Усовершенствование технологического процесса изготовления ступицы переднего колеса трактора Т15




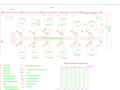
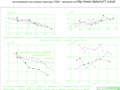
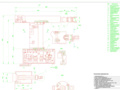
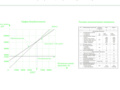
- Добавлен: 24.01.2023
- Размер: 3 MB
- Закачек: 0
Описание
Состав проекта
![]() |
![]() |
![]() ![]() ![]() |
![]() ![]() ![]() |
![]() |
![]() ![]() ![]() ![]() |
![]() ![]() ![]() |
![]() ![]() ![]() |
![]() ![]() ![]() ![]() |
![]() ![]() ![]() ![]() |
![]() ![]() ![]() |
![]() ![]() ![]() ![]() |
![]() ![]() ![]() |
![]() ![]() ![]() |
![]() ![]() ![]() ![]() |
![]() ![]() ![]() |
![]() ![]() ![]() ![]() |
Дополнительная информация
техпроцесс.doc
Ступица переднего колеса
Код. наименование операции
Обозначение документа
Код. наименование оборудования
Ток. полуавтомат мод. 1734
Спец. сверл. станок мод. АМ-7787
Спец. расточн. станок мод. ОС-4555
Ток. многорезцовый ст. мод. 1Н713
ГОСТ 3.1404 – 86 Форма 3
Шестерня малая (левая)
Наименование операции
Оборудование устройство ЧПУ
Обозначение програмы
Установить деталь в приспособлении е и закрепить её
Точить деталь выдерживая размеры 1234
Резец 864-11; 25 Наладка РО-12875
Пластина 03111-120412 ВК6 ГОСТ 19049-80
Пластина 01111-160412 ВК6 ГОСТ 19049-80
Размер 153-04 Размер 245-052
Штангенциркуль ШИ II-250-005-1 ГОСТ 166
Плита 2-1-250х250 ГОСТ 10905
Набор щупов №2-2 ТУ 2-034-225-87
Очки 0.02-68 ГОСТ 12.4.013-85
Б. Открепить и снять деталь с приспособления
Резец 864-11; 25 Наладка РО-12876
Пластина 01111-160412 ВК6 ГОСТ 19043-80
Скоба 133-025 СТП 202ю507-80
Скоба 80-046 М20-9702
Скоба 238-021 М20-9701
Спец. сверлильный АМ-7787
А. Установить деталь в приспособление и закрепить её.
Приспособление 404-11898
Плита кондукторная 40411899
Сверлить одновременно 4 отв. 68 +0182 на глубину 18+18 и зенковать фаски в отверстиях под углом 120º до наружного
диаметра резьбы выдерживая размер 9
Сверло 397-08 6810 - 4 шт.
Удлинитель 1-26 х 445 НО6712 - 4 шт.
Штангенциркуль ШЦ-I-125-01-1 ГОСТ 166
Пробка ГМ8-7Н СТП 202395-88
Зенкеровать отв. 5 выдерживая размеры 14 и фаску 23
Зенкер 747-21 71А4 ВК8; Нож 545-25 ВК8 - 4 шт; Нож 545-89 ВК8 - 2 шт
Пробка 71Н11 СТП 202.392-78
Сверлить одновременно 5 отв. 16 напрооход выдерживая размер 7 и т.т. п.1
Сверло 563-100 16 - 5 шт.
Удлинитель 2-26 х 420 НО6712 - 4 шт.
Зенкеровать одновременно отв.5 177 напроход
Зенкер 742-5030 177-0035 ВК8; Нож 545-25 ВК8 - 5 шт;
Удлинитель 2-26 х 420 НО6712 - 5 шт.
Развернуть одновременно 5 отв. 8
Развёртка 728-5045 18Н9 ВК6 - 5 шт.
Патрон 22х190 НВ03-042-5 шт.
Удлинитель 22-2 х 320 НВ О5-18 - 5 шт.
Пробка 18+0035 СТП 202.392-78
Калибр на расположение 5-и отв. 18+0035 М28-8944
Нарезать резьбу одновременно в 4-х отв. 10 на длине 13 мм.
Метчик 85-12 М8Н12 - 4 шт.
Зажим для метчика В 36-9229 А-07 - 4 шт.
Резьбовой копир. 2-125х40 НО256 - 4 шт.
Пробка резьб. М8-7Н СТП202.565-85
Открепить и снять деталь с приспособления
Смещение осей отверстий Е 02 мм обеспечивается кондуктором.
Проверить выборочно в КСП 2-3 дет. от партии.
Приспособление 404-11900
Плита кондукторная 40411901
Зенкеровать отв. 6 выдерживая размер 7 и фаску 34
Зенкер 747-20 61 А4ВК8; Нож 545-25 ВК8 - 4 шт; Нож 545-89 ВК8 - 2 шт.
Пробка 61Н11 СТП 202.392-78
Размер 63±02 Штангенглубиномер М28-9234
Сверлить одновременно 4 отв. 68 +0182 на глубину 18+18 и зенковать фаски в отверстиях под углом 120º до наружного диаметра
резьбы выдерживая размеры 29
Удлинитель 1-26 х 490 НО 6712 - 4 шт.
Пробка ГМ8-7Н СТП 202.395-88
Зенкеровать отв. 8 напроход
Зенкер 747-03 А 545Н11ВК8; Нож 545-73 ВК8 - 4 шт;
Пробка 54Н14 СТП 202.392-78
Нарезать резьбу одновременно в 4-х отв. 1 на длине 13 мм.
Метчик 85-12 М8-Н2 - 4 шт.
Зажим для метчика В36-9229 А-07- 4 шт.
Копир резьб. 2-125х470 НО 256 - 4 шт.
Смещение осей отверстий Г от номинального расположения 02 мм обеспечивается кондуктором.
Спец. расточ. п.авт. ОС-4555
Расточить отв.1 выдерживая размеры 2 и 6
Резец 518-20 16 х 50 ВК3 - 2шт.
Бортштанга В32-9359 - 2шт.
Прибор для настр. М36-9072
Пробка 62Р7 СТП 202.392-78
Скоба 625-03 М20-8727
Нутромер НИ 50-100-1 ГОСТ 868
Кольцо уст. 62 М27-8006
Расточить отв.5 выдерживая размеры 3 и 4
Пробка 72Р7 СТП 202.392-78
Кольцо уст. 72 М27-8007
Приспособление для проверки биения М26-8039
Б. Открепить и снять деталь с приспособления.
Токарный многорез. павт. 1Н713
Приспособление 402 12706
Подрезать торец детали и точить поверхность с одной стороны выдерживая размеры 345
Резец 529-09; 25х16х140 ВК6
Державка В34-13584 (пер. 12)
Штангенциркуль ШЦ-II-250-005-1 ГОСТ 166
Очки 002-68 ГОСТ 12.4.013-85
Подрезать торец детали и точить поверх. с другой стороны
Выдерживая размеры 126
Резец 529-10; 25х16х140 ВК6
Скоба 132315 h13 СТП 202.507-80
Размер 20-052 Штангенциркуль ШЦ-I-125-01-1 ГОСТ 166
Приспособление М26-8039
Б. Открепить и снять деталь с оправки.
Зачистить заусенцы в местах механической обработки
Напильник Е 315 №1 ГОСТ 1465-80
Очки 02-68 12.4.013-85
Рукавицы АМП ГОСТ 12.4.010-75
записка.doc
ФЕДЕРАЛЬНОЕ АГЕНСТВО ПО ОБРАЗОВАНИЮ
Государственное образовательное учреждение высшего
профессионального образования
Московский Государственный Индустриальный Университет
РАСЧЕТНО-ПОЯСНИТЕЛЬНАЯ ЗАПИСКА
К ДИПЛОМНОМУ ПРОЕКТУ
Студент Архипов П.О.
ФакультетТехнологический
КафедраМеталлорежущие станки
СпециальностьТехнология машиностроения
ТЕМА ДИПЛОМНОГО ПРОЕКТА
Усовершенствование технологического процесса изготовления ступицы переднего колеса трактора Т15
Консультант по безопасности и
Консультант по организационно-
Допустить дипломный проект к защите
в Государственной аттестационной комиссии
Кафедра «Металлорежущие станки»
на выпускную квалификационную работу
Архипов Павел Олегович
(Фамилия имя отчество)
«Усовершенствование технологического процесса изготовления ступицы переднего колса трактора Т15
Руководитель работы консультант по технологической части
(ученая степень должность)
Консультант по технологической части
Консультант по конструкторской части
Консультант по спецвопросу
Консультант по части безопасности и экологичности производства
Консультант по организационно-экономической части
Технологическая часть
1. Назначение детали в сборочной единице анализ технических требований на деталь
2. Расчёт такта выпуска
3. Качественная оценка технологичности конструкции детали
4. Выбор метода получения заготовки
5. Разработка маршрута обработки основных поверхностей детали
6. Выбор технологических баз
7. Выбор технологического оборудования
8. Определение межоперационных припусков
9. Расчет режимов резания
10. Расчет технической нормы времени
Конструкторская часть
1. Проектирование станочного зажимного приспособления
1.1 Описание работы электропривода
1.2 Описание работы 3-х кулачкового патрона
1.3 Расчёт погрешности базирования
1.4 Расчёт зажимного механизма приспособления
1.5 Расчёт усилия зажима
1.6 Расчёт электромеханического привода
2. Проектирование контрольного приспособления
2.1 Описание и принцип работы контрольного приспособления
2.2 Описание устройства индикатора
2.3 Расчёт контрольного приспособления на точность
3. Средства автоматизации
Научно-исследовательская часть
1. Анализ вопроса повышения качества деталей путем применения алмазных пластин
2. Прочность алмазных режущих пластин
3. Тепловой режим резания
4. Исследование влияния различных факторов на качественные показатели
4.1 Анализ шероховатости обрабатываемой поверхности
4.2 Исследование микротвердости обрабатываемой поверхности
4.3 Анализ количества остаточного аустенита при точении
4.4 Исследование показателя точения
Организационная часть
1. Определение такта ритма и темпа производства
2 Определение потребного количества оборудования (рабочих мест)
3. Определение коэффициента загрузки оборудования использования оборудования и времени работы для выполнения сменного задания
4. Определение состава работающих на поточной линии
4.1. Определение числа основных рабочих-станочников
4.2. Определение числа рабочих-ремонтников
4.3. Определение руководителей и специалистов
5. Расчет площади участка
1. Определение затрат на основные материалы
2. Определение стоимости основных производственных фондов
3. Определение стоимости всех видов энергии и услуг для производственных нужд
4. Определение годового фонда заработной платы
4.1. Определение годового фонда заработной платы основных рабочих
4.2. Определение годового фонда заработной платы рабочих-ремонтников
4.3. Определение годового фонда заработной платы руководителей и специалистов
5. Определение цеховой себестоимости изделия
6. Определение годового экономического эффекта
7. Определение критического объёма производства
Безопасность и экологичность
1. Анализ условий труда на производстве
2.1. Общие положения
2.2. Ослабление шума в источнике его возникновения
2.3. Снижение шума методом звукоизоляции
Техпроцесс изготовления ступицы
Список использованной литературы
Подробный и качественный диплом на тему
“Усовершенствование техпроцесса изготовления
детали 'Ось колеса переднего
ведущего моста трактора Т35А”
по специальности “Технология машиностроения”
Основным требованием к результатам деятельности современной промышленности являются повышение качества выпускаемой продукции и производительности труда в основном определяющееся технологией производства и степенью применения в ней новейших прогрессивных методов обработки деталей оборудования и средств оснащения контроля и автоматизации.
Основные направления развития машиностроения связаны с применением:
-поточного метода производства;
-механизации и автоматизации производства;
-концентрации операций;
-малооперационной и малоотходной технологии роботизации и полной автоматизации технологических процессов обработки и контроля качества деталей; современных и прогрессивных методов обработки сборки и транспортирования деталей и изделий;
-новых высокопроизводительных многошпиндельных многопозиционных многоместных и других видов приспособлений загрузочно-разгрузочных устройств и контрольных автоматов;
-напряжённых режимов резания высокопрочных и экономичных материалов и конструкций режущих инструментов;
-высокоточных производительных неразрушающих и автоматизированных методов контроля качества деталей и изделий.
Данная ступица является основной деталью конструкции переднего колеса трактора МТЗ и через подшипники вращается на оси колеса. Она относится к классу “деталь вращения” изготовлена из серого чугуна СЧ15. К наружной стороне ступицы крепится колеса автомобиля а во внутреннюю часть вставляется ось ступицы с подшипниками.
Ступица имеет 4 ступени уменьшения диаметров снаружи и 4 ступени внутри (рис. 1.1) чистота обработки большинства поверхностей ступицы 5 мкм а подшипниковых диаметров 62Р7 и 72Р7 мм - чистота обработки 08 мкм. Основным высоким требованием к детали предъявляется радиальные биения торцевых поверхностей относительно подшипниковых диаметров - 25 мкм. Для контроля данного параметра используется индикатор для контроля диаметров используются калиброванные пробки.
С точки зрения механической обработки деталь изготавливается достаточно просто без особых затруднений. Она достаточно технологична поэтому допускает применение высокопроизводительных методов и режимов обработки имеет достаточно хорошие базовые поверхности.
Химический состав и механические свойства материала приведены в таблицах 1.1 и 1.2.
Таблица 1.1. Химический состав
Массовое содержание элементов %
Таблица 1.2. Механические свойства
Рис. 1.1 Эскиз детали
Деталь не имеет сложных для обработки поверхностей поэтому может быть обработана на универсальном оборудовании с использованием стандартного инструмента.
Тип производства согласно ГОСТ 3.1108-74 характеризуется коэффициентом закрепления операции за одним рабочим местом или единицей оборудования. Тип производства определяется коэффициентом:
Q - число различных операций;
Рм - число рабочих мест на которых выполняются данные операции.
Так как на данном этапе расчёта неизвестны вышеуказанные показатели для расчёта то для предварительного определения типа производства можно использовать годовой объём и массу детали.
Так как масса детали 61 кг а годовая программа выпуска 150то тип производства мелкосерийный.
Мелкосерийное производство характеризуется ограниченной номенклатурой изделий изготовляемых периодически повторяющимися партиями и сравнительно большим объёмом выпуска чем в единичном производстве. В мелкосерийном производстве в отличии от массового и крупносерийного технологический процесс изготовления изделия преимущественно сконцентрирован т.е. одинаковые виды обработок выполняются на одном оборудовании и на одном рабочем месте.
Такт выпуска: = 60*Fg*KN где
Fg - эффективный годовой фонд рабочего времени оборудования при заданном количестве рабочих смен ч.
N - годовая программа выпуска шт.
К - нормативный коэффициент загрузки оборудования 08-095.
= 60*22*09150 = 08 мин.
При конструкции отдельных деталей необходимо достичь удовлетворения
не только эксплуатационных требований но так же требований наиболее
рационального и экономического выполнения изделия.
Технологичной считается такая конструкция детали которая позволяет
изготавливать деталь наиболее рациональным и экономичным способом.
Основными критериями технологичности являются трудоемкость и
себестоимость изготовления детали. Чем меньше трудоемкость изготовления
детали и себестоимость тем больше экономичность.
Таблица 1.4 Анализ технологичности детали “Ступица”
Должны быть взаимно параллельны или взаимно перпендикулярны
Поверхности взаимно параллельны или взаимно перпендикулярны
Должны быть сквозными без
Внутренних канавок и выточек
Должны быть не менее 25 мм что позволяет применять
многошпиндельные сверлильные станки
Должна быть не более двух
номинальных диаметров резьбы
Должны быть доступны для
обработки на металлорежущих станках
Обработка по месту должна
отсутствовать в конструкции
Соответствие точности и шероховатости поверхности
Точные по размерам поверхности должны иметь соответствующие параметры шероховатости
Точные поверхности имеют соответствующие параметры шероховатости
Размеры конструкторских
Должны иметь размеры по типовым правилам базирования
Имеют размеры по типовым правилам базирования
Конструкция детали должна
быть такой что при её изготовлении можно было применять высокопроизводительные методы обработки
Возможно применение высокопроизводительных методов обработки
Рассчитываем коэффициент технологичности детали:
Т - количество показателей ТКД соответствующие требованиям технологичности.
N - общее число анализируемых показателей.
Рис. 1.2 Эскиз детали с обозначением поверхностей
Таблица 1.5 Анализ технологичности конструкции детали по точностным требованиям
Наименование поверхности
Количество поверхностей обрабатываемых по следующим квалитетам точности
Наружные цилиндрические
Внутренние ци-линдрические
Вывод: квалитет точности 7 для поверхностей 3 8 и 5 достигается зенкерованием и тонким точением для 3 и 8 а для поверхности 5 сверлением зенкерованием и развёртыванием. Для остальных поверхностей квалитеты точности 12 и 13 достигается черновым и чистовым точением.
Таблица 1.6. Анализ технологичности конструкции детали по величине параметров шероховатости обрабатываемых поверхностей
Вывод: Шероховатость для поверхностей 3 и 8 достигается зенкерованием и тонким точением а для поверхности 5 сверление зенкерование и развёртыванием. Шероховатости 5 и 16 мкм достигаются черновым и чистовым точением.
Таблица 1.7. Анализ технологичности конструкции детали по соответствию возможности выполнения принципа постоянства баз
Наименование поверхностей используемых в качестве баз
Для выполнения технологических операций
Количество используемых баз
Наружная поверхность (двойная направляющая база) и торец (опорная база)
Черновое и чистовое точение
Сверление зенкерование и развёртывание
Центровочные отверстия и торцевая поверхность (двойные направляющие и опорная базы )
Технологичность детали удовлетворяет всем требованиям предъявляемым к изделию. Вышеприведённый анализ показал что деталь в целом технологична.
Заготовку ступицы получают литьём в песчано-глинистые формы. Для получения отливки изготавливают верхнюю и нижнюю половины формы отливки. Модели для отливки изготавливают из дерева. Вначале формируют рабочий слой формы толщиной 20-40мм который включает в себя специальные жидкостойкие вещества. Затем набивают опоку песчано-глинистой смесью утрамбовывают. Потом вдавливают верхнюю половину модели в форму. Удаление моделей литников и прибылей делают путём перемещения их вверх а верхней части выталкиванием вниз таким же способом делают нижнюю часть формы. Затем соединяют их и заливают в литейную форму расплавленный чугун при температуре 750-850°С температура выбивки заготовки из формы 200°С. После этого производится термическая закалка:
) Загружают деталь в электропечь с температурой 530-540°С;
) Выдерживают при данной температуре 10-15 часа;
) Охлаждают в воде при температуре 50-60 ºC;
Затем производят старение:
) Загружают деталь в печь с температурой 150°С;
) Выдерживают при данной температуре 2-25 часа;
) Охлаждают на воздухе;
Масса поковки: Мпок = 75 кг
Коэффициент использования материала:
Назначение методов обработки произведём табличным методом.
Величина шероховатости Ra (мм)
Наименование методов обработки
Наименование операции
Ток. полуавтомат мод. 1734
Резец 864-11; 25 Пластина 03111-120412 ВК6 ГОСТ 19049-80
Штангенциркуль ШИ II-250-005-1 ГОСТ 166-89
Спец. сверл. станок мод. АМ-7787
Приспособление 404-11898;
Плита кондукторная 40411899
Зенкер 747-21 71А4 ВК8;
Зенкер 742-5030 177-0035 ВК8;
Развёртка 728-5045 18Н9 ВК6;
Штангенциркуль ШЦ-I-125-01-1 ГОСТ 166;
Пробка ГМ8-7Н СТП 202395-88;
Пробка 71Н11 СТП 202.392-78;
Пробка 18+0035 СТП 202.392-78;
Пробка резьб. М8-7Н СТП202.565-85
Приспособление 404-11900;
Плита кондукторная 40411901
Зенкер 747-20 61 А4ВК8;
Зенкер 747-03 А 545Н11ВК8;
Пробка 61Н11 СТП 202.392-78;
Пробка ГМ8-7Н СТП 202.395-88;
Пробка 54Н14 СТП 202.392-78;
Копир резьб. 2-125х470
Спец. расточн. станок мод. ОС-4555
Резец 518-20 16 х 50 ВК3
Скоба 625-03 М20-8727;
Нутромер НИ 50-100-1 ГОСТ 868;
Пробка 62Р7 СТП 202.392-78;
Пробка 72Р7 СТП 202.392-78
Ток. многорезцовый ст. мод. 1Н713
Приспособление 402 12706;
Резец 529-09; 25х16х140 ВК6
Штангенциркуль ШЦ-II-250-005-1 ГОСТ 166;
Скоба 132315 h13 СТП 202.507-80
Напильник Е 315 №1 ГОСТ 1465-80
Всё выше перечисленное
Операция 005. Токарная
Начерно точить торцы 1 и 2 (рис. 1.2).
Операция 010. Токарная
Начерно точить поверхность 6.
Начерно точить торцы 4 и 7.
Операция 015. Сверлильная
Зенкеровать поверхность 3.
Переход 1. Сверлить отв. 5.
Переход 2. Зенкеровать отв. 5.
Переход 3. Развёртывать отв. 5.
Переход 1. Сверлить на поверхности 2 отверстия.
Переход 2. Нарезать резьбу в просверленных отверстиях.
Операция 020. Сверлильная
Зенкеровать поверхность 8.
Переход 1. Сверлить на пов-ти 7 отверстия.
Операция 025. Алмазно-расточная
Начисто точить поверхности 3 и 8.
Начисто точить торцы 1 2 и 4.
Начисто точить поверхность 6.
При обработке деталей на станках заготовки должны быть правильно ориентированы относительно основных поверхностей и узлов станка. Задачи взаимной ориентировки деталей и сборочных единиц в машинах при их сборке и заготовок на станках при изготовлении деталей решаются их базированием.
Базированием называют придание заготовке или изделию требуемого положения относительно выбранной системы координат. При механической обработке заготовок на станках базированием принято считать придание заготовке требуемого положения относительно элементов станка определённой траектории движения подачи обрабатывающего инструмента. Для повышения точности изготовления деталей а следовательно и лучших эксплуатационных результатов необходимо стремится к тому чтобы конструкторские технологические и измерительные базы представляли собой одни и те же поверхности. В этом и состоит принцип единства и совмещения баз. В процессе обработки детали для базовых поверхностей используют как необработанные черновые поверхности так и обработанные чистовые. Черновой установочной базой могут служить поверхности относительно которых при первой операции обрабатываются поверхности используемые в качестве баз при последующих операциях. Нужно стремиться чтобы черновая база использовалась лишь один раз для обработки установочных чистовых баз. В качестве черновых баз следует выбирать поверхности с наименьшими припусками. Чистовые базы следует выбирать так что бы чистовые установочные базы были конструкторскими это исключает погрешность базирования. Чистовые базы должны иметь наибольшую точность формы и размеров и малую шероховатость. Установочные базы должны обладать наибольшей устойчивостью при базировании и обеспечивать наименьшую деформацию заготовки от зажатия и воздействия сил резания.
Принципы постоянства баз заключаются в том что при выборе чистовых баз нужно стремиться к тому чтобы обработанные поверхности на всех операциях осуществлялось с использованием одних и тех же установочных баз. Это диктуется тем что каждая установка на новую технологическую базу неизменно приводит к появлению дополнительной погрешности.
Таблица 1.10 Операционные схемы базирования
Наименование обработки ро этапу технологического процесса
Теоретическая схема базирования
Формирование торцев предварительным точением
Формирование отверстий сверлением зенкерованием и развёртыванием
Формирование торцев наружных и внутренних цилиндрических поверхностей
Последовательность выполнения операций зависит от следующих факторов: конструктивной формы и размеров детали размеров производственной программы свойств обрабатываемого материала шероховатости и техпроцесса.
Выбранный станок должен обеспечивать выполнение технических требований предъявляемых к детали.
Мощность и жёсткость кинематические возможности станка должны позволять вести обработку на оптимальных режимах резаниях с наименьшими затратами времени и себестоимостью.
Изходя из всех требований подбираем станки:
Сверлильный станок мод. АМ-7787:
- предназначен для сверления и последующих обработок отверстий;
Наименьший и наибольший диаметр обрабатываемого изделия - 20 90 мм;
наименьшая и наибольшая длина обработки - 100 200 мм;
количество барабанов - 1;
количество тисков для крепления заготовок - 6.
Сверлильная головка:
Пределы чисел оборотов шпинделя - 250 2410;
пределы рабочих подач - 20 300 мм мин.
Токарный многорезцовый ст. мод. 1Н713:
Наибольший диаметр обработки: на станиной - 400 мм
над суппортом - 250 мм;
наибольшая длина хода переднего суппорта - 250 мм;
наибольшее расстояние между центрами - 450 мм;
наибольшая длина рабочего хода заднего суппорта - 135 мм;
наибольший рабочий ход копировального суппорта - 510 мм;
пределы чисел оборотов шпинделя - 125 1250 обмин;
габариты - 2750 1050 2025 мм.
Силовая головка ТЕМ23:
зенкерование и развертывание
расход мощности привода насоса подачи - 17 кВт;
рабочий ход - 400 630 мм;
максимальный диаметр зенкерования - 85 мм:
диапазон чисел оборотов шпинделя - 138 1119 обмин;
диапазон подач - 07 15 ммоб;
диапазон скоростей подач - 15 650 ммин;
регулирование подач - бесступенчатое;
скорость ХХ - 65 ммин;
усилие подачи - 5000 кг;
ориентировочный вес - 1260 1760 кг
Определение аналитическим методом операционных припусков и межоперационных размеров:
Zmin i = 2*(Rz i-1 + h i-1 + )
где R z i-1 – высота неровностей профиля на предшествующем переходе
hi-1 – глубина дефектного слоя на предшествующем переходе (отбеленный или обезуглероженный слой)
r i-1 - суммарное пространственное отклонение расположения обтачиваемой поверхности относительно базовых поверхностей
ei – погрешность установки заготовки на выполняемом переходе:
где eб – погрешность базирования;
Минимальный припуск:
- под чистовое растачивание:
- под тонкое растачивание:
Определение межоперационных размеров:
а. Определение размеров под тонкое растачивание:
Dmaxi-1=Dmaxi-2zmini=61979-0248=61742 мм
Dmini=Dmaxi-1-Tdi-1=61742-005=61692 мм
б. Определение размеров под чистовое растачивание:
Dmaxi-1=Dmaxi-2zmini=61742-0392=6135 мм
Dmini-1=Dmaxi-1-Tdi-1=6135-01=6125 мм
в. Определение размеров под зенкерование:
Dmaxi-1=Dmaxi-2zmini=6135-375=576 мм
Dmini-1=Dmaxi-1-Tdi-1=576-32=544 мм
Все значения заносим в таблицу 1.11:
Таблица 1.12 Табличный расчёт припусков на остальные размеры
Поверхность детали и технологический маршрут её обработки
Расчётный припуск 2Zmin мкм
Расчётный минималь-ный размер мкм
Допуск на изготовление мкм
Принятые размеры по переходам мм
Полученные предельные припуски мкм
Расчет режимов резания производим с помощью справочника инженера-технолога. Расчёты произведём для токарной и сверлильной обработок для остальных видов обработок расчёты произведём на компьютере.
Операция 005: токарная:
Поперечный суппорт: подрезать торцы ступицы выдерживая размеры: 24 – 052 мм и 23 +02 мм на максимальном диаметре 210 мм.
Глубина резания: t = 1 (мм).
Длина рабочего хода суппорта определяется по формуле:
L р.х. = L рез. + y = 100 (мм)
где L рез. – длина резания мм;
y – длина подвода врезания и перебега мм.
Табличная подача суппорта на оборот шпинделя:
S табл = 03 13 ммоб.
Определяем стойкость инструмента:
Т = Тт*kти*kтс*kтj*kr = 60*17*14*1*1 = 1428 (мин)
где Тт – табличное значение стойкости;
kти; kтс; kтj; kr – коэффициенты при многоинструментальной обработке.
Скорость резания определяется по формуле:
T — стойкость инструмента мин;
t — глубина резания мм;
S — подача скорректированная по паспорту станка ммоб;
Kv — поправочный коэффициент:
где Kмv — коэффициент учитывающий влияние материала заготовки;
где Кг – коэффициент характеризующий группу чугуна по обрабатываемости;
nv — показатель степени;
Kпv — коэффициент учитывающий состояние поверхности;
Kиv — коэффициент учитывающий материал инструмента.
Частота вращения определяется по формуле:
n = 1000 * Vрез.(p * Dmax) = 1000 * 1055(314 * 210) = 1599 (мин –1)
где Dmax – максимальный диаметр обрабатываемого участка мм.
Корректируем полученную частоту вращения по паспортным данным станка: n ст = 160 (мин –1).
Определяем фактическую скорость станка:
Vф = p * D * n пр 1000 = 314 * 210 * 160 1000 = 1055 (ммин).
Определяем силу резания по формуле:
Pz = 10 Cp txSyVnKp = 10300110350751055-01511 = 106695 (Н)
Kp – произведение коэффициентов определяется по справочнику.
Определяем мощность резания по формуле:
Nрез = Pz Vрез (60 1020) = 106695*1055(60*1020) = 18 (кВт).
Основное технологическое время:
То1 = L р.х. (n ст * Sо) = 100160*04 = 156 (мин).
Операция 015: вертикально – сверлильная:
В данной операции сделаем расчёт для сверления 5 отв. так как для данной обработки требуется наибольшая мощность станка.
Сверлить одновременно 5 отверстий напроход 16 мм.
Глубина резания определяется по формуле:
t = 05*D = 05*16 = 8 (мм)
где D – диаметр сверла мм.
Подачу выбираем с помощью справочника:
S табл = 015023 (ммоб).
Подача станка: S ст = 01116 (ммоб).
Скорость резания при рассверливании вычисляется по формуле :
Т – период стойкости Т = 20
КV – общий поправочный коэффициент на скорость резания учитывающий фактические условия резания:
здесь КMV – коэффициент на обрабатываемый материал КMV = 057;
КИV – коэффициент на инструментальный материал КИV = 1;
К при рассверливании данный коэффициент не учитывается и формула принимает вид:
КV = КMV* КИV = 057*1 = 057.
Частота вращения инструмента или заготовки мин -1 определим по формуле:
n = 1000 * Vрез.(p * Dmax) = 1000 * 91(314 * 16) = 1811 (мин –1).
Корректируем по паспорту станка. Получаем n ст = 180 (мин –1).
Крутящий момент при рассверливании Н*м и осевую силу Ро Н рассчитывают по формулам:
Ро = 10 СР tx sy KP = 10 67 8 09 01508 079 = 1249 (Н)
KP – коэффициент учитывающий фактические условия обработки в данном случае зависит только от материала обрабатываемой заготовки и определяется выражением:
Мощность резания кВт определяют по формуле:
Основное технологическое время необходимое для выполнения данной операции вычислим по формуле:
То = L р.х. (n * S) = 30180*015 = 11 (мин)
где L р.х – длина рабочего хода многошпиндельной сверлильной головки.
На другие операции расчет режимов резания произведем на компьютере.
Таблица 1.12 Выбор режимов резания при расточной обработке на операции 025
Максимальный обрабатываемый диаметр D мм
Фактическая скорость станка vф мс
Подача резца на один оборот S0 ммоб
Частота вращения шпинделя обеспечиваемая станком n мин -1
Мощность резания кВт
Глубина резания t мм
Длина рабочего хода инструмента мм
Технологическое время То мин
Таблица 1.13 Выбор режимов резания при зенкеровании на операции 015
Обрабатываемый диаметр отверстия D мм
Подача инструмента на один оборот S0 ммоб
Таблица 1.14 Выбор режимов резания при развёртывании на операции 015
Технические нормы времени в условиях данного производства устанавливаются расчетно-аналитическим методом.
В мелкосерийном производстве рассчитывается норма штучного времени Тшт дополнительно подготовительно-заключительное время Тп-з и штучно-калькуляцион-ное время Тшт-к.
Норма штучного времени рассчитывается по следующей формуле:
Тшт = То + Тв + Тобсл + Тотд
гдеТшт — норма штучного времени мин;
То — основное технологическое время мин;
Тв — вспомогательное время мин;
Тобсл — время на обслуживание рабочего места мин;
Тотд — время перерывов на отдых и личные надобности мин.
Определение основного ( технологического ) времени
Основное (технологическое) время То затрачивается на непосредственное осуществление технологического процесса т.е. на изменение формы размеров и качества обрабатываемой поверхности детали. Расчет основного времени производится на основании кинематики данного метода обработки и выбранных режимов резания.
В нашем случае основное (технологическое) время для нормируемой операции рассчитано в разделе «Расчёт режимов резания».
Определение вспомогательного времени
Вспомогательное время Тв расходуется рабочим на действия обеспечивающие выполнение основной работы. При расчете нормы штучного времени учитывается только часть вспомогательного времени не перекрываемая машинным временем.
При определении нормы вспомогательного времени суммируют следующие его элементы:
время на установку и снятие детали (если оно не перекрывается машинным временем при работе на многопозиционных станках);
время на приемы управления станком. Сюда входит время затрачиваемое на пуск и остановку станка включение и выключение подачи изменение числа оборотов шпинделя или величины подачи поворот и перемещение частей станка и приспособлений смену инструмента в быстросменном патроне смену быстросменных кондукторных втулок и другие приемы непосредственно обеспечивающие выполнение обработки;
время на измерение деталей (если оно не может быть перекрыто машинным временем).
Таким образом определим вспомогательное время по следующей формуле:
Тв = Тус + Тз.о. + Туп + Тизм
гдеТус — время на установку и снятие детали мин;
Тз.о. – время на закрепление и открепление детали мин;
Туп — время на приемы управления станком мин;
Тизм — время на измерение детали мин.
Вспомогательное время Тв вместе с основным (технологическим) временем То составляет оперативное время Топ:
Определение времени обслуживания рабочего места и времени перерывов на отдых и личные надобности
Время на обслуживание рабочего места Тобсл состоит из двух частей:
времени на техническое обслуживание рабочего места Ттех которое затрачивается на смену затупившегося режущего инструмента на регулировку и подналадку станка во время работы и на уборку стружки на рабочем месте во время работы:
времени на организационное обслуживание рабочего места t орг которое требуется для раскладки инструмента в начале смены и уборки его в конце смены осмотра и опробования оборудования получения инструктажа в течение рабочего дня смазки и чистки станка в течение смены и уборки рабочего места в конце смены:
Таким образом время на обслуживание рабочего места Тоб определяется по формуле:
Определение времени перерывов на отдых и личные надобности
Время перерывов на отдых и личные надобности Тотд зависит от веса обрабатываемой детали процента машинного времени величины оперативного времени характера подачи и определяется в процентах от оперативного времени Топ в крупносерийном производстве:
Определение нормы штучно-калькуляционного времени
Норма штучно-калькуляционного времени Тшк определяется по следующей формуле:
Тшт-к = Тшт + Тп-з n
Тп-з — подготовительно-заключительное время мин;
n — размер партии (число деталей) шт.
В состав подготовительно-заключительного времени входит ознакомление с работой настройка оборудования на выполнение данной работы и на требуемые режимы резания пробная обработка деталей получение на рабочем месте заданий заготовок инструмента приспособлений сдача продукции и доставка на рабочее место инструмента и приспособлений.
Подготовительно-заключительное время задается по нормативам и зависит от характера и объема подготовительных работ.
Подготовительно-заключительное время определим по формуле:
Тп-з = a + (b Nи) + (с Рр)
гдеa b c — постоянные коэффициенты;
Nи — число режущих инструментов шт.;
Рр — число устанавливаемых исходных режимов работы станка.
Значения коэффициентов: а = 113; в = 08; с = 05.
Размер партии (число деталей в партии) n находим по следующей формуле:
гдеN — годовая программа выпуска деталей шт.;
а — число дней запаса заготовок на складе (50 дней);
Ф — число рабочих дней в году (Ф=260 дней).
Определяем штучно – калькуляционное время для 005 операции: токарная по формуле:
Тшт-к = Тп-з n + То + (Ту.с.+ Тз.о.+ Туп + Тиз) + Тоб.от
Результаты определения Тшт-к записываем в табл. 1.15.
Таблица 1.15 Сводная таблица технических норм времени
Номер и наименование операции
Основное технологическое время То мин
Время на установку и снятие детали tус мин
Время на приемы управления станком tуп мин
Время на измерение детали tизм мин
Вспомогательное время Твсп мин
Оперативное время Топ мин
Время на обслуживание рабочего места Тобсл мин
Время на отдых Тотд мин
Определение нормы штучного времени
Норма штучного времени Тшт мин
Годовая программа выпуска деталей N шт.
Число режущих инструментов Nи шт.
Число устанавливаемых исходных режимов работы станка Рр
Норма штучно-калькуляционного времени Тшк мин
На остальные операции расчет штучно – калькуляционного времени произведем с помощью ЭВМ. Результаты расчета сведем в табл. 1.16.
Таблица 1.16 Расчёт штучно-калькуляционного времени Тш-к с помощью ЭВМ
Данное зажимное приспособления применяется на токарной операции механообработки ступицы обрабатываемой на станке мод. 1Н713. Приспособление должно обладать необходимой жёсткостью конструкции точностью и достаточной силой зажима. В качестве приспособления разрабатываем 3-х кулачковый патрон. Патрон будет устанавливать в переднюю бабку станка. Так как производство автоматизированная и ступица обрабатывается на автоматической линии то к патрону разрабатываем ещё и электромеханический привод который будет зажимать и разжимать обрабатываемую деталь без участия человека во время подачи или захвата промышленного робота.
Рис. 2.1 Кинематическая схема электромеханического привода.
Для закрепления и раскрепления заготовки был разработан зажимной патрон с электромеханическим приводом. Двигатель 1 (рис. 2.1) задаёт крутящий момент приводу через червячный редуктор 2 уменьшается частота вращения зажимного механизма. Кулачки патрона 10 зажимают вал 11 до определённого усилия как нужное усилие заготовки достигнуто в процессе сопротивления зубья полумуфт 5 и 6 благодаря своему геометрическому конструктиву выходят из зацепления. Вследствие чего подвижная в осевом направлении полумуфта 5 смещается назад сжимая пружину 4 давит через рычаг на выключатель 8 который обесточивает двигатель 1 и выключает привод также подаётся сигнал на клапан 7 который подаёт шток на рычаг и держит полумуфту 5 вне зацепления с муфтой 6. Гайкой 3 можно регулировать момент выхода из зацепления полумуфт 5 и 6 затягивая гайку пружина 4 сдавливается момент увеличивается расслабляя момент уменьшается. Зубчатое колесо 9 закреплённое на валу шпинделя входит в зацепление с шестерней механизма главного движения станка и задаёт шпинделя главное вращение при токарной обработке.
Рис. 2.2 3-х кулачковый патрон.
Обрабатываемая деталь 1 зажимается тремя кулачками 2 (рис. 2.2) кулачки приводятся в движении посредством резьбового соединения от круга 3 который закреплён на валу привода. Также в зацеплении с кругом находятся три конических шестерни 4 которые работают в качестве стопора от разворачивания круга и ослабления зажима заготовки в процессе обработки. Кулачки 2 прикреплены к зубчатым рейкам 5 винтами 6. Данные рейки совершают поступательные движения в пазах корпуса 7. Данное приспособление обеспечивает равномерный зажим и центрирование заготовки. Силовые части патрона корпус 7 кулачки 2 зубчатые рейки 5 и круг 3 выполнены из прочностной стали 45 ГОСТ 1055-48.
Базирование – это придание заготовке или изделию требуемое положение относительно выбранной системы координат.
Применительно к механической обработке на станках при базировании заготовок производится придание заготовке требуемого положения относительно элементов станка которое определяет траекторию движения подачи обрабатывающего инструмента.
Выбор технологической базы начинается с выбора технологической базы с первой операции. База на первой операции называется черновой и ее можно использовать только один раз.
Базы различаются по назначению:
Конструкторская – база используемая для определения положения детали или сборочной единицы в изделии;
Технологическая – база используемая для определения положения заготовки или изделия в процессе изготовления или ремонта.
Выбор базовых поверхностей для обработки детали является важным этапом проектирования технологического процесса.
При применении разрабатываемого приспособления приложение усилия закрепления происходит в направлении перпендикулярном торцовой поверхности в результате чего обеспечивается стабильность базирования детали. Базой обрабатываемого диаметра является ось ступицы а ступица крепится в кулачке по оси. Так как установочная и измерительная база совпадают то погрешность базирования равна нулю.
Для данного расчёта необходимо знать усилие резания при токарной обработки подшипниковых диаметров:
глубина резания t = 06 мм
назначаем подачу SO = 06 ммоб
период стойкости резца Т = 60 мин
KV – произведение коэффициентов.
KV = KMV KПV KИV = 1* 08 * 1 = 08
KMV – коэффициент учитывающий влияние материала заготовки.
KПV - коэффициент учитывающий состояние поверхности
KИV - коэффициент учитывающий влияние материала инструмента
Частота вращения шпинделя
Корректируем частоту вращения шпинделя по паспортным данным
станка: nст=150 обмин
Тогда действительная скорость резания равна:
Определяем главную составляющую силы резания:
PZ = 10 CP tx Sy Vn KP
KP – произведение ряда коэффициентов учитывающих
фактические условия резания.
KP = КМР KjP KgP KlP
KP = 074*094*1*1 = 069
PZ = 10 * 300 * 11 * 06075 * 176-015 * 069 = 760 Н
Определим необходимую величину зажимного усилия вала при условии недопустимости проворачивания его в кулачках при количестве кулачков равным трём.
f - коэффициент трения; f = 015
W = 760·256(015·3) = 4632 Н
Крутящий момент на валу круга 3 (рис. 2.2) будет равен:
Мкр = 13·f·W·(D3-d3)(D2-d2)
f - коэффициент трения в резьбовом соединении между кругом 3 и кулачками 5;
D - диаметр круга 3;
d - обрабатываемый диаметр ступицы на данной операции;
Мкр = 13·025·4632·(2053-1503)(2052-1502) = 86007 H·мм = 86 H·м
Для нормальной работы привода принимаем частоту вращения вала круга 3 равным 150 обмин.
Угловая скорость вала равна: = 314·15030 = 157 c-1
Мощность на валу равна: Р = ·Мкр = 157·86 = 1350 Вт = 135 кВт
Подбираем электродвигатель под данные параметры:
частота вращения двигателя: nдв = n · Uр = 150·5 = 750 обмин
Uр - передаточное число червячного редуктора
мощность двигателя: Pдв = Р(·Uр) = 135(065·5) = 042 кВт
- суммарное КПД подшипников и червячной передачи привода.
На основании расчётов выбираем электродвигатель трехфазный короткозамкнутый серии 4А закрытый обдуваемый с синхронной частотой вращения 750мин-1 4А132М4 с параметрами Рном = 5кВт nном= 750 мин -1.
Приспособление применяется для комплексного контроля радиального торцевого биения поверхностей деталей вращения а также плоскостности.
Показателем кинематической точности наряду с допуском на кинематическую погрешность вращающегося основания приспособления 2 (см. чертёж) на которое установлена проверяемая деталь является допуск на колебание подшипников 16 зависящий от степени точности самих подшипников
Таким образом контроль радиальных и торцевых биений детали производится посредством индикатора 5 прикреплённого к стойке 3 вместе с держателем 4. Держатель может передвигаться вверх и вниз в определённых стойки. В право
влево передвигается стойка индикатора по направляющим держателя.
Закрепление заготовки происходит посредством гайки 9 заворачивая гайку происходит давление в гидросистеме и под действием масла в гидрополости корпуса 1 шпонка давит на внутреннюю поверхность проверяемой детали. Для раскрепления детали необходимо на несколько оборотов отвернуть гайку.
Показания торцевого и радиального биения детали вращения отражаются на электронном дисплее 5. Точность данного приспособления зависит от допусков входящих деталей в механическую вращающуюся часть приспособления и должна быть не более 001 мм. Данное приспособление компактно и удобно в применение не требует дополнительных технологических оснасток.
Рис. 2.3 Устройство индикатора И-160М.
Для контроля диаметров и радиального биения вала используем индикатор модели И-160М ГОСТ 862-82 1 класса точности и с ценой деления индикатора 001 мм.
Таблица 1. Технические характеристики индикатора И-160М
Предел допускаемой основной погрешности мм
Измерительное усилие Н
на любом участке 1 мм диапазона измерений
в пределах всего перемещения измерительного стержня
Индикатор (рис. 2.3) состоит из корпуса 1 и трубы 2 на которой крепятся ручка 3 и зажим 4. Зажим служит для закрепления всего индикатора. В корпус вворачивается винт 6 который ограничивает давление штока 7 на рычаг 9. Шток 7 под действием пружины возвращается в исходное положение при ослаблении давления на него. Данный шток через рычаг 9 сидящий на оси 8 перемещает измерительный стержень индикатора 10. Измерительное усилие индикатора равно сумме усилия пружины штока 7 и усилия пружины 11. Монтаж и закрепления индикатора в приспособлении производиться по трубе 2 а после этого надевается верхний цилиндрический корпус 12 вместе с циферблатом 5 и закрепляется винтами к трубе 2. Внутренние штоки индикатора передвигаются в осевом направлении по посадке в нарправляющих втулках 13 и 14. Эти втулки запрессованы в трубу 2 и цилиндрические корпуса по жёсткой посадке.
Комплект сменных измерительных стержней позволяет производить установку индикатора на размер в пределах диапазона измерений.
Для того чтобы контрольное приспособление обеспечивало правильность контроля требуется чтобы его погрешность была не более допуска на контролируемый параметр:
TD – допуск контролируемого размера мм.
Так как контрольное приспособление устанавливается на суппорт станка то все погрешности кроме погрешности измерения инструмента и погрешности самого контрольного приспособления берём из расчётов станочного приспособления.
Погрешности в процессе измерения:
б – погрешность базирования (б = 0);
З – погрешность закрепления (З = 0);
у – погрешность станка (у = 001 мм);
изм. средства – погрешность индикатора (изм. средства = 001 мм - по паспорту индикатора).
пр – погрешность контрольного приспособления (пр = 005 мм – сумма полей допусков плоскостности кондукторной плиты посадочных размеров стойки и кронштейна контрольного приспособления);
i = (0012 + 0012 + 0032)12 = 0031 мм
Допуск на обрабатываемый диаметр 70 мм равен 005 мм
Условие выполнено приспособление пригодно к применению.
Для замены физического труда рабочего данная поточная линия на которой выполняется механообработка ступицы снабжена межоперационными портальными роботами модели ПРЦ-1и автоматизированной транспортно-накопительной системой. Портальный робот установлен возле каждого станка его функция заключается в захвате заготовки в межоперационном накопители и подаче его в зажимное приспособления станка. После того как закончится полный цикл обработки детали робот захватывает заготовку и передаёт её обратно в накопительный бункер в отсек обработанных деталей.
Для передачи деталей между станками используется транспортно-накопительная система (рис. 2.4) которая забирает обработанные на данной операции детали из накопительного бункера и передаёт в накопительный бункер следующей операции.
Рис. 2.4 Транспортно-накопительная система
- Передвижной промышленный робот; 3- Рука робота; 4- Захватываемая заготовка; 5- Межоперационные накопители;
Основными элементами транспортно-накопительной системы являются: межоперационные накопители состоящие из двух отсеков обработанных и предстоящих обработке на данной операции заготовок линии системы и манипулятора модели “Универсал-5”. Данный манипулятор может передвигаться как вдоль линии системы так и поперечно ей благодаря этому станки могут располагаться по обе стороны маршрутной межоперационной линии.
Одним из путей повышения эффективности производства и качества изделий является все более широкое применение обработки деталей абразивными алмазными и другими инструментами. Алмазная обработка позволяет обеспечить требуемые точность и качество деталей при высокой производительности а значит обеспечить высокую надежность и долговечность машиностроительной продукции в процессе эксплуатации поэтому объем и роль отделочных операций в современном машиностроении непрерывно возрастают.
Свойства любого алмазного инструмента зависят от его конструкции вида и свойства алмазного материала природного состава и технологии их производства последующей технологии формирования алмазного режущего инструмента посредством механических термических химических и других видов воздействия.
Алмазные инструменты имеют существенные преимущества по сравнению с инструментами из твёрдосплавных материалов при обработке высоколегированных сталей и сплавов когда лимитирующими факторами являются высокие требования к отсутствию прижогов и трещин. Они обладают хорошей самозатачиваемостью и позволяют обрабатывать детали с меньшим выделением тепла в зоне резания по сравнению с обычными инструментами.
К прочности алмазных пластин предъявляют очень высокие требования выполнение которых гарантирует безопасную эксплуатацию резцов. Наибольшие напряжения у алмазных пластин возникают на поверхности крепления к корпусу резца:
st max = * [(3 + m)*d2k + (1 - m)*d2]
где r - плотность алмаза гсм3;
w - угловая скорость заготовки;
m - коэффициент Пуассона;
d k d – диаметры соответственно отверстия крепления пластин;
g – ускорение свободного падения g = 981 мс2.
Полагая отношение диаметров dd k = 036 и коэффициент Пуассона m = 025 это соотношение примет вид:
где uk = w* - окружная скорость мс.
Постоянный коэффициент в этой формуле справедлив только для принятого соотношения dd k = 036.
Плотность крупнокристаллических алмазов твердостью СМ1 обычно находится в пределах 15 – 200 гсм3 у средне кристаллических той же твердости – 20 – 22 гсм3. Поэтому максимальные напряжения у крупнокристаллических будут соответственно меньше. Это подтверждается также экспериментальными данными по определению предела прочности на разрыв в форме восьмерок (табл. 3.1.).
Таблица 3.1 Предел прочности образцов при испытании на разрыв МПа
крупнокристаллическая
средне кристаллическая
По экспериментальным данным изменение степени твердости от СМ1 до СТ1 повышает предел прочности абразивных образцов более чем в два раза.
При увеличении объемного содержания порообразователя с 10 до 20 % наблюдается незначительное уменьшение предела прочности образцов на разрыв (табл. 4.2.2.2.).
Таблица 3.2 Относительное уменьшение предела прочности образцов на разрыв при увеличении объема порообразователя с 10 до 20 %
Наиболее трудоемкими операциями алмазной обработки являются операции точения деталей из сталей и сплавов подверженным прижогам и трещинам. Здесь эффективность и качество являются тесно связанными показателями: можно достигнуть необходимого качества за счет снижения производительности труда либо высокой производительности в ущерб качеству. Исследования показали что возникающие в процессе точения прижоги вызывающие структурные изменения в значительной степени снижают долговечность деталей и стойкость инструмента.
Введение в сталь легирующих добавок вольфрама молибдена никеля ванадия и др. резко снижает обрабатываемость. Объясняется это снижением теплопроводности и образованием твердых карбидов. Особенно теплопроводность снижается при введении в сталь хрома и никеля.
С уменьшением теплопроводности большое количество тепла концентрируется в поверхностном слое детали ухудшается отвод его из зоны контакта возрастает налипание частиц металла на режущие частицы алмазного материала что усугубляет возможность появления прижогов и трещин. Из структурных составляющих сталей самую низкую теплопроводность имеет аустенит. В порядке возрастания теплопроводности структурные составляющие располагаются следующим образом: аустенит мартенсит мартенсит отпуска троостит сорбит перлит. При точении деталей из сталей закаленных на мартенсит в результате аустенитного превращения происходят объемные изменения вызывающие внутренние напряжения в поверхностном слое. Легирующие добавки хрома вольфрама молибдена ванадия образуют твердые карбиды которые ухудшают обрабатываемость сталей.
Для улучшения теплового режима резания предлагается использовать схему прерывистого точения суть которой заключается в применении режущих пластин состоящих из сегментов или изготовленных с пропилами. Такая конструкция режущей кромки позволяет прерывать процесс точения дает возможность детали остывать уменьшает тепловые нагрузки на деталь способствует лучшему самозатачиванию резца. Наряду с достоинствами эти круги имеют недостатки заключающиеся в ударном характере их работы (в период врезания и выхода инструмента из металла). В результате этого возникают вибрации технологической системы СПИД вызывающие на поверхности детали волнистость и огранку а также уменьшение долговечности оборудования. К недостаткам этих видов алмазов следует отнести также сравнительную сложность их изготовления. Поэтому режущие инструменты с прерывистой поверхностью имеют ограниченное применение. Считают что для уменьшения температуры точения следует применять алмазные инструменты с более высокими кристаллами.
Для уменьшения прижогов при точении часто переходят к более открытой структуре при этом в зону точения подаются специализированные СОЖ.
Во время исследований с помощью профилометра был проведен контроль шероховатости по параметру R a. Образцы точили с подачей на глубину 002 – 006 мм снимаемый припуск был равен 05 мм. Некоторые результаты экспериментов приведены в табл. 3.3.
Таблица 3.3. Шероховатость обтачиваемой поверхности мкм
Степень прочности заготовки
Марка алмазного материала
Примечание: С – заготовка средней пористости
В - заготовка повышенной прочности.
Анализ данных приведенных в табл. 3.3 позволяет сделать два вывода: с увеличением глубины точения tф увеличивается шероховатость поверхности; при многопроходном точении в режиме затупления высококристаллистный алмазный инструмент обеспечивает шероховатость поверхности на уровне обычного инструмента.
Анализ графиков показывает что при одинаковых режимах шероховатость поверхности обработанной крупнокристаллическим алмазом выше на 1 – 2 разряда.
При исследовании зависимости микротвердости от температуры в зоне резания алмазными резцами с разными характеристиками при различных скоростях детали был сделан важный вывод что на качество поверхностного слоя влияет только температура точения независимо от того инструментом с какой геометрией рельефа режущей поверхности она получена.
Анализируя зависимости микротвердости от фактической глубины точения было замечено что для алмаза со средне кристаллической решёткой наблюдается наиболее интенсивное снижение твердости. Более плавно твердость с увеличением фактического съема уменьшается при точении крупными алмазами. И даже уменьшение скорости детали в 3 раза при точении крупнокристаллическим алмазом не ухудшает качества поверхности по сравнению со средне кристаллическим алмазом. Производительность точения крупно алмазным инструментом при условии обеспечения одинакового качества обработки на уровне границы бесприжоговой зоны может быть увеличена в 15 – 20 раза по сравнению с средне кристаллическим.
Из графиков зависимостей количества остаточного аустенита от фактической глубины при точении алмазным инструментом и твёрдосплавных инструментов представленных в графической части дипломного проекта видно что большие значения количества остаточного аустенита А зафиксированы на образцах после обработки твёрдосплавными инструментами. Данное обстоятельство подчеркивает преимущество использования алмазного инструмента.
Представляет интерес сравнение показателей точения резцов с одинаковыми параметрами геометрии рельефа при одновременном изменении структуры инструмента. Показатели точения всех исследованных резцов с учетом и без учета правки изменялись следующим образом. При переходе от твёрдосплавных резцов к алмазным показатель обработки увеличивается на 25 – 30 %.
В результате произведённых испытаний крупнокристаллического алмазного инструмента установлено следующее: применение алмазных резцов улучшает показатели процесса точения увеличивает общую стойкость его между перепадами температур; при производственных режимах обеспечивает обработку без прижогов и трещин что в ряде случаев снижает брак; позволяет найти равноценную замену импортному инструменту.
“ Усовершенствование техпроцесса изготовления
Такт поточной линии – промежуток времени между запуском или выпуском отдельный изделий.
= Фд Вгод = 325 * 60 15000 = 13 миншт.
Фд – годовой фонд времени необходимый для изготовления годовой программы выпуска (325 ч.);
Вгод – годовая программа выпуска;
Таблица 4.1 Технологический маршрут и нормировочные данные обработки детали
R = p * = 1 * 13 = 13 мин;
р – количество деталей в транспортной партии;
– такт поточной линии;
Таблица 4.2 Расчётное и принятое кол-во оборудования
Таблица 4.3 Сводная ведомость оборудования
Станок расточной 2431
Шлифовальный станок 3Б61
Всм – сменное задание;
Тсм – продолжительность рабочей смены (8 ч.);
Таблица 4.4 коэффициент загрузки оборудования использование оборудования и времени работы для выполнения сменного задания
Росн = Тшт * Вгод (Fд * 60);
Тшт – штучное время всего техпроцесса:
Fд – действительный годовой фонд времени рабочего (1820 ч);
Для базы Росн = 24 принимаем 3;
Для проекта Росн = 22 принимаем 3;
Ррем = ΣСпр * Ксм 8;
ΣСпр – количество станков на поточной линии;
Ксм – число смен (1 смена);
– норма обслуживания станков на наладчика в смену;
Для базы Ррем = 16 принимаем 2;
Для проекта Ррем = 15 принимаем 2;
Принимаем 1 мастер – занятость 40% 1 нач. участка – занятость 15 % 1 инженер-технолог – занятость 20%.
Площадь занимаемая участками механической обработки определяется из соотношения:
где Нс — удельная площадь на один станок Нс = 30 м2;
Спр – количество станков.
Для базы Спр = 390 м2;
Для проекта Спр = 360 м2;
К основным материалам относятся отливки поковки листовой прокат и прочие комплектующие.
Сом = qэ * Вгод * См – qотх * Вгод * Сотх = 75 * 15000 * 50 – 3 * 15000 * 12 = 5571000 руб;
qэ – масса заготовки (75 кг);
qотх – масса отходов (12 кг);
См – стоимость 1 кг материала (1 кг серого чугуна – 50 руб.);
Сотх – стоимость 1 кг отходов (3 руб.);
Ц1м2 зд. – стоимость 1 м2 здания (10000 руб);
Vуч – площадь участка;
Для базы Сзд. = 3900000 руб;
Для проекта Сзд. = 3600000 руб;
Стоимость подъёмно-транспортных средств берётся 4 % от стоимости рабочего оборудования стоимость приспособления и инструментов 10 % от стоимости рабочего оборудования а инвентаря 15 %.
Таблица 5.1 Стоимость основных производственных фондов
Стоимомсть тыс. руб.
Рабочее оборудование
Подъёмно-транспортные средства
Приспособления и инструмент
Хозяйственный инвентарь
а. Затраты на силовую электрическую энергию:
Сэл.= Ц1кВт * N * Фд;
Ц1кВт. - 2 руб. - цена 1 кВт электрической энергии в час
N - устанавливаемая мощность всех электрических двигателей станков на участке (54 кВт);
Фд – годовой фонд времени оборудования необходимый для изготовления годовой программы выпуска (325 ч.);
И для базы и для проекта Сзд. = 35100 руб;
б. Определение затрат на сжатый воздух:
Ссж.= Цсж.1м3 * Qсж.
Для базы - Ссж.= 80 * 3915 = 313200 руб.
Для проекта - Ссж.= 80 * 3613 = 289040 руб.
Ссж.1м3 = 80 руб. - цена 1 м3 сжатого воздуха;
Qсж.= Fмо. Кз.ср. (Спн. q+Собд. q’)
Для базы - Qсж.= 390 0832 (12 01+11 1) = 3915 м3
Для проекта - Qсж.= 360 0832 (12 01+11 1) = 3613 м3
Qсж. - годовой расход сжатого воздуха;
Спн. - количество станков оснащенных оснасткой с пневмоприводами;
q - расход сжатого воздуха на один станок с пневмозажимом;
q’= 1мчас - расход сжатого воздуха на один станок с обдувом
в. Определение затрат на воду для производственных нужд:
Свод.= Ц1м3 Qвод. Кз.ср. Спр
Свод.= 100 25 0832 12 = 24690 руб.
Ц1м3= 100 руб. - цена 1 м3 воды;
Qвод. = 25м3 - удельный годовой расход воды на один станок;
Кз.ср. - средний коэффициент загрузки оборудования;
Спр. - количество принятых станков на участке.
г. Электрическая энергия для освещения помещений:
Сэл.осв.= Фосв.+Sуч. qосв. Ц1кВт 1000
Для базы - Сэл.осв.=2700 390 16 20 1000 = 336960 руб.
Для проекта - Сэл.осв.=2700 360 16 20 1000 = 311040 руб.
Фосв.=2700 час. - годовое число часов освещения помещений;
qосв.=16 Вт.час.м - удельный расход электрической энергии на 1 м2 площади участка;
д. Стоимость пара для отопления помещений:
Спар.=16000 1078= 1724800 руб.
Q- расход пара в течение года.
Qпар.= Sуч. Нчас. q (i1000)
Qпар.=390 4700 20 340 1000=1078 т
Нчас.= 4700 час. - количество часов отопительного сезона в году;
q=20 к.кал.час. - удельный расход топлива на 1м час.
i=540 к.кал.час - тепловая отдача 1 кг пара.
е. Определение затрат на воду для хозяйственных нужд:
Свод.хоз.=Qвод. Ц1м3 Чобщ. Кр.д. 1000
Свод.хоз.=75 100 253 5 1000 = 9487 руб.
Qвод.=75 л - суточный расход воды на одного рабочего;
Чобщ. - количество всех работающих на участке.
Таблица 5.1 Стоимость энергии и прочих услуг
Силовая электрическая энергия
Вода для производственных нужд
Электрическая энергия для освещения помещений
Пар для отопления помещений
Вода для хозяйственных нужд
Часовая тарифная ставка (ЧТС) руб.
Расценка на операцию руб
Фтар = Σ(ЧТС) * Вгод;
Фтар – тарифный фонд заработной;
Фосн – основной фонд заработной;
Д – премия (50% от Фтар);
Фдоп – дополнительный фонд заработной;
Фсоц = (Фосн + Фдоп) * 0356;
Фсоц – социальные отчисления;
Фпол = Фсоц + Фосн + Фдоп;
Фпол – полная зп основных рабочих
Фтар = (ЧТС)рем * Ррем * Фд = 160 * 2 * 325 = 104000 руб;
(ЧТС)рем – часовая тарифная ставка рабочего-ремонтника 4-го разряда;
Фтар = Σ(должностной оклад) * Кз * М;
Кз – коэффициент занятости;
М – число рабочих месяцев в течении которых выполняется годовая программа (2 месяца);
Для мастера - Фтар = 20000 * 04 * 2 = 16000 руб
для начальника участка - Фтар = 28000 * 015 * 2 = 8400 руб
для инженера-технолога - Фтар = 21000 * 02 * 2 = 8400 руб
Общий Фтар = 16000+8400+8400=32800 руб;
Таблица 5.3 Сводная таблица зп по всем категориям персонала
Руководители и специалисты
Таблица 5.4 Затраты на годовые амортизационные отчисления
Стоимость фондов тыс. руб
амортизационных отчислений тыс. руб
Помимо всех ранее рассчитанных статей расходов связанных с производством изделия в цеховую себестоимость также входят такие статьи как: текущий ремонт участка (5% от стоимости участка) расходы по охране труда и ТБ (2000 руб. на одного рабочего в год) расходы на вспомогательные материалы (5% от стоимости основных материалов).
Таблица 5.5 Цеховая себестоимость изделия
Амортизация основных фондов
Текущий ремонт участка
Расходы по охране труда
Расходы на основные материалы
Расходы на вспомогательные материалы
Расходы на энергию и все виды услуг
Полная зп всего персонала
З – приведённые затраты;
С – себестоимость единицы продукции;
Ен – нормативный коэффициент экономической эффективности кап. вложений (025);
К – стоимость отсновных производственных фондов;
Для базы К’ = 2639 руб;
Для проекта К’ = 2473 руб;
Для базы З = 14325 руб;
Для проекта З = 13518 руб;
Эф = (Зб - Зп) * Вгод = (14325 - 13518) * 15000 = 1210500 руб.
Эф – годовой экономический эффект;
Таблица 5.6 Анализ технико-экономических показателей
Наименование показателей
Абсолютные показатели
Годовой выпуск изделия:
Основные произв. фонды:
- рабочее оборудование
- подъёмно-транс. средства
- присп. и инструмент
- хозяйст. инвентарь
- ИТР и специалистов
Относительные показатели
Производственная площадь на ед. оборудования
Средняя мощность оборудования
Средний коэффициент загрузки оборудования
Станкоёмкость изготовления изделия
Средний разряд рабочих
Цеховая себестоимость:
Ркр = Зпост (Ц - Сц) = 37095000 (13205 – 7336) = 63207 шт.
где Ркр – величина производимой продукции впри которой проект полностью окупается;
Ц = 18 * Сц = 13205 руб;
Сц – цеховая себестоимость единицы изделия (руб.);
Ц – цена одной детали при рентабельности продажи 80%;
Зпост – постоянные расходы (равны стоимости основных производственных фондов).
В табл. 6.1. приведены некоторые данные по базовому предприятию и их сравнение с нормативно – допустимыми значениями.
Таблица 6.1 Анализ факторов действующих в механическом цехе
Загрязнение воздушной среды (предельно допустимая концентрация вредных веществ в воздухе рабочей зоны)
“Определение пре-дельно допустимой концентрации вред-ных веществ в воз-духе рабочей зоны производственных помещений”
Ультрафиолетовое облучение
Производственная вибрация
ГОСТ 12.1.01293.ССБТ
“Вибрация. Общие требования безопас-ности”
Электромагнитные поля на производстве (плотность потока энергии)
“Электромагнитные поля радиочастот. Общие требования безопасности”
Освещение в механическом цехе
Электробезопасность в механическом цехе
Производственный шум на рабочих местах
“Шум. Общие требо-вания безопасности”
Анализ факторов действующих в механическом цехе показал что уровни загрязнения воздушной среды ультрафиолетового облучения производственных вибраций электромагнитных полей на производстве освещенности и электробезопасности соответствуют ГОСТ а уровень шума – не соответствует. Поэтому остановимся на этом факторе более подробно.
Предлагается исследовать 6 рабочих мест. Результаты измерений приведены в табл. 6.2.
Таблица 6.2. Производственный шум на рабочих местах
Служба энергетика сварки
Заточное отделение станок №13346
Заточное отделение станок №11046
Из анализа результатов видно что не соответствует норме 1 рабочее место. Рассмотрим этот вопрос подробней.
Научно – технический прогресс в различных отраслях народного хозяйства связан с ростом уровня шума на рабочих местах. Например с ростом единичной мощности оборудования и стремлением к снижению металлоемкости увеличивается удельная мощность и снижается жесткость конструкции оборудования что приводит к повышенной вибрации отдельных его частей и как следствие к увеличению звуковой мощности.
Постоянное воздействие шума на организм человека приводит к изменению функционирования пищеварительного тракта нервной системы сердечно – сосудистой системы кроме этого шум может вызвать ослабление слуха а при очень большой интенсивности шума и к полной его потере.
Поэтому нужно постоянно стремиться к понижению уровня шума особенно в тех местах где он может повредить человеку.
Подавление шума и вибраций на предприятиях осуществляется следующими способами:
уменьшают шум и вибрации в источнике их возникновения путем рационального конструирования оборудования и инструмента качественного изготовления монтажа и эксплуатации;
проводят организационно-технические мероприятия;
заменяют шумное оборудование менее шумным;
рационально размещают шумные из них в отдельных помещениях;
планируют работы шумного оборудования на такое время когда число работающих меньше;
осуществляют автоматизацию технологического процесса которая частично или полностью устраняет вредное воздействие шума на работающих;
применяют звукопоглощающие материалы и конструкции звукоизолирующие строительные преграды;
используют виброизолирующие устройства и вибропоглощающие материалы;
применяют различного рода глушители струйных шумов;
эти мероприятия осуществляют в комплексе в соответствии с конкретными условиями.
Эти мероприятия осуществляют в комплексе в соответствии с конкретными условиями.
По частотному составу шумы подразделяют на три класса:
) низкочастотные шумы наибольшие уровни звукового давления которых расположены в спектре ниже частоты 350 Гц. Сюда могут быть отнесены шумы тихоходных агрегатов неударного действия и т. п.;
) среднечастотные шумы наибольшие уровни звукового давления в спектре которых расположены в диапазоне 350-800 Гц.
) высокочастотные шумы наибольшие уровни звукового давления в спектре которых расположены выше частоты 800 Гц. Таким спектром характеризуются звенящие шипящие и свистящие источники шума.
Технический комитет 43-й Международной организации по стандартизации (ИСО-ТК-43) рекомендовал для оценки и нормирования шума пользоваться семейством кривых имеющих критерии шумности N от 0 до 130. Кривые лимитируют уровни в восьми октавных полосах со среднегеометрическими частотами 63 125 250 500 1000 2000 4000 8000 гц.
На основании этого приняты Санитарные нормы и правила по ограничению шума на территориях и в помещениях производственных предприятий (СН-785-69). Предельно допустимые уровни звукового давления нормируются в октавных полосах частот.
Нормы установленные СН-785-69 должны соблюдаться в следующих фиксированных точках: на всех рабочих местах на высоте 15 м от уровня пола или на рабочей площадке на расстоянии не менее 2 м от ограждающих конструкций а на территории – не ближе 2 м от зданий.
Метод уменьшения шума в источнике его возникновения должен являться преобладающим по сравнению с другими методами и именно с него должна начинаться борьба с указанными производственными вредными воздействиями на любом производственном участке.
Причинами высоких уровней шума машин и технологического оборудования могут быть:
) конструктивные особенности машин в результате которых появляются удары и трения узлов и деталей; например удары толкателей на штоки клапанов работа кривошипно-шатунных механизмов зубчатых колес недостаточная жесткость отдельных частей машины;
) технические недостатки появившиеся в процессе изготовления оборудования: плохая динамическая балансировка вращающихся деталей и узлов недостаточное выполнение шага зацепления и формы профиля зуба зубчатых колес ничтожно малые отклонения в размерах деталей машин отражаются на спектре и уровне шума;
) некачественный монтаж оборудования на производственных площадках который приводит к перекосам и эксцентриситету работающих деталей и узлов машин а также к вибрациям строительных конструкций;
) нарушение правил технической эксплуатации машин и агрегатов неправильный режим работы оборудования т. е. режим отличающийся от паспортного режима плохой уход за станочным парком и др.;
) несвоевременный ремонт и некачественный планово-предупредительный ремонт который приводит не только к ухудшению качества работы машины но и способствует увеличению производственного шума;
) непродуманные в отношении шумового режима отдельные технологические процессы которые должны быть устранены (сбрасывание
деталей из звонких металлов которое должно быть заменено спуском их по направляющим выполненным из незвучного материала) и др.
Устранение указанных недостатков будет способствовать снижению уровня шума в производственных помещениях. Автоматизация производственных процессов как правило позволяет полностью ликвидировать воздействие шума на обслуживающий персонал. Аналогичны причины вибраций оборудования и инструмента.
Звукопоглощение осуществляется использованием звукопоглощающей способности материалов и конструкций при размещении которых в цехе понижается уровень производственного шума. Поглощая звуковую энергию волн распространяющихся по воздуху звукопоглощающие материалы трансформируют ее в тепловую.
Звукопоглощающие материалы и конструкции подразделяют на четыре класса:
)волокнисто – пористые поглотители (войлок вата фетр акустическая штукатурка акустические плиты типа ПАС ПАО и др.);
)мембранные поглотители (полихлорвиниловые или другие виды пленок клеенка тонкие листы металла или фанеры набитые на деревянные обрешетки);
)резонаторные поглотители представляющие собой специальные конструкции основанные на акустических свойствах резонатора Гельмгольца;
)комбинированные звукопоглощающие конструкции использующие два или все три вида упомянутых поглотителей для увеличения эффективности звукопоглощения и расширения частотного диапазона их работы.
Рассмотрим подробно случай достижения звукоизоляции созданием специальных строительных преград препятствующих распространению шума по воздуху из одного помещения (или части помещения) в другое.
Для сравнительной оценки перегородок и перекрытий при борьбе с распространением воздушного шума служит звукоизолирующая способность R:
R = L1 – L2 + 10*lg (дБ)
где L1 – уровень звукового давления в помещении где находится источник шума дБ;
L2 – уровень звукового давления в изолируемом помещении дБ;
S – площадь преграды изолируемого помещения м2;
А – полное внутреннее звукопоглощение в изолируемом
Ограждающие конструкции подразделяют на однослойные колеблющиеся как одно целое и многослойные (несколько слоев не имеющих жесткой связки) способные колебаться с разными для каждого слоя амплитудами.
У однослойных ограждений частотная характеристика имеет четыре диапазона (рис. 6.1).
Рис. 6.1. Зависимость звукоизолирующей
преграды R от частоты f
В первом частотном диапазоне звукоизоляция определяется жесткостью ограждения и резонансными явлениями. Для большинства однослойных ограждений этот диапазон лежит ниже 50 Гц и в расчетах R не учитывается.
Второй диапазон характеризуется увеличением звукоизолирующей способности с частотой (закон массы):
R = 20*lgQ + 20*lg f – 54 (дБ).
ЗдесьQ – вес преграды приходящийся на 1 м2 кгм2;
f – частота звука Гц.
В третьем диапазоне происходит ухудшение звукоизоляции преграды вследствие эффекта волновых совпадений который реализуется при условии равенства длины изгибной волны в преграде и проекции падающей звуковой волны.
В этом случае амплитуда волн изгиба значительно возрастает и происходит интенсивная передача энергии по другую сторону ограждения.
В легких звукоизолирующих преградах целесообразно уменьшать их жесткость изгибу и тем самым повышать граничную частоту волнового совпадения. В тяжелых преградах наоборот выгодно увеличивать их жесткость изгибу и тем самым снижать граничную частоту волнового совпадения.
Диапазон волновых совпадений занимает интервал частот примерно в две октавы.
Четвертый диапазон характеризуется увеличением звукоизолирующей способности преграды на протяжении одной октавы – 10 дБоктава и далее ~ 6 дБоктава.
Звукоизолирующая способность однослойной преграды на частоте 500 Гц может быть также рассчитана по формулам:
а) при весе ограждения до 200 кгм2:
б) при весе ограждения выше 200 кгм2:
гдеQ – вес 1 м2 ограждения кг.
Определив звукоизолирующую способность ограждения на частоте 500 Гц можно построить частотную характеристику звукоизолирующей способности на других частотах в результате внесения поправок в расчетную величину R.
Снижение уровня прошедшей в помещение энергии DL за счет наличия дверного или оконного проема:
L = - 10*lg + 10*lg10 –01( R1-R2 ) (дБ)
или считая что звукоизолирующая способность ограждения с проемом равна RS получим:
RS = R1 - - 10*lg + 10*lg10 –01( R1-R2 ) (дБ)
гдеR1 – звукоизолирующая способность глухой стены дБ;
R2 – звукоизолирующая способность проема дБ;
S1 – площадь глухой стены м2;
S2 – площадь проема м2.
Щели и отверстия в заграждениях существенно понижают звукоизоляцию особенно в области низких частот. Примерное снижение звукоизолирующей способности DR в диапазоне частот от 800 до 1800 Гц вызванное отверстием можно определить по формуле:
R = 10*lg(1 + n**10 01R) (дБ)
гдеR – звукоизолирующая способность ограждения дБ;
S – площадь ограждения м2;
S0 – площадь отверстия м2;
n – коэффициент n = 3 12.
Звукоизолирующая способность правильно спроектированных многослойных преград больше однослойных преград той же массы. Так звукоизоляционные качества двойной перегородки с несвязанными панелями зависят от массы панелей величины воздушного промежутка граничной частоты каждой панели резонанса конструкции.
Учитывая содержание вышесказанного выполним соответствующий расчет.
Звукоизолирующая способность:
R = L1 – L2 + 10*lg (дБ).
Отсюда L2 = L1 + 10*lgR - уровень звукового давления в изолируемом помещении.
В качестве строительных преград используем картон в несколько слоев 1 м2 которого весит 12 кг ( Q = 12 кг ) [табл. 8 7].
Ограждающая контурная однослойная величина звукоизолирующей способности:
диапазон 1 – определяется жесткостью ограждения и в расчетах не учитывается;
диапазон 3 – ухудшение звукоизоляции;
R = 135*lgQ + 13 = 135*lg12 + 13 = 277 дБ.
С учетом поправки R1 = 4 дБ:
R = 277 + 4 = 317 дБ.
Исходя из полученных результатов строим частотную характеристику:
Рис. 6.2. Частотная характеристика
Здесь L1 – уровень звукового давления в помещении L1=87 дБ
S = 35 м2 – площадь преграды изолируемого помещения;
где d – коэффициент звукопоглощения данного материала d = 095;
А1 – полное звукопоглощение отдельных предметов м2.
где d1 – коэффициент звукопоглощения отдельных предметов d1 = 004
A = 095*35 + 14 = 3468 м2.
L2 = 87 + 10*lg - 317 = 554 дБ.
Таким образом при установке звукоизоляционных преград уровень шума существенно снижается и становится допустимым. Поставленная цель достигнута.
С целью повышения производительности и эффективности обработки на расточной операции подшипниковых диаметров ступицы был использован алмазно-расточной станок повышенной точности и резец с алмазно-режущей кромкой вместо обычного расточного станка с твёрдосплавным инструментом используемом в базовом техпроцессе. В результате этого пропала необходимость в шлифовальной обработке данных диаметров что позволило сократить трудоёмкость и уменьшить количество оборудования на один станок.
В конструкторской части выполнена конструктивная разработка 3-х кулачкового патрона для токарной операции а также представлено контрольное приспособление для проверки торцевого и радиальных биений ступицы.
В спецвопросе (в научно-исследовательской части) был произведён сравнительный анализ между алмазными и твёрдосплавными резцами. Там же было обосновано преимущество в применении алмазного инструмента.
В части «безопасность и экологичность» рассмотрен вопрос защиты от шума. Предложены методы понижения уровня звукового давления.
В экономической части усовершенствование техпроцесса изготовления ступицы позволило получить годовой экономический эффект в размере 1210500 руб. при годовой программе в 15000 штук.
Альбом чертежей и технологических наладок В. Г. Гусев В. Н. Жарков Е. Н. Петухов – Владимир 2001.
Ансеров М. А. Приспособления для металлорежущих станков. М.: Машиностроение 1966.
Безопасность труда на производстве. Защитные устройства. Справочное пособие. Коллектив авторов. Под ред. проф. Б. М. Злобинского. М.: Металлургия 1971.
Горбацевич А. Ф. Шкред В. А. Курсовое проектирование по технологии машиностроения. Минск: Высшая школа 1983.
Горбунов Б. И. Обработка металлов резанием металлорежущий инструмент и станки. М.: Машиностроение 1981.
Горошкин А. К. Приспособления для металлорежущих станков: Справочник. М.: Машиностроение1979.
Дипломное проектирование по технологии машиностроения. Под ред.
В. В. Бабука. М.: Высшая школа 1979.
Долин П. А. Справочник по технике безопасности. М.: Энергоиздат 1984.
Допуски и посадки: Справочник в 2-х ч. Ч. 1 Под ред. В. Д. Мягкова. – 5-е изд. перераб. и доп. – Л.: Машиностроение. Ленингр. отд – ние 1983.
Егоров М. Е. Основы проектирования машиностроительных заводов. М.: Машиностроение 1983.
Известия высших учебных заведений. №2. М.: Машиностроение 1987.
Корсаков В. С. Основы конструирования приспособлений. М.: Машиностроение 1983.
Металин А. А. Технология машиностроения. Л.: Машиностроение 1985.
Мельников Г. Н. Вороненко В. П. Проектирование сборочных цехов. М.: Машиностроение 1990.
Металлорежущие станки. Под ред. В. К. Тепинкичева. М.: Машиностроение 1973.
Методические рекомендации по проведению патентных исследований при дипломном проектировании. Сост.: Л. Ф. Жаркова. – Владимир 1981.
Методические указания к выполнению дипломного проекта по технологии машиностроения. Под ред. В. Г. Гусева. – Владимир 1992.
Методические указания к курсовому и дипломному проектированию. Сборные абразивные круги с прерывистой режущей поверхностью. Сост. В. Г. Гусев В. Н. Жарков. – Владимир 1984.
Методические указания по оформлению технологической документации при выполнении курсовых и дипломных проектов. Сост. В. Г. Гусев В. Н. Жарков. – Владимир 1998.
Методические указания к практическим занятиям по проектированию механосборочных цехов. Сост.: В. Д. Мирошникова В. А. Каширин. – Владимир 1991.
Охрана труда в машиностроении. Под ред. Е. Я. Юдина С. В. Белова. М.: Машиностроение 1983.
Попов С. А. Ананьян Р. В. Шлифование высокопористыми кругами. - М.: Машиностроение 1980.
Проектирование заводов и механосборочных цехов в автотракторной промышленности. А. А. Андерс Н. М. Потапов А. В. Шулешкин. М.: Машиностроение 1982.
Проектирование технологических процессов механической обработки в машиностроении. Под ред. В. В. Бабука. – Минск: Высшая школа 1987.
Разработка технологических процессов в машиностроении. Учебное пособие. Сост.: В.Г. Гусев А. И. Желобов Т. А. Желобова. – Владимир1995.
Справочник инструментальщика. Под ред. А. В. Ординарцева. – Л.: Машиностроение 1987.
Справочник конструктора – инструментальщика. Под ред. В. Н. Барабанщикова. – М.: Машиностроение 1994.
Справочник нормировщика. Под ред. А. В. Ахумова. - Л.: Машиностроение 1987.
Справочник технолога. Обработка металлов резанием. Под ред. А. В. Панова. – М.: Машиностроение 1988.
Справочник технолога – машиностроителя. Т.1 2. Под ред. А. Г. Косиловой Р. К. Мещеркова. М.: Машиностроение 1985.
Проектирование машиностроительных заводов и цехов. Справочник. Т.6. Под ред. М. И. Храмой Е. С. Янпольского. М.: Машиностроение 1976.
Режимы резания металлов. Справочник. Под ред. Ю. В. Барановского. М.: Машиностроение 1972.
Лист 12 (экономическая часть).dwg

Технико-экономические показатели График безубыточности
Участок механической обработки ступицы переднего колеса колесного трактора т25 с подробной разработкой технологического процесса механической обработки
Количество единиц продукции
График безубыточности
Технико-экономические показатели
Лист 1 (деталь и заготовка).dwg
Ступица переднего колеса
163 229 НВ. 2. Неуказанные литейные уклоны 1° 2°
радиусы 3..5 мм. 3. Отливка III группы по ГОСТ 26645-85. i-8
На обработанных поверхностях кроме С
И допускаются раковины глубиной до 3 мм
не доходящие до контуров поверхностей и отверстий. 5. Допуск радиального биения поверхностей С и Д относительно друг друга 0
Допуск непостоянства диаметров С и Д в поперечном и продолбном сечениях 0
5 мм. 7. **Размеры обеспечиваются инструментом. i0
Неуказанные предельные отклонения по h14
Покрытие: Эмаль КМЛ-13 тёмно-серая ТУ 2312-021-16952278-95.V.У1.
Ступица переднего колеса (заготовка)
Твёрдость 163 229 НВ. 2. Неуказанные литейные уклоны 1 2 радиусы 3 5 мм. 3. На обрабатываемых поверхностях допускаются любые литейные уклоны
выводимые мех. обработкой. 4. Допускается исправление литейных дефектов качественной заваркой. 5. Точность отливки 11т - 10 ГОСТ 26645 - 85
Участок механической обработки ступицы переднего колеса колесного трактора т25 с подробной разработкой технологического процесса механической обработки
Лист 2 (наладка инструментальная).dwg
Наладка инструментальная
Цикл работы вертикального силового стола
Цикл резьбонарезных шпинделей
Торец вертикальной шпиндельной головки
Участок механической обработки ступицы переднего колеса колесного трактора т25 с подробной разработкой технологического процесса механической обработки
Операция 015: сверлильная
Оборудование: Спец. сверлильный. станок мод. АМ-7787
Лист 7 (контрольное приспособление).dwg

Приспособление контрольное
Техническая характеристика 1. Гидропластическое давление вполости приспособления Р=118 кгссм2 2. Исходная сила развиваемая гайкой поз. Q=28
Технические требования 1. Размеры для справок 2. Допуск радиального биения пов.А и торцевого пов.Б в сборе относительно оси шпинделя не более 0
мм 3. Положение стойки поз.3 определять по месту контролируемой детали
Приспособление контрольное
Участок механической обработки ступицы переднего колеса колесного трактора т25 с подробной разработкой технологического процесса механической обработки
Используется для торцеввых и радиальных биений внутренних и наружных диаметров детали на контрольной операции
Поточная линия механической обработки детали
Барабан фрикциона 150М.37.700." трактора ХТ3.
Лист 11 (планировка участка).dwg

Транспортно-накопительная система
Участок механической обработки ступицы переднего колеса колесного трактора т25 с подробной разработкой технологического процесса механической обработки
ПОДВОД СЖАТОГО ВОЗДУХА
КОНТЕЙНЕР ДЛЯ ЗАГОТОВОК
КОНТЕЙНЕР ДЛЯ ДЕТАЛЕЙ
СТЕНД ТЕХНИКИ БЕЗОПАСНОСТИ
ПОЖАРНЫЙ ЯЩИК С ПЕСКОМ
ПОДВОД ЭЛЕКТРОЭНЕРГИИ
ПОДВОД СРЕДСТВ ОХЛАЖДЕНИЯ
НАПРАВЛЕНИЕ ДВИЖЕНИЯ РОБОТА
МЕЖОПЕРАЦИОННЫЕ НАКОПИТЕЛИ
РОБОТ ДЛЯ ПОДАЧИ ЗАКОТОВКИ МОД. "ПРЦ-1
КОНТРОЛЬНОЕ ПРИСПОСОБЛЕНИЕ
График загрузки оборудования при обработке ступицы
Лист 5 (наладка технологическая №3).dwg
Наладка технологическая
Операция 025: алмазно-расточная
Оборудование: Спец. расточной станок мод. ОС-4555
Резец расточной алмазный ГРО
Участок механической обработки ступицы переднего колеса колесного трактора т25 с подробной разработкой технологического процесса механической обработки
Лист 8 (портальный робот).dwg

агрегатно-модульной конструкции
Число степеней подвижности
Горизонтальное перемещение руки
Вертикальное перемещение руки
Поворот оси вокруг вертикальной оси
Поворот (качение) кисти
Поворот схвата относительно продольной оси
Скоростт линейных перемещений
Скорость угловых перемещений
Число програмируемых позиций(при повороте
и вертикальном перемещение руки)
Ц1-цилиндр венртика-
тального перемещения
Качественный и подробный дипломный проект "Усовершенствование техпроцесса изготовления оси колеса трактора Т35А"
Участок механической обработки ступицы переднего колеса колесного трактора т25 с подробной разработкой технологического процесса механической обработки
Цилиндры силовые моду-
ля поворота 100-6795-00
Цилиндр горизонталь-
Цилиндр модуля схвата
Цилиндр вертикального
перемещения ПЦ-100-00
Выключатель конечный
Пневмораспределитель
Блок упоров 110-6795-00
Промышленный робот ПРЦ-1 агрегатно-мо- дульной конструкции
кг 10 2. Число степеней подвижности 5 3. Горизонтальное перемещение руки
мм 600 4. Вертикальное перемещение руки
мм 300 5. Поворот оси вокруг вертикальной оси
град 220 6. Поворот (качение) кисти
град 90 7. Поворот схвата относительно продольной оси
град 90 и 180 8. Скоростт линейных перемещений
мс 0.5 9. Скорость угловых перемещений
градс 60 10. Число програмируемых позиций(при повороте и вертикальном перемещение руки) 3 11. Масса
Техническая характеристика
Лист 4 (наладка технологическая №2).dwg
Наладка технологическая
Операция 015: сверлильная
Оборудование: Спец. сверлильный. станок мод. АМ-7787
Участок механической обработки ступицы переднего колеса колесного трактора т25 с подробной разработкой технологического процесса механической обработки
Лист 3 (наладка технологическая №1).dwg
Наладка технологическая
Операция 005: токарная
Оборудование: Токарный полуавтомат мод. 1734
Участок механической обработки ступицы переднего колеса колесного трактора т25 с подробной разработкой технологического процесса механической обработки
Лист 10 (научно-исследовательская часть).dwg

- твердосплавные резцы ; - алмазные резцы
сплошная линия U =52ммин;
Зависимость микротвердости Н (а) и шероховатости поверхности (б) от фактической глубины tф при точении
сплошная линия U =52ммин ; штриховая линия U =34ммин
Изменение микротвердости Н (а) и количества остаточного аустенита (б) на шлифуемой поверхности от
твeрдосплавным и алмазным резцом (U
Микротвердость исходной структуры
температуры в зоне резания (U =67мс)
научно-исследовательская
Участок механической обработки ступицы переднего колеса колесного трактора т25 с подробной разработкой технологического процесса механической обработки
Лист 6 (наладка технологическая №4).dwg
Наладка технологическая
Операция 030: токарная
Оборудование: Токарный многорезцовый павт. 1Н713
Участок механической обработки ступицы переднего колеса колесного трактора т25 с подробной разработкой технологического процесса механической обработки
Лист 9 (зажимное приспособление).dwg

-х кулачковый патрон
Участок механической обработки ступицы переднего колеса колесного трактора т25 с подробной разработкой технологического процесса механической обработки
Усилие зажима заготовки - 4
Рекомендуемые чертежи
- 01.07.2014
- 25.06.2017
- 05.01.2022