Автогрейдер ДЗ-143 дипломная работа




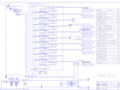

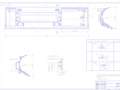
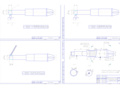
- Добавлен: 25.10.2022
- Размер: 3 MB
- Закачек: 5
Описание
Состав проекта
![]() |
![]() |
![]() ![]() ![]() ![]() |
![]() ![]() ![]() ![]() |
![]() |
![]() |
![]() ![]() ![]() ![]() |
![]() |
![]() |
![]() ![]() ![]() ![]() |
![]() |
![]() ![]() ![]() ![]() |
![]() |
![]() ![]() ![]() ![]() |
![]() |
![]() |
![]() ![]() ![]() ![]() |
![]() |
![]() ![]() |
![]() ![]() |
![]() ![]() |
![]() |
![]() ![]() ![]() |
![]() ![]() ![]() |
![]() ![]() ![]() |
![]() ![]() ![]() |
![]() ![]() ![]() |
![]() ![]() ![]() |
![]() ![]() ![]() |
![]() ![]() ![]() |
![]() ![]() ![]() |
![]() ![]() ![]() |
![]() |
![]() |
![]() ![]() |
![]() |
![]() ![]() |
![]() ![]() |
![]() ![]() |
![]() ![]() |
![]() ![]() |
![]() ![]() |
![]() ![]() |
![]() |
![]() ![]() ![]() ![]() |
![]() ![]() ![]() ![]() |
![]() ![]() ![]() ![]() |
Дополнительная информация
ПРИСПОСОБА.dwg

Неуказанные предельные отклонения размеров
ТЕХНОЛОГИЧЕСКИЙ ПРОЦЕСС ВОССТАНОВЛЕНИЯ.dwg

восстановления валика
Неуказанные предельные отклонения размеров:
ОТВАЛ.dwg

заподлицо с основным материалом
врезание в материал при этом
* Размеры для справок.
Обозначение и изображение шва
№1 ГОСТ 5264-80-Т1-&i6
№2 ГОСТ 5264-80-Т1-&i6
СХЕМА ГИДРАВЛИЧЕСКАЯ.dwg

Насос-дозатор ХУ85-101
Распределитель 346 3ккккк3
Гидрораспределитель
Клапан предохранительный
Гидроусилитель 7772А.011-1А-В4
Фильтр линейный 11.32-254-У2
Регулятор потока МПГБ5-22М
Рабочее давление 10МПа
Рабочая жидкость - масло индустриальное
Схема гидравлическая
АВТОГРЕЙДЕР.dwg

Боковой выос грейдерного отвала
в обе стороны относительно тяговой рамы
Кабина одноместная закрытого типа
* Размеры для справок
БЖД.dwg

еплоноситель охлаждающая
еплопроизводительность
емпература теплоносителя
отребляемая мощность
Основные данные кондиционера АК - 150УХЛ.5.01
Схема расположения кондиционера
Воздухораспределител?
Механизация.dwg

Технологическая схема
комплексной механизации
возведения зеляного
3 Конструкторский расчет.doc
1 Тяговый расчет автогрейдера
Тяговый расчет заключается в определении силы тяги на валу ведущих колес и площади поперечного сечения срезаемой стружки грунта исходя из свободной силы тяги автогрейдера ДЗ-143 равной φсц×Gсц 14
Рисунок 3.1 – Схема усилий к тяговому расчету автогрейдера
Исходные данные для расчета
Сила тяжести автогрейдера G кН 131
Режим работы установившийся
Категория разрабатываемого грунта III
Удельное сопротивление грунта резанию к кНм2 140
Коэффициент внутреннего трения грунта f 073
Коэффициент трения грунта об отвал f1 075
Максимальная глубина резания h м 008
Угол захвата ножа α град. 90
Угол резания ножа град. 45
Тяговый расчет автогрейдера производится при следующих условиях: перемещение автогрейдера происходит по участку земляного полотна не имеющего продольного уклона при установившемся режиме работы. Грейдерный отвал всей длиной погружен на глубину резания h. Силы инерции в расчете не учитываем.
Далее приведем тяговый расчет автогрейдера 14 .
Для нормальной работы автогрейдера необходимо соблюдение следующего условия
Pк ≥ Wраб ≤ φсц × Gсц ( 3.1 )
где Pк – сила тяги на ведущих колесах кН;
Wраб – общее сопротивление при установившемся рабочем режиме кН;
φсц – коэффициент сцепления ведущих колес с грунтом φсц=075 14
Gсц – сцепной вес автогрейдера кН.
Общее сопротивление при установившемся рабочем режиме складывается из следующих составляющих
Wраб = Wр + Wп + Wв + Wт ( 3.2 )
где Wр – сопротивление грунта резанию ножом кН;
Wп – сопротивление поступательному перемещению перед отвалом
призмы волочения грунта кН;
Wв – сопротивление грунта при движении его вверх по отвалу кН;
Wт – сопротивление перекатыванию колес кН;
Определим сопротивление Wр
где к – удельное сопротивление грунта резанию кНм2;
F – площадь поперечного сечения вырезаемой стружки м2.
F = × φсц × G ( кк × m ) ( 3.4 )
где – коэффициент использования сцепного веса автогрейдера;
G – сила тяжести автогрейдера кН;
кк – удельное сопротивление грунта копанию кНм2;
m – коэффициент учитывающий неравномерность сечения стружки при
= 045 14 ; кк = 240 кНм2 14 ; m = 135 14 .
F = 045 × 075 × 131 ( 240 × 135 ) = 013 м2.
Wр = 140 × 013 = 182 кН.
Определим сопротивление Wп
Wп = Qгр × f ( 3.5 )
где Qгр – вес призмы грунта перед отвалом кН;
f – коэффициент внутреннего трения грунта.
Qгр = Vф × λ ( 3.6 )
где Vф – объем призмы волочения перед отвалом м3 ;
λ – насыпной вес призмы волочения кНм3 .
Vф = ( H – hср)2 × l × кз (2 × tgφ ) ( 3.7 )
где Н – высота отвала м;
hср – среднее значение глубины резания м;
кз – коэффициент заполнения отвала;
φ – угол естественного откоса грунта град.
Н = 062 м; кз = 093 14 ; φ = 35 град. 14 .
hср = 008 4 = 002 м;
Vф = ( 062 – 002 )2 × 65 × 093 ( 2 × tg35) = 155 м3 ;
Qгр = 155 × 160 = 248 кН.
Wп = 248 × 073 = 181 кН.
Определяем сопротивление Wв
Wв = Qгр × cos2 × f1 ( 3.9 )
где – угол резания ножа град. ;
f1 – коэффициент трения грунта об отвал.
Wв = 248 × cos245 × 075 = 93 кН.
Определяем сопротивление Wт
где – коэффициент сопротивления качению колес по грунту;
Wт = 131 × 016 = 210 кН.
Таким образом общее сопротивление равно
Wраб = 182 +181 + 93 + 210 = 666 кН.
Максимальная сила тяги автогрейдера определяемая по сцепному весу автогрейдера равна
φсц × Gсц = φсц × 0 × G ( 3.11 )
где φсц – коэффициент сцепления ведущих колес с грунтом;
φсц × Gсц = 075 × 082 × 131 = 806 кН.
Значит условие ( 5.1 ) выполняется то есть Wраб φсц × Gсц
Определяем величину тяговой силы
Рк = Me × iт × м ( rc × 1000 ) ( 3.12 )
где Me – максимальный крутящий момент на валу двигателя Н×м;
м – коэффициент полезного действия трансмиссии;
rc – силовой радиус колеса м.
Me = 641 Н×м; м = 097.
где rст – статический радиус колеса rст = 06 м;
rc = 093×06 = 056 м.
Рк = 641 × 90 × 097 ( 056 × 1000 ) = 100 кН.
Следовательно условие ( 5.1 ) выполняется то есть Рк > Wраб.
Таким образом в тяговом расчете были определены: площадь поперечного сечения вырезаемой стружки грунта F = 013 м2; общее сопротивление при установившемся рабочем режиме автогрейдера Wраб = 666 кН; а также величина силы тяги колес Рк = 100 кН.
2 Расчет тяговой рамы на прочность
Задачей расчета является проверка работоспособности тяговой рамы при использовании дополнительного оборудования в рассматриваемом расчетном положении.
Сила тяжести автогрейдера приходящаяся на
его передний мост G1 кН 350
его задний мост G2 кН 960
Сила тяжести тяговой рамы Gтр кН 140
Колесная база машины L м 584
Положение кромки отвала l1 м 561
Положение центра тяжести автогрейдера
( по продольной оси машины ) l2 м 15
Положение центра тяжести автогрейдера по вертикали H м 17
Рисунок 3.2 – Схема действия усилий для расчета тяговой рамы.
Расстояние от оси О1О2 ( рисунок 3.2 ) до точки приложения
силы тяжести тяговой рамы a1 м 36
Расстояние от оси О3О4 ( рисунок 3.2 ) до точки приложения
силы тяжести тяговой рамы а2 м 224
Расчет на прочность тяговой рамы производится при следующих условиях: автогрейдер ДЗ-143 движется по горизонтальному участку на первой передаче со скоростью 25 42 кмч. Отвал внезапно уперся в непреодолимое препятствие и произошла остановка автогрейдера до полного буксования. Наиболее неблагоприятные условия при этом складываются когда наезд на препятствие происходит краем выдвинутого в сторону отвала.
Положение автогрейдера и тяговой рамы соответствующее этому случаю изображено на рисунке 3.2 на котором обозначено:
О – конец режущей кромки ножа отвала;
О1 и О2 – проекции середины балансира на опорную поверхность;
О3 и О4 – точки контакта передних колес автогрейдера с опорной поверхностью;
Са – центр тяжести автогрейдера;
Сm – точка приложения силы тяжести тяговой рамы;
G1 и G2 – силы тяжести автогрейдера приходящиеся на его передний и задний мосты соответственно;
Gтр – сила тяжести тяговой рамы;
Ри – равнодействующая сил инерции приложенная в центре тяжести машины;
Ry – боковое усилие в точке О;
Rz – вертикальное усилие в точке О;
Z1 Z2 Z 3 Z4 – вертикальные реакции;
Y1 Y2 – боковые усилия действующие на переднем и заднем мостах автогрейдера соответственно.
Принимаем что боковая реакция действующая на задний мост (ось О1О2 ) равна нулю то есть все сцепление идет только на создание силы тяги. Боковая реакция действующая на передний мост возникает от эксцентричного приложения сил сопротивления на отвал.
Далее произведем расчеты указанных сопротивлений и усилий 14 .
Определяем вертикальное усилие возникающее на конце режущей кромки ножа отвала
Rz = ––––––––––––––––––––––––––––––––––– ( 3.13 )
[ 1 + f1 ( ctg – f1 × tg )] – ( L – l1) × φ L
где G2 – сила тяжести автогрейдера приходящаяся на его задний мост кН;
φ – коэффициент использования сцепного веса автогрейдера;
Ри – равнодействующая сил инерции кН;
Gтр – сила тяжести тяговой рамы кН;
f1 – коэффициент трения грунта о сталь;
– угол резания ножа отвала град.;
L – колесная база машины м;
l1 – положение кромки отвала м.
φ = 075 14 ; f1 = 075 14 .
Ри = ( кд – 1 ) × φ× G2 ( 3.14 )
где кд – коэффициент динамичности кд = 15 14 .
Ри = ( 15 – 1 ) × 075 × 96 = 36 кН.
Rz = ––––––––––––––––––––––––––––––––––––––––––––––––––––– =
[ 1 + 075 ( ctg 45 – 075 × tg 45 )] – ( 584 – 561) × 075 584
Определяем горизонтальное усилие возникающее на кромке ножа отвала
Rx = ( G2 + Rz × ( L – l1 L )) × φ + Ри – Gтр × f1 ( 3.15 )
Rx = ( 96 + 1543 × ( 584 – 561 584 )) × 075 + 36 – 14 × 075 =
Определяем боковое усилие действующее на передний мост автогрейдера
Y1 = [ G1 + ( l1 L ) × Rz + ( H L ) × Pи + ( a1 L ) × Gтр ] × φ max ( 3.16 )
где G1 – сила тяжести автогрейдера приходящаяся на
его передний мост кН;
Н – положение центра тяжести автогрейдера по вертикали м;
а1 – расстояние от оси О1О2 до точки приложения силы тяжести тяговой
φ max – максимальный коэффициент бокового сдвига.
φ max = φ + ( 3.17 )
где – коэффициент сопротивления перекатыванию движителя по грунту
φ max = 075 + 016 = 091.
Y1 = [ 35 + ( 561 584 ) × 1543 + ( 17 584 ) × 36 + ( 36 584 ) × 14 ] ×
Как уже говорилось ранее боковое усилие действующее на задний мост автогрейдера равно нулю т.е. Y2 = 0.
Определяем боковое усилие действующее на режущей кромке ножа отвала в точке О
Ry = Y1 + Y2 ( 3.18 )
Ry = 6273 + 0 = 6273 кН.
Определяем вертикальные реакции грунта действующие на передний и задний мосты
Z1 = ( G2 2 ) – [ Ри × Н (2 × L)] + Rz×[( L – l1) L] + ( Gтр×а1) L ( 3.19 )
Rz – вертикальное усилие возникающее на конце режущей кромки ножа
Z1=(96 2)– [36 × 17(2×584)]+1543 ×[( 584 – 561) 584] +(14×36) 584 =
Z2 = ( G2 2 ) – Ри × H ( 2×L) + Gтр × a2 L ( 3.20 )
где а2 – расстояние от оси О3О4 до точки приложения силы тяжести тяговой
Z2 = ( 96 2 ) – 36 × 17 ( 2 × 584 ) + 14 × 224 584 = 481 кН;
Z3 = (G1 2) + Ри × Н (2 × L) + ( Rz × l1 ) L + ( Gтр × a1 ) L ( 3.21 )
Z3 = (35 2) + 36 × 17 (2 × 584) + ( 1543 × 561) 584 + (14 × 36) 584 =
Z4 = (G1 2) + Ри × H (2×L) + ( Gтр× a1 ) L ( 3.22 )
Z4 = (35 2) + 36 × 17 ( 2×584 ) + ( 14 × 36 ) 584 = 314 кН.
Определяем усилия в шаровом шарнире тяговой рамы пользуясь схемой на рисунке 3.2 14 .
Заменяем шарнир Ош равновеликой системой сил Xш Yш Zш .
Определяем горизонтальное усилие в шарнире
Xш = Rx + ( Gтр + Rz ) × f1 ( 3.23 )
где Rx – горизонтальное усилие действующее на конце режущей кромки
ножа отвала определенное по формуле ( 3.15 ) кН;
Rz – вертикальное усилие действующее на конце режущей кромки ножа
отвала определенное по формуле ( 3.13 ) кН;
f1 – коэффициент трения грунта о сталь.
Рисунок 3.3 – Схема сил действующих на шаровой шарнир
Хш = 17797 + ( 14 + 1543 ) × 075 = 20004 кН.
Усилие Хш в данном случае является преобладающим поэтому рассматриваемое расчетное сечение проверяем на прочность по горизонтальному усилию Хш которое подвергает тяговую раму деформации – растяжение-сжатие.
Необходимо чтобы выполнялось следующее условие
где р – напряжение в расчетном сечении возникающее при растяжении
[р] – допускаемое напряжение растяжения кНм2 ;
к – общий запас прочности.
Для стали 3 ГОСТ 380-71 [р] = 9×104 кНм2 1 ; к = 13 14 .
Напряжение в расчетном сечении определяется по формуле
где F – площадь расчетного сечения м2 ;
Хш - горизонтальное усилие в шаровом шарнире тяговой рамы кН.
Тяговая рама представляет собой V – образную сварную конструкцию изготовленную из прокатной угловой равнополочной стали ГОСТ 8509-72 номер проката 14. Таким образом расчетное сечение коробчатого вида имеет площадь
F = 10932 × 10-4 м2
тогда напряжение в расчетном сечении равно
р = 20004 ( 10932 × 10-4 ) = 18×104 кНм2.
Проверим условие ( 3.24 )
р ≤ 9×104 13 = 69×104 кНм2.
Следовательно условие ( 3.24 ) выполняется.
Таким образом тяговая рама автогрейдера ДЗ-143-2 удовлетворяет прочностным расчетам и является работоспособной при использовании дополнительного оборудования.
3 Расчет на прочность рабочего органа автогрейдера
Задача расчета на прочность заключается в проверке на прочность ползунов и направляющих по напряжениям возникающим в их сечениях от действия различных нагрузок.
МатериалСталь 35 ХГСА
Максимальная реакция грунта
приложенная на конце отвала R кН36
Угол резания d град58
Допустимое напряжение стали [s] МПа500
Схема сил приведена на рисунке 3.4
Рисунок 3.4–Схема сил для расчета рабочего органа.
За расчетную схему принята консольная статически определимая балка защемленная одним концом. Действие внешних сил приводит к сложному напряженному состоянию (изгиб с кручением стержня).
Действие результирующей внешней силы для расчета представлено горизонтальной и вертикальной составляющими.
Вертикальная составляющая равна
Горизонтальная составляющая равна
Крутящий момент определяется как
Эпюры моментов и перерезывающих сил представлены на рисунке 3.5
Рисунок 3.5–Эпюры моментов и перерезывающих сил для расчета рабочего органа.
Анализ эпюр внутренних сил показывает что опасное сечение находится в защемлении.
Для дальнейших расчетов определим геометрические характеристики опасного сечения (рисунок 3.6)
Рисунок 3.6–Схема для определения центра тяжести.
Согласно рекомендациям изложенным в 16 трапециидальное сечение заменяется на прямоугольное (рисунок 3.7).
Рисунок 3.7–Схема замены сечения.
Расчетное эквивалентное сечение принято следующих размеров (рисунок 3.8).
Рисунок 3.8–Геометрические параметры сечения.
Так как сечение находится в сложном напряженном состоянии то для определения опасной точки рассмотрим несколько точек (рисунок 3.9).
Рисунок 3.9–Схема для определения опасной точки.
Напряжение в точке В определяем по формуле 16
где WZ WY–моменты сопротивлений см3.
Напряжение в точке L определяется по формуле 16
В результате расчета определено что напряжение в опасной точке L меньше допустимого напряжения (1339 МПа500МПа). Таким образом геометрические параметры направляющих и ползунов удовлетворяют условиям прочности.
Для обеспечения прочности отвала переменной длины в рабочем положении в качестве упоров ограничивающих вылет боковых секций приняты уголки равнобокие №2 ГОСТ 8509–75 16. Геометрические параметры упоров и схемы их зацепления приведены на рисунке 3.10.
Рисунок 3.10–Геометрические параметры и схемы зацепления упоров.
2 Механизация строительства.doc
Проектирование механизации строительства дорог связано с определением типов машин и их количества которые впоследствии объединяются в комплекты и комплексы. Оптимальным будет тот парк машин использование которого обеспечит выполнение заданных объёмов работ в заданные сроки с минимальными денежными энергетическими трудовыми и другими видами затрат.
Общепринятым методом определения оптимального состава специализированного комплекта машин (СКМ) в настоящее время является сравнение технико-экономических показателей различных комплектов машин для принятого темпа строительства.Целью данного раздела дипломного проекта является определение количественных составов СКМ и сопоставление их технико-экономических показателей.
1Описание объекта строительства
Вид работ: возведение земляного полотна.
Место строительства: Омская область.
Объём работ: 700000 м3.
Категория грунта – I.
Параметры объекта: высота насыпи Н = 08 м ширина дороги L = 15 м уклон m = 1:115.
Ведущая машина: скрепер самоходный объём ковша ДЗ - 11 q = 9 м3.
Дальность транспортирования: 05; 10; 15; 20 км.
2 Технология механизация и организация строительства
2.1 Технология производства работ
Технологическая схема строительства земляного полотна и
задействованный при этом комплект машин приведён в таблице 2.1
Таблица 2.1-Схема строительства земляного полотна
Срезка растительного слоя
Автогрейдер ДЗ-143 ДЗ-143М
Разработка и премещение грунта в I-й слой насыпи
Разработка и премещение грунта в II-й слой насыпи
Планировка верха земляного полотна
Прикатка верха земляного полотна
Планирование откосов насыпи
При разработке карьера мы считаем что вскрышные работы проведены и грунт находится в состоянии оптимальной влажности.
2.2 Механизация строительства
Для устройства земляного полотна формируется специализированный комплект машин (СКМ) ведущей машиной в котором является скрепер ДЗ - 11 и модернизированный автогрейдер ДЗ-143М.
Для срезки растительного слоя применяем модернизированный автогрейдер ДЗ – 143М.
Для разработки грунта в резерве и доставке его тело земляного полотна используется прицепной скрепер ДЗ-11.
В разделе механизация строительства будут рассчитаны два варианта СКМ которые мы условно назовём “старый” или СКМ-1 и “новый” – CКМ-2. Соответственно СКМ-1 работает по схеме с базовым автогрейдером ДЗ – 143 а СКМ-2 с модернизированным автогрейдером ДЗ-143М. Это даст нам возможность сравнить эффективность изменения конструкции автогрейдера.
В таблице 2.2 приведены марки машин используемых в двух вариантах СКМ с указанием их цены мощности силовой установки и технологических операций на которых они используются.
Таблица 2.2 – Марки машин используемых в СКМ.
Разработка и перемещение грунта
Планировка верха земляного
Прикатка верха земляного
3 Организация производства работ
Под организацией работ понимается установление сроков выполнения работ режима сменности работы обеспечение строящегося объекта материалами машинами транспортными средствами трудовыми ресурсами электроэнергией связью и другими ресурсами.
В дорожном строительстве наибольшее распространение получил поточный метод организации работ. Основным показателем потока является его темп то есть объём готовой продукции выпускаемый в единицу времени. Темп потока t определяется выражением 12
Определение темпа работ
Темп работ t м3смену определяется по формуле:
гдеVобщ – общий объём работ м3 Vобщ = 700000 м3;
Nрд – число рабочих смен в строительном сезоне. В Омской области строительный сезон начинается с 25.05 по 8.10 число нерабочих дне по метеоусловиям – 5. По календарю определяем число рабочих дней Nрд = 85. Число рабочих смен определяется по формуле:
гдеКсм – коэффициент сменности Ксм = 14 2; примем Ксм = 14.
3.1 Определение длины сменной захватки
Рисунок 2.1- Поперечное сечение полотна
По рисунку 2.1 определяем расстояния l1 l2 и площади поперечного сечения насыпи.
Общая площадь поперечного сечения насыпи м2 определяется по формуле:
гдеН – высота насыпи Н = 08 м;
расстояние l2 м определяется по формуле:
Поперечные сечения слоёв определятся соответственно по формулам:
гдеh – высота насыпи h = 04 м;
расстояние l1 м определяется по формуле:
Длина сменной захватки мсмену определится по формуле:
гдеt – темп работ м3смену t = 5882 м3смену.
3.2 Определение эксплуатационных производительностей машин
Эксплуатационные производительности машин м2см входящих в составы СКМ-1 и СКМ-2 кроме автогрейдера ДЗ – 143 и ДЗ-143М определим по формуле 12
Квi – коэффициент использования i-й машины по времени в течении смены учитывающий непроизводительные затраты времени ма шины по техническим технологическим причинам.
Значения эксплуатационных производительностей машин определённых по формуле (2.6) значения сменных производительностей средств механизации определённые по ЕниР и принятые значения коэффициентов использования по времени в течение смены для машин входящих в составы СКМ-1 и СКМ-2 кроме скрепера приведены в таблице 2.3.
Работа по срезке растительного слоя производится автогрейдером ДЗ-143. Объём работы в смену м2смену определяется по формуле:
гдеLп – длина полосы (см. рисунок 1) Lп = 194 м.
Сменная эксплуатационная производительность автогрейдера при срезке растительного слоя м2смену определяется по формуле:
Производительность автогрейдера при планировании откосов производим по формуле
где L – длина технологической захватки м; bз – ширина захватки м; n – число проходов; tср – среднее время операций за один проход.
t1 – время на перемещение отвалом грунта с; t2 – время подъёма отвала t2=5c; t3 – время на переключение передач и повороты t3=40 с; t4 – время на опускание отвала в рабочее положение t4=3с.
Определим сменную производительность для базовой машины ДЗ - 143
Определим сменную производительность для модернизированной
Необходимое число машиносмен определяется по формуле:
гдеVсм – сменный объём работ;
П – производительность.
Расчёт необходимого числа машиносмен сведён в таблице 2. 4.
Разработка и перемещение грунта в первый слой насыпи
Разработка грунта производится скрепером самоходным (см. тех. характеристику стр. 80 1). Производительность скрепера м3смену определяется по формуле:
гдеНВ – норма времени выполнения операции копания час определяется по формуле:
гдеНВо – основная норма времени час НВо = 25 часа (табл.1 стр. 82 1);
Д – добавочное время час Д = 017 часа (табл.1 стр. 82 1);
lтр – дальность транспортирования.
Результаты расчёта по формуле (1.13) сведены в таблице 2.3.
Таблица 2.3- Расчёт производительности скрепера
Дальность транспортирования м.
Производительность скрепера ДЗ-11
Число машиносмен необходимых для выполнения общего объёма работ Vобщ определяется по формуле:
гдеt – темп работ м3смену t = 5882 м3смену;
Результаты расчёта по формуле (2.15) сведены в таблице 2.4.
Таблица 2.4- Число машиносмен скреперов
В качестве расчётного значения принимаем число скреперов Nскр = 21 расчётная производительность
Объём работы в смену м3смену определяется по формуле:
гдеLсм – длина захватки Lсм = 4539 м;
S1 – площадь поперечного сечения первого слоя м2 S1 = 672 м2.
Необходимое число скреперов:
= 1056 примем Nскр = 11.
Уплотнение первого слоя насыпи
Уплотнение насыпи проводим только тяжёлым катком ДУ-29 т.к. при отсыпке скрепер достаточно уплотняет насыпь и проходов среднего катка не требуется. Уплотнение проводим при четырёх проходах по одному следу. Объём работы в смену м3смену определяется по формуле (2.16). 3050 м3смену. Сменная производительность катков при уплотнении насыпи м3сменуопределяется
гдеТсм – продолжительность смены Тсм = 82 часа;
НВ – норма времени выполнения операции часов для ДУ-29: НВ = 022 часа.
Производительность ДУ-29:
Необходимое число машиносмен катков определяется по формуле (2.15) расчёт сведен в таблице 2.4.
Разработка и перемещение грунта во второй слой насыпи
S2 – площадь поперечного сечения второго слоя м2 S2 = 624 м2.
Необходимое число машиносмен скреперов определяется по формуле (2.12) расчёт сведен в таблице 2.4.
Уплотнение второго слоя насыпи
Объём работы в смену м3смену определяется по формуле (2.18). 2832 м3смену. Сменная производительность катков при уплотнении насыпи м3сменуопределяется
Необходимое число машиносмен определяется по формуле (2.12) расчёт сведен в таблице 2.4.
Планировка верха полотна производится автогрейдером ДЗ-143 илиДЗ-143М. Объём работы в смену м2смену определяется по формуле:
гдеВ – ширина дороги м В = 15 м.
Сменная производительность автогрейдера при при планировке земляного полотна м2смену определяется по формуле (2.11).
Прикатку полотна осуществляем средним катком ДУ-31А. Объём работы в смену м2смену определяется по формуле (2.17). 6808 м2смену. Сменная производительность катка при уплотнении поверхности м2смену определяется по формуле:
гдеНВ – норма времени выполнения операции часов для ДУ-31А при уплотнении поверхности НВ = 079 часа часа (табл.3 стр.104 1).
Планировка откосов насыпи
Планирование откосов насыпи производим автогрейдером ДЗ-143. Способ
планировки – рабочий ход в двух направлениях. Ширина откоса м определяется по формуле:
гдеН – высота насыпи м Н = 08 м;
m – уклон насыпи m = 1115.
Объём работы в смену м2смену определяется по формуле:
необходимое число машиносмен определяется по формуле (2.12) расчёт сведен в таблице 2.4.
Таблица 2.4-Технологический расчёт строительства земляного полотна
Технологическая операция
Сменная производительность
Необходимое число машиносмен
Рассматривая весь технологический процесс можно отметить что при использовании модернизированного автогрейдера ДЗ-143М количество машиносмен существенно снижается.
Для ДЗ -143 – 134 машиносмена
Для ДЗ -143М – 043 машиносмена
В таблице 2.5 сведен расчёт необходимого количества машиносмен скрепера при всех дальностях транспортирования.
Таблица 2.5- Количество машиносмен скреперов
Разработка и перемещение грунта в I-й слой насыпи
Разработка и перемещение грунта в II-й слой насыпи
3.3 Выбор количества машин в комплекте
Основываясь на данных таблицы 2.4 окончательно принимаем следующий комплекты машин:
Таблица 2. 6 -Комплекты машин
Делая вывод по главе можно отметить что использование модернизированного автогрейдера ДЗ – 143М позволяет уменьшить количество автогрейдеров во втором комплекте СКМ 2 что выгодно его отличает от базового комплекта т.к. при одинаковом объёме работы требуется меньшее количество машин и положительно скажется на эффективности строительства земляного полотна.
Список использованных источников.doc
Бируля А. К. Эксплуатация автомобильных дорогА. К. Бируля. – М.: НТИ Автотрансп. Лит 1956. 340 с.
Борадочёв И. П. Справочник конструктора дорожных машин И. П. Борадочёв- Изд. 2-е перераб. и доп. М.: Машиностроение 1973. – 503 с.
Борадочёв И. П. Дорожные машины И. П. Борадочёв В. А Васильев.- М.: Машгиз 1953. – 506 с.: ил.
Горелышев Н. В. Технология и организация строительства автомобильных дорог Н. В. Горелышев. - М. 1992. – 551с.
Дорожные машины. Ч. 1. Машины для земляных работ Т. В. Алексеева К. А. Артемьев А. А. Бромберг и др.- Изд. 3-е перераб. и доп. –М.: Машиностроение 1972. –504 с.
Строительные нормы и правила. Автомобильные дороги: СниП 3.06.03-85: Срок введ. в действие 1.01.86 Госстрой СССР . – М.: ЦНТП Госстроя СССР 1986.- 112 с
5 Безопасность жизнедеятельности.doc
1 Анализ вредных факторов возникающих при работе
В процессе труда человек-оператор взаимодействует с производственной обстановкой и окружающей средой. В этом случае организм человека подвергается неблагоприятному воздействию ряда факторов :
- отклонение от норм микроклимата;
- производственный шум;
- систематическое воздействие вибрации;
- производственная пыль;
- воздействие токсичных веществ и газов;
- постоянное напряжение зрения при недостаточном освещении;
- ограниченный обзор;
- устойчивость машины.
Влияние всех этих факторов может вызвать профессиональное заболевание либо отклонение здоровья человека-оператора.
Для обеспечения безопасности человека для нормальной его работоспособности и в конечном итоге повышения производительности планировочных работ необходимо решить задачу по устранению перечисленных вредных факторов или уменьшению их воздействия до предельно допустимых норм установленных ГОСТами ССБТ и СН и П.
Производственный шум имеющий высокий уровень вызывает притупление слуха отрицательно сказывается на нервной системе человека при этом повышается кровеносное давление происходит ослабление внимания. Основным источником шума при работе автогрейдера является двигатель внутреннего сгорания. Другие источники шума – трансмиссия ходовое оборудование и прочие элементы машины их уровень шума сравнительно ниже уровня шума двигателя. ГОСТ 12.1.003-83 устанавливает допускаемые значения шумовых характеристик машин и оборудования. По этому ГОСТу уровень шума должен находиться в пределах 89 95 дБ. Для предотвращения или уменьшения уровня шума от двигателя необходимо проводить своевременный качественный ремонт и техническое обслуживание всех систем и механизмов двигателя. Уменьшает уровень шума звукоизоляция шумных узлов машины в частности на автогрейдере для понижения уровня шума от работы двигателя установлен звукоизолирующий капот. Кабина человека-оператора одновременно служит тепло – и звукоизоляционным устройством рабочего места. Звукоизолирующая кабина позволяет снизить шум от 20 до 30 дБ в средних и высокочастотных диапазонах.
Длительное воздействие вредных факторов микроклимата может вызвать тепловой ( солнечный ) удар ( в летнее время года ); при высокой влажности происходит нарушение терморегуляции тела человека. Оптимальные и допустимые нормы температуры относительной влажности и скорости движения воздуха в рабочей зоне машины установлены ГОСТ 12.2.023-76 7 ГОСТ 12.2.019-76 6 . В них сказано что в кабине принудительная вентиляция должна обеспечить подачу свежего воздуха в количестве не менее 30 м3ч на одного человека. Температура воздуха в кабине должна быть на 2-3 С выше температуры наружного воздуха но не ниже +14 С и не выше +28 С при относительной влажности 40-60 %. Естественная вентиляция обеспечивается люками открывающимися окнами которыми снабжена кабина автогрейдера ДЗ-143-2. Для очистки обзорных стекол кабины от атмосферных осадков предусмотрены стеклоочистители.
Оператор автогрейдера подвергается общей вибрации которая вызывает сотрясение всего организма человека а также локальной вибрации. Систематическое воздействие вибрации может вызвать виброболезнь с необратимыми патологическими изменениями. Причинами возникновения вибрации на автогрейдере являются неуравновешенность вращающихся масс и возвратно-поступательно движущихся. Дебаланс приводит к возникновению центробежных сил которые вызывают вибрацию. Действующие гигиенические оценки вибрации изложены в ГОСТ 12.1.012-90 5 . Методы и средства вибрационной защиты изложены в ГОСТ 12.4.064-78 8 . На автогрейдере ДЗ-143 установлена виброизоляция сидения человека-оператора по ГОСТ 12.2.023-76 7 которая представляет собой гидроамортизатор. Для снижения колебаний ( вибрации ) передаваемых от двигателя к раме или остову на автогрейдере предусмотрены амортизаторы резинометаллические устанавливаемые между двигателем и рамой.
Воздействие пыли и газов может привести к поражению органов дыхания человека-оператора. Особую опасность для здоровья человека представляют соединения окиси углерода окиси азота и альдегиды содержащиеся в отработавших газах двигателя. Источниками выделения токсичных компонентов являются системы выпуска питания смазки и вентиляции картерной полости двигателя. Для обеспечения защиты оператора от пыли газов а также атмосферных осадков люки и окна кабины автогрейдера герметизированы. Для предотвращения попадания пыли и газов через неплотности пола в области рычагов управления ручек руля педалей предусмотрены специальные кожухи прикрывающие эти неплотности. Интенсивный выход токсичных веществ при работе двигателя может являться результатом неправильной регулировки двигателя поэтому необходимо своевременно и тщательно проводить все плановые мероприятия по ремонту и техническому обслуживанию двигателя и автогрейдера в целом.
При неудовлетворительном освещении зрительная способность глаз снижается. СН и П II-4-79 17 предусматривает нормированные значения освещенности на рабочих местах при естественном и искусственном освещении. Для обеспечения нормальных условий эксплуатации механизмов и приборов внутри кабины автогрейдера освещенность должна быть не менее 50 лк. Величина освещенности приборов и указателей должна быть в пределах 03 11 лк. Днем естественное освещение в кабине автогрейдера реализуется через оконные проемы расположенные на боковых передней и задней стенках кабины. Для работы в темное время суток на автогрейдере предусмотрены фонари которые обеспечивают освещение рабочих органов и планируемой поверхности.
Для обеспечения хорошей обзорности по ГОСТ 12.2.023-76 7 кабина оборудована с четырех сторон окнами а также с боков кабины установлены зеркала заднего вида.
Опрокидывающий момент в результате которого автогрейдер может потерять устойчивость складывается из действия различных сил: реакции грунта на режущие грани рабочих органов воздействия сил инерций сил возникающих от уклона или подъема пути и других. Автогрейдер ДЗ-143 снабжен механизмом наклона передних колес тем самым увеличивается устойчивость автогрейдера обеспечиваются лучшие условия нагружения подшипников колес облегчается работа рулевого управления что непосредственно уменьшает утомляемость оператора автогрейдера.
C целью обеспечения пожарной безопасности кабина автогрейдера оснащается кронштейном для крепления огнетушителя а также крепления специального молотка для разбивания окон в случае когда использовать огнетушитель не удаётся и затруднено открывание дверей кабины.
В данном дипломном проекте рассматривается модернизированная конструкция автогрейдера ДЗ-143 добавляются дополнительные выдвижные секции отвала. При их полном выдвижении длина отвала составляет 4570 мм. Для обозначения кромок выдвинутых секций последние снабжаются габаритными указателями в виде красно-белых полос. Оператор при выдвижении секций подает звуковой сигнал для оповещения о возможной опасности.
2 Расчет кондиционера
Одним из основных компонентов микроклимата в кабине оператора является температура воздуха. Расчет системы кондиционирования нужен для правильного выбора который сможет поддерживать необходимую температуру воздуха в кабине оператора.
При расчете нужно учитывать что при температуре воздуха окружающей среды менее + 10 С температура воздуха в кабине оператора должна быть равна + 17 С при температуре наружного воздуха более + 10 С – не выше + 28 С. Скорость воздуха в кабине при температуре наружного воздуха менее + 10 С не выше 03 мс при температуре более + 10 С не выше 15 мс. Относительная влажность воздуха 40-60 % содержание пыли не более 10 мгм3 11 .
2.1 Определение количества вентиляционного воздуха
Количество вентиляционного воздуха определяется по формуле 11
L = Q C × ( tд – tn ) ( 5.1 )
где Q – выделение явного тепла Q = 738 кДж 11 ;
tд – температура воздуха в кабине в холодное время года tд = + 17С в теплое время года tд = + 28С ;
С – теплоемкость воздуха в кабине оператора.
С = Суд × ρ × V ( 5.2 )
где Суд – удельная теплоемкость воздуха Суд = 101 кДж кг × С ;
ρ – плотность воздуха ρ = 124 кг м3 ;
V – свободный объем в кабине автогрейдера V = 21 м3 .
С = 101 × 124 × 21 = 263 кДж.
Находим количество вентиляционного воздуха
- в холодное время года составит
L = 738 263 × ( 17 + 27 ) = 63 м3 г ;
- в теплое время года составит
L = 738 263 × ( 28 – 26 ) = 140 м3 г .
Потребляемую мощность определяем из выражения 11
N = ( Q × p × n ) ( 3600 × 102 × в × п ) ( 5.3 )
где Q – производительность определяемая по большому количеству
потребляемого воздуха Q = 140 м3 г ;
р – давление создаваемое вентилятором р = 20 × 103 Па ;
n – кратность воздухообмена n = 2 19 ;
в – коэффициент полезного действия вентилятора в = 055 19 ;
п - коэффициент полезного действия передачи п = 1 19 .
N = ( 140 × 20 × 2 ) ( 3600 × 102 × 055 × 1 ) = 27 кВт.
Определяем установочную мощность
Nуст = кз × N ( 5.4 )
где кз – коэффициент запаса кз = 13 11 ;
N – потребляемая мощность кВт.
Nуст = 13 × 27 = 351 кВт.
Эффективность фильтра для очистки воздуха определяем из выражения 11
Е = –––––––––– × 100 % ( 5.5 )
где С1 – концентрация пыли в неочищенном воздухе С1 = 50 мг м3 ;
С2 – концентрация пыли в очищенном воздухе С2 = 10 мг м3 .
Е = –––––––––– × 100 % = 80 % .
По определенной эффективности выбираем фильтр пористый смоченный масляный самоочищающийся ФС -111 с удельной пылеемкостью до 15 % от массы масла в ванной 11 .
Параметры фильтра ФС-111:
- начальное пылеудержание мг м3 – 10
- нормальная удельная нагрузка м3 м2 г – 4000
Определяем габариты по площади очищения поверхности 19
где g ф – удельная нагрузка фильтрующей поверхности g ф = 4000 м3 м2 г.
Fф = 140 4000 = 0035 м2
Определяем габариты масляной ванны 19
Количество масла определяем из условия пылеемкости 15 % от массы масла в ванне 19
m м = ( L × T × G 15 ) × 100 ( 5.8 )
m м = ( 140 × 240 × 0004 15 ) × 100 = 896 г.
2.3 Выбор калорифера
Выбираем калорифер с жидкостным теплоносителем. Нагрев теплоносителя от двигателя автогрейдера.
Определяем расход тепла на нагрев воздуха в кабине 19
Q = L × Cyд × ρ × V × ( tд – tn ) (5.9 )
Q = 140 × 101 × 124 × 21 × ( 17 + 27 ) = 1620105 Дж
Необходимое живое сечение в калорифере для прихода воздуха определяем из выражения 19
f = L × ρ ( 3600 × vp ) ( 5.10 )
где vp – скорость движения воздуха vp = 4 кг м2 с 19 .
f = 140 × 124 ( 3600 × 4 ) = 0012 м2.
Выбираем калорифер алюминиевый с живым сечением f = 00386 м2 площадью поверхности Fп = 25 Н м2 .
Определяем скорость теплоносителя в трубках радиатора из выражения 19
W = Q ( 3600 ×1000 × f тр × Тср ) ( 5.11 )
где Тср – температура теплоносителя Тср = 40 С 11
W = 1620105 ( 3600 ×1000 × 0000651 × 40 ) = 0176 м с
Проверим теплопередачу калорифера
Q к = Fп × к × ( Тср – t ср ) ( 5.12 )
где к – коэффициент теплопередачи;
к = А × ( L f ) 05 × [ W ( ρo × f тр ) ] 02 ( 5.13 )
где ρo – плотность теплоносителя кг м3
к = 50 × ( 140 00385 ) 05 × [ 0176 ( 1000 × 0000651 ) ] 02 =
Q к = 2597 × 231 × ( 40 – 5 ) = 209976 Вт .
По полученным данным выбираем кондиционер АК-150 УХЛ.5.01 19
Тип кондиционера радиаторный
Теплоноситель антифриз
Теплопроизводительность кВт 18 + 08
Температура теплоносителя на входе С 80 + 5
Потребляемая мощность при номинальной
производительности по воздуху Вт 120 + 12
3 Экологическая безопасность
Создание строительно-дорожных машин форсированных по мощностям и нагрузкам в конструкциях которых все более широко используются виброактивные рабочие органы неизбежно приводит к увеличению уровней шума и вибрации вредно воздействующих на операторов ( машинистов ) этих машин а при работе машины в черте жилой застройки – и к акустическому ( шумовому ) загрязнению окружающей среды. В связи с этим необходимо проводить мероприятия по устранению внешнего шума или снижению его до величины допускаемой ГОСТами ССБТ.
Внешний шум строительно-дорожных машин определяется санитарными нормами 1102-73 15 в которых говорится что на расстоянии 75 м от строительно-дорожной машины уровень звука не должен превышать величины 85 дБ.
Как уже говорилось в анализе вредных факторов основными источниками шума при работе автогрейдера является двигатель внутреннего сгорания.
Исследования по шумоизмерению показали что доля механического шума двигателя во внешнем шуме машины почти в два раза превышает долю шума выпуска ( с глушителем ) 10 . Это означает что установка глушителя на выпускной патрубок не способна защитить окружающую среду от шумового загрязнения в значительно степени.
На двигатель автогрейдера ДЗ-143 установлен звукоизолирующий капот (трехслойный ) состоящий из следующих слоев: металлический лист лист из звукопоглощающего материала перфорированный лист. В конструкции капота предусмотрены люки и съемные панели для обеспечения удобного доступа к различным узлам двигателя. Такой звукоизолирующий капот снижает уровень внешнего шума на 15 20 дБ.
Глушитель установленный в системе выпуска отработавших газов автогрейдера ДЗ-143 снижает уровень шума системы выпуска двигателя примерно на 20 дБ.
Картина экологической безопасности не будет полная без освещения вопроса защиты почв и гидросферы. С этой точки зрения нужно отметить что основным источником загрязнений такого вида являются поддоны картеры и прочие ёмкости содержащие ГСМ и рабочие жидкости. Предотвращение выброса подобных жидкостей возможно при периодическом контроле состояния уплотнительных устройств и заливных горловин. Потому соблюдение механиками и обслуживающем персоналом правил рабочей дисциплины простой и надежный путь предотвращения загрязнений почв и гидросферы.
1 Обоснование выбора машины.doc
В современных условиях повышение производительности труда в строительном производстве следует рассматривать с точки зрения применения новых нетрадиционных технологий максимального использования потенциальных возможностей средств механизации и широкого внедрения результатов научных разработок. Эти задачи могут быть успешно решены путем комплексной механизации и автоматизации технологических процессов внедрением скоростного строительства.
Процесс внедрения новой технологии строительства земляного полотна связан с необходимостью обеспечения ровности его поверхности и геометрических параметров поперечного и продольного профилей. Несоответствие проектным отметкам и недостаточная ровность поверхности земляного полотна приводит к перерасходу строительных материалов при сооружении слоев дорожной одежды .
Высокие требования к качеству технологических операций (в частности планирования) обеспечивающих ровность земляного полотна вступают в противоречие с производительностью машин занятых на этих операциях.
Наиболее распространенной машиной применяемой при планировании поверхности земляного полотна является автогрейдер. Профиль спланированной поверхности определяется положением рабочего органа машины во время процесса планирования. Управление отвалом является сложной задачей вместе с тем требования к точности соблюдения проектного профиля очень высоки. Поэтому их выполнение при ручном управлении отвалом требует многократных проходов машины по одному следу что приводит к снижению производительности.
Однако эти требования к профилю земляного полотна могут быть выполнены автогрейдером с системой автоматического управления (САУ) рабочим органом (РО). Вместе с этим существующие САУ РО не позволяют в пол-
ной мере реализовать максимальную рабочую скорость машины обеспеченную ресурсом двигателя по мощности а следовательно достичь высокой производительности при выполнении планировочных работ.
С другой стороны повышение производительности автогрейдера на планировочных работах с сохранением заданной точности возможно путем совершенствования конструкции рабочего органа. Изменяя длину отвала можно оказывать значительное влияние на производительность машины.
Таким образом совершенствование конструкции отвала автогрейдера и САУ РО с целью повышения производительности с обеспечением требуемого качества производства работ является актуальной научно-технической задачей.
Развитие строительного и дорожного машиностроения характеризуется появлением автоматизированных комплексов и систем машин широким применением машин с многоцелевым оборудованием развертыванием работ по созданию строительных манипуляторов и роботов. Возрастает число возможных вариантов параметров рабочих органов обеспечивающих оптимальное производство работ в различных условиях строительства при минимальных энергетических материальных и трудовых затратах. Принятие неоптимальных решений влечет за собой существенные потери .
Одним из основных показателей эффективности использования автогрейдера на планировочных работах является его производительность. Большая часть работ по совершенствованию автогрейдера направленных
на повышение производительности машины имеет целью модификацию отвала уменьшение числа проходов по обрабатываемому участку земляного полотна и по одному следу а также сокращение времени установки РО в требуемое положение перед рабочим проходом.
Модификация отвала например установка на него выдвижных гидро-управляемых боковых секций позволяет увеличить длину РО а следовательно и ширину захвата.
Недостатком такого рабочего органа является низкая производительность из-за повышения сопротивления грунта резанию вызванного нахождением на одном уровне нижних ножей основной и боковых секций в положении когда боковые секции не выдвинуты или выдвинуты частично по отношению к центральной. Это вызывает увеличение мощностных затрат на осуществление планировочных работ. С целью снижения сопротивления грунта резанию прибегают к уменьшению общего угла заострения нижних ножей. Однако уменьшение угла заострения ножей приводит к быстрому их затуплению и выкрашиванию снижению точности к увеличению энергоемкости процесса и стоимости производства планировочных работ.
Для устранения недостатков рассмотренной конструкции рабочего органа было предложено использовать рабочее оборудование включающее отвал состоящий из центральной секции с открытой с торцов и по краям нижней стороны внутренней пазухой в которой размещены боковые секции смонтированные на ползунах и направляющих. Направляющие выполнены в виде винтовых линий с подъемом по направлению к середине центральной секции. Каждый гидроцилиндр управления боковой секцией закреплен шарнирно корпусом на центральной секции и соединен штоком с боковой секцией посредством имеющего несколько степеней свободы шарнирного соединения.
Недостатками такого рабочего органа являются сложность конструкции большая металлоемкость и невысокая производительность автогрейдера при планировочных работах (длина отвала в рабочем положении не превышает 524 м).
Повышение производительности автогрейдера за счет сокращения числа проходов по обрабатываемому участку земляного полотна предлагается в различных работах. Информация о достижении требуемого качества поверхности земляного сооружения предоставляется механику - водителю с помощью устройства индикации.
Уменьшение количества проходов по одному следу за которое достигается требуемое качество поверхности земляного полотна возможно при условии точности управления рабочим органом.
В дорожном строительстве огромное значение имеет качество возводимого полотна. Его геометрические параметры такие как уклоны высотные отметки линейные размеры ровность поверхности и др. строго регламентированы СНиПом поэтому особое внимание в работах посвященных вопросу повышения точности планировочных работ уделяется совершенствованию САУ РО.
Заключение.doc
4 Технология ремонта.doc
Для рассмотрения технологического процесса восстановления детали в дипломном проекте восстановим изношенную резьбовую часть вала насоса. Дефект установлен путём осмотра замера резьбы резьбовым калибром 0-30. Рекомендуемый способ восстановления состоит из 3-х частей: 1) наплавка; 2) точение; 3) нарезка резьбы. Материал детали сталь 50Г ГОСТ 5632-72 твёрдость – HRc45 масса – 145 кг количество изделий – 1 шт.
Наплавку будем производить в среде углекислого газа т.к. вал является ответственной деталью с малым диаметральным размером из стали 50Г и с относительно небольшим износом (с.93 [1]).
Основными преимуществами наплавки в среде углекислого газа являются: а) отсутствие коробления детали; б) небольшие размеры дуги и сварочной ванны позволяющие работать во всех положениях детали; в) возможность механизации процесса наплавки деталей со сложными профилями изношенных поверхностей а также наплавки цилиндрических поверхностей диаметром менее 45 мм.
Восстановить изношенную резьбовую часть (М25×15) вала насоса изготовленного из стали 50Г. По ТУ изношенную резьбу вала можно восстановить наплавкой с последующей механической обработкой. Восстановление ведется в такой технологической последовательности: после мойки поверхность резьбы зачищают стальной щеткой до металлического блеска. Подготовленную резьбовую часть вала наплавляют на установке для наплавки в углекислом газе за 2 прохода до диаметра 28 мм. Наплавку ведут электродной проволокой Св-10Х13 диаметром 08 мм при величине тока 90А и напряжении 18-19В. Скорость подачи проволоки 235 мч; смещение электродной проволоки 3-5 мм; скорость наплавки 40 мч; вылет электродной проволоки 8 мм; шаг наплавки 3 мм; толщина слоя наплавки 1мм (с.109 [1]).
Нормирование наплавочных работ:
Определить норму времени и расход электродной проволоки на наплавку резьбовой части вала насоса. Номинальный диаметр резьбы 25 мм длина 15 мм. Величина износа 05 мм на сторону. Припуск на обработку 15 мм на сторону.
Определим вес наплавленного металла G по формуле:
где F – площадь поперечного сечения слоя наплавки см2;
L – резьбовой части 15 см;
γ – удельный вес металлического электрода γ =75 гсм3 (с.112[1]);
d – номинальный диаметр резьбы d=25 см;
– толщина слоя наплавки (величина износа плюс припуск на обработку) =02 см;
Подставляя существующие значения получим: .
Норму штучно-калькуляционного времени на наплавку определяем по формуле:
где ТО – основное время ч.;
КП – коэффициент учитывающий затраты вспомогательного и подготовительно-заключительного времени на обслуживание рабочего места отдых и естественные надобности КП =12 (с.117 [1]);
I – величина сварочного тока I=90 А;
аН – коэффициент наплавки аН =11-18 гА-ч.;
Расход электродной проволоки GЭ.П. при механизированной наплавке определяется по формуле:
где КЭ.П. – коэффициент расхода электродной проволоки с учётом потерь на угар и разбрызгивание КЭ.П. =11 (с.117 [1]);
Назначить режим резания и определить норму времени на обточку вала насоса после наплавки в среде защитного; вал длиной 320 мм длина резьбовой части 15 мм диаметр 25 мм после наплавки диаметр резьбовой части 28 мм вес вала 145 кг; материал сталь 50Г В =95 кгсмм2. Резец из быстрорежущей стали Р9. Обработка производится в 3-кулачковом патроне с поджатием центром задней бабки на токарно-винторезном станке 16Б04А без охлаждения.
Для чистовой обработки устанавливаем припуск на сторону 05 мм; для черновой остаётся 1 мм на сторону который снимаем за 1 проход. Для установленной глубины резания по табл. 41 [1] подача S=02 ммоб – для черновой обработки и S=015 ммоб – для чистовой. Согласно табл. 45 [1] для выбранной глубины резания и подачи скорость резания Vчерн.=150 ммин и Vчист.=170 ммин.
Учитывая что поверхность обрабатывается после наплавки принимаем коэффициент 075 (с.148 [1]). Другие поправочные коэффициенты определяем по соответствующим таблицам (с.150-151 [1]): kм=04; kм.р.=1; kох.=09; kх=085.
Откорректированная скорость резания:
Vчерн.=150×075×04×1×09×085=344 ммин;
Vчист.=170×075×04×1×09×085=39 ммин;
Число оборотов в минуту n для данных скоростей по формуле:
где V –скорость резания ммин;
d – диаметр резьбовой части d=28 мм;
Проверим мощность станка для выбранного режима резания по формуле:
где РZ – усилие резания кгс;
где CP – постоянная CP =200 [4];
t – глубина резания;
KP – поправочный коэффициент;
– КПД станка =085-095;
Мощность станка по паспорту 11 кВт. Использование станка по мощности для данной работы составит: =042:11=038 или 38% т.е. мощность станка для работы с выбранным режимом резания используется достаточно.
Производим расчёт основного (машинного) времени. Величина врезания и перебега по табл. 51 [1] равна 2 мм. Расчётная длина составляет L=15+2=17 мм. Подставляя найденные значения в формулу (4. 8) определим основное время ТО:
Общее основное время:
Вспомогательное время на установку вала весом 145 кг в 3-кулачковом патроне с поджатием центром задней бабки по табл. 53 [1] составляет 09 мин а вспомогательное время связанное с проходом по табл. 54 [1] – 11 мин.
Всего вспомогательное время на обработку вала будет ТВ =09+11=2 мин.
Дополнительное время при токарной обработке составляет 8% (с.155 [1]) от оперативного ТДОП =(046+2)×008=02 мин.
Штучное время определяем по формуле:
Подготовительно-заключительное время при токарной обработке ТП.З. =10 мин (табл. 55 [1]). Тогда норма времени составит:
3 Операция нарезание резьбы
Нарезание резьбы на токарно-винторезных станках производится резьбовыми резцами режущие кромки которых затачивают в соответствии с профилем резьбы. Основными элементами режима резания при нарезании резьбы являются скорость резания и число проходов. Продольная подача S соответствует щагу резьбы. Для нашей резьбы М25×15 S=15мм.
Число проходов при нарезании наружной метрической резьбы резцами из быстрорежущей стали с шагом 15 мм для стали 50Г по табл. 57 [1]:
При черновом проходе – 36 ммин;
При чистовом проходе – 64 ммин;
Число оборотов детали определяем по формуле (4.4):
Основное (машинное) время по формуле (4.4) где расчётная длина обрабатываемой поверхности L=15+3=18 мм (с.154 [1]):
Суммарное основное время:
Вспомогательное время на установку вала весом 145 кг в 3-кулачковом патроне с поджатием центром задней бабки по табл. 53 [1] составляет 09 мин а вспомогательное время связанное с проходом по табл. 54 [1] – 005 мин.
Всего вспомогательное время на обработку вала будет ТВ =09+005=095 мин.
Дополнительное время при токарной обработке составляет 8% (с.155 [1]) от оперативного ТДОП =(017+005)×008=002 мин.
Штучное время определяем по формуле (4.9):
Подготовительно-заключительное время при токарной обработке ТП.З. =10 мин (табл. 55 [1]). Тогда норма времени по формуле (4.6) составит:
4 Разработка приспособления для выполнения технологической операции (при ремонте детали)
Для выполнения всех вышеперечисленных операций по восстановлению вала насоса деталь закрепляем в 3-кулачковом патроне с поджатием центром задней бабки. Необходимо рассчитать требуемое усилие закрепления вала в патроне.
Усилие закрепления РЗ определим по формуле:
где К – коэффициент запаса [4];
где К0 – коэффициент гарантийного запаса К0 =15;
К1 – коэффициенты учитывающие увеличение сил резания из-за случайных неровностей на обрабатываемой поверхности К1=12 – при черновой К1=1 – при чистовой;
К2 – характеризует увеличение сил резания вследствие затупления режущего инструмента К2=1;
К3 – учитывает увеличение сил резания при прерывистом резании К3=12;
К4 – характеризует постоянные силы закрепления в патроне К4=13;
К5 – характеризует эргономику ручных зажимных механизмов ЗМ К5=1;
К6 – коэффициент учитывающийся только при наличии моментов стремящихся повернуть заготовку установленную плоской поверхностью на постоянные опоры;
L – длина выступающей из патрона части детали L=250 мм;
РZ – усилие резания
DЗ – диаметр вала DЗ =30 мм;
f – коэффициент трения f=02-025;
В данной главе был разработан технологический процесс ремонта детали расчёт усилия закрепления детали в зажимном механизме.
6 Экономическая часть.doc
Экономическую эффективность использования нового автогрейдера буем оценивать путём сравнения технико-экономических показателей работы строительных комплектов машин с базовой (ДЗ-143) и новой техникой (ДЗ-143М).
1 Определение трудоёмкости единицы продукции
Трудоёмкость единицы продукции – это затраты труда машинистов средств механизации в человеко-часах отнесённые к единице продукции. Этим показателем оценивается количественный состав рабочих занятых на основных и вспомогательных работах. Трудоёмкость единицы продукции А чел-часм2 определяется выражением 12
гдеАi – количество машинистов занятых на i-ом средстве механизации
человек на любом из используемых средств механизации Аi =1.
Результаты расчётов проведённых по формуле (6.1) приведены в таблице 6.1.
Таблица 6.1 – Расчётная трудоёмкость единицы продукции для различных дальностей перемещения грунта.
транспортирования L м
Расчётная трудоёмкость единицы продукции А чел-часм2
2 Определение энергоёмкости единицы продукции
Удельная энергоёмкость единицы продукции показывает расход мощности силовых установок комплекта машин на производство единицы продукции. Удельная энергоёмкость единицы продукции Э кВт×часм2 определяется следующим выражением 12
гдеNcуi – мощность силовой установки i-ой машины кВт.
Мощности силовых установок машин Ncуi приведены в таблице 6.2. Значения необходимого количества машиносмен работы различных средств механизации приведены в таблицах 6.5 – 6.6. В таблице 6.2 приведены значения удельной энергоёмкости единицы продукции определённые по формуле (6.2).
Таблица 6.2 – Расчётная удельная энергоёмкость единицы продукции при различных дальностях транспортирования грунта.
Расчётная энергоёмкость единицы продукции Э кВт×часм2
3 Определение металлоёмкости единицы продукции
Удельная металлоёмкость единицы продукции показывает какая часть массы комплекта машин приходится на единицу продукции. Удельная металлоёмкость единицы продукции М тм2 определяется следующим выражением 12
гдеМмi – масса i-ой машины т.
Массы машин Ммi приведены в таблице 6.2. Значения необходимого количества машиносмен работы различных средств механизации приведены
в таблицах 6.5 – 6.6.
В таблице 6.3 приведены значения удельной металлоёмкости единицы продукции определённые по формуле (6.3).
Таблица 6.3 – Расчётная удельная металлоёмкость единицы продукции при различных дальностях возки грунта.
металлоёмкость единицы продукции М тм2
4 Определение удельных приведённых затрат
Удельные приведённые затраты являются критерием с помощью которого определяют эффективность использования того или иного состава СКМ путём сравнения нескольких вариантов СКМ. Расчётные (теоретические) удельные приведённые затраты рубм2 определяются по формуле 14
гдеЕ – нормативный коэффициент эффективности использования удель ных капитальных вложений (норма дисконта) примем Е = 015;
– расчётные удельные капитальные затраты удельные капитальные затраты отражают общественно необходимые затраты труда на изготовление машины в виде её стоимости приходящейся на единицу продукции.
Расчётные (теоретические) удельные затраты рубм2 можно определить по формуле 14
гдеа – коэффициент учитывающий затраты на доставку машин к месту производства работ принимаем а = 105;
Цi – цена i-й машины руб цены машин входящих в состав СКМ приведены в таблице 1.2.
Значения удельных приведённых затрат и удельных капитальных затрат определённые по формулам (6.4) и (6.5) являются расчётными (теоретическими) поскольку они рассчитаны исходя из необходимого количества машиносмен. В таблице 6.5 приведены расчётные значения удельных приведённых и удельных капитальных затрат.
Себестоимость единицы продукции рубм2 определяется по формуле 12
гдеCi – себестоимость машиночаса работы i-й машины комлекта определяется по 7.
В таблице 6.4 приведены расчётные значения себестоимости единицы продукции при различных дальностях возки грунта полученные при вычислении по формуле (6.6).
Таблица 6.4 – Себестоимость единицы продукции при различных дальностях транспортирования грунта.
Транспортирования L м
себестоимость единицы продукции рубм2
Таблица 6.5 – Расчётные удельные капитальные и удельные приведённые затраты при различных дальностях транспортирования грунта
Расчётные приведённые затраты
Расчётные удельные приведённые затраты
5 Определение годового экономического эффекта от применения СКМ2
Зная удельные приведённые затраты и годовую производительность комплектов машин можно определить годовой экономический эффект
где - расчётные удельные приведённые затраты рубм2 Пг – годовая производительность комплекта м2год.
Определим годовой экономический эффект при работе СКМ 2 – дальность возки грунта составляет 500 м.
Итак можно отметить что использование комплекта машин с автогрейдером ДЗ-143М при дальности возки грунта на расстояние 500 м годовой экономический эффект составит 20548230 рублей.
6 Анализ эффективности механизации строительства
Рассматривая эффективность от использования того или иного состава СКМ можно определить минимумом финансовых трудовых энергетических и других видов затрат. В ходе выполнения расчётов в настоящем дипломном проекте были установлены зависимости определённых видов затрат на единицу продукции от различных параметров таких как: расстояние транспортирования грунта на верх земляного полотна и темп производства работ.
Графически эти показатели изображены на листе технико-экономических показателей настоящего дипломного проекта.
Тщательно анализируя показатели можно легко выяснить что комплект СКМ-2 с модернизированным автогрейдером ДЗ-143М использовать гораздо эффективнее нежели комплект СКМ-1. Можно с уверенностью сказать что модернизация автогрейдером ДЗ-143М значительно уменьшает себестоимость металлоёмкость трудоёмкость и удельные приведённые затраты единицы продукции СКМ а также значительно уменьшает энергоёмкость процесса резания грунта.
Содержание.doc
Механизация строительства .
1 Описание объекта строительства
2 Технология механизация и организация строительства ..
2.1 Технология производства работ
2.2 Механизация строительства ..
3 Организация производства работ
3.1 Определение длины сменной захватки
3.2 Определение эксплуатационных производительностей машин
3.3 Выбор количества машин в комплекте
Конструкторский расчет
1 Тяговый расчет автогрейдера
2 Расчет тяговой рамы на прочность ..
3 Расчет на прочность рабочего органа автогрейдера ..
Технологический процесс восстановления детали
1 Операция наплавка ..
2 Операция точение .
3 Операция нарезание резьбы
4 Разработка приспособления для выполнения технологической операции .
Безопасность жизнедеятельности .
1 Анализ вредных факторов возникающих при работе автогрейдера
2 Расчет кондиционера
2.1 Определение количества вентиляционного воздуха ..
3 Экологическая безопасность
Экономическая часть
1 Определение трудоёмкости единицы продукции .
2 Определение энергоёмкости единицы продукции
3 Определение металлоёмкости единицы продукции .
4 Определение удельных приведённых затрат .
5 Определение годового экономического эффекта от применения СКМ2 ..
6 Анализ эффективности механизации строительства
Список использованных источников .
Введение.doc
В данном дипломном проекте предлагается усовершенствование конструкции автогрейдера ДЗ – 143.
РАБОЧЕЕ ОБОРУД.dwg

Гидроцилиндр поршневой
10.1.У-6340250 ОСТ 22-1417-79
ПАТРОН.dwg

РАМА ТЯГОВАЯ.dwg

Болт М30 55.5.8 ГОСТ 7808-70
Гидроцилиндр поршневой
10.1.У-6340250 ОСТ 22-1417-79
Гайка М30 ГОСТ 2524-70
Шайба 3065Г ГОСТ 6402-70
Шплинт 545-001 ГОСТ 397-66