15мм
где ВВН – расстояние между пластинками внутреннего звена (см. табл. 7.15).
Диаметр делительной окружности звёздочек мм:
Межосевое расстояние a мм
Диаметр окружности выступов звёздочек мм:
Сила давления на вал Fв Н
Допускаемые значения
Частота вращения ведущей звёздочки n5 обмин
Коэффициент запаса прочности S
Давление в шарнирах цепи [p] Hмм2
Предварительный расчет валов
Назначение предварительных размеров отдельных участков ведущего вала:
Определим диаметр входного вала:
где = 15 МПа – допускаемое касательное напряжение на кручение.
Принимаем большее значение диаметра входного вала из стандартного ряда.
Согласно ГОСТ 6636-69
Определим диаметр входного вала под подшипники:
Определим диаметр центральной части входного вала:
Определим диаметр промежуточного вала:
Принимаем большее значение диаметра промежуточного вала из стандартного ряда. Согласно ГОСТ 6636-69
Определим диаметр промежуточного вала под подшипники:
Определим диаметр центральной части промежуточного вала:
Определим диаметр выходного вала:
Принимаем большее значение диаметра выходного вала из стандартного ряда. Согласно ГОСТ 6636-69
Определим диаметр выходного вала под подшипники:
Определим диаметр центральной части выходного вала
Типоразмер муфты выбирают по диаметру вала и по величине расчетного вращающего момента (формула 9.1):
где k = 15 – коэффициент учитывающий условия эксплуатации привода
Выбираем флянцевую разнодиаметровую муфту ГОСТ 20761-80
dВХ=20 мм dдв = 22 мм Т= 315 Н*м
D = 90 мм; L = 104 мм; материал – сталь40.
При расчете болтовых соединений муфт следует учитывать что половина общего числа болтов устанавливаются в отверстия без зазора поэтому достаточно только проверить их на срез по условию прочности:
где - окружная сила приходящаяся на один болт;
D1 – диаметр окружности расположения болтов;
z1 – число болтов поставленных без зазора.
Диаметр стержня болта dб = 008· dдв = 008·22=2 мм(М2)
Принимаем большее значение диаметра болта из стандартного ряда.
Так как 12606 МПа160 МПа то условие прочности выполняется.
Предварительный выбор подшипников
Намечаем для опор быстроходного вала - два радиальных шарикоподшипника 105 ГОСТ 8338-75; для опор промежуточного вала – два радиальных шарикоподшипника 107 ГОСТ 8338-75; для опор выходного вала редуктора - два радиальных шарикоподшипника 109 ГОСТ 8338-75.
По каталогу подшипников имеем
Определение конструктивных размеров зубчатых колес звездочек корпуса и крышки редуктора
Цилиндрическая зубчатая передача быстроходной ступени:
Шестерню выполняем за одно целое с валом.
Зубчатое колесо кованое.
Принимаем :; толщина диска: .
Цилиндрическая зубчатая передача тихоходной ступени:
Размеры шестерни: ; .
Зубчатое колесо кованое. Его размеры: ;
=20 мм dдв = 22 мм Т= 315 Н*м
Диаметры делительных окружностей звездочек:;
Диаметры наружных окружностей звездочек:; .
Размеры ведущей звездочки:
Ступица звездочки ; ;
Толщина диска звездочки :.
Толщина стенки корпуса: ;
Толщина стенки крышки редуктора: ;
Толщина верхнего пояса (фланца) корпуса: .
Толщина нижнего пояса (фланца) крышки корпуса: .
Толщина нижнего пояса корпуса: .
Диаметры болтов: фундаментных: принимаем болты с резьбой М16; крепящих крышку к корпусу у подшипников: принимаем болты с резьбой М12; соединяющих крышку с корпусом: принимаем болты с резьбой М10.
Зазор между торцом шестерни с одной стороны и ступицы с другой и внутренней стенкой корпуса А1=12=10 мм.
Зазор от окружности вершин зубьев колеса до внутренней стенки корпуса а также расстояние между наружным кольцом подшипника ведущего вала и внутренней стенкой корпуса А==8 мм.
Эскизная компоновка основного вида редуктора
Первый этап компоновки привода служит для приближённого определения положения зубчатых колес и звёздочек (шкивов) относительно опор для последующего определения опорных реакций и подбора подшипников.
В качестве способа смазывания принимаем картерную смазку.
Вычерчиваем упрощенно шестерни и колеса зубчатых передач в масштабе 1:1 чертим тонкими линиями.
Плоскость разъема корпуса редуктора – по оси тихоходного вала. Опоры быстроходного и промежуточного валов расположим в крышке редуктора.
Очерчиваем внутреннюю стенку корпуса:
а) принимаем зазор между торцом шестерни и внутренней стенкой корпуса
А1=12=10 мм; при наличии ступицы зазор берется от торца ступицы;
б) принимаем зазор от окружности вершин зубьев колеса до внутренней стенки корпуса А==8 мм;
в) принимаем расстояние между наружным кольцом подшипника ведущего вала и внутренней стенкой корпуса y==8 мм.
Если диаметр окружности вершин зубьев шестерни окажется больше наружного диаметра подшипника то расстояние А надо брать от шестерни.
Наносим габариты подшипников.
Измерением устанавливаем расстояния:
f1 = 47 мм c1= 395 мм m1 = 395 мм;
f2 = 395 мм c2= 53 мм
f3 =925 мм c3= 925 мм l3 = 57 мм.
Расчет шпоночных соединений
Шпонки призматические со скругленными торцами. Размеры сечений шпонок и пазов и длины шпонок — по ГОСТ 23360 — 78.
Материал шпонок — сталь 45 нормализованная.
Напряжения смятия и условие прочности по формуле
Допускаемые напряжения смятия .
d = 20 мм; b х h = 6 х 6 мм; глубина паза:t1 = 35 мм; t2 = 28 мм; длина шпонки момент на ведущем валу ;
Условие см [см] выполнено.
Шпонка под зубчатым колесом: d = 28 мм; b х h = 8 х 7 мм; глубина паза: t1 = 4 мм; t2 = 33 мм; длина шпонки момент на валу ;
Шпонка под зубчатым колесом: d = 38 мм; b х h = 12 х 8 мм; глубина паза:
t1 = 5 мм; t2 = 33 мм; длина шпонки момент на валу ;
Шпонка под звездочкой: d = 30 мм; b х h = 8 х 7 мм; глубина паза:t1 = 4 мм; t2 = 33 мм; длина шпонки момент на валу ;
Условие см [см] выполнено.
Проверочный расчет подшипников
Рис. 1 Расчетная схема ведущего вала
Из предыдущих расчётов имеем Ft = 407 H Fr =151 H Fa = 73 H; из первого этапа компоновки f1=47 мм c1=395 мм l1=106 мм m1=395 мм. Со стороны шкива ременной передачи на быстроходный вал редуктора действует сила .
Рис. 2 Расчетная схема промежуточного вала
Из предыдущих расчётов имеем FtБ = 407H FrБ =151 H FaБ= 73 H; FtТ =1389 H FrТ =514 H FaТ= 251 H; из первого этапа компоновки f2 = 395 мм c2= 53 мм l2 = 53 мм m2 = 395 мм.
Рис. 3 Расчетная схема выходного вала
Из предыдущих расчётов имеем FtТ =1389 H FrТ =514 H FaТ= 251 H; FB = 1783H из первого этапа компоновки f3=925 мм c3=925 мм l3= 57 мм.
Определяем долговечности подшипников.
Для определения долговечности подшипников используем формулу:
где р - показатель степени для шариковых подшипников р = 3 для роликовых подшипников р = 103;
n -частота вращения вала;
С - динамическая грузоподъемность;
Р - эквивалентная нагрузка которая определяется по формуле [2 с.209]:
где Fr - радиальная нагрузка;
Fa - осевая нагрузка;
V - коэффициент вращения при вращении внутреннего кольца V = 10;
Kб -коэффициент безопасности Kб =10;
KТ -температурный коэффициент KТ =105;
XY -коэффициенты радиальной и осевой нагрузок.
Подбираем подшипники по более нагруженным опорам.
Для опоры В быстроходного вала:
Для опоры В промежуточного вала:
Для опоры В выходного вала:
Расчетная долговечность меньше 20000 ч. Принимаем подшипники 207 у которых С = 255кН С0 = 137кН и повторяем расчет.
Долговечности подшипников удовлетворяют требуемому ресурсу .
Окончательно принимаем для быстроходного вала два радиальных шарикоподшипника 105 ГОСТ 8338-75; для опор промежуточного вала – два радиальных шарикоподшипника 107 ГОСТ 8338-75; для опор выходного вала редуктора - два радиальных шарикоподшипника 207 ГОСТ 8338-75.
Проверочный расчет валов
Примем что нормальные напряжения от изгиба изменяются по симметричному циклу а касательные от кручения — по отнулевому (пульсирующему).
Уточненный расчет состоит в определении коэффициентов запаса прочности s для опасных сечений и сравнении их с требуемыми (допускаемыми) значениями [s]. Прочность соблюдена при s > [s].
Будем производить расчет для предположительно опасных сечений каждого из валов.
Сечение А-А. Концентрация напряжений обусловлена посадкой подшипника с гарантированным натягом.
Материал вала тот же что и для шестерни (шестерня выполнена заодно с валом) т. е. сталь 45 улучшенная; в = 780 МПа.
Предел выносливости при симметричном цикле изгиба
Предел выносливости при симметричном цикле касательных напряжений
Суммарный изгибающий момент
Осевой момент сопротивления .
Амплитуда нормальных напряжений .
Коэффициент запаса прочности по нормальным напряжениям
Полярный момент сопротивления .
Амплитуда и среднее значение цикла касательных напряжений
Коэффициент запаса прочности по касательным напряжениям
Результирующий коэффициент запаса прочности
Для обеспечения прочности коэффициент запаса должен быть не меньше . Полученное значение достаточно.
Сечение Б-Б. Диаметр вала в этом сечении 28 мм. Концентрация напряжений обусловлена наличием шпоночной канавки: к=18 и к= масштабные
факторы = 087; и = 075; коэффициенты = 015 и = 01.
Осевой момент сопротивления
Полярный момент сопротивления
Сечение В-В. Материал вала — сталь 45 улучшенная; в = 780 МПа.
Концентрация напряжений обусловлена посадкой подшипника с гарантированным натягом.
Выбор посадок сопряженных деталей
Назначаем следующие посадки для деталей редуктора:
- посадка зубчатых колес на валах
- посадка крышек подшипников в корпусе Н7
- посадка внутренних колец подшипников на валах
- посадка наружных колец подшипников в корпусе Н7
- посадка полумуфты на вал Н8
- посадка шпонки в паз вала посадка шпонки в паз втулки Js9h9.
Смазывание зубчатых зацеплений производится окунанием зубчатого колеса тихоходной ступени в масло заливаемое внутрь корпуса до погружения колеса на всю длину зуба.
Камеры подшипников заполняем пластичным смазочным материалом при монтаже. Сорт мази – солидол марки УС-2.
Устанавливаем вязкость масла. При контактных напряжениях = 312 МПа и скорости V = 03 мс рекомендуемая вязкость масла должна быть примерно равна . Принимаем масло индустриальное И-30А (по ГОСТ 20799-75).
Чернавский С.А Курсовое проектирование деталей машин С.А. Чернавский К.Н. Боков И.М. Чернин Г.М. Ицкович В.П. Козинцов. М.; "Альянс" – 2005. – 416 с.
Единая система конструкторской документация (EСKД).
Основные положения. ГОСТ 2.101—68 — ГОСТ 2.121—73.
Единая система конструкторской документации (ЕСКД).
Общие правила выполнения чертежей. ГОСТ 2.301—68 —
Единая система конструкторской документации (ЕСКД). Правила выполнения чертежей различных изделий. ГОСТ 2.401—68— ГОСТ 2.426—74.
Рекомендуемые чертежи
- 20.06.2022