Конвейер скребковый (бревнотаска)


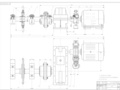
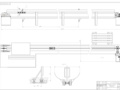
- Добавлен: 25.10.2022
- Размер: 1 MB
- Закачек: 1
Описание
Состав проекта
![]() |
![]() ![]() ![]() ![]() |
![]() |
![]() ![]() ![]() |
![]() |
![]() ![]() |
![]() ![]() |
![]() ![]() ![]() ![]() |
![]() ![]() ![]() |
Дополнительная информация
Бревнотаска.dwg

Курсач по Бревнотаска.docx
1 Назначение область применения и общее устройство 5
2 Составные части и элементы пластинчатого конвейера .8
Патентно-технический анализ .. 9
Выбор и расчет параметров конвейера . ..17
Тяговый расчет конвейера .19
Определение мощности и расчёт привода 20
1 Выбор двигателя 20
2 Определение расчетного натяжения тягового элемента 21
3 Выбор редуктора 22
5 Расчет приводного вала ..22
6 Расчет натяжного устройства . 24
Устройства безопасности ..25
Техника безопасности при работе на конвейере 26
Смазка механизмов ..28
Задачей данной работы является разработка транспортирующего конструкторского изделия которое бы могло при относительной простоте своей конструкции и сравнительной дешевизне перемещать бревна предназначенные для дальнейшей отделки на деревообрабатывающих фабриках в специальные накопители. Процесс осуществления транспортирования должен быть непрерывным в течение рабочей смены. То есть машина которую я собираюсь разработать в этом проекте не должна прерывать перемещение материала не понижая при этом своей производительности.
Такие машины как скребковые конвейеры который я взял за аналог так как они обладают необходимыми для моего задания преимуществами широко используются в промышленности.
Сегодня производством конвейеров занимаются большое количество фирм. Не только в России и Беларуси но и в других развитых странах.
ОБЩИЕ СВЕДИНЬЯ О КОНВЕЙЕРЕ
1Назначение область применения и общее устройство
Скребковый конвейер служит для непрерывного транспортирования насыпных и штучных грузов по трассе расположенной в горизонтальной плоскости или (при специальном исполнении) в пространстве.
Тяговым элементом конвейера с высокими скребками служат обычно одна или две пластинчатые катковые цепи типа 4 по ГОСТ 588-81 с шагом 160 200 250 315 и 400 мм.
Рис. 5. Тяговые цепи:
а - втулочная; б - втулочная с роликом; в - тоже с опорным колесом
Основными недостатками пластинчатых цепей являются загрязнение втулок и катков и прекращение их работы в условиях сильного загрязнения. Это приводит к увеличению натяжения цепи и ее ускоренному изнашиванию. Поэтому имеются попытки использования специальных бескат-ковых цепей. Однако качественно изготовленная пластинчатая цепь с термически обработанными деталями и надежной защитой подшипников катков и направляющих путей будет более долговечной чем бескатковая цепь.
В одноцепном вертикально замкнутом конвейере тяговая цепь располагается посередине ширины скребка над ним или редко под ним. Ходовая часть конвейера перемещается при скольжении цепи со скребками по желобу скольжении накладок-ползунов по желобу или боковым направляющим путям или при качении катков цепи по направляющим путям. У двухцепного конвейера тяговые цепи располагаются по бокам скребков и движутся как правило на катках по боковым направляющим путям. Движение ходовой части на катках наиболее предпочтительно. Оно является важным преимуществом конвейеров с высокими скребками по сравнению с конвейерами других типов у которых цепь и скребки скользят по желобу или трубе конвейера.
Выбор числа тяговых цепей (одной или двух) обусловливается необходимым тяговым усилием шириной скребка (определяющей производительность конвейера) и потребной длиной конвейера а главное — устойчивостью положения скребка. Поэтому для скребков шириной до 400 мм применяют одну тяговую цепь при большей ширине — две цепи.
Недостатком одноцепных конвейеров (особенно при узких скребках) является неудобство загрузки (при верхнем положении цепи) или разгрузки (при нижнем положении цепи) желоба конвейера потому что цепь располагается посередине желоба. Двухцепные конвейеры и одноцепные горизонтально замкнутые конвейеры с консольными скребками этого недостатка не имеют.
Скребки выполняют трапецеидальной полукруглой или прямоугольной (одинарные или двойные) формы; последние необходимы для конвейеров с двумя рабочими ветвями. Изготовляют скребки из листовой стали толщиной 3 — 8 мм для жесткости их укрепляют ребрами. Известно изготовление полукруглых скребков небольшой ширины (до 320 мм) из пластмассы (нейлона). Одинарные скребки имеют консольное а двойные — симметричное крепление к тяговым цепям. Ширина плоских скребков составляет до 650 мм включительно а ящичных 500—1200 мм. Высоту скребка обычно принимают в 2 — 3 раза меньшей их ширины (большие цифры относятся к большей ширине). При значительном увеличении высоты скребка возрастает расчетная площадь сечения желоба но и повышается консольная нагрузка на скребки и цепь что нецелесообразно.
Шаг скребков определяется в зависимости от кусковатости и угла естественного откоса транспортируемого груза высоты скребка и шага цепи. Для кусковых грузов шаг скребков должен быть больше размера наибольшего куска груза. Для остальных грузов выбранный шаг скребков должен обеспечивать наибольшее заполнение пространства между скребками. Обычно принимают шаг скребков ас равным двум шагам цепи (320 — 800 мм) или ас = (2 4)hс где hс — высота скребка.
Желоб конвейера изготовляют сварным или штампованным из листовой стали толщиной 4 — 6 мм прямоугольного трапецеидального или полукруглого (по форме скребка) сечения. При транспортировании абразивных грузов для повышения срока службы дно желоба футеруют износостойким покрытием например каменными плитами (из базальта). Для транспортирования легких грузов (опилок зерна и т. п.) а также грузов вызывающих коррозию металла (например поваренной соли) желоба делают иногда деревянными. Желоб собирают по секциям длиной 3 — 6 м; зазор между скребком и желобом принимают равным 5 — 15 мм на сторону.
Привод — редукторный устанавливается на концевой звездочке. В передаточный механизм привода особенно для конвейеров среднего и тяжелого типов целесообразно устанавливать предохранительное устройство (срезной штифт) или муфту предельного момента для предохранения конвейера от поломок при случайных перегрузках.
Натяжное устройство — винтовое или пружинно-винтовое; его ход не менее 16 шага цепи. В конвейерах с высокими скребками натяжное устройство помимо обычного назначения обеспечивает устойчивое положение скребков (исключает возможность их опрокидывания из-за консольного приложения нагрузки) за счет увеличенного первоначального натяжения.
Станину конвейера изготовляют из прокатных профилей по секциям длиной 3 — 6 м. В отдельных конструкциях кожух делают в виде несущего каркаса закрывающего цепь и желоб.
Рис. 1. Скребковый конвейер.
Рис.2. Схемы трасс скребковых конвейеров.
а — горизонтальной; б — наклонной; в— горизонтально-наклонной; г и д — сложной комбинированной; е —положение груза на наклонном участке конвейера
2 Составные части и элементы скребкового конвейера
Скребковый конвейер состоит из одной бесконечной пластинчатой длиннозвенной цепи которая огибает установленные по концам конвейера приводные и натяжные звездочки; в пролете между ней цепь опирается роликами на направляющие закрепленные на раме. Ведущие (приводные) звездочки установлены в головной части конвейера. Привод конвейера не отличается от привода ленточных конвейеров и выполняется обычно редукторным иногда — при малых скоростях конвейера — с дополнительной зубчатой передачей к валу ведущих звездочек. Цепи натягиваются винтовым натяжным устройством.
В отличие от ленточных конвейеров в которых работа натяжного устройства заключается в обеспечении передачи тягового усилия трением в скребковых конвейерах тяговое усилие передается зацеплением и работа натяжного устройства заключается только в выборе слабины тягового элемента. Поэтому предварительное натяжение должно быть минимальным (1 2 кН) но не меньше динамического усилия.
К цепям прикрепляется скребок состоящий из металлических пластин (гладких или фигурных штампованных или литых). Конвейер загружается автоматическим устройством разгружается — через сталкивателем. Скорость перемещения рабочих элементов v = 05 1 мс.
Станину конвейера как правило изготовляют из угловой или швеллерной стали (рис. 8). Концевые части выполняют в виде отдельных рам для привода и натяжного устройства а среднюю часть (рис. 8. а) для опоры настила — в виде отдельных секций металлоконструкции длиной по 4 — 6 м. В качестве опорных (направляющих) путей для ходовых катков цепей служат уголки 1 для конвейеров легкого типа и швеллеры или узкоколейные рельсы – для конвейеров тяжелого типа. На криволинейных секциях (рис. 86) над путевыми профилями устанавливают контршины 2. На конвейерах поточной линии у станины средней части и цепи рабочей ветви размещают предохранительные ограждения и сиденья для рабочих.
Рис. 7. Натяжное устройство скребкового конвейера:
а — винтовое; б — пружинно - винтовое
Рис. 8. Металлоконструкция секций станины скребкового конвейера:
а — средней; б — криволинейной
Патентно – технический анализ.
Патентно-информационные исследования проводятся с целью изучения основных направлений и тенденций дальнейшего развития и совершенствования транспортирующих машин их составных частей и отдельных узлов а также методов их расчета и результатов исследований.
Существует огромное количество изобретений которые относятся к конвейерам с бесконечными тяговыми элементами а точнее к пластинчатым конвейерам.
Развитие и совершенствование транспортирующих машин их составных частей и отдельных узлов а также методов их расчета и результатов исследований рассмотрим на основании патентов по данному конвейеру.
Использование: изобретение предназначено для транспортирования распиленной древесины от распилочной машины. Сущность изобретения:цепной конвейер например для транспортирования распиленной древесины от распилочной машины содержит по меньшей мере две смежные параллельно расположенные конвейерные цепи с закрепленными на них скребками для поддержания распиленной древесины при этом скребки закреплены на конвейерных цепях шарнирно с возможностью регулирования ширины конвейера в соответствии с требуемой путем изменения расстояния между конвейерными цепями. Скребок шарнирно закреплен своей центральной частью с образованием V-образного тупого угла при максимальной ширине конвейера и V-образного острого угла при минимальной ширине конвейера с возможностью бесступенчатого регулирования ширины конвейера. Скребки могут быть выполнены в виде цепей или лент или плоских стальных пружин. 3 з.п. ф-лы 8 ил.
Изобретение относится к цепному конвейеру например для транспортировки распиленной древесины от распилочной машины.
Обычный цепной конвейер выполнен по крайней мере из двух смежных конвейерных цепей на которых размещены конвейерные скребки поддерживающие распиленную древесину.
В ранее известных конвейерах эти скребки представляют собой различные плоские стальные пластины длиной равной расстоянию между цепями неподвижно смонтированные поперек верхней части цепи так что они простираются за цепь настолько насколько позволяет ее ширина. Когда цепи расположены смежно плоская стальная пластина точно так же располагается и над второй цепью. Это простая конструкция но при этом максимальная ширина конвейера лишь вдвое превышает его минимальную ширину. При использовании конвейера более широкого чем связка распиленной древесины от которого транспортируются доски перемещаемые с помощью направляющих или ножей к боковым конвейерам расположенными по сторонам основного не может быть обеспечена сила достаточная для выталкивания досок. Последующая доска должна давить на предыдущую в связи с чем они будут беспорядочно падать на боковые конвейеры. Доски будут заклинивать друг друга особенно если они обзолены.
Из авт.св.СССР N54979 известен цепной конвейер для транспортировки распыленной древесины от распилочной машины включающий по меньшей мере две смежные параллельно расположенные конвейерные цепи с неподвижно закрепленными на них скребками для поддержания распиленной древесины.
Однако этот конвейер не решает вышеуказанных проблем.
Техническим результатом изобретения является создание цепного конвейера для транспортировки распиленной древесины от распиленной машины имеющего регулируемую ширину.
Этот технический результат достигается тем что в цепном конвейере например для транспортировки распиленной древесины от распиленной машины включающем по меньшей мере две смежные параллельно расположенные конвейерные цепи с закрепленными на них скребками для поддержания распиленной древесины согласно изобретению скребки закреплены на конвейерных цепях шарнирно с возможностью регулирования ширины конвейера в соответствии с требуемой путем изменения расстояния между конвейерными цепями.
Система в соответствии с изобретением отделяет верхние доски от основного потока сбрасывая их в сторону от конвейера в то время как основной поток продолжает двигаться вперед. Доски удерживаются давлением основного потока с помощью ведущих колес пока они целиком находятся вне распилочной машины.
Целесообразно чтобы скребок был шарнирно закреплен своей центральной частью с образованием V-образного тупого угла при максимальной ширине конвейера и V-образного острого угла при минимальной ширине конвейера с возможностью бесступенчатого регулирования ширины конвейера.
Предпочтительно чтобы конвейер имел установленные с возможностью регулирования ширины конвейера направляющие в которых размещены с возможностью перемещения конвейерные цепи.
Можно также чтобы между конвейерными цепями размещалась направляющая рейка или цепь поддерживающая конвейерные скребки.
Такой цепной конвейер достаточно прост экономичен в производстве и удобен в эксплуатации.
На фиг. 1 изображен вид снизу секции цепного конвейера при максимальной его ширине;
на фиг.2 то же вид сверху;
на фиг.3 то же вид сбоку;
на фиг.4 то же вид снизу при минимальной его ширине; на фиг.5 то же вид сверху секции цепного конвейера на фиг.4; на фиг.6 то же вид сбоку секции цепного конвейера на фиг. 4;
на фиг.7 то же вид сверху на секцию цепного конвейера со скребками выполненными в виде цепей; на фиг.8 то же вид сверху на секцию цепного конвейера со скребками выполненными в виде плоских стальных пружин или лент.
Цепной конвейер например для транспортировки распиленной древесины от распилочной машины выполнен из двух смежных параллельно расположенных конвейерных цепей 1 (фиг.1) с закрепленными на них скребками 2 для поддержания распиленной древесины. Скребки 2 закреплены на цепях 1 шарнирно с возможностью регулирования ширины конвейера в соответствии с требуемой шириной путем изменения расстояния между конвейерными цепями 1.
Скребок 2 шарнирно закреплен своей центральной частью с образованием V-образного тупого угла при максимальной ширине конвейера как показано на фиг. 1-3 или V-образного острого угла при минимальной ширине конвейера как показано на фиг.4-6. Таким образом обеспечивается бесступенчатое регулирование ширины цепного конвейера.
Конвейерные цепи 1 размещены в направляющих 3 с возможностью перемещения в них. Направляющие 3 установлены с возможностью регулирования ширины конвейера. Между конвейерными цепями 1 размещена направляющая рейка 4 или цепь поддерживающая скребки 2. Последние могут быть выполнены в виде цепей 5 (фиг.7) или лент 6 (фиг.8) или плоских стальных пружин.
Цепной конвейер например для транспортировки распиленной древесины от распилочной машины включающий по меньшей мере две смежные параллельно расположенные конвейерные цепи с закрепленными на них скребками для поддержания распиленной древесины отличающийся тем что скребки закреплены на конвейерных цепях шарнирно с возможностью регулирования ширины конвейера в соответствии с требуемой путем изменения расстояния между конвейерными цепями.
Конвейер по п. 1 отличающийся тем что скребок шарнирно закреплен своей центральной частью с образованием V-образного тупого угла при максимальной ширине конвейера и V-образного острого угла при минимальной ширине конвейера с возможностью бесступенчатого регулирования ширины конвейера.
Конвейер по п. 1 или 2 отличающийся тем что он имеет установленные с возможностью регулирования ширины конвейера направляющие в которых размещены с возможностью перемещения конвейерные цепи.
Конвейер по любому из пп.1 3 отличающийся тем что он имеет размещенную между конвейерными цепями направляющую рейку или цепь поддерживающую конвейерные скребки.
ВЫБОР И РАСЧЕТ ПАРАМЕТРОВ КОНВЕЙЕРА
Транспортируемый груз – древесные бревна после раскряжевки максимальные размеры бревен – DxL = 800x8000 мм производительность – 360 штчас.
Разгрузка –сталкиванием;
Геометрические параметры трассы:
L=180 м – длина рабочей или холостой ветви.
Рисунок 2.1 – Схема конвейера
Тип конвейера выбираем в зависимости от его назначения. В соответствии с заданной схемой трассы расстояний и условий транспортирования рода и параметров транспортируемого груза производительности принимаем скорость транспортирования из диапазона =02 1 мс .
Основываясь на опыте использования конвейеров для транспортирования бревен принимаю конвейер скребковый.
Диаметр желоба принимаю равным 1м изходя из того что бревна могут оказаться разной величины и некоторые могут дойти диаметром до 1м. :
В качестве тягового органа предварительно принимаем пластинчатую катковую без реборд на катках (тип 3) разборные цепи со сплошными валиками (исполнение 2) и разрушающей нагрузкой Fразр=315 кН. Номер цепи – М315 обозначение цепи:
Цепь тяговая М315 ГОСТ 588–74.
Вес цепи на один метр равен q0 = 2378 кг шаг цепи t=200 мм.
Принимаем расстояние между скребками на конвейере a0 при максимальной длине бревна 8 м :
Из практики известно что бревна поступающие на конвейер редко имеют максимальную величину и доходят до 8 м. В основном средняя длина бревна примерно равна 6 м.
a1 = 6м – средняя длина бревна.
ρ=065 гсм3=650 кгм3.
Объем бревна находим с условием что средний диаметр бревен будет равен 05 м а средняя длина равна 6 м:
Линейная сила тяжести груза:
ТЯГОВЫЙ РАСЧЕТ КОНВЕЙЕРА
Тяговый расчёт конвейера выполняем методом обхода точек по контуру
Рисунок 4.1 – Схема трассы для расчета конвейера
Цепь движется на катках по двум швеллерам следовательно на колесики действует сопротивление качения. Принимаю коэффициент сопротивления качению равный = 004 [2].
Коэффициент сопротивления при огибании отклоняющих устройств: k1=108 при угле перегиба 1800 .[2 стр. 176]
Обходим трассу от точки 1 по направлению движения цепи.
Принимаем наименьшее натяжение цепей в точке их сбегания с приводных звездочек Smin=S1=3000Н.[2 стр.175]
Wц = q0. · L ·g = 2378 10 ·180 ·004 = 171216 Н.
Где Wц – сопротивление движению цепи по швеллерам g – ускорение свободного падения.
Натяжение в первой расчетной точке:
Натяжение в точке 2:
S2 = S1 + Wц =3000 + 171216 = 4712 Н.
Натяжение в точке 3:
S3 = k1 · S2 = 108 · 4712 = 5089 Н.
Натяжение в точке 4:
S4 = Smax = S3 + Wц + Fтр = S3 + Wц +mg fтр · n= 5089 + 171216 + 76710 02·18= 5089 + 171212 + 27612 = 34413 Н.
Где Fтр – сила трения бревен о желоб fтр – коэффициент трения дерева о сталь (fтр = 02) n – среднее число бревен помещающихся на транспортирующем устройстве (n = 18).
Рисунок 4.2 Диаграмма натяжения тягового элемента.
Определение мощности и расчёт привода
Тяговое усилие на приводных звездочках
W0 = Sнб – Sсб = S4 - S1 =
=34413-3000= 31413 Н
При коэффициенте запаса kз=115 и КПД привода 0=08 мощность двигателя [2]:
По полученному значению мощности выбираем АИР250M8 с мощностью N = 45 кВт и частотой вращения n = 750 обмин [7].
2 Определение расчетного натяжения тягового элемента
Принимаем тяговый элемент состоящий пластинчатой цепи с шагом t= 200 мм = 02 м; приводную звездочку с числом зубьев z0=8.
Вычисляем динамическое усилие:
где Ки – коэффициент учитывающий интерференцию упругих волн Ки=033 [2 стр. 49];
k’ – коэффициент участия в колебательном процессе массы перемещаемого груза k’=1 при 200;
k” – коэффициент участия в колебательном процессе массы ходовой части конвейера k”=05 при Lобщ=360 м
где L – длина контура тягового элемента Lобщ.=2*L=360м;
mг – масса груза находящегося на конвейере mг = m·n =767·18 = 13806 кг;
mх.ч. – масса ходовой части конвейера mх.ч = q0·Lобщ =2378 ·360 = 4280 кг.
Расчетное натяжение тягового элемента при установившемся движении:
Sрасч = Smax+ Sдин = 34413+16230=50643 Н
Разрывающая нагрузка выбранной цепи Qр.в.=315 кН.
Запас прочности цепи:
kз= Qр.в Sрасч.ц = 31500054086 =62 > [6..10].
т.е. выбранная цепь удовлетворяет условиям
Частота вращения приводного вала конвейера [2 стр. 93]:
Передаточное число привода:
Выбираем редуктор Ц2-500 имеющий передаточное число uр = 1988 с мощностью на быстроходном валу Nр = 587 кВт при частоте вращения этого вала nб=750 обмин.
Выбор соединительной муфты производим по расчётному моменту муфты [2]:
T = W · D2 = 31413·052 =7853 Н·м
k – коэффициент условий работы =2 [2] D –диаметр звездочки;
D = z0·t = 8·02314=05;
Тр = 2 · 7853 = 15702 Н·м
По ГОСТ 5006–83 принимаем зубчатую муфту передающую наибольший крутящий момент 19000 Н·м.
5 Расчет приводного вала
Крутящий момент определяется (рисунок 5.1) по формуле
Изгибающий момент определяется по формуле:
где L2 = L12 L1 – длина вала на котором закреплена звездочка конструктивный размер L1=04 м L2 = 02 м.
Рисунок 5.1 Схема для расчета приводного вала.
Результирующий момент определяется по формуле [7 стр. 19]:
Валы изготавливаю из стали 45 с пределом выносливости -1 =250 МПа
Диаметр вала определяется по следующему выражению [4 стр.68]:
Принимаю диаметр в опасном сечении 50 мм.
6 Расчет натяжного устройства
Из конструктивных соображений устанавливаю на свой скребковый конвейер винтовое натяжное устройство.
Для цепных конвейеров у которых удлинение цепи может быть незначительным ход натяжного устройства должен быть на 50 – 100 мм больше длины половины секции цепи чтобы можно было при большом износе уменьшить длину цепи на одну секцию (секцией цепи называют два парных звена с прямыми пластинами).
Следовательно ход винтового натяжного устройства для данного конвейера составит хр = 250 мм.
Натяжное усилии Рн необходимое для перемещения подвижного поворотного устройства определяется по формуле [2 – 2.18]:
где Т – усилие перемещения натяжной тележки т.к. оно не значительно этим усилием пренебрегаем.
Усилие прилагаемое для вращения винта [2 – 2.19]:
где kв.т =1 – коэффициент распределения усилия между натяжными винтами d1 – средний диаметр резьбы винта в = 4– угол подъема винтовой линии = 6 приведенный угол трения =025 коэффициент трения в торце упорной поверхности гайки или головки винта d2 =14·d1 – средний диаметр опорной поверхности гайки или головки винта.
УСТРОЙСТВА БЕЗОПАСНОСТИ.
Вопросам техники безопасности при проектировании и эксплуатации транспортирующих машин уделяется большое внимание. На всех стадиях создания машины – от проектирования монтажа и до постоянной эксплуатации – закладываются условия её безопасной работы и обслуживания.
Общие требования безопасности при проектировании конвейеров регламентированы ГОСТ 12.2.022 -80. Они включают требования к конструкции (по назначению конвейера особенностям транспортируемых грузов и безопасности эксплуатации) устройствам средств защиты (защитным ограждениям блокировкам сигнализации) и размещению конвейеров в производственном помещении (устройству проходов переходов для обслуживания и т.п.). Требования к электрооборудованию регламентированы «Правилами устройства электроустановок».
Безопасность при эксплуатации машин определяется соответствующими правилами эксплуатации и подробным инструктажем рабочих и обслуживающегося персонала.
ТЕХНИКА БЕЗОПАСТНОСТИ ПРИ РАБОТЕ НА КОНВЕЙЕРЕ
К эксплуатации конвейера допускаются лица не моложе 18 лет.
Перед началом работы необходимо проверить техническое состояние основных механизмов и узлов.
Также необходимо проверить техническое состояние и исправность устройств безопасности рассмотренных ранее.
Все машины непрерывного транспорта сменные элементы и сменные приспособления должны быть изготовлены в полном соответствии с настоящими правилами и стандартами.
Электрическое оборудование машин его монтаж и демонтаж токопровод и заземление должны отвечать правилам устройства электроустановок.
Металлоконструкции и металлические детали конвейеров должны быть предохранены от коррозии.
К механизмам предохранительным устройствам электрооборудованию требующим постоянного технического обслуживания а также для осмотра металлоконструкции конвейера должен быть обеспечен безопасный доступ. Машины непрерывного транспорта с электрическим приводом должны быть оборудованы устройствами для автоматической остановки.
Легкодоступные находящиеся в движении части конвейера которые могут быть причиной несчастного случая должны быть закрыты прочно укрепленными металлическими заграждениями допускающими удобный осмотр и смазку.
Одним из условии бесперебойной работы конвейеров является правильная организация их работы. В целях предотвращения неожиданного и преждевременного выхода конвейеров из строя эти мероприятия проводятся по плану. Системой предусматривается межремонтное обслуживание и ремонт конвейеров: малый средний капитальный. Межремонтное обслуживание – наблюдение регулировочные работы и устранение мелких неисправностей. Нормальное в том числе и безопасная эксплуатация конвейеров обеспечивается при условии что износ деталей не превышает некоторых предельных величин.
На работоспособность и надежность деталей КПД конвейерных механизмов и соответственно на расход электроэнергии при эксплуатации конвейеров большое влияние оказывает выбор и режим смазки которое кроме уменьшения трения предохраняет также от коррозии попадания во взаимодействующие поверхности абразивных пылевидных частиц уплотняет зазоры отводит тепло от трущихся поверхностей.
Смазка конвейера осуществляется согласно технологической карты.
В конвейерах смазываются зубчатые передачи и зацепления подшипники качения шарниры (тормозов и систем управления).
При унификации режимов смазки и материалов должен обеспечиваться минимальный ассортимент применяемых марок а также возможность большей длительности периодов между смазочными операциями и очистки смазочных систем.
Из систем смазки наиболее прогрессивной является централизованная однако для некоторых элементов целесообразно применение индивидуальной ручной смазки.
Смазка редукторов производится автотракторным маслом АКЗп-6 или другими близкими по свойствам по ГОСТ 1862-63.
Зубчатые муфты по рекомендации ГОСТ 50006-83 заполняют следующими смазочными материалами в зависимости от окружающей температуры: ТСп-10 МТ-8п ИПП-200.
При систематическом обслуживании осуществляется доливка масла в редуктора до требуемого уровня. Подшипники качения смазываются через масленки.
Стандартизация – это деятельность заключающееся в нахождении решений для повторяющихся задач в сфере науки техники и экономики направленная на достижение оптимальной степени упорядочения в определенной области.
В зависимости от сферы действия Государственный комитет по стандартизации предусматривает следующие категории стандартов: государственные отраслевые стандарты предприятия.
При выполнении графической части использовались ГОСТы ЕСКД.
При выполнении курсового проекта использовались следующие стандарты и ГОСТы:
ГОСТ 588-81 – Цепи тяговые пластинчатые.
ГОСТ 22281-76 – Настил пластинчатых конвейеров.
ГОСТ 4366-76 - Смазка для подшипников.
СТ СЭВ 189-75 – Размеры сечений шпонок и пазов.
ГОСТ 20720-75 – Муфты зубчатые МЗ.
ГОСТ 21424-75 – Муфты втулочно-пальцевые типа МУВП.
ГОСТ 19523-81 – Электродвигатели асинхронные типа 4А.
ГОСТ 5720-75 – Подшипники роликовые радиальные сферические двухрядные.
ГОСТ 5721-75 – Подшипники шариковые радиальные сферические двухрядные.
В данном курсовом проекте была разработана модель пластинчатого конвейера с промежуточной разгрузкой - сталкиватилем по заданными техническими параметрами.
Конвейер включает четыре основные части: тяговый элемент желоб привод и натяжное устройство.
В данном курсовом проекте имеется графический материал представленный следующими листами: общий вид конвейера в трех проекциях; сборочный чертеж привода и третьего листа на котором представлена усовершенствованная конструкция составной части. Пояснительная записка включает все пункты указанные в содержании.
Все стандартные и покупные изделия были выбраны в соответствии с ГОСТом.
Конвейер полностью отвечает техническим нормам эксплуатации и требованиям безопасности и охраны труда.
Кузьмин А.В. Справочник по расчетам механизмов подъемно-
транспортных машин А.В. Кузьмин Ф.Л. Марон. - 2-е изд. перераб. и доп. -
Мн: Выш. щк. 1983. - 350 с.
Спиваковский А.О. Транспортирующие машины: Учеб. пособие для
машиностроительных вузов А.О. Спиваковский В.К. Дьячков. - 3-е изд. перераб. - М.: Машиностроение 1983. - 487 с.
Вайнсон А.А. Подъемно-транспортные машины: Учеб. для вузов. -
-е изд. перераб. и доп. - М.: Машиностроение 1989. - 536 с. .
Иванченко Ф.К. Расчеты грузоподъемных и транспортирующих ма
шин. - Киев: Вища шк. 1978. - 576 с.
.Иванченко Ф.К. Конструкция и расчет подъемно-транспортных ма
шин.-Киев: Вищашк. 1983. - 351 с.
. Зенков Р.Л. Машины непрерывного транспорта: Учеб. Р.Л. Зенков
Й.И. Ивашков Л.Н. Колобов. - 2-е изд. перераб. и доп. - М.: Машинострое
В.И.Анурьев. «Справочник Конструктора Машиностроителя в 3 томах». Т.3 Издательство Москва «Машиностроение» 2001г.
Привод Бревнотаски.dwg

* Размеры для справок
Остальные технические требования
спецификация к бревнотаске.doc
Стандартные изделия
Шпонка ГОСТ 23360-78
КС-120. 00. 00. 000 ВО