ТЭЦ мощностью 520 МВт с турбиной К-520-23.5 ЛМЗ




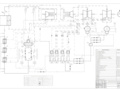
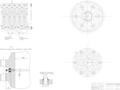
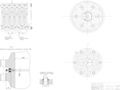
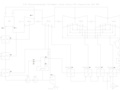
- Добавлен: 24.01.2023
- Размер: 3 MB
- Закачек: 0
Описание
Состав проекта
![]() |
![]() |
![]() |
![]() |
![]() |
![]() |
![]() |
![]() |
![]() ![]() ![]() |
![]() |
![]() |
![]() ![]() ![]() |
![]() ![]() ![]() ![]() |
![]() ![]() ![]() ![]() |
![]() ![]() ![]() ![]() |
![]() |
![]() ![]() ![]() ![]() |
![]() |
![]() ![]() ![]() |
![]() ![]() ![]() |
![]() |
![]() ![]() ![]() |
![]() |
![]() |
![]() ![]() ![]() |
![]() ![]() ![]() ![]() |
![]() |
![]() ![]() ![]() |
![]() ![]() ![]() |
![]() ![]() ![]() |
![]() ![]() ![]() |
![]() |
![]() ![]() ![]() ![]() |
![]() |
![]() ![]() ![]() |
![]() |
![]() ![]() ![]() |
![]() |
![]() ![]() ![]() |
![]() ![]() ![]() ![]() |
Дополнительная информация
Выбор оборудования РАМОР.doc
Выбор основного и вспомогательного оборудования для энергоблока будем производить исходя из данных полученных при расчете тепловой схемы турбоустановки К-520-235 а также рекомендаций по выбору теплообменного оборудования для данной турбины по литературе [1] [2] [3]. Выбор оборудования должен обеспечивать надежную и экономичную работу турбоустановки в требуемом диапазоне нагрузок.
1. Основные характеристики турбины К-520-235.
Турбина спроектирована на начальные параметры пара 235 МПа 560 °С с промежуточным перегревом ее до 560 °С на давление в конденсаторе 33кПа и частоту вращения 50 с.
Пар из парогенератора по двум паропроводам подается к двум блокам стопорно-регулирующих клапанов установленным рядом с турбиной.
От регулирующих клапанов пар по 4 перепускным трубам поступает к штуцерам сопловых коробок ЦВД.
Цилиндр высокого давления – противоточной конструкции. Пройдя одновенечную регулирующую ступень и 5 ступеней левого потока расположенных во внутреннем корпусе поток пара поворачивает на 180° и проходи сначала по межкорпусному пространству а затем – через последние 6 ступеней ЦВД расположенных во внешнем корпусе.
Пар покидает ЦВД и по двум паропроводам направляется в котел на промежуточный перегрев. Из котла по двум паропроводам пар поступает к стопорным клапанам ЦСД.
Цилиндр среднего давления – двухпоточный. Пройдя 11 ступеней ЦСД пар по 4 патрубкам поступает в ЦНД.
Турбоустановка К-520-235 имеет 2 симметричных двухпоточных ЦНД. После ЦНД отработавший пар поступает в конденсатор где он конденсируется.
2 Выбор парового котла.
Тип парового котла определяется выбранным типом турбины а также видом топлива суммарной мощностью и режимом работы ТЭС.
Для данной принципиальной тепловой схемы КЭС с турбоустановкой типа К-520-235 мощностью 520МВт паропроизводительность котла работающего на каменном угле Кузнецкого месторождения составляет:
Поскольку начальное давление составляет p0=235 МПа то в данной тепловой схеме необходимо применение прямоточного котла.
Основные параметры пара и питательной воды необходимые для выбора котельного агрегата:
По данным параметрам по таблице1.1 литературы [1] выбираем тип котла.
За прототип берём котёл заводской маркировки П-57Р рассчитанного на параметры:
Основные характеристики парового котла П-57Р:
Котел П-57Р предназначен для работы на экибастузских каменных углях в блоке с турбиной мощностью 500 МВт.
Котел прямоточный на сверхкритические параметры пара с промперегревом однокорпусный выполнен по Т-образной компоновке с уравновешенной тягой и с твердым шлакоудалением.
Топочная камера – призматическая. Топочная камера оборудована 24 пылеугольными горелками расположенными встречно в два яруса на боковых стенах топки
Котел имеет две одинаковые конвективные шахты в которых по ходу газа расположены следующие поверхности нагрева: конвективного пароперегревателя высокого давления из плавниковых труб; конвективного пароперегревателя промперегрева второй ступени; два пакета конвективного промперегревателя первой ступени водяной экономайзер.
В горизонтальных газоходах имеется ширмовый пароперегреватель.
Техническое задание:
Т.к. некоторые из моих расчётных параметров() превышают те же параметры() котла заводской маркировки П-57Р то необходимо спроектировать прямоточный котёл на основе котла указанного выше.
Технические параметры требуемого котла:
КПД котла брутто – 90%
Котел маркировки П-57Р спроектирован для работы на Экибастусском угле а проектируемый мною котёл должен работать на Кузнецком угле.
Данный пылеугольный котел работает под разряжением. Тип воздухоподогревателя – трубчатый.КПД котла брутто – 90% аэродинамическое сопротивление газового и воздушного тракта:
Высота котла равная расстоянию от нулевой отметки до верхнего коллектора испарительного тракта прямоточного котла .
3. Выбор схемы пылеприготовления.
Выбор схемы пылеприготовления производим с помощью лит[1]. В данном случае применяется замкнутая система с прямым вдуванием. Отработавший после сушки топлива воздух вместе с угольной пылью и выделившимися водяными парами сбрасывается в топку.
Рис. 3.3.2 Схема пылеприготовления с прямым вдуванием пыли.
-бункер сырого угля 2- молотковая мельница с гравитационным сепаратором 3-горелки 4- короб горячего воздуха 5- воздухоподогреватель.
Из бункера сырого угля 1 топливо поступает в мельницу 2.Размолотое в мельнице топливо попадает в шахту которая является гравитационным сепаратором тонкая пыль через горелку 3 выбрасывается в топку потоком воздуха а крупные частицы угля возвращаются в мельницу. В схеме отсутствует пылевой бункер что упрощает и удешевляет установку.
4. Выбор оборудования пылеприготовления.
Качество угольной пыли характеризуется тонкостью помола и влажностью. Тонкость помола зависит от реакционной способности угля характеризуемой выходом летучих фракций . Важной характеристикой угля является размолоспособность. Для дальнейшего выбора оборудования выпишем из лит [1] основные характеристики топлива:
Тип топлива – Кузнецкий Т
Теоретические объемы
Рекомендуемый тип мельницы – ММТ
4.1 Выбор типа мельниц.
С учетом характеристик топлива выбираем мельницы типа ММТ.
Мельница состоит из стального корпуса и ротора с шарнирно укрепленными на нем билами. Уголь попадая на быстровращающиеся била размалываются и увлекаются из корпуса потоком воздуха.
4.2 Выбор числа и производительности мельницы.
Число мельниц установленных на котле зависит от его производительности и от типа мельниц. С учетом рекомендаций по выбору числа мельниц (лит. [2]) примем число мельниц z=6. Расчетная производительность одной мельницы определяется по известному из расчета тепловой схемы расходу топлива на котел и принятому числу мельниц.
Т.к. Z ≥ 5 то воспользуемся следующей формулой:
По справочнику [2] определяем типоразмер мельницы: 20002590750К600К
Технические характеристики мельницы:
Диаметр ротора D=2000 мм
Длина ротора L=2590 мм
Максимальная температура сушильного агента
Пересчет производительности с “характерного” вида топлива
5. Выбор тягодутьевых машин.
В данной схеме в качестве топлива используется Кузнецкий уголь котел работает под разряжением. На котле установлены дутьевые вентиляторы и дымососы.Котел имеет негазоплотное исполнение. Присосы воздуха по тракту котла оказывают большое влияние на работу тягодутьевых устройств увеличивая объем перекачиваемых газов что приводит к увеличению расхода энергии на собственные нужды и снижению экономичности работы котла.
Для дальнейших расчетов выпишем значения основных присосов воздуха при движении продуктов сгорания по тракту котла:
коэффициент избытка воздуха в топке – αт=12
присосы в топке αт=005
суммарные присосы воздуха в конвективных газоходах первичного и вторичного пароперегревателя αкп=012
присосы воздуха и протечки газов в воздухоподогревателе αвп=003
присосы в золоулавителях αзу=010
Расход топлива по которому выбираются дутьевые вентиляторы и дымососы определяются с учетом физической неполноты сгорания твердого топлива. Принимаем по [3] q4=2%. Тогда расход топлива:
6. Выбор дутьевых вентиляторов.
Дутьевой вентилятор подает холодный воздух в воздухоподогреватель забирая его из верхней части котельной.
Принимаем согласно [1] температуру холодного воздуха Производительность вентилятора определяется расходом воздуха необходимым для горения топлива с учетом коэффициента избытка воздуха в топке и присосов по тракту котла [1]:
Расчетная производительность вентилятора принимается с коэффициентом запаса [1]. Кроме того вводится поправка на барометрическое давление. Принимаем число вентиляторов z=4. Расчетная производительность одной машины:
Напор дутьевого вентилятора зависит от сопротивления воздушного тракта. Суммарное сопротивление тракта по [1]: . Расчетное значение напора принимается с коэффициентом запаса [1].
По найденным расчетным значениям производительности и напора определяем типоразмер дутьевого вентилятора. По[2] выбираем тип дутьевого вентилятора – ВДН-32Б.
Технические характеристики дутьевого вентилятора:
Подача V=475385 тыс.м³ч
Полное давление p=61004000 Па
Температура газа t=30°C
Частота вращения n=730590 обмин
Мощность на валу дутьевого вентилятора определяется по формуле:
Мощность привода берется с коэффициентом запаса необходимым для преодоления инерции при пуске вентилятора.
Производительность дымососа определяется объемными расходами газов уходящих из котла и воздуха присасываемого в тракт после котла в золоулавителях и газоходах. С учетом температуры газов перед дымососом объемная производительность машины по [1]
Объем уходящих газов равен сумме теоретического объема газов и объема присосов воздуха по тракту котла
Объем присосов за пределами котла
Определим температуру газов перед дымососом.
Т.к. величина суммарных присосов =013 ≥01 то температура газов перед дымососом определяется по формуле смешения:
Тогда производительность дымососа:
Принимаю по [1] число дымососов равное числу дутьевых вентиляторов z=4. Тогда расчетная производительность дымососа с учетом коэффициента запаса 1=11 (по [1]):
Напор дымососа принимаем по [1] -
С учетом коэффициента запаса 2=12 расчетный напор дымососа:
По оцененным выше производительности и напору по [2] выбираем дымосос ДОД-43.
Технические характеристики дымососа:
Подача V=13351520 тыс.м³ч
Полное давление Р=35004500 Па
Частота вращения n=370 обмин
Значение КПД при работе с расчетной производительностью:
Мощность на валу дымососа
Мощность привода берется с запасом 3=105
Насосы тепловых электростанций как и другие типы машин служащие для перемещения среды и сообщения ей энергии характеризуются параметрами:
- объемной производительностью Q м³с
- давлением на стороне нагнетания рн Па
- плотностью перемещаемой среды r кгм³
8.1 Выбор питательных насосов.
На блоке 520 МВт устанавливают по 2 насоса с турбоприводом на 50% подачи каждый. Для блочной электростанции производительность насосов определяется максимальным расходом питательной воды на котел с запасом не менее 5%.
В этом случае объемная производительность такова [1]:
Давление нагнетания питательных насосов определяется в соответствии с рекомендациями [1]. Для прямоточного котла:
- давление пара на выходе из котла значение взято из расчета тепловой схемы
- суммарное гидравлическое сопротивление [1] учитывающее гидравлическое сопротивление прямоточного котла сопротивление регулирующего клапана питания котла сопротивление группы ПВД и трубопроводов питательного тракта.
Значение геодезического напора оцениваем по литературе [1].
- высота подъема воды от оси насоса до верхнего коллектора испарительного контура котла
ρ=840087 м³кг – средняя плотность воды принятое по средним параметрам давления и температуры воды в нагнетательном тракте
Давление нагнетания:
Давление на всосе питательного насоса должно удовлетворять условию недопущения вскипания воды при попадании ее на быстровращающиеся лопасти колеса насоса (условие обеспечения бескавитационной работы). Так как в данной схеме предусмотрена установка быстроходных насосов то для обеспечения бескавитационной работы недостаточно подъема деаэратора на высоту 22-25 м. Для создания давления на всосе питательного насоса устанавливают предвключенные бустерные насосы. Для энергоблока 520 МВт бустерный насос является встроенным в главный питательный насос имея с ним общий привод от турбины через понижающий редуктор. С учетом рекомендаций [1] давление на всосе: рв=068 МПа.
р=рн-рв=2917-068=2849 МПа
Мощность потребляемая насосом:
По найденным характеристикам и учитывая что необходимо установить 2 ПН на 50% подачи каждый по [2] выбираем 2 питательных насоса типа ПН-950-350 с параметрами:
Частота вращения – 4600
Тип и мощность привода – ОК-18ПУ. Завод-изготовитель ПО Пролетарский завод’ г. Санкт – Петербург.
8.2 Выбор конденсатных насосов.
Конденсатные насосы представляют особую группу энергетических насосов работающих с минимальным кавитационным запасом. Они обладают более низкой экономичностью большей металлоемкостью и более высокой стоимость по сравнению с другими насосами на аналогичные подачи и напоры. Поэтому по возможности число насосов должно быть минимальным.
Для блока с прямоточным котлом примем двухподъемную схему установки конденсатных насосов. При такой схеме КН разделяют на 2 ступени.
8.2а. Выбор конденсатных насосов I ступени.
Общая подача насосов принятая по расчету тепловой схемы - Dкн=25346 кгс ( с учетом добавочной воды)
Объемная производительность конденсатных насосов I ступени(подача):
Q=Dкнρ=25346996=025 м³с=9161 м³ч
Рбоу=06 МПа - гидравлическое сопротивление БОУ [1]
Ртр=01 МПа - сопротивление участка трубопроводов от КНI до БОУ [1]
Рпод=015 МПа – величина давления необходимого подпора на входе в КНII
Давление перед КНI должно быть достаточным для предотвращения кавитации
Рк=00033 МПа давление пара в конденсаторе взятое из расчета тепловой схемы
Р =003 МПа необходимый напор для предотвращения кавитации [1]
Напор конденсатных насосов:
РкнI=Рн-Рв=085-00333=0817 МПа
Напор выраженный в метрах столба перемещаемой жидкости
По найденным характеристикам выбираем 3 насоса по 50% производительности каждый (2 рабочих и 1 резервный) типа КсВ500-85
частота вращения – 1000 обмин
Допустимый кавитационный запас – 16 м
8.2б. Выбор конденсатного насоса II ступени.
Определим параметры КН II.
Объемная производительность конденсатных насосов II ступени(подача):
Q=Dкнρ=25346996=025 м³с=9161 м³ч
Рд=069 МПа - давление в деаэраторе из расчета тепловой схемы
Нд=23 м – высота установки деаэратора относительно оси насоса [1]
Суммарное сопротивление тракта:
Рпнд=035МПа - суммарное сопротивление всех ПНД [1]
Ррпк=004 МПа - сопротивление регулятора питания конденсата [1]
Ртр=01 МПа - суммарное гидравлическое сопротивление трубопроводов
PОЭ=006 МПа – сопротивление охладителя пара эжекторов
Давление перед КН II принимаем равным давлению на которое рассчитана БОУ – блочная обессоливающая установка т.е. не более 08 МПа
Напор выраженный в метрах столба перемещаемой жидкости:
Частота вращения – 1500 обмин
9. Выбор регенеративных подогревателей.
В регенеративных подогревателях осуществляется подогрев питательной воды и конденсата паром отбираемым из отборов турбины. Различают регенеративные подогреватели высокого и низкого давления.
9.1 Выбор подогревателей низкого давления.
Исходные данные берем из расчета тепловой схемы.
Для примера подробно рассмотрим расчет ПНД6. Остальные подогреватели рассчитываются аналогично.
Принимаем коэффициент теплопередачи по лит[3]:
Из расчета тепловой схемы берем температуру насыщения во втором подогревателе:
Определим температурный напор:
Площадь поверхности теплообмена:
Расчетный тепловой поток:
По литературе [2] выбираем тип теплообменника: ПН-1100-23-5-IIIнж.
Сводим данные в таблицу.
Для трех подогревателей низкого давления выбираем тип теплообменника ПН-1100-23-5-IIIнж.
Технические характеристики данного теплообменника:
Площадь поверхности: F=1165 м²
Номинальный массовый расход: D=3361 кгс
Расчетный тепловой поток: Q=435 МВт
Максимальная температура: tmax=350 ºС
Габаритные размеры: H=7750 м
Гидравлическое сопротивление при номинальном расходе воды: Pг=005Мпа
9.2 Выбор подогревателей высокого давления.
ПВД предназначены для регенеративного подогрева питательной воды за счет охлаждения и конденсации пара. Все три подогревателя поверхностного типа. Для более полного использования теплоты подводимого пара предусматриваются специальные поверхности нагрева для охлаждения пара до параметров близких к параметрам насыщения – охладители пара и для охлаждения конденсата пара – охладители конденсата.
Исходные данные для выбора ПВД берем из расчета тепловой схемы.
Выберем подогреватель на примере ПВД 3 остальные подогреватели выбираются аналогично.
При выборе ПВД исходными данными являются :
Gпв = 42781 кгс - расход питательной воды
Dп = 1812 кгс - расход пара на подогреватель
Dдр = D1 + D2 = 6396 кгс - расход дренажа из верхнего подогревателя
hдр2 = 89308 кДжкг – энтальпия дренажа верхнего подогревателя
hдр3 = 75928 кДжкг – энтальпия дренажа из ПВД 3
tдр3 = 17904 0C – температура дренажа за подогревателем
hвх = 6929 кДжкг – энтальпия воды на входе в подогреватель
h н = 85384 кДжкг– энтальпия воды на линии насыщения в подогревателе
tп3 = 20032 0C – температура насыщения греющего пара
Рпв = 315 МПа – давление питательной воды на входе в ПВД 3
k = 3 кДжм2К – коэффициент теплопередачи
=5 0C – недогрев воды до температуры насыщения после СП
ОД = 0985 – КПД охладителя дренажа
Рис. 3.9.2 Принципиальная схема СП и ОД для нахождения
площади поверхности собственно подогревателя
Определим параметры воды на выходе из охладителя дренажа для этого составим уравнение теплового баланса для ОД:
h``пкп = hн = 85384 кДжкг – энтальпия конденсата греющего пара на выходе из конвективной поверхности отсюда получаем:
По HS диаграмме по Рпв и находим t``вод = 17634 °С
Найдем параметры воды на входе в собственно подогреватель для этого составим уравнение теплового баланса для точки смешения за охладителем дренажа:
В данном уравнении расход основного конденсата сокращается в итоге получим:
По HS диаграмме по Рпв и находим t`всп = 16525 °С
Температура питательной воды на выходе из собственно подогревателя найдем с учетом недогрева:
t``всп = tн – = 20032 – 5 = 19532 °С
По HS диаграмме по Рпв и находим h``всп = 84556 °С
Количество теплоты передаваемой в собственно подогревателе:
Температурный напор в собственно подогревателе:
Площадь поверхности собственно подогревателя:
Тепловой поток для всего подогревателя:
Аналогично для ПВД 2 и ПВД 1 производим расчёт полученные результаты т.е. расчет площади теплообмена разности энтальпий среднелогарифмической температуры теплового потока заносим в таблицу.
По литературе [2] выбираем:
Тип подогревателя ПВД3 – ПВ-1800-380-45.
Его технические характеристики:
Полная площадь поверхности теплообмена –1890 м²
Площадь зоны ОП – нет
Площадь зоны ОК – 1260 м²
Номинальный расход воды – 4722 кгс
Максимальная температура – 300 0С
Тип подогревателя ПВД2 – ПВ-1800-380-45.
Тип подогревателя ПВД1 – ПВ-1700-380-58.
Полная площадь поверхности теплообмена –1678 м²
Площадь зоны ОП – 1340 м²
Площадь зоны ОК – 2010 м²
Номинальный расход воды – 2861 кгс
Максимальная температура – 310 0С
10. Выбор деаэратора.
Деаэраторная колонка и деаэраторный бак рассматриваются отдельно. По Рд=069 МПа и Dпв=42781 кгс выбираем деаэратор ДП -500-1 [1]
10.1 Выбор деаэрационного бака.
По полученным данным выбираем тип бака - БДП-100-1
Технические характеристики бака БДП-100-1:
Типоразмер устанавливаемых колонок – КДП-1000(КДП-500)
Объём бака – 113(118) м3
Максимальная длина – 13500 мм
Все детали колонок и баков изготавливаются из углеродистой стали за исключением дырчатых листов изготавливаемых из стали 08Х18Н10Т.
10.2 Выбор деаэрационной колонки.
В технической характеристике деаэрационного бака указывается типоразмер устанавливаемых колонок.
Типоразмер выбранной мною колонки - КДП-500
В типоразмере выбранного мною бака(БДП-100-1) последняя цифра – это количество колонок устанавливаемых на бак. В моём случае на бак ставится одна колонка.
Технические характеристики колонки КДП-500:
Номинальная производительность – 138.9 кгс
Рабочее давление – 0.59; 069 МПа
Давление допустимое при работе предохранительных клапанов – 085 МПа
Пробное гидравлическое давление – 10 МПа
Рабочая температура – 15808;164.17 0С
Диаметр колонки – 2032 мм
Высота колонки – 3625 мм
Масса колонки заполненной водой – 3.9 т.
ПВ-1700-380-58(РАМОР).dwg
К предохранительным клапанам
Вход воздуха из ПВД высшей ступени
Вход конденсата из ПВД высшей ступени
К водоуказательному прибору
Отвод неконденсирующихся газов
Выход питательной воды из дополнительного ОП
Вход питательной воды в дополнительный ОП
Выход конденсата греющего пара
Выход питательной воды
Вход питательной воды
Характеристика присоединения ПВД
МЭИ.022.1005.01.02.02.0020020386
Развернутая тепловая схема Рамор.dwg

Тепловая схема блока 520 МВт
Условное обозначение
Измерительная диафрамма
Задвижка с электроприводом
Химобессоленная вода
Конденсатный насос I ступени
МЭИ кафедра ТЭС гр. ТФ-2-02
МЭИ.022.1005.01.02.02.0020020386
Конденсатный насос II ступени
Деаэраторная колонка
ПВ-1700-380-58 Разрезы(РАМОР).dwg

Приварка спиралей к
коллекторным трубам.
Зона охлаж- дения кон- денсата
Схема движения воды в трубной системе
Зона конденсации пара
В линию перед котлом
Зона охлаж- дения пара
МЭИ.022.1005.01.02.02.0020020386
Спец Вопрос (РАМОР).dwg

Схема 1: Потоки монтажа оборудования для ГРЭС 4000МВт
Схемы и графики поточного монтажа
Продолжительность монтажа
Схема 2: График поточного монтажа энергоблоков 500МВт
МЭИ.022.1005.01.02.02.0020020386
Прнинципиальная тепл.сх. 520МВт(РАМОР).dwg

Сводная таблица(Рамор).doc
Вода за подогревателем
9.Сводная таблица результатов
Бакалавр (Рамор).doc
Проектный расчет принципиальной тепловой схемы энергоблока .стр.9
1.Построение процесса расширения пара в турбине стр.9
2.Определение параметров пара и воды в группе ПВД .стр.10
2.1.Первая ступень ПВД (П1) ..стр.10
2.2.Вторая ступень ПВД (П2) ..стр.10
2.3.Третья ступень ПВД (П3) ..стр.11
3.Определение дренажей группы ПВД ..стр.12
4.Определение параметров пара воды и дренажей группы ПНД стр.13
4.1.Подогреватель П8 (поверхностного типа) ..стр.13
4.2.Подогреватель П7 (поверхностного типа) ..стр.14
4.3.Подогреватель П6 (поверхностного типа) ..стр.14
4.4.Подогреватель П5 (поверхностного типа) ..стр.15
4.5.Подогреватель П4 (деаэратор) ..стр.15
5.Решение уравнений теплового баланса теплообменников определение
расхода пара на каждый теплообменник и в конденсатор ..стр.16
5.1.Подогреватель П1 стр.16
5.2.Подогреватель П2 стр.16
5.3.Подогреватель П3 стр.17
5.4.Отбор на приводную турбину .стр.17
5.5.Деаэратор питательной воды(П4) ..стр.17
5.6.Подогреватель П5 стр.18
5.7.Подогреватель П6 стр.18
5.8.Подогреватели П7 и П8 .стр.18
6.Контроль материального баланса пара и конденсата стр.19
7.Энергетическое уравнение и определение расходов пара и воды стр.20
8.Энергетические показатели энергоблока ..стр.21
9.Сводная таблица результатов .стр.24
10.Принципиальная тепловая схема энергоблока 520МВт ..стр.25
11.Процесс расширения пара ..стр.26
Выбор основного и вспомогательного оборудования стр.27
1.Основные характеристики турбины К-520-235 .. стр.27
2.Выбор парового котла стр.27
3.Выбор схемы пылеприготовления .стр.29
4. Выбор оборудования пылеприготовления стр.30
4.1.Выбор типа мельниц стр.30
4.2.Выбор числа и производительности мельницы стр.30
5. Выбор тягодутьевых машин стр.31
6. Выбор дутьевых вентиляторов ..стр.32
7.Выбор дымососов стр.33
8.Выбор насосов .стр.34
8.1.Выбор питательных насосов .стр.34
8.2.Выбор конденсатных насосов стр.36
8.2а.Выбор конденсатных насосов I ступени стр.36
8.2б.Выбор конденсатного насоса II ступени стр.37
9.Выбор регенеративных подогревателей стр.38
9.1.Выбор подогревателей низкого давления ..стр.38
9.2.Выбор подогревателей высокого давления стр.40
10.Выбор деаэратора .стр.43
10.1.Выбор деаэрационного бака стр.43
10.2.Выбор деаэрационной колонки ..стр.43
Конструкторский расчёт подогревателя высокого давления подключённому
к первому отбору турбины стр.44
1.Описание конструкции подогревателя высокого давления стр.44
2.Тепловой и конструктивный расчет подогревателя высокого давления типа
ПВ со встроенными охладителями пара и дренажа .стр.47
2.1.Исходные данные для теплового расчета ПВД1 стр.47
2.2.Определение тепловых нагрузок .стр.48
2.3.Расчет собственно подогревателя стр.49
2.4.Расчет охладителя пара .стр.52
2.5.Расчет охладителя дренажа стр.55
3.Гидравлический расчет стр.58
3.1.Расчёт потери давления для собственно подогревателя .стр.58
3.2.Расчёт потери давления для охладителя пара ..стр.59
3.3.Расчёт потери давления для охладителя конденсата стр.59
4.Расчет на прочность элементов подогревателя стр.60
4.1.Расчет толщины стенки подогревателя .стр.60
Организация монтажа энергоблоков мощностью 500 МВт поточным методом ..стр.62
1.Основные принципы организации поточного монтажа оборудования ..стр.62
2.Характеристики поточного метода монтажа стр.63
3.График движения рабочей силы .стр.65
4.Организация поточного монтажа на примере ГРЭС мощностью 4000МВт
(8 блоков по 500МВт) стр.66
4.1.Потоки монтажа оборудования для ГРЭС 4000МВт стр.68
4.2.График поточного монтажа энергоблоков 500МВт .стр.69
Список используемой литературы стр.72
Работа включает в себя:
- 70 листов расчетно-пояснительной записки
В данной бакалаврской работе была рассчитана принципиальная тепловая схема блока мощностью 520 МВт с турбиной К-520-235 ЛМЗ. В качестве специального задания было задано подробное описание организации монтажа оборудования поточным методом энергоблоков мощностью 500МВт.
Бакалаврская работа включает в себя следующие основные расчеты:
- Расчет принципиальной тепловой схемы блока К-520-235
- Расчет показателей тепловой экономичности
- Выбор вспомогательного оборудования
- Расчет подогревателя высокого давления
- Монтаж оборудования поточным методом энергоблоков мощностью 500МВт.
Энергетика является важнейшей и необходимой отраслью экономики России. Производство электроэнергии является одним из главных показателей экономического уровня страны и отражает общее состояние производственных сил.
Но помимо этого необходимо выпускать высококвалифицированный персонал подготовленный как теоретически так и практически.
Цель данной выпускной работы – этап в обучении проффесиональных энергетиков. Совместив в себе такие специальные предметы как «тепловые и атомные станции» «тепломеханическое оборудование» эта работа затрагивает и такие базовые знания как термодинамика и тепломассообмен. Таким образом бакалаврская работа вмещает в себя все знания накопленные за 4 года обучения и показывает мой уровень подготовленности.
Описание тепловой схемы энергоблока электрической мощностью 520 МВт.
Конденсационный энергоблок 520 МВт предназначен преимущественно для установки на крупных ГРЭС работающих на твердом топливе.
Паровой котел спроектированный мною выполнен по Т-образной компоновке с 24 вихревыми горелками при шести молотковых мельницах производительностью 44 тч. Номинальная производительность котла 41943 кгс (150995 тч) давление и температура перегретого пара за котлом 235 МПа и 5600С.
Конденсационная паровая турбина К-520-235 одновальная работает с электрогенератором ТВВ-520. Турбина состоит из ЦВД ЦСД и двух двухпоточных ЦНД. Расход свежего пара на турбину 41943 кгс (150995 тч); параметры свежего пара 235 МПа 5600С.
Конденсатор турбоустановки типа К-11520 приварен к 4 выхлопам ЦНД. Его паровое пространство разделено перегородкой. Что позволяет осуществить двухступенчатую конденсацию пара. Потери рабочего тела основного энергоблока восполняются добавкой обессоленной воды из химической водоочистки.
Вакуум в конденсаторе поддерживается изменением числа включенных насосов а также поворотом рабочих лопаток насосов.
Турбина имеет 8 нерегулируемых отборов пара для регенеративного подогрева питательной воды. Основной конденсат после КН I ступени проходит 100% очистку в БОУ и направляется в конденсатные насосы II ступени. Затем конденсатные насосы II ступени подают конденсат в поверхностные ПНД 8 ПНД7 ПНД6 ПНД5 и деаэратор.
Деаэратор питательной воды ДП-500-1. При нагрузках близких к номинальной деаэратор работает при постоянном давлении 069 МПа.
Питательная установка энергоблока состоит из 2 питательных турбонасосов каждый из которых рассчитан на 50% подачи по воде.
Общий турбинный привод бустерного и питательного насосов от конденсационной турбины имеет переменную частоту вращения для изменения производительности установки по питательной воде.
Группа ПВД выполнена в одну нитку из трех последовательно включенных подогревателей типа ПВ-1800-380-45 без охладителя пара и ПВ-1700-380-58 с пароохладителем и охладителем дренажа. Конденсат греющего пара каскадно сливается в деаэратор. Уровень этого конденсата в каждом ПВД поддерживается регулятором уровня. Воздействующим на клапан дренажной линии. ПВД снабжены общим байпасом защиты и обводной линией «холодного» питания котла при отключении ПВД.
Проектный расчет принципиальной тепловой схемы энергоблока.
1. Построение процесса расширения пара в турбине.
Р0=235 МПа t0=560 0C h0= 33878 кДжкг S0= 62645 кДж(кгК)
Р2=01Рпп+ Рпп=01358+358=3938 МПа S2= S0 t2а=27894 0C
H0ЦВД= h0- h2а=33878 – 29022 = 4856 кДжкг
HiЦВД=oiЦВДH0ЦВД=0854856 = 41276 кДжкг
h2= h0- HiЦВД= 33878 – 41276 = 297504 кДжкг
По Р2 и h2 по таблице воды и водяного пара находим t2 :
Рпп=358 МПа tпп=560 0C hпп= 35869 кДжкг Sпп=73176 кДж(кгК)
Точка выхода пара из ЦСД:
РкЦСД=005Рпп=005358=0179 МПа
oiЦСД=087 SкЦСДа= 73176 кДж(кгК) hаЦСД=27633кДжкг
H0ЦСД=hпп-hаЦСД= 35869 – 27633= 8236 кДжкг
HiЦСД=oiЦСДH0ЦСД=0878236 = 716532 кДжкг
hкЦСД= hпп- HiЦСД= 35869 – 716532 = 2870368 кДжкг
SкЦСД=75579 кДж(кгК) tкЦСД=1993 0C
Рк=33 кПа tк=25677 0C
Т.к. Sка = SкЦСД находим hка опускаясь из точки кЦСД по линии S=const до пересечения с давлением Рк
hка= 2252 кДжкг Sка= 75579 кДж(кгК)
oiЦНД=081 H0ЦНД= hкЦСД-hка= 2870368 – 2252 = 618368 кДжкг
HiЦНД=оiЦНДH0ЦНД=081618368 = 50088 кДжкг
hk= hкЦСД- HiЦНД= 2870368 – 50088 = 236949 кДжкг
Точка К: (по давлению в конденсаторе находим энтропию и температуру конденсата):
Рк=33 кПа ts=25677 0C h к= 10767 кДжкг
2. Определение параметров пара и воды в группе ПВД.
2.1 Первая ступень ПВД (П1):
Известно что температура воды за подогревателем высокого давления № 1(П1) равна температуре питательной воды: tв1=tпв=268 0C а давление за П1 будет равно:
Потеря давления в каждом ПВД составляет : Рпвд =05 МПа
Потеря давления в РПК: Ррпк =5 МПа
Потеря давления в трубопроводах котла: Ррпк =15 МПа
Рв1 = 235 + 5 + 15 Рв1 =30 МПа
По температуре tв1 и давлению Рв1 по таблице теплофизических свойств воды и водяного пара находим: h в1 = 1172.1 кДжкг
Температура питательной воды за П1 будет ниже температуры насыщения в П1 на величину недогрева =15 0C. Таким образом температура насыщения в П1 будет равна: tн1=tпв + =268+15=2695 0C. Зная температуру насыщения греющего пара найдем давление греющего пара:
Энтальпия греющего пара:
Находим параметры (давление) пара в отборе турбины приняв потерю давления в паропроводе 5%:
Р1=105Рн1=105546 = 5733 МПа
По диаграмме расширении пара (h-s диаграмма) находим температуру и энтальпию пара в отборе турбины:
t1=35475 0C h1=3064 кДжкг
2.2. Вторая ступень ПВД (П2):
Греющий пар для П2 отбирается из «холодной» нитки промежуточного перегрева пара. Давление насыщения пара в П2 будет меньше давления пара на выходе из ЦВД на 5% (за счет сопротивления паропровода).
Давление насыщения пара в П2:
Рн2=Р2095=3938095 = 374 МПа
По давлению насыщения Рн2 находим температуру и энтальпию пара в П2:
tн2=2464 0C hн2 = 10682 кДжкг
Температура воды за П2 будет ниже чем tн2 на величину недогрева =15 0C:
tв2=tн2-=2464-15=2449 0C
Давление за подогревателем принимается с учётом потерь в подогревателе ПВД 3:
Рв2 = Р0 + Ррпк + Ртр + Рпвд
По давлению Рв2 и температуре tв2 по таблице теплофизических свойств воды и водяного пара находим энтальпию воды за П2:
2.3. Третья ступень ПВД (П3):
Определим энтальпию питательной воды за ПН. Давление воды на входе в питательный насос равно давлению на выходе из деаэратора а т.к. вода на входе в ПН находится в состоянии насыщения то температуру воды на входе в ПН ищем по давлению насыщения воды которая нам известна:
По Рвдпв = 0.69 МПа и tвдпв = 164 оС находим удельный объём питательной воды на входе в насос до пн = 0001107 м3кг
По Рпн = 315 МПа и tпн = 164 оС находим удельный объём питательной воды после питательного насоса после пн = 0001085 м3кг
Рд=069 МПа – давление в деаэраторе с помощью которого по таблице теплофизических свойств воды и водяного пара находим энтальпию насыщения в деаэраторе: hд =6929 кДжкг
– средний удельный объем воды в ПН
ПН=085 – КПД питательного насоса
Нагрев воды в питательном насосе:
tпн=( ср (Рпн – Рд))*1000 ПН=(0001096(315-069))*1000085=3976 кДжкг
Энтальпия питательной воды за ПН:
hв.ПН=tпн+hд где hд – энтальпия воды в деаэраторе при P = 0.69 МПа и t =164 0C
hв.ПН = 3976 + 6929 = 73266 кДжкг
По давлению Рпн и энтальпии hв.ПН по таблице теплофизических свойств воды и водяного пара находим более точную температуру воды на выходе из ПН:
Для нахождения параметров за П3 составим систему уравнений.
Обеспечение подогрева воды паром из «холодной нитки» энергетически более выгодно чем из «горячей нитки» тогда:
+ 3= hв2- hвПН=1065 – 73266 = 33234 кДжкг
Решая эту систему получим:
= 20452 кДжкг – нагрев воды в П2
= 12782 кДжкг – нагрев воды в П3
Параметры питательной воды за П3:
hв3= hвПН + 3=73266 + 12782 = 86048 кДжкг
Рв3= Рв2 + Рпвд = 31 МПа
По Рв3 и tв3 по таблице теплофизических свойств воды и водяного пара находим температуру воды за П3:
Температура воды за П3 будет ниже чем tн3 на величину недогрева =15 0C:
Температура пара в П3:
tн3=tв3 + = 19882 + 15 = 20032 0C
Давление греющего пара также ищем по таблице теплофизических свойств воды и водяного пара по tн3 :
Рн3= 156 МПа а по Рн3 и tн3 находим энтальпию пара в П3:
Параметры пара в отборе:
Р3=105Рн3=105156 = 164 МПа - с учетом потерь давления в паропроводе (5%)
t3=44503 0C - из h-s диаграммы по известному давлению
3. Определение дренажей группы ПВД.
од=10 0C - температурный напор на холодном конце в охладителе дренажа
tдр3=tвПН+ од=16904+10 = 17904 0C
tдр2=tв3+ од=19882 + 10 = 20882 0C
tдр1=tв2+ од=2449 + 10 = 2549 0C
По известным температуре и давлениям в подогревателях определяем энтальпии дренажей:
4. Определение параметров пара воды и дренажей группы ПНД.
Рассмотрим распределение регенеративного подогрева группы ПНД.
Выберем способ распределения подогрева в ПНД: способ равномерного подогрева по ступеням.Для подогревателей смешивающего типа недогрев равен 00C. При расчете ПНД учитывалось то что деаэратор входит в число ПНД.
Недогрев в ПНД поверхностного типа принимаем равным 450C
Давление создаваемое конденсатным насосом можно принять равным давлению в деаэраторе с учетом потерь при сопротивлении конденсата в самих ПНД и давления необходимого для поднятия конденсата на нивелирный уровень Д.
Напор конденсатного насоса второй ступени можно рассчитать следующим образом:
Ркн2=Рд + 4·Рсопр_пнд + Рнив =069+4·01+022= 131 МПа
Параметры конденсата на выходе из конденсатора:
tк=25677 0CРк=00033 МПаhк=10767 кДжкг
Т.к. деаэратор можно принять за подогреватель смешивающего типа значит hД = hвД т.к. в подогревателях смешивающего типа недогрев не учитывается.
Подогрев приходящийся на каждую ступень ПНД:
пнд=(hд-h`к)5=(6929-10767)5=11704 кДжкг
4.1. Подогреватель П8 (поверхностного типа).
Энтальпия конденсата за П8:
hв8=h`к+ пнд=10767+11704 = 22471 кДжкг
tв8=5343 0C - по таблице теплофизических свойств воды и водяного пара по энтальпии воды и давлению Ркн2 минус Рсопр_пнд находим давление воды за П8:
Параметры воды за подогревателем поверхностного типа принимаются равными параметрам пара в подогревателе с учётом недогрева в ПНД:
Температура греющего пара в П8:
tН8=5343 + 45 = 5793 0C
По tН8 по таблице воды и водяного пара находим давление и энтальпию пара в П8:
Рн8 =0018 МПа hн8= 2425 кДжкг
Р8=105Рн8=1050018=00189 МПа
t8=5884 0C - из h-s диаграммы по известному давлению
4.2. Подогреватель П7 (поверхностного типа).
Энтальпия конденсата за П7 равна:
hв7=hв8+ пнд= 22471+11704 = 34175 кДжкг
tв7= 8142 0C - по таблице теплофизических свойств воды и водяного пара по энтальпии воды и давлению Ркн2 минус 2·Pсопр_пнд находим давление воды за П7:
Параметры в подогревателе:
tн7 = tв7 + 450C = 8142+45 =8592 0C
Рн7=0059 МПа hн7 =3598 кДжкг
Р7=105Рн7=1050059 = 0062 МПа
t7=11571 0C - из h-s диаграммы по известному давлению
4.3. Подогреватель П6 (поверхностного типа).
Рв6=Ркн3-3·Рсопр_пнд=131-3·01=101 МПа
hв6=hв7+ пнд= 34175 +11704 = 45879 кДжкг
По hв6 и Рв6 по таблице воды и водяного пара находим:
Недогрев в ПНД принимаем: =45 0C
Температура греющего пара в П6:
tн6=tв6+=10924+45=11374 0C
По таблице теплофизических свойств воды и водяного пара по известной температуре находим давление и энтальпию пара в ПНД6:
Рн6=016 МПаhн6=47721 кДжкг
Р6=105Рн6=105016=0168 МПа - с учетом потерь давления в паропроводе (5%)
t6=19186 0C - из h-s диаграммы по известному давлению
4.4. Подогреватель П5 (поверхностного типа).
hв5=hв6+ пнд= 45879 +11704 = 57583 кДжкг
По таблице теплофизических свойств воды и водяного пара по энтальпии воды и давлению Рв5 =091 МПа находим температуру воды за П5:
Температура греющего пара в П5:
tн5=tв5+=13679+45=14129 0C
По таблице теплофизических свойств воды и водяного пара по известной температуре находим давление и энтальпию пара в ПНД5 :
Рн5=0375 МПаhн5=59474 кДжкг
Р5=105Рн5=1050375=0394 МПа
t5=27889 0C - из h-s диаграммы по известному давлению
По t находим остальные параметры на линии насыщения:
4.5. Подогреватель П4 (деаэратор).
Рн4 находим по таблице воды и водяного пара по известной температуре насыщения tн4
Р4 = 105·069 = 0724 МПа
t4=34635 0C - из h-s диаграммы по известному
5. Решение уравнений теплового баланса теплообменников определение расхода пара на каждый теплообменник и в конденсатор.
α0=1 - доля расхода в ЦВД турбины
αут=002 - доля утечек пара
αдв=αут=002 - доля добавочной воды для восполнения потерь утечек
5.1. Подогреватель П1.
aп.в = aо + aут = 1 + 0.02 = 1.02
a1(h1 - hдр1) = aп.в(hв1 – hв2) Примем hп = 0.985
5.2. Подогреватель П2.
a2(h2 - hдр2) + a1(hдр1 - hдр2) = aпв(hв2 – hв3)
5.3. Подогреватель П3.
a3h3h+ (a1+a2) hдр2h + aп.вhвпн = aп.вhв3 +(a1+a2+a3) hдр3h
a3 =aп.вhв3 – (a1+a2) hдр2h - aп.вhвпн + (a1+a2) hдр3h (h3 - hдр3 ) h
5.4.Отбор на приводную турбину.
Здесь hнi = 0.85 hмтп = 0.99
Теплоперепад на приводной турбине Hiтп = h3 - hктп
Потери давления пара при дросселировании в арматуре подвода пара к приводной турбине примем равным 5 % те давление пара в голову приводной турбины: Ротп = 0.95 Р3 = 0.95164 = 1558 МПа.
Примем hоiтп = 0.84 тогда внутренний теплоперепад Hiтп = Hотп hоiтп = (h3 – hкттп) hоiтп hкттп определим по h s – диаграмме опускаясь от точки с параметрами Ротп hотп = h3 по линии S = const до пересечения с давлением Рктп = 4 кПа hкттп = 2232 кДжкг
Hiтп = (3352 – 2232)0.84 = 9408 кДжкг
По Ротп и h3 по таблице воды и водяного пара находим tотп :
Действительное значение энтальпии hктп турбопривода:
hктп = h3 - Hiтп = 3352 – 9408 = 24112 кДжкг
По Рктп и hктп по таблице воды и водяного пара находим tктп :
5.5. Деаэратор питательной воды(П4).
Уравнение материального баланса:
αпв=( α1+ α2+ α3)+ αд+ αок
Уравнение теплового баланса:
αпвh`д= ( α1+ α2+ α3)hдр3 + αдh4+ αокhок
Pок = Pв5 – Pнив = 091-022 = 069 МПа
tок = tв5 = 136.79 0C
По таблице воды и водяного пара по известным нам Pок и tок находим hок
Решая систему из двух уравнений находим долю расхода пара на деаэратор:
αок = (αпвh`д - ( α1+ α2+ α3)hдр3 - αдh4) hок
αд = 08243 – (αпвh`д + ( α1+ α2+ α3)hдр3 + αдh4) hок
αд = (08243· hок - αпвh`д + ( α1+ α2+ α3)hдр3) (hок - h4 )
αд = (08243·57567-102·6929+(00567+00958+00432)·75928)(57567-3156)
Доля расхода основного конденсата:
5.6. Подогреватель П5.
α5(h5-hдр5) = αок(hв5-hв6)
5.7. Подогреватель П6.
[α6(h6-hдр6)+ α5(hдр5-hдр6)]= αок(hв6-hв7)
5.8. Подогреватели П7 и П8.
Уравнение теплового баланса подогревателя:
Уравнение теплового баланса точки смешения:
Уравнение материального баланса точки смешения:
Решая систему из четырёх уравнений находим
6. Контроль материального баланса пара и конденсата.
αк=αок- α5-α6-α7- α8=07913-00389-00426-0035-0027= 06478
Пропуск пара в конденсатор:
αвх-к=α0- α1- α2- α3-αд-αтп - α5-α6-α7- α8 =1-00567-00958-00432-0033-00435-00389-00426-0035-0027=05843
Поток конденсата из конденсатора:
αвых_к=αвх_к+αд.в + αтп =05843+002+00435= 06478
Погрешность сведения материального баланса:
Доля пропуска пара через отсек a
Теплоперепад в отсеке H кДжкг
Внутренняя работа пара в отсеке aH кДжкг
h0-h1=33878-3064=3238
h1-h2=3064-297504=8896
-a1-a2=1-00567-00958= 08475
hпп-h3=35869-3352=2349
-a1-a2-a3-aтп=1-00567-00958-00432-00435= 07608
-a1-a2-a3-aтп-aд=1-00567-00958-00432-00435-0033= 07278
-a1-a2-a3-aтп-aд-a5=1-00567-00958-00432-00435-0033-00389= 06889
-a1-a2-a3-aтп-aд-a5-a6=1-00567-00958-00432-00435-0033-00389-00426= 06463
-a1-a2-a3-aтп-aд-a5-a6-a7=1-00567-00958-00432-00435-0035-00389-00426-0035= 06113
-a1-a2-a3-aтп-aд-a5-a6-a7-a8=1-00567-00958-00432-00435-0033-00389-00426-0035-0027= 05843
h8-hк=2560-236949=19051
7. Энергетическое уравнение и определение расходов пара и воды.
Таблица для расчета приведенного теплоперепада Hпр:
Обозначим сумму αiHij= 126493 кДжкг через: S αiHij
Расход пара на турбину:
Удельный расход пара на турбину:
8. Энергетические показатели энергоблока.
Полный расход теплоты на турбоустановку :
hпв=hв1=1172.1 кДжкг
Qту=D0(h0-hпв)+Dпп(hпп-h2)=
=419433600(33878-11721)+355463600(35869-297504)=4128 ГДжч
Удельный расход теплоты турбоустановки на выработку электроэнергии:
КПД турбоустановки по выработке электроэнергии:
Тепловая нагрузка парового котла:
hпе=33878 кДжкг- при давлении и температуре свежего пара: Pпе=235 МПа tпе=560
hп.в_п.к=hпв=11721 кДжкг
hп.п_0.п.к=297504 кДжкг - при давлении и температуре пара перед пп: Pпе=3938 МПа tпе=30405
hп.п_п.к=35869 кДжкг - при давлении и температуре пара после пп: Pпе=358 МПа tпе=560
Qпк= Dпк(hпе-hпв_пк)+Dпп(hпп_пк-hпп_0.пк) =
=427813600 (33878-11721)+ 355463600(35869-297504) =4195 ГДжч
КПД транспорта теплоты:
Количество теплоты топлива на паровой котел:
Задамся КПД парового котла
КПД энергоблока брутто:
КПД энергоблока нетто:
Удельный расход теплоты энергоблока нетто:
Часовые расходы условного и натурального топлива:
Удельный расход условного топлива нетто:
9. Сводная таблица результатов.
Выбор основного и вспомогательного оборудования.
Выбор основного и вспомогательного оборудования для энергоблока будем производить исходя из данных полученных при расчете тепловой схемы турбоустановки К-520-235 а также рекомендаций по выбору теплообменного оборудования для данной турбины по литературе [1] [2] [3]. Выбор оборудования должен обеспечивать надежную и экономичную работу турбоустановки в требуемом диапазоне нагрузок.
1. Основные характеристики турбины К-520-235.
Турбина спроектирована на начальные параметры пара 235 МПа 560 °С с промежуточным перегревом ее до 560 °С на давление в конденсаторе 33кПа и частоту вращения 50 с.
Пар из парогенератора по двум паропроводам подается к двум блокам стопорно-регулирующих клапанов установленным рядом с турбиной.
От регулирующих клапанов пар по 4 перепускным трубам поступает к штуцерам сопловых коробок ЦВД.
Цилиндр высокого давления – противоточной конструкции. Пройдя одновенечную регулирующую ступень и 5 ступеней левого потока расположенных во внутреннем корпусе поток пара поворачивает на 180° и проходи сначала по межкорпусному пространству а затем – через последние 6 ступеней ЦВД расположенных во внешнем корпусе.
Пар покидает ЦВД и по двум паропроводам направляется в котел на промежуточный перегрев. Из котла по двум паропроводам пар поступает к стопорным клапанам ЦСД.
Цилиндр среднего давления – двухпоточный. Пройдя 11 ступеней ЦСД пар по 4 патрубкам поступает в ЦНД.
Турбоустановка К-520-235 имеет 2 симметричных двухпоточных ЦНД. После ЦНД отработавший пар поступает в конденсатор где он конденсируется.
2 Выбор парового котла.
Тип парового котла определяется выбранным типом турбины а также видом топлива суммарной мощностью и режимом работы ТЭС.
Для данной принципиальной тепловой схемы КЭС с турбоустановкой типа К-520-235 мощностью 520МВт паропроизводительность котла работающего на каменном угле Кузнецкого месторождения составляет:
Поскольку начальное давление составляет p0=235 МПа то в данной тепловой схеме необходимо применение прямоточного котла.
Основные параметры пара и питательной воды необходимые для выбора котельного агрегата:
По данным параметрам по таблице1.1 литературы [1] выбираем тип котла.
За прототип берём котёл заводской маркировки П-57Р рассчитанного на параметры:
Основные характеристики парового котла П-57Р:
Котел П-57Р предназначен для работы на экибастузских каменных углях в блоке с турбиной мощностью 500 МВт.
Котел прямоточный на сверхкритические параметры пара с промперегревом однокорпусный выполнен по Т-образной компоновке с уравновешенной тягой и с твердым шлакоудалением.
Топочная камера – призматическая. Топочная камера оборудована 24 пылеугольными горелками расположенными встречно в два яруса на боковых стенах топки
Котел имеет две одинаковые конвективные шахты в которых по ходу газа расположены следующие поверхности нагрева: конвективного пароперегревателя высокого давления из плавниковых труб; конвективного пароперегревателя промперегрева второй ступени; два пакета конвективного промперегревателя первой ступени водяной экономайзер.
В горизонтальных газоходах имеется ширмовый пароперегреватель.
Техническое задание:
Т.к. некоторые из моих расчётных параметров() превышают те же параметры() котла заводской маркировки П-57Р то необходимо спроектировать прямоточный котёл на основе котла указанного выше.
Технические параметры требуемого котла:
КПД котла брутто – 90%
Котел маркировки П-57Р спроектирован для работы на Экибастусском угле а проектируемый мною котёл должен работать на Кузнецком угле.
Данный пылеугольный котел работает под разряжением. Тип воздухоподогревателя – трубчатый.КПД котла брутто – 90% аэродинамическое сопротивление газового и воздушного тракта:
Высота котла равная расстоянию от нулевой отметки до верхнего коллектора испарительного тракта прямоточного котла .
3. Выбор схемы пылеприготовления.
Выбор схемы пылеприготовления производим с помощью лит[1]. В данном случае применяется замкнутая система с прямым вдуванием. Отработавший после сушки топлива воздух вместе с угольной пылью и выделившимися водяными парами сбрасывается в топку.
Рис. 3.3. Схема пылеприготовления с прямым вдуванием пыли.
-бункер сырого угля 2- молотковая мельница с гравитационным сепаратором 3-горелки 4- короб горячего воздуха 5- воздухоподогреватель.
Из бункера сырого угля 1 топливо поступает в мельницу 2.Размолотое в мельнице топливо попадает в шахту которая является гравитационным сепаратором тонкая пыль через горелку 3 выбрасывается в топку потоком воздуха а крупные частицы угля возвращаются в мельницу. В схеме отсутствует пылевой бункер что упрощает и удешевляет установку.
4. Выбор оборудования пылеприготовления.
Качество угольной пыли характеризуется тонкостью помола и влажностью. Тонкость помола зависит от реакционной способности угля характеризуемой выходом летучих фракций . Важной характеристикой угля является размолоспособность. Для дальнейшего выбора оборудования выпишем из лит [1] основные характеристики топлива:
Тип топлива – Кузнецкий Т
Теоретические объемы
Рекомендуемый тип мельницы – ММТ
4.1 Выбор типа мельниц.
С учетом характеристик топлива выбираем мельницы типа ММТ.
Мельница состоит из стального корпуса и ротора с шарнирно укрепленными на нем билами. Уголь попадая на быстровращающиеся била размалываются и увлекаются из корпуса потоком воздуха.
4.2 Выбор числа и производительности мельницы.
Число мельниц установленных на котле зависит от его производительности и от типа мельниц. С учетом рекомендаций по выбору числа мельниц (лит. [2]) примем число мельниц z=6. Расчетная производительность одной мельницы определяется по известному из расчета тепловой схемы расходу топлива на котел и принятому числу мельниц.
Т.к. Z ≥ 5 то воспользуемся следующей формулой:
По справочнику [2] определяем типоразмер мельницы: 20002590750К600К
Технические характеристики мельницы:
Диаметр ротора D=2000 мм
Длина ротора L=2590 мм
Максимальная температура сушильного агента
Пересчет производительности с “характерного” вида топлива
5. Выбор тягодутьевых машин.
В данной схеме в качестве топлива используется Кузнецкий уголь котел работает под разряжением. На котле установлены дутьевые вентиляторы и дымососы.Котел имеет негазоплотное исполнение. Присосы воздуха по тракту котла оказывают большое влияние на работу тягодутьевых устройств увеличивая объем перекачиваемых газов что приводит к увеличению расхода энергии на собственные нужды и снижению экономичности работы котла.
Для дальнейших расчетов выпишем значения основных присосов воздуха при движении продуктов сгорания по тракту котла:
коэффициент избытка воздуха в топке – αт=12
присосы в топке αт=005
суммарные присосы воздуха в конвективных газоходах первичного и вторичного пароперегревателя αкп=012
присосы воздуха и протечки газов в воздухоподогревателе αвп=003
присосы в золоулавителях αзу=010
Расход топлива по которому выбираются дутьевые вентиляторы и дымососы определяются с учетом физической неполноты сгорания твердого топлива. Принимаем по [3] q4=2%. Тогда расход топлива:
6. Выбор дутьевых вентиляторов.
Дутьевой вентилятор подает холодный воздух в воздухоподогреватель забирая его из верхней части котельной.
Принимаем согласно [1] температуру холодного воздуха Производительность вентилятора определяется расходом воздуха необходимым для горения топлива с учетом коэффициента избытка воздуха в топке и присосов по тракту котла [1]:
Расчетная производительность вентилятора принимается с коэффициентом запаса [1]. Кроме того вводится поправка на барометрическое давление. Принимаем число вентиляторов z=4. Расчетная производительность одной машины:
Напор дутьевого вентилятора зависит от сопротивления воздушного тракта. Суммарное сопротивление тракта по [1]: . Расчетное значение напора принимается с коэффициентом запаса [1].
По найденным расчетным значениям производительности и напора определяем типоразмер дутьевого вентилятора. По[2] выбираем тип дутьевого вентилятора – ВДН-32Б.
Технические характеристики дутьевого вентилятора:
Подача V=475385 тыс.м³ч
Полное давление p=61004000 Па
Температура газа t=30°C
Частота вращения n=730590 обмин
Мощность на валу дутьевого вентилятора определяется по формуле:
Мощность привода берется с коэффициентом запаса необходимым для преодоления инерции при пуске вентилятора.
Производительность дымососа определяется объемными расходами газов уходящих из котла и воздуха присасываемого в тракт после котла в золоулавителях и газоходах. С учетом температуры газов перед дымососом объемная производительность машины по [1]
Объем уходящих газов равен сумме теоретического объема газов и объема присосов воздуха по тракту котла
Объем присосов за пределами котла
Определим температуру газов перед дымососом.
Т.к. величина суммарных присосов =013 ≥01 то температура газов перед дымососом определяется по формуле смешения:
Тогда производительность дымососа:
Принимаю по [1] число дымососов равное числу дутьевых вентиляторов z=4. Тогда расчетная производительность дымососа с учетом коэффициента запаса 1=11 (по [1]):
Напор дымососа принимаем по [1] -
С учетом коэффициента запаса 2=12 расчетный напор дымососа:
По оцененным выше производительности и напору по [2] выбираем дымосос ДОД-43.
Технические характеристики дымососа:
Подача V=13351520 тыс.м³ч
Полное давление Р=35004500 Па
Частота вращения n=370 обмин
Значение КПД при работе с расчетной производительностью:
Мощность на валу дымососа
Мощность привода берется с запасом 3=105
Насосы тепловых электростанций как и другие типы машин служащие для перемещения среды и сообщения ей энергии характеризуются параметрами:
- объемной производительностью Q м³с
- давлением на стороне нагнетания рн Па
- плотностью перемещаемой среды r кгм³
8.1 Выбор питательных насосов.
На блоке 520 МВт устанавливают по 2 насоса с турбоприводом на 50% подачи каждый. Для блочной электростанции производительность насосов определяется максимальным расходом питательной воды на котел с запасом не менее 5%.
В этом случае объемная производительность такова [1]:
Давление нагнетания питательных насосов определяется в соответствии с рекомендациями [1]. Для прямоточного котла:
- давление пара на выходе из котла значение взято из расчета тепловой схемы
- суммарное гидравлическое сопротивление [1] учитывающее гидравлическое сопротивление прямоточного котла сопротивление регулирующего клапана питания котла сопротивление группы ПВД и трубопроводов питательного тракта.
Значение геодезического напора оцениваем по литературе [1].
- высота подъема воды от оси насоса до верхнего коллектора испарительного контура котла
ρ=840087 м³кг – средняя плотность воды принятое по средним параметрам давления и температуры воды в нагнетательном тракте
Давление нагнетания:
Давление на всосе питательного насоса должно удовлетворять условию недопущения вскипания воды при попадании ее на быстровращающиеся лопасти колеса насоса (условие обеспечения бескавитационной работы). Так как в данной схеме предусмотрена установка быстроходных насосов то для обеспечения бескавитационной работы недостаточно подъема деаэратора на высоту 22-25 м. Для создания давления на всосе питательного насоса устанавливают предвключенные бустерные насосы. Для энергоблока 520 МВт бустерный насос является встроенным в главный питательный насос имея с ним общий привод от турбины через понижающий редуктор. С учетом рекомендаций [1] давление на всосе: рв=068 МПа.
р=рн-рв=2917-068=2849 МПа
Мощность потребляемая насосом:
По найденным характеристикам и учитывая что необходимо установить 2 ПН на 50% подачи каждый по [2] выбираем 2 питательных насоса типа ПН-950-350 с параметрами:
Частота вращения – 4600
Тип и мощность привода – ОК-18ПУ. Завод-изготовитель ПО Пролетарский завод’ г. Санкт – Петербург.
8.2 Выбор конденсатных насосов.
Конденсатные насосы представляют особую группу энергетических насосов работающих с минимальным кавитационным запасом. Они обладают более низкой экономичностью большей металлоемкостью и более высокой стоимость по сравнению с другими насосами на аналогичные подачи и напоры. Поэтому по возможности число насосов должно быть минимальным.
Для блока с прямоточным котлом примем двухподъемную схему установки конденсатных насосов. При такой схеме КН разделяют на 2 ступени.
Рис.3.8.2. Принципиальная схема расположения конденсатных насосов.
8.2а. Выбор конденсатных насосов I ступени.
Общая подача насосов принятая по расчету тепловой схемы - Dкн=25346 кгс ( с учетом добавочной воды)
Объемная производительность конденсатных насосов I ступени(подача):
Q=Dкнρ=25346996=025 м³с=9161 м³ч
Рбоу=06 МПа - гидравлическое сопротивление БОУ [1]
Ртр=01 МПа - сопротивление участка трубопроводов от КНI до БОУ [1]
Рпод=015 МПа – величина давления необходимого подпора на входе в КНII
Давление перед КНI должно быть достаточным для предотвращения кавитации
Рк=00033 МПа давление пара в конденсаторе взятое из расчета тепловой схемы
Р =003 МПа необходимый напор для предотвращения кавитации [1]
Напор конденсатных насосов:
РкнI=Рн-Рв=085-00333=0817 МПа
Напор выраженный в метрах столба перемещаемой жидкости
По найденным характеристикам выбираем 3 насоса по 50% производительности каждый (2 рабочих и 1 резервный) типа КсВ500-85
частота вращения – 1000 обмин
Допустимый кавитационный запас – 16 м
8.2б. Выбор конденсатного насоса II ступени.
Определим параметры КН II.
Объемная производительность конденсатных насосов II ступени(подача):
Q=Dкнρ=25346996=025 м³с=9161 м³ч
Рд=069 МПа - давление в деаэраторе из расчета тепловой схемы
Нд=23 м – высота установки деаэратора относительно оси насоса [1]
Суммарное сопротивление тракта:
Рпнд=035МПа - суммарное сопротивление всех ПНД [1]
Ррпк=004 МПа - сопротивление регулятора питания конденсата [1]
Ртр=01 МПа - суммарное гидравлическое сопротивление трубопроводов
PОЭ=006 МПа – сопротивление охладителя пара эжекторов
Давление перед КН II принимаем равным давлению на которое рассчитана БОУ – блочная обессоливающая установка т.е. не более 08 МПа
Напор выраженный в метрах столба перемещаемой жидкости:
Частота вращения – 1500 обмин
9. Выбор регенеративных подогревателей.
В регенеративных подогревателях осуществляется подогрев питательной воды и конденсата паром отбираемым из отборов турбины. Различают регенеративные подогреватели высокого и низкого давления.
9.1 Выбор подогревателей низкого давления.
Исходные данные берем из расчета тепловой схемы.
Для примера подробно рассмотрим расчет ПНД6. Остальные подогреватели рассчитываются аналогично.
Принимаем коэффициент теплопередачи по лит[3]:
Из расчета тепловой схемы берем температуру насыщения во втором подогревателе:
Определим температурный напор:
Рис.3.9.1.График зависимости температуры пара и воды от площади теплообмена.
Площадь поверхности теплообмена:
Расчетный тепловой поток:
По литературе [2] выбираем тип теплообменника: ПН-1100-23-5-IIIнж.
Сводим данные в таблицу.
Для трех подогревателей низкого давления выбираем тип теплообменника ПН-1100-23-5-IIIнж.
Технические характеристики данного теплообменника:
Площадь поверхности: F=1165 м²
Номинальный массовый расход: D=3361 кгс
Расчетный тепловой поток: Q=435 МВт
Максимальная температура: tmax=350 ºС
Габаритные размеры: H=7750 м
Гидравлическое сопротивление при номинальном расходе воды: Pг=005Мпа
9.2 Выбор подогревателей высокого давления.
ПВД предназначены для регенеративного подогрева питательной воды за счет охлаждения и конденсации пара. Все три подогревателя поверхностного типа. Для более полного использования теплоты подводимого пара предусматриваются специальные поверхности нагрева для охлаждения пара до параметров близких к параметрам насыщения – охладители пара и для охлаждения конденсата пара – охладители конденсата.
Исходные данные для выбора ПВД берем из расчета тепловой схемы.
Выберем подогреватель на примере ПВД 3 остальные подогреватели выбираются аналогично.
При выборе ПВД исходными данными являются :
Gпв = 42781 кгс - расход питательной воды
Dп = 1812 кгс - расход пара на подогреватель
Dдр = D1 + D2 = 6396 кгс - расход дренажа из верхнего подогревателя
hдр2 = 89308 кДжкг – энтальпия дренажа верхнего подогревателя
hдр3 = 75928 кДжкг – энтальпия дренажа из ПВД 3
tдр3 = 17904 0C – температура дренажа за подогревателем
hвх = 6929 кДжкг – энтальпия воды на входе в подогреватель
h н = 85384 кДжкг– энтальпия воды на линии насыщения в подогревателе
tп3 = 20032 0C – температура насыщения греющего пара
Рпв = 315 МПа – давление питательной воды на входе в ПВД 3
k = 3 кДжм2К – коэффициент теплопередачи
=5 0C – недогрев воды до температуры насыщения после СП
ОД = 0985 – КПД охладителя дренажа
Рис. 3.9.2 Принципиальная схема СП и ОД для нахождения
площади поверхности собственно подогревателя.
Определим параметры воды на выходе из охладителя дренажа для этого составим уравнение теплового баланса для ОД:
h``пкп = hн = 85384 кДжкг – энтальпия конденсата греющего пара на выходе из конвективной поверхности отсюда получаем:
По HS диаграмме по Рпв и находим t``вод = 17634 °С
Найдем параметры воды на входе в собственно подогреватель для этого составим уравнение теплового баланса для точки смешения за охладителем дренажа:
В данном уравнении расход основного конденсата сокращается в итоге получим:
По HS диаграмме по Рпв и находим t`всп = 16525 °С
Температура питательной воды на выходе из собственно подогревателя найдем с учетом недогрева:
t``всп = tн – = 20032 – 5 = 19532 °С
По HS диаграмме по Рпв и находим h``всп = 84556 °С
Количество теплоты передаваемой в собственно подогревателе:
Температурный напор в собственно подогревателе:
Площадь поверхности собственно подогревателя:
Тепловой поток для всего подогревателя:
Аналогично для ПВД 2 и ПВД 1 производим расчёт полученные результаты т.е. расчет площади теплообмена разности энтальпий среднелогарифмической температуры теплового потока заносим в таблицу.
По литературе [2] выбираем:
Тип подогревателя ПВД3 – ПВ-1800-380-45.
Его технические характеристики:
Полная площадь поверхности теплообмена –1890 м²
Площадь зоны ОП – нет
Площадь зоны ОК – 1260 м²
Номинальный расход воды – 4722 кгс
Максимальная температура – 300 0С
Тип подогревателя ПВД2 – ПВ-1800-380-45.
Тип подогревателя ПВД1 – ПВ-1700-380-58.
Полная площадь поверхности теплообмена –1678 м²
Площадь зоны ОП – 1340 м²
Площадь зоны ОК – 2010 м²
Номинальный расход воды – 2861 кгс
Максимальная температура – 310 0С
10. Выбор деаэратора.
Деаэраторная колонка и деаэраторный бак рассматриваются отдельно. По Рд=069 МПа и Dпв=42781 кгс выбираем деаэратор ДП -500-1 [1]
10.1 Выбор деаэрационного бака.
По полученным данным выбираем тип бака - БДП-100-1
Технические характеристики бака БДП-100-1:
Типоразмер устанавливаемых колонок – КДП-1000(КДП-500)
Объём бака – 113(118) м3
Максимальная длина – 13500 мм
Все детали колонок и баков изготавливаются из углеродистой стали за исключением дырчатых листов изготавливаемых из стали 08Х18Н10Т.
10.2 Выбор деаэрационной колонки.
В технической характеристике деаэрационного бака указывается типоразмер устанавливаемых колонок.
Типоразмер выбранной мною колонки - КДП-500
В типоразмере выбранного мною бака(БДП-100-1) последняя цифра – это количество колонок устанавливаемых на бак. В моём случае на бак ставится одна колонка.
Технические характеристики колонки КДП-500:
Номинальная производительность – 138.9 кгс
Рабочее давление – 0.59; 069 МПа
Давление допустимое при работе предохранительных клапанов – 085 МПа
Пробное гидравлическое давление – 10 МПа
Рабочая температура – 15808;164.17 0С
Диаметр колонки – 2032 мм
Высота колонки – 3625 мм
Масса колонки заполненной водой – 3.9 т.
Конструкторский расчёт подогревателя высокого давления подключённому к первому отбору турбины.
1.Описание конструкции подогревателя высокого давления.
Подогреватели высокого давления предназначены для регенеративного подогрева питательной воды за счет охлаждения и конденсации пара.
Конструктивно подогреватель высокого давления выполняется вертикальным коллекторного типа.
Поверхность теплообмена набирается из свитых в плоские спирали гладких труб наружным диаметром 32 мм присоединенных к вертикальным раздающим и собирающим коллекторным трубам.
Основными узлами подогревателя являются корпус и трубная система.
Все элементы корпуса выполняются из качественной нержавеющей стали 1Х18Н9Т. Верхняя объемная часть корпуса крепится фланцевым соединением к нижней части. Гидравлическая плотность соединения обеспечивается предварительной приваркой к фланцам корпуса и днища мембран которые свариваются между собой по наружной кромке и соединяются другими методами. Само фланцевое соединение крепится шпильками.
Конструкция трубной системы включает в себя шесть коллекторных труб для распределения и сбора воды. В нижней части корпуса устанавливаются специальные развилки и тройники для соединения коллекторных труб с патрубками подвода и отвода питательной воды. Между спиральными трубными элементами в зоне СП через 8—12 рядов плоскостей навивки спиралей установлены горизонтальные перегородки предназначенные для организации движения пара и отвода конденсата. Спиральные элементы поверхности зон ОП и ОК располагаются в специальных кожухах.
В кожухе ОП перегретый пар в несколько ходов омывает трубный пучок и передает теплоту перегрева. В СП пар распределяется по всей высоте. Конденсат пара с помощью перегородок отводится за пределы трубного пучка и вдоль стенок корпуса стекает в нижнюю часть где расположена зона ОК. Неконденсирующиеся газы отводятся в подогреватель с более низким давлением пара по специальной трубе установленной в зоне СП над верхним днищем кожуха зоны ОК. Все подогреватели высокого давления помимо автоматического устройства регулирования уровня конденсата в корпусе которым оснащены и ПНД имеют также автоматическое защитное устройство. Назначение этого устройства — защита турбины от попадания воды в случае превышения уровня ее в корпусе в результате разрыва труб появления свищей в местах сварки и других причин.
Предусматривается одно защитное устройство на группу ПВД. Однако подача импульсов по уровню конденсата на него осуществляется от каждого корпуса подогревателя. При срабатывании защиты все ПВД отключаются по питательно воде.
Рассматриваемый подогреватель высокого давления подключен к 1 отбору турбины. Подогреватель имеет охладитель конденсата и охладитель пара. ПВД 1 выполнен по классической схеме: пар поступает в охладитель пара отдает некоторое количество теплоты питательной воде; затем поступает в собственно подогреватель где конденсируется; образовавшийся конденсат сливается в охладитель конденсата а затем в более низкий по давлению подогреватель. Питательная вода частично подается в охладитель конденсата где подогревается на 5-100С. Затем подогретая вода смешивается с остальной частью питательной воды перед собственно подогревателем. За собственно подогревателем питательная вода вновь делится на две части: меньшая часть проходит через охладитель пара большая часть поступает в линию питания котла. Схема движения греющего пара и питательной воды и график распределения температур в теплообменнике показаны соответственно на рис. 4.1.1 и рис. 4.1.2.
Рис. 4.1.1. Схема движения питательной воды и греющего пара в ПВД1.
Рис. 4.1.2. График распределения питательной воды и греющего пара по поверхностям нагрева теплообменника.
2.Тепловой и конструктивный расчет подогревателя высокого давления типа ПВ со встроенными охладителями пара и дренажа.
2.1. Исходные данные для теплового расчета ПВД1.
Исходные данные для расчета приняты по данным расчета тепловой схемы.
Параметры греющего пара:
Рп=5733 МПа – давление греющего пара на входе в теплообменник
tп=35475 ºС – температура греющего пара на входе в теплообменник
hп=3064кДжкг – энтальпия греющего пара на входе в теплообменник
Р`п=546 МПа – давление греющего пара в подогревателе
tспн=2695 ºС – температура насыщения пара
hспн=11826 кДжкг – энтальпия конденсата за собственно подогревателем
tдр=25490С – температура конденсата на выходе из охладителя дренажа
hдр=11095 кДжкг – энтальпия конденсата на выходе из охладителя дренажа
Параметры питательной воды:
Gпв=42781 кгс - расход питательной воды
Рпв=305 МПа - давление питательной воды
tв=2449 ºС - температура питательной воды на входе в охладитель конденсата
hв=1065 кДжкг - энтальпия питательной воды на входе в охладитель конденсата
Поверхность нагрева включает охладитель пара собственно подогреватель и охладитель дренажа.
Расход питательной воды составляет:
-через охладитель дренажа Gод = 6117 кгс – 143% от Gпв
-через собственно подогреватель Gоп = 1664 кгс - 70% от Dп
-через охладитель пара Gсп = Gпв = 42781 кгс
Dп – расход пара в ПВД 1
Для расчета теплового баланса подогревателя необходимо знать температуру питательной воды на входе в собственно подогреватель t`сп.
Кроме того необходимо знать температуру конденсата греющего пара на выходе из охладителя дренажа.
Температура питательной воды на выходе из собственно подогревателя принимаем с учетом недогрева т.е.
Примем =45 ºС[5] тогда t``сп =2695-45=2650С соответственно энтальпия питательной воды при Рпв=305МПа - h``сп=1158кДжкг.
Температура питательной воды на выходе из подогревателя определяется с учетом использования тепла перегрева пара и принимается из условий исключения конденсации пара в охладителе т.е. при условии что температура стенки трубы будет выше температуры насыщения греющего пара.
Греющий пар на выходе из охладителя пара имеет температура на 20+30ºС выше температуры насыщения. Примем
По t`п и Р`п определяем:
h`п=28889 кДжкг – энтальпия пара поступающего в собственно подогреватель
Определим энтальпию воды на выходе из охладителя конденсата:
По давлению и энтальпии воды на выходе из охладителя конденсата по [1] определим температуру: t``од=250140С
Определим энтальпию воды на входе в собственно подогреватель:
По давлению и энтальпии воды на входе в собственно подогреватель по [1] определим температуру: t`сп=244670С
Определим энтальпию воды на выходе из охладителя пара:
По давлению и энтальпии воды на выходе из охладителя пара по [1] определим температуру: t``оп=31490С
2.2. Определение тепловых нагрузок.
Уравнения теплового баланса:
а) для охладителя пара
Qоп=Dп(hп-hп)п=Gоп(h``оп-h``сп)
б) для собственно подогревателя
Qсп=Dп(hп-hспн)п=Gсп(h``сп-hсп)
в) для охладителя дренажа
Qод=Dп(hн-hдр)п=Gод(h``од-hв)
Тепловая нагрузка охладителя пара:
Qоп= Dп(hп-hп)п =2378(3064-28889)099=412224 кВт
Тепловая нагрузка собственно подогревателя:
Qсп= Dп(hп-hспн)п =2378(28889-11826)099=4017005 кВт
Тепловая нагрузка охладителя дренажа:
Qод= Dп(hспн -hдр)п =2378(11826-11095)099=172093 кВт
Суммарная тепловая нагрузка ПВД:
Расчет поверхностей нагрева подогревателя производим отдельно ввиду разных условий теплопередачи.
Принимаем: диаметр трубок 3222 мм выполненных из нержавеющей стали марки 1Х18Н9Т; расположение трубок: горизонтальные двойные спирали (6 двойных спиралей в каждой из шести секций между перегородками) следовательно число трубок по вертикали одна над другой n=12.
2.3. Расчет собственно подогревателя.
Поверхность нагрева подогревателя определяется из уравнения теплопередачи
Средний температурный напор:
Определение коэффициента теплопередачи производим графоаналитическим методом.
Определим коэффициент теплоотдачи от стенок труб к воде:
Установим режим течения.
Принимаем скорость течения воды в трубках подогревателя равной в=17 мс [6]
Средняя температура воды:
Принимаем внутренний диаметр трубок собственно подогревателя равным dвн=22 мм.
Физические параметры воды при и Рпв=305 МПа по [7]
Удельный объем воды =000122 м3кг
Плотность воды ρ=81967 кгм3
Динамическая вязкость воды =0110810-3 Пас
Кинематическая вязкость воды =013510-6 м2с
Теплопроводность воды λ=0643 ВтмК
Критерий Прандтля Pr=0796
Число Рейнольдса при данных параметрах
Поскольку расчетное значение числа Рейнольдса Re=277104>Re*=104 режим течения в трубках теплообменника турбулентный. Тогда выражение для нахождения коэффициента теплоотдачи можно определить по следующей формуле [7]
Определим термическое сопротивление стенки труб собственно подогревателя:
- теплопроводность стенки трубы по [7] (для стали марки 1Х18Н9Т)
ст=5 мм – толщина стенки трубы собственно подогревателя
- термическое сопротивление стенки труб собственно подогревателя
Определение коэффициента теплоотдачи от пара к стенке труб собственно подогревателя:
По [6] коэффициент теплоотдачи можно рассчитать по следующей формуле:
где С для горизонтальных труб равно 0728 - средний перепад температур в пограничном слое со стороны греющего пара - поправка на шероховатость и загрязнение внешней поверхности труб( для нержавеющих труб = 1).
где = 0603 ВтмК и = 78003 кгм3 - коэффициент теплопроводности и плотность конденсата = 012910-6 м2с – кинематическая вязкость конденсата = 2459 кгм3 - плотность пара = 16498 кДжкг - удельная теплота конденсации пара= 98 мс2 - ускорение свободного падения = 32 мм - наружный диаметр труб.
Величина b (принята по [5]) определяется по средней температуре плёнки конденсата.
Средняя температура плёнки конденсата:
Коэффициент теплоотдачи α1:
q1=α1t1=2066064t1075
С помощью математического пакета MathCAD построим график зависимости t=f(q) и по графику определим значение плотности теплового потока при среднем логарифмическим напором tсп=1190С.
Рис. 4.2.3 График зависимости температурного напора от плотности теплового потока.
По графику определяем что при tсп=1190С q=31027 Втм2
Коэффициент теплопередачи в собственно подогревателе при этих условиях:
Площадь поверхности нагрева собственно подогревателя:
На практике площадь поверхности нагрева должна быть больше за счет возможного загрязнения поверхности коррозии и т.п. Принимаем Fсп=1310 м2
При принятой скорости течения воды в трубках число трубок собственно подогревателя определим из формулы [6]:
Таким образом на собственно подогреватель приходится 808 трубок; в каждой из 6-ти секций будет 8086=134 двойных спиралей т.е.1342=268 рядов труб по высоте.
Длина спирали в этом случае
Шаг трубок по высоте выбирается равный 36 мм.
Общая высота трубной системы:
Hсп=26836=9648 мм. Спираль навита в два яруса по семь витков в каждом ярусе. Шаг витков равен s=36 мм.
Определим средний радиус витка:
=2(R1+ R2+ R3+ R4+ R5+ R6+ R7)2=2[R1+( R1+s)+ ( R1+2s)+ ( R1+3s)+
+( R1+4s)+( R1+5s)+ ( R1+6s)]2=2(7R1+2136)2=16130 мм
Откуда внутренний радиус витка равен:
Наружный радиус витков: R2=292 мм
2.4. Расчет охладителя пара.
Тепловая нагрузка охладителя пара составляет Qоп=4122.24 кВт.
Встроенный пароохладитель выполняется в виде шести секций заключенных в специальный кожух. Конструктивные размеры секций такие же как и в собственно подогревателе. Задачей моего расчета в этом случае является определение поверхности нагрева и для принятых размеров секций и определение числа и длины трубок.
Расход воды через пароохладитель
Температура питательной воды на входе
Температура питательной воды на выходе
Температура пара на входе
Температура пара на выходе
Расход пара Dп=23.78 мс
Поскольку движение воды в двойных спиралях и движение пара можно рассматривать как многократный перекрестный ток температурный напор определяется как для противоточной схемы:
Определим коэффициент теплоотдачи от пара к стенке трубы:
Средняя температура пара в межтрубном пространстве:
Физические параметры пара приняты при и Р`п=546 МПа
Удельный объем пара =0044 м3кг
Критерий Прандтля Pr=1138
Вязкость пара =020910-4 Пас
Теплопроводность пара λ=547910-3 ВтмК
Площадь живого сечения для прохода пара определяю по формуле:
= 098 – коэффициент учитывающий часть длины труб участвующей в теплообмене по [6]
= 0004 м – расстояние между трубами
Эквивалентный диаметр:
Скорость пара в межтрубном пространстве охладителя пара:
Критерий Рейнольдса:
Поскольку Re>1104 и Pr>07 коэффициент теплоотдачи определяю по формуле пригодной для каналов с размещенными в них трубками при продольном обтекании
Найдем коэффициент теплоотдачи α2 от стенки труб к воде:
Принимаем скорость воды в трубках оп=21 мс
Средняя температура воды в ОП:
Физические параметры воды при и Рпв=305 МПа
Удельный объем воды =00013 м3кг
Плотность воды ρ=76923 кгм3
Вязкость воды =09710-4 Пас
Теплопроводность воды λ=0601 ВтмК
Критерий Рейнольдса:
Коэффициент теплопередачи:
Так как α1=1290 α2=16210 то за определяющий размер берем dн=0032 м.
Поверхность нагрева по внешнему диаметру труб:
Число змеевиков охладителя пара с учетом :
Определим температуру стенки трубы на выходе из пароохладителя:
Термические сопротивления:
Таким образом температура стенки трубы выше температуры насыщения и пар на выходе из пароохладителя не конденсируется. На этом можно закончить расчет охладителя пара.
2.5. Расчет охладителя дренажа.
Принимаем охладитель дренажа состоящий из 72 двойных спиралей по 12 спиралей в каждой из 6 секций заключенных в кожух. Кожух закреплен перегородками между которыми располагаются по 4 двойных спирали (8 трубок одна над другой с шагом 36мм).
Конструкцию принимаем такую же как и в пароохладителе.
Расход питательной воды через охладитель дренажа:
Температура воды на входе
Температура воды на выходе
Температура конденсата на входе
Температура конденсата на выходе
Температурный напор:
Так как ОД последний по ходу питательной воды то в охладитель дренажа поступает только конденсат от 1 отбора. Это означает что средняя температура в межтрубном пространстве находится как среднеарифметическое от суммы температур на входе и выходе охладителя дренажа.
Средняя температура конденсата в межтрубном пространстве:
По и Р`п=546 МПа находим физические параметры конденсата:
Удельный объем =000128 м3кг
Критерий Прандтля Pr=0835
Динамическая вязкость =01009210-3 Пас
Теплопроводность λ=0603 ВтмК
Охладитель дренажа имеет такую же конструкцию как и охладитель пара. Разница заключается в числе спиралей по высоте поэтому dэ = 000784 м = 006323м2.
Скорость конденсата в межтрубном пространстве:
Значение числа Рейнольдса при найденной скорости:
Коэффициент теплоотдачи от конденсата к внешней стенке трубы:
Средняя разность температур воды в трубах охладителя:
Физические параметры воды при и Рпв=30.5 МПа
Удельный объем воды =000121 м3кг
Вязкость воды =011310-3 Пас
Теплопроводность воды λ=06486 ВтмК
Критерий Прандтля Pr=0799
Принимая скорость воды в трубах од=2 мс определим число Рейнольдса:
Коэффициент теплоотдачи от стенки к воде:
Коэффициент теплопередачи:
Поверхность нагрева определяем по наружному диаметру т.к. α1=5714186 α2=14429226:
Принимаем площадь поверхности пара Fод=82 м2
Число змеевиков с учетом :
Общая высота трубной системы охладителя конденсата:
Таким образом суммарная поверхность нагрева подогревателя высокого давления
3.Гидравлический расчет.
Задачей гидравлического расчета подогревателей является определение их гидравлического сопротивления . Для любого элемента или участка подогревателя гидравлическое сопротивление определяется выражением [6] :
- определяет гидравлические потери возникающие при движении тепло- носителя за счёт трения о стенки труб;
- гидравлические потери при движении теплоносителя вызванные местными сопротивлениями (поворотами сужениями или расширениями и т. п.).
Значение коэффициента трения зависит от шероховатости стенок труб и от режима движения теплоносителя определяемого числом Re . С достаточной степенью точности значение может быть определено из выражения [6]:
для стальных труб равна 02 мм.
3.1.Расчёт потери давления для собственно подогревателя.
Число Рейнольдса определяем по формуле:
Коэффициент сопротивления трения [6]:
Из расчета собственно подогревателя l=1613м.
Коэффициент местного сопротивления (вход потока в спираль выход из спирали и влияние кривизны спирали) находим по литературе [6]:
Для собственно подогревателя
Потеря давления потока питательной воды в собственно подогревателе:
3.2.Расчёт потери давления для охладителя пара.
Коэффициент сопротивления трения:
Из расчета l=16.13м.
Коэффициент местного сопротивления (вход потока в спираль выход из спирали и влияние кривизны спирали):
Для охладителя пара
Потеря давления потока питательной воды в охладителе пара:
3.3.Расчёт потери давления для охладителя конденсата.
Из расчета l=16.13 м.
Общая потеря давления в подогревателе:
4.Расчет на прочность элементов подогревателя.
4.1.Расчет толщины стенки подогревателя.
Допустимое напряжение:
Номинальная толщина корпуса подверженному внутреннему давлению должна быть не менее определенной по данной формуле (4-1а) [5]
- внутренний номинальный диаметр (из прототипа).
Элементы корпуса выполняются из качественной углеродистой стали 20К.
(из [5] в табл. П14)-допустимое напряжение при расчете только на действие давления.
Для данного случая =1.
φ ≤ 1 - минимальный коэффициент прочности элемента приведенный к продольному направлению. Для корпусов и обечаек регенеративных подогревателей а также трубок поверхностей нагрева любого теплообменника φ = 1.
- прибавка компенсирующая минусовое отклонение по толщине стенки полуфабриката а также утонение при штамповке или гибки обечаек ;
- прибавка учитывающая искажение правильной геометрической формы окружности в сечении и характерная для гибов. Для прямолинейных цилиндрических элементов обечаек и прямолинейных участков труб прибавка не учитывается ;
- прибавка компенсирующая потери металла в эксплуатации за счет коррозии эрозии и окалинообразования . Для станционных теплообменников с расчетной температурой стенки менее 400 поправку можно не учитывать.
Прибавка пропорциональна толщине стенки :
Коэффициент принимается в зависимости от предельного относительного минусового отклонения толщины стенки(привеличина В=0048).
Организация монтажа энергоблоков мощностью 500 МВт поточным методом.
1. Основные принципы организации поточного монтажа оборудования.
Основным принципом поточного метода строительства и монтажа оборудования является непрерывное и равномерное производство что обеспечивается осуществлением следующих организационно-технологических мероприятий:
-расчленение процессов производства на составляющие процессы;
-разделение труда между исполнителями;
-создание производственного ритма;
-совмещение монтажных процессов во времени и пространстве.
Поточный метод монтажа оборудования может применяться:
-при возведении отдельных энергетических блоков;
-при строительстве всего комплекса электростанций в составе нескольких энергетических блоков;
-при выполнении монтажных работ в период длительного времени на ряде электростанций.
В ряде случаев возникает необходимость смонтировать энергоблок в кротчайшие сроки. Тогда применяется скоростной метод основанный на производстве работ в минимальные технически возможные сроки путём применения наибольшего совмещения работ по времени с организацией работы по скользящему графику в две и три смены для чего привлекается большое количество рабочих.
Поточный метод монтажа обладает достоинствами скоростного метода и поэтому находит наибольшее применение для сооружения электростанции в целом а скоростной монтаж – для ввода одного или двух блоков.
При организации монтажа оборудования на тепловых электростанциях различают следующие разновидности монтажных потоков:
Частный поток - элементарный поток представляющий собой последовательное выполнение одного простого процесса на ряде узлов агрегата;
Специализированный поток – совокупность частных потоков объединённых единой системой для завершения монтажа агрегата (например турбины; котельного агрегата и др.);
Объектный поток – совокупность специализированных потоков обеспечивающих завершение монтажа всего оборудования энергетического блока;
Комплексный поток – группа организационно связанных объектных потоков обеспечивающих завершение монтажа оборудования электростанций в целом.
В монтажной практике специализированные потоки называются также продольными потоками когда оборудование главного корпуса монтируется потоками: машинный зал деаэраторная; котельная; оборудование открытой установки (электрофильтры регенеративные воздухоподогреватели тягодутьевая установка).
2. Характеристики поточного метода монтажа.
Потоки делятся на ритмичные и неритмичные а по продолжительности - на краткосрочные и непрерывные когда поток функционирует длительное время (например для монтажа всех энергоблоков одной электростанции).
При монтаже на электростанции нескольких энергоблоков могут также быть и специализированные поперечные потоки когда в один поток включён например монтаж всех трубопроводов высокого давления от питательных насосов к котлоагрегату и паропроводов от него к турбине.
В условиях строительства электростанций применяется стационарно – поточный метод монтажа котельных и турбинных агрегатов когда поток организовывается последовательно в двух местах:
-на сборочной площадке для укрупнения заводских блоков из заводских узлов и деталей;
-на постоянном фундаменте агрегата где производятся установка блоков соединение их с отдельными деталями и оформление законченного агрегата. При этом блоки и узлы в процессе работы над ними кроме подъёма их остаются неподвижными а бригады монтажников постоянно выполняющие определённые циклы работ меняются.
На сборочной площадке имеются два или три параллельных потока оборудованных козловыми кранами для разгрузки сборки и погрузки на транспорт собранных блоков устройствами для резки и сварки и другими приспособлениями необходимыми для производства сборочных работ.
В главном корпусе электростанции организуются три или четыре специализированных потока оборудованных мостовыми кранами для монтажа оборудования всеми устройствами для производства сборочных сварочных и проверочных работ. В каждый поток вводится железнодорожный путь или автодорога для подачи оборудования.
При осуществлении комплексного потока когда одновременно монтируются несколько энергетических блоков рекомендуется организовать следующие специализированные потоки:
-сборки оборудования в укрупнённые блоки на укрупительно – сборочной площадке;
-в главном корпусе монтажа оборудования и трубопроводов машинного зала;
-монтажа оборудования и трубопроводов деаэраторной этажерки;
-монтажа оборудования котельного отделения со всеми трубопроводами;
-монтажа оборудования наружной установки электрофильтров тягодутьевого устройства.
Кроме того в главном корпусе для осуществления подготовки к пуску и опробования всех агрегатов энергетического блока организуется поток пусконаладочных работ (поперечный) который поточно по мере завершения монтажа переходит от одного энергоблока к другому.
Для всего комплекса или очереди монтируемой электростанции параллельно организуются дополнительные специализированные потоки:
-монтажа оборудования топливоподачи;
-монтажа оборудования мазутного хозяйства с трубопроводами от насосной до главного корпуса;
-монтажа оборудования химводоочистки с трубопроводами между ХВО и главным корпусом.
Для поточного монтажа агрегат разбивается на отдельные секции – потоки а весь комплекс работ по монтажу агрегатов расчленяется на частные потокистрого увязанные между собой которые последовательно выполняются закреплёнными специализированными бригадами рабочих постоянного состава оснащёнными грузоподъёмными механизмами механизированным инструментом и приспособлениями. Бригады монтажников выполняют работы последовательно на всех потоках передвигаясь с одного на другой; заканчивая работы на очередном потоке подготавливают тем самым фронт работ для следующей по потоку бригады. Создаётся система цикловых частных потоков из которых слагается общий специализированный поток. При этом работы выполняются в порядке технологической последовательности монтажа агрегата. После разворота монтажа работы ведутся одновременно на всех потоках агрегата. Такая поточная организация создаёт наиболее полное совмещение работ по времени и обеспечивает высокие и устойчивые темпы монтажа.
Особенность выполнения работ на разных частных и специализированных потоках монтажа заключается в том что к определённому периоду – к началу пуска энергоблока должны быть завершены операции на всех потоках опробованы вхолостую все механизмы промыты и продуты все трубопроводы блока.
Для выполнения монтажных работ на перечисленных потоках выделяются отдельные мастера прорабы а для крупных объектов – и отдельные самостоятельные участки.
Поточный монтаж оборудования характеризуется системой показателей связанных между собой и определяемых как для специализированных объектных комплексных так и частных потоков.
Основными расчётными параметрами монтажных потоков являются:
Интенсивность потока – количество работ выполняемых потоком за единицу времени измеренное в натуральных показателях или масса оборудования смонтированного поточным методом за определённое время.
Интенсивность потока IТ (тмес) определяется по следующей формуле:
где PОБ – общая масса оборудования подлежащего монтажу (т); ТП – нормативная продолжительность монтажных работ (мес).
Продолжительность потока – период выполнения работ объём трудоёмкость работ;
Ритм потока – время выполнения частного потока;
Шаг потока – время через которое последовательно начинается монтаж отдельных агрегатов:
t = Тобщ – Тперв n – 1
где t – шаг потока (мес); Тобщ – общая продолжительность монтажа всех агрегатов (мес); Тперв – продолжительность монтажа первого агрегата (мес); n – количество агрегатов подлежащих монтажу.
При поточном монтаже обеспечивается непрерывная и равномерная загрузка рабочих за счёт ликвидации перерывов и простоев при производстве работ а также повторяемость производственных процессов при монтаже последующих однотипных агрегатов. Приобретаются навыки снижается трудоёмкость монтажных работ и возрастает производительность труда.
3. График движения рабочей силы.
В отличие от графиков движения рабочей силы для монтажа отдельных энергоблоков имеющих выпуклую кривую для поточного монтажа график имеет форму трапеции с постоянным составом рабочих.
При монтаже энергетических блоков непрерывным потоком для составления графиков следует определить наивыгоднейшую продолжительность и необходимое наименьшее количество рабочих.
В основу расчётов принимаются суммарные трудовые затраты монтажа энергетических блоков участвующих в потоке.
При поточном строительстве число рабочих в период у3становившегося потока определяется по формуле:
где Т – продолжительность потока (дни); Qобщ – суммарная трудоёмкость на всех объектах данного потока (чел-дни); - коэффициент обозначающий отрезки времени через которое число рабочих увеличивается в среднем на одного.
Для строительства ТЭС коэффициент колеблется от 012 до 018; для монтажа оборудования может быть принят 014 – 016.
Период наращивания числа работников: (дни).
Рис. 5.3 График движения рабочей силы
4. Организация поточного монтажа на примере ГРЭС мощностью 4000МВт (8 блоков по 500МВт).
Характеристики энергоблоков 500МВт:
Наименование оборудования
Количество комплексов
Тягодутьевое устройство
Станционное оборудование
Станционные трубопроводы
Мостовые краны (котельной машинного зала дымососной РВП и др.)
Склад угля и топливоподачи
Прочие общестанционные объекты
Технологические металлоконструкции связанные с монтажом оборудования:
-по котельному отделению
-по деаэраторной установке
Итого металлоконструкций
Всего оборудования и металлоконструкций
Поточный монтаж энергоблоков 500МВт организуется исходя из следующих основных принципов.
Все монтажные работы выполняются в непрерывном по времени потоке.
Подготовительные работы по оборудованию включая разгрузку хранение комплектацию и укрупнительную сборку в блоки выполняются в централизованной базе где осваивается не менее 30% всех трудозатрат на монтажные работы.
Доставка блоков с базы на электростанции к месту монтажа производится железнодорожным и большегрузным автотранспортом.
Монтажные работы производятся в полностью законченном главном корпусе закрытом и отопляемым в зимнее время.
Совмещение строительных и монтажных работ допустимо только для установки на проектные места отдельных крупногабаритных узлов оборудования осуществляемой строительными кранами.
Монтаж оборудования котельного отделения выполняется мостовыми кранами грузоподъёмностью 50т.
Коэффициент монтажной блочности намечается довести до 095 – 097 при средней массе блока не ниже расчётной для данного котельного агрегата.
Монтажные блоки следует укомплектовать приспособлениями для строповки кантовки и подъёма.
4.1. Потоки монтажа оборудования для ГРЭС 4000МВт.
Для осуществления поточного монтажа технологического оборудования трубопроводов и металлоконструкций связанных с ними организуются следующие специализированные потоки:
Первый поток – машинный зал; турбоустановка; БОУ; металлоконструкции вокруг турбоустановки; грузоподъёмные механизмы; станционные трубопроводы высокого и низкого давления.
Второй поток – деаэраторная этажерка; станционное оборудование; технологические металлоконструкции; станционные трубопроводы высокого и низкого давления.
Третий поток – котельное отделение; котельные агрегаты; пылеприготовление; газовоздухопроводы; топливоподача; гидрозолоудаление; станционные трубопроводы высокого и низкого давления; грузоподъёмные механизмы; металлоконструкции.
Четвёртый поток – установка регенеративных воздухоподогревателей; оборудование воздухоподогревателей; газовоздухопроводы; топливоподача; грузоподъёмные механизмы; металлоконструкции.
Пятый поток – газоочистка и тягодутьевые машины; электрофильтры; тягодутьевые машины и газовоздухопроводы; грузоподъёмные машины; металлоконструкции.
Шестой поток – химводоочистка; оборудование и трубопроводы ХВО; оборудование и трубопроводы прочих вспомогательных цехов.
Седьмой поток – склад угля и топливоподача; краны для склада топлива и топливоподача главного корпуса; оборудование прочих общестанционных объектов.
Дополнительно в потоки включаются конструкции для обмуровки котлоагрегатов и тепловая изоляция оборудования и трубопроводов.
4.2. График поточного монтажа энергоблоков 500МВт.
Продолжительность монтажа проверяется в зависимости от общих трудовых затрат на месте монтажа для одного блока по формуле:
где R – коэффициент номинальной продолжительности:
где - трудозатраты на монтажной площадке с учётом выполнения 30% на базе.
Продолжительность монтажа измеряется в рабочих днях а если измеренное в днях разделить на число 212 получим измеренное в месяцах. Число 212 – количество рабочих дней в месяце по пятидневной неделе.
Учитывая принятый режим работы на монтажной площадке корректируем продолжительность монтажа по следующей формуле:
где - продолжительность монтажа при семидневной рабочей неделе (мес); - доля времени работы по семидневной рабочей неделе.
Продолжительность монтажа для первого блока:
где =185-195 - наиболее эффективный коэффициент совмещения для поточного монтажа;
Общая продолжительность монтажа всех энергоблоков:
Определяем потребность в рабочей силе по формуле для поточного монтажа учитывающей равномерное количество рабочих для всего периода монтажа:
где Т – продолжительность потока (дни); - коэффициент обозначающий отрезки времени через которое число рабочих увеличивается в среднем на одного.
Период увеличения числа рабочих:
Ритмичность монтажа в потоке восьми энергоблоков проверяем по формуле коэффициента ритмичности с учётом того что каждый блок вводится в одном квартале года:
Интенсивность потока:
Как видно из графика поточного монтажа энергоблоков 500МВт первый блок не может быть пущен в первый год начала производства монтажных работ но в последующие годы обеспечиваются монтаж и пуск по два и три блока ежегодно.
В графике поточного монтажа ( для упрощения) трудозатраты и продолжительность монтажа приняты для всех блоков кроме первого одинаковыми.
В представленной выпускной работе бакалавра был произведен расчет принципиальной тепловой схемы энергоблока с турбоустановкой К-520-235 по результатам которого были определены:
-расход пара в голову турбины
-все потоки пара и воды в схеме
-показатели тепловой экономичности
В соответствии с существующими нормами и правилами был проведен выбор основного и вспомогательного оборудования этого энергоблока а также выполнены необходимые для этого расчеты.
В индивидуальном задании был выполнен тепловой конструкторский расчет подогревателя высокого давления поверхностного типа.
В специальной части было представлено подробное описание организации поточного монтажа энергоблоков мощностью 500МВт и подробно разобрано на примере ГРЭС 4000МВт (8 энергоблоков по 500МВт).
Список используемой литературы:
«ТЭС и АЭС» справочник под редакцией В.А. Григорьева Москва «Энергоиздат» 1982г.
Л.А Рихтер Д.П. Елизаров В.М. Лавыгин «Вспомогательное оборудование ТЭС». Москва «Энергоаомиздат» 1987г.
В.Я. Рыжкин «Тепловые электрические станции». Москва «Энергоатомиздат» 1987г.
Л.А. Федорович А.П Рыков «Выбор вспомогательного оборудования ТЭС» Москва МЭИ 1999г.
В.Я. Гиршфильд А.М. Князев В.Е. Куликов «Расчет станционных теплообменников» Москва МЭИ 1974г.
Назмеев Ю.Г. Лавыгин В.М. «Теплообменные аппараты ТЭС» Москва МЭИ 1998г.
Винницкий Д.Я. «Организация монтажа оборудования тепловых электростанций». Москва «Энергия» 1980г.
«ТЭС и АЭС» справочник под редакцией А.В. Клименко и В.М. Зорина МЭИ Москва 2003г.
Заключение.doc
-расход пара в голову турбины
-все потоки пара и воды в схеме
-показатели тепловой экономичности
В соответствии с существующими нормами и правилами был проведен выбор основного и вспомогательного оборудования этого энергоблока а также выполнены необходимые для этого расчеты.
В индивидуальном задании был выполнен тепловой конструкторский расчет подогревателя высокого давления поверхностного типа.
В специальной части была представлена организация поточного монтажа энергоблоков мощностью 500МВт и подробно разобрана на примере ГРЭС 4000МВт (8 энергоблоков по 500МВт).
ПВ-1700-380-58(РАМОР).dwg
К предохранительным клапанам
Вход воздуха из ПВД высшей ступени
Вход конденсата из ПВД высшей ступени
К водоуказательному прибору
Отвод неконденсирующихся газов
Выход питательной воды из дополнительного ОП
Вход питательной воды в дополнительный ОП
Выход конденсата греющего пара
Выход питательной воды
Вход питательной воды
Характеристика присоединения ПВД
ПВ-1700-380-58 Разрезы(РАМОР).dwg

Приварка спиралей к
коллекторным трубам.
Зона охлаж- дения кон- денсата
Схема движения воды в трубной системе
Зона конденсации пара
В линию перед котлом
Зона охлаж- дения пара
Расчёт ПВД-1(ПВ-1700-380-58)РАМОР.doc
1.Описание конструкции подогревателя высокого давления.
Подогреватели высокого давления предназначены для регенеративного подогрева питательной воды за счет охлаждения и конденсации пара.
Конструктивно подогреватель высокого давления выполняется вертикальным коллекторного типа.
Поверхность теплообмена набирается из свитых в плоские спирали гладких труб наружным диаметром 32 мм присоединенных к вертикальным раздающим и собирающим коллекторным трубам.
Основными узлами подогревателя являются корпус и трубная система.
Все элементы корпуса выполняются из качественной нержавеющей стали 1Х18Н9Т. Верхняя объемная часть корпуса крепится фланцевым соединением к нижней части. Гидравлическая плотность соединения обеспечивается предварительной приваркой к фланцам корпуса и днища мембран которые свариваются между собой по наружной кромке и соединяются другими методами. Само фланцевое соединение крепится шпильками.
Конструкция трубной системы включает в себя шесть коллекторных труб для распределения и сбора воды. В нижней части корпуса устанавливаются специальные развилки и тройники для соединения коллекторных труб с патрубками подвода и отвода питательной воды. Между спиральными трубными элементами в зоне СП через 8—12 рядов плоскостей навивки спиралей установлены горизонтальные перегородки предназначенные для организации движения пара и отвода конденсата. Спиральные элементы поверхности зон ОП и ОК располагаются в специальных кожухах.
В кожухе ОП перегретый пар в несколько ходов омывает трубный пучок и передает теплоту перегрева. В СП пар распределяется по всей высоте. Конденсат пара с помощью перегородок отводится за пределы трубного пучка и вдоль стенок корпуса стекает в нижнюю часть где расположена зона ОК. Неконденсирующиеся газы отводятся в подогреватель с более низким давлением пара по специальной трубе установленной в зоне СП над верхним днищем кожуха зоны ОК. Все подогреватели высокого давления помимо автоматического устройства регулирования уровня конденсата в корпусе которым оснащены и ПНД имеют также автоматическое защитное устройство. Назначение этого устройства — защита турбины от попадания воды в случае превышения уровня ее в корпусе в результате разрыва труб появления свищей в местах сварки и других причин.
Предусматривается одно защитное устройство на группу ПВД. Однако подача импульсов по уровню конденсата на него осуществляется от каждого корпуса подогревателя. При срабатывании защиты все ПВД отключаются по питательно воде.
Рассматриваемый подогреватель высокого давления подключен к 1 отбору турбины. Подогреватель имеет охладитель конденсата и охладитель пара. ПВД 1 выполнен по классической схеме: пар поступает в охладитель пара отдает некоторое количество теплоты питательной воде; затем поступает в собственно подогреватель где конденсируется; образовавшийся конденсат сливается в охладитель конденсата а затем в более низкий по давлению подогреватель. Питательная вода частично подается в охладитель конденсата где подогревается на 5-100С. Затем подогретая вода смешивается с остальной частью питательной воды перед собственно подогревателем. За собственно подогревателем питательная вода вновь делится на две части: меньшая часть проходит через охладитель пара большая часть поступает в линию питания котла. Схема движения греющего пара и питательной воды и график распределения температур в теплообменнике показаны соответственно на рис. 4.1.1 и рис. 4.1.2.
Рис. 4.1.1. Схема движения питательной воды и греющего пара в ПВД1.
Рис. 4.1.2. График распределения питательной воды и греющего пара по поверхностям нагрева теплообменника.
2.Тепловой и конструктивный расчет подогревателя высокого давления типа ПВ со встроенными охладителями пара и дренажа.
2.1. Исходные данные для теплового расчета ПВД1.
Исходные данные для расчета приняты по данным расчета тепловой схемы.
Параметры греющего пара:
Рп=5733 МПа – давление греющего пара на входе в теплообменник
tп=35475 ºС – температура греющего пара на входе в теплообменник
hп=3064кДжкг – энтальпия греющего пара на входе в теплообменник
Р`п=546 МПа – давление греющего пара в подогревателе
tспн=2695 ºС – температура насыщения пара
hспн=11826 кДжкг – энтальпия конденсата за собственно подогревателем
tдр=25490С – температура конденсата на выходе из охладителя дренажа
hдр=11095 кДжкг – энтальпия конденсата на выходе из охладителя дренажа
Параметры питательной воды:
Gпв=42781 кгс - расход питательной воды
Рпв=305 МПа - давление питательной воды
tв=2449 ºС - температура питательной воды на входе в охладитель конденсата
hв=1065 кДжкг - энтальпия питательной воды на входе в охладитель конденсата
Поверхность нагрева включает охладитель пара собственно подогреватель и охладитель дренажа.
Расход питательной воды составляет:
-через охладитель дренажа Gод = 6117 кгс – 143% от Gпв
-через собственно подогреватель Gоп = 1664 кгс - 70% от Dп
-через охладитель пара Gсп = Gпв = 42781 кгс
Dп – расход пара в ПВД 1
Для расчета теплового баланса подогревателя необходимо знать температуру питательной воды на входе в собственно подогреватель t`сп.
Кроме того необходимо знать температуру конденсата греющего пара на выходе из охладителя дренажа.
Температура питательной воды на выходе из собственно подогревателя принимаем с учетом недогрева т.е.
Примем =45 ºС[5] тогда t``сп =2695-45=2650С соответственно энтальпия питательной воды при Рпв=305МПа - h``сп=1158кДжкг.
Температура питательной воды на выходе из подогревателя определяется с учетом использования тепла перегрева пара и принимается из условий исключения конденсации пара в охладителе т.е. при условии что температура стенки трубы будет выше температуры насыщения греющего пара.
Греющий пар на выходе из охладителя пара имеет температура на 20+30ºС выше температуры насыщения. Примем
По t`п и Р`п определяем:
h`п=28889 кДжкг – энтальпия пара поступающего в собственно подогреватель
Определим энтальпию воды на выходе из охладителя конденсата:
По давлению и энтальпии воды на выходе из охладителя конденсата по [1] определим температуру: t``од=250140С
Определим энтальпию воды на входе в собственно подогреватель:
По давлению и энтальпии воды на входе в собственно подогреватель по [1] определим температуру: t`сп=244670С
Определим энтальпию воды на выходе из охладителя пара:
По давлению и энтальпии воды на выходе из охладителя пара по [1] определим температуру: t``оп=31490С
2.2. Определение тепловых нагрузок.
Уравнения теплового баланса:
а) для охладителя пара
Qоп=Dп(hп-hп)п=Gоп(h``оп-h``сп)
б) для собственно подогревателя
Qсп=Dп(hп-hспн)п=Gсп(h``сп-hсп)
в) для охладителя дренажа
Qод=Dп(hн-hдр)п=Gод(h``од-hв)
Тепловая нагрузка охладителя пара:
Qоп= Dп(hп-hп)п =2378(3064-28889)099=412224 кВт
Тепловая нагрузка собственно подогревателя:
Qсп= Dп(hп-hспн)п =2378(28889-11826)099=4017005 кВт
Тепловая нагрузка охладителя дренажа:
Qод= Dп(hспн -hдр)п =2378(11826-11095)099=172093 кВт
Суммарная тепловая нагрузка ПВД:
Расчет поверхностей нагрева подогревателя производим отдельно ввиду разных условий теплопередачи.
Принимаем: диаметр трубок 3222 мм выполненных из нержавеющей стали марки 1Х18Н9Т; расположение трубок: горизонтальные двойные спирали (6 двойных спиралей в каждой из шести секций между перегородками) следовательно число трубок по вертикали одна над другой n=12.
2.3. Расчет собственно подогревателя.
Поверхность нагрева подогревателя определяется из уравнения теплопередачи
Средний температурный напор:
Определение коэффициента теплопередачи производим графоаналитическим методом.
Определим коэффициент теплоотдачи от стенок труб к воде:
Установим режим течения.
Принимаем скорость течения воды в трубках подогревателя равной в=17 мс [6]
Средняя температура воды:
Принимаем внутренний диаметр трубок собственно подогревателя равным dвн=22 мм.
Физические параметры воды при и Рпв=305 МПа по [7]
Удельный объем воды =000122 м3кг
Плотность воды ρ=81967 кгм3
Динамическая вязкость воды =0110810-3 Пас
Кинематическая вязкость воды =013510-6 м2с
Теплопроводность воды λ=0643 ВтмК
Критерий Прандтля Pr=0796
Число Рейнольдса при данных параметрах
Поскольку расчетное значение числа Рейнольдса Re=277104>Re*=104 режим течения в трубках теплообменника турбулентный. Тогда выражение для нахождения коэффициента теплоотдачи можно определить по следующей формуле [7]
Определим термическое сопротивление стенки труб собственно подогревателя:
- теплопроводность стенки трубы по [7] (для стали марки 1Х18Н9Т)
ст=5 мм – толщина стенки трубы собственно подогревателя
- термическое сопротивление стенки труб собственно подогревателя
Определение коэффициента теплоотдачи от пара к стенке труб собственно подогревателя:
По [6] коэффициент теплоотдачи можно рассчитать по следующей формуле:
где С для горизонтальных труб равно 0728 - средний перепад температур в пограничном слое со стороны греющего пара - поправка на шероховатость и загрязнение внешней поверхности труб( для нержавеющих труб = 1).
где = 0603 ВтмК и = 78003 кгм3 - коэффициент теплопроводности и плотность конденсата = 012910-6 м2с – кинематическая вязкость конденсата = 2459 кгм3 - плотность пара = 16498 кДжкг - удельная теплота конденсации пара= 98 мс2 - ускорение свободного падения = 32 мм - наружный диаметр труб.
Величина b (принята по [5]) определяется по средней температуре плёнки конденсата.
Средняя температура плёнки конденсата:
Коэффициент теплоотдачи α1:
q1=α1t1=2066064t1075
С помощью математического пакета MathCAD построим график зависимости t=f(q) и по графику определим значение плотности теплового потока при среднем логарифмическим напором tсп=1190С.
Рис. 4.2.3 График зависимости температурного напора от плотности теплового потока.
По графику определяем что при tсп=1190С q=31027 Втм2
Коэффициент теплопередачи в собственно подогревателе при этих условиях:
Площадь поверхности нагрева собственно подогревателя:
На практике площадь поверхности нагрева должна быть больше за счет возможного загрязнения поверхности коррозии и т.п. Принимаем Fсп=1310 м2
При принятой скорости течения воды в трубках число трубок собственно подогревателя определим из формулы [6]:
Таким образом на собственно подогреватель приходится 808 трубок; в каждой из 6-ти секций будет 8086=134 двойных спиралей т.е.1342=268 рядов труб по высоте.
Длина спирали в этом случае
Шаг трубок по высоте выбирается равный 36 мм.
Общая высота трубной системы:
Hсп=26836=9648 мм. Спираль навита в два яруса по семь витков в каждом ярусе. Шаг витков равен s=36 мм.
Определим средний радиус витка:
=2(R1+ R2+ R3+ R4+ R5+ R6+ R7)2=2[R1+( R1+s)+ ( R1+2s)+ ( R1+3s)+
+( R1+4s)+( R1+5s)+ ( R1+6s)]2=2(7R1+2136)2=16130 мм
Откуда внутренний радиус витка равен:
Наружный радиус витков: R2=292 мм
2.4. Расчет охладителя пара.
Тепловая нагрузка охладителя пара составляет Qоп=4122.24 кВт.
Встроенный пароохладитель выполняется в виде шести секций заключенных в специальный кожух. Конструктивные размеры секций такие же как и в собственно подогревателе. Задачей моего расчета в этом случае является определение поверхности нагрева и для принятых размеров секций и определение числа и длины трубок.
Расход воды через пароохладитель
Температура питательной воды на входе
Температура питательной воды на выходе
Температура пара на входе
Температура пара на выходе
Расход пара Dп=23.78 мс
Поскольку движение воды в двойных спиралях и движение пара можно рассматривать как многократный перекрестный ток температурный напор определяется как для противоточной схемы:
Определим коэффициент теплоотдачи от пара к стенке трубы:
Средняя температура пара в межтрубном пространстве:
Физические параметры пара приняты при и Р`п=546 МПа
Удельный объем пара =0044 м3кг
Критерий Прандтля Pr=1138
Вязкость пара =020910-4 Пас
Теплопроводность пара λ=547910-3 ВтмК
Площадь живого сечения для прохода пара определяю по формуле:
= 098 – коэффициент учитывающий часть длины труб участвующей в теплообмене по [6]
= 0004 м – расстояние между трубами
Эквивалентный диаметр:
Скорость пара в межтрубном пространстве охладителя пара:
Критерий Рейнольдса:
Поскольку Re>1104 и Pr>07 коэффициент теплоотдачи определяю по формуле пригодной для каналов с размещенными в них трубками при продольном обтекании
Найдем коэффициент теплоотдачи α2 от стенки труб к воде:
Принимаем скорость воды в трубках оп=21 мс
Средняя температура воды в ОП:
Физические параметры воды при и Рпв=305 МПа
Удельный объем воды =00013 м3кг
Плотность воды ρ=76923 кгм3
Вязкость воды =09710-4 Пас
Теплопроводность воды λ=0601 ВтмК
Критерий Рейнольдса:
Коэффициент теплопередачи:
Так как α1=1290 α2=16210 то за определяющий размер берем dн=0032 м.
Поверхность нагрева по внешнему диаметру труб:
Число змеевиков охладителя пара с учетом :
Определим температуру стенки трубы на выходе из пароохладителя:
Термические сопротивления:
Таким образом температура стенки трубы выше температуры насыщения и пар на выходе из пароохладителя не конденсируется. На этом можно закончить расчет охладителя пара.
2.5. Расчет охладителя дренажа.
Принимаем охладитель дренажа состоящий из 72 двойных спиралей по 12 спиралей в каждой из 6 секций заключенных в кожух. Кожух закреплен перегородками между которыми располагаются по 4 двойных спирали (8 трубок одна над другой с шагом 36мм).
Конструкцию принимаем такую же как и в пароохладителе.
Расход питательной воды через охладитель дренажа:
Температура воды на входе
Температура воды на выходе
Температура конденсата на входе
Температура конденсата на выходе
Температурный напор:
Так как ОД последний по ходу питательной воды то в охладитель дренажа поступает только конденсат от 1 отбора. Это означает что средняя температура в межтрубном пространстве находится как среднеарифметическое от суммы температур на входе и выходе охладителя дренажа.
Средняя температура конденсата в межтрубном пространстве:
По и Р`п=546 МПа находим физические параметры конденсата:
Удельный объем =000128 м3кг
Критерий Прандтля Pr=0835
Динамическая вязкость =01009210-3 Пас
Теплопроводность λ=0603 ВтмК
Охладитель дренажа имеет такую же конструкцию как и охладитель пара. Разница заключается в числе спиралей по высоте поэтому dэ = 000784 м = 006323м2.
Скорость конденсата в межтрубном пространстве:
Значение числа Рейнольдса при найденной скорости:
Коэффициент теплоотдачи от конденсата к внешней стенке трубы:
Средняя разность температур воды в трубах охладителя:
Физические параметры воды при и Рпв=30.5 МПа
Удельный объем воды =000121 м3кг
Вязкость воды =011310-3 Пас
Теплопроводность воды λ=06486 ВтмК
Критерий Прандтля Pr=0799
Принимая скорость воды в трубах од=2 мс определим число Рейнольдса:
Коэффициент теплоотдачи от стенки к воде:
Коэффициент теплопередачи:
Поверхность нагрева определяем по наружному диаметру т.к. α1=5714186 α2=14429226:
Принимаем площадь поверхности пара Fод=82 м2
Число змеевиков с учетом :
Общая высота трубной системы охладителя конденсата:
Таким образом суммарная поверхность нагрева подогревателя высокого давления
3.Гидравлический расчет.
Задачей гидравлического расчета подогревателей является определение их гидравлического сопротивления . Для любого элемента или участка подогревателя гидравлическое сопротивление определяется выражением [6] :
- определяет гидравлические потери возникающие при движении тепло- носителя за счёт трения о стенки труб;
- гидравлические потери при движении теплоносителя вызванные местными сопротивлениями (поворотами сужениями или расширениями и т. п.).
Значение коэффициента трения зависит от шероховатости стенок труб и от режима движения теплоносителя определяемого числом Re . С достаточной степенью точности значение может быть определено из выражения [6]:
для стальных труб равна 02 мм.
3.1.Расчёт потери давления для собственно подогревателя.
Число Рейнольдса определяем по формуле:
Коэффициент сопротивления трения [6]:
Из расчета собственно подогревателя l=1613м.
Коэффициент местного сопротивления (вход потока в спираль выход из спирали и влияние кривизны спирали) находим по литературе [6]:
Для собственно подогревателя
Потеря давления потока питательной воды в собственно подогревателе:
3.2.Расчёт потери давления для охладителя пара.
Коэффициент сопротивления трения:
Из расчета l=16.13м.
Коэффициент местного сопротивления (вход потока в спираль выход из спирали и влияние кривизны спирали):
Для охладителя пара
Потеря давления потока питательной воды в охладителе пара:
3.3.Расчёт потери давления для охладителя конденсата.
Из расчета l=16.13 м.
Общая потеря давления в подогревателе:
4.Расчет на прочность элементов подогревателя.
4.1.Расчет толщины стенки подогревателя.
Допустимое напряжение:
Номинальная толщина корпуса подверженному внутреннему давлению должна быть не менее определенной по данной формуле (4-1а) [5]
- внутренний номинальный диаметр (из прототипа).
Элементы корпуса выполняются из качественной углеродистой стали 20К.
(из [5] в табл. П14)-допустимое напряжение при расчете только на действие давления.
Для данного случая =1.
φ ≤ 1 - минимальный коэффициент прочности элемента приведенный к продольному направлению. Для корпусов и обечаек регенеративных подогревателей а также трубок поверхностей нагрева любого теплообменника φ = 1.
- прибавка компенсирующая минусовое отклонение по толщине стенки полуфабриката а также утонение при штамповке или гибки обечаек ;
- прибавка учитывающая искажение правильной геометрической формы окружности в сечении и характерная для гибов. Для прямолинейных цилиндрических элементов обечаек и прямолинейных участков труб прибавка не учитывается ;
- прибавка компенсирующая потери металла в эксплуатации за счет коррозии эрозии и окалинообразования . Для станционных теплообменников с расчетной температурой стенки менее 400 поправку можно не учитывать.
Прибавка пропорциональна толщине стенки :
Коэффициент принимается в зависимости от предельного относительного минусового отклонения толщины стенки(привеличина В=0048).
Титульник.doc
Курсовой проект по курсу: «Выбор теплотехнического вспомогательного оборудования» на тему: «Расчет подогревателя высокого давления подключенного к первому отбору турбины»
Студент: Романов Р.Ю.
Преподаватель: Рожнатовский Д.В.
Список использованной литературы(Гарик).doc
«ТЭС и АЭС» справочник под редакцией В.А. Григорьева Москва «Энергоиздат» 1982г.
Л.А Рихтер Д.П. Елизаров В.М. Лавыгин «Вспомогательное оборудование ТЭС». Москва «Энергоаомиздат» 1987г.
В.Я. Рыжкин «Тепловые электрические станции». Москва «Энергоатомиздат» 1987г.
Л.А. Федорович А.П Рыков «Выбор вспомогательного оборудования ТЭС» Москва МЭИ 1999г.
В.Я. Гиршфильд А.М. Князев В.Е. Куликов «Расчет станционных теплообменников» Москва МЭИ 1974г.
Назмеев Ю.Г. Лавыгин В.М. «Теплообменные аппараты ТЭС» Москва МЭИ 1998г.
Содержание.doc
Тепловой расчет подогревателя высокого давления типа ПВ со встроенными
охладителями пара и дренажа:
- исходные данные для теплового расчета ПВД1 . стр.4
- определение тепловых нагрузок .. стр.5
- расчет собственно подогревателя стр.5
- тепловой расчет охладителя пара стр.8
- расчет охладителя дренажа . cтр.11
Гидравлический расчет:
- расчёт потери давления для собственно подогревателя стр.13
- расчёт потери давления для охладителя пара стр.14
- расчёт потери давления для охладителя конденсата . стр.14
Расчет на прочность элементов подогревателя:
-расчет толщины стенки подогревателя стр.15
Список использованной литературы стр.17
Прнинципиальная тепл.сх. 520МВт(РАМОР).dwg

Расчёт тепловой схемы РАМОР.doc
1. Построение процесса расширения пара в турбине.
Р0=235 МПа t0=560 0C h0= 33878 кДжкг S0= 62645 кДж(кгК)
Р2=01Рпп+ Рпп=01358+358=3938 МПа S2= S0 t2а=27894 0C
H0ЦВД= h0- h2а=33878 – 29022 = 4856 кДжкг
HiЦВД=oiЦВДH0ЦВД=0854856 = 41276 кДжкг
h2= h0- HiЦВД= 33878 – 41276 = 297504 кДжкг
По Р2 и h2 по таблице воды и водяного пара находим t2 :
Рпп=358 МПа tпп=560 0C hпп= 35869 кДжкг Sпп=73176 кДж(кгК)
Точка выхода пара из ЦСД:
РкЦСД=005Рпп=005358=0179 МПа
oiЦСД=087 SкЦСДа= 73176 кДж(кгК) hаЦСД=27633кДжкг
H0ЦСД=hпп-hаЦСД= 35869 – 27633= 8236 кДжкг
HiЦСД=oiЦСДH0ЦСД=0878236 = 716532 кДжкг
hкЦСД= hпп- HiЦСД= 35869 – 716532 = 2870368 кДжкг
SкЦСД=75579 кДж(кгК) tкЦСД=1993 0C
Рк=33 кПа tк=25677 0C
Т.к. Sка = SкЦСД находим hка опускаясь из точки кЦСД по линии S=const до пересечения с давлением Рк
hка= 2252 кДжкг Sка= 75579 кДж(кгК)
oiЦНД=081 H0ЦНД= hкЦСД-hка= 2870368 – 2252 = 618368 кДжкг
HiЦНД=оiЦНДH0ЦНД=081618368 = 50088 кДжкг
hk= hкЦСД- HiЦНД= 2870368 – 50088 = 236949 кДжкг
Точка К: (по давлению в конденсаторе находим энтропию и температуру конденсата):
Рк=33 кПа ts=25677 0C h к= 10767 кДжкг
2. Определение параметров пара и воды в группе ПВД.
2.1 Первая ступень ПВД (П1):
Известно что температура воды за подогревателем высокого давления № 1(П1) равна температуре питательной воды: tв1=tпв=268 0C а давление за П1 будет равно
Потеря давления в каждом ПВД составляет : Рпвд =05 МПа
Потеря давления в РПК: Ррпк =5 МПа
Потеря давления в трубопроводах котла: Ррпк =15 МПа
Рв1 = 235 + 5 + 15 Рв1 =30 МПа
По температуре tв1 и давлению Рв1 по таблице теплофизических свойств воды и водяного пара находим: h в1 = 1172.1 кДжкг
Температура питательной воды за П1 будет ниже температуры насыщения в П1 на величину недогрева =15 0C. Таким образом температура насыщения в П1 будет равна: tн1=tпв + =268+15=2695 0C. Зная температуру насыщения греющего пара найдем давление греющего пара:
Энтальпия греющего пара:
Находим параметры (давление) пара в отборе турбины приняв потерю давления в паропроводе 5%:
Р1=105Рн1=105546 = 5733 МПа
По диаграмме расширении пара (h-s диаграмма) находим температуру и энтальпию пара в отборе турбины:
t1=35475 0C h1=3064 кДжкг
2.2. Вторая ступень ПВД (П2):
Греющий пар для П2 отбирается из «холодной» нитки промежуточного перегрева пара. Давление насыщения пара в П2 будет меньше давления пара на выходе из ЦВД на 5% (за счет сопротивления паропровода).
Давление насыщения пара в П2:
Рн2=Р2095=3938095 = 374 МПа
По давлению насыщения Рн2 находим температуру и энтальпию пара в П2:
tн2=2464 0C hн2 = 10682 кДжкг
Температура воды за П2 будет ниже чем tн2 на величину недогрева =15 0C:
tв2=tн2-=2464-15=2449 0C
Давление за подогревателем принимается с учётом потерь в подогревателе ПВД 3:
Рв2 = Р0 + Ррпк + Ртр + Рпвд
По давлению Рв2 и температуре tв2 по таблице теплофизических свойств воды и водяного пара находим энтальпию воды за П2:
2.3. Третья ступень ПВД (П3):
Определим энтальпию питательной воды за ПН. Давление воды на входе в питательный насос равно давлению на выходе из деаэратора а т.к. вода на входе в ПН находится в состоянии насыщения то температуру воды на входе в ПН ищем по давлению насыщения воды которая нам известна:
По Рвдпв = 0.69 МПа и tвдпв = 164 оС находим удельный объём питательной воды на входе в насос до пн = 0001107 м3кг
По Рпн = 315 МПа и tпн = 164 оС находим удельный объём питательной воды после питательного насоса после пн = 0001085 м3кг
Рд=069 МПа – давление в деаэраторе с помощью которого по таблице теплофизических свойств воды и водяного пара находим энтальпию насыщения в деаэраторе: hд =6929 кДжкг
– средний удельный объем воды в ПН
ПН=085 – КПД питательного насоса
Нагрев воды в питательном насосе:
tпн=( ср (Рпн – Рд))*1000 ПН=(0001096(315-069))*1000085=3976 кДжкг
Энтальпия питательной воды за ПН:
hв.ПН=tпн+hд где hд – энтальпия воды в деаэраторе при P = 0.69 МПа и t =164 0C
hв.ПН = 3976 + 6929 = 73266 кДжкг
По давлению Рпн и энтальпии hв.ПН по таблице теплофизических свойств воды и водяного пара находим более точную температуру воды на выходе из ПН:
Для нахождения параметров за П3 составим систему уравнений
Обеспечение подогрева воды паром из «холодной нитки» энергетически более выгодно чем из «горячей нитки» тогда:
+ 3= hв2- hвПН=1065 – 73266 = 33234 кДжкг
Решая эту систему получим:
= 20452 кДжкг – нагрев воды в П2
= 12782 кДжкг – нагрев воды в П3
Параметры питательной воды за П3:
hв3= hвПН + 3=73266 + 12782 = 86048 кДжкг
Рв3= Рв2 + Рпвд = 31 МПа
По Рв3 и tв3 по таблице теплофизических свойств воды и водяного пара находим температуру воды за П3:
Температура воды за П3 будет ниже чем tн3 на величину недогрева =15 0C:
Температура пара в П3:
tн3=tв3 + = 19882 + 15 = 20032 0C
Давление греющего пара также ищем по таблице теплофизических свойств воды и водяного пара по tн3 :
Рн3= 156 МПа а по Рн3 и tн3 находим энтальпию пара в П3:
Параметры пара в отборе:
Р3=105Рн3=105156 = 164 МПа - с учетом потерь давления в паропроводе (5%)
t3=44503 0C - из h-s диаграммы по известному давлению
3. Определение дренажей группы ПВД.
од=10 0C - температурный напор на холодном конце в охладителе дренажа
tдр3=tвПН+ од=16904+10 = 17904 0C
tдр2=tв3+ од=19882 + 10 = 20882 0C
tдр1=tв2+ од=2449 + 10 = 2549 0C
По известным температуре и давлениям в подогревателях определяем энтальпии дренажей:
4. Определение параметров пара воды и дренажей группы ПНД.
Рассмотрим распределение регенеративного подогрева группы ПНД.
Выберем способ распределения подогрева в ПНД: способ равномерного подогрева по ступеням.Для подогревателей смешивающего типа недогрев равен 00C. При расчете ПНД учитывалось то что деаэратор входит в число ПНД.
Недогрев в ПНД поверхностного типа принимаем равным 450C
Давление создаваемое конденсатным насосом можно принять равным давлению в деаэраторе с учетом потерь при сопротивлении конденсата в самих ПНД и давления необходимого для поднятия конденсата на нивелирный уровень Д.
Напор конденсатного насоса второй ступени можно рассчитать следующим образом:
Ркн2=Рд + 4·Рсопр_пнд + Рнив =069+4·01+022= 131 МПа
Параметры конденсата на выходе из конденсатора:
tк=25677 0CРк=00033 МПаhк=10767 кДжкг
Т.к. деаэратор можно принять за подогреватель смешивающего типа значит hД = hвД т.к. в подогревателях смешивающего типа недогрев не учитывается.
Подогрев приходящийся на каждую ступень ПНД:
пнд=(hд-h`к)5=(6929-10767)5=11704 кДжкг
4.1. Подогреватель П8 (поверхностного типа).
Энтальпия конденсата за П8:
hв8=h`к+ пнд=10767+11704 = 22471 кДжкг
tв8=5343 0C - по таблице теплофизических свойств воды и водяного пара по энтальпии воды и давлению Ркн2 минус Рсопр_пнд находим давление воды за П8:
Параметры воды за подогревателем поверхностного типа принимаются равными параметрам пара в подогревателе с учётом недогрева в ПНД:
Температура греющего пара в П8:
tН8=5343 + 45 = 5793 0C
По tН8 по таблице воды и водяного пара находим давление и энтальпию пара в П8:
Рн8 =0018 МПа hн8= 2425 кДжкг
Р8=105Рн8=1050018=00189 МПа
t8=5884 0C - из h-s диаграммы по известному давлению
4.2. Подогреватель П7 (поверхностного типа).
Энтальпия конденсата за П7 равна:
hв7=hв8+ пнд= 22471+11704 = 34175 кДжкг
tв7= 8142 0C - по таблице теплофизических свойств воды и водяного пара по энтальпии воды и давлению Ркн2 минус 2·Pсопр_пнд находим давление воды за П7:
Параметры в подогревателе:
tн7 = tв7 + 450C = 8142+45 =8592 0C
Рн7=0059 МПа hн7 =3598 кДжкг
Р7=105Рн7=1050059 = 0062 МПа
t7=11571 0C - из h-s диаграммы по известному давлению
4.3. Подогреватель П6 (поверхностного типа).
Рв6=Ркн3-3·Рсопр_пнд=131-3·01=101 МПа
hв6=hв7+ пнд= 34175 +11704 = 45879 кДжкг
По hв6 и Рв6 по таблице воды и водяного пара находим:
Недогрев в ПНД принимаем: =45 0C
Температура греющего пара в П6:
tн6=tв6+=10924+45=11374 0C
По таблице теплофизических свойств воды и водяного пара по известной температуре находим давление и энтальпию пара в ПНД6:
Рн6=016 МПаhн6=47721 кДжкг
Р6=105Рн6=105016=0168 МПа - с учетом потерь давления в паропроводе (5%)
t6=19186 0C - из h-s диаграммы по известному давлению
4.4. Подогреватель П5 (поверхностного типа).
hв5=hв6+ пнд= 45879 +11704 = 57583 кДжкг
По таблице теплофизических свойств воды и водяного пара по энтальпии воды и давлению Рв5 =091 МПа находим температуру воды за П5:
Температура греющего пара в П5:
tн5=tв5+=13679+45=14129 0C
По таблице теплофизических свойств воды и водяного пара по известной температуре находим давление и энтальпию пара в ПНД5 :
Рн5=0375 МПаhн5=59474 кДжкг
Р5=105Рн5=1050375=0394 МПа
t5=27889 0C - из h-s диаграммы по известному давлению
По t находим остальные параметры на линии насыщения:
4.5. Подогреватель П4 (деаэратор).
Рн4 находим по таблице воды и водяного пара по известной температуре насыщения tн4
Р4 = 105·069 = 0724 МПа
t4=34635 0C - из h-s диаграммы по известному
5. Решение уравнений теплового баланса теплообменников определение расхода пара на каждый теплообменник и в конденсатор.
α0=1 - доля расхода в ЦВД турбины
αут=002 - доля утечек пара
αдв=αут=002 - доля добавочной воды для восполнения потерь утечек
5.1. Подогреватель П1.
aп.в = aо + aут = 1 + 0.02 = 1.02
a1(h1 - hдр1) = aп.в(hв1 – hв2) Примем hп = 0.985
5.2. Подогреватель П2.
a2(h2 - hдр2) + a1(hдр1 - hдр2) = aпв(hв2 – hв3)
5.3. Подогреватель П3.
a3h3h+ (a1+a2) hдр2h + aп.вhвпн = aп.вhв3 +(a1+a2+a3) hдр3h
a3 =aп.вhв3 – (a1+a2) hдр2h - aп.вhвпн + (a1+a2) hдр3h (h3 - hдр3 ) h
5.4.Отбор на приводную турбину.
Здесь hнi = 0.85 hмтп = 0.99
Теплоперепад на приводной турбине Hiтп = h3 - hктп
Потери давления пара при дросселировании в арматуре подвода пара к приводной турбине примем равным 5 % те давление пара в голову приводной турбины: Ротп = 0.95 Р3 = 0.95164 = 1558 МПа.
Примем hоiтп = 0.84 тогда внутренний теплоперепад Hiтп = Hотп hоiтп = (h3 – hкттп) hоiтп hкттп определим по h s – диаграмме опускаясь от точки с параметрами Ротп hотп = h3 по линии S = const до пересечения с давлением Рктп = 4 кПа hкттп = 2232 кДжкг
Hiтп = (3352 – 2232)0.84 = 9408 кДжкг
По Ротп и h3 по таблице воды и водяного пара находим tотп :
Действительное значение энтальпии hктп турбопривода:
hктп = h3 - Hiтп = 3352 – 9408 = 24112 кДжкг
По Рктп и hктп по таблице воды и водяного пара находим tктп :
5.5. Деаэратор питательной воды(П4).
Уравнение материального баланса:
αпв=( α1+ α2+ α3)+ αд+ αок
Уравнение теплового баланса:
αпвh`д= ( α1+ α2+ α3)hдр3 + αдh4+ αокhок
Pок = Pв5 – Pнив = 091-022 = 069 МПа
tок = tв5 = 136.79 0C
По таблице воды и водяного пара по известным нам Pок и tок находим hок
Решая систему из двух уравнений находим долю расхода пара на деаэратор:
αок = (αпвh`д - ( α1+ α2+ α3)hдр3 - αдh4) hок
αд = 08243 – (αпвh`д + ( α1+ α2+ α3)hдр3 + αдh4) hок
αд = (08243· hок - αпвh`д + ( α1+ α2+ α3)hдр3) (hок - h4 )
αд = (08243·57567-102·6929+(00567+00958+00432)·75928)(57567-3156)
Доля расхода основного конденсата:
5.6. Подогреватель П5.
α5(h5-hдр5) = αок(hв5-hв6)
5.7. Подогреватель П6.
[α6(h6-hдр6)+ α5(hдр5-hдр6)]= αок(hв6-hв7)
5.8. Подогреватели П7 и П8.
Уравнение теплового баланса подогревателя:
Уравнение теплового баланса точки смешения:
Уравнение материального баланса точки смешения:
Решая систему из четырёх уравнений находим
6. Контроль материального баланса пара и конденсата.
αк=αок- α5-α6-α7- α8=07913-00389-00426-0035-0027= 06478
Пропуск пара в конденсатор:
αвх-к=α0- α1- α2- α3-αд-αтп - α5-α6-α7- α8 =1-00567-00958-00432-0033-00435-00389-00426-0035-0027=05843
Поток конденсата из конденсатора:
αвых_к=αвх_к+αд.в + αтп =05843+002+00435= 06478
Погрешность сведения материального баланса:
Доля пропуска пара через отсек a
Теплоперепад в отсеке H кДжкг
Внутренняя работа пара в отсеке aH кДжкг
h0-h1=33878-3064=3238
h1-h2=3064-297504=8896
-a1-a2=1-00567-00958= 08475
hпп-h3=35869-3352=2349
-a1-a2-a3-aтп=1-00567-00958-00432-00435= 07608
-a1-a2-a3-aтп-aд=1-00567-00958-00432-00435-0033= 07278
-a1-a2-a3-aтп-aд-a5=1-00567-00958-00432-00435-0033-00389= 06889
-a1-a2-a3-aтп-aд-a5-a6=1-00567-00958-00432-00435-0033-00389-00426= 06463
-a1-a2-a3-aтп-aд-a5-a6-a7=1-00567-00958-00432-00435-0035-00389-00426-0035= 06113
-a1-a2-a3-aтп-aд-a5-a6-a7-a8=1-00567-00958-00432-00435-0033-00389-00426-0035-0027= 05843
h8-hк=2560-236949=19051
7. Энергетическое уравнение и определение расходов пара и воды.
Таблица для расчета приведенного теплоперепада Hпр:
Обозначим сумму αiHij= 126493 кДжкг через: S αiHij
Расход пара на турбину:
Удельный расход пара на турбину:
8. Энергетические показатели энергоблока.
Полный расход теплоты на турбоустановку :
hпв=hв1=1172.1 кДжкг
Qту=D0(h0-hпв)+Dпп(hпп-h2)=
=419433600(33878-11721)+355463600(35869-297504)=4128 ГДжч
Удельный расход теплоты турбоустановки на выработку электроэнергии:
КПД турбоустановки по выработке электроэнергии:
Тепловая нагрузка парового котла:
hпе=33878 кДжкг- при давлении и температуре свежего пара: Pпе=235 МПа tпе=560
hп.в_п.к=hпв=11721 кДжкг
hп.п_0.п.к=297504 кДжкг - при давлении и температуре пара перед пп: Pпе=3938 МПа tпе=30405
hп.п_п.к=35869 кДжкг - при давлении и температуре пара после пп: Pпе=358 МПа tпе=560
Qпк= Dпк(hпе-hпв_пк)+Dпп(hпп_пк-hпп_0.пк) =
=427813600 (33878-11721)+ 355463600(35869-297504) =4195 ГДжч
КПД транспорта теплоты:
Количество теплоты топлива на паровой котел:
Задамся КПД парового котла
КПД энергоблока брутто:
КПД энергоблока нетто:
Удельный расход теплоты энергоблока нетто:
Часовые расходы условного и натурального топлива:
Удельный расход условного топлива нетто:
Описание тепл.схемы 520МВт (РАМОР).doc
Конденсационный энергоблок 520 МВт предназначен преимущественно для установки на крупных ГРЭС работающих на твердом топливе.
Паровой котел спроектированный мною выполнен по Т-образной компоновке с 24 вихревыми горелками при шести молотковых мельницах производительностью 44 тч. Номинальная производительность котла 41943 кгс (150995 тч) давление и температура перегретого пара за котлом 235 МПа и 5600С.
Конденсационная паровая турбина К-520-235 одновальная работает с электрогенератором ТВВ-520. Турбина состоит из ЦВД ЦСД и двух двухпоточных ЦНД. Расход свежего пара на турбину 41943 кгс (150995 тч); параметры свежего пара 235 МПа 5600С.
Конденсатор турбоустановки типа К-11520 приварен к 4 выхлопам ЦНД. Его паровое пространство разделено перегородкой. Что позволяет осуществить двухступенчатую конденсацию пара. Потери рабочего тела основного энергоблока восполняются добавкой обессоленной воды из химической водоочистки.
Вакуум в конденсаторе поддерживается изменением числа включенных насосов а также поворотом рабочих лопаток насосов.
Турбина имеет 8 нерегулируемых отборов пара для регенеративного подогрева питательной воды. Основной конденсат после КН I ступени проходит 100% очистку в БОУ и направляется в конденсатные насосы II ступени. Затем конденсатные насосы II ступени подают конденсат в поверхностные ПНД 8 ПНД7 ПНД6 ПНД5 и деаэратор.
Деаэратор питательной воды ДП-500-1. При нагрузках близких к номинальной деаэратор работает при постоянном давлении 069 МПа.
Питательная установка энергоблока состоит из 2 питательных турбонасосов каждый из которых рассчитан на 50% подачи по воде.
Общий турбинный привод бустерного и питательного насосов от конденсационной турбины имеет переменную частоту вращения для изменения производительности установки по питательной воде.
Группа ПВД выполнена в одну нитку из трех последовательно включенных подогревателей типа ПВ-1800-380-45 без охладителя пара и ПВ-1700-380-58 с пароохладителем и охладителем дренажа. Конденсат греющего пара каскадно сливается в деаэратор. Уровень этого конденсата в каждом ПВД поддерживается регулятором уровня. Воздействующим на клапан дренажной линии. ПВД снабжены общим байпасом защиты и обводной линией «холодного» питания котла при отключении ПВД.
Спец вопрос (Рамор).doc
1. Основные принципы организации поточного монтажа оборудования.
Основным принципом поточного метода строительства и монтажа оборудования является непрерывное и равномерное производство что обеспечивается осуществлением следующих организационно-технологических мероприятий:
-расчленение процессов производства на составляющие процессы;
-разделение труда между исполнителями;
-создание производственного ритма;
-совмещение монтажных процессов во времени и пространстве.
Поточный метод монтажа оборудования может применяться:
-при возведении отдельных энергетических блоков;
-при строительстве всего комплекса электростанций в составе нескольких энергетических блоков;
-при выполнении монтажных работ в период длительного времени на ряде электростанций.
В ряде случаев возникает необходимость смонтировать энергоблок в кротчайшие сроки. Тогда применяется скоростной метод основанный на производстве работ в минимальные технически возможные сроки путём применения наибольшего совмещения работ по времени с организацией работы по скользящему графику в две и три смены для чего привлекается большое количество рабочих.
Поточный метод монтажа обладает достоинствами скоростного метода и поэтому находит наибольшее применение для сооружения электростанции в целом а скоростной монтаж – для ввода одного или двух блоков.
При организации монтажа оборудования на тепловых электростанциях различают следующие разновидности монтажных потоков:
Частный поток - элементарный поток представляющий собой последовательное выполнение одного простого процесса на ряде узлов агрегата;
Специализированный поток – совокупность частных потоков объединённых единой системой для завершения монтажа агрегата (например турбины; котельного агрегата и др.);
Объектный поток – совокупность специализированных потоков обеспечивающих завершение монтажа всего оборудования энергетического блока;
Комплексный поток – группа организационно связанных объектных потоков обеспечивающих завершение монтажа оборудования электростанций в целом.
В монтажной практике специализированные потоки называются также продольными потоками когда оборудование главного корпуса монтируется потоками: машинный зал деаэраторная; котельная; оборудование открытой установки (электрофильтры регенеративные воздухоподогреватели тягодутьевая установка).
2. Характеристики поточного метода монтажа.
Потоки делятся на ритмичные и неритмичные а по продолжительности - на краткосрочные и непрерывные когда поток функционирует длительное время (например для монтажа всех энергоблоков одной электростанции).
При монтаже на электростанции нескольких энергоблоков могут также быть и специализированные поперечные потоки когда в один поток включён например монтаж всех трубопроводов высокого давления от питательных насосов к котлоагрегату и паропроводов от него к турбине.
В условиях строительства электростанций применяется стационарно – поточный метод монтажа котельных и турбинных агрегатов когда поток организовывается последовательно в двух местах:
-на сборочной площадке для укрупнения заводских блоков из заводских узлов и деталей;
-на постоянном фундаменте агрегата где производятся установка блоков соединение их с отдельными деталями и оформление законченного агрегата. При этом блоки и узлы в процессе работы над ними кроме подъёма их остаются неподвижными а бригады монтажников постоянно выполняющие определённые циклы работ меняются.
На сборочной площадке имеются два или три параллельных потока оборудованных козловыми кранами для разгрузки сборки и погрузки на транспорт собранных блоков устройствами для резки и сварки и другими приспособлениями необходимыми для производства сборочных работ.
В главном корпусе электростанции организуются три или четыре специализированных потока оборудованных мостовыми кранами для монтажа оборудования всеми устройствами для производства сборочных сварочных и проверочных работ. В каждый поток вводится железнодорожный путь или автодорога для подачи оборудования.
При осуществлении комплексного потока когда одновременно монтируются несколько энергетических блоков рекомендуется организовать следующие специализированные потоки:
-сборки оборудования в укрупнённые блоки на укрупительно – сборочной площадке;
-в главном корпусе монтажа оборудования и трубопроводов машинного зала;
-монтажа оборудования и трубопроводов деаэраторной этажерки;
-монтажа оборудования котельного отделения со всеми трубопроводами;
-монтажа оборудования наружной установки электрофильтров тягодутьевого устройства.
Кроме того в главном корпусе для осуществления подготовки к пуску и опробования всех агрегатов энергетического блока организуется поток пусконаладочных работ (поперечный) который поточно по мере завершения монтажа переходит от одного энергоблока к другому.
Для всего комплекса или очереди монтируемой электростанции параллельно организуются дополнительные специализированные потоки:
-монтажа оборудования топливоподачи;
-монтажа оборудования мазутного хозяйства с трубопроводами от насосной до главного корпуса;
-монтажа оборудования химводоочистки с трубопроводами между ХВО и главным корпусом.
Для поточного монтажа агрегат разбивается на отдельные секции – потоки а весь комплекс работ по монтажу агрегатов расчленяется на частные потокистрого увязанные между собой которые последовательно выполняются закреплёнными специализированными бригадами рабочих постоянного состава оснащёнными грузоподъёмными механизмами механизированным инструментом и приспособлениями. Бригады монтажников выполняют работы последовательно на всех потоках передвигаясь с одного на другой; заканчивая работы на очередном потоке подготавливают тем самым фронт работ для следующей по потоку бригады. Создаётся система цикловых частных потоков из которых слагается общий специализированный поток. При этом работы выполняются в порядке технологической последовательности монтажа агрегата. После разворота монтажа работы ведутся одновременно на всех потоках агрегата. Такая поточная организация создаёт наиболее полное совмещение работ по времени и обеспечивает высокие и устойчивые темпы монтажа.
Особенность выполнения работ на разных частных и специализированных потоках монтажа заключается в том что к определённому периоду – к началу пуска энергоблока должны быть завершены операции на всех потоках опробованы вхолостую все механизмы промыты и продуты все трубопроводы блока.
Для выполнения монтажных работ на перечисленных потоках выделяются отдельные мастера прорабы а для крупных объектов – и отдельные самостоятельные участки.
Поточный монтаж оборудования характеризуется системой показателей связанных между собой и определяемых как для специализированных объектных комплексных так и частных потоков.
Основными расчётными параметрами монтажных потоков являются:
Интенсивность потока – количество работ выполняемых потоком за единицу времени измеренное в натуральных показателях или масса оборудования смонтированного поточным методом за определённое время.
Интенсивность потока IТ (тмес) определяется по следующей формуле:
где PОБ – общая масса оборудования подлежащего монтажу (т); ТП – нормативная продолжительность монтажных работ (мес).
Продолжительность потока – период выполнения работ объём трудоёмкость работ;
Ритм потока – время выполнения частного потока;
Шаг потока – время через которое последовательно начинается монтаж отдельных агрегатов:
t = Тобщ – Тперв n – 1
где t – шаг потока (мес); Тобщ – общая продолжительность монтажа всех агрегатов (мес); Тперв – продолжительность монтажа первого агрегата (мес); n – количество агрегатов подлежащих монтажу.
При поточном монтаже обеспечивается непрерывная и равномерная загрузка рабочих за счёт ликвидации перерывов и простоев при производстве работ а также повторяемость производственных процессов при монтаже последующих однотипных агрегатов. Приобретаются навыки снижается трудоёмкость монтажных работ и возрастает производительность труда.
3. График движения рабочей силы.
В отличие от графиков движения рабочей силы для монтажа отдельных энергоблоков имеющих выпуклую кривую для поточного монтажа график имеет форму трапеции с постоянным составом рабочих.
При монтаже энергетических блоков непрерывным потоком для составления графиков следует определить наивыгоднейшую продолжительность и необходимое наименьшее количество рабочих.
В основу расчётов принимаются суммарные трудовые затраты монтажа энергетических блоков участвующих в потоке.
При поточном строительстве число рабочих в период у3становившегося потока определяется по формуле:
где Т – продолжительность потока (дни); Qобщ – суммарная трудоёмкость на всех объектах данного потока (чел-дни); - коэффициент обозначающий отрезки времени через которое число рабочих увеличивается в среднем на одного.
Для строительства ТЭС коэффициент колеблется от 012 до 018; для монтажа оборудования может быть принят 014 – 016.
Период наращивания числа работников: (дни).
Рис. 5.3 График движения рабочей силы
4. Организация поточного монтажа на примере ГРЭС мощностью 4000МВт (8 блоков по 500МВт).
Характеристики энергоблоков 500МВт:
Наименование оборудования
Количество комплексов
Тягодутьевое устройство
Станционное оборудование
Станционные трубопроводы
Мостовые краны (котельной машинного зала дымососной РВП и др.)
Склад угля и топливоподачи
Прочие общестанционные объекты
Технологические металлоконструкции связанные с монтажом оборудования:
-по котельному отделению
-по деаэраторной установке
Итого металлоконструкций
Всего оборудования и металлоконструкций
Поточный монтаж энергоблоков 500МВт организуется исходя из следующих основных принципов.
Все монтажные работы выполняются в непрерывном по времени потоке.
Подготовительные работы по оборудованию включая разгрузку хранение комплектацию и укрупнительную сборку в блоки выполняются в централизованной базе где осваивается не менее 30% всех трудозатрат на монтажные работы.
Доставка блоков с базы на электростанции к месту монтажа производится железнодорожным и большегрузным автотранспортом.
Монтажные работы производятся в полностью законченном главном корпусе закрытом и отопляемым в зимнее время.
Совмещение строительных и монтажных работ допустимо только для установки на проектные места отдельных крупногабаритных узлов оборудования осуществляемой строительными кранами.
Монтаж оборудования котельного отделения выполняется мостовыми кранами грузоподъёмностью 50т.
Коэффициент монтажной блочности намечается довести до 095 – 097 при средней массе блока не ниже расчётной для данного котельного агрегата.
Монтажные блоки следует укомплектовать приспособлениями для строповки кантовки и подъёма.
4.1. Потоки монтажа оборудования для ГРЭС 4000МВт.
Для осуществления поточного монтажа технологического оборудования трубопроводов и металлоконструкций связанных с ними организуются следующие специализированные потоки:
Первый поток – машинный зал; турбоустановка; БОУ; металлоконструкции вокруг турбоустановки; грузоподъёмные механизмы; станционные трубопроводы высокого и низкого давления.
Второй поток – деаэраторная этажерка; станционное оборудование; технологические металлоконструкции; станционные трубопроводы высокого и низкого давления.
Третий поток – котельное отделение; котельные агрегаты; пылеприготовление; газовоздухопроводы; топливоподача; гидрозолоудаление; станционные трубопроводы высокого и низкого давления; грузоподъёмные механизмы; металлоконструкции.
Четвёртый поток – установка регенеративных воздухоподогревателей; оборудование воздухоподогревателей; газовоздухопроводы; топливоподача; грузоподъёмные механизмы; металлоконструкции.
Пятый поток – газоочистка и тягодутьевые машины; электрофильтры; тягодутьевые машины и газовоздухопроводы; грузоподъёмные машины; металлоконструкции.
Шестой поток – химводоочистка; оборудование и трубопроводы ХВО; оборудование и трубопроводы прочих вспомогательных цехов.
Седьмой поток – склад угля и топливоподача; краны для склада топлива и топливоподача главного корпуса; оборудование прочих общестанционных объектов.
Дополнительно в потоки включаются конструкции для обмуровки котлоагрегатов и тепловая изоляция оборудования и трубопроводов.
4.2. График поточного монтажа энергоблоков 500МВт.
Продолжительность монтажа проверяется в зависимости от общих трудовых затрат на месте монтажа для одного блока по формуле:
где R – коэффициент номинальной продолжительности:
где - трудозатраты на монтажной площадке с учётом выполнения 30% на базе.
Продолжительность монтажа измеряется в рабочих днях а если измеренное в днях разделить на число 212 получим измеренное в месяцах. Число 212 – количество рабочих дней в месяце по пятидневной неделе.
Учитывая принятый режим работы на монтажной площадке корректируем продолжительность монтажа по следующей формуле:
где - продолжительность монтажа при семидневной рабочей неделе (мес); - доля времени работы по семидневной рабочей неделе.
Продолжительность монтажа для первого блока:
где =185-195 - наиболее эффективный коэффициент совмещения для поточного монтажа;
Общая продолжительность монтажа всех энергоблоков:
Определяем потребность в рабочей силе по формуле для поточного монтажа учитывающей равномерное количество рабочих для всего периода монтажа:
где Т – продолжительность потока (дни); - коэффициент обозначающий отрезки времени через которое число рабочих увеличивается в среднем на одного.
Период увеличения числа рабочих:
Ритмичность монтажа в потоке восьми энергоблоков проверяем по формуле коэффициента ритмичности с учётом того что каждый блок вводится в одном квартале года:
Интенсивность потока:
Как видно из графика поточного монтажа энергоблоков 500МВт первый блок не может быть пущен в первый год начала производства монтажных работ но в последующие годы обеспечиваются монтаж и пуск по два и три блока ежегодно.
В графике поточного монтажа ( для упрощения) трудозатраты и продолжительность монтажа приняты для всех блоков кроме первого одинаковыми.
Спец Вопрос (РАМОР).dwg

Схема 1: Потоки монтажа оборудования для ГРЭС 4000МВт
Схемы и графики поточного монтажа для ГРЭС 4000МВт
Продолжительность монтажа
Схема 2: График поточного монтажа энергоблоков 500МВт