Дизель-молот




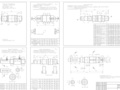
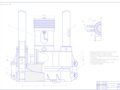
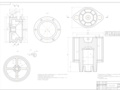
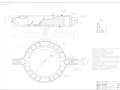
- Добавлен: 25.10.2022
- Размер: 2 MB
- Закачек: 1
Описание
Состав проекта
![]() |
![]() |
![]() ![]() ![]() ![]() |
![]() ![]() ![]() ![]() |
![]() ![]() ![]() ![]() |
![]() ![]() ![]() ![]() |
![]() ![]() ![]() ![]() |
![]() ![]() ![]() ![]() |
![]() ![]() ![]() ![]() |
![]() ![]() ![]() ![]() |
![]() ![]() ![]() ![]() |
![]() ![]() ![]() ![]() |
![]() ![]() ![]() |
![]() |
![]() |
![]() ![]() |
![]() ![]() |
![]() ![]() |
![]() ![]() |
![]() ![]() |
![]() ![]() |
![]() ![]() |
![]() ![]() |
![]() ![]() |
![]() ![]() |
![]() ![]() |
![]() ![]() |
![]() ![]() |
![]() ![]() |
![]() ![]() |
![]() ![]() |
![]() ![]() |
![]() ![]() |
![]() ![]() |
![]() ![]() |
![]() ![]() |
![]() ![]() ![]() |
![]() ![]() ![]() |
![]() |
![]() ![]() |
![]() ![]() |
![]() ![]() ![]() ![]() |
![]() ![]() |
![]() ![]() ![]() ![]() |
![]() ![]() ![]() ![]() |
![]() ![]() |
![]() ![]() |
![]() ![]() |
![]() ![]() |
![]() ![]() |
![]() ![]() |
![]() ![]() ![]() ![]() |
![]() ![]() ![]() ![]() |
![]() ![]() ![]() ![]() |
![]() ![]() ![]() ![]() |
![]() ![]() ![]() ![]() |
![]() ![]() ![]() ![]() |
![]() ![]() ![]() |
Дополнительная информация
Дизель-молот+.dwg

Копровое оборудование на базе экскаваторв Э-10011+.dwg

Дипломный проект.dwg

Заготовка - штамповка ГКМ
Материал Сталь 45 ГОСТ 1050-74
Неуказанные радиусы R1 2мм
Операция №2 Фрезерно - центровочная
Оборудование: Фрезерно - центровальный
Инструмент: 1) Торцевая фреза
) Центровочное сверло
Приспособление: самоцентрирующие призмы ГОСТ 12197-68
Операция №4 Фрезерная
Оборудование: Шпоночно - фрезерный станок 692М
Инструмент: Фреза концевая
Приспособление: Тисы самоцентрующие 7200-0154
Операция №6 Шлифовальная
Оборудование: Круглошлифовальный станок ЗМ153А
Инструмент: Шлифовальный круг ПП200
Приспособление: Центррифленый ГОСТ 12206-80 хомутик
Операция №3 Токарная
Оборудование: Токарно - винторезный станок 1К62Б
Инструмент: 1) Проходной прямой упорный резец с пластиной из твердого сплава Т15К6 ГОСТ 18878-73
) Подрезной резец ГОСТ 10042-78
Приспособление: Центр ГОСТ 12203-78
Термообработка HRC 34 40
Неуказанные предельные отклонения размеров валов h14
Точить начерно пов. 6
Точить начисто: пов. 1
Точить начерно: пов. 1
Траверса+.dwg

электродами Э42А ГОСТ 9467-75.
Прорези А во втулках выполнить вместе с бобышками
поз. 5 после их приварки.
* размеры для справок.
Болт поз. 2 условно не показан.
Блок поршня+.dwg

электродами типа Э42 А ГОСТ 9467-65.
Свайный наголовник условно не показан.
В сечении А-А серьга поз.11 и палец поз.10 условно
Неуказанные предельные отклонения размеров
по классу точности "средний".
Сварные швы очистить от окалины и шлака.
размеры для справок.
Цилиндр+.dwg

Перекос осей отверстий "В" допускается не более 0
* Размеры для справок.
Предельные отклонения размеров отливки по II кл. точности ГОСТ 2009-55
Форомовочные уклоны по ГОСТ 3212-80
Неуказанные литейные радиусы 5 8 мм
Неуказанные пределньные отклонения размеров остальных
по классу точности "средний".
Отжечь и пескоструить.
Категория ремонтного размера
Шабот+.dwg

точности ГОСТ 2009-55.
Формовочные уклоны по ГОСТ 3212-80.
Неуказанные литейные радиусы 5 8мм.
Отжечь и пескоструить.
К исправлению допускаются одиночные раковины по
наибольшему измерению не более 20мм
Без исправления допускаются раковины в наидольшем
не более 5-ти раковин.
Неуказанные предельные отклонения размеров:
t2 по классу точности.
Обработку по размерам в квадратных скобках
производить совместно с дет.
Наголовник для свай+.dwg

стальным диском толшиной 14 16мм.
Неуказанные предельные отклонения размеров:
t2 по классу точности
Сварные соединения выполнить по ГОСТ 5264-80
электродами Э42А ГОСТ 9467-75.
Сварные швы отчистить от шлака.
размеры для справок.
Дизель-молот СП-6Б+.dwg

Поршень+.dwg

Сварной шов по ГОСТ 5264-80 электродом Э42А ГОСТ 9467-75.
* размеры для справок.
Реферат.doc
Дизель-молот принцип действия классификация конструкция свая технология свайных работ тепловой расчет заготовка маршрут обработки безопасность экологичность стоимость капитальные вложения текущие затраты приведенные затраты экономический эффект.
Дипломный проект посвящен модернизации дизель-молота с целью повышения технико-экономических показателей.
В работе проведен поиск работ с целью выявления технического решения направленного на повышение эффективности работы дизельных молотов.
В стадии технического проекта выполнены чертежи общего вида основных сборочных единиц и др.
Определены основные параметры дизель-молота выполнены необходимые расчеты дизель-молота и расчет технико-экономических показателей.
В технологической части проекта разработана технология изготовления детали.
Рассмотрены вопросы безопасности и экологичности проекта.
Выполнены расчеты экономического эффекта. Ожидаемый годовой экономический эффект на 1 дизель-молот составляет 32290 руб.
Дипломная работа_.doc
2.Перечень работ предшествующих устройству свайного фундамента.
3.Разбивка свайного фундамента.
4.Технология свайных работ.
5.Способы устройства лидерных скважин.
6.Подготовка к бурению лидерных скважин.
9.Сваебойные установки.
10.Погружатели свай.
11.Устройство дизель-молота.
12.Работа дизель-молота.
13.Расчет погружения сваи ударом дизель-молота.
14.Тепловой расчет дизель-молота.
15.Расчет главных размеров цилиндра и его кинематика.
16.Расчет шпоночного соединения.
17.Расчет подшипников.
0.Технологическая часть.
1.Технология изготовления вала.
0.Экономическая часть.
1. Расчет капитальных вложений.
0. Охрана окружающей среды.
0. Безопасность жизнедеятельности.
Список используемой литературы.
Одним из основных направлений экономического и социального развития нашего государства является интенсивное освоение северо-восточных районов страны и непрерывное наращивание их производственного потенциала строительство объектов промышленного гражданского и транспортного назначения которые возводятся преимущественно на свайных фундаментах. Свайные фундаменты относятся к весьма ответственным видам строительных машин. Их надёжность на длительный срок зависит от ряда весьма существенных факторов: качественного выполнения инженерно-геологического измерения строительной площадки; принятого принципа непользования грунта основания; уровня механизации строительного цикла и принятой технологии; соответствия машин и механизмов строительным и технологическим требованиям; профессионального уровня рабочих и инженерно-технических работников ведущих строительство объекта.
До 1963 года погружение свай осуществляется в талые грунты низкочастотный вибропогружатель со сваебойной установкой СКВ-1 (местного изготовления).
В качестве базы машины применялся экскаватор Э-652. В дальнейшем для устройства свайных фундаментов на талых и вечномёрзлых грунтах с более глубоким погружением свай была создана сваебойная установка СКВ-12 на базе экскаватора Э-10011. Низкочастотный вибропогружатель заменён штанговым дизель-молотом С-268 с массой ударной части 25 т.
1. Подготовка строительной площадки.
В подготовку строительной площадки к производству свайных работ входит:
Передача строительной организации заказчиком (генподрядчиком) проектно-технологической документации состоящей из отчёта инженерно-геологического изыскания строительной площадки проекта свайного фундамента разрешения административного органа на строительство объекта.
Снос наземных строений и коммуникаций находящихся в зоне строительной площадки.
Очистка строительной площадки от строительного и прочего мусора снега льда и т. п.
Срезка грунта планировка площадки подсыпка выемка котлована устройство съезда в котлован с уклоном к горизонту не более 15 градусов.
Подвод на строительную площадку электроэнергии с установкой подключающего устройства (рубильника автомата) на номинальную мощность 100 квт.
Установка ограждения (забора) высотой два метра вблизи жилых домов промышленных зданий и сооружений.
Оборудование наружного освещения со степенью освещенности рабочих мест не менее 50 люкс (30 Вт на один квадратный метр рабочего места).
Устройство обноски в соответствии с проектом производства работ (ППР). Нанесение на обноске главных разбивающих осей здания сооружения. Отклонения главных осей от проектного положения не должны превышать одного сантиметра на сто метров ряда.Подготовительную площадку заказчик (генподрядчик) передаёт строительной организации по акту.
2. Перечень работ предшествующих устройству свайного фундамента.
Ознакомление с проектом свайного фундамента и отчётом инженерно-геологического изыскания геологической площадки.
Выбор технологической схемы на способ погружения свай исходя из инженерно-геологического изыскания строительной площадки и принятого проектом способа передачи сваей нагрузки на грунт.
Составление проекта производства работ ППР.
Доставка на строительную площадку сваебойного и бурового оборудования.
Монтаж сваебойной установки наладка контроль технического состояния и готовности к вводу в работу.
Завоз на строительную площадку контрольных (пробных) свай в количестве указанном в проекте свайного фундамента.
Погружение контрольных (пробных) свай забивным или бурозабивным способом в зависимости от мерзлотно-грунтовых условий строительной площадки.
Завоз на строительную площадку проектных или откорректированных свай в полном объёме.
Разметка свай по длине через каждый погонный метр. Нумерация меток наносится красной краской арабскими цифрами начиная от низа (острия) сваи.
3. Разбивка свайного фундамента.
Разбивка свайного фундамента – одна из наиболее ответственных технологических операций которая заключается в переносе положения проектных главных и вспомогательных осей на местность где намечено сооружение свайного фундамента. Точки пересечения осей переносят с помощью теодолита и рулетки и фиксируют инвентарными металлическими штырями. Для переноса проектного положения свай на местность составляется исполнительная схема разбивки свайного поля с указанием всех проектных размеров расположения свай отмеренных от главных осей. По двум взаимно перпендикулярным направлениям пересечения главных осей на расстоянии 10 метров от осей здания выносят контрольные точки устанавливаемые для геодезической привязки на тот случай если будут главные оси сбиты в процессе работы. Для разбивки свайного поля на обноску по длине здания сооружения с помощью теодолита переносятся главные оси здания (свайного поля). Промежуточные оси соответствующие отдельным участкам разбивки свайного поля наносят на обноску при помощи рулетки.
Положение главных и промежуточных осей на обноске закрепляют гвоздями. Между вынесенными на обноску точками осей свайного поля натягивают мягкую проволоку фиксирующую положение переносимых на местность осей здания сооружения. Точки пересечения осей переносят с помощью отвеса на поверхность участка и закрепляют металлическими штырями. Места расположения свай между зафиксированными на местности основными линиями по главным и промежуточным осям разбивают на каждом участке с применением рулетки. Отклонение разбивочных осей свайных рядов от проектных не должно превышать 1 сантиметра на каждые 100 метров ряда. Разбивку свайных рядов оформляют актом к которому прилагают схемы расположения знаков разбивки данные о привязке к базисной линии и к высотной опорной сети.
4. Технология свайных работ.
Устройство свайных фундаментов в сложных мерзлотно-геологических условиях выполняются тремя наиболее приемлемыми и эффективными способами погружения свай: забивным бурозабивным и буроопускным.
Забивной способ погружения непосредственно в целик грунта применяется на талых оттаявших и оттаянных грунтах содержащих в своей массе до 25% крупнообломочных включений (гальки гравия) без валунов.
Бурозабивной способ погружения свай в лидерные скважины применяется на мёрзлых и вечномёрзлых грунтах независимо от содержания в них крупнообломочных включений. На талых и оттаянных грунтах только при наличии в них крупнообломочных включений более 25%.
Буроопускной способ с установкой свай в лидерные скважины под собственным весом применяется в случаях когда устройство свайного фундамента забивным или бурозабивным способом может вызвать деформацию фундамента близко стоящего здания сооружения.
Из применяемых способов погружения свай бурозабивной способ имеет значительное преимущество. Поэтому и подготовка к непосредствен-ному погружению свай начинается с устройства лидерных скважин.
В строительной практике применяются разные способы устройства лидерных скважин например: ударно- канатный при помощи станков УНС-30м БС-1м УКС-22м и др.; ударно- разового и циклического заглубления с помощью модернизированного штангового дизель-молота СП-6Б1М; вращательный – самоходными буровыми машинами СО-2 СБМ и др.; навесными буровыми приводами 2НБП; НБП-90 НБП-10 и др. со сваебойных установок СКВ-12 СБУ-12.
Предпринимались попытки внедрить и другие способы бурения например виброударный и термомеханический однако оба эти способа практического применения не получили. Механизмы изготовляемые для этих целей оказались или непригодными или нецелесообразными. Виброударные установки конструкции ПКБ Главстроймеханизации Минтрансстроя при попытке бурить скважины в мёрзлых грунтах содержащие крупнообломочные включения не выдерживали чрезмерных виброударных нагрузок.
Лидеры сжимались или разрывались пружины вибромолота сварные соединения электродвигатель и другие сложные узлы быстро выходили из строя. Виброударная установка монтировалась на тракторе Т-180. Термомеханический способ бурения не получил признания из-за нецелесообразности его применения так как мог применяться в тех же мерзлотно-грунтовых условиях в которых бурение успешно выполнялось вращательным методом навесными буровыми приводами с более высокой производительностью и меньшими затратами. Оборудование для термомеханического способа бурения устанавливалось на тяжелом дорогостоящем тракторе ДП-250.
Размеры лидерных скважин назначаются по таблицам 12 в зависимос-ти от мерзлотно-грунтовых условий строительной площадки проектной нагрузки на сваю способа передачи сваей нагрузки на грунт. Глубина бурения скважины для свай-стоек принимается равной проектному заглублению.
Параметры лидерных скважин и бурового инструмента.
Для многолетне-мерзлых (вечномёрзлых) грунтов и грунтов с
сезонным промерзанием.
Коэффициент забуривания
Диаметр забурения ммм
Размер квадратной скважины мм
Для талых и оттаянных грунтов при условии наличия в них крупнооб-ломочных включений более 25 %.
Диаметр забурения мм
Глубина проходки лидерных скважин для свай - висячих принимается ссссссс в зависимости от проектной нагрузки на сваю геологического состава грунта и его температурного состояния.
Надёжность свайных фундаментов сооружаемых бурозабивным способом зависит от размера скважин в сечении и по глубине бурения надлежащего контроля за степенью износа бурового инструмента и своевременной его замены. По мере износа забурника и шнека скважины одна за другой уменьшается в диаметре а по глубине приобретают форму усечённого конуса. В процессе погружения (забивки) свай в конусные скважины наступает момент когда погружатель свай например дизель-молот не в состоянии преодолевать сопротивление сваи погружению. В результате свая останавливается недопогруженной до проектной отметки с критическими и ложными отказами. При попытке добить её до проектного заглубления она разрушается в первую очередь в головной части. Разрушенные сваи для добивки становятся непригодными а для фундамента – неполноценными.
6. Подготовка к бурению лидерных скважин.
Навеска бурового привода на мачту сваебойной установки.
Фиксация бурового привода в нижней части мачты копра для подсоединения к нему бурового става (шнека с забурником).
Подсоединение бурового става соответствующего проектному диаметру к буровому приводу посредством форкопа (крестообразного шарнира).
Подъём бурового привода вместе с буровым ставом на высоту равную длине шнека.
Установка копровой мачты в вертикальное положение механизмами выравнивания.
Наведение бурового става на точку бурения механизмами точного координатного наведения.
Установка мачты копра на грунт при помощи опорного механизма.
Пуск в работу бурового привода: бурение скважин на проектную глубину; извлечение шнека из скважины.
Подсоединение к нижней части шнека (вместо забурника) зачистного устройства для зачистки забоя скважины.
Перемещение сваебойной установки к последующему месту бурения.
При бурении последующих скважин очерёдность технологических операций повторяется. Бурение скважин составным или телескопическим шнеком на глубину более шести метров выполняется циклично с очисткой шнека. Результат бурения каждой скважины вносится в журнал бурения. Проходка скважин периодически чередуется с погружением свай в скважины.
По окончании бурения некоторого количества скважин с мачты копра снимается буровой привод и навешивается дизель-молот. Сваебойную установку например СКВ 12 с навешанным молотом перемещают к месту погружения свай – к пробуренным скважинам. К мачте копра подтаскивается свая и стропуется специальной подвешенной рамкой соединённой стропами (цепями) с наголовником дизель-молота. Застропованную сваю вместе с дизель-молотом машинист по команде копровщика поднимает к мачте копра. Поднятая свая благодаря подвешенной рамке занимает отвесное положение. Ходом машины и поворотом платформы машинист подводит сваю (в отвесном положении) к скважине а электромеханическими устройствами координатного наведения – на центр скважины. Установкой молота на сваю заканчивается подготовка к погружению сваи в скважину. По команде копровщика машинист при помощи дистанционного пневматического управления производит зацеп и подъём ударной части молота на высоту 1.3 - 1.5 метра затем сброса ударной части молота запускается в работу молот. Через 5-6 пробных ударов копровщик останавливает молот проверяет положение и состояние погружаемой сваи вновь запускает молот в работу. При достижении сваей заглубления близко к проектному забивка сваи приостанавливается для подготовки к замеру отказа. К свае копровщик приставляет козелок-подставку проверяет соосность дизель-молота со сваей. РИС 1.
Замер отказа сваи проводится тремя залогами: два первых – контрольные выполняются двадцатью ударами по десять ударов в залоге. Фактический остаточный отказ замеряется на третьем залоге тридцатью ударами. Если при первых двух залогах ударная часть молота в рабочем режиме не достигает нормативной высоты ссссссссссс замер отказа на третьем залоге выполняется одиночными ударами с выключенной подачей топлива с высоты сброса ударной части 24 – 22 метра – для штангового дизель-молота и 25-23 метра для трубчатых дизель-молотов. Перед выполнением третьего залога высотное положение сваи фиксируется нанесением на ней риски на уровне козелка-подставки. Вторая фиксирующая риска наносится после десяти последних ударов молота. Промежуток между двумя последними рисками измеряется мерной линейкой с точностью до одного миллиметра и делится на десять последних ударов. Одна десятая часть промежутка между двумя рисками и есть фактический отказ погруженной сваи который заносится в журнал забивки свай.
При погружении свай в сложных мерзлотно-грунтовых условиях фактические отметки заглубления свай не всегда соответствуют проектным. Сваи погружённые на проектные отметки и не давшие расчетного отказа оставляются на «отдых» продолжительность которого зависит от состава и характера прорезных и подстилающих под концами свай грунтов. В песчаных грунтах «отдых; длится трое суток в связных и разнородных грунтах – 6 суток в глинистых грунтах – от 12 до 16 суток. По истечении срока отведённого для «отдыха» проводится повторный (контрольный) замер отказа десятью ударами с высоты сброса 22-24метра одиночными ударами с отключённой подачей топлива. Если и после «отдыха» фактический остаточный отказ по-прежнему превышает расчётный дальнейшие погружения сваи прекращается для выявления причины и принятия решения проектной организацией которая и определяет необходимость проведения статического испытания корректировки проекта свайного фундамента или части его.
Сваи длиной до 10 метров недопогруженные более чем на 15% проектной глубины и сваи большей длины недопогруженные более чем на 10% проектного заглубления дают критический отказ или близкий критическому подвергаются обследованию для выяснения причин и принятия решений о необходимости погружения дублирующих свай. При погружении свай молотом двойного действия продолжительность последнего залога принимается три минуты а отказ определяется как среднее значение глубины погружения сваи от одного удара в течение последней минуты в залоге.
9. Сваебойные установки.
Сваебойная установка СНВ 12 (общий вид) предназначена для погружения в грунт свай длиной: цельных – до 12 метров составных – до 24 метров забивным и бурозабивным способами для проходки лидерных скважин вращательным способом навесным буровым приводом при помощи шнека. Эффективность производства свайных работ во многом зависит от правильности выбора копров и копрового оборудования специальной технологической оснастки и приспособлений обеспечивающих работоспособность установок в любых климатических и грунтовых условиях. Этот выбор должен быть сделан с учётом принятой технологии и сроков производства свайных работ природно-климатических и грунтовых условий конструктивных решений свайных фундаментов и требуемой производительности установок. При выборе и технико-экономическом обосновании количества и конструкций копров в составе комплекта сваебойного оборудования необходимо учитывать требуемую точность и качество погружения свай оптимальную технологию и организацию работ в пределах свайного поля возможность комплексной механизации производства свайных работ в зимних условиях.
В качестве погружателей на копрах используют трубчатые СП-54 СП-47А СП-48 и штанговые СП-6Б СП-60. Создаются как универсальные так и специальные копровые установки предназначенные для выполнения свайных работ при сооружении фундаментов в особых условиях строительства. Основными факторами определяющими выбор копров и свайного оборудования являются: масса и длина погружаемых свай конфигурация свайного поля и расположение свай гидрогеологические условия физико-механические характеристики грунтов толщина мерзлого слоя требуемая точность погружения свай сроки осуществления свайных работ.
Каждая машина предназначенная для производства свайных работ имеет свою область рационального применения. Эффективность использования того или иного типа копров обосновывается сравнением их технико-экономических показателей (стоимость трудоёмкость).
Наиболее рациональной машиной для погружения свай расположенных в один или два ряда являются серийно выпускаемые копры на базе тракторов с боковой навеской оборудования а также мостовые копры. Последние наиболее целесообразно использовать при типовой массовой застройке и выполнении свайных полей прямоугольно формы. Копровое оборудование с подвешенными копровыми мачтами требует обязательного опирания мачты на грунт в процессе всего цикла погружения свай за исключением перемещения установки с одной рабочей позиции на другую. Самоходные копровые установки на базе тракторов могут выполнять все технологические операции связанные с погружением свай длиной до 16 метров. Более длинные сваи погружают специальными копровыми агрегатами или рельсовыми копрами чаще всего отделенными элементами со стыковкой. Для погружения свай применяют копровые агрегаты на базе полноповоротных базовых машин стреловых кранов экскаваторов и тракторов.
Оборудование сменного типа в виде навесных копровых стрел устанавливают на экскаваторы практически без переделки последних. Сменные копровые стрелы навесного и подвесного типов наиболее распространены: их выполняют в виде вертикально расположенной решетчатой конструкции изготовленной из металлических уголков или из труб с направляющими для захвата свайных молотов погружателей наголовников. Копровые стрелы навесного типа обеспечивают погружение свай на вылетах от оси вращения экскаватора до 4-6 метров и не требуют применения устройств для ссссссссс петы копровой стрелы на грунт в процессе подтаскивания и наведения свай. При работе на больших вылетах применяют копровые стрелы подвесного типа. Эти стрелы позволяют погружать сваи на вылетах до 8-10 метров от оси вращения экскаватора но при этом в процессе подтаскивания установки и забивки свай необходимо опирать пету копровой стрелы на грунт.
Копровое оборудование монтируется на гусеничном экскаваторе типа Э-10011 с пневматическим управлением.
Сваебойная установка оснащена электромеханическими устройствами для вспомогательных операций:
Установка копровой мачты вертикально координатного наведения сваи на проектную точку погружения установка мачты на грунт на время погружение сваи и проходка лидерной скважины. Конструкция копра позволяет применять: модернизированный дизель-молот СП-6Б с массой ударной части 2-5 тонн.
10. Погружатели свай.
Погружателями называются механизмы применяющиеся для погружения в грунт элементов разных по материалу форме конструкции и назначению ударным виброударным и вибрационным способами.
Свайные молоты различают по роду привода: механические паровоздушные дизельные гидравлические электрогидравлические. Наибольшее распространение в сссс свайных работ получили дизельные молоты в силу следующих преимуществ: полная автономность работы простота и надёжность конструкции безотказность работе при изменении температуры наружного воздуха.
Различают две группы дизель-молотов: штанговые где сгорание топлива происходит в камере сгорания при форсуночном распылении; и трубчатые – с ударно-компрессионным сгоранием топлива. По отношению длины рабочего хода цилиндра к его диаметру дизельные молоты подразделяются на длинноходные (19 : 15) и короткоходные (10 : 05) Расход топлива составляет 10-12 лч. Если частота ударов обычных дизель- молотов составляет 42-43 удара в 1 минуту то для быстроходных она равна 65-80 ударов.
По способу разгона ударной части при её ходе вниз штанговые молоты бывают со свободным падением ударной части (с неподвижными штангами) и с механическим (пружинным) буфером аккумулирующем часть энергии которая затем расходуется на разгон ударной части увеличение энергии и частоты ударов молота (с подвижными штангами).
Штанговые молоты хорошо зарекомендовали себя на свайных работах ввиду следующих качеств: автономность и независимость от посторонних источников энергии простота и надёжность конструкции безотказность в работе при низкой температуре воздуха и значительной осадке свай. При выборе молота для забивки свай учитывают предусмотренную проектом несущую способность сваи и её массу а также грунтовые условия площадки.
Штанговые дизель-молоты – для погружения свай в грунты слабые и средней плотности. Применение штанговых дизель-молотов наиболее эффективно но при отношении массы ударной части молота к массе сваи более 125.
Штанговый дизель-молот с массой ударной части 25т является основным и наиболее приемлемым погружателем свай в сложных мерзлотно-грунтовых условиях Севера. И это не случайно так как в отличие от трубчатого дизель-молота имеет ряд существенных преимуществ: отсутствует жесткий удар вызывающий разрушение головной части сваи; легко запускается в работу при низкой температуре окружающего воздуха (- 40ºС); устойчиво работает в южных районах; конструктивно пригоден и практически применяется для пробивки лидерных скважин в сезонном промерзании грунта при помощи лидера разового заглубления; смена поршневых колец производится без снятия молота с копровой установки. Штанговый дизель-молот повсеместно признан лучшим погружателем ударного воздействия для погружения свай.
Вместе с тем его технический уровень по-прежнему остаётся крайне низким. С момента изготовления первого его образца и до настоящего времени (на протяжении более 40 лет) поставляется строительным организациям с примитивным управлением при помощи четырёх верёвок без свайного наголовника. Оголовок приданный молоту под видом свайного наголовника ни в коей мере не отвечает этому назначению. Плавающая шарнирная его подвеска не позволяет удерживать погруженную сваю на оси молота. Моторесурс до капитального ремонта крайне мал: по паспортным данным составляет 1000 часов а промежуточные малозатратные ремонты путём замены изношенных деталей новыми или ремонтных размеров заводом-изготовителем не предусмотрены. Энергия удара после 4-5 месяцев эксплуатации молота резко снижается в результате сваи остаются недопогруженными до проектных отметок создавая реальную опасность деформации сооружений.
Чтобы ввести в эксплуатацию новый дизель-молот необходимо прежде всего изготовить к нему свайный наголовник.
Модернизация предусматривает:
Устранение конструктивных недостатков с целью повышения производительности сокращение вспомогательных операций высвобождение излишних рабочих на сваебойных установках за счёт изменения способа управления молотом. При устройстве свайных фундаментов на слабых грунтах имеющих значительную толщину всё большее распространение получают длинные сваи. Необходимое в этом случае увеличение мощности свайного молота обычно делают за счёт повышения массы ударной части. Представляет интерес возможность создания такого молота который без изменения массы и габарита ударной части позволит повысить осадку сваи при ударе а для длинных составных свай – обеспечить их эффективное погружение. Исследованиями установлено что отказ сваи зависит не только от величины передаваемой ей энергии но в значительной мере от формы импульса усилия. В частности теоретически и экспериментами установлена прямая зависимость осадки сваи от площади активной части импульса усилия формирующегося в голове длинной сваи.
Анализ структуры ударных импульсов создаваемых поршнями существующих конструкций свайных молотов показывают их невысокую эффективность. Дело в том что обладающие значительной динамичной жесткостью по сравнению с жесткостью сваи поршни создают в её голове ударные импульсы с большой неравномерностью распределения усилий по времени. Кратковременная часть импульса часто связана с разрушением головы сваи; хвостовая же часть импульса аккумулирующая большую долю энергии из-за малых величин усилий теряется бесполезно. Вот почему существующая тенденция увеличения массы молота реализуемая обычно за счёт увеличения его площади поперечного сечения с целью стабильности вертикальных размеров копра приводит к ухудшению структуры импульса. Оптимальная форма импульса кинетической энергии удара молота по свае – прямоугольная. Выполнение этого условия требует чтобы площадь поперечного сечения молота была в 6-7 раз меньше чем сваи. Поскольку соотношение площадей соударяющихся элементов близко к единице сохранение прежней длины ударной части значительно уменьшает её массу и энергию удара молота. Увеличение длины молота снижает его устойчивость при значительном удорожании копра. В связи с этим предложены новые конструкции многоместных молотов которые создавая оптимальную прямоугольную форму импульса увеличивают его длительность пропорционально количеству элементов и значительно повышают производительность. При ударе по свае молотом в голове сваи формируется импульс усилия сжатия и скорости смещения постоянной интенсивности.
Первая модернизация была проведена в 1966 году. В результате усовершенствования были высвобождены по одному рабочему на каждой сваебойной установке управление молотом при помощи верёвки было заменено пневматическим с пульта машиниста копра. При повторной модернизации в 1987 году на молоте выполнены дополнительные усовершенствования: установлены свешные головки поршня; компрессионные кольца в количестве четырёх штук расположены по новой схеме позволяющей поддерживать постоянную компрессию на протяжении длительного срока службы молота; на молоте (ударной части) установлен специальный клапан принудительной очистки цилиндра от отработанных газов.
Известно что в камере сгорания после очередного рабочего цикла остаётся часть газообразных продуктов сгорания ввиду отсутствия вентиляции что создаёт помехи для полноценного смесеобразования последующего рабочего цикла. Для устранения этого недостатка применяется продувка малым компрессором СО-2 или принудительная вентиляция камер сгорания с помощью кинетичного отсеятеля выхлопных газов экскаватора струя которых подводится резиновым шлангом к камере продувая и удаляя продукты сгорания. Это создаёт хорошие условия качественного образования рабочей смеси; эффективность удара возрастает на 10-15%. Затраты времени при забивке 10-метровых свай сократились на 20-25%.
Возможны следующие пути увеличения мощности свайных молотов: увеличение масс ударных частей частоты и количества ударов растягивание длительности ударного импульса снижение скорости передачи нагрузки от молота к свае.
Повышение эффективности погружения сваи в грунт можно получить за счёт снижения высоты подноса ударной части и введения в конструкцию дизель-молота пневмобуфера. Быстроходные дизель-молоты с пневмобуфером развивают частоту 72-78 ударов в одну минуту что ускоряет погружение сваи в 15-2 раза.
Для обеспечения большей стабильности работы молота в зимний и летний периоды необходимо регулировать момент впрыска топлива в камеру сгорания. При температуре окружающего воздуха +10ºС и выше момент впрыска должен быть раньше а при отрицательной ниже - 15ºС - позже. Изменение момента впрыска достигается регулировкой зазора между болтом рычага подачи и толкателем сссссссссс ссссссссс.
11. Устройство дизель-молота.
Штанговый дизель-молот СП-6Б состоит из поршневого блока ударной части направляющих штанг траверсы топливной системы и наголовника.
Модернизация включает в себя:
Разработку конструкторской и технологической документации.
Изготовление по рабочим чертежам заменяемых деталей и сборок в соответствии чертежа общего вида в который входят:
а) шабот в сварном варианте и отливка;
б) фиксаторы шабота;
в) серьги подвески шабота;
г) проушины привариваемые к блоку поршня;
д) свайный наголовник для свай;
е) пневматическое устройство на корпусе кошки для дистанционного управления молотом;
ж) дополнительное крепление траверсы на штангах;
и) пальцы присоединения шабота;
к) болты крепления наголовника к шаботу.
Поршневой блок представляет собой стальную отливку состоящую из поршня и основания. Поршень полый внутри в верхней части имеет проточки для компрессионных колец. В центре днища поршня расположен топливопровод верхняя часть которого заканчивается форсункой а нижняя – гнездом для установки топливного насоса. С помощью четырёх рёбер поршень прочно соединён с основанием поршневого блока.
В передней части основания находится резервуар для топлива а в задней – два кронштейна с направляющими ссссс для удержания молота в мачте копра. Нижняя часть основания поршневого блока сссссссс шарнирной опорой 9 состоящей из сферической петы и наголовника которые соединены серьгой.
Шарнирная опора обеспечивает центральный удар по свае в случае некоторого смещения осей молота и сваи.
Ударная часть молота – это чугунный цилиндр 2 в котором расположена камера сгорания. Перед ударной частью расположен штырь приводящий в действие топливной насос. Снизу ударная часть молота заканчивается четырьмя выступами которые проходят через окна поршневого блока и передают удар шарнирной опоре 9.
Направляющие штанги 3 полые внутри в верхней части соединены между собой траверсой 5. Между траверсой и ударной частью на направляющих штангах расположен подвижной захват – кошка 4 который служит для подъема ударной части при запуске молота. В углублении верхней части цилиндра помещён валик.
Захват – кошка зацепляется за валик с помощью крюка. Захват 4 разъединяется с ударной частью вручную поворотом рычага 6. В верхней части захвата - кошки находятся два крюка которыми он соединён с траверсой. Траверсу поднимают канатом от лебедки копра.
12. Работа дизель-молота.
Для пуска молота захват вместе с цилиндром поднимают канатом идущим от баребиса лебедки копра в крайнее верхнее положение. Затем захват траверсы отсоединяют и цилиндр под действием силы тяжести падает на поршень и сжимает заключенный в нем воздух температура которого при этом повышается до 60ºС.
При падении цилиндра расположенный на его поверхности штырь приводит в действие топливный насос который подает топливо в цилиндр где воспламеняется смесь воздуха с топливом. В результате сгорания смеси отработанные газы подбрасывают цилиндр верх. При разъединении цилиндра с поршнем отработанные газы выходят в атмосферу.
Достигнув крайнего верхнего положения цилиндр снова падает. С этого момента молот начинает работать автоматически до остановки топливного насоса. Высота подъема цилиндра зависит от размера отказа (сссссс погружения сваи от одного удара молота) сваи и достигает максимума при наименьшем отказе.
В гидросистему заливают рабочие жидкости соответствующих марок в зависимости от температуры окружающей среды: при температуре - 20ºС трансформаторное масло ТКП; при температуре - 40ºС используются рабочие жидкости марок типа АМН-10.
Техническая характеристика дизель-молотов.
Высота сброса ударной части для
Расчётная энергия одного удара
Рабочий ход цилиндра мм
13 Расчет погружения сваи ударом дизель-молота.
Произведем расчет применительно к штанговому молоту СП-6Б при следующих исходных данных
- энергия удара = 2400 кгсм
- вес сваи = 2050 кг
- вес ударной части = 4400 кг
- модуль упругости = 10104 кгсм2
- поперечное сечение = 9102 см2
- длина сваи = 910102 см
Находим статическое перемещение верхнего сечения сваи под действием силы
После удара сваи вместе с цилиндром будет совершать цилиндром колебания с частотой 101.
Подставив найденную величину в формулу
определяем вынужденные колебания:
Следовательно продолжительность совместного движения цилиндра и верхнего сечения сваи донной характеристики составляет см.
найдем величину динамических колебаний
отсюда минимальное перемещение цилиндра вместе с головой сваи
14. Тепловой расчет дизель-молота
Основными данными для теплового расчета дизель-молота являются топливо и его состав степень сжатия Е давление окружающего воздуха Р0 температура окружающего воздуха Т0 эффективная энергия и т.д. Для иллюстрации порядка расчета произведем тепловой расчет дизель-молота штангового типа СП-6Б при следующих исходных данных:
Le- эффективная энергия = 2400 кгм
Дизельное топливо со следующим химическим составом:
Вначале находим теоретически необходимое количество воздуха L0
где - молекулярный вес воздуха
- весовая доля содержания кислорода в воздухе
Для определения действительного количества воздуха следует принять значение коэффициента избытка воздуха который колеблется от 13 до17. Принимаем
Тогда действительное количество воздуха будет равно:
Определим состав продукта сгорания в кг.
Состав продуктов сгорания в молях:
Коэффициент молекулярного изменения равен
Средние молекулярные теплоемкости продуктов сгорания
где - объемные доли газов в смеси;
- средняя молярная теплоемкость составляющих газов при
Средняя молярная теплоемкость продуктов сгорания при постоянном давлении будет
Средняя молярная теплоемкость продуктов сгорания при постоянном объеме равна
Определим значение параметров в начале сжигания и в конце сжатия
Для расчета принимаем атм температура окружающего воздуха К фактическая степень сжатия для штангового молота давление остаточных газов а температура
Температура в конце впуска с учетом теплообмена определяется по формуле
где - повышение температуры за счет теплообмена со степенями
Величина коэффициента остаточных газов может быть принята в пределах значений приведенных ранее или рассчитана по формуле
Температура конца сжатия определяется по формуле
Давление в конце сжатия равно
где - средний показатель линии сжатия принимается равным 137.
Для определения параметров процесса сгорания задается степенью повышения давления и коэффициентом выделения тепла. В нашем расчете принимается . Коэффициент выделения тепла принимаем
При этих условиях минимальное давление в цилиндре будет равно:
Температура сгорания определяется из следующего уравнения:
где и - температура газов в точках и индикаторной диаграммы;
- средняя молекулярная теплоемкость воздуха величина которой принимается по таблицам для температуры С ;
- низкая теплотворная способность топлива (для нашего примера калкг).
Степень предварительного расширения определяется по формуле: (16)
Параметры (давление и температура ) в конце расширения рассчитывается по следующим формулам:
где - средний показатель линии расширения: принят равным 128.
Среднее индикаторное давление нагружемой диаграммы () рассчитывается по формуле:
При переходе к среднему индикаторному давлению действительной диаграммы применяется следующая формула:
где - коэффициент полноты диаграммы или коэффициент округления диаграммы численно изменяющийся от 092 до 097.
Среднее эффективное давление () будет иметь значение
где - механический К.П.Д. для дизель-молотов принимается в пределах от 07 до 08.
Удельный индикаторный расход топлива равен:
Эффективный расход топлива гл сч (22)
15. Расчет главных размеров цилиндра и его кинематики.
Главные размеры цилиндра рассчитываются исходя из заданной энергии удара молота и найденной величины среднего эффективного давления .
Эффективная энергия дизель-молота равна:
где - рабочий объем цилиндра
Следовательно зная можно определить или диаметр или рабочий ход цилиндра (поршня) из следующих соотношений
откуда диаметр цилиндра будет равен:
Коэффициент отношения рабочего хода к диаметру в современных дизель-молотах колеблется в больших пределах поэтому рекомендуется принимать для штанговых молотов отношение в пределах 13-16.
Пользуясь приведенными формулами и заданным значением
кгм а также принимая коэффициент отношения равным 13 находим и .
Диаметр цилиндра равен:
Ход цилиндра (поршня) равен:
Полный объем цилиндра () равен:
где - объем камеры сгорания.
Полный объем () может быть выражен через рабочий объем следующей зависимостью:
Объем камеры сгорания равен:
Для исследования динамики дизель-молота можно рассматривать или энергетические преобразования или изменение сил и ускорений. Воспользуемся первым вариантом и рассмотрим индикаторную работу по ходам ударной части.
Работа расширения равна:
где - индикаторная работа за один двойной ход (определяется расчетом).
Для нашего примера равна:
где - работа сжатия воздуха рассчитывается по формуле:
Известно что при работе молота на погружающейся свае часть энергии расширения идет на осадку сваи а другая на подъем ударной части. Величина энергии затрачиваемая на осадку сваи силой газов изменяется от минимума при малом сопротивлении сваи до минимума – в конце забивки сваи когда её погружение в грунт практически прекращается. Если принять что величина работы совершаемой силой давления газов в погружении сваи составляет в начале забивки 25% от индикаторной работы то на подъем ударной части вверх остается энергия падения равная:
При движении ударной части вверх часть энергии расходуется на преодоление силы трения и лобовое сопротивление воздуха.
Потери на трение и лобовое сопротивление можно принимать в пределах 025-020 от
Найденное значение и позволяют определить рабочую высоту подъема ударной части:
При нулевом отказе то есть при работе дизель-молота на жестком основании вся энергия будет расходоваться на падение ударной части и преодоление сопротивлений.
Тогда при полной подаче топлива минимальная высота подъема будет равна:
Для расчета числа ударов молота можно исходить из предположения что большая часть движения ударной части происходит под действием постоянного усилия или при подъеме так и при свободном падении.
Поэтому время полного цикла можно определить по формуле:
где - рабочая высота подъема ударной части при нормальном режиме молота.
Таким образом рассматриваемый дизель-молот будет делать 45 ударов в минуту.
Перспективы развития.
Дальнейшее повышение производства агрегатов можно добиться несколькими путями. Одним из них является многопозиционность проведения операции другим – применение одного погружающего механизма с конструктивными устройствами позволяющими совмещать операции забивки с операциями например подтаскивание сваи и заводкой её в наголовник. В ближайшее время учитывая возрастающий спрос а также повышение требования к эксплутационным качествам машины представляется необходимым провести ряд исследовательских и конструкторских работ направленных на повышение эффективности и надёжности дизель-молотов.
0. Технологическая часть
Расчётно-аналитический метод определения припусков на механическую обработку.
Тип производства – серийный.
Масса заготовки – 288.
Рассчитать припуск на механическую обработку поверхности диаметром 30 К6
Коэффициент использования металла:
Заготовка штампование на ТКМ.
Расчет припусков заготовки считаем по формуле:
где - высота неровностей;
- глубина дефектовочного слоя поверхности;
- пространственные отклонения;
- допуск диаметрического размера заготовки;
Расчет величины пространственных отклонений штамповки подготовленной к токарной обработке производится по формуле:
где - погрешность заготовки по смещению мм (табл. 18 (1) );
- погрешность заготовки по кривизне
где - кривизна штамповки типа
- погрешность центровки
где - допуск на диаметрический размер заготовки
(табл. 32 стр. 192 (1) );
Величина пространственных отклонений (остаточной кривизны) для рассматриваемого случая:
После предварительного шлифования
Величиной остаточных отклонений после окончательного шлифования пренебрегаем ввиду его малости
Таблица данных для выполнения расчета промежуточных припусков аналитическим методом (3 : стр. 89)
Последовательность выполнения
Предварительное точение
Предварительное шлифование
Расчет минимальных промежуточных припусков для случая обработки в центрах проводим по формуле (3; стр.86):
Для удобства расчета сводим в таблицу 2.
Расчет промежуточных припусков ведем от исходного размера шейки – наибольшего предельного размера путем последовательного прибавления к исходному расчетному размеру диаметра номинальных припусков
в порядке обратном ходу технологического процесса. Округление промежуточных размеров производим в сторону увеличения припусков до того же знака десятичной дроби.
Величина номинального промежуточного припуска и формула для его расчёта мм
Числовое значение припусков мм
При предварительном точении
При чистовом точении
При предварительном шлифовании
При чистовом шлифовании
Общий припуск заготовки
Производим расчет промежуточных припусков от исходного размера шейки – наибольшего предельного размера готовой шейки детали путем последовательного прибавления к исходному расчетному диаметру номинальных припусков
в порядке обратному ходу технологического процесса.
Округление промежуточных размеров производим в сторону увеличения припусков до того же знака десятичной дроби.
Расчет сводим в таблицу 3.
Наименование определяемой величины и формула для её расчёта
Условное обозначение
Числовое значение величины
Чертёжный размер поверхности
Наибольший предельный размер
продолжение таблицы 3
Номинальный припуск на диаметр при чистовом шлифовании
Расчётный диаметр после предварительного шлифования
Округлённый диаметр после предварительного шлифования
Номинальный припуск на диаметр при предварительном шлифовании
Расчётный диаметр после чистового точения
Округлённый диаметр после чистового точения
Номинальный припуск на диаметр при чистовом точении
Расчётный диаметр после предварительного точения
Округлённый диаметр после предварительного точения
Номинальный припуск на диаметр при предварительном точении
Расчётный диаметр заготовки-штамповки
Округлённый диаметр заготовки-штамповки
Расчет режима резания при точении 30 h 6
Для обработки поверхности 30 мм выбирали резец проходной прямой упорный с пластиной из твердого сплава Т 15 К6 ГОСТ 18878-73.
Н=20 мм; В=12 мм; L=100 мм; табл.7 (2).
Резец токарный отрезной пластинчатый ГОСТ 18881-73.
Н=12; В=3; L=85 мм; а=3 табл.7 (2)
Токарно-винторезный станок
Подача при черновом точении
где - постоянная величина зависящая от ряда факторов: материала инструмента
- среднее значение стойкости режущего инструмента
- показатели в степени зависящие от характеристики подачи режущего материала резца и вида обработки
- коэффициент учитывающий влияние материала заготовки состояние поверхности материала инструмента .
- коэффициент учитывающий качество обрабатываемого материала.
Подача при чистовом точении
Уточняем скорость при черновом точении
Уточняем скорость при чистовом точении
Определяем силу резания
- показатели степени сссссс качество обрабатываемого материала.
Определяем мощность резания
При полученной мощности выбираем токарно-винторезный станок
Коэффициент загрузки станка
Технологические нормы времени
где - длина обработки
- число рабочих ходов
Вспомогательное время:
В дипломном проекте разрабатывается оборудование для погружения свай в грунт. Оборудование дизель-молот установлено на базе экскаватора Э-10011. При эксплуатации строительных машин и оборудования имеют место следующие опасные факторы: физические – движущиеся элементы механизмов и машины в целом; недопустимая температура поверхностей машин и оборудования и воздуха в рабочей зоне; недопустимый уровень шума вибрации электромагнитных полей метеорологических колебаний в рабочей зоне; недостаточная или повышенная освещенность рабочей зоны; химические токсические и канцерогенные факторы появляющиеся при работе с топливами маслами а также с охлаждающимися жидкостями. Для того чтобы исключить вредное воздействие опасных факторов на организм работающих необходимо включить в конструкцию машин и оборудования различные элементы позволяющие уменьшить действие опасных производственных факторов.
При выполнении работ необходимо строго соблюдать технику безопасности. Требование безопасности труда в строительстве регламентируются СНиП 111-4-80.
Безопасность работы с дизель-молотом можно обеспечить только при соблюдении требований техники безопасности. Как правило травмирование трудящихся является следствием нарушения правил эксплуатации и правил техники безопасности при работе обслуживании или ремонте машин.
Допуск к работе с дизель-молотом оператор получает только после инструктажа по технике безопасности. Допустимые уровни звукового давления в активных полосах частот в кабинах строительно-дорожных машин в соответствии с ГОСТ 12. 1003-83. «Шум. Общие требования безопасности» в таблице 4.1 здесь же приведены фактические уровни звукового давления на рабочем месте и полученные превышения звукового давления.
Уровни звукового давления дб вактивных полосах частоты Гц.
Из таблицы 4.1 видно что фактические уровни шума превышают допустимые значения на частотах 250 500 1000 2000 4000 гц.
Основным источником шума является корпус двигателя. Действие шума на организм человека проявляется в поражении органов слуха и нарушении систем (сердечно-сосудистой центральной нервной) чувствительности. Степень вредного воздействия шума на организм человека зависит от частоты уровня и продолжительности воздействия. Шум вызывает раздражение приводит к утомлению ослаблению внимания замедлению психических реакций. Интенсивный шум часто у людей вызывает головные боли головокружение чувство страха неустойчивое психическое состояние.
Определим снижение уровня шума в кабине за счет звукоизоляционных свойств материалов из которых она изготовлена. Конструкция кабины приведена на рис. 4.1.
Толщина листа стали из которого изготовлена кабина мм. Толщина стекла кабины мм.
Толщина теплоизоляции (пенопласт) мм.
Толщина внутренней облицовки (фанеры) мм.
Сводим коэффициенты звукопоглощения пенопласта и фанеры а также звукоизолирующие способности стали и стекла в
Снижение шума в кабине найдем по формуле: где - суммарная звукопоглощающая способность и звукоизолирующая
стали пенопласта фанеры дб;
- звукоизолирующая способность остекленения дб.
Схема кабины экскаватора.
- толщина стали 3 мм.
- толщина пенопласта 50 мм.
- толщина фанеры 4 мм.
- толщина стекла 8 мм.
Найдем площади стен и окон.
Задняя стенка (без окон): м2
Площадь стен кабины: м2
Площадь пола и потолка: м2
Общая площадь стен пола и потолка: м2
Площадь остекленения кабины:
Значение и на частотах Гц.
Определим на активных полосах частот: 250 500 1000 2000 4000 гц.
Как видно из расчетов шум в кабине будет соответствовать нормам на всех активных полосах частот.
Согласно ГОСТ 12.1.005-76 нормируемыми показателями определяющими микроклимат на рабочем месте являются: температура относительная влажность скорость движения воздуха интенсивность теплового излучения.
В соответствии с нормами температура в кабине должна быть tв = 18 200С при скорости движения воздуха не более 02 мс и относительной влажности воздуха 40-60 %; в теплый период tв=21-230С при скорости движения воздуха не более 03 мс и относительной влажности воздуха 40-60 %.
Проведем оценку теплоизоляционных свойств кабины.
Кабина состоит из трех слоев: слой стали толщиной 3 мм слой пенопласта толщиной 60 мм слой фанеры толщиной 4 мм. Потери тепла в кабине происходят через прозрачные и непрозрачные ограждения (стены и остекленение кабины).
Площадь остекленения кабины м2.
Учитывая что температура в кабине должна быть постоянной пиведем расчет:
Уравнение теплового баланса: где - теплопоступление в кабину от источников теплоты и теплопотери через прозрачные и непрозрачные ограждения кабины.
- потери тепла через непрозрачные ограждения (стены пол потолок) Вт.
- потери тепла через прозрачные ограждения (остекленение кабины) Вт.
- теплопоступление от человека Вт.
Потери тепла через непрозрачные ограждения определим по формуле:
где - площадь непрозрачных ограждений м2с)
- коэффициент теплоотдачи многослойной конструкции кабины Вт(м2с).
- температура в кабине tк=18ºС
- температура окружающего воздуха tокр=-30ºС.
где - коэффициенты теплоотдачи на наружной и внутренней обшивке кабины Втм2ºС; Втм2ºС
- теплопроводность стали Втм2ºС
- теплопроводность пенопласта Втм2ºС
- теплопроводность фанеры Втм2ºС
Потери тепла через прозрачные ограждения (остекленение)
где - коэффициент теплоотдачи стекла для одинарного остекленения
Теплопоступление от человека
где - коэффициент учитывающий тяжесть труда
- коэффициент учитывающий теплоизолирующие свойства одежды
- скорость звука в кабине
Теплопотери кабины составляют
Из расчета видно что потери тепла в холодный период составляют
2 Вт; для компенсации потерь необходимо установить отопитель. В качестве отопителя можно установить электропечь работающую от генератора экскаватора. На экскаваторе установлен генератор выдающий электрический ток напряжением 230 В.
Найдем необходимое сопротивление электрической печи:
Печь состоит из нихромовой проволоки диаметром d=1 мм намотанной на фарфоровый сердечник D=05 мм.
Определим длину проволоки и число витков:
где - удельное сопротивление нихрома 10010-6 ом.
- площадь поперечного сечения проволоки:
Найдем число витков наматываемых на сердечник диаметром D=0005 м
Длина одного витка м
В теплый период года кабина должна защитить машиниста от избытка тепла. Произведем расчет количества тепла поступающего в кабину в теплый период при температуре окружающего воздуха 30ºС. Температура в кабине должна быть 23ºС.
где - тепло поступающее от человека.
- теплопоступление от солнечной радиации через остекленение кабины.
- теплопоступление от солнечной радиации через непрозрачные ограждения.
- тепло поступающее от непрозрачных ограждающих конструкций путем теплоотдачи.
- тепло поступающее через остекленение кабины путем теплопередачи.
где Втм2 - теплопоступление от солнечной радиации для остекленения по СНиП 11-33-75 «Отопление вентиляция кондиционирование воздуха».
- поверхность остекленения м2
- коэффициент теплопередачи стекла
втм2 – теплопоступление от солнечной радиации через многослойное покрытие согласно СНиП 11-33-75
- площадь потолка кабины м2
Суммарное количество тепла поступившее в кабину (избыток тепла):
Как видно из расчетов избыток тепла в кабине Вт. Избыточное тепло необходимо компенсировать. Это возможно осуществить путем установки кондиционера. Больше всего тепла поступает в кабину от человека и через остекленение кабины от солнечной радиации.
Проблема загрязнения атмосферного воздуха возникла в связи с развитием промышленного производства. Особую остроту она приобрела во второй половине 20 века в период научно-технической революции характеризующейся чрезвычайно высокими темпами роста промышленного производства потреблением электроэнергии и использованием некоторых транспортных средств.
Научно-технический процесс в промышленном производстве привел к расширению использования природных ресурсов. Перечень химических элементов вовлекаемых человеком в промышленное производство свидетельствует о его существенном возрастании в последние десятилетия. Если в начале 20 века использовалось 19 химических элементов то в середине его в промышленное производство было вовлечено около 50 их (В.И. Вернидский 1954) а в 70-х уже более 100. Эти изменения в промышленном производстве естественно сказались на составе промышленных выбросов что привело к качественно новому загрязнению атмосферного воздуха в частности аэрозоляции тяжелых и редких металлов.
Наряду с новым загрязнением природного характера во внешней среде появились синтетические соединения не существующие и не образующиеся в природе что связано с развитием производств органического синтеза и созданием новых отраслей химической промышленности. Исследования показали что ряд новых синтетических соединений оказались в биологическом отношении высокоактивными другие соединения еще требуют гигиенической оценки.
Сварка наплавка при ремонте и восстановлении узлов и деталей машин.
Характеристика технологического процесса и вредных веществ.
На предприятиях выполняется большой объем сварочно-наплавочных работ. При этом применяется аргонодуговая сварка деталей из алюминиевых сплавов вибродуговая наплавка изношенных деталей наплавка под слоем флюса наплавка и сварка в среде углекислого газа контактная сварка ручная электродуговая сварка различными типами электродов ручная газовая сварка деталей плазменное напыление электрометализация.
В процессе перечисленных сплавочно-наплавочных операций в воздушный бассейн выделяется значительное количество пыли аэрозолей окислов металлов окиси углерода окиси азота фтористого водорода. Количество вредных веществ образующихся при сварке наплавке и напылении удобнее всего приводить к расходу сварочных материалов так как в основной своей массе эти процессы нестабильны во времени.
Удельные показатели выделения вредных веществ для процесса сварки наплавки напыления приведены в таблице 1 (электросварка наплавка напыление) и в таблице 2 (газосварка).
Количество вредных веществ выделяющихся при сварке или наплавке под флюсом отнесено к 1 кг расходуемой сварочной проволоки.
Удельные показатели выделения вредных веществ при сварке наплавке.
Операции технологического процесса
Вну вредное вещество
Удельное сопротивление
Электродуговая сварка или на плавки под слоем флюса (автоматические)
Ручная электродуговая сварка штучными электродами и низколегированных конструкционных
Определение количества выбросов вредных веществ.
Количество вредных веществ выделяемых в воздушный бассейн в процессах сварки наплавки и напыления можно определить по следующей формуле
где - удельный показатель выделения ингредиента гкг сварочных материалов (в зависимости от способа наплавки и сварки марок электрода наплавочных материалов флюса и т.д.).
- масса расходуемых электродов наплавочного материала или газовой смеси.
Мероприятия по сокращению выбросов вредных веществ.
На производстве сварочных работ выделяются высокодисоционные аэрозоли металлов и газообразные вещества обладающие особой тонанностью. Наибольшее количество фтористых соединений выделяется при сварке под слоем флюса ОСУ-45 и АН-348 А.
Для сокращения выделения фтористых соединений при электросварке рекомендуется применять:
рутиловые электроды марок АНО-1 АНО-2.
керамические флюсы К-2 К-5 К-11 КС-12.
порошковую проволоку НП-ДСИ
Для очистки отходящего воздуха следует применять электрофильтры. Рекомендуется система: рулонный фильтр грубой очистки и электрофильтр тонкой очистки. Система имеет высокую эффективность экономна в эксплуатации однако её установка требует больших капитальных затрат и большой производственной площадки.
Для улавливания сварочного аэрозоля можно применять тонкие фильтры которые необходимо дополнять фильтрами грубой очистки. Регенерация встряхиванием.
Новое средство - переносные дымоочистители улавливающие дымы у мест их образования перекачивают небольшие количества и выпускают воздух после электровальных элементов. Эффективность очистки – 99 %. При выделении тонанных газов дымоочистители могут оснащаться малогабаритными поглотителями на активированном угле. ГОСИНТИ имеет чертежи установки «Вихрь-2» в которой электродвигатель пылесоса выключается при зажигании дуги гибкий шланг объединен электродержателем воздух удаляется непосредственно из зоны сварки.
Перспективным является также применение волокнистых материалов и адсорбционных методов очистки воздуха.
Газовая и плазменная резка металлов.
Процессы резки металлов получили большое распространение в ремонтном производстве. При этом различают газовую и плазменную резку металлов с выделением пыли окиси углерода двуокиси азота. В процессе резки металла удельные показатели выражены в граммах на погонный метр длины резки и имеют разные значения в зависимости от толщины разрезаемого металла. Удельные показатели выделения вредных веществ для процессов резки металлов приведены в таблице 5.2.
Удельные показатели выделения вредных веществ при резке металлов.
Топуши разруши листов
Выделяемое вредное вещество
Разовая резка малоуглеродных сталей
Газовая резка качественных лигированных сталей
Газовая резка сплавов титана
Плазменная резка малоуглеродных сталей
Плазменная резка АМТ
Электродуговая резка алюминиевых сплавов
Количество вредных веществ выделяемых в воздушный бассейн в процессе резки металлов можно определить по следующей формуле:
где - удельный показатель выделения ингредиента гнол.м реза при толщине разрезаемого металла б.
- длина реза пос.мч.
На производстве резки металлов выделяются высокодиссационные аэрозоли металлов и газообразные вещества обладающие особой тонанностью. Наибольшее количество фтористых соединений выделяется при резке под слоем флюса ОСУ-45 и АН-348 А.
Для сокращения выделений фтористых соединений при резке металлов рекомендуется применять:
рутиловые электроды марок АНО-1 АНО-24;
керамические флюсы К-2 К-5 К-11;
порокановую проволоку ПН-ДСИ
Для очистки воздуха следует применять электрофильтры. Для улавливания сварочного аэрозоля можно применять тонкие фильтры которые необходимо дополнять фильтрами грубой очистки.
Анализ аварий и катастроф последних 10-15 лет как в нашей стране так и за рубежом показывает что происходит накопление потенциальных опасностей природных и в особенности техногенных катастроф. При работе механизмами часто возникают ситуации когда жизни людей или их деятельности угрожает опасность. При работе с машинами необходимо обеспечивать безопасность жизнедеятельности. Этого можно добиться проанализировав конструкцию машин и технологию работ выполняемых этой машиной и выявив опасные факторы. Можно говорить о способах и средствах защиты людей. Для комплексного решения обеспечения безопасных условий труда в нашей стране действует система стандартов по безопасности жизнедеятельности которая включает в себя правила. Нормы.
Производство строительных работ связано с применением различных механизмов агрегатов оборудования и технологической оснастки. В связи с этим на строительных площадках существует множество опасных факторов угрожающих безопасности жизнедеятельности людей. Основными причинами аварий и несчастных случаев является грубое нарушение установленных норм и правил производства строительных работ техники безопасности и производственной дисциплины.
Свайные работы являются одной из разновидностей строительных работ при их выполнении возникает множество опасных факторов. Существуют различные виды оборудования для погружения свай в частности существует технология погружения свай с помощью вибрации. Машиной которая осуществляет погружение является дизель-молот. При работе дизель-молота возникают опасные факторы которые являются угрозой человеку и его безопасности. Одним из таких факторов является поражение людей электрическим током.
Большая опасность электрического тока для здоровья и жизни людей обусловлена тем что проходящий ток не виден человеком и зачастую не воспринимается им как источник непосредственной опасности. Его можно обнаружить с помощью специальных приборов. Электроток проходя через тело человека оказывает термическое электролитическое и биологическое воздействие на различные системы организма. Из всех видов поражения электротоком наибольшую опасность представляют электрические удары. Характерные признаки электрического удара - появление у человека судорог столбняка потеря сознания прекращение или сильное ослабление деятельности органов дыхания и кровообращения.
На степень поражения электрическим током влияют: сила электрического тока протекающего через тело человека; род; частота и продолжительность воздействия тока; путь тока и индивидуальные свойства организма человека. При действии переменного тока 100 МА - 5 А с частотой 50 ГЦ и постоянного тока 300МА - 5 А у человека может наступить фибрилляция сердца сопровождающая прекращение движения. В связи с выше перечисленным особенно важным становятся защита человека от поражения электрическим током.
К методам защиты от поражения электрическим током можно отнести ограждение электрооборудования и заземление его корпусов. В необходимых местах должны быть вывешены таблицы с предупредительными надписями «Опасно!»; «Под напряжением!» и т.п. Перед началом работ необходимо осуществлять проверку электрооборудования при проверке оно должно быть обесточено. Необходимо проверять крепление клемм отсутствие повреждения кабелей надёжность заземления корпусов и т.д. Нельзя допускать использование кабелей с повреждённой изоляцией нельзя сссссс замерзшие кабели и прокладывать провода непосредственно по грунту. Проверяющий должен предупредить обслуживающий персонал о том что он осуществляет проверку чтобы исключить случайное подключение напряжения во время проверки.
При работе дизель-молота появляются интенсивные вибрации что является следующим опасным производственным фактором. Действие вибрации на человека негативно сказывается на его здоровье и жизнедеятельность. Поскольку под воздействием вибрации части тела человека перемещаются относительно друг друга связки между частями тела напрягаются подвергаются взаимному соударению и надавливанию. Продолжительные колебания человека с частотой f = 3-5 ГЦ вредно отражаются на вестибулярном аппарате сердечно-сосудистой системе и вызывают синдром уставания. Колебания с частотой f = 5-11 ГЦ вызывают расстройства вследствие резонансных колебаний головы желудка кишечника в конечном итоге всего тела. При колебании с частотой f =11-45 ГЦ ухудшается зрение возникают тошнота рвота нарушается нормальная деятельность других органов. Колебания с частотой f ≥ 45 ГЦ вызывают повреждение сосудов головного мозга; происходит расстройство циркуляции крови и высшей нервной деятельности с последующим развитием вибрационной болезни. Для исключения вибрации как вредного фактора необходимо применять дистанционное управление вибромашины.
Следующим путем устранения вибрации на человека является применение виброгасителей и виброизоляторов которые позволяют изолировать человека и непосредственно его рабочее место от вибрационных воздействий также возможно применение средств автоматического контроля и сигнализации. Вибрация создается в вибромашинах от направленного влияния центробежных сил. Центробежные силы появляются при вращении больших масс со значительными скоростями. При поломке может возникнуть также ситуация когда сссс обладающий большой массой и скоростью может слететь с вала. В таком случае сссссс отлетит довольно далеко от места своего крепления что неизбежно приведет к несчастным случаям и аварии. Поэтому места установки сссссс необходимо надежно закрывать прочными крышками и своевременно проверять их крепление.
К опасным факторам можно причислить и наличие вращающихся частей машины. При нахождении рядом с вращающимися частями машины людей возможно возникнет такая ситуация когда одежда людей зацепится за вращающиеся части и начнется затягивание человека в машину. Также может быть неосторожное соприкосновение различных частей тела человека с вращающимися частями. Всё это может привести к несчастным случаям. Для защиты от этого опасного фактора необходимо применять кожухи для вращающихся частей машины или ограждение.
Производство свайных работ связано с транспортировкой и установкой свай в рабочее положение. При транспортировке свай их концы свешиваются за край кузова что в свою очередь является опасным фактором т.к. при поворотах возможны удары концами свай или зацепление людей или транспорта. Для предотвращения этого необходимо ограничить длину свешивающихся концов свай т.е. если сваи длинные то необходимо их перевозить на машинах с прицепом.
Прицеп предназначенный для перевозки длинных конусных свай должен быть оборудован поворотным столом. Таким же столом должен быть оборудован и автомобильный тягач. Высота площадки прицепа и стола тягача должна быть одинаковой.
Свайные работы связаны с подъемными работами. Перед погружением сваи в грунт её поднимают устанавливают в необходимое положение закрепляют и только после этого начинают осуществлять забивку т.е. само погружение.
При выполнении подъемных работ появляется опасность обрыва и придавливания людей сваей. Для сведения к минимуму этой опасности необходимо строго соблюдать правила техники безопасности при выполнении подъемных работ. Для подъема свай необходимо применять траверсы а также другие ссссс приспособления исключающие самопроизвольное отцепление и обеспечивающие устойчивость сссссс во время его перемещения. Канаты должны иметь акты - сертификаты с указанием их конструкции. Необходимо следить за износом канатов. Норма износа каната определяется числом оборванных проволок в наружных слоях прядей на длине одного типа свивки и устанавливается по нормам и правилам Госгортехнадзора. При превышении норм канат должен быть забракован или заменен.
Разборка и сборка копрового оборудования связаны с перемещением тяжелых металлических элементов причем последовательность отдельных операций должна выполняться в соответствии с утвержденной технической инструкцией.
Монтаж и демонтаж выполняют с помощью автомобильного крана в тех случаях когда копер устанавливают для забивки свай под углом его монтируют так чтобы наклон стрелы отвечал установленным требованиям проекта погружения свай. В этом случае пользуются указателями монтажа стрелы. После окончания монтажа стрелы устанавливают дизель-молот и осуществляют ссссссссс. При работе дизель-молота температура поверхности может достигать больших значений поэтому периодически необходимо останавливать работу и выдерживать время необходимое для остывания нагретых поверхностей. При погружении тяжелых свай в грунты следует следить за состоянием каната подтягивающего сваю. В таких случаях следует ослаблять канат постепенно чтобы не вызывать опрокидывания копра. Разворачивать забиваемые сваи в вертикальной плоскости можно только при помощи разворотного сссссссс соответствующего поперечному сечению сваи.
Для избежания несчастных случаев запрещено допускать в зону работы копра в радиусе не менее 25 метров. Во избежание просадки грунта под копром грунт должен быть достаточно плотным. В случае необходимости подсыпают песок и утрамбовывают его или ссссссссс железобетонные плиты. Перемещение установки и работа машины вблизи выемок с откосами разрешается только за пределами призмы оборудования грунта на расстоянии устанавливаемом проектом производства работ с СНиП 111-90.
Категорически запрещен допуск к работе лиц с алкогольным опьянением что неизбежно повлечет за собой несчастные случаи и травмы не только указанных лиц но и остального обслуживающего персонала.
Проанализировав конструкцию дизель-молота и технологию работ выполняемых с помощью свайного оборудования можно сделать вывод что применив все необходимые меры защиты от возникающих опасных факторов и строго соблюдая технику безопасности возможно обеспечить безопасность людей работающих с дизель-молотом.
Список используемой литературы
Мартынов В.Д. и др. Строительные машины и монтажное оборудование М.: Машиностроение 1990 – 352 с.
Сергеев В.П. Строительные машины и оборудование. М.: Высшая кола 1987. – 376 с
Домбровский Н.Г. Гальпуши М.Н. Строительные машины ( в 2-х ч.) – М.: Высшая школа 1985. – 224 с.
Под редакцией М.И. Сшородинова. 2-е изд. .. – М: Стройиздат 1988. – 223 с.: ил. – Справочник строителя.
Бадьин Т.М. Механизация свайных работ в зимних условиях. – Л.: Стройиздат Ленинград. Отделение 1987 – 184 с.
Косолапов В.Г. Копровое и буровое оборудование для свайных работ – М.: Высшая школа 1978. – 256 с. ил
Суровов А.В. Левинзон А.А. Машины для свайных работ под ред. С.П. Епифанова и др. 2-е изд. перераб. И доп. – М.: Стройиздат. 1982 – 150 с. ил.
Суровов А.В. Лубнин В.В. Зимина В.З. Машины и оборудование для погружения свай: Учебн. для техн. Училищ. – М.: Высшая шк. 1984 – 176 с. ил
Руководство по гигиене атмосферного воздуха. Под ред. К.А.Буштдевой. М Миридина 1976 416 с. ил.
Басиров Г.Н. Краткий справочник конструктора – Л.: Машиностроение 1984 – 464 с ил.
Федоренко В.А. Справочник по машиностроительному черчению – 14-е перераб. И доп. Машиностроение 1981 г.
Справочник технолога – машиностроителя. В 2-х т. Т1 Под редакцией А.Г. Косиловой и Г.Н. Мещерепова – 4 – е изд. М.: Машиностроение 1985. 656 с. ил.
Сваебойное оборудование. Под редакцией М.И.Смородикова М.: Машиностроение 1967 189 с. ил.
ПЗ+.doc
2.Перечень работ предшествующих устройству свайного фундамента.
3.Разбивка свайного фундамента.
4.Технология свайных работ.
5.Способы устройства лидерных скважин.
6.Подготовка к бурению лидерных скважин.
9.Сваебойные установки.
10.Погружатели свай.
11.Устройство дизель-молота.
12.Работа дизель-молота.
13. Расчет погружения сваи ударом дизель-молота.
14.Тепловой расчет дизель-молота.
15.Расчет главных размеров цилиндра и его кинематика.
0.Технологическая часть.
1.Технология изготовления вала.
0.Экономическая часть.
0. Безопасность жизнедеятельности.
Список используемой литературы.
Одним из основных направлений экономического и социального развития нашего государства является интенсивное освоение северо-восточных районов страны и непрерывное наращивание их производственного потенциала строительство объектов промышленного гражданского и транспортного назначения которые возводятся преимущественно на свайных фундаментах. Свайные фундаменты относятся к весьма ответственным видам строительных машин. Их надёжность на длительный срок зависит от ряда весьма существенных факторов: качественного выполнения инженерно-геологического измерения строительной площадки; принятого принципа непользования грунта основания; уровня механизации строительного цикла и принятой технологии; соответствия машин и механизмов строительным и технологическим требованиям; профессионального уровня рабочих и инженерно-технических работников ведущих строительство объекта.
До 1963 года погружение свай осуществляется в талые грунты низкочастотный вибропогружатель со сваебойной установкой СКВ-1 (местного изготовления).
В качестве базы машины применялся экскаватор Э-652. В дальнейшем для устройства свайных фундаментов на талых и вечномёрзлых грунтах с более глубоким погружением свай была создана сваебойная установка СКВ-12 на базе экскаватора Э-10011. Низкочастотный вибропогружатель заменён штанговым дизель-молотом С-268 с массой ударной части 25 т.
В подготовку строительной площадки к производству свайных работ входит:
Передача строительной организации заказчиком (генподрядчиком) проектно-технологической документации состоящей из отчёта инженерно-геологического изыскания строительной площадки проекта свайного фундамента разрешения административного органа на строительство объекта.
Снос наземных строений и коммуникаций находящихся в зоне строительной площадки.
Очистка строительной площадки от строительного и прочего мусора снега льда и т. п.
Срезка грунта планировка площадки подсыпка выемка котлована устройство съезда в котлован с уклоном к горизонту не более 15 градусов.
Подвод на строительную площадку электроэнергии с установкой подключающего устройства (рубильника автомата) на номинальную мощность 100 квт.
Установка ограждения (забора) высотой два метра вблизи жилых домов промышленных зданий и сооружений.
Оборудование наружного освещения со степенью освещенности рабочих мест не менее 50 люкс (30 Вт на один квадратный метр рабочего места).
Устройство обноски в соответствии с проектом производства работ (ППР). Нанесение на обноске главных разбивающих осей здания сооружения. Отклонения главных осей от проектного положения не должны превышать одного сантиметра на сто метров ряда.Подготовительную площадку заказчик (генподрядчик) передаёт строительной организации по акту.
2. Перечень работ предшествующих устройству свайного фундамента.
Ознакомление с проектом свайного фундамента и отчётом инженерно-геологического изыскания геологической площадки.
Выбор технологической схемы на способ погружения свай исходя из инженерно-геологического изыскания строительной площадки и принятого проектом способа передачи сваей нагрузки на грунт.
Составление проекта производства работ ППР.
Доставка на строительную площадку сваебойного и бурового оборудования.
Монтаж сваебойной установки наладка контроль технического состояния и готовности к вводу в работу.
Завоз на строительную площадку контрольных (пробных) свай в количестве указанном в проекте свайного фундамента.
Погружение контрольных (пробных) свай забивным или бурозабивным способом в зависимости от мерзлотно-грунтовых условий строительной площадки.
Завоз на строительную площадку проектных или откорректированных свай в полном объёме.
Разметка свай по длине через каждый погонный метр. Нумерация меток наносится красной краской арабскими цифрами начиная от низа (острия) сваи.
2.Разбивка свайного фундамента.
Разбивка свайного фундамента – одна из наиболее ответственных технологических операций которая заключается в переносе положения проектных главных и вспомогательных осей на местность где намечено сооружение свайного фундамента. Точки пересечения осей переносят с помощью теодолита и рулетки и фиксируют инвентарными металлическими штырями. Для переноса проектного положения свай на местность составляется исполнительная схема разбивки свайного поля с указанием всех проектных размеров расположения свай отмеренных от главных осей. По двум взаимно перпендикулярным направлениям пересечения главных осей на расстоянии 10 метров от осей здания выносят контрольные точки устанавливаемые для геодезической привязки на тот случай если будут главные оси сбиты в процессе работы. Для разбивки свайного поля на обноску по длине здания сооружения с помощью теодолита переносятся главные оси здания (свайного поля). Промежуточные оси соответствующие отдельным участкам разбивки свайного поля наносят на обноску при помощи рулетки.
Положение главных и промежуточных осей на обноске закрепляют гвоздями. Между вынесенными на обноску точками осей свайного поля натягивают мягкую проволоку фиксирующую
положение переносимых на местность осей здания сооружения. Точки пересечения осей переносят с помощью отвеса на поверхность участка и закрепляют металлическими штырями. Места расположения свай между зафиксированными на местности основными линиями по главным и промежуточным осям разбивают на каждом участке с применением рулетки. Отклонение разбивочных осей свайных рядов от проектных не должно превышать 1 сантиметра на каждые 100 метров ряда. Разбивку свайных рядов оформляют актом к которому прилагают схемы расположения знаков разбивки данные о привязке к базисной линии и к высотной опорной сети.
4. Технология свайных работ.
Устройство свайных фундаментов в сложных мерзлотно-геологических условиях выполняются тремя наиболее приемлемыми и эффективными способами погружения свай: забивным бурозабивным и буроопускным.
Забивной способ погружения непосредственно в целик грунта применяется на талых оттаявших и оттаянных грунтах содержащих в своей массе до 25% крупнообломочных включений (гальки гравия) без валунов.
Бурозабивной способ погружения свай в лидерные скважины применяется на мёрзлых и вечномёрзлых грунтах независимо от содержания в них крупнообломочных включений. На талых и оттаянных грунтах только при наличии в них крупнообломочных включений более 25%.
Буроопускной способ с установкой свай в лидерные скважины под собственным весом применяется в случаях когда устройство свайного фундамента забивным или бурозабивным способом может вызвать деформацию фундамента близко стоящего здания сооружения.
Из применяемых способов погружения свай бурозабивной способ имеет значительное преимущество. Поэтому и подготовка к непосредствен-ному погружению свай начинается с устройства лидерных скважин.
В строительной практике применяются разные способы устройства лидерных скважин например: ударно- канатный при помощи станков УНС-30м БС-1м УКС-22м и др.; ударно- разового и циклического заглубления с помощью модернизированного штангового дизель-молота СП-6Б1М; вращательный – самоходными буровыми машинами СО-2 СБМ и др.; навесными буровыми приводами 2НБП; НБП-90 НБП-10 и др. со сваебойных установок СКВ-12 СБУ-12.
Предпринимались попытки внедрить и другие способы бурения например виброударный и термомеханический однако оба эти способа практического применения не получили. Механизмы изготовляемые для этих целей оказались или непригодными или нецелесообразными. Виброударные установки конструкции ПКБ Главстроймеханизации Минтрансстроя при попытке бурить скважины в мёрзлых грунтах содержащие крупнообломочные включения не выдерживали чрезмерных виброударных нагрузок.
Лидеры сжимались или разрывались пружины вибромолота сварные соединения электродвигатель и другие сложные узлы быстро выходили из строя. Виброударная установка монтировалась на тракторе Т-180. Термомеханический способ бурения не получил
признания из-за нецелесообразности его применения так как мог применяться в тех же мерзлотно-грунтовых условиях в которых бурение успешно выполнялось вращательным методом навесными буровыми приводами с более высокой производительностью и меньшими затратами. Оборудование для термомеханического способа бурения устанавливалось на тяжелом дорогостоящем тракторе ДП-250.
Размеры лидерных скважин назначаются по таблицам 12 в зависимос-ти от мерзлотно-грунтовых условий строительной площадки проектной нагрузки на сваю способа передачи сваей нагрузки на грунт. Глубина бурения скважины для свай-стоек принимается равной проектному заглублению.
Параметры лидерных скважин и бурового инструмента.
Для многолетне-мерзлых (вечномёрзлых) грунтов и грунтов с сезонным промерзанием.
Коэффициент забуривания
Диаметр забурения ммм
Размер квадратной скважины мм
Для талых и оттаянных грунтов при условии наличия в них крупнооб-ломочных включений более 25 %.
Диаметр забурения мм
Глубина проходки лидерных скважин для свай - висячих принимается ссссссс в зависимости от проектной нагрузки на сваю геологического состава грунта и его температурного состояния.
Надёжность свайных фундаментов сооружаемых бурозабивным способом зависит от размера скважин в сечении и по глубине бурения надлежащего контроля за степенью износа бурового инструмента и своевременной его замены. По мере износа забурника и шнека скважины одна за другой уменьшается в
диаметре а по глубине приобретают форму усечённого конуса. В процессе погружения (забивки) свай в конусные скважины наступает момент когда погружатель свай например дизель-молот не в состоянии преодолевать сопротивление сваи погружению. В результате свая останавливается недопогруженной до проектной отметки с критическими и ложными отказами. При попытке добить её до проектного заглубления она разрушается в первую очередь в головной части. Разрушенные сваи для добивки становятся непригодными а для фундамента – неполноценными.
6. Подготовка к бурению лидерных скважин.
Навеска бурового привода на мачту сваебойной установки.
Фиксация бурового привода в нижней части мачты копра для подсоединения к нему бурового става (шнека с забурником).
Подсоединение бурового става соответствующего проектному диаметру к буровому приводу посредством форкопа (крестообразного шарнира).
Подъём бурового привода вместе с буровым ставом на высоту равную длине шнека.
Установка копровой мачты в вертикальное положение механизмами выравнивания.
Наведение бурового става на точку бурения механизмами точного координатного наведения.
Установка мачты копра на грунт при помощи опорного механизма.
Пуск в работу бурового привода: бурение скважин на проектную глубину; извлечение шнека из скважины.
Подсоединение к нижней части шнека (вместо забурника) зачистного устройства для зачистки забоя скважины.
Перемещение сваебойной установки к последующему месту бурения.
При бурении последующих скважин очерёдность технологических операций повторяется. Бурение скважин составным или телескопическим шнеком на глубину более шести метров выполняется циклично с очисткой шнека. Результат бурения каждой скважины вносится в журнал бурения. Проходка скважин периодически чередуется с погружением свай в скважины.
По окончании бурения некоторого количества скважин с мачты копра снимается буровой привод и навешивается дизель-молот. Сваебойную установку например СКВ 12 с навешанным молотом перемещают к месту погружения свай – к пробуренным скважинам. К мачте копра подтаскивается свая и стропуется специальной подвешенной рамкой соединённой стропами (цепями) с наголовником дизель-молота. Застропованную сваю вместе с дизель-молотом машинист по команде копровщика поднимает к мачте копра. Поднятая свая благодаря подвешенной рамке занимает отвесное положение. Ходом машины и поворотом платформы машинист подводит сваю (в отвесном положении) к скважине а электромеханическими устройствами координатного наведения – на центр скважины. Установкой молота на сваю заканчивается подготовка к погружению сваи в скважину. По команде копровщика машинист при помощи дистанционного пневматического управления производит зацеп и подъём ударной части молота на высоту 1.3 - 1.5 метра затем сброса ударной части молота запускается в работу молот. Через 5-6 пробных ударов копровщик останавливает молот проверяет положение и состояние погружаемой сваи вновь запускает молот в работу. При достижении сваей заглубления близко к проектному забивка сваи
приостанавливается для подготовки к замеру отказа. К свае копровщик приставляет козелок-подставку проверяет соосность дизель-молота со сваей.
Замер отказа сваи проводится тремя залогами: два первых – контрольные выполняются двадцатью ударами по десять ударов в залоге. Фактический остаточный отказ замеряется на третьем залоге тридцатью ударами. Если при первых двух залогах ударная часть молота в рабочем режиме не достигает нормативной высоты то замер отказа на третьем залоге выполняется одиночными ударами с выключенной подачей топлива с высоты сброса ударной части 24 – 22 метра – для штангового дизель-молота и 25-23 метра для трубчатых дизель-молотов. Перед выполнением третьего залога высотное положение сваи фиксируется нанесением на ней риски на уровне козелка-подставки. Вторая фиксирующая риска наносится после десяти последних ударов молота. Промежуток между двумя последними рисками измеряется мерной линейкой с точностью до одного миллиметра и делится на десять последних ударов. Одна десятая часть промежутка между двумя рисками и есть фактический отказ погруженной сваи который заносится в журнал забивки свай.
При погружении свай в сложных мерзлотно-грунтовых условиях фактические отметки заглубления свай не всегда соответствуют проектным. Сваи погружённые на проектные отметки и не давшие расчетного отказа оставляются на «отдых»
продолжительность которого зависит от состава и характера прорезных и подстилающих под концами свай грунтов. В песчаных грунтах «отдых; длится трое суток в связных и разнородных грунтах – 6 суток в глинистых грунтах – от 12 до 16 суток. По истечении срока отведённого для «отдыха» проводится повторный (контрольный) замер отказа десятью ударами с высоты сброса 22-24метра одиночными ударами с отключённой подачей топлива. Если и после «отдыха» фактический остаточный отказ по-прежнему превышает расчётный дальнейшие погружения сваи прекращается для выявления причины и принятия решения проектной организацией которая и определяет необходимость проведения статического испытания корректировки проекта свайного фундамента или части его.
Сваи длиной до 10 метров недопогруженные более чем на 15% проектной глубины и сваи большей длины недопогруженные более чем на 10% проектного заглубления дают критический отказ или близкий критическому подвергаются обследованию для выяснения причин и принятия решений о необходимости погружения дублирующих свай. При погружении свай молотом двойного действия продолжительность последнего залога принимается три минуты а отказ определяется как среднее значение глубины погружения сваи от одного удара в течение последней минуты в залоге.
9. Сваебойные установки.
Сваебойная установка СНВ 12 (общий вид) предназначена для погружения в грунт свай длиной: цельных – до 12 метров составных – до 24 метров забивным и бурозабивным способами для проходки лидерных скважин вращательным способом навесным буровым приводом при помощи шнека. Эффективность производства свайных работ во многом зависит от правильности выбора копров и копрового оборудования специальной технологической оснастки и приспособлений обеспечивающих работоспособность установок в любых климатических и грунтовых условиях. Этот выбор должен быть сделан с учётом принятой технологии и сроков производства свайных работ природно-климатических и грунтовых условий конструктивных решений свайных фундаментов и требуемой производительности установок. При выборе и технико-экономическом обосновании количества и конструкций копров в составе комплекта сваебойного оборудования необходимо учитывать требуемую точность и качество погружения свай оптимальную технологию и организацию работ в пределах свайного поля возможность комплексной механизации производства свайных работ в зимних условиях.
В качестве погружателей на копрах используют трубчатые СП-54 СП-47А СП-48 и штанговые СП-6Б СП-60. Создаются
как универсальные так и специальные копровые установки предназначенные для выполнения свайных работ при сооружении фундаментов в особых условиях строительства. Основными факторами определяющими выбор копров и свайного оборудования являются: масса и длина погружаемых свай конфигурация свайного поля и расположение свай гидрогеологические условия физико-механические характеристики грунтов толщина мерзлого слоя требуемая точность погружения свай сроки осуществления свайных работ.
Каждая машина предназначенная для производства свайных работ имеет свою область рационального применения. Эффективность использования того или иного типа копров обосновывается сравнением их технико-экономических показателей (стоимость трудоёмкость).
Наиболее рациональной машиной для погружения свай расположенных в один или два ряда являются серийно выпускаемые копры на базе тракторов с боковой навеской оборудования а также мостовые копры. Последние наиболее целесообразно использовать при типовой массовой застройке и выполнении свайных полей прямоугольно формы. Копровое оборудование с подвешенными копровыми мачтами требует обязательного опирания мачты на грунт в процессе всего цикла погружения свай за исключением перемещения установки с одной рабочей позиции на другую. Самоходные копровые установки на
базе тракторов могут выполнять все технологические операции связанные с погружением свай длиной до 16 метров. Более длинные сваи погружают специальными копровыми агрегатами или рельсовыми копрами чаще всего отделенными элементами со стыковкой. Для погружения свай применяют копровые агрегаты на базе полноповоротных базовых машин стреловых кранов экскаваторов и тракторов.
Оборудование сменного типа в виде навесных копровых стрел устанавливают на экскаваторы практически без переделки последних. Сменные копровые стрелы навесного и подвесного типов наиболее распространены: их выполняют в виде вертикально расположенной решетчатой конструкции изготовленной из металлических уголков или из труб с направляющими для захвата свайных молотов погружателей наголовников. Копровые стрелы навесного типа обеспечивают погружение свай на вылетах от оси вращения экскаватора до 4-6 метров и не требуют применения устройств для пяты копровой стрелы на грунт в процессе подтаскивания и наведения свай. При работе на больших вылетах применяют копровые стрелы подвесного типа. Эти стрелы позволяют погружать сваи на вылетах до 8-10 метров от оси вращения экскаватора но при этом в процессе подтаскивания установки и забивки свай необходимо опирать пету копровой стрелы на грунт.
Копровое оборудование монтируется на гусеничном экскаваторе типа Э-10011 с пневматическим управлением.
Сваебойная установка оснащена электромеханическими устройствами для вспомогательных операций:
Установка копровой мачты вертикально координатного наведения сваи на проектную точку погружения установка мачты на грунт на время погружение сваи и проходка лидерной скважины. Конструкция копра позволяет применять: модернизированный дизель-молот СП-6Б с массой ударной части 2-5 тонн.
10. Погружатели свай.
Погружателями называются механизмы применяющиеся для погружения в грунт элементов разных по материалу форме конструкции и назначению ударным виброударным и вибрационным способами.
Свайные молоты различают по роду привода: механические паровоздушные дизельные гидравлические электрогидравлические. Наибольшее распространение в сссс свайных работ получили дизельные молоты в силу следующих преимуществ: полная автономность работы простота и надёжность конструкции безотказность работе при изменении температуры наружного воздуха.
Различают две группы дизель-молотов: штанговые где сгорание топлива происходит в камере сгорания при форсуночном распылении; и трубчатые – с ударно-компрессионным сгоранием топлива. По отношению длины рабочего хода цилиндра к его диаметру дизельные молоты подразделяются на длинноходные (19 : 15) и короткоходные (10 : 05) Расход топлива составляет 10-12 лч. Если частота ударов обычных дизель- молотов составляет 42-43 удара в 1 минуту то для быстроходных она равна 65-80 ударов.
По способу разгона ударной части при её ходе вниз штанговые молоты бывают со свободным падением ударной части
(с неподвижными штангами) и с механическим (пружинным) буфером аккумулирующем часть энергии которая затем расходуется на разгон ударной части увеличение энергии и частоты ударов молота (с подвижными штангами).
Штанговые молоты хорошо зарекомендовали себя на свайных работах ввиду следующих качеств: автономность и независимость от посторонних источников энергии простота и надёжность конструкции безотказность в работе при низкой температуре воздуха и значительной осадке свай. При выборе молота для забивки свай учитывают предусмотренную проектом несущую способность сваи и её массу а также грунтовые условия площадки.
Штанговые дизель-молоты – для погружения свай в грунты слабые и средней плотности. Применение штанговых дизель-молотов наиболее эффективно но при отношении массы ударной части молота к массе сваи более 125.
Штанговый дизель-молот с массой ударной части 25т является основным и наиболее приемлемым погружателем свай в сложных мерзлотно-грунтовых условиях Севера. И это не случайно так как в отличие от трубчатого дизель-молота имеет ряд существенных преимуществ: отсутствует жесткий удар вызывающий разрушение головной части сваи; легко запускается в работу при низкой температуре окружающего воздуха (- 40ºС); устойчиво работает в южных районах; конструктивно пригоден и практически применяется для пробивки лидерных скважин в
сезонном промерзании грунта при помощи лидера разового заглубления; смена поршневых колец производится без снятия молота с копровой установки. Штанговый дизель-молот повсеместно признан лучшим погружателем ударного воздействия для погружения свай.
Вместе с тем его технический уровень по-прежнему остаётся крайне низким. С момента изготовления первого его образца и до настоящего времени (на протяжении более 40 лет) поставляется строительным организациям с примитивным управлением при помощи четырёх верёвок без свайного наголовника. Оголовок приданный молоту под видом свайного наголовника ни в коей мере не отвечает этому назначению. Плавающая шарнирная его подвеска не позволяет удерживать погруженную сваю на оси молота. Моторесурс до капитального ремонта крайне мал: по паспортным данным составляет 1000 часов а промежуточные малозатратные ремонты путём замены изношенных деталей новыми или ремонтных размеров заводом-изготовителем не предусмотрены. Энергия удара после 4-5 месяцев эксплуатации молота резко снижается в результате сваи остаются недопогруженными до проектных отметок создавая реальную опасность деформации сооружений.
Чтобы ввести в эксплуатацию новый дизель-молот необходимо прежде всего изготовить к нему свайный наголовник.
Модернизация предусматривает:
устранение конструктивных недостатков с целью повышения производительности сокращение вспомогательных операций высвобождение излишних рабочих на сваебойных установках за счёт изменения способа управления молотом. При устройстве свайных фундаментов на слабых грунтах имеющих значительную толщину всё большее распространение получают длинные сваи. Необходимое в этом случае увеличение мощности свайного молота обычно делают за счёт повышения массы ударной части. Представляет интерес возможность создания такого молота который без изменения массы и габарита ударной части позволит повысить осадку сваи при ударе а для длинных составных свай – обеспечить их эффективное погружение. Исследованиями установлено что отказ сваи зависит не только от величины передаваемой ей энергии но в значительной мере от формы импульса усилия. В частности теоретически и экспериментами установлена прямая зависимость осадки сваи от площади активной части импульса усилия формирующегося в голове длинной сваи.
Анализ структуры ударных импульсов создаваемых поршнями существующих конструкций свайных молотов показывают их невысокую эффективность. Дело в том что обладающие значительной динамичной жесткостью по сравнению с жесткостью сваи поршни создают в её голове ударные импульсы с большой неравномерностью распределения усилий по времени.
Кратковременная часть импульса часто связана с разрушением головы сваи; хвостовая же часть импульса аккумулирующая большую долю энергии из-за малых величин усилий теряется бесполезно. Вот почему существующая тенденция увеличения массы молота реализуемая обычно за счёт увеличения его площади поперечного сечения с целью стабильности вертикальных размеров копра приводит к ухудшению структуры импульса. Оптимальная форма импульса кинетической энергии удара молота по свае – прямоугольная. Выполнение этого условия требует чтобы площадь поперечного сечения молота была в 6-7 раз меньше чем сваи. Поскольку соотношение площадей соударяющихся элементов близко к единице сохранение прежней длины ударной части значительно уменьшает её массу и энергию удара молота. Увеличение длины молота снижает его устойчивость при значительном удорожании копра. В связи с этим предложены новые конструкции многоместных молотов которые создавая оптимальную прямоугольную форму импульса увеличивают его длительность пропорционально количеству элементов и значительно повышают производительность. При ударе по свае молотом в голове сваи формируется импульс усилия сжатия и скорости смещения постоянной интенсивности.
Первая модернизация была проведена в 1966 году. В результате усовершенствования были высвобождены по одному рабочему на каждой сваебойной установке управление молотом
при помощи верёвки было заменено пневматическим с пульта машиниста копра. При повторной модернизации в 1987 году на молоте выполнены дополнительные усовершенствования: установлены свешные головки поршня; компрессионные кольца в количестве четырёх штук расположены по новой схеме позволяющей поддерживать постоянную компрессию на протяжении длительного срока службы молота; на молоте (ударной части) установлен специальный клапан принудительной очистки цилиндра от отработанных газов.
Известно что в камере сгорания после очередного рабочего цикла остаётся часть газообразных продуктов сгорания ввиду отсутствия вентиляции что создаёт помехи для полноценного смесеобразования последующего рабочего цикла. Для устранения этого недостатка применяется продувка малым компрессором СО-2 или принудительная вентиляция камер сгорания с помощью кинетичного отсеятеля выхлопных газов экскаватора струя которых подводится резиновым шлангом к камере продувая и удаляя продукты сгорания. Это создаёт хорошие условия качественного образования рабочей смеси; эффективность удара возрастает на 10-15%. Затраты времени при забивке 10-метровых свай сократились на 20-25%.
Возможны следующие пути увеличения мощности свайных молотов: увеличение масс ударных частей частоты и количества ударов растягивание длительности ударного импульса снижение
скорости передачи нагрузки от молота к свае.
Повышение эффективности погружения сваи в грунт можно получить за счёт снижения высоты подноса ударной части и введения в конструкцию дизель-молота пневмобуфера. Быстроходные дизель-молоты с пневмобуфером развивают частоту 72-78 ударов в одну минуту что ускоряет погружение сваи в 15-2 раза.
Для обеспечения большей стабильности работы молота в зимний и летний периоды необходимо регулировать момент впрыска топлива в камеру сгорания. При температуре окружающего воздуха +10ºС и выше момент впрыска должен быть раньше а при отрицательной ниже - 15ºС - позже. Изменение момента впрыска достигается регулировкой зазора между болтом рычага подачи и толкателем .
11. Устройство дизель-молота.
Штанговый дизель-молот СП-6Б состоит из поршневого блока ударной части направляющих штанг траверсы топливной системы и наголовника.
Модернизация включает в себя:
Разработку конструкторской и технологической документации.
Изготовление по рабочим чертежам заменяемых деталей и сборок в соответствии чертежа общего вида в который входят:
а) шабот в сварном варианте и отливка;
б) фиксаторы шабота;
в) серьги подвески шабота;
г) проушины привариваемые к блоку поршня;
д) свайный наголовник для свай;
е) пневматическое устройство на корпусе кошки для дистанционного управления молотом;
ж) дополнительное крепление траверсы на штангах;
и) пальцы присоединения шабота;
к) болты крепления наголовника к шаботу.
Поршневой блок представляет собой стальную отливку состоящую из поршня и основания. Поршень полый внутри в верхней части имеет проточки для компрессионных колец. В центре днища поршня расположен топливопровод верхняя часть которого заканчивается форсункой а нижняя – гнездом для
установки топливного насоса. С помощью четырёх рёбер поршень прочно соединён с основанием поршневого блока.
В передней части основания находится резервуар для топлива а в задней – два кронштейна с направляющими служат для удержания молота в мачте копра. Нижняя часть основания поршневого блока соединена шарнирной опорой 9 состоящей из сферической петы и наголовника которые соединены серьгой.
Шарнирная опора обеспечивает центральный удар по свае в случае некоторого смещения осей молота и сваи.
Ударная часть молота – это чугунный цилиндр 2 в котором расположена камера сгорания. Перед ударной частью расположен штырь приводящий в действие топливной насос. Снизу ударная часть молота заканчивается четырьмя выступами которые проходят через окна поршневого блока и передают удар шарнирной опоре 9.
Направляющие штанги 3 полые внутри в верхней части соединены между собой траверсой 5. Между траверсой и ударной частью на направляющих штангах расположен подвижной захват – кошка 4 который служит для подъема ударной части при запуске молота. В углублении верхней части цилиндра помещён валик.
Захват – кошка зацепляется за валик с помощью крюка. Захват 4 разъединяется с ударной частью вручную поворотом рычага 6. В верхней части захвата - кошки находятся два крюка которыми он соединён с траверсой. Траверсу поднимают канатом от лебедки копра.
12. Работа дизель-молота.
Для пуска молота захват вместе с цилиндром поднимают канатом идущим от баребиса лебедки копра в крайнее верхнее положение. Затем захват траверсы отсоединяют и цилиндр под действием силы тяжести падает на поршень и сжимает заключенный в нем воздух температура которого при этом повышается до 60ºС.
При падении цилиндра расположенный на его поверхности штырь приводит в действие топливный насос который подает топливо в цилиндр где воспламеняется смесь воздуха с топливом. В результате сгорания смеси отработанные газы подбрасывают цилиндр верх. При разъединении цилиндра с поршнем отработанные газы выходят в атмосферу.
Достигнув крайнего верхнего положения цилиндр снова падает. С этого момента молот начинает работать автоматически до остановки топливного насоса. Высота подъема цилиндра зависит от размера отказа (длины погружения сваи от одного удара молота) сваи и достигает максимума при наименьшем отказе.
В гидросистему заливают рабочие жидкости соответствующих марок в зависимости от температуры окружающей среды: при температуре - 20ºС трансформаторное масло ТКП; при температуре - 40ºС используются рабочие жидкости марок типа АМН-10.
Техническая характеристика дизель-молотов.
Высота сброса ударной части для
Расчётная энергия одного удара
Рабочий ход цилиндра мм
13 Расчет погружения сваи ударом дизель-молота.
Произведем расчет применительно к штанговому молоту СП-6Б при следующих исходных данных
- энергия удара = 2400 кгсм
- вес сваи = 2050 кг
- вес ударной части = 4400 кг
- модуль упругости = 10104 кгсм2
- поперечное сечение = 9102 см2
- длина сваи = 910102 см
Находим статическое перемещение верхнего сечения сваи под действием силы
После удара сваи вместе с цилиндром будет совершать цилиндром колебания с частотой 101.
Подставив найденную величину в формулу
определяем вынужденные колебания:
Следовательно продолжительность совместного движения цилиндра и верхнего сечения сваи донной характеристики составляет см.
найдем величину динамических колебаний
отсюда минимальное перемещение цилиндра вместе с головой сваи
14. Тепловой расчет дизель-молота
Основными данными для теплового расчета дизель-молота являются топливо и его состав степень сжатия Е давление окружающего воздуха Р0 температура окружающего воздуха Т0 эффективная энергия и т.д. Для иллюстрации порядка расчета произведем тепловой расчет дизель-молота штангового типа СП-6Б при следующих исходных данных:
Le- эффективная энергия = 2400 кгм
Дизельное топливо со следующим химическим составом:
Вначале находим теоретически необходимое количество воздуха L0
где - молекулярный вес воздуха
- весовая доля содержания кислорода в воздухе
Для определения действительного количества воздуха следует принять значение коэффициента избытка воздуха который колеблется от 13 до17. Принимаем
Тогда действительное количество воздуха будет равно:
Определим состав продукта сгорания в кг.
Состав продуктов сгорания в молях:
Коэффициент молекулярного изменения равен
Средние молекулярные теплоемкости продуктов сгорания
где - объемные доли газов в смеси;
- средняя молярная теплоемкость составляющих газов при
Средняя молярная теплоемкость продуктов сгорания при постоянном давлении будет
Средняя молярная теплоемкость продуктов сгорания при постоянном объеме равна
Определим значение параметров в начале сжигания и в конце сжатия
Для расчета принимаем атм температура
окружающего воздуха К фактическая степень сжатия для штангового молота давление остаточных газов а температура
Температура в конце впуска с учетом теплообмена определяется по формуле
где - повышение температуры за счет теплообмена со степенями
Величина коэффициента остаточных газов может быть принята в пределах значений приведенных ранее или рассчитана по формуле
Температура конца сжатия определяется по формуле
Давление в конце сжатия равно
где - средний показатель линии сжатия принимается равным 137.
Для определения параметров процесса сгорания задается степенью повышения давления и коэффициентом выделения тепла. В нашем расчете принимается . Коэффициент выделения тепла принимаем
При этих условиях минимальное давление в цилиндре будет равно:
Температура сгорания определяется из следующего уравнения:
где и - температура газов в точках и индикаторной диаграммы;
- средняя молекулярная теплоемкость воздуха величина которой принимается по таблицам для температуры С ;
- низкая теплотворная способность топлива (для нашего примера калкг).
Степень предварительного расширения определяется по формуле: (16)
Параметры (давление и температура ) в конце расширения рассчитывается по следующим формулам:
где - средний показатель линии расширения: принят равным 128.
Среднее индикаторное давление нагружемой диаграммы () рассчитывается по формуле:
При переходе к среднему индикаторному давлению действительной диаграммы применяется следующая формула:
где - коэффициент полноты диаграммы или коэффициент округления диаграммы численно изменяющийся от 092 до 097.
Среднее эффективное давление () будет иметь значение
где - механический К.П.Д. для дизель-молотов принимается в пределах от 07 до 08.
Удельный индикаторный расход топлива равен:
Эффективный расход топлива гл сч (22)
15. Расчет главных размеров цилиндра и его кинематики.
Главные размеры цилиндра рассчитываются исходя из заданной энергии удара молота и найденной величины среднего эффективного давления .
Эффективная энергия дизель-молота равна:
где - рабочий объем цилиндра
Следовательно зная можно определить или диаметр или рабочий ход цилиндра (поршня) из следующих соотношений
откуда диаметр цилиндра будет равен:
Коэффициент отношения рабочего хода к диаметру в современных дизель-молотах колеблется в больших пределах поэтому рекомендуется принимать для штанговых молотов отношение в пределах 13-16.
Пользуясь приведенными формулами и заданным значением
кгм а также принимая коэффициент отношения равным 13 находим и .
Диаметр цилиндра равен:
Ход цилиндра (поршня) равен:
Полный объем цилиндра () равен:
где - объем камеры сгорания.
Полный объем () может быть выражен через рабочий объем следующей зависимостью:
Объем камеры сгорания равен:
Для исследования динамики дизель-молота можно рассматривать или энергетические преобразования или изменение сил и ускорений. Воспользуемся первым вариантом и рассмотрим индикаторную работу по ходам ударной части.
Работа расширения равна:
где - индикаторная работа за один двойной ход (определяется расчетом).
Для нашего примера равна:
где - работа сжатия воздуха рассчитывается по формуле:
Известно что при работе молота на погружающейся свае часть энергии расширения идет на осадку сваи а другая на подъем ударной части. Величина энергии затрачиваемая на осадку сваи силой газов изменяется от минимума при малом сопротивлении
сваи до минимума – в конце забивки сваи когда её погружение в грунт практически прекращается. Если принять что величина работы совершаемой силой давления газов в погружении сваи составляет в начале забивки 25% от индикаторной работы то на подъем ударной части вверх остается энергия падения равная:
При движении ударной части вверх часть энергии расходуется на преодоление силы трения и лобовое сопротивление воздуха.
Потери на трение и лобовое сопротивление можно принимать в пределах 025-020 от
Найденное значение и позволяют определить рабочую высоту подъема ударной части:
При нулевом отказе то есть при работе дизель-молота на жестком основании вся энергия будет расходоваться на падение ударной части и преодоление сопротивлений.
Тогда при полной подаче топлива минимальная высота подъема будет равна:
Для расчета числа ударов молота можно исходить из предположения что большая часть движения ударной части происходит под действием постоянного усилия или при подъеме так и при свободном падении.
Поэтому время полного цикла можно определить по формуле:
где - рабочая высота подъема ударной части при нормальном режиме молота.
Таким образом рассматриваемый дизель-молот будет делать 45 ударов в минуту.
Перспективы развития.
Дальнейшее повышение производства агрегатов можно добиться несколькими путями. Одним из них является многопозиционность проведения операции другим – применение одного погружающего механизма с конструктивными устройствами позволяющими совмещать операции забивки с операциями например подтаскивание сваи и заводкой её в наголовник. В ближайшее время учитывая возрастающий спрос а также повышение требования к эксплутационным качествам машины представляется необходимым провести ряд исследовательских и конструкторских работ направленных на повышение эффективности и надёжности дизель-молотов.
0. Технологическая часть.
Расчётно-аналитический метод определения припусков на механическую обработку.
Тип производства – серийный.
Масса заготовки – 288.
Рассчитать припуск на механическую обработку поверхности диаметром 30 К6
Коэффициент использования металла:
Заготовка штампование на ТКМ.
Расчет припусков заготовки считаем по формуле:
где - высота неровностей;
- глубина дефектовочного слоя поверхности;
- пространственные отклонения;
- допуск диаметрического размера заготовки;
Расчет величины пространственных отклонений штамповки подготовленной к токарной обработке производится по формуле:
где - погрешность заготовки по смещению мм (табл. 18 (1) );
- погрешность заготовки по кривизне
где - кривизна штамповки типа
- погрешность центровки
где - допуск на диаметрический размер заготовки
(табл. 32 стр. 192 (1) );
Величина пространственных отклонений (остаточной кривизны) для рассматриваемого случая:
После предварительного шлифования
Величиной остаточных отклонений после окончательного шлифования пренебрегаем ввиду его малости
Таблица данных для выполнения расчета промежуточных припусков аналитическим методом (3 : стр. 89)
Последовательность выполнения
Предварительное точение
Предварительное шлифование
Расчет минимальных промежуточных припусков для случая обработки в центрах проводим по формуле (3; стр.86):
Для удобства расчета сводим в таблицу 2.
Расчет промежуточных припусков ведем от исходного размера шейки – наибольшего предельного размера путем последовательного прибавления к исходному расчетному размеру диаметра номинальных припусков
в порядке обратном ходу технологического процесса. Округление промежуточных размеров
производим в сторону увеличения припусков до того же знака десятичной дроби.
Величина номинального промежуточного припуска и формула для его расчёта мм
Числовое значение припусков мм
При предварительном точении
При чистовом точении
При предварительном шлифовании
При чистовом шлифовании
Общий припуск заготовки
Производим расчет промежуточных припусков от исходного размера шейки – наибольшего предельного размера готовой шейки детали путем последовательного прибавления к исходному расчетному диаметру номинальных припусков
в порядке обратному ходу технологического процесса.
Округление промежуточных размеров производим в сторону увеличения припусков до того же знака десятичной дроби.
Расчет сводим в таблицу 3.
Наименование определяемой величины и формула для её расчёта
Условное обозначение
Числовое значение величины
Чертёжный размер поверхности
Наибольший предельный размер
продолжение таблицы 3
Номинальный припуск на диаметр при чистовом шлифовании
Расчётный диаметр после предварительного шлифования
Округлённый диаметр после предварительного шлифования
Номинальный припуск на диаметр при предварительном шлифовании
Расчётный диаметр после чистового точения
Округлённый диаметр после чистового точения
Номинальный припуск на диаметр при чистовом точении
Расчётный диаметр после предварительного точения
Округлённый диаметр после предварительного точения
Номинальный припуск на диаметр при предварительном точении
Расч. диаметр заготовки-штамповки
Округ. диаметр заготовки-штамповки
Расчет режима резания при точении 30 h 6
Для обработки поверхности 30 мм выбирали резец проходной прямой упорный с пластиной из твердого сплава Т 15 К6 ГОСТ 18878-73.
Н=20 мм; В=12 мм; L=100 мм; табл.7 (2).
Резец токарный отрезной пластинчатый ГОСТ 18881-73.
Н=12; В=3; L=85 мм; а=3 табл.7 (2)
Токарно-винторезный станок
Подача при черновом точении
где - постоянная величина зависящая от ряда факторов: материала инструмента
- среднее значение стойкости режущего инструмента
- показатели в степени зависящие от характеристики подачи режущего материала резца и вида обработки
- коэффициент учитывающий влияние материала заготовки состояние поверхности материала инструмента .
- коэффициент учитывающий качество обрабатываемого материала.
Подача при чистовом точении
Уточняем скорость при черновом точении
Уточняем скорость при чистовом точении
Определяем силу резания
- показатели степени качества обрабатываемого материала.
Определяем мощность резания
При полученной мощности выбираем токарно-винторезный станок
Коэффициент загрузки станка
Технологические нормы времени
где - длина обработки
- число рабочих ходов
Вспомогательное время:
0.Безопасность жизнедеятельности.
В дипломном проекте разрабатывается оборудование для погружения свай в грунт. Оборудование дизель-молот установлено на базе экскаватора Э-10011. При эксплуатации строительных машин и оборудования имеют место следующие опасные факторы: физические – движущиеся элементы механизмов и машины в целом; недопустимая температура поверхностей машин и оборудования и воздуха в рабочей зоне; недопустимый уровень шума вибрации электромагнитных полей метеорологических колебаний в рабочей зоне; недостаточная или повышенная освещенность рабочей зоны; химические токсические и канцерогенные факторы появляющиеся при работе с топливами маслами а также с охлаждающимися жидкостями. Для того чтобы исключить вредное воздействие опасных факторов на организм работающих необходимо включить в конструкцию машин и оборудования различные элементы позволяющие уменьшить действие опасных производственных факторов.
При выполнении работ необходимо строго соблюдать технику безопасности. Требование безопасности труда в строительстве регламентируются СНиП 111-4-80.
Безопасность работы с дизель-молотом можно обеспечить только при соблюдении требований техники безопасности. Как правило травмирование трудящихся является следствием нарушения правил эксплуатации и правил техники безопасности при работе обслуживании или ремонте машин.
Допуск к работе с дизель-молотом оператор получает только после инструктажа по технике безопасности. Допустимые уровни звукового давления в активных полосах частот в кабинах строительно-дорожных машин в соответствии с ГОСТ 12. 1003-83. «Шум. Общие требования безопасности» в таблице 4.1 здесь же приведены фактические уровни звукового давления на рабочем месте и полученные превышения звукового давления.
Уровни звукового давления дб вактивных полосах частоты Гц.
Из таблицы 4.1 видно что фактические уровни шума превышают допустимые значения на частотах 250 500 1000 2000 4000 гц.
Основным источником шума является корпус двигателя. Действие шума на организм человека проявляется в поражении органов слуха и нарушении систем (сердечно-сосудистой центральной нервной) чувствительности. Степень вредного воздействия шума на организм человека зависит от частоты уровня и продолжительности воздействия. Шум вызывает раздражение приводит к утомлению ослаблению внимания замедлению психических реакций. Интенсивный шум часто у людей вызывает головные боли головокружение чувство страха неустойчивое психическое состояние.
Определим снижение уровня шума в кабине за счет звукоизоляционных свойств материалов из которых она изготовлена.
Толщина листа стали из которого изготовлена кабина мм. Толщина стекла кабины мм.
Толщина теплоизоляции (пенопласт) мм.
Толщина внутренней облицовки (фанеры) мм.
Сводим коэффициенты звукопоглощения пенопласта и фанеры а также звукоизолирующие способности стали и стекла в
Снижение шума в кабине найдем по формуле: где - суммарная звукопоглощающая способность и звукоизолирующая
стали пенопласта фанеры дб;
- звукоизолирующая способность остекленения дб.
Схема кабины экскаватора.
- толщина стали 3 мм.
- толщина пенопласта 50 мм.
- толщина фанеры 4 мм.
- толщина стекла 8 мм.
Найдем площади стен и окон.
Задняя стенка (без окон): м2
Площадь стен кабины: м2
Площадь пола и потолка: м2
Общая площадь стен пола и потолка: м2
Площадь остекленения кабины:
Значение и на частотах Гц.
Определим на активных полосах частот: 250 500 1000 2000 4000 гц.
Как видно из расчетов шум в кабине будет соответствовать нормам на всех активных полосах частот.
Согласно ГОСТ 12.1.005-76 нормируемыми показателями определяющими микроклимат на рабочем месте являются: температура относительная влажность скорость движения воздуха интенсивность теплового излучения.
В соответствии с нормами температура в кабине должна быть tв = 18 200С при скорости движения воздуха не более 02 мс и относительной влажности воздуха 40-60 %; в теплый период tв=21-
0С при скорости движения воздуха не более 03 мс и относительной влажности воздуха 40-60 %.
Проведем оценку теплоизоляционных свойств кабины.
Кабина состоит из трех слоев: слой стали толщиной 3 мм слой пенопласта толщиной 60 мм слой фанеры толщиной 4 мм. Потери тепла в кабине происходят через прозрачные и непрозрачные ограждения (стены и остекленение кабины).
Площадь остекленения кабины м2.
Учитывая что температура в кабине должна быть постоянной пиведем расчет:
Уравнение теплового баланса: где - теплопоступление в кабину от источников теплоты и теплопотери через прозрачные и непрозрачные ограждения кабины.
- потери тепла через непрозрачные ограждения (стены пол потолок) Вт.
- потери тепла через прозрачные ограждения (остекленение кабины) Вт.
- теплопоступление от человека Вт.
Потери тепла через непрозрачные ограждения определим по формуле:
где - площадь непрозрачных ограждений м2с)
- коэффициент теплоотдачи многослойной конструкции кабины Вт(м2с).
- температура в кабине tк=18ºС
- температура окружающего воздуха tокр=-30ºС.
где - коэффициенты теплоотдачи на наружной и внутренней обшивке кабины Втм2ºС; Втм2ºС
- теплопроводность стали Втм2ºС
- теплопроводность пенопласта Втм2ºС
- теплопроводность фанеры Втм2ºС
Потери тепла через прозрачные ограждения (остекленение)
где - коэффициент теплоотдачи стекла для одинарного остекленения
Теплопоступление от человека
где - коэффициент учитывающий тяжесть труда
- коэффициент учитывающий теплоизолирующие свойства одежды
- скорость звука в кабине
Теплопотери кабины составляют
Из расчета видно что потери тепла в холодный период составляют
2 Вт; для компенсации потерь необходимо установить отопитель. В качестве отопителя можно установить электропечь работающую от генератора экскаватора. На экскаваторе установлен генератор выдающий электрический ток напряжением 230 В.
Найдем необходимое сопротивление электрической печи:
Печь состоит из нихромовой проволоки диаметром d=1 мм намотанной на фарфоровый сердечник D=05 мм.
Определим длину проволоки и число витков:
где - удельное сопротивление нихрома 10010-6 ом.
- площадь поперечного сечения проволоки:
Найдем число витков наматываемых на сердечник диаметром D=0005 м
Длина одного витка м
В теплый период года кабина должна защитить машиниста от избытка тепла. Произведем расчет количества тепла поступающего в кабину в теплый период при температуре окружающего воздуха 30ºС. Температура в кабине должна быть 23ºС.
где - тепло поступающее от человека.
- теплопоступление от солнечной радиации через остекленение кабины.
- теплопоступление от солнечной радиации через непрозрачные ограждения.
- тепло поступающее от непрозрачных ограждающих конструкций путем теплоотдачи.
- тепло поступающее через остекленение кабины путем теплопередачи.
где Втм2 - теплопоступление от солнечной радиации для остекленения по СНиП 11-33-75 «Отопление вентиляция кондиционирование воздуха».
- поверхность остекленения м2
- коэффициент теплопередачи стекла
втм2 – теплопоступление от солнечной радиации через многослойное покрытие согласно СНиП 11-33-75
- площадь потолка кабины м2
Суммарное количество тепла поступившее в кабину (избыток тепла):
Как видно из расчетов избыток тепла в кабине Вт. Избыточное тепло необходимо компенсировать. Это возможно осуществить путем установки кондиционера. Больше всего тепла поступает в кабину от человека и через остекленение кабины от солнечной радиации.
Проблема загрязнения атмосферного воздуха возникла в связи с развитием промышленного производства. Особую остроту она приобрела во второй половине 20 века в период научно-технической революции характеризующейся чрезвычайно высокими темпами роста промышленного производства потреблением электроэнергии и использованием некоторых транспортных средств.
Научно-технический процесс в промышленном производстве привел к расширению использования природных ресурсов. Перечень химических элементов вовлекаемых человеком в промышленное производство свидетельствует о его существенном возрастании в последние десятилетия. Если в начале 20 века использовалось 19 химических элементов то в середине его в промышленное производство было вовлечено около 50 их (В.И. Вернидский 1954) а в 70-х уже более 100. Эти изменения в промышленном производстве естественно сказались на составе промышленных выбросов что привело к качественно новому загрязнению атмосферного воздуха в частности аэрозоляции тяжелых и редких металлов.
Наряду с новым загрязнением природного характера во внешней среде появились синтетические соединения не существующие и не образующиеся в природе что связано с развитием производств органического синтеза и созданием новых отраслей химической промышленности. Исследования показали что ряд новых синтетических соединений оказались в биологическом отношении высокоактивными другие соединения еще требуют гигиенической оценки.
Сварка наплавка при ремонте и восстановлении узлов и деталей машин.
Характеристика технологического процесса и вредных веществ.
На предприятиях выполняется большой объем сварочно-наплавочных работ. При этом применяется аргонодуговая сварка деталей из алюминиевых сплавов вибродуговая наплавка изношенных деталей наплавка под слоем флюса наплавка и сварка в среде углекислого газа контактная сварка ручная электродуговая сварка различными типами электродов ручная газовая сварка деталей плазменное напыление электрометализация.
В процессе перечисленных сплавочно-наплавочных операций в воздушный бассейн выделяется значительное количество пыли аэрозолей окислов металлов окиси углерода окиси азота фтористого водорода. Количество вредных веществ образующихся при сварке наплавке и напылении удобнее всего приводить к расходу сварочных материалов так как в основной своей массе эти процессы нестабильны во времени.
Удельные показатели выделения вредных веществ для процесса сварки наплавки напыления приведены в таблице 1 (электросварка наплавка напыление) и в таблице 2 (газосварка).
Количество вредных веществ выделяющихся при сварке или наплавке под флюсом отнесено к 1 кг расходуемой сварочной проволоки.
Удельные показатели выделения вредных веществ при сварке наплавке.
Операции технологического процесса
Вну вредное вещество
Удельное сопротивление
Электродуговая сварка или на плавки под слоем флюса (автоматические)
Ручная электродуговая сварка штучными электродами и низколегированных конструкционных
Определение количества выбросов вредных веществ.
Количество вредных веществ выделяемых в воздушный бассейн в процессах сварки наплавки и напыления можно определить по следующей формуле
где - удельный показатель выделения ингредиента гкг сварочных материалов (в зависимости от способа наплавки и сварки марок электрода наплавочных материалов флюса и т.д.).
- масса расходуемых электродов наплавочного материала или газовой смеси.
Мероприятия по сокращению выбросов вредных веществ.
На производстве сварочных работ выделяются высокодисоционные аэрозоли металлов и газообразные вещества обладающие особой тонанностью. Наибольшее количество фтористых соединений выделяется при сварке под слоем флюса ОСУ-45 и АН-348 А.
Для сокращения выделения фтористых соединений при электросварке рекомендуется применять:
рутиловые электроды марок АНО-1 АНО-2.
керамические флюсы К-2 К-5 К-11 КС-12.
порошковую проволоку НП-ДСИ
Для очистки отходящего воздуха следует применять электрофильтры. Рекомендуется система: рулонный фильтр грубой очистки и электрофильтр тонкой очистки. Система имеет высокую эффективность экономна в эксплуатации однако её установка требует больших капитальных затрат и большой производственной площадки.
Для улавливания сварочного аэрозоля можно применять тонкие фильтры которые необходимо дополнять фильтрами грубой очистки. Регенерация встряхиванием.
Новое средство - переносные дымоочистители улавливающие дымы у мест их образования перекачивают небольшие количества и выпускают воздух после электровальных элементов. Эффективность очистки – 99 %. При выделении тонанных газов дымоочистители могут оснащаться малогабаритными поглотителями на активированном угле. ГОСИНТИ имеет чертежи установки «Вихрь-2» в которой электродвигатель пылесоса выключается при зажигании дуги гибкий шланг объединен электродержателем воздух удаляется непосредственно из зоны сварки.
Перспективным является также применение волокнистых материалов и адсорбционных методов очистки воздуха.
Газовая и плазменная резка металлов.
Процессы резки металлов получили большое распространение в ремонтном производстве. При этом различают газовую и плазменную резку металлов с выделением пыли окиси углерода двуокиси азота. В процессе резки металла удельные показатели выражены в граммах на погонный метр длины резки и имеют разные значения в зависимости от толщины разрезаемого металла. Удельные показатели выделения вредных веществ для процессов резки металлов приведены в таблице 5.2.
Удельные показатели выделения вредных веществ при резке металлов.
Топуши разруши листов
Выделяемое вредное вещество
Разовая резка малоуглеродных сталей
Газовая резка качественных лигированных сталей
Газовая резка сплавов титана
Плазменная резка малоуглеродных сталей
Плазменная резка АМТ
Электродуговая резка алюминиевых сплавов
Количество вредных веществ выделяемых в воздушный бассейн в процессе резки металлов можно определить по следующей формуле:
где - удельный показатель выделения ингредиента гнол.м реза при толщине разрезаемого металла б.
- длина реза пос.мч.
На производстве резки металлов выделяются высокодиссационные аэрозоли металлов и газообразные вещества обладающие особой тонанностью. Наибольшее количество фтористых соединений выделяется при резке под слоем флюса ОСУ-45 и АН-348 А.
Для сокращения выделений фтористых соединений при резке металлов рекомендуется применять:
рутиловые электроды марок АНО-1 АНО-24;
керамические флюсы К-2 К-5 К-11;
порокановую проволоку ПН-ДСИ
Для очистки воздуха следует применять электрофильтры. Для улавливания сварочного аэрозоля можно применять тонкие фильтры которые необходимо дополнять фильтрами грубой очистки.
Список используемой литературы
Мартынов В.Д. и др. Строительные машины и монтажное оборудование М.: Машиностроение 1990 – 352 с.
Сергеев В.П. Строительные машины и оборудование. М.: Высшая кола 1987. – 376 с
Домбровский Н.Г. Гальпуши М.Н. Строительные машины ( в 2-х ч.) – М.: Высшая школа 1985. – 224 с.
Под редакцией М.И. Сшородинова. 2-е изд. .. – М: Стройиздат 1988. – 223 с.: ил. – Справочник строителя.
Бадьин Т.М. Механизация свайных работ в зимних условиях. – Л.: Стройиздат Ленинград. Отделение 1987 – 184 с.
Косолапов В.Г. Копровое и буровое оборудование для свайных работ – М.: Высшая школа 1978. – 256 с. ил
Суровов А.В. Левинзон А.А. Машины для свайных работ под ред. С.П. Епифанова и др. 2-е изд. перераб. И доп. – М.: Стройиздат. 1982 – 150 с. ил.
Суровов А.В. Лубнин В.В. Зимина В.З. Машины и оборудование для погружения свай: Учебн. для техн. Училищ. – М.: Высшая шк. 1984 – 176 с. ил
Руководство по гигиене атмосферного воздуха. Под ред. К.А.Буштдевой. М Миридина 1976 416 с. ил.
Басиров Г.Н. Краткий справочник конструктора – Л.: Машиностроение 1984 – 464 с ил.
Федоренко В.А. Справочник по машиностроительному черчению – 14-е перераб. И доп. Машиностроение 1981 г.
Справочник технолога – машиностроителя. В 2-х т. Т1 Под редакцией А.Г. Косиловой и Г.Н. Мещерепова – 4 – е изд. М.: Машиностроение 1985. 656 с. ил.
Сваебойное оборудование. Под редакцией М.И.Смородикова М.: Машиностроение 1967 189 с. ил.
спец.ВО2+.dwg

спец.СБ4+.dwg

спец.СБ5+.dwg

спец.ВП+.dwg

для одноковшового экскаватора
Пояснительная записка
Копровое оборудование на
базе экскаватора э-10011
Наголовник для свай 300x300
Документация по деталям
спец.ВО+.dwg

спец.ВО1+.dwg

спец.СБ2+.dwg

спец.СБ1+.dwg

спец.СБ3+.dwg

Экономика СДМ.doc
1 Краткая характеристика и вариант для сравнения.
Для производства свайных работ на строительных объектах применяют сваебойная установка СКВ-12 на базе гусеничного экскаватора Э-00111.
При перебазировке сваебойной установки с одного объекта на другой требуется использовать транспортные средства трейлеры полуприцепы автотягачи. При погрузке транспортировке и разгрузке возникают дополнительные простои сваебойной установки что снижает коэффициент ее использования. Также возникают дополнительные затраты от использования транспортных средств.
Применение шлангового дизель-молота СП-6Б на базе пневмоколесного экскаватора ЭО-4321 позволяет без задержек и простоев перебазировать машину с одного объекта на другой. Отпадает потребность в транспортных средствах для перевозки дизель-молота что позволяет снизить затраты на транспортировку. Снижение затрат на транспортировку позволяет уменьшить себестоимость использования дизель-молота СП-6Б.
2. Методика расчета экономического
эффекта внедрения новой техники.
Экономический эффект определяется по формуле:
Э = S1 – S2 = (K1*Eн + C1)-(K2*EH + C2)
где S1 – приведенные затраты на транспортировку внедряемого дизель-молота;
S2 – приведенные затраты на транспортировку сваебойной установки;
К1 – капитальные вложения на транспортировку дизель-молота;
К2 – капитальные вложения на транспортировку сваебойной установки;
Ен – коэффициент эффективности капитальных вложении Ен = 015;
С1 – себестоимость транспортировки дизель-молота;
С2 – себестоимость транспортировки сваебойной установки;
При расчетах используем технико-экономические показатели приведенные в таблице 3.1
Технико-экономические показатели.
Продолжительность одной транспортировки сваебойной установки
Среднее расстояние транспортировки
Среднее количество транспортировок сваебойной установки по объектам в год
Сваебойная установка СКВ-12 на базе гусеничного экскаватора Э-00111 автотягач КрАЗ-258 и трейлер гп 20 т.
Шланговый дизель-молот СП-6Б на базе пневмоколесного экскаватора ЭО-4321
Рассчитываем приведенные затраты на транспортировку сваебойной установки СКВ-12.
Перевозка с одного объекта на другой сваебойной установки СКВ-12 на базе гусеничного экскаватора Э-00111 производится на трейлере УМЗАП грузоподъемностью 20 тонн который буксируется тягачем КрАЗ-258.
Определим стоимость капитальных вложений на транспортировку сваебойной установки СКВ-12.
Стоимость капитальных вложений складывается из суммы балансовой стоимости сваебойной установки СКВ-12 экскаватора Э-00111 трейлера УМЗАП и тягача КрАЗ-258.
Балансовая стоимость сваебойной установки СКВ-12 – 32800 рублей.
Балансовая стоимость экскаватора Э-00111 – 86340рублей.
Балансовая стоимость трейлера УМЗАП – 96350рублей.
Балансовая стоимость тягача КрАЗ-258 – 126840рублей.
К1 = 86340 + 32800 + 126840 + 96350 = 342330 рублей.
Рассчитываем себестоимость транспортировки сваебойной установки на строительные объекты в течении года.
Определим стоимость одного часа работы всего комплекса машин.
Повременный тариф за перевозку грузов автомобилей грузоподъемностью свыше пяти тонн за один автомобилечас использования при пробеге до 9 км – 114 рубля свыше пяти тонн за каждую дополнительную тонну грузоподъемности 18 рубля.
Грузоподъемность автомобиля КрАЗ 12 тонн стоимость одного часа работы автотягача КрАЗ-258:
Сат = [114 + 18(12-5)]*18 = 432 рубля
где 18 – коэффициент применяемый в северных районах.
Стоимость одной машиносмены работы трейлера грузоподъемностью 20 тонн – 114 рубля (ценник N2 n 187).
Стоимость работы одного часа трейлера грузоподъемностью 20 тонн:
Стр = 1148 = 1425 рублей.
Стоимость одной машиносмены работы сваебойной установки СКВ-12 на базе гусеничного экскаватора Э-00111 2754 рубля (дополнение к ценнику N2 n2).
Стоимость одного часа работы сваебойной установки СКВ-12:
Св = 27548 = 34425 рублей.
Стоимость одного часа работы всего комплекса машин:
Ск = 432 + 1425 + 34425 = 91875 рублей.
Определим затраты на одну транпортировку сваебойной установки:
Ст1 = 91875 * 4 = 3675 рублей
где 4 – продолжительность одной транспортировки сваебойной установки.
Определяем себестоимость транспортировок сваебойной установки на строительные объекты в течении года:
С1 = 3675 * 96 = 35280 рублей.
Данные расчета заносим в таблицу 3.2.
Рассчитываем приведенные затраты на транспортировку внедряемого дизель-молота СП-6Б.
Шланговый дизель-молот СП-6Б смонтирован на базе экскаватора ЭО-4321 имеющего пневмоколесный ход. Поэтому перебазировка шлангового дизель-молота СП-6Б не требует использования автотягача и трейлера. Дизель-молот может переезжать своим ходом с одного объекта на другой по любым дорогам.
Определим стоимость капитальных вложений на транспортировку дизель-молота.
Стоимость капитальных вложений складывается из суммы балансовой стоимости дизель-молота СП-6Б и экскаватора ЭО-4321.
Балансовая стоимость дизель-молота СП-6Б – 12660рублей.
Балансовая стоимость экскаватора ЭО-4321 – 326000рублей.
К2 = 12660 + 326000 = 338660 рублей.
Рассчитываем себестоимость транспортировки дизель-молота на строительные объекты в течении года.
Стоимость одной машиносмены работы шлангового дизель-молота СП-6Б на базе ЭО-4321 – 480 рублей (дополнение к ценнику N2 n23).
Определим стоимость одной часа работы шлангового дизель-молота СП-6Б на базе ЭО-4321:
Сд = 4808 = 60 рублей.
Определим затраты на одну транпортировку дизель-молота:
Ст2 = 60 * 3 = 180 рублей
где 3 – продолжительность одной транспортировки дизель- молота.
Определяем себестоимость транспортировок дизель-молота на строительные объекты в течении года:
С2 = 180 * 96 = 17280 рублей.
Себестоимость транспортировок сваебойных установок на строительные объекты.
) Прямые затраты в расчете на 1 час работы
) Затраты по эксплуатации на 1 транспортировку установки
) Затраты по эксплуатации на транспортировку установки в течение года
Сваебойная установка СКВ-12 на базе гусеничного экскаватора Э-00111 транспортируется тягачом КрАЗ-258 на трейлере гп 20 т.
Шланговый дизель-молот СП-6Б на базе пневмоколесного экскаватора ЭО-4321 транспортируется на объект своим ходом
Итого себестоимость работ:
Исходные данные для расчета годового объема работ при транспортирование сваебойных установок по строительным нормам.
Себестоимость транспортировок
Балансовая стоимость машин и сваебойных установок
Сваебойная установка СКВ-12 - 32800
Шланговый дизель-молот СП-6Б - 12660
3. Расчет экономического эффекта.
Э =S1–S2 = (K1*Eн + C1)-(K2*EH + C2) = (342330*015+ +35280)-(338660*015+17280)= 866295–68079 =185505 рублей.
Вывод: Применение шлангового дизель-молот СП-6Б на базе пневмоколесного экскаватора ЭО-4321 оказалось выгоднее использования сваебойной установки СКВ-12 на базе гусеничного экскаватора Э-00111 из-за быстрой и оперативной перебазировки с одного объекта на другой без помощи автотягача и трейлера. Отказ от тягача с трейлером позволяет сократить расходы и время на перебазировку сваебойной установки.
Экономический эффект составляет 185505 рублей.
Рекомендуемые чертежи
Свободное скачивание на сегодня
Другие проекты
- 20.08.2014