Структурная многокритериальная оптимизация тех.процесса



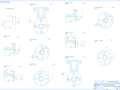
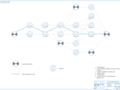
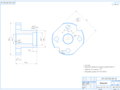
- Добавлен: 24.01.2023
- Размер: 244 KB
- Закачек: 0
Описание
Состав проекта
![]() |
![]() |
![]() |
![]() ![]() ![]() ![]() |
![]() ![]() ![]() ![]() |
![]() ![]() ![]() ![]() |
![]() |
![]() |
![]() |
![]() |
![]() |
![]() |
![]() |
![]() |
![]() |
![]() |
![]() |
![]() |
![]() |
![]() |
![]() ![]() ![]() |
![]() |
Дополнительная информация
математическая модель ПТП.cdw

- значение приведенных затрат
- значение штучно-калькуляционного
- дуга оптимального пути
Чертеж плана обработки.cdw

Вершина 17. Фрезерная
Вершина11. Фрезерная
Маршрутно-операционное
описание перспективного
технологического процесса
Оп.003 Заготовительная
Чертеж детали.cdw

Неуказанные предельные отклонения размеров: валов h14
Маркировать шрифтом ПО-5 ГОСТ2930-62
Курсовая работа по мат. моделированию.doc
1 Структурный анализ технологического процесса и построение
2 Нормирование модели по критериям оптимизации
Анализ технико-экономических резервов производства и выявление приоритетности критериев оптимизации
Оптимизационные расчеты на ЭВМ
1 Пороговая оптимизация
2 Использование обобщенного критерия
Приложение А. Таблица исходных данных статистического анализа
Приложение Б. Распечатка файла исходных данных для расчетов на
ПЭВМ при пороговой оптимизации
Приложение В. Распечатка файла результатов расчета на ПЭВМ при
пороговой оптимизации
Приложение Г. Распечатка файлов результатов расчета критериев на
максимум для построения обобщённого критерия
Приложение Д. Распечатка файла исходных данных для
оптимизационных расчетов по обобщенному
Целью курсовой работы по дисциплине «Математическое моделирование» является приобретение практических навыков в решении следующих задач:
а)системный анализ структуры технологических процессов действующего производства и выявление резервов повышения его эффективности;
б)определение критериев повышения эффективности действующего производства и поиск функциональных параметров предпочтительности при оптимизации по этим критериям;
в)математическое моделирование технологических процессов для реализации многокритериальной структурной оптимизации на уровне их маршрутного описания.
Структурная оптимизация предусматривает решение трёх основных задач:
построение математической модели
выявление приоритетности критериев оптимизации на основе анализа действующей технологии
поиск оптимальной структуры.
Математическая модель
Рассматривая структуру технологического процесса приходим к представлению отдельных его частей в виде множества технологических операций. Целостность системы в данном случае определяется упорядоченным расположением операций как во времени (определен порядок их следования друг за другом) так и в пространстве (определены рабочие места на которых выполняются операции). Такое преставление структуры технологического процесса относится к уровню маршрутного описания.
При выполнении структурной оптимизации технологического процесса на уровне их маршрутного описания в качестве математической модели используется сетевой граф . Вершинами такого графа являются элементы множества возможных вариантов технологических операций отличающихся концентрацией используемыми технологическими методами (в том числе при получении исходной заготовки) и оборудованием. Дуги графа – это логические связи возможности последовательного выполнения пар технологических операций соответствующих инцидентным вершинам.
Базовый технологический процесс обработки детали состоит из одиннадцати операций и представлен на чертеже 2011 000000000 МО:
)токарные операции (5 10) выполняемые на станке 16К20;
)сверлильная операция (15) выполняемая на станке 2М150;
)фрезерная операция (20) выполняемая на станке 6Р13Б;
)фрезерная операция (25) выполняемая на станке 6Р83.
Математическая модель представлена на чертеже 2011 000000000 ММ.
Построение модели осуществлено путем анализа возможных многовариантных технологических структурных решений а именно:
а) различной концентрацией операций:
– концентрация операций 15 20 приводит к включению вместо них операции которая соответствует вершине 12 на сетевом графе;
– концентрация операций 15 20 25 приводит к включению вместо них операции которая соответствует вершине 13 на сетевом графе;
– концентрация операций 20 25 приводит к включению вместо них операции которая соответствует вершине 13 на сетевом графе. Данные операции объединяют сверлильные и фрезерные операции и выполняются на станке 6902ПМФ2;
б) различного технологического оборудования выполнения операции:
– токарные операции соответствующие вершинам 2 4 выполняются на альтернативном станке 16К20Ф3;
– сверлильная операция соответствующая вершине 6 выполняются на альтернативном станке 2Р135Ф2-1;
– фрезерные операции соответствующие вершинам 10 выполняется на альтернативном станке 6Р13Ф3;
– фрезерная операция соответствующая вершине 16 выполняется на альтернативном станке 6Р13.
Вершина входа сети отображает операцию получения исходной заготовки а вершина выхода – операцию окончательного контроля уже готовой детали.
Так как значения критериальных параметров вершин входа и выходы сети не влияют на результат оптимизации то при нормировании модели их можно взять нулевыми.
Для того чтобы определяемые моделью варианты технологических процессов имели одинаковую длину сетевой граф строится с отношением строгого порядка разбитым на слои так что:
а)любая дуга соединяет вершины только соседних слоев;
б)в первом и последнем слоях имеется по одному элементу;
в)вершины одного слоя не соединены между собой дугами.
Такая конфигурация модели получается несложно путем введения фиктивных вершин.
2Нормирование модели по критериям оптимизации
Нормирование модели подразумевает постановку в соответствие каждой вершине графа вещественных чисел ( – номер критерия) представляющих из себя значение выходных функциональных параметров соответствующих используемым критериям оптимизации (см. таблицу 1.1).
Таблица 1.1 – Соответствие критериев оптимизации функциональным параметрам технологического процесса
Критерий оптимизации
Функциональный (критериальный) параметр
Максимальная технологическая производительность
Штучно-калькуляционное время на выполнение технологической операции () мин
Минимальные приведенные затраты на реализацию технологического процесса
Приведенные затраты на выполнение технологической операции () руб.
Минимальная производственная площадь
Площадь занимаемая станками на данной операции () м2
Минимальное количество технологического оборудования
Количество станков на данной операции
Для рассмотрения критерия максимальной производительности необходимо определить соответствующий критериальный параметр – штучно-калькуляционное время . Для его расчёта необходимо предварительно рассчитать режимы резания для каждой вершины графа.
Расчёт режимов резания произведён по [4] следующим образом:
а) определена максимальная глубина резания с учётом максимальной величины припуска;
б) по таблицам [4] определены табличные значения подачи и поправочные коэффициенты учитывающие изменённые условия работы (формулы см. ниже);
в)найденное значение подачи (ммоб) скорректировано по паспортному значению станка (для оборудования со ступенчатым изменением подачи);
г)по таблицам [4] с учётом подачи и глубины резания
определено табличное значение скорости и поправочные коэффициенты (формулы см. ниже);
д)по результатам расчета скорости резания (ммин)
вычислена частота вращения шпинделя:
где – диаметр обрабатываемой поверхности или диаметр осевого инструмента;
e) найденная частота вращения скорректирована по паспортному значению станка (для оборудования со ступенчатым изменением частоты вращения шпинделя);
ж) с учётом скорректированной частоты вращения найдена фактическая скорость резания:
з) определена минутная подача:
В соответствии с [4] расчёт режимов резания произведен по следующим формулам.
Токарная обработка. Подача определена как
где – табличное значение подачи ( ммоб);
– поправочный коэффициент учитывающий сечение державки резца ();
– поправочный коэффициент учитывающий прочность режущей части ();
– поправочный коэффициент учитывающий механические свойства обрабатываемого материала ();
– поправочный коэффициент учитывающий схема установки заготовки ();
– поправочный коэффициент учитывающий состояние поверхности заготовки ();
– поправочный коэффициент учитывающий геометрические параметры резца ();
– поправочный коэффициент жесткость станка ().
Скорость резания определена по формуле
где – табличное значение скорости ( ммин);
– поправочный коэффициент учитывающий группу обрабатываемости материала ();
– поправочный коэффициент учитывающий вид обработки:
(при продольном точении)
(при подрезании торца);
– поправочный коэффициент учитывающий жёсткость станка ();
– поправочный коэффициент учитывающий геометрические параметры резца
– поправочный коэффициент учитывающий период стойкости инструмента ( при мин);
– поправочный коэффициент учитывающий наличие охлаждения ( при наличии СОЖ).
Сверление. Согласно [4]:
где – поправочный коэффициент учитывающий механические свойства обрабатываемого материала ();
– поправочный коэффициент учитывающий наличие охлаждения ( при наличии СОЖ);
– поправочный коэффициент учитывающий состояние поверхности заготовки:
(так как поверхность без корки);
– поправочный коэффициент учитывающий свойства инструментального материала ();
– поправочный коэффициент учитывающий форму заточки инструмента:
(при типе заточки H);
– поправочный коэффициент учитывающий длину рабочей части сверла
(так как сверло по ГОСТ 10902-77);
– поправочный коэффициент учитывающий наличие и состав покрытия:
– поправочный коэффициент учитывающий период стойкости инструмента ( при мин).
Табличные значения режимов:
Фрезерование концевой фрезой. Согласно [4]:
где – подача на зуб (рассчитываемое значение);
ммзуб – табличное значение подачи;
– поправочный коэффициент учитывающий твердость обрабатываемого материала ();
– поправочный коэффициент учитывающий материал режущей части фрезы ();
– поправочный коэффициент учитывающий отношение фактического числа зубьев к нормативному:
(так как фреза стандартная);
– поправочный коэффициент учитывающий отношение вылета фрезы к диаметру ().
Значение подачи на один оборот фрезы
где – число зубьев фрезы.
где – поправочный коэффициент учитывающий свойства обрабатываемого материала ();
– поправочный коэффициент учитывающий отношение фактической ширины фрезы к нормативной ();
– поправочный коэффициент учитывающий состояние поверхности заготовки ()
Фрезерование дисковой фрезой. Согласно [4]:
– поправочный коэффициент учитывающий отношение вылета оправки к диаметру оправки ();
– поправочный коэффициент учитывающий форму обрабатываемой поверхности ().
Результаты расчёта режимов приведены в таблице 1.2
На основе полученных режимов резания выполнено временное нормирование операций.
Расчёт норм времени для универсальных станков с ручным управлением выполнен по методике [5].
Значение штучно-калькуляционного времени рассчитано по формуле
где – подготовительно-заключительное время мин;
– число деталей в партии шт.;
– штучное время рассчитываемое в свою очередь как
где – основное (машинное) время мин;
– вспомогательное время на операцию мин;
– время затрачиваемое на обслуживание рабочего места и личные надобности рабочего берущееся в процентах от оперативного () времени.
Основное время рассчитано как
где – ход инструмента мм;
– минутная подача мммин;
Вспомогательное время рассчитано по формуле
где – вспомогательное время на установку и снятие детали;
– вспомогательное время связанное с переходом (подвод и отвод инструмента смена инструмента изменение режимов обработки и др.);
– вспомогательное время на контрольные измерения по каждому переходу
Подготовительно-заключительное время:
где – подготовительно-заключительное время на наладку станка инструмента и приспособлений;
– подготовительно-заключительное время на дополнительные приёмы;
– подготовительно-заключительное время на получение инструмента приспособления и заготовок до начала работы и сдачу после окончания обработки.
Размер партии определяется по фактическим данным или расчетом ( при оценке экономической эффективности):
где – годовой выпуск деталей шт.;
– число запусков в год.
Для серийного производства (600 – 1200) можно принять .
Нормативные значения вспомогательного и подготовительно-заключительного времени следующие (взяты из [5]).
мин в патроне с креплением ключом с выверкой на биение мелом;
мин при продольном точении растачивании;
мин при поперечном точении с предварительным промером
мин на изменение оборотов шпинделя;
мин на изменение величины и направления подачи
мин установить и снять инструмент;
мин при контроле штангенциркулем;
мин при контроле калибр-пробкой;
мин при контроле фаскомером;
мин при измерении штангенглубиномером.
для токарных станков с наибольшим диаметром изделия устанавливаемого над станиной до 400 мм;
мин на растачивание сырых кулачков;
мин на поворот верхней части суппорта с возвратом в первоначальное положение;
мин при сверлении по разметке;
мин на включение оборотов шпинделя;
мин на установку инструмента в конусе шпинделя;
мин поставить и снять кондукторную втулку;
мин при фрезеровании плоскостей фасонных поверхностей со взятием одной пробной стружки;
мин на изменение число оборотов шпинделя;
мин на изменение величины или направления подачи;
Расчёт норм времени для станков с числовым программным управлением выполнен согласно методики и нормативов [6].
где – время на техническое и организационное обслуживание рабочего места на отдых и личные потребности;
где – вспомогательное время связанное с операцией;
где – подготовительно-заключительное время на организационную подготовку;
– подготовительно-заключительное время на наладку станка приспособлений инструмента программных устройств;
– время на пробную обработку детали.
Нормативные значения вспомогательного и подготовительно- заключительного времени следующие.
мин при установке в патроне с механизированным приводом и выверкой биения индикатором;
как на универсальных станках (см. выше);
мин на получение наряда чертежа программоносителя режущего мерительного инструмента и сдачу их после окончания обработки партии деталей;
мин на ознакомление с работой и чертежом;
мин на инструктаж мастера;
мин на расточку сырых кулачков;
мин на установку и снятие одного режущего инструмента;
мин набрать программу с пульта время на один размер;
мин на установку и снятие специальных кулачков;
мин на установку исходных координат z и х;
мин на настройку устройства для подачи СОЖ;
мин при установке в спецприспособлении;
мин на получение наряда чертежа инструмента приспособлений заготовок;
мин на ознакомление с работой чертежом осмотр заготовок;
мин на установку спецприспособления с выверкой;
мин переместить стол в зону удобную для наладки;
мин на установку исходных режимов;
мин на установку одного инструмента в инструментальный магазин;
мин на установку исходных координат;
Обработка на многоцелевых станках (сверлильно-фрезерно-расточных).
По результатам выполненных расчетов штучно-калькуляционного времени являющегося одним из критериальных параметров (см. таблицу 1.1 осуществлен поиск значений остальных критериальных параметров).
Приведённые затраты на выполнение технологической операции соответствующей вершине графа вычислены по формуле:
где – нормативное (см. [6]) значение часовых приведённых затрат связанных с работой оборудования на соответствующей операции.
Количество станков на операции соответствующей вершине можно рассчитать по формуле
где – годовая программа выпуска данных деталей шт.;
– нормативный коэффициент загрузки оборудования;
н-час – нормативное значение годового фонда времени работы технологического оборудования.
Площадь занимаемая станками на технологической операции соответствующей вершине графа рассчитана по формуле:
где – норматив площади занимаемой технологическим оборудованием на операции соответствующей вершине м2.
Результаты расчёта критериальных параметров приведены в таблице 1.2.
Таблица 1.2 – Исходные данные и результаты нормирования модели
Номер технологического перехода
Скорость резания ммин
Часовые приведенные затраты руб.час
Приведенные затраты руб.
Занимаемая площадь м2
Количество станков шт.
Обобщенный критериальный параметр
Подготовительно-заключительное
Штучно-калькуляционное
Таблица 1.2 – Продолжение
Анализ технико-экономических резервов производства и
выявление приоритетности критериев оптимизации
В данном разделе произведен анализ технико-экономических резервов действующего производства на основе полученных статистических данных. Анализ выполнен по методике [3] с выявлением приоритетности основных критериев оптимизации.
К нормативным показателям уровня технологии относятся приведённые затраты и суммарное штучное время на реализацию перспективного технологического процесса. Поскольку множество полных путей на полученной в разд.1 модели определяет множество допустимых вариантов структуры ПТП а следовательно и соответствующих им значений и то получив эти значения в виде статистического материала можно выявить закономерности формирования резервов технологической эффективности.
Для получения статистического материала математическая модель просчитана на предмет поиска значений длин всех путей графа по параметрам приведённых затрат и штучного времени. Для этого использована специальная программа для ПЭВМ “Перебор” исходные данные для которой подготовлены в виде текстового файла [8] (см. приложение Б). В результате расчёта получены значения длин 72 путей (вариантов структур ПТП). Генеральная совокупность полученных таким путем статистических данных использованная для дальнейшего анализа приведена в приложении А.
На основе полученной статистики была выявлена эмпирическая функциональная зависимость в виде степенной функции
где и – эмпирические коэффициенты.
Для этого была выполнена аппроксимация [9] с использованием программного приложения «Microsoft Excel» пакета программ «Microsoft Office – 2000» с построением соответствующего графика (см. рисунок 2.1).
Рисунок 2.1 – Эмпирическая модель зависимости суммарного штучного времени от приведённых затрат:
– значение приведенных затрат на внедрение ПТП;
– значение суммарного штучно-калькуляционного времени выполнения ПТП.
В результате расчета эмпирических коэффициентов получена зависимость:
Для выявления вида технико-экономического резерва действующего производства рассчитаны следующие показатели [3]:
где и – значения приведённых затрат и суммарного штучного времени действующего технологического процесса (путь 1-3-5-7-11-17-19) на модели 2011200000000ММ):
Так как то основное внимание при оптимизации проектируемого перспективного технологического процесса следует уделять повышению его производительности так как эффект от сокращения суммарного штучного времени во много раз превышает вызванное этим возможное увеличение приведённых затрат.
Поиск оптимальной структуры ПТП выполнен по методике [3]. В качестве главного критерия назначен более приоритетный определённый в разделе 2 то есть максимальная производительность технологического процесса (критериальный параметр – штучно-калькуляционное время). Остальные критерии – второстепенные. На длину пути по каждому второстепенному критерию назначено пороговые значения ( – номер критерия) то есть ограничение сверху в качестве которых приняты длины пути действующего технологического процесса (путь 1-3-5-7-11-17-19 на модели 2011200000000ММ) по соответствующим критериям:
Далее произведены оптимизационные расчёты на ПЭВМ с помощью программы "AMACONT" [8] то есть выполнен поиск упорядоченного множества путей графа по главному критерию. Распечатка файла исходных данных приведена в приложении Б результатов – в приложении В.
Для выявления оптимального пути рассмотрим ранее полученное упорядоченное множество путей (приложение В) по порядку начиная с первого пути проверяя справедливость соотношения ( – номер пути в упорядоченной последовательности) то есть длина пути по каждому второстепенному критерию должна быть меньше соответствующего порогового значения.
В результате анализа выяснилось что условию оптимального выбора соответствует путь под номером 40 который удовлетворяет условию оптимизации ():
2 Использование обобщённого критерия оптимизации
Для выполнения расчётов значений обобщённого критерия был произведен поиск максимальных длин путей по каждому из критериев. Для этого в исходных данных используемых для расчётов при пороговой оптимизации значения критериальных параметров в вершинах были заменены на отрицательные. Затем на ПЭВМ с помощью программы “AMACONT” выполнен расчёт по каждому критерию. Значения соответствовали первым путям при расчёте по соответствующему критерию.
В результате получено:
Распечатки файлов результатов расчёта критериев на максимум приведены в приложении Г.
Далее рассчитаны значения обобщённого критерия для каждой вершины по формуле:
где – количество критериев оптимизации;
– коэффициент принимающий положительное значение если значение параметра стремиться к минимуму и отрицательное в противном случае;
– весовые коэффициенты определяющие значимость соответствующего критерия и назначаемые экспертно с учётом анализа выполненного в разд.2. Так как более приоритетным является критериальный параметр то имеет наибольшее значение. В результате принято
– величина k-ого критерия приведенная к относительно безразмерному виду по формуле:
где – максимальная длина среди всех путей графа по k-ому критерию.
После расчёта обобщённого критерия (полученные значения приведены в таблице 1.2) для каждой вершины задача поиска оптимальной структуры технологического процесса сведена к решению однокритериальной оптимизационной задачи то есть поиску кратчайшего пути на сетевом графе по обобщённому критерию.
Распечатка файла исходных данных приведена в приложении Д распечатка результатов – в приложении Е.
По результатам расчётов первый путь из упорядоченного множества по обобщённому критерию принят в качестве оптимального:
Результатом курсовой работы является получение оптимальной структуры технологического процесса при многокритериальной оптимизации. Так как улучшение одного критериального параметра приводит к ухудшению другого то невозможно минимизировать длину пути по каждому из критериев одновременно. Поэтому в работе реализовано два подхода к проблеме многокритериальной оптимизации пороговая оптимизация и оптимизация по обобщённому критерию. При этом пути на графе (варианты технологического процесса) найденные двумя способами совпадают на три четверти своей длины.
При сравнении результатов оптимизации по обобщённому критерию с результатами пороговой оптимизации получено снижение приведённых затрат на 139% увеличение занимаемой площади на 286% уменьшение количества станков на 23% и уменьшение суммарного штучного времени на 23%.
При сравнении варианта технологического процесса полученного при пороговой оптимизации с действующим технологическим процессом получено снижение приведённых затрат на 34% уменьшение занимаемой площади на 46% уменьшение количества станков на 3% и уменьшение суммарного штучного времени на 3%.
При сравнении варианта технологического процесса полученного при оптимизации по обобщённому критерию с действующим технологическим процессом получено снижение приведённых затрат на 42% уменьшение занимаемой площади на 41% уменьшение количества станков на 52% и уменьшение суммарного штучного времени на 54%.
Следовательно при использовании в качестве основы для технического перевооружения производства варианта технологического процесса полученного при оптимизации по обобщённому критерию достигается максимальный экономический эффект. Применение станков с числовым программным управлением позволило снизить трудоёмкость производства и учесть социальный фактор.
Анфёров М.А. Селиванов С.Г. Структурная оптимизация технологических процессов в машиностроении. – Уфа: Изд-во «Гилем» АНРБ 1996. – 185с.
Анфёров М.А. Моделирование и оптимизация структуры технологических процессов: Учеб. Пособие. – Уфа: изд-во УГАТУ 1998. – 82с.
Анфёров М.А. Методические указания по организации выполнения курсовой работы по дисциплине «Системный анализ и математическое моделирование процессов в машиностроении». – Уфа: изд-во УГАТУ 2003. – 37с.
Общемашиностроительные нормативы времени и режимов резания для нормирования работ выполняемых на универсальных и многоцелевых станках с числовым программным управлением. Ч.2: Нормативы режимов резания. – М: Экономика 1990. – 474с.
Общемашиностроительные нормативы времени вспомогательного на обслуживание рабочего места и подготовительно-заключительного для технического нормирования станочных работ. – М.: Машиностроение 1967. – 396с.
Общемашиностроительные нормативы времени и режимов резания для нормирования работ выполняемых на универсальных и многоцелевых станках с числовым программным управлением. Ч.1: Нормативы времени. – М: Экономика 1990. – 208с.
Расчет экономической эффективности новой техники: СправочникПод общ. ред. К.М. Великанова. 2-е изд.– Л.: Машиностроение 1990. – 448с.
Анфёров М.А. Методические указания по использованию программы «AMACONT» при структурной оптимизации технологических процессов в курсовом и дипломном проектировании. – Уфа: изд-во УГАТУ 2002. – 28с.
Анфёров М.А. Шехтман С.Р. Методические указания по использованию программной среды «Microsoft Excel» для расчета эмпирических моделей в курсовом и дипломном проектировании. – Уфа: изд-во УГАТУ 2002. – 26с
Исходные данные статистического анализа
Значения суммарного штучного времени при реализации технологического процесса мин
Значение приведенных затрат на внедрение технологического процесса руб.
Распечатка файла исходных данных для расчетов на ПЭВМ при пороговой оптимизации
Распечатка файла результатов расчетов на ПЭВМ при пороговой оптимизации
ПРОГРАММА СТРУКТУРНОЙ ОПТИМИЗАЦИИ "AMACONT
ОПТИМИЗАЦИОННАЯ ОЧЕРЕДЬ ТЕХНОЛОГИЧЕСКИХ МАРШРУТОВ
критерии: 24.600 4.100 0.120 0.590
критерии: 24.670 4.290 0.120 0.510
критерии: 25.200 4.470 0.123 0.470
критерии: 25.270 4.660 0.123 0.390
критерии: 26.060 4.000 0.127 0.620
критерии: 26.130 4.190 0.127 0.540
критерии: 26.300 2.760 0.128 0.710
критерии: 26.300 2.800 0.128 0.710
критерии: 26.370 2.950 0.128 0.630
критерии: 26.370 2.990 0.128 0.630
критерии: 26.390 4.130 0.129 0.610
критерии: 26.460 4.320 0.129 0.530
критерии: 26.540 3.240 0.129 0.900
критерии: 26.550 3.170 0.129 0.880
критерии: 26.550 3.210 0.129 0.880
критерии: 26.610 3.430 0.129 0.820
критерии: 26.620 3.360 0.129 0.800
Приложение В (продолжение)
критерии: 26.620 3.400 0.129 0.800
критерии: 26.630 2.890 0.130 0.700
критерии: 26.630 2.930 0.130 0.700
критерии: 26.660 4.370 0.130 0.500
критерии: 26.700 3.080 0.130 0.620
критерии: 26.700 3.120 0.130 0.620
критерии: 26.730 4.560 0.130 0.420
критерии: 26.790 3.650 0.130 1.070
критерии: 26.860 4.040 0.131 0.670
критерии: 26.860 4.080 0.131 0.670
критерии: 26.860 3.840 0.130 0.990
критерии: 26.870 3.370 0.131 0.890
критерии: 26.880 3.300 0.131 0.870
критерии: 26.880 3.340 0.131 0.870
критерии: 26.900 3.130 0.131 0.590
критерии: 26.900 3.170 0.131 0.590
критерии: 26.930 4.230 0.131 0.590
критерии: 26.930 4.270 0.131 0.590
критерии: 26.940 3.560 0.131 0.810
критерии: 26.950 3.490 0.131 0.790
критерии: 26.950 3.530 0.131 0.790
критерии: 26.970 3.320 0.131 0.510
критерии: 26.970 3.360 0.131 0.490
критерии: 26.990 4.500 0.132 0.490
критерии: 27.060 4.690 0.132 0.410
критерии: 27.100 4.520 0.132 0.860
критерии: 27.120 3.780 0.132 1.060
критерии: 27.140 3.610 0.132 0.780
критерии: 27.150 3.540 0.132 0.760
критерии: 27.150 3.580 0.132 0.760
критерии: 27.170 4.710 0.132 0.780
критерии: 27.190 3.970 0.132 0.980
критерии: 27.210 3.800 0.132 0.700
критерии: 27.220 3.730 0.132 0.680
критерии: 27.220 3.770 0.132 0.680
критерии: 27.230 3.260 0.133 0.580
критерии: 27.230 3.300 0.133 0.580
критерии: 27.300 3.450 0.133 0.500
критерии: 27.300 3.490 0.133 0.500
критерии: 27.390 4.020 0.133 0.950
критерии: 27.460 4.210 0.133 0.870
критерии: 27.460 4.410 0.134 0.550
критерии: 27.460 4.450 0.134 0.550
критерии: 27.470 3.740 0.134 0.770
критерии: 27.480 3.670 0.134 0.750
критерии: 27.480 3.710 0.134 0.750
критерии: 27.530 4.600 0.134 0.470
критерии: 27.530 4.640 0.134 0.470
критерии: 27.540 3.930 0.134 0.690
критерии: 27.550 3.860 0.134 0.670
критерии: 27.550 3.900 0.134 0.670
критерии: 27.700 4.890 0.135 0.740
критерии: 27.720 4.150 0.135 0.940
критерии: 27.770 5.080 0.135 0.660
критерии: 27.790 4.340 0.135 0.860
Распечатка файлов результатов расчета критериев на максимум для построения обобщённого критерия оптимизации
критерии: -27.790 -4.340 -0.135 -0.860
критерии: -27.770 -5.080 -0.135 -0.660
критерии: -27.720 -4.150 -0.135 -0.940
критерии: -27.700 -4.890 -0.135 -0.740
критерии: -27.550 -3.900 -0.134 -0.670
критерии: -27.550 -3.860 -0.134 -0.670
критерии: -27.540 -3.930 -0.134 -0.690
критерии: -27.530 -4.640 -0.134 -0.470
критерии: -27.530 -4.600 -0.134 -0.470
критерии: -27.480 -3.710 -0.134 -0.750
критерии: -27.480 -3.670 -0.134 -0.750
критерии: -27.470 -3.740 -0.134 -0.770
критерии: -27.460 -4.450 -0.134 -0.550
критерии: -27.460 -4.410 -0.134 -0.550
Приложение Г (продолжение)
критерии: -27.170 -4.710 -0.132 -0.780
критерии: -27.060 -4.690 -0.132 -0.410
критерии: -25.270 -4.660 -0.123 -0.390
критерии: -26.730 -4.560 -0.130 -0.420
критерии: -27.100 -4.520 -0.132 -0.860
критерии: -26.990 -4.500 -0.132 -0.490
критерии: -25.200 -4.470 -0.123 -0.470
критерии: -26.660 -4.370 -0.130 -0.500
критерии: -27.460 -4.210 -0.133 -0.870
критерии: -26.790 -3.650 -0.130 -1.070
критерии: -27.120 -3.780 -0.132 -1.060
критерии: -26.860 -3.840 -0.130 -0.990
критерии: -27.190 -3.970 -0.132 -0.980
критерии: -27.390 -4.020 -0.133 -0.950
критерии: -26.540 -3.240 -0.129 -0.900
критерии: -26.870 -3.370 -0.131 -0.890
критерии: -26.550 -3.210 -0.129 -0.880
критерии: -26.550 -3.170 -0.129 -0.880
критерии: -26.880 -3.340 -0.131 -0.870
критерии: -26.880 -3.300 -0.131 -0.870
Распечатка файлов результатов оптимизационного расчета на ПЭВМ по обобщенному критерию
критерии: 26.370 2.950 0.128 0.630 0.777
критерии: 26.370 2.990 0.128 0.630 0.780
критерии: 26.300 2.760 0.128 0.710 0.781
критерии: 26.300 2.800 0.128 0.710 0.783
критерии: 26.970 3.320 0.131 0.510 0.786
критерии: 26.970 3.360 0.131 0.510 0.788
-й оптимальный путь
критерии: 26.700 3.080 0.130 0.620 0.789
критерии: 26.900 3.130 0.131 0.590 0.790
критерии: 26.700 3.120 0.130 0.620 0.791
критерии: 26.900 3.170 0.131 0.590 0.792
критерии: 26.630 2.890 0.130 0.700 0.793
критерии: 24.670 4.290 0.120 0.510 0.794
критерии: 26.630 2.930 0.130 0.700 0.795
критерии: 24.600 4.100 0.120 0.590 0.798
критерии: 27.300 3.450 0.133 0.500 0.798