Мобильная бурильная установка




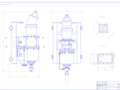
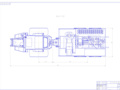
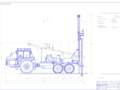
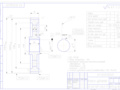
- Добавлен: 25.10.2022
- Размер: 5 MB
- Закачек: 2
Описание
Состав проекта
![]() |
![]() |
![]() ![]() ![]() ![]() |
![]() ![]() ![]() |
![]() ![]() ![]() |
![]() ![]() ![]() |
![]() ![]() ![]() ![]() |
![]() ![]() ![]() |
![]() ![]() ![]() ![]() |
![]() ![]() ![]() ![]() |
![]() ![]() ![]() ![]() |
![]() ![]() ![]() |
![]() ![]() ![]() |
![]() ![]() ![]() ![]() |
![]() ![]() ![]() ![]() |
![]() ![]() ![]() |
![]() ![]() ![]() ![]() |
![]() ![]() ![]() |
![]() ![]() ![]() |
![]() ![]() ![]() |
![]() ![]() ![]() |
![]() ![]() ![]() ![]() |
![]() ![]() ![]() |
![]() ![]() ![]() ![]() |
![]() ![]() ![]() ![]() |
![]() ![]() ![]() |
![]() ![]() ![]() ![]() |
![]() ![]() ![]() ![]() |
![]() |
![]() ![]() ![]() |
![]() ![]() ![]() |
![]() ![]() ![]() |
![]() ![]() ![]() |
![]() ![]() ![]() |
![]() ![]() ![]() |
![]() ![]() ![]() |
![]() ![]() ![]() |
![]() ![]() ![]() |
![]() ![]() ![]() |
![]() ![]() ![]() |
![]() ![]() ![]() |
![]() ![]() ![]() |
![]() ![]() ![]() |
![]() |
![]() |
![]() |
![]() |
![]() |
![]() |
Дополнительная информация
Редуктор-разрез.cdw

Шестерня.dwg
Неуказанные предельные отклонения размеров:
Точность зубчатого колеса в соответствии с ГОСТ 1643-81
Угол наклона линии зуба
Дл. общ. норм. на 5 зуб.
Сборка-вал.cdw

Вид сбоку.cdw

Монтажно-транспортная база
Габаритные размеры агрегата
в транспортном положении
Технические требования:
Использование изделия.cdw

Система высот Балтийская.
Сплошные горизонтали проведены через 0
Съёмка карьера Овсище дана по состоянию на 1988 г.
Сетки расположения геологоразведочных скважин в зависимости от необходимой
Количество скважин: 6
Количество скважин: 11
Количество скважин: 21
Условные обозначения:
Линия геолого-литолического разреза.
Контур подсчёта запасов по категории В.
Граница карьерного поля.
Скважина. Справа-номер выработок и абсолютная отметка их устьев в метрах.
Слева-мощность вскрышных работ в м.;
мощность сухой песчано-гравийной смеси в м.;
мощность обводнной песчано-гравийной смеси в м.;
содержание граия размером более 5 мм в %.
Вверху над выработкой вид опробования.
Внизу под выработкой глубина появления вод.
Контур подсчёта запасов по категории С
Технологическая схема работы
Эскиз1.frw

Шестерня.cdw

Неуказанные предельные отклонения размеров:
Точность зубчатого колеса в соответствии с ГОСТ 1643-81
Угол наклона линии зуба
Дл. общ. норм. на 5 зуб.
Кинематика переделанная.cdw

Привод синхронного ВОМ
Гидронасос 310.356-03
Шина пневматическая 60055-26.5
Шина пневматическая 30
Вращатель.cdw

Кинематика.dwg
Гидромотор 3103.112-00
Гидродомкрат подачи
Привод синхронного ВОМ
Схема кинематическая
Кинематика переделанная.dwg
Привод синхронного ВОМ
Гидронасос 310.356-03
Шина пневматическая 60055-26.5
Шина пневматическая 30
Наука.dwg
режимных параметров бурения
Графики основных зависимостей расчёта
режимных параметров шнекового бурения
Минимальная частота вращения шнека
Максимальная теоретическая производительность шнека
необходимый для обеспечения подъёма породы шнеком
Мощность двигателя вращателя
Техническая скорость шнекового бурения
учитывающий затупление инструмента
величина заглубления шнека
приведенный предел прочности породы
Потребное усилие подачи на долото
для разрушения породы
Потребный момент вращения долота
необходимый для разрушения породы
количество зубьев на долоте;
– коэффициент трения породы о сталь;
угол наклона винтовой линии шнека;
– коэффициент трения породы о породу;
– предельная частота вращения долота;
– диаметр вала шнека;
коэффициент просыпания породы в зазор между шнеком и
– предельная частота вращения долота;
– коэффициент разрыхления породы;
глубина бурения породы;
– показатель буримости породы.
Частота вращения долота
Результаты предпроектных исследований
Результаты анализа рабочего процесса агрегата бурильного
Расчётная схема исполнительного органа агрегата бурильного
Основные расчётные зависимости:
Матрица плана многовариантного расчетного анализа параметров бурения:
Вид сбоку.dwg
Монтажно-транспортная база
Габаритные размеры агрегата
в транспортном положении
Технические требования:
Кинематика.cdw

Гидромотор 3103.112-00
Гидродомкрат подачи
Привод синхронного ВОМ
Схема кинематическая
Использование изделия.dwg
Система высот Балтийская.
Сплошные горизонтали проведены через 0
Съёмка карьера Овсище дана по состоянию на 1988 г.
Сетки расположения геологоразведочных скважин в зависимости от необходимой
Количество скважин: 6
Количество скважин: 11
Количество скважин: 21
Условные обозначения:
Линия геолого-литолического разреза.
Контур подсчёта запасов по категории В.
Граница карьерного поля.
Скважина. Справа-номер выработок и абсолютная отметка их устьев в метрах.
Слева-мощность вскрышных работ в м.;
мощность сухой песчано-гравийной смеси в м.;
мощность обводнной песчано-гравийной смеси в м.;
содержание граия размером более 5 мм в %.
Вверху над выработкой вид опробования.
Внизу под выработкой глубина появления вод.
Контур подсчёта запасов по категории С
Технологическая схема работы
Наука.cdw

режимных параметров бурения
Графики основных зависимостей расчёта
режимных параметров шнекового бурения
Минимальная частота вращения шнека
Максимальная теоретическая производительность шнека
необходимый для обеспечения подъёма породы шнеком
Мощность двигателя вращателя
Техническая скорость шнекового бурения
учитывающий затупление инструмента
величина заглубления шнека
приведенный предел прочности породы
Потребное усилие подачи на долото
для разрушения породы
Потребный момент вращения долота
необходимый для разрушения породы
количество зубьев на долоте;
– коэффициент трения породы о сталь;
угол наклона винтовой линии шнека;
– коэффициент трения породы о породу;
– предельная частота вращения долота;
– диаметр вала шнека;
коэффициент просыпания породы в зазор между шнеком и
– предельная частота вращения долота;
– коэффициент разрыхления породы;
глубина бурения породы;
– показатель буримости породы.
Частота вращения долота
Результаты предпроектных исследований
Результаты анализа рабочего процесса агрегата бурильного
Расчётная схема исполнительного органа агрегата бурильного
Основные расчётные зависимости:
Матрица плана многовариантного расчетного анализа параметров бурения:
Вид сверху.cdw

Гидравлика.dwg
Клапан обратный Г51-31
Клапан обратный Г51-35
Клапан предохранительный МКПВ 103С2Р2
Клапан предохранительный МКПВ 203С2Р2
Клапан предохранительный У 462.8 7
Распределитель Рн203-ФМ14
Распределитель Р103 В 64
Манометр МП3; р=250; кл. 2
Гидроцилиндр подъёма мачты
Гидроцилиндр домкрата опорного
Гидроцилиндр механизма подачи
Схема гидравлическая
Гидравлика.cdw

Клапан обратный Г51-31
Клапан обратный Г51-35
Клапан предохранительный МКПВ 103С2Р2
Клапан предохранительный МКПВ 203С2Р2
Клапан предохранительный У 462.8 7
Распределитель Рн203-ФМ14
Распределитель Р103 В 64
Манометр МП3; р=250; кл. 2
Гидроцилиндр подъёма мачты
Гидроцилиндр домкрата опорного
Гидроцилиндр механизма подачи
Схема гидравлическая
Эскиз2.frw

6. Охрана труда.doc
1.1 Актуальность охраны труда
Охрана труда – это система законодательных актов социально-экономических организационных технических гигиенических лечебно-профилактических мероприятий и средств обеспечивающих безопасность сохранение здоровья и работоспособность человека в процессе труда.
Законодательство по охране труда представляет собой правовую основу при проведении организационных технических и санитарно-гигиенических мероприятий направленных на создание безопасных высокопроизводительных условий труда [1].
На каждом предприятии в любом производстве и при различных видах деятельности очень часто имеют место аварии несчастные случаи и производственный травматизм поэтому особенно актуальным является вопрос охраны труда.
Во избежание аварий несчастных случаев и производственного травматизма в настоящее время на каждом предприятии обязаны: обеспечивать контроль за охраной труда; создавать работникам здоровые и безопасные условия труда; осуществлять контроль общей системы правления профилактической работой в организации по предупреждению производственного травматизма профессиональных и производственно обусловленных заболеваний улучшению условий труда работников; организовывать планирование мероприятий направленных на создание безопасных и здоровых условий труда и контролировать их выполнение; контролировать соблюдение действующего законодательства по охране труда; контролировать соответствие вводимых в эксплуатацию новых и реконструированных объектов требованиям норм и правил охраны труда; контролировать организацию и своевременное проведение обучения по охране труда и переаттестации специалистов предприятия а также руководителей организации их заместителей главных инженеров руководителей служб и подразделений специалистов службы охраны труда .
1.2 Техника безопасности при работе буровых станков.
Рабочее место - место постоянного или временного пребывания работника в процессе трудовой деятельности. Рабочим местом называют ограниченную зону рассчитанную на одного или нескольких человек занятых выполнением одной работы или операции [2].
Высокопроизводительная работа возможно лишь при правильной организации рабочего места заключающейся в правильном расположении средств производства инструментов и приспособлений рациональном расположении рычагов управления. От правильной организации рабочего места зависят также безопасность работы и повышение производительности труда.
Рабочее место делится на основную (рабочую) зону и вспомогательную. При организации рабочего места в первую очередь требуется учитывать безопасность работ принятый метод обслуживания и основные преимущества и недостатки того или иного типа оборудования.
К работе на буровом станке допускаются только лица прошедшие специальное обучение сдавшие техминимум прошедшие стажировку на рабочем месте и получившие права на управление станком. Доступ посторонних лиц к управлению агрегатом категорически запрещается.
Запрещается подъём и опускание мачты а так же все работы при неисправной гидросистеме.
Скорость передвижения агрегата не более 50 кмч боковой крен не более 15 градусов наибольший угол подъёма и спуска агрегата не более 25 градусов.
При транспортировании агрегата рукоятки всех органов управления агрегатом должны находиться в нейтральном или выключенном положении.
Бурильные работы при ветре более 15 мс и более во время ливня сильного снегопада и тумана с видимостью менее 50 м запрещаются.
Запрещается эксплуатация агрегата при нагрузках и давлениях превышающих допустимые а так же при температуре ниже минус 40º С.
На крепёжных узлах и деталях должны быть предусмотрены приспособления (контрагайки шплинты клинья и др.) предотвращающие во время работы самопроизвольное раскрепления и рассоединение.
Не допускается эксплуатация оборудования и механизмов:
При разрушении элементов системы;
При давлениях и нагрузках выше паспортных;
При любых повреждениях или отказах манометров и других измерительных приборов;
При появлении наружних утечек;
При появлении повышенного шума стука вибрации;
При неисправных устройствах безопасности (блокировочные фиксирующие и сигнальные приспособления и приборы).
Перед началом работ агрегат должен быть заземлён.
Не допускается работа на агрегата:
С неисправным инструментом;
С незаконтрагаенными аутригерами;
Со светильниками без защитного стекла и ограждения.
Перед началом работ необходимо предупредить персонал подачей звукового сигнала.
1.3 Опасные и вредные производственные факторы
Техника безопасности – система организационных и технических мероприятий и средств предотвращающих воздействие на работающих опасных производственных факторов.
Опасный производственный фактор – это такой фактор воздействие которого на работающего приводит к резкому изменению состояния здоровья [3].
Производственная санитария - система организационных санитарно-гигиенических мероприятий технических средств и методов предотвращающих или уменьшающих воздействие на работающих вредных производственных факторов до значений не превышающих допустимые.
Вредный производственный фактор – это такой фактор систематическое воздействие которого на работающего приводит к профессиональному заболеванию.
При ведении буровых работ на калийных и соляных горизонтах возможны обрушения пород кровли и газовыделение из пласта вмещающих пород отработанного пространства.
метод регионального прогнозирования зон опасных по газодинамическим явлениям с помощью математических моделей;
региональное и локальное управление газодинамическими процессами в зонах геологических нарушений.
К вредным производственным факторам машинистов бурильных установок можно отнести следующие:
Бурение является основным источником пылевыделения при ведениии горных работ на карьерах. Количество выделяемой пыли по результатам измерений: на рабочем месте машиниста бурильного агрегата – 57 - 400 мгм3. Оно зависит в значительной степени от направления и скорости движения воздуха.
Мероприятия по борьбе с пылью проводятся в нескольких направлениях: применение средств предупреждения пылеобразования снижение его интенсивности и удаление пыли путём естественного или искусственного проветривания. При бурении предупреждение избыточного выделения пыли достигается использованием метода сухого пылеулавливания с полнлй или частичной схемой очистки воздуха от пыли а так же применение мокрого бурения.
Методы борьбы с пылью:
монтаж на корпусе оборудования пылеотсасывающей установки всасывающе-нагнетательного действия;
орошение водой через форсунки из специальной гидросистемы бурильного става;
в качестве дополнительных средств защиты органов дыхания человека от пыли используются противопылевые респираторы.
Применение бурильной техники в той или иной степени сопровождается шумом и вибрацией . Их характеристики зависят от типа машин цикла работы степени изношенности механизмов твёрдости горной массы благоустройства кабины.
На буровых станках различных типов уровень шума в кабине машиниста и на рабочей площадке колеблется от 93 до 105 дБ.
Всё бурильное оборудование является источниками апериодической непостоянной непостоянной средне- и низкочастотной вибрации. Наиболее выражена общая вибрация на станках шарошечного бурения: она превышает допустимые уровни для рабочих мест.
Технические мероприятия по снижению шума и вибрации должны проводить как правило предприятия – изготовители горной техники и в порядке исключения – её потребители.
Среди технических мероприятий различают активный (под которым понимаются все методы снижения шума в источнике возникновения ) и пассивный способ включающий все строительно-акустические методы уменьшения шума возле источника на пути его распространения от источника к рабочему месту и на самом рабочем месте [4].
Технические меры по снижению вибрации на бурильных станках сводится к борьбе с самовозбуждающимися колебаниями снижению вибрации в источнике возникновения виброизоляции и виброгашению.
В настоящее время имеется большое число конструкций кресел для машинистов с различными типами амортизаторов.
Места частого пребывания рабочих должны иметь коврики или настилы из виброгасящего материала. Оптимальным в гигиеническом отношении является дистанционное управление машинами и оборудованием с созданием благоустроенных мест управления.
1.4. Расчет времени за которое концентрация вредного вещества достигнет предельно допустимого значения (ПДК).
Исходные данные и начальные условия:
- фактическая концентрация вредного вещества в воздушной среде;
- функция приращения массы вредных веществ в воздухе;
мгс2 - коэффициент пропорциональности;
t с - определяемое время выполнения условия .
Закон превращения массы имеет вид:
Его можно так же представить в виде
Интегрируем полученное выражение:
Прологарифмируем полученное выражение
2 Пожарная безопасность
2.1 Причины возникновения пожара.
Пожар наносит большой материальный ущерб и очень часто сопровождается несчастными случаями с людьми.
Основными причинами способствующими возникновению и развитию пожаров являются: нарушение правил применения и эксплуатации приборов и оборудования с низкой противопожарной защитой; использование материалов не отвечающих требованиям пожарной безопасности; неисправность отопительных приборов; самовозгорание от неправильного хранения материалов; наличие статического электричества; отсутствие молниеотводов; неосторожное обращение с огнем; отсутствие на многих объектах и в подразделениях пожарной охраны эффективных средств борьбы с огнём [6].
Пожарная безопасность предусматривает комплекс организационных и технических мероприятий направленных на обеспечение безопасности людей предотвращение пожара ограничение его распространения а также создание условий для успешного тушения пожара.
Пожарная безопасность предусматривает: хранение транспортирование и содержание на рабочих местах огнеопасных жидкостей и растворов только в закрытых емкостях обеспечение успешной эвакуации людей и материальных ценностей из сферы пожара; создание условий эффективного пожаротушения.
2.2 Организационные мероприятия по обеспечению пожарной безопасности
Общие правила пожарной безопасности предусматривают соблюдение противопожарных режимов запрещается курение и разведение открытого огня вблизи агрегата. При возникновении пожара на рабочем месте рабочий обязан принять меры по тушению пожара всеми допустимыми средствами: песком породной мелочью огнетушителями. Запрещается тушить водой и пенными огнетушителями загоревшийся кабель или электрооборудование находящееся под напряжением. Во всех случаях воспламенения ликвидацию огня следует производить только после отключения электроэнергии питающей загоревшееся оборудование если есть такое.
Машинист бурильного агрегата обязательно должен знать Правила обращения с легко воспламеняющимися и горючими жидкостями.
Под горючей жидкостью понимается топливо смазочные материалы и тормозная жидкость используемые при эксплуатации машин и механизмов.
Вся тара предназначенная для хранения и перевозки горючих жидкостей должна быть металлической и иметь металлические резьбовые пробки и плотные крышки.
Наполненная и порожняя тара из-под горючих жидкостей должна быть постоянно закрыта.
Запрещено держать тару из-под горючих жидкостей помимо минимально необходимых для их хранения и перевозки а также использовать эту тару для посторонних целей.
2.3 Средства пожаротушения
Первичные средства пожаротушения – это такие средства которые используются в начальной стадии возгорания. Они предназначены для ликвидации начинающихся очагов пожара силами персонала обнаружившего возгорание. К первичным средствам пожаротушения относятся: огнетушители; пожарные щиты укомплектованные шанцевым инструментом; ящики с песком асбест войлок емкости с водой.
Основными первичными средствами пожаротушения являются огнетушители которые классифицируются следующим образом:
- по виду огнегасящего состава (жидкостные пенные порошковые аэрозольные комбинированные);
- по размеру и количеству огнетушащего состава (малолитражные промышленные ручные передвижные и стационарные);
- по способу выброса огнетушащего состава (под давлением самого заряда или рабочего газа находящегося над огнетушащим составом; под давлением газа находящегося в отдельном баллончике расположенном внутри или снаружи корпуса огнетушителя).
Переносные пенные огнетушители предназначены для тушения загораний твердых материалов органического происхождения (дерево бумага ткани) горючих жидкостей (масла битума) и плавящихся веществ (стеарин сера). Этот вид огнетушителя запрещено применять для тушения ценных материалов (книгохранилища картинные галереи музеи магазины и т.п.) т.к. химическая пена оставляет пятна и ожоги. Его также не применяют для тушения загораний в электроустановках т.к. струя пены является токопроводящей средой.
Углекислотные огнетушители бывают ручные стационарные и передвижные. Углекислый газ является незаменимым средством в тех случаях когда требуется потушить пожар в течение 2-10 секунд. При применении углекислотных огнетушителей необходимо учитывать токсичность СО2 т.к. при вдыхании воздуха с содержанием в нем 10 % СО2 наступает паралич дыхания и смерть что особенно опасно если учесть что газ не имеет запаха. Поэтому использовать углекислые огнетушители в непроветриваемых помещениях запрещено.
Порошковые огнетушители применяют для ликвидации пожаров всех классов. Огнетушители бывают 3 типов: ручные (переносные) возимые и стационарные. Порошки используются для тушения пожаров и загораний легковоспламеняющихся жидкостей газов древесины щелочных металлов алюминий- и кремнийорганических соединений и других пирофорных веществ.
В особо опасных в пожарном отношении производствах где требуется прекратить пожар в самом начале его возникновения используют спринклерные и дренчерные установки если в качестве огнегасящего вещества допустима вода.
Спринклерная система совмещает в себе функции системы подачи сигнала и тушения загорания.
Дренчерные установки используются для тушения пожаров в помещениях где требуется одновременно орошение площади создание водяных завес орошение отдельных элементов технологического оборудования.
Денисенко Г. Ф. Охрана труда: Учеб. Пособие: М.: Высш. Шк. 1985 – 319 с. ил.
Юдин Е.Я. Охрана труда в машиностроении М.: Машиностроение 1985.-520 с. ил.
Долин П. А. Справочник по технике безопасности. – 6-е изд. перераб. и доп. – М.: Энергоатомиздат 1984. –824 с. ил.
Средства защиты в машиностроении: Расчеты и проектирование: Справочник С. В. Белов А. Ф. Козьянов и др.; Под ред. С . В. Белова.-М.: Машиностроение 1989.- 368 с. ил.
Лазаренков А.М. Учебно–методическое пособие по дисциплине «Охрана труда» для студентов – заочников А. М. Лазаренков. – Мн.: БНТУ 2002. - 57 с.
ППБ РБ 1.01-94. Общие правила пожарной безопасности Республики Беларусь для промышленных предприятий. – Мн.: Фоиск 1995. – 68 с.
Реферат.doc
Дипломный проект: 119 с. 28 рис. 6 табл. 21 источник 2 прил.
Темой представленного дипломного проекта является агрегат бурильный.
Цель работы – разработка агрегата бурильного со шнековым рабочим органом для бурения геологоразведочных скважин глубиной до 30 м и диаметром до 180 мм на базе шарнирно-сочленённого тракторного шасси “Беларус” c колёсной формулой 6x6 и приводом бурильного оборудования от двигателя шасси.
В процессе проектирования разработана методика выбора оптимальных режимных параметров шнекового бурения и выполнены следующие исследования: произведен обзор и исследования существующих конструкций агрегатов бурильных произведен анализ недостатков и преимуществ аналогичных конструкций. Выполнена разработка конструкции изделия и произведен расчет основных параметров рассмотрено использование агрегата бурильного в производственных условиях разработан технологический процесс по ремонту зубчатого колеса рассмотрены мероприятия по технике безопасности и охране труда а также рассчитан экономический эффект при использовании разрабатываемого агрегата бурильного.
Областью возможного практического применения являются предприятия занимающиеся геологоразведкой а так же строительные организации.
Результатом внедрения явилась разработка кинематической схемы привода бурильного оборудования и привода задних колёс тракторного шасси от ВОМ тракторного шасси.
Студент-дипломник подтверждает что приведенный в дипломном проекте расчетно-аналитический материал объективно отражает состояние разрабатываемого объекта все заимствованные из литературных и других источников теоретические и методологические положения и концепции сопровождаются ссылками на их авторов.
Ведомость.doc
Задание по дипломному проектированию
Пояснительная записка
Схема кинематическая
Схема гидравлическая
Схема технологическая
Результаты предпроектных исследований
ДП - 10. 00. 00. 000
3. Использование компьютерных технологий.doc
В области конструирования и проектирования горной техники в данное время наблюдаются положительные изменения. Существующие системы автоматизированного проектирования позволяют значительно ускорить процессы разработки и конструирования. Самые современные механизмы разрабатываются в данное время с такой высокой скоростью которую раньше невозможно было представить а мощные программные средства предоставляют готовые решения отвечающие персональным требованиям заказчика. Новые технологии позволяют повышать надежность и качество продукции снижая при этом стоимость затрат на проектирование производства.
При выполнении проектных расчетов по выбору рациональных параметров бурильного агрегата а также при разработке конструкторской документации проекта многократно необходимо выполнять типовые проектные процедуры анализа и синтеза. Использование средств вычислительной техники позволяет существенно ускорить процесс проектирования горной машины сократить затраты труда проектировщиков повысить точность расчетов и качество проектирования в целом.
Для достижения эффекта от применения вычислительной техники была создана автоматизированная подсистема функционального проектирования бурильного агрегата которая включает программные модули-приложения обеспечивающие выполнение процедур моделирования его важнейших эксплуатационных свойств расчета анализа и оптимизации основных проектных параметров изделия и его составных частей синтеза схем функциональных систем объекта проектирования.
Основные задачи разработки АПФП состоят в создании инструментария реализации системного подхода в проектировании горной техники при котором оптимизируются структура объекта его внутренние и внешние связи.
Важнейшими показателями разрабатываемого изделия являются оценки его технического уровня и качества изготовления и входящие в формирование этой оценки показатели функциональных свойств надежности.
Под техническим уровнем понимается техническое совершенство конструкции изделия оптимальное значение функциональных параметров и другие показатели характеризующие данные разрабатываемого изделия (например техническая производительность машины затраты мощности на работу машины износостойкость и так далее) и определяющие во многом его конкурентоспособность.
Качество проектируемого изделия характеризуется как совокупность его свойств которые обусловливают пригодность изделия удовлетворять конкретные потребности в соответствии с назначением и определяется при сравнении показателей разрабатываемого изделия с показателями аналогичной продукции признанной наиболее совершенной в данной области техники отечественного и зарубежного производства.
Технический уровень и качество изделия закладывается на стадии проектирования и поэтому необходимо еще на ранних стадиях разработки иметь представление о будущем техническом уровне и качестве изделия что достигается применением современных методов проектной оценки качества и его оптимизации в том числе посредством использования автоматизированной подсистемы функционального проектирования данного вида горной техники.
На рис. 3.1 представлена структурная схемы АПФП агрегата бурильного.
Важнейшими показателями разрабатываемого бурильного агрегата является оценка его технического уровня и качества а также показателей функциональных свойств.
Под техническим уровнем понимается техническое совершенство конструкции изделия оптимальное значение функциональных параметров и другие показатели характеризующие данные разрабатываемого изделия (производительность габаритные размеры и т.д.) и определяющие во многом его конкурентоспособность.
Рис.3.1. Структурная схемы АПФП бурильного агрегата
Качество проектируемого изделия характеризуется как совокупность его свойств которые обуславливают пригодность изделия удовлетворять конкретные потребности подсистемы функционального проектирования бурильного агрегата. В соответствии с назначением и определяется при сравнении показателей разрабатываемого изделия с показателями аналогичной продукции признанной наиболее современной в данной области техники отечественного и зарубежного производства.
Рассмотрим блок-схему алгоритма (рисунок 3.2) автоматизированной системы функционального проектирования и многовариантного анализа рабочего процесса бурильного агрегата.
Рис.3.2 Обобщенная блок схема алгоритма работы АПФП бурильного агрегата
Блок 1.. Начало работы приложения.
Блок 2.. На экране ЭВМ выводится главное меню АПФП где отображаются все подменю расчетных и обрабатывающих данные процедур.
Блок 3.. С помощью устройств ввода вводится код выбора i-ой процедуры Блок 4.. Производится сравнение введенного кода с существующими кодами и переход к выполнению выбранной проектной процедуры (Блок 5 Блок п+1) либо выбор предлагается повторить.
Блок 8.. На дисплее выводится подменю например:
Блок 9.. Осуществляется выбор пункта подменю вводится код.
Блок 10.. Сравнение кода с существующими.
Блок 11.. Выполнение выбранной проектной задачи.
Блок 12.. Вывод полученных результатов на печать.
Затем осуществляется возврат АПФП в исходное положение - выводится главное меню находящееся в режиме ожидания.
С применением ЭВМ в рамках АПФП выполняют все виды расчетов по данному изделию разрабатывают конструкторскую документацию прогнозируют его надежность наблюдают рабочий процесс в динамике строят графики изменения значений одних физических величин от ряда исследуемых параметров будущего агрегата привлекая при этом возможности других программных приложений таких как MatLab MathCAD MAPLE. Mathematica - системы математического анализа со средствами визуального программирования. Excel - программа для создания электронных таблиц и их графических иллюстраций разной сложности а также универсальных программных приложений инженерного анализа (САЕ) ProMechanika ANSYS ADAMS NASTRAN EUCLID Mechanical Desktop CAT1A и многих других.
Далее представим (рисунок 3.3) подробную блок-схему алгоритма процедуры многовариантного анализа проектирования бурильного агрегата которая отражает оценку влияния основных режимных параметров бурения таких как:
– частота вращения бурильных шнеков;
– диаметр кважины и глубина бурения;
на выходные показатели установки разведочного бурения.
Рис.3.3 Блок-схема алгоритма работы процедуры многовариантного анализа проектирования агрегата бурильного.
Блок 1 Начало работы приложения.
Блок 2..Ввод исходных данных.
Блок 3..Начало цикла по диаметру долота.
Блок 4..Начало цикла по частоте вращения бурильных шнеков.
Блок 5..Начало цикла по глубине бурения.
Блок 6..Подпрограмма расчета выходных показателей бурения.
Блок 7..Вывод результатов на печать.
Блок 8..Завершение работы.
Таким образом использование средств автоматизации проектирования при разработке бурильного агрегата позволяет сократить время на разработку проекта изделия а также повысить качество проектирования. Предложенная автоматизированная подсистема функционального проектирования позволит существенно сократить затраты времени на выполнение основных проектных процедур функционального проектирования. Поэтому для выполнения проектных обоснований проходческого стрелового комбайна или оборудования и разработки конструкторской документации проекта целесообразно широко использовать средства автоматизации проектирования.
При выполнении раздела “Использование компьютерных технологий в проектировании изделия” было проведено вариантное исследование бурильного агрегата с целью выбора оптимальных параметров что было реализовано в разработанной машине.
Результаты исследований выполненные при помощи программ Microsoft Word и Microsoft EXCEL приведены на листе графической части дипломного проекта и в разделе 1.2 (Рис.1.2. – 1.4.) пояснительной записки.
1. Техническое обоснование и задание на проектирование изделия.doc
Шнековое бурение позволяет совместить операции непосредственно по бурению с удалением породы из забоя без применения промывки или продувки. Шнековый способ бурения имеет специфические особенности заключающиеся в том что удаление разрушенной породы производится не промывочной жидкостью а шнеками являющимися вертикальным винтовым транспортёром. Подача разрушенной породы на лопасть шнека производится долотом при наличии подпора нижних слоёв породы при её разрыхлении.
Таким образом при шнековом бурении долото выполняет две функции – разрушает породу и подаёт разрушенную породу на спираль шнека. Работа долота складывается из трёх операций:
внедрение рабочей части долота в породу под действием осевой нагрузки;
срез породы при вращении долота;
подача разрушенной породы на спираль шнека.
Если при использовании способов бурения с очисткой забоя скважины глинистым раствором или воздухом содержание разрушенной породы в стволе скважины едва достигает 2 – 4 % то при шнековом бурении оно составляет 10 – 20 %. Это обеспечивает высокие механические скорости бурения в мягких и рыхлых породах.
В связи с отсутствием необходимости применять при шнековом бурении промывку этот способ так же с успехом используется для проходки мелких скважин в безводных районах в многолетнемёрзлых породах и в зимнее время при отрицательных температурах.
Шнековое бурение ведётся как сплошным забоем так и кольцевым. В последнем случае удаётся получить образцы пород характеризующие геологическое строение данного участка.
К недостаткам шнекового бурения следует отнести относительно небольшую глубину бурения (30 – 50 м) невозможность бурения скважин в породах 7 категории по буримости и выше в породах с наличием твёрдых прослоев и валунов трудности бурения в грунтах ниже уровня подземных вод требующих применение других способов для проходки и закрепления этих грунтов трудности бурения шнеками в вязких и липких глинистых грунтах относительно большую энергоёмкость шнекового бурения.
Таким образом буровые станки шнекового бурения находят широкое применение в различных отраслях народного хозяйства а наибольшее распространение они получили при бурении геологоразведочных и взрывных скважин на открытых горных работах.
Учитывая устойчивую на длительный период времени перспективу применения буровых агрегатов в геологоразведке а так же при бурении: сейсморазведочных структурно-картировочных и водозаборных скважин инженерно-геологических изысканий и обустройства скважин при строительстве различных сооружений работы в данном направлении весьма актуальны.
ТЕХНИЧЕСКОЕ ОБОСНОВАНИЕ И ЗАДАНИЕ НА ПРОЕКТИРОВАНИЕ ИЗДЕЛИЯ
1.Требования предъявляемые к разрабатываемому изделию
В природных условия нашей страны где наблюдается большое количество лесов и болот что приводит порой к затруднениям при ведении горно-геологических работ к проектируемым мобильным бурильным установкам должны предъявляться следующие основные требования :
высокая мобильность и проходимость;
возможность проходки пород различных категорий;
возможность отбора проб пород и воды.
Здесь так же следует отметить что большое значение при шнековом бурении имеет буровой инструмент состоящий из бурового наконечника и комплекта шнеков. Существуют многочисленные типы буровых шнеков и долот.
Разнообразие конструкций бурового инструмента определяется геолого-техническими условиями его применения и назначения.
2.Исследование и выбор оптимальных режимных параметров бурения
При вращательном бурении порода разрушается под действием осевого усилия подачи Pос и крутящего момента передаваемого станком резцовому долоту. При этом осевое усилие должно преодолеть сопротивление породы внедрению торцовых площадок режущих лезвий долота даже при их затуплении а крутящий момент должен превысит сопротивление сколу участков породы прилегающим к передним режущим граням резца.
Техническое обоснование бурильного агрегата заключается именно в расчёте и выборе наиболее оптимальных режимных параметров бурения (толщины стружки h скорости бурения и частоты вращения шнека ) с последующим анализом производительности агрегата и затрат мощности на бурение.
Толщина стружки h (м) находится по формуле (1.1):
где Pос – осевое усилие кН
кз – коэффициент учитывающий затупление инструмента; к=1;
D – диаметр долота; D=0180 м. ;
– приведенный предел прочности породы; =20 МПа.
Зависимость толщины стружки от осевого усилия при заданных остальных параметрах представлена на рис.1.1.
Рисунок 1.1. Зависимость толщины стружки от осевого усилия
На практике для режущих долот устанавливаются нагрузки в пределах 8 – 16 кН. Приняв Pос=10 кН расчетное значение толщины стружки h=0011 м.
Прежде чем проводить дальнейшее исследование зададимся параметрами рабочего органа. При этом необходимо руководствоваться мощностью двигателя агрегата. Зависимость мощности необходимой для привода вращателя от диаметра скважины представлена на рис. 1.2.
Рисунок 1.2. Зависимость мощности привода вращателя от диаметра скважины
В качестве рабочего органа при шнековом бурении вместо бурильных труб используются шнеки которые при вращении транспортируют породу с забоя на поверхность.
Шнеком называется такой транспортёр в котором рабочим органом является винт вращающийся в неподвижной трубе (скважине). Шнек применяемый в бурении представляет собой полый вал с укрепленной на нём винтовой поверхностью из толстого листового железа. Снизу шнек несёт резец который разрушает породу забоя. Ввинчиваясь в породу как в гайку шнек передвигает её к поверхности по своим винтовым линиям.
Итак в качестве резца примем режущее двухпёрое долото РК4М из хромоникелевой стали 12ХН2 (ГОСТ 1245-83 ) с диаметром D = 180 мм позволяющее бурить породы с приведенным пределом прочности = 20 МПа.
Наружный диаметр шнека D1 для уменьшения трения о стенки скважины должен быть приблизительно на 10% меньше диаметра долота. Принимаем D1=0160 м.
Ход винтовой линии шнека Н составляет в среднем (11-12) D1. Принимаем Н=175 мм.
Для проведения исследования и выбора рациональных проектных параметров построим и проанализируем графические зависимости v = f(D) v = f(n) при этом следует учитывать что выбираемые параметры должны лежать в интервалах указаных в скобках поскольку это наиболее рациональные пределы значений данных величин и также они должны приблизительно давать заданную производительность поскольку в сумме по всем параметрам мы должны выйти на требуемую производительность.
Рассмотрим сперва зависимость v = f(D) представленную на рис.1.3.
Рисунок 1.3 Зависимость v = f(D)
Полученная зависимость в ходе реализации математической модели бурильного агрегата позволяет установить что при заданном диаметре долота D=180 мм установка сможет обеспечить заданную производительность Q=45 м. пог.ч.
Далее уже задавшись диаметром скважины проследим как же будет влиять частота вращения бурильного става на производительность. Эта зависимость представлена на рис. 1.4.
При выборе частоты вращения будем руководствоваться условием возможности нормального удаления породы из скважины для этого принимаем частоту вращения n=2 c-1.
Рисунок 1.4 Зависимость v = f(n)
3. Техническое задание на разработку бурильного агрегата
Наименование и область применения (использования) изделия
Наименование изделия
-Согласно заявок по заключенным контрактам
Основание для разработки
-Задание Министерства промышленности РБ.
-Требования потребителей РБ и внешнего рынка по расширению гаммы бурильных агрегатов.
-Тематический план РУП «Белгеология»
Цель и назначение разработки
-Создание конкурентоспособного на внешнем рынке бурильного агрегатаой для оснащения геологоразведочной отрасли
Бурение разведочных скважин глубиной до 30 м и диаметром до 180 мм
Источник разработки и финансирования
Источники разработки
-Исходные требования Минпрома РБ
-Анализ состояния рынков бурильных агрегатов
-Анализ технологических принципов горных производств и тенденций их развития
-Анализ материалов по бурильным агрегатам выпускаемым другими фирмами и тенденции их развития
-НИиОКР проводимые в БНТУ на кафедре «Горные машины» с математическими моделями бурильных агрегатов
Источники финансирования
-50 % средства РУП «Белгеология»
Технические требования
Состав продукции и требования к устройству:
Агрегат бурильный расположенный на колёсном шасси 6Х6 шарнирно-сочленнёном на базе трактора МТЗ. Привод бурильного ротора осуществляется от ВОМ шасси.
Показатели назначения и экономного использования сырья материалов топлива и энергии
Суммарная установленная мощность
Требования к надежности
Ресурс до первого капитального ремонта
Наработка на сложный отказ единичного изделия
Суммарная трудоемкость технического обслуживания за 1000 часов наработки
Коэффициент готовности
Требования к технологичности
Число сортов масел и смазок применяемых для дробилки
Удельная трудоемкость изготовления
Компоновка узлов мест регулировок и обслуживания должна обеспечивать удобство их осмотра и проведения регламентных работ
Коэффициент сборности
Требования к уровню унификации и стандартизации
Коэффициент стандартизации изделия
Коэффициент применяемости
Требования по безопасности и экологии
Конструкция агрегата обеспечивать травмобезопасность обслуживающего персонала отвечать требованиям ССБТ
Эстетические и эргономические требования
Конструкция агрегата бурильного должна соответствовать тенденциям современного дизайна ГПО по всем частным показателям с оценкой не ниже 35 балла
Эргономические показатели агрегата должны соответствовать ССБТ и стандартам ИСО 3000-ой серии
Требования к патентной чистоте
Агрегат бурильный должен обладать патентной чистотой в отношении стран предполагаемого экспорта
Техническое решение агрегата должно быть защищено патентами РБ
Требования к составным частям продукции (при их наличии)
исходным и эксплуатационным материалам
Ограждения безопасности должны быть окрашены согласно требованиям стандартов ССБТ
Категория крепости буримой породы
Условия эксплуатации (использования) требования к техническому обслуживанию и ремонту (при необходимости)
Условия эксплуатации – воздействие климатических факторов внешней среды по ГОСТ 15150-69
Вид обслуживания – плановое периодическое: ежедневное через 125 250 500 1000 часов работы и общее. Работа без обслуживания не допускается
Количество и квалификация персонала для работы – один оператор 2-го разряда
Агрегат должен быть приспособлена к техническому диагностированию по ГОСТ 24925-81
Требования к маркировке и упаковке
На агрегате и основных узлах должны быть нанесены порядковые номера на ЗИП – маркировка по ГОСТ 14192-77
Агрегат должен отгружаться потребителю без упаковки а ЗИП – упакованным в ящик по ГОСТ 2991-85 и ГОСТ 15841-87
Требования к транспортированию и хранению
Агрегат бурильный вместе с ящиком ЗИП должен быть приспособлен к транспортированию железнодорожным автомобильным путем
Консервация агрегата и ЗИП должна обеспечивать срок хранения не менее одного года для жесткой категории хранения и транспортирования
Погрузка и крепление агрегата и ящика ЗИП в соответствии с техническими требованиями на виды перевозок
Хранение агрегата в соответствии с ГОСТ 7751-85
Дополнительные и специальные требования
-Агрегаты предназначенные для экспорта и работы в зонах с тропическим или заполярным климатом должны быть подвергнуты дополнительной отделке поверхностей и комплектации узлами и деталями под эти условия эксплуатации не влияющими на взаимозаменяемость деталей и узлов обычного исполнения
Экономические показатели
Предварительная цена бурильного агрегата 55000 долларов США
Стадии и этапы разработки
Согласование и утверждение ТЗ.
Разработка технического проекта
Рабочая документация
Разработка рабочего проекта
(заводские) испытания
Изготовление опытных образцов.
Проведение лабораторных и эксплуатационно-технологических испытаний.
При положительных предварительных испытаниях образцы их проходящие переводятся на приемочные испытания.
Доработка КД по результатам приемочных испытаний и проверка КД на технологичность.
Выпуск установочной партии агрегатов.
Проведение квалификационных испытаний.
Выдача документации службам завода для ведения подготовки производства.
Порядок контроля и приемки материалы предъявляемые
по окончании отдельных стадий (этапов) и работы в целом
-Порядок контроля качества продукции и приемки ее заказчиком осуществляется по стадиям и этапам соответствующими службами производственного контроля в соответствии с согласованными техническими условиями на изготовление продукции и СТБ 972-94.
Количество изготавливаемых опытных образцов
-изготавливается два опытных образца
Сроки выполнения работ
-Основные сроки выполнения работ определяются планом НИиОКР РУП «Белгеология» и директивными документами Минпрома РБ.
Маршрутная карта.doc
Код наименование операции
Обозначение документа
Код оборудования модель инвентарный номер
Станок вертикально-фрезерный 6Н104
Фрезеровать зуб выдерживая размеры 12
Штангенциркуль ШЦ1-0-125-01 ГОСТ 166-89
V=525 ммин; n=250 мин-1; S=0.16 ммзуб; t=045 мм; To=0.012мин
Станок вертикально-сверлильный 2Н150
Сверлить отверстие выдерживая размеры 1234
Сверло 10 ГОСТ 4010 – 77(Р6М5)
Штангенциркуль ШЦ11-0-160-005 ГОСТ 162-90
V=314 ммин; n=1000 мин-1; S=0.26 ммзуб; t=1 мм; To=0.07мин
Установить необходимое количество ввёртышей
Отправить на наплавку
Фрезеровать зуб выдерживая размеры m=4 dw=368мм L=110118 мм
Шлифовать зуб выдерживая размеры m=4 dw=368мм L=110018 мм
Заключение и список литературы.doc
1. Требования предъявляемые к разрабатываемому изделию
2. Исследование и выбор оптимальных режимных параметров бурения
3. Техническое задание на разработку бурильного агрегата
Разработка конструкции изделия
1. Обзор существующих конструкций
2. Выбор и обоснование конструкции изделия
3.1. Расчёт устойчивости
3.1.1. Определение центра масс машины
3.1.2. Определение реакций на колёсах при транспортном
положении машины и подбор шин
3.1.3. Определение реакций на аутригерах при рабочем
3.2. Расчёт маневренности
3.3. Мощностной баланс
3.3.1 Мощность необходимая на передвижение машины
3.3.2. Мощность необходимая на поворот машины
3.3.3. Мощность необходимая для работы вращателя
3.4. Расчёт на проходимость.
3.5. Кинематический расчёт
3.6. Гидравлический расчёт
3.4.1. Расчёт гидроцилиндрoв
3.4.2. Подбор гидрооборудования
3.5 Расчёт сборочной единицы
3.5.1. Расчёт общего передаточного числа редуктора
3.5.2. Проектный расчёт зубчатой передачи
3.5.4. Проверка шпоночных соединений
Использование компьютерных технологий в проектировании изделий
Использование изделия в производственных условиях
Технология ремонта (изготовления) составной части изделия
1 Описание конструкции и назначение детали
3 Выбор метода ремонта
Мероприятия по охране труда и технике безопастности
1 Техника безопасности и производственная санитария
1.1 Актуальность охраны труда
1.2 Техника безопасности при работе буровых станков
1.3 Опасные и вредные производственные факторы
1.4. Расчет времени за которое концентрация вредного вещества
достигнет предельно допустимого значения (ПДК).
2 Пожарная безопасность
2.1 Причины возникновения пожара
2.2 Организационные мероприятия по обеспечению пожарной
2.3 Средства пожаротушения
Ожидаемые технико-экономические показатели
1.Исходные данные для расчета
2. Расчет эксплутационных расходов
3. Расчёт и обоснование цены бурения скважин
4. Определение “точки безубыточности”
5. Расчёт и анализ основных технико-экономических показателей
Список использованных источников
В дипломном проекте разработан агрегат бурильный шнекового бурения. Агрегат предназначен для бурения: сейсморазведочных структурно-картировочных геологоразведочных взрывных и водозаборных скважин глубиной до 30 м и диаметром до 180 мм. Так же он может применяться для инженерно-геологических изысканий и обустройства скважин при строительстве различных сооружений.
В ходе дипломного проектирования произведен общий расчет изделия расчет основных узлов (редуктор гидросистема). На основании этих расчетов выполнены чертежи машины и сборочных единиц.
Произведено подбор и обоснование основных параметров агрегата бурильного с помощью компьютерных технологий.
Разработана и приведена оптимальная технологическая схема расположения работы и график организации работ агрегата бурильного.
Кроме того разработан технологический процесс ремонта детали.
Так же разработаны мероприятия по охране труда техники безопасности и производственной санитарии. Произведен расчет вентиляции в кабине агрегата.
Технико-экономические показатели спроектированного агрегата бурильного лучше чем у аналогичных машин что делает его конкурентно способным на рынке.
СПИСОК ИСПОЛЬЗОВАННЫХ ИСТОЧНИКОВ
Нанкин Ю.А. Станки вращательного бурения. М.: Изд-во “Недра” 1970. – 328 с.
Волков А.С. Долгов Б.П. Пономарёв Г.И. вращательное бурение разведочных скважин. М. “Недра” 1977. 368 с.
Подэрни Р.Ю. Горные машины и комплексы для открытых горных работ: Учебник для вузов. – 2-е издание. перераб. и доп. – М.: Недра 1985. – 544 с.
Кузьмин А. В. Чернин И. М. Козинцов Б. С. Расчеты деталей машин. Справочное пособие. Мн. : Высш. шк. 1986. - 400с.
Курмаз Л. В. Скойбеда А. Т. Детали машин. Проектирование. Мн. : БГПА 2000. - 176 с.
Фролов С.А. Воинов А.В. Феоктистова Е.Д. “Машиностроительное черчение” – М.: Машиностроение 1981 – 315 с.
Барановского А.Н. “Режимы резания металлов. Справочник.” – М.: Машиностроение 1972 - 408 с.
Малова А.Н. ”Справочник технолога–машиностроителя” – М.: Машиностроение 1972 – 568 с.
Петренко С. М. Основы проектирования объемных гидроприводов горных машин: Учебно-метод. пособие. Мн. : БНТУ 2003. - 97с.
Казаченко Г.В. Кислов Н.В. Методическое пособие по курсу “ Торфяные машины и комплексы”. – Мн.:БПИ 1985 – 52с.;
Таяновский Г.А. Разработка раздела “Компьютерное проектирование дипломного проекта”. Методические указания для студентов специальности “Горные машины и оборудование.” - Мн.: 2002 –8 с.
Кислов Н. В. Шавель В. В. Разработка графической части курсовых и дипломных проектов. Мн. : БПИ. 1983. - 42.
Денисенко Г. Ф. Охрана труда: Учеб. Пособие: М.: Высш. Шк. 1985 – 319 с. ил.
Юдин Е.Я. Охрана труда в машиностроении М.: Машиностроение 1985.-520 с. ил.
Долин П. А. Справочник по технике безопасности. – 6-е изд. перераб. и доп. – М.: Энергоатомиздат 1984. –824 с. ил.
Средства защиты в машиностроении: Расчеты и проектирование: Справочник С. В. Белов А. Ф. Козьянов и др.; Под ред. С . В. Белова.-М.: Машиностроение 1989.- 368 с. ил.
Лазаренков А.М. Учебно–методическое пособие по дисциплине «Охрана труда» для студентов – заочников А. М. Лазаренков. – Мн.: БНТУ 2002. - 57 с.
ППБ РБ 1.01-94. Общие правила пожарной безопасности Республики Беларусь для промышленных предприятий. – Мн.: Фоиск 1995. – 68 с.
ГОСТ 2.106-96. ЕСКД. Текстовые документы. - Госстандарт Беларуси 1997.
ГОСТ 2.105-95. ЕСКД. Общие требования к текстовым документам. - Белстандарт 1996.
Дубков В.У. Мелешко В.К. Санько Е.Е. Методические указания по экономической части дипломного проекта для студентов специальности “Горные машины и оборудование.” – Мн.: БГПА 1995 – 44 с.
4. Использование изделия в произв условиях.doc
Отличительной особенностью бурения геологоразведочных скважин на малые глубины является то что оно не требует проведения ряда подготовительных и вспомогательных процессов. Так например при глубинном бурении необходимо сперва подготовить площадку для буровой вышки - вырубить лес срезать бугры засыпать овраги построить подъездные пути. При бурении же на небольшие глубины благодаря малым габаритным размерам высокой проходимости и маневренности бурильных агрегатов проведение этих операций не требуется [ ].
Перед началом работы необходимо: осмотреть установку проверить крепления насосов и маслобаков к раме состояние и натяжку канатов талевой системы затяжку болтов вращателя; проверить уровень масла в раздаточной коробке установки вращателе и масляном баке при необходимости долить до нормы; убедиться нет ли подтекания масла в соединениях механических узлов и гидросистемы.
В процессе работы и в перерывах необходимо проверять надёжность включения всех механизмов установки и надёжность фиксации всех рукояток управления; проверять на ощупь нагрев подшипников раздаточной коробки вращателя масляных насосов и гидромотора; проверять герметичность системы под давлением.
В конце работы необходимо очистить от грязи и вымыть установку; устранить все неисправности обнаруженные в процессе работы; произвести ежедневные смазочные работы.
Основными параметрами шнекового бурения являются нагрузка на породоразрушающий инструмент и число оборотов шнековой колонны. Поэтому необходимо стараться поддерживать число оборотов наиболее высоким насколько позволяет мощность двигателя. При снижении числа оборотов до 150 обмин скорость подъема выбуренной породы уменьшается в результате она скапливается на забое и снижает скорость бурения. В мягких и сыпучих породах нагрузка на породоразрушающий инструмент принимается минимальной т.е. равной массе шнековой колонны. Число оборотов колонны увеличивают до 200—300 в 1 мин. При бурении применяют плоские двухпёрые долота.
В плотных породах нагрузку на породоразрушающий инструмент увеличивают до 7 —10 кН а число оборотов долота снижают до 80—130 обмин.
Долото и шнеки охлаждаются буримой породой вследствие большой скорости углубки. В твердых породах скорость углубки мала поэтому долота быстро нагреваются и выходят из строя.
Устанавливая нагрузку на породоразрушающий инструмент рекомендуется по возможности осуществлять равномерную подачу. При резкой подаче инструмента вниз с одной стороны создаются неблагоприятные условия работы для двигателя а с другой например в вязких глинистых породах между скважиной и спиралями шнеков образуются пробки из спрессованной глины.
При бурении необходимо следить за износом режущих граней долот за исправностью шнеков (смятия искривления) за плавностью сопряжения спиралей шнеков; не допускать засыхания комков породы на спиралях тормозящих движение рыхлого породного материала.
При бурении по сухим глинам суглинкам и другим породам для уменьшения трения при перемещении породы между шнеками и стенками скважины в нее подливают воду. Для этого несколько минут прокручивают шнеки без подачи пока не прекратится подъем разбуренной ранее породы. Остановив вращение заливают 1—2 ведра воды в скважину между спиралями шнеков и дают обратное вращение колонне в течение нескольких минут. Вода доходит до забоя и при этом равномерно увлажняет стенки скважины.
При бурении в вязких породах на шнеках образуются сальники из-за сильного прилипания к ним разрушенного липкого шлама. Такие сальники часто приводят к прихвату инструмента поэтому бурение приходится прерывать через каждые 15—20 м. Это резко сокращает производительность кроме того требуется немало труда и времени на очистку шнеков от породы.
В настоящее время разработано специальное устройство для механической очистки шнеков а для борьбы с образованием сальников при бурении в вязких породах рекомендуется подливать воду в скважину.
Большую производительность шнековое бурение развивает при бурении по галечникам где механическая скорость составляет 9 мч вместо 46 мч по норме.
Вопрос о глубине и расположении геологоразведочных скважин решается заранее в соответствии с рельефом местности и категорией разведки. Рассмотрим этот вопрос непосредственно на примере карьера Овсище. Площадь этого карьера составляет S = 100 га. После бурения на этой площади нескольких пробных скважин было установлено что там возможны крупные залежи ПГС. Для установления достоверности этих предположений необходимо провести бурение геологоразведочных скважин по трём категориям: А В и С. Средняя глубина скважин с учётом рельефа местности должна быть равной 20 метрам. Определим общее количество скважин объём необходимых работ и затраты времени на выполнение поставленной задачи после чего зададимся оптимальным количеством бурильных агрегатов необходимых для проведения бурения всех скважин по трём категориям разведки.
Рассмотрим категорию С.
Сетка скважин для данной категории разведки месторождения ПГС представлена на рис.4.1.
Количество скважин: N = 6
Объём работ: V = 36
Необходимое количество дней для выполнения всего объёма работ при односменной работе с 8 – ми часовым рабочим днём.
Рисунок 4.1. Сетка скважин для категории С.
Рассмотрим категорию В.
Сетка скважин для данной категории разведки месторождения ПГС представлена на рис.4.2.
Количество скважин: N = 11
Объём работ: V = 121
Необходимое количество дней: дня.
Рисунок 4.2. Сетка скважин для категории В.
Рассмотрим категорию А.
Сетка скважин для данной категории разведки месторождения ПГС представлена на рис.4.3.
Рисунок 4.3. Сетка скважин для категории А.
Количество скважин: N = 21
Объём работ: V = 441
Необходимое количество дней:дней.
Схема движения машины при проведении бурильных работ представлена на рис. 4.4.
Рисунок 4.4. Схема движения машины.
7. Экономика.doc
1.Исходные данные для расчета.
Исходные данные для расчета приведены в таблице 7.1.
Исходные данные для расчета
Номинальная мощность двигателя
Показатели характеризующие параметры рабочего органа:
а) глубина бурения м
б) диаметр скважины мм
Производительность машины за один час чистой работы мч
Коэффициент использования рабочего времени
Производительность машины за один час валовой работы
Продолжительность работы машины в сутки ч
Суточная производительность машины м
Число рабочих дней году
Продолжительность работы машины в году:
Годовая производительность машины мгод
Годовой объем работ м
Потребное количество оборудования шт
Численность производственного персонала чел
Режим работы: прерывный круглогодовой одна смена в сутки продолжительность смены – 8 часов.
Исходя из заданного режима работы годовая производительность базовой техники (БТ):
где Qч – часовая производительность соответствующей техники мч;
tг – продолжительность работы техники ч;
где Дв=111 дней – число выходных и праздничных дней в году;
Др=30 дней – простой во всех видах технического обслуживания и ремонта;
tсм=8 ч – продолжительность смены;
Rсм=1 – коэффициент сменности;
Годовая производительность новой техники (НТ):
Годовой объём работ:
Необходимое количество машин:
В связи с округлением количества машин в большую сторону изменится время выполнения заданного объёма работ поэтому пересчитаем это время:
2. Расчет эксплутационных расходов.
2.1 Топливо на технологические цели
По данной статье учитывается стоимость дизельного топлива бензина смазочных и обтирочных материалов необходимых для выполнения основных технологических операций.
Количество дизельного топлива:
где qт – удельный расход топлива двигателем ;
N – мощность двигателя кВт;
кз – коэффициент загрузки двигателяк кз =07;
Tг – годовой фонд времени ч;
кх – коэффициент учитывающий холостые проходы кх =11;
т – число одновременно работающих машин т =2;
Цену дизельного топлива принимаем равной 1000 руб за 1 кг.
Стоимость смазочных и обтирочных материалов принимаем для укрупнённых расчётов в размере 20% от стоимости дизтоплива.
Итак стоимость топлива на технологические цели:
2.2 Основная заработная плата
где Зпр - основная заработная плата рабочих руб;
сумма доплат; принимаем укрупнено в размере 80% от основной заработной платы.
где Сч – часовая тарифная ставка;
где 61000 руб - месячная тарифная ставка рабочего первого разряда
0 - среднемесячное число рабочих часов
кт - тарифный коэффициент соответствующего разряда;
ко – отраслевой повышающий коэффициент.
Итак для машиниста (6 разряд): руб;
для слесаря (3 разряд): руб.
Тг – условное время выполнения годового объёма работ;
No – число работающих на установке с одинаковым разрядом.
2.3. Дополнительная заработная плата
2.4. Отчисления в фонд социальной защиты населения
2.5. Амортизация основных фондов
Определяем в зависимости от стоимости оборудования по нормам амортизационных отчислений.
где Тэ – нормативное время эксплуатации агрегата.
Величина амортизации
где к – стоимость оборудования;
- поправочный коэффициент используемый при недогрузке оборудования.
В данной статье учитываются затраты на капитальные и текущие ремонты.
Капитальный ремонт 40% от сумм амортизационные отчисления на оборудование
Текущий ремонт – 12% от капитальных вложений по соответствующим группам оборудования
2.7. Цеховые участковые и прочие накладные расходы.
Связаны с управлением и обслуживанием подразделений предприятий.
Принимаются 05 % от сумм расходов по предыдущим статьям.
2.8.Накладные расходы
Учитывают цеховые общезаводские и прочие производственные расходы. Размер затрат по данной статье принимаем в размере 20% от суммы прямых затрат по предыдущим статьям.
2.9. Налоги на себестоимость продукции.
Принимают в размере 18% от фонда основной заработной платы.
Результаты расчётов сводим в таблицу 7.2 и подсчитываем себестоимость единицы работ.
Калькуляция бурения 1 м.п. скважины диметром 135 мм базовой техникой и диаметром 180 мм новой техникой
Наименование статей расходов
Топливо на технологи-ческие цели
Основная заработная плата
Дополнительная зара-ботная плата
Отчисления на соци-альное страхование
Амортизация основ-ных фондов
Подготовка и освое-ние производства
Полная себестоимость
Учитывая что диаметры скважин разные введём поправочный коэффициент:
С учётом этого коэффициента себестоимость одного “приведенного” погонного метра:
По таблице 7.2 строим гистограмму себестоимости работ новой техники (рис. 7.3)
Рис.7.3. Гистограмма себестоимости по новому варианту
3. Расчёт и обоснование цены бурения скважин
Налог на недвижимость по базовому варианту машины:
где к =170000 тыс. руб.- капитальные вложения по базовому варианту машин;
h=1% - норма налога на недвижимость.
где 025 – нормативная рентабельность;
- себестоимость продукции.
Прибыль налогооблагаемая:
где hн.пр. – норма на налогооблагаемую прибыль.
Объём выпуска продукции в условных оптовых ценах
Добавленная стоимость
где МБТ – прямые материальные затраты;
Налог на добавленную стоимость
где hНДС – норма на налогооблагаемую прибыль.
Условная отпускная цена продукции работ:
Условная отпускная цена единицы продукции работ:
Определим чистую прибыль и рентабельность в проектируемом варианте.
Объём выпуска продукции в условиях отпускных цен:
Объём выпуска продукции в условных оптовых ценах:
Налог на недвижимость по новому варианту машины:
где к =170000 тыс. руб.- капитальные вложения по новому варианту машин.
4. Определение “точки безубыточности”
Проводим расчёт по новой машине.
Выручка от реализованной продукции:
где x – объём производства в пределах производственной программы.
Себестоимость продукции:
где F – условно постоянные расходы в себестоимости продукции;
где v – условно переменные расходы в себестоимости продукции;
В точке безубыточности выручка должна быть равна нулю:
где xт.б. – объём работ в точке безубыточности.
5. Расчёт и анализ основных технико-экономических показателей
Рентабельность инвестиций
Срок окупаемости инвестиций
Основные технико-экономические показатели производства
Годовой объём буровых работ:
а) в натуральном выражении м
б) в стоимостном тыс. руб.
Стоимость основных фондов тыс. руб.
Амортизационные отчисления тыс. руб.
Численность рабочих чел
Производительность труда тыс.руб.чел.
Себестоимость продукции тыс.руб.м
б) вида работ (прибыльполная себ.)
Условная отпускная цена 1 м тыс.руб.
Прибыль остающаяся в распоряжении предприятия тыс.руб.
Период возврата инвестиций
Произведём анализ основных технико-экономических показателей:
Производительность труда
Период возврата инвестиций
Проведя сравнительный анализ экономических показателей новой техники с базовой техникой можно сделать следующие выводы:
- рентабельность инвестиций Ри=29%;
- срок окупаемости инвестиций Ток=29 года;
-точка безубыточности Q=3675 мгод при номинальной производительности;
Все вышеперечисленное говорит о том что применение новой бурильной установки с точки зрения технико-экономической точки зрения эффективно.
5. Технология ремонта.doc
1 Описание конструкции и назначение детали
Деталь “колесо зубчатое” (рис. 5.1.) является деталью расположенной на входном валу вращателя бурового. Колесо зубчатое предназначено для передачи вращения от гидромотора к промежуточному валу редуктора вращателя.
Рисунок 5.1. Эскиз колеса зубчатого
Для зубчатого колеса имеется шпоночный паз. Колесо изготовлено из литейной стали 45Х ее масса составляет 12 кг. Посадочный размер 80Н7.
Торец колеса для обеспечения работоспособности и достаточного срока службы обрабатывается до шероховатости 5.
Все многообразие процессов изнашивания может быть сведено к следующим основным: изнашивание механическое абразивное окислительное осповидное (усталостное) и коррозионное.
Механическое изнашивание наблюдающееся при трении скольжения проявляется в изменении размеров формы и. шероховатости трущихся поверхностей деталей. Если процесс скольжения протекает с малыми скоростями (до 025 мсек) и при значительных давлениях то наблюдается пластическое деформирование малых участков поверхности приводящее к вырыванию частиц металла с поверхностей детали. Эти частицы либо остаются на поверхности трения в виде нароста либо уносятся из зоны трения. Этот вид изнашивания называют схватыванием первого рода. При больших скоростях скольжения и значительных давлениях в местах контакта наблюдается интенсивный нагрев поверхности; при этом температура на отдельных участках контакта возрастает до такой степени что вызывает размягчение и оплавление поверхности называемое схватыванием второго рода.
Механическое изнашивание в наиболее полном виде наблюдается при сухом трении скольжения.
В условиях граничной смазки механическое изнашивание наблюдается при разрыве масляной пленки перерыве в подаче смазки при перегреве поверхности контакта и при резком изменении режима трения.
Абразивное изнашивание представляет собой процесс постепенного разрушения поверхностного слоя деталей вследствие трения о них мельчайших частиц твердость и механическая прочность которых выше твердости и механической прочности деталей.
Окислительное изнашивание наиболее распространено в деталях двигателей. Ему подвержены коренные и шатунные шейки коленчатых валов поршневые пальцы втулки гильзы цилиндров и др. Этот вид изнашивания возникает при трении скольжения причем кроме микропластического деформирования поверхностного слоя детали наблюдается диффузия кислорода воздуха в тончайшие верхние слои детали с образованием химических соединений. В результате трения наблюдается выкашивание твердых и очень хрупких окислов приводящих к постепенному изменению размеров и формы детали.
Осповидное (усталостное) изнашивание представляет собой процесс разрушения поверхностного слоя детали вызываемый повторно-переменными нагрузками. Способность детали воспринимать переменные и знакопеременные нагрузки носит название циклической прочности. Циклическая прочность оценивается пределом усталости (пределом выносливости) которая характеризуется наибольшим напряжением при определенном числе повторений цикла нагрузки без проявления признаков разрушения.
Процесс разрушения материала в результате усталости на первой стадии проявляется в виде пластической деформации отдельных кристаллов приводящей к образованию микротрещин. В зоне микротрещин напряжения резко возрастают поэтому микротрещины увеличиваются и сливаются в общую трещину приводящую к разрушению поверхностного слоя т.е. выкашиванию с образованием осповидных углублений. Причиной появления микротрещин может быть также неоднородность материала (пустоты включения) а также повреждения поверхности (риски надиры и др.). Дальнейшему разрушению поверхностного слоя способствует сопутствующий процесс окисления детали. Осповидное изнашивание можно наблюдать на рабочих поверхностях подшипников качения на боковых поверхностях зубьев колес на поверхностях скольжения антифрикционных материалов.
Коррозионное изнашивание представляет собой процесс разрушения поверхностного слоя детали под воздействием водных растворов кислот щелочей или солей (электрохимическая коррозия) либо при непосредственном взаимодействии металла с жидкой или газовой средой (химическая коррозия). Коррозии подвержены все детали не защищенные от действия влаги растворов или газов. Применяя различные защитные покрытия (противокоррозионные масла гальванические покрытия др.) можно снизить коррозионное разрушение деталей. Коррозионному изнашиванию особенно подвержены детали двигателей внутреннего сгорания работающие в условиях высоких температур (клапаны поршень головка цилиндров) а также глушитель выпускная труба и др.
3 Выбор метода ремонта
В результате эксплуатации детали “колесо зубчатое” произошло выкрашивание нескольких зубьев за счёт действующих больших динамических нагрузок в связи с передачей большего крутящего момента. На основании вышеизложенного а также исходя из условий эксплуатации детали принимаем решение о ремонте детали.
Возможным вариантом ремонта является замена сломанных зубьев.
Замена поломанных зубьев новыми допустима только в неточных тихоходных передачах. Чаще всего зубья восстанавливают при помощи ввертышей башмаков или вставок. В этом случае поломанные зубья фрезеруют до основания изготавливают с припуском вышеуказанные элементы устанавливают их а затем обрабатывают контролируя с помощью шаблонов и скоб.
Для данного вида износа наиболее подходящим видом ремонта является метод ввертышей который осуществляется за 5 операции:
- фрезерование: удаление профиля надломанного зуба;
- сверление: получение отверстий под ввёртыши;
- завёртывание и обварка ввёртышей;
- фрезерование: нарезание нового профиля зуба;
- шлифование нового зуба.
5 Фрезерная операция
Исходные данные для расчета:
обрабатываемый материал – сталь 45 ГОСТ 1050 - 88;
инструмент – фреза ГОСТ 7063 - 72;
станок вертикально-фрезерный 6Н104;
Определение рабочего хода:
Lрх = Lрез + y + Lдоп ;
Где Lрез – длина резания мм;
У – величина перебега инструмента мм;
Lдоп – дополнительная длина хода;
Продольная подача SZ=0.07 ммзуб
Поперечная подача SПОП=04 ммход
Данное значение совпадает со значением в паспорте станка.
Расчет скорости резания V мс и числа оборотов шпинделя n в мин.
КMV – коэффициент учитывающий качество обрабатываемого материала;
КNV - коэффициент учитывающий состояние поверхности заготовки;
КUV - коэффициент зависящий от типа материала и стойкости инструмента;
б) определим рекомендуемое число оборотов шпинделя:
np = 1000 × V × d =1000 ×059 314 × 14=120 обмин ;
в) уточним число оборотов и скорость резания по паспорту станка:
V = d×n1 1000 = 314 × 14 × 250 1000 = 1099 ммин
в) рассчитаем основное машинное время обработки tм:
tм = Lрх ( S0 × n) =56(20×250)=0012мин ;
Результаты вычислений заносим в таблицу.5.1.
Таблица 5.1- Режимы резания на фрезерной операции
Содержание перехода – сверление отверстий.
обрабатываемый материал – сталь 45 ГОСТ 1050-88;
инструмент – сверло 10 ГОСТ 4010 – 77(Р6М5);
станок вертикально-сверлильный 2Н150;
глубина резания t = 5 мм.
Определение длины рабочего хода суппорта:
Lрх = Lрез + y + Lдоп
Где Lрез – длина обрабатываемой поверхности мм; Lрез = 14мм;
y– величина перебега инструмента мм; у = 2 мм;
Lдоп – дополнительная длина хода; Lдоп = 195мм (длина врезания);
Lрх=14+2+195=1795мм;
Глубина резания при сверлении t=05D=0510=5мм.
Табличное значение подачи суппорта на оборот шпинделя:
Значение подачи суппорта на оборот шпинделя по паспорту станка S0=026 ммоб.
Скорость резания при сверлении определяется по формуле:
где Сv – коэффициент Сv=98;
m y q – показатели степени m=020 y=050 q=040;
Т – период стойкости зависящий от материала режущей части инструмента обрабатываемого материала диаметра инструмента Т=25мин;
Кv – общий поправочный коэффициент на скорость резания учитывающий фактические условия резания. Определяется следующим образом:
КМv – коэффициент учитывающий влияние материала заготовки;
где КГ – коэффициент характеризующий группу стали по обрабатываемости;
nv – показатель степени.
Kuv – коэффициент учитывающий влияние инструментального материала на скорость резания Kuv =09;
Kiv – коэффициент учитывающий влияние глубины сверления на скорость резания.
Рекомендуемое число оборотов шпинделя:
Уточненное число оборотов и скорость резания по паспорту станка:
vпр=Dnпр1000=314ммин.
Крутящий момент и осевая сила рассчитываются по следующим формулам:
Для крутящего момента:
Мкр=10003451020026081=11 Нм.
РО=10681010026071=2463Н.
Мощность резания определяется по формуле:
Мощность станка Nстанка=4кВт.
Основное машинное время обработки tм:
tм = Lрх ( S0 × nпр) =1795(026 ×1000)=007 мин;
Результаты вычислений отражены в таблице 5.2.
Таблица 5.3 – Режимы резания на сверлильной операции
Титульный лист.doc
БЕЛОРУССКИЙ НАЦИОНАЛЬНЫЙ ТЕХНИЧЕСКИЙ УНИВЕРСИТЕТ
Факультет природных ресурсов и экологии
Кафедра «Горные машины»
Заведующий кафедрой
ПОЯСНИТЕЛЬНАЯ ЗАПИСКА
« Агрегат бурильный »
Специальность (Специальность направления) Т 05.01 «Горные машины и оборудование»
шифрнаименование специальности
Специализация Т 05.01.01 «Машины и комплексы открытых горных работ»
шифр наименование специализации
по разделу «Использование изделия в производственных
по разделу «Технология ремонта или изготовления
2. Разработка конструкции .doc
1.Обзор существующих конструкций
В ходе выполнения дипломного проекта был проведен патентно-информационный поиск в результате которого было найдено большое количество патентов как на буровые станки со шнековым рабочим органом так и на отдельные механизмы и узлы.
В общем передвижные буровые установки шнекового бурения обеспечивающие бурение скважин различного назначения широко распространены. Так например итальянской фирмой “Apageo Segelm” выпускаются небольшие станки “Apafor 22” и “Apafor 30” для бурения скважин различного характера. Известны так же буровые станки фирмы “АТЛАС КОПКО” МКСМ-800 (Курганского машзавода) ПУМ-500 600 и 1000 (Уралвагонзавода) BOBCAT-500 и 600 фирмы “CLARK” машины фирмы “GENLMAX Champion”.
У нас широкое распространение получили буровые станки российских заводов “Стройдормаш” и “Уралмаш”. Рассмотрим далее их технические характеристики.
Самоходная гидроприводная буровая установка УРБ-2А-2Б
Рисунок 2.1. Буровая установка УРБ-2А-2Б
Самоходная гидроприводная буровая установка УРБ-2А-2Б (рис.2.1) предназначена для бурения скважин при сейсмических исследованиях и на воду.
Обеспечивает вращательное бурение шнеками диаметром до 135 мм и шарошечными долотами на глубину до 200 м при конечном диаметре 97 мм и начальном 190 мм.
ТЕХНИЧЕСКАЯ ХАРАКТЕРИСТИКА
Максимальная частота вращения подвижного вращателя 300.
Грузоподъемность механизма подачи с ходом 5200 м - 62 кН.
Привод маслостанции мощностью 44 кВт от двигателя транспортной базы. Модификация установки УРБ-2А-2Д имеет дизельный привод.
Буровой насос с подачей 594 лмин при давлении до 40 МПа.
Компрессор с подачей 60 м3мин при давлении 05 МПа.
Установка монтируется на автомашинах ЗИЛ УРАЛ КАМАЗ.
Масса буровой установки на автомашине 10000 кг.
Самоходные технологический комплекс КГК
Рисунок 2.2. Самоходные технологические комплексы КГК
Самоходный технологический комплекс КГК (рис. 2.2.) предназначен для бурения скважин при геохимических исследованиях картировании покровных отложений и пород фундамента заверки геофизических аномалий оконтуривании перспективных участков полезных ископаемых в породах преимущественно мягких и рыхлых с забуриваем в породы фундамента средней твердости на 05 - 10 м.
- на стальных трубах диаметром 57 мм коронками диаметром 66 и 76 мм 200
- на стальных трубах диаметром 73 мм коронками диаметром 76; 84; 93100
- для труб диаметром 57 мм 25
- для труб диаметром 73 мм 40
основных элементов комплекса кг
- буровая установка 10000
- прицеп-емкость 3000
- комплект бурильных труб:
а) диаметром 57 мм на 200 м 1400
б) диаметром 73 мм на 100 м 1150
Буровая установка УБР-2М
Рисунок 2.3. Буровая установка УБР-2М
Буровая установка УБР-2М (рис. 2.3.) предназначена для бурения геологоразведочных скважин при поисках и разведке россыпных месторождений полезных ископаемых и строительных материалов. Её можно использовать также при бурении скважин на воду.Установка обеспечивает бурение скважин в сухих обводнённых рыхлых отложениях с содержанием большого количества валунов и гальки.
Диаметр скважины мм:
Диаметр обсадных труб мм
Приводной двигатель:
скорость навивки каната на барабан мс
Высота подъёма ударного снаряда м
Число ударов снаряда в минуту
Масса ударного снаряда кг
Высота мачты до оси блока м
Грузоподъёмность мачты т
Масса установки (без транспортной базы) т
Буровая установка УРБ-2М
Рисунок 2.4. Буровая установка УРБ-2М
Буровая установка УРБ-2М (рис. 2.4.) предназначена для бурения: сейсморазведочных структурно-картировочных скважин геологоразве-дочных скважин на все виды полезных ископаемых взрывных скважин водозаборных скважин. Буровая установка может применяться для инженерно-геологических изысканий и обустройства скважин при строительстве различных сооружений
Технические параметры
-вращательное с промывкой или продувкой
-шарошечное ударно-вращательное погружным пневмоударником
Глубина бурения с промывкой
Глубина бурения с продувкой (в том числе пневмоударником)
Глубина бурения шнеком
Диаметр бурения начальный
Диаметр бурения конечный
Диаметр бурения шнеками
Буровая установка УРБ-2А-2
Рисунок 2.5. Буровая установка УРБ-2А-2
Буровая установка УРБ-2А-2 (рис. 2.5.) предназначена для бурения геофизических и структурно-поисковых скважин на нефть и газ разведки месторождений твердых полезных ископаемых строительных материалов и подземных вод инженерно-геологические изыскания бурения водозаборных и взрывных скважин.
Техническая характеристика:
2. Выбор и обоснование конструкции изделия
В процессе выполнения дипломного проекта необходимо было спроектировать станок разведочного бурения для бурения скважин шнеками на глубину до 30 м и диаметром до 180 мм на базе тракторного шасси.
По аналогии с уже существующей установкой разведочного бурения УРБ-2А-2 разработанная установка (рис.2.6) со всеми механизмами входящими в её состав смонтирована на собственной раме 2 прикреплённой к тракторному шасси “Беларус” 1 и приводится в действие от его двигателя.
Установка имеет: сварную односекционную мачту подъём – опускание которой осуществляется при помощи одного гидроцилиндра 7; перемещающийся по мачте вращатель 9 с гидроприводом который используется в процессе бурения наращивания бурильных шнеков без отрыва породоразрушающего инструмента от забоя. Перемещение вращателя обеспечивается гидроцилиндром и талевой системой которая обеспечивает в свою очередь увеличение хода перемещения в 2 раза.
Управление установкой полностью гидрофицировано в том числе подъём – опускание мачты и сконцентрировано на пульте управления 6. С целью повышения устойчивости станка там установлена два аутригера 11.
Так же на установке предусмотрена установка промывочного насоса 3 который обеспечит очистку скважины в случае бурения штангами.
В качестве рабочего органа используются шнеки 10 на конце которых размещается долото.
Рисунок 2.6 – Схема разрабатываемой установки
3.1. Расчёт устойчивости
3.1.1. Определение центра масс машины
Начало системы координат в которой определяются координаты центра масс расположим в центре машины. В этом случае рациональность пространственного положения её частей оценивается мерой близости центра давления к началу системы (рис. 2.7.).
Рис.2.7. Координаты центров масс
Определение центра масс будем производить как для рабочего положения машины при поднятой мачте так и для транспортного.
Массы соответствующих частей бурового агрегата и координаты их центров масс представлены в табл. 1.
Координаты центров масс
Шасси тракторное МТЗ
- в рабочем положении
- в транспортном положении
Общая масса установки
)Координаты центра масс машины в рабочем положении:
)Найдём координаты центра масс машины в транспортном положении:
3.1.2. Определение реакций на колёсах при транспортном положении машины и подбор шин
Для определения нагрузок на ходовые колёса рассмотрим схему представленную на рис.2.8.
Рис.2.8 Схема нагружения мостов машины
Cуммарная нагрузка на колёса автомобиля приложенная к центру масс машины с учётом поперечного крена:
Нагрузку на передние колёса:
Так как центр масс машины приблизительно расположен по центру то нагрузка на каждое переднее колесо:
Нагрузка на задние колёса:
Так как центр масс машины приблизительно расположен по центру то нагрузка на каждое
По каталогу шин выбираем следующие размеры колёс
3.1.3. Определение реакций на аутригерах при рабочем положении машины
Для определения нагрузок на аутригеры рассмотрим схему представленную на рис.2.9. Причём будем считать что нагрузка на задние колёса полностью снимается аутригерами.
Рис.2.9. Схема нагружения аутригеров
Cуммарная нагрузка на аутригеры приложенная к центру масс машины с учётом поперечного крена:
Находим реакции на передних колёсах:
Так как центр масс машины расположен по центру то нагрузка на каждый переднее колесо:
Реакции на задних аутригерах:
Так как центр масс машины расположен по центру то нагрузка на каждый задний аутригер:
3.2. Расчёт маневренности
Схема агрегата для оценки маневренности представлена на рисунке 2.10.
Оценку маневренности машины будем производить по двум условиям: фактору маневренности и максимальному габаритному радиусу разворота.
) Фактор маневренности:
где -показатель маневренности;
-габаритная ширина машины м;
-ширина поворотной полосы м;
) Максимальный габаритный радиус разворота должен быть меньше допустимого =12м.
Рис.2.10.Схема к оценке манёвренности.
Для расчётов введём обозначения:
А – геометрический центр переднего моста разрабатываемой машины;
В – точка поворота рамы;
С – геометрический центр заднего моста разрабатываемой машины;
А1 А2 – крайние точки переднего моста разрабатываемой машины;
С1 С2 – крайние точки заднего моста разрабатываемой машины;
АВ = L1 = 1370 мм – расстояние от геометрического центра А передней оси разрабатываемой машины до точки поворота рамы B .
ВC = L2 = 3415 мм – расстояние от геометрического центра C задней оси разрабатываемой машины до точки поворота рамы B .
AA1 = B1 = 2860 мм – расстояние между крайними габаритами задней оси машины.
СС1 = B2 = 2870 мм – расстояние между крайними габаритами передней оси машины.
Задавшись максимальным углом поворота относительно точки В найдём максимальный габаритный радиус разворота .
Из АВЕ получим:EB = мм
AF=AD+DF=AD+BC=1049+3415=4464 мм
EC=EB+BC=1788+3415=5203 мм.
Рассмотрим подобные треугольники OАF и OEC:
Приравняем полученные выражения:
Найдём ширину поворотной полосы :
В целом маневренность для условий работы обеспечена.
3.3. Мощностной баланс
3.3.1 Мощность необходимая на передвижение машины по прямой
При движении по прямой агрегат преодолевает следующие силы сопротивления движению:
Сила сопротивления деформированию несущего основания
где =01 - коэффициент сопротивления качению колеса;
q =2 угол поперечного крена машины.
Сила сопротивления от составляющей силы тяжести перпендикулярной опорной поверхности при движении машины в гору
где φ =5 угол продольного крена машины.
Сила сопротивления инерции при разгоне (трогании с места) агрегата
где с – коэффициент учитывающий наличие вращающихся масс в трансмиссии движителя;
dv- изменение действительной скорости; dv =10 кмч =2778 мc;
dt – время разгона; dt = 80 c.
Сила сопротивления в подшипниках качения
Мощность необходимая для передвижения агрегата по прямой
где v – действительная скорость движения машины; dv =10 кмч =2778 мc;
– КПД привода движителя; = 09.
Таким образом мы видим что указанной мощности двигателя (Nдв=100 кВт) достаточно для обеспечения движения машины по прямой.
3.3.2. Мощность необходимая на поворот машины
При повороте колесного хода преодолевается все те же сопротивления что и при прямолинейном движении включая сопротивление повороту которое равно:
где –коэффициент сопротивления качению колеса; =025;
f –коэффициент трения; f=05;
R – радиус поворота машины; R=84 м ;
D – ширина колёсной базы машины; D=287 м.
Мощность необходимая для поворота агрегата
Указанной мощности двигателя (Nдв=100 кВт) достаточно для обеспечения поворота машины на скорости 5 кмч.
3.3.3. Мощность необходимая для работы вращателя
Потребное усилие подачи на долото Рос для разрушения породы
где кз – коэффициент учитывающий затупление инструмента; к=1;
D – диаметр долота; D=0180 м. ;
h – величина заглубления шнека; h=0011 м. ;
– приведенный предел прочности породы; =20 МПа.
Потребный момент вращения долота М1 необходимый для разрушения породы
где z – количество зубьев на долоте; z=2;
– коэффициент трения породы о сталь; 1=1.
Минимальная частота вращения шнека
где – угол наклона винтовой линии шнека; =30;
– коэффициент трения породы о породу; 2=12.
D1 – диаметр шнека; D1=0160 м.
Максимальная теоретическая производительность шнека
где пвр – предельная частота вращения долота; пвр=2 с-1;
d – диаметр вала шнека; d=007;
к – коэффициент просыпания породы в зазор между шнеком и стенками скважины; к=08.
Момент необходимый для обеспечения подъёма породы шнеком
где vпод – предельная частота вращения долота; vпод =002 мс ;
ρ – плотность породы; ρ=18 тм3.
кр– коэффициент разрыхления породы; кр=13.
Н – глубина бурения породы; Н=30 м.
Мощность двигателя вращателя
Техническая скорость шнекового бурения
где Пб – показатель буримости породы; Пб =5 ;
3.4. Расчёт на проходимость
Схема к расчету на проходимость представлена на рис. 2.11.
Рис.2.11. Схема к расчету на проходимость.
Помимо проверки достаточности мощности двигателя на передвижение разрабатываемого бурильного агрегата (раздел 2.3.) произведём проверку проходимости по сцеплению колёс с грунтом и по опорным давлениям на грунт.
) Сцепление колёс с грунтом.
Определим тяговое усилие:
где - коэффициент сопротивления качению колёс;
- соответствующие реакции (найдены в разделе 2.3.1.);
-скатывающая сила Н.
где -угол подъёма дорожного полотна 50.
Коэффициент сцепления колёс с грунтом тогда возможный максимум тягового усилия при тягаче по схеме 6 X 6 равен
Если то движение возможно.
850 – 51217=29633 > 0 условие выполнено.
Следовательно проходимость бурильного агрегата по сцеплению колёс с грунтом обеспечена.
) Проверка на проходимость по опорным давлениям:
где - опорное давление
-допустимое давление на колесо Па;
-длина пятна контактам.
Проверка по осадке грунта:
где -осадка колеса м;
-допустимая осадка колеса м.
где -коэффициент объёмного смятия ;
-приведенный диаметр 156 м.
В целом проходимость обеспечена.
3.5. Кинематический расчёт
При общем кинематическом расчёте будем руководствоваться условием обеспечения требуемой частоты вращения для гидронасосной станции бурильного агрегата. В следствие того что привод насосов и привод задних колёс тракторного шасси предполагается осуществлять от ВОМ по средствам одного вала необходимо учесть тот факт что частота вращения вала при движении машины состовляет 500 – 600 обмин а при приводе гидронасосов 1700 обмин. Для решения этой проблемы и обеспечения плавности включения привода насосной станции и заднего моста в конструкции агрегата имеется фрикцион обеспечивающей возможность переключения частот вращения карданных валов
Кинематическая схема привода вращателя представлена на рис. 2.10.
Рисунок 2.12. Кинематическая схема привода вращателя
Вращение от двигателя тракторного шасси через коробку передач гидроподжимную фрикционную муфту включения ВОМ по средствам карданного вала передаётся на ведущий вал коробки раздаточной буровой установки. На выходных концах коробки раздаточной установлены масляные насосы а так же шкив с зубчатой муфтой включения для привода по средствам клиноременной передачи насоса бурового.
Для привода вращателя служит гидромотор от которого вращение через муфту передаётся на вал XVI. На валу XVII свободно перемещается блок-шестерня которая может входить в зацепление с одной из двух шестерён посаженных на вал XVIII что обеспечивает вращение этого вала с двумя различными частотами.
Перемещается вращатель по мачте при помощи гидроцилиндра и талевой системы обеспечивающей удвоение хода.
Номинальная частота вращения ВОМ n1=1050 обмин.
Номинальная частота входных валов насосов:
-типа 3103.112-03 для привода исполнительных механизмов n2=1700 обмин;
-типа Пл12516 – n3=935 обмин.
Исходя из этого рассчитаем требуемые передаточные числа раздаточной коробки.
Подбираем числа зубьев зубчатых колес исходя из значения передаточных чисел размеров раздаточной коробки и принимая во внимание конструкцию аналоговой техники.
Частоты вращения валов:
Кинематический расчёт редуктора вращателя приведен в разделе .
3.6. Гидравлический расчёт
Схема гидравлическая установки бурильной представлена на рис. 2.13.
Рисунок 2.13. Схема гидравлическая
К исполнительным органам имеющим гидравлический привод рабочая жидкость подается насосами H1 НЗ и Н4 из маслобака.
Насос H1 служит для медленного подъёма и подачи инструмента на забой а также для подъёма - опускания мачты. От насоса H1 масло через обратные клапаны КО1 и КО2 поступает в распределитель P2 который нормально должен быть включён в положение (“подъём”) и попадает в нижнюю (поршневую) полость гидроцилиндра Ц1 обеспечивая таким образом подъём инструмента. Из верхней штоковой полости гидроцилиндра Ц1 масло через распределитель РЗ и P2 поступает в сливную магистраль. Подъём инструмента с помощью насоса Н1 происходит только при закрытом вентиле BH1 (“регулятор подачи”).
Чтобы остановить подъём и оставить интрумент в любом поднятом положении достаточно вентиль Н1 полностью открыть и масло от насоса H1 направить на слив. Спуск инструмента под собственным весом можно осуществить с помощью распределителя Р2 установив его в нейтральное положение.
Для создания нагрузки на забой необходимо распределитель P2 переключить в положение (“вниз”) т. е. масло от насоса H1 направить в верхнюю (штоковую) полость гидроццлиндра Ц1. Нагрузка на забой регулируется вентилем ВН1.
Кроне функции распределителя жидкости распределитель Р2 выполняет функции дросселя. Установв рукоятку распределителя в положение промежуточное между положениями подъём" и нейтральным можно регулировать как скорость подъёма вращателя так и скорость опускания его под собственным весом.
Для подъёма или опускания мачты необходимо включить распределитель P2 в положение вниз" открыть вентиль ВН1 и включить распределитель Р4 в положение “подъём” или “спуск”. Пpu этом вращатель и шток гидроцилиндра Ц1 будут находиться в крайнем нижнем положении и масло от насоса Н1 будет поступать в распределитель Р4 и далее в нижнюю или верхнюю полость гидроцилиндра Ц4.
Для предохранения системы от перегрузки в нагнетательной линии насоса Н1 установлен предохранительный клапан КП1.
Насос Н4 служит для подъёма инструмента. Масло от насоса Н4 через фильтр Ф2 и обратный клапан КОЗ поступает в распределитель P2. От перегрузок насос Н4 защищён предохранительно — разгрузочным клапаном КП3 который имеет дистанционное управление вентилем ВН3 (регулятор скорости подъёма”).
Управление подъемом и спуском вращателя при работе насоса Н4 аналогично yправлению при работе насоса Н1. Для остановки вращателя в любом приподнятом положении достаточно открыть вентиль ВН3 и масло от насоса Н4 через клапан КП3 без давления пойдёт на слив.
Распределитель Р3 обеспечивает дифференциальную работу гидроцилиндра подачи. При включении его в положение “б” обеспечивается нормальная работа гидроцилиндра подачи а при включении его в положение “в” – дифференциальна т.е. поршневая и штоковая полости гидроцилиндра соединяются между собой и с подводом. Давление масла при этом в обеих полостях одинакова но за счёт разности площадей поршневой и штоковой полостей гидроцилиндра шток выдвигается из гидроцилиндра а масло вытесненное из штоковой полости перетекает в поршневую вместе с маслом поступающим от насоса что обеспечивает быстрый подъём вращателя со скоростью в 22 раза превышающей скорость при нормальной работе гидроцилиндра.
Опускание вращателя под действием собственного веса при дифференциальной работе гидроцилиндра происходит так же с большей скоростью чем при нормальной его работе. Подача инструмента на забой а так же работа опорных домкратов могут быть обеспечены при нормальной работе гидроцилиндра т.е. при включении распределителя Р3 в положение “б”.
Насос Н3 предназначен для привода вращателя. Масло от насоса Н3 через фильтр Ф1 поступает в распределитель Р1 с ручным управлением при включении которого в положение “б” или “в” масло подаётся к гидромотору М и обеспечивает правое или левое вращение шпинделя вращателя.
При включении распределителя Р1 в положении “а” (“нейтральное”) масло через него направляется в сливную магистраль и поступает в масляный бак.
От перегрузок насос Н3 защищён предохранительно-разгрузочным клапаном КП2 который имеет дитанционное управление вентилем ВН2 (“регулятор частоты вращения”) что при необходимости позволяет плавно включать вращение и регулировать частоту вращения шпинделя вращателя.
Для разгрузки тракторного шасси от усилий возникающих во время бурения и при подъёме инструмента а так же для удобства в эксплуатации установка снабжена гидравлическими опорными домкратами Ц2 и Ц3. Верхние полости опорных домкратов соединены с нижней полостью гидроцилиндра Ц1 трубопроводами которое врезаны вентили ВН4 и ВН5.нижние полости опорных домкратов между собой и с верхней полостью гидроцилиндра Ц1. созданием давления в нижней (поршневой) полости гидроцилиндра Ц1 при открытых вентилях. ВН4 и ВН5 обеспечивается выдвижением опорных домкратов на необходимую величину после чего вентили должны быть закрыты. Наличие раздельного управления опорными домкратами позволяет производить корректировку вертикального положения мачты.
Для снятия установки с опорных домкратов необходимо открыть оба вентиля и создать давление в верхней (штоковой) полости гидроцилиндра Ц1.
На установке предусмотрен аварийный ручной насоа Н2 применяемый при выходе из строя двигателя тракторного шасси. В этом случае отсоединяют шнеки от шпинделя поднимают насосом Н2 вращатель опускают мачту и установку можно транспортировать буксиром. Управление насосом Н2 осуществляется так же как и при работе насоса Н1.
Для создания оптимального режима бурения по давлению на забой и крутящему моменту а так же для поддержания постоянного режима в процессе бурения в нагнетательных линиях установлены манометры МН1 и МН2.
Для очистки масла от механических примесей в нагнетательных линиях насосов Н3 и Н4 установлены фильтры Ф1 и Ф2 с тонкостью фильтрации 25 микрон.
3.4.1. Расчёт гидроцилиндров
При расчёте гидроцилиндра в первую очередь необходимо найти усилие на шток. Для определения нагрузок рассмотрим схему представленную на рис.2.14.
Усилие на штоках гидроцилиндров:
Нагрузка на штоке гидроцилиндра:
Рис. 2.14. Схема нагружения гидроцилиндров подъёма мачты
С точки зрения надёжности и безопасности разрабатываемой машины примем усилие на штоке кН.
Рабочая площадь поршня
где р1 принятое рабочее давление в гидросистеме; p1=20 МПа;
мц=095 механический КПД гидроцилиндра;
г=090 гидравлический КПД гидропередачи.
Внутренний диаметр цилиндра при подаче рабочей жидкости в поршневую полость
Толщина стенки корпуса стального гидроцилиндра:
где []=550.105 Па – допустимое напряжение растяжения для стали;
=03 – коэффициент Пуассона (для стали).
Диаметр штока гидроцилиндра
3.4.2. Подбор гидрооборудования.
Крутящий момент на валу гидромотора
где Мкр потребный момент вращения долота;
р=090 КПД редуктора.
Частота вращения вала гидромотора 116
где пвр – частота вращения долота; пвр=2 с-1.
По крутящему моменту на валу гидромотора и по частоте вращения этого же вала подбираем гидромотор 3103.112-00:
номинальный крутящий момент 250 н*м;
давление: номинальное 20 МПа;
максимальное 25 МПа;
частота вращения: номинальная 1450 ;
Требуемое давление на выходе из насоса
где требуемый момент на волу гидромотора;
рабочий объем гидромотора;
гидравлический КПД передачи.
Требуемая подача насоса
где объемный КПД гидромотора.
Подбор насоса осуществляется по необходимой подаче и по рабочему давлению .
Подбираем насос 3103.112-03:
расход Q = 112 лмин;
КПД: объемный 095; общий 087;
Определение размеров сечения трубопроводов.
Внутренний диаметр трубопровода
где расход жидкости через трубопровод Q1= 112 лмин = 00018 м3c;
скорость движения рабочей жидкости в трубопроводе vж = 4 мсек.
Толщина стенки трубы из условия работы на разрыв
где p максимальное давление рабочей жидкости;
- допускаемое напряжение растяжения для материала трубы ( для стали 20 126 МПа).
Принимаем трубопровод 12 Х 1 ГОСТ 8734-75Б 20 ГОСТ 8733-74.
Определение потерь давления и гидравлического КПД гидропривода.
В гидроприводах имеют место потери давления в гидроаппаратуре и вспомогательных устройствах .
Потери давления при движении жидкости в цилиндрических трубах (формула Дарси)
=906 кг плотность рабочей жидкости;
коэффициент сопротивления;
где - абсолютная величина эквивалентной равномерно-зернистой шероховатости (для стальных бесшовных труб и рукавов высокого давления =003 мм);
Re- число Рейнольдса;
где - кинематический коэффициент вязкости.
Потери давления в местных сопротивлениях
где - коэффициент местного сопротивления.
Гидравлический КПД гидропривода
Мощность потребляемая гидромотором
Полный КПД гидропривода
Мощность подводимая к насосу
Подбор гидроаппаратуры.
Распределитель: Рн203-ФМ14
расход: номинальный 160лмин;
максимальный 180 лмин;
давление: номинальное 25 МПа;
максимальное 32 МПа.
Клапан предохранительный: МКПВ-103 С2Р2: давление 20МПа;
3.5 Расчёт сборочной единицы
3.5.1. Расчёт общего передаточного числа редуктора вращателя
Кинематическая схема редуктора вращателя представлена на рис. 2.15.
Рисунок 2.15. Кинематическая схема редуктора вращателя
Для нормальной работы бурового станка необходимо выполнение следующих условий:
Мощность приводного двигателя вращателя должна быть не меньше расчётной (Nвр=364 кВт).
Частота вращения вращателя должна быть больше расчётной минимальной частоты вращения. Примем предельную частоту вращения вращателя равной 2 обc.
Итак приняв в качестве приводного двигателя гидромотор мощностью 40кВт и номинальной частотой вращения вала 1470 обмин общее передаточное число редуктора
3.5.2. Проектный расчёт зубчатой передачи
Рассчитывать будем наиболее быстороходную цилиндрическую пару.
Для первой шестерни 8 принимаем материал сталь 45. Термическая обработка – нормализация твердость 205 HB.
Для второй шестерни 9 принимаем материал сталь 45. Термическая обработка – нормализация твердость 175 HB.
Предел контактной выносливости
Допускаемые контактные напряжения
SH =11 – коэффициент запаса прочности.
Расчетное межосевое расстояние
где ка =49 – коэффициент зависящий от типа зацепления;
yа =0315 – коэффициент ширины шестерни;
Т2 – момент на валу
где N = 40 кВт мощность двигателя.
Значение mt округляем до ближайшей величины в соответствии с ГОСТ. Окончательно принимаем mt = 4 мм.
Число зубьев зубчатого колеса 1
Окончательно принимаем z1=23.
Число зубьев зубчатого колеса 2
Диаметры делительных диаметров колёс:
Диаметры вершин зубьев колёс:
Диаметры впадин зубьев колёс:
Уточняем межосевое расстояние:
aw = (dw1+dw2)2 = (92+368)2 = 230 мм
Окружная сила в зацеплении скорость колёс:
Окружная скорость колёс:
По таблице выбираем 7 степень точности.
Удельная окружная динамическая сила
где – коэффициент учитывающий влияние вида зубчатой передачи и модификации профиля зуба ( табл.4.2.10 [1]); ;
– коэффициент учитывающий влияние разности шагов зацепления зубьев шестерни и колеса ( табл.4.2.12 [1]); ;
Удельная расчётная окружная сила в зоне её наибольшей концентрации:
Коэффициент учитывающий динамическую нагрузку в зацеплении:
Удельная расчётная окружная сила
Расчётное контактное напряжение
-условие прочности выполняется.
Принимаем [tk] = 25 МПа для стали 45.
Находим эквивалентный момент на валу:
Суммарный изгибающий момент в наиболее опасном сечении вала
Эквивалентный момент
Эпюры моментов показаны на рис. 2.14.
Расчетный диаметр вала
Под присоединительный конец вала выбираем диаметр вала: 500 мм.
Под 1-й элемент (манжета) выбираем диаметр вала: 550 мм.
Под 2-й элемент (подшипник) выбираем диаметр вала: 600 мм.
Под 3-й элемент (ведущий) выбираем диаметр вала: 650 мм.
Под 4-й элемент (подшипник) выбираем диаметр вала: 600 мм.
Диаметры остальных валов назначаем исходя из конструктивных соображений и в соответствии с аналогичными конструкциями.
Рисунок 2.14. – Эпюры моментов на валу
3.5.4. Проверка шпоночных соединений
Рассмотри шестерню на быстроходном валу.
Для данного элемента подбираем одну призматическую шпонку со скруглёнными торцами 15x8x36. Размеры сечений шпонки и пазов и длины шпонок по ГОСТ 23360-78 (см. табл. 89[1]).
Материал шпоноки - сталь 45 нормализованная.
Напряжение смятия и условие прочности проверяем по формуле 8.22[1].
см = Т (dвала x (l - b) x (h - t1)) =
= 26000 (50 x (36 - 15) x (8 -4 )) = 619 МПа = [см]
где Т = 26000 Н мм - момент на валу;
dвала = 50 мм - диаметр вала;
h = 8 мм - высота шпонки;
b = 15 мм - ширина шпонки;
t1 = 4 мм - глубина паза вала.
Допускаемые напряжения смятия при переменной нагрузке и при стальной ступице [см] = 750 МПа.
Проверим шпонку на срез по формуле 8.24[1].
ср = Т (dвала x (l - b) x b) =
= 26000 (50 x (36 - 15) x 15) = 165 МПа = [ср]
Допускаемые напряжения среза при стальной ступице [ср]=06 [см] =45 МПа.
3.6. Расчёт диаметра пальца.
Расчёт проводим по изгибающему моменту
С учётом того что палец должен обеспечивать надёжность соединения а так же с учётом аналогичных конструкций примем его диаметр равный 40 мм.
Содержание.doc
1. Требования предъявляемые к разрабатываемому изделию10
2. Исследование и выбор оптимальных режимных параметров
3. Техническое задание на разработку бурильного агрегата15
Разработка конструкции изделия19
1. Обзор существующих конструкций19
2. Выбор и обоснование конструкции изделия25
3.1. Расчёт устойчивости27
3.1.1. Определение центра масс машины27
3.1.2. Определение реакций на колёсах при транс-
портном положении машины и подбор шин29
3.1.3. Определение реакций на аутригерах при рабочем
3.2. Расчёт маневренности31
3.3. Мощностной баланс34
3.3.1. Мощность необходимая на передвижение
3.3.2. Мощность необходимая на поворот машины35
3.3.3. Мощность необходимая для работы вращателя36
3.4. Расчёт на проходимость37
3.5. Кинематический расчёт40
3.6. Гидравлический расчёт42
3.6.1. Расчёт гидроцилиндра подъёма мачты46
3.6.2. Подбор гидрооборудования48
3.7 Расчёт сборочной единицы51
3.7.1. Расчёт общего передаточного числа редуктора
3.7.2. Проектный расчёт зубчатой передачи52
3.7.3. Расчёт валов55
3.7.4. Проверка шпоночных соединений58
Использование компьютерных технологий в проектировании
Использование изделия в производственных условиях67
Технология ремонта (изготовления) составной части изделия73
1 Описание конструкции и назначение детали73
3 Выбор метода ремонта76
Мероприятия по охране труда и технике безопастности82
1 Техника безопасности и производственная санитария82
1.1 Актуальность охраны труда82
1.2 Техника безопасности при работе буровых станков83
1.3 Опасные и вредные производственные факторы85
1.4 Расчёт времени за которое концентрация вредного
вещества достигнет предельно допустимого значения87
2 Пожарная безопасность89
2.1 Причины возникновения пожара89
2.2 Организационные мероприятия по обеспечению пожарной
2.3 Средства пожаротушения90
Ожидаемые технико-экономические показатели93
1.Исходные данные для расчета93
2. Расчет эксплутационных расходов94
3. Расчёт и обоснование цены бурения скважин99
4. Определение “точки безубыточности”101
5. Расчёт и анализ основных технико-экономических показателей102
Список использованных источников106
Приложение А Патенты108
Приложение Б Маршрутные и операционные карты 112
где -угол подъёма дорожного полотна 50.
Коэффициент сцепления колёс с грунтом тогда возможный максимум тягового усилия при тягаче по схеме 6 X 6 равен
Если то движение возможно.
850 – 51217=29633 > 0 условие выполнено.
Следовательно проходимость бурильного агрегата по сцеплению колёс с грунтом обеспечена.
) Проверка на проходимость по опорным давлениям:
где - опорное давление
-допустимое давление на колесо Па;
-длина пятна контактам.
Проверка по осадке грунта:
где -осадка колеса м;
-допустимая осадка колеса м.
где -коэффициент объёмного смятия ;
-приведенный диаметр 156 м.
Условие выполнено. В целом проходимость обеспечена.
3.5. Кинематический расчёт
При общем кинематическом расчёте будем руководствоваться условием обеспечения требуемой частоты вращения для гидронасосной станции бурильного агрегата. Вследствие того что привод насосов и привод задних колёс тракторного шасси предполагается осуществлять от ВОМ по средствам одного вала необходимо учесть тот факт что частота вращения вала при движении машины состовляет 500 – 600 обмин а при приводе гидронасосов 1700 обмин. Для решения этой проблемы и обеспечения плавности включения привода насосной станции и заднего моста в конструкции агрегата имеется фрикцион обеспечивающей возможность переключения частот вращения карданного вала.
Кинематическая схема привода вращателя представлена на рис. 2.10.
Вращение от двигателя тракторного шасси через коробку передач гидроподжимную фрикционную муфту включения ВОМ по средствам карданного вала передаётся на ведущий вал коробки раздаточной буровой установки. На выходных концах коробки раздаточной установлены масляные насосы а так же шкив с зубчатой муфтой включения для привода по средствам клиноременной передачи насоса бурового.
Вращение от двигателя тракторного шасси через коробку передач гидроподжимную фрикционную муфту включения ВОМ по средствам карданного вала передаётся на ведущий вал коробки раздаточной буровой установки.
На выходных концах коробки раздаточной установлены масляные насосы а так же шкив с зубчатой муфтой включения для привода по средствам клиноременной передачи насоса бурового.
Рисунок 2.12. Кинематическая схема привода вращателя
Для привода вращателя служит гидромотор от которого вращение через муфту передаётся на вал XVI. На валу XVII свободно перемещается блок-шестерня которая может входить в зацепление с одной из двух шестерён посаженных на вал XVIII что обеспечивает вращение этого вала с двумя различными частотами.
Перемещается вращатель по мачте при помощи гидроцилиндра и талевой системы обеспечивающей удвоение хода.
Номинальная частота вращения ВОМ n1=1050 обмин.
Номинальная частота входных валов насосов:
-типа 3103.112-03 для привода исполнительных механизмов n2=1700 обмин;
-типа Пл12516 – n3=935 обмин.
Исходя из этого рассчитаем требуемые передаточные числа раздаточной коробки.
Подбираем числа зубьев зубчатых колес исходя из значения передаточных чисел размеров раздаточной коробки и принимая во внимание конструкцию аналоговой техники.
Частоты вращения валов:
Кинематический расчёт редуктора вращателя приведен в разделе 2.3.7.
3.6. Гидравлический расчёт
Схема гидравлическая установки бурильной представлена на рис. 2.13.
К исполнительным органам имеющим гидравлический привод рабочая жидкость подается насосами H1 НЗ и Н4 из маслобака.
Насос H1 служит для медленного подъёма и подачи инструмента на забой а также для подъёма - опускания мачты. От насоса H1 масло через обратные клапаны КО1 и КО2 поступает в распределитель P2 который нормально должен быть включён в положение (“подъём”) и попадает в нижнюю
Введение.doc
Шнековое бурение позволяет совместить операции непосредственно по бурению с удалением породы из забоя без применения промывки или продувки. Шнековый способ бурения имеет специфические особенности заключающиеся в том что удаление разрушенной породы производится не промывочной жидкостью а шнеками являющимися вертикальным винтовым транспортёром. Подача разрушенной породы на лопасть шнека производится долотом при наличии подпора нижних слоёв породы при её разрыхлении.
Таким образом при шнековом бурении долото выполняет две функции – разрушает породу и подаёт разрушенную породу на спираль шнека. Работа долота складывается из трёх операций:
внедрение рабочей части долота в породу под действием осевой нагрузки;
срез породы при вращении долота;
подача разрушенной породы на спираль шнека.
Если при использовании способов бурения с очисткой забоя скважины глинистым раствором или воздухом содержание разрушенной породы в стволе скважины едва достигает 2 – 4 % то при шнековом бурении оно составляет 10 – 20 %. Это обеспечивает высокие механические скорости бурения в мягких и рыхлых породах.
В связи с отсутствием необходимости применять при шнековом бурении промывку этот способ так же с успехом используется для проходки мелких скважин в безводных районах в многолетнемёрзлых породах и в зимнее время при отрицательных температурах.
Шнековое бурение ведётся как сплошным забоем так и кольцевым. В последнем случае удаётся получить образцы пород характеризующие геологическое строение данного участка.
К недостаткам шнекового бурения следует отнести относительно небольшую глубину бурения (50 – 70 м) невозможность бурения скважин в породах 7 категории по буримости и выше в породах с наличием твёрдых прослоев и валунов трудности бурения в грунтах ниже уровня подземных вод требующих применение других способов для проходки и закрепления этих грунтов трудности бурения шнеками в вязких и липких глинистых грунтах относительно большую энергоёмкость шнекового бурения.
Таким образом буровые станки шнекового бурения находят широкое применение в различных отраслях народного хозяйства а наибольшее распространение они получили при бурении геологоразведочных и взрывных скважин на открытых горных работах.
Учитывая устойчивую на длительный период времени перспективу применения буровых агрегатов в геологоразведке а так же при бурении: сейсморазведочных структурно-картировочных и водозаборных скважин инженерно-геологических изысканий и обустройства скважин при строительстве различных сооружений работы в данном направлении весьма актуальны.