Кран подвесной г/п 6.3 т




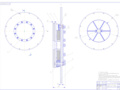
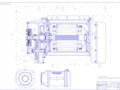
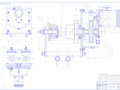
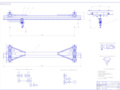
- Добавлен: 25.10.2022
- Размер: 2 MB
- Закачек: 0
Описание
Состав проекта
![]() |
![]() |
![]() ![]() ![]() ![]() |
![]() ![]() ![]() |
![]() ![]() ![]() |
![]() ![]() ![]() |
![]() ![]() ![]() ![]() |
![]() ![]() ![]() |
![]() ![]() ![]() ![]() |
![]() ![]() ![]() ![]() |
![]() ![]() ![]() ![]() |
![]() ![]() ![]() |
![]() ![]() ![]() |
![]() ![]() ![]() ![]() |
![]() ![]() ![]() ![]() |
![]() ![]() ![]() |
![]() ![]() ![]() |
![]() ![]() ![]() |
![]() ![]() ![]() ![]() |
![]() ![]() ![]() ![]() |
![]() ![]() ![]() ![]() |
![]() ![]() ![]() ![]() |
![]() ![]() ![]() |
![]() ![]() ![]() ![]() |
![]() ![]() ![]() ![]() |
![]() ![]() ![]() |
![]() ![]() ![]() |
![]() ![]() ![]() |
![]() |
![]() ![]() ![]() |
![]() ![]() ![]() |
Дополнительная информация
Тормоз спец.cdw

mekhanizm_peredvizhenia_tali_ispravlennaya.dwg
Механизм передвижения
Размеры для справок.
Остальные технические требования по СТБ 1022-96.
На привалочную поверхность Б нанеси равномерным слоем.
толщиной 1..2мм герметик У-30М УТ-31ГОСТ 13489-79.Наносить
Подшипники заполнить на 13 смазкой МЛи313 ГОСТ23252-79
mekhanizm_podema (2).cdw

*Размеры для справок
Подшипники заполнить смазкой МЛи313 ГОСТ23252-79
Остальные технические требования по СТБ 1022-96
Тормоз спец2.cdw

Общий вид спец.cdw

Канат ЛК-Р 6x19(1+6+66)+1
Вновь разработанные изделия
Механизм передвижения тали
механизм подъема2.cdw

Общий вид спец.dwg
Вновь разработанные изделия
Механизм передвижения тали
VO_isppravlenny (3).dwg
Скорость подъема груза
Скорость передвижения тали
Технические требования
Кинематическая схема запасовки каната
Кинематическая схема механизма подъема
Кинематическачя схема передвижения крана
Кинематическачя схема передвижения тали
Механизм передвижения 2.cdw

Кольцо уплотнительное 030-033-19
Винты M4-6gx12.58.016
Шайбы А 16.01.08nc.16
Механизм передвижения тали 3.cdw

mekhanizm_peredvizhenia_tali_ispravlennaya.cdw

Механизм передвижения
Размеры для справок.
Остальные технические требования по СТБ 1022-96.
На привалочную поверхность Б нанеси равномерным слоем.
толщиной 1..2мм герметик У-30М УТ-31ГОСТ 13489-79.Наносить
Подшипники заполнить на 13 смазкой МЛи313 ГОСТ23252-79
tormoz.cdw

Наличие смазывающих
* Размеры для справок
Гайки поз. 14 зажать обеспечив равномерное усилие
веществ на пов.В не допускается
При достижении износа фрикционной накладки до пов.Г
Остальные технические требования по СТБ 1022-96
Механизм передвижения 1.cdw

VO_isppravlenny (3).cdw

Скорость подъема груза
Скорость передвижения тали
Технические требования
Кинематическая схема запасовки каната
Кинематическая схема механизма подъема
Кинематическачя схема передвижения крана
Кинематическачя схема передвижения тали
mekhanizm_podema (2).dwg
*Размеры для справок
Подшипники заполнить смазкой МЛи313 ГОСТ23252-79
Остальные технические требования по СТБ 1022-96
механизм подъема3.cdw

механизм подъема.cdw

tormoz.dwg
Наличие смазывающих
* Размеры для справок
Гайки поз. 14 зажать обеспечив равномерное усилие
веществ на пов.В не допускается
При достижении износа фрикционной накладки до пов.Г
Остальные технические требования по СТБ 1022-96
Содержание.docx
1. Исходные данные 4
2. Выбор каната и крюка .4
3. Расчет диаметра барабана и блоков определение данных барабана 5
4. Выбор двигателя 7
5. Выбор параметров зубчатого зацепления 7
6. Расчет закрытых зубчатых передач ..8
6.1. Проверка расчетных контактных напряжений .9
6.2. Проверка расчетных напряжений изгиба ..10
7. Расчет тормозного момента. Выбор тормоза проверочный расчет тормоза 11
8.Расчет грузоупорного тормоза .12
9. расчет крепления каната к барабану 14
10. Расчет оси барабана 16
11. Выбор подшипников оси барабана 18
12. Проверочный расчет крюковой подвески 20
12.1. Упорный подшипник ..20
12.2. Расчет траверсы крюка 20
12.3. Расчет подшипников блоков ..23
Расчет механизма передвижения тали ..25
2. Сопротивление передвижения тали 25
3. Расчет мощности двигателя . 26
4. Проверка электродвигателя на время разгона 27
5 Проверка запаса сцепления с опорной поверхностью при разгоне ..29
Расчет механизма передвижения крана 30
1. Определение статических нагрузок на ходовые колеса крана 30
2. Сопротивление передвижению крана 31
3. Выбор электродвигателя . 32
4.Выбор параметров зубчатого зацепления . .. 33
5. Выбор тормоза ..33
6. Проверка элетродвигателя на время разгона .35
7.Проверка запаса сцепления с опорной поверхностью при разгоне ..36
Расчет металлоконструкции крана .37
Смазка узлов и деталей крана ..40
Техника безопасности 41
Список литературы 43
zapiska.docx
Увеличение производительности и улучшение технико-экономических показателей подъемно-транспортных машин повышение их прочности надежности и долговечности неразрывно связано с применением новейших методов расчета и конструирования.
Инженер должен обладать знаниями необходимыми для выполнения основных расчетов подъемно-транспортных машин и уметь обоснованно подобрать их в комплекс оборудования. При выполнении курсового проекта реальной машины студентам приходиться анализировать условия работы составлять кинематические схемы механизмов правильно компоновать узлы и машины определять производительность машин мощность приводов и т. д.
Расчёт механизма подъёма крана
ГрузоподъёмностьQ=6.3 т
Высота подъёма грузаН=12 м
Скорость подъёма грузаVгр=19 ммин
Скорость передвижения кранаVкр=17 ммин
Группа режима работы кранаA5
По рекомендациям принимаем сдвоенный полиспаст (а=1) кратностью i=2.
Рисунок 1.1 – Схема полиспаста
3 Выбор каната и крюка
Максимальное натяжение в канате набегающем на барабан при подъёме груза определяется по формуле
z=i.a=2*1=2 количество ветвей на которых висит груз
Канат выбираем по разрывному усилию:
где zp=55 – минимальный коэффициент использования каната для режима работы А5
По полученному разрывному усилию выбираем канат стальной двойной свивки типа ЛК-Р конструкции 6x19(1+6+66)+1 о.с. ГОСТ 7665-69 диаметром dк=18 мм при расчётном пределе прочности проволок =1800 МПа площадью сечения всех проволок Fк=12473 мм2 и с разрывным усилием Sр=181 кН.
По номинальной грузоподъёмности и режиму работы выбираем крюк однорогий тип А №15 ГОСТ 6627-74.
4 Расчёт диаметров барабана и блоков определение длины барабана
Диаметр блоков по средней линии навитого каната определяем по формуле:
где h2=224 – коэффициент выбора диаметра для блока для режима работы А5.
Из стандартного ряда выбираем диаметр блока мм
Диаметр барабана по средней линии навитого каната определяем по формуле:
где h1=20 – коэффициент выбора диаметра для барабана для режима работы A5
Учитывая габариты двигателя принимаем диаметр барабанамм.
Определяем шаг нарезки на барабане
Длина барабана определяется по формуле:
где - число витков нарезки
Принимаем длину барабана мм
Толщина стенки барабана выполненного из чугуна СЧ 15 определяется из расчета на сжатие:
где []сж – допускаемое напряжение сжатия стенок барабана определенное для чугуна по зависимости
где в предел прочности для чугуна при сжатии. Для чугуна СЧ 15 в = 650 МПа;
k – коэффициент запаса прочности. Согласно таблицы для крюковых кранов k = 425.
Однако исходя из технологии отливки барабана толщина стенки не должна быть меньше определенной по зависимости:
=002Dб+(610)=002380+8=156мм (1.9)
принимаем толщину стенки барабана 158 мм ;
Кроме того стенка барабана испытывает напряжения изгиба и кручения. При соотношении длины барабана к диаметру Lб Dб = 480380= 126 3 расчет на прочность по изгибу и кручению можно не выполнять.
Определяем статическую мощность на подъем груза номинальной массы по формуле:
Подбираем электродвигатель серии АО2-72-6 при ПВ 25% номинальная мощность Nном =22кВт частота вращения ротора n1=970 мин-1 момент инерции ротора Iр=04 кг·м2 ;
6 Выбор параметров зубчатого зацепления
Определяем частоту вращения барабана:
Следовательно потребное передаточное отношение механизма:
Определяем момент на тихоходном валу редуктора:
Определяем фактическую скорость груза:
Разница скорости составляет:
что в пределах нормы.
7 Расчет закрытых зубчатых передач
Расчет производится на выносливость по контактным напряжениям и на прочность зубьев при изгибе:
Принимаем модуль зубчатого зацепления m=5
Передаточное число первой ступени: U1=z1 z2 =12020=6
Передаточное число второй ступени: U2=z4 z3 =10020=5
Делительный диаметр: мм
Межосевое расстояние: мм
Выбираем Ст.20 : HB =180
7.1 Проверка расчетных контактных напряжений
Окружная сила в зацеплении:
Коэффициент учитывающий динамическую нагрузку в зацеплении:
Коэффициент учитывающий неравномерность распределения нагрузки по ширине венца: кH =1.05
Удельная расчетная окружная сила:
Расчетные контактные напряжения:
zн =177 ( коэф. учитывающий форму сопряженных поверхностей зубьев )
zЕ =275 МПа ( коэф. учитывающий механические свойства материалов колес )
z =1.05 ( коэф. суммарной длины контактных линий)
Запас прочности по контактным напряжениям:
Условие прочности соблюдается.
7.2 Проверка расчетных напряжений изгиба
Удельная расчетная окружная сила при изгибе:
Коэффициент учитывающий неравномерность распределения нагрузки по ширине венца: кF =1
Коэффициент учитывающий неравномерность распределения нагрузки для одновременно зацепляющихся пар зубьев: кFα =1
Коэффициент внешней динамической нагрузки: кА=125
Расчетные напряжения изгиба:
YFS=4.2 (коэффициент учитывающий форму зуба)
Y=1 (коэффициент учитывающий наклон зуба)
Y=1 (коэффициент перекрытия зубьев)
Запас прочности по напряжениям изгиба:
Условие прочности выполняется
8 Расчёт тормозного момента. Выбор тормоза проверочный расчёт тормоза
Статический момент на тормозном валу:
где - КПД полиспаста
= КПД зубчатой муфты
где km=15 – коэффициент запаса торможения
По приложению LI выбираем тормоз ТКТ-200100 развивающий тормозной момент 400 Н·м. При этом масса тормоза (m) 25 кг диаметр тормозного шкива (Dшк) 200 мм угол обхвата шкива =70о.
Тормоз регулируется на необходимый тормозной момент.
Проверочный расчёт на удельное давление:
где - коэффициент трения
где B=90 мм – ширина тормозного шкива
[q] – допускаемое удельное давление
Удельное давление в допускаемых пределах.
Проверочный расчёт на нагрев:
где [qv] – допускаемая удельная мощность трения
v – окружная скорость вращения шкива
q – удельное давление
Выбранный тормоз отвечает условию нагрева.
9 Расчет грузоупорного тормоза
Рисунок 1.2 – Схема грузоупорного тормоза
Определим угол трехзаходной резьбы тормозного вала:
где: α =3 –число заходов резьбы
Осевая сила возникающая при торможении и зажимающая фрикционные кольца тормоза:
где: ρ=2 3 – угол трения в резьбовой паре при работе в масляной ванне
f=012-коэффициент трения вальцованной ленты по стали в масле
Rc=0.145-средний радиус поверхности трения
Тормозной момент грузоупорного тормоза:
где: n=2-число пар трущихся поверхностей
Тормозной момент должен удовлетворять следующему условию:
Грузоупорный тормоз в электротали используется в качестве второго тормоза механизма подъема поэтому коэффициент запаса торможения принимается равным 1.25
Движущийся вниз груз остановится при условии:
Проверка резьбы на смятие:
где: dН-диаметр наружный винтовой резьбы
dВ-диаметр внутренний винтовой резьбы
z-число витков резьбы воспринимающих нагрузку
10 Расчёт крепления каната к барабану
Рисунок 1.6 – Крепление каната к барабану
Определим выдергивающее усилие:
где: - угол обхвата канатом барабана принимаем =4
f - коэффициент трения между канатом и барабаном (f=010 016)
Необходимое осевое усилие болта:
где - приведенный коэффициент трения между канатом и барабаном
где =40о – угол заклинивания каната
=2 - угол обхвата барабана канатом при переходе от одной канавки планки к другой
где [сж] – допускаемое напряжение сжатия болта.
d1=4928 – внутренний диаметр болта М6
Принимаем 10 прижимных планок.
Суммарное напряжение в болте при затяжке крепления с учётом растягивающих и изгибающих усилий:
где n=15 – коэффициент запаса надёжности крепления каната к барабану
z=2 – количество болтов на одной планке
l=9 мм – расстояние от дна канавки на барабане до верхней плоскости прижимной планки
- усилие изгибающее болты
Допускаемое напряжение для болта:
МПа - предел текучести для стали Ст5
Так как болты отвечают условию прочности.
11 Расчёт оси барабана
Нагрузки действующие на барабан:
Определим опорные реакции:
Строим эпюру изгибающих моментов:
Сложное напряжение от изгиба и кручения
где мм- диаметр барабан по дну канавки.
мм- внутрений диаметр стенки барабана.
=075- коэффициент приведения.
Рисунок 1.7 – Расчёт барабана
12 Выбор подшипников оси барабана
Подшипник опоры А. Поскольку ось барабана не вращается относительно вала редуктора то подшипник опоры А выбираем по статической нагрузке.
Расчётная нагрузка на подшипник:
где - коэффициент безопасности (прил. Х [1])
По этой нагрузке выбираем подшипник который должен иметь наружный диаметр 80 мм.
Таким условиям удовлетворяет роликовый радиальный упорный подшипник № 7207 А (ГОСТ 27365–87) имеющий следующие параметры:
D=80 мм d=50мм B=1825 мм С0=32500 Н С=48400 Н.
Так как подшипник опоры В работает при переменном режиме нагрузки определяем эквивалентную нагрузку:
где Р1 Р2 Р3 Р4 – эквивалентный нагрузки
L1 L2 L3 L4 – номинальные долговечности млн. об.
Радиальные нагрузки на подшипник при среднем режиме работы:
Fr2=05·Rа=05.13275=66375 H
Fr3=0195·Rа=0195.13275=258863 H
Fr4=005·Rа=005.13275=66375 H
Номинальная долговечность подшипника млн. об.:
где Lh=3500 ч – ресурс подшипника (прил. ХII [1])
n – частота вращения барабана
Номинальные долговечности при каждом режиме нагрузки млн. об.:
L1= L3=01·L=137298 млн. об.
L2=05·L=68649 млн. об.
L4=03·L=411894 млн.об.
Для радиального роликоподшипника эквивалентную нагрузку вычисляют по формуле:
где Fr – радиальная нагрузка
Fа – осевая нагрузка в нашем случае Fа=0
V =1 – коэффициент вращения
kt – температурный коэффициент kt=1 (так как рабочая температура подшипника t01000C)
- коэффициент безопасности
X – коэффициент радиальной нагрузки для радиальных двухрядных роликоподшипников Х=1
Эквивалентные нагрузки для каждого режима нагружения:
Эквивалентная нагрузка:
Динамическая грузоподъёмность:
где - показатель степени для роликоподшипников =33
С целью унификации для опоры В принимаем подшипник № 7207 А который удовлетворяет по динамической грузоподъёмности.
13 Проверочный расчёт крюковой подвески
13.1 Упорный подшипник
Расчётная нагрузка на подшипник должна быть равна или меньше статической грузоподъёмности:
Для крюка диаметром шейки d1=17 мм выбираем упорный однорядный подшипник лёгкой серии 8204 (ГОСТ 6874-75) со статической грузоподъёмностью С0=80600 Н внутренний диаметр d=30 мм наружный D=60 мм (прил. IX [1]).
13.2 Расчёт траверсы крюка
Траверса изготовлена из Стали 45 имеющей предел прочности в=600 МПа предел текучести т=600 МПа предел выносливости -1=240 МПа.
Траверсу рассчитывают на изгиб при допущении что действующие на неё силы сосредоточенные; кроме того считают что перерезывающие силы незначительно влияют на изгибающий момент. Из приложения XI [1] определяем расстояние между креплениями траверсы b=50 мм.
Максимальный изгибающий момент (рис. 5 сечение А–А):
где Qp – расчётная нагрузка на траверсу (как и на упорный подшипник)
Момент сопротивления среднего сечения траверсы:
где [] – допускаемое напряжение материала на изгиб
где d2 =d1+(2 5)=20+5=25 мм
b1 – ширина траверсы; назначается с учётом наружного диаметра D1 посадочного гнезда для упорного подшипника
b1=D1+(10 20)=60+10=70 мм
Изгибающий момент в сечении Б – Б:
Минимальный диаметр цапфы под подшипник:
Рисунок 1.5 – Траверса
13.3 Расчёт подшипников блоков
Поскольку подшипники блоков работают при переменном режиме нагрузки то их подбираем так же как и подшипник опоры В оси барабана.
где zбл – число блоков
zпод – число подшипников на которых установлен блок
Fr2=05·Fr1=05.4900 =2450 H
Fr3=0195·Fr1=0195.4900=955 H
Fr4=005·Fr1=005.4433=245 H
n – частота вращения подвижного блока
где Dбл – диаметр блока по центру наматывания каната
L1= L3=01·L=089 млн. об.
L2=05·L=445 млн. об.
L4=03·L=293 млн. об.
V =12 – коэффициент вращения
X – коэффициент радиальной нагрузки для однорядных шарикоподшипников Х=1
где - показатель степени для шарикоподшипников =3
По динамической грузоподъёмности выбираем шарикоподшипник радиальный однорядный 1000908 (ГОСТ 8338-75) имеющий следующие характеристики D=62 мм d=40 мм В=12 мм С0=6900 Н.
Расчёт механизма передвижения тали
Рисунок 2.1 - Кинематическая схема механизма передвижения тали
По таблице 52[3] с учетом Рст max выбираем диаметр колеса D=100 мм.
По диаметру выбираем по таблице колеса с зубчатым венцом типа К1Р1-150К.
Диаметр цапфы колес dц =005 м; количество реборд колеса zр=1; форма поверхности катания – коническая; тип подшипника – роликовый радиальный сферический двухрядный
2Сопротивление передвижения тали
При расчётах подвесных кранов работающих в закрытых помещениях сопротивление передвижению тележки вычисляют по формуле:
где d=50 мм – диаметр цапфы ходового колеса
f=0015 – коэффициент трения в подшипниках колёс
=06 мм – коэффициент трения качения колеса по рельсу с выпуклой головкой
kp=25 – коэффициент учитывающий сопротивление от трения реборд о рельсы и от трения токосъёмников о троллеи (табл. 28 [1]).
=0002 – расчётный уклон пути
Сопротивление создаваемое уклоном:
Сопротивление создаваемое силами инерции:
где: -коэффициент учитывающий инерцию вращающихся частей механизма
а- ускорение при разгоне
Полное сопротивление передвижению тали:
3 Расчёт мощности двигателя
Предварительное значение КПД механизма принимаем равным пр=085
Определяем необходимую мощность:
Выбираем двигатель 4АА63В4УЗ имеющий параметры: N=23кВт; n=1365 мин-1; d=15 мм; m=85 кг; TпускTном = 2 Н.м.
Частота вращения колеса:
Требуемое передаточное отношение:
Фактическое передаточное число редуктора:
Фактическая скорость передвижения тали:
Расчёт механизма передвижения крана
Рисунок 3.1 - Кинематическая схема механизма передвижения крана
1 Определение статических нагрузок на ходовые колеса крана
Ориентировочная масса крана: mкр=2245 т
Для крана грузоподъемностью до 8 т следует использовать Рmin и Рmax схему изображенную на рисунке 3.2
Рисунок 3.2 – Расчетная схема механизма передвижения крана
Определяем максимальную нагрузку на все колеса одной стороны
Минимальная нагрузка на колеса одной стороны:
Принимаем число ходовых колес крана Zх.к.=8
Минимальная нагрузка на одно колесо:
где: nх.к.1-число ходовых колес с одной стороны
Максимальная нагрузка на одно колесо:
Выбираем колесо D=200 мм; стандартную колесную установку КР1-200К; диаметр цапфы колес dц=50 мм; количество реборд колеса zp=1; форма поверхности катания – коническая.
2 Сопротивление передвижению крана
Сопротивление создаваемое силами трения:
Ускорение при разгоне:
Полное сопротивление передвижению крана:
3 Выбор электродвигателя
Задаемся предварительным значением КПД механизма передвижения крана
Необходимая мощность электродвигателя:
По [1] предварительно определяем электродвигатель MTКF 312-6 развивающий мощность 19.5 кВт при частоте вращения n1=945 мин-1; максимальный момент 480 Н·м момент инерции ротора 00318 кг·м2 масса электродвигателя 210 кг.
4 Выбор параметров зубчатого зацепления
Определяем частоту ходовых колес по формуле:
Требуемое передаточное число механизма:
Угловая скорость вращения вала электродвигателя:
Фактическая скорость передвижения крана:
Сопротивление передвижению крана без груза от уклона:
Сопротивление создаваемое трением:
Сопротивление создаваемое инерцией:
Момент создаваемый уклоном:
Момент создаваемый силами трения:
Момент создаваемый силами инерции:
Расчетный тормозной момент механизма передвижения тали при работе без груза:
Исходя из того что значение требуемого тормозного момента очень мало и
учитывая рекомендации тормоз на механизм передвижения крана можно не устанавливать.
6 Проверка электродвигателя на время разгона.
Среднепусковой момент двигателя:
Момент статических сопротивлений при разгоне приведенный к валу двигателя:
Момент инерции при разгоне поступательно движущихся частей механизма приведенный к валу двигателя:
Время разгона для механизма передвижения крана:
Время разгона для тали не должно превышать 4 с [1]. Полученное время tр.ф. удовлетворяет этому условию. Следовательно выбранный двигатель обеспечит необходимую интенсивность работы.
Проверим среднее ускорение при разгоне:
Это значение не превышает среднего допускаемого [а]=03 мс2 [1]
7 Проверка запаса сцепления колес с опорной поверхностью при разгоне
Минимальное значение коэффициента сопротивления передвижению при Кдоп=1
Статическое сопротивление движению при разгоне:
Сила инерции масс тали:
Запас сцепления ходовых колес с опорной поверхностью при разгоне на подъем:
где: [ксц]-допускаемый коэффициент запаса сцепления при работе без ветровой нагрузки
Запас сцепления колес с опорной поверхностью обеспечен.
Расчёт металлоконструкции крана
Приведем расчет главной балки моста по которой передвигается таль. Балка выполнена из прокатного двутаврового профиля и по концам упирается на концевые сварные балки.
Для подсчета нагрузки от собственной массы предварительно принимаем массу балки qб=30 кгм массу механизма передвижения и горизонтальной решетки моста qг=07 кгм. Эту массу считаем равномерно распределенной по длине балки между главной балкой и вспомогательной фермой.
Соответственно расчетная нагрузка на 1м балки:
Определим величину прогиба:
Коэффициент жесткости моста:
Расчетная нагрузка от масс поднимаемого груза и тали:
где: =11- коэффициент динамичности
Эту нагрузку принимаем равномерно распределенной на колеса тали. В соответствии с этим расчетная нагрузка на каждое колесо:
Рисунок 4.1 –Расчетная схема моста крана
Опорная реакция балки в соответствии с расчетной схемой (рис.4.1):
где: bb1-размеры принятые конструктивно
Изгибающий момент от подвижной нагрузки:
Изгибающий момент от собственной массы моста:
Суммарный изгибающий момент:
Допускаемое напряжение для принятого материала балки []=170 МПа
Необходимый момент сопротивления балки при этих напряжениях:
По ГОСТ 8239-89 выбираем балку двутаврового профиля №22 с моментом инерции относительно оси x-x Ix=2550 см4 и моментом сопротивления Wx=232см3
Рисунок 4.2 –Поперечное сечение главной балки
Прогиб балки от подвижной нагрузки:
Допускаемый прогиб:мм
Смазка узлов и деталей крана
Для смазки подшипников качения блоков барабана и механизмов крана применяется смазка пресс-солидол синтетический ГОСТ 4366-64 и солидол синтетический ГОСТ 4366-64.
Для смазки каната применяется смазка канатная по ТУ 38-1-1-67.
Смазка редукторов производится автотракторным маслом АКЗп-6 или другими близкими по свойствам по ГОСТ 1862-63.
Зубчатые муфты по рекомендации ГОСТ 50006-83 заполняют следующими смазочными материалами в зависимости от окружающей температуры: ТСп-10 МТ-8п ИПП-200. Смазка реборд колес и рельсов производится графитной смазкой.
Техника безопасности
К управлению краном допускаются лица не моложе 18 лет имеющие соответствующее удостоверение и прошедшие медицинский осмотр для пригодности работы на кране.
Перед началом работы машинист обязан проверить техническое состояние основных механизмов и узлов крана (тормозов крюка канатов блоков металлоконструкции крана) и исправной работы приборов безопасности.
Правилами ГГТН а также стандартом СЭВ 725-77 на грузоподъёмных кранах с электрическим приводом предусмотрена установка концевых выключателей для автоматической остановки:
крана если его скорость может превышать 0533 мс (по стандарту СЭВ–05 мс);
при опасном сближении кранов;
механизма подъёма грузозахватного устройства перед подходом к упору.
Концевой выключатель механизма передвижения устанавливают таким образом чтобы в момент выключения тока расстояние от буфера до упоров составляло не менее половины пути торможения. Концевые выключатели устанавливают в электрической цепи так чтобы при их размыкании сохранилась цепь для обратного движения механизма. Для данного крана применяем концевой выключатель КУ 704 который предназначен для механизма горизонтального перемещения имеющего привод фиксированного положения.
Концевой выключатель механизма подъёма устанавливают так чтобы после остановки грузозахватного устройства зазор между ним и упором на тележке составлял не менее 200 мм. Для этой цели применяют выключатели типа КУ 703 имеющий двухплечий рычаг.
Основной целью данного курсового проекта было обучение основам конструирования сложной машины закрепление углубление и обобщение знаний приобретенных при изучении теории дисциплины “Грузоподъемные машины” и ”Строительная механика и металлоконструкции подъемно-транспортных машин”.
В данном курсовом проекте был разработан кран подвесной грузоподъемностью 6.3 т. Произведены расчеты механизмов крана подобраны двигатели редуктора тормоза механизма подъема а так же даны рекомендации по технике безопасности при работе с краном и условия смазки узлов. Проверочные расчёты показали что спроектированный кран отвечает всем требованиям стандартов и способен выполнять необходимые технологические операции.
Иванченко Ф. А. Расчеты грузоподъемных и транспортирующих машин.-2изд. перераб. и доп.-Киев.: Вища школа 1978.-574 с.
Справочник по кранам. Т. 2. Под ред. А.И. Дукельского. – Л.: Машиностроение 1973. – 472с.
Курсовое проектирование грузоподъёмных машин. Руденко Н.Ф. Александров М.П. и Лысяков А.Г. Изд. 3-е перераб. и доп. М.: Машиностроение 1971 464 с.
Курсовое проектирование грузоподъёмных машин: Учеб. Пособие для студентов машиностр. вузов; Под ред. С.А. Казака.-М.:Высш. Шк. 1989. – 319 с.
Марон Ф. Л. Справочник по расчетам механизмов подъемно-транспортных машин. Минск "Вышэйш. школа" 1977. 272 с. с ил.
Правила устройства и безопасной эксплуатации грузоподъемных кранов