Станок 6Р13Б




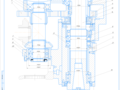
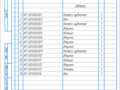
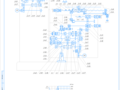
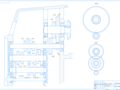
- Добавлен: 25.01.2023
- Размер: 379 KB
- Закачек: 0
Описание
Станок 6Р13Б
Состав проекта
![]() |
![]() ![]() ![]() ![]() |
![]() ![]() ![]() ![]() |
![]() ![]() ![]() ![]() |
![]() ![]() ![]() |
![]() ![]() ![]() ![]() |
Дополнительная информация
Развертка и свертка.cdw

Поворотная головка.spw

Подшипник ГОСТ 831 -75
Подшипник 311 ГОСТ 8338 -75
Гайка ГОСТ 11871 - 88
Винт ГОСТ 11738 - 84 М4 20
Кинематика .cdw

Размеры рабочей поверхности стола
Количество скоростей вращения шпинделя
Пределы частот вращения шпинделя
Конец шпинделя ГОСТ 24644-81
Ход гильзы шпинделя фрезерной головки
Угол поворота фрезерной головки
в продольной плоскости стола
Техническая характеристика станка
ПЗ.doc
Российской Федерации
Владимирский государственный университет
Пояснительная записка к курсовому проекту по дисциплине
«Металлорежущие станки»
Тема: «Спроектировать привод главного движения вертикального консольно-фрезерного станка по типу модели 6Р13Б»
I. Обоснование технических характеристик привода 2
II. Кинематический расчёт станка 4
III. Определение силовых и кинематических параметров привода ..6
IV. Геометрический расчёт привода 7
V. Определение контактных напряжений и напряжений изгиба зубьев
зубчатых колёс привода. Выбор материала и термообработки . 10
VI. Расчетные схемы валов коробки скоростей 12
VII. Проверочный расчёт подшипников 22
VIII. Описание узла станка ..24
Список использованной литературы ..25
Приложение 1. Спецификация 26
Приложение 2. Графическая часть .28
Фрезерные станки предназначены для выполнения широкого круга операций. Они позволяют обрабатывать наружные и внутренние фасонные поверхности нарезать прямые и винтовые канавки фрезеровать зубья зубчатых колёс и прочее.
Вертикально – фрезерные станки характеризуются вертикальным расположением шпинделя. На фундаментной части установлена станина внутри которой размещены: механизм главного движения с приводом от электродвигателя и коробка скоростей. На вертикальных направляющих станины смонтирована консоль которая может перемещаться вертикально по направляющим станины. На горизонтальных направляющих консоли установлены салазки поперечные на которых находится рабочий стол. Таким образом деталь установленная на столе может получить подачу в трёх направлениях. Привод подач стола от отдельного электродвигателя и коробка подач размещены внутри консоли. При обработке на вертикально – фрезерных станках используются дисковые цилиндрические торцевые концевые и шпоночные фрезы.
Целью курсового проекта является разработка привода главного движения по заданным размерам стола материалам инструмента и обрабатываемой заготовки на базе существующего станка модели 6Р13Б. В ходе выполнения курсового проекта формируются навыки конструирования металлорежущих станков.
I. Обоснование технических характеристик привода
Определение ширины фрезерования
Наибольшая ширина фрезерования Bб = мм.
Наименьшая ширина фрезерования Bм = мм.
Наибольший диаметр фрезы Dб = 05b= 05400 = 200 мм.
Наименьший диаметр фрезы из стандартного ряда Dм = 100 мм.
Определение рациональных режимов обработки
Наибольшая глубина резания для сталей при максимальной ширине фрезерования tб = 8 мм при минимальной – tб = 4 мм. Наименьшая глубина резания для сталей tм = 1 мм. Наибольшая глубина резания для чугунов при максимальной ширине фрезерования tб = 12 мм при минимальной – tб = 6 мм. Наименьшая глубина резания для чугунов tм = 1 мм.
Наибольшая подача при обработке самой мягкой стали:
фрезами из быстрорежущей стали Szб = 02 ммзуб.;
фрезами из твёрдого сплава Szб = 015 ммзуб.
Наименьшая подача при обработке самой мягкой стали:
фрезами из быстрорежущей стали Szм = 002 ммзуб.;
фрезами из твёрдого сплава Szм = 001 ммзуб.
Наибольшая подача при обработке самой твёрдой стали:
фрезами из быстрорежущей стали Szб = 012 ммзуб.;
фрезами из твёрдого сплава Szб = 008 ммзуб.
Наименьшая подача при обработке самой твёрдой стали:
фрезами из быстрорежущей стали Szм = 001 ммзуб.;
фрезами из твёрдого сплава Szм = 0007 ммзуб.
Наибольшая подача при обработке чугуна:
фрезами из быстрорежущей стали Szб = 04 ммзуб.;
фрезами из твёрдого сплава Szб = 03 ммзуб.
Наименьшая подача при обработке чугуна:
фрезами из быстрорежущей стали Szм = 0016 ммзуб.;
фрезами из твёрдого сплава Szм = 002 ммзуб.
По рекомендациям находим наибольшую и наименьшую скорость резания:
vб = СvDq TM tx Szy znBz = (3321000.2) (1800.210.100070.4101800.2) = 8941 ммин.
vм = СvDq TM tx Szy znBz = (6472000.25) (3000.2120.1040.4300.12000.15) = 2813 ммин.
Найдём предельные значения частот вращения шпинделя:
nб = 1000vб Dм = (10008941) (314100) = 2847 обмин
nм = 1000vм Dб = (10002813) (314200) = 778 обмин.
Найдём предельные значения подач:
Sб = Szб zб nм = 0430448 = 5376 мммин
Sм = Szм zм nб = 0007102847 = 20 мммин.
Определим диапазоны регулирования:
Определение силовых параметров процесса резания
Определим силу резания при фрезеровке (главную составляющую)
Pz = cp tx Szy Bn z Dq nw = 825121040752001130 2001344802 = 242 кН.
Крутящий момент на шпинделе
Расчёт эффективной мощности привода и мощности электродвигателя
Эффективная мощность:
Мощность электродвигателя:
Nдв = Nэ k = 246 (1208) = 256 кВт.
Выбираем двигатель типа – А02-32-4-С2 у которого N = 3 кВт и U = 1460 мин-1.
II. Кинематический расчёт станка
Определение числа ступеней привода
В этих целях задаёмся знаменателем геометрической прогрессии привода равным φ = 126 как наиболее часто принимаемым в универсальных станках. Тогда
Зная Zn запишем структурную формулу привода в общем виде:
В частном виде: Zn =
Построение структурной сетки
График частот вращения валов привода
Реальное передаточное отношение через числа зубьев колёс с использованием нормали станкостроения Н21 – 5 приведено в табл.1.
Кинематическая схема привода главного движения и всего станка представлена в графической части.
III. Определение силовых и кинематических параметров привода
Так как для проектных расчётов нас интересует наиболее нагруженный режим то рассчитываем силовые и кинематические параметры для наименьших угловых скоростей валов.
Порядок и результаты расчетов представлены в табл. 2.
Минимальная частота вращения n обмин
Минимальная угловая скорость 1с
Максимальный вращающий момент Т
IV. Геометрический расчёт привода
Расчёт геометрических параметров зубчатых колёс
Для ступени выбираем модуль m = 3.
Диаметр делительной окружности: d = mz = 327 = 81 мм.
Диаметр окружности вершин зубьев: da = d + 2m = 81 + 23 = 87 мм.
Диаметр окружности впадин зубьев: df = d – 24m = 81 – 243 = 738 мм.
Диаметр делительной окружности: d = mz = 353 = 159 мм.
Диаметр окружности вершин зубьев: da = d + 2m = 159 + 23 = 165 мм.
Диаметр окружности впадин зубьев: df = d – 24m = 159 – 243 = 1518 мм.
Для второй ступени выбираем модуль m = 4.
Диаметр делительной окружности: d = mz = 416 = 64 мм.
Диаметр окружности вершин зубьев: da = d + 2m = 64 + 24 = 72 мм.
Диаметр окружности впадин зубьев: df = d – 24m = 64 – 244 = 544 мм.
Диаметр делительной окружности: d = mz = 438 = 152 мм.
Диаметр окружности вершин зубьев: da = d + 2m = 152 + 24 = 160 мм.
Диаметр окружности впадин зубьев: df = d – 24m = 152 – 244 = 1424 мм.
Диаметр делительной окружности: d = mz = 422 = 88 мм.
Диаметр окружности вершин зубьев: da = d + 2m = 88 + 24 = 96 мм.
Диаметр окружности впадин зубьев: df = d – 24m = 88 – 244 = 784 мм.
Диаметр делительной окружности: d = mz = 419 = 76 мм.
Диаметр окружности вершин зубьев: da = d + 2m = 76 + 24 = 84 мм.
Диаметр окружности впадин зубьев: df = d – 24m = 76 – 244 = 664 мм.
Для третей ступени выбираем модуль m = 4.
Диаметр делительной окружности: d = mz = 417 = 68 мм.
Диаметр окружности вершин зубьев: da = d + 2m = 68 + 24 = 76 мм.
Диаметр окружности впадин зубьев: df = d – 24m = 68 – 244 = 584 мм.
Диаметр делительной окружности: d = mz = 437 = 148 мм.
Диаметр окружности вершин зубьев: da = d + 2m = 148 + 24 = 156 мм.
Диаметр окружности впадин зубьев: df = d – 24m = 148 – 244 = 1384 мм.
Диаметр делительной окружности: d = mz = 432 = 128 мм.
Диаметр окружности вершин зубьев: da = d + 2m = 128 + 24 = 136 мм.
Диаметр окружности впадин зубьев: df = d – 24m = 128 – 244 = 1184 мм.
Диаметр делительной окружности: d = mz = 426 = 104 мм.
Диаметр окружности вершин зубьев: da = d + 2m = 104 + 24 = 112 мм.
Диаметр окружности впадин зубьев: df = d – 24m = 104 – 244 = 944 мм.
Диаметр делительной окружности: d = mz = 469 = 276 мм.
Диаметр окружности вершин зубьев: da = d + 2m = 276 + 24 = 284 мм.
Диаметр окружности впадин зубьев: df = d – 24m = 276 – 244 = 2664 мм.
Для четвёртой ступени выбираем модуль m = 3.
Диаметр делительной окружности: d = mz = 338 = 114 мм.
Диаметр окружности вершин зубьев: da = d + 2m = 114 + 23 = 120 мм.
Диаметр окружности впадин зубьев: df = d – 24m = 114 – 243 = 1068 мм.
Диаметр делительной окружности: d = mz = 382 = 246 мм.
Диаметр окружности вершин зубьев: da = d + 2m = 246 + 23 = 252 мм.
Диаметр окружности впадин зубьев: df = d – 24m = 246 – 243 = 2388 мм.
Для конической пары шестерен выбираем модуль m = 5067.
Угол делительного конуса для обеих шестерен
Длина образующей делительного конуса
Диаметр делительной окружности
Диаметр окружности выступов
Диаметр окружности впадин
Для колёс z = 54 выбираем модуль m = 4.
Диаметр делительной окружности: d = mz = 454 = 216 мм.
Диаметр окружности вершин зубьев: da = d + 2m = 216 + 24 = 225 мм.
Диаметр окружности впадин зубьев: df = d – 24m = 216 – 244 = 2064 мм.
Длина зуба b = 02a = 432 мм.
Для конической пары шестерен выбираем модуль m = 15.
Расчёт диаметров валов
Диаметры валов рассчитываются приближённо по формуле
где М = Т – Крутящий момент равный вращающему моменту на валу;
[]k – допускаемое напряжение на кручение.
V. Определение контактных напряжений и напряжений изгиба зубьев зубчатых колёс привода. Выбор материала и термообработки
Определим контактные напряжения в зацеплении Н Нм по формуле:
для цилиндрических колёс:
для конических колёс:
где К – вспомогательный коэффициент (для прямозубых колёс К = 436);
Ft = 2T2103d2 – окружная сила в зацеплении;
KHα – коэффициент учитывающий распределение нагрузки между зубьями (для прямозубых колёс KHα = 1);
- коэффициент вида конических колёс (для прямозубых колёс )
KH – коэффициент неравномерности нагрузки по длине зуба (для прямозубых колёс KH = 1);
KH – коэффициент динамической нагрузки зависящий от окружной скорости колёс и степени точности передачи.
Определим напряжение изгиба зубьев шестерни и колеса:
для цилиндрических колёс
для конических колёс
где KFα – аналогичен KHα;
YF1 и YF2 – коэффициенты формы зуба шестерни и колеса;
После определения контактных напряжений и напряжений изгиба подбираем материал и термообработку обеспечивающие прочность на изгиб и износостойкость.
Порядок и результаты расчётов представлены в табл. 3.
Материал для обоих колёс
закалка по сечению HRC
закалка по сечению HRC сердцевина HRC 30
VI. Расчётные схемы валов коробки скоростей
Вертикальная плоскость
а) определим реакции в опорах:
б) строим эпюру изгибающих моментов относительно оси X:
Горизонтальная плоскость
б) строим эпюру изгибающих моментов относительно оси Y:
Строим эпюру крутящих моментов:
Определяем суммарные радиальные реакции:
Определяем суммарный изгибающий момент в опасном сечении:
VII. Проверочный расчёт подшипников
Пригодность подшипников определяется сопоставлением расчётной динамической грузоподъёмности Crp и базовой Cr .
Расчётная динамическая грузоподъёмность Crp определяется по формуле:
где m = 3 для шариковых подшипников;
Lh = 10000 ч для зубчатых передач;
для данного случая:
где Ra – осевая нагрузка подшипника;
Rr – суммарная реакция подшипника;
V – коэффициент вращения (V = 1);
X – коэффициент радиальной нагрузки;
K – коэффициент безопасности (K = 115);
KT – температурный коэффициент (KT = 1).
VIII. Описание узла станка
Поворотная головка центрируется в кольцевой выточке горловины станины и крепится к ней четырьмя болтами входящими в Т – образный паз фланца станины.
Шпиндель смонтирован на шариковых и роликовых подшипниках с внутренним натягом в гильзе которая может двигаться в вертикальной плоскости. Шпиндель получает вращение через пару конических и пару цилиндрических колёс смонтированных в головке причём последнее колесо сидит на втулке. Так как втулка вращается на независимых подшипниках то усилия в зацеплении не передаются шпинделю который связан со втулкой скользящими шпонками. Смазка подшипников осуществляется разбрызгиванием от централизованной системы смазки.
Перемещение гильзы осуществляется с помощью передачи винт – гайки скольжения.
Также в поворотной головке смонтировано устойство электромеханического зажима. Оно предназначено для закрепления инструмента в шпинделе станка. Затяжка и выталкивание инструмента производятся с помощью тяги расположенной внутри шпинделя. Возвратно – поступательное перемещение тяги обеспечивается резьбовым соединением её со шлицевым валом получающим вращательное движение от головки электромеханического зажима инструмента. На конце тяги имеется Т – образная головка которая соединяется с Т - образным пазом захвата ввёрнутого в оправку с фрезой.
Список использованной литературы
Шейнблит А.Е. Курсовое проектирование деталей машин: Учеб. пособие для техникумов. – М.: Высш. шк. 1991. – 432 с.
Тихомиров Р.А. Жарков В.Н. Обоснование технических характеристик приводов металлорежущих станков: Учеб. пособие. – Владимир1984.– 68 с.
Тихомиров Р.А. Жарков В.Н. Металлорежущие станки: Метод. указания. – Владимир 2003. – 72 с.
Проников А.С. Расчёт и конструирование металлорежущих станков: 2-е изд. – М.: Высш. шк. 1986. – 431 с.
Тарзиманов Г.А. Проектирование металлорежущих станков. – М.: Машиностроение 1972. – 312 с.
Пуш В.Э. Конструирование металлорежущих станков. - М.: Машиностроение 1977. – 390 с.
Кучер И.М. Металлорежущие станки. - М.: Машиностроение 1969. – 720 с.
Поворотная головка..cdw

Отклонение от соосности серьги и шпинделя
Радиальное биение конического отверстия
а) у торца шпинделя - 10 мкм;
б) на расстоянии - 20 мкм.
Осевое биение шпинделя не более 10 мкм.
Торцевое биение опорного торца шпинделя
Радиальное биение центрирующей шейки шпин-
деля не более 10 мкм.