Технологический процесс изготовления детали - втулка с годовым объемом выпуска 18000 шт




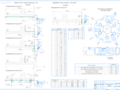
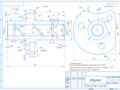
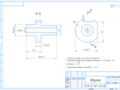
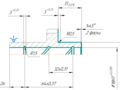
- Добавлен: 24.01.2023
- Размер: 498 KB
- Закачек: 1
Описание
Состав проекта
![]() |
![]() ![]() ![]() |
![]() ![]() ![]() |
![]() ![]() ![]() |
![]() ![]() ![]() |
![]() ![]() ![]() |
![]() ![]() ![]() |
![]() ![]() ![]() ![]() |
![]() ![]() ![]() ![]() |
![]() ![]() ![]() |
![]() ![]() ![]() ![]() |
![]() ![]() ![]() |
![]() |
![]() ![]() ![]() |
Дополнительная информация
опер2_2008.doc
2150.0000 (1) – Резец подрезной черновой 25х25 К-01-4254-000 СБ ВК8 ГОСТ21151-75;
Точить поверхности 2 3 4 5 по программе начисто.
2150.0000 (1) – Резец подрезной чистовой 25х25 К-01-4255-000 СБ ВК8 ГОСТ21151-75;
3310.0000 (3 ) – Штангенциркуль ШЦ-I-125-01 ГОСТ 166-89
Точить канавку 6 с подрезкой торца 7 по программе начисто.
2150.0000 (1) – Резец канавочный 25х25 К-01-4205-000 СБ ВК8 ГОСТ21151-75;
ГОСТ 3.1404-86форма 2а
Программа Fanuc.docx
FANUK СЕРИИ 21I 210I – TA
№ 001 % М19 Т0101 F0.2 S1=600;
№ 005 G 71 P6 Q7 U0.3 W0 F0.3
№ 006 G00 X17.7 Z2.0 F0.21
№ 008 G90 G00 Z300.0
№ 011 G72 P12 Q 15 U0.4 W0.3 F0.3
№ 012 G00 X16.0 Z0 F0.6
№ 016 G90 G00 Z300.0 T0301
опер1_2010.doc
Наименование операции
Оборудование устройство ЧПУ
Обозначение программы
Токарный мод. 16Б16Т1
А. Установить и закрепить заготовку.
2801.0000(1)-Патрон трехкулачковый самоцентрирующий D=25-250 мм ГОСТ 24351-80.
Точить поверхность 1 по программе начерно.
2150.0000 (1) – Резец расточной черновой 25х25 К-01-4205-000 СБ ВК8 ГОСТ21151-75;
4250.0000(0)- Нутромер НИ 160 ГОСТ 868-82.
Обработка деталей на станках с ЧПУ
Контрольная по чугунной втулке.doc
и условиям эксплуатации . . . . . . . . . . . . . . . . . . . . . . . . . . . . . . . . . . . . . .
Анализ технологичности конструкции детали . . . . . . . . . . . . . . . . . . . . . . . .
Определение типа производства . . . . . . . . . . . . . . . . . . . . . . . . . . . . . . . . . .
Выбор и обоснование способа получения заготовки. . . . . . . . . . . . . . . . . . .
Список использованных источников . . . . . . . . . . . . . . . . . . . . . . . . . . . . . . .
Технические требования на деталь по чертежу и условиям эксплуатации
Втулка фланцевая изготовлена из чугуна с пластинчатым графитом СЧ15 ГОСТ 1412-85 предел прочности при растяжении В 150 МПа твердость 156-224 НВ химический состав: С - 35-367 % Si - 2-24 % Mn - 05-08 % P не более 02 % S не более 015 % [2].
К конструкции детали предъявляются следующие технические требования: неуказанные предельные отклонения размеров отверстий – Н14 валов – h14 остальных - ±JT142. Допуск торцевого биения фланца относительно обработанной цилиндрической поверхности втулки – 002 мм торца относительно той же поверхности – 005 мм.
Анализ технологичности конструкции детали
Под технологичностью детали понимают ее конструктивные особенности которые при наилучшем соответствии назначению детали обеспечивают минимальный уровень затрат на её изготовление.
Технологичной считают такую конструкцию литой детали которая в максимальной степени отвечает требованиям как литейной технологии так и технологии механической обработки.
Анализируя основные технологические требования и условия рациональной конструкции отливки [1] можно сделать вывод что конструкция отливки заданной детали технологична поскольку является типовой – фланцевая втулка.
Конструктивные особенности детали как то радиальная и прямая грани фланца являются нетиповыми и незначительно усложнят технологическую литейную оснастку и в целом на технологичность отливки не повлияют.
Вцелом деталь имеет хорошие установочные базы позволяю-
щие обрабатывать поверхности с заданной точностью. Возможно применение высокопроизводительных методов обработки при токарных операциях с совместной обработкой центрального отверстия и операции сверления отверстий с цековками. Для прямой грани фланца требуются фрезерные операции.
Нетехнологичными в конструкции детали являются:
- фаска 2×45° на фланце. С точки зрения технологичности следует оставить литейный радиус
- угол 16° является нецелесообразным. Следует заменить на угол 15° что приведет к равным углам между осями отверстий и позволит применять типовые многошпиндельные сверлильные головки;
- глухой смазочный паз – является труднодоступным и непроизводительным в обработке. Его целесообразно исключить из конструкции втулки заменив спиральной канавкой.
При устранении вышеизложенных недостатков технологичность детали повысится на порядок.
Определение типа производства
Предварительно определяем тип производства в зависимости от массы детали и от объема выпуска по ГОСТ 3.1119-83:
Масса детали: m = 0866 кг
Годовая программа выпуска деталей N = 18 000 штгод.
На основании чего определяем: тип производства – среднесерийное.
Для уточненного определения типа производства находим коэффициент закрепления операций:
где н - планируемый нормативный коэффициент загрузки станка всеми закрепленными за ним однотипными операциями;
з - фактический коэффициент загрузки станка.
н=08 для среднесерийного производства.
где mp- расчетное количество оборудования на заданной операции;
mпр- принятое количество оборудования на заданной операции.
где Тш-к- штучно-калькуляционное время;
N- объем выпуска деталей в год;
Fд- действительный годовой фонд работы оборудования.
mпр получаем округлением mp до ближайшего большего целого числа.
Определим действительный годовой фонд работы оборудования для работы в две смены [2]:
Определим расчетное количество оборудования для каждой операции:
Операция токарная. Черновая и чистовая подрезка торца фланца и торцев втулки обточка внешней цилиндрической поверхности:
То = 0037(D2-d2)10-3 основное время черновой подрезки мин;
То = 0049(D2-d2)10-3 чистовая подрезка торцев мин;
То = 024dl10-3 тонкое обтачивание мин.
То = 10-3 (0037(802-312)+ 0049(802-312)+ 0037(382-152)+ +0049(382-152)+ 0173231+0243231)= 0815 мин.
Тш-к = 0815214 = 174
Операция токарная. Черновая и чистовая подрезка торца втулки расточка и двойное развёртывание нарезание спиральной канавки: φк=214;
То = 0037(D2-d2)10-3 основное время черновой подрезки мин;
То = 086dl10-3 развёртывание мин.
То = 04dl10-3 нарезка спиральной канавки мин.
То = 10-3 (0037(322-152)+ 0049(322-152)+ 0181895+ +08618952+041885)= 3932 мин.
Операция сверлильная. Сверление трёх отверстий с цековками за проход. Сверление отверстия с фаской.
То = 052dl10-3 сверление мин.
То =10-3(05211515+05237) = 0105 мин.
Тш-к = 0105172 = 0181
Операция фрезерная. Фрезерование прямой грани фланца цилиндрической фрезой за проход.
То = 5l10-3 фрезерование цилиндрической фрезой мин.
То = 56010-3 = 03 мин.
ΣОi = 615+127+57+20 = 8442
Производство мелкосерийное т.к. 20 Кз.о. 40 [3].
Выбор и обоснование способа получения заготовки
При выборе способа получения литой заготовки рассматривалось два возможных варианта: литьё в кокиль и центробежное.
При литье в кокиль главными отрицательными факторами оказались: необходимость применения стержня для формирования центрального отверстия; большая вероятность возникновения трещин и усадочных рыхлот в теле заготовки из-за неподатливости формы и присутствия температурных узлов; аллотропное строение структуры металла что не удовлетворяет требованиям и ведёт к необходимости последующей длительной и многоступенчатой термической обработке для ее исправления.
При центробежном литье с горизонтальной осью вращения отпадает необходимость в стержне для формирования центрального отверстия; получается подходящая структура металла втулки; под действие центробеж-
ных сил все нежелательные включения и усадочные рыхлоты сдвигаются в зоны удаляемые при механической обработке.
Недостатками в нашем случае является неточность внутренней полости отливки. Однако этот недостаток несущественен так как за базу принята внешняя поверхность втулки которая при центробежном литье получается достаточно точной и с учётом припусков на мех. обработку центральное отверстие будет обработано в соответствии с чертежом.
Проанализировав оба способа выбираем центробежное литье с горизонтальной осью вращения. Этот способ наиболее подходящий по экономическим и технологическим показателям [4].
Группа сложности отливки – 2.
Определим размеры и параметры качества заготовки:
) Класс размерной точности – 8;
) Основные допуски размеров (приведены в таблице 1).
Для обрабатываемых конструктивных элементов отливок всегда устанавливается симметричное расположение полей размерных допусков относительно номинальной размерной линии. Для необрабатываемых типа "вал" – в минус типа "отверстие" – в плюс.
) Степень коробления – 5. При такой степени коробления для нашей детали допуски формы и расположения поверхностей отсутствуют. [4]
) Степень точности поверхности – 8. Допуск отклонения неровностей поверхностей – 024 мм. Шероховатость поверхности отливки – Rа 10.
) Назначаемая степень точности массы – 8. Допуск на ее отклонение - 10%.
) Литейные припуски:
- основной – назначается в зависимости от допусков на размер и ряда припусков (ряд припусков на обработку – 2);
- дополнительный – в зависимости от допусков на коробление (в нашем случае отсутствуют) и смещения элементов отливки поплоскости разъёма (06 мм);
- общий – сумма основного и дополнительного припуска.
Таблица 1. Допуски и припуски на механическую обработку
Припуски мм (на сторону)
) Расчёт размеров отливки (приведены в таблице 2).
Таблица 2. Размеры отливки с припусками на механическую
) Обозначение точности отливки:
-5-8-8 ГОСТ 26645-85.
Список используемых источников
Проектирование технологических процессов в машиностроении: Учебное пособие для вузов. И. П. Филонов и др.; Под общ. ред. И. П. Филонова; +CD. – Мн.: УП "Технопринт" 2003. – 910 с.
Горбацевич А. Ф. Шкред В. А. Курсовое проектирование по технологии машиностроения: [Учеб. пособие для машиностроит. спец. вузов]. – 4-е изд. перераб. и доп. – Мн.: Высшая школа 1983. – 256 с.
Технология машиностроения : В 2кн. Кн. 1. Основы технологии машиностроения: Учеб. пособ. для вузов. Э. Л. Жуков И. И. Козарь С. Л. Мурашкин и др.; Под ред. С. Л. Мурашкина. – М.: Высш. шк. 2003 - 278 с.
Моргунов В.Н. Основы конструирования отливок. Параметры точности и припуски на механическую обработку: Учеб. Пособие.- Пенза: Изд-во Пенз. гос. ун-та 2004.- 164 с.
_РПЗ_2010_ТМС Чугунная втулка 2.doc
Кафедра «Технология машиностроения»
РАСЧЕТНО-ПОЯСНИТЕЛЬНАЯ ЗАПИСКА
по дисциплине «Технология машиностроения»
на тему: «Разработать технологический процесс изготовления детали – втулка с годовым объемом выпуска 18000и спроектировать средства технологического оснащения на сверлильную операцию»
Проектирование процесса механической обработки детали
1 Служебное назначение и технические требования на деталь по чертежу
и условиям эксплуатации
2 Анализ технологичности конструкции детали
3 Определение типа производства
4 Выбор и обоснование способа получения заготовки
5 Разработка маршрутной технологии обработки детали
6 Определение припусков расчётно-аналитическим методом
7 Проектирование операционной технологии
7.1 Расчет режимов резания на основные операции и их нормирование
7.2 Расчет точности обработки на чистовой операции
7.3 Выбор станковинструментасредств измерения и технологического оснащения
Проектирование средств технологического оснащения
1. Техническое описание конструкции и принципа работы приспособления ..
2. Определение параметров пневмозажима
Список использованных источников Заключение Приложение .
Приложение 1 Комплект технологической документации на обработку детали
Приложение 2 Спецификации на приспособление
Приложение 3 Ведомость проекта
Разработать технологический процесс
механической обработки детали -
Пояснительная записка содержит 35 листов
рисунка 2 таблицы 14 источников
Графическая часть - 2 листа формата А1
КЛЮЧЕВЫЕ СЛОВА: ВТУЛКА ПРИПУСК РЕЖИМЫ РЕЗАНИЯ НОРМЫ ВРЕМЕНИ СУММАРНАЯ ПОГРЕШНОСТЬ ОБРАБОТКИ ТЕХНОЛОГИЧЕСКАЯ НАЛАДКА ПРИСПОСОБЛЕНИЕ.
Разработаны технологический процесс механической обработки втулки и операционная технология.
Произведены технологические расчеты точности обработки. Сконструировано приспособление для сверлильной операции определены его технические характеристики и требования.
В условиях современной рыночной экономики предприятию необходимо постоянно совершенствовать технологию производства продукции чтобы выиграть преимущество в конкурентной борьбе. Эффективность производства его технический прогресс качество выпускаемой продукции во многом зависят от внедрения нового оборудования машин станков и аппаратов а также новых технологий. Поэтому необходимо совершенствовать технологию механической обработки и внедрять новое высокопроизводительное оборудование. В этой связи был разработан технологический процесс механической обработки детали - втулка. Механообработка детали производится на станках с числовым программным управлением которые позволяют повысить эффективность обработки и качество обработанных поверхностей уменьшить количество операций и время обработки.
Проектирование процесса механической обработки детали
1 Разработка маршрутной технологии обработки детали
Рисунок 1.1- Эскиз детали
Таблица 1.1 Маршрут обработки втулки
Наименование и содержание операции
Технологические базы
Токарная программная с ЧПУ
Расточить поверхность 7 по программе (начерно). 2 . Подрезать торец 4 точить поверхность 6подрезать торец 5 по программе (начерно). 3.Точить фаску 10 подрезать торец 4 точить фаску 9точить поверхность 6 по программе(начисто).
Подрезать торец 5 с точением канавки по программе(начисто).
Расточить поверхность 7точить канавку8 (начисто).
Подрезать торец 1(начерно). 2.Точить фаску 3подрезать торец 1 точить фаску 2.
Фрезеровать поверхность 11
Вертикально- фрезерный 6А12П
Вертикально-сверлильная
Сверлить 3 отверстия 13
Цековать 3 отверстия 12
Вертикально-сверлильный 2А135
Вертикально-сверлильная
Сверлить отверстие 15
Вертикально-сверлильный
2 Определение припусков расчетно-аналитическим методом
Проведем расчет припусков расчетно-аналитическим методом на один наиболее точный размер.
Рассчитаем припуски на обработку и промежуточные предельные размеры для отверстия диаметр 18Н7 (+0018).
Заготовка представляет собой отливку массой 11 кг. Технологический маршрут обработки отверстия диаметром 18Н7 (+0018) состоит из двух переходов: чистового и чернового растачивания выполняемых при одной установке обрабатываемой детали. Базами для заготовки служит противоположная цилиндрическая поверхность диаметром 32 мм.
Расчет припусков на обработку отверстия диаметром 18Н7 (+0018) приведен в таблице 1.2
Таблица 1.2 Расчет припусков на обработку отверстия диаметром 18Н7 (+0018)
ческие операции и переходы обработки отверстия
Элементы припусков мкм
ные значения припусков мм
Определение параметров качества обработки
Параметры качества поверхности Rza и Ta выбираем по таблицам [3] и заносим в таблицу 1.2.
Суммарное значение пространственных отклонений для заготовки данного типа определится по следующей формуле [3]:
где ρсм равно допуску на размер 38 мм ρсм=1100 мкм
Суммарное значение пространственных отклонений для отверстия после чернового и чистового растачивания определится соответственно [3]:
Погрешность установки при черновом растачивании определится [3]:
Погрешность базирования в данном случае равна нулю так как заготовка устанавливается в трехкулачковый патрон. Погрешность закрепления закр определяется по таблицам.
Погрешность установки при чистовом растачивании определится [3]:
Значения заносим в соответствующие графы таблицы 1.2
Допуск на размер заготовки получается по IT14 Td=1000мкм.
Допуск на размер после чернового растачивания получается по IT10 Td=70 мкм.
Допуск на размер после чистового растачивания получается по IT7 Td=18 мкм.
Определение расчетных минимальных припусков на обработку
Расчетный минимальный припуск определится [3]:
Определение расчетных размеров
Данная графа заполняется начиная с конечного размера последовательным вычитанием расчетного минимального припуска каждого технологического перехода.
Определение предельных размеров
В данной графе наибольшее значение получается по расчетным размерам округленным до точности допуска соответствующего перехода. Наименьшие предельные размеры определяются из наибольших предельных размеров вычитанием допусков соответствующих переходов.
Определение предельных значение припусков
Минимальные предельные значения припусков равны разности наибольших предельных размеров выполняемого и предшествующего переходов а максимальные значения- соответственно разности наименьших предельных размеров.
Определение общего номинального припуска:
где zоmin- суммарный минимальный припуск
ESз ESд- верхние отклонения на размер заготовки и детали.
Номинальный размер заготовки:
Проверка правильности расчетов
Расчеты произведены верно если выполнено условие [3]:
– 2518 = 1 – 0018 мм;
Построение схемы графического расположения припусков и допусков на обработку отверстия диаметром 18Н7 (+0018)
Рисунок 1.2- Схема графического расположения припусков и допусков на обработку отверстия диаметром 18Н7 (+0018) втулки
Припуск на заготовку полученный расчетно-аналитическим методом (3 мм) меньше такой же как определенный по ГОСТ 26645-85 (3 мм). Однако применение расчетно-аналитического метода требует большого и трудоемкого расчета поэтому для назначения припусков будем пользоваться методикой приведенной в ГОСТ 26645-85.
Проектирование операционной технологии
1. Выбор станков инструмента средств измерения и технологического оснащения
Выбираем станок модели 16Б16Т1 [14].
Выбор режущего инструмента:
Для черновой подрезки торцев и точения шейки выбираем резец с механическим креплением твердосплавной пластины К-01-4254-000 СБ [1]. Длина резца L=88 мм сечение державки bh=2525 мм твердосплавная пластина- трехгранная материал ВК8.
Для чистовой подрезки торца и точения шейки выбираем резец с механическим креплением твердосплавной пластины К-01-4255-000 СБ [1]. Длина резца L=88 мм сечение державки bh=2525 мм твердосплавная пластина - трехгранная материал ВК8 радиус при вершине резца R=1 мм.
Для чернового растачивания выбираем расточной резец с механическим креплением твердосплавной пластины К-01-4205-000 СБ [1]. Длина резца L=100 мм диаметр сечения державки d=15 мм твердосплавная пластина- трехгранная материал ВК8.
Для чистовой подрезки торца выбираем резец SRDC L 3225 PO5-N Длина резца L=170 мм сечение державки 32×25 мм твердосплавная пластина из материала ВК8 шириной 3 мм радиус при вершине резца R=05 мм.
Для чистового растачивания и Для растачивания канавки выбираем резец К-01-4150-000 СБ [1]. Длина резца L=100 мм диаметр сечения державки d=15 мм.
Выбор средств измерения:
Так как тип производства мелкосерийное в качестве измерительного инструмента выбираем:
Штангенциркуль ШЦ-I-125-001 ГОСТ 166-89;
Нутромер НИ 100 ГОСТ 868-82;
Штангенглубиномер ШГ-160 ГОСТ 162-89.
Выбор установочно-зажимного приспособления:
Выбираем патрон трехкулачковый самоцентрирующий ГОСТ 24351-80 установочный диаметр D=25-250 мм.
2. Расчет режимов резания на основные операции
Проведем расчет режимов резания на операцию 010 Токарная программная с ЧПУ. На данной операции выполняется черновое и чистовое растачивание отверстий детали справа черновая и чистовая подрезка двух торцев расточка канавки. Операция содержит пять инструментальных позиций.
Расчет режимов резания для инструментальной позиции 1:
На первой инструментальной позиции выполняется черновое растачивание диаметра 18 мм. Расчет режимов резания будем проводить в следующем порядке:
Определение глубины резания t (по табл. 1.2)
t = 125 мм. (на сторону)
Подачу выбираем в зависимости от глубины резания диаметра сечения резца и вида обрабатываемого материала [6]:
Определение расчетной скорости резания Vp
Скорость резания определяется в зависимости от подачи и глубины резания [6]:
Определение частоты вращения шпинделя n
где D- диаметр обрабатываемого отверстия
Округляем значение n = 1600 мин-1.
Определение фактической скорости резания V
Для первого перехода ммин
Проверка по мощности
Должно выполняться условие: Nтреб≤Nэд
где Nтреб- требуемая мощность
Nэд- мощность электродвигателя станка определяется из паспорта станка.
где Nрез- мощность резания
- коэффициент полезного действия станка.
где Pz- сила резания
Vф- скорость резания.
Расчет режимов резания для инструментальной позиции 2:
На второй инструментальной позиции выполняется три технологических перехода: черновая подрезка торца диаметром 32 мм черновое точение шейки диаметром 32 мм черновая подрезка торца диаметром 80 мм. Расчет режимов проводим по лимитирующему переходу то есть переходу на котором скорость резания будет максимальной. Максимальная скорость резания будет при подрезке торца диаметром 80 мм.
Расчет режимов резания будем проводить в следующем порядке:
Определение глубины резания t
Для черновых операций глубина резания определяется как 75% от припуска на обработку z:
для торца ø80 мм: t = 075z = 07524 = 18 мм.
где D- диаметр торца
Округляем значение n=315 мин-1.
Для второго перехода ммин
Для третьего перехода ммин.
Условие выполняется.
Расчет режимов резания для инструментальной позиции 3:
На третьей инструментальной позиции выполняются два технологических перехода: чистовая подрезка торца диаметром 32 мм с расточкой фасок и чистовое точение шейки диаметром 32 мм. Максимальная скорость резания будет при подрезке торца диаметром 32 мм.
для торца t = 32 – 24 = 08 мм
для шейки t = 30 – 22 = 08 мм
Подачу выбираем в зависимости от шероховатости достигаемой после операции и радиуса при вершине резца [6]:
Округляем значение n =1000 мин-1.
Расчет режимов резания для инструментальной позиции 4:
На четвёртой инструментальной позиции выполняется чистовая подрезка торца диаметром 80 мм и точение канавки шейки.
где D- обрабатываемый диаметр
Округляем значение n = 400 мин-1.
Расчет режимов резания для инструментальной позиции 6:
На пятой инструментальной позиции выполняется два технологических перехода: чистовая расточка отверстия диаметром 18 мм и точение спиральной канавки диаметром 21 мм шириной 3 мм. Расчет режимов проводим по лимитирующему переходу то есть переходу на котором скорость резания будет максимальной. Максимальная скорость резания будет при чистовой расточки отверстия диаметром 18 мм.
Расчет режимов резания для первого перехода будем проводить в следующем порядке:
Скорость резания определяется [6]:
где D- диаметр канавки
Округляем значение n = 2000 мин-1.
3. Расчет норм времени
Штучно-калькуляционное время определяется [3]:
где Тш- штучное время
Тп-з- подготовительно-заключительное время
n- количество деталей в партии.
где Тца- время цикла автоматической обработки
Тв- вспомогательное время
k- процент затрат времени на обслуживание рабочего места и отдых для мелкосерийного производства принимается 8%.
где То- основное время
Тм-в- машинно-вспомогательное время.
Определим основное время:
Основное время для чернового растачивания отверстия диаметром 18 мм.
где Lр- путь резания
где l0- длина обрабатываемой поверхности по чертежу
l2- длина перебега принимается 05 2 мм
l3- величина подвода инструмента принимается 05 1 мм.
Основное время для черновой подрезки торца диаметром 32 мм.
Lр=(32-17)2+15+1=10 мм
Основное время для чернового точения шейки диаметром 32 мм.
Основное время для черновой подрезки торца диаметром 80 мм.
Lр=(80-32)2+1+1=26 мм
Основное время для чистового растачивания отверстия диаметром 18 мм.
Основное время для чистовой подрезки торца диаметром 32 мм и растачивания фасок.
Основное время для чистового точения шейки диаметром 32 мм.
Основное время для чистовой подрезки торца диаметром 80 мм.
Lр=(80-32)2+05+05=25 мм
Основное время для расточки канавки.
То=029+005+0175+0138+0485+0056+0103+0208+0005=1504 мин
Определим машинно-вспомогательного времени:
где Тхх- время холостых ходов
Тси- время смены инструмента для револьверной головки принимается 01 мин [1].
где Lхх- длина холостых ходов
Vбп- скорость быстрых перемещений определяемая по паспорту станка [14].
Lхх=95+40+32+31+24=222 мм
Тм-в=0022+01=0122 мин.
Время цикла автоматической обработки:
Тца=1504+0122=1626 мин.
Определим вспомогательное время:
Тв=185(Тус+Тзо+Тупр+Тизм)
где Тус- время на установку и снятие детали;
Тзо- время на закрепление и открепление;
Туп- время на приемы управления станком;
Тиз- время на измерение.
Составляющие Тв определяются по таблицам [3]:
Тв=185(022+0024+003+09)=22 мин.
Определим штучное время:
Подготовительно-заключительное время определяется по таблицам [3]:
Определим штучно-калькуляционное время:
Количество деталей в партии n определяется:
где N- годовая программа выпуска деталей
a- количество дней на которое должен быть обеспечен запас деталей при условии непрерывности процесса сборки;
Dk- число рабочих дней в году.
4. Расчет точности обработки на чистовой операции
Рассчитаем суммарную погрешность обработки при чистовом растачивании отверстия диаметром 18 мм.
Суммарная погрешность обработки отверстия может быть определена по формуле:
где ΔУ- погрешность возникающая в результате упругих отжатий звеньев технологической системы под действием сил резания;
- погрешность установки;
Н- погрешность настройки станка на размер;
И- погрешность возникающая в результате размерного износа инструмента;
Т- погрешность вызванная температурными деформациями технологической системы;
ф- сумма погрешностей формы детали вызываемая геометрическими неточностями станка.
Определение погрешности установки
Погрешность установки складывается из погрешностей базирования закрепления и приспособления.
Примем погрешность базирования равной нулю так как заготовка устанавливается в трехкулачковый патрон. Погрешность закрепления также можно принять равной нулю так как заготовка является жесткой.
Определение погрешности вызываемой упругими отжатиями.
Величина погрешности определяется по следующей формуле [16]:
где суп пб- податливость суппорта и передней бабки станка соответственно.
суп=0516 мкмкг [13].
Наибольшее и наименьшее усилие резания возникает из-за колебания глубины резания.
где Cp x y u- постоянная и показатели степени для конкретных условий обработки определяются по таблицам [15]:
Cp=54 x=09 y=075 u=0.
Kp- поправочный коэффициент учитывающий влияние качества обрабатываемого материала на силовые зависимости.
где НВ- твердость обрабатываемого материала.
Определение погрешности настройки станка.
Для поверхностей вращения Н определяется [13]:
где Δр- погрешность регулирования резца при наладке на размер;
Δизм- погрешность измерения размера детали при настройке;
Kр Kи- коэффициенты учитывающие отклонение закона рассеивания Δр и Δизм от нормального закона.
Определение погрешности возникающей вследствие размерного износа резца:
Основное время обработки То=049 мин
Период стойкости резца Т=20 мин.
Количество деталей обрабатываемых за период стойкости:
Определим путь резания при обработке nc деталей:
L1=V1То1nс=11304048540=2193 м.
L2=V2То2nс=82425000540=165 м
L=L1+L2=2193+165=22095 м
Участок начального износа принимаем Lн=100 м.
где uo- относительный износ резца [13]:
Определение погрешности вызванной температурными деформациями [16]:
где ТР- температурные деформации резца
ТД- температурные деформации детали.
где m- величина полного удлинения соответствующая установившемуся тепловому равновесию;
to- основное время обработки детали
tпер- время перерыва.
С- постоянная величина (С=45);
Lр- вылет резца (Lр=100 мм);
в- предел прочности обрабатываемого материала;
t S V- режимы резания.
F=1010 мм; в=176 МПа; t=03 мм; S=01 ммоб; V=11304 ммин.
α- коэффициент линейного расширения материала детали;
R- радиус обрабатываемой детали;
t- температура нагрева детали;
Q- количество тепла идущего на нагрев детали;
С- удельная теплоемкость материала детали;
- количество тепла в процентах идущее на нагрев детали;
Определение погрешности формы детали вызываемой геометрическими неточностями станка.
Суммарная погрешность обработки:
5 мкм 18 мкм- заданная точность на операции выдерживается.
Проектирование средств технологического оснащения
1. Описание приспособления
Проектируемая технологическая оснастка представляет собой специализированное приспособление предназначенное для сверления отверстия в цилиндрической поверхности заготовки [1213].
Выбор конструкции приспособления обусловлен особенностями технологического процесса и годовой производственной программой простотой надёжностью приемлемой точностью обработки а также невысокой себестоимостью. В частности в целях повышения производительности в приспособлении принято решение использовать пневмозажим.
Состоит: (Рис.3.1) из опоры 1 с оправкой 7 и с кондукторной планкой 2 задней бабки 3 с пневмоцилиндром 4 и базирующим упором основания 5 крепёжных элементов пневмопроводов и пневмоарматуры. Приспособление монтируется на столе 6 вертикально - сверлильного станка модели 2А135.
Установка заготовки в приспособлении осуществляется: на оправке 7 опоры 1 и базирующем упоре (на схеме не показан). Прижимается с помощью конусного центра 8 пневмоцилиндра задней бабки. При этом достигается возможность одновременного зажима и центрирования заготовки.
В зону сверления предусмотрена подача СОЖ под давлением в 17 Атм.
Закладывается потенциал для автоматической загрузки заготовок и выгрузки готовых деталей.
Управление пневмозажимом осуществляется распределительным краном (см. рис.3.2).
Рис. 3.1 Схема приспособления
2. Определение параметров пневмозажима
При выборе силового элемента зажима принято решение использовать пневмоцилиндр.
Определение диаметра и усилия прижима пневмоцилиндра.
Исходя из расчетов номинального усилия прижима Q определим диаметр пневмоцилиндра D по формуле:
где F – усилие на штоке поршня (здесь F = Q) Н; D – диаметр пневмоцилиндра м; р – давление в пневмосистеме Па.
Исходя из формулы (13) получим:
D = √(2754 31404106) = 00094 м = 94 мм.
Принято решение использовать стандартный пневмоцилиндр без торможения двойного действия с креплением на фланце и с резьбовыми отверстиями для подвода воздуха М10×1.
Однако минимальный диаметр цилиндра по ГОСТ 15608 – 70 составляет D = 25 мм.
Исходя из чего расчётное усилие на штоке F ( а следовательно и усилие прижима Q) составит:
F = (31400252 4)04106 = 19625 (Н)
Однако потери на трение в уплотнениях поршня и штока пневмоцилиндров составляет 22% от расчетного усилия на штоке.
Исходя из чего действительное усилие составит:
F = 19625078 = 153 (Н)
По опыту использования подобных приспособлений данное усилие является достаточным.
Подключение пнавмоцилиндра к сети питания.
Подключение пневмоцилиндра к сети питания осуществляется посредством необходимой арматуры фитингов и трубопроводов (рис.3.2) [14].
Рис. 3.2 Схема подключения пневмоцилиндра к сети питания.
– кран управления типа В71-2;
– маслораспылитель типа В44-2;
– фильтр-влагоотделитель;
В курсовом проекте разработан технологический процесс механической обработки детали. Произведены соответствующие технологические расчеты (разработка маршрутной и операционной технологии) проектирование приспособления для сверлильной операции и обзор литературы и опыта производства.
Список использованных источников
Белашов А.С. Соколов В.О. Дорофеев В.Д. Проектирование технологических операций обработки деталей на токарных станках с ЧПУ. Методические указания.- Пенза: Изд-во ППИ 1985.-36 с.
Воздвиженский В.М. и др. Литейные сплавы и технология их плавки в машиностроении: Учеб. Пособие для машиностроительных вузов по специальности «Машины и технология литейного производства».- М.: Машиностроение 1984.- 432 с.
Горбацевич А.Ф. Шкред В.А. Курсовое проектирование по технологии машиностроения. Учебное пособие для машиностроительных специальностей ВУЗов.- Мн.: Высшая школа 1983.- 256 с.
ГОСТ 26645-85. Отливки из металлов и сплавов. Допуски размеров массы и припуски на механическую обработку.
ГОСТ 3212-92. Комплекты модельные. Уклоны формовочные стержневые знаки допуски размеров.
Каштальян И.А. Клевзович В.И. Обработка на станках с числовым программным управлением: Справ. пособие.- Мн.: Выш. шк. 1989.-271 с.
Моргунов В.Н. Основы конструирования отливок. Параметры точности и припуски на механическую обработку: Учеб. Пособие.- Пенза: Изд-во Пенз. гос. ун-та 2004.- 164 с.
Справочник технолога- машиностроителя. Том 1. Под ред. Косиловой Р.К. Мещерякова.- М.: Машиностроение 1972.- 694 с.
Справочник технолога- машиностроителя. В 2 т. Т. 1. Под ред. А.М. Дальского А.Г. Суслова А.Г. Косиловой Р.К. Мещерякова. 5-е изд. перераб. И доп.- М.: Машиностроение-1 2001.- 944 с.
Справочник технолога- машиностроителя. В 2 т. Т.2. Под ред. А.М. Дальского А.Г. Суслова А.Г. Косиловой Р.К. Мещерякова. 5-е изд. перераб. И доп.- М.: Машиностроение-1 2001.- 944 с.
Шестопал Ю.Т. Белашов А.С. Мартынов А.Н. Сухарев О.Н. Руководство к решению задач по технологии машиностроения. Расчеты точности механической обработки.- Пенза: Изд-во ППИ 1974. - 56с.
Уткин Н. Ф. Приспособления для механической обработки. – Л.: «Лениздат» 1969.
Горошкин А. К. Приспособления для металлорежущих станков. Справочник. 4-е изд. перераб. и доп. – М.: Машгиз. 1961.
Анурьев В. И. Справочник конструктора-машиностроителя: В 3-х т. Т.3 5-е изд. перераб. и доп. – М.: Машиностроение. 1980.
Чугунная втулка Деталь.cdw

Допуск на размеры необрабатываемых поверхностей по ГОСТ 1855-95
Неуказанные пред. откл. размеров отверстий - Н14; валов - остальных -
Направление витков спиральной канавки - безразличное.
СЧ15-32 ГОСТ 1412-85
Чугунная втулка Заготовка.bak.cdw

Неуказанные пред. откл. размеров отверстий - Н14; валов -
Неуказанные радиусы скруглений - 2 мм.
СЧ15-32 ГОСТ 1412-85
Операция лист 3.doc
2150.0000 (1) – Резец расточной для внутренней обработки 32х25 SVQBRL R300 – 0828E -
3310.0000 (3) - Штангенглубиномер ШГ-160 ГОСТ 162-89.
Б. Раскрепить и снять заготовку
А. Установить и закрепить заготовку.
2801.0000(1)-Патрон трехкулачковый самоцентрирующий D=25-250 мм ГОСТ 24351-80.
Точить поверхности 123 по программе начисто..
2150.0000 (1) – Резец подрезной чистовой 25х25 К-01-4255-000 СБ ВК8 ГОСТ21151-75;
3310.0000 (3 ) – Штангенциркуль ШЦ-I-125-01 ГОСТ 166-89
ГОСТ 3.1404-86форма 2а
НАЛАДКА ДЛЯ .cdw

Резец подрезной для черновой обработки К-01-4254-000 СБ
Резец подрезной для чистовой обработки К-01-4255-000 СБ
Резец расточной К-01-4205-000 СБ
Резец канавочный К-01-4150-000 СБ
Резец для расстачивания внутренних канавок SVQBRL
Операция № 010. Токарная программная c ЧПУ Оборудование. Станок токарный с ЧПУ 16Б16Т1
Инструментальная позиция № 1
Инструментальная позиция № 2
Инструментальная позиция № 3
Инструментальная позиция № 4
Инструментальная позиция № 5
Фрагмент втулка.frw

Рекомендуемые чертежи
- 04.11.2022
- 24.01.2023
- 24.01.2023
- 13.12.2022