Одноковшовый экскаватор драглайн ЭШ 6,5/45


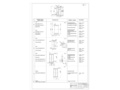
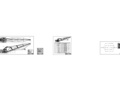
- Добавлен: 25.10.2022
- Размер: 515 KB
- Закачек: 0
Описание
Состав проекта
![]() |
![]() |
![]() ![]() ![]() ![]() |
![]() ![]() ![]() ![]() |
![]() |
![]() ![]() ![]() |
![]() ![]() ![]() |
Дополнительная информация
rrer-2004.dwg

Среднее удельное давление на грунт рамы при работе в кПа
Среднее удельное давление на грунт опорных башмаков
мм до 2 000 Скорость передвижения
3 Наибольший подъем и уклон преодолеваемый экскаватором
в ° 10° Диаметр опорно поворотного круга
мм 7'700 Скорость вращения поворотной платформы
при установившемся движении
Наибольший радиус копания и разгрузки
Наибольшая высота разгрузки
м 22 Наибольшая глубина копания
Техническая характеристика
Наименование смазываемого узла
Периодичность смазывания
Подшипник подъемного вала
Шарнирное сочленение рычагов тормоза
Подшипники качения механизма шагания
Червячная пара лебедки подъема стрелы
Поверхности катания роликов
Втулка центральной цапфы
Подшипники качения блоков
Втулки разгрузочного блока
Оси блоков надстройки
Подшипники качения следящего блока
Зубчатая муфта тягового вала
ОЗП-1 ТУ 38 УССР 201117-76
Нагнетать до появления свежего
смазочного материала
Подшипники качения элкектро- двигателя тяговой лебедки
Прекращение работы и выключение электрооборудования Осмотр и мойка необходимых узлов Ревизия поворотной платформы Устранение дефектов корпуса экскаватора Ремонт металлических конструкций в основании стрелы Дефектовка отверстий в ступицах механизма шагания Развертка изношенных болтовых отверстий Проверка опорно-поворотного устройства Замена изношенных осей роликов поворотного круга Замена изношенного зубчатого зацепления венца Обследование втулки центральной цапфы Проверка канатов Снятие ковша и подвеса Ремонт изношенных зубьев Ремонт поврежденных стенок ковша Замена втулок разгрузочного блока Натяжение подъемного каната Демонтаж электролебедки Ремонт корпуса редуктора Замена червячной пары лебедки подъема стрелы Проверка барабана лебедки подъема стрелы Сборка и установка лебедки Установка в ремонтное положение стрелы Осмотр и обследование металлоконструкций стрелы Восстановление резьбовых соединений Замена опорных подшипников подпятника стрелы Монтаж стрелы в рабочее положение Запуск экскаватора и проверка работы
КП ЭиР-14000000000 СБ
КП ЭиР-14000000000 КС
КП ЭиР-14000000000 СГ
ЦИАТИМ-201 ГОСТ 6267-74
АСЗп-10 ТУ 38.101267-72
Масло Компрессорное К-12
Подшипники вала чевяка механизма поворота
КП ЭиР-13052000000СБ
Ходовое оборудование
КП ЭиР-14052070000СБ
КП ЭиР-14052000000ПЗ
Пояснительная записка
КП ЭиР-14052060000СБ
КП ЭиР-14052050000СБ
КП ЭиР-14052040000СБ
КП ЭиР-14052030000СБ
КП ЭиР-14052010000СБ
КП ЭиР-14052020000СБ
КП ЭиР-14052080000СБ
КП ЭиР-14052090000СБ
КП ЭиР-14052100000СБ
КП ЭиР-14052110000СБ
Стрелоподъемный полиспаст
КП ЭиР-14052120000СБ
КП ЭиР-13052000000КС
КП ЭиР-13052000000КР
rrssr-srrrrsr2004.dwg

Наименование операции и содержание переходов
Оборудование и инструмент
Технологический эскиз
Рассточить канавку выдерживая размеры (1-5);
Контрольная. Контроль окончательный согласно чертежу детали
Микрометр МТ 0-50 ГОСТ 6507-90
Токарно-винторезный станок 16Т02А; резец подрезной2112-0005 Т15К6 ГОСТ 18880-73;
V=70 ммин; n=315 мин-1; S=0
КП ЭиР-14000000000 КР
Сталь 45 ГОСТ 1050-88
Резец проходной2100-0407 Т15К6 ГОСТ188878-73;
Резец отрезной 2130-0009 ГОСТ 18884-73
V=63 ммин; n=315 мин-1; S=0
Токарно-винторезный станок 16Т02А; Сверло 1100 ø150 ГОСТ 10903-77 Резец расточной 25х25х240 2140-0010 Т15К15 ГОСТ 18882-73
V=40 ммин; n=400мин-1; S=0
Резец расточной 25х25х240 2140-0010 Т15К15 ГОСТ 18882-73
V=42 ммин; n=400 мин-1; S=0
Резец проходной 2101-0013 Т15К6 ГОСТ 18879-73
Токарно-винторезный станок 16Т02А; Резец канавочный Р-ТО-30-158 ;
V=51 ммин; n=400 мин-1; S=0
Зачистить канавку шкуркой
24А 15М ГОСТ 13344-79;
V=6 ммин; n=80 мин-1; S=0
Токарно-винторезный станок 16Т02А; Резец В6 РД 63 ;
Обточить поверхность (2) выдерживая размер (7)
Токарно-винторезный станок 16Т02А; Резец подрезной 25х16х140 2112-0005 ГОСТ 18880-73;
V=52 ммин; n=315 мин-1; S=0
Резец подрезной 25х16х140 2112-0058 ГОСТ 18880-73;
V=50 ммин; n=315 мин-1; S=0
Проточить сопряжение выдерживая размеры (1)
Резец канавочный Р-ТО 30-162;
Шлифовать поверхность (2) выдерживая размер (1)
Круг шлифовальный ПП600х80х305 24А 40 СМ17К6 ГОСТ 2424-83
V=15 ммин; n=100 мин-1; t=0
Круглошлифовальный станок3Б161
Проточить канавку выдерживая размеры (6)
Обточить поверхность (4) до кулачков (3)
выдерживая размер (5)
Рассточить отверстие (1)
Обточить поверхность (4)
Сверлить отверстие ø150 на размер (3)
Обточить поверхность (2) до ø200
Титульник.docx
по дисциплине «Эксплуатация и ремонт»
на тему: «Ремонт и эксплуатация одноковшового экскаватора драглайна ЭШ 6545»
ПЗ. ЭКсплуатация и ремонт.docx
2. Организация технического обслуживания и ремонта драглайнов 11
Техника безопасности при ремонтных работах
1. Меры безопасности при подготовке к эксплуатации машины 16
2. Меры безопасности при работе драглайна 21
Технология обслуживания машины
1. Сущность процесса очистки и ее цель 24
2. Разборка машин и сборочных единиц 27
Приемка машин и сборочных единиц в ремонт 30
Технология ремонта 34
Расчет ремонтного предприятия 41
Правила хранения Экскаваторов ЭШ 6545м 47
Список используемой литературы 53 Приложение
Обеспечение работоспособного состояния парков машин и оборудования предприятий связано со значительными трудовыми и материальными затратами. С помощью нормативов определяются квартальные и годовые прогнозы потребности в техническом обслуживании и ремонте по парку машин что необходимо но недостаточно для управления надежностью в эксплуатации. Требуется также выявлять потребность в ремонтных воздействиях конкретных экземпляров машин и их агрегатов что дает краткосрочный прогноз конкретизирующий потребность определяемую по нормативным данным.
Для этих целей используют техническую диагностику. Она необходима также при поиске отказов и определении качества выполнения работ по техническому обслуживанию и ремонту машин сложной конструкции к которым относятся подъемно-транспортные строительные дорожные и коммунальные машины (ПТСДиКМ) а так же их агрегаты и системы.
Выполнение технического обслуживания и ремонта требует создания и последующего эффективного использования производственно-технической базы а также наличия складов запасных частей агрегатов и материалов.
В сложившихся условиях развития отечественного дорожно-строительного и автомобильного машиностроения формируется тенденция к увеличению объема ремонтных работ что в сочетании с замедлением темпов развития системы технического обслуживания и ремонта машин вызывает существенное повышение потерь всех видов ресурсов. В связи с этим широкое применение и совершенствование методов технологии ремонта системы ремонтных предприятий исключительно актуально и перспективно в процессе развития народного хозяйства. Работы по техническому обслуживанию предусматривают профилактические цели и должны способствовать главным образом снижению интенсивности изнашивания деталей и обеспечивать их нормативную долговечность. Ремонт предполагается выполнять в соответствии с необходимостью. Создание системы технического обслуживания и ремонта направленной на поддержание парка машин в работоспособном состоянии в течение всего срока их службы также предполагает обеспечить высокий технический уровень готовности парка и минимальные затраты для его достижения независимо от ведомственной принадлежности.
Интенсивное поступление в Россию в последние годы импортной дорожно-строительной и автотранспортной техники также вынуждает специалистов пересмотреть ранее сложившиеся подходы к организации и технологии ремонта машин. Новые материалы (синтетические полимерные композиционные) постоянно совершенствующееся диагностическое и технологическое оборудование обеспечивают возможности постоянного развития существующих и разработки новых методов контроля состояния и восстановления работоспособности машин.
Современные рыночные отношения между производителем и потребителем техники вызвали необходимость формирования новой концепции обеспечения качества ремонта машин в условиях минимума затрат на обеспечение ресурса запланированного заводом-изготовителем.
Эксплуатация включает: обеспечение технически грамотного с максимальной экономической эффективностью использования машины их техническое обслуживание и ремонт; научно - исследовательские работы направленные на совершенствование форм и методов эксплуатации парков машин.
1. Организация эксплуатации технического обслуживания и ремонта
Высокий уровень организации и технической эксплуатации и ремонта строительных машин позволяет содержать парк машин в исправном состоянии обеспечивает повышение их работоспособности и восстановление ресурса.
У нас в стране принята планово-предупредительная система технического обслуживания и ремонта строительных машин (система ПНР). Эта система представляет собой комплекс организационно-технических мероприятий проводимых в плановом порядке. В соответствии с ГОСТ 18322—78 все работы предусмотренные системой ППР подразделяются на техническое обслуживание и ремонт.
Техническое обслуживание представляет собой комплекс операций по поддержанию работоспособности машины при использовании по назначению ожидании хранении и транспортировании. Техническое обслуживание предусматривает обязательный периодически выполняемый по плану объем работ заранее установленный для данного типа и модели машины. Несмотря на плановость проведения работ по техническому обслуживанию при известной степени изнашивания дальнейшее использование машины становится технически и экономически нецелесообразным или даже опасным (аварийным). В этом случае возникает необходимость в ремонтных работах.
Ремонт — это комплекс операций по восстановлению работоспособности машины и восстановлению ресурса машины и ее составных частей. Объем работ по ремонту машин зависит от качества технического обслуживания условий использования машины квалификации машиниста в большинстве случаев он не регламентирован и устанавливается на основании фактической потребности.
В соответствии со строительными правилами (СанПиН 111-1-76) и нормативными документами предусматривается проведение ежесменного технического обслуживания (ЕО) периодического технического обслуживания (ТО) сезонного технического обслуживания (СО) и плановых ремонтов: текущего (Т) и капитального (К).
Ежесменное техническое обслуживание должно обеспечить работоспособность машины на протяжении всей рабочей смены. Его выполняют перед началом в течение или после окончания рабочей смены. В состав этого вида обслуживания входят смазка узлов и деталей машины и подготовка ее к передаче при смене бригад а также контрольный осмотр перед работой.
Периодическое техническое обслуживание выполняется через установленные в эксплуатационной документации значения наработки или интервала времени. Этот вид обслуживания предупреждает интенсивность изнашивания сопряженных деталей машин за счет проведения профилактических мероприятий. Для машин смонтированных на базе автомобиля предусмотрено проведение двух технических обслуживании (ТО-1 и ТО-2) а для машин смонтированных на базе трактора или с тракторным двигателем — трех технических обслуживании (ТО-1 ТО-2 и ТО-3). В состав периодических технических обслуживании входят: внешний уход диагностирование крепежные и регулировочные работы а также смазывание машины.
Сезонное техническое обслуживание приводят для подготовки машин к осенне-зимней и весенне-летней эксплуатации а также перед их хранением. Обычно этот вид обслуживания осуществляют два раза в год. При сезонном обслуживании производят замену масел топлива и охлаждающей жидкости при переходе к соответствующему периоду эксплуатации.
Текущий ремонт выполняют для обеспечения работоспособности машины; он состоит из операции по восстановлению и замене деталей и сборочных единиц при частичной разборке машины.
Капитальный ремонт проводят для устранения неисправностей и восстановления полного или близкого к полному ресурса машины включая любые ее части и даже базовые.
В системе ППР предусматривается выполнение в машине необходимых воздействий после отработки ею определенного количества часов. В соответствии с этим для каждой машины разрабатывается план-график периодичности выполнения технических обслуживании и ремонтов (на время жизненного цикла машины определенный год месяц). Основополагающим для разработки является ремонтный цикл т. е. время работы машины (в ч) между очередными капитальными (К) ремонтами. Он устанавливается для каждой машины в зависимости от ее назначения и основных параметров. Ремонтный цикл рассчитывается так чтобы каждая остановка машины на ремонт соответствовала времени достижения предельного износа определенной группы деталей и сборочных единиц. Например для землеройной машины продолжительность ремонтного цикла (Ц) составляет 5760 ч. За это время необходимо провести четыре текущих (Т) ремонта через каждые 960 ч. В каждом цикле текущего ремонта Цт проводится три ТО-2 со временем цикла Цто-2 = 240 ч а в каждом Цто-2 — три ТО-1 со временем цикла Цто-i = 60 ч. Интервалы между отдельными видами воздействий всегда являются величиной кратной и для приведенной периодичности представлены соотношением 1:4:16:96 или в часах как 60:240:960:5760. Для башенных кренов 5 9 размерных групп (М = 250. 1400 т-м) это отношение составит 1:3:6:72 или в часах — 200:600:1200:14400 т. е проведение двух ТО-1 и одного ТО-2 до текущего ремонта и одиннадцати текущих ремонтов в полном ремонтном цикле.
Технологический процесс технического обслуживания машин состоит из совокупности операций каждая из которых составляет часть процесса осуществляемого одним или несколькими рабочими. Операция представляет собой комплекс последовательных действий по обслуживанию сборочной единицы (узла или агрегата) или группы сборочных единиц. Так операциями технического обслуживания являются: замена масла в поддоне картера двигателя регулирование тормозов регулирование фрикционной муфты и т. п.
Техническое обслуживание машины состоит из большого числа операций которые по своему характеру и условиям выполнения могут быть объединены в определенные группы охватывающие цикл работ. Практика показывает что техническое обслуживание независимо от его вида можно подразделить на следующие основные работы: уборочно-моечные диагностические крепежные регулировочные смазочные и заправочные. Такое подразделение обусловливается во-первых необходимостью использования рабочих соответствующих специальностей и квалификации при выполнении каждой работы и во-вторых применением специального оборудования приборов и инструмента на месте выполнения работ.
Перечисленные группы работ характеризуются определенной значимостью. Уборочно-моечные работы (внешний уход) которые предшествуют всем остальным видам работ позволяют установить наличие внешних неисправностей строительных машин а также определяют качество последующих работ их производительность и культуру выполнения.
Диагностирование строительных машин которое заключается в определении их технического состояния без предварительной разборки позволяет предусмотреть появление неисправностей и принять соответствующие меры предупреждающие нарастание износов сопряженных деталей. Существенно важным является также то обстоятельство что в результате проведения диагностирования представляется возможным установить остаточный ресурс машины и ее сборочных единиц т. е. определить время нормальной работы машины до ее капитального ремонта.
В процессе выполнения практической работы строительная машина систематически подвергается воздействию динамических нагрузок которые приводят к нарушению затяжки резьбовых соединений. Это обстоятельство вызывает необходимость в периодической затяжке резьбовых соединений что требует выполнения крепежных работ. Несвоевременное проведение крепежных работ может вызвать аварийный дефект.
Сопряженные детали сборочных единиц характеризуются определенным расположением в пространстве и возникновением между деталями зазоров определенной величины. В процессе работы машин величины этих зазоров изменяются и после определенного промежутка времени их размер достигает предельных значений. С целью восстановления первоначальных зазоров и возникает необходимость в выполнении регулировочных работ.
Во время работы машины между трущимися поверхностями сопряженных деталей образуются силы трения приводящие к повышению температуры обеих деталей и к их заеданию. Чтобы уменьшить трение а следовательно нагрев и износ между этими деталями вводят смазочные материалы позволяющие перейти от трения без смазки к трению граничному а в отдельных случаях и к жидкостному.
Места смазывания вид смазочного материала периодичность смазывания и требования к нему указываются в заводской инструкции по эксплуатации для каждой машины. Система смазывания делится на индивидуальную и централизованную. В первом случае смазочные материалы подводятся к трущимся поверхностям индивидуально с помощью смазочного устройства расположенного рядом с сопрягаемыми деталями. Во втором случае одно смазочное устройство обслуживает ряд сопряженных деталей расположенных в различных местах машины.
Заправочные работы выполняются с целью заполнения систем строительных машин эксплуатационными материалами и специальными жидкостями: топливом маслом тормозной и гидравлическими жидкостями.
Наряду с плановыми ремонтами возможен и аварийный (непланируемый) ремонт (мелкий средний) который выполняют эксплуатационные и ремонтные участки строительных организаций (управлений механизации).
2. Организация технического обслуживания и ремонта шагающих экскаваторов
Работы по техническому обслуживанию и ремонту строительных машин выполняют централизованно частично централизованно и децентрализованно.
Все технологические операции технического обслуживания и текущего ремонта скреперов выполняют бригады рабочих высокой квалификации под руководством инженерно-технического персонала. Таким образом при этой форме обслуживания машинисты скреперов полностью освобождены от этих работ. Централизованное обслуживание относится к числу наиболее прогрессивных форм. Оно направлено на выполнение всех элементов планово-предупредительной системы в соответствии с техническими условиями и при наименьших затратах. Особенностью этой формы обслуживания является специализация отдельных операций что позволяет решать следующие задачи: увеличить объем механизированных работ применительно к отдельным элементам технического обслуживания; повысить производительность машин в процессе эксплуатации за счет сокращения простоев в результате увеличения количества рабочих и механизации работ; улучшить качество обслуживания благодаря высокой квалификации рабочих. Разновидностью централизованного обслуживания является проведение работ специализированными звеньями.
Сущность специализации заключается в том что звенья осуществляют работы только по техническому обслуживанию определенных видов или марок скреперов а каждый из членов звена при этом выполняет с помощью выделенных ему средств механизации установленные однотипные виды работ сложность которых соответствует присвоенному ему разряду. Специализированные звенья целесообразно создавать для выполнения периодических технических обслуживании (ТО-1 ТО-2 и ТО-3). В эксплуатационных организациях характеризующихся наличием смешанных парков машин звенья целесообразно специализировать на обслуживание отдельных видов машин (землеройные стреловые краны и т. д.).
Частично централизованная форма организации технического обслуживания характеризуется тем что ежесменное обслуживание выполняют машинисты которые закреплены за данными машинами а периодические ТО и текущий ремонт — специализированные бригады рабочих. Недостатками этой формы организации технического обслуживания являются снижение эффективности системы ППР; уменьшение рабочего времени машины в результате ее простоя при техническом обслуживании; значительное против плановых норм повышение трудовых затрат на рабочие операции из-за немеханизированного их выполнения; трудность осуществления должного контроля за работами по техническому обслуживанию и текущему ремонту.
Децентрализованная форма технического обслуживания характеризуется тем что все виды работ выполняют машинисты машин. Специализированные бригады осуществляют лишь текущий ремонт машин. Недостатки этой формы организации технического обслуживания те же что и при частично централизованной форме. Кроме того при этой форме организации значительно увеличиваются простои машин при обслуживании.
Выше указывалось что организацию технического обслуживания и ремонта строительных машин осуществляют эксплуатационные предприятия (управления механизации) в состав которых входят стационарные и передвижные мастерские. В зависимости от состава парка машин стационарные мастерские развиты в большей или меньшей степени. Так при наличии в управлении механизации большого количества мобильных строительных машин основной объем работ по техническому обслуживанию и ремонту выполняется в условиях стационарных мастерских которые в этом случае оснащены всем необходимым оборудованием для выполнения работ. При эксплуатации машин малой мобильности (экскаваторы бульдозеры и др.) рассредоточенных на значительном расстоянии друг от друга существенно важным является использование передвижных мастерских входящих в состав управления механизации. Современные мастерские оснащаются оборудованием (компрессором сварочным трансформатором гидропрессом пароводоструйным очистителем емкостями для дизельного трансмиссионного масла и для гидрожидкости солидолонагнетателем станками инструментами запасными частями гидроманипулятором-краном и т. д.) обеспечивающим высокий уровень механизации ремонтных работ.
Для проведения работ по техническому обслуживанию промышленностью выпускаются универсальные и специальные передвижные мастерские. Последние характеризуются значительным разнообразием и могут предназначаться для технического обслуживания одного типа машин: башенных кранов экскаваторов и т. п. Для технического диагностирования строительных машин используют передвижные диагностические станции КИ-4070А КИ-5164 и КИ-13905 смонтированные на базе автомобиля. Станции оснащены комплексом приборов и инструментов наличие которых позволяет осуществлять диагностирование машин с определением 60 130 параметров диагностирования.
Текущий ремонт строительных машин выполняется в стационарных мастерских управлений механизации и передвижными мастерскими в условиях строительной площадки
Капитальный ремонт осуществляется ремонтными заводами. В настоящее время используют два метода капитального ремонта: индивидуальный и агрегатно-узловой. При индивидуальном методе ремонта отремонтированные сборочные единицы устанавливают на ту же машину с которой они были сняты. При агрегатно-узловом методе ремонта сборочные единицы обезличиваются. Снятые с машины сборочные единицы направляют в ремонт а взамен их устанавливают на машины сборочные единицы из оборотного фонда которые заранее отремонтированы. Агрегатно-узловой метод ремонта характеризуется рядом преимуществ. В частности исключается необходимость транспортирования машин от эксплуатационного предприятия на ремонтный завод кроме этого значительно сокращается время на выполнение собственно ремонта машин.
Экскаватор ЭШ-6545 состоит из рабочего оборудования поворотной платформы с установленными на ней механизмами и шагающего оборудования.
Механизмы на поворотной платформе за исключением напорной лебедки закрыты кузовом. Съемные секции крыши кузова обеспечивают доступ ко всем механизмам при проведении ремонтных работ с использованием грузоподъемных средств. Установленная на крыше кузова вспомогательная лебедка пред назначена для механизации работ при ремонтах и замене быстроизнашивающихся деталей и канатов. В передней части платформы справа установлена кабина машиниста с органами управления экскаватором и контурной аппаратурой.
Поворотная платформа стрела рукоять нижняя рама ходовой тележки представляют собой сварные металлические конструкции из проката и стальных отливок.
Основных механизмы экскаватора (подъема поворота напора хода и открывания днища ковша) приводятся в действие двигателями постоянного тока вспомогательные механизмы — двигателями переменного тока. Электродвигатели постоянного тока основных механизмов питаются от соответствующих генераторов преобразовательного агрегата по схеме генератор — двигатель электродвигатели переменного тока вспомогательных приводов — от понижающего трансформатора.
Тормоза подъемной и напорной лебедок поворотного механизма управляются сжатым воздухом от компрессорной установки. Тормоза ходовых механизмов — электрические.
1. Меры безопасности при подготовке к эксплуатации
Производство земляных работ требует строгого соблюдения правил техники безопасности. Несчастные случаи при производстве земляных работ обычно относятся к разряду тяжелых. По законам РФ администрация несет уголовную ответственность за несоблюдение этих правил.
Исключение травм может быть достигнуто квалифицированным обучением рабочих-механизаторов и инженерно-технических работников строительно-монтажных управлений и их предприятий безопасным приемам и методам работы в различных условиях строительного производства и своевременным проведением с ними инструктажей периодической проверкой знаний ими норм и правил техники безопасности.
Так машинистов допускают к работе только после предварительного обучения их и сдачи ими экзамена (аттестации). При аттестации машинистов (водителей) работающих с двигателями на этилированном бензине проверяют знание ими соответствующих мер предосторожности. При аттестации машинистов грузоподъемных кранов и кранов-экскаваторов в состав квалификационной комиссии входит представитель органа Госгортехнадзора РФ. Результаты аттестации оформляют протоколом. В удостоверении машиниста указывают тип машины к управлению которой он допущен. Назначение на работу оформляют приказом по организации (предприятию) на балансе которой находится машина.
Машинистами могут быть лица не моложе 18 лет прошедшие медицинское освидетельствование обучение по соответствующей программе сдавшие зачеты квалификационной комиссии и имеющие на руках удостоверение на право управления соответствующим типом (моделью) машины.
Помощника машиниста назначают когда это необходимо по местным условиям работы или предусмотрено инструкцией по эксплуатации машины.
При переводе машиниста с одного типа машины на другой его предварительно обучают по сокращенной программе и аттестуют в установленном правилами порядке. При переводе машиниста с одной модели машины на другую такого же типа дополнительное обучение не проводят. В этом случае машинист знакомится с конструктивными особенностями машины управлением периодичностью и объемом технических обслуживания и проходит стажировку в течение 3 6 смен. После проверки усвоения практических навыков его допускают к самостоятельной работе.
В соответствии с законодательством и требованиями норм и правил по технике безопасности перед допуском к работе с рабочими служащими и инженерно-техническими работниками проводят инструктаж по безопасным приемам работы. Инструктаж подразделяется на вводный и инструктаж на рабочем месте.
Вводный инструктаж проводят при приеме на работу. В специализированных управлениях механизации ПМК строительных и монтажных организациях на предприятиях и участках механизации инструктаж проводит главный инженер а в его отсутствие — инженер (старший инженер) по технике безопасности.
В задачи вводного инструктажа входит ознакомление вновь поступающего работника с правилами внутреннего трудового распорядка и общими правилами безопасности.
Инструктаж на рабочем месте проводит инженерно-технический работник (механик энергетик мастер производитель работ начальник участка) в непосредственное подчинение которого направляется рабочий. Инструктаж проводят в форме беседы с практическим показом безопасных приемов работы и подробным разбором конкретных приемов из практики производственной деятельности организации. Инструктаж на рабочем месте по технике безопасности (производственный инструктаж) подразделяется на первичный повторный и внеочередной.
Первичный инструктаж проводят при допуске вновь принятого рабочего к управлению техническому обслуживанию и ремонту машин и оборудования.
При проведении инструктажа рабочего подробно знакомят:
С конструктивными особенностями машины установки оборудования на котором он должен работать;
С условиями безопасной работы при управлении осмотрах смазывании со сроками и объемами проведения технических обслуживании;
С правилами запуска двигателя и заправки горючим
Со способами устранения основных неисправностей и выполнения
С мерами безопасности при замене рабочего оборудования и сцепке машин при буксировке;
С приборами безопасности предохранительными устройствами защитными приспособлениями (ограждениями) средствами сигнализации аварийным освещением их назначением и правилами пользования;
С правилами погрузки машин на транспортные средства и передвижения собственным ходом и на буксире;
С особенностями эксплуатации в различных производственных условиях и зимой.
Повторный инструктаж проводят все рабочие независимо от квалификации и стажа работы по данной профессии не реже 1 раза в 3 мес. на рабочем месте. Повторный инструктаж по безопасным приемам работы проводят по программе первичного инструктажа. Его цель — периодическое напоминание рабочему о безопасных приемах и методах труда. Инструктирующий должен убедиться в знании и правильном усвоении рабочим правил техники безопасности на рабочем месте.
Внеочередной инструктаж проводят:
При переводе машиниста на машину другой марки (модели) при изменении условий или характера работы замене рабочего и строительного оборудования;
При выдаче наряда-допуска на опасные работы;
При нарушении рабочим правил техники безопасности или при несчастном случае связанным с эксплуатацией машин и оборудования.
Инструктирование рабочего заканчивается после практической проверки освоения им безопасных приемов и способов работы не рабочем месте и в конкретных производственных условиях.
Инженерно-технический работник проводивший инструктаж не должен допускать рабочего к самостоятельной работе если последний не усвоил безопасных приемов и методов выполнения порученной работы.
О проведении инструктажа по технике безопасности на рабочем месте (первичного повторного внеочередного) делают запись в журнале.
За несвоевременное и несоответствующее проведение инструктажа а также за необеспечение технического надзора за безопасным производством работ руководители несут ответственность согласно действующему законодательству.
Производство механизированных земляных работ землеройными машинами должно выполняться безопасными и безвредными приемами и методами отвечающими требованиям СанПиН II1-4-80 «Техника безопасности в строительстве».
2. Меры безопасности при работе драглайна.
Начиная работу дать звуковой сигнал предупреждения.
Передвижение автотранспортных средств начинать только по сигналу
машиниста экскаватора.
При остановке экскаватора ковшовую раму очистить от грязи.
При появлении неисправности работу на экскаваторе немедленно прекратить двигатель выключить до устранения поломки.
Во время разработки грунта необходимо выполнять периодическое отшагивание что бы предупредить
Во время работы находиться на экскаваторе посторонним лицам.
Во время работы двигателя производить крепление деталей и их смазку также их осмотр в узких местах.
Ставить экскаватор в зоне возможного сползания грунта или работать под "козырьком" грунта.
Работать в ночную смену с неисправным освещением неполной заправкой топливом водой маслом и рабочей жидкостью в гидросистеме.
Оставлять без присмотра экскаватор с работающим двигателем.
Для безопасного ведения работ машинист и его помощник обязаны строго соблюдать правила техники безопасности на рабочем месте и знать те положения которые оказывают влияние на работу экскаватора.
Нарушение этих правил может привести к несчастным случаям как с обслуживающим персоналом так и с другими работниками находящимися на объекте где работает экскаватор.
Перед началом земляных работ должна быть получена справка об отсутствии подземных коммуникаций. Наличие таких коммуникаций должно быть отмечено знаками.
В вечернее и ночное время фронт работы экскаватора в забое место разгрузки грунта и подъездные пути должны быть хорошо освещены.
В населенной местности забои и участки работы экскаватора следует ограждать и устанавливать щиты с предупредительными надписями. В ночное время ограждения должны быть освещены.
Обслуживающий персонал должен получать каждый раз точные указания о порядке выполнения нового задания а также о соблюдении необходимых мер предосторожности.
Лица не имеющие соответствующей квалификации и не прошедшие инструктажа по технике безопасности к работе на экскаваторе не допускаются.
Стажировка учащихся проводится под непосредственным наблюдением мастера.
Перед пуском двигателя машинист экскаватора обязан внимательно осмотреть машину и убедился в полной ее исправности. Работа на неисправном экскаваторе ни в коем случае не разрешается. О всех неисправностях машины или ненормальных условиях эксплуатации которые могут привести к аварии машинист обязан немедленно довести до сведения администрации предприятия.
На экскаваторе нужно соблюдать чистоту весь необходимый инвентарь и инструмент следует хранить в предназначенном для этой цели месте. Находящиеся на поворотной платформе посторонние предметы могут вызвать аварию.
Все вращающиеся детали — зубчатые колеса цепные передачи маховики и т. д. — должны быть ограждены кожухами. Пуск в действие механизмов при снятых кожухах не разрешается.
Перед пуском в ход двигателя и механизмов машинист должен давать сигнал предупреждения.
При передвижении экскаватора:
При передвижении экскаватора стрела его должна быть установлена строго по оси движения а ковш поднят на максимально допустимую величину
Запрещается передвижение экскаватора с наполненным ковшом.
Запрещается передвигаться по неукрепленным грунтам и к местам близким к обвалу а так же движение по уклону большем чем указано в паспорте машины (в данном случаи больше 10).
Запрещается перемещение экскаватора на сыпучем грунте.
1. Сущность процесса очистки и ее цель
Процессом очистки называется процесс удаления загрязнений с поверхностей объектов очистки с помощью химического физико-химического теплового и механического воздействия. Объектами очистки при ремонте служат автомобили дорожные и строительные машины тракторы сельскохозяйственные машины навесное оборудование на этих машинах а также составные частиц этих машин (агрегаты узлы комплекты и детали). Цели очистки в процессе ремонта машин следующие:
обеспечение качества ремонта высокой производительности труда ремонтников культуры производства и выполнение санитарно-гигиенических требований;
обеспечение возможности измерения геометрических и физико-механических параметров деталей;
обеспечение подготовки деталей для нанесения на них защитных покрытий;
исключение или значительное сокращение коррозии деталей в период нахождения машин в ремонте;
обеспечение требуемой чистоты поверхностей деталей при сборке агрегатов узлов и систем.
Очистные работы представляют собой сумму многостадийных операций очистки объектов ремонта способствующих повышению качества обеспечению необходимых санитарно-гигиенических условий работы ремонтников и повышению производительности их труда. Известно что в результате работы и контакта с окружающей средой детали машин загрязняются ухудшаются эксплуатационные характеристики машин: снижается мощность двигателей эффективность фильтрующих элементов работа радиаторов увеличивается расход топлива и масел в узлах трения возрастает абразивное изнашивание и в результате меняются посадки в сопряжениях деталей. Эти явления приводят к снижению надежности машин Поэтому очистные работы при ремонте машин имеют первостепенное значение. Работы многих научно-исследовательских организаций доказали что только благодаря качественной очистке сборочных единиц и деталей в процессе их ремонта ресурс отремонтированных двигателей повышается на 25 30% а производительность ремонтников — на 15-20%.
Очистка машин сборочных единиц и деталей заключается в удалении с поверхностей загрязнений до такой степени при которой оставшиеся загрязнения не препятствуют проведению ремонтных операций а также последующей эксплуатации машин после ремонта. Очистка поверхностей состоит не только в удалении загрязнений с поверхностей деталей машин но и в исключении процесса повторного загрязнения очищенных поверхностей.
Объекты очистки характеризуются следующими основными параметрами: составом количеством и свойствами находящихся на их поверхностях загрязнений; коэффициентом рельефности взаимной экранизацией поверхностей; массой и размерами; качеством поверхности (шероховатостью); составом свойствами материалов из которых они изготовлены; температурой до начала процесса очистки; допустимой остаточной загрязненностью поверхностей.
Масса и размеры очищаемых объектов меняются от нескольких граммов до нескольких тонн и от нескольких миллиметров до нескольких метров. Это влияет на выбор способа очистки и соответствующего оборудования.
При организации процесса очистки учитываются свойства материалов деталей поскольку они могут меняться при использовании разных способов очистки что может являться причиной коррозионного разрушения при воздействии агрессивных моющих и очищающих сред или механического повреждения поверхностей в результате соударения частиц твердой очищающей среды с поверхностями деталей.
Качество поверхности (шероховатость) значительно влияет на накопление загрязнений чем меньше шероховатость на поверхности тем меньше загрязненность поверхности.
Значительное влияние на выбор способа очистки оказывает требование к остаточной загрязненности очищаемой поверхности. Количественное значение остаточной загрязненности определяется технологическим процессом ремонта. Например применительно к сборочным операциям допустимое количество загрязнений не должно превышать 010 015 мгсм2 при окраске — 0005 мгсм2 при дефектации — 125 мгсм2 при шероховатости поверхности R — до 10 мкм.
2. Разборка машин и сборочных единиц
Машины вначале разбирают на отдельные сборочные единицы узлы а затем — не детали. В условиях специализированных ремонтных предприятии разборку выполняют поточным методом) а на мелких ремонтных предприятиях или в мастерских применяют тупиковый метод (стенды верстаки столы).
При тупиковом методе машины разбирают полностью на универсальном рабочем месте. Такая система организации разборки имеет определенные недостатки — длительный простой машины необходимость использования высококвалифицированных кадров что увеличивает стоимость работ. К преимуществам этого вида разборки можно отнести — простоту организации и персональную ответственность исполнителя за качество выполнения работ.
Использование поточного метода (специализированных рабочих мест) повышает производительность труда а также снижает требования к квалификации исполнителей.
Порядок выполнения разборочных операций и переходов устанавливается в соответствии с требованиями технологической документации. На основании государственных стандартов на предприятии оформляют соответственно маршрутные и операционные карты.
Последовательность выполнения разборочных операций определяется технологической необходимостью очередности снятия тех агрегатов и сборочных единиц без демонтажа которых затруднена или невозможна последующая разборка с обязательным соблюдением условий безопасности труда на рабочем месте.
Вначале демонтируют рабочие органы капоты кабину ограждения вращающихся частей цепные передачи топливные баки и баки для гидравлической жидкости. Затем снимают вспомогательное оборудование двигателя (радиатор система очистки воздуха система питания) механизмы управления (гидроаппаратура) коробку передач и на заключительном этапе — агрегаты ходовой части. Сложные агрегаты или сборочные единицы например двигатели топливную и гидравлическую аппаратуры и т.п. без разборки направляют на соответствующие участки (цеха) ремонта где производят их дальнейшую разборку мойку дефектовку ремонт и сборку. В целях повышения производительности труда и обеспечения требований техники безопасности при выполнении сборочно-разборочных работ рекомендуется широко применять механизированные подъемно-транспортные и другие средства.
Топливные насосы форсунки турбокомпрессоры элементы гидросистемы разбирают только после проведения предварительных испытаний с целью оценки уровня их технического состояния.
В процессе подготовки машины к ремонту необходимо разбирать подвижные и неподвижные соединения которые бывают разъемными и неразъемными. Неподвижные разъемные соединения осуществляются при помощи резьбы шпонок клиньев штифтов шлицев и посадок (с зазором переходные и с натягом) а неподвижные неразъемные соединения фиксируются с помощью заклепок сварки пайки клеевых композиций развальцовки и посадок (горячих прессовых).
Разборка резьбовых соединений вызывает необходимость приложения крутящего момента в 15 25 раза большего чем был приложен при сборке этого же соединения в процессе изготовления машины. Не следует разукомплектовывать резьбовые соединения повышенного класса точности при их годности к дальнейшей работе. Болты крепления крышек коренных опор блока цилиндров крышек шатунов маховика к коленчатому валу и т.п. целесообразно устанавливать на прежнее место или маркировать.
Для разборки резьбовых соединений в целях повышения производительности труда и уровня механизации производства необходимо применять инструмент имеющий электро- и пневмоприводы со специальными насадками (гайковерты шпильковерты шуруповерты а также универсальные рожковые и накидные ключи).
Для обеспечения сохранности посадочных поверхностей деталей при разборке соединений с натягом (втулок подшипников качения шестерен и т.п.) применяют различные съемники (винтовые гидравлические) и прессы а также вспомогательные приспособления — оправки разъемные кольца и др.
При разборке нельзя обезличивать и разукомплектовывать детали конструктивно объединенные в один комплект (блок цилиндров и крышки коренных опор шатуны и крышки шатунов приработанные шестерни и т.п.) поскольку они в процессе производства проходят окончательную механическую обработку в собранном виде. Не рекомендуется также разбирать сопряжения в которых присоединительные размеры (зазоры натяги) не имеют отклонений от допуска.
Для предупреждения появления возможных повреждений (вмятин царапин сколов и т.п.) детали после разборки запрещается укладывать в тару навалом. Также следует соблюдать требования транспортированию деталей при их перемещении от одного рабочего места до другого.
Приемка машин и сборочных единиц в ремонт
Предприятие эксплуатирующее машины (заказчик) руководствуясь существующими положениями направляет подлежащие ремонту машины и сборочные единицы в ремонт а ремонтное предприятие или ремонтное подразделение эксплуатирующего предприятия принимает их на основании тех же положений. Технические условия на сдачу машин и сборочных единиц в капитальный ремонт должны соответствовать требованиям государственных стандартов и руководствам на капитальный ремонт.
Заказчик сдает в ремонт машины и сборочные единицы: выработавшие установленный ресурс и достигшие предельного состояния имеющие аварийные повреждения которые могут устраняться только на предприятиях по капитальному ремонту при наличии соответствующего акта; достигшие предельного состояния но не выработавшие установленного ресурса с приложением соответствующего акта. Техническое состояние сдаваемой в капитальный ремонт машины должно обеспечивать как правило возможность запуска дни и геля и опробование машины вхолостую. Машина имеющая повреждения аварийного характера или неисправности при которых запуск двигателя и движение невозможны или могут повлечь дальнейшее разрушение деталей сдается в капитальный ремонт не на ходу.
Машины и агрегаты направляемые в ремонт должны быть комплектными и иметь лишь те неисправности которые возникли в результате естественного износа деталей. Комплектной признается машина находящаяся в рабочем состоянии с надлежаще установленными узлами и деталями и имеющая один из видов сменного рабочего или навесного оборудования а также годные для работы эксплуатационные материалы (трос авторезина и т.д.).
В отдельных случаях (как исключение) ремонтное предприятие может принимать в ремонт машины и сборочные единицы в комплектности отличной от установленной. При этом доукомплектование машин и сборочных единиц производится по калькуляции ремонтного предприятия согласованной с заказчиком. Машины и их сборочные единицы выработавшие свой ресурс но не достигшие предельного состояния не подлежат капитальному ремонту.
Для определения технического состояния машины и сборочных единиц необходимо использовать средства диагностирования. Результатом диагностирования является заключение о техническом состоянии машины и сборочных единиц с указанием места и причины дефекта. Наружные поверхности машины и сборочных единиц должны быть очищены от грязи а также укомплектованы необходимыми деталями предусмотренными конструкцией.
Навесное оборудование может поступать в ремонт отдельно энергетической установки.
Машины и их сборочные единицы не должны иметь деталей которые отремонтированы способами исключающими возможность последующего их использования или ремонта (приварка сопряженных деталей и др. не предусмотренные конструкцией и т.д.). Все сборочные единицы детали и приборы должны быть закреплены на машине в соответствии с конструкцией. Машины на пневматическом ходу (автогрейдеры автогудронаторы тракторы и т.д.) должны сдаваться в ремонт с накаченными и годными для эксплуатации шинами. Кабина машины должна быть опломбирована.
К каждой машине должны быть приложены следующие документы; формуляр с указанием данных о наработке машины с начала эксплуатации или предыдущего капитального ремонта; аварийный акт если машину направляют в ремонт после аварии; акт о техническом состоянии если направляют в ремонт машину не выработавшую ресурс; паспорт. Сборочные единицы сдаваемые в ремонт отдельно должны иметь справку подтверждающую необходимость капитального ремонта составленную заказчиком. Машины поступающие на капитальный ремонт как правило не обезличиваются.
Машины должны быть смазаны и заправлены соответствующими смазочными материалами (включая гидравлическую систему) и заправлены топливом в объеме 5% топливных баков. Сборочные единицы должны быть смазаны соответствующими смазочными материалами без заправки жидкой смазкой. Машины комплектуются приведенными в рабочее состояние и годными для эксплуатации аккумуляторными батареями.
Дизели и их сборочные единицы сдаются в капитальный ремонт согласно требованиям государственных стандартов и технических условий на ремонт. Сдаваемые на ремонт дизели должны быть укомплектованы сборочными единицами и деталями предусмотренными конструкцией. Несоответствие комплектности дизелей допускается в пределах конструктивных изменений внесенных в данную модель организацией-разработчиком. Допускается отсутствие на дизелях и сборочных единицах отдельных крепежных деталей (болтов гаек шпилек) и мелких деталей (колпачков и т.п.).
Дизели и их сборочные единицы не должны иметь деталей отремонтированных способами исключающими последующее их использование или ремонт; должны быть очищены и вымыты снаружи а жидкий смазочный материал и вода — слиты. Отверстия через которые могут проникнуть атмосферные осадки и пыль во внутренние полости дизелей и их сборочных единиц должны быть закрыты крышками или пробками-заглушками. Наружные неокрашенные металлические поверхности предохраняются от коррозии антикоррозионным смазочным материалом. Тара и транспортные средства применяемые для перевозки дизелей и сборочных единиц должны обеспечивать их сохранность. К каждому дизелю и отдельно сдаваемому топливному насосу прилагаются паспорт и справка подтверждающая необходимость проведения капитального ремонта. К сборочным единицам сдаваемым в ремонт отдельно прилагается справка подтверждающая необходимость капитального ремонта.
Процесс приемки состоит из следующих стадий: предварительный технический осмотр и выявление комплектности; наружная мойка; окончательный технический осмотр. Ремонтному предприятию предоставляется право при приемке вскрывать любую сборочную единицу.
Машина или сборочная единица не отвечающая техническим условиям на приемку на капитальный ремонт не принимается но может быть принята на восстановительный ремонт.
Ремонтное производство развертывается в структуре ремонтных органов объединенных частными задачами и общей цепью восстановления изношенных или поврежденных машин (агрегатов деталей). Ремонтное производство конкретизируется в рамках каждого ремонтного органа в виде производственного процесса ремонта машины (агрегата).
Технология ремонта машин и ее элементов включает в себя понятие технологического процесса. Как инженерный термин это понятие определяет процесс непосредственного воздействия по содержанию объему и последовательности на ремонтный фонд с целью восстановления изделия соответствии с действующими техническими условиями. Технологический процесс как нормативный документ включает в себя технологические операции проводимые в определенной последовательности с целью обеспечения заданного уровня качества при наименьших затратах всех видов ресурсов.
Операции технологического процесса ремонта скрепера могут выполняться последовательно параллельно или последовательно-параллельно В зависимости от установленного порядка выполнения операций технологического процесса расположения технологического оборудования количества изделий и направления их движения в процессе ремонта или изготовления установлены две формы организации технологических процессов: групповая предусматривающая группирование изделий по конструктивно-технологическим признакам характеризующаяся единством средств технологического оснащения одной или нескольких технологических операций и специализацией рабочих мест. Группы изделий для обработки в определенном структурном подразделении цехе участке устанавливаются с учетом трудоемкости обработки и объема выпуска; поточная характеризующаяся специализацией каждого рабочего места на определенной операции размещением рабочих мест в последовательности строго соответствующей технологическому процессу согласованным и ритмичным выполнением всех операций технологического процесса на основе постоянства такта выпуска.
В зависимости от номенклатуры изделий выделяют одно- и многономенклатурную поточные линии. Однономенклатурная линия характеризуется обработкой изделия одного наименования и в зависимости от количества изделий может быть однопоточной или многопоточной. Поточные линии в зависимости от характера движения изделий по операциям могут быть прерывными и непрерывными.
Ремонт деталей скрепера может вестись по технологическому процессу разработанному на каждый дефект (подефектная технология) комплекс дефектов определенного сочетания возникающих на деталях данного наименования (маршрутная технология) и группу однотипных деталей определенного класса в соответствии с типовыми технологическими процессами (групповая или маршрутно-групповая технология).
Подефектной технологии присущи следующие недостатки: сложность расчета производственной программы и планомерной загрузки рабочих мест невозможность восстановления по данной технологии партии деталей громоздкость первичной документации и трудность учета трудовых и материальных затрат трудность обеспечении правильного своевременного и объективного контроля за соблюдением последовательности выполнения операций и за движением деталей. Подефектная технология применялась на первой стадии развития авторемонтного производства и сохранились лишь на небольших предприятиях.
Маршрутная технология предложенная К.Т. Кошкиным предусматривает устранение комплекса дефектов одной детали в определенной последовательности названной маршрутом. Партии деталей при маршрутной технологии не делятся перемещаются в процессе производства только по определенным маршрутам. В результате улучшается организация транспортных работ создаются условия для ритмичной работы и загрузки оборудования сокращается вспомогательное время упрощается система контроля и учета повышается качество работ снижается стоимость ремонта. В основе методики группирования сочетаний дефектов в маршруты лежит целесообразность наименьшее перемещение деталей (общность рабочих мест устранения дефектов) взаимосвязь дефектов наименьшая разница трудоемкости устранения дефектов. Для деталей одного наименования должно быть не более пяти маршрутов.
Применение маршрутной технологии целесообразно при централизованном ремонте деталей и в крупном специализированном производстве.
Маршрутно-групповая технология основана на использовании общих положений проектирования технологических процессов на основе классификации деталей и типизации процессов ремонта определенных групп деталей. При маршрутно-групповой технологии технологический процесс разрабатывается для групп деталей дефекты которых устраняются одними способами с последующей обработкой проводимой на однотипном технологическом оборудовании. В качестве представителя деталей данной группы для которой разрабатывается типовой технологический процесс выбирается характерная деталь структурные характеристики и дефекты которой наиболее полно отражают совокупность этих свойств у других деталей этой группы и создают возможность формирования маршрута. Маршрутно-групповая технология позволяет широко использовать групповые приспособления и настройку технологического оборудования для ремонта групп деталей. Это сокращает номенклатуру и количество необходимой технологической оснастки документации снижает трудовые затраты.
Групповые технологические процессы могут служить основанием для организации поточной формы организации технологического процесса
Реализация основных принципов организации производственных процессов виды и формы технологических процессов определяются конструктивной сложностью машин их ремонтопригодностью и технологичностью уровнем технологической оснащенности ремонтных предприятий видом ремонта и типом производства и другими условиями.
В зависимости от разнообразия номенклатуры регулярности стабильности и объема ремонта машин и агрегатов ремонтное производство может быть единичным серийным и массовым характеризующимся коэффициентом закрепления операций.
Коэффициент закрепления операций k представляет собой отношение числа всех различных технологических операций выполняемых в течение месяца к числу рабочих мест:
где n0 — число различных операций;
np — число рабочих мест для выполнения различных операций.
Для массового производства k=1 серийного k=1 40 единичного k>40.
Чем меньше значение k тем более совершенные технологические процессы могут быть применены в производстве.
В зависимости от вида ремонта машин и агрегатов различают технологические процессы текущего среднего и капитального ремонта машин текущего и капитального ремонта агрегатов. Наиболее полным является технологический процесс капитального ремонта машин остальные технологические процессы представляют собой его частные случаи.
Технологический процесс ремонта машин и агрегатов по этапам определяется схемой как правило последовательно а операции в них могут осуществляться последовательно последовательно-параллельно или параллельно.
Основными работами на этапе разборки являются моечно-очистные и выполняемые последовательно за ними разборочные операции. Очищенные от загрязнений детали дефектуются и сортируются по группам а затем направляются в специальной таре в комплектовочное отделение (годные) отделение деталей требующих ремонта или в утиль.
На следующем этапе выполняют ремонт деталей. Наибольшее распространение в ремонтных предприятиях получила маршрутная технология ремонта деталей. Основными видами работ при ремонте деталей являются наплавочные и сварочные а также электролитическое наращивание металла восстановление изношенных и поврежденных поверхностей клеевыми композициями термическая термохимическая и механическая обработка деталей восстановление поверхностей тонколистовыми вставками. Началом сборочного этапа является комплектация деталей и передача комплектов на рабочие места для сборки узлов и агрегатов. Сборка изделий начинается со сборки узлов и агрегатов которые в соответствии с техническими условиями могут подвергаться приработке и испытаниям. Принятые отделом технического контроля узлы и агрегаты передаются на сборку машины. Собранная машина подвергается испытанию. Обнаруженные дефекты устраняются машину красят и поставляют в отдел технического контроля. По завершении технологического процесса принятая машина ставится на хранение или сдается заказчику.
Технологический процесс среднего ремонта машин отличается от технологического процесса капитального ремонта объемом выполняемых операций. Так внешняя очистка и мойка машины выполняются в полном объеме а моют и чистят только те агрегаты и узлы которые отправляют в ремонт на предприятия для капитального ремонта или подвергаются текущему ремонту и обслуживанию в ремонтных подразделениях. В таком же порядке осуществляются разборочные работы дефектация и сортировка деталей и узлов. Почти полностью исключены работы по изготовлению деталей. Изготовляется лишь некоторая часть простейших и неответственных деталей. При ремонте простейших деталей выполняются в основном сварочные и наплавочные работы заварка трещин и разрывов поврежденных деталей заделка трещин клеевыми композициями слесарные и механические электротехнические медницко-жестяницкие кузнечные вулканизационные деревообделочные работы.
Ограничен объем работ и при сборке машин: собираются и регулируются лишь те агрегаты и узлы которые подвергались текущему ремонту.
Сборка машины осуществляется на готовых агрегатах. После испытания и устранения неисправностей машину подкрашивают и сдают заказчику.
Технологический процесс капитального ремонта двигателей и агрегатов имеет незначительные отличия от технологического процесса ремонта машины по последовательности операций и объему работ. Схема технологического процесса текущего ремонта машин и агрегатов представляет собой частный случай схем рассмотренных выше. Разборке мойке и дефектации подвергаются лишь неисправные и поврежденные узлы и агрегаты. Для восстановления изношенных и поврежденных деталей и узлов применяются те же способы что и при среднем ремонте машин. Для сборки используются подменные отремонтированные агрегаты восстановленные детали и узлы. Одновременно ведутся регулировочные и смазочные работы устраняются неисправности на неснимаемых с машины агрегатах узлах и приборах. Машину испытывают и подкрашивают после чего сдают заказчику.
Схема технологического процесса ремонта машины имеет графическую или текстуальную форму и включает в себя отдельные этапы всех видов работ по ремонту машины или агрегата. Эта схема раскрывает тот объем ремонтных воздействий который обязано сделать ремонтное средство. С использованием схемы определяется трудоемкость и количество рабочих необходимое для каждого этапа.
На основе определения числа работающих формируется организационная структура предприятия. На основе этой схемы трудоемкости отдельных этапов и числа рабочих формируются требования к структуре предприятия.
Расчет ремонтного предприятия
Основные исходные данные необходимые для планирования технического обслуживания и ремонта машин:
) Списочный состав парка машин эксплуатационного предприятия (5 экскаваторов ЭШ-6.545).
) Режим работы – 8 месяцев в году в одну смены.
) Коэффициент использования машин Кисп. = 075.
) Режим работ технической службы предприятия – круглый год в одну смену.
) Планировочное решение – зона текущего ремонта.
) Нормативные материалы по ТО и ремонту машин:
Таблица 6.1. Нормативные материалы по ТО и ремонту машин.
Вид технического обслуживания и ремонта
Периодичность выполнения технических обслуживаний и ремонтов ч
Трудоемкость выполнения одного технического обслуживания и ремонта чел.-ч
Продолжительность отдельного технического обслуживания и ремонта в рабочих днях
Нормативы периодичности трудоёмкости и продолжительности ТО и ремонта машин установлены по типам и маркам машин применительно к условиям их работы в организациях расположенных в центральной природно-климатической зоне имеющих в своём составе 100 200 машин различного типа и обеспеченных ремонтно-эксплуатационными базами. Для всех других условий работы машин нормативы корректируются с помощью коэффициентов k1 и k2 значения которых приведены в табл. 6.2.
Таблица 6.2. Коэффициенты корректировки нормативов
Количество машин в парке
Природно-климатические условия - районы холодного и жаркого климата
специализированный парк
Принимаем k1=105 и k2=115.
Средний удельный простой определяется по каждому виду воздействий с учётом того что в состав очередного ТО имеющего более высокий порядковый номер входят работы каждого предыдущего. Следовательно при совпадении например ТО-1 с ТО-2 учитывать ТО-1 не следует. Частота совпадений определяется отношением периодичностей выполнения соответствующих ТО. С учётом этого имеем:
где t1 t2 tтр tкр – периодичности проведения соответственно ТО-1 ТО-2 текущего и капитального ремонтов скорректированные в соответствии с условиями эксплуатации мото-ч;
D1 D2 Dтр Dкр – продолжительности проведения соответствующих технических воздействий дни простоя.
Для экскаватора ЭШ – 6.545:
Для обеспечения расчётного значения коэффициента технического использования необходимо регулярно проводить предусмотренные системой ППР воздействия в соответствии с установленными периодичностями.
Наработка машины в часах за планируемый период tпл прямо пропорциональна дням работы предприятия за этот период Dраб коэффициенту технического использования Kти равному 090 так как машины отдельные дни простаивают в ТО и ремонте а также среднесуточной наработке машин tсс:
tпл = Dраб Kти tсс (6.2)
tпл = 176 090 6 = 9504(ч)
При расчёте производственной программы определяют количество технических воздействий: ежедневных обслуживании ТО-1 ТО-2 ТО-3 сезонных обслуживании (СО) текущих (ТР) и капитальных ремонтов (КР) за плановый обычно годовой период. Производственная программа СО и ЕО определяется режимом использования машин. При разностороннем составе парка машин расчет программы ведётся отдельно по каждой группе однородных машин.
Годовое количество плановых технических воздействий на списочную численность парка машин Мc (для одной марки машин) составляет:
- капитальных ремонтов:
- текущих ремонтов (плановых):
- технических обслуживаний №3:
- технических обслуживаний №2:
- технических обслуживаний №1:
- сезонных обслуживаний:
- ежедневных обслуживаний (определяется только для количества машин ежедневно возвращающихся на базу):
В формуле (6.9) Кти учитывает обязательное проведение ЕО перед каждым плановым воздействием т.е. Nсо определяет количество самостоятельных ЕО. Количество и разновидности диагностических воздействий определяются принятым местом диагностики в технологическом процессе ТО и ремонта машин.
Годовой объём работ выполняемых в эксплуатационном предприятии включает прежде всего работы по ТО и ремонту машин а также работы связанные с обслуживанием самого предприятия.
Годовой объём работ (в чел.-ч) по ТО и ремонту определяется по каждому виду технических воздействии раздельно для каждого типа машин.
Годовой объём работ:
где ТЕО Т1 Т2 Ттр Ткр – трудоемкости выполнения соответствующих технических воздействий (чел.-ч) скорректированные в соответствии с условиями эксплуатации.
Для скрепера МоАЗ-546П:
В эксплуатационном предприятии может предусматриваться капитальный ремонт несложных машин и оборудования. Объём этих работ принимается в размере 25% от трудоёмкости капитального ремонта машин.
Годовой объём выполняемых в эксплуатационном предприятии плановых работ по ТО и ремонту для одной 1-ой марки машин определяется по формуле:
Для экскаватора ЭШ – 6545:
Правила хранения экскаватора ЭШ – 6.545.
Экскаватор должен храниться в закрытых помещениях или под навесом. Допускается хранение на открытых оборудованных площадках при обязательном выполнении работ по консервации герметизации и снятию составных частей требующих складского хранения.
Не допускается хранение экскаватора и его составных частей в помещениях содержащих (выделяющих) пыль примеси агрессивных паров или газов.
При межсменном хранении допускается хранение экскаватора на площадках и пунктах межсменного хранения или непосредственно на местах проведения работ.
Экскаватор необходимо поставить на кратковременное хранение не позднее чем через 10 суток после окончания работ. Экскаваторов ставится на кратковременное хранение комплектно т.е. без снятия с него сборочных единиц и деталей.
Экскаватор ставят на хранение:
межсменное - перерыв в использовании до 10 суток;
кратковременное - от 10 суток до 2 месяцев;
длительное - более 2 месяцев.
При подготовке к кратковременному хранению необходимо:
- очистить экскаватор от пыли грязи и подтеков масла;
- провести консервацию двигателя в соответствии с указаниями инструкции по эксплуатации;
- плотно закрыть все отверстия и щели через которые атмосферные осадки могут попасть во внутренние полости экскаватора;
- открыть сливные краники для обеспечения свободного выхода охлаждающей жидкости из системы охлаждения и конденсата;
- отключить аккумуляторные батареи уровень и плотность электролита должны быть доведены до нормы (в случаях хранения экскаватора при низких температурах или свыше 1 месяца аккумуляторные батареи должны быть сняты и сданы на склад);
- нанести смазку ПВК ГОСТ 19537-87 на поверхности рабочих органов экскаватора а также на внешние сопрягаемые механически обработанные поверхности;
- обернуть парафинированной бумагой и обвязать шпагатом сапуны на картерах и пробки заливных горловин;
- обернуть полиэтиленовой пленкой и обвязать шпагатом заборники воздухоочистителей;
- восстановить места повреждений окраски;
- закрыть и опломбировать капот;
При подготовке экскаватора к длительному хранению выполнить требования кратковременного хранения.Для длительного храненияэкскаватора необходимо:
- слить масло из всех емкостей и залить свежее масло с антикоррозийными присадками. Масло должно быть обезвожено нагревом до устранения пенообразования;
- слить топливо из топливного бака подвесить мешочек с силикагелем (200 300 г) или заполнить бак обезвоженным топливом;
- смазать экскаватор согласно карте смазки;
- очистить от следов коррозии рабочую поверхность шкива привода компрессора ослабить натяжение ремня;
- наклеить бумажную этикетку с указанием даты консервации.
- очистить экскаватор от пыли;
- удалить парафинированную бумагу;
- очистить наружные поверхности деталей и механизмов от смазки ПВК;
- установить аккумуляторные батареи;
- провести ежесменное техническое обслуживание экскаватора.
Особенности эксплуатации машин при низких температурах.
Эксплуатация машин при низких температурах снижает их работоспособность в 12-15 раза. При отрицательных температурах ухудшаются условия смесеобразования сгорания смеси пусковая надежность двигателя и самочувствие машинистов увеличивается момент сопротивления вращению всех деталей возрастает число отказов машин.
Повышение вязкости топлива в 5-10 раз при понижении температуры от 20 до -20°С приводит к снижению прокачиваемости степени и однородности распыливания. Хорошие распыливание испарение и смесеобразование обеспечиваются если вязкость топлива составляет 2-8 мм2с. Практикуется утепление топливных баков обмазкой такого состава; асбестовая крошка — 35% сухие опилки 40% огнеупорная глина — 20% жидкое стекло — 5%.
Предварительно на бак накладывают арматуру из проволоки и наносят указанный состав слоем 15-25 мм. После сушки бак обертывают матерчатой лентой и покрывают краской. Топливопроводы утепляют лентами из грубошерстной ткани и сверху лентами из парусины с последующим покрытием водомаслостойкой краской.
Затруднение запуска двигателя связано со сложностью создания пусковой частоты и низкой температурой в конце сжатия. Минимальная частота вращения обеспечивающая запуск зависит от температуры окружающей среды и типа двигателя.
При отрицательных температурах ухудшается самочувствие машиниста наблюдается быстрая утомляемость замедляется реакция на сложные ситуации. Для повышения его работоспособности утепляется рабочее место и предотвращается обледенение стекол. Для нормальной работы машиниста температура в кабине должна быть в пределах 14-18°С поэтому в зимний период кабину герметизируют стены и попы утепляют устанавливают обогреватели.
Промышленностью выпускаются автономные отопительные установки работающие на бензине (О15 и О30) или на дизельном топливе (ОВ65 и ОВ95). Для отопления кабины можно использовать тепло двигателя внутреннего сгорания через систему смазки или охлаждения. Для исключения обледенения стекол и обеспечения видимости применяют обдув стекол теплым воздухом или смазывают их соляно-глицериновой смесью.
Повышение вязкости смазочных материалов с понижением температуры приводит к потерям до 50% мощности вследствие увеличения сил трения в сопряжениях. В отдельных случаях начало движения невозможно без предварительного подогрева. При отрицательных температурах необходимо применять масла с загущающими присадками.
При эксплуатации скрепера МоАЗ-546П можно применять смеси трансмиссионных масел с дизельным топливом а моторных масел - с бензином. Количество бензина необходимое для разжижения масла зависит от температуры окружающей среды и вместимости системы смазки.
До разогрева масла в процессе работы детали в агрегатах работают без достаточной смазки что повышает вероятность их отказа. Так интенсивность изнашивания шестерен трансмиссии при температуре масла ниже 5°С на порядок выше чем при температуре 35°С.
Общий износ двигателя за период пуска и разогрева до оптимальной температуры равноценен его работе на установившемся режиме в течение смены. Работа двигателя с температурой охлаждающейся жидкости до 40°С приводит к уменьшению мощности на 6-9% и увеличению расхода топлива на 7-75%.
На гидрофицированных машинах при отрицательных температурах ухудшается работа гидропривода. Повышение вязкости рабочих жидкостей вызывает разрывы сплошности потока и подсос воздуха что приводит к гидравлическим ударам в гидросистеме износу и выходу из строя ее элементов.
В зимний период эксплуатации наблюдаются отказы пневмосистем из-за конденсации влаги что вызывает образование ледяных пробок в трубопроводах заклинивание поршней в пневмоцилиндрах.
При отрицательных температурах увеличивается вязкость электролита что ухудшает проникновение его в поры пластин и приводит к резкому падению емкости аккумуляторной батареи. Особенно отрицательно это явление сказывается при запуске двигателя когда зимой требуется более высокая частота вращения.
При охлаждении всех резиновых изделий нарушается их уплотняющая способность. В шинах в зимний период теряется упругость возникает остаточная деформация которая приводит к появлению трещин и расслоению.
В ходе выполнения курсовой работы были закреплены и обобщены полученные знания по курсу «Эксплуатация и ремонт строительных машин» Основными задачами курсового проектирования являются:
- изучение основных операций технического обслуживания и ремонта строительных машин;
- закрепление знаний об используемых методиках расчёта;
- выработка умений и навыков принятия обоснованных решений по результатам расчетов;
- закрепление навыков использования специальной технической нормативной и справочной литературы.
На основании проведенной работы можно сделать выводы:
) несмотря на огромные достижения в области ремонта машин в нашей стране открываются новые перспективы ее развития для реализации которых необходимо привлечение молодых специалистов.
) ремонтные мероприятия позволяют восстановить утраченную работоспособность машины или ее деталей. Их актуальность обусловлена большими материальными затратами на приобретение нового оборудования.
Список используемой литературы:
Васильев Б.С. и др. Ремонт дорожных машин автомобилей и тракторов.- М.: Издательский центр «Академия» 2006.
Зайков В.И. Берлявский Г.П. «Эксплуатация горных машин и оборудования» В.И. Зайков Г.П. Берлявский– Москва 1972. – 504 с.
Герике Б.Л. «Диагностика горных машин и оборудования» Б.Л. Герике. – Москва 1972. – 504 с.
Подерни Р.Ю. Механическое оборудование карьеров. Издательство
Московского государственного горного университета 2007. – 680 с.
Инструкция по эксплуатации экскаватора ЭШ – 6.545.