Спроектировать вытяжной пресс-автомат с выровненным ходом


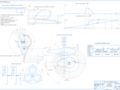
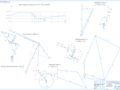
- Добавлен: 24.01.2023
- Размер: 7 MB
- Закачек: 0
Описание
Состав проекта
![]() |
![]() |
![]() ![]() ![]() ![]() |
![]() ![]() ![]() |
![]() ![]() ![]() |
![]() ![]() ![]() ![]() |
![]() ![]() ![]() |
Дополнительная информация
Лист2.cdw

Расчетное положение механизма
Структурная группа 4-5
Структурная группа 2-3
Структурная группа 0-1
КП ТММ кафедра механики
вытяжной пресс автомат.doc
В машиностроительном производстве широко используется прессова - ние – технологический процесс обработки различных материалов давлением на прессах.
Прессованием получают заготовки и изделия из металлов пластмасс и других материалов; из металлов получают валы оси шкивы зубчатые колеса и т.д.
Если изделия имеют массовое применение – болты гайки капоты автомобилей и т.п. для их изготовления применяют прессы-автоматы.
Вытяжка – операция листовой штамповки – свертка листовой заготовки между пуансоном и матрицей вытяжного пресса в полое изделие. Вытяжкой получают капоты автомобилей кабины тракторов фюзеляжи самолетов и т.п. изделия.
Кузнечно-прессовые машины занимают видное место в сфере машиностроительного производства а прессы для глубокой вытяжки – перспективный вид этих машин. В прессах как и других машинах с выровненным ходом используется принцип их конструирования при котором их назначение обеспечивается при использовании в механизмах звеньев с односторонним вращательным движением взамен таких из них движение которых – вращательное но возвратное. Использование этого принципа позволяет повысить эксплуатационные характеристики работы машин за счет снижения маховых масс при увеличении энергоемкости их звеньев.
Выполняя проект студент получает навыки выбора функциональных механизмов обеспечивающих работу задаваемой ему машины навыки вы-числения размеров из звеньев оценки геометрических силовых и массовых характеристик машин анализа составляющих общего энерго-потребления. Получаемые материалы дают достаточное представление о контурах зарож- дающейся машины необходимое для принятия обоснованного решения о выделении средств на продолжение проектирования.
Технико-экономическое обоснование выбора схемы
вытяжного пресса-автомата с выровненным ходом.
Прототип – известное техническое решение со свойствами близкими к заданным. В процессе проектирования машин он служит своеобразным ориентиром для получения решения с требуемыми свойствами. Цели проектирования достигают обоснованным изменением свойств выбранного прототипа.
Изучая рекомендованную и иную литературу в работе находим схему вытяжного преса-авто- мата с выровненным ходом которую в дальнейшем рассматриваем как прототип (рис.1.1).
Рис.1.1. Вытяжной пресс-автомат с выровненным ходом.
Пресс-автомат предназначен для изготовления деталей путем вытяжки из тонкого листового либо полосового металла с прижимом заготовки. Дефор-мация заготовки осуществляется в матрице пуансоном установленным на ползуне 5 двухкривошипного коленного механизма состоящего из звеньев 1-2-3-4-5. На рис.1.1.а представлена диаграмма изменения усилий вытяжки в функции перемещения пуансона-ползуна 5.
Кривошип 1 приводится во вращение электродвигателем через ступенчатую передачу (рис.1.1.б) включающую планетарную и простую ступень. Кулачковый механизм зажимного устройства прижимает деталь к столу во время обработки ее в матрице пуансоном и при выходе пуансона из матрицы кулачек посажен на вал кривошипа 1. График изменения аналогов ускорений изображен на рис.1.1.в.
Наличие в несущем рычажном механизме второго кривошипа 3 позволяет сократить до минимума количество звеньев с возвратным движением увеличить маховые массы и динамическую устойчивость работы пресса-автомата лишь за счет увеличения запаса кинетической энергии его звеньев.
2. Пояснения к выбору структуры пресса.
Структуру вытяжного пресса-прототипа принимаем за основу. В состав пресса включаем источник механического движения – простейший и наиболее распространенный нерегулируемый асинхронный электродвигатель 1 (рис.1.2) несущий механизм 2 который обеспечит преобразование вращательного движения электродвигателя в требуемое возвратно-поступательное движение рабочего органа – пуансона 3 зубчатый механизм снижающий частоту вращения вала электродвигателя до частоты вращения входного звена несущего механизма при которой обеспечивается заданная производительность механизм прижима заготовок 5 состоящий из коромыслово-ползунного и кулачкового механизмов.
Для динамической устойчивости технологического процесса высадки снижения тепловых потерь электродвигателя 1 и в конечном счете для по-вышения общего к.п.д. процесса в его состав при необходимости будет введена дополнительная маховая масса 7 в виде махового колеса способно-го накапливать необходимую кинематическую энергию. В результате по-лучаем предварительную блок-схему пресса которую и принимаем в качестве основы:
электродвигатель приводной
механизм несущий * = 0.544
рабочий орган-пуансон
механизм прижима заготовок
маховик Jmax = 2.788кгм2
В дальнейшем определим параметры выбранной схемы уточним расположение ее элементов.
3. Оценка энергопотребления проектируемого
Рассматриваемый пресс-автомат относится к технологическим машинам и основной расход энергии приходится на стадию установившегося движения.
За один полный цикл установившегося движения работа двигателя (Адв.) расходуется на преодоление сил полезного (Ап.с.) и вредного (Ав.с.) сопротивлений:
Адв. = Ап.с. + Ав.с..
Поскольку работа других сил – потенциальных (веса упругости) и сил инерции за цикл установившегося движения равна нулю работу сил трения (Атр.=Ав.с.) учитываем с помощью к.п.д.(). Тогда за цикл:
Работу полезных сил (Ап.с.) находим интегрируя заданный график полезных нагрузок (рис.1.1.а).
Интегрирование выполняем исходя из геометрического смысла интеграла как площади заключенной между осью относительных перемещений и кривой относительных нагрузок . Получаем:
где А1 А2– площади треугольника трапеции и треугольника в относительных единицах.
Искомая работа полезных сил:
Передаточный механизм от вала двигателя к рабочему органу-пуансону Е включает зубчатый и несущий рычажный механизмы. Поэтому его к.п.д.:
где з.м и р.м. – цикловые к.п.д. зубчатого и рычажного механизмов.
Предполагая что зубчатый механизм будет включать плпнетарную и простую компенсирующую передачу его к.п.д. оцениваем как (13стр322-333)
Предполагая далее что рычажный механизм будет шестизвенным (как у пресса-прототипа) его к.п.д. в первом приближении оцениваем как:
Тогда искомый к.п.д. передаточного механизма:
и работа двигателя за цикл установившегося движения должна составлять:
Затраты энергии на обработку одной детали составят:
а потребление ее из сети будет достигать:
где = 0.92 – к.п.д современных асинхронных электродвигателей.
Определение параметров схемы вытяжного пресса-автомата.
Привод служит источником механического движения звеньев пресса причем эти движения должны находиться в строгом соответствии с заданной производительностью Пр = 950 изделийчас. В рассматриваемом случае привод включает нерегулируемый короткозамкнутый асинхронный электродвигатель 1 (рис.1.2) и зубчатую передачу 4 согласующую обороты электродвигателя с оборотами кривошипа несущего механизма.
Будем считать что кривошип несущего механизма насажен на главный вал пресса т.е. за один его оборот будет изготовлена одна деталь. Тогда частота вращения кривошипа:
Продолжительность цикла:
а цикловая мощность приводного электродвигателя должна превышать величину:
При данных мощности и величине производим синтез элементов привода механизма вытяжного пресса.
1.1. Выбор электродвигателя и вида понижающей передачи.
Из каталога электродвигателей Европейской серии ИР либо серии 4А и выписываем в таблицу 2.1 параметры электродвигателей с ближайшей большей мощностью по сравнению с:
Марка электродви-гателя
Отношение к минимальному моменту
Махо-вой момент ротора
Передаточ-ное отношение редуктора
Крити-ческо-го момента
Чтобы получить частоту вращения кривошипа несущего механизма nкр = 158мин-1 в каждом из этих случаев выбора электродвигателя привод дол-жен содержать понижающую передачу с передаточным отношением:
Рассчитанные по этой формуле значения Uпер также заносим в табл.2.1.
Из всех известных передач с постоянным передаточным отношением наименьшими габаритами весом наибольшей надежностью и к.п.д. обладают зубчатые передачи среди них прежде всего планетарные. Поэтому основные функции по преобразованию вращательного движения двигателя во вращательное кривошипа несущего механизма т.е. главного вала пресса будем возлагать на планетарный механизм. Т.к. однорядный планетарный механизм позволяет получить передаточное отношение Uпл не более 9 а передаточное отношение простой одноступенчатой зубчатой передачи с прямыми зубьями Uк обычно не превышает 4 то для планетарного механизма выбираем более схожую схему. С помощью этой схемы при ведущем водиле Н можно получить передаточное отношение механизма Uпл = . Исходя из этих соображений производим разбивку общего передаточного отношения привода Uпер следующим образом (таблица 2.2).
Общее передаточное отношение зубчатой передачи (табл.2.1)
Передаточное отношение по ступеням
Дополнительный вариант
Анализируя данные таблиц 2.1 и 2.2 приходим к выводу что по основным параметрам (простота и вес конструкций пусковые характеристики двигателя и к.п.д.) для нашего случая является привод от двигателя марки 4А90L4Y3 с основным вариантом редуктора Uпл с одноступенчатой парой цилиндрических зубчатых колес (Uк = 2.5).
1.2. Синтез зубчатых колес.
Рис. 2.1 Схема зубчатой передачи.
Основу передачи составляет планетарный механизм м передаточным отношением:
Открытая зубчатая передача имеет передаточное отношение:
Синтез (подбор чисел зубьев) планетарной ступени производим на основе условий:
условия выполнения требуемого передаточного отношения
условия правильности зацепления
Условие выполнения требуемого передаточного отношения:
и запишем условие соосности:
Преобразованием из этих условий получим:
Подставляем в эти формулы возможные комбинации получим соответствующие комбинации чисел зубьев (табл.2.3)
По условию правильности зацепления во всех вариантах можно принять γ =1.
Наименьшие габариты будут у варианта №7:
Z1 = 91; Z2 = 26; = 25; Z3 = 90.
Поэтому варианту из условия соседства находим число сателлитов:
Чтобы механизм был уравновешен и не имел большой сложности принимаем K = 3.
Проверяем условие сборки:
удовлетворяется при любом П (Ц получается целым).
Проверяем условие соосности т.е. 91 – 26= 90 – 25.
Для уравнительной зубчатой передачи U4-5 = 25.
Приняв Z4 = Zmin = 17 найдем Z5 = Z4 U4-5 = 17 2.5 = 42.5
а при Z4 = 18 получим Z5 = 18 2.5 = 45.
Окончательно принимаем Z4 = 18 и Z5 = 45.
Модуль зубчатых колес планетарного механизма определяем по максимальному моменту в этом механизме действующему на выходной его вал (вал водила).
где номинальная угловая скорость двигателя:
Ближайший больший модуль первого ряда по СТСЭВ 310-76:
Модуль зубчатых колес открытой передачи рассчитываем по моменту на валу кривошипа:
Мкр = Мн U4-5 = 358.752.5 = 896.88 н.м.
Учитывая повышенный износ при работе без смазки принимаем для открытой уравнительной передачи = 6 мм.
Делительные диаметры колес определяем по формуле:
d1 = m Z1 = 4 91 = 364 мм
d2 = m Z2 = 4 26 = 104 мм
d2 = m Z2 = 4 25 = 100 мм
d3 = m Z3 = 4 90 = 360 мм
d4 = m1 Z4 = 6 18 = 108 мм
d5 = m1 Z5 = 6 45 = 270 мм
Находим диаметр водила:
dн > d1 – d2 = 364 – 104 = 260 мм
Принимаем dн = 300 мм.
2. Выбор и синтез несущего механизма.
Несущий механизм связан с рабочим органом и должен обеспечить ему возвратно-поступательное движение с достаточной величиной коэффициента производительности *.
В соответствии с входными данными получим:
Из простейших четверозвенных механизмов возвратно-поступательное движение рабочему органу могут обеспечить:
- кривошипно-ползунные;
Однако тангенсный механизм не может иметь кривошипы что необходимо если привод от электродвигателя осуществлять через зубчатую передачу синусный механизм имеет *=05 независимо от размеров звеньев а кривошипно-ползунный при * > 0522 имеет неприемлемую величину интервала угла давления (γ > 30). Поэтому усложним схему несущего механизма – рассмотрим шестизвенную схему включающую два четырехзвенных механизма. По соображению долговечности ведущим пусть будет двухкривошипный шарнирный четырехзвенник позволяющий получить ( при приемлемых интервалах углов γ) * ≤ 055(5) на второй – аксиальный кривошипно-ползунный механизм способный преобразовать вращательное движение шарнирного четырехзвенника в поступательное инструмента (пуансона).
Рис. 2.2 Схема несущего механизма.
В результате получаем схему несущего механизма (рис.2.2) способную обеспечить требуемую величину * максимально возможную долговечность (имеет лишь одну поступательную кинематическую пару) записать максимально возможную кинетическую энергию (нет звеньев являющихся коромыслами). Произведем геометрический синтез указанной схемы.
Отсоединим кривошипно-ползунный механизм СДЕ и изобразим его в двух крайних и одном промежуточном положении (кривошип СД перпендикулярен направляющей ползуна Е) в котором угол давления шатуна ДЕ на ползун Е принимает максимальное значение γmax (рис.2.3).
Рис.2.3 Присоединенный кривошипно-ползунный механизм СДЕ в двух крайних
(СДоЕо и СД2Е2) положениях и в положении (СД1Е1) максимума угла давления γmax
Рассмотрим два крайних положения механизма СД0Е0 и СД1Е1 между которыми перемещение ползуна Е составляет требуемую величину Н приходим к выводу что:
Анализируя промежуточное положение механизма СД1Е1 из прямоугольного треугольника СД1Е1 получаем:
где = 30 - максимально допустимый угол давления шатуна ДЕ на ползун Е.
Для присоединяющего шарнирного двухкривошипного четырехзвенника ОАВС (рис.2.3) входными параметрами служат:
* = 0.554 и (принимаем) .
Найдем другие размеры этого механизма.
Как следует из полученного чтобы спроектировать двухкривошипный шарнирный четырехзвенник с заданной величиной * необходимо с помощью приведенных в этой работе формул и таблиц найти размеры кривошипно-коромыслового механизма с теми же значениями * интервала угла давления γ1 и относительных размеров звеньев затем поставить полученный четырехзвенник на кривошип а его стойку сделать кривошипом. При этом крайние положения четырехзвенника наступают когда ведомый кривошип ВС совмещается со стойкой ОС.
Определяем угол перекрытия исходного и преобразованного механизмов:
= α р.х – 180 = 360 * - 180 = 360 0.554 – 180 = 19.5
где α р.х = 360 * = 360 0.554 = 199.5 - угол рабочего хода.
Из ближайшей по таблице (таблица для = 20) выбираем четырехзвенник с оптимальным интервалом угла давления:
где границы интервала
(несколько превышает предельно-допустимое значение [γ]= 45 ).
Для выбранного интервала γ1 из таблицы выписываем значение угла размаха коромысла ВС ( =10) шаг изменения при исследованиях полярного угла φ в круге единичного радиуса R = 1.0 (Δφ = 3.9) порядковый номер точки на дуге круга (n = 5).
Тогда значение полярного угла получаем таким:
φ = + n Δφ = 20 + 5 3.9 = 39.5.
Вычисляем параметр Р выбора исходного четырехзвенника из таблиц:
Находим относительные размеры звеньев преобразованием двухкривошипного четырехзвенника ОАВС (рис.2.2) с выровненным ходом:
Чтобы найти предельные значения γ получим предварительно:
Выберем абсолютный размер звена ВС. Примем:
Тогда длина относительной единицы (в м) составит:
а абсолютные размеры звеньев будут:
По конструктивным соображениям угол между направлениями стойки ОС шарнирного четырехзвенника OABC и направляющей ползуна Е присоединенного кривошипно-ползунного механизма принимаем:
Рис. 2.4 Несущий рычажный шестизвенник в начальном положении.
Чтобы обеспечить синхронизацию работы механизмов присоединяем их в одном из крайних положений когда начинается рабочий ход. При этом у шарнирного четырехзвенника ОАВС кривошип ВС расположен на прямой ОС слева от шарнира С (рис.2.4) а кривошип DС расположен по направляющей ползуна Е сверху шарнира С. Очевидно угол излома рычага () принадлежащего шарнирному четырехзвеннику ОАВС и кривошипно-ползунному механизму СDЕ должен составлять величину:
Таким образом имеем:
Полученные размеры используем при построении плана характерных положений несущего механизма. Построение производим методом засечек.
Положения : 0 6 - соответствует крайним положениям механизма;
4 5 7 - соответствуют точка излома графика нагрузок;
8 - соответствуют наступлению экстремумов углов давления γ1 (γma
- соответствуют эктремуму угла давления γ1 (γm
- соответствует середине фазы удаления в кулачковом механизме;
- промежуточная точка.
План положений механизма используем как для проверки результатов синтеза (ход Н угол рабочего хода αр.х.) так и в дальнейшем для определе-ния величины обобщенной координаты (табл.2.8)
3. Синтез кулачкового механизма.
В описании прототипа указано что фазовый угол возвращения толкателя φв может быть равен фазовому углу удаления причем эти углы разделены между собой фазовым углом дальнего стояния φд.с. = 20. При повороте кулачка на угол φб.с. механизм прижима заготовок фиксируется в одном из своих крайних положений прижимая заготовку к матрице.
Для привода механизма прижима заготовок к столу во время обработки изделий принимаем плоский кулачковый механизм с поступательным движением роликового толкателя со следующими параметрами:
ход толкателя h = 56мм;
фазовый угол удаления φу = 114;
фазовый угол дальнего выстоя φд.в. = 20;
фазовый угол возвращения φв = 114;
допускаемый угол давления [γ] = 30.
Величины фазовых углов и работу прижимного механизма назначаем в соответствии с циклограммой работы механизма: во время прессования и в начале холостого хода пуансона осуществляется ближний выстой толкателя (φб.с.= 360-φу– φв – φд.с. = 360–114–114–20 =112).
Выбираем синусный закон движения толкателя на фазе удаления ( в соответствии с описанием прототипа) и с равномерно- убывающим уско-рением на фазе возвращения.
Из таблицы 4.3. выписываем формулы для определения функций поло-жения толкателя и передаточных функций 1-го и 2-го порядков.
Рассчитываем эти функции на фазе удаления где толкатель движется по закону синусоиды:
На фазе возвращения выходное звено движется по закону с равно-убывающим ускорением:
где () и () – относительные значения текущего угла отсчитыва-емые от начала фазы удаления либо возвращения.
Поскольку в нашем случае φу и φв разбиты на 6 равных частей то
Т.е. указанные функции в пределах каждой из фаз будут определены в 6-ти равностоящих точках.
Результаты расчетов заносим в таблицу 2.5.
Задачу об определении минимального радиуса при проектировании кулачка решаем графическим методом в координатах S-S.
Для устранения самопересечения профиля а также из условий равенства износа кулачка и ролика радиус rр последнего выбираем из двух соотношений:
Графически (замерами) получаем:
Принимаем rр = 18 мм
Полученную схему кулачкового механизма совмещаем со схемой несущего механизма (в удобном положении его стойки) и замеряем угол между кривошипом ОА и радиус вектором кулачка в начале фазы удаления α = 118.
4. Динамический синтез кривошипно-коленного пресса.
Динамический синтез пресса проводим с целью повышения его общего к.п.д. путем приведения в «норму» теплового излучения обмоток приводного электродвигателя за счет равномерности вращения внутри цикла.
Задачу решаем подбором и перераспределением масс звеньев введением при необходимости дополнительной маховой массы в виде махового колеса с постоянным моментом инерции.
Предварительно произведем учет инертных свойств звеньев уже задействованных в рассматриваемом прессе механизмов.
4.1. Расчет масс и моментов инерции звеньев механизмов.
Инертные свойства звеньев характеризуют показатели массы (при поступательном движении) и момента инерции (при вращательном движении).
В первом приближении можем принять что по длине рычагов массы распределены равномерно что интенсивность распределения q = 30 кгм и что зубчатые колеса – сплошные диски с шириной bк зависящей от межосевого расстояния как
где а = 0205 6180 представляет собой коэффициент ширины зуба.
При этом центры масс рычагов располагаются по их серединам массы определяются как
моменты инерции звеньев относительно их центров масс находятся как:
а относительно оси вращения (для вращающихся масс) как
Массы зубчатых колес определяем через делительные диаметры d и межосевые расстояния aw по формуле:
которая при плотности материала ρ=78103 кгм3 (сталь чугун) и при принятом а = 025 для облегчения вычислений предварительно должна быть приведена к виду:
Моменты инерции колес относительно оси вращения определяем через их массу и делительный диаметр как для однородных дисков:
Результаты расчетов заносим в таблицу 2.6.
Оценку динамических характеристик прочих деталей пресса производим следующим образом:
Массу пуансона Е вместе с перемещающим его ползуном оцениваем как
Массу толкателя кулачкового механизма ориентировочно оцениваем как
где - длина толкателя замеренная по чертежу.
Массу кулачка и момент инерции Jк оцениваем по среднему радиусу:
и ширине которую задаем как
Массу водила планетарной ступени редуктора находим с помощью формулы:
где ширину водила принимаем равной ширине смонтированного в нее сателлита z2 т.е.:
а момент инерции Jн как для сплошного диска:
Момент инерции ротора электродвигателя определяем по маховому моменту:
Динамические характеристики остальных движущихся звеньев – ходовой винт валы ролик кулачкового механизма и т.п. из-за малых масс либо скоростей точек считаем пренебрежимо малыми и далее не учитываем.
Полученные данные заносим в таблицу 2.6 и используем при после-дующем динамическом синтезе машины.
Наименование параметра и его обозначение
Длина рычага диаметр колеса (м)
Момент инерции относительно оси вращения
Момент инерции относительно центра масс кгм2
4.2. Расчет приведенных моментов инерции.
Инертные свойства машин и механизмов характеризуют приведенной массой либо приведенным моментом инерции в зависимости от того линейным или угловым является перемещение звена приведения. Приведенным к звену момент инерции масс звеньев механизмов вычисляют как сумму приведенных масс звеньев и их моментов инерции на квадраты передаточных функций в движениях этих звеньев относительно звена приведения.
Приведенный момент инерции механизма приводим к главному валу машины умножая его величину на квадрат передаточной функции от звена приведения к указанному валу.
Т.о. приведенный к валу кривошип ОА (рис. 2.3) несущего механизма – принимаем его за главный вал вытяжного пресса-автомата – и момент инерции масс подвижных звеньев можем представить как сумму приведенных моментов инерции следующих механизмов узлов и деталей:
Ротора приводного электродвигателя:
Зубчатой передачи (рис. 2.1):
где - приведенный к валу колеса Z3 момент инерции планетарного механизма. Величину вычисляем как:
где К = 3 – число сателлитов а передаточные функции будут (рис. 2.5):
Рис. 2.5 Схема планетарной передачи и план скоростей.
Остальные данные берем из таблицы 2.6.
Jпл =0.2 362 + 0.48 +3 [(2.15 + 1.99) 5.42 + (2.910-3 + 2.5 10-3) 103.852] = 975.5 кгм2
Тогда приведенный момент инерции для зубчатой передачи будет равен:
Jпер.пр = (975.5 + 4.9 10-3) 2.52 + 192 10-3 = 6097.2 кгм2
Приведенного к валу кривошипа момента инерции механизма прижима заготовки Jприж.пр.
Указанный момент влияет на движение вытяжного пресса лишь в периоды движения толкателя кулачкового механизма – на фазах удаления и возвращения. Причем на концах этих фаз Jприж.пр = 0 т.к. передаточная функция от толкателя к кулачку т.е. к валу кривошипа ОА при этом равна нулю.
Максимальное значение Jприж.пр приобретает вблизи середины этих фаз .
В этом положении величина приведенного момента инерции прижима заготовок может быть приведена к виду:
для фазы возвращения:
Рис. 2.6 Схема механизма прижима заготовок.
Приведенного к валу кривошипа ОА момента инерции несущего механизма (рис.2.7):
Рис. 2.7 Кинематическая схема несущего механизма.
где передаточная функция в движении ползуна 5 относительно кривошипа ОА может быть вычислена как:
В шарнирном четырехзвеннике ОАВС:
Отсюда угол передачи:
где А = 0.26085; В = 0.4576 получены выше в разделе 2.2 φ1 – значения обобщенной координаты механизма замеренные от положения его стойки (ОС).
В кривошипно-ползунном присоединенном механизме CDE:
Функцию положения шатуна DE определяем двумя параметрами – углом давления γ:
и координатой Y ползуна
Передаточные функции кривошипно-ползунного механизма получаем из повернутого плана скоростей:
Вычисления по полученным формулам производим в положениях несущего механизма соответствующих построенному плану положений. Значения угла φ1 кривошипа ОА со стойкой ОС шарнирного четырех-звенника замеряем непосредственно на чертеже. Результаты расчетов заносим в таблицу 2.7.
Данные таблицы 2.7 в одном из положений механизма проверяем при помощи планов положений и скоростей затем используем для вычисления приведенного к валу кривошипа ОА его момента инерции (Jнес.пр –таблица 2.8).
Приращение кинетической энергии ΔТ кДж
Момент инерции приведенный к валу кривошипа ОА
где φ10 – угол поворота кривошипа ОА от своего начального положения соответствующего одному из крайних положений ползуна. Величина его вычислена как:
где - угол кривошипа ОА со стойкой ОС в начальном (крайнем) положении механизма.
Значения приведенного момента инерции пресса в различных его положениях определяем как:
где Jmax.пр – подлежащий определению приведенный к валу кривошипа ОА момент инерции масс махового колеса и рассматриваемый в виде суммы двух составляющих:
где - частично известная постоянная составляющая приведенного момента инерции передаточного механизма пресса
- переменная составляющая известная во всех положениях пресса (табл.2.8)
На листе I графической части проекта в осях ΔTi – ΔJпр.i устанавливаем вид диаграммы энергомасс (кривой Ti – Jпр.i) и положение начала координат позволяющее установить постоянные составляющие и To = Ti – ΔTi. Вид устанавливаем ориентируясь на то что во всех параллельных осях он одинаков а при определении координат начала исходим из необходимости обеспечить динамическую устойчивость выполнения технологического процесса глубокой вытяжки при помощи пресса с подобранными механизмами. Динамическую устойчивость обеспечиваем задаваясь коэффициентом неравномерности хода с помощью таблиц.
Момент инерции дополнительной массы маховика (Jmax) находим по величине Jпр*. Задачу решаем в следующем порядке:
Находим углы наклона касательных в створе которых диаграмма энергомасс видима из начала координат Ti – Jпр.i
где ; - масштабы осей ΔJi и ΔTi принятые при определении вида диаграммы энергомасс и а - средняя угловая скорость главного вала пресса т.е. кривошипа АО.
Т.о. получаем (рис.2.9):
Проводим касательные к диаграмме под полученными углами max и min находим отрезки О1K = 107мм и О1L = -108мм пересечения касательных с осью Δ. Отрезки используем для определения координат начала О системы T – Jпр.
Рис.2.8 Диаграмма энергомасс и ее параметры.
Записываем уравнения касательных как прямых проходящих в известных направлениях и известно пересекающих ось Δ:
Эти уравнения решаем совместно вычитая второе уравнение из первого получаем:
Подстановкой значения «x» в первое уравнение получаем:
у = -434782.6 0.006674 + 107 = -2794.75мм
Находим параметры дополнительно вводимой массы – маховика.
Из рис.2.9 видно: чтобы перейти от системы координат ΔT – ΔJпр к системе T – Jпр из начала О которой диаграмма энергомасс видна под углами max и min необходимо к переменной части момента инерции пресса прибавить постоянную часть
Jпр* = xy = 434782.60.066 = 28692.65
Часть этого момента инерции в виде приведенного момента инерции ротора электродвигателя и планетарной передачи в проектируемой схеме вытяжного пресса уже имеется.
вводим в виде дополнительной маховой массы – махового колеса. Принимая диаметр этого колеса Dmax = 10 м получаем массу обода
Большой вес и габариты маховика обуславливают необходимость переноса его на более быстроходный вал.
При оборудовании маховика на валу электродвигателя момент его инерции будет:
и при радиусе обода например R = 025м его масса окажется равной
Такой маховик сможет запасать кинетическую энергию не менее чем
4.3. Определение расхода материалов и энергии при запуске.
Из рис.2.8 максимальная энергия пресса запасаемая звеньями при его запуске составит:
Что соответствует подводимой из сети энергии.
В заключении найдем ориентировочную массу пресса.
На основании таблицы 2.6 ориентировочная масса подвижных звеньев:
а с учетом масс электродвигателя соединительных валов и деталей (принимаем mснд = 01m) станины (принимаем mстан = 12m)ориентировочная масса пресса окажется приблизительно равной:
Ориентировочно массу пресса оцениваем как .
Исследование схемы вытяжного пресса.
1. Определение закона установившегося движения
главного вала пресса.
Обобщенная координата – угол поворота кривошипа ОА а обобщенная скорость – угловая скорость этого кривошипа. При установившемся дви-
жении пресса обобщенную его скорость определяем из выражения кинетической энергии:
где кинетическая энергия звеньев пресса:
а приведенный момент инерции:
Ранее определены постоянные:
Переменные Δi и ΔJпр.i в каждом положении пресса берем из табл.2.8. Результаты вычислений заносим в таблицу 2.9.
С помощью таблицы 2.9 проверяем достоверность определения параметров маховика:
что приблизительно соответствует принятым значениям (ср = 1.65с-1; = 0.04).
По данным таблицы 2.9. строим график обобщенной скорости транспортера в функции его обобщенной координаты i = (φi) в пределах одного цикла установившегося движения
С помощью этого графика можем определить угловое ускорение кривошипа в том или ином его положении как:
и φ – масштабы по этим осям;
α – угол касательной к графику =(φ) в рассматриваемой точке.
В рассматриваемом 9-м положении пресса по полученной формуле
= 0.001; φ = 0.0348
2 Определение реакции в кинематических парах.
Для определения реакций в кинематических парах пресса воспользуемся методом кинетостатики согласно которому (принцип Даламбера) если ко всем действующим на звенья силам прибавить силы инерции то движение этих звеньев можно описать известными уравнениями статики. принцип Даламбера применяют к простейшим статически определенным кинема-тическим цепям степень подвижности которых W = 0. Отсоединение указанных цепей от машины ведут от рабочего звена последовательно при-ближаясь к валу приводного электродвигателя расчет которого ведут последним.
2.1. Определение ускорений.
Чтобы воспользоваться принципом Даламбера необходимо найти ускорения центров масс и угловые ускорения звеньев. В расчетном 9-м положении рассматриваемой кинематической цепи при установившемся
режиме движения пресса из табл.2.9 находим:
Далее для шестизвенного рычажного механизма OABCDE (рис. 2.7) на листе 2 строим план ускорений.
По теореме о вращательном движении кривошипа ОА ускорение точки А:
где нормальная составляющая ускорения:
в масштабе построения на чертеже изображено вектором с модулем:
направленным от точки А кривошипа ОА к центру его вращения О а тангенциальная составляющая
изображена вектором с модулем
направленным в соответствии с угловым ускорением перпендикулярно кривошипу ОА.
В соответствии с теоремой о плоском движении точки В в системе звена АВ и движении этой точки в системе кривошипа ВС имеем систему векторных равенств:
на чертеже откладываем в векторах и
направленных соответственно от точки В к точке А и от нее к точке С. В пересечении этих векторов находим точку “” а - вектор ускорения точки В.
Ускорение точки D находим по теореме о подобии строя ΔBCD с одинаковым направлением обхода вершин при обходе их по часовой стрелке.
Ускорение точки Е найдем по уравнению:
Вектор изображающий ускорение имеет длину:
и направление от точки Е к точке D.
Построенный план ускорений используем для определения ускорений центров масс и угловых ускорений звеньев:
2.2. Расчет сил инерции.
Имея ускорения находим силы инерции:
2.3 Определение реакций в кинематических парах.
Прикладываем силы инерции и моменты сил инерции к соответствующим звеньям противоположно ускорениям центров масс и угловым ускорениям этих звеньев. Кроме того в центрах масс прикладываем силы тяжести звеньев:
К рабочему органу прикладываем силу полезного сопротивления которая в соответствии с графиком полезных нагрузок в рассматриваемом положении механизма составляет:
К кривошипу ОА прикладываем ”уравновешивающую” силу действующую на колесо Z5 со стороны отбрасываемого колеса Z4 по линии зацепления зубьев колес составляющей угол 70 с линией их межосевого расстояния.
Для определения реакций в кинематических парах разбиваем несущий механизм пресса на структурные группы: два последних звена 4 и 5 группу звеньев 2 и 3 кривошип ОА с зубчатым колесом Z5 и кулачком.
Для определения модулей неизвестных реакций строим план сил:
Выбираем масштаб построения .
Составляем уравнение равновесия:
Замеряем плечи сил на чертеже: ; .
Неизвестные силы определяем из плана умножая соответствующие им отрезки на масштаб. Получим:
Рассматриваем группу состоящую из звеньев 2 и 3. Для того чтобы определить неизвестные силы и разложим эти силы на составля-ющие и составим уравнение равновесия в форме моментов для каждого из звеньев.
Плечи сил: ; ; ; ; берем с чертежа.
Для звена 2 уравнение моментов будет:
Далее рассматриваем кривошип ОА вместе с зубчатым колесом Z5 и кулачком. Усилие в зацеплении колес Z4 – Z5 действует под углом 20 к касательной делительных окружностей этих колес – в полюсе зацепления.
Уравнение равновесия в форме моментов относительно центра О вращени вала кривошипа АО:
Из планов сил также находим силы:
3. Определение мгновенного к.п.д.
Оценка интенсивности износа кинематических пар.
Мгновенный к.п.д. рассмотренного шестизвенника находим по формуле:
где - мгновенная (в рассматриваемом положении механизма) мощность сил трения в кинематических парах О А В С DE45 и Е50.
Предполагаем что вращательные кинематические пары выполнены как цилиндр в цилиндре с радиусом сопрягаемой поверхности rц = 0001м а материалы трущихся поверхностей выбраны так что коэффициент трения составляет = 015 (например сталь по стали при отсутствии смазки).
Тогда мгновенные мощности во вращательных кинематических парах можно определить как:
где а и в – угловая скорость звеньев
Vав – относительная скорость
Судя по мощности наибольшему износу в данном положении механизма подвергается поступательная кинематическая пара Е05 (NТрЕ05 = 274)
В рассматриваемом положении механизма полезная сила Fп.с. = 0 и ее мощность также равна нулю. Поэтому в указанном положении = 0.
Краткие выводы и результаты.
Выполнено первое приближение проекта пресса получены ориентировочные технико-экономические показатели которые подлежат защите и утверждению.
Эти показатели сводятся к следующим.
Производительность пресса (издчас)
Средняя скорость прямого хода (ммин)
Максимальное технологическое усилие (кН)
Потребляемая энергия (кВтчас)
Запасаемая энергия (кВтчас)
Ориентировочная масса (кг)
Список использованной литературы.
Методические указания по ТММ. Левитский Н.И. Солдаткин Е.П. М.: Высшая школа1983.
С.А.Попов Г.А.Тимофеев. Курсовое проектирование по теории механизмов и механике машин. М.: Высшая школа 1998.
И.И.Артобалевский. Теория механизмов и машин. М.: Наука 1975.
А.С.Касаткин М.В.Немцов. Электротехника. М.: Энергоиздат 1982.
Двигатели переменного тока мощностью от 006 до 100квт. Номенклатурный каталог НК 01401-90 М.: Информэлектро 1990.
Курсовое проектирование деталей машин. Справочное пособие. Часть I. А.В.Кузьмин и др. М.: Высшая школа 1982
Д.Л.Василенко Е.В.Волынец. Материалы XXXI СНТК. Новополоцк 2001.
А.А.Улитин. К синтезу коромыслово-ползунного присоеди-ненного механизма с основным и вспомогательным ходом ползуна XXXI. Новополоцк 2003.
В.Ф.Коренский А.А.Улитин. К выбору обобщенных координат.
Технико-экономическое обоснование выбора схемы
вытяжного пресса-автомата с выровненным ходом 6
2. Пояснения к выбору структуры пресса 7
3. Оценка энергопотребления проектируемого пресса-томата 8
Определение параметров схемы вытяжного пресса-автомата 9
1.1. Выбор электродвигателя и вида понижающей передачи 10
1.2. Синтез зубчатых колес 11
2. Выбор и синтез несущего механизма 15
3. Синтез кулачкового механизма 19
4. Динамический синтез кривошипно-коленного пресса 22
4.1. Расчет масс и моментов инерции звеньев механизма 22
4.2. Расчет приведенных моментов инерции 26
4.3. Определение расхода материалов и энергии при запуске 36
Исследование схемы вытяжного пресса 36
1. Определение закона установившегося движения главного 36
2. Определение реакции в кинематических парах 38
2.1. Определение ускорений 38
2.2. Расчет сил инерции 41
2.3. Определение реакций в кинематических парах 41
3. Определение мгновенного к.п.д. Оценка интенсивности износа
кинематических пар 44
Краткие выводы и результата 46
Список использованных литературных источников 47
расчетно-пояснительная записка.doc
2. Пояснения к выбору структуры пресса.7
3. Оценка энергопотребления проектируемого пресса-автомата.8
ОПРЕДЕЛЕНИЕ ПАРАМЕТРОВ СХЕМЫ ВЫТЯЖНОГО ПРЕСС-АВТОМАТА.10
1. РАСЧЕТ ПРИВОДА.10
1.1. Выбор электродвигателя и вида понижающей передачи.11
1.2. Синтез зубчатых колес12
2. Выбор и синтез несущего механизма.15
3. Синтез кулачкового механизма.19
4. Динамический синтез кривошипно-коленного пресса.21
4.1. Расчет масс и моментов инерции звеньев механизмов.21
4.2. Расчет приведенных моментов инерции.24
4.3. Определение расхода материалов и энергии при запуске.30
ИССЛЕДОВАНИЕ СХЕМЫ ВЫТЯЖНОГО ПРЕССА.31
1. Определение закона установившегося движения главного вала пресса.31
2 Определение реакции в кинематических парах.33
2.1. Определение ускорений.33
2.2. Расчет сил инерции.35
2.3 Определение реакции в кинематических парах.36
КРАТКИЕ ВЫВОДЫ И РЕЗУЛЬТАТЫ.38
СПИСОК ИСПОЛЬЗОВАННОЙ ЛИТЕРАТУРЫ.38
Машиностроение является ведущей отраслью народного хозяйства поскольку главная его цель - изготовление орудий производства. От совершенства орудий зависит производительность общественного труда.
В машиностроительном производстве широко используется прессование - технологический процесс обработки различных материалов давлением на прессах [1].
Прессованием получают заготовки и изделия из металлов пластмасс и других материалов; из металлов получают валы оси шкивы зубчатые колеса и т.д.
Если изделия имеют массовое применение - болты гайки капоты автомобилей и т.п.. для их изготовления применяют пресс-автоматы.
Вытяжка - операция листовой штамповки - свертка листовой заготовки между пуансоном и матрицей вытяжного пресса в полое изделие. Вытяжкой получают капоты автомобилей кабины тракторов фюзеляжи самолетов и т.п. изделия.
Кузнечно-прессовые машины занимают видное место в сфере машиностроительного производства а прессы для глубокой вытяжки - перспективный вид этих машин. В прессах как и других машинах с выровненным ходом используется принцип их конструирования при котором их назначение обеспечивается при использовании в механизмах звеньев с односторонним вращательным движением взамен таких из них. движение которых - вращательное но возвратное. Использование этого принципа позволяет повысить эксплуатационные характеристики работы машин за счет снижения маховых масс при увеличении энергоемкости их звеньев.
В настоящем проекте (по ТММиМ) рассматривается методические основы проектирования новых машин в ЕСКД на этапе «разработки технического предложения». Указанный этап - первый отклик на «Техническое задание» которое формирует руководство предприятий исходя из производства производимых ими промышленных изделий.
Учебное техническое задание (на проектирование) разработано на кафедре и в качестве исходного помещено на стр.1 настоящей записки.
Выполняя проект студент получает навыки выбора функциональных механизмов обеспечивающих работу задаваемой ему машины навыки вычисления размеров из звеньев оценки геометрических силовых и массовых характеристик машин анализа составляющих общего энергопотребления. Получаемые материалы дают достаточное представление о контурах зарождающейся машины необходимое для принятия обоснованного решения о выделении средств на продолжение проектирования
Технико-экономическое обоснование выбора схемы вытяжного пресса-автомата с выровненным ходом.
Прототип - известное техническое решение со свойствами близкими к заданным. В процессе проектирования машин он служит своеобразным ориентиром для получения решения с требуемыми свойствами. Цели проектирования достигают обоснованным изменением свойств выбранного прототипа.
Изучая рекомендованную и иную литературу в работе [2] находим схему вытяжного пресс-автомата с выровненным ходом которую в дальнейшем рассматриваем как прототип (рис. 1.1).
Пресс-автомат предназначен для изготовления деталей путем вытяжки из тонкого листового либо полосового металла с прижимом заготовки. Деформация заготовки осуществляется в матрице пуансоном установленным на ползуне 5 двухкривошипного коленного механизма состоящего из звеньев 1-2-3-4-5. На риса представлена диаграмма изменения усилий вытяжки в функции перемещения пуансона-ползуна 5.
Кривошип 1 приводится во вращение электродвигателем через ступенчатую передачу (рис. 1.1.б) включающую планетарную и простую ступень. Кулачковый механизм зажимного устройства прижимает деталь к столу во время обработки ее в матрице пуансоном и при выходе пуансона из матрицы кулачек посажен на вал кривошипа 1. График изменения аналогов ускорений изображен на рис. 1.1 .в.
Наличие в несущем рычажном механизме второго кривошипа 3 позволяет сократить до минимума количество звеньев с возвратным движением увеличить маховые массы и динамическую устойчивость работы пресс-автомата лишь за счет увеличения запаса кинетической энергии его звеньев.
2. Пояснения к выбору структуры пресса.
Структуру вытяжного пресса-прототипа принимаем за основу. В состав пресса включаем источник механического движения - простейший и наиболее распространенный нерегулируемый асинхронный электродвигатель 1 (рис. 1.2) несущий механизм 2 который обеспечит преобразование вращательного движения электродвигателя в требуемое возвратно-поступательное движение рабочего органа - пуансона 3 зубчатый механизм снижающий частоту вращения вала электродвигателя до частоты вращения входного звена несущего механизма при которой обеспечивается заданная производительность механизм прижима заготовок 5 состоящий из коромыслово-ползунного и кулачкового механизмов.
Для динамической устойчивости технологического процесса высадки снижения тепловых потерь электродвигателя 1 и в конечном счете для повышения общего к.п.д. процесса в его состав при необходимости будет введена дополнительная маховая масса 7 в виде махового колеса способного накапливать необходимую кинематическую энергию. В результате получаем предварительную блок-схему пресса которую и принимаем в качестве основы
электродвигатель приводной
рабочий орган-пуансон
механизм прижима заготовок
В дальнейшем гл.2 определим параметры выбранной схемы уточним расположение ее элементов.
3. Оценка энергопотребления проектируемого пресса-автомата.
Рассматриваемый пресс-автомат относится к технологическим машинам и основной расход энергии приходится на стадию установившегося движения.
За один полный цикл установившегося движения работа двигателя (Ада) расходуется на преодоление сил полезного () и вредного ()сопротивлений:
Поскольку работа других сил - потенциальных (веса упругости) и сил инерции за цикл установившегося движения равна нулю работу сил трения (.) учитываем с помощью к.п.д.( ). Тогда за цикл:
Работу полезных сил (Апс) находим интегрируя заданный график полезных нагрузок (рис. 1.1.а).
Интегрирование выполняем исходя из геометрического смысла интеграла как площади и
заключенной между осью относительных перемещений и кривой относительных нагрузок . Получаем:
где А1 А2 А3;- площади треугольника трапеции и треугольника в относительных единицах.
Искомая работа полезных сил:
Передаточный механизм от вала двигателя к рабочему органу-пуансону Е включает зубчатый и несущий рычажный механизмы. Поэтому его к.п.д.:
где и . - цикловые к.п.д. зубчатого и рычажного механизмов. Предполагая что зубчатый механизм будет включать плпнетарную и простую компенсирующую передачу его к.п.д. оцениваем как (13 стр322-333)
Предполагая далее что рычажный механизм будет шестизвенным (как у пресса-прототипа) его к.п.д. в первом приближении оцениваем как:
и работа двигателя за цикл установившегося движения должна составлять:
Затраты энергии на обработку одной детали составят:
а потребление ее из сети будет достигать:
где - к.п.д современных асинхронных электродвигателей(5стр.354)
Определение параметров схемы вытяжного пресс-автомата.
Привод служит источником механического движения звеньев пресса причем эти движения должны находиться в строгом соответствии с заданной производительностью Пр = 250. изделийчас. В рассматриваемом случае привод включает нерегулируемый короткозамкнутый асинхронный электродвигатель 1 (рис.1.2) и зубчатую передачу 4 согласующую обороты электродвигателя с оборотами кривошипа несущего механизма.
Будем считать что кривошип несущего механизма насажен на главный вал пресса т.е. за один его оборот будет изготовлена одна деталь. Тогда частота вращения кривошипа:
Продолжительность цикла
а цикловая мощность приводного электродвигателя должна превышать величину:
При данных мощности и величине производим синтез элементов привода механизма вытяжного пресса.
1.1. Выбор электродвигателя и вида понижающей передачи.
Из каталога электродвигателей Европейской серии ИР либо серии 4А выписываем в таблицу 2.1 параметры электродвигателей с ближайшей. большей мощностью по сравнению с
Марка электродвигателя
Номинальная мощность кВт
Передаточное отношение редуктора Up
Чтобы получить частоту вращения кривошипа несущего механизма пкр = 4167 обмин в каждом из этих случаев выбора электродвигателя привод должен содержать понижающую передачу с передаточным отношением:
Рассчитанные по этой формуле значения Unep также заносим в табл.2.1.
Из всех известных передач с постоянным передаточным отношением наименьшими габаритами весом наибольшей надежностью и к.п.д. обладают зубчатые передачи среди них прежде всего планетарные. Поэтому основные функции по преобразованию вращательного движения двигателя во вращательное кривошипа несущего механизма т.е. главного вала пресса будем возлагать на планетарный механизм. Т.к. однорядный планетарный механизм позволяет получить передаточное отношение ипл не более 9 а передаточное отношение простой одноступенчатой зубчатой передачи с прямыми зубьями обычно не превышает 4 161 стр.31) то для планетарного механизма выбираем более схожую схему (3стр40 рис2.1).
Анализируя данные таблицы 2.1 приходим к выводу что по основным параметрам (простота и вес конструкций пусковые характеристики двигателя и к.п.д.) для нашего случая является привод от двигателя марки 4A80А8Y3.
1.2. Синтез зубчатых колес
Схема зубчатой передачи представлена на рис.2.1.
Основу передачи составляет планетарный механизм передаточным отношением:
Для получения необходимого передаточного отношения устанавливаем подряд два таких механизма и однорядную передачу
Синтез (подбор чисел зубьев) планетарной ступени производим на основе условий:
oусловия выполнения требуемого передаточного отношения
oусловия правильности зацепления
Условие выполнения требуемого передаточного отношения:
и запишем условие соосности
Для выполнения условия соосности домножим на 2 и учитывая получим
По условию соседства определим число сателлитов
Чтобы механизм был уравновешен и не имел большой сложности принимаем К = 3. Проверяем условие сборки
Для однорядной передачи примем
Модуль зубчатых колес планетарного механизма определяем по максимальному моменту в этом механизме действующему на выходной его вал (вал водила).
Модуль (131 стр205):
Ближайший больший модуль первого ряда по СТСЭВ 310-76(6) m=4мм
Модуль зубчатых колес открытой передачи рассчитываем по моменту на валу кривошипа:
Учитывая повышенный износ при работе без смазки принимаем для открытой уравнительной передачи т4-5 = 6 мм.
Делительные диаметры колес определяем по формуле
Находим диаметр водила
2. Выбор и синтез несущего механизма.
Несущий механизм связан с рабочим органом и должен обеспечить ему возвратно-поступательное движение с достаточной величиной коэффициента производительности соответствии с входными данными получим:
Из простейших четверозвенных механизмов возвратно-поступательное движение рабочему органу могут обеспечить:
oкривошипно-ползунные;
Однако тангенсный механизм не может иметь кривошипы что необходимо если привод от электродвигателя осуществлять через зубчатую передачу синусный механизм имеет т)*=05 независимо от размеров звеньев а кривошипно-ползунный при > 0522 имеет неприемлемую величину интервала угла давления (у > 30°). Поэтому усложним схему несущего механизма - рассмотрим шестизвенную схему включающую два четырехзвенных механизма. По соображению долговечности ведущим пусть будет двухкривошипный шарнирный четырехзвенник позволяющий получить ( при приемлемых интервалах углов у) ц 055(5) на второй - аксиальный кривошипно-ползунный механизм способный преобразовать вращательное движение шарнирного четырехзвенника в поступательное инструмента (пуансона)
В результате получаем схему несущего механизма (рис.2.2) способную обеспечить требуемую величину максимально возможную долговечность (имеет лишь одну поступательную кинематическую пару) записать максимально возможную кинетическую энергию (нет звеньев являющихся коромыслами). Произведем геометрический синтез указанной схемы.
Отсоединим кривошипно-ползунный механизм СДЕ и изобразим его в двух крайних и одном промежуточном положении (кривошип СД перпендикулярен направляющей ползуна Е) в котором угол давления шатуна ДЕ на ползун Е принимает максимальное значение утах (рис.2.3).
Рассмотрим два крайних положения механизма СДоЕо и СД1Е1 между которыми перемещение ползуна Е составляет требуемую величину Н приходим к выводу что:
Анализируя далее промежуточное положение механизма СД1Е1 из прямоугольного треугольника СД1Е1 получаем:
где = 30 - максимально допустимый угол давления шатуна ДЕ на ползун Е.
Для присоединяющего шарнирного двухкривошипного четырехзвенника ОАВС (рис.2.3) входными параметрами служат: = 0554 и (принимаем)
Найдем другие размеры этого механизма.
Как следует из полученного в работе [ ] чтобы спроектировать двухкривошипный шарнирный четырехзвенник с заданной величиной необходимо с помощью приведенных в этой работе формул и таблиц найти размеры кривошипно-коромыслового механизма с теми же значениями интервала угла давления и относительных размеров звеньевзатем поставить полученный четырехзвенник на кривошип а его стойку сделать кривошипом. При этом крайние положения четырехзвенника наступают когда ведомый кривошип ВС совмещается со стойкой ОС.
Определяем угол перекрытия исходного и преобразованного механизмов:
Из ближайшей по 0 таблице (таблица для 0 = 20') выбираем четырехзвенник с оптимальным интервалом угла давления:
где границы интервала
Для выбранного интервала из таблицы выписываем значение угла размаха коромысла ВС шаг изменения при исследованиях полярного угла в круге единичного радиуса порядковый номер точки на дуге круга
Тогда значение полярного угла получаем таким
Вычисляем параметр Р выбора исходного четырехзвенника из таблиц
Находим относительные размеры звеньев преобразованного двухкривошипного четырехзвенника ОАВС (рис.2.2) с выровненным ходом:
Выберем абсолютным размер звена ВС.
Тогда длина относительной единицы (в м) составит:
а абсолютные размеры звеньев будут:
По конструктивным соображениям угол между направлениями стойки ОС шарнирного четырехзвенника ОАВС и направляющей ползуна Е присоединенного кривошипно-ползунного механизма принимаем:
Чтобы обеспечить синхронизацию работы механизмов присоединяем их в одном из крайних положений когда начинается рабочий ход. При этом у шарнирного четырехзвенника ОАВС кривошип ВС расположен на прямой ОС слева от шарнира С (рис.2.4) а кривошип DC расположен по направляющей ползуна Е сверху шарнира С. Очевидно угол излома рычага (ZBCD) принадлежащего шарнирному четырехзвеннику ОАВС и кривошип-но-ползунному механизму CDE должен составлять величину:
Полученные размеры используем при построении плана характерных положений несущего механизма. Построение производим методом засечек.
3. Синтез кулачкового механизма.
В описании прототипа указано что фазовый угол возвращения толкателя ер может быть равен фазовому углу удаления причем эти углы разделены между собой фазовым углом дальнего стояния При повороте кулачка на угол . механизм прижима заготовок фиксируется в одном из своих крайних положений прижимая заготовку к матрице.
Для привода механизма прижима заготовок к столу во время обработки изделий принимаем плоский кулачковый механизм с поступательным движением роликового толкателя со следующими параметрами:
ход толкателя h = 52мм;
фазовый угол удаления
фазовый угол дальнего выстоя
фазовый угол возвращения ;
допускаемый угол давления
Величины фазовых углов и работу прижимного механизма назначаем в соответствии с циклограммой работы механизма: во время прессования и в начале холостого хода пуансона осуществляется ближний выстой толкателя
Выбираем синусный закон движения толкателя на фазе удаления ( в соответствии с описанием прототипа) и с равномерноубывающим ускорением на фазе возвращения.
Из таблицы 4.3. [8]выписываем формулы для определения функций положения толкателя и передаточных функций 1 -го и 2-го порядков
Рассчитываем эти функции на фазе удаления где толкатель движется по закону синусоиды
На фазе возвращения выходное звено движется по закону с равноубывающим ускорением
Поскольку в нашем случаев разбиты на 6 равных частей то указанные функции в пределах каждой из фаз будут определены в 6-ти равностоящих точках.
Результаты расчетов заносим в таблицу 2.5.
Задачу об определении минимального радиуса при проектировании кулачка решаем графическим методом в координатах S-S’ .
Для устранения самопересечения профиля а также из условий равенства износа кулачка и ролика радиус последнего выбираем из двух соотношений:
4. Динамический синтез кривошипно-коленного пресса.
Динамический синтез пресса проводим с целью повышения его общего к.п.д. путем приведения в «норму» теплового излучения обмоток приводного электродвигателя за счет равномерности вращения внутри цикла.
Задачу решаем подбором и перераспределением масс звеньев введением при необходимости дополнительной маховой массы в виде махового колеса с постоянным моментом инерции.
Предварительно произведем учет инертных свойств звеньев уже задействованных в рассматриваемом прессе механизмов.
4.1. Расчет масс и моментов инерции звеньев механизмов.
Инертные свойства звеньев характеризуют показатели массы (при поступательном движении) и момента инерции (при вращательном движении).
В первом приближении можем принять что по длине рычагов массы распределены равномерно что интенсивность распределения q = 30 кгм 7 стр.240 и что зубчатые колеса - сплошные диски с шириной зависящей от межосевого расстояния как
где = 02 - 05 6180 представляет собой коэффициент ширины зуба.
При этом центры масс рычагов располагаются по их серединам массы определяются как
моменты инерции звеньев относительно их центров масс находятся как 11
а относительно оси вращения (для вращающихся масс) как
Массы зубчатых колес определяем через делительные диаметры d и межосевые расстояния aw по формуле
которая при плотности материала р=78 103 кгм3 (сталь чугун) и при принятом = 025 для облегчения вычислений предварительно должна быть приведена к виду
Моменты инерции колес относительно оси вращения определяем через их массу и делительный диаметр как для однородных дисков:
Результаты расчетов заносим в таблицу 2.6.
Оценку динамических характеристик прочих деталей пресса производим следующим образом
Массу пуансона Е вместе с перемещающим его ползуном оцениваем как
Массу толкателя кулачкового механизма ориентировочно оцениваем как
где ( =05м - длина толкателя замеренная по чертежу.
Массу кулачка mkи момент инерции JK оцениваем по среднему радиусу:
Массу водила планетарной ступени редуктора находим с помощью формулы:
где ширину водила принимаем равной ширине смонтированного в нес сателлита Z2 т.е
а момент инерции JH как для сплошного диска:
Момент инерции ротора электродвигателя определяем по справочнику:
Динамические характеристики остальных движущихся звеньев ходовой винт валы ролик кулачкового механизма и т.п. из-за малых масс либо скоростей точек считаем пренебрежимо малыми и далее не учитываем.
Полученные данные заносим в таблицу 2.6 и используем при последующем динамическом синтезе машины.
эаметра и его обозначение
Длина рычага диаметр колеса (м)
Момент инерции относительно оси вращения кг-м2
Момент инерции относительно центра масс кг-м2
4.2. Расчет приведенных моментов инерции.
Инертные свойства машин и механизмов характеризуют приведенной массой либо приведенным моментом инерции в зависимости от того линейным или угловым является перемещение звена приведения. Приведенным к звену момент инерции масс звеньев механизмов вычисляют как сумму приведенных масс звеньев и их моментов инерции на квадраты передаточных функций в движениях этих звеньев относительно звена приведения.
Приведенный момент инерции механизма приводим к главному валу машины умножая его величину на квадрат передаточной функции от звена приведения к указанному валу.
Т.о. приведенный к валу кривошип ОА несущего механизма - принимаем его за главный вал вытяжного пресс-автомата - и момент инерции масс подвижных звеньев можем представить как сумму приведенных моментов инерции следующих механизмов узлов и деталей:
Ротора приводного электродвигателя:
Зубчатой передачи (рис. 2.1):
Приведенного к валу кривошипа момента инерции механизма прижима заготовки
Указанный момент влияет на движение вытяжного пресса лишь в периоды движения толкателя кулачкового механизма - на фазах удаления и возвращения. Причем на концах этих фаз Jnp = 0 т.к. передаточная функция от толкателя к кулачку т.е. к валу кривошипа ОА при этом равна нулю.
для фазы возвращения
Приведенного к валу кривошипа ОА момента инерции несущего механизма (рис.2.7):
где передаточная функция в движении ползуна 5 относительно кривошипа ОА может быть вычислена как:
В шарнирном четырехзвеннике ОАВС:
Отсюда угол передачи
В кривошипно-ползунном присоединенном механизме CDE
Функцию положения шатуна DE определяем двумя параметрами - углом давления
и координатой Y ползуна
Вычисления по полученным формулам производим в положениях несущего механизма соответствующих построенному плану положений. Значения угла ф кривошипа ОА со стойкой ОС шарнирного четырехзвенника замеряем непосредственно на чертеже. Результаты расчетов заносим в таблицу 2.7.
Данные таблицы 2.7 в одном из положений механизма проверяем при помощи планов положений и скоростей затем используем для вычисления приведенного к валу кривошипа ОА его момента инерции (JHecnp-таблица 2.8).
Положение кривошипа 0A
обобщенной координаты
Приращение кинетической энергии кДж
Момент инерции приведенный к валу кривошипа ОА кг ■ м2
где - угол поворота кривошипа ОА от своего начального положения соответствующего одному из крайних положений ползуна. Величина его вычислена как:
угол кривошипа ОА со стойкой ОС в начальном (крайнем) положении механизма
Значения приведенного момента инерции пресса в различных его положениях определя
где Jmax.np - подлежащий определению приведенный к валу кривошипа ОА момент инерции масс махового колеса и рассматриваемый в виде суммы двух составляющих:
На листе I графической части проекта в осях - A-Jnp устанавливаем вид диаграммы энергомасс (кривой Т - Jnp.Вид устанавливаем ориентируясь на то что во всех параллельных осях он одинаков а при определении координат начала исходим из необходимости обеспечить динамическую устойчивость выполнения технологического процесса глубокой вытяжки при помощи пресса с подобранными механизмами. Динамическуюустойчивость обеспечиваем задаваясь коэффициентом неравномерности хода C помощью таблиц 5.12 работы [4].
Момент инерции дополнительной массы маховика (Jmax) находим по величине Jnp*. Задачу решаем в следующем порядке:
Находим углы наклона касательных в створе которых диаграмма энергомасс видима из начала координат Т; - Jnp j
Проводим касательные к диаграмме под полученными углами инаходим отрезки ОК = 37мм и OL = -55мм пересечения касательных с осью Т. Отрезки используем для определения координат начала О системы Т-J
Рис.2.8 Диаграмма энергомасс и ее параметры.
Записываем уравнения касательных как прямых проходящих в известных направлениях и известно пересекающих ось Т:
Эти уравнения решаем совместно вычитая второе уравнение из первого получаем:
Подстановкой значения «х» в первое уравнение получаем:
Находим параметры дополнительно вводимой массы - маховика.
Из рис.2.9 видно: чтобы перейти от системы координат к системе из начала О которой диаграмма энергомасс видна под углами и необходимо к переменной части момента инерции пресса прибавить постоянную часть Jnp' = х = 145.841 кг м2
Часть этого момента инерции в виде приведенного момента инерции ротора электродвигателя и планетарной передачи в проектируемой схеме вытяжного пресса уже имеется.
Остальную часть:вводим в виде дополнительной маховой массы - махового колеса. Принимая диаметр этого колеса Dmax = 10 м получаем массу обода
Большой вес и габариты маховика обуславливают необходимость переноса его на более быстроходный вал.
При оборудовании маховика на валу электродвигателя момент его инерции будет:
и при радиусе обода например R =01м его масса окажется равной
Такой маховик сможет запасать кинетическую энергию не менее чем
4.3. Определение расхода материалов и энергии при запуске.
Из рис.2.8 максимальная энергия пресса запасаемая звеньями при его запуске составит:
Что соответствует подводимой из сети энергии
Исследование схемы вытяжного пресса.
1. Определение закона установившегося движения главного вала пресса.
Обобщенная координата - угол поворота кривошипа ОА а обобщенная скорость - угловая скорость этого кривошипа. При установившемся движении пресса обобщенную его скорость определяем из выражения кинетической энергии:
где кинетическая энергия звеньев пресса:
приведенный момент инерции:
Ранее определены постоянные:
С помощью таблицы 2.9 проверяем достоверность определения параметров маховика:
что приблизительно соответствует принятым значениям
По данным таблицы 3.1 строим график обобщенной скорости транспортера в функции его обобщенной координаты в пределах одного цикла установившегося движения .
С помощью этого графика можем определить угловое ускорение кривошипа в том или ином его положении как
где и - приращения координат по осям
угол касательной к графику в рассматриваемой точке. В рассматриваемом 9-м положении пресса по полученной формуле
2 Определение реакции в кинематических парах.
Для определения реакций в кинематических парах пресса воспользуемся методом кинетостатики согласно которому (принцип Даламбера) если ко всем действующим на звенья силам прибавить силы инерции то движение этих звеньев можно описать известными уравнениями статики принцип Даламбера применяют к простейшим статически определенным кинематическим цепям степень подвижности которых W = 0. Отсоединение указанных цепей от машины ведут от рабочего звена последовательно приближаясь к валу приводного электродвигателя расчет которого ведут последним.
2.1. Определение ускорений.
Чтобы воспользоваться принципом Даламбера необходимо найти ускорения центров масс и угловые ускорения звеньев. В расчетном 9-м положении рассматриваемой кинематической цепи при установившемся режиме движения пресса из табл.2.9 находим:
Далее для шестизвенного рычажного механизма OABCDE (рис. 2.7) на листе 2 строим план ускорений.
По теореме о вращательном движении кривошипа ОА ускорение точки А:
где нормальная составляющая ускорения:
в масштабе построения на чертеже изображено вектором mi с модулем направленным от точки А кривошипа ОА к центру его вращения О а тангенциальная составляющая изображена вектором направленным в соответствии с угловым ускорением е перпендикулярно кривошипу ОА
В соответствии с теоремой о плоском движении точки В в системе звена АВ и движении этой точки в системе кривошипа ВС имеем систему векторных равенств:
на чертеже откладываем в векторах
направленных соответственно от точки В к точке А и от нее к точке С. В пересечении этих векторов находим точку "в " а пв - вектор ускорения точки В.
Ускорение точки D находим по теореме о подобии строя Aecd со ABCD с одинаковым направлением обхода вершин при обходе их по часовой стрелке.
Ускорение точки Е найдем по уравнению:
т.к мало на плане его не изображаем
Построенный план ускорений используем для определения ускорений центров масс и угловых ускорений звеньев:
2.2. Расчет сил инерции.
Имея ускорения находим силы инерции:
Т.к значения моментов инерции пренебрежительно малы их в расчете не учитываем.
2.3 Определение реакции в кинематических парах.
Прикладываем силы инерции и моменты сил инерции к соответствующим звеньям противоположно ускорениям центров масс и угловым ускорениям этих звеньев. Кроме того
К рабочему органу прикладываем силу полезного сопротивления которая в соответствии с графиком полезных нагрузок в рассматриваемом положении механизма составляет:
К кривошипу ОА прикладываем "уравновешивающую" силу действующую на колесо Z5 со стороны отбрасываемого колеса Z4 по линии зацепления зубьев колес составляющей угол 20* с горизонтальной линией
Для определения реакций в кинематических парах разбиваем несущий механизм пресса на структурные группы: два последних звена 4 и 5 группу звеньев 2 и 3 кривошип ОА с зубчатым колесом Zs и кулачком.
Для определения модулей неизвестных реакций строим план сил:
Силы инерции на плане не изображаем из-за их малого значения
Рассматриваем группу состоящую из звеньев 2 и 3. Для того чтобы определить неизвестные силы F12 и F30 разложим эти силы на составляющие и составим уравнение равновесия в форме моментов для каждого из звеньев.
Краткие выводы и результаты.
Выполнено первое приближение проекта пресса получены ориентировочные технико-экономические показатели которые подлежат защите и утверждению.
Эти показатели сводятся к следующим.
Производительность пресса (издчас)' - 250
Средняя скорость прямого хода (ммин)- 139
Ход пуансона (м)- 018
Максимальное технологическое усилие (кН)- 38
Потребляемая энергия (кВт*час)- 28 10-2
Запасаемая энергия (кВт*час)- 3 10-2
Список использованной литературы.
«Курсовое проектирование по теории механизмов и машин» под общей редакцией Г.Н. Девойно Минск «Высшая школа» 1986 г.
В.А. Юдин Л.В. Петрокас «Теория механизмов и машин» Москва «Высшая школа» 1977 г.
Э.А. Горов С.А. Гайдай «Типовой лабораторный практикум по теории механизмов и машин» Москва «Машиностроение» 1990 г.
«Теория механизмов и машин» К.В. Фролов С.А. Попов Москва «Высшая школа» 1987 г.
И.И. Артоболевский «Теория механизмов и машин» Москва «Наука» 1975г.
Лист1.cdw

Электродвигатель короткозамкнутый асинхронный 4А80А8УЗ
Редуктор планетарный U
Передача зубчатая одноступенчатая U
Механизм несущий рычажный
Кулачковый механизм(синтез)
График полезных нагрузок
График работы полезных сил
Зубчатый механизм(схема)
Циклограмма работы станка
Диаграмма энергомасс
КП ТММ кафедра механики
Окончательная блок-схема вытяжного пресс-автомата
Рабочий орган (пуансон)
Механизм прижима заготовок (кулачковый)
Титульник 2.doc
УО «Полоцкий государственный университет»
Кафедра теоретической механики
Расчётно – пояснительная записка
К курсовому проекту по теории механизмов
Машин и манипуляторов на тему:
“Разработка основы технического предложения
На вытяжной пресс – автомат с выровненным ходом”
Учреждение образования
«Полоцкий государственный университет»
По теории механизмов машин и манипуляторов на тему:
«Разработка основы технического предложения на вытяжной пресс – автомат с выровненным ходом».
студент группы 04 - ТМ