Сосуд высокого давления



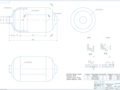
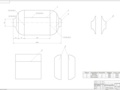
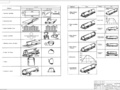
- Добавлен: 28.11.2022
- Размер: 2 MB
- Закачек: 3
Описание
Изготовление, эксплуатация и ремонт сосудов работающих под давлением находится под особым контролем Ростехнадзора России и поэтому осуществляемые работы по изготовлению четко регламентированы нормативными документами.
Цель данного курсового проекта – разработать технологический процесс изготовления корпуса сосуда из листов изготовленных прокаткой, для этого необходимо изучить технологии изготовления сосудов, изучить свойства и особенности сварки применяемых материалов, способы контроля сварных соединений, ознакомиться с оборудованием и технологической оснасткой, а также средствами механизации и автоматизации производства сосудов. Разработка техпроцесса изготовления данной конструкции предполагает изучение процессов резки, правки, гибки, подготовки кромок, а также особенностей сборочно-сварочных операций и ознакомление с технологией контроля.
Состав проекта
![]() |
![]() ![]() ![]() ![]() |
![]() ![]() ![]() |
![]() ![]() ![]() ![]() |
![]() ![]() ![]() ![]() |
![]() ![]() ![]() ![]() |
Дополнительная информация
Деталировка СВД.cdw

ПЗ.doc
Факультет: «Энергетика и машиностроение»
Кафедра: «Технология машиностроения»
Описание сварной конструкции и ТУ на изготовление
1. Назначение сварной конструкции.
2.Особенности материала СВД
3. Технические условия на изготовление
Литературный обзор по изготовлению типовых конструкций
Анализ предлагаемых вариантов при разработке техпроцесса
1. Очистка под сварку
2. Выбор сварочной проволоки
3. Выбор способа сварки
4. Выбор способа контроля
5. Выбор метода ультразвукового контроля
. Разработка техпроцесса заготовительных операций и выбор оборудования
1. Правка листов на многовалковой листоправильной машине
4. Очистка под сварку
Разработка техпроцесса сборочно-сварочных операций
1 Технология сборки и сварки корпуса
2. Особенности сварки применяемых материалов
3. Расчет режимов сварки
3.1. Режим ручной сварки для выполнения прихваток
4 Характеристика применяемого оборудования и сборочно - сварочных
Проектирование компоновки установки и описание ее работы
1 Состав установки и предъявляемые к ней требования
2. Описание работы установки
Разработка технологии контроля
Техника безопасности при выполнении технологического процесса
Интенсивное развитие химической и нефтехимической промышленности обуславливает увеличение выпуска аппаратов различных типов и размеров работающих при высоких давлениях и температуре. Создание крупногабаритных корозионностойких сосудов и аппаратов предназначенных для оснащения высокопроизводительных технологических линий производства химических продуктов требует нового подхода к решению конструкторских и технологических вопросов поэтому при изготовлении данных конструкций следует стремится к высокотехнологичным методам производства и учитывать степень механизации и автоматизации при изготовлении подобных конструкций.
В настоящее время одной из основных технологических операций используемых при изготовлении сосудов работающих под давлением является сварка. По сути дела создание этих сосудов без использования сварки невозможно. Кроме того применение сварки позволяет создавать сосуды сложной конструкции а также значительно сокращает цикл их производства и стоимость.
Также необходимо учитывать воздействие агрессивных и коррозионных сред которые могут приводить к межкристаллитной коррозии вызывать ускоренную коррозию в зонах концентрации напряжений и преждевременный выход конструкции из строя. Поэтому при изготовлении сосудов из высоколегированных коррозионно-стойких сталей наряду с требованиями высокой коррозионной стойкости к конструкционным материалам также предъявляются требования высокой механической прочности жаропрочности и жаростойкости [1].
Изготовление эксплуатация и ремонт сосудов работающих под давлением находится под особым контролем Ростехнадзора России и поэтому осуществляемые работы по изготовлению четко регламентированы нормативными документами.
Цель данного курсового проекта – разработать технологический процесс изготовления корпуса сосуда из листов изготовленных прокаткой для этого необходимо изучить технологии изготовления сосудов изучить свойства и особенности сварки применяемых материалов способы контроля сварных соединений ознакомиться с оборудованием и технологической оснасткой а также средствами механизации и автоматизации производства сосудов. Разработка техпроцесса изготовления данной конструкции предполагает изучение процессов резки правки гибки подготовки кромок а также особенностей сборочно-сварочных операций и ознакомление с технологией контроля.
1. Назначение сварной конструкции
Конструкция сосудов должна обеспечивать надежность и безопасность эксплуатации в течение расчетного срока службы и предусматривать возможность проведения технического освидетельствования очистки промывки полного опорожнения продувки ремонта эксплуатационного контроля металла и соединений.
Для каждого сосуда должен быть установлен и указан в паспорте расчетный срок службы с учетом условий эксплуатации.
Устройства препятствующие наружному и внутреннему осмотрам сосудов (мешалки змеевики рубашки тарелки перегородки и другие приспособления) должны быть как правило съемными.
При применении приварных устройств должна быть предусмотрена возможность их удаления для проведения наружного и внутреннего осмотров и последующей установки на место. Порядок съема и установки этих устройств должен быть указан в руководстве по эксплуатации сосуда.
Если конструкция сосуда не позволяет проведение наружного и внутреннего осмотров или гидравлического испытания предусмотренных требованиями Правил разработчиком проекта сосуда в руководстве по эксплуатации должны быть указаны методика периодичность и объем контроля выполнение которых обеспечит своевременное выявление и устранение дефектов. В случае отсутствия в руководстве таких указаний методика периодичность и объем контроля определяются специализированной организацией.
Конструкции внутренних устройств должны обеспечивать удаление из сосуда воздуха при гидравлическом испытании и воды после гидравлического испытания.
Сосуды должны иметь штуцера для наполнения и слива воды а также для удаления воздуха при гидравлическом испытании.
На каждом сосуде должны быть предусмотрены вентиль кран или другое устройство позволяющее осуществлять контроль за отсутствием давления в сосуде перед его открыванием; при этом отвод среды должен быть направлен в безопасное место.
Расчет на прочность сосудов и их элементов должен производиться по НД согласованной с Госгортехнадзором России. Сосуды предназначенные для работы в условиях циклических и знакопеременных нагрузок должны быть рассчитаны на прочность с учетом этих нагрузок.
При отсутствии нормативного метода расчет на прочность должен выполняться по методике согласованной со специализированной научно-исследовательской организацией.
Сосуды которые в процессе эксплуатации изменяют свое положение в пространстве должны иметь приспособления предотвращающие их самоопрокидывание.
Конструкция сосудов обогреваемых горячими газами должна обеспечивать надежное охлаждение стенок находящихся под давлением до расчетной температуры.
Для проверки качества приварки колец укрепляющих отверстия для люков лазов и штуцеров должно быть резьбовое контрольное отверстие в кольце если оно приварено снаружи или в стенке если кольцо приварено с внутренней стороны сосуда.
Данное требование распространяется также и на привариваемые снаружи к корпусу накладки или другие укрепляющие элементы.
Наружные глухие элементы (например накладки) не работающие под давлением должны иметь дренажные отверстия в самых низких местах.
Заземление и электрическое оборудование сосудов должны соответствовать правилам технической эксплуатации электроустановок потребителей и правилам техники безопасности при эксплуатации электроустановок потребителей в установленном порядке.
Сосуды должны быть снабжены необходимым количеством люков и смотровых лючков обеспечивающих осмотр очистку и ремонт сосудов а также монтаж и демонтаж разборных внутренних устройств.
Сосуды состоящие из цилиндрического корпуса и решеток с закрепленными в них трубками (теплообменники) и сосуды предназначенные для транспортировки и хранения криогенных жидкостей а также сосуды предназначенные для работы с веществами 1-го и 2-го классов опасности по ГОСТ 12.1.007-76 но не вызывающие коррозии и накипи допускается изготовлять без люков и лючков независимо от диаметра сосудов при условии выполнения требования п. 2.1.4 Правил.
Сосуды с внутренним диаметром более 800 мм должны иметь люки а с внутренним диаметром 800 мм и менее - лючки.
Внутренний диаметр круглых люков должен быть не менее 400 мм. Размеры овальных люков по наименьшей и наибольшей осям в свету должны быть не менее 325×400 мм.
Внутренний диаметр круглых или размер по наименьшей оси овальных лючков должен быть не менее 80 мм.
Люки лючки необходимо располагать в местах доступных для обслуживания. Требования к устройству расположению и обслуживанию смотровых окон в барокамерах определяются проектной организацией и указываются в инструкции по монтажу и эксплуатации завода-изготовителя.
Крышки люков должны быть съемными. На сосудах изолированных на основе вакуума допускаются приварные крышки.
Крышки массой более 20 кг должны быть снабжены подъемно-поворотными или другими устройствами для их открывания и закрывания.
Конструкция шарнирно-откидных или вставных болтов хомутов а также зажимных приспособлений люков крышек и их фланцев должна предотвращать их самопроизвольный сдвиг
При наличии на сосудах штуцеров фланцевых разъемов съемных днищ или крышек внутренний диаметр которых не менее указанных для люков в п. 2.2.3 Правил обеспечивающих возможность проведения внутреннего осмотра допускается люки не предусматривать.
При сварке обечаек и труб приварке днищ к обечайкам должны применяться стыковые швы с полным проплавлением.
Допускаются сварные соединения в тавр и угловые с полным проплавлением для приварки плоских днищ плоских фланцев трубных решеток штуцеров люков рубашек.
Применение нахлесточных сварных швов допускается для приварки к корпусу укрепляющих колец опорных элементов подкладных листов пластин под площадки лестницы кронштейны и т.п.
Конструктивный зазор в угловых и тавровых сварных соединениях допускается в случаях предусмотренных НД согласованной в установленном порядке.
Сварные швы должны быть доступны для контроля при изготовлении монтаже и эксплуатации сосудов предусмотренного требованиями Правил соответствующих стандартов и технических условий.
Продольные швы смежных обечаек и швы днищ сосудов должны быть смещены относительно друг друга на величину трехкратной толщины наиболее толстого элемента но не менее чем на 100 мм между осями швов.
Указанные швы допускается не смещать относительно друг друга в сосудах предназначенных для работы под давлением не более 16 МПа (16 кгссм2) и температуре стенки не выше 400 °С с номинальной толщиной стенки не более 30 мм при условии что эти швы выполняются автоматической или электрошлаковой сваркой и места пересечения швов контролируются методом радиографии или ультразвуковой дефектоскопии в объеме 100 %.
При приварке к корпусу сосуда внутренних и внешних устройств (опорных элементов тарелок рубашек перегородок и др.) допускается пересечение этих сварных швов со стыковыми швами корпуса при условии предварительной проверки перекрываемого участка шва корпуса радиографическим контролем или ультразвуковой дефектоскопией.
В случае приварки опор или иных элементов к корпусу сосуда расстояние между краем сварного шва сосуда и краем шва приварки элемента должно быть не менее толщины стенки корпуса сосуда но не менее 20 мм.
Для сосудов из углеродистых и низколегированных марганцовистых и марганцово-кремнистых сталей (приложение 3) подвергаемых после сварки термообработке независимо от толщины стенки корпуса расстояние между краем сварного шва сосуда и краем шва приварки элемента должно быть не менее 20 мм.
В горизонтальных сосудах допускается местное перекрытие седловыми опорами кольцевых (поперечных) сварных швов на общей длине не более 035D а при наличии подкладного листа - не более 05D где D - наружный диаметр сосуда. При этом перекрываемые участки сварных швов по всей длине должны быть проверены методом радиографии или ультразвуковой дефектоскопии. Перекрытие мест пересечения швов не допускается.
В стыковых сварных соединениях элементов сосудов с разной толщиной стенок должен быть обеспечен плавный переход от одного элемента к другому путем постепенного утонения кромки более толстого элемента. Угол наклона поверхностей перехода не должен превышать 20°.
Если разница в толщине соединяемых элементов составляет не более 30 % толщины тонкого элемента и не превышает 5 мм то допускается применение сварных швов без предварительного утонения толстого элемента. Форма швов должна обеспечивать плавный переход от толстого элемента к тонкому.
При стыковке литой детали с деталями из труб проката или поковок необходимо учитывать что номинальная расчетная толщина литой детали на 25 - 40 % больше аналогичной расчетной толщины стенки элемента из труб проката или поковок поэтому переход от толстого элемента к тонкому должен быть выполнен таким образом чтобы толщина конца литой детали была не менее расчетной величины.
Сталь 12ХМ – низколегированная конструкционная жаропрочная. Обладает высокими показателями устойчивости к экстремальным температурам. При своей стоимости является одним из лучших жаропрочных металлов по соотношению ценакачество. Подходит для эксплуатации в условиях постоянных нагрузок что делает ее незаменимой для выполнения сложных и ответственных промышленных задач. Сталь используется на атомных и других электростанциях из нее производят трубы коллекторы котлы и другое оборудование подверженное давлению и перегревам. Надежность универсальность простота производства и отличные характеристики стали обеспечивают ей прекрасную репутацию на рынке.
Цифры и буквы в маркировке стали указывают на ряд важных показателей – ключевые химические элементы и уровень их концентрации в составе степень раскисления качество стали по содержанию вредных примесей серы и фосфора.
– указывает на содержание углерода в сотых долях %. В стали 12ХМ содержится приблизительно 0.12% углерода. Содержание углерода оказывает большое влияние на свойства стали изменяя этот показатель можно приспособить металл под нужды любой промышленности. Высокий показатель содержания углерода означает что сталь твердая жесткая прекрасно справляется с постоянными нагрузками и идеально подходит для изготовления несущих металлоконструкций. Такие стали особенно популярны в строительстве. Недостатки сталей с высоким содержанием углерода – это неустойчивость к ударным нагрузкам низкие показатели текучести и ударной вязкости ограниченная свариваемость сложности механической обработки ломкость. Низкое содержание углерода указывает на мягкость стали. Такие металлы не самый лучший выбор для строительных металлоконструкций т.к. не обладают достаточной жесткостью и твердостью. Однако они идеально подходят для изготовления деталей работающих в условиях постоянной динамической нагрузки – ударов или вибраций т.к. малоуглеродистые стали обладают хорошей ударной вязкостью и текучестью. Детали из таких сталей можно изготавливать методом холодной штамповки и всеми видами вытяжки. Малоуглеродистые стали практически никогда не имеют ограничений по свариваемости и отлично поддаются механической обработке. Недостаток твердости и прочности можно нивелировать с помощью термической обработки – закалки а также путем добавления в состав легирующих элементов таких как хром никель кремний медь или марганец.
Х – указывает на содержание хрома в количестве приблизительно равном 1%. Хром – один из самых популярных элементов используемых для легирования стали. Существует два вида стали с добавлением стали – хромированная и хромистая. Хромированная сталь – это обыкновенная углеродистая сталь покрытая защитным слоем хрома. Она неуязвима для воздействия внешней среды до тех пор пока защитный слой сохраняет целостность но при механическом повреждении слоя становится уязвимой для коррозии. Хромистая сталь содержит хром в составе как добавку. Если хрома достаточно много сталь становится нержавеющей. Антикорозионные свойства хромистой стали не зависят от внешнего покрытия и сохраняются на протяжении всего срока эксплуатации металла. Хром повышать прочность и твердость сплава.
М – указывает на содержание молибдена. Молибден как и хром в больших количествах защищает от коррозии и упрочняет сталь а также повышает возможности ее эксплуатации при высоких температурах.
Другие элементы – кремний марганец никель – содержатся в составе стали 12ХМ в незначительных количествах и в маркировке не указываются.
Сталь 12ХМ – это низколегированная жаропрочная перлитная конструкционная сталь. Жаропрочная – означает что сталь можно использовать при высоких температурах нагрева. Низколегированная – значит повышенной прочности применяемая для изготовления металлоконструкций. Конструкционные стали используются для изготовления сварных или не сварных металлоконструкций различного назначения.
Особенности производства деталей
Термическая обработка для стали 12ХМ является обязательной процедурой. Изделия из стали подвергаются подогреванию чтобы исключить образование холодных трещин в шовной области. Закалять сталь 12ХМ необходимо при температуре около 900С. Процедуру можно проводить как в масле так и на воздухе это зависит от габаритов изделия. Весь процесс длится 3 часа после чего стали необходимо дать остыть на открытом воздухе.
Основные достоинства стали обеспечены наличием в составе хрома и молибдена. Благодаря хрому сплав сохраняет свои характеристики очень долго и более устойчив к коррозии чем нелегированные углеродистые стали. Молибден придает стали жаропрочность и существенно повышает допустимые температуры эксплуатации. Кроме того металл относительно прост в производстве легируется доступными компонентам благодаря чему не отличается высокой стоимостью.
К минусам можно отнести уязвимость к кислотным и щелочным средам – в результате взаимодействия с кислотами и солями возникает коррозия. При использовании стали 12ХМ в режущем инструменте например в пилах ножах или фрезах режущая поверхность быстро тупится. Рекомендуется применять сталь 12ХМ в инструменте для обработки древесины и использовать только по назначению.
Сталь 12ХМ применяется при изготовлении конструкций и деталей механизмов преднахначенных для работы при экстремальных температурах и под постоянной нагрузкой. Такими деталями являются элементы паровых котлов крепления и запорная арматура для трубопроводов пароперегревательные трубы трубы и коллекторы высокого давления. Изделия из стали применяется на электростанциях (в том числе – атомных) котельных промышленных предприятиях.
Этот материал имеет обширное применение. Элементы изготовленные из него предназначены для эксплуатации в условиях значительных нагрузок и экстремально высоких температур.
Самыми основными считаются:
трубопроводные крепления;
пароперегревательные трубы;
трубы для высокого давления.
Температура критических точек материала 12ХМ.
Ac1= 720 Ac3(Acm) = 880 Ar3(Arcm) = 790 Ar1= 695
Механические свойства при Т=20oС материала 12ХМ
Нормализация 910 - 930oCОтпуск 670 - 690oCОхлаждение воздух
Массовая доля элементов стали 12ХМ поГОСТ 5520-79
Прочностные показатели отличные так как в металле есть маленькая доза углерода.Введённый молибден который сочетают с никелем и хромом создаёт эффект мелкого зерна а также гарантирует свойства жаростойкости красностойкости.Стоимость сплава довольно высока из-за присутствия в нём ферромолибдена.
B03 - Обработка металлов давлением. Поковки
В23 - Листы и полосы
В33 - Листы и полосы
Свойства по стандарту ГОСТ 10885-85
Предел текучести 02 МПа
Временное сопротивление разрыву в МПа
Относительное удлинение при разрыве5 %
Физические свойства материала 12ХМ
Зарубежные аналоги марки стали 12ХМ
A182 A387Gr.12Cl.2 Gr.P12 K11562 K11572 K11597 K11757 K12062
7335 13CrMo4 13CrMo4-5 13CrMo44
SFVA12 SFVAF12 STBA20 STBA22 STFA22 STPA20 STPA22
CrMo4-5 14CrMo4-5 15CD3.5 15CD4.05 15CD4.5
CrMo4-5 1501-620 1501-621 620-440 620-470 620-540
CrMo4-5 14CrMo3 16CrMo3
CrMo4-5 F.2613 F.2631
SFVAF12 STHA20 STHA22
В виду коррозионной неустойчивости к щелочным и кислотным средам рекомендуется избегать контакта с солями и кислотами. Если ржавчина уже образовалась используйте специальные растворы например баллистол. Для очистки поверхности не рекомендуются использовать хлорсодержащие вещества т.к. они пагубно влияют на сталь. В качестве защитного слоя можно нанести водостойкую краску. Очистить металл от старого слоя краски можно с помощью спирта. Сталь не защищенную специальным покрытием рекомендуется держать в сухости.
3.Технические условия на изготовление
При изготовлении представленной конструкции необходимо соблюдать следующие требования [3].
Требования к основным материалам :
- листовой материал должен изготавливатся по ГОСТ 7350-77;
- материал должен иметь сертификат подтверждающий требования по изготовлению стандарту;
- механические свойства листов проверяют по ГОСТ 5520-88;
Требования к сварочным материалам:
- сварочная проволока и флюс для сварки должны иметь сертификат подтверждающий требования по изготовлению ГОСТу 2246-70 и ГОСТу 9087 -79
- сварочная проволока должна быть испытана на склонность к МКК по ГОСТ 6032-89
- на мотках сварочной проволоки должны быть бирки с указанием данных соответствующих сертификату;
- на мешках с флюсом должны быть ярлыки с указанием данных соответствующих сертификату;
Требования к заготовительным операциям :
- При перемещении листа не допускать ударного воздействия на лист;
- кромки листов подготовленных под сварку должны иметь отклонение размеров не более +- 05 мм;
Требования к сборке:
- смещение кромок в кольцевых швах выполняемых дуговой сваркой не должно превышать 0.1S + 1 мм.
- отклонение по длине не более ±03% от номинальной длины но не более ±50 мм;
- отклонение от прямолинейности не более 2 мм на длине 1м но не более 20 мм при длине корпуса до 10 м и не более 30 мм при длине корпуса свыше 15 м.
-отклонение внутреннего (наружного) диаметра корпуса сосудов допускается не более ±1% номинального диаметра.
- увод (угловатость) кромок в сварных швах не должен превышать 01+3 мм но не более 5 мм независимо от диаметра;
Требования к производству сварочных работ;
- методы сварки сосудов и их элементов должны обеспечивать минимальный уровень деформаций свариваемых конструкций обеспечивать непрерывность получения сварного шва;
- Все сварочные работы при изготовлении сосудов и их элементов должны производиться при положительных температурах в закрытых помещениях.
Требования к качеству сварных соединений;
Контроль качества сварных соединений следует проводить следующими методами:
а) визуальным осмотром и измерением;
б) механическими испытаниями;
В сварных соединениях не допускаются следующие наружные дефекты:
трещины всех видов и направлений;
-свищи и пористость наружной поверхности шва;
- подрезы не более 10% толщины стенки но не более 05 мм
- наплывы прожоги и незаплавленные кратеры;
-чешуйчатость поверхности и глубина впадин между валиками шва более 1 мм;
Механические испытания произвести по ГОСТ 6996 свойства сварных соединений должны быть не ниже норм указанных в таблице:
Механические свойства сварных соединений
Механические свойства
Временное сопротивление разрыву при Т 20 С
Не ниже нижнего значения для основного металла
Минимальное значение
ударной вязкости Джсм2
а) при температуре 20°С
а) при температуре ниже минус 20°С
Минимальное значение угла
Твердость металла шва
сварных соединений НВ не менее
В сварных соединениях не допускаются следующие внутренние дефекты:
-трещины всех видов и направлений в том числе микротрещины выявленные при микроисследовании;
-поры выходящие за пределы норм;
Определение содержания ферритной фазы в металле шва должно проводиться объемным магнитным методом согласно ГОСТ 9466. Содержание феррита определяется ферритометром удовлетворяющим требованиям ГОСТ 26364.
дефектные места следует удалять механическим способом с последующей заваркой исправленного места и повторным контролем исправление дефектов на одном и том же участке допускается не более 3-х раз.
Сосуды со стенками из листов средней толщины (до 40 мм) изготовляют преимущественно с помощью автоматической сварки под флюсом. Сосуды работающие в агрессивных средах изготовляют из хромоникелевых и хромистых сталей цветных металлов и их сплавов автоматической сваркой под флюсом и по слою флюса полуоткрытой дугой (алюминиевые сплавы) а также аргонодуговой сваркой.
В данном разделе приводится описание сборки и сварки цилиндрических типовых изделий с учетом механизации сварочных процессов обе представленные установки созданы на Уралмашзаводе. [4]
Одна из них предназначена для автоматической сварки продольных внутренних и наружных швов в обечайках в среде углекислого газа и сваркой под флюсом. Установка состоит из тележки 5 с роликовыми опорами 6 площадки сварщика 3 и подъемной консоли 2 с приводом 1 Тележка 5 с роликовыми опорами перемещается по рельсовому пути 4 от собственного привода.
Рис.2. Установка для автоматической сварки обечаек
Техническая характеристика
Диаметр свариваемых обечаек в мм 450-2000
Длина свариваемых обечаек в мм. До 3500
Толщина свариваемых обечаек в мм 5-30
Скорость передвижения тележки в ммин
Окружная скорость обечайки в ммин
Ход флюсовой подушки (по высоте) в мм 240
Грузоподъемность в кГ 500
Скорость подъема и опускания в ммин 6
Ход площадки в мм 1789
Вылет от оси колонны до оси горелки в мм 4580 Средняя скорость подъема (опускания) в ммин 1.92
Ход консоли в мм 1400
Габаритные размеры (длина ширина высота) в
Сварка обечаек на установке производится следующим образом: на роликоопоры тележки отведенной в крайнее правое положение краном устанавливается свальцованная обечайка имеющая необходимое количество прихваток по стыку. Первоначально в обечайке сваривается внутренний шов на флюсовой подушке. Максимальное усилие с которым флюсовая подушка поджимается к обечайке равно 700 кГ. С помощью привода роликоопор обечайка поворачивается в удобное положение для зачистки протеков шва шлака и брызг с наружной стороны.
Для сварки наружного шва обечайки ее поворачивают стыком вверх под мундштук полуавтомата А-537. Площадка для сварщика устанавливается по высоте над обечайкой так чтобы расстояние между нею и электродом было 15—25 мм.
Вторая установка спроектирована для выполнения кольцевых и продольных наружных швов в изделиях цилиндрической формы диаметром 500—5000 мм. Установка состоит из портала и роликового стенда для укладки обечаек и вращения их при сварке кольцевых швов.
Рис.3. Портал установки
Диаметр свариваемых обечаек в мм 500—5000
Наибольшая длина непрерывного продольного шва
Тип сварочной головки АБС
Скорость передвижения портала в ммин 126
Ход портала в мм 25 000
Скорость перемещения подвижной площадки в ммин 2
Ход подвижной площадки в мм 5000
Наибольшая грузоподъемность подвижной площадки
Габаритные размеры портальной сварочной машины
(длина ширина высота) в мм 9240x822x8900
Вес машины в кг 36100
Сварка производится следующим образом:
установленные на роликоопоры обечайки стыкуются и прихватываются электросваркой. Затем выполняется сварка наружных продольных швов обечаек для чего обечайку повертывают приводными роликами разделкой вверх. Портал с поднятым над изделием балконом располагается над швом. С помощью направляющей балки портала мундштук сварочного аппарата устанавливается над швом. После выполнения всех настроечных операций производят сварку под флюсом при помощи движения головки АБС со сварочной скоростью по направляющей балке.
Наружные кольцевые швы сваривают так же как и продольные с той только разницей что перемещение обечайки относительно сварочного аппарата осуществляется роликовым стендом который сообщает изделию скорость сварки.
Обе рассмотренные установки по конструктивным особенностям имеют ограничение при сварке внутренних кольцевых швов. В разрабатываемой технологии следует учесть это условие и предусмотреть возможность выполнения всех швов на одной установке.
Еще одним примером может служить изготовление цилиндрической части котла железнодорожной цистерны [25].
Особенность производства рассмотрим на примере поточной линии Мариупольского завода тяжелого машиностроения. Цилиндрическую часть котла цистерны вместимостью 60 т составляют из пяти листов (рис.4 а) ее поперечное сечение после вальцовки показано на (рис.4б).
Рис. 4. Обечайка котла железнодорожной цистерны
Рис. 5. Схема стенда для автоматической сварки листов обечайки
Верхние 1 и средние 2 листы имеют толщину 8 мм нижний лист 3 — 11 мм. Листы с механически обработанными кромками раскладывают на сборочном стенде и стыковые швы полотнища собирают на прихватках с постановкой заходных и выходных планок. Собранное полотнище приподнимают системой роликов и передают на сварочный стенд (рис.5). Кромки листов 1 прижимами 2 прижимаются к стенду а флюсовые подушки 4 с пневмошлангами 5 обеспечивают поджатие флюса с нижней стороны. Четыре сварочные головки 3 одновременно выполняют сварку всех продольных швов. После сварки с одной стороны кантователь переворачивает полотнище а на второй сварочной установке одновременно сваривают все стыки.
Кромки деталей перед сваркой должны быть очищены от различных загрязнений в соответствии с требованиями технологического процесса.
Зачистка может производиться на специальных зачистных станках например с помощью магнитно-абразивной обработки . Толщина зачищаемой кромки 3-20 мм производительность зачистки 02-15 ммин.
Преимуществами данного метода являются:
- одновременная зачистка кромок листа с обеих сторон;
- формирование поверхностного слоя с минимумом дефектов структуры;
- экологическая чистота.
Недостаток же состоит в гораздо более дорогостоящем оборудовании больших габаритах и стационарности установки.
Также зачистку кромок можно производить с помощью пневматических шлифовальных машин. Достоинства их заключаются в малых габаритах малой стоимости и возможности последующего использования для зачистки швов от шлака. Недостатками являются меньшая производительность из-за необходимости ведения зачистки вручную. Однако для мелкосерийного производства это приемлемо. [8]
Принятый вариант: пневматическая шлифовальная машина.
Для сварки данной марки стали типа (12Х18Н10Т) предусмотрено ОСТом 26.260.3 – 2001(Сварка в химическом машиностроении) следующие марки сварочных проволок : Св-06Х19Н9Т и Св -07Х18Н9ТЮ.
К числу основных трудностейкоторые приходится преодолевать при сварке высоколегированных сталей относятся: обеспечение стойкости против образования трещин и обеспечение коррозионной стойкости. Исходя из этих соображений следует проводить выбор сварочной проволоки.
Св-06Х19Н9Т- проволока имеет пониженное содержание углерода что обеспечивает лучшую стойкость металла шва против межкристаллитной коррозии также проволока имеет повышенное содержание хрома. Как основной ферритизатор этот элемент снижает склонность к образованию горячих трещин за счет создания в металле шва двухфазной структуры.
Проволока Св - 07Х18Н9ТЮ содержит в составе легирующий элемент –алюминий добавки этого элемента обладающего химическим сродством к азоту воздуха и связывающие его в нитридыуменьшают вероятность образования пор вызываемых этим газом.Основным критерием при выборе проволоки является наличие требований по межкристаллитной коррозии предъявляемые при изготовлении к химаппаратуре согласно вышеназванного ОСТа поэтому выбор проволоки осуществляем согласно нормативному документу.[9]
Принятый вариант: сварочная проволока Св- 07Х18Н9ТЮ.
Дуговая сварка является популярной технологией во время которой тепловая энергия требуемая для оплавления соединяемых кромок и электрода достигает благодаря воздействию постоянным или высокочастотным током свариваемые металлические поверхности. Этот вид сваривания используется на многих производствах и предприятиях. Он обладает простым технологическим процессом экономичностью расходных материалов.
Все элементы которые применяются при сваривании имеют компактные размеры это намного облегчает маневренность а высокая производительность обеспечивает около 10 часов беспрерывной работы. И это еще не все положительные качества сварочного процесса.
Ручная дуговая сварка - это распространенный способ сваривания который обладает важными особенностями. Во время технологии осуществляется быстрое разогревание металла до температурных показателей плавления. Все это достигается благодаря влиянию электрической дуги возникающей как эффект пробоя воздуха между электродом и свариваемыми заготовками. В область сварного шва вводятся дополнительные материалы они заполняют зазор который часто образуется между свариваемыми деталями.
Чтобы точно понять определение ручная дуговая сварка стоит внимательно рассмотреть особенности создания сварочной ванны. Она образуется в области нагревания. В этой зоне смешивается расплавленный металл детали с материалом присадочной проволоки.
Обычно наверх всплывает шлак в расплавленном виде - это сгоревшая обмазка плавящегося электрода или остатки неплавящегося стержневого элемента. Шлак обеспечивает защиту раскаленной металлической основы от вредного воздействия газовых смесей которые находятся в атмосфере. Данное воздействие может вызвать окисление шва. Это облегчает попадание в его структуру атомов газа в итоге происходит снижение прочностных качеств сварного соединения. Ручная дуговая сварка может осуществляться при помощи двух видов электродов - плавящегося и неплавящегося. Первый вид является присадкой он может применяться без дополнительных элементов. При применении второго вида обязательно в расплав следует вводить присадочную проволоку.
Существует разные техники проведения дугового сварочного процесса. Простая рекомендует использовать простой и недорогой сварочный аппарат переменного или постоянного тока а также необходимые защитные средства для сварщика.
Но существуют сложные виды сварок к примеру аргонодуговая которая требует наличия горелки с соплом через которую подается аргон или другая защитная газовая смесь. Инициирование сварочной дуги осуществляется при помощи короткого замыкания которое образуется в результате контакта электрода с массой. Показатель температуры дуги может доходить до 50000С.
Преимущества и недостатки
Что такое дуговая сварка мы рассмотрели но все же пред тем как приступать к этому процессу стоит узнать его положительные и негативные качества. Эта технология пользуется высокой популярностью она прекрасно подходит для разных областей производства. При помощи нее можно производить сваривание разных видов металлов использовать для ремонта важных металлических конструкций.
РД сварка имеет другие не менее важные положительные особенности:
Способ сварки РД требует применения недорогих и простых сварочных аппаратов тип РДС. Они обладают компактными размерами и легким применением.
Для работы нет необходимости использовать дополнительные средства защиты для сварочной зоны в виде флюса или газовых смесей. С данной функцией отлично справляются электроды.
Вид сварки РД позволяет производить работы в любых условиях - на улице в цехах на ветру под плавящимся солнцем. Это имеет особую важность при проведении работ в «полевых» условиях.
Ручная сварка отлично подходит для работы с разными видами металлов. Ее можно применять для углеродистых легированных сталей чугуна алюминия меди.
Сварка может применяться для металлических изделий толщина которых может быть 2-3 сантиметра.
Этот вид сварочного процесса обладает простой технологией с ней может справиться даже неопытный сварщик.
Однако стоит помнить что технология ручной дуговой сварки имеет отрицательные качества:
Проведение ручного дугового сварочного процесса требует постоянные перерывы в работе. Они необходимы для смены расплавленного электрода на новый.
При отсутствии опыта или во время сваривания толстых металлических изделий может наблюдаться чрезмерный расход электродов. Замена производится когда длина электрода достигает 5 см и меньше.
Технология ручной дуговой сварки плавящимся электродом сопровождается образованием шлака. Он оказывает положительное влияние на состояние сварочного процесса шлак защищает область сварной ванный от кислорода. Однако после работы поверхность необходимо будет хорошо очистить и это может вызвать некоторые сложности.
Качество сварных соединений напрямую зависит от квалификации сварщика.
Ручная сварка по сравнению с другими методами сваривания имеет низкий КПД и относительно невысокую производительность.
При помощи ручной дуговой наплавки угольным электродом не получится сварить изделия из оловянной или цинковой основы а точнее все металлы имеющие низкую температуру плавления. Это связано с тем что при проведении сварки электрической дугой отмечается сильное повышение коэффициента тепловложения.
Ручная дуговая сварка плавящимся электродом не предназначена для работы с титаном танталом и любыми другими видами металла которые имеют активные химические свойства. Стержневые элементы не смогут предотвратить окисление области шва.
Во время проведения сварки ток проходит по всей длине электрода. Если его показатели будут высокими то стержень перегреется и сварное покрытие разрушится.
Ручная дуговая сварка MMA пользуется широкой популярностью. Ее применяют при сваривании конструкции разного назначения и размера. Она может использоваться при выполнении обычных работ в доме на даче а также в более широких масштабах - а производстве при изготовлении огромных изделий из металла.
Среди главных областей промышленности где применяют данный вид сварочной технологии можно выделить:
разные сервисные и ремонтные работы к примеру автомобильная техника;
сваривание трубных конструкций для воды газа нефтяных продуктов;
кораблестроение (сварка листов корпуса);
многие разновидности машиностроения.
РД сварочные работы часто применяются для проведения наплавок на поверхность деталей иных видов металла. Этот метод нашел широкое применение в бытовых условиях его часто используют для сваривания беседок скамеек мангалов качелей применяют для ремонта изделий из металлической основы.
Особенности технологии
Техника и технология дуговой ручной сварки основывается на создании замкнутого контура по которому проходит ток разного вида - постоянного переменного или высокочастотного импульсивного типа. Образование дуги происходит во время моментальной подаче напряжения к электроду после его касания со свариваемой металлической поверхностью. Тепло которое необходимо для плавления кромок получают от электрической дуги. В зоне действия дуги происходит образование области жидкого расплава в которой возникает перемешивание металла обеих заготовок. Во время остывания они кристаллизуются образуют единое целое а именно сварной шов. Данную область расплава перемещающуюся вслед за электродом и дугой вдоль линии шва называют сварочной ванной.
Металлический стержень электрода покрывают специальным составом который называется флюсом. Во время сильного нагревания он расплавляется образует инертный газ который формирует защитное облачко над рабочей зоной и предотвращает окислительные процессы при взаимодействии расплава с кислородом.
Для поддержания электродуги на держатель и на заготовки подается напряжение от источника. Технология выполнения ручной дуговой сварки цветных металлов и сплавов которые проявляют высокую химическую активность в нагретом состоянии выполняется в атмосфере специально подаваемых газов с защитным действием в рабочую зону.
Имеется несколько основных приемов и движений стержней относительно поверхностей:
затягивание отверстий и прожогов «перетаскиванием». Во время этого процесса расплавленная металлическая смесь натягивается с поверхности на поверхность при помощи электродов;
сварочный процесс «полумесяцем» или «зигзагом».
Обычный балансный инвертор с мощностью 220 В при номинальном повышении тока может применяться для разрезания листовых металлических заготовок а также в виде прутка. При стандартном режиме аппарат используется для сварочного процесса.
Чтобы выполнение ручной дуговой сварки было правильным а шов качественным стоит запомнить несколько важных правил:
Подача тока должна осуществляться постоянно.
Все поверхности и электроды должны быть в сухом состоянии иначе сварочная ванна начнет искрить а шов будет кривым и непрочным.
Сварочный кабель не должен иметь трещин повреждений обрывов. В противном случае ток перейдет в фазу и электрод залипнет в сварочной ванне. В результате это приведет к замыканию и порче сварного шва под воздействием раскаленного электрода.
Аргонодуговая сварка
Чтобы сварить детали из нержавеющей стали меди титана алюминия различных цветных металлов и сплавов обычные методы сварки не всегда подходят. Часто для этих целей многие опытные сварщики применяют сварку аргоном. Этот процесс достаточно тяжелый длительный и специфический. Но чтобы понять технологию стоит рассмотреть важные особенности нюансы правила проведения. Это позволит создать прочную и неразъемную конструкцию.
Перед тем как приступать к работе стоит рассмотреть что такое аргонная сварка и для чего она проводится. Это технология гибридного типа которая позволяет соединять конструкции из капризных и устойчивых металлических основ -от огромных труб до мелких деталей статуэток из бронзового металла.
Прежде чем понять что это такое аргонно-дуговая сварка стоит разобраться с физикой данного процесса. Для того чтобы соединить металлические поверхности их требуется предварительно прогреть. Нагревание обычно производится при помощи огня. Именно это способствует вступлению в реакцию кислорода который находится в воздухе -происходит процесс окисления. Стоит учитывать что цветные металлы легированные стали окисляются намного быстрее чем обычные металлы.
Окисление которое проявляется во время сварочного процесса вызывает ухудшение качества соединений. В связи с тем что в составе швов появляются многочисленные пузырьки они теряют свою прочность и быстро разрушается. А алюминиевый металл варить невозможно при нагревании он горит и разрушается.
Технология аргонодуговой сварки основывается на использовании сварочной ванны которая защищает от газов и примесей. Для этих целей часто применяются инертные газы которые выполняют роль защитной оболочки. Помимо аргона к инертным газам относится гелий который обладает такими же свойствами. Однако гелий намного дороже аргона и он расходуется намного быстрее и больше.
Применение аргона позволяет сэкономить силы и финансовые вложения. Кроме этого этот газ может использоваться для всех цветных металлов включая нержавейку медь алюминий. К главным свойствам аргона стоит отнести:
Аргон значительно тяжелее воздуха по этой причине он отлично вытесняет его из сварочной ванны тем самым защищая зону плавления от ненужных газовых примесей;
Аргон является инертным веществом которое не способно вступать ни с какими элементами включая свариваемые металлические поверхности;
Не стоит забывать про важный нюанс аргонового газа. Во время применения тока с обратной полярностью аргон переходит в состояние электропроводной плазмы со всеми негативными последствиями.
Классификация аргонодуговой сварки
Сварка аргоном цветных металлов может производиться несколько способами. Каждый из них обладает отличительными особенностями от которых зависит качество и прочность сварного шва.
Выделяют следующие виды аргоновой сварки:
Ручной способ -РАД сварка.Перед тем как приступать к РАД сварке стоит рассмотреть что это за процесс. Работа выполняется сварщиком он производит перемещение горелки подачу сварочной проволоки. Во время него применяются только вольфрамовые электроды;
Механизированная или полуавтоматическаясварка металла аргоном. Во время этого процесса проволока подается при помощи машины а горелку удерживает сварщик. К самому популярному примеру этого метода относится сварка нержавейки полуавтоматом. Механизированная аргоновая сварка дуговая при помощи плавящегося электрода также относится к этому методу. Сварочный процесс нержавейки полуавтоматом в среде углекислого газа -является еще одной узкоспециализированной технологией которая также относится к этой группе;
Автоматическая аргонодуговая сварка.Во время этого процесса автомат управляется дистанционно оператором и производит перемещение и подачу проволоки. В последнее время часто во время автоматических сварочных процессов применяются специальные устройства -роботы которые не требуют участия человека. Данный метод пользуется популярностью на больших производствах.
Особенности сварного шва при аргонодуговой сварке
Рассматривая что это такое аргонная сварка стоит обратить внимание на особенности сварного шва. Важно помнить о том чем больше будет угол наклона между поверхностью основного металла и соединения тем выше будет концентрация напряжения в области сварки. Если к сварному шву предъявляются высокие требования по равнопрочности то после сварки требуется произвести стачивание шовного валика.
Техника сварки аргоном предполагает правильный подбор материала электрода и присадочной проволоки также требуется выбрать необходимый режим сварки. Обязательно выбирается способ защиты металлического шва который обеспечивается за счет меньшего количества примесей а сама область шва при этом должна быть немного мягче основного металла.
Чтобы обеспечить высокую прочность и износостойкость мягкая зона должна быть узкой. Это усложняет проведение сварочного процесса но избавляет от необходимости усиления конструктивных элементов в области соединения.
Различные технологии
Помимо отечественной терминологии применяются зарубежные обозначения которые помогают разделить сварку в среде аргона на несколько подвидов. Каждый из них обладает уникальными качествами особенностями. Обычно они применяются для сваривания сталей с различными добавками сплавов из алюминиевой основы.
Сварка в аргоновой среде разделяется на следующие подвиды:
Сварка ММА.Процесс производится по ручной технологии в поле электрической дуги образованном электродом с покрытием. При переменном токе данным способом можно варить углеродистую сталь. А если будет оказываться постоянным ток то будет возможность производить сварку углеродистой и нержавеющей стали а также алюминия и его сплавов;
Сварочный процесс TIG.Он выполняется в ручном режиме в аргоне или в другом инертном газе при помощи вольфрамового электрода. При переменном токе так можно варить только алюминий и его сплавы. При постоянном -углеродистые и нержавеющие виды сталей;
Сварка MIG.Это полуавтоматическое сваривание которое производится при помощи плавящейся проволоки. Данная технология аргоновой сварки производится с использованием переменного тока. Свариванию подлежать оба типа металлов а также алюминий со сплавами.
Преимущества и недостатки аргонодуговой сварки
Рассматривая что такое аргонодуговая сварка стоит изучить ее важные положительные и отрицательные особенности. Они оказывают влияние на проведение процесса на свойства получаемого соединения на его прочность и другие важные нюансы.
Среди преимуществ стоит выделить:
Принцип аргонной сварки предполагает проведение нагрева с невысокой температурой. Именно это свойство позволяет в полной мере сохранить размеры и формы двух свариваемых изделий;
Аргон для сварки является инертным газом а именно он плотнее и тяжелее воздуха. Именно это обеспечивает максимальную защиту зоны сваривания;
Тепловая мощность дуги обладает высокими показателями именно это позволяет проводить процесс сварки за короткий промежуток времени;
Аргонодуговая сварка обладает простой техникой проведения которую смогут понять даже неопытные сварщики;
Сварочный процесс позволяет соединить разные виды металлов которые не получается состыковать при помощи других типов сварок.
Но не стоит забывать про некоторые недостатки аргонной сварки:
В теории указывается что сварка аргоном не должна проводиться при сильных сквозняках и ветре. Во время данных условиях происходит улетучивание часть аргонной защиты. Именно это снижает качество сварного шва. По этой причине весь процесс требуется проводить в закрытых помещениях с хорошей вентиляцией;
Сварочное оборудование которое применяется для сварочного процесса обладает сложной конструкцией и тяжелым управлением. Это может усложнить проведение настройки режимов сварки;
Если в процессе соединения потребуется высокоамперная дуга то обязательно требуется продумать дополнительное охлаждение стыкуемых компонентов.
Что это такое аргонная сварка и для чего она нужна? Чтобы понять этот процесс и его главное назначение стоит рассмотреть его главные особенности характерные качества и нюансы. Данная техника может использовать для капризных и устойчивых металлов к примеру для сваривания меди бронзы алюминия и разных цветных металлов.
Проведение процесса простое и легкое с ним сможет справиться даже начинающий сварщик. Но все же не стоит забывать про правила и главные особенности сварочных работ в аргоне.
При неразрушающем контроле высоколегированных сталей возникают определенные трудности как при контроле ультразвуковыми способами так и при радиографическом контроле.[13]
Основными проблемами возникающими при проведении УЗК аустенитных сварных швов по сравнению с углеродистыми и низколегированными сталями являются значительное затухание и высокий уровень структурных помех вызванных рассеянием ультразвуковых волн в поликристаллическом материале.
Идентификация (распознавание) изображений структуры основывается на общей схеме идентификации изображений сомнительного происхождения включающей в себя три последовательных этапа причем каждый последующий этап реализуется если предыдущие этапы не дают гарантированного однозначного ответа на вопрос о происхождении идентифицируемых изображений:
Использование эталонных снимков с характерными изображениями различной природы.
Проведение повторного просвечивания сомнительных участков сварных соединений при измененных параметрах просвечивания.
Послойное вскрытие или металлографические исследования (вырезка шлифов) сомнительных участков сварных соединений.
К преимуществам рентгенографии можно отнести:
- визуализацию дефектов сварного шва и однозначное их понимание;
- незначительные в сравнении с ультразвуковым контролем требования к квалификации дефектоскопистов.
Сравнительная характеристика выявляемости дефектов радиационным и ультразвуковым методами приводится в табл. 2.
Сравнительная выявляемость дефектов методами неразрушающего контроля в сварных соединениях выполненных сваркой плавлением
Выявляемость дефекта баллы
Газовые поры и шлаковые включения
Трещины поверхностные и подповерхностные
Таким образом подытожив вышесказанное и с необходимым обеспечением режима сварки позволяющего получить швы с мелкозернистой структурой остановимся на ультразвуковом способе.
Принятый вариант: ультразвуковая дефектоскопия.
Рассмотрим два метода ультразвукового контроля применяемых для небольших толщин не требующих слишком сложного оборудования и двухстороннего доступа.
Импульсный эхо-метод широко используют для основных видов сварных соединений — стыковых угловых и тавровых с толщиной листов от 4 до 20 мм (и более). Этим методом контролируют примерно 90 % всех сварных соединений толщиной более 4 мм. Чувствительность эхо-метода высокая: она достигает 05 мм2 на глубине 100 мм.
К преимуществам следует также отнести:
- возможность использовать односторонний доступ к зоне шва поскольку достаточен только один преобразователь и для излучения и для приема У3-сигналов;
- хорошую помехоустойчивость;
- высокую точность определения координат дефектов.
Рис. 6. Контроль эхо-методом: 1 – генератор; 2 – усилитель; 3 – индикатор; 4 – объект контроля; 5 – преобразователь
Недостатки эхо-метода: низкая помехоустойчивость к наружным отражателям и значительная зависимость отражённого сигнала от ориентации дефекта.
Рис. 7. Контроль зеркально-теневым методом: 1 – генератор; 2 – усилитель; 3 – ЭЛТ; 4 – ПЭП; 5 – шов
Зеркально-теневой метод также не требует двустороннего доступа к соединению. Его используют когда дефекты не дают эхо-сигнала (например из-за наличия мёртвой зоны или в связи с неблагоприятной ориентацией дефекта) но ослабляют донный сигнал. Его преимуществами являются низкая зависимость амплитуды сигнала от ориентации дефекта высокая помехоустойчивость и отсутствие мёртвой зоны. Недостатками метода являются: сложность ориентации ПЭП относительно центральных лучей диаграммы направленности невозможность точной оценки координат дефектов и более низкая чувствительность (в 10-20 раз) по сравнению с эхо-методом.
Принятый вариант: эхо-метод ультразвукового контроля.
Править сталь листовую:
предел текучести металла : 200 Мпа; предел прочности 500 Мпа;
Правка достигается многократным изгибом при пропускании листов между верхним и нижним рядами валков расположенных в шахматном порядке. Технические данные листоправильных машин приводятся в табл.2 . По её данным выбираем машину 11×230×1700 с 11 валками.
Технические данные многовалковых листоправильных машин
С помощью мостового крана захватываем лист и перемещаем к листоправильной машине.
Заводим лист с помощью кранбалки в валки и осуществляем правку за один пропуск листа между валками .
С помощью мостового крана подаем выправленный лист на координатный стол установки для резки. Модель установки R—LCM 3060.
Рис.9. Установка гидроабразивной резки
Технические характеристики установки для гидроабразивной резки
Наименование параметра
Скорость перемещения головки мммин
Рабочее давление бар
Давление воздуха бар
Абразивная трубка мм
Уровень подачи абразива гр.мин
Разреаемая толщина материала мм
Регулировка потока абразива
Индикация нижнего уровня абразива
Программное обеспечение
Насос высокого давления
Задаем координаты линии реза и производим резку листа в размер 3774х1201 мм.
Рис.10. Схема раскроя листа
Требуется завальцевать лист в обечайки диаметром внутренним 1200 мм.
Для этой цели используем четырехвалковый станок модели – ИА 2426
Техническая характеристика станка
Толщина изгтбаемых листов при т = 250 Мпа
Наименьший радиус изгиба
Краном установить лист в валки;
Проверить параллельность оси валка и кромок листа;
Вальцевать лист без подгибки кромок начиная со средней части.[12]
Рис. 11. Схема гибки
Необходимо зачистить листы под сварку в обе стороны от оси стыка на величину не менее 20 мм.
Для данной операции выберем пневматическую шлифовальную машинку ПШМ-08-60.
Технические характеристики шлифмашинки
Наибольший диаметр шлифовального круга в мм
Скорость вращения шпинделя в обмин
Расход воздуха под нагрузкой м. кубмин
Краном снять обечайку с вальцев и установить на стенд для сборки ;
Зачистить прилегающую зону от оси стыка с внутренней стороны;
Повернуть обечайку на 90 градусов и зачистить прилегающую зону от оси стыка с наружней стороны;
1. Технология сборки и сварки корпуса
Процесс сборки и сварки корпуса осуществляется в приведенной ниже последовательности:
Стропить завальцованную обечайку и подать на стенд для сборки продольных швов;
Установить гидравлическую стяжку и выровнять торцевые кромки в плоскости перпендикулярной продольной оси обечайки;
Рис. 13. Схема выравнивания обечайки по тоцевым кромкам
Установить гидравлическую стяжку и выровнять кромки продольного стыка;
Рис.14. Схема сборки продольного стыка
Прихватить обечайку ручной дуговой сваркой начиная с середины стыка;
Прихватить выводные планки;
Рис.15. Выводные технологические планки
Закрепить собранную обечайку с помощью захватов специальных и подать на роликовый стенд;
Установить сварочный трактор в зону наложения внутреннего продольного шва;
Установить флюсовую подушку;
Установить сварочную проволоку относительно оси зазора соединения;
Заварить внутренний шов;
Повернуть обечайку на 180 градусов;
Установить сварочный автомат в зону наложения наружного продольного шва;
Заварить наружный шов;
Срезать выводные планки и зачистить места среза;
Закрепить обечайку и подать на гибочные вальцы;
Калибровать обечайку с точностью +-1.5 мм;
( Примечание: операции повторить по количеству обечаек);
Установить сваренные обечайки в установку для сборки кольцевых стыков;
Завести скобу в обечайки
Рис.16. Сборка обечаек по кольцевым стыкам
Поджать левую обечайку к упору;
Рис.17. Схема прижима левой обечайки
Прижать правую обечайку к левой;
Рис. 18. Схема прижатия правой обечайки к левой
Прижать кромки обеих обечаек к верхним упорам
Рис.19. Схема поджатия кромок
Прихватить состыкованные обечайки;
Установить сварочный трактор в зону наложения внутреннего кольцевого шва шва;
Заварить внутренний кольцевой шов;
Установить сварочный автомат в зону наложения наружного кольцевого шва шва;
Заварить наружный кольцевой шов;
Сварочный электрод— металлический или неметаллический стержень из электропроводного материала предназначенный для подвода тока к свариваемому изделию. В настоящее время выпускается более двухсот различных марок электродов причем более половины всего выпускаемого ассортимента составляют плавящиеся электроды для ручной дуговой сварки].
Для образования электрической дуги для сварочного процесса необходимы токопроводящие элементы - две детали подлежащие сварке и электрод. Электрическая дуга появляется при их соприкосновении и сразу начинают одновременно плавиться металл изделия и конец электрода. Удачно выбрать электрод можно согласно рекомендациям и советам продавца а правильно им пользоваться для получения красивого надежного и прочного шва является искусством.
Умение как правильно варить сваркой электродами приходит с опытом. Промышленность выпускает большое разнообразие этого инструмента в зависимости от диаметра технологии процесса наличия покрытия. Существенным является и ценовое различие. Для ответственных конструкций выбор более дорогого варианта окупит себя получением надежного соединения и сведением к минимуму возникновение дефектов.
Сварочные электроды делятся на плавящиеся и неплавящиеся. Неплавящиеся электроды изготовляют из тугоплавких материалов таких каквольфрампо ГОСТ 23949-80[4]"Электроды вольфрамовые сварочные неплавящиеся" синтетическийграфитили электротехническийуголь. Плавящиеся электроды изготавливают из сварочной проволоки которая согласно ГОСТ 2246—70[5]разделяется на углеродистую легированную и высоколегированную[6]. Поверх металлического стержня методом опрессовки под давлением наносят слой защитного покрытия. Роль покрытия заключается в металлургической обработкесварочной ванны защите её от атмосферного воздействия и обеспечении более устойчивого горениядуги.
Для этой конструкции возьмем электрод марки УОНИ-1345 диаметром стержня 3мм
Характеристики электродов УОНИ-1345
Основное назначение материала – сварка деталей из низко- или среднеуглеродистой стали при монтаже особо ответственных конструкций. Благодаря этим электродам получают шов с повышенной пластичностью и ударной вязкостью. Созданные конструкции могут десятилетиями эксплуатироваться в условиях низких температур. Типичный пример – трубопроводы прокладываемые в северных широтах России.
Высокая пластичность и ударная вязкость металла шва обеспечиваются благодаря основному покрытию стержня:
-в составе обмазки присутствует фторид кальция (CaF2);
-в процессе сварки вредный для металла водород связывается с фтором в летучее соединение и испаряется с поверхности металла.
Таким образом количество водорода в металле сводится к минимуму. Благодаря этому в нем исключены горячие трещины а риски появления холодных (из-за диффузии водорода) также практически сведены к нулю. Благодаря этим же свойствам шов не растрескивается в сероводородной среде. Это позволяет использовать трубы не просто в северных климатических зонах но и на участках где присутствуют месторождения с высоким содержанием сероводорода (нефтяные и газовые).
Стандарт в соответствии с которым выпускаются электродыУОНИ-1345– ГОСТ 9467–75. Материал стержней – сталь марок СВ08А и СВ08.
Электроды имеют основное (фтористо-кальциевое) покрытие.
Временное сопротивление разрыву – 460 МПа.
Предел текучести – 350 МПа.
Коэффициент наплавки – 95 гА·ч.
Производительность наплавки – 13 кгч (для d 3 мм).
Расход электродов на 1 кг наплавленного металла – 16 кг.
Род используемого при сварке тока – постоянный обратной полярности.
Пространственное положение сварки – любое за исключением вертикального на спуск.
Изделия изготавливаются диаметром 2 25 3 4 5 мм.
Основные преимущества УОНИ-1345
Легкое начальное и повторное зажигание.
Устойчивое горение электродуги.
Высокая глубина проплавления что позволяет варить толстостенные детали.
Малое количество разбрызгиваемого металла.
Легкое отделение шлаковой корки.
Крайне низкое содержание водорода в металле шва.
Высокая стойкость металла к появлению кристаллизационных трещин.
Сравнительно невысокий расход стержней.
Типичный химический состав наплавленного металла: C – 009% Mn – 057% Si – 025% S – 0014% P – 0017%.
Особенности использования
Перед сваркой электроды необходимо прокалить в течение часа при температуре 350°С. В числе других особенностей:
Сварка выполняется на воздухе или в хорошо проветриваемых помещениях. Это обусловлено выделением вредных для здоровья летучих фтористых соединений.
Поверхности свариваемых деталей должны быть очищены от окалины грязи следов ржавчины влага должна быть удалена.
Удлинять дугу не рекомендуется – это нарушает стабильность ее горения и может вызвать образование пор в металле.
Использование для сварки переменного тока возможно но также не рекомендуется из-за рисков неустойчивого горения электродуги.
Помимо трубопроводов используемых в нефтяной газовой химической промышленности электроды этой марки широко применяются для производства:
-строительных конструкций;
-транспортного оборудования (в том числе для перевозки опасных грузов);
-оборудования для предприятий металлургии.
Также с их помощью изготавливаются котлы и котельное оборудование техника для нефтедобывающей отрасли.
Под режимом сварки понимают совокупность условий протекания процесса сварки. Параметры режима сварки подразделяют на основные и дополнительные. К основным параметром режима сварки при ручной сварки относят величину род и полярность тока диаметр электрода напряжение скорость сварки и величину поперечного колебания конца электрода а к дополнительным-величину вылета электрода начальную температуру основного металла положения электрода в пространстве и положения изделия в процессе сварки. При ручной дуговой сварке за один проход могут свариваться швы катетом не более 8мм. При больших катетах швов сварка производится за два или более проходов. Максимальное сечение металла наплавленного за один проход не должно превышать 30-40 мм² (Fмах= 30-40мм²).
Площадь поперечного сечения углового шва которую необходимо знать для определении числа проходов рассчитывают по формуле:
Где Fн – площадь поперечного сечения наплавленного металла мм²;
h-высота детали; f-область сварки.(ГОСТ)
Определив переменную площадь сечения углового шва и зная максимально возможную площадь сечения получаемую за один проход находят число проходов «n» по формуле:
n = Fн(30-40) = 6.7530 = 02251
Силу сварного тока определяют по формуле:
где dэл – диаметр электрода мм;
j – допустимая плотность тока Aмм²;
Iсв – сила сворного тока A
Плотность тока выбирается в пределах рекомендуемых в таблице:
Диаметр электрода мм
Iсв = (314 30²4) 145 = 9891 A
После следует вычеслить скорость сварки который определяется по формуле:
Vсв = Lн Iсв(γ Fн) = 95 9891(78 675) = 18 мr
где Lн – коэффициент наплавки rA час;
γ – плотность наплавленного металла rсм³;
Fн – площадь поперечного сечения
Напряжения дуги определяется по формуле:
U = 20 + 004 Iсв = 20 + 004 9891 = 24B
Объем наплавленного металла:
V= Fнl=11610^(-6) 1=0.000116 м^2
Масса наплавленного металлл:
M=Vγ=0.0001167850=1кгм
Диаметр электрода выбирается в зависимости от толщины металла при S стенки равной 14 мм примем диаметр электрода равный 4 мм.
При приближенных подсчетах сила сварочного тока может быть определена по формуле
где к - (теоретический коэффициент) =35; [17]
d- диаметр электрода;
4. Характеристика применяемого оборудования и сборочно -сварочных приспособлений
При изготовлении корпуса выберем следующее оборудование:
- Для сварки наружных кольцевых и продольных швов используем самоходный сварочный автомат АБС.
Технические данные автомата АБС.
-диаметр электродной проволоки 2 – 6 мм;
-скорость подачи электродной проволоки 048 – 366 ммин;
-скорость сварки 14 – 110 мч;
-номинальный сварочный ток 1500 А;
-диапазон регулирования сварочного тока 300 – 1500 А;
-напряжение питающей сети 220380 В;
-габаритные размеры сварочного аппарата 6105851750 мм;
Для сварки внутренних продольных и кольцевых швов выберем сварочный трактор ТС 73УХЛ3
Технические характеристики сварочного трактора ТС 73УХЛЗ
Номинальный сварочный ток постоянный при ПВ 100% А
Диапазон регулирования скорости подачи мч
Диапазон регулирования скорости сварки мч
Наибольшая скорость сварки мч
Регулировка мундштука по горизонтали поперек шва град
в кассете электродной проволоки кг
Вместимость бункера для флюса дм3
Габаритные размеры трактора мм не более L х B х H
трактора без флюса электродной проволоки кг
Габаритные размеры шкафа управления мм не более L х B х H
Масса шкафа управления кг
Диаметр электродной проволоки мм
Для перемещения сварочной головки используем велосипедную тележку ВТ-2 [20].
Технические характеристики ВТ-2
Расстояние от оси колонны до оси электрода при установке автомата АБС мм
Высота уровня сварки (от основания колонны до конца электрода мм
Скорость подъема и опускания каретки с консолью
Пределы бесступенчатого регулирования рабочей скорости перемещения тележки
Габаритные размеры (длина ширина высота)
Для обеспечения вращения изделия со скоростью необходимой для сварки используем роликовый стенд 70 СДА
Техническая характеристика стенда 70 СДА
Максимальный крутящий момент на выходном валу привода
номинальная грузоподъемность стенда
Регулировка скорости сварки
плавная бесступенчатая
В качестве источников питания для сварки используются:
Выпрямитель сварочный ВДУ 1250У3 для автоматической сварки
Технические данные ВДУ 1250У3.
Для выполнения прихваток при ручной дуговой сварке применяем выпрямитель сварочный ВД 506 ДК У3
Технические данные ВД 506 ДК У3.
Для сборки продольных стыков обечаек используется
установка состоящая из :
-струбцина гидравлическая;
-стяжка гидравлическая для выравнивания торцов обечаек;
Рис.21. Установка для сборки продольных швов
Установка применяется для обечаек диаметром 05-15 м при длине обечаек до 21 м. Цилиндры стяжек развивают усилие до 1200 кгссм.кв.
Для сборки кольцевых стыков используется установка состоящая из:
- направляющая вертикального перемещения скобы;
- привод перемещения скобы;
- привод вертикального перемещения скобы;
-14 – конечные выключатели;
Рис.22. Установка для сборки по кольцевым стыкам
На подобных установках собирают сосуды диаметром от 05 м (при толщине стенки до 16 мм) до 5 м (при толщине стенки до 50 мм).
Проектирование компоновки установки и описание ее работы
1. Состав установки и предъявляемые к ней требования
Установка для сварки состоит из следующих частей:
-Велосипедная тележка ВТ-2
-Самоходный сварочный автомат АБС
-Роликовый стенд 70 СДА
Рис.23. Общий вид установки
При проектировании установки каждое из устройств должно отвечать определенным требованиям:
Роликовый стенд должен обладать необходимой грузоподъемностью обеспечивать необходимую скорость вращения;
Сварочный автомат должен обеспечивать подачу сварочной проволоки с необходимой скоростью требуемой для сварки.
В качестве устройства для вращения изделия используем роликовый стенд 70 СДА. Стенд имеет шкаф управления с дистанционным пультом. На шкафу имеются переключатели диапазона скоростей :
- диапазон 4- 200 мч
Скорость обеспечивается плавной бесступенчатой регулировкой с помощью регулятора.
Для автоматической сварки под флюсом используем сварочный автомат АБС с подъемным механизмом и флюсоаппаратом. Данный аппарат имеет следующие пределы установочных и регулировочных перемещений головки:
- вертикальный подъем 200 мм
- поперечная корректировка электрода +- 75 мм
- угол наклона мундштука +- 45 градусов
Для коррекировки сварочной головки вдоль изделия и перемещения вверх и вниз используется велосипедная тележка ВТ-2.
Тележка перемещается по нижнему опорному рельсу на бегунках приводимых в движение электродвигателем постоянного тока установленным на платформе через редуктор и передачу из шестерен вращающую вал ходового механизма [21].
Работа установки описывается следующим образом:
После сборки обечаек по кольцевым стыкам с пульта управления расположенного на платформе тележки следует осуществить опускание консоли с автоматом на требуемое расстояние от стыка засыпать флюс в бункер выставить вылет электрода в пределах 30 мм и произвести поперечную корректировку электрода относительно оси стыка.
Установить с помощью сменных шестерен необходимую скорость подачи проволоки сместить электрод от зенита на величину в пределах 40 мм. На роликовом стенде установить с помощью реостата требуемую скорость сварки на источнике питания установить необходимый для сварки ток. Для обеспечения лучшего контакта с изделием откусить конец проволоки и с помощью подачи уперев в изделие засыпать флюсом. Включить сварочный ток и одновременно с дистанционного пульта включить роликовый стенд на необходимой скорости. Осуществить процесс сварки.
Разработка технологии контроля
Подвергнуть внешнему осмотру 100 % длины всех сварных соединений корпуса по РД 03-606-03. При проведении контроля используют лупу ×3 и универсальный шаблон А.И.Красовского.
По внешнему виду сварные швы должны удовлетворять следующим требованиям:
- швы должны иметь гладкую или равномерно чешуйчатую поверхность (высота или глубина впадин не должна превышать 1 мм);
- металл шва должен иметь плавное сопряжение с основным металлом;
- швы не должны иметь недопустимых внешних дефектов.
К недопустимым внешним дефектам сварных соединений оболочковых конструкций относятся трещины любых видов и размеров несплавления наплывы грубая чешуйчатость наружные поры и цепочки пор прожоги и свищи.
Только после внешнего осмотра изделия подвергают каким-либо физическим методам контроля для определения внутренних дефекто .
2. Контроль наличия внутренних дефектов
Произвести ультразвуковой контроль по ГОСТ 14782. Контроль осуществляется с помощью УЗ-дефектоскопа УД2-70 технические характеристики которого приводятся в табл. 16.
Основные технические характеристики ультразвукового дефектоскопа УД2-70
Диапазон толщин контролируемого материала (по стали)
; 1.25; 1.8; 2.5; 5.0; 10.0 МГц
Частота зондирующих импульсов
; 60; 120; 250; 500; 1000 Гц
Полярность зондирующего импульса
Амплитуда зондирующего импульса на нагрузке 50 Ом
Длительность зондирующего импульса
Диапазон регулировки усиления
Шаг регулировки усиления
Дискретность изменения усиления скачком "+дБ
Диапазон задержки развертки
Диапазон измерения глубины залегания дефектов (по стали)
Дискретность измерения глубины
Погрешность измерения глубины
Диапазон установки угла ввода ПЭП
Дискретность установки
Количество стробов АСД
Диапазон установки скорости УЗК
Глубина регулировки ВРЧ
Размер рабочей части экрана
не менее 320 х 240 точек.
Диапазон рабочих температур
Электрическое питание:
- сеть переменного тока
Время непрерывной работы
Степень защиты корпуса
Масса с аккумулятором
При проведении ультразвукового контроля необходимо выполнить следующие требования [22].
-Поверхность околошовной зоны вдоль контролируемого шва с обеих сторон должна быть зачищена на расстояние – 100 мм;
- Прозвучивание стыкового соединения корпуса произвести с двух сторон от шва с контролем прямым и однократно отраженными лучами обеспечивающими контроль всего сечения сварного соединения.
Рис.24. Схема прозвучивания
-Сканирование выполнять путем поперечно-продольного перемещения преобразователя. В процессе перемещения осуществляют поворот преобразователя на ± (10-15)° относительно линии поперечного перемещения.
Рис. 25. Схема продольно-поперечного сканирования
Параметры контроля при Sст = 14 мм.
- Угол ввода луча 70 градусов
- Рабочая частота 25 МГц
- Стрела преобразователя 10 мм
- Предельная чувствительность 20 мм
отраженный луч 35-75 мм
При выполнении работ ручной дуговой сварки рабочий может столкнуться со следующими опасностями:
-Ожоги от капель металла.
-Поражение глаз дугой.
-Поражение кожи электродугой.
-Порезы и ушибы в процессе подготовки металла к свариванию.
-Отравление опасными газами.
-Пожар из-за плавки металла.
-Взрывы при расположении рядом взрывоопасных предметов.
Работа в рамках техники безопасности начинается с очистки рабочего места затем проверяется работоспособность оборудования заземление и пр.
Таким образом электросварщик в ходе своей работы подвергается различным опасностям. Знание основ техники безопасности охраны труда и пожарной безопасности позволит ему избежать проблем. При этом необходимо учитывать специфику процесса: при дуговой сварке действуют иные факторы риска которое отличаются от газовой. Разница связана с применением электричества для питания дуги а точнее ее ультрафиолетовым и тепловым излучением и образуемыми газами.
Одежда и средства спецзащиты
Сварочная дуга является источником излучения с разной длиной волн. Здесь присутствуют и ультрафиолетовые и инфракрасные волны. Яркость этих волн является достаточно высокой. Помимо указанных факторов риска стоит учесть что дуга горит с перерывами что обуславливает контрастность освещения.
Световое излучение при сварке может ослеплять ультрафиолетовое – приводит к ожогу роговицы инфракрасное – может вызвать помутнение и катаракту. Для избегания негативного влияния излучения сварщик должен наблюдать за работами через специальное защитное стекло. Оно защищает сетчатку глаза от светового излучения и УФ-лучей которые могут привести к ожогам. Такое стекло должно полностью удерживать ультрафиолет и стать преградой для ИК-лучей.
Остальные части тела также должны быть защищены: для этого используются маска рукавицы и спецодежда. Наиболее популярной защитной сварочной маской считается «Хамелеон». Она может адаптироваться под любую разновидность сварки и обеспечивает оптимальную видимость и надежную защиту. Отдельные модели масок оснащаются специальным турбоблоком который закачивает воздух под маску что обеспечивает длительную непрерывную работу сварщика.
По требованиям безопасности защищать следует не только самого сварщика но и лиц которые работают по соседству с ним.
К одежде сварщика также предъявляются следующие требования:
Она должна находиться в идеальном защитном состоянии и быть сухой.
Работы нужно проводить в специальных рукавицах.
При попадании капель металла спецодежда не должна тлеть и прогорать.
Без защитного головного убора проведение работ запрещено.
Желательно использование респираторов для дополнительной защиты от выделяемых газов.
Таким образом во время работы методом ручной дуговой сварки сварщик обязательно должен пользоваться индивидуальными средствами защиты: рукавицами маской и пр.
Помещение и рабочее место
Недопустимо наличие обгоревших электродов на площадке. Если рабочий материал заканчивается то остаток перемещается в специальную емкость.
Требования к помещению во многом основаны на рисках возникновения пожара и направлены на их максимальное уменьшение. Работы по сварке проводятся на первом этаже а пожаробезопасность должна соответствовать категории «Г».
Все строительные и отделочные материалы обладают уровнем огнестойкости не менее 2 степени. Запрещено делать полы которые обладают теплопроводностью. Они должны иметь несгораемую поверхность легко очищаемую от мусора и грязи.
При наличии в помещении каких-либо деревянных конструкций их нужно обшить асбестовыми листами. Поверхности которые относят к легковоспламеняемым защищаются при помощи щитков.
Вся проводка в помещении подлежит защите резиново-тканевыми шлангами. Горючие жидкости не допускается хранить в том помещении где проводятся работы так как траектория полета искры может быть непредсказуемой.
Помещение для проведения сварочных работ не должно быть стесненным и сырым. Если шланги аппарата отсыреют то это может привести к взрыву и возгоранию в процессе сварки газами и огнем. В частности идеальные показатели микроклимата в помещении – это температура в помещении порядка 15 градусов и влажность около 40%. Нужно также следить чтобы в помещении отсутствовали вредители и грызуны.
Желательно чтобы стены были окрашены в темные матовые цвета для избегания отражения лучей при сварочных работах.
Если работы производятся на улице то недопустимо проведение работ во время снега и дождя.
Сварочное место должно быть оснащено средствами пожаротушения. С учетом ведения работ с электроприборами в качества таких средств не должна выступать вода: это может быть песок углекислотный или порошковый огнетушитель. Поэтому все работники должны уметь обращаться с противопожарным оборудованием и пройти соответствующий инструктаж.
На рабочем месте не должно быть посторонних людей и предметов (в особенности горючих материалов). В закрытых помещениях нужно пользоваться резиновым ковриком во время сваривания.
Требования к помещению должны неукоснительно соблюдаться. Это является залогом безопасной работы.
Требования к оборудованию
Немаловажным для снижения риска возникновения проблем при проведении сварки является предварительная проверка сварочного оборудования. Сварочный трансформатор провода заземление клеммы прочие элементы должны быть исправны и не иметь дефектов. При наличии каких-либо неисправностей использование оборудования строго недопустимо.
Все элементы должны быть подключены и находиться на местах. Необходимо заземлить корпус у источника питания дуги и свариваемого изделия а также изолировать рукоятку держателя электрода.
Перед началом работ необходимо проверить все системы безопасности оборудования: прерывание напряжения во время холостого хода защиту от перегрева.
Электроды для выполнения работ рекомендовано хранить в сухом прохладном месте. При отсыревании они могут напитаться влагой из-за чего невозможно будет создать рабочую дугу. Если же они отсырели то перед работой стоит дополнительно просушить их в духовке.
Генераторы в процессе работы рекомендовано устанавливать таким образом чтобы не допустить их падения или неустойчивого положения. Недопустимо использование генераторов без водяного затвора. Генератор должен располагаться вертикально и быть в рабочем состоянии.
При использовании генератора при отрицательной температуре важно контролировать состояние воды. При ее замерзании шланг и затор отогревают и только затем приступают к работам.
Шланги для выполнения работ должны быть как минимум 20 м в длину. Базовые требования к шлангам: их целостность и исправность. Когда шланги складываются нельзя забывать о нормах хранения сварочных материалов: шланги складываются кольцами для того чтобы избегать их переламывания и придавливания.
Особую осторожность нужно соблюдать при работе с баллонами. При снятии металлического колпака следует проверить вентиль и штуцер на отсутствие повреждений. Запрещается резко выбивать колпак с применением ударных инструментов. При откручивании вентиля следует отслеживать чтобы газ не попадал на людей.
При выполнении самих работ с использованием сварочного оборудования необходимо придерживаться таких правил:
При соединении металла между баллоном и газом должно быть расстояние не менее 5 метров.
При длительной металлообработке шланги подвешиваются для того чтобы не допустить их повреждения.
Сварочные кабели должны располагаться на расстоянии минимум 05 м от баллонов.
Недопустимо резкое снижение давления кислорода.
Не допускается перегрев мундштука его требуется периодически прочищать для избегания засорения.
При проведении работ необходимо периодически охлаждать горелку.
Не допускается обработка трубопроводов которые находятся под давлением. Предварительно их следует опустошить а затем приступать к работе.
Работник не должен контактировать с защитой электросети (зажимами и клеммами).
Разработанный технологический процесс изготовления корпуса химического аппарата позволяет получать продукцию в количестве предусмотренным в единичном производством. При разработке технологии учтены особенности конструкции и эксплуатации изделия а также все предъявленные к нему технические требования.
Технологии изготовления типовых конструкций внедренные в производство на отечественных заводах в изучении характера соединения деталей между собой позволили определиться со способом сварки помогли с выбором оборудования для сварки а также указали на особенности сварки используемых материалов.
Проведенный анализ вариантов позволил изучить достоинства и недостатки различных способов резки сварки контроля разнообразие и возможности применяемого оборудования а также особенности применяемых схем и материалов при резке сварке и контроле.
Разработка технологического процесса заготовительных операций познакомила с некоторыми особенностями и приемами при очистке резке правке с соответствующим оборудованием и дала выяснить суть этих операций.
Разработка технологического процесса сборочно-сварочных операций позволила изучить способы и особенности транспортировки установки и закрепления деталей последовательность и характер выполнения каждой операции свойства применяемых материалов а также методику определения параметров режима который позволяет получить соединения требуемого качества.
Разработка установки для сварки наглядно продемонстрировала метод повышения уровня механизации и автоматизации процесса сварки а также возможности оборудования.
Изучение методов дефектоскопии показало каким образом осуществляется контроль сварных соединений в чем преимущества и недостатки того или иного способа возможности аппаратуры и характер ее работы.
При изучении вопросов техники безопасности удалось узнать какие условия необходимо соблюдать при работе на производстве с применением сварки и механизированного оборудования.
Таким образом разработка технологического процесса изготовления корпуса аппарата позволила изучить характер особенности и уровень механизации и автоматизации единичного производства и работу различного оборудования
Карзов Г.П. Леонов В.П. Тимофеев Б.Т. Сварные сосуды высокого давления: Прочность и долговечность. – Л.: Машиностроение Ленингр. Отд-ие 1982.
Сварка в машиностроении. Справочник. 3 – том . Под редакцией В.А. Винокурова.
ОСТ 26291-94 «Сосуды и аппараты стальные сварные. Общие технические условия» 1994 ПБ 03-584-03.
Рыжков Н.И. Производство сварных конструкций в тяжелом машиностроении Организация и технология. – М.: Машиностроение 1980.
Мошнин Е.Н. Гибка и правка на ротационных машинах Технология и оборудование.
Алешин Н.П. Чернышов Г.Г. Акулов А.И. Сварка. Резка Контроль. Справочник.
М. С. Баранов. Технология производства сварных конструкций. М.: Машиностроение 1966.
ОСТ 26.260.3 – 2001 (Сварка в химическом машиностроении).
Технология электрической сварки металлов и сплавов плавлением Под ред. Патона Б. Е. – М.: Машиностроение 1974.
А.Г. Потапьевский Сварка в защитных газах плавящимся электродом.
Н.Н. Потапов. Сварочные материалы для дуговой сварки Справочное пособие в двух томах.
Контроль качества сварки Под ред. В. М. Волченко. – М.: Машиностроение 1975.
И.А. Закс. Свака разнородных сталей Справочное пособие.
Сварка в машиностроении. Справочник. 2 – том . Под редакцией А.И. Акулова.
И.И Каховский В.Г. Фартушный К.А. Ющенко. Электродуговая сварка сталей Сравочник.
А. И. Акулов Г. А. Бельчук В. П. Демянцевич. Технология и оборудование сварки плавлением. – М.: Машиностроение 1977.
А.Н. Климов Обработка металлов давлением и сварка.
Л.П. Шебеко. Оборудование и технология автоматической и полуавтоматической сварки.
А.Д. Гитлевич. Л.А. Этингоф. Механизация и автоматизация сварочного производства.
П.И. Севбо. Конструирование и расчет механического сварочного оборудования.
СТО 00220256-014-2008 Инструкция по ультразвуковому контролю стыковых угловых тавровых соединений химической аппаратуры из сталей аустенитного и аустенитно-ферритного классов с толщиной стенки от 4 до 30 мм.
Безопасность производственных процессов: справочник С.В. Белов В.Н. Бринза Б.С. Векшин и др.; Под общ. ред. С.В.Белова. – М.: Машиностроение 1985.
РТМ 26-17-034-84 Сварка автоматическая и ручная химнефтеаппаратуры из высоколегированных хромоникелевых и хромоникельмолибденовых
корозионностойких сталей.
С.А. Куркин Г.А. Николаев. Сварные кострукции. Технология изготовления механизация автоматизация и контроль качества в сварочном производстве.
Приспособление.cdw

Ташкентский Государственный Технический Ууниверситет им И. Каримова
Сосуд высокого давления.cdw

Толщина стенки 16 мм.;
Рабочее давление 5МПа.
ТашГТУ им. И.Каримова
Тех.изготовления и сборка.cdw

Рекомендуемые чертежи
- 09.08.2014
- 23.08.2014
- 23.08.2014