Кран башенный с подъемной стрелой г/п 4 т




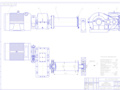
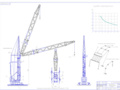
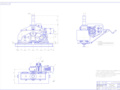
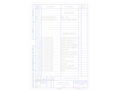
- Добавлен: 25.10.2022
- Размер: 1 MB
- Закачек: 1
Описание
Состав проекта
![]() |
![]() ![]() ![]() |
![]() ![]() |
![]() ![]() ![]() |
![]() ![]() |
![]() ![]() |
![]() ![]() ![]() |
![]() |
![]() ![]() ![]() ![]() |
![]() ![]() ![]() ![]() |
![]() ![]() ![]() ![]() |
![]() ![]() ![]() ![]() |
![]() ![]() ![]() ![]() |
![]() ![]() ![]() ![]() |
![]() ![]() |
![]() ![]() ![]() |
![]() ![]() |
![]() ![]() |
Дополнительная информация
Механизм передвижения.doc
Условия соблюдаемые при расчёте. Допустимое отклонение кранового пути от проектной схемы по высоте в пределах базы (колеи) при определении наибольших реакции опор используемых при расчёте на прочность.
Определяем вертикальную реакцию принимая что кран опирается на четыре опоры:
где расчётная вертикальная нагрузка на основание:
среднее квадратическое отклонение случайной составляющей груза;
Принимаем в каждой из четырёх опор балансирные тележки в каждой по два ходовых колеса с нагрузкой на одно колесо
Из условия прочности подкранового пути и допускаемых давлений на грунт принимаем (1. приложение XLVIII) рельс Р43 с допускаемой нагрузкой на ходовое колесо . По (1. приложение XLV) выбираем ходовое двухребордное колесо диаметром и допускаемой нагрузкой при легком режиме работы и скорости передвижения не более или
Определяем сопротивление передвижению башенного крана. Это сопротивление определяем как сумму сопротивлений трения ветра уклона от нормальных и случайных составляющих нагрузок веса крана веса груза и ветровой нагрузки с учётом уклона подкранового пути:
где сопротивление от сил трения:
где суммарная вертикальная нагрузка;
(1. табл. 38) для ходового колеса диаметром 400 мм на подшипниках качения;
сопротивление от сил ветра действующего на кран и на груз.
Сопротивления от сил ветра на стрелу башню с кабиной платформу балласт и груз определены выше и равны соответственно:
Сопротивление от сил ветра на неповоротную часть:
Случайные составляющие ветровых нагрузок на стрелу башню платформу балласт груз также были определены ранее:
где случайная составляющая ветровой нагрузки на неповоротную часть:
Сопротивление от уклона:
Инерционное сопротивление передвижению крана в пусковой период:
где среднее ускорение крана при пуске (1. таблица 39).
Мощность двигателей механизма передвижения:
где скорость передвижения;
среднепусковой коэффициент перегрузки;
Применяем механизм передвижения с раздельным приводом тележек. Устанавливаем приводные тележки в опорных точках по диагонали опорного контура.
Мощность двигателя расчётная:
По каталогу крановых двигателей принимаем два асинхронных электродвигателя с фазовыми роторами MTH 211-6 и момент инерции упругой муфты
Общее передаточное число механизма:
где частота вращения ходового колеса.
Выбираем тормоз ТТ – 200 диаметры ходовых колёс с дальнейшей аналогичной проверкой.
Определяем время пуcка:
где приведённый к валу двигателя момент инерции одного приводного агрегата и половины масс крана:
Статический момент от половинного сопротивления передвижению:
Ускорение при пуске:
Необходимо применение пуско – регулирующих устройств.
Проверка запаса сцепления при пуске:
сопротивление передвижению крана при
число приводных колёс;
диаметр оси ходового колеса (1. таблица38);
диаметр ходового колеса;
коэффициент сцепления колеса с рельсом;
Сила ветра на кран определиться по формуле:
Сопротивление от уклона определяется по формуле:
Определяем сопротивление трению:
Проверка двигателя по моменту. Условие правильности выбора электродвигателя:
где коэффициент перегрузки определяемый по (1. таблицы 22);
момент на валу двигателя от нормативных составляющих нагрузок при торможении:
расчётная несущая способность по моменту
коэффициент условий работы
где коэффициент ответственности (1. таблица 24);
коэффициент учитывающий особенности работы;
Определение тормозного момента и выбор тормоза. Расчётный тормозной момент:
По каталогу выбираем тормоз ТТ-200 с тормозным моментом и регулируем на расчётный момент.
Проверка тормоза по моменту. Условие правильности выбора тормоза:
где коэффициент ответственности для тормозов механизмов;
коэффициент учитывающий особенности работы тормоза (1. таблица 25);
Следовательно тормоз удовлетворяет проверке по моменту.
Изменение вылета.doc
1. Определение усилий в стреловом расчале.
Механизм изменения вылета как и механизм подъема груза должен рассчитываться на действие нормативной ( (т)) и случайной составляющей ( (т)) массы груза определяемой по формуле
где коэффициент принимаемый по табл. и равный 005
Тогда расчетная грузоподъемность т
Усилие в стреловом расчале (кН) без учета инерционных нагрузок определяется по формуле
где расчетная грузоподъемность ( ) т;
масса крюковой подвески т;
ускорение свободного падения мс²;
ветровая нагрузка на груз кН;
ветровая нагрузка на стрелу кН;
усилие в грузовом канате кН;
угол наклона стрелы град;
плечо действия усилия в грузовом канате относительно пяты стрелы м;
плечо действия усилия в расчале стрелы относительно пяты стрелы м.
Масса крюковой подвески т
Ветровые нагрузки кН определяются на основании нормативного давления ветра по ГОСТ 1451-77
где и наветренная площадь груза и стрелы м2;
распределенная ветровая нагрузка на стрелу Па
где скоростной напор или динамическое давление ветра Па =125 Па;
коэффициент учитывающий возрастание скоростного напора в зависимости от высоты установки элемента крана над поверхностью земли =175
аэродинамический коэффициент (для конструкций из прямоугольных профилей =15 19; для груза =12);
коэффициент перегрузки (для рабочего состояния =1).
Наветренная площадь груза ( м2) определяется в зависимости от массы груза по формуле
Наветренная площадь стрелы м2 определяется по формуле
где площадь стрелы по ее контуру м2;
коэффициент заполнения 02 06 для ферм из прямоугольных профилей.
Предварительно площадь стрелы по ее контуру можно определить по формуле
Усилие в грузовом канате при максимальной грузоподъемности кН
Коэффициент полезного действия грузового полиспаста при кратности до 4 определяется по формуле
При наличии в системе подвески груза обводных блоков общий КПД будет равен
где КПД одного блока на подшипниках качения и нормальной смазке ().
где кратность грузового полиспаста;
число ветвей каната наматываемых на грузовой барабан;
общий КПД грузового полиспаста (определяется ниже).
2.Определение кратности стрелового полиспаста и подбор каната.
Кратность стрелового полиспаста
Коэффициент полезного действия стрелового полиспаста
Максимальное усилие в ветви стрелового каната (кН) набегающего на барабан
где максимальное усилие в стреловом расчале кН.
Необходимое минимальное разрывное усилие в канате кН
где коэффициент использования каната (прил. Б) определяемый в зависимости от группы классификации механизма по ИСО 43011.=335
-Г-I-H-1764 ГОСТ 2688-80 F=5345kH
Фактический коэффициент использования каната
где табличное значение разрывного усилия в стреловом канате (кН) принятое по стандарту при данной маркировочной группе.
3. Определение геометрических размеров барабана.
Минимальный диаметр барабана (мм) блока (мм) согласно требованиям правил Ростехнадзора
где диаметр каната мм;
коэффициенты выбора диаметров =125 =14
Длина наматываемого на барабан каната м
где и расстояние между оголовком стрелы и оголовком башни
Расстояния и вычисляются по формуле
Количество рабочих витков
где число слоев навивки каната (не более 4);
коэффициент неплотности навивки каната (для гладких барабанов =09 095).
где число запасных витков (=15÷2);
число витков каната находящихся под зажимным устройством (=3÷4).
Длина гладкого барабана (мм) вычисляется по формуле
Конструктивно соотношение между длиной барабана и его диаметром должно находиться в пределах:
Гладкие барабаны выполняются с ребордами диаметр которых (мм) равен
4. Расчет и выбор электродвигателя.
Необходимая мощность электродвигателя (кВт) механизма изменения вылета
где среднее расчетное усилие в ветви каната набегающей на барабан кН;
средняя скорость навивки каната на барабан мс;
– КПД редуктора (085).
Средняя скорость навивки каната на барабан мс
где время изменения вылета с.
Среднее расчетное усилие в ветви каната набегающей на барабан (кН)
Выбираю электродвигатель марки МТH 511-8:
Мощность при ПВ 15%
Максимальный момент
Момент инерции ротора
Габаритные размеры электродвигателя марки МТН 511-8:
Высота оси ротора = 250(мм);
Радиус корпуса двигателя =212 (мм);
Диаметр конца выходного вала =70(мм);
5.Кинематический расчет лебедки подбор редуктора.
Частота вращения барабана обмин
Необходимое расчетное передаточное число редуктора
где частота вращения вала электродвигателя обмин.
Для механизма изменения вылета расчетное значение мощности на быстроходном валу редуктора
где номинальное значение мощности двигателя кВт;
коэффициент нагрузки (назначается в зависимости от режима работы: =15 при Л; =13 при С; = 11 при Т).
Для уменьшения габаритов лебедки барабан и электродвигатель располагают по одну сторону от редуктора. Зная габаритные размеры барабана и электродвигателя необходимо провести их компоновку проверить возможность размещения их на раме лебедки по одну сторону редуктора. Расположение их на раме должно удовлетворять следующему условию
где межосевое расстояние редуктора мм;
диаметр гладкого барабана по ребордам или по болтам крепления каната к барабану накладкой при нарезных барабанах () мм;
радиус корпуса электродвигателя мм;
минимальный зазор между ребордой барабана и корпусом электродвигателя мм ().
После подбора редуктора определяют фактическую скорость навивки каната на барабан (мс) при действительном передаточном числе выбранного редуктора .
Фактическое время перевода стрелы из крайнего нижнего положения в крайнее верхнее (с) определим по формуле:
Отклонение времени изменения вылета от заданного
не должно превышать ± 5 %.
Номинальный момент двигателя Нм
Максимальный статический момент двигателя Нм
Минимальный статический момент двигателя Нм
Среднепусковой момент двигателя Нм
где максимальный момент двигателя Нм
Муфты выбираются по наибольшему расчетному крутящему моменту (Нм) который для муфты устанавливаемой между редуктором и двигателем определится по формуле
где коэффициент учитывающий степень ответственности механизма (для механизма изменения вылета =14);
коэффициент учитывающий режим работы (значения принимаются равными при Л 11; С 12; Т 13: ВТ 15);
передаточное число выбранного редуктора.
По каталогу выбираем муфту МУВП-3:
Наибольший передаваемый момент
Диаметр тормозного шкива =400(мм);
Ширина тормозного шкива =185(мм);
Масса муфты =125(кг);
Момент инерции муфты
Размеры зубчатой муфты тихоходного вала:
Диаметр начальной окружности =400(мм);
Размер посадочного места под подшипник оси барабана:
7.Подбор и расчет тормоза.
Расчетный тормозной момент (Нм) в соответствии с рекомендациями Ростехнадзора РФ равен
где коэффициент запаса торможения (табл. 3)=175;
статический тормозной момент приведенный к валу электродвигателя при максимальном усилии в стреловом полиспасте (Нм)
Статический тормозной момент при минимальном усилии в стреловом полиспасте Нм
Зная расчётный тормозной момент по каталогу выбираем тормоз типа ТКТГ-400М с электрогидравлическим толкателем с максимальным тормозным моментом
Диаметр тормозного шкива
Ширина тормозного шкива =185 (мм);
Высота центра шкива =320(мм);
Работоспособность тормоза будет долговечной если удельное давление фрикционных накладок будет меньше допустимого:
где нормальное давление колодки на шкив Н;
площадь фрикционной накладки мм2;
допустимое удельное давление передаваемое колодкой на шкив.
где коэффициент трения между колодкой и шкивом
диаметр тормозного шкива;
где угол обхвата шкива тормозными колодками;
ширина тормозных накладок
8. Проверка двигателя и тормоза по моменту.
Выбранный двигатель необходимо проверить по моменту. Условие правильности его выбора
где коэффициент перегрузки для механизма изменения вылета =135;
момент на валу двигателя от нормативной статической нагрузки Нм ();
максимальный момент развиваемый электродвигателем принимаемый по каталогу Нм;
коэффициент условий работы;
где коэффициент ответственности принимаемый в зависимости от класса ответственности механизма и элемента (при II классе ответственности =095);
коэффициент учитывающий условия работы (для электродвигателей механизмов изменения вылета =08).
Условие правильности выбранного тормоза по моменту аналогично запишется в следующем виде:
где максимальный тормозной момент развиваемый тормозом принимаемый по каталогу Нм.
Коэффициент перегрузки при проверке тормозов:
где коэффициент надежности (для II класса ответственности механизма и элемента =5);
коэффициент изменчивости ..
9.Расчет времени пуска и торможения механизма.
Среднее время пуска (с) при максимальном и минимальном усилии в стреловом полиспасте определяется по формуле
где кинетическая энергия стрелы и груза (кгм2рад2)с2;
угловая скорость вращения вала электродвигателя радс
максимальный () и минимальный () статический момент на валу электродвигателя Нм;
момент инерции вращающихся масс механизма кгм2.
где масса стрелы кг;
линейная скорость движения груза при подъеме стрелы (принимаем =0 так как в кране при изменении вылета осуществляется горизонтальное перемещение груза).
Угловая скорость вращения стрелы (радс)
где максимальный и минимальный углы наклона стрелы рад;
время изменения вылета с.
где коэффициент учитывающий приведенное значение моментов инерции вращающихся деталей редуктора и барабана (=12);
момент инерции ротора двигателя и муфты с тормозным шкивом значения которых принимаются по каталогу (кгм2).
Время торможения механизма изменения вылета (с) при максимальном и при минимальном усилии в стреловом полиспасте
где тормозной момент на который отрегулирован тормоз определенный выше Нм.
10.Расчет барабана на прочность.
Минимальная толщина стенки барабана (мм) из расчета на сжатие
где максимальное усилие в канате наматываемом на барабан Н;
шаг нарезки для нарезных ( диаметр каната для гладких) барабанов мм;
допускаемое напряжение на сжатие МПа;
коэффициент учитывающий повышение напряжения сжатия в стенке барабана в зависимости от слоев навивки каната на барабан (=1 при =1; =128 при =2;
=136 при =3; =141 при =4).
Допускаемое напряжение на сжатие (МПа) для чугунных барабанов принимают равным:
Для чугуна марки СЧ-15 =650 МПа.
Для чугунных барабанов исходя из требований технологии отливки минимальная толщина стенки (м) должна быть не менее
где диаметр барабана который для нарезных измеряется по дну канавки м.
Поэтому при расчете барабана на прочность рекомендуется сначала найти затем определить напряжения сжатия (МПа) сравнить их с допускаемыми:
Окончательно принимаем толщину стенки =12 мм.
11. Расчет крепления каната к барабану.
Натяжение каната в месте крепления (Н) на барабане будет меньше чем усилие в канате из-за наличия 15 2 запасных витков и определится по теории Л. Эйлера
где коэффициент трения между канатом и барабаном (=01 016);
угол обхвата барабана запасными витками рад.
При креплении конца каната на барабане накладкой сила (Н) растягивающая один болт
- приведенный коэффициент трения между канатом и накладкой с трапециидальным сечением канавки.
где - угол наклона боковой грани канавки;
Сила (Н) изгибающая болт определяется по формуле
Необходимо подобрать требуемый диаметр резьбы болта (мм) и определить суммарное напряжение (МПа) в каждом болте по формуле
где коэффициент учитывающий напряжения кручения при затяжке болтов;
коэффициент запаса надежности крепления каната;
расстояние от головки болта до барабана мм
внутренний диаметр резьбы болта мм (материал болтов сталь Ст3 Ст4 (=240 МПа));
допускаемое напряжение на растяжение материала болта МПа
где =1; =13; =1 при Л.
12.Расчет оси барабана и подбор подшипников.
Передача крутящего момента от редуктора на барабан может быть выполнена принципиально по различным схемам. Однако наиболее надёжна и совершенна схема механизма у которой выходной вал редуктора соединён с барабаном зубчатой муфтой. Конец выходного вала редуктора в этом случае выполняется в виде зубчатого диска во внутреннюю полость которого устанавливается подшипник оси барабана. Передача крутящего момента от редуктора происходит в этом случае непосредственно через зубчатый венец на барабан вращающийся на оси. Второй опорой оси барабана является кронштейн устанавливаемый на раме лебёдки. Возможные перекосы при монтаже лебёдки компенсируются установкой сферических подшипников качения.
Определим диаметр оси барабана:
где максимальный изгибающий момент
допускаемое напряжение при приближённом расчёте (для обеспечения достаточной жёсткости оси как условия нормальной работы подшипников принимают ).
где - максимальная радиальная нагрузка на подшипник;
расстояние от опоры барабана до внутреннего края реборды барабана;
Подшипники оси барабана подбираем по динамической грузоподъёмности пользуясь следующей эмпирической зависимостью:
для шариковых подшипников;
эквивалентная нагрузка кН;
где минимальная и максимальная радиальная нагрузка на подшипник кН.
где - частота вращения барабана;
- номинальная долговечность подшипника;
Условие подбора подшипника:
Марка подшипника сферический двухрядный радиальный Тип – 1213
Динамическая грузоподьемерсть318 кН
Статическая грузоподъемность 295 кН
Размеры.doc
1.Определение габаритных характеристик крана.
Размер поперечного сечения башни (сторона квадрата):
Размер поперечного сечения стрелы (сторона прямоугольника):
Высота головки рельса до шарнира пяты стрелы:
Высота головки башни (от центра пяты стрелы до центра верхних блоков):
Расстояние от оси вращения крана до оси башни:
Расстояние от оси вращения башни до пяты стрелы:
Длина распорки (подстрелка) от оси вращения крана до оси блока:
Колея и база ходовой части крана:
Расчётная длинна стрелы:
Ориентировочный диаметр опорно-поворотного круга:
Ширину поворотной платформы определим по формуле:
Радиус хвостовой части поворотной платформы:
2.Определение массовых и весовых характеристик крана:
Определим общую массу крана по формуле:
где момент грузовой
Укрупненное распределение общей массы крана:
металлоконструкции:
механизмы и электрооборудование:
балласт и контргруз:
Металлоконструкции крана:
масса поворотной платформы:
масса неповоротной рамы:
лебедка подъёма груза:
лебедка механизма изменения вылета:
механизм вращения крана:
механизм передвижения крана:
грузовой полиспаст и крюк:
стреловой полиспаст:
ходовой тележки и колеса (4 комплекта):
М груза.dwg

Число слоев навивки каната 2
Передаточное число 9
Элетродвигатель МТН-311-6
Спецификация.ВО..dwg

КБ-202.00.00.000.Р.П.З
Расчетно-пояснительная записка
Лебедка грузоподьемная
Ходовая тележка неприводная
Ходовая тележка приводная
Неповоротная платформа
Поворотная платформа
Механизм передвижения груза
Общий вид КБ..dwg

Ось вращения поворотной части
Грузовая характеристика
Размещение механизмов на поворотной платформе М 1:100
Схема запасовки грузового каната
Схема запасовки каната стрелового расчала
Тележка(Спецификация).dwg

Механизм передвижения крана 405.dwg

и оси крепления шкворня 0
Неуказанные предельные отклонения размеров
вала по h11 отверстий по H11 угловых
+AT 112 остальных +JT 112
клещевого противоугонного
Лебедка грузоподьемная (Спецификация).dwg

Механизм подъема груза.doc
1 Определение КПД полиспаста и подбор каната
Определяем кратность грузового полиспаста:
- количество ветвей каната на которых подвешено грузозахватное устройство. =2;
- количество ветвей каната наматываемых на барабан. =1.
КПД полиспаста при кратности не более 4-х определяется:
u-кратность полиспаста.
При наличии в системе подвески груза обводных блоков общий КПД будет равен:
- количество обводных блоков. =3.
Механизм подъема груза должен рассчитываться на действие нормативной (т) и случайной составляющей (т) массы груза определяемой по формуле:
- коэффициент принимаемый в зависимости от грузоподъемности и режима работы крана. =005.
Тогда расчетная грузоподъемность (т) составит:
Масса крюковой подвески (т) вычислим по формуле:
Расчёт стальных канатов на прочность производится согласно правилам Ростехнадзора. Максимальное усилие в ветви каната (кН) наматываемого на барабан:
где расчетная грузоподъемность т;
g – ускорение свободного падения мс2;
Необходимое минимальное разрывное усилие в канате усилие (кН):
где коэффициент использования каната определяемый в зависимости от группы классификации механизма по ИСО 43011
Диаметр и маркировочную группу каната выбираем в зависимости от разрывного усилия.
Условное обозначение стального каната: 13-Г-I-H-1568 ГОСТ 2688-80
(мм) – диаметр каната;
I – обозначение марки стали проволоки;
Н – нераскручивающийся правой свивки прядей;
68 – маркировочная группа (временное сопротивление разрыву одной проволоки) МПа по которой взят диаметр каната и разрывное усилие;
Фактический коэффициент использования каната:
где табличное значение разрывного усилия в канате принятое по стандарту при данной маркировочной группе. =8125 кН.
2 Определение геометрических размеров барабана
Минимальный диаметр барабана:
Диаметр уравнительного блока:
где коэффициенты выбора диаметров; ; ; .
d –диаметр каната мм.
Длина барабана будет завесить от длины наматываемого каната и его конструкции.
Длина наматываемого на барабан каната (м) определяется по следующей формуле:
где H – высота подъема груза м.
Число слоёв навивки каната на барабан m=2. При навивки каната в несколько слоёв барабан принимаем гладким.
Количество рабочих витков:
где число слоёв навивки каната на барабан;
коэффициент не плотности навивки каната.
Для гладких барабанов коэффициент не плотности находится в пределах от 09 до 095.
где число запасных витков от 15 до 2 витков. ;
Число витков каната находящихся под зажимным устройством от 3 до 4 витков. ;
Длину гладкого барабана определяем по следующей формуле:
Конструктивно соотношение между длиной барабана и его диаметром должно находиться в пределах:
Гладкие барабаны выполняют с ребордами диаметр которых равен:
3 Расчёт и выбор электродвигателя
Необходимая статическая мощность электродвигателя при подъеме номинального груза:
где скорость подъёма груза ммин;
КПД лебедки определяется по формуле:
где - КПД редуктора. =085.
Выбираю электродвигатель марки МТF 312-6:
Мощность при ПВ 15%
Максимальный момент
Момент инерции ротора
Габаритные размеры электродвигателя марки МТF 312-6:
Высота оси ротора = 180(мм);
Радиус корпуса двигателя =176 (мм);
Диаметр конца выходного вала =50(мм);
4 Кинематический расчёт лебёдки подбор редуктора
Частоту вращения барабана определяем по среднему диаметру навивки каната:
Необходимое расчётное передаточное число редуктора:
- частота вращения вала электродвигателя.
Для механизма подъема груза расчётное значение мощности на быстроходном валу редуктора определим по формуле:
где коэффициент нагрузки.
Для уменьшения габаритов лебёдки барабан и электродвигатель располагают по одну сторону от редуктора. Зная габаритные размеры барабана и электродвигателя необходимо провести их компоновку – проверить возможность размещения их на раме лебёдки по одну сторону редуктора. Расположение их на раме должно удовлетворять следующему условию:
где межосевое расстояние редуктора;
диаметр гладкого барабана по ребордам;
радиус корпуса электродвигателя;
минимальный зазор между ребордой барабана и корпусом электродвигателя
По каталогу выбираем редуктор типа Ц2 соответствующего исполнения по требуемому передаточному синхронной частоте вращения выбранного вала двигателя режиму работы и мощности двигателя межосевому расстоянию входного и выходного валов.
После выбора редуктора определяем фактическую скорость подъема груза при действительном передаточном числе выбранного редуктора:
Отклонение скорости подъема груза от заданной:
В электрореверсивных лебёдках соединение вала двигателя с валом редуктора осуществляется упругой муфтой одна из полумуфт которой играет роль тормозного шкива. Чаще всего применяют муфты типа МУВП (муфта упругая втулочно – пальцевая). Для соединения барабана с редуктором применяют зубчатые муфты при этом выходной конец тихоходного вала редуктора является опорой для барабана.
Муфты выбираются по наибольшему расчётному крутящему моменту который для муфты устанавливаемой между редуктором и двигателем определяется по формуле:
где коэффициент учитывающий степень ответственности механизма для механизма подъёма груза
коэффициент учитывающий режим работы
Для зубчатой муфты устанавливаемой между редуктором и барабаном:
По каталогу выбираем муфту МУВП-2:
Наибольший передаваемый момент
Диаметр тормозного шкива =300(мм);
Ширина тормозного шкива =145(мм);
Масса муфты =60(кг);
Момент инерции муфты
Размеры зубчатой муфты тихоходного вала:
Диаметр начальной окружности =320(мм);
Размер посадочного места под подшипник оси барабана:
6 Подбор и расчёт тормоза
В электрореверсивных лебёдках устанавливаются нормально замкнутые колодочные тормоза замыкаемые усилием пружины и размыкаемые электромагнитом или гидротолкателем. Расчётный тормозной момент в соответствии с рекомендациями Ростехнадзора РФ равен:
где коэффициент запаса торможения .
статический тормозной момент от веса номинального груза приведённый к валу электродвигателя:
Зная расчётный тормозной момент по каталогу выбираем тормоз типа ТКТГ-300М с электрогидравлическим толкателем с максимальным тормозным моментом
Диаметр тормозного шкива
Ширина тормозного шкива =145 (мм);
Высота центра шкива =240(мм);
Работоспособность тормоза будет долговечной если удельное давление фрикционных накладок будет меньше допустимого:
где нормальное давление колодки на шкив Н;
площадь фрикционной накладки мм2;
допустимое удельное давление передаваемое колодкой на шкив.
где коэффициент трения между колодкой и шкивом
диаметр тормозного шкива;
где угол обхвата шкива тормозными колодками;
ширина тормозных накладок
7 Проверка двигателя и тормоза по моменту
Выбранный двигатель необходимо проверить по моменту. Условие правильности его выбора:
где -коэффициент перегрузки для механизма подъёма груза
коэффициент условия работы;
где коэффициент ответственности принимаемый в зависимости от класса ответственности механизма и элемента при втором классе ответственности механизма и элемента.
коэффициент учитывающий условия работы для электродвигателей механизмов подъёма
- максимальный момент развиваемый электродвигателем принимаемый по каталогу.
максимальный статический момент двигателя.
Условие правильности выбранного тормоза по моменту аналогично запишется в следующем виде:
- максимальный тормозной момент развиваемый тормозом принимаемый по каталогу;
К - коэффициент перегрузки при проверке тормозов определяем по формуле:
где коэффициент надёжности для II класса ответственности механизма и элемента
коэффициент изменчивости:
8 Расчёт времени пуска и торможения механизма.
Для выбранного двигателя необходимо определить время пуска при подъеме номинального груза. Оно должно удовлетворять рекомендуемым значениям для данного механизма. При малых его значениях возрастает ускорение при подъёме груза и динамические нагрузки а при больших – перегрев двигателя так как по его обмотке длительное будет протекать большой пусковой ток.
Среднее время пуска при подъёме номинального груза:
где момент инерции всех вращающихся и поступательно движущихся масс механизма приведенных к валу двигателя:
где коэффициент учитывающий приведенное значение моментов инерции вращающихся деталей редуктора и барабана
момент инерции ротора двигателя и муфты с тормозным шкивом значения которых принимаются по каталогу;
- номинальная частота вращения ротора двигателя:
- средний пусковой момент развиваемый электродвигателем:
где - максимальный момент развиваемый двигателем;
- номинальный момент развиваемый двигателем:
Среднее ускорение при пуске двигателя:
Необходимо применение пуско – регулирующих устройств.
Среднее время пуска при опускании номинального груза:
Время торможения при опускании номинального груза:
где - тормозной момент на который отрегулирован тормоз;
- статический тормозной момент от веса номинального груза приведенный к валу электродвигателя.
Путь торможения груза механизма подъёма:
Допускаемы путь торможения принимается в зависимости от режима работы механизма:
9 Расчёт барабана на прочность
При подъёме груза барабан испытывает сложное напряженное состояние. От усилия в канате стенка барабана сжимается подвергается изгибу и кручению. Основными деформациями являются деформации сжатия. Основным материалом для изготовления барабанов является серый чугун СЧ-15.
Минимальная толщина стенки барабана из расчёта на сжатие:
где - максимальное усилие в канате;
допускаемое напряжение на сжатие;
коэффициент учитывающий повышение напряжения сжатия в стенки барабана в зависимости от слоёв навивки каната на барабан. Так как то
Допускаемое напряжение для чугуна:
где =650 МПа – предел прочности для чугуна на сжатие.
Для чугунных барабанов исходя из требований технологии отливки минимальная толщина стенки должна быть не менее:
Определим напряжения на сжатие:
Окончательно принимаю толщину стенки барабана
10 Расчёт крепления каната к барабану
Натяжение каната в месте крепления на барабане будет меньше чем усилие в канате из-за наличия 15 2 запасных витков и определиться по теории Л.Эйлера:
где коэффициент трения между канатом и барабаном
угол обхвата барабана запасными витками
При креплении конца каната на барабане накладкой сила растягивающая один болт:
где - число болтов; =2.
- приведенный коэффициент трения между канатом и накладкой с трапециидальным сечением канавки.
где - угол наклона боковой грани канавки;
Сила изгибающая болт:
Суммарное напряжение в каждом болте:
где коэффициент запаса надёжности крепления каната
– коэффициент учитывающий напряжения кручения при затяжке болтов;
расстояние от головки болта до барабана;
внутренний диаметр резьбы болта;
допускаемое напряжение на растяжение материала болта
Материал болтов – сталь Ст3
11 Расчёт оси барабана и подбор подшипников
Передача крутящего момента от редуктора на барабан может быть выполнена принципиально по различным схемам. Однако наиболее надёжна и совершенна схема механизма у которой выходной вал редуктора соединён с барабаном зубчатой муфтой. Конец выходного вала редуктора в этом случае выполняется в виде зубчатого диска во внутреннюю полость которого устанавливается подшипник оси барабана. Передача крутящего момента от редуктора происходит в этом случае непосредственно через зубчатый венец на барабан вращающийся на оси. Второй опорой оси барабана является кронштейн устанавливаемый на раме лебёдки. Возможные перекосы при монтаже лебёдки компенсируются установкой сферических подшипников качения.
Определим диаметр оси барабана:
где максимальный изгибающий момент
допускаемое напряжение при приближённом расчёте (для обеспечения достаточной жёсткости оси как условия нормальной работы подшипников принимают ).
где - максимальная радиальная нагрузка на подшипник;
расстояние от опоры барабана до внутреннего края реборды барабана;
Подшипники оси барабана подбираем по динамической грузоподъёмности пользуясь следующей эмпирической зависимостью:
для шариковых подшипников;
эквивалентная нагрузка кН;
где минимальная и максимальная радиальная нагрузка на подшипник кН.
где - частота вращения барабана;
- номинальная долговечность подшипника;
Условие подбора подшипника:
Марка подшипника сферический двухрядный радиальный Тип – 1316
Динамическая грузоподьемерсть884 кН
Статическая грузоподъемность 42 кН
Рекомендуемые чертежи
- 25.10.2022