Крано-манипуляторная установка грузоподъёмностью 3 т на базе автомобиля КамАЗ-6510




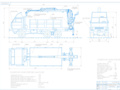
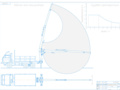
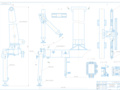
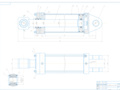
- Добавлен: 25.10.2022
- Размер: 8 MB
- Закачек: 1
Описание
Состав проекта
![]() |
![]() |
![]() ![]() ![]() |
![]() ![]() ![]() |
![]() ![]() ![]() |
![]() ![]() ![]() |
![]() ![]() ![]() |
![]() ![]() |
![]() ![]() ![]() |
![]() ![]() ![]() |
![]() ![]() ![]() |
![]() ![]() ![]() |
![]() |
![]() ![]() ![]() ![]() |
![]() ![]() ![]() ![]() |
![]() ![]() |
![]() ![]() |
![]() ![]() ![]() ![]() |
![]() ![]() ![]() ![]() |
![]() ![]() |
![]() ![]() ![]() ![]() |
![]() ![]() ![]() ![]() |
![]() ![]() |
![]() ![]() ![]() ![]() |
![]() ![]() |
![]() ![]() ![]() ![]() |
![]() ![]() |
![]() |
![]() ![]() |
![]() ![]() |
![]() ![]() |
![]() ![]() |
![]() ![]() |
![]() ![]() |
![]() ![]() |
![]() ![]() |
![]() ![]() |
![]() ![]() |
![]() ![]() |
![]() ![]() |
![]() ![]() |
![]() ![]() |
Дополнительная информация
Техн.ч., Заключение и Список лит-ры - 5 (23стр.).docx
В данном разделе производится разработка технологического процесса изготовления траверсы крюковой подвески крана. Деталь изготавливается из стали – 45.
Общий вид детали представлен на рисунке 44.
Рисунок 44 - Общий вид детали
В качестве заготовки выбираем листовой прокат толщиной 60 мм (Лист ). Габариты и размеры предварительной резки (ручная газовая или плазморез) представлены на рисунке 45.
Рисунок 45 - Габариты и размеры заготовки изготовления траверсы
Назначаем следующий маршрут:
3 Расчетно-аналитический метод определения припусков на механическую обработку
Тип производства – единичное;
масса заготовки – 64 кг;
масса детали – 54 кг.
Коэффициент использования металла:
Технологический маршрут предусматривает последовательность выполнения технологических операций с выбором типа оборудования. При установке последовательности обработки сначала обрабатывают поверхности принятые за технологические базы а затем остальные поверхности в последовательности обратной степени их точности.
Технологический маршрут обработки поверхности состоит из операций предварительного точения чистового точения. Припуском называют слой материала удаляемый для достижения заданной точности и качества обрабатываемой поверхности. Различают припуски промежуточные и общие. Промежуточным называется слой металла удаляемый при выполнении технологического перехода. Общим называют слой металла который удаляют с заготовки на всех технологических переходах обработки данной поверхности. Общий припуск на обработку равен сумме промежуточных припусков:
где - промежуточный припуск
m – число технологических переходов.
Исходные данные необходимые для расчета величины припусков промежуточных на выполнение каждого перехода вносятся в таблицу 37.
Таблица 37 - Исходные данные необходимые для расчета величины припусков
Последовательность выполнения обработки
Класс или квалитет точности
Обозначение величины допуска мкм
Шероховатость поверхности мкк
пространственных отклонений мкм
погрешности установки мкм
Предварительное точение
где - допустимые погрешности измерения линейных размеров (диаметров длин) в зависимости от допусков и квалитетов точности 9;
- параметры шероховатости в зависимости от метода обработки 9;
- величина дефектного слоя 9;
- величина пространственных отклонений штамповки;
где = 10 мм - погрешность заготовки по смещению штампов;
- погрешность заготовки по кривизне 3175=525 мкм = 05мм здесь 3 мкммм а L – длина заготовки;
- погрешность зацентровки
где =45 мм - допуск диаметрального размера заготовки.
Примем для данного случая =10 мм =05 мм.
Расчет номинальных промежуточных припусков для удобства сведем в таблицу 38.
Таблица 38 – Расчет номинальных промежуточных припусков
Величина номинального промежуточного
припуска и формула для расчета мкм
Чистовое значение припуска мм
При предварительном точении
= 2(160+300+1939)+4500=9298 мкм
При чистовом точении
=2(160+250+116)+250=1302 мкм
Общий припуск штамповки на диаметр при механической обработке
Округление промежуточных припусков производится в сторону увеличения припусков до того же знака десятичной дроби с каким дан допуск промежуточного размера. Расчет сведем в таблице 39.
Таблица 39 – Расчет детали
Наименование определяемой величины и формула для ее расчета
Условное обозначение величины
Числовое значение величины мм
Чертежный размер поверхности
Исходный расчетный размер (наибольший предельный размер наружной поверхности)
Номинальный припуск на диаметр при чистовом точении
Расчетный диаметр после предварительного точения
Диаметр после предварительного точения (округленный)
Номинальный припуск на диаметр при предварительном точении
Расчетный диаметр заготовки штамповки
Диаметр заготовки-штамповки с допуском (округленный)
4 Расчет режимов резания для токарной операции
Определим скорость резания для токарной операции при черновой обработке. Скорость резания определяется по эмпирической формуле:
где Т – среднее значение стойкости резца Т=30 60 мин 10;
S = 04 ммоб – подача резца 10;
t = 465 мм – глубина резания;
где - коэффициент учитывающий влияние материала заготовки 10;
где - коэффициент характеризующий группу стали по обрабатываемости 10;
- показатель степени зависящий от вида обрабатывающего инструмента 10;
- предел прочности стали 40Х при растяжении =800 МПа 8;
- коэффициент учитывающий влияние состояния поверхности заготовки 10;
- коэффициент учитывающий влияние материала инструмента 10;
Рассчитаем частоту вращения шпинделя:
где D1=493 мм – диаметр после чернового точения.
Выбираем из стандартного ряда чисел оборотов станка 1000обмин. Уточним скорость резания:
Определим силу резания (тангенциальную):
где =300 – коэффициент 10;
- показатели степени 10;
- общий поправочный коэффициент учитывающий измененные по сравнению с табличными условия резания представляющий собой произведение из ряда коэффициентов 10:
Определим эффективную мощность резания:
Необходимая мощность станка:
где =09 - коэффициент полезного действия станка.
По полученному значению мощности выбираем станок токарно-винторезный 16К20 11.
Рассчитаем основное и вспомогательное время.
где - длина обрабатываемой поверхности;
- частота вращения шпинделя;
Определим скорость резания для токарной операции при чистовой обработке. Скорость резания определяется по эмпирической формуле 11:
где Т – среднее значение стойкости резца Т=30 60 мин 11;
S =025 ммоб - подача резца 11;
t =067 мм - глубина резания;
Выбираем из стандартного ряда чисел оборотов станка 1600обмин. Уточним скорость резания:
Рассчитаем режимы резания на обработку остальных поверхностей вала. Поверхность №2:
5 Расчет режимов резания для фрезерно-центровальной операции
Определим скорость резания для фрезерно-центровальной операции при черновой обработке. Скорость резания определяется по эмпирической формуле:
B=586мм t=25мм - параметры срезаемого слоя: ширина фрезерования глубина обрабатываемой поверхности соответственно 11;
D = 100 мм – диаметр фрезы 11;
T = 180 мин – период стойкости фрезы 11;
= 300мммин - подача на фрезы 11;
z – число зубьев фрезы z=6 11;
где - коэффициент учитывающий влияние материала заготовки 11.
где - коэффициент характеризующий группу стали по обрабатываемости 11;
- показатель степени зависящий от вида обрабатывающего инструмента 11;
- предел прочности стали 45 при растяжении 8;
- коэффициент учитывающий влияние состояния поверхности заготовки 11;
- коэффициент учитывающий влияние материала инструмента 11.
Рассчитаем силу резания. Главная составляющая силы резания при фрезеровании – окружная сила Н.
где n – частота вращения фрезы обмин.
Выбираем из стандартного ряда чисел оборотов станка n=249обмин тогда уточняем :
где – коэффициент и показатели степени 11;
- поправочный коэффициент на качество обрабатываемого материала 11.
где - предел прочности стали 45 при растяжении 8;
n – показатель степени при определении окружной силы резания при фрезеровании 11.
Крутящий момент на шпинделе:
Мощность резания (эффективная):
Выбираем по полученной мощности выбирается фрезерно-центровальный станок МР73 11.
6 Расчет вертикально-сверлильной операции
Рассчитаем режимы резания для сверлильной операции образующей отверстие в траверсе под крюк.
Скорость резания ммин при сверлении
где q m y – коэффициенты: =98 q=04 m=02 y=05 11;
мм – диаметр сверла;
0 мин – период стойкости 11;
s=042 мм – подача 11.
где =10 - коэффициент на обрабатываемый материал 11;
=10 - коэффициент на инструментальный материал 11;
=10 - коэффициент учитывающий глубину сверления 11.
Частота вращения сверла:
Выбираем из стандартного ряда чисел оборотов станка 250обмин тогда
Определим крутящий момент:
где =00345 – коэффициент 11;
q = 2 - показатели степени 11;
- общий поправочный коэффициент учитывающий измененные по сравнению с табличными условия сверления представляющий собой произведение из ряда коэффициентов 11:
Определим осевую силу:
где СP = 68 q =1 y = 07;
Р0 = 1068501042071 = 185 кН
По полученному значению мощности выбираем сверлильный станок 2Г175 11.
- частота вращения патрона;
7 Расчет режимов резания для фрезерной операции
Определим скорость резания при фрезеровании поверхности. Скорость резания определяется по эмпирической формуле 11:
B – ширина фрезерования В=85 мм;
t – глубина паза t = 12 мм;
D – диаметр фрезы D = 85 мм;
T – период стойкости фрезы T=180 мин 11;
- подача на один зуб фрезы =01 мм 11;
z – число зубьев фрезы z=10 11;
где - коэффициент учитывающий влияние материала заготовки 11;
где =1 - коэффициент характеризующий группу стали по обрабатываемости 11;
=1 - показатель степени зависящий от вида обрабатывающего инструмента 11;
=08 - коэффициент учитывающий влияние состояния поверхности заготовки 11;
=1 - коэффициент учитывающий влияние материала инструмента 11.
Частота вращения фрезы обмин:
Выбираем из стандартного ряда чисел оборотов станка n=800 обмин тогда уточняем :
Рассчитаем силу резания. Окружная сила Н:
где 825 1 075 11 13 – коэффициент и показатели степени 11;
– показатель степени при определении окружной силы резания при фрезеровании 11.
Выбираем по полученной мощности вертикально-фрезерный станок с ЧПУ 6Р13Ф3 11.
Рассчитаем основное и вспомогательное время:
В выпускной квалификационной работе был разработан крано-манипуляторная установка грузоподъёмностью три тонны на базе автомобиля КамАЗ-6510. Манипулятор в качестве сменного рабочего оборудования имеет крюковую подвеску ротатор клещевой захват и траверсу.
Манипулятор установлен в задней части кузова автомобиля на дополнительной раме что позволяет обслуживать большее рабочее пространство чем манипулятор установленный за кабиной автомобиля.
При проектировании с манипулятором были проведены силовые и прочностные расчёты расчёт на устойчивость сделан анализ конструкций машин данного класса выполнены разделы по мерам безопасности при эксплуатации КМУ и экономической части разработан технологический процесс изготовления траверсы крюковой подвески.
Внедрение предлагаемой машины на предприятии позволит увеличить мобильность рабочей бригады исключит зависимость от крана позволит не отвлекать дорогостоящий кран от его основной работы что позволит предприятию получить значительный экономический эффект.
Список используемой литературы
Эксплуатация дорожных машинПод ред. А.М. Шейнина. – М.: Транспорт 1992. – 328 с.
Рекомендации по организации технического обслуживания и ремонта строительных машин. – М.: Стройиздат 1973.–92с.
Дьякова Г.Д. Конструкция и модернизация машин и оборудования. Методические указания по разработке экономической части дипломных проектов для студентов специальности 150400 “Подъёмно-транспортные строительные и дорожные машины и оборудование”. Хабар. Гос. техн. университет 1993. - 42 с.
Добронравов С.С. Строительные машины и оборудование: Справочник для строит. Спец. вузов и инж. –техн. работников. М.: Машиностроение 1985.
Панкратов С.А. Ряхин В.А. Основы расчета и проектирования металлических конструкций строительных и дорожных машин М.: Машиностроение 1967.
Красников В.В. и др. Подъемно-транспортные машины – 4-е изд. перераб. И доп. – М.: Агропромиздат 1987.-272 с.
Каверзин С.В. Курсовое и дипломное проектирование по гидроприводу самоходных машин. М.: Машиностроение 1997. – 85 с.
Анурьев В.И. Справочник конструктора машиностроителя: В 3 т. Т2. – М.: Машиностроение 1982. – 584 с. ил.
Косилова А.Г. Мещеряков Р.К. Точность обработки заготовки и припуски в машиностроении. Справочник в 2 т. – Т.2. – М.: Машиностроение 1985. – 496 с.
Горбацевич А.Ф Шкред В.А. Курсовое проектирование по технологии машиностроения. – Минск: Высшая школа 1983.
Панов А.А. Обработка металлов резанием: Справочник технолога А.А. Панов В.В. Аникин Н.Г. Бойм и др.: Под ред. А.А. Панова – М. 1988.
Воробьев Л.Н. Технология машиностроения и ремонт машин. – М.: Машиностроение 1981.
Салов А.И. Охрана труда на предприятиях автомобильного транспорта. – М.: Транспорт 1985. – 351 с.
ГОСТ 12.1.003-83* "Система стандартов безопасности труда. Шум. Общие требования безопасности
ГОСТ 12.1.012-90 "Система стандартов безопасности труда. Вибрационная безопасность. Общие требования".
ГОСТ 12.1.005-88 "Система стандартов безопасности труда. Общие санитарно-гигиенические требования к воздуху рабочей зоны".
Филиппов Б.И. Охрана труда при эксплуатации строительных машин. – М.: Высшая школа 1984. – 247 с.
СНИП 23-05-95. Естественное и искусственное освещение.
Исследование естественной освещённости: Методичесие указания к лабораторной работе по курсу безопасности жизнедеятельности для студентов всех специальностей Сост. П.Ю. Юрасова Л.П. Майорова М.Н. Кофанов.: Хабаровск Изд-во Хабар. гос. тех. ун-та. 1998. – 27 с.
ГОСТ 12.1.046-85 «Освещение. Общие требования».
СНИП 21-01-97 Пожарная безопасность зданий и сооружений.
Дьякова Г.Д. Конструкция и модернизация машин и оборудования. Методические указания по разработке экономической части дипломных проектов для студентов специальности 170900 “Подъёмно-транспортные строительные и дорожные машины и оборудование”. Хабар. Гос. техн. университет 2002. -26 с.
Расчеты - 2 (53стр.).docx
В данной части работы была выбрана компоновочная схема и произведены расчёты манипулятора на устойчивость а также выполнен тяговый расчёт.
1 Выбор компоновочной схемы и ее расчет
1.1 Расчет центра тяжести манипулятора
Расчетная схема манипулятора изображена на рисунке 21.
Рисунок 21 – Исходные данные для расчета центра тяжести манипулятора
Исходные данные для расчета:
) - координаты точки А; - координаты центра тяжести колонны; - сила тяжести колонны кН;
) - минимальный угол подъема стрелы; - максимальный угол подъема стрелы; - длина стрелы мм; - расстояние от точки А до центра тяжести стрелы мм; - сила тяжести стрелы кН;
) - минимальный угол выноса рукояти; - максимальный угол выноса рукояти; - минимальная длина рукояти (удлинитель задвинут) мм; - максимальная длина рукояти (удлинитель выдвинут) мм; - расстояние от точки В до центра тяжести рукояти при задвинутом удлинителе мм; - расстояние от точки В до центра тяжести рукояти при выдвинутом удлинителе мм; - сила тяжести рукояти кН; - высота от оси рукояти до точки С мм; - коэффициент равный отношению изменения расстояния к изменению расстояния ;
) - расстояние от точки С до нижней точки грейфера мм; - расстояние от точки С до центра тяжести грейфера ротатора и подвески мм; - сила тяжести захвата (грейфера) кН; - угол отклонения захвата (отклонение в сторону начала координат – знак "минус").
1.1.1 Расчет центра тяжести стрелы
Расчет сводится к определению координат центра тяжести стрелы и определению координат центра тяжести точки В для возможности построения траектории движения стрелы при различных значениях угла . Расчетная схема изображена на рисунке 22.
Рисунок 22 – Схема определения координат центра тяжести стрелы
Координаты центра тяжести определяются по формулам:
Координаты точки В определяются по формулам:
1.1.2 Расчет центра тяжести рукояти
Расчет сводится к определению центра тяжести рукояти и координат точки С в зависимости от угла выноса рукояти и расстояния вылета удлинителя.
Расчетная схема представлена на рисунке 23.
Рисунок 23 – Схема определения координат центра тяжести рукояти
Координаты точки С определяются по формулам:
Координаты центра тяжести рукояти манипулятора определяются по формулам:
1.1.3 Расчет координат центра тяжести клещевого захвата
Расчет сводится к определению координат нижней точки захвата Д и координат центра тяжести клещевого захвата с ротатором.
Расчетная схема представлена на рисунке 24.
Координаты точки Д определяются по формулам:
Координаты точки центра тяжести захвата определяются по формулам:
Рисунок 24 – Схема координат центра тяжести клещевого захвата
1.1.4 Изменение координат центра тяжести манипулятора
При вращении колонны манипулятора вокруг своей оси необходимо вводить третью пространственную координату Z и делать поправку в других координатах центра тяжести из-за их изменения в результате этого вращения.
Расчетная схема изображена на рисунке 25.
Координаты точки А при повороте колонны на угол определяются по формулам:
Рисунок 25 – Схема изменения координат при вращении колонны
1.2 Расчет центров тяжести манипулятора
Производится расчет центров тяжести манипулятора в транспортном положении и в положении при движении автомобиля с грузом.
Исходя из расчетов центров тяжести элементов манипулятора определяется центр тяжести всего манипулятора по формулам:
где - координаты центров тяжести элементов манипулятора в положении "с грузом";
- массы элементов манипулятора;
- координаты центров тяжести элементов манипулятора в положении "без груза";
- координаты центра тяжести манипулятора в положении "с грузом";
- координаты центра тяжести манипулятора в положении "без груза".
Расчет производиться по приведенному выше алгоритму. Исходные данные и результаты расчетов центра тяжести манипулятора сведен в таблицу 5.
Таблица 5 – Расчет центра тяжести манипулятора
Наименование элемента манипулятора
Гидроцилиндр рукояти
1.3 Компоновка манипулятора
В данной работе будет рассмотрено шасси базового автомобиля КамАЗ-6510.
Эта модель достаточно хорошо обладает свойствами необходимыми автомобилю-сортаментовозу: высокая проходимость хороший дорожный просвет высокая мощность двигателя (при установке на автомобиль КамАЗ-6510 германского двигателя KHD BF8L413) надежность автомобиля.
Основные габаритные размеры шасси автомобиля КамАЗ-6510 изображены на рисунке 26 а краткие технические характеристики автомобиля сведены в таблицу 6.
Рисунок 26 – Основные габаритные размеры автомобиля КамАЗ-6510
Таблица 6 – Краткая техническая характеристика автомобиля-тягача КамАЗ-6510
Технические параметры
Мощность двигателя л.с.
Номинальный оборот коленвала обмин
Номинальный крутящий момент кгсм
Продолжение таблицы 6
Передаточные числа коробки передач:
Передаточные числа раздаточной коробки:
КПД раздаточной коробки
Передаточное число главной передачи
КПД главной передачи
Межосевое расстояние задней тележки мм
Расстояние от оси задней тележки до центра тяжести автомобиля мм
Высота центра тяжести автомобиля мм
Снаряженная масса кг
Допустимая полная масса кг
Расход топлива при скорости 40 кмч л100 км
Ресурс автомобиля тыс. км
Схема компоновки представлена на рисунке 27.
Рисунок 27 – Схема компоновки автомобиля с КМУ
Центры тяжести манипуляторов приведены к оси задней тележки для удобства расчетов. Параметры базового автомобиля приведены по данным 1.
Рассматривая сумму моментов относительно точки 1 получаем формулу для определения реакции дороги на заднюю тележку автомобиля:
Рассматривая сумму моментов относительно точки 2 получаем формулу для определения реакции дороги на переднюю ось автомобиля:
Параметры компоновки для манипулятора и результаты расчетов сведены в таблицу 7.
Таблица 7 – Параметры компоновок автомобиля с КМУ
Параметры компоновок
1.4 Расчет центров тяжести манипулятора
Для упрощения дальнейших расчетов будет целесообразно рассчитать координаты центров тяжести автомобиля с КМУ в груженом и порожнем положениях.
Расчет производиться по формулам:
Исходные данные для расчета приведены в таблице 7. Результаты расчетов координат центров тяжести автомобиля с КМУ представлены в таблице 8.
Таблица 8 – Координаты центров тяжести манипулятора
2 Расчет устойчивости автомобиля с КМУ
2.1 Расчет продольной статической устойчивости автомобиля на уклоне
Схема сил для определения максимального уклона для данного положения автомобиля представлена на рисунке28.
Рассмотрим сумму моментов относительно точки А; принимая во внимание что в момент отрыва переднего колеса .
Из этого уравнения получается формула для определения максимального угла
Рисунок 28 – Схема сил для продольной устойчивости автомобиля с КМУ на уклоне в статике
Результаты расчетов сведены в таблицу 9.
Таблица 9 – Предельные углы уклона для статического положения
2.2 Расчет максимального угла подъема при движении автомобиля на уклоне
Схема сил для определения максимального угла подъема для данного положения автомобиля представлена на рисунке29.
Рисунок 29 – Схема сил для продольной устойчивости автомобиля при движении на подъем
Рассмотрим систему моментов относительно точки А принимая во внимание что в момент отрыва колеса.
где - реактивный момент кгсм.
Реактивный момент рассчитывается по формуле:
где - коэффициент трения качения;
- динамометрический радиус колеса м.
Динамический радиус колеса определяется по формуле:
где - внутренний диаметр шины м;
- высота обода шины м.
Здесь где - ширина шины м.
Тогда максимальный угол подъема определяется по формуле:
Предельный угол подъема ограничивается сцеплением движителя с почвой и определяется по формуле:
где - коэффициент сцепления колес с грунтовой дорогой.
Предельный угол подъема ограничивается мощностью движителя и определяется по формуле:
где - касательная сила тяги кгс;
- суммарная сила сопротивления движению машины кгс.
Касательная сила тяги определяется по формуле:
где - эффективный крутящий момент на валу двигателя кгсм;
- общее передаточное число трансмиссии;
Суммарная сила сопротивления движению автомобиля определяется по формуле:
Необходимые исходные данные и результаты вычисления представлены в таблице 10.
Таблица 10 – Предельные углы подъема в динамике
2.3 Расчет поперечной устойчивости автомобиля с КМУ в транспортном положении на склоне
Расчетная схема сил для определения минимального угла склона для данного положения автомобиля представлена на рисунке 30.
Рисунок 30 – Схема сил для определения поперечной устойчивости в транспортном положении
Рассмотрим сумму моментов относительно точки А принимая во внимание что в момент отрыва колеса .
Отсюда максимальный угол склона определяется по формуле:
Результаты расчета максимального угла для различных видов компоновки автомобиля представлены в таблице 11.
Таблица 11– Расчет поперечной устойчивости в транспортном положении
2.4 Расчет устойчивости автомобиля с максимальным вылетом манипулятора в сторону
Расчетная схема сил действующих на автомобиль с КМУ представлена на рисунке 31.
Рисунок 31– Схема сил для определения поперечной устойчивости автомобиля при работе манипулятора на максимальном вылете
Рассмотрим моменты относительно точки А. Устойчивость характеризуется коэффициентом устойчивости:
где - стабилизирующий момент кгсм;
- опрокидывающий момент.
Стабилизирующий момент определяется по формуле:
где - вес порожнего автомобиля кг;
- половина расстояния между аутригерами м;
- координата манипулятора в системе координат (см. 2.1.1) м;
- вес манипулятора кг.
Координата в данном случае равна:
где - угол поворота платформы;
- координата центра тяжести манипулятора мм;
- расстояние между осью 0Y и точкой А в транспортном положении манипулятора мм;
- расстояние между осью поворота колонны и точкой А мм.
Опрокидывающий момент определяется как:
где - расстояние от оси поворота колонны до груза при максимальном вылете м.
Результаты расчетов представлены в таблице 12.
Таблица 12 – Расчет поперечной устойчивости при погрузке
Допустимая величина коэффициента устойчивости . Следовательно для автомобиля с КМУ условие устойчивости выполняется.
2.5 Расчет устойчивости автомобиля при поперечном склоне с максимальным вылетом манипулятора
Расчетная схема сил для определения устойчивости при данном положении автомобиля представлена на рисунке 32.
Рисунок 32 – Схема сил для определения устойчивости при работе на уклоне
Рассмотрим моменты относительно точки А. Устойчивость характеризуется коэффициентом устойчивости который определяется по формуле:
В данном случае стабилизирующий момент будет равен:
Опрокидывающий момент будет равен:
где - высота центра тяжести базового автомобиля м;
- высота центра тяжести манипулятора м;
- высота подъема груза при максимальном вылете КМУ м.
Подставив данные выражения в формулу (33) и проведя необходимые математические преобразования получаем формулу для определения максимального угла поперечного уклона при данном положении автомобиля:
Исходя из условия что допустимый коэффициент устойчивости производиться расчет максимального угла поперечного уклона.
Исходные данные и результаты расчета максимального угла представлены в таблице 13.
Таблица 13 – Расчет продольной устойчивости при работе автомобиля на склоне
2.6 Расчет устойчивости при движении автомобиля с КМУ на повороте
Условие опрокидывания автомобиля при движении на повороте определяется по формуле:
где - ширина колеи автомобиля м;
- радиус поворота автомобиля м;
- высота центра тяжести груза м;
- ускорение свободного падения;
- скорости движения при опрокидывании.
При движении автомобиля с КМУ на повороте возможен случай заноса. Условие заноса автомобиля укладывается в формулу:
где = 06 – коэффициент скольжения для грунтовой дороги с щебеночным покрытием.
Желательно чтобы выполнялось условие .
Необходимые исходные данные и результаты расчетов представлены в таблице 14.
Таблица 14 – Расчет устойчивости автомобиля при движении на повороте
2.7 Тяговый расчет автомобиля с КМУ
По данным технических характеристик автомобилей КамАЗ (таблица 6) производиться расчет тяговой характеристики для данного автомобиля. Тяговое усилие определяется по формуле (33). Скорость движения кмч на различных передачах определяется по формуле:
где - крутящий момент на валу электродвигателя обмин;
- передаточное число трансмиссии.
Результаты расчета для автомобиля КамАЗ-6510 представлены в таблице 15.
Таблица 15 – Тяговая характеристика автомобиля КамАЗ-6510
Обороты двигателя обмин
Продолжение таблицы 15
3 Проектирование и расчет манипулятора
3.1 Расчет проектных параметров манипулятора
3.1.1 Данные для расчета
- сила тяжести клещевого захвата;
- сила тяжести рукояти с удлинителем и гидроцилиндром удлинителя;
- сила тяжести стрелы;
- сила тяжести механизмов складывания стрелы;
- сила тяжести гидроцилидра рукояти;
- сила тяжести гидроцилиндра стрелы;
- плечи указанных выше сил для трех положений манипулятора (приведенных в таблице 16 относительно шарнира и в таблице 17 – относительно шарнира С);
- плечи усилий в механизме складывания относительно шарниров С и С' (рисунок 33). Значения для трех положений манипулятора приведены в таблице 17;
- плечо действия усилия развиваемого гидроцилиндрами стрелы относительно шарнира В (рисунок 33).
Указанные плечи сил для трех положений манипулятора рассчитываются аналитически исходя из экспериментально найденных расстояний между осями различных шарниров манипулятора.
3.1.2 Расчетная схема и расчет параметров
Расчетная схема манипулятора представлена на рисунке 33.
Рисунок 33 – Расчетная схема манипулятора для трех положений
Максимальное усилие развиваемое поршневой полостью гидроцилиндра стрелы определяется по формуле:
где мм – диаметр поршня гидроцилиндра стрелы;
МПа – давление рабочей жидкости;
- КПД гидроцилиндра.
Максимальное усилие развиваемое штоковой полостью гидроцилиндра рукояти манипулятора определяется по формуле:
где м – диаметр поршня гидроцилиндра рукояти;
м – диаметр штока гидроцилиндра рукояти.
Рассматривая сумму моментов относительно шарнира В и учитывая потерю мощности в шарнирах при трении выводится формула для определения грузоподъемности манипулятора которую позволяет каждый из гидроцилиндров.
Для гидроцилиндра стрелы:
где здесь - количество шарниров трение которых необходимо преодолевать гидроцилиндру стрелы.
Для гидроцилиндра рукояти:
Результаты расчетов сведены в таблицу 16 и таблицу 17.
Таблица 16 – Параметры манипулятора относительно шарнира В
Положения манипулятора
Продолжение таблицы 16
Таблица 17 – Параметры манипулятора относительно шарнира О
3.2 Расчет нагрузок манипулятора
3.2.1 Расчет реальных усилий гидроцилиндра рукояти и гидроцилиндра стрелы
Сравнивая последние строки таблиц 16 и 17 выбираются для каждого положения манипулятора наименьшие значения силы тяжести груза определяются грузоподъемность манипулятора.
Усилие в гидроцилиндре рукояти определяется по формуле:
где - сумма изгибающих моментов относительно шарнира О от сил тяжести элементов манипулятора;
- грузоподъемность манипулятора в данном положении.
Усилие в гидроцилиндре стрелы определяется по формуле:
где - сумма изгибающих моментов относительно шарнира В от сил тяжести элементов манипулятора.
Исходные данные и результаты вычислений сведены в таблицу 18.
Таблица 18 – Реальные усилия в гидроцилиндрах манипулятора
3.2.2 Расчет усилий в механизме складывания рукояти
Механизм складывания рукояти рассчитывается для положений манипулятора (II') и (I') как наиболее нагруженных. Расчетная схема для определения усилий в механизме складывания приведена на рисунке 34.
Рисунок 34 – Расчетная схема механизма складывания рукояти
Их масштабной расчетной схемы механизма складывания рукояти определяется:
) угол между линией действия усилия в шатуне СД () и горизонталью;
) угол между линией действия усилия гидроцилиндра рукояти и вертикалью;
) Плечо ОК – расстояние от шарнира О до линии действия усилия в шатуне.
Рассматривая рукоять отдельно от стрелы заменяя ее воздействие реакциями в шарнирах.
Рассматривая сумму моментов сил относительно шарнираО получается формула для определения усилия в шатуне:
где здесь - количество шарниров трение в которых мешает вращению.
Рассматривая суммы сил по горизонтали и вертикали получаем формулы для определения составляющих реакции в шарнире О:
Рассматривая стрелу отдельно от рукояти соответственно заменяя ее воздействие реакциями в шарнирах.
Рассматривая суммы сил по горизонтали и по вертикали получаем формулы для определения составляющих реакции в шарнире О':
Исходные данные и результаты расчетов сведены в таблице 19.
Таблица 19 – Расчет усилий в механизме складывания рукояти
Положение манипулятора
Сила тяжести рукояти кН
Сила тяжести захвата кН
Продолжение таблицы 19
Сила тяжести груза кН
3.2.3 Расчет реакций в шарнире В и в шарнирах гидроцилиндра стрелы
Расчетная схема для определения указанных реакций приведена на рисунке 35 для положения II'.
Рисунок 35 – Расчетная схема
Расчет производится для положения II' как наиболее нагруженного.
Реакции в шарнире М от усилия гидроцилиндра стрелы определяются по формулам:
где - усилие гидроцилиндра подъема стрелы в положении манипулятора II';
- угол между линией действия усилия и осью Y (вертикалью).
Рассматривая сумму сил по оси Y (вертикали) получаем формулу для определения вертикальной составляющей реакции в шарнире В:
Рассматривая сумму сил по оси X (горизонтали) получаем формулу для определения горизонтальной составляющей реакции в шарнире В:
Тогда реакция в шарнире В определяется по формуле:
Исходные данные и результаты расчетов представлены в таблице 20.
Таблица 20 – Расчет реакции в шарнире В (II')
Примечание: Угол для данного положения манипулятора рассчитан исходя из экспериментально найденных расстояний между осями рассматриваемых шарниров с применением для расчета теорем косинусов.
Расчетная схема для определения реакции в шарнире В при положении манипулятора I' приведена на рисунке 36.
Рисунок 36 – Расчетная схема
Вертикальная и горизонтальная составляющие реакции в шарнире В определяются по формулам при расчете тех же реакций для положения II'. Результаты расчетов представлены в таблице 21.
Таблица 21 – Расчет реакции в шарнире В (I')
3.4 Расчет шарнирных узлов
3.4.1 Расчет шатуна на прочность
Шатун работает на растяжение сжатия. Сила действующая вдоль оси шатуна =38405 кН (таблица 19).
Определяется напряжение растяжения-сжатия в сечении I-I и в сечении II-II согласно рисунку 37.
Площадь сечения м2 определяется по формуле:
Момент инерции сечения относительно OX м4 определяется по формуле:
Рисунок 37 – Геометрические параметры шатуна
Исходные геометрические данные и результаты расчетов сведены в таблицу 22.
Таблица 22 – Геометрические параметры шатуна
Коэффициент динамичности определяются по формуле:
где - масса манипулятора и груза приведенная к конце рукояти кг;
– скорость перемещения груза мс;
- максимальный вылет манипулятора м;
- модуль упругости стали нм2;
- момент инерции сечения элементов манипулятора м4;
- величина прогиба металлоконструкции в статике м.
Приведенная к концу рукояти масса манипулятора и груза определяется по формуле:
- вылет манипулятора относительно сечения м.
Для положения II' (2.3.1.1) м; м;
Скорость перемещения груза есть скорость опускания рукояти которая определяется по формуле:
где - скорость подъема рукояти мс
где м – длина рукояти;
- угол поворота рукояти;
м – ход поршня гидроцилиндра рукояти;
- скорость движения поршня гидроцилиндра рукояти мс.
Скорость движения поршня определяется по формуле:
где - объемный КПД насоса;
мс - расход рабочей жидкости;
м - диаметр поршня гидроцилиндра рукояти.
Величина прогиба металлоконструкции в статике определяется по формуле:
где мс – ускорение свободного падения.
Результаты расчета скоростей и коэффициента динамичности представлены в таблице 23.
Таблица 23 – Расчет коэффициента динамичности сечения шатуна в положении II'
Напряжение растяжения-сжатия в сечении I-I определяется по формуле:
Допустимое напряжение для стали 16Г2АФ МПа.
Напряжение разрыва в сварных швах определяется по формуле:
где м – толщина соединяемых деталей;
- длина сварного шва м.
Длина сварного шва для данной детали определяется по зависимости:
Напряжение разрыва в сварных швах с учетом коэффициента динамичности определяется по формуле:
Допускаемые напряжения основного металла в металлических строительных и крановых конструкциях определяются по формуле:
где - расчетное сопротивление разрушению для низколегированной стали;
- коэффициент условий работы;
МПа – напряжение разрыва согласно 4 для стали 16Г2АФ.
При переменных нагрузках расчетные напряжения умножают на коэффициент который определяется по формуле:
- характеристика цикла.
Величина МПа определяется по формуле:
где кН – усилие в шатуне при согласно формуле (54).
Результаты расчетов действующих и допускаемых напряжений в сечениях I-I и II-II представлены в таблице 24.
Таблица 24 – Расчетные и допускаемые напряжения в сечениях I-I и II-II
Сравнивая допускаемые напряжения с расчетными делается вывод о выполнении условия прочности так как .
3.4.2 Расчет на прочность пальцев шарниров
В манипуляторе 13 шарнирных узлов. Их расположение и обозначение указано на рисунке 38.
Пальцы в манипуляторе рассчитываются на срез. Расчетная схема изображена на рисунке 39.
Вид поперечного сечения пальцев показан на рисунке 40.
Рисунок 38 – Схема расположения шарниров
Рисунок 39 – Расчетная схема для расчета пальцев
Рисунок 40 – Поперечное сечение пальцев
Площадь сечения пальцев определяется по формуле:
где - наружный диаметр пальца м;
- внутренний диаметр пальца м.
Напряжение среза определяется по формуле:
- площадь сечения i-го шарнира м2.
Исходные данные и результаты расчетов представлены в таблице 25.
Таблица 25 – Расчет пальцев на срез
Расчетная схема для определения усилий в шарнирах 2-2 и 3-3 представлена на рисунке 41.
Рисунок 41 – Схема сил в шарнирах 2-2 и 3-3
Срезающее усилие в шарнирах 2-2 и 3-3 определяется по формуле:
где - срезающая составляющая от силы тяжести груза и захвата с ротатором;
- срезающая составляющая от момента инерции создаваемого вращением ротатора.
Составляющая срезающей силы определяется по формуле:
где - грузоподъемность манипулятора в данном положении кН.
Для определения составляющей срезающей силы записываем основное уравнение динамики для данной системы
Отсюда следует формула:
где - момент инерции в системе кНм;
- момент создаваемый ротатором кНм;
- i-ое плечо равное расстоянию от оси подвески до сечения среза пальца м.
Тогда составляющая срезающей силы будет равна:
Расчетная схема для определения усилий в шарнирах 9-9 и 10-10 представлена на рисунке 42.
Рассматривая сумму сил на ось Х получается формула для определения усилия гидроцилиндра телескопа:
где - угол подъема рукояти;
- коэффициент трения. Для пары трения сталь-фторопласт .
Рисунок 42 – Схема сил в шарнирах 9-9 и 10-10
3.4.3 Расчет втулок шарнирных узлов
Расчет производиться по удельным давлениям. Удельное давление во втулке шарнира определяется по формуле:
- внутренний диаметр втулки м;
Исходные данные и результаты расчетов сведены с таблицу 26.
Таблица 26 – Расчет втулок в шарнирах
Расчетные и исходные параметры
3.4.4 Расчет проушин шарнирных узлов
Расчет производиться на напряжение смятия и изгиба с растяжением.
3.4.4.1 Расчет проушин на смятие
Удельное давление в проушине определяется по формуле:
где - внутренний диаметр проушины м;
- ширина проушины в месте вероятного сжатия м.
Исходные данные и результаты расчетов сведены в таблицу 27.
Обозначение проушин соответствует обозначению шарнирных узлов согласно рисунку 38.
Таблица 27 – Расчет втулок в шарнирах
Допустимые напряжения для стали 16Г2АФ МПа 8 следовательно можно сделать вывод о выполненных условиях прочности на смятие.
3.4.4.2 Расчет проушины на изгиб с растяжением
Рассматриваем проушину как кривой брус. Расчетная схема и сечение проушины представленные на рисунке 43.
Рисунок 43 – Расчетная схема для расчета проушины на изгиб с растяжением
Напряжение в проушине от изгиба и растяжения определяется по формуле:
где - изгибающий момент в сечении кНм;
- площадь сечения м2;
- радиус кривизны оси бруса м;
- радиус кривизны нейтрального слоя;
- расстояние от центра кривизны бруса до точки в которой определяется напряжение;
- продольная сила растяжения сжатия.
Изгибающий момент в сечении определяется по формуле:
где - максимальное значение конечной радиальной нагрузки распределенной по закону синуса кНм;
- угол определяющий сечение бруса.
Продольная сила растяжения-сжатия определяется по формуле:
где - угол сечения I-I;
- угол сечения II-II.
Площадь сечения определяется по формуле:
Радиус кривизны нейтрального слоя в сечении определяется по формуле:
Исходные данные и результаты вычислений сведены в таблицу 28.
Удельное давление на проушины определяется по формуле:
где - реакция опоры на телескоп кН
Допустимое удельное давление для материала МАС .
БЖД - 3 (22стр.).docx
Охрана труда— система сохранения жизни и здоровья работников в процессе трудовой деятельности.
Инцидент - небезопасное происшествие связанное с работой или произошедшее в процессе работы но не повлекшее за собой несчастного случая.
Опасность - фактор среды и трудового процесса который может быть причиной травмы острого заболевания или внезапного резкого ухудшения здоровья. В зависимости от количественной характеристики и продолжительности действия отдельных факторов рабочей среды они могут стать опасными.
Оценка опасностей - систематическое оценивание опасностей.
Оценка риска - процесс анализа рисков вызванных воздействием опасностей на работе для определения их влияния на безопасность и сохранение здоровья работников.
Подрядчик - лицо или организация представляющие услуги работодателю на территории работодателя в соответствии с договором согласованными техническими требованиями сроками и условиями.
Проверка - систематический независимый оформленный в виде документа процесс получения и объективной оценки данных степени соблюдения установленных критериев.
Производственный участок - физическая зона находящаяся под контролем работодателя где работник должен находиться или куда ему необходимо прибыть для выполнения трудовых обязанностей.
Работник - физическое лицо вступившее в трудовые отношения с работодателем.
Риск - сочетание вероятности возникновения в процессе трудовой деятельности опасного события тяжести травмы или другого ущерба для здоровья человека вызванных этим событием.
2 Требования к персоналу
К самостоятельной работе оператором (машинистом) крана-манипулятора допускаются лица не моложе 18 лет прошедшие медицинское освидетельствование вводный инструктаж первичный инструктаж на рабочем месте обучение и стажировку на рабочем месте проверку знаний требований охраны труда соответствующую подготовку имеющие удостоверение на право вождения автомобильного крана-манипулятора и профессиональные навыки машиниста имеющие группу по электро-безопасности не ниже II и соответствующую квалификацию согласно тарифно-квалификационного справочника.
2.1. Общие требования охраны труда
Оператор (машинист) обязан: выполнять только ту работу которая определена рабочей инструкцией; выполнять правила внутреннего трудового распорядка; правильно применять средства индивидуальной и коллективной защиты; соблюдать требования охраны труда; немедленно извещать своего непосредственного или вышестоящего руководителя о любой ситуации угрожающей жизни и здоровью людей о каждом несчастном случае происшедшем на производстве или об ухудшении состояния своего здоровья в том числе о проявлении признаков острого профессионального заболевания (отравления); проходить обучение безопасным методам и приемам выполнения работ и оказанию первой помощи пострадавшим на производстве инструктаж по охране труда проверку знаний требований охраны труда; проходить обязательные периодические (в течение трудовой деятельности) медицинские осмотры (обследования) а также проходить внеочередные медицинские осмотры (обследования) по направлению работодателя в случаях предусмотренных Трудовым кодексом и иными федеральными законами; уметь оказывать первую доврачебную помощь пострадавшим от электрического тока и при других несчастных случаях; уметь применять средства первичного пожаротушения;
При выполнении производственных процессов с краном-манипулятором возможны воздействия следующих опасных и вредных производственных факторов:
повышенный уровень шума на рабочем месте;
повышенный уровень вибрации;
повышенное содержание в воздухе рабочей зоны пыли и вредных веществ;
нахождение рабочего места на высоте;
повышенное напряжение в электрической цепи замыкание которой может пройти через тело человека;
движущиеся машины механизмы и их части;
опрокидывание машин падение их частей;
повышенная или пониженная температура воздуха рабочей зоны;
Оператор (машинист) крана-манипулятора после перерыва в работе по специальности более одного года должен пройти проверку знаний в установленном порядке и в случае удовлетворительных результатов проверки могут быть допущены к стажировке для восстановления необходимых навыков. Повторная проверка знаний должна проводиться:
периодически не реже одного раза в 12 мес.;
при переходе на другое место работы;
по требованию инспектора Ростехнадзора или инженерно-технического работника по надзору за безопасной эксплуатацией кранов-манипуляторов.
В процессе повседневной деятельности оператор (машинист) должен:
применять в процессе работы машины по назначению в соответствии с инструкциями заводов-изготовителей;
поддерживать машину в технически исправном состоянии не допуская работу с неисправностями при которых эксплуатации запрещена;
содержать механизмы и оборудование крана-манипулятора в чистоте и исправности;
своевременно производить смазку всех механизмов крана-манипулятора и канатов;
быть внимательным во время работы и не допускать нарушений требований охраны труда.
Оператор (машинист) прошедший обучение и имеющий удостоверение на право управления грузоподъемными кранами-манипуляторами должен знать:
руководства по эксплуатации кранов-манипуляторов и приборов безопасности предприятий-изготовителей;
производственную инструкцию;
устройство кранов-манипуляторов назначение принципы действия и устройство узлов механизмов и приборов безопасности кранов-манипуляторов;
знать сроки и результаты проведенных технических освидетельствований и технических обслуживании (ТО-1 ТО-2 ТО-3 СО) крана-манипулятора;
знать сроки и результаты проведенных слесарями и электромонтерами профилактических периодических осмотров крана-манипулятора и его отдельных механизмов и узлов по записям в журнале периодических осмотров.
устройство грузозахватных приспособлений методы строповки грузов;
инструкцию по охране труда;
приемы и способы оказания первой помощи пострадавшим.
В случаях травмирования или недомогания необходимо прекратить работу известить об этом руководителя работ и обратиться в медицинское учреждение. За невыполнение данной инструкции виновные привлекаются к ответственности согласно законодательства Российской Федерации.
2.2 Требования охраны труда перед началом работы
Прежде чем приступить к работе оператор (машинист) должен убедиться в исправности всех механизмов металлоконструкций и других частей крана-манипулятора. При этом он должен:
осмотреть механизмы крана-манипулятора их крепление и тормоза а также ходовую часть тяговые и буферные устройства;
проверить наличие и исправность ограждений механизмов;
проверить смазку передач подшипников и канатов а также состояние смазочных приспособлений и сальников;
осмотреть в доступных местах металлоконструкции и соединения секций стрелы и элементов ее подвески (канаты растяжки блоки серьги и т.п.) а также металлоконструкции и сварные соединения ходовой рамы (шасси) и поворотной части;
осмотреть в доступных местах состояние канатов и их крепление на барабане стреле грейфере а также укладку канатов в ручьях блоков и барабанов;
осмотреть крюк и его крепление в обойме;
проверить исправность дополнительных опор (выдвижных балок домкратов) и стабилизаторов;
проверить наличие и исправность приборов и устройств безопасности;
проверить исправность освещения крана-манипулятора буферных фонарей и фар;
при приемке крана-манипулятора с гидроприводом осмотреть систему привода гибких шлангов если они применяются насосов и предохранительных клапанов на напорных линиях.
Оператор (машинист) обязан вместе со стропальщиком проверить соответствие грузозахватных приспособлений массе и характеру груза их исправность и наличие на них клейм или бирок с указанием грузоподъемности даты испытания и номера.
После осмотра крана-манипулятора перед его пуском в работу оператор (машинист) убедившись в соблюдении требуемых габаритов приближения обязан опробовать все механизмы на холостом ходу и проверить при этом исправность действия:
механизмов крана-манипулятора и электрической аппаратуры если таковая имеется;
приборов и устройств безопасности имеющихся на кране-манипуляторе;
При обнаружении во время осмотра и опробования крана-манипулятора неисправностей или недостатков в его состоянии препятствующих безопасной работе и невозможности их устранения своими силами оператор (крановщик) не приступая к работе должен доложить об этом инженерно-техническому работнику ответственному за содержание крана-манипулятора в исправном состоянии и поставить в известность лицо ответственное за безопасное производство работ кранами-манипуляторами.
Работа крана-манипулятора вблизи линии электропередачи должна производиться под непосредственным руководством лица ответственного за безопасное производство работ кранами-манипуляторами которое должно указать оператору (машинисту) место установки крана-манипулятора обеспечить выполнение предусмотренных нарядом-допуском условий работы и произвести запись в вахтенном журнале о разрешении работы.
Разрешение на пуск в работу гусеничных и пневмоколесных кранов-манипуляторов после перестановки их на новый объект выдается инженерно-техническим работником по надзору за безопасной эксплуатацией кранов-манипуляторов на основании проверки состояния крана-манипулятора и обеспечения безопасных условий его работы с записью в вахтенном журнале.
Краны-манипуляторы могут быть допущены к перемещению только тех грузов масса которых не превышает их грузоподъемность с учетом положения выносных опор. При эксплуатации крана-манипулятора не должны нарушаться требования изложенные в его паспорте и руководстве по эксплуатации. Перемещение груза несколькими кранами-манипуляторами производится в соответствии с проектом производства работ или технологической картой в которых должны быть приведены схемы строповки и перемещения груза с указанием последовательности выполнения операций положения стрел а также требования по безопасному перемещению груза. При подъеме и перемещении груза несколькими кранами-манипуляторами нагрузка приходящаяся на каждый из них не должна превышать его грузоподъемность. Работа по перемещению груза несколькими кранами-манипуляторами должна производиться под непосредственным руководством лица ответственного за безопасное производство работ кранами-манипуляторами.
Находящиеся в эксплуатации краны-манипуляторы должны быть снабжены табличками с четко обозначенным регистрационным номером грузоподъемностью и датой следующего частичного или полного технического освидетельствования.
Краны-манипуляторы и съемные грузозахватные приспособления не прошедшие технического освидетельствования к работе не допускаются. Неисправные грузозахватные приспособления а также приспособления не имеющие бирок (клейм) не должны находиться в местах производства работ.
При эксплуатации кранов-манипуляторов необходимо принять меры по предотвращению их опрокидывания или самопроизвольного перемещения под действием ветра или при наличии уклона площадки.
Владельцем крана-манипулятора или производителем работ должны быть разработаны способы правильной строповки грузов которым должны быть обучены стропальщики. Графическое изображение способов строповки грузов должно быть выдано на руки стропальщикам и операторам (машинистам) или вывешено в местах производства работ. Перемещение груза на который не разработаны схемы строповки должно производиться в присутствии и под руководством лица ответственного за безопасное производство работ кранами-манипуляторами.
Место производства работ кранами-манипуляторами должно быть освещено в соответствии с проектом производства работ или нормативными документами. Работа крана-манипулятора должна быть прекращена во время снегопада дождя или тумана а также в других случаях когда оператор (машинист) не различает сигналы стропальщика или перемещаемый груз.
2.3 Требования охраны труда во время работы
При работе крана-манипулятора оператор (машинист) должен руководствоваться требованиями и указаниями изложенными в руководстве по эксплуатации крана-манипулятора инструкции по охране труда и производственной инструкции. Оператор (машинист) во время работы механизмов крана-манипулятора не должен отвлекаться от своих прямых обязанностей а также производить чистку смазку и ремонт механизмов.
При необходимости ухода с крана-манипулятора оператор (машинист) обязан остановить двигатель приводящий в движение механизмы крана-манипулятора и убрать ключ зажигания у автомобильных кранов-манипуляторов. При отсутствии оператора (машиниста) стажеру и другим лицам управлять краном-манипулятором не разрешается.
Прежде чем осуществить какое-либо движение краном-манипулятором оператор (машинист) обязан убедиться в том что стажер находится в безопасном месте а в зоне работы крана-манипулятора нет посторонних людей.
Если в работе механизмов крана-манипулятора был перерыв то перед их включением крановщик обязан подать предупредительный звуковой сигнал.
Во время перемещения крана-манипулятора с грузом положение стрелы и грузоподъемность крана-манипулятора следует устанавливать в соответствии с указаниями содержащимися в руководстве по эксплуатации крана-манипулятора. Производить одновременно перемещение крана-манипулятора и поворот стрелы не разрешается.
Оператор (машинист) обязан устанавливать кран-манипулятор на все дополнительные опоры во всех случаях когда такая установка требуется по паспортной характеристике крана-манипулятора; при этом он должен следить чтобы опоры были исправны и под них были подложены прочные и устойчивые подкладки являющиеся инвентарной принадлежностью крана-манипулятора. Подкладывать под дополнительные опоры случайные предметы не разрешается.
Запрещается нахождение оператора (машиниста) в кабине при установке крана-манипулятора на дополнительные опоры а также при освобождении его от опор.
Установка крана-манипулятора на краю откоса котлована (канавы) допускается при условии соблюдения расстояний от начала откоса котлована (канавы) до края опорного контура крана-манипулятора не менее указанных в таблице. При невозможности соблюдения этих расстояний откос должен быть укреплен. Условия установки крана-манипулятора на краю откоса котлована (канавы) должны быть указаны в проекте производства работ кранами-манипуляторами.
Таблица 29 - Минимальное расстояние от начала откоса до края КМУ
песчаный и гравийный
Установка кранов-манипуляторов должна производиться на спланированной и подготовленной площадке с учетом категории и характера грунта. Устанавливать краны-манипуляторы для работы на свеженасыпанном неутрамбованном грунте а также на площадке с уклоном превышающим допустимый для данного крана-манипулятора в соответствии с руководством по эксплуатации крана-манипулятора не разрешается.
Устанавливать КМУ следует так чтобы при работе расстояние между поворотной частью крана-манипулятора при любом его положении и строениями штабелями грузов и другими предметами было не менее 1 м.
Совместная работа по перемещению груза двумя или несколькими кранами-манипуляторами может быть допущена лишь в отдельных случаях и должна осуществляться в соответствии с проектом производства работ или технологической картой в которых должны быть приведены схемы строповки и перемещения груза с указанием последовательности выполнения операций положения грузовых канатов а также содержаться требования к подготовке площадки и другие указания по безопасному перемещению груза.
При перемещении грузов оператор (машинист) должен руководствоваться следующими правилами:
работать краном-манипулятором можно только по сигналу стропальщика. Если стропальщик подает сигнал действуя в нарушение требований инструкции то крановщик по такому сигналу не должен производить требуемого маневра крана-манипулятора. За повреждения причиненные действием крана-манипулятора вследствие выполнения неправильно поданного сигнала несет ответственность как оператор (машинист) так и стропальщик подавший неправильный сигнал. Обмен сигналами между стропальщиком и оператором (машинистом) должен производиться по установленному на предприятии (в организации) порядку. Сигнал «Стоп» оператор (машинист) обязан выполнять независимо от того кто его подает;
необходимо определять по указателю грузоподъемности грузоподъемность крана-манипулятора для каждого вылета;
перед подъемом груза следует предупреждать звуковым сигналом стропальщика и всех находящихся около крана-манипулятора лиц о необходимости уйти из зоны перемещаемого груза возможного падения груза и опускания стрелы. Перемещать груз можно только при отсутствии людей в зоне работы крана-манипулятора. Указанные требования оператор (машинист) должен выполнять также при подъеме и перемещении грейфера. Стропальщик может находиться возле груза во время его подъема или опускания если груз находится на высоте не более 1 м от уровня площадки;
загружать и разгружать вагонетки автомашины и прицепы к ним железнодорожные полувагоны и платформы разрешается только при отсутствии людей на транспортных средствах в чем оператор (машинист) должен предварительно убедиться;
устанавливать крюк подъемного механизма над грузом следует так чтобы при подъеме груза исключалось косое натяжение грузового каната;
при подъеме груза необходимо предварительно поднять его на высоту не более 200—300 мм чтобы убедиться в правильности строповки устойчивости крана-манипулятора и исправности действия тормозом после чего можно поднимать груз на нужную высоту;
при подъеме груза расстояние между обоймой крюка и блоками на стреле должно быть не менее 500 мм;
перемещаемые в горизонтальном направлении грузы (грузозахватные приспособления) следует предварительно приподнять на 500 мм выше встречающихся на пути предметов;
при подъеме стрелы необходимо следить чтобы она не поднималась выше положения соответствующего наименьшему рабочему вылету;
при перемещении груза находящегося вблизи стены колонны штабеля железнодорожного вагона автомашины станка или другого оборудования следует предварительно убедиться в отсутствии стропальщика и других людей между перемещаемым грузом и указанными частями здания транспортными средствами или оборудованием а также в невозможности задевания стрелой или перемещаемым грузом за стены колонны вагоны и др. Укладку грузов в полувагоны на платформы и в вагонетки а также снятие его следует производить не нарушая равновесия полувагонов вагонеток и платформ;
перемещение мелкоштучных грузов должно производиться в специально предназначенной для этого таре при этом должна исключаться возможность выпадения отдельных грузов подъем кирпича на поддонах без ограждения разрешается производить только при погрузке и разгрузке (на землю) автомашин прицепов железнодорожных полувагонов и платформ;
перед подъемом груза из колодца канавы траншеи котлована и т.п. и перед опусканием груза в них следует путем опускания свободного (ненагруженного) крюка предварительно убедиться в том что при его низшем положении на барабане остаются навитыми не менее полутора витков каната не считая витков находящихся под зажимным устройством;
укладывать и разбирать груз следует равномерно не нарушая установленные для складирования грузов габариты и не загромождая проходы;
необходимо внимательно следить за канатами; при спадании их с барабанов или блоков образовании петель или обнаружении повреждений канатов следует приостановить работу крана-манипулятора;
при наличии у крана-манипулятора двух механизмов подъема одновременная их работа не разрешается. Крюк неработающего механизма должен быть всегда поднят в наивысшее положение;
строповка грузов должна производиться в соответствии со схемами строповки. Для строповки должны применяться стропы соответствующие массе и характеру поднимаемого груза с учетом числа ветвей и угла их наклона; стропы общего назначения подбираются так чтобы угол между их ветвями не превышал 90°;
при работе крана-манипулятора с грейфером предназначенным для сыпучих и кусковых материалов не разрешается производить перевалку материала наибольший размер кусков которого превышает 300 мм а также если насыпная масса превышает величину установленную для данного грейфера. Перевалка штучного груза может производиться только специальным грейфером;
работа грейферных кранов допускается при отсутствии в зоне их действия людей. Подсобные рабочие могут допускаться к выполнению своих обязанностей только после перерыва в работе крана после того как грейфер будет опущен на землю;
опускать перемещаемый груз разрешается только на предназначенное для этого место где исключается возможность падения опрокидывания или сползания устанавливаемого груза. На место установки груза должны быть предварительно уложены подкладки соответствующей прочности.
Производство работ кранами-манипуляторами на расстоянии менее 30 м от подъемной выдвижной части крана-манипулятора в любом ее положении а также от груза до вертикальной плоскости образуемой проекцией на землю ближайшего провода воздушной линии электропередачи напряжением 50 В и более должно выполняться по наряду-допуску определяющему безопасные условия работы.
Безопасные расстояния от частей крана или груза в любом их положении до ближайшего провода линии электропередачи составляют: при напряжении до 1 кВ — 15 м от 1 до 20 кВ — не менее 2 м от 35 до 110 кВ — не менее 4 м от 150 до 220 кВ — не менее 5 м до 330 кВ — не менее 6 м от 500 до 750 кВ — не менее 9 м.
В случае производственной необходимости если невозможно выдержать указанные расстояния работа краном-манипулятором в запретной зоне может производиться при отключенной линии электропередачи по наряду-допуску в котором указывается время проведения работ.
Оператор (машинист) не должен приступать к работе если лицо ответственное за безопасное производство работ кранами-манипуляторами не обеспечило выполнение предусмотренных нарядом-допуском условий работы не указало место установки крана-манипулятора и не сделало следующую запись в вахтенном журнале: «Установку крана-манипулятора на указанном мною месте проверил. Работы разрешаю (дата время подпись)».
Работа кранов-манипуляторов под неотключенными контактными проводами городского транспорта может производиться при соблюдении расстояния между стрелой крана-манипулятора и контактными проводами не менее 1 м при установке ограничителя (упора) не позволяющего уменьшить указанное расстояние при подъеме стрелы.
При возникновении неисправностей оператор (машинист) обязан опустить груз прекратить работу крана-манипулятора и сообщить об этом лицу ответственному за безопасное производство работ кранами-манипуляторами. Так же должен действовать оператор (машинист) в следующих случаях:
при приближении грозы сильном ветре скорость которого превышает допустимую для данного крана-манипулятора и указанную в его паспорте;
при недостаточной освещенности места работы крана-манипулятора сильном снегопаде или тумане а также в других случаях когда оператор (машинист) плохо различает сигналы стропальщика или перемещаемый груз;
при температуре воздуха ниже допустимой минусовой указанной в паспорте крана-манипулятора;
при закручивании канатов грузового полиспаста.
2.4 Требования охраны труда по окончании работы
По окончании работы крана-манипулятора оператор (машинист) обязан соблюдать следующие требования:
не оставлять груз или грейфер в подвешенном состоянии;
поставить кран-манипулятор в предназначенное для стоянки место затормозить его и закрыть кабину на замок;
установить стрелу и крюк в положение указанное в руководстве по эксплуатации крана-манипулятора;
остановить двигатель;
занести в вахтенный журнал сведения о выявленных дефектах и неисправностях узлов и элементов крана-манипулятора сообщить о них руководителю.
При работе крана-манипулятора в несколько смен оператор (крановщик) сдающий смену должен сообщить своему сменщику обо всех неполадках в работе крана-манипулятора и сдать смену сделав в вахтенном журнале соответствующую запись.
Снять и убрать спецодежду средства индивидуальной защиты в предназначенные для хранения места.
Вымыть руки с мылом и принять душ выполнить другие мероприятия личной гигиены.
Сообщить лицу ответственному за производство работ о всех недостатках замеченных во время работы и принятых мерах по их устранению
3 Мероприятия по повышению безопасности и повышению условий труда
В качестве основных мероприятий по повышению безопасности и условий труда представим расчет искусственного освещения кабины и прожекторного освещения строительной площадки.
Кроме того проводятся мероприятия по снижению уровня шума и вибрации.
Целью виброизоляции является защита организма человека приборов и сооружений от вредного влияния вибрации. Виброизоляцию можно создать путем специальных устройств вводимым между механизмом генерирующим вибрации и человеком с целью препятствия передачи колебаний. К таким устройствам относятся демпферы пружины резиновые прокладки.
Практический опыт показывает что при недостаточных характеристиках освещенности производственное освещение может быть вредным и опасным производственным фактором17. При неудовлетворительной освещенности ухудшаются условия для осуществления зрительных функций и жизнедеятельности организма: появляются утомление глазные болезни головные боли что может быть косвенной причиной несчастных случаев. Плохо освещенные опасные зоны слепящие прожекторы и лампы блики от них резкие тени ухудшают или вызывают полную потерю ориентации работающих.
При увеличении освещенности значительно возрастает производительности труда и уменьшается утомление.
4 Расчет искусственного освещения
Свет - один из видов электромагнитного излучения который вызывает зрительные ощущения. Электромагнитные колебания характеризуются двумя параметрами: длиной волны и энергией излучения. Длина волны измеряется в нанометрах (миллионных долях метра - нм).
Видимый свет занимает узкий участок спектра приблизительно от 380 до 760 нм. Участок спектра от 760 нм до 340 мкм называется инфракрасным светом а от 10 до 380 нм – ультрафиолетовым 17.
Различие в длине волны света воспринимается как различие по цветам. Зрительные ощущения различаются как в количественных соотношениях по яркости так и качественно по цветности.
Весь спектр содержащий в определенном соотношении лучи всех длин волн от 380 до 760 нм вызывает ощущение белого цвета. Примером белого цвета является естественный свет солнца или свет от обычных ламп накаливания. Такой свет называется сложным излучением.
Свет состоящий из колебаний только одной длины волны называется простым или монохроматическим излучением.
Для удобства сравнения различных тепловых излучателей используют число указывающее цветовую температуру излучения.
Понятие цветовой температуры распространяется только на такие излучения спектр которых близок к тепловому (например свет ламп накаливания) и выражается в градусах Кельвина.
Различные источники излучения излучают не одинаковый спектр. В зависимости от типа источника света различают непрерывный смешанный и линейчатый спектры излучения.
Непрерывный спектр излучают источники света излучение которых определяется температурой их нагрева например лампы накаливания.
Смешанный спектр имеет излучение газоразрядных источников света например люминесцентных ламп. Их излучение можно охарактеризовать величиной цветовой температуры только приближенно.
Линейчатый спектр имеют газоразрядные натриевые лампы ртутные лампы низкого давления неоновые рекламные огни и т.д. к которым понятие цветовой температуры применить невозможно.
Сравнивая ощущения вызываемые в глазу излучением различных длин волн одинаковой интенсивности обнаруживается что глаз не одинаково чувствителен к лучам различных длин волн.
Наибольшей чувствительностью глаз обладает к желто-зеленым лучам с длиной волны 560 нм.
Проводится расчет искусственного освещения поста ремонта. Искусственное освещение обычно создают электрическими источниками света которые включают по мере необходимости регулируют интенсивность светового потока и его направленность. Такое освещение требует затрат электроэнергии и отличается по спектру от естественного освещения.
Осветительной установкой называется электроустановка состоящая из источника света вместе с арматурой и пуско-регулирующей аппаратурой.
Источник света устанавливается в арматуре имеющей детали его крепления и защиты от внешней среды защиты глаз человека от прямых лучей света. Совокупность этих деталей составляет светильник. Он имеет также петли крепления его в нужном месте.
Расчет искусственного освещения поста производится по методу светового потока. Этот метод позволяет обеспечить среднюю освещенность: поверхности с учетом всех падающих на нее прямых и отраженных потоков света. В соответствии с этими особенностями метод применяют для расчета общего равномерного освещения горизонтальных поверхностей.
Необходимый световой поток лампы определим по формуле:
где - минимальная нормативная освещенность лк;
- площадь освещаемой поверхности м2 в данном случае площадь поста;
- коэффициент запаса учитывающий запыленность светильников и износ источников света;
— коэффициент учитывающий неравномерность освещения;
- количество светильников шт.;
- количество ламп в светильнике шт.;
- коэффициент использования светового потока;
- коэффициент учитывающий затенение рабочего места работающим.
Исходя из полученного результата выбирается лампа ЛБ-40.
Технические характеристики лампы ЛБ-40 20:
Определяется фактическая освещенность. Для этого из формулы (98) выражают значение нормативной освещенности а за место светового потока подставляется световой поток лампы.
Определяется процентное превышение фактической освещенности над нормативной по зависимости:
Таким образом подставляя известные значения получиться:
Теперь провидится расчет прожекторного освещения.
Применение прожекторного освещения строительных площадок имеет ряд существенных преимуществ по сравнению с освещением светильниками: экономичность благоприятное для объемного видения соотношение вертикальной и горизонтальной освещенности меньшая загруженность территории столбами и воздушной проводкой а также удобство обслуживания осветительной установки. В то же время прожекторное освещение требует принятия мер по снижению слепящего действия и исключению теней. Целесообразно комбинировать прожекторное освещение со светильниками для участков с малой шириной.
Метод расчета по мощности прожекторной установки рекомендован ГОСТ 12.1.046-85 «Освещение. Общие требования».
Расчет числа прожекторов производят исходя из нормируемой освещенности и мощности лампы. Ориентировочное число прожекторов определим по формуле:
где коэффициент учитывающий световую отдачу источника света КПД прожекторов и коэффициент использования светового потока;
- нормируемая освещенность горизонтальной поверхности лк;
- коэффициент запаса;
- освещаемая площадь м2;
- мощность лампы Вт для прожекторов типа ОЗС-35 или ПСМ-40 20.
Округляя в большую сторону получается шт.
Сделаем вывод что для освещения строительной площадки достаточно двух прожекторов типа ПЗС-35 или ПСМ-40.
Минимальная высота установки прожектора определяется по зависимости:
где - максимальная сила света кд.
Минимальная высота установки прожекторов м.
Определяется оптимальный угол наклона прожектора к горизонтальной плоскости по формуле:
где и - угол рассеивания прожектора соответственно в вертикальной и горизонтальной плоскостях.
Подставляя углы в зависимость получиться:
Для расчета вертикальной освещенности наивыгоднейший угол наклона прожекторов определиться по формуле:
1стр. - Содержание.docx
1 Общие сведения об автомобилях с крано-манипуляторными установками 6
2 Классификация автомобилей с крано-манипуляторными установками 11
3 Конструкция крана-манипулятора: автомобильное шасси и крано-манипуляторная установка 22
4 Основные требования оснащения грузового автомобиля крано-манипуляторной установкой 35
Проект и расчет крано-манипуляторной установки на грузовой автомобиль 38
1 Выбор компоновочной схемы и ее расчет 38
1.1 Расчет центра тяжести манипулятора 38
1.1.1 Расчет центра тяжести стрелы 39
1.1.2 Расчет центра тяжести рукояти 41
1.1.3 Расчет координат центра тяжести клещевого захвата 42
1.1.4 Изменение координат центра тяжести манипулятора 43
1.2 Расчет центров тяжести манипулятора 44
1.3 Компоновка манипулятора 46
1.4 Расчет центров тяжести манипулятора 50
2 Расчет устойчивости автомобиля с КМУ 50
2.1 Расчет продольной статической устойчивости автомобиля на уклоне 50
Таблица 28 (2 раздел) 91 стр..dwg
Введение и Теор.ч. - 1 (34стр.).docx
Так классическая схема «грузовик + автокран» оправдывает себя в случаях когда для выполнения погрузочно-разгрузочных и транспортных операций требуется несколько единиц техники что обусловлено большими объемами и сроками осуществления процесса. С подобной ситуацией можно столкнуться например при отгрузке лесоматериалов на лесосеках при производстве строительных и монтажных работ.
В случае большой рассредоточенности или малого объема грузов применение схемы «грузовик + автокран» становится нерентабельным поскольку возрастают удельные затраты на единицу груза. Возникает необходимость применения мобильной крановой установки способной помимо погрузочно-разгрузочных осуществлять и транспортные операции. В таком случае исчезает необходимость применения дополнительной единицы техники в результате чего заметно снижаются затраты на эксплуатационные материалы а также на оплату труда персонала.
Поэтому возникает необходимость применения мобильной крановой установки способной помимо погрузочно-разгрузочных осуществлять и транспортные операции. В таком случае исчезает необходимость применения дополнительной единицы техники в результате чего заметно снижаются затраты на эксплуатационные материалы а также на оплату труда персонала.
Современное машиностроение предлагает огромный ассортимент подобных мобильных автомашин объединенных в категорию кранов-манипуляторов (КМУ).
В данном проекте принято решение о установки КМУ грузоподъемностью 3 тонны на автомобиль КамАЗ-6510. Подобная работа позволит отказаться от услуг крана и значительно снизит издержки на ремонт техники.
Всемерное повышение уровня механизации работ ведёт к повышению производительности комплектов машин и снижению сроков выполнения работ а качественный ремонт и обслуживание техники являются залогом получения предприятием высокой прибыли.
Обзор и анализ состояния проблемы реализации установки КМУ на грузовые автомобили
1 Общие сведения об автомобилях с крано-манипуляторными установками
Организация погрузочно-разгрузочных работ (ПРР) требует комплексного подхода к решению проблемы минимизации затрат. Необходимо учитывать как технико-экономические показатели оборудования так и показатели погрузочно-разгрузочных и транспортных процессов.
Для решения проблемы в современных условиях существует множество вариантов каждый из которых характеризуется определенным набором факторов определяющих целесообразность и эффективность применения схемы. К таким факторам можно отнести характеристики рабочего процесса (объемы грузов рассредоточенность работ время выполнения количество единиц техники) дорожные и погодные условия.
Так классическая схема «грузовик + автокран» оправдывает себя в случаях когда для выполнения ПРР и транспортных операций (ТрО) требуется несколько единиц техники что обусловлено большими объемами и сроками осуществления процесса. В таком случае самоходный кран однократно транспортируется на рабочее место где в дальнейшем осуществляется погрузка в несколько грузовых автомобилей формирующих практически непрерывный транспортный поток. С подобной ситуацией можно столкнуться например при отгрузке лесоматериалов на лесосеках.
И вот в конце 40-х гг. прошлого столетия появилась альтернативная схема выполнения ПРР и ТрО – механические краны-манипуляторы (рисунок 1). Технология предполагает применение крано-манипуляторных установок на шасси грузовых автомобилей. В отличие от классической схемы организации ПРР и ТрО здесь задействован один автомобиль который при помощи крано-манипуляторной установки способен производить погрузку-разгрузку различной номенклатуры грузов себе в кузов и осуществлять дальнейшее транспортирование. Данная схема может быть реализована как в стесненных городских условиях так и на ненаселенных малоосвоенных территориях. Это возможно благодаря широкому спектру кранов-манипуляторов которые могут быть выполнены на гусеничном автомобильном железнодорожном шасси. Таким образом машины с КМУ способны работать практически в любых дорожных и климатических условиях. Единственным ограничением по их применению остаются объемы работ.
Рисунок 1 – Общий вид крана-манипулятора на шасси автомобиля КамАЗ
Наличие неоспоримых преимуществ применения кранов-манипуляторов на малых объемах грузов обусловило совершенствование оборудования крано-манипуляторных установок. В 60-х гг. 20 века в манипуляторных установках был применен гидропривод что послужило толчком для ускоренного завоевания популярности в странах Европы и выделения кранов-манипуляторов в отдельный класс грузоподъемного оборудования.
По данным статистиков в 2014 году в Европе каждый пятый грузовой автомобиль оснащен КМУ. Капиталистические основы хозяйствования позволили предпринимателям подсчитать выгоду которую можно извлечь из грузовика имеющего КМУ. Он выполняет работу сразу двух машин – собственно транспортного средства и подъемного крана (или экскаватора – в случае если КМУ оборудована грейферным ковшом). Таким образом не нужно тратить деньги на приобретение (или аренду) стороннего погрузочного устройства на топливо для его работы на заработную плату его оператора и т.д.
Кроме экономического аспекта необходимо рассматривать и вопросы организации рабочего пространства и всего погрузо-разгрузочного процесса. Неоспоримым преимуществом автомобиля с КМУ является его маневренность и малые габариты т.е. кран-манипулятор занимает вдвое меньше места чем грузовик и кран. Для плотной городской застройки это особенно актуально.
Мобильность многофункциональность компактность маневренность и универсальность автомобиля оборудованного крано-манипуляторной установкой с каждым годом привлекает все большее количество потребителей.
Благодаря сочетанию функций - крана и грузовой платформы на одном шасси - достигается высокая эффективность использования техники сокращаются расходы на топливо сводится до минимума дорогостоящий и трудоемкий ручной труд при выполнении погрузочно-разгрузочных работ сокращаются количество занятой или просто простаивающей на объекте техники порой весьма дорогостоящей а также число задействованных людей (таблица 1).
В связи с тем что вес КМУ обычно не превышает 20-25% от полезной грузоподъемности шасси автомобиль используется по своему главному предназначению — для перевозки грузов.
Таблица 1 – Эффективность применения автокрана и крана-манипулятора
Количество занятого персонала
Количество задействованной техники
(грузовой автомобиль с КМУ)
(грузовой автомобиль автокран)
Продолжение таблицы 1
Занимаемая площадь при проведении работ (для расчета берется автомобиль МАЗ) м. кв.
Управление процессом
С пультов операторов расположенных по бокам автомобиля (расстояние до груза 2-3 метра)
Из кабины автокрана (расстояние 10-15)
Из таблицы видно что при применении кранов-манипуляторов существенно снижаются эксплуатационные затраты и увеличивается эффективность производства работа.
Увеличение эффективности обеспечивается наличием неоспоримых преимуществ кранов-манипуляторов к которым можно отнести:
Широкий диапазон закладываемых технических характеристик. Существующий модельный ряд КМУ позволяет подобрать оборудование точно соответствующее производственным задачам. К услугам потребителей предлагаются краны различной грузоподъемности с грузовым моментом от 28 до 180 кНм вылетом стрелы от 575 до 177 м возможна комплектация.
Многофункциональность. Благодаря возможности использования различных грузозахватных приспособлений одна и та же единица КМУ способна производить погрузку-разгрузку практически любых грузов – паллет катушек поддонов кирпича панелей бордюрного камня фундаментных блоков и многого другого. Кроме этого в качестве навесного оборудования для КМУ можно использовать люльки грейферные захваты и буры.
Универсальность. КМУ может монтироваться на любой грузовой автомобиль имеющийся на балансе организации – будь то МАЗ КамАЗ «Volvo» «Scania» или «Газель». Устанавливается как за кабиной так и на задней части грузовой платформы что позволяет заполнять не только кузов автомобиля но и при необходимости прицеп.
Безопасность работы. Каждая установка оснащена автоматической системой защиты от перегрузок и запорно-тормозными клапанами исключающими возможность самопроизвольного опускания груза. Выдвижные опоры аутригеров обеспечивают устойчивость установки во время работы. Все это делает оборудование безопасным при эксплуатации.
Таким образом КМУ являются оптимальным и экономически обоснованным решением в области грузоперевозок погрузочно-разгрузочных работ проведения монтажно-демонтажных и восстановительных работ в условиях плотной городской застройки а также для выполнения самых разнообразных подъемных и монтажных операций.
2 Классификация автомобилей с крано-манипуляторными установками
Указанные выше преимущества потребитель может получить при рациональной организации работ и правильном подборе типоразмера крана-манипулятора для осуществления погрузочно-разгрузочных и транспортных операций. В связи с этим важно установить основные параметры автомобилей с КМУ и соответствующую им классификацию.
Основными параметрами кранов-манипуляторов определяющими возможность применения являются:
максимальный и минимальный вылет стрелы;
грузовой момент и грузоподъемность стрелы;
высота подъема и опускания груза;
радиус поворота крановой установки;
исполнение стрелового оборудования (исполнение подвески форма поперечного сечения тип системы телескопического выдвижения);
В соответствии с указанными характеристиками производится и классификация кранов-манипуляторов.
По грузоподъемности КМУ можно условно разделить на четыре класса:
Микроманипуляторы (до 15 т);
Сверхтяжелые (более 25 т).
Однако масса поднимаемого груза является несколько субъективной характеристикой для классификации поскольку не отражает зависимости от вылета стрелы. В связи с этим более верным будет разделение по грузовому моменту:
Легкие – до 5 т*м (рисунок 2);
Рисунок 2 – Схема легкого крана-манипулятора на шасси автомобиля ГАЗ (грузовой момент 2 52 т*м)
Средние – до 30 т*м (рисунок 3);
Рисунок 3 – Внешний вид среднего крана-манипулятора на шасси автомобиля МАЗ
Тяжелые – свыше 30 т*м (рисунок 4).
Рисунок 4 – Внешний вид тяжелого крана-манипулятора
По типу подвески стреловое оборудование может быть:
Жесткая подвеска: шарнирное закрепление грузозахватного органа на оголовке стрелы (рисунок 5);
Рисунок 5 – Схема КМУ с жесткой подвеской крюка
Гибкая подвеска: размещение грузового крюка на конце канатной лебедки (рисунок 6).
Рисунок 6 – Схема КМУ с гибкой подвеской крюка
По типу складывания рабочее оборудование кранов-манипуляторов может быть разделено на две категории:
Шарнирно-сочлененная («коленная» или Z-образная): складывается в несколько колен в транспортном положении расположена поперек рамы машины (рисунок 7);
Рисунок 7 – Схема крана-манипулятора с шарнирно-сочлененной стрелой на шасси автомобиля КамАЗ
L-образная: прямая телескопическая стрела с тросовой подвеской крюка в транспортном положении расположена над кузовом или кабиной (рисунок 8).
Рисунок 8 - Схема крана-манипулятора с прямой телескопической стрелой на шасси автомобиля МАЗ
Сравнительная характеристика стрелы КМУ по типу складывания сведена в таблицу 2.
Таблица 2 – Сравнительная характеристика стрел по типу складывания
Частичное перераспределение массы установки на заднюю ось; плавные подъем и опускание груза строго по вертикали; работа в стесненных условиях; работы ниже уровня стоянки; работа из-за препятствий
Ограничение по габаритам груза в кузове при расположении стрелы над кузовом
Продолжение таблицы 2
Компактность в транспортном положении; подъемопускание грузов в труднодоступных местах
Сложность ПРР вблизи от колонны крана; большая масса и габаритные размеры оборудования; большая нагруженность передней оси; меньшая точность работ
По месту расположения КМУ:
Непосредственно за кабиной (преимущественное расположение): возможность работы по бокам от кабины оптимальное распределение нагрузки;
На заднем свесе автомобиля (спец. заказы): возможность работы с прицепом без расцепления автопоезда большие нагрузки на ось опасность консольного расположения.
По способу управления установкой:
управление рычагами с земли
управление со стойки оператора на уровне платформы
управление джойстиками с кресла оператора наверху колонны крана
дистанционное управление выносным пультом
По стационарности КМУ разделяются на передвижные и стационарные.
По виду используемого ходового устройства передвижные КМУ разделяются на:
Специальное шасси автомобильного типа
На шасси гусеничного или колесного трактора
Рельсовые (на опорной платформе перемещаемой по рельсам)
Железнодорожные (на платформах)
На плавучих платформах
Наиболее мобильными и эффективными являются краны-манипуляторы на колесном ходу. КМУ могут быть смонтированы на следующих типах автомобилей:
Бортовой автомобиль с КМУ (рисунок 9)
Рисунок 9 – Внешний вид бортового автомобиля с крано-манипуляторной установкой
Самосвалы с КМУ (рисунок 10)
Рисунок 10 – Внешний вид самосвала с крано-манипуляторной установкой
Седельные тягачи с КМУ (рисунок 11)
Рисунок 11 – Внешний вид седельного тягача с крано-манипуляторной установкой
Полуприцеп с КМУ (рисунок 12)
Рисунок 12 – Внешний вид полуприцепа с крано-манипуляторной установкой
Наиболее популярным и распространенным является автомобильное шасси что обусловлено назначением кранов-манипуляторов – ПРР и транспортировка а именно автомобильный транспорт занимает первое место по объемам грузоперевозок. Индивидуальные и частные предприниматели также как и многие крупные промышленные предприятия используют грузовые автомобили как наиболее экономически оправданный вид транспорта.
Классификация кранов-манипуляторов и анализ рынка КМУ в России позволяют сделать следующие выводы:
Наибольший экономический эффект несет применение бортового автомобиля с КМУ поскольку данный тип позволяет не только осуществлять погрузочно-разгрузочные но и транспортные операции с большой номенклатурой грузов;
Наиболее рациональным расположением КМУ на шасси автомобиля – за кабиной что обусловлено оптимальным распределением нагрузок на раму автомобиля а также позволяет создавать большой радиус рабочей зоны вокруг него;
Стреловое оборудование должно иметь L-образное исполнение для более плавного и точного выполнения погрузочно-разгрузочных операций;
Применение гибкой подвески наиболее рационально при L-образном исполнении и позволяет производить манипуляции с грузом за счет работы лебедки а не телескопирования что упрощает работу а также позволяет выполнять операции ниже уровня стоянки и из-за препятствий.
На основании приведенной классификации геометрических и технических характеристик грузовых шасси и КМУ можно сделать вывод о возможных сферах применения различных видов кранов-манипуляторов. Так в малоэтажном строительстве могут быть полезны тросовые краны-манипуляторы с грузоподъемностью 1500 кг при вылете стрелы до 15 м при этом бортовая платформа должна иметь длину до 6 м что обеспечивает маневренность и возможность транспортировки длинномерных и тяжеловесных грузов.
Для осуществления в основном транспортных операций без необходимости подъема груза на большую высоту возможно применение тросового или гидравлического КМУ с грузоподъемностью до 15 т при максимальном вылете до 10 м а длина борта шасси превышает 6 м.
Применение экономичных маломощных установок может быть оправдано в сфере коммунального хозяйства. К этой категории могут быть отнесены тросовые краны-манипуляторы с длиной борта до 4 м и грузоподъемностью не выше 900 кг при вылете 5 метров. Может оказаться рациональным их применение и для транспортировки небольших грузов с дальнейшей выгрузкой около борта.
В условиях же транспортировки крупногабаритных грузов может быть оправдано применение тросовых КМУ с грузоподъемность 1500 кг при вылете 10 метров бортовая платформа которых имеет в длину 13-15 м.
Общепромышленные КМУ среднего класса по грузоподъемности ввиду своей универсальности имеют чрезвычайно широкую область применения – промышленность строительство лесозаготовки и т.д. Преимуществом таких манипуляторов является возможность установки дополнительного навесного оборудования возможность для транспортировки длинномерных и крупногабаритных грузов.
3 Конструкция крана-манипулятора: автомобильное шасси и крано-манипуляторная установка
Кран-манипулятор – это машина предназначенная для подъема и опускания груза состоящая из крано-манипуляторной установки (КМУ) смонтированной на ходовом устройстве или стационарно.
Крано-манипуляторной установкой называется подъемное устройство которое включает стреловое рабочее оборудование грузозахватные органы (крюковая подвеска грейфер и т.д.) систему управления и опорную раму.
Основание КМУ представляет собой трехопорную сварную конструкцию из высокопрочной конструкционной стали к которой крепятся все остальные детали КМУ. В поперечную балку основания с двух сторон вмонтированы балки аутригеров. К центральной части основания крепятся гидроцилиндры механизма поворота (либо гидромотор поворота колонны) и смонтирована колонна КМУ. Основание КМУ крепится на монтажной установочной раме автомобиля (подрамникенадрамнике) с помощью шпилек из высокопрочной легированной стали.
Механизм поворота КМУ состоит из двух гидроцилиндров одностороннего действия (или гидромотора) прикрепленных непосредственно к основанию КМУ зубчатой рейки с закрепленными на ней поршнями и шестерни изготовленной как одно целое с колонной КМУ.
Колонна КМУ представляет собой сварную конструкцию коробчатого сечения из высокопрочной стали. Нижняя часть колонны кованая круглого сечения выполнена как одно целое с шестерней механизма поворота. В нижней части коробчатой конструкции имеются проушины для крепления цилиндра подъема первой стрелы а в верхней части - проушины для крепления второй стрелы. Колонна конструктивно нижней частью вставляется в основание КМУ и вращается в нем на подшипниках скольжения.
Балки аутригеров сварные прямоугольного сечения двигаются в основании КМУ на поддерживающих роликах и фиксируются в конечных положениях фиксирующим устройством. Для предотвращения самопроизвольного выдвижения балок фиксаторы имеют дополнительную блокировку исключающую их открытие. К наружным сторонам балок приварены монтажные фланцы к которым с помощью болтов прикреплены цилиндры опор.
Первая стрела КМУ коробчатого сечения сварена из высокопрочной конструкционной стали. Крепится корневой частью шарнирно к колонне КМУ посредством пальца и приводится в движение цилиндром подъема первой стрелы. Все шарнирные соединения снабжены подшипниками скольжения и имеют точки смазки. В нижней части боковых щек имеются проушины для крепления цилиндров подъема первой и второй стрел. К концевой части первой стрелы манипулятора шарнирно присоединена корневая часть второй стрелы.
Вторая стрела представляет собой трубу шестигранного профиля сваренную из высокопрочной конструкционной стали. К концевой части второй стрелы приварен кронштейн для крепления цилиндра выдвижения удлинителей стрелы и проушина для крепления грузозахватных приспособлений. В передней части второй стрелы имеются отверстия для крепления подшипников скольжения (скользунов) по которым двигаются секции удлинителей.
Удлинительные телескопические секции стрелы представляют собой трубы шестигранного сечения каждая из которых имеет меньшее сечение чем предыдущая. К концевым частям каждой секции приварены проушины для крепления цилиндров выдвижения секции и подвески грузозахватных приспособлений. В корневой части каждой секции установлены скользуны для уменьшения сил трения.
Гидробак представляет собой герметичную емкость сложной формы с рабочей жидкостью снабженную фильтром низкого давления сапуном смотровым окном выполненным как одно целое с указателем температуры рабочей жидкости и всасывающим трубопроводом с шаровым краном. Для слива рабочей жидкости гидробак имеет сливную пробку. Как правило бак установлен непосредственно на основании КМУ и расположен выше всасывающего патрубка гидронасоса.
Общее устройство крано-манипуляторной установки представлено на рисунке 13.
Рисунок 13 – Схема устройства крано-манипуляторной установки:
– пульт управления; 2 – крепежные шпильки; 3 – поворотный цилиндр опоры; 4 – неповоротный цилиндр опоры; 5 – балка опор; 5а - телескопическая балка опор; 6 – фиксатор балки опор ручного выдвижения; 7 – бак гидравлический с указателями температуры и уровня масла; 8 – механизм поворота; 9 – основание крана; 10 – колонна крана; 11 – главный цилиндр подъема; 12 – верхнее сидение с пультом управления; 13 – траверса; 14 – лебедка; 15 – главная стрела; 16 – цилиндр дополнительной стрелы; 17 – цилиндр выдвижения гидравлических выдвижных секций стрелы; 18 – дополнительная стрела; 19 – гидравлическая выдвижная секция стрелы; 20 – механическая секция удлинителя стрелы; 21 – грузовой крюк; 22 – ПДУ; 23 – балансир.
Одним из самых важных элементов КМУ является гидравлическая система при помощи которой и осуществляются рабочие процессы установки (рисунок 14).
Рисунок 14 – Принципиальная гидравлическая схема КМУ
Гидравлическая система КМУ обеспечивает выдвижение и поворот опор установку автомобиля на опоры подъем опускание стрел и поворот КМУ и включает в себя:
- гидробак со встроенным фильтром низкого давления;
- магистральный фильтр высокого давления;
- гидрораспределители для управления КМУ и опорами;
- гидроцилиндры с гидрозамками и клапанами удержания груза;
- трубопроводы и рукава высокого давления (РВД).
Перечень гидрооборудования по принципиальной гидравлической схеме приведен в таблице 3.
Таблица 3 – Гидрооборудование принципиальной гидравлической схемы КМУ
Дополнительные опоры
Дроссель с обратным клапаном 9Р4008
Рукав высокого давления
Гидравлический привод КМУ выполнен по одноконтурной открытой схеме. Для выполнения всех рабочих операций при установке крана-манипулятора на выносные опоры а также для приведения его в транспортное и рабочее положение используются гидроцилиндры.
Рабочая жидкость из гидробака Б1 насосом Н1 через фильтр высокого давления Ф2 подается к гидрораспределителю РС1 затем к гидрораспределителю выносных опор РС2 и далее через фильтр низкого давления Ф1 сливается обратно в гидробак Б1.
Гидрораспределители РС1 и РС2 работают последовательно от насоса Н1. Гидрораспределитель РС1 предназначен для управления гидроцилиндрами поворота колонны МП подъема и опускания первой Ц1 и второй Ц2 стрелы и телескопирования выдвижной секции второй стрелы ЦЗ.
Гидрораспределитель РС2 предназначен для управления гидроцилиндрами выдвижения и установки выносных опор Ц4 Ц5 Ц6 Ц7 (Ц8 Ц9 при их наличии).
Рабочие органы гидравлической системы сообщаются между собой посредством рукавов высокого давления и жестких трубопроводов.
При нажатом клапане К1 возможно опускание второй стрелы для снятия режима перегрузки остальные движения заблокированы:
- главными клапанами ограничения рабочего давления встроенными в каждый гидрораспределитель и определяющими рабочее давление;
- клапанами ограничения давления работающими при следующих режимах: опускание первой стрелы; поворот колонны; выдвижение секции телескопирования;
- гидроклапанами тормозными на гидроцилиндрах подъема и опускания первой ЗМ1 и второй стрелы ЗМ2 и телескопирования выдвижной секции второй стрелы ЗМЗ служащими для удержания груза в поднятом состоянии и ограничения давления в гидроцилиндрах первой и второй стрелы и механизмов телескопирования;
- гидрозамками на гидроцилиндрах подъема и опускания выносных опор ЗМ4 и ЗМ5;
- дросселями ограничивающими скорость поворота колонны в крайних угловых положениях.
Для заправки в гидробак рабочей жидкости имеется заливная горловина с фильтром ФЗ.
Все гидроцилиндры двухстороннего действия. При подаче жидкости в поршневую полость шток гидроцилиндра выдвигается а жидкость из штоковой полости вытесняется в бак и наоборот.
Общий вид гидрооборудования КМУ приведен на рисунке 15.
Рисунок 15 – Общий вид гидрооборудования КМУ:
– цилиндр телескопирования; 2 – цилиндр второй стрелы; 3 – цилиндр первой стрелы; 4 – система гидроуправления стреловым оборудованием; 5 – гидробак; 6 – управление гидроцилиндрами выносных опор; 7 – механизм поворота; 8 – цилиндр выдвижения выносной опоры; 9 – гидронасос; 10 - цилиндр выносной опоры.
Для обеспечения нормальной работы гидросистемы в качестве рабочей жидкости следует применять минеральные масла в соответствии с таблицей 4.
Таблица 4 – Рабочие жидкости гидросистемы КМУ
Летнее масло - МГЕ-46В ТУ 38 001347-83
Всесезонное - ВМГЗ ТУ 38.101479-86
Опорно-поворотное устройство
Летнее - ТАп-15 В ГОСТ 23652
Зимнее - ТСп-10 ГОСТ 23652
Технические показатели гидравлического оборудования крано-манипуляторных установок имеют различные значения в зависимости от типоразмера и лежат в пределах: производительность насоса 10-50 лмин; рабочее давление гидросистемы 20-30 МПа.
Крано-манипуляторные установки могут быть оснащены дополнительным рабочим оборудованием. Сменные рабочие органы являются специализированными грузозахватными приспособлениями предназначенными для работы с различными типами грузов что позволяет значительно расширить области применения гидроманипуляторов и обеспечить их высокую производительность и универсальность при использовании их в различных отраслях народного хозяйства.
Краны –манипуляторы могут быть оснащены следующими типами навесного оборудования:
Грейферы предназначены для работы с лесными материалами и используются для трелевки погрузки и разгрузки подтаскивания и штабелирования а также для работы с металлоконструкциями погрузки сыпучих и малосыпучих грузов силоса и сенажа (рисунок 16)
Рисунок 16 – Грейферное оборудование:
а – трелевочный; б – клещевой; в – ковшовый; г – вильчатый.
Захваты для рулонов используются для перемещения рулонов сенажа и иных материалов в рулонной упаковке (рисунок 17)
Рисунок 17 – Захват для рулонов сенажа ЗР-3
Вилочные подхваты поддонов предназначены для перемещения паллетированных грузов массой до 15 т (рисунок 18)
Рисунок 18 – Вилочный подхват поддонов ВП-1.00
Устройство грузозахватное для перемещения бордюрного камня и других предметов прямоугольного сечения (рисунок 19)
Рисунок 19 – Грузозахват для бордюрного камня УГ-1.00
Устройство грузозахватное для перемещения грузов имеющих отверстие (рисунок 20)
Рисунок 20 – Грузозахват для грузов имеющих отверстие УГ-2.00
4 Основные требования оснащения грузового автомобиля крано-манипуляторной установкой
Оснастить крано-манипуляторной установкой можно любую грузовую машину имеющуюся в организации будь то МАЗ КAМАЗ «Volvo» «Scania» или «Газель». Установка монтируется на переднюю или заднюю часть шасси.
Возникает вопрос о величине дополнительных капиталовложений в подобный проект о сроке его окупаемости и экономической целесообразности. Экономисты фирм-поставщиков оборудования просчитали что установка на грузовой навесного кранового оборудования влечет за собой экономию на автокране грузчиках сокращаются и временные затраты поскольку подготовка КМУ к работе - дело нескольких минут. В зависимости от интенсивности эксплуатации установка окупается от 4 месяцев до одного года.
Большой объем работ и многообразный ассортимент грузов формируют разнообразие автомобильных шасси на которые устанавливаются КМУ. На большинство известных грузовых марок осуществляется монтаж КМУ: Volvo MAN Scania Mercedes Isuzu и многие другие. К этому списку можно смело добавить полный перечень отечественных производителей грузовых автомобилей: ГАЗ ЗИЛ МАЗ КамАЗ КрАЗ Урал и прочие.
Многие российские предприниматели отдают предпочтение отечественным шасси в силу меньших экономических затрат на его приобретение. Такой огромный спрос на КМУ с отечественным шасси создал предпосылки для появления большого числа компаний в том числе дилеров известных европейских производителей кранов-манипуляторов занимающихся установкой КМУ зарубежного производства на отечественные шасси. На данный момент можно констатировать что российский рынок КМУ в большинстве своем представлен именно такими «гибридами». КМУ на отечественном шасси находят широкое применение в лесозаготовительной отрасли в сельском хозяйстве используются для перевозки (эвакуации) автотранспортных средств.
Необходимо добавить что КМУ на шасси зарубежного производства также широко представлены в нашей стране. Ряд отечественных предприятий занимается сборкой таких машин используя краны-манипуляторы различных европейских производителей и шасси японских китайских и корейских грузовиков.
Особенностью монтажа КМУ на шасси грузовых автомобилей является отсутствие необходимости заказа специального шасси все модели монтируются на серийные автомобили. Это безусловно снижает стоимость конечного автомобильного крана-манипулятора а также позволяет произвести монтаж на любой имеющийся в парке грузовой автомобиль. Применение серийного шасси позволяет упростить техническое обслуживание крана-манипулятора ведь все расходные материалы и запасные части в таком случае широко представлены на рынке.
Среди отечественных шасси можно выделить следующие наиболее распространенные марки: КамАЗ Урал ЗИЛ. Потребитель отдает предпочтение этим маркам в силу их технических и экономических характеристик. Представленная техника а в особенности автомобили КамАЗ наиболее приспособлены к дорожным и климатически условиям страны неприхотливы и достаточно просты в техническом обслуживании. Наибольшим спросом среди всего модельного ряда автомобилей КамАЗ пользуются: КамАЗ 65117 и КамАЗ 43118. Выбор покупателей обусловлен характеристиками привода грузоподъемностью бортов колесной формулой автомобилей. Эти представители отечественного производства нашли свое применение и на Дальнем Востоке где традиционно сильны позиции японских и китайских машиностроителей.
Анализ рынка кранов-манипуляторов на автомобильном шасси позволил выявить недостатки методики выбора потребителями грузовых автомобилей с достаточным остаточным ресурсом в качестве шасси крано-манипуляторных установок (КМУ). Это приводит к существенному увеличению удельной себестоимости монтажа и эксплуатации.
На основе рассмотрения данной проблемы предложены меры позволяющие по мнению авторов оптимизировать расходы потребителей. Важнейшей из которых является необходимость удовлетворения комплексу требований которому должны отвечать базовые грузовые автомобили предоставляемые для монтажа КМУ:
Грузоподъемность автомобиля должна превышать вес установки не менее чем в 3-5 раз;
Привод базовой машины должен обеспечивать возможность установки коробки отбора мощности и гидронасоса;
Запас прочности конструкции и узлов автомобиля а также ресурс его работы должны соответствовать аналогичным параметрам КМУ;
Узлы и агрегаты грузового автомобиля должны соответствовать принципам унификации быть ремонтопригодными;
После монтажа манипуляторной установки должна быть обеспечена развеска соответствующая конструкторской документации автомобиля;
Геометрические характеристики кузова должны соответствовать номенклатуре грузов;
Габариты автомобиля и исполнение ходового оборудования должны обеспечивать маневренность крана-манипулятора;
Базовый автомобиль должен быть адаптирован к дорожным и климатическим условиям;
Шасси крана-манипулятора должно иметь оптимизированный расход топлива.
Экономическая часть г..docx
1 Расчет эксплуатационных затрат проектируемой машины с КМУ на год
Эксплуатационные затраты определяется по формуле:
где - амортизационные отчисления на полное восстановление руб.;
- затраты на выполнение ремонтов и полное обслуживание руб.;
- затраты на замену быстроизнашивающихся частей руб.;
- оплата труда рабочих управляющих машиной (машинистов водителей) руб.;
- затраты на смазочные материалы руб.;
- затраты на гидравлическую жидкость руб.;
- затраты на топливо руб;
ФОТ – фонд оплаты труда руб.
Готовые амортизационные отчисления на год:
где - стоимость машины с КМУ;
- норма амортизационных отчислений %;
- годовой режим эксплуатации машины 23.
Затраты на выполнение технических обслуживаний и ремонтов:
где - норма годовых затрат на ремонт и тех. обслуживание
Затраты на замену быстроизнашивающихся частей определяются по формуле:
где - цена быстроизнашивающейся части франко-продавец (для рукавов насосов);
- затраты на доставку быстроизнашивающихся частей к потребителю с учетом транспортных расходов;
- оплата труда ремонтных рабочих исключая машиниста занятых на замене быстроизнашивающихся частей;
ед. - количество быстроизнашивающихся частей данного вида одновременно заменяемых в машине;
- индивидуальные нормы соответственно накладных расходов и прибыли в долях от оплаты труда рабочих занятых на замене быстроизнашивающихся частей;
- нормативный ресурс (срок службы) быстроизнашивающейся части;
Затраты на замену шин для строительных машин определяется по формуле:
где - количество одновременно заменяемых шин на машине;
- стоимость шины автомобиля КамАЗ-6510;
– нормативный пробег шины.
Расходы на оплату труда З (руб.ч.) определяются по формуле:
где - часовая тарифная ставка рабочих управляющих машиной;
- начисления стимулирующего характера принимаются равными 50% от ;
- начисления стимулирующего и компенсирующего характера принимаем равными 16% от ;
- затраты на оплату труда сохраняемую работникам на время отпуска принимаются 15% от ;
- надбавки обусловленные районным регулированием оплаты труда принимаются равными 80% от .
Начисления на фонд оплаты труда (ФОТ):
где ПФ = 86 руб.час. – пенсионный фонд принимается 22% от зарплаты труда рабочего (З);
ФМС = 2 руб.час. – фонд медицинского страхования принимается 51% от зарплаты труда рабочего (З);
ФСС = 11 руб.час. – фонд социального страхования принимается 29% от зарплаты рабочего (З).
Затраты на дизельное топливо для строительных машин (руб.маш.-ч.) определяются по формуле:
где - норма расхода дизельного топлива на 100 км при работе машины в технологическом режиме;
- текущая рыночная цена приобретения дизельного топлива;
кгл – плотность дизельного топлива;
- затраты на доставку дизельного топлива до заправляемой машины.
Затраты на смазочные материалы (руб.маш.-ч.) для дизельных машин определяются по формуле:
где - затраты на жидкое топливо (в данном случае дизельное);
- коэффициент перехода от к затратам на смазочные материалы; .
Затраты на гидравлическую жидкость:
где - средневзвешенная емкость гидросистемы крано-манипуляторной установки л;
кгл – плотность гидрожидкости;
- коэффициент доливок гидравлической жидкости восполняющих систематические её утечки при работе машины;
год – периодичность полной смены масла;
руб.кг – стоимость гидрожидкости;
руб.кг – стоимость доставки гидрожидкости;
- годовой режим автомобиля с КМУ.
2 Расчет эксплуатационных затрат машин
Эксплуатационные затраты рассчитываемого комплекта машин:
- затраты на замену шин частей руб.;
- затраты дизельное топливо комплекта машин руб;
- фонд оплаты труда руб.
Готовые амортизационные отчисления на год определятся
где - амортизационные отчисления для автомобильного крана (на базе автомобиля КамАЗ);
- амортизационные отчисления для автомобиля не оборудованного гидроманипулятором.
Амортизационные отчисления определяются аналогично ранее выполненному расчёту. Стоимость автомобильного крана принимается согласно 24 тогда
Затраты на выполнение технических обслуживаний и ремонтов комплекта можно определить
где - затраты на выполнение ремонтов и полное обслуживание крана автомобильного (на базе автомобиля КамАЗ);
- затраты на выполнение ремонтов и полное обслуживание грузового автомобиля руб.
Затраты определяются аналогично выше изложенным
где - затраты на замену быстроизнашивающихся деталей крана автомобильного (на базе автомобиля КамАЗ);
- затраты на замену быстроизнашивающихся деталей грузового автомобиля руб.
Затраты определяются по формуле:
ед. - количество быстроизнашивающихся частей данного вида одновременно заменяемых в машине (для крана автомобильного);
ед. - количество быстроизнашивающихся частей данного вида одновременно заменяемых в машине (для автомобиля);
- нормативный ресурс (срок службы) быстроизнашивающейся части.
Затраты на замену шин для комплекта машин определяется по формуле:
где - затраты на замену шин на автомобиле;
- затраты на замену шин крана автомобильного.
Расходы на оплату труда З (руб.ч.) комплекта машин определяются по формуле:
где - расходы на оплату труда водителя автомобиля (определены ранее);
- расходы на оплату труда крановщика (принимаются равными оплате труда водителя).
Начисления на фонд оплаты труда (ФОТ) комплекта машин определяются:
где - начисления на фонд оплаты труда водителя автомобиля (определены ранее);
- начисления на фонд оплаты труда крановщика (принимается равными оплате труда водителя).
Затраты на дизельное топливо для комплекта машин (руб.маш.-ч.) определяются по формуле:
где - затраты на энергоноситель крана автомобильного;
- затраты на энергоноситель грузового автомобиля.
где - норма расхода дизельного топлива при работе машины в технологическом режиме;
Затраты определяются аналогично выше рассчитанным по формуле:
где - затраты на дизельное топливо для комплекта машин;
Затраты на гидравлическую жидкость для автомобиля не рассчитываются а для автомобильного крана определяются аналогично выше проведённым расчётам
где л - средневзвешенная емкость гидросистемы автомобильного крана;
- годовой режим работы автомобиля с КМУ.
Таблица 30 – Калькуляция себестоимости эксплуатационных затрат
Автомобиль с гидравлическим манипулятором
Комплект “Кран + Автомобиль”
Амортизационные отчисления
Затраты на ТО и ремонт
Затраты на быстроизнашивающиеся детали
Затраты на замену шин
Затраты на оплату труда работающих
Затраты на фонд оплаты труда
Затраты на дизельное топливо
Продолжение таблицы 30
Затраты на смазочные материалы
Затраты на гидравлическую жидкость
3 Расчет экономических показателей
Чистый дисконтированный доход:
Расчет ЧДД ведется в форме таблицы 31.
Таблица 31 – Расчёт чистого дисконтированного дохода
Объём работ вып. машин.
Продолжение таблицы 31
Срок окупаемости 26 года.
Индекс рентабельности проекта:
Поскольку индекс доходности больше единицы а ЧДД равен 1442400 руб. проект по внедрению автомобиля с КМУ можно считать экономически эффективным. Технико-экономические показатели проекта представлены в таблице 32.
Таблица 32 – Технико-экономические показатели
Наименование показателей
Первоначальная стоимость тыс. руб.
Продолжение таблицы 32
Фонд времени в году смен
Трудоёмкость выполнения работ чел.-ч.
Количество работающих чел.
Себестоимость машино-часа
Удельные капитальные вложения на ед. продукции тыс.руб.маш.-ч.
Себестоимость человека-часа работ руб.
Срок окупаемости капитальных вложений годы
Чистый дисконтированный доход тыс. руб.
Индекс доходности (рентабельность)
Снижение себестоимости в год крано-манипуляторной установки на автомобиле КамаАЗ – 6510 по сравнению с комплектом машин «Кран + Автомобиль» составляет 135700 рублей. Окупаемость предложенного проекта 26 года.
Содержание (продолжение).docx
2.3 Расчет поперечной устойчивости автомобиля с КМУ в транспортном положении на склоне 55
2.4 Расчет устойчивости автомобиля с максимальным вылетом манипулятора в сторону 56
2.5 Расчет устойчивости автомобиля при поперечном склоне с максимальным вылетом манипулятора 58
2.6 Расчет устойчивости при движении автомобиля с КМУ на повороте 60
2.7 Тяговый расчет автомобиля с КМУ 62
3 Проектирование и расчет манипулятора 63
3.1 Расчет проектных параметров манипулятора 63
3.1.1 Данные для расчета 63
3.1.2 Расчетная схема и расчет параметров 64
3.2 Расчет нагрузок манипулятора 68
3.2.1 Расчет реальных усилий гидроцилиндра рукояти и гидроцилиндра стрелы 68
3.2.2 Расчет усилий в механизме складывания рукояти 69
3.2.3 Расчет реакций в шарнире В и в шарнирах гидроцилиндра стрелы 72
3.4 Расчет шарнирных узлов 76
3.4.1 Расчет шатуна на прочность 76
3.4.2 Расчет на прочность пальцев шарниров 81
3.4.3 Расчет втулок шарнирных узлов 85
3.4.4 Расчет проушин шарнирных узлов 86
3.4.4.1 Расчет проушин на смятие 87
3.4.4.2 Расчет проушины на изгиб с растяжением 88
Меры безопасности при эксплуатации КМУ 92
1 Основные термины 92
2 Требования к персоналу 93
2.1 Общие требования охраны труда 93
2.2 Требования охраны труда перед началом работы 96
2.3 Требования охраны труда во время работы 99
2.4 Требования охраны труда по окончании работы 106
3 Мероприятия по повышению безопасности и повышению условий труда 107
4 Расчет искусственного освещения 108
Экономическая часть 114
1 Расчет эксплуатационных затрат проектируемой машины с КМУ на год 114
2 Расчет эксплуатационных затрат машин 119
3 Расчет экономических показателей 126
Технологическая часть 130
1 Выбор заготовки 130
2 Маршрут обработки 131
3 Расчетно-аналитический метод определения припусков на механическую обработку 131
4 Расчет режимов резания для токарной операции 135
5 Расчет режимов резания для фрезерно-центровой операции 140
6 Расчет вертикально-сверлильной операции 143
7 Расчет режимов резания для фрезерной операции 146
Список используемой литературы 151
Описание.docx
Кран-манипулятор на автомобиле грузоподъемностью 3 тонны
установка КМУ грузоподъемностью 3 тонны на автомобиль КамАЗ-6510.
проект состоит из 4 частей:
В случае большой рассредоточенности или малого объема грузов применение схемы «грузовик + автокран» становится нерентабельным поскольку возрастают удельные затраты на единицу груза. Возникает необходимость применения мобильной крановой установки способной помимо погрузочно-разгрузочных осуществлять и транспортные операции. В таком случае исчезает необходимость применения дополнительной единицы техники в результате чего заметно снижаются затраты на эксплуатационные материалы а также на оплату труда персонала.
Поэтому возникает необходимость применения мобильной крановой установки способной помимо погрузочно-разгрузочных осуществлять и транспортные операции. В таком случае исчезает необходимость применения дополнительной единицы техники в результате чего заметно снижаются затраты на эксплуатационные материалы а также на оплату труда персонала.
Современное машиностроение предлагает огромный ассортимент подобных мобильных автомашин объединенных в категорию кранов-манипуляторов (КМУ).
В данном проекте принято решение о установки КМУ грузоподъемностью 3 тонны на автомобиль КамАЗ-6510. Подобная работа позволит отказаться от услуг крана и значительно снизит издержки на ремонт техники.
Всемерное повышение уровня механизации работ ведёт к повышению производительности комплектов машин и снижению сроков выполнения работ а качественный ремонт и обслуживание техники являются залогом получения предприятием высокой прибыли.
ВКР дипломный проект
Кран-манипулятор на автомобиле грузоподъёмностью 10 тонн Чертёж общего вида
Гидроцилиндр подъема опускания сборка
Рабочая зона манипулятора
Рама прицепного устройства
Устройство опорно-поворотное
Карта технологических эскизов изготовления траверсы
Содержание дипломного проекта
Обзор и анализ состояния проблемы реализации установки КМУ на грузовые автомобили
1 Общие сведения об автомобилях с крано-манипуляторными установками
2 Классификация автомобилей с крано-манипуляторными установками
3 Конструкция крана-манипулятора: автомобильное шасси и крано-манипуляторная установка
4 Основные требования оснащения грузового автомобиля крано-манипуляторной установкой
Проект и расчет крано-манипуляторной установки на грузовой автомобиль
1 Выбор компоновочной схемы и ее расчет
1.1 Расчет центра тяжести манипулятора
1.1.1 Расчет центра тяжести стрелы
1.1.2 Расчет центра тяжести рукояти
1.1.3 Расчет координат центра тяжести клещевого захвата
1.1.4 Изменение координат центра тяжести манипулятора
1.2 Расчет центров тяжести манипулятора
1.3 Компоновка манипулятора
1.4 Расчет центров тяжести манипулятора
2 Расчет устойчивости автомобиля с КМУ
2.1 Расчет продольной статической устойчивости автомобиля на уклоне
2.2 Расчет максимального угла подъема при движении автомобиля на уклоне
2.3 Расчет поперечной устойчивости автомобиля с КМУ в транспортном положении на склоне
2.4 Расчет устойчивости автомобиля с максимальным вылетом манипулятора в сторону
2.5 Расчет устойчивости автомобиля при поперечном склоне с максимальным вылетом манипулятора
2.6 Расчет устойчивости при движении автомобиля с КМУ на повороте
2.7 Тяговый расчет автомобиля с КМУ
3 Проектирование и расчет манипулятора
3.1 Расчет проектных параметров манипулятора
3.1.1 Данные для расчета
3.1.2 Расчетная схема и расчет параметров
3.2 Расчет нагрузок манипулятора
3.2.1 Расчет реальных усилий гидроцилиндра рукояти и гидроцилиндра стрелы
3.2.2 Расчет усилий в механизме складывания рукояти
3.2.3 Расчет реакций в шарнире В и в шарнирах гидроцилиндра стрелы
3.4 Расчет шарнирных узлов
3.4.1 Расчет шатуна на прочность
3.4.2 Расчет на прочность пальцев шарниров
3.4.3 Расчет втулок шарнирных узлов
3.4.4 Расчет проушин шарнирных узлов
3.4.4.1 Расчет проушин на смятие
3.4.4.2 Расчет проушины на изгиб с растяжением
Меры безопасности при эксплуатации КМУ
2 Требования к персоналу
2.1 Общие требования охраны труда
2.2 Требования охраны труда перед началом работы
2.3 Требования охраны труда во время работы
2.4 Требования охраны труда по окончании работы
3 Мероприятия по повышению безопасности и повышению условий труда.
4 Расчет искусственного освещения
Экономическая часть
1 Расчет эксплуатационных затрат проектируемой машины с КМУ на год
2 Расчет эксплуатационных затрат машин
3 Расчет экономических показателей
Технологическая часть
2 Маршрут обработки
3 Расчетно-аналитический метод определения припусков на механическую обработку
4 Расчет режимов резания для токарной операции
5 Расчет режимов резания для фрезерно-центровой операции
6 Расчет вертикально-сверлильной операции
7 Расчет режимов резания для фрезерной операции
Список используемой литературы
Техническая характеристика КАМАЗ 6510
Снаряжённая масса т - 108.
Дополнительная нагрузка на коник тягача т - 122.
Дополнительная полная масса тягача т - 230.
Дополнительная нагрузка на передний мост т - 55.
Дополнительная нагрузка на заднюю тележку т - 175.
Двигатель - КамАЗ-740.51-320.
Мощность двигателя кВт (л.с.) - 235 (320).
Колёсная формула - 6 6.
Размер шин - 42585 R21.
ТЕХНИЧЕСКАЯ ХАРАКТЕРИСТИКА
Грузовой момент кНм - 75.
Максимальный вылет м - 78.
Ход удлинителя стрелы м - 12.
Угол поворота стрелы град - 360.
Угол подъёма стрелы град - 85.
Снаряжение - крюкгрейфер
Момент поворота кНм -16.
Управление – прямое.
Гидроцилиндр подъема опускания сборка.dwg

Устройство опорно-поворотное_А1.dwg

ЭО А1.dwg

грузоподъёмностью 10 тонн
Карта технологических эскизов изготовления траверсы
Рама прицепного устройства_А1.dwg

элементов швов выполненых ручной дуговой сваркой
*. Размер для справок.
Рама манипулятора_А2.dwg

Электроды Э42 ГОСТ 9467-75
*. Размер для справок.
Рабочая зона манипулятора_А1.dwg

грузоподъёмностю 10 тонн
Рабочая зона манипулятора
Грузовая характеристика
Рукоять_А2.dwg

Общий вид манипулятора_А1.dwg

Ход удлинителя стрелы
Угол поворота стрелы
Снаряжение - крюкгрейфер
Управление - прямое.
Дополнительная нагрузка на коник тягача
Дополнительная полная масса тягача
Дополнительная нагрузка на передний мост
Дополнительная нагрузка на заднюю тележку
Двигатель - КамАЗ-740.51-320.
кВт (л.с.) - 235 (320).
Колёсная формула - 6
Размер шин - 42585 R21.
Рама прицепного устройства
Сменное оборудование
Опорно поворотное устройство
Кран-манипулятор на автомобиле
грузоподъёмностью 10 тонн
ТЕХНИЧЕСКАЯ ХАРАКТЕРИСТИКА КамАЗ 6510