Тепловой и динамический расчет двигателя ВАЗ-1111 (1113)



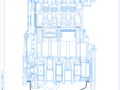
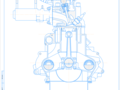
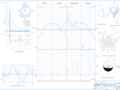
- Добавлен: 25.01.2023
- Размер: 776 KB
- Закачек: 1
Описание
Состав проекта
![]() |
![]() ![]() ![]() |
![]() ![]() ![]() ![]() |
![]() ![]() ![]() ![]() |
![]() ![]() ![]() ![]() |
Дополнительная информация
КУРСАЧ.docx
Государственное образование учреждение высшего профессионального образования
Ижевский государственный технический университет
ПОЯСНИТЕЛЬНАЯ ЗАПИСКА:
к курсовой работе по дисциплине:
«Двигатели внутреннего сгорания»
на тему «Тепловой и динамический расчет двигателя»
Тепловой расчет . . . 4
1 Процесс впуска .. . 7
2 Процесс сжатия . . 10
3 Процесс сгорания . 12
4 Процесс расширения и выпуска . .. 16
5 Индикаторные параметры рабочего цикла . 18
6 Эффективные показатели двигателя . 19
7 Основные параметры цилиндра и двигателя .. . 21
8 Построение индикаторной диаграммы .. . 23
9 Тепловой баланс двигателя . . . 27
1 Индикаторная диаграмма .. 29
Мощность двигателя Ne = 25 кВт;
Частота вращения коленчатого вала nN = 5700 обмин;
Тактность двигателя = 4;
Количество цилиндров
Степень сжатия = 99;
Тип охлаждения – жидкостное.
Режимы для проведения теплового расчета:
а) режим минимальной частоты вращения nmin = 1000 обмин.
б) режим максимального крутящего момента nM =056nM = 3200 обмин.
в) режим максимальной (номинальной) мощности nN = 5700 обмин.
г) режим максимальной скорости движения nmax = 1105nN = 6000 обмин.
четырехтактный бензиновый карбюраторный
Число и расположение цилиндров
Диаметр цилиндра и ход поршня
Номинальная мощность при частоте вращения коленчатого вала 5600 обмин по ГОСТ 14846—81 (нетто) кВт (л.с.)
Максимальный крутящий момент при частоте вращения коленчатого вала 3200 обмин по ГОСТ 14846—81 (нетто) Н.м(кгс. м)
Тепловой расчет двигателя
Расчет проводится для заданной частоты вращения коленчатого вала карбюраторного двигателя n = 5700 обмин.
Топливо. В соответствии с заданной степенью сжатия = 99 можно использовать бензин марки АИ-93.
Средний элементарный состав и молекулярная масса бензина
С = 0855; Н = 0145; T= 115 кгкмоль.
Определим низшую теплоту сгорания топлива
Параметры рабочего тела. Теоретическое необходимое количество воздуха для сгорания 1кг. топлива
Коэффициент избытка воздуха α = 096 на основных режимах (литература 1). На режимах минимальной частоты вращения α = 086.
Количество горючей смеси.
При n = 3200 5700 6000 обмин
Количество отдельных компонентов продуктов сгорания при К = 05 (отношения количества киломолей водорода к количеству киломолей окиси углерода) и принятых скоростных режимах:
При n = 1000 обмин:
[кмольСО2кг топлива].
[кмольСОкг топлива].
= 00625 [кмольН2 Окг топлива].
= 00100 [кмольН2 кг топлива].
[кмольN2кг топлива].
При n = 3200 5700 6000 обмин:
= 00655 [кмольСО2 кг топлива].
= 00696 [кмольН2 Окг топлива].
= 00029 [кмольН2 кг топлива]. [кмольN2 кг топлива].
Общее количество продуктов сгорания:
М2 = МСО2 + МСО + МН2О + МН2 + МN2 = C12 + H2 + 079αL0 = 00512 + 002 + 00625 + 001 + 03515 = 04952 [кмоль пр.сгор кг топлива].
М2 = МСО2 + МСО + МН2О + МН2 + МN2 = C12 + H2 + 079αL0 = 00655 + 00057 + 00696 +00029+03923 = 05360 [кмоль пр.сгор кг топлива].
Проверка: М2 = 081512 + 01452 + 0792*096*0516 = 05360.
Результаты занесем в таблицу
Рабочее тело; Карбюраторный двигатель
[кмоль гор.смеси кг топлива].
[кмольСО2кг топлива].
[кмольН2Окг топлива].
[кмольН2 кг топлива].
[кмольN2 кг топлива].
[кмоль пр.сгор кг топлива].
Параметры окружающей среды и остаточные газы.
Давление и температура окружающей среды при работе двигателей без наддува Рк = Ро = 01 МПа и Тк = То = 293 К.
Температура остаточных газов.
При постоянном значении степени сжатия = 99 температура остаточных газов практически линейно возрастает с увеличением скоростного режима при постоянном коэффициенте избытка воздуха но уменьшается при обогащении смеси. Учитывая что при n = 1000 обмин α = 086 а на остальных режимах - α = 096 принимается:
Давление остаточных газов.
Для карбюраторного двигателя на номинальном скоростном режиме:
PrN = 118 Po = 118 01 = 0118 МПа.
pr = p0(1035+ Ap 108 n2)
Ap=(prN p0 1035) 108(nN2p0) = (0118 – 01 1035)108(56002*02)=04624
Температура подогрева свежего заряда. С целью получения хорошего наполнения карбюраторных двигателей на номинальных скоростных режимах принимается Δ ТN = 8ºС. Тогда
T = AT (110 – 00125n) = 22 – 00025n
где AT = TN (110 – 00125nN) = 02;
Плотность заряда на выпуске.
ρr = Ро 106 (RBTO) = 01 106 (287 293) = 1189 кг м3
где RB = 287 Дж(кг. градус) – удельная газовая постоянная для воздуха.
Потери давления на впуске.
В соответствии со скоростными режимами (n = 5700 мин–1) и при учёте качественной обработки внутренних поверхностей впускных систем можно принять для карбюраторного двигателя 2 +вп =28 и вп =95 мс ( – коэффициент затухания скорости движения заряда в рассматриваемом сечении цилиндра ВП – коэффициент сопротивления впускной системы отнесенный к наиболее узкому ее сечению ВП – средняя скорость движения заряда в наименьшем сечении впускной системы).
Тогда Ра на всех скоростных режимах двигателей рассчитывается по формуле:
ΔРа = (2 + вп) Аn2n2 ρr*10-62
где Аn = вп nN = 95 5700 = 001667
При n = 5700 ΔРа = 28 * 0016672 * 57002 * 1189 * 10-6 2 = 00155
Давление в конце пуска.
Коэффициент остаточных газов.
где φоч – коэффициент очистки
φдоз – коэффициент дозарядки на номинальном скоростном режиме.
Температура в конце впуска.
Та = (То + ΔТ + γr T) (1 + γr)
При n = 5700 Та = (293+8+00413*1060)(1+00413) = 344810413 = 331 К.
Коэффициент наполнения.
Результаты вычислений занесем в таблицу 1.
Таблица 1. Результаты исследования процесса пуска и газообмена
Процесс впуска и газообмена
Средний показатель адиабаты сжатия k1 (при = 99 а также рассчитанных значениях Та) определяется по номограмме а средний показатель политропы сжатия n1 принимается несколько меньше k1. При выборе n1 учитывается что с уменьшением частоты вращения теплоотдача от газов в стенки цилиндра увеличивается а n1 уменьшается по сравнению с k1 более значительно.
Давление в конце сжатия.
При n = 5700 мин-1 Рс = 00845*991376 = 19095 МПа.
Температура в конце сжатия.
При n = 5700 мин-1 Тс = 331 991376-1 = 756 К.
Средняя мольная теплоемкость в конце сжатия.
а) свежей смеси (воздуха)
6 + 2638 * 10-3 tc где tc = Тс - 273 ºС
определяется методом интерполяции по таблице.
При n = 5700 мин-1 α = 086 и tc = 483 ºС
) = 23303+(23450 – 23303)*001005 = 23332 кДж(кмоль град)
где 23303 и 23450 – значения теплоёмкости продуктов сгорания при 400 °С соответственно взятые из таблицы.
) = 23707+(23867 – 23707)* 001005 = 23332 кДж(кмоль град)
) = 23332 +(23332 – 23332)* 83100 = 23689 кДж(кмоль град).
При n = 5700 мин-1 α = 086 и tc = 483 ºС.
) = кДж(кмоль градус).
Результаты вычислений заносим в таблицу 2.
Таблица 2. Результаты исследования процесса сжатия
Коэффициент молекулярного изменения горючей смеси:
Коэффициент молекулярного изменения рабочей смеси:
Количество теплоты потерянное вследствие химической неполноты сгорания:
ΔНu = 119950*(1-α)*L0 кДжкг.
При n = 5700 мин-1 ΔНu = 119950*(1-096)*0516 = 2476 кДжкг
Теплота сгорания рабочей смеси:
Нраб.см. = кДжкмоль раб.см
При n = 5700 мин-1 Нраб.см. кДжкмоль раб.см
Средняя мольная теплоемкость продуктов сгорания:
Определяется по эмпирическим формулам:
При n = 1000 мин-1 ) = [кДжкмоль раб.см]
При n = 3200 5700 6000 мин-1 ) = [кДжкмоль раб.см]
При проведении расчётов двигателя z выбирается по опытным данным в зависимости от конструктивных особенностей двигателя. На рисунке 1.1 приведена достаточно реальная зависимость z от скоростного режима двигателя исходя из чего величина коэффициента использования теплоты для карбюраторного двигателя c = 091 при nN = 5700 мин–1. Поэтому же рисунку определяем значения z для всех расчётных режимов.
Температура в конце видимого процесса сгорания
z Нраб.см + (m) tc = (m)tz
Максимальное давление сгорания теоретическое
Максимальное давление сгорания действительное
Степень повышения давления
Результаты вычислений сведём в таблицу:
Таблица 3. Результаты исследования процесса сгорания.
Процессы расширения и выпуска
Средний показатель адиабаты расширения k2 определяется по номограмме при заданном = 99 для соответствующих значений α и Tz а средний показатель политропы расширения n2 оценивается по величине среднего показателя адиабаты:
Давление и температура в конце процесса расширения:
При n = 5700 мин-1 Рв = Pz n2=76596991252 = 04326 Мпа
Тв = Tz n2-1=2859990253=1601 К
Проверка ранее принятой температуры остаточных газов:
При n = 1000 мин-1 TrК ΔТr = -47%
При n = 3200 мин-1 TrК ΔТr = 15%
При n = 5700 мин-1 TrК ΔТr = 20%
При n = 6000 мин-1 TrК ΔТr = -41%
Где Δ Тr – погрешность расчета 5 % – допустимая погрешность. На всех скоростных режимах температура остаточных газов принята достаточно удачно.
Результаты расчетов приведены в таблице 4:
Таблица 4. Результаты исследования процесса расширения и впуска.
Процесс расширения и выпуска
Индикаторные параметры рабочего цикла
Теоретическое среднее индикаторное давление:
При n = 5700 мин-1 =
Среднее индикаторное давление
Pi = φu Рj’ где φu = 096 – коэффициент полноты индикаторной диаграммы.
При n = 5700 мин-1 Pi = 096*09442 = 09064 МПа.
Индикаторный КПД и индикаторный удельный расход топлива
Эффективные показатели двигателя
Среднее давление механических потерь для бензиновых двигателей с числом цилиндров до шести и отношением SD≤1.
Pм = 0034 + 00113Vп.ср МПа.
Для нашего карбюраторного двигателя предварительно приняв ход поршня S равным 78 мм. получим значения средних скоростей поршня:
При n = 5700 мин-1 мс.
Тогда: Pм = 0034 + 00113*1482 = 02015 МПа.
Среднее эффективное давление и механический КПД:
Эффективный КПД и эффективный удельный расход топлива:
Таблица 5. Результаты исследования индикаторных и эффективных пареметров двигателя
Индикаторные и эффективные параметры двигателя
Основные параметры цилиндра и двигателя
Рабочий объем одного цилиндра:
Рабочий объём двигателя:
Часовой расход топлива:
Литровая мощность двигателя:
Таблица 6. Результаты исследования основных параметров и показателей двигателя
Основные параметры и показатели двигателя
Построение индикаторных диаграмм
Индикаторная диаграмма карбюраторного двигателя построена для номинального режима работы двигателя т.е. при Ne = 249446 кВт и n = 5700 мин–1 аналитическим методом.
Масштабы диаграммы: масштаб хода поршня MS = масштаб давлений Mp = 005 МПа в мм.
Величины в приведённом масштабе соответствующие рабочему объёму цилиндра и объёму камеры сгорания:
Максимальная высота диаграммы (точка z):
Ординаты характерных точек:
ВМТ: Pr = 24 мм; Рс = 3819 мм; Pz = 15519 мм.
НМТ: Ра = 165 мм; Рв = 865 мм.
Построение политроп сжатия и расширения аналитическим методом:
а) политропа сжатия отсюда
где OB = OA + AB = 876 + 78 = 8676 мм;
б) политропа расширения отсюда
Результаты расчетов приведены в таблице 7.
Скругление индикаторной диаграммы осуществляется на основании следующих соображений и расчётов. Так как рассчитываемый двигатель достаточно быстроходный (n = 5700 мин–1) то фазы газораспределения необходимо устанавливать с учётом получения хорошей очистки цилиндра от отработавших газов и обеспечения дозарядки в пределах принятых в расчёте. В связи с этим начало открытия впускного клапана (точка r') устанавливается за 18° до прихода поршня в в.м.т. а закрытие (точка а") – через 60° после прохода поршнем н.м.т.; начало открытия выпускного клапана (точка b) принимается за 55° до прихода поршня в н.м.т. а закрытие (точка а') – через 25° после прохода поршнем в.м.т. Учитывая быстроходность двигателя угол опережения зажигания принимается равным 35° а продолжительность периода задержки воспламенения – 1 =5°. В соответствии с принятыми фазами газораспределения и углом опережения зажигания определяют положение точек r a a c f и b по формуле для перемещения поршня
Где выбор величины λ производится при проведении динамического расчёта а при построении индикаторной диаграммы предварительно принимается λ = 0285.
Расчёты ординат точек r' a' a" c' f и b' сведены в таблицу.
Положение точки с определяется из выражения:
Pc = (115 125) Pc =12019095=22914 МПа;
Положение точки zд определяется из выражения:
Для упрощения расчётов можно принять что максимальное давление сгорания достигается через – 100 после в.м.т. Соединяя плавными кривыми точки и далее с zd и кривой расширения и линией выпуска получим скруглённую действительную индикаторную диаграмму
Политропа расширения
Таблица 7. Расчет политроп сжатия и расширения.
Таблица 8. Положение точек на индикаторной диаграмме.
Расстояние точек от ВМТ
Рис. 1. Индикаторная диаграмма
Теоретическое среднее индикаторное давление
где мм2 - площадь диаграммы . Это близко к рассчитанному.
Тепловой баланс двигателя
Общее количество теплоты введенной в двигатель с топливом:
Теплота эквивалентная эффективной работе за 1 с:
Теплота передаваемая охлаждающей среде:
где с = 045 053 — коэффициент для четырехтактных двигателей. D — диаметр цилиндра см; n — частота вращения коленчатого вала двигателя обмин; m = 06 07 — показатель степени для четырехтактных двигателей. В расчете принято при n= 1000 обмин m = 06 а на всех остальных скоростных режимах — m = 065.
Теплота унесенная с отработанными газами:
Теплота потерянная из-за химической неполноты сгорания топлива
Неучтенные потери теплоты
Результаты вычислений занесем в таблицу 9.
Таблица 9. Тепловой баланс двигателя
Динамический расчет кривошипно-шатунного механизма
1.Кинематический расчет кривошипно-шатунного механизма
Величины инерционных усилий действующих в двигателе зависят от размеров кривошипно-шатунного механизма и их соотношений.
Установлено что с уменьшением (за счёт увеличения ) происходит снижение инерционных и нормальных сил но при этом увеличивается высота двигателя и его масса. В связи с этим в автомобильных и тракторных двигателях принимают
Для двигателей с малым диаметром отношение выбирают с таким расчётом чтобы избежать задевания шатуна за нижнюю кромку цилиндра.
Рис. 2. Схема кривошипно-шатунного механизма
для определения минимальной длины шатуна
Минимальную длину шатуна и максимально допустимое значение λ без задевания шатуна за кромку цилиндра определяют следующим образом (рис. 2.4): на вертикальной оси цилиндра наносят центр коленчатого вала О из которого радиусом проводят окружность вращения центра шатунной шейки. Далее пользуясь конструктивными размерами элементов коленчатого вала из точки В (центр кривошипа находящихся в н.м.т.) радиусом проводят окружность шатунной шейки из центра О радиусом – вторую окружность вращения крайней точки щеки или противовеса.
Выбор и длины шатуна. В целях уменьшения высоты двигателя без значительного увеличения инерционных и нормальных сил отношение радиуса кривошипа к длине шатуна предварительно было принято в тепловом расчёте . При этих условиях:
Итак исходными данными для расчета являются:
Определение кинематических параметров производится по формулам:
Расчёт производится аналитически через каждые 10° угла поворота коленчатого вала рассчитанные значения заносятся в таблицу.
Таблица 2.1. Кинематический анализ КШМ.
По данным табл. 2.7 построены графики (рис. 2.5) в масштабе в мм – в масштабе в мм – в масштабе
в мм.угла поворота коленчатого вала
При а на кривой – эта точка перегиба.
Рис 3. График перемещений поршня
Рис 4. График скоростей поршня
Рис 5. График ускорений поршня
2.Динамический расчет кривошипно-шатунного механизма
Динамический расчет КШМ состоит в определении суммарных сил и моментов возникающих от давления газов в цилиндре и сил инерции движущихся масс деталей КШМ. По найденным силам рассчитывают детали КШМ на прочность и износ определяют неравномерность крутящего момента и степень неравномерности вращения двигателя. В ходе расчета должны быть определены:
Сила давления газов инерционные и суммарные силы действующие на поршневой палец;
сила действующая на стенку цилиндра;
составляющие силы действующей по шатуну: тангенциальная сила направленная по касательной окружности радиуса кривошипа и нормальная (радиальная) сила направленная по радиусу кривошипа;
Эти силы определяются для положении коленчатого вала от 0° до 720° через каждые 15°.
Силы давления газов. Индикаторную диаграмму (см. рис. 1) полученную в тепловом расчёте развертывают по углу поворота кривошипа
Эта диаграмма представляет собой график избыточных давлений газов на поршень. Её строим в том же масштабе что и индикаторную диаграмму.
Для построения развернутой диаграммы Рг на индикаторной диаграмме находим ординаты соответствующие различным положениям коленчатого вала от 00 до 7200 через каждые 300. В интервале от 3600 до 3900 ординаты определяются через 100.
Связь между углом поворота коленчатого вала и перемещением поршня определяем графически с учетом поправки на конечную длину шатуна (поправки Брикса). Для этого под индикаторной диаграммой из точки О радиусом проводим полуокружность. Затем от центра полуокружности в сторону НМТ откладываем отрезок ОО1 равный . Полуокружность из центра О1 делим лучами с интервалом 300. Из точек полученных на полуокружности проводим вертикальные линии до пересечения с линиями индикаторной диаграммы. Отрезки их от оси абсцисс до соответствующей линии индикаторной диаграммы отображают абсолютное давление газов в цилиндре для данного положения коленчатого вала.
Масштаб по оси абсцисс
Следовательно ось абсцисс делим на 24 части по 16 мм и через эти точки проводим вертикальные линии.
Ось абсцисс проводим на уровне линии атмосферного давления Р0 индикаторной диаграммы так как развернутая диаграмма должна представлять собой избыточное давление газов Рг. Избыточное давление газов начиная с ВМТ такта впуска переносим с индикаторной диаграммы на соответствующие вертикали.
Полученные точки диаграммы соединяем плавной сплошной линией.
Масштабы развёрнутой диаграммы: давлений и удельных сил ; полных сил или угла поворота кривошипа .
По развёрнутой диаграмме через каждые 15° угла поворота кривошипа определяют значения и заносят в табл. 2.2 динамического расчёта.
Конструктивные массы частей кривошипно-шатунного механизма.
С учётом диаметра цилиндра отношения рядного расположения цилиндров и достаточно высокого значения устанавливаются:
Конструктивная масса поршневой группы (для поршня из алюминиевого сплава)
Конструктивная масса шатуна (для стального кованого шатуна)
Конструктивная масса неуравновешенных частей одного колена вала без противовесов (для литого чугунного вала)
Конструктивная масса шатуна сосредоточенная на оси поршневого пальца:
Конструктивная масса шатуна сосредоточенная на оси кривошипа:
Массы совершающие возвратно-поступательное движение:
Силы инерции. Сила инерции возвратно – поступательно движущихся деталей отнесенная к площади поршня равна:
Суммарные силы. Суммарная сила (МПа) сосредоточенная на оси поршневого пальца:
Сила действующая вдоль шатуна.
Сила действующая по радиусу кривошипа.
Тангенциальная сила.
Таблица 2.1. Динамический анализ КШМ.
Если все результаты расчетов получены в мм то для перевода в размерность давлений или сил их необходимо соответственно умножить на
По данным таблицы строим графики всех сил: .
При построении графиков необходимо обращать внимание на следующее:
а) при > 025 – кривая вблизи НМТ (точки 6 и 18) будет вогнутой;
б) в точках где остальные силы также должны равняться нулю. Поэтому необходимо спроектировать эти точки на оси абсцисс сил N K и Т и кривые указанных сил проводить через эти точки;
в) сила обращается в нуль и при положении кривошипа Для правильного построения диаграммы силы необходимо провести вертикальные штриховые линии из точек пересечения с осью абсцисс диаграммы сил инерции Pj (так как при + = 90 Pj = 0);
г) кривые сил T и N пересекают ось абсцисс и изменяют знак во всех мертвых точках (точки 0 6 12 18) и в точках в которых сила P равна нулю. Следует также иметь ввиду что характер протекания и знак сил Т и N одинаковы.
Полярная диаграмма сил действующей на шатунную шейку коленчатого вала.
Полярная диаграмма показывает величину и направление силы . Она представляет собой геометрическую сумму силы действующей вдоль оси шатуна и силу (центробежной силы создаваемой массой ) направленной по радиусу кривошипа.
Полярную диаграмму строим следующим образом. Проводим по оси ординат. По горизонтали откладываем силы : вправо – положительные влево – отрицательные. По вертикали откладываем силы : вниз – положительные вверх – отрицательные. Найдя пересечение соответствующих точек строим полярную диаграмму силы действующей по шатуну с полюсом .
Для учета центробежной силы равной: достаточно сместить полюс диаграммы из точки в точку на расстояние:
Расстояние от нового полюса до любой точки диаграммы равно геометрической сумме векторов и :
Для большей наглядности в полюсе изображается шатунная шейка и часть щеки.
Для определения сил действующих на шатунный подшипник эта диаграмма разворачивается по углу поворота коленчатого вала.
Диаграмма износа шатунной шейки.
Диаграмма износа строится с целью определения зоны в которой следует располагать канал подвода масла к шатунному подшипнику.
Построение этой диаграммы основывается на предположении что износ шейки пропорционален величине вектора и распространяется на дугу протяженностью 120 расположенную симметрично относительно точки приложения этого вектора.
Сначала строится вспомогательная окружность радиусом на которую наносятся кольцевые секторы характеризующие износ шейки от каждого вектора за исключением промежуточного вектора мм. Вправо и влево от точки приложения вектора откладываются секторы протяженностью по 60 которые заштриховываются. Толщина сектора определяется умножением силы на масштаб.
Для получения фактической диаграммы износа проводится еще одна окружность произвольного радиуса изображающая шатунную шейку она как и вспомогательная окружность разбивается на 12 частей и по каждому из 12 лучей в произвольном масштабе откладывается суммарная ширина зачерненных на вспомогательной диаграмме секторов.
Масло подводится в зону наименьшего износа исходя из полученной диаграммы масло подводящий канал высверливается под углом к вертикали.
Диаграмма суммарного индикаторного крутящего момента от всех цилиндров двигателя.
Величину суммарного крутящего момента от всех цилиндров получаем графическим сложением моментов от каждого цилиндра одновременно действующих на коленчатый вал при данном значении угла .
После построения диаграмм необходимо проверить их правильность. Для этого определяется средняя величина крутящего момента по диаграмме и сравнивается с расчетной величиной крутящего момента. Разница между ними не должна превышать 5%.
Определение по диаграмме производится в следующем порядке:
определяется положительная результирующая площадь и делится на расстояние между крайними ординатами. Очевидно что равновеликого по площади прямоугольника будет в масштабе диаграммы ординатой среднего крутящего момента.
где – масштаб крутящих моментов.
Расчетное значение момента определяется через мощность двигателя:
Разница между расчетным значением и определяемым по диаграмме значением :
КОНСТРУКТИВНАЯ РАЗРАБОТКА И РАСЧЕТ ДВИГАТЕЛЯ
В конструкции поршня принято выделять следующие элементы: головку и юбку. Головка включает днище огневой и уплотняющий пояса. Юбка поршня состоит из бобышек и направляющей части.
Конструктивные параметры основных элементов поршня.
При конструктивной разработке поршневой группы за основу принимаем поршень прототипа двигателя (днище поршня форма камеры сгорания юбка поршня). Выбираем число и тип поршневых колец.
Предварительные размеры деталей поршневой группы выбираем по статическим данным затем проверяем и уточняем. Расчету подлежат следующие детали поршневой группы: юбка поршня компрессионное кольцо поршневой палец. Поршневая группа на поперечном и продольном разрезах двигателя вычерчивается в разрезе.
Элементы поршневой группы:
Форма нижней кромки юбки поршня должна соответствовать траектории движения противовеса расположенного на коленчатом валу и отстоять от него на расстоянии не менее 2 мм при нахождении поршня в НМТ.
Расчетным режимом при расчете поршневой группы является режим максимального крутящего момента.
Критерием правильности выбора длинны юбки hю является допустимое удельное давление.
где – максимальная боковая сила (Н) определяемая из динамического расчета;
– диаметр цилиндра (м).
1.2 Поршневые кольца
Расчет колец заключается в определение среднего радиального давления и напряжений в кольце в рабочем сечении и при надевание его на поршень для заданных на основании статических данных отношений: Dt и S0t.
Dt = 22 – 23 при D = 60 – 90 мм;
Кольца современных двигателей имеют неравномерную эпюру давлений для таких колец среднее удельное давление определяется по формуле:
Для карбюраторных двигателей значение величины лежит в пределах:.
- напряжение в кольце рабочем состоянии:
– напряжение в кольце при надевании его поршень:
где m = 157 – коэффициент зависящий от способа надевания кольца у существующих двигателей значения напряжений следующие:
Т.к. величины max max и Рср находятся в пределах статических данных то радиальная толщина кольца выбрана правильно.
1.3. Поршневой палец
Поршневой палец стальной запрессован в верхнюю головку шатуна и свободно вращается в бобышках поршня.
Правильность выбора наружного диаметра пальца dп проверяется по допускаемым удельным давлениям в бобышках поршня и в поршневой головке шатуна
Принимаем: dп = 20 мм; а = 23 мм.
Для карбюраторных двигателей удельное давление должны лежать в пределах:
Внутренний диаметр пальца dвн определяется из условий обеспечения прочности критерием которой является допускаемые напряжения изгиба (max) среза (max) и овализации (i):
Максимальная овализация пальца:
поправочный коэффициент
Материал поршневого пальца Ст40ХА.
Допускаемые пределы напряжений и деформаций:
max = 200 250 МПа max = 80 120 МПа
i = 120 230 МПа dmax = (0001 0002)dп.
Все рассчитанные значения выдерживают данные требования.
В состав шатунной группы входят: шатун со съёмной крышкой кривошипной головки шатунные вкладыши шатунные болты с элементами их фиксации.
Проектирование шатунной группы сводится к разработке элементов шатуна: поршневой головки кривошипной головки стержня шатуна.
2.1. Поршневая головка шатуна
В поршневой головке шатуна возникают напряжения от натяга при запрессовке втулки или пальца и нагреве шатуна от силы инерции поршневой группы и от силы газов.
Напряжение от натяга втулки:
где – удельное давление втулки на головку:
где диаметр головки;
МПа – модуль упругости стали;
МПа – модуль упругости бронзы;
коэффициент Пуасона;
– температурный натяг;
Напряжение от запрессовки пальца:
Напряжение от силы инерции поршневой группы
При определении М и N принимаем абсолютные значения Pjn.
Функции f1(з) и f2(з) определяем из графиков.
Напряжения от силы сжимающей поршневую головку шатуна:
Максимальное значение напряжения цикла:
Минимальное напряжение:
Материал шатуна Cт 40ХН; ; ;.
Запас прочности поршневых головок шатунов должен лежать в пределах 2.5 5.0 что выполняется.
2.2. Стержень шатуна
Расчет стержня производится по среднему сечению В - В Запас прочности стержня:
Среднее сечение стержня:
Сила инерции растягивающая стержень:
Сила сжимающая стержень:
Болты рассчитываются на режиме максимальной частоты вращения холостого хода. Примем конструктивно Болт М10х55 ГОСТ 7798-70.
Максимальная сила растягивающая болт:
– коэффициент основной нагрузки резьбового соединения
Из условия не раскрытия стыка:
Минимальная сила растягивающая болт
– площадь поперечного сечения болта по внутреннему диаметру.
Запас прочности должен быть не менее 2.
Прочность коленчатого вала определяется следующими факторами:
размерами и формами отдельных элементов вала;
наличием концентраторов напряжений на кромках масляных каналов галтелей и других переходах;
характеристиками прочности материала;
использованными при изготовлении вала конструктивными и технологическими методами упрочнения;
наличием и ориентацией внутренних упорядоченных структур расположением волокон зависящим от способа изготовления коленчатого вала.
Исходные данные для расчета:
Коренные шейки нагружаются главным образом крутящим моментом поэтому запас прочности оцениваем только по касательным напряжениям.
Момент сопротивления коренной шейки кручению:
Коэффициент запаса прочности
Расчет на кручение производится так же как и расчет коренных шеек. Запас прочности на изгиб должен определиться по результирующему изгибающему моменту действующему вдоль масляного канала созданному силами К и Т.
Экстремальные значения крутящего момента:
где расстояние от полюса до точек А1 и А2
расстояние между центрами цилиндров
масштаб сил диаграммы.
Запас прочности по касательным напряжениям:
момент сопротивлению кручению
расстояние от середины коренной шейки до середины щеки
Запас прочности по нормальным напряжениям
Результирующий запас прочности:
4. Блок цилиндров головка и картер двигателя
4.1. Блок цилиндров.
Блок цилиндров выполняется с толщиной стенок водяной рубашки 4 6 мм а верхней стенки – 8 12 мм.
Пространство для охлаждающей жидкости в рубашке блока выполняется равным 6 8 мм. Нижнее положение рубашки определяется из условия чтобы уплотняющий пояс поршня в НМТ находился в зоне цилиндра омываемой охлаждающей жидкостью. Для сообщения полости водяной рубашки блока с полостью головки цилиндра в верхней стенке блока делаются отверстия диаметром 8 12 мм.
В качестве материалов применяют серый перлитный чугун СЧ – 26 чугун СЧ–18-36 специальный легированный чугун или сплавы алюминия АЛ – 9 и АЛ – 4.
Цилиндры двигателя выполняются вместе с блоком и отливаются из чугуна. Толщина стенок цилиндра задается на основание статических данных по выражению:
Принимаем = 6 мм и далее проверяем расчетом:
У современных двигателей
Полная длина цилиндра устанавливается из условия чтобы при положении поршня в ВМТ он выступал за пределы цилиндра не более чем на 10 15мм. Следуя условию принимаем l = 128 мм.
5. Механизм газораспределения
Для получения высоких мощностных и экономических показателей работы двигателя механизм газораспределения должен прежде всего обеспечивать эффективную смену рабочего тела и хорошее наполнение цилиндров. Это достигается экспериментальным подбором оптимальных фаз газораспределения наибольшими проходными сечениями в горловинах и седлах клапанов и наименьшими гидродинамическими сопротивлениями впускного и выпускного трактов.
Кроме того конструкция механизма газораспределения должна обеспечивать надежную работу механизма на всех режимах работы двигателя без разрыва кинематической связи. Последнее обстоятельство требует внимательного подхода к расчету кинематики и динамики механизма газораспределения.
Повышение долговечности деталей механизма газораспределения обеспечивается за счет подбора материалов наиболее отвечающих условиям работы этих деталей; хорошего отвода тепла от клапанов (в первую очередь от выпускных) обеспечение достаточной смазки трущихся поверхностей деталей механизма принудительного вращения клапанов и ряда других мероприятий.
Конструирование механизма газораспределения сводится к разработке привода механизма газораспределения распределительного вала с фиксацией его от осевых перемещений толкателей штанг коромысел клапанов и т.д.
Размеры деталей механизма газораспределения определяются по размерам прототипа двигателя по чертежам отечественных двигателей справочникам и статистическим данным. Принятые размеры уточняются расчетом.
Расчет механизма газораспределения сводится к определению проходных сечений клапанов и выполнению прочностных расчетов отдельных элементов.
Подбор массы маховика
Определяем момент инерции маховика:
– безразмерный момент инерции.
Средний диаметр маховика:
где – ускорение свободного падения ;
– коэффициент толщины ;
– коэффициент ширины ;
– плотность материала сталь .
Определяем массу маховика:
Анализ уравновешенности и уравновешивание двигателей с линейным расположением цилиндров
Двигатель 2P (с углом между кривошипами = 360°). Компоновочная схема двигателя приведена на рис. 7 а. Практическая целесообразность его в значительной мере определяется возможностью обеспечения равномерного чередования рабочих ходов (через 360° поворота коленчатого вала) в четырехтактных ДВС.
По уравновешенности данный двигатель эквивалентен двигателю одноцилиндровому имеющему удвоенные массы подвижных элементов. В соответствии с этим силовые факторы определяющие его уравновешенность:
На рис. 7 б приведена схема уравновешивания согласно которой на продолжении щек размещаются противовесы со статическим моментом .
Неуравновешенность вызываемая силой относительно невелика и данный силовой фактор в большинстве конструкций ДВС оставляют неуравновешенным.
Обязательному уравновешиванию в двигателях 2Р (с углом между кривошипами = 360°) подвергается наиболее значимый из неуравновешенных силовых факторов — . На практике эта задача может быть решена двумя способами:
)использованием части механизма Ланчестера предназначенной для уравновешивания силы инерции первого порядка приняв статический момент противовесов на дополнительных валах;
)применением уравновешивающего механизма с двумя дополнительными валами вращающимися в одном направлении с угловой частотой — и дополнительными противовесами на коленчатом валу.
Схема такого механизма приведена на рис. 7 в. Здесь сила замещена эквивалентной ей геометрической суммой двух сил с модулем С одна из которых (С+) вращается с угловой скоростью (синхронно с кривошипом) а другая (С-) — с угловой частотой .
Для уравновешивания силы С+ масса противовесов на коленчатом валу увеличивается совокупно на величину в результате чего возникает центробежная сила . Условие уравновешивания выполняется при .
Сила С- уравновешивается равнодействующей 2 двух центробежных сил возникающих от вращения противовесов на двух дополнительных валах вращающихся с угловой частотой — (синхронно с уравновешиваемой силой). Оси вращения валов с противовесами смещены относительно оси коленчатого вала на величину а в направлении ВМТ.
Условие уравновешивания выполняется при
При этом за счет смещения осей вращения коленчатого вала и дополнительных валов возникает момент который взаимодействует с Мопр как это показано на рис. 7 г. В результате результирующий момент передаваемый на опоры имеет меньшую неравномерность чем момент опрокидывающий. Это позволяет улучшить уравновешенность двигателя по опрокидывающему моменту.
Величина смещения осей коленчатого и дополнительных валов а определяется из условия обеспечения максимального эффекта выравнивания Мопр на наиболее характерном эксплуатационном режиме работы двигателя (обычно это режим номинальной мощности). Учитывая то обстоятельство что Мопр(t) — периодическая функция с периодом для четырехтактного двигателя он может быть разложен в ряд Фурье:
Так как то и может нейтрализовать один из членов тригонометрического полинома а именно член с . Это возможно при вследствие чего .
Вахламов В.К. Автомобиль. Теория и конструкция. М.: Машиностроение 1976.
Двигатели внутреннего сгорания. Динамика и конструирование. Под ред. В.Н. Луканина. – М.: Высшая школа 2005.
Федоров В. М. Чепикова Т. П. Тепловой и динамический расчет двигателей внутреннего сгорания ЧТИ ИжГТУ. – Чайковский 2005.
Поперечный разрез ВАЗ-1113.cdw

Индикаторная диаграмма ВАЗ-1113.cdw

Диаграмма износа шатунной шейки
Графики сил давления газов
радиальных сил и сил
действующих на шатуннуб шейку
График суммарного крутящего момента
Индикаторная диаграмма
Продольный разрез ВАЗ-1113.cdw
