Технология механической обработки детали ''Кронштейн''




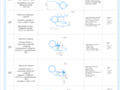
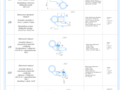
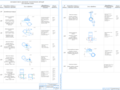
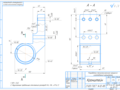
- Добавлен: 24.01.2023
- Размер: 1 MB
- Закачек: 0
Описание
Состав проекта
![]() |
![]() |
![]() ![]() ![]() ![]() |
![]() ![]() ![]() ![]() |
![]() ![]() ![]() ![]() |
![]() ![]() ![]() ![]() |
![]() |
![]() ![]() ![]() ![]() |
![]() ![]() ![]() ![]() |
![]() ![]() ![]() |
![]() ![]() ![]() ![]() |
![]() ![]() ![]() ![]() |
![]() ![]() ![]() ![]() |
Дополнительная информация
Заготока.cdw

изготовления кронштейна
БГТУ им. В.Г. Шухова
Кронштейн.cdw

Разработка технологического процесса
изготовления кронштейна
БГТУ им. В.Г. Шухова
Кронштейн(V5).cdw

Разработка технологического процесса
изготовления кронштейна
БГТУ им. В.Г. Шухова
Заготовка(V11).cdw

изготовления кронштейна
БГТУ им. В.Г. Шухова
Кронштейн(V11).cdw

Заготовка(V5).cdw

изготовления кронштейна
БГТУ им. В.Г. Шухова
Пояснительная записка кронштейна с рамкой.docx
Технологическая часть
1. Определение типа производства
2. Метод получения заготовки
Разработка технологического маршрута
1. Назначение технологических баз и выбор способов обработки поверхностей
2. Технологический маршрут обработки детали
3. Выбор оборудования
4. Выбор режущего и вспомогательного инструментов
5. Выбор приспособлений
6. Выбор измерительного инструмента
8. Расчет режимов резания сил и моментов резания
9. Техническое нормирование
Список использованной литературы
Целью курсовой работы является разработка одного из возможных технологических процессов обработки детали «кронштейн».
При его разработке были учтены: тип производства свойства и особенности обрабатываемого материала точность размеров качество поверхности действующие стандарты и нормативы.
Курсовая работа состоит из пояснительной записки операционных карт карт эскизов и чертежей.
Графическая часть работы содержит: чертеж детали заготовки (отливка для получения одной детали и для получения десяти деталей) чертеж технологического маршрута обработки детали с указанием технологических размеров оборудования режущего и вспомогательного инструментов приспособлений и измерительного инструмента.
При оформлении графической части проекта и альбома операционных карт и карт эскизов учитывались требования ЕСКД и ЕСТПП.
Выполнение данной курсовой работы способствует развитию навыков самостоятельного решения инженерных задач в области проектирования технологических процессов в выборе оборудования режущего и вспомогательного инструментов приспособлений и измерительного инструмента для получения годной детали механической обработкой; а также помогает студенту более глубоко освоить изученные ранее дисциплины их практическое применение и значимость.
Кронштейн – деталь сложной формы имеющая габаритные размеры: высота – 165 мм длина – 69 мм ширина – 100 мм. Деталь представляет собой полку переходящую в цилиндр.
На полке имеются сквозные отверстия диаметром ∅8 мм (3 отв.) с фасками 1х45° на расстоянии от гладкой поверхности в 15 мм и на расстоянии 75 мм отверстия диаметром ∅ 11 мм (3 отв.).
Цилиндр диаметром ∅70 мм имеет центральное сквозное отверстие ∅55 мм с фасками 15х45° с точностью – 7 квалитет и качеством шероховатости Ra 125 мкм.
На цилиндре перпендикулярно полке имеется лыска на расстоянии 33 мм от оси цилиндра с качеством поверхности Rz 80 мкм. На нижней стенке цилиндра имеется четырехгранное отверстие глубиной 8 мм.
Неуказанные предельные отклонения линейных размеров на чертеже выполняются в соответствии с IT142 т.е. с допуском на собственный размер по 14 квалитету.
На чертеже не указаны допуски на отклонения формы детали и взаимного расположения поверхностей следовательно они не превышают допуск на соответствующий размер.
Деталь кронштейн изготовляется из серого чугуна СЧ20 ГОСТ 1412-85 физико-механические свойства и химический состав которого указаны в таблице 1 и 2 соответственно.
Временное сопротивление на растяжение
Временное сопротивление на изгиб
Временное сопротивление на сжатие
Модуль упругости при растяжении МПа
Удельная теплоемкость при температуре от 20 до 2000 С
Коэффициент линейного расширения при температуре от 20 до 2000 С 10 С
Теплопроводность при 200 С
Массовая доля элементов
Твердость чугуна не более HB 240.
Масса готовой детали составляет 174 кг.
Тип производства и соответствующая ему форма труда определяют характер технологического процесса и его построение.
В соответствии с массой втулки (M=174 кг) и годовой программой выпуска (N=5000 штгод) определяем тип производства как массовое (см. таблицу 3)
Выбор типа производства по программе выпуска
Качество обрабатываемых в год деталей (изделий) одного наименования и типоразмера
Обоснование выбора вариантов заготовки
Учитывая массовое производство геометрическую форму и механические свойства материала (серый чугун – литейный материал) предлагается получить деталь методом литья в кокиль и литья в песчано-глинистые формы.
Литье в песчаные формы - самый распространенный (универсальный) способ получения отливок который применяется во всех типах производства. Отливки получаемые этим способом занимают до 80% от общего объема отливок.
Сущность способа заключается в заливке расплава в песчаную форму полость которой имеет конфигурацию отливки.
Литьем в песчаные формы получают отливки массой от 1 кг до 200 тон из чугуна стали цветных металлов и сплавов. Точность и шероховатость отливок получают по 14 18 квалитету (IT) и Rz до 40 мкм из тяжелых цветных сплавов и серого чугуна.
Литье в кокиле. Сущность метода заключается в заливке расплава в металлические формы (называемые кокили) имеющие конфигурацию отливки и которые используются многократно.
Этот метод литья применяется в крупносерийном и массовом производствах.
Отливки можно получить из чугуна стали и цветных сплавов с толщиной стенок 3 100 мм и массой от десятков граммов до сотен килограммов. Точность отливок достигает 12 15-го квалитетов а шероховатость поверхности Ra=25 25 мкм.
Высокая скорость охлаждения отливки обеспечивает образование в ней мелкозернистой структуры что обеспечивает стабильность по механическим свойствам и плотности.
Определение припусков на механическую обработку допусков и размеров заготовки:
Литье в песчано-глинистые формы
Для решения поставленной задачи воспользуемся ГОСТ 26645-85 – «Отливка из черныхцветных металлов»:
Определение класса точности: класс точности принимаем – 8.
Определение ряда припуска: ряд припуска – 3.
Определяем допуски и припуски размеров отливок для отливки 9 класса точности (размеры больше 100мм) и 8 класса точности (до 100мм) c 3 рядом припуска и определяем размеры заготовки.
Точность вид обработки
Определение класса точности: класс точности принимаем – 6.
Определение ряда припуска: ряд припуска – 1.
Определяем допуски и припуски размеров отливок для отливки 7 класса точности (размеры больше 100мм) и 6 класса точности (до 100мм) c 1 рядом припуска и определяем размеры заготовки.
Расчет массы заготовок:
Объем заготовки получаемой литьем в песчано-глиняных формах равен:
V1 = 671*268*701= 126 см3
V2 = 42*701*30 = 913 см3
V3 = *342*42= 15 см3
V4 = *3712*701= 3023 см3
V5= *2472*701= 1343 см3
V = V1 + V2 - 3V3 + V4 - V5 = 3808 (см3)
Объем заготовки получаемой литьем в кокиль равен:
V1 = 661*261*691= 1192 см3
V2 = 411*691*30 = 852 см3
V3 = *442*411= 25 см3
V4 = *3612*691= 2828 см3
V5= *2612*691= 1478 см3
V = V1 + V2 - 3V3 + V4 - V5 = 3319 (см3)
Масса заготовки получаемой литьем в ПГФ равен Мз = 27 кг.
Масса заготовки получаемой литьем в кокиль равна: Мз = 236 кг.
Определение технико-экономических показателей:
Себестоимость заготовки:
Q - масса заготовки;
kT - коэффициент зависящий от точности;
kС - коэффициент зависящий от группы сложности;
kB - коэффициент зависящий от массы;
kM - коэффициент зависящий от марки материала;
kП - коэффициент зависящий от объема производства;
Sотх - себестоимость 1 т отходов.
Коэффициент использования металла:
)Для поковок получаемых литьем в ПГФ:
СSОТХ = 248 рубтонну; q = 174 кг;
кТ = 1; кС = 07; кВ = 084; кМ = 1; кП = 1.
Ки.м. = qQ = 17427 = 064
)Для поковок получаемых горячекатаным прокатом:
Ки.м. = qQ = 174236 = 074
Из расчетов видно что себестоимость заготовки и коэффициент использования металла изготовленной литьем в кокиль незначительно но выше чем у заготовки изготовленной литьем в ПГФ поэтому предпочтительным будет считаться изготовление заготовки литьем в кокиль.
Чертеж заготовки см. в приложениях.
Разработка технологического процесса изготовления заготовки.
Подготовка кокиля - очистка поверхностей полуформ и разъемов.
Контроль - проверка смещений центрирования и крепления подвижных частей кокиля.
Нагрев (предварительный) кокиля до 150 200С (для лучшего сцепления облицовки и краски).
Покрытие рабочей поверхности кокиля и металлических стержней (он раскрыт) водной суспензией в несколько слоев (пульверизатором или кистью). Сверху облицовка покрывается краской которая имеет тот же состав но более жидкая. Краска способствует уменьшению шероховатости поверхности.
Облицовка и краска - так называемые огнеупорные покрытия - защищают кокиль от резкого нагрева и схватывания с отливкой.
Нагрев кокиля до рабочей температуры (150 350С) которая зависит от размеров и свойств металла отливки.
Сборка кокиля и установка если необходимо песчаного стержня. Полуформы скрепляются специальными зажимами или механизмом запирания кокильной машины.
Заливка кокиля расплавом.
Охлаждение отливки. Из не совсем остывшей отливки частично извлекаются металлические стержни чтобы избежать чрезмерного обжатия их усаживающейся отливкой.
Разборка кокиля - удаление (окончательное) металлический стержней раскрытия кокиля и извлечение отливки.
Выбивка песчаного стержня обрезка литников прибылей и выпоров и зачистка отливки.
Термообработка отливок.
Способы обработки поверхностей и технологические базы удобно свести в таблицу 6. Поверхности пронумерованы и показаны на рис. 1.
Рис.1. Эскиз детали с обозначением поверхностей
Способы обработки поверхностей и технологические базы
Номер и наименование обрабатываемой поверхности
Вид механической обработки
Номер базовой поверхности
Количество лишенных степеней свободы
– наружная поверхность
Фрезерование черновое
Фрезерование и получистовое шлифование
– внутренняя цилиндрическая поверхность
Растачивание и внутреннее шлифование
Далее рассмотрим последовательность обработки поверхностей.
Заготовительная операция
Получаем заготовку отливая ее в кокиль.
Вертикально-фрезерная операция
Данная операция выполняется на вертикально-фрезерном станке. На данной операции обрабатывается основание кронштейна которое послужит установочной базой для остальных операций. Деталь закрепляется в тисках с упором в торец.
Обрабатываем две наружные плоские поверхности образующие угол 90 градусов. Деталь устанавливается в тисках. Необходимый угол получается с помощью конструкции фрезы.
Сверлильная операция
Сверлим 3 сквозных отверстия ∅8 с помощью специального кондуктора применение которого значительно увеличит точность обработки и снизит вспомогательное время на разметку детали.
Сверлим 3 сквозных отверстия ∅8 с помощью специального кондуктора применение которого значительно увеличит точность обработки и снизит вспомогательное время на разметку детали. Зенкуем фаски
Обрабатываем торцевые поверхности за 2 установа растачиваем отверстие ∅55 оставив припуск под шлифование точим фаски. Операция выполняется на токарном станке. Заготовка устанавливается на станок с помощью планшайбы со специальными закрепленными упорами для автоматического позиционирования.
Заготовка крепится в тисках базируясь на уже обработанные поверхности. Сверлится отверстие ∅8 инструмент – спиральное сверло ∅8 с цх фаска зенкуется.
Круглошлифовальная операция
Шлифуется отверстие ∅55 начисто образуя поверхность с требуемой точностью и шероховатостью. Станок круглошлифовальный.
Шлифовальная операция
Шлифуется основание кронштейна начисто образуя поверхность с требуемой точностью и шероховатостью. Станок плоскошлифовальный.
Наименование и содержание операции
Оборудование приспособление инструмент
Литье заготовки в кокиль
Вертикально-фрезерная операция
Установка заготовки в тиски с упором в торец.
Фрезерование плоскости выдерживая размер 100.3-022
Станок вертикально-фрезерный на базе 6Р13 с ЧПУNC-210
Тиски для точных станочных работ с пневмозажимом ГОСТ 20746-84
Торцовая насадная фреза со вставными ножами оснащенными пластинами из твердого сплава ∅100 мм
Фрезерование уступа выдерживая размеры 40-025 мм 33+025 мм.
Фреза концевая ∅600 х 195 х 365 Z=5 КМ5 кхв Р6М5 ГОСТ1092-85
Установка детали в специальное устройство – кондуктор.
Рассверливание 3 отверстий ∅11+018 мм с шероховатостью Rz 80.
Вертикально-сверлильный станок 2Н118
Сверло спиральное Р6М5 ∅11 мм с цх
сверление 3 отверстий ∅8+015 мм с шероховатостью Rz 80.
Зенкование 3 фасок 1х45О.
Сверло спиральное с цилиндрическим хвостовиком ∅8
Зенковка коническая
Установка детали на планшайбу.
Точение торцев выдерживая размер 69
Растачивание отверстия ∅55.1 с качеством поверхности Ra 25.
Точение 3х фасок 1х45О
Токарный станок 16К20Ф3С5
Резец проходной отогнутый 450 ГОСТ 18869-73
Резец токарный фасочный ГОСТ 18875-73
Резец расточной для скв отв 16х16х140 ВК8 ГОСТ 18882-82
Сверление отверстия ∅8
Зенкование фаски 1х45О
Тиски для точных станочных работ с пневмозажимом ГОСТ 20746-84
Внутришлифовальная операция
Шлифовать отверстие ∅55+003 шероховатость Ra 1.25
Внутришлифовальный станок 3К225В
А 40-П С2 5 К5 35мс-1 1кл. А. ГОСТ 2424-82
Плоскошлифовальная операция
Шлифовать плоскость выдерживая размер 100-0087 и требования шероховатости Ra 1.25
Плоскошлифовальный станок мод. 3756
СП 25 60 125 23А23С26К
Контрольная операция
Проверка требуемых размеров. Проверка качества шероховатости Ra125.
Штангенциркуль 0-250 мм (005 мм) ШЦ-II (ЧИЗ) ГОСТ 166-89
Микрометр МК 50-1 ГОСТ 6507-90
Набор эталонов для измерения шероховатости
Выбор оборудования для механической обработки кронштейна будем производить в соответствии со следующими принципами:
- оборудование должно иметь возможность достигать требуемую точность обрабатываемых поверхностей;
- оборудование должно соответствовать типу производства;
- рабочая зона станка должна вмещать в себя обрабатываемую деталь но не быть чрезмерно просторной что ведет к недогруженности станка;
- станок должен обеспечивать требуемую жесткость закрепления детали и инструмента при обработке и кинематические возможности;
- желательно по возможности сократить номенклатуру станков и подобрать их таким образом чтобы была возможность производить обработку за наименьшее количество операций.
Проведем подбор оборудования для операции 005 - вертикально-фрезерная. На данной операции производится фрезерование основания.
Для данной операции выберем Вертикально-фрезерный станок 6Р13 с ЧПУ NC-210 который предназначен для фрезерования плоскостей торцевыми фрезами черных металлов в цехах машиностроительных предприятий.
Основные технические характеристики станка 6Р13 с ЧПУ NC-210 представлены в таблице 8.
Технические характеристики станка 6Р13 с ЧПУ NC-210
Наименование параметров
Класс точности по ГОСТ 8-71
Длинна рабочей поверхности стола
Ширина рабочей поверхности стола
Число Т-образных пазов
Наибольшее продольное перемещение стола
Наибольшее поперечное перемещение стола
Наибольшее вертикальное перемещение стола
Наименьшее и наибольшее расстояния от торца шпинделя до стола
Расстояние от оси шпинделя до вертикальных направляющих станины
Перемещение стола на одно деление лимба (продольное поперечное вертикальное)
Перемещение стола на один оборот лимба (продольное поперечное и вертикальное)
Наибольшая масса обрабатываемой детали
Наибольшее осевое перемещение пиноли шпинделя
Перемещение пиноли на один оборот лимба
Перемещение пиноли на одно деление лимба
Наибольший угол поворота шпиндельной головки
Цена одного деления поворота шпиндельной головки
Мощность привода главного движения
Частота вращения главного привода
Мощность привода подач
Частота вращения приводов подач
Проведем подбор оборудования для операции 010 - вертикально-фрезерная. На данной операции производится фрезерование основания.
Проведем подбор оборудования для операции 015 - сверлильная. На данной операции производится сверление 3-х отверстий.
Для данной операции выберем вертикально-сверлильный станок 2Н118 который предназначен для сверления отверстий сверлами зенкерами и т.д. различной конструкции в заготовках из черных металлов в цехах машиностроительных предприятий.
Основные технические характеристики станка 2Н118 представлены в таблице 9.
Наибольший диаметр сверления мм
Расстояние от конца шпинделя до стола мм:
Габариты станка (длина×ширина×высота) мм
Наибольшее осевое перемещение мм
Перемещение на 1 оборот маховичка-рукоятки мм
Цена деления лимба мм
Перемещение шпиндельной головки на 1 оборот маховичка мм
Наибольшее перемещение шпиндельной головки мм
Наибольшее вертикальное перемещение стола мм
Премещение стола на 1 оборот рукоятки мм
Электродвигатель главного движения:
Число оборотов в минуту
Проведем подбор оборудования для операции 020 - сверлильная. На данной операции производится сверление 3-х отверстий.
Проведем подбор оборудования для операции 025 - токарная. На данной операции производится точение двух торцов детали растачивание отверстия и точение фасок.
Для данной операции выберем Токарный станок 16К20Ф3С5 который предназначен для выполнения токарных работ в серийном производстве машиностроительных предприятий с применением технологий ЧПУ.
Основные технические характеристики станка 16К20Ф3С5 представлены в таблице. 10
Наибольший диаметр обрабатываемой заготовки мм.:
Наибольшая длина обрабатываемой заготовки мм
Частота вращения шпинделя мин-1
Число автоматически переключаемых скоростей
Скорость быстрых перемещений суппорта мммин.:
Скорость подачи мммин.:
Перемещение суппорта на один импульс мм.:
Проведем подбор оборудования для операции 030 - сверлильная. На данной операции производится сверление отверстия и зенкование фаски.
Проведем подбор оборудования для операции 035 – внутришлифовальная. На данной операции производится шлифование отверстия.
Для данной операции выберем внутришлифовальный станок 3К225В который предназначен для выполнения точных внутришлифовальных работ в серийном производстве машиностроительных предприятий.
Основные технические характеристики станка 3К225В представлены в таблице 11.
Класс точности по гост 8-82
Наибольший диаметр шлифуемого отверстия мм
Наименьший диаметр шлифуемого отверстия мм
Наибольший диаметр устанавливаемого изделия мм
Наибольший диаметр устанавливаемого изделия в кожухе мм
Наибольшая длина устанавливаемого изделия мм
Наибольшая длина шлифования при наибольшем диаметре шлифования мм
Наибольшая длина шлифования при наименьшем диаметре шлифования мм
Диаметр гильзы внутришлифовальной головки мм
Условный размер конца шпинделя изделия по ГОСТ 12595-72
Расстояние от зеркала стола до оси шпинделя изделия мм
Расстояние от оси шпинделя изделия до подошвы станины мм
Наибольшее расстояние от опорного торца фланца шпинделя изделия до торца корпуса шлифовальной бабки мм
Расстояние от торца нового круга торцешлифовального приспособления до опорного торца фланца шпинделя изделия мм
Наибольший диаметр шлифовального круга мм
Габаритные размеры станка без баков и электрошкафа
Масса станка кг ( с электрошкафом баком эмульсии баком гидросистемы и принадлежностями)
Проведем подбор оборудования для операции 040 –шлифовальная. На данной операции производится шлифование основания.
Для данной операции выберем плоскошлифовальный станок мод. 3756 который предназначен для выполнения точных внутришлифовальных работ в серийном производстве машиностроительных предприятий.
Основные технические характеристики станка 3756 представлены ниже:
Max размеры шлифуемых поверхностей (диаметр или ширина высота) мм: 750 350
Размер электромагнитного стола (наружный внутренний) мм: 750 -
Наиб. вертикальное перемещение шлиф. бабки мм 450
Колич. шлифовальных бабок 1
Ускоренное перемещение шлиф. бабки ммин 0586
Наибольшее продольное перемещение стола мм 550
Скорость продольного перемещения стола ммин 39
Бесступенчатое регулировавание Бесступенчатое регулировавание
Пределы или вертикальный подачи шлифов бабки мммин 016-16
Вертикальное перемещение шлифов бабки за одно деление лимба мм 001
Диаметр шлифовального круга (сегментного кольцевого) 450 450
Число оборотов шлифовального круга в минуту 975
Число скоростей вращения стола 6
Числа оборотов или пределы чисел оборотов стола в минуту 5; 7; 10; 14; 20; 29
Мощность электродвигателя главного движения кВт 28
Габариты станка мм: 2600x1565x2530
Масса станка кг 7300
Анализируя данные выбранных станков можно сделать следующие выводы:
станки подходят по назначению для выполнения требуемых операций;
габариты рабочей зоны станков обладают достаточными размерами для размещения в ней приспособления и детали;
применение станков в среднесерийном производстве приемлемо;
точность обработки на станках обеспечивает требуемую точность получаемых поверхностей.
Следовательно выбранные станки подходят для выполнения соответствующих заданных операций.
Проведем выбор режущего инструмента для операции 005 – вертикально-фрезерной. Исходными данными для этой операции будут:
- материал детали – Чугун СЧ20 ГОСТ 1412-85;
- размер обрабатываемой поверхности – 69х100 мм (Rz40 мкм 14-й квалитет точности);
- содержание операции – фрезерование поверхности;
- оборудование – станок вертикально-фрезерный 6Р13.
Для фрезерования примем материал режущей части инструмента твердый сплав – ВК8. Данный материал обладает следующими свойствами: предел прочности на изгиб ; плотность ; твердость HRC≥875 который подходит для обработки стали твердостью НВ не более 241.
В качестве инструмента выберем торцовую насадную фрезу со вставными ножами 2214-0153 ГОСТ 9473-80 оснащенными пластинами из твердого сплава ВК8.
Проведем выбор режущего инструмента для операции 010 – вертикально-фрезерной. Исходными данными для этой операции будут:
- размер обрабатываемой поверхности – приблизительно 40х40 мм (Rz40 мкм 14-й квалитет точности);
- содержание операции – фрезерование уступа;
Для точения наружной цилиндрической поверхности детали и снятия фасок примем материал режущей части инструмента - легированная сталь - Р6М5. Данный материал обладает следующими свойствами: Сталь марки Р6М5 содержит 6% вольфрама и 5% молибдена.
Характерные физико-механические свойства: Повышенная прочность повышенная склонность к обезуглероживанию и выгоранию молибдена.
Шлифуемость:Удовлетворительная.
Область применения: Для всех видов режущего инструмента при обработке углеродистых и легированных конструкционных сталей предпочтительны для изготовления резьбонарезного инструмента а также инсрумента работающего с ударными нагрузками.
Химический состав в %: C - 0.82 - 0.9 Si - до 0.5 Mn - до 0.5 Ni - до 0.4 S - до 0.025 P - до 0.03 Cr - 3.8 - 4.4 Mo - 4.8 - 5.3 W - 5.5 - 6.5 V - 1.7 - 2.1 Co - до 0.5
В качестве инструмента выберем фрезу концевую ∅600 х 195 х 365 Z=5 КМ5 кхв Р6М5 ГОСТ1092-85
Проведем выбор режущего инструмента для операции 015 –сверлильной. Исходными данными для этой операции будут:
- диаметр сверления – ∅11 мм ;
- содержание операции – сверление 3-х отверстий;
- оборудование – Вертикально-сверлильный станок 2Н118.
Для сверления отверстий в качестве инструмента выберем сверло спиральное Р6М5 ∅11 мм с цх ГОСТ 10902-77.
Проведем выбор режущего инструмента для операции 020 – сверлильной. Исходными данными для этой операции будут:
- содержание операции – сверление 3-х отверстий зенковка 3-х фасок;
Для сверления и зенковки выберем материал режущей части инструмента – Р6М5.
Сталь марки Р6М5 содержит 6% вольфрама и 5% молибдена.
Шлифуемость: удовлетворительная.Область применения: Для всех видов режущего инструмента при обработке углеродистых и легированных конструкционных сталей предпочтительны для изготовления резьбонарезного инструмента а также инструмента работающего с ударными нагрузками. Химический состав в %: C - 0.82 - 0.9 Si - до 0.5 Mn - до 0.5 Ni - до 0.4 S - до 0.025 P - до 0.03 Cr - 3.8 - 4.4 Mo - 4.8 - 5.3 W - 5.5 - 6.5 V - 1.7 - 2.1 Co - до 0.5
В качестве инструмента выберем сверло спиральное с цилиндрическим хвостовиком 2300-0758 ГОСТ 10902-77 (Исполнение 1 правое; диаметр сверла - ∅8 мм длина сверла – 105 мм длина рабочей части – 48 мм) зенковку коническую ГОСТ 1953-80
Проведем выбор режущего инструмента для операции 025 – токарной. Исходными данными для этой операции будут:
- диаметр обрабатываемой поверхности – ∅551 мм (Ra25 10 квалитет точности);
- содержание операции – точение торцов растачивание отверстия точение фасок;
- оборудование – токарный станок 16К20Ф3С5
Для точения внутренней цилиндрической поверхности детали и снятия фасок примем материал режущей части инструмента - твердый сплав - ВК6. Данный материал обладает следующими свойствами: предел прочности на изгиб ; плотность ; твердость HRC≥885 который подходит для обработки чугунов твердостью НВ 240.
Резец проходной отогнутый 450 ГОСТ 18869-73 Резец токарный фасочный ГОСТ 18875-73 с пластинами из твердого сплава ВК6 (сечения державки ВxH=20х20) и токарный расточной резец для скв отв ВК8 ГОСТ 18882-82 (сечения державки ВxH=16х16).
Резец будет закрепляться в резцедержателе 1-30 ОСТ 2 П15-7-84.
Проведем выбор режущего инструмента для операции 035 – внутришлифовальная. Исходными данными для этой операции будут:
- диаметр обрабатываемой поверхности – ∅55 мм (Ra125 9 квалитет точности);
- содержание операции – шлифование отверстия;
- оборудование – внутришлифовальный станок 3К225В.
Для шлифования наружной цилиндрической поверхности в качестве инструмента выберем шлифовальный круг ПП 13235 9А 40-П С2 5 К5 35мс-1 1кл. А. ГОСТ 2424-82.
Анализируя полученные сведения можно сделать вывод о том что выбранный режущий и вспомогательный инструмент подходит для соответствующих операций выполняемых при механической обработке детали.
Выберем приспособление для выполнения операции 005 – вертикально-фрезерной. Исходными данными для выбора приспособления являются:
-габаритные размеры детали 69х100х165 мм
-тип производства – массовый
-габариты рабочей зоны станка (наибольший диаметр устанавливаемой детали над станиной – 200 мм наибольшая длина обрабатываемой детали – 100мм)
-принятая схема базирования (наружная поверхность).
Для осуществления данной схемы базирования и обеспечения остальных требований наиболее приемлемым приспособлением являются тиски для точных станочных работ с пневмозажимом ГОСТ 20746-84.
По габаритным размерам детали и станка подбираем модель тисков 7033-0035.
Данная модель обладает следующими характеристиками:
- размеры зажимной детали – 25 175 мм
Выберем приспособление для выполнения операции 015 - сверлильной.
Для осуществления данной схемы базирования и обеспечения остальных требований наиболее приемлемым приспособлением является кондуктор УСПО.
По габаритным размерам детали и станка подбираем модель необходимый кондуктор УСПО8Е (габариты базовых плит 300-200 мм; максимальная масса устанавливаемых заготовок – 5 кг).
Выберем приспособление для выполнения операции 025 - токарной. Исходными данными для выбора приспособления являются:
-габаритные размеры детали (наибольший диаметр - ∅34 мм длина – 40 мм)
-тип производства – среднесерийный
-габариты рабочей зоны станка (наибольшее осевое перемещение - 150 мм наибольший диаметр сверления в стали 45 ГОСТ 1050-88 - 18мм)
-принятая схема базирования (наружная цилиндрическая поверхность и торцы).
Для осуществления данной схемы базирования и обеспечения остальных требований наиболее приемлемым приспособлением является общемашиностроительный комплекс универсально-сборной и переналаживаемой оснастки УСПО.
По габаритным размерам детали и станка подбираем УСПО8Е (габариты базовых плит 300-200 мм; максимальная масса устанавливаемых заготовок – 5 кг).
Выберем приспособление для выполнения операции 035 - внутришлифовальной. Исходными данными для выбора приспособления являются:
Для осуществления данной схемы базирования и обеспечения остальных требований наиболее приемлемым приспособлением является планшайба со специальными закрепленными упорами для автоматического позиционирования.
Из перечисленных выше характеристик приспособлений следует что соответствующие приспособления подходят для выполнения операций
механической обработки детали.
6. Выбор измерительного инструмента.
Измерительный инструмент - это техническое устройство используемое при измерениях и имеющее нормированные метрологические свойства. При выборе измерительного инструмента учитываются формы контроля (сплошной или выборочный масштаб производства конструктивные характеристики детали точность её изготовления).
В соответствии с габаритными размерами детали в качестве основного измерительного инструмента выбираем: штангенциркуль ШЦ – II (ЧИЗ) (0-250) ГОСТ 166-89 с ценой делений 005 мм и микрометр МК 50-1 ГОСТ 6507-90.
Для проверки шероховатости поверхностей с качеством поверхности соответственно Ra125 и Ra25 используем набор эталонов шероховатости ГОСТ 9378-93.
Рассчитаем припуски на обработку функциональной поверхности – внутренней цилиндрической поверхности ∅55H7.
Технологический маршрут обработки поверхности ∅55H7 состоит из растачивания чистового и предварительного и чистового шлифования.
Расчет припусков и предельных размеров по технологическим переходам на обработку поверхности D=55+003 мм.
Технологические переходы обработки поверхности D=50
Расчетный припуск zmin
Расчетный размер Rp мм
Предельный размер мм
Предельные значения припусков мкм
Предварительное шлифование
Общий припуск - zобщ
Технологический маршрут обработки поверхности D=55мм состоит из растачивания предварительного и шлифования предварительного и чистового. Растачивание и шлифование производится в специальном приспособлении планшайбе.
Записываем технологический маршрут обработки в расчетную табл. В таблицу также записываем соответствующие заготовке и каждому технологическому переходу значения элементов припуска.
Суммарное отклонение:
ρм-отклонение межосевого расстояния отверстий .мм
ρр-отклонение расположения отверстий относительно технологических баз. Мм
Погрешность установки в приспособлении:
Расчет минимальных значений припусков производим пользуясь основной формулой:
i — погрешность установки заготовки на выполняемом переходе.
Минимальный припуск:
под предварительное растачивание:
zmin1 =(50+50)+4250+50= 4400 мкм
под предварительное шлифование:
zmin1 =(25+25)+510+50= 600 мкм
под чистовое шлифование:
zmin1 =(20+20)+410+50= 500 мкм
Максимальный припуск:
TDi-1 — допуски размеров на предшествующем переходе и TDi — допуски размеров на выполняемом переходе.
zmax1 =4400+500= 4900 мкм
zmax2 =600+318= 918 мкм
zmax3 = 500+ 218=718
Производим расчет по остальным графам таблицы.
Определим номинальный припуск:
zном1=500+600+4400=4900 мкм
zном2=4900+718+918=6618 мкм
Номинальный размер заготовки:
Следовательно на чертеже заготовки будет диаметр. D=4830+20
Расчет режимов резания сил и моментов резания для операции 005 вертикально-фрезерная
I. Фрезерование плоскости
Глубина фрезерования рассчитывается по формуле:
t=H-h=1013-1003=1 мм
Режущий инструмент: фреза торцовая насадная 2214-0153 ВК8 ГОСТ 9473-80 число зубьев ширина фрезерования .
Подача. При фрезеровании различают подачу на один зуб подачу на один оборот фрезы и подачу минутную которые находятся в следующем соотношении:
где - частота вращения фрезы
- число зубьев фрезы.
Подача на зуб фрезы при фрезеровании торцовыми фрезами с пластинами из твёрдого сплава ВК8 при мощности станка 6Р13 равной 34 кВт равна: сравнив с техническими характеристиками станка 6Р13 принимаем тогда .
Скорость резания – окружная скорость фрезы определяется по формуле
гдезначения коэффициента и показателей степени смотрим по таблице:
- период стойкости его определяем по таблице ;
- общий поправочный коэффициент на скорость резания учитывающий фактические условия резания
где - коэффициент учитывающий качество обрабатываемого материала : .
- коэффициент учитывающий состояние поверхности заготовки (без корки) .
- коэффициент на инструментальный материал .
Рассчитываем скорость резания
Определяем по формуле:
Сравнивая с техническими характеристиками станка 6Р13 выбираем ближайшее меньшее значение частоты вращения - .
Фактическая скорость резания определяется по формуле:
Сила резания. Главная составляющая силы резания при фрезеровании – окружная сила она рассчитывается по формуле:
гдезначения коэффициента и показателей степени смотрим по таблице: ; .
Значение коэффициента приведено в таблице .
Таким образом получаем .
Рассчитываем силу резания
Крутящий момент на шпинделе определяем по формуле:
Мощность резания определяют по формуле:
По техническим характеристикам станка 6Р13 его максимальная мощность . Так как то рассчитанные режимы резания подходят.
Расчет режимов резания сил и моментов резания для операции 010 вертикально-фрезерная
Глубина фрезерования
На этой операции фрезеруется уступ срезая радиус R5 поэтому принимаем глубину резания 5 мм при ширине фрезерования 5мм.
Режущий инструмент: Фреза концевая ∅600 х 195 х 365 Z=5 КМ5 кхв Р6М5 ГОСТ1092-85 ширина фрезерования .
Подача на зуб фрезы при фрезеровании торцовыми фрезами с пластинами из твёрдого сплава Р6М5 при мощности станка 6Р13 равной 34 кВт равна: сравнив с техническими характеристиками станка 6Р13 принимаем тогда .
Расчет режимов резания сил и моментов резания для операции 015 - Сверлильная
Рассверливание отверстия ∅88 до 11 мм l = 40 мм.
Глубина резания. При сверлении глубина резания определяется по формуле:
Режущий инструмент: сверло спиральное Р6М5 .
Подача. При сверлении отверстий глубиной подачу определяют по табличному значению. Табличное значение подачи для сверла диаметром - 3.
Сравнив табличное значение подачи с техническими характеристиками станка выбираем .
Скорость резания. Скорость резания при сверлении определяется по формуле:
гдезначения коэффициента и показателей степени смотрим по таблице:;
где - коэффициент на обрабатываемый материал
- коэффициент учитывающий глубину сверления .
Рассчитываем скорость резания.
Частота вращения. Определяем по формуле:
Сравнивая с техническими характеристиками станка выбираем ближайшее меньшее значение частоты вращения - .
Крутящий момент и осевая сила. Они рассчитываются по формулам:
где и и показатели степени и определяем по таблице:
- для крутящего момента;
- коэффициент учитывающий фактические условия обработки в данном случае зависит только от материала обрабатываемой заготовки и определяется выражением .
Значение коэффициента приведено в таблице: .
Тогда крутящий момент .
Мощность резания определяют по формуле т.е..
По техническим характеристикам станка 2Н118 его максимальная мощность . Так как то рассчитанные режимы резания подходят.
Аналагично рассчитываем режимы резания для операции 020 – сверлильная
Переход 1. Сверление 3-х отверстий ∅8 мм
Переход 2. Зенкование фаски 15х45° (3 фаски)
Расчет режимов резания сил и моментов резания для операции 025 - Токарная
Черновое точение внутренней цилиндрической поверхности ∅56 мм и l = 69 мм.
Глубина резания при черновом точении и отсутствии ограничений принимается максимально возможной .
Режущий инструмент: резец проходной упорный ВК6 ГОСТ 18879-73 размер державки 16х25мм.
Подача определяется по таблице. При диаметре детали ∅56 мм подача равна . Принимаем сопоставив табличное значение подачи с техническими характеристиками станка 16К20Ф3.
Скорость резания определяется по формуле
где - стойкость режущего инструмента принимается в пределах 30-60мин примем .
Значения коэффициента и показателей степени смотрим по таблице:
Сравнивая с техническими характеристиками станка 16К20Ф3 выбираем ближайшее меньшее значение частоты вращения - .
Сила резания. Силу резания принято раскладывать на составляющие силы направленные по осям координат станка (тангенциальную радиальную и осевую ). Эти составляющие рассчитываются по формуле:
гдезначения коэффициента и показателей степени смотрим по таблице для составляющей : .
Поправочный коэффициент представляет собой произведение ряда коэффициентов: учитывающих фактические условия резания. Численные значения этих коэффициентов берём из таблиц:
; ; - передний угол ; - угол наклона главного лезвия ; - радиус при вершине .
Таким образом сила резания будет равна:
По техническим характеристикам станка 16К20Ф3 его максимальная мощность . Так как то рассчитанные режимы резания подходят.
Расчет режимов резания сил и моментов резания для операции 030 – Сверлильная
Сверление отверстия ∅8 мм l = 10 мм.
Расчет режимов резания сил и моментов резания для операции 035 внутришлифовальная
Шлифование отверстия ∅55 мм.
Режимы резания силы и моменты резания сводятся в таблицу 13.
Вертикально-фрезерная
- глубина резания мм;
- подача (продольная при шлифовании) мм;
- подача на один зуб фрезы при фрезеровании ммзуб;
- поперечная подача при шлифовании мммин;
- скорость резания ммин;
- скорость круга при шлифовании ммин;
- скорость заготовки при шлифовании ммин.
- тангенциальная составляющая силы резания (окружная сила при сверлении) Н;
- мощность резания кВт.
Произведем расчет технического нормирования операций 025 и 040 для остальных операций устанавливаем по нормативам.
Нормирование для операции 025 токарная
Основное (технологическое) время для обтачивания внутренней поверхности определится как
где - расчетная длина пути резца имеющего наибольшую длину обтачивания; - число проходов; n - число оборотов шпинделя в минуту; s - подача резца за один оборот шпинделя в мм.
Число оборотов шпинделя
где - скорость резания; d - диаметр наружной поверхности.
где - длина поверхности обтачиваемой резцом; - величина врезания резца включая путь на подход резца; - величина перебега резца.
Величина врезания поперечным перемещением продольного суппорта определяется по формуле
где - глубина резания; - главный угол резца в плане.
Величина перебега резца
Количество проходов .
Определим состав подготовительно-заключительного времени : установка заготовки на планшайбе – 7 мин; установка резца в многорезцовой державке – 2 мин; получение инструмента и приспособлений до начала работы и сдачи их после завершения работы – 7 мин. Т.о. .
Время на установку и снятие детали закрепление ее и открепление (планшайба) .
Время на приемы управления : включить и выключить станок кнопкой – 001 мин; переместить каретку суппорта в продольном направлении – 006 мин. Тогда .
Время затраченное на измерение детали равно 016 мин; при 20% контролируемых деталей получим .
Поправочный коэффициент на вспомогательное время при массовом производстве .
Вспомогательное время .
Время на обслуживание рабочего места и отдых составляет 8% оперативного времени тогда
Штучно-калькуляционное время определим по формуле:
где n – количество изделий в партии.
Нормирование для операции 035 плоскошлифовальная
Основное (технологическое) время для плоского шлифования торцом круга на станках продольного типа определится как
где - длина хода стола в мм; - припуск на сторону; - скорость продольного хода стола в ммин - вертикальная подача круга на один проход в мм; m – количество деталей одновременно устанавливаемых на столе; - коэффициент учитывающий точность шлифования.
При ; ; ; ; m=1; основное время будет равно
Определим состав подготовительно-заключительного времени : установка заготовки в тисках – 8 мин. Т.о. .
Время на установку и снятие детали закрепление ее и открепление (тиски) .
Время на приемы управления : включить и выключить станок кнопкой – 001 мин; подвести или отвести шлифовальный круг к детали в вертикальном направлении – 004 мин. Тогда .
Время затраченное на измерение детали равно 022 мин; при 20% контролируемых деталей получим .
Поправочный коэффициент на вспомогательное время при среднесерийном производстве .
Время на техническое обслуживание рабочего места для шлифовальных операций где - время на одну правку шлифовального круга; - период стойкости абразивного инструмента.
Время на организационное обслуживание рабочего места составляет 15% оперативного времени тогда
Время перерывов на отдых и личные надобности составляет 4% от основного тогда .
Расчеты норм времени сводятся в таблицу 14.
Общее время изготовления одной детали
При выполнении данной курсовой работы был разработан один из возможных вариантов технологического процесса обработки детали «Кронштейн».
Было подобрано соответствующее оборудование и станочные приспособления с установлением рациональных режимов резания и технологически обоснованных норм времени режущий вспомогательный и измерительный инструмент. Произведен расчет припусков на обрабатываемые поверхности детали.
Проделанная работа позволила закрепить и применить полученные знания по курсам: Технология машиностроения; Метрология стандартизация сертификация.
Выполнение данной курсовой работы способствовало более подробному ознакомлению с принятой в машиностроении терминологией с общей последовательностью выполнения проектных работ; получению навыков оценки степени технологичности изделия и способам ее повышения. а также получению первичных знаний и навыков варианта технологического процесса обеспечивающего получение заданного качества изделия наиболее производительными и рентабельными способами.
Ансеров М.А. Приспособления для металлорежущих станков. Расчеты и конструкции. - изд. 3-е стереотип. - М.: изд-во "Машиностроение" 1966. - 652 с. ил.
Анурьев В.И. Справочник конструктора-машиностроителя: В 3 т. Т.1. - 8-е изд. перераб. и доп. Под ред И.Н. Жестковой. - М.: Машиностроение 2001. - 920 с. ил.
Допуски и посадки: Справочник в 2-х ч. Ч.1Под ред. В.Д. Мягкова. - 5-е изд. перераб. и доп. - Л.: Машиностроение. Ленингр. отд-ние 1979. - 544 с. ил.
Допуски и посадки: Справочник в 2-х ч. Ч.2Под ред. В.Д. Мягкова. - 5-е изд. перераб. и доп. - Л.: Машиностроение. Ленингр. отд-ние 1979. - 544 с. ил.
Егоров М.Е. Технология машиностроения: Учебник для вузовМ.Е. Егоров В.И. Дементьев В.Л. Дмитриев. - М.: Высш. школа 1976. - 534 с. ил.
Кожевников Д.В. Гречишников В.А. Кирсанов С.В. Кокарев В.И. Схиртладзе А.Г. Режущий инструмент: Учебник для вузов [Текст] Под редакцией С.В. Кирсанова. М.: Машиностроение 2004. - 512 с. ил.
Лебедев Л.В. Шрубченко И.В. Погонин А.А. Схиртладзе А.Г. Основы технологии машиностроения: учеб. пособие Л.В. Лебедев И.В. Шрубченко А.А. Погонин А.Г. Схиртладзе. - 3-изд. перераб. и доп. - Белгород: Изд-во БГТУ им. В.Г. Шухова 2005. - 264 с. ил.
Маталин А.А. Технология машиностроения: Учебник для машиностроительных вузов по специальности "Технология машиностроения металлорежущие станки и инструменты". - Л.: Машиностроение Ленингр. отд-ние 1985. - 496 с. ил.
Металлорежущие станки (альбом общих видов кинематических схем и узлов). Кучер А.М. Киватицкий М.М. Покровский А.А. Изд-во "Машиностроение" 1972. - 308 с. ил.
Оборудование машиностроительных предприятий: Учебник А.Г. Схиртладзе В.И. Выходец Н.И. Никифоров Я.Н. Отений ВолгГТУ Волгоград 2005. - 128 с.
Справочник инструментальщика И.А. Ординарцев Г.В. Филиппов А.Н. Шевченко и др.; Под общ. ред. И.А. Ординарцева. - Л.: Машиностроение. Ленингр. отд-ние 1987. - 846 с. ил.
Справочник технолога-машиностроителя. В 2-х т. Т.1Под ред А.Г. Косиловой и Р.К. Мещерякова. - 4-е изд. перераб и доп. - М.: Машиностроение 1985. - 656 с. ил.
Справочник технолога-машиностроителя. В 2-х т. Т.2Под ред А.Г. Косиловой и Р.К. Мещерякова. - 4-е изд. перераб и доп. - М.: Машиностроение 1986. - 496 с. ил.
ГОСТ 3.1118-82 Единая система технологической документации. Формы и правила оформления маршрутных карт.
ГОСТ 3.1125-88 Правила графического выполнения элементов литейных форм и отливок.
ГОСТ 3.1404 Формы и правила оформления документов на технологические процессы и операции обработки резанием.
ГОСТ 2675-80 Патроны самоцентрирующиеся трехкулачковые.
ГОСТ 17123-79 Круги эльборовые шлифовальные. Типы и основные размеры.
ГОСТ 18868-73 Резцы токарные проходные отогнутые с пластинками из быстрорежущей стали. Конструкция и размеры.
ГОСТ 18880-93 Резцы токарные подрезные отогнутые с пластинами из твердого сплава. Конструкция и размеры.
ГОСТ 26645-85 Отливки из металлов и сплавов. Допуски размеров массы и припуски на механическую обработку.
Тех. процесс А1(V5).cdw

содержание переходов
Заготовительная операция
ПОСЛЕДОВАТЕЛНОСТЬ ВЫПОЛНЕНИЯ ТЕХНОЛОГИЧЕСКИХ ОПЕРАЦИЙ
Штангенциркуль 0-250 мм (0
ШЦ - II (ЧИЗ) ГОСТ 166-89
Микрометр МК 50-1 ГОСТ 6507-90
Набор эталонов для измерения
Вертикально-фрезерная
Установка заготовки в
тиски с упором в торец.
Фрезерование плоскости
Станок вертикально-фрезерный
на базе 6Р13 с ЧПУ NC-210
Тиски для точных станочных
работ с пневмозажимом ГОСТ
Торцовая насадная фреза со
пластинами из твердого сплава
?100 мм ГОСТ 9473-80
работ с пневмозажимом
кхв Р6М5 ГОСТ 1092-85
Сверлильная операция
специальное устройство
Рассверливание 3 отверстий
мм с шероховатостью
специальное устройство
сверление 3 отверстий
Зенкование 3 фасок 1х45О.
Точение торцев выдерживая
Растачивание отверстия
?55.1 с качеством поверхности
Точение 3х фасок 1х45О
Сверление отверстия ?8
Зенкование фаски 1х45О
Установить заготовку
Шлифовать отверстие
Плоскошлифовальная операция
выдерживая размер 100-0
и требования шероховатости
Контрольная операция
Проверка требуемых размеров.
Вертикально-сверлильный
Сверло спиральное Р6М5
?11 мм с цх ГОСТ 10902-77
Сверло спиральное с
цилиндрическим хвостовиком ?8
Зенковка коническая
Токарный станок 16К20Ф3С5
Резец проходной отогнутый 45
Резец токарный фасочный
Резец расточной для скв отв
х16х140 ВК8 ГОСТ 18882-82
Разработка технологического процесса
изготовления кронштейна
Внутришлифовальный станок
А 40-П С2 5 К5 35мс-1 1кл. А.
Плоскошлифовальный станок
Последовательность выполнения
технологических операций
изготовления кронштейнаи
БГТУ им. В.Г. Шухова
Тех. процесс А1(V11).cdw

содержание переходов
Заготовительная операция
ПОСЛЕДОВАТЕЛНОСТЬ ВЫПОЛНЕНИЯ ТЕХНОЛОГИЧЕСКИХ ОПЕРАЦИЙ
Штангенциркуль 0-250 мм (0
ШЦ - II (ЧИЗ) ГОСТ 166-89
Микрометр МК 50-1 ГОСТ 6507-90
Набор эталонов для измерения
Вертикально-фрезерная
Установка заготовки в
тиски с упором в торец.
Фрезерование плоскости
Станок вертикально-фрезерный
на базе 6Р13 с ЧПУ NC-210
Тиски для точных станочных
работ с пневмозажимом ГОСТ
Торцовая насадная фреза со
пластинами из твердого сплава
∅100 мм ГОСТ 9473-80
работ с пневмозажимом
кхв Р6М5 ГОСТ 1092-85
Сверлильная операция
специальное устройство
Рассверливание 3 отверстий
мм с шероховатостью
специальное устройство
сверление 3 отверстий
Зенкование 3 фасок 1х45О.
Точение торцев выдерживая
Растачивание отверстия
∅55.1 с качеством поверхности
Точение 3х фасок 1х45О
Сверление отверстия ∅8
Зенкование фаски 1х45О
Установить заготовку
Шлифовать отверстие
Плоскошлифовальная операция
выдерживая размер 100-0
и требования шероховатости
Контрольная операция
Проверка требуемых размеров.
Вертикально-сверлильный
Сверло спиральное Р6М5
∅11 мм с цх ГОСТ 10902-77
Сверло спиральное с
цилиндрическим хвостовиком ∅8
Зенковка коническая
Токарный станок 16К20Ф3С5
Резец проходной отогнутый 45
Резец токарный фасочный
Резец расточной для скв отв
х16х140 ВК8 ГОСТ 18882-82
Внутришлифовальный станок
А 40-П С2 5 К5 35мс-1 1кл. А.
Плоскошлифовальный станок
Разработка технологического процесса
изготовления кронштейна
Последовательность выполнения
технологических операций
изготовления кронштейнаи
БГТУ им. В.Г. Шухова
Тех. процесс А1.cdw

содержание переходов
Заготовительная операция
ПОСЛЕДОВАТЕЛНОСТЬ ВЫПОЛНЕНИЯ ТЕХНОЛОГИЧЕСКИХ ОПЕРАЦИЙ
Штангенциркуль 0-250 мм (0
ШЦ - II (ЧИЗ) ГОСТ 166-89
Микрометр МК 50-1 ГОСТ 6507-90
Набор эталонов для измерения
Вертикально-фрезерная
Установка заготовки в
тиски с упором в торец.
Фрезерование плоскости
Станок вертикально-фрезерный
на базе 6Р13 с ЧПУ NC-210
Тиски для точных станочных
работ с пневмозажимом ГОСТ
Торцовая насадная фреза со
пластинами из твердого сплава
∅100 мм ГОСТ 9473-80
работ с пневмозажимом
кхв Р6М5 ГОСТ 1092-85
Сверлильная операция
специальное устройство
Рассверливание 3 отверстий
мм с шероховатостью
специальное устройство
сверление 3 отверстий
Зенкование 3 фасок 1х45О.
Точение торцев выдерживая
Растачивание отверстия
∅55.1 с качеством поверхности
Точение 3х фасок 1х45О
Сверление отверстия ∅8
Зенкование фаски 1х45О
Установить заготовку
Шлифовать отверстие
Плоскошлифовальная операция
выдерживая размер 100-0
и требования шероховатости
Контрольная операция
Проверка требуемых размеров.
Вертикально-сверлильный
Сверло спиральное Р6М5
∅11 мм с цх ГОСТ 10902-77
Сверло спиральное с
цилиндрическим хвостовиком ∅8
Зенковка коническая
Токарный станок 16К20Ф3С5
Резец проходной отогнутый 45
Резец токарный фасочный
Резец расточной для скв отв
х16х140 ВК8 ГОСТ 18882-82
Внутришлифовальный станок
А 40-П С2 5 К5 35мс-1 1кл. А.
Плоскошлифовальный станок
Разработка технологического процесса
изготовления кронштейна
Последовательность выполнения
технологических операций
изготовления кронштейнаи
БГТУ им. В.Г. Шухова
Рекомендуемые чертежи
- 28.05.2016
- 18.10.2023
- 24.01.2023
- 25.09.2011
- 25.09.2011