Технологическая карта изготовления железобетонной балки



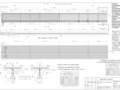
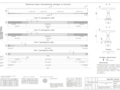
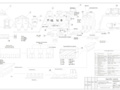
- Добавлен: 24.01.2023
- Размер: 454 KB
- Закачек: 0
Описание
Состав проекта
![]() |
![]() ![]() ![]() ![]() |
![]() ![]() ![]() ![]() |
![]() ![]() ![]() |
![]() ![]() ![]() ![]() |
Дополнительная информация
TechScheme.dwg

кафедра "Мосты и тоннели"
Технологическая схема
и смазка форм(711412)
Армирование (СМЖ 84)
Укладка и уплотнение
Термообработка изделий
бетоновозная эстакада
BalkaNapr33.dwg

Армирование напрягаемой арматурой балок длиной 33 м.
Изготовление железобетонной балки
Продольный разрез (ненапрягаемая арматура не показана)
План lll арматурного ряда
План II арматурного ряда
План I арматурного ряда
Спецификация семипроволочных прядей и спиралей на одну балку
Выборка стали на одну балку
Сечение концевых участков прядей
Обмотка из плотной промасленной бумаги по битумной обмазке
или паклей (мешковиной) пропитанной битумом
или трубка из термофита по жировой обмазке
Условные обозначения
Конструкция пряди дана для натяжения с двух сторон;
в скобках даны размеры в заготовке
При натяжении прядей с одной стороны
должна быть изменена с учетом имеющихся
захватных приспособлений и деформаций стенда.
Полная длина пряди равна L+2x600
где L - длина пролет-
Расчетная температура
Усилие в пряди при перетяжке
Наименьшая прочность бетона
Удлинение пряди при вытяжке
План IV арматурного ряда
Jakub.docx
Белорусский национальный технический университет
Факультет транспортных коммуникаций
Кафедра «Мосты и тоннели»
«Технологическая карта изготовления железобетонной балки пролётом 33м высотой 17м армированные полигональными пучками с натяжением пучков на упоры»
«Технология производства конструкций мостов и тоннелей»
Руководитель: д.т.н.профессор
Исходные данные ..14
Общий вид конструкции 15
1 Маркировка балок .. . ..19
Эскиз конструкции в аксонометрии с указанием её размеров 20
Расчёт массы балки ..21
Выбор варианта армирования .22
Расчет массы металла включая закладные детали 24
Проектирование состава тяжелого бетона с учетом его особенностей. Расчет раствора рабочей концентрации добавок 26
Приготовление и транспортирование бетонной смеси 35
Технология изготовления железобетонных конструкции ..39
Основные положения правил охраны труда ..53
В нашей стране здания и сооружения из монолитного бетона возводят круглогодично. Известно что при температуре +5оС бетонные смеси резко снижают набор прочности. Все реакции гидратации замедляются. При температуре ниже 0оС химически несвязанная вода превращается в лед и увеличивается в объеме приблизительно на 9%. В результате в бетоне возникают напряжения разрушающие его структуру. Замерзший бетон обладает высокой прочностью но только за счет сцепления замерзшей воды. При оттаивании процесс гидратации цемента возобновляется но из-за нарушений структуры бетон не может набрать проектной прочности т.е. его прочность значительно ниже чем прочность бетона не подвергавшегося замерзанию. Экспериментами установлено что на процесс набора прочности бетона существенно влияют условия твердения. Если бетон до замерзания наберет 30-50% прочности от проектной то дальнейшее воздействие низких температур не влияет на его физико-механические характеристики.
Прочность после набора которой дальнейшее воздействие замерзания не влияет на физико-механические характеристики бетона называется критической. Значение критической прочности зависит от класса бетона.
Необходимый температурный режим твердения бетона создают различными приемами: разогревом бетона при его приготовлении выдерживанием бетона в утепленных опалубках (метод термоса); внесением в бетон химических добавок снижающих температуру замерзания; тепловым воздействием на свежеуложенный бетон греющих опалубок; электродным прогревом; инфракрасными источниками теплоты. Технологический прием выбирают с учетом условий бетонирования вида конструкций особенностей используемых бетонов экономической эффективности.
Бетонирование с применением химических добавок.
Основная причина прекращения твердения бетонных смесей при воздействии низких температур – замерзание в них воды. Известно что содержание в воде солей резко снижает температуру ее замерзания. Если в процессе приготовления в бетонную смесь ввести определенное количество растворенных солей то процесс твердения будет протекать и при температуре ниже 0оС.
В качестве противоморозных добавок применяют:
нитрит натрия (НН) NaNO2 (ГОСТ 19906-74);
хлорид кальция (ХК) CaC
хлорид кальция (ХК) + нитрит натрия (НН);
нитрат кальция (НК) Ca(NO3)2 (ГОСТ 4142-77) + мочевина (М) CO(NH2)2 (ГОСТ 2081-75E);
нитрит-нитрат кальция (ННК) + хлорид кальция (ХК);
нитрит-нитрат - хлорид кальция (ННХК) + мочевина (М);
поташ (П) K2CO3 (ГОСТ 10690-73).
Выбор противоморозных добавок и их оптимальное количество зависят от вида бетонируемой конструкции степени ее армирования наличия агрессивных сред и блуждающих токов температуры окружающей среды.
Область применения добавок представлена в таблице №1.
Таблица №1. Область применения добавок.
Тип конструкций и условия их эксплуатации
Железобетонные конструкции с арматурой диаметром мм:
Конструкции монолитные; стыки имеющие выпуски арматуры или закладные части:
без специальной защиты стали
с металлическими покрытиями
с комбинированными покрытиями
Железобетонные конструкции предназначенные для эксплуатации:
В неагрессивной газовой среде при относительной влажности воздуха до 60%
В агрессивной газовой среде
Примечание: Знак (-) означает запрещение применения.
Противоморозные химические добавки запрещается использовать при бетонировании предварительно напряженных конструкций армированных термически упрочненной сталью; при возведении железобетонных конструкций для электрифицированных железных дорог и промышленных предприятий где возможно возникновение блуждающих токов способствующих разрушению бетона.
Внесение химических добавок приводит к некоторому замедлению набора прочности бетоном по сравнению со скоростью твердения бетона в нормальных условиях. Так при внесении поташа прочность бетона в возрасте 28 суток при температуре окружающего воздуха -25оC составляет 50% а в возрасте 90 суток-60%. При температуре -5оС набор прочности протекает более интенсивно и к 28- суточному возрасту он может составлять 75%.
В зависимости от температуры наружного воздуха возможны различные сочетания добавок. Бетон с противоморозными добавками применяют в тех случаях когда достигается набор критической прочности до их замерзания.
При выборе добавок учитывают их стоимость и влияние на физико-механические и технологические свойства бетонов и бетонных смесей. Так при внесении поташа сокращаются сроки схватывания цемента в результате чего ухудшается удобоукладываемость смеси. Наиболее дешевые и доступные добавки – хлориды кальция и натрия. Добавки вводят в виде водяных растворов в процессе приготовления бетонных смесей в количестве 3-18% от массы цемента. Применение добавок целесообразно в сочетании с дополнительным подогревом. Растворы содержащие мочевину не следует подогревать выше 40оС. Растворы солей рабочей концентрации не должны иметь осадков не растворившихся солей.
Некоторые добавки например хлористые соли ухудшают качество поверхности возводимых конструкций вследствии образования высолов. Поэтому их применяют при возведении сооружений небольших объемов к качеству поверхностей которых не предъявляют высоких требований (например фундаменты балки). Процесс укладки и уплотнения смесей не отличается от обычных методов бетонирования.
Бетонная смесь с противоморозными добавками (приготовление транспортирование и укладка)
Бетонную смесь с противоморозными добавками вводимыми с водой затворения готовят на цементах проектной марки и соответствующих мелких и крупных заполнителях. Запрещается применять смерзшийся заполнитель; температура составляющих зависит от вида и дозировки добавки условий транспортирования бетонной смеси и области ее применения. При укладке в стыки следует внести поправку на остывание бетонной смеси в зоне контакта конструкций. Если используются подогретые составляющие то технология приготовления бетонной смеси не отличается от обычной (за исключением использования вместо воды водного раствора добавки).
При выполнении работ с холодными материалами предпочтителен следующий порядок приготовления бетонной смеси: сначала заполнитель вводят в раствор добавки рабочей концентрации и после их перемешивания в течение 15— 2 мин загружают цемент с последующим перемешиванием в течение 4—5 мин.
В случае коротких сроков схватывания цемента с противоморозной добавкой и небольших объемов бетонной смеси (например для стыков) целесообразно применять раздельный способ приготовления: сухую смесь из цемента песка и щебня доставляют на строительный участок и там готовят путем смешения с раствором добавки рабочей концентрации (перемешивание в течение 3— 35 мин).
Бетонную смесь с противоморозной добавкой можно перевозить без утепления но с обязательной защитой от атмосферных осадков и наледей. Доставленная к месту укладки бетонная смесь должна иметь заданную температуру и подвижность; при невозможности выполнения этих условий ее нужно утеплить. Контроль за температурой и подвижностью бетонной смеси а также за продолжительностью ее перевозки выполняет лаборатория.
В зависимости от назначения принятой технологии работ концентрации и вида добавки температура бетонной смеси в момент ее укладки может изменяться в широких пределах. Однако ее минимальная температура должна быть не менее чем на 5 градусов выше температуры начала замерзания водного раствора добавки. Укладку бетонной смеси с противоморозной добавкой следует вести непрерывно а если это невозможно то поверхность бетона нужно утеплять. При снегопадах и сильном ветре бетонирование производят в легких тепляках.
Выдерживание бетонной смеси и бетона с противоморозными добавками и уход за ними
При возведении монолитных бетонных и железобетонных конструкций во избежание потерь влаги попадания осадков и образования высолов необходимо их открытую поверхность укрывать слоем гидроизоляционного материала сразу же по окончании бетонирования а также обеспечить их утепление.
При распалубливании конструкций их прочность должна составлять: для предварительно напряженных конструкций — не менее 80 % проектной; для конструкций сразу же подвергаемых циклическому замораживанию и оттаиванию— не менее 70 % проектной.
Имеется опыт зимнего безобогревного бетонирования в вертикальной скользящей опалубке с введением в бетонную смесь противоморозных добавок — нитрита натрия и поташа и в горизонтальной скользящей опалубке с введением добавок НКМ и ННКМ
Бетонные смеси с добавками нитрита натрия и поташа можно использовать при возведении в вертикальной скользящей опалубке внутренних стен жесткости (ядер) в крупнопанельных многоэтажных зданиях приставных и внутренних стен монолитных лифтовых и лестничных блоков в многоэтажных кирпичных и каркасных зданиях и наружных стен многоэтажных зданий.
Бетонные смеси с добавками НКМ и ННКМ применяются при возведении в горизонтальной скользящей опалубке монолитных стен линейных сооружений. Специфика этой технологии требует получения плотного бетона что ограничивает ВЦ значением 05—055 а подвижность бетонной смеси (по осадке конуса)—значением 60—80 мм.
Для установления ритма подъема опалубки и скорости возведения конструкции нужно дополнительно определить прочность бетона в возрасте 1 2 3 и 7 сут.
Заполнение опалубки бетонной смесью необходимо осуществлять постоянно с хорошим уплотнением каждый последующий слой следует укладывать до начала схватывания предыдущего. Первоначальное передвижение опалубки производят сразу же после ее заполнения бетонной смесью. При этом нижний слой бетона должен приобрести минимальную прочность 01—02 МПа для сохранения приданной ему формы. В дальнейшем передвижение опалубки осуществляют непрерывно со скоростью определяемой сроками схватывания цемента и интенсивностью его твердения.
Оптимальная скорость передвижения опалубки в каждом конкретном случае определяется лабораторией. Для бетонирования в вертикальной скользящей опалубке с добавками нитрита натрия и поташа она составляет в среднем 006— 01 мч в горизонтальных формах с добавками НКМ и ННКМ —4—5 мч.
При временном прекращении работ следует предусмотреть меры по снижению сил сцепления бетона с поверхностью опалубки.
Требования к цементу
Поскольку основная цель преследуемая при введении таких добавок заключается в том чтобы обеспечить в сжатые сроки достижение проектной прочности бетона независимо от температуры окружающего воздуха цемент должен обладать высокой активностью. Рекомендуется применять портландцементы марок не ниже 400.
В связи с тем что С3А взаимодействует с большинством противоморозных добавок с образованием двойных солей в результате чего содержание добавок в жидкой фазе бетонной смеси и бетона понижается оптимальными оказываются высокоалитовые низко- и среднеалюминатные цементы. До накопления дополнительных данных не допускается применять глиноземистые цементы и приготовленные на их основе безусадочные расширяющиеся и напрягающие цементы.
В дорожных бетонах можно применять с противоморозными добавками только цемент удовлетворяющий требованиям соответствующего стандарта. Шлакопортландцемент для этих целей неприменим. Применение шлакопортландцемента соответствующей марки для других объектов разрешается только после проведения необходимых испытаний.
В связи с более высокой энергией активации шлаковых минералов применение шлако портландцемента с высоким содержанием шлака при зимнем бетонировании с применением противоморозных добавок должно сочетаться с методом электропрогрева. Целесообразно при зимнем бетонировании свести к минимуму содержание в цементе минеральных добавок.
Шлакопортландцемент в зимнем строительстве можно сочетать с применением противоморозных добавок для массивных низкомодульных конструкций и сооружений при условии что их начнут эксплуатировать только в весенне-летний период.
Сульфатостойкий портландцемент можно использовать при зимнем бетонировании с применением противоморозных добавок в сочетании с электроподогревом.
Современные противоморозные добавки применяемые в зимнем строительстве.
В соответствии СНиП 3.03.01-87 при зимнем бетонировании конструкций до -15°C применимы следующие способы выдерживания бетона:
термос + ускорители твердения
термос + комплексные добавки с противоморозными и пластифицирующими функциями
В первом случае температура бетонной смеси в начале укладки должна быть более +5 градусов. В случае когда применяются противоморозные добавки температура смеси должна быт как минимум на 5° градусов больше температуры эффективности добавки например ускоритель твердения «Морозостоп» обеспечивает твердение бетона при температуре до -15° значит температура смеси должна быть не менее -10° градусов.
Для приготовления бетонных смесей зимой необходимо использовать бетонные смесители с подогревом а время смешивания увеличивается минимум на 25%. Средства передвижения должны иметь условия сохраняющие тепло. Основание на которое укладывается бетон должно иметь температуру исключающую замерзание смеси на границе контактирования.
В случае когда производится зимнее бетонирование армированной конструкции необходимо прогреть металл до положительной температуры либо с помощью вибрирования продолжительность которого увеличивается на 25%.
Большое применение получила следующая противоморозная добавка:
Ускоритель твердения «Морозостоп»
для бетонных и растворных цементных смесей противоморозный
ГОСТ 30459-96 ГОСТ 24211-91.
Готовый к применению водный состав на основе комплексных солей.
Не имеет запаха не оказывает вредного воздействия на человека и окружающую среду.
Состав разрешен к применению и эксплуатации Минздравом РБ для внутренних и наружных работ при строительстве и ремонте жилых общественных и промышленных зданий и сооружений предприятий пищевой промышленности .
Ускорение твердения бетонных и растворных смесей с повышением прочности бетона на 20% и более в возрасте 1 суток нормального твердения.
Обеспечение твердения бетона за счет повышения тепловыделения при пониженных и отрицательных температурах - от плюс 15° С до минус 15° С.
Увеличение подвижности бетонных смесей с П1 до П3 – пластифицирующая эффективность III группы по ГОСТ 24211.
Снижение расхода воды затворения на 6-11% - водоредуцирующая эффективность III группы по ГОСТ 24211.
Модифицирование бетонных смесей приготовленных на низкомарочных и высокомарочных цементах.
Снижение деформаций усадки бетона и раствора;
Уменьшает водоотделение и расслаиваемость.
Позволяет исключить тепловлажностную обработку бетона и раствора.
Повышает плотность однородность и прочность бетона и раствора;
Повышает прочность сцепления старого и нового бетона и раствора;
Повышает марку бетона по водонепроницаемости на 1-2 ступени и морозостойкости;
Отсутствует коррозия стальной арматуры.
Снижает трудозатраты и стоимость производства работ.
Указания к применению:
Перед применением состав взболтать в заводской упаковке вылить в воду затворения и перемешать.
Оптимальный расход состава на 100 кг цемента:
л (12 кг) при температурах от + 15°С до - 5°С;
л (18 кг) при температурах от - 5°С до - 10°С;
л (24 кг) при температурах от -10°С до - 15°С.
Состав пожаробезопасен.
Работы производить соблюдая требования безопасности при работе с щелочами с рН=9-12.
Упакованный состав транспортируется автомобильным жд и другими видами транспорта в соответствии с правилами перевозок и крепления грузов действующими на данном виде транспорта. Упакованный состав хранится в не отапливаемых помещениях в условиях обеспечивающих сохранность упаковки и защиту от увлажнения. Гарантийный срок хранения состава – 1 год со дня изготовления. Состав содержит взвесь и осадок. Не замерзает на морозе.
При составлении технологических карт использованы рабочие чертежи изделий государственные отраслевые и республиканские стандарты на бетонные и железобетонные изделия методы контроля и испытания материалов и изделий требования безопасности труда; строительные нормы и правила на производство строительных конструкций изделий и материалов; технические условия инструкции и указания нормы технического проектирования предприятия сборного железобетона (ОНТП-07-85); нормы операционного контроля при производстве железобетонных изделий обеспечивающие сведения о требуемом уровне качества изделий и отдельных выполняемых технологических операций монографии справочники и учебная литература по технологии бетона; требования по автоматизации производственных процессов.
В соответствии с требованиями настоящих технических условий балка изготавливается по рабочим чертежам серии 15-8-18-1. Они удовлетворяют требованиям ГОСТов: по прочности жесткости морозостойкости и трещиностойкости по показателям фактической прочности бетона (в проектном возрасте) по защите от коррозии по маркам и классам сталей по применению стальных ферм для изготовления изделий.
Материалы применяемые для приготовления железобетонных балок соответствуют требованиям действующих стандартов: цемент – ГОСТ 10178-76 заполнители – ГОСТ 10268-80.
Балки изготавливают из тяжелого бетона марок М400. Передачу усилий обжатия на бетон т.е. отпуск напряженной арматуры производится после достижения бетоном требуемой прочности (передаточной) устанавливаемой по ГОСТ 18105.0-80 ГОСТ 18105.01-80 в зависимости от фактической однородности бетона.
Общий вид конструкции
Железобетонные балки в строительстве имеют широкое применение. Они считаются конструктивными элементами с высокой прочностью надежностью и долговечности. Стандартные технологии совершенствуют внедрением новых строительных материалов улучшением качества бетонной смеси и обновлением оборудования.
По конструктивному типу железобетонные балки подразделяют:
Фундаментные балки. Они предназначены для опирания на них стен или устройства конструкций подземных сооружений.
Балки перекрытий. Предназначаются для выполнения каркаса зданий и придания ему определенной жесткости.
Стропильные балки. Применяют при устройстве крыш и их конструкций а также перекрытий промышленных сооружений.
Подкрановые балки. Применяются для устройства на них подкрановых путей.
Основные размеры балки:
Железобетонные балки пролётных строений должны изготавливаться в соответствии со СНиП 2.05.03-84 по рабочим чертежам серии 3.503-81 выпуск 5-5-ТТ.
Для изготовления балок пролётных строений применяется тяжёлый бетон по ГОСТ 25192 ГОСТ 26633 (средней плотности 2400 до 2500 кгм3 включительно).
Допускается применение бетона класса С3240 для ускорения набора передаточной прочности. Марка бетона по морозостойкости в зависимости от температурной зоны строительства:
- для температурных зон 1236 и 7 –
- для температурных зон 45 и 8 – F300.
Таблица 2.1. Характеристика температурных зон
Средняя температура наиболее холодного месяца
Средняя температура наиболее холодной пятидневки с обеспечённостью 092
Ниже -30°С до -40°С включительно
Номер температурной зоны при влажности воздуха
Отклонение размеров балок не превышают:
а) по длине балок 20 мм;
б) по ширине сечения поясов и по толщине полосок 3мм;
в) по толщине стенок 10 мм;
г) по ширине опорной части 3 мм;
д) по высоте сечения 5 мм;
е) по толщине защитного бетонного слоя для напрягаемой арматуры проволочной и прядевой 5 мм; для напрягаемой стержневой арматуры 5 мм то же для поперечной арматуры 3 мм
Внешний вид балок удовлетворяет следующим требованиям:
а) углы между торцевыми гранями и нижней гранью балок должны быть прямыми. Отклонение от перпендикуляра допускается не более 2 мм на 1 м длины торцевой грани.
б) поверхности граней балок плоские; кривизна допускается на верхней нижней и торцевых гранях балки не более 2 мм на 1 м; на остальных поверхностях - 3 мм на 1 м.
в) около кромок поясов и опорных ребер допускаются на глубине не более 10 мм.
г) раковины до 15 мм и глубиной до 5 мм допускаются не более двух на 1 м длины стенки или пояса
Защитный слой бетона для рабочей арматуры обеспечивает совместную работу конструкции и также защиту арматуры от внешних атмосферных воздействий.
Для продольной рабочей арматуры (ненапрягаемой и напрягаемой натягиваемой на упоры) толщина защитного слоя мм принимается не менее диаметра стержня или каната и не менее 30 мм в балках и ребрах с высотой 50 и более.
Толщина защитного слоя бетона у концов предварительно напряженных элементов на длине зоны передачи напряжения составляет не менее: 50 мм для стержневой арматуры класса А - 2.
Железобетонная балка запроектированы без диафрагм.
В проекте даны конструкции крайних и промежуточных балок. Крайние балки отличаются от промежуточных наличием односторонних выпусков арматуры из плиты проезжей части. Проектируемая балка является промежуточной поэтому выпуски присутствуют с обеих сторон.
Свесы верхней бетонной плиты от оси балки – 90 см.
Балки пролётных строений изготавливаются на стендах с применением пучков арматуры натягиваемой на упоры до бетонирования.
Напрягаемая арматура состоит из прямолинейных горизонтальных пучков. Каждый пучок состоит из 24 проволок диаметром 5 мм и снабжён двумя каркасно-стержневыми анкерами. Часть пучков «обрывается» в пролёте. «Обрыв» пучков осуществляется изоляцией концевых участков пучков промасленной плотной бумагой по битумной мастике либо паклей (мешковиной) пропитанной в битуме. Также возможно применение трубок из термофита по жировой обмазке или любого другого материала при условии сцепления пучков с бетоном.
Для пролётных строений длиной 12 15 18 и 21 м дан вариант армирования семипроволочными стальными прядями диаметром 15 мм по ГОСТ 13840-68.
Передача арматурой предварительного напряжения на бетон предусмотрена при 80-90% прочности бетона заданной марки. Прочность бетона при передаче предварительного напряжения а также величина контролируемого усилия в каждом случае указана на чертежах.
Верхняя плита армируется сварными сетками с постоянным шагом поперечных стержней 100 мм. Для усиления концевых участков плиты применяются арматурные стержни большего диаметра с тем же шагом.
Рёбра армируются плоскими сварными сетками с шагом для вертикальных стержней 100 мм на концевых участках и 200 мм на средних участках. Шаг горизонтальных стержней – 150 мм.
Нижние пояса балок армируются составными каркасами состоящими из согнутых плоских сварных сеток. Шаг хомутов каркасов постоянны – 150 мм.
Все закладные детали должны иметь антикоррозийное покрытие в соответствии с СН 313-65.
Для мостов расположенных на продольном уклоне до 1% и в районах с сейсмичностью до 6 баллов включительно при установке балок на резиновые опорные части. Проектируем состав бетона который имел бы через 14 суток прочность при сжатии 65 МПа. В результате проведённых расчётов получили что для приготовления м3 бетонной смеси необходимо:
цемента = 563 кг; песка = 239 кг; крупного заполнителя = 725кг; воды = 248л.
Железобетонная балка обозначается маркой в соответствии с требованием ГОСТ 20372-86. Балки настоящего выпуска обозначены марками в которых указаны индекс номинальный пролет и категория балки на несущую способность.
Так 1Б1-21-1 обозначаем балку с проволочной арматурой пролетом 24 м под расчетную нагрузку I категории.
Маркировка проектируемой балки:
Пр- промежуточная балка с нормальными свесами плиты;
Кр - крайняя балка с нормальными свесами плиты;
Прк – промежуточная балка стоящая на месте крайней;
(12151821243341) – длинна балки в метрах;
Г(П) – горизонтальные пучки полигональные пучки;
7891012142026 – количество пучков или прядей напрягаемой арматуры;
УК- балки с уменьшенными свесами плиты;
Кроме этого должна быть предусмотрена маркировка балок:
по марке бетона на морозостойкость – 200300
по расчетной температуре воздуха наиболее холодных суток где будет использоваться балка
Эскиз конструкции в аксонометрии
Выбранная схема армирования конструкции представлена на листах графического материала.
Расчёт массы балки произведён на основе исходных данных с учётом выбранного варианта армирования включая массу закладных деталей и других арматурных элементов (фиксаторов и стяжек). Двускатная балка обозначается маркой в соответствии с требованием ГОСТ 20372-86.
Принимаем сечение балки за тавровое и также добавляем площадь на припуски. Площадь поперечного сечения состоит из площади верхней полки S1 стойки S2 нижней части S3 и площадь на припуски Sп: SБ = S1 + S2 + S3 + Sп.
S1 = 015·33 = 0495 м2 ;
S2 = 0795·018 = 0143 м2;
S3 = 019·061 = 012 м2;
Общая площадь: SБ = 0495+0143+012+084 = 1598 м2
Объём балки: VБ = l*SБ = 33·1598 = 52734 м3.
Балки изготавливаем из тяжелого бетона (средней плотности 24 до 25 тм3 включительно).
Масса бетона в балке: Mб = VБ·ρб = 52734м3·24тм3 = 12656 т.
Масса стали в балке состоит из массы напрягаемой арматуры М1 массы ненапрягаемой арматуры М2 и массы закладных деталей М3: Мс = М1 + М2 + М3. Расчет массы стали приведен в разделе 7.
М1 = 8494 кг. М2 =2517кг. М3 = 2401кг.
Мс = 6503+2517+2401 = 34074кг 341 т.
Общая масса балки: МБ = Mб + Мс = 12656 т + 341 т = 12997 т
Выбор варианта армирования балки
В случае использования ненапрягаемой арматуры в балке мы должны проармировать балку по двум вариантам. В первом варианте необходимо взять арматуру класса А-II во втором варианте армируем балку арматурой класса А-III. Спецификации армирования по двум вариантам приведены в таблицах 5.1 и 5.2.
Таблица 5.1.Армирование балок с использованием стали класса А-II
Масса стали ненапрягаемой арматуры в армировании по первому варианту составляет 2939 5 кг.
Таблица 5.2.Армирование балок с использованием стали класса А-III
Масса стали ненапрягаемой арматуры в армировании по второму варианту составляет 2517 кг. Принимаем наиболее экономичный с использованием арматуры класса А-III масса стали – М2 =2517 кг.
Расчет массы металла включая закладные детали
Спецификация напрягаемой арматуры в балке представлена в таблице 6.1
Таблица 6.1.Спецификация семипроволочных прядей и спиралей в балке
Общая масса стали состоящей из напрягаемой арматуры в балке приведена в таблице 6.2.
Таблица 6.2.Выборка стали на одну балку
Итого масса стали напрягаемой арматуры в балке М1 = 8494 кг.
Расход металла на закладные детали представлен в таблице 6.3.
Таблица 6.3.Выборка стали на один элемент
Итого вес стали на закладные детали составляет:
М3 = (52+536)*2+189*2+ 30*225+2*256 = 2401 кг.
Проектирование состава тяжелого бетона с учетом его особенностей. Расчет раствора рабочей концентрации добавок
Проектируем состав бетона который имел бы через 14 суток прочность при сжатии 45 МПа.
Прочность бетона через 28 суток нормального твердения исходя из формулы RСЖ28 = RСЖ14 lg28 lg14 =505 МПа.
Вид конструкции: железобетонная балка.
Способ формования: на виброуплотнение с пригрузом.
Подвижность бетонной смеси требуемая условиями работ характеризуется осадкой конуса 1-3 см.
Допускаемая наибольшая крупность заполнителя: 20 мм.
Материалы: цемент - портландский с активностью в 14 суточном возрасте 45 МПа (в 28 суточном возрасте - 505 МПа);
нормальной густотой теста Кнг = 031 и плотностью ц = 3020 кгм3.
Крупный заполнитель – гранит с плотностью в виброуплотнённом состоянии кв =1884 кгм3 плотностью зёрен к = 2670 кгм3 пустотностью Пк = 0285.
Зерновой состав: фракции
Мелкий заполнитель: песок речной с плотностью в виброуплотнённом состоянии пв = 1882 кгм3; с плотностью зёрен п = 2634 кгм3 и пустотностью Пп = 0279.
Определяем максимальную насыпную плотность смеси заполнителей в виброуплотнённом состоянии:
смв = Пкз·рпв + ркв·1 =0285·1882 + 1884 = 242037 кгм3 где
Максимальная плотность смеси зёрен заполнителей равна
см=[рп+ркв·рк(Пкз·рпв)][1+ркв(Пкз·рпв)]= =[2634+1884·2670(0285·1882)][1+1884(0285·1882)]= 266998 кгм3
Минимальная пустотность смеси заполнителей.
Vпсм = (см - смв )см = (266998-242037)266998=0098 => 98%
Строим график изменения пустотности в зависимости от объёмов песка и щебня на 1м3 смеси заполнителей.
Определяем оптимальную пустотность Vп смеси заполнителей:
Принимаем Vпсм = 01м3 Vп = 032 м3 Vк = 097 м3 тогда П1 = 1882·032 = 602 кг– масса песка К1 = 1884·097 =1828 кг–масса крупного заполнителя.
Vп >=11·Vк·Vпк= 11·1·0285 = 031 м3 принимаем Vп=032 м3.
Определяем суммарную площадь зёрен крупного заполнителя и песка с учётом каждой фракции заполнителя и величины её удельной поверхности:
Sсм=Sк+Sп=0001·(П1·Рni·Sni+К1·Ркi·Sкi)= 0001·[602·(117·94 + 178·202 + +307·370 + 203·720 + 108·1410 + 27·2930) + 1828·(656·27+ 315·54 + +29·81)] = 391698 м2
где Ркi Рni - содержание каждой фракции крупного и мелкого заполнителей в %
Sкi Sni – удельная поверхность i-ой фракции крупного заполнителя и песка.
Находим объём цементного теста для приготовления 1 м3 бетонной смеси и выход бетона.
Vб =1+0000013· Sсм= 1 + 0000013·391698 = 105 м3;
Vт=(Vпсм+0000013· Sсм) Vб =(01+0000013·391698)105=0144 м3.
В связи с тем что объём бетона вследствие раздвижки зёрен заполнителей цементным тестом получается больше чем 1м3 проводим корректировку расхода заполнителей по выходу бетона:
П2 = П1 Vб =602105 = 574 кг; К2 = К1 Vб =1828105 = 1741кг.
Общая водопотребность заполнителей в кг:
Вз=00001(П2·Рni·Вni+К2·Ркi·Вкi)=00001·[574·(117·1914 + 178·207 + +307·23 + 203·346 + 108·60 + 27·1201) + 1741·(656·093 + 315·121 + 29·138)] = 3504 кг
где Вni Вкi – общее водопоглащение песка и крупного заполнителя.
Определяем количество воды адсорбированной на поверхности зёрен заполнителей:
Вад=00001(П2·Рni·Вnадi+К2·Ркi·Вкадi)=00001·[574·(117·0374 + 178·081 + 307·148 + 203·286 + 108·565 + 27·117) + 1741·(656·051 + 315·081 + 29·11)] = 2316 кг
где Вnадi Вкадi - количество воды адсорбирующейся на i-ой фракции песка и крупного заполнителя.
Определяем расход цемента для приготовления 1 м3 бетонной смеси при =096 где - относительное водосодержание цементного теста: =(ВЦ)тКнг=027028=096;
(ВЦ)т – водоцементное отношение цементного теста в бетонной смеси (ВЦ)т=3504(144-(3504-2316))=027.
Приведенная плотность цемента:
п = 1000(1000рц - 0012 + 0263*Кнг) = 1000(10003100 – 0012 + +0263·028) =2603 кгм3;
Ц1=(1000·Vт-Вад)102·(1000рп+Кнг(-0293)=(1000·0144-2316)102·[10002603 + 028·(096 – 0293)] = 208 кг.
Определяем водоцементное отношение бетонной смеси:
(ВЦ) =·Кнг+ВзЦ= 096·028 + 3504208 = 044.
Находим проектную прочность бетона для приготовления бетонной смеси с использованием обычных способов уплотнения.
Rсж=Кпер·К3·Rц([(1+165·Кнг)·(ВЦ)Кнг]-165·Кнг);
Кпер- переходной коэффициент для пересчета результатов определения марки цемента от жестких растворов к пластичным по ГОСТ 3104-81 принимаемый в зависимости от водопотребности цемента при Кнг=028 Кпер=13;
К3 - коэффициент учитывающий вид крупного заполнителя К3=113.
Rц – активность цемента МПа.
Rсж=13·113·45([(1+165·028)·044028]-165·028)= 36 МПа.
Уточняем объём цементного теста т.к. вычисленный расход цемента ниже допустимого и ввиду необходимости получения осадки конуса 1-3 см повышаем расход цемента принимая Дц=55: Vтц=102·Ц1·(1+Дц)·[1000рц+Кнг·(–0293)]1000;
где Дц – добавка к цементу в % от цемента.
Vтц=102·208·(1+55)·[10002603+028·(096–0293)]1000=0787 м3
Определяем объёмы песка и крупного заполнителя осадку конуса:
Vп = П2рпв=5741882 = 031 м3;
Vк = К2ркв= 17411884 = 0924 м3;
r = Vп (Vп -Vк)= 031(031+ 0924) = 0251;
ОК= 20·r·рбсм·Vту·(–0876)0774=20·0251·24·0787·(096–0876)0774 = =103 см где ОК- осадка стандартного конуса см;
рбсм – средняя плотность бетонной смеси принимаемая 24 кгм3.
Уточняем выход бетонной смеси
Vбс=Ц1·(1+Дц)рц+П2рп+К2рк+(ВЦ)·Ц1(1+Дц)рв где рв –плотность воды рв=1000 кгм3
Vбс = 208·(1+55)3100+5741882+17411884+044·208·(1+55)1000=24 м3.
Определяем расход материала на 1 м3 бетона (кг). Т.к. выход бетонной смеси больше 1 м3то расход материалов на 1 м3 бетона составит:
цемента Ц =Ц1·(1+ Дц) Vбс =208·(1 + 55) 24 = 563 кг;
пескаП = П2 Vбс = 574 24 = 239 кг;
крупного заполнителяК = К2 Vбс =1741 24 = 725 кг;
водаВ = Ц1·(1+Дц)·(ВЦ) Vбс =208·(1+55)·04424= 248 л.
В результате проведённых расчётов получили что для приготовления м3 бетонной смеси необходимо:
Расход раствора добавки повышенной концентрации (л) на 1 м3 бетона определяют по формуле
где Ц - расход цемента на 1 м3 бетона кг; Д — дозировка добавки (% от массы цемента); Кр — концентрация приготовленного раствора добавки %; р — плотность приготовленного раствора добавки кгм3.
Расчетный расход воды корректируют с учетом ее расхода на приготовление раствора добавки повышенной концентрации. Поэтому с учетом воды в добавке рабочий расход воды на затворение 1 м3 бетона (л) определяют по формуле:
где Вф— расчетный расход воды на 1 м3 бетона л.
При приготовлении бетонной смеси одного и того же состава в течение не менее одной смены целесообразно заранее готовить водные растворы добавок рабочей концентрации которую устанавливают при расчете состава бетона а их расход (л) на 1 м3 бетона определяют по формуле
Растворы добавок рабочей или повышенной концентрации готовят в емкостях посредством растворения и последующего разбавления твердых пастообразных или жидких продуктов. Для ускорения растворения веществ воду рекомендуется подогревать до температуры 40 70 °С и растворы перемешивать а твердые вещества при необходимости дробить.
После полного растворения вещества проверяют плотность полученного раствора и доводят до заданной добавлением вещества или воды. Рекомендуется определять плотность жидкости посредством денсиметра (ареометра). Денсиметр погружают в раствор до тех пор пока масса вытесненной жидкости не станет равна его массе. Деление шкалы против которой будет находиться поверхность жидкости укажет значение ее плотности.
Необходимо рассчитывать изменение плотности в зависимости от температуры раствора по формуле
где ррэ — замеряемая плотность раствора кгм3;
рр — плотность раствора при 20°С кгм ;
Крt - температурный коэффициент плотности раствора;
t — температура раствора в момент определения его плотности °С.
Необходимое количество жидкого продукта (л) для раствора добавки
где V — объем приготовляемого раствора л;
Сд — содержание безводного вещества добавки в 1 л жидкого концентрата добавки кг.
Количество воды (л) необходимое для заправки емкости запаса
На производстве возникает необходимость решить следующие задачи: приготовить запас (с учетом беспрерывной работы предприятия) раствора рабочей концентрации для затворения бетонной смеси; определить расход концентрированного раствора добавки для затворения 1 м3 бетонной смеси.
Добавки вводят в бетонную смесь для улучшения её технологических свойств ускорения или замедления твердения бетона улучшения морозостойкости водонепроницаемости коррозионной стойкости и др. а также уменьшения расхода цемента за счёт введения активных наполнителей до 40%. При введении их надо учитывать что активность цемента может быть снижена на 1% введения добавки.
В бетоносмеситель вместе с водой затворения подаётся расчётное количество добавки для этого заранее приготавливаются водные растворы добавок повышенной концентрации а именно 1-5%-ый для воздухововлекающих добавок; 50%-ый для пластифицирующих пластифицирующе-воздухововлекающих уплотняющих и супер-пластификаторов замедлителей схватывания; 10%-ый для ускорителей твердения ингибиторов коррозии стали; 10-20%-ый для противоморозных добавок.
В дозаторах водные растворы повышенной концентрации разбавляют до получения рабочих растворов расход раствора повышенной концентрации в литрах на 1 м3 бетона определяется из выражения:
где Ц- расход цемента
Д- количество добавки в % от массы цемента
Кр- концентрация приготовленного раствора добавки в %
рр- плотность приготовленного раствора добавки в кгм3.
Корректировка расхода воды с учётом её расхода на приготовление раствора добавки повышенной концентрации: фактический расход равен
Вф= В - Qкр·рр(1-Кр100)
Для приготовления бетонной смеси одного и того же состава в течение 1 смены или более готовят заранее водные растворы добавок рабочей концентрации расход водных растворов определяют из формулы:
Qкр=(100·В+Ц·Д)100·рр
В случае использования добавок в виде паст их необходимое количество для приготовления раствора повышенной концентрации определяется по следующей формуле:
где Р-необходимое количество пастообразногожидкого концентрата в л
V - обьём приготавливаемого раствора в л
Д – количество добавки в % по массе от цемента
Сд - содержание безводного вещества в 1 литре концентрата пасты в кг.
В курсовом проекте необходимо приготовить раствор рабочей концентрации для затворения бетонной смеси с использованием смесителя вместимостью 600л при расходе цемента на замес Ц = 125 кг воды В =69л. Содержание добавки СДБ- 03% от массы цемента. Содержание сухих веществ в жидком концентрате СДБ 30%.
По технологическим нормам (картам) для смесителя принудительного действия принимаем 40 замесов в 1ч. Запас рабочего раствора добавки 8ч. Определяем объём ёмкости для приготовления рабочего раствора СДБ в воде:
Vp = B·n· = 69·40·8 = 22080 л
гдеn – количество замесов в 1ч;
- время запаса рабочего раствора.
Принимаем объём ёмкости 23м3.
Рассчитываем необходимое количество СДБ в л:
P=Vр·Ц·Д100·В·Сд=23000·125·03(100·69·0429) = 2914 л.
Необходимое количество воды для заправки ёмкости:
Взапр = Vр – P = 23000 – 2914 = 227086 л.
Для приготовления объёма рабочей концентрации объёмом 23000 л необходимо смешать 290 л раствора СДБ и 22710л воды.
Расход раствора рабочей концентрации СДБ на замес бетоносмесителя при плотности раствора добавки 1144 гсм3 составит
Qp = (100B +Ц·Д)100·р = (100·69 + 125·03)(100·1144) = 6064 л.
Приготовление и транспортирование бетонной смеси
Бетонные смеси на предприятиях сборного железобетона получают в бетоносмесительных цехах. Производство бетонных смесей может быть организовано как в стационарных так и в перебазируемых или мобильных установках. По принципу действия различают бетоносмесительные установки цикличного и непрерывного действия. Для первых характерны периодически повторяющиеся операции загрузки перемешивания и выгрузки для вторых - непрерывность указанных процессов.
В состав бетоносмесительных цехов или бетонных заводов входят склады цемента и заполнителя установки для приготовления добавок расходные бункеры для образования оперативного запаса материалов транспортное оборудование аппаратура для базирования компонентов смесительное оборудование и устройства для выдачи бетонной смеси устройства автоматического управления и контроля вспомогательные установки (энергетическое хозяйство компрессорная отопительная система).
Цемент поступает на склад с помощью различных транспортных средств специализированных автомобилей (автоцементовозов опрокидных цементовозов) обычных крупных вагонов.
Из цементовозов бункерного типа цемент самотёком через люки выгружается в приёмные устройства складов. Разгрузку цементовозов-цистерн производят с помощью сжатого воздуха для выгрузки цемента из крытых железнодорожных вагонов применяют механические или пневматические способы разгрузки. Более совершенен пневматический способ. Он основан на перемещении взвешенных частиц материала движущимся потоком воздуха. Характеризуется герметизацией и отсутствием потерь цемента лучшими условиями труда компактностью полной механизацией.
Заполнители бетона хранятся в складах открытого закрытого и комбинированного типа. В зависимости от рода транспортных средств доставки заполнителей склады разделяются на прирельсовые безрельсовые и береговые.
Заполнители выгружают с помощью погрузчиков с железнодорожных платформ или подают в приёмный бункер непосредственно из саморазгружающихся вагонов и автосамосвалов. Из приёмных бункеров с помощью ленточных конвейеров заполнители поступают в расходные бункеры бетоносмесителей. На складах в зимнее время подогревают песок а в некоторых случаях и крупный заполнитель. Температура подогрева заполнителя колеблется в зависимости от вида и марки цемента. Максимальная допустимая температура заполнителя при разгрузке в смеситель и применения обычного портландцемента а также его разновидностей не должна быть выше 50 ºС.
Запас заполнителя принимают в зависимости от характера его доставки как и для цемента он рассчитан на 5-10 суток однако может храниться и более продолжительное время. Потребность в заполнителях как и в цементе при проектировании склада определяется на основе подборки состава бетона. Ориентировочно на 1 м3 тяжелого бетона требуется 045 м3 песка и 09 м3 щебня или гравия.
Дозирование - это процесс отмеривания количества исходных материалов при выгрузке их в смеситель. Дозирование компонентов бетонной смеси должно выполняться с точностью обеспечивающей достижение необходимых проектных свойств бетона. При приготовлении бетонной смеси дозированным способом компоненты дозируют по массе; воду и жидкие добавки можно дозировать по массе и по объёму. Точность дозирования цемента воды и добавок может отклоняться от расчётной не более чем на 2% заполнителей - не более чем на 25%. Этим условиям должны удовлетворять не менее 80% замеров.
Дозаторы характеризуются по характеру работы на цикличные и непрерывного действия а по принципу действия- на объёмные весовые и смешанные; по способу управления - с ручным полуавтоматическим и автоматическим управлением. Выбор типа дозаторов определяется компановкой бетоносмесительной установки видом бетоносмесителя количеством марок смеси и другими факторами. Важнейшим условием достижения требуемых свойств бетона является постоянство водоцементного отношения. Необходимое условие стабилизации ВЦ - учёт влажности заполнителя которая даже при благоприятных условиях может колебаться от 10% до 15% а при неблагоприятных может достигать 20% - 30%. Влажность заполнителей определяют обычно высушиванием проб 1-2 раза в сутки. Наиболее перспективным является нейтральный метод определения влажности заполнителя. Он позволяет контролировать влажность в интервале 15% – 10% непрерывно с точностью 02% – 03%.
Для однородности бетонной смеси её перемешивают. Для перемешивания компонентов бетонной смеси широко применяют циклические бетоносмесители. В такие бетоносмесители загружают новый замес который может быть загружен лишь после выгрузки из бетоносмесителя предыдущего готового объёма смеси. Оптимальная продолжительность перемешивания зависит от состава и характеристик смеси.
Бетонные смесительные узлы завода компонуют в большинстве случаев по вертикальной схеме с однократным загружением материалов в расходные бункеры. Высота здания цеха достигает 25-30 м. Материалы попадают в надбункерный этаж с помощью ленточных конвейеров. Для подачи заполнителей цемента и др. используются также поворотные воронки для порошкообразных материалов - лотки и пневматический транспорт. В последнем случае для очистки воздуха от цементной пыли применяют циклоны.
Расходные бункеры делятся на отсеки. Для крупных заполнителей предусматривают обычно три отсека для мелких заполнителей и цемента - по два. С целью свободного перемещения сыпучих материалов углы наклона днищ бункеров выполняют больше углов естественного откоса соответствующих материалов. Углы наклона днищ как правило составляют не менее 55 - 60º чтобы не было зависания заполнителей при повышении влажности а на стенках нижней части бункера устанавливают вибрационные свободообрушители. В бункерах предусматривают также устройства для аэрации цемента (подобие решетки) и указатели уровней заполнения отсеков бункера.
Запас материалов в исходных бункерах принимают обычно для заполнителей на 1-2 часа цемента - 2-3 часа. Дозаторы сухих компонентов бетонной смеси загружают их из соответствующих отсеков бункера. Вода поступает в дозатор из установленного под ним бака наполняемого из водопроводной магистрали. Водные растворы добавок поступают в дозатор с помощью циркуляционного трубопровода от установок по приготовлению добавок.
Смесители загружают сухими компонентами по рукавному желобу с перекидным клапаном готовую смесь из бетоносмесителей выгружают в раздаточные бункеры вместимость которых должна быть не менее 2-3 замесов.
На заводах сборного железобетона бетонную смесь транспортируют к месту потребления различными способами: мостовыми кранами или автокранами самоходными бетоновозами перемещая по рельсовому пути ленточными конвейерами пневматическими устройствами. В цехах с высокомеханизированным производством применяют бетонораздатчики.
Максимальная высота подачи бетонной смеси при ее выдаче на транспортные средства должна быть не более 2 м. Использование пневматических установок может оказаться радикальным при подаче б.с.
Технология изготовления железобетонных конструкции
Технологический процесс производства сборных железобетонных изделий состоит из ряда самостоятельных операций объединяемых в отдельные процессы.
Операции условно подразделяют на основные вспомогательные и транспортные. К основным операциям относят: приготовление бетонной смеси включая подготовку соответствующих материалов; изготовление арматурных элементов и каркасов; формование изделий куда входит и армирование; тепловую обработку отформованных изделий из форм и подготовка форм к очередному циклу; отделка и обработка лицевой поверхности некоторых видов изделий и т.п.
Кроме основных технологических операций на каждом этапе производят вспомогательные операции: получение и подачу пара и воды сжатого воздуха электроэнергии складирование сырьевых материалов полуфабрикатов и готовой продукции пооперационный контроль и контроль качества готовой продукции и др.
К транспортным относятся операции по перемещению материалов полуфабрикатов и изделий без изменения их состояния и формы.
На заводах сборного железобетона приняты поточные методы организации технологического процесса сущность которых состоит в том что весь процесс расчленяется на отдельные операции которые выполняются в строгой последовательности на определённых рабочих местах (постах) оснащённых специализированным оборудованием. На каждом рабочем месте в соответствии с принятыми методами обработки оборудованием и организационным строением выполняется одна или несколько близких между собой технологических операций.
Технологический процесс при изготовлении железобетонных изделий организуют по трём основным способам: агрегатно-поточному конвейерному стендовому и кассетному.
Сущность стендового метода состоит в том что формование и твердение изделий осуществляется в стационарном положении на стенде или специальной установке без перемещений а все материалы формирующее и другое технологическое оборудование а также обслуживающие его рабочие звенья перемещаются от одной формы на стенде к другой; за каждым стендом или формой закрепляется одно или несколько технологически однородных изделий. Этот способ требует больших производственных площадей усложнения механизации и автоматизации производства высоких трудозатрат. Стендовый способ позволяет производить широкую номенклатуру изделий при сравнительно несложной переналадке оборудования.
Стенды для изготовления бывают длинные и короткие. Длинномерные линейные изделия с напряжённым армированием формуют на длинных стендах длиной 75 м и более а также на коротких стендах имеющих длину равную одному изделию а ширину двум и более.
Длинные стенды применяют для одновременного изготовления нескольких одинаковых изделий в формах располагаемых одна за другой и образующих единую формовочную линию. На этой линии укладку и натяжение арматуры а также бетонирование и твердение изделий осуществляют сразу по всей длине стенда.
Разновидностью коротких стендов являются металлические силовые формы на которых изготавливают предварительно напряжённые изделия.
1. Описание технологической схемы.
Приготовление бетонной смеси осуществляется в установках-смесителях принудительного типа СМЖ.
Предварительно до подачи бетонной смеси на стенд осуществляются следующие виды работ: чистка формы и вкладышей от остатков предыдущего бетона с помощью щёток и скребков затем на поверхность формы наносится смазка ("Эмульсол") форма собирается вставляются стержни (армирование конструкции). Сначала арматура подвергается предварительному напряжению с помощью домкратов. Создается преднапряжение до 110% выдерживается 5 мин и отпускается до 100% после идёт установка арматурных каркасов сеток и вкладышей с помощью крана. После этого форма готова для додачи а армирование конструкции подлежит освидетельствованию ОТК.
Бетонная смесь по бетонным течкам попадает на тележку бетоновозной эстакады перегружается в бетонный раздатчик передвигающийся по рельсам. Выгрузка бетонной смеси из ёмкости бетонного раздатчика осуществляется с помощью вибратора. Бетонораздатчик перемещается над стендом и заполняет форму цельноперевозимой балки бетонной смесью в два приёма. Уплотнение бетонной смеси осуществляется с помощью глубинных вибраторов.
После уплотнения бетонной смеси открытая поверхность изделий заглаживается. Когда изделие готово стенд закрывается крышкой и подвергается тепловой обработке по режиму:
- предварительная выдержка;
- подъём температуры;
- изотермическая выдержка;
– охлаждение изделия до 20 ºС.
По окончании тепловой обработки производится передача напряжения арматуры на бетон достигший 100% прочности. Передача напряжения на бетон осуществляется при помощи электродуговой сварки. Готовое изделие с помощью мостового крана подается на пост выдержки изделий где производится ремонт покраска и маркировка изделий которые потом принимается ОТК. Качественные балки после приемки грузятся на тележку и вывозятся на склад готовой продукции. Складирование осуществляется согласно ГОСТ 20372-66.
Цемент может доставляться в вагонах бункерного типа (m= 60 т) или в обычных крытых а также в цементовозах-цистернах в автоцементовозах а также водным транспортом. Затем с помощью пневматического механического или аэрационно-пневматического транспорта подаётся в силосы для хранения. Доставка осуществляется когда цемент находится во взвешенном состоянии т.к. цемент высокодисперсная система. Давление компрессора 03 МПа. Диаметр силоса 5м вмещаемый объём 250т высота силоса 15м. Воздухо-цементное отношение по объему 06. В фильтре создается давление очищенный воздух выходит и цемент осядет а затем по распределению заполняет силоса. Далее по трубопроводу посредствам сжатого воздуха подается в дозатор (2ДБУ-1000). Затем цемент в определенных пропорциях подаётся в бетоносмеситель принудительного действия СБ-138А.
Песок и щебень на завод могут поступать на платформах в специальных саморазгружающихся четырёхосных полувагонах-гондолах с люками в полу или бортовой части в опрокидных вагонах (думпкарах) а также автотранспортом и речным транспортом (в баржах). Выгрузка производится гравитационным способом сталкиванием или черпанием. Затем по ковшово-ленточным конвейерам подается в приёмный бункер склада заполнителей затем через весовые дозаторы подается на руковной желоб с вентилем после чего попадает в приёмные бункеры. Затем с этих бункеров подаётся на дозаторы (обычно 2ДБП-1600 и 2ДБЩ-1000). Дозатор для воды (2ДБЖ-400). С дозаторов заполнитель подаётся в бетоносмеситель непрерывного действия. Перемешивание происходит 2 минуты. После приготовления смеси посредствам бетоновозной эстакады цементная смесь попадает в раздаточный бункер который передвигается по рельсовому пути (вместительность 2-3 замеса).
В формовочном цехе перед бетонированием производят очистку форм смазку натяжение арматуры установку каркасов и сеток закладных деталей и строповочных петель. Далее формы наполняют бетоном и происходит виброуплотнение с помощью навешиваемых на неё вибраторов. После уплотнения балки попадают в камеры для последующей экзотермической обработки в течение 11 часов. После этого опалубки извлекают из пропар-камеры и проиходит распалубка изделий. После распалубки производят выдачу изделия приёмку ОТК и далее транспортируют на склад готовой продукции.
2. Подготовка рабочих поверхностей формы.
Процесс формования изделий – важнейшая стадия их изготовления на заводах сборного железобетона. Процесс формования изделий состоит из сборки очистки и смазки форм и бортовой оснастки установки и фиксации арматурного каркаса в форме натяжения арматуры на упоры укладки распределения и уплотнения бетонной смеси в форме а также отделки открытой поверхности изделия и наконец извлечения готового изделия из формы после тепловой обработки.
После каждого цикла формования формы чистят и смазывают. Для очистки форм и поддонов применяют машины рабочими органами которых являются цилиндрические щётки из стальной проволоки абразивные круги и инерционная фреза из металлических колец. Машины с относительно мягкими металлическими щётками применяют после каждого цикла формования. Машины с жёсткими щётками используют не чаще одного раза в 2-3 месяца.
Поддоны можно очищать по двум схемам: первая – когда машина передвигается над поддоном вторая – если поддон перемещается под машиной. Для очистки разделительных стенок кассетных форм применяют передвижную шлифовочную машину.
Для очистки форм применяют также химический способ который основан на свойстве некоторых кислот например соляной разрушать цементную плёнку. Химическую очистку можно производить не чаще одного раза в год
На качество жб изделий влияет сцепление бетона с поверхностью форм. Один из способов уменьшения сцепления – использование смазок. Смазка должна удовлетворять следующим требованиям: иметь консистенцию позволяющую наносить её распылителем или кистью на холодные и горячие (до 40-50°C) поверхности сплошным тонким слоем (01-03 мм); обладать достаточной адгезией с металлом форм быть достаточно водостойкой и не смешиваться с бетоном не оказывать вредного действия на твердеющий бетон не оставлять пятен на поверхности изделий не вызывать коррозии рабочей поверхности формы не создавать антисанитарных условий в цехах и быть безопасной в пожарном отношении.
На заводах применяют три вида смазок: водные и водно-масляные суспензии (известковые глиняные меловые и шлаковые) водно-масляные и водно-мыльные эмульсии (эмульсол) машинные масла нефтепродукты и их смеси.
Приготовление смазок производят при помощи различных смесителей в том числе эмульсий с использованием ультразвуковых или механических эмульгаторов которые дают возможность смешивать между собой жидкости не смешивающиеся в обычных условиях.
Смазку на поверхность форм наносят обычно различными распылителями а в тех местах где неудобно их использовать применяют специальные механизмы. Более тонкое распыление и большой факел могут получиться если применить для нанесения смазки сжатый воздух. Расход смазки зависит от её консистенции конструкции и типа форм способа нанесения смазки качества поверхности смазк Для смазки опалубки допускается применение проверенных на практике составов типа прямой эмульсии обратной эмульсии и т.д.
Рекомендуется также вместо смазки поверхность опалубки покрывать полихлорвиниловым пластикатом толщиной 2-3мм.
Покрытие может быть выполнено также оклейкой опалубки листами пластиката. Покрытие поверхности опалубки пластикатами должно предусматриваться при её изготовлении чтобы сохранить опалубочные размеры конструкции.
3. Уплотнение рабочей смеси.
Бетонная смесь обладает рыхлой нестабильной структурой с высокой пористостью и большим объёмом вовлечённого воздуха. Необходимое условие получения однородного по плотности и прочности бетона – уплотнение бетонной смеси на стадии формования изделий.
В процессе формования и уплотнения частицы бетонной смеси находятся под воздействием силового поля слагаемого из сил тяжести частиц и внешнего силового воздействия оказываемого на частицы. Вместе с тем частицы находятся под воздействием внутренних сил в системе (сил трения межмолекулярные и др.).
Оптимальное соотношение между силами тяжести частиц и внешним силовым воздействием – необходимое условие качественного формования и уплотнения бетонной смеси которое зависит в основном от реологических свойств а также от формы изделия и его насыщенности арматурой.
Основными способами механического воздействия на бетонную смесь с целью её уплотнения являются вибрирование прессование и центрифугирование.
Виброуплотнение. Виброформование сводится к разрушению сложившейся первоначальной структуры бетонной смеси и переводу её в состояние пластично-вязкого течения при котором смесь подчиняется действию силы тяжести свободно растекается хорошо заполняет форму самоуплотняется и приобретает более плотную структуру.
Прессование. При прессовании происходит принудительное перемешивание и взаимное сближение твёрдых частичек бетонной смеси характеризуемое большим или меньшим объёмным сжатие системы.
Центробежное формование. Сущность этого метода в том что форма вместе с загруженной в неё бетонной смесью вращается вокруг своей продольной оси с заданной скоростью. Под действием развивающихся центробежных сил частицы смеси отбрасываются к стенкам формы прижимаются к ним и смесь распределяется равномерным слоем в форме.
Применяемые методы и механизмы для уплотнение бетонной смеси должны обеспечить высококачественную укладку бетона.
Для уплотнения бетонной смеси допускается применение глубинных и навесных вибраторов или вибропригруза для уплотнения плиты. В нашем случае используется вибрирование с пригрузом (амплитуда колебаний (035±003) мм частота колебаний - 50 Гц).
Режим вибрации ( амплитуда частота и время вибрирования) а также шаг установки навесных вибраторов должны обеспечивать необходимое качество уплотнения бетонной смеси равномерное её уплотнение по длине изделия.
Признаком достаточного уплотнения является появление на поверхности формуемого изделия цементного молока. Режим обработки плиты поверхностным вибратором и длительность повторного вибрирования должны быть выбраны опытным путём так чтобы под верхней плитой не появлялись горизонтальные трещины.
Для обеспечения высококачественного формования изделий из жёстких бетонных смесей рекомендуется на заводах МЖБК применять объёмное виброуплотнение бетонной смеси с помощью резонансных виброопалубок виброплощадок виброподдонов и вибропригрузов а также других проверенных устройств для интенсивного уплотнения бетонных смесей.
4. Порядок приемного контроля складирования и транспортирования мостовой конструкции
Приёмочный контроль сборных железобетонных конструкций производится по совокупности показателей качества обеспечивающих требуемые потребительские свойства конструкции.
Балки должны быть приняты ОТК предприятия изготовителя. Результаты приёмочного контроля и испытаний должны быть записаны в журнале ОТК или заводской лаборатории. Приёмка балок должна производиться в соответствии с ГОСТ 13015-1 и ГОСТ 20372-90. Исходя из этих документов балки принимают:
- по результатам периодических испытаний (по показателям прочности и трещиностойкости жёсткости балок морозостойкости балок из бетона пористости а также по водонепроницаемости бетона);
- по результатам приёмочных испытаний - по показателям прочности бетона (классу бетона по прочности на сжатие передаточной и отпускной прочности) по средней плотности бетона соответствия арматурных и закладных деталей рабочим чертежам по прочности сборных соединений точности геометрических параметров толщине защитного слоя бетона ширине раскрытия трещин категории бетонных поверхностей.
Периодическое испытание балок загружением для контроля их прочности жёсткости и трещиностойкости проводят перед началом массового изготовления балок и в дальнейшем при возникновении в них конструкционных изменений в соответствии с ГОСТ 130151.
В процессе серийного производства балок испытания нагружением проводят не реже одного раза в 10 дней. Испытания двухскатной балки длиной до 7800 мм включительно в процессе их серийного производства допускается не проводить.
Текущий приёмный контроль балок следует выполнять неразрушающими методами приём балок производится партиями. Партия должна состоять из балок изготовленных предприятием по одной технологии из материалов одного вида и качества размер партии не должен превышать 50 балок. Партия балок оценивается по результатам поштучного приёмного контроля изделий.
При проверке прочности бетона методами неразрушающего контроля фактическую передаточную и отпускную прочность бетона на сжатие определяют ультразвуковым методом по ГОСТ 176424 или приборами механического действия по ГОСТ 22690. Морозостойкость - по ГОСТ 10060-77. Водонепроницаемость определяют по ГОСТ 12730 и ГОСТ 12730-5; методы контроля и испытания сварных и закладных деталей по ГОСТ 10922-75 и ГОСТ 23858-79; изменения натяжения напрягаемой арматуры - по ГОСТ 22362-77. Потребитель имеет право произвести повторный выборочный или поштучный контроль качества балок применяя при этом порядок и правила приёмки установленные в настоящей технологической карте и перечисленные в стандартах.
Складирование хранение и транспортирование цельноперевозимых балок производится в соответствии с требованиями по ГОСТ 13015.4-84 и рабочих чертежей балок.
При транспортировании цельноперевозимых балок необходимо соблюдать места опирания и строповки конструкции не допускать образования консольных свесов длина которых превышает разрешённые проектом размеры. Балки изготовленные для эксплуатации при расчётной температуре ниже 40°С разрешается вывозить с завода при достижении бетоном 100% прочности.
Хранятся балки на специальных складах складирование должно осуществляться таким образом чтобы маркировка была у торца.
Перевозятся балки на специально приспособленных автомобилях в соответствии с правилами перевозки грузов автомобильным транспортом Республики Беларусь. Балки транспортируются в рабочем состоянии.
5. Операционный контроль качества основных технологических процессов
Пооперационный контроль на заводах ЖБИ осуществляется производственно-техническим персоналом цехов под методическим руководством и при участии ОТК с привлечением заводской лаборатории. Для каждого вида выпускаемых изделий должны быть составлены технические карты в которых отражаются требования к качеству материалов полуфабрикатов а также к условиям и режимам при выполнении отдельных операций технологического процесса. С учетом этих карт составляют специальные карты пооперационного контроля в которых устанавливаются основные этапы производственного контроля его объекты и содержание а также способы контроля на данном этапе.
Первым этапом в пооперационном контроле является проверка качества материалов и полуфабрикатов при поступлении их на завод. Начинается она с проверки наличия всех технологических документов прибывших вместе с материалами. Порядок отбора проб от каждой прибывшей партии материала и способы лабораторных испытаний устанавливаются и осуществляются согласно ГОСТ.
Контроль качества изготовления арматурных сеток каркасов и металлических закладных деталей осуществляется производственно-техническим персоналом арматурного цеха. Проверке подлежит правильность размеров качество и прочность сварных соединений.
Проверяется соответствие марки и вида применённой стали диаметра числа и взаимного расположения стержней требованиям проекта а также соответствие мест установки и способа анкеровки закладных деталей и монтажных петель. Окончательная приёмка арматурных изделий производится работниками ОТК на месте их изготовления. По их же требованиям осуществляются лабораторные испытания сварных соединений.
Контроль качества приготовления бетонной смеси заключается в проверке правильности дозирования её составляющих и тщательности перемешивания смеси а также в проверке правильности дозирования её составляющих и тщательное перемешивание смеси проверка подвижности или чёткости бетонной смеси. В зимнее время подлежит контролю температура подогрева составляющих и самой смеси при выходе ее из бетоносмесителя при укладке в формы. Дозирование составляющих является одним из ответственных этапов технологического процесса производства сборного ЖБ.
От точности дозирования цемента заполнителей вида различных добавок зависит качество бетонной смеси.
Подлежит систематическому контролю влажность заполнителей с учетом которой производится уточнение и корректировка дозировки составляющих бетонной смеси. Для контроля влажности песка применяют приборы ВП-1. Контролируют также однородность бетона транспортирование смеси от места ее приготовления к месту укладки качество формования изделий. Арматурные стали должны обладать достаточной пластичностью что важно по условиям работы конструкции под нaгpyзкой а также при заготовке арматуры. Пластичность характеризуется относительным удлинением при ее испытании на разрыв. Арматурная сталь не должна снижать механических свойств при сварке. К хорошо свариваемым относятся горячекатанные стали с малым содержанием углерода - Ст-3 Ст.5 и 10ГТ
Проверяется соответствие марки и вида примененной стали диаметра числа и взаимного расположения стержней требованием проекта а также соответствие мест установки и способа анкеровки закладных деталей и монтажных петель. Окончательная приемка арматурных изделий производится работниками ОТК на месте их изготовления. По их же требованиям осуществляются лабораторные испытание сварных соединений.
Контроль также предусматривает: проверку исправности собранных форм их очистку и смазку правильность укладки смеси в форму режим уплотнения смеси величину предварительного натяжения арматуры. Для определения амплитуды и частоты колебаний виброплощадки или других вибрирующих элементов можно применять ручной вибратор Вр-1.
Контроль степени уплотнения можно осуществлять электрическим механическим и равнометрическими методами с применением различных приборов.
Контролируют также режим тепловой обработки. Во время тепловой обработки должен вестись систематический контроль температуры с помощью дистанционных термометров термографов и автоматических программных регуляторов. Контроль прочности бетона к концу тепловой обработки качества лицевой обработки изделий после расформовки а также качества обработки и отделки поверхностей изделий.
Пооперационный контроль осуществляется на основе разрабатываемых на заводе технологических карт по каждому виду продукции.
6. Оборудование приспособления и инструменты
Стендовая схема производства характеризуется тем что фopмование и твердение изделий осуществляется на стадии постах без их перемещении за время производственного цикла. Все материалы и механизмы необходимые для формования твердения распалубки и съема изделий. Для этой схемы характерно применение простого универсального оборудования.
Таблица 9.6.1 Универсальное оборудование применяемое при стендовой схеме производства.
Краткая технологическая характеристика
Бетоносмеситель принудительного действия
Дозатор весовой для щебня
Предел взвеш. 400-1600кг
Дозатор весовой для песка
Предел взвеш. 80-400кг
Кран мостовой электрический
Грузоподъемность 125т
Устройство для автоматической смазки
Длина с ручкой 300 мм
Основные положения правил охраны труда
Освещённость рабочих мест должна соответствовать строительным нормам и правилам. Все технологические операции выполняются в строгом соответствии с инструкциями по безопасному производству работ и под контролем сменного мастера. Рабочие должны иметь исправную спецодежду применять индивидуальные защитные средства предусмотренные в технологическом процессе; инструктаж на рабочем месте производится один раз в квартал и при изменении характера работ; очередная проверка знаний безопасных методов работ у рабочих проводится один раз в год комиссией; мастеру и бригадиру помимо "Положения о функциональных безопасностях" производственных инструкций на все виды работ необходимо руководствоваться производственной инструкцией №101 и инструкцией по технической эксплуатации каждого вида оборудования. Все рабочие должны быть закреплены расположением по ходу цеха за мастерами; на каждый вид оборудования вывешивают таблицы о закреплении. В формовочных цехах и других помещениях где используются вибрационные и ударные механизмы выполняются мероприятия по устранению вибрации и снижению уровня шума. Должны быть вывешены инструкции предупреждающие плакаты и памятки.
Нагрузка и разгрузка цельноперевозимых балок должны быть выполнены под руководством инженерно-технического работника специально назначенного приказом. Все съёмные грузозахватные приспособления до их использования или после ремонта должны подвергаться осмотру и испытанию нагрузкой в 1-25 раза превышающую их номинальную нагрузку с длительностью выдержки 10 мин. Результаты осмотра съёмных грузозахватных приспособлений и тары заносятся в журнал осмотра и учёта. При погрузке балок шофёр выходит из кабины автомашины. Не допускается подъём балок примёрзших к земле засыпанных слоем грунта. Подъём балок производится за петли подъёма; после заводки крюков в петли стропильщик обязан отойти в сторону от поднимаемой конструкции; подъём балок должен осуществляться с применением верёвок- оттяжек; при перевозке стропильной балки специализированным автотранспортом необходимо соблюдать требования определяемые "Правилами дорожного движения". Строповка балок грузозахватными приспособлениями не предусмотренными проектом запрещается.
В производственных и вспомогательных зданиях независимо от степени загрязнения воздуха необходимо предусматривать естественную или принудительную вентиляцию. В формовочных цехах и других помещениях где используются вибрационные и ударные механизмы особое внимание необходимо уделить устранению воздействия вибрации на работающих и снижению уровня шума.
Режим работы предприятия - 265 дней в году. Количество рабочих суток - 250 15 суток отводятся на капитальный ремонт.
Две рабочие смены в сутки.
Продолжительность рабочей смены составляет 8 часов.
Баланс рабочего времени:
Вр = 250·2·8 = 4000 часов в год.
График пересменки бригад при 2-х сменной работе на производстве двускатной балки для промышленных зданий:
смена - с 7:00 до 15:30;
смена - с 15:30 до 24:00.
Обеденный перерыв должен составлять 30 минут.
смена - с 11:00 до 11:30;
смена - с 19:30 до 20:00.
Время на личные потребности рабочих - через каждые 2 часа после начала рабочей смены по 15 мин.
В соответствии с нормативно-технической документацией («Типовые конструкции и детали зданий и сооружений» серия 3503-12выпуск 15(19)) и учебной литературой разработана технологическая карта изготовления цельноперевозимой железобетонной балки пролётом 33 м высотой 17м армированной горизонтальными пучками с натяжением пучков на упоры.
Предоставляется эскиз балки в аксонометрии с описанием всех размеров описываются все особенности конструкции.
В соответствии с правилами маркировки железобетонных балок данная балка маркируется как ПР-33Г-26 что значит: промежуточная балка длиной 33 м армированная 26 горизонтальными пучками напрягаемой арматуры под расчетную нагрузку I категории.
Подробно описываются требования ко всем используемым материалам: цементу арматуре воде песку заполнителю и добавкам. Приводятся спецификации напрягаемой и ненапрягаемой арматуры в балке. В случае ненапрягаемой арматуры выбирался выгодный вариант армирования с использованием арматуры класса АIII.
Масса всей балки полученная путём её расчёта равна 12997 т; 341 т которой составляет сталь напрягаемой ненапрягаемой арматуры и закладных деталей 12656 – бетон.
Для изготовления балок запроектирован бетон класса В40 что достигается смесью (для приготовления 1м3 бетона): цемента марки М500 - 563 кг; песка - 239 кг; гранит – 725 кг; воды - 248 л.
Рассчитан расход раствора рабочей концентрации добавки СДБ в количестве 03% от массы цемента с содержанием сухих веществ – 30% на замес бетоносмесителя при плотности раствора СДБ 1144 гсм3 который составит 6064л.
Технологический процесс при изготовлении железобетонной балки осуществляется по стендовому способу.
При натяжении рабочей арматуры применяют электротехнический способ. Температура нагрева - 400 ºС продолжительность нагрева - 5 мин.
В курсовом проекте используемый метод уплотнения – виброуплотнение с пригрузом.
Тепловая обработка происходит по режиму:
- подъем температуры;
- изотермическая выдержка при температуре 85-95°С;
По окончании тепловой обработки производится передача напряжения арматуры на бетон достигший 100% прочности. Готовое изделие с помощью мостового крана подаётся на пост выдержки изделий где производится ремонт покраска и маркировка балок которые потом принимаются ОТК.
Балка подвергается пропариванию в камерах при нормальном атмосферном давлении пара и температуре 80°C. Продолжительность тепловой обработки - 12 ч.
При подготовке форм используется смазка «Эмульсол» удовлетворяющая необходимым требованиям: имеет консистенцию позволяющую наносить её распылителем или кистью на холодные и горячие (до 40-50°C) поверхности сплошным тонким слоем (01-03 мм); обладает достаточной адгезией с металлом форм достаточно водостойкая и не смешивается с бетоном и др.
Контроль используемых материалов в полном объёме обеспечивает требования ГОСТов.
Изготавливаемая балка по основным габаритам соответствует проекту. Отсутствуют сколы трещины внешний вид соответствует СНиПу.Углы между торцевыми гранями и нижней гранью прямые (отклонение от перпендикуляра не более 2 мм на 1 м длины торцевой грани); поверхности граней плоские без раковин выбоин и сколов.
Складирование осуществляется согласно ГОСТ 20372-66.
При изготовлении балок длиной 18 м серии 3503-12 марки ПР-18Г-20 руководствуются инструкциями №86 - по эксплуатации стальных форм; №30 - для стропильщика; №44- для машиниста натяжной станции и гидродомкрата; №60 - по технике безопасности при обслуживании оборудования. Принятые меры и инструкции обеспечивают безопасное выполнение работ.
Для стендовой схемы использовалось простое универсальное оборудование необходимые для формования твердения распалубки и съема изделий.
Ахвердов И.Н. «Технология железобетонных изделий и конструкций специального назначения» - Мн.: Наука и техника 1993. – 240 с.
Ю.М. Баженов А.Г. Комар. «Технология бетонных и железобетонных изделий»- М.: Стройиздат 1984. – 632 с.
Методическое пособие к курсовому проектированию по дисциплине «Технология производства мостовых конструкций» для студентов специальности Т.19.03- «Строительство дорог и транспортных объектов» Минск БГПА 1999г. – 14 с.
ГОСТ 10181.0-81 ГОСТ 10181.4-81. Бетонные смеси.
СНИП 2.03.01-84. Бетонные и железобетонные конструкции.
Типовые конструкции и детали зданий и сооружений серия 3.503-12 выпуск - 15(19).
Общесоюзные нормы технологического проектирования предприятий сборного железобетона ОНТП-07-85 Минстройматериалов СССР.- М. 1986. – 52 с.
Рекомендации по тепловой обработке тяжелого бетона с учетом активности цемента при пропаривании НИИЖБ Госстроя СССР. – М.: Стройиздат 1984. – 42с.
Руководство по применению химических добавок в бетоне НИИЖБ Госстроя СССР.- М.: Стройиздат 1980. – 55 с.
Руководство по технологии формования железобетонных изделий НИИЖБ Госстроя СССР. – М.: Стройиздат 1977. – 995 с.
Руководство по технологии изготовления предварительно напряженных
железобетонных конструкций. – М.: Стройиздат 1975.- 67 с.
СНиП 3.04-80. Техника безопасности в строительстве. Правила производства и приёмки работ Госстрой СССР.- М.: Стройиздат 1982. - 255с.
Афанасьев А.А. Бетонные работы . М. Высшая Школа 1991.
Баженов Ю.М.Технология бетонных и железобетонных изделий. М. 1984.
Рамачандран В.С. Фельдман Р.Ф. Добавки в бетон. М. Стройиздат 1988.
BalkaNenap33r.dwg

Изготовление железобетонной балки
кафедра "Мосты и туннели"
кафедра "Мосты и тоннели"
Армирование ненапрягаемой арматурой балок длиной 33 м.
План верхних сеток плиты
(напрягаемая арматура не показана)
О с ь с и м м е т р и и
эксплуатируемых в районах с сейсмичностью 7
и 9 баллов вместо закладных деталей М-1 ставить М-21
а при установке на резиновые опорные части в районах с сейсмичностью до 6 баллов при продольном уклоне моста до 1 % закладные детали М-1 не ставить
Защитный слой бетона
Примечания 1. Сетки и каркасы в местах их сопряжений связать вязальной проволокой. 2. Стержни сеток плиты и ребра в местах пересечения с отверстием для строповки отогнуть по месту. 3. Все размеры в мм.
Сварные швы К=6 мм длиной 9
Расход стали на одну балку
вариант армирования балок
с использованием стали класса А-II
Каркасы нижнего пояса
Отверстие для строповки
Рекомендуемые чертежи
- 24.01.2023
- 24.04.2014
- 24.04.2014
- 24.04.2014
- 20.08.2014