Совершенствование производственно-технической базы ООО РАО Наровчатское Наровчатского района с модернизацией стенда для разборки-сборки двигателей грузовых автомобилей




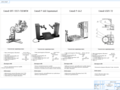
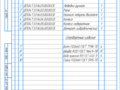
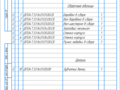
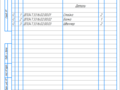
- Добавлен: 25.01.2023
- Размер: 5 MB
- Закачек: 3
Описание
Совершенствование производственно-технической базы ООО РАО Наровчатское Наровчатского района с модернизацией стенда для разборки-сборки двигателей грузовых автомобилей
Состав проекта
![]() |
![]() |
![]() |
![]() ![]() ![]() ![]() |
![]() ![]() ![]() ![]() |
![]() ![]() ![]() ![]() |
![]() ![]() ![]() ![]() |
![]() ![]() ![]() ![]() |
![]() ![]() ![]() ![]() |
![]() ![]() ![]() ![]() |
![]() ![]() ![]() ![]() |
![]() ![]() ![]() |
![]() ![]() ![]() ![]() |
![]() ![]() ![]() ![]() |
![]() ![]() ![]() ![]() |
![]() ![]() ![]() ![]() |
![]() ![]() ![]() ![]() |
![]() ![]() ![]() ![]() |
![]() |
![]() ![]() ![]() |
![]() ![]() ![]() |
![]() ![]() ![]() |
![]() ![]() ![]() |
![]() ![]() ![]() |
![]() ![]() ![]() |
![]() ![]() ![]() |
![]() ![]() ![]() |
![]() ![]() ![]() |
![]() ![]() ![]() |
Дополнительная информация
Спецификация лебедка.spw

ДП.047.33.16.01.01.00.
ДП.047.33.16.01.02.00.
Вал барабана в сборе
ДП.047.33.16.01.03.00.
Вал-шестерня в сборе
ДП.047.33.16.01.04.00.
ДП.047.33.16.01.05.00.
ДП.047.33.16.01.06.00.
ДП.047.33.16.01.07.00.
Ручка лебедки в сборе
ДП.047.33.16.01.00.08
Общий вид.cdw

Максимальная грузоподъемность лебедки
Технические требования
* Размер для справок
Неуказанные предельные отклонения размеров по 14 квалитету
Усилие затяжки болтов 10 Н
Проверить устройство после сборки
ДП.047.33.16.00.00.00.
Стенд для разборки-сборки
двигателей модернизированный
Спецификация рама.spw

Рама.cdw

Сварные швы по ГОСТ 14806-80.
*Размер для справок.
ДП.047.33.16.02.00.00.
Эконом. проекта1.cdw

План мастерской.cdw

Дефектовочно-комплектовочный
Ремонта электрооборудования
Административно-бытовые помещения
Инструментально-раздаточная кладовая
Вспомогательные помещения
Б - грузовые автомобили
- направление грузопотока
- потребитель электроэнергии.
вал1.cdw

Неуказанные предельные отклонения размеров по 14 квалитету
Несоостность отверстий: 0
ДП.047.33.16.01.02.01
Сталь 45 ГОСТ 1050-88
Лебедка.cdw

Неуказанные предельные отклонения размеров по 14 квалитету
Усилие затяжки болтов 10 Н
Проверить устройство после сборки
ДП.047.33.16.01.00.00.
ОБЗОР.CDW

вал2.cdw

Коэффициент смещения
Степень точности по ГОСТ 1643-81
взаимного положения
разноименных профилей зубьев
Делительный диаментр
Прочие справочные данные
ДП.047.33.16.01.03.01
Сталь 45 ГОСТ 1050-88
Неуказанные предельные отклонения размеров по 14 квалитету
барабан.cdw

АХД-2010.cdw

ГП-2010.cdw

Коэффициент застройки Кз = 0
Коэффициент озеленения Ко = 0
Контрольно пропускной пункт
Склад масел наружный
Автозаправочная колонка
Ремонтная мастерская
Профелактический корпус
Производственный корпус
Административное здание
- направление грузопотока;
- зеленые насаждения.
зубчатый венец.cdw

Коэффициент смещения
Степень точности по ГОСТ 1643-81
взаимного положения
разноименных профилей зубьев
Делительный диаментр
Прочие справочные данные
ДП.047.33.16.01.00.08
Сталь 45 ГОСТ 1050-88
Некрулость отверстий по квалитету Н7
Спец ВИД ОБЩИЙ.cdw

Стенд для разборки-сборки
двигателей модернизированный
ДП.047.33.16.00.00.00.ВО
ДП.047.33.16.01.00.00.СБ
ДП.047.33.16.02.00.00.СБ
ДП.047.33.16.03.00.00.СБ
ДП.047.33.16.04.00.00.СБ
ДП.047.33.16.05.00.00.СБ
Стенд для разборки-сборки двигателей модернизированный
Механизм поворота двигателя
Болт М20х60 ГОСТ 7798-70
ДП.047.33.16.06.00.00.СБ
Домкрат гидравлический
Гайка М20х6Н ГОСТ 5915-70
Аннотация.doc
Для повышения производительности работ по разборке-сборке ДВС автомобилей в дипломном проекте была предложена конструкция модернизированного стенда проведены необходимые прочностные расчеты.
Так же были рассмотрены вопросы по охране труда и окружающей среды рассчитано искусственное освещение производственного корпуса и объем отходов промывочной жидкости масел и бытовых отходов.
Проведённые расчеты экономической эффективности предлагаемой конструкции стенда показал целесообразность разработанного проекта.
Экономичка-2010.doc
1 Определение затрат на конструкторскую разработку
Затраты на изготовление стенда для разборки–сборки ДВС находятся [16]
Сц.кон = Ск.д. + Со.д. + Сп.д. + Зп + Свм + Ноп(5.1)
где Сц.кон – стоимость изготовления конструкции руб.;
Ск.д. – стоимость изготовления корпусных деталей рам каркасов руб.;
Со.д. – стоимость изготовления оригинальных деталей руб.;
Зп – оплата труда производственных рабочих занятых на изготовлении и сборке конструкции руб.;
Сп.д. – цена покупных деталей изделий узлов руб.;
Свм – стоимость вспомогательных материалов (2 4 % от затрат на основные материалы) руб.;
Ноп – общепроизводственные накладные расходы на изготовление конструкции руб.
Затраты на изготовление корпусных деталей:
Ск.д = См.к. + Зпк(5.2)
где См.к. – стоимость материала израсходованного на изготовление корпусных деталей руб.;
Зпк – зарплата (с начислениями) производственных рабочих занятых на изготовлении корпусных деталей руб.
См.к. = Цз.к × Qк.д.(5.3)
где Qк.д – масса заготовки кг;
Цз.к – цена 1 кг металла руб.
Раму стенда изготавливаем из сортового проката . Рама состоит из конструктивных элементов: двух балок поперечных балки продольной двух опора общей массой 61 кг (см. спецификацию ДП.047.33.16.02.00.00.СБ «Графическая часть»).
Таким образом – Цз.к = 1065 кг.
См.к. = 1065 × 61 = 649650 руб.
Зпк = Зо + Зд + Ссоц
где Тизг – средняя трудоемкость изготовления рамы (сварочные работы) чел–ч
Сч – часовая тарифная ставка руб.ч. Сч = 42 руб.ч. (по среднему разряду).
Зо = 25 × 42 = 105 руб.
Зд = (Кд – 1) × Зо(5.5)
где Кд – коэффициент учитывающий доплаты к основной зарплате Кд = 1125.
Зд = (113 – 1) × 105 = 1313 руб.
Ссоц = Rсоц × (Зо + Зд) = 0261 × (105 + 1313) = 30 руб.
Зпк = 105 + 1313 + 3083 = 14896 руб.
Ск.д = 64965 + 14896 = 664546 руб.
Затраты на изготовлении оригинальных деталей руб.:
Со.д. = Зпо + См.о.(5.6)
где Зпо – зарплата производственных рабочих занятых на изготовлении оригинальных деталей руб.;
См.о –стоимость материала заготовок для изготовления оригинальных деталей руб.
См.о = Цз.о × Qо.д(5.7)
где Цз.о – цена 1 кг материала оригинальных деталей руб.;
Qо.д – масса заготовок оригинальных деталей кг.
Данные по затратам связанным с изготовлением оригинальных деталей приведены в таблице 5.1.
Стоимость покупных деталей (домкрат – 2000 руб. болт М20 – 4по 21 руб. гайка М20 – 4по 15 руб. шайба 20 – 8по 095 руб. шайба пружинная 20 – 4по 12 руб.) для стенда составляет Сп.д. = 20268 руб.
См = 664546 + 594588 + 20268 = 1461813 руб.
Основная зарплата производственных рабочих занятых на сборке конструкции руб.:
Зпс = Зо + Зд + Ссоц
где Тсб – нормативная трудоемкость сборки элементов конструкции чел–ч.
Таблица 5.1 – Затраты на изготовление оригинальных деталей
Цена 1 кг материала руб.
Количество деталей шт.
Стоимость материала руб.
Затраты на изготовление руб.
где Кс – коэффициент учитывающий соотношение между полным и оперативным временем сборки Кс = 11;
tСБ – трудоемкость сборки составных частей конструкции чел–ч.
Тсб = 11 × 45 = 495 чел–ч.
Зо = 495 × 42 = 2079 руб.
Зд = 013 · Зо = 013 · 2079 = 2599 руб.
Ссоц = 0261 · (Зо + Зд) = 0261 · (2079 + 2599) = 6104 руб.
Зпс = 2079 + 2599 + 6104 = 29493 руб.
Стоимость вспомогательных материалов:
Свм = 004 · См = 004 · 1461813 = 46437 руб.
Общепроизводственные накладные расходы на изготовление конструкции:
Ноп = 001 · Спр · RОП(5.10)
где Спр – основная заработная плата производственных рабочих занятых на сборке и изготовлении конструкции руб.;
RОП – процент общепроизводственных расходов (62%).
Ноп = 001 · 330384· 62 = 535221 руб.
Сц.кон = 664546 + 594588 + 20268 + 29493 + 46437 + 535221 = 2072965 руб.
2 Определение экономической эффективности
предлагаемой разработки
Внедрение в производство модернизируемой конструкции стенда позволит снизить затраты труда рабочих при выполнении разборочно–сборочных операций технологического процесса ремонта автомобильных ДВС. А именно уменьшит трудоемкость установки и снятия ремонтируемых двигателей на стенд. При существующей технологии ремонта подразумевается установка двигателя тремя работниками – двое поднимают третий закрепляет. Предлагаемая конструкция позволит ту же работу выполнить одному работнику. Продолжительность данного технологического перехода – То = 008 ч. таким образом для постановки ДВС на имеющийся стенд необходимо затратить трудоемкость
tб = 024 ч. а на модернизируемый те же tп = 008 ч. что при годовой программе ремонтов в 2750 двигателей (см. раздел «2 Определение годового объема работ по ремонту и техническому обслуживанию») дает Тб = 660 чел-ч. и
Тп = 220 чел-ч. соответственно. Обеспечение загрузки производственного участка потребным количеством автомобилей планируется проводить за счет привлечения для ремонта техники соседних хозяйств и частного населения.
Затраты на заработную плату рассчитываются по формуле:
Для существующего варианта:
Для внедряемого варианта:
Затраты на амортизацию находятся по формуле
где – балансовая стоимость соответственно стенда применяющегося при существующей технологии ремонта и внедряемого;
– процент амортизационных отчислений = 125 %.
Затраты на ТО и ремонт находятся по формуле
где Р – процент отчислений на ремонт и ТО Р = 10 %.
Итого эксплуатационные затраты
где – процент прочих прямых затрат = 10 % или коэффициент = 11.
Снижение прямых эксплуатационных затрат
Годовые приведённые затраты находятся по формуле
Снижение приведённых затрат
Годовой экономический эффект
Срок окупаемости внедряемой установки
где ΔК – дополнительные материально–денежные затраты руб.
К = Соб.кон. = 2072965 руб.
Т = 2072965 2370722 = 087 года
Результаты проведённых расчётов сведём в таблицу 5.3.
Таблица 5.3 – Экономическая эффективность модернизированного стенда
Балансовая стоимость стенда тыс. руб.
Затраты на модернизацию стенда тыс. руб.
Затраты труда чел-ч.
Снижение трудоёмкости от внедрения модернизированного стенда %
Годовые эксплуатационные затраты тыс. руб.
Снижение эксплуатационных затрат %
Годовая экономия эксплуатационных затрат тыс. руб.
Срок окупаемости дополнительных капитальных вложений лет
Данные таблицы показывают что в результате внедрения модернизированного стенда для разборки-сборки двигателей снижается трудоёмкость проведения ремонтных работ на 67 % в год. В результате этого эксплуатационные издержки сокращаются на 408% годовая экономия эксплуатационных затрат составит 237 тыс. руб. а срок окупаемости дополнительных материально-денежных затрат 087 года.
Техпроцесс.DOC
6.1 Краткая характеристика детали. Выбор и определение размеров заготовки
Вал из стали 45 ГОСТ 1050-88 предназначен для передачи крутящего момента от рукоятки к барабану лебедки. Он представляет собой деталь ступенчатой формы с участками ø35 40 34 мм. С двух торцов имеются осевые отверстия с резьбой М18 на глубину 62 мм. (см. карту эскизов 20.1.41). Количество деталей – 1 штука.
Материалом для изготовления рычага является горячекатанная сталь круглого профиля обычной точности по ГОСТ 2590-71 (НВ = 197 sв = 750 МПа).
Максимальный диаметр вала – 40 мм общая длина – 232 мм. Тогда LD = 232 40 = 58. Диаметр заготовки составит 45 мм. В соответствии с ГОСТ 2590-71 прокат такого диаметра выпускается с предельными отклонениями: верхнее +03; нижнее –05. Припуск на черновое подрезание торцов составляет 4 мм; на чистовое – 2 · 12 = 24 мм. Тогда общая длина заготовки должна быть: L = 232 + 4 + 2 · 12 = 2384 мм.
Предельные отклонения по 14 квалитету составляют 1 мм.
Масса заготовки определяется следующим образом.1 м стали ø45 мм составляет 10617 кг тогда масса прутка длиной 6914 мм будет равна
mз = 10617 · 02384 » 253 кг.
6.2 Выбор технологического маршрута изготовления вала оборудования и технологической оснастки
Для изготовления вала необходимо выполнить токарную (005) и слесарную (010) операции.
Токарная операция выполняется на станке 1К62; технологическая оснастка: установка и закрепление заготовки осуществляется в трехкулачковом самоцентрирующем патроне – патрон 7100-009 ГОСТ 2675-80; резец проходной упорный с пластиной из твердого сплава – резец 2103-0057 Т15К6 ГОСТ 18880-73; резец проходной отогнутый правый с пластиной из твердого сплава – резец 2102-0055 Т15К6 ГОСТ 18880-73; средства измерения – штангенциркуль ШЦ-2-160-005 ГОСТ 166-80.
Слесарная (010) операция выполняется на слесарном верстаке ОРГ- 1468 01-060; технологическая оснастка: установка и закрепление детали осуществляется в слесарных тисках с ручным приводом – тиски 7827-0257 ГОСТ 4045-75Е для нарезания резьбы метчиком используется вороток; режущий инструмент – метчик М18×20-Н3 ОСТ 2-И50-1-73.
6.3 Выбор режимов резания и нормирование
токарной операции – 005
Норма времени на любую операцию определяется по формуле:
Тн = То + Тв + Тд + (Тп.з.n) мин.
где То – основное время мин.;
Тв – вспомогательное время мин.;
Тд – дополнительное время мин.;
Тп.з. – подготовительно-заключительное время мин.;
n – количество деталей в партии n = 10 шт.
Подготовительно-заключительное время назначается один раз на всю операцию в данном случае: Тп.з. = 9 мин.
Переход 1. Установить и снять заготовку (см. карту эскизов 20.1.41 к операции 005 1й лист).
Вспомогательное время на переход зависит от способа установки характера выверки и массы заготовки. Тву = 038 мин.
Переход 2. Подрезать торец предварительно. Глубина резания t = 2 мм число рабочих ходов i = 1. Подача выбирается в зависимости от характера обработки: Sт = 015 025 ммоб.
Согласно паспортным данным станка принимается Sф = 02 ммоб.
В зависимости от глубины резания и подачи назначается скорость резания Vт= 220 м·мин-1. Данное значение скорости резания корректируется в зависимости от марки обрабатываемого материала (Км) характера заготовки и состояния ее поверхности (Кх) марки режущей части резца (Кмр) и применения охлаждения (Кох). Назначаем Км = 10; Кх = 09; Кмр = 10; Кох =10. Корректирование заключается в умножении на поправочные коэффициенты:
Vр = Vт · Км · Кх · Кмр · Кох = 220 · 10 · 09 · 10 · 10 = 198 м·мин-1
По расчетной скорости резания определяется расчетная частота вращения шпинделя:
nр = (Vр · 1000)p · D
где D – максимальный диаметр заготовки на данном переходе мм.
nр = (198 · 1000)(314 · 45) = 1401 мин-1.
Согласно паспортным данным станка принимается nф = 1250 мин-1.
Вспомогательное время на переход ТВ2 = 02 мин.
Основное время определяется по формуле:
То = (L · i)(nф · Sф) мин
где L – расчетная длина хода режущего инструмента мм;
nф – фактическая частота вращения заготовки мин-1;
Sф – фактическая подача режущего инструмента ммоб.
где D – диаметр заготовки мм;
У – величина врезания и перебега мм.
D = 45 мм; У = 35 мм; поскольку при подрезке торца перебега нет то принимается У = 175 мм.
ТО2 = [(452 + 175) · 1](1250 · 02) = 01 мин.
Переход 3. Подрезать торец окончательно.
t = 12 мм. Sт = 015 025 ммоб.; Sф = 02 ммоб.; Vт = 220 м·мин-1; Vр = 220 · 09 = 198 м·мин–1;
nр = (198 · 1000)(314 · 45) = 1401 мин-1 ; nф = 1250 мин-1; i = 1.
ТВ3 = 02 мин. ТО3 = (452 + 1)(1250 · 02) = 01 мин.
Переход 4. Сверлить центровое отверстие ø315 мм выдерживая размер 1.
Переход осуществляется на частоте вращения предыдущего перехода n = 1250 мин-1; подача ручная; t = 3152 = 16 мм.
ТВ4 = 04 мин. ТО4 = 008 мин.
Переход 5. Сверлить осевое отверстие ø16 мм выдерживая размер 2.
Переход осуществляется на частоте вращения предыдущего перехода n = 1250 мин-1; подача ручная; t = 162 = 8 мм.
ТВ5 = 06 мин. ТО5 = 02 мин.
Переход 6. Переустановить заготовку (см. карту эскизов 20.1.41.).
Переход 7. Точить поверхность выдерживая размеры 3 и 4.
Припуск снимается за 1 рабочий ход тогда глубина резания
t = Zм2 · SТ = 04 05 ммоб.; Sф = 04 ммоб.; VТ = 149 м·мин-1; Vр = 149 · 09 = 1341 м·мин-1; nр = (1341 · 1000)(314 · 45) = 1220 мин-1; nф = 1200 мин-1.
Поскольку ни врезания ни перебега нет то У = 7 мм
ТО7 = [(216 +35) · 1](1200 · 04) = 457 мин.
Переход 8. Точить поверхность выдерживая размеры 5 и 6.
t = Zм2 · SТ = 04 05 ммоб.; Sф = 04 ммоб.; VТ = 149 м·мин-1; Vр = 149 · 09 = 1341 м·мин-1; nр = (1341 · 1000)(314 · 40) = 1334 мин-1; nф = 1200 мин-1.
ТО8 = [(16 +35) · 1](1200 · 04) = 04 мин.
Переход 9. Точить проточку на поверхности выдерживая размеры 7 и 8.
ТО8 = [(34 +35) · 1](1200 · 04) = 01 мин.
Переход 10. Снять фаску 1545°.
Переход выполняется на частоте вращения предыдущего перехода подача ручная глубина резания переменная.
ТВ10 = 007 мин.; ТО10 = 008 мин.
Переход 11. Переустановить заготовку.
Переход 12. Подрезать торец предварительно.
Содержание и режимы перехода соответствуют переходу 2.
Переход 13. Подрезать торец окончательно.
Содержание и режимы перехода соответствуют переходу 3.
Переход 14. Сверлить центровое отверстие ø315 мм выдерживая размер 1.
Переход 15. Сверлить осевое отверстие ø16 мм выдерживая размер 2.
Переход 16. Точить поверхность выдерживая размеры 9 и 10.
Припуск на обработку составляет d = 45 – 35 = 10 мм. Количество рабочих ходов SТ = 03 04 ммоб.; Sф = 04 ммоб.; VТ = 175 м·мин-1; Vр = 175 · 09 = 1575 м·мин-1; nр = (1575 · 1000)(314 · 45) = 1115 мин-1; nф= 1000 мин-1.
У = 2; поскольку перебега нет то У = 1 мм.
ТО16 = [(16 + 1) · 1](1000 · 04) = 004 мин.
Переход 17. Снять фаску 1545°.
ТВ17 = 007 мин.; ТО17 = 008 мин.
Вспомогательное время на операцию определяется из выражения:
где ТВi – вспомогательное время i-го перехода.
ТВ = 038 + 02 + 04 + 007 +06+ 038 + 05 + 05 + 05 + 007+01+02+02+02+05+007 = 487 мин.
Основное время на операцию определяется из выражения:
где ТОi – основное время на выполнение i-го перехода.
ТО = 01 + 01 + 008 + 0 2 + 04 + 01 + 008+01+01+01+004+008 = 148 мин.
Дополнительное время на операцию:
ТД = (ТОп · К)100 мин
где ТОп – оперативное время мин.;
ТОп = ТВ + ТО = 487 + 148 = 635 мин;
К – процентное соотношение дополнительного времени к оперативному для токарной операции К = 8 %.
ТД = (635 · 8)100 = 05 мин.
Тшт = ТВ + ТО + ТД = 487 + 148 + 05 = 685 мин
Норма времени на операцию:
ТН = 148 + 487 + 05 + (910) = 775 мин.
6.4 Нормирование слесарной операции – 010
Подготовительно-заключительное время на операцию Тп.з. = 5 мин.
Переход 1. Установить закрепить и снять заготовку (см. карту эскизов 20.1.41 к операции 010).
Переход 24. Нарезать резьбу М6 в отверстии метчиком
Переход 3. Переустановить заготовку
Норма времени на выполнение слесарной операции:
ТН = (2 · 02 + 141) + 5 = 681 мин.
СОДЕРЖАНИЕ.doc
2 Анализ показателей производственно-технической
ОПРЕДЕЛЕНИЕ ГОДОВОГО ОБЪЕМА РАБОТ ПО РЕМОНТУ И ТЕХНИЧЕСКОМУ ОБСЛУЖИВАНИЮ
1 Количество технических воздействий для автомобилей
2 Определение трудоёмкости по ремонту и ТО автомобилей
3 Планировка производственного корпуса. Расчеты площадей
оборудования количества рабочих
КОНСТРУКТОРСКАЯ ЧАСТЬ
1 Обзор существующих конструкций стендов
для разборки-сборки двигателей
2 Устройство и принцип работы модернизируемого стенда для разборки и сборки двигателей
3 Расчет ручной лебедки
4 Расчет стопорного устройства
5 Расчет устойчивости стенда
6 Проектирование технологического процесса изготовления
6.1 Краткая характеристика детали. Выбор и определение размеров заготовки
6.2 Выбор технологического маршрута изготовления вала оборудования и технологической оснастки
6.3 Выбор режимов резания и нормирование токарной операции – 005
6.4 Нормирование слесарной операции – 010
БЕЗОПАСНОСТЬ ЖИЗНЕДЕЯТЕЛЬНОСТИ НА ПРОИЗВОДСТВЕ
1 Расчет искусственного освещения
2 Экологическая безопасность
3 Безопасность жизнедеятельности в чрезвычайных ситуациях
ЭКОНОМИЧЕСКАЯ ЭФФЕКТИВНОСТЬ ПРОЕКТА
1 Определение затрат на конструкторскую разработку
2 Определение экономической эффективности предлагаемой разработки
БЖД.doc
В процессе выполнения работ по техническому обслуживанию возможно действие на работающих следующих опасных и вредных производственных факторов:
движущиеся машины и механизмы;
незащищенные подвижные части стационарно оборудования и движущихся машин и механизмов;
недостаточно защищенное оборудование работающее под давлением;
повышенное значение напряжения в электрической цепи замыкание которой может произойти через тело человека;
недостатки освещенности рабочей зоны.
В связи с этим устанавливаются общие требования безопасности к производственным процессам производственным помещениям состоянию техники в соответствии с ГОСТ 12.3.002-95.
Безопасность производственных процессов должна быть обеспечена:
применением передовой технологии производства а также порядком обслуживания производственного оборудования;
рациональной организацией рабочих мест;
размещением производственного оборудования;
профессиональным отбором и обучением работающих;
применением средств защиты работающих;
включением требований безопасности в технологическою документацию;
контролем за выполнением требований безопасности.
Основная задача техники безопасности на любом производстве заключается в создании таких условий труда которые предупреждали бы и исключали причины вызывающие несчастные случаи. Для этого совершенствуют конструкции машин и механизмов на рабочих местах машинах оборудовании устанавливают защитные и предохранительные устройства и приспособления.
Одно из основных условий соблюдения правил техники безопасности – твердое знание их и умение применять на своем рабочем месте.
Проведение комплекса организационных и профилактических мероприятий непосредственное руководство а также контроль за выполнением работ осуществляет инженер по технике безопасности.
На производственных участках ответственными являются руководители производственных участков.
Инженерно-технические работники и другие специалисты проводят инструктаж по технике безопасности со всеми работниками независимо от квалификации и стажа рабочих. Инструктаж проводится во всех бригадах независимо от степени опасности производственных процессов.
К работе с оборудованием используемым на предприятии допускают лиц изучивших инструкцию знающих правила безопасности и гигиены труда. Необходимо осматривать и очищать электрооборудование один раз в три месяца и проводить испытание изоляции корпуса один раз в год; при осмотрах проверять изоляцию проводов и т.д. Если при осмотре электрооборудования обнаруживают неисправности то немедленно устраняют их. Запрещается работать на токоведущих частях электрооборудования и в местах движущихся механизмов не отключив и не сняв напряжение со щита управления.
Категорически запрещается работать при неисправном оборудовании и отсутствии ограждений регулировать смазывать очищать оборудование при работающих механизмах. Выполняя регулировочные и ремонтные работы отключают общий рубильник на силовом щите и вывешивают плакат ''Не включать – работают люди''.
Моющие и дезинфицирующие вещества снабжают сертификатом с указанием способа применения хранят в закрытой таре на складе. Обслуживающий персонал должен иметь допуск для работы с моющими и дезинфицирующими веществами и спецодежду. Не допускается применять растворы без надлежащего сертификата и указаний по способу применения привлекать для их изготовления лиц не имеющих допуска и медицинского разрешения.
Шум возникающий в процессе работы оборудования должен быть на более 60дБ в зоне постоянного пребывания работающих. Для предотвращения аварий и травм обслуживающего персонала необходимо ежемесячно проверять затяжку гаек болтов винтов заземление. Большое внимание на предприятии уделяется мерам противопожарной безопасности. В соответствии с ГОСТом 12.1.004-76 ССБТ пожарная безопасность обеспечивается системой предотвращения пожаров и организационными мероприятиями. Цеха оборудованы противопожарными щитами. Расстояние между корпусами соответствует противопожарным требованиям.
Для успешной борьбы с пожарами работники предприятия должны знать причины их возникновения и выполнять правила пожарной безопасности. Чтобы предупредить пожар в помещении необходимо строго соблюдать противопожарный режим правильную эксплуатацию тепловых агрегатов и установок машин и электрооборудования приборов освещения и отопления.
Помещения для ремонта техники а также территорию вокруг них необходимо содержать в чистоте и порядке. Особое внимание следует обращать в зимнее время на очистку от снега путей эвакуации людей и транспорт. Ко всем зданиям должен быть свободный доступ. Нельзя делать к существующим зданиям различные пристройки навесы. Вороты и двери на путях эвакуации должны открываться только наружу.
Важнейшее условие обеспечения пожарной безопасности – правильное использование ГСМ в зависимости от среды помещения в котором они должны эксплуатироваться.
Ответственность за противопожарную безопасность в мастерских возложена на руководителя предприятия и начальников цехов.
Безопасность жизнедеятельности обеспечивает социальную защищенность рабочих на производстве. Задача службы охраны труда состоит в том чтобы обеспечить надежную защиту работающих от воздействия опасных и вредных производственных факторов. Организационные вопросы по безопасности жизнедеятельности определяются законами законодательными актами и нормативно-технической документацией. Кроме технической документации работники инженерно-технической службы и специализированных звеньев ежегодно проходят обучение по технике безопасности с последующей проверкой знаний специальной комиссией. При проведении курсового обучения по технике безопасности используют инструкции плакаты и другие наглядные пособия а также показывают правила и приемы отдельных операций по использованию техники и технического обслуживания при хранении машин.
Общие вопросы техники безопасности на производственном участке
Техническое обслуживание ремонт и проверка технического состояния АТС производится на специально отведенных местах (постах) оснащенных необходимыми оборудованием устройствами приборами приспособлениями и инвентарем.
АТС направляемые на посты технического обслуживания ремонта и проверки технического состояния должны быть вымыты очищены от грязи и снега. Постановка АТС на посты осуществляется под руководством ответственного работника (мастера начальника участка контролера технического состояния АТС и т.п.).
Въезд АТС в производственное помещение станций и пунктов государственного технического осмотра (СГТО ПГТО) и их постановку на рабочие посты проверки должны осуществлять контролеры технического состояния АТС которые должны иметь удостоверения водителя АТС соответствующей категории.
После постановки АТС на пост необходимо затормозить его стояночным тормозом выключить зажигание (перекрыть подачу топлива в автомобиле с дизельным двигателем) установить рычаг переключения передач (контроллера) в нейтральное положение под колеса подложить не менее двух специальных упоров (башмаков). На рулевое колесо должна быть повешена табличка с надписью "Двигатель не пускать - работают люди!". На АТС имеющих дублирующее устройство для пуска двигателя аналогичная табличка должна вывешиваться и у этого устройства.
Присутствие людей в полосе движения АТС при въезде выезде или маневрировании в производственном помещении запрещается.
При обслуживании автомобиля на подъемнике (гидравлическом электромеханическом) на пульте управления подъемником должна быть вывешена табличка с надписью "Не трогать – под автомобилем работают люди!".
В рабочем (поднятом) положении плунжер гидравлического подъемника должен надежно фиксироваться упором (штангой) гарантирующим невозможность самопроизвольного опускания подъемника.
В помещениях технического обслуживания с поточным движением АТС обязательно устройство сигнализации (световой звуковой или др.) своевременно предупреждающей работающих на линии обслуживания (в осмотровых канавах на эстакадах и т.д.) о моменте начала перемещения АТС с поста на пост.
Включение конвейера для перемещения АТС с поста на пост разрешается только после включения сигнала (звукового светового) диспетчером или специально выделенным работником назначаемым приказом по организации. Посты должны быть оборудованы устройствами для аварийной остановки конвейера.
Пуск двигателя АТС на постах технического обслуживания или ремонта разрешается осуществлять только водителю-перегонщику бригадиру слесарей или слесарю назначаемым приказом по организации и прошедшим инструктаж при наличии у них удостоверения водителя АТС.
Перед проведением работ связанных с проворачиванием коленчатого и карданного валов необходимо дополнительно проверить выключение зажигания (перекрытие подачи топлива для дизельных автомобилей) нейтральное положение рычага переключения передач (контроллера) освободить рычаг стояночного тормоза.
После выполнения необходимых работ АТС следует затормозить стояночным тормозом.
Работники производящие обслуживание и ремонт АТС должны обеспечиваться соответствующими исправными инструментами приспособлениями а также средствами индивидуальной защиты (СИЗ).
При необходимости выполнения работ под АТС находящимся вне осмотровой канавы подъемника эстакады работники должны обеспечиваться лежаками.
При вывешивании части автомобиля прицепа полуприцепа подъемными механизмами (домкратами талями и т.п.) кроме стационарных необходимо вначале подставить под неподнимаемые колеса специальные упоры (башмаки) затем вывесить АТС подставить под вывешенную часть козелки и опустить на них АТС.
Ремонт замена подъемного механизма кузова автомобиля-самосвала самосвального прицепа или долив в него масла должны производиться после установки под поднятый кузов специального дополнительного упора исключающего возможность падения или самопроизвольного опускания кузова.
При ремонте и обслуживании верхней части автобусов и грузовых автомобилей работники должны быть обеспечены подмостями или лестницами-стремянками. Применять приставные лестницы не разрешается.
Убирать рабочее место от пыли опилок стружки мелких металлических обрезков разрешается только с помощью щетки.
При работе на поворотном стенде (опрокидывателе) необходимо предварительно надежно укрепить на нем АТС слить топливо из топливных баков и жидкость из системы охлаждения и других систем плотно закрыть маслозаливную горловину двигателя и снять аккумуляторную батарею.
При снятии и установке деталей узлов и агрегатов массой 30 кг мужчинами и 10 кг – женщинами (до 2 раз в час) и 15 кг – мужчинами и 7 кг – женщинами (более 2 раз в час) необходимо пользоваться подъемно-транспортными механизмами.
При снятии и установке агрегатов и узлов которые после отсоединения от АТС могут оказаться в подвешенном состоянии нужно применять страхующие (фиксирующие) устройства и приспособления (тележки-подъемники подставки канатные петли крюки и т.п.) исключающие самопроизвольное смещение или падение снимаемых и устанавливаемых агрегатов и узлов.
– работать лежа на полу (земле) без лежака;
– выполнять какие-либо работы на автомобиле (прицепе полуприцепе) вывешенном только на одних подъемных механизмах (домкратах талях и т.п.) кроме стационарных;
– выполнять какие-либо работы без подкладывания козелков (упора или штанги под плунжер) под вывешенный АТС (автомобиль прицеп полуприцеп) на передвижные (в том числе канавные) подъемники и подъемники не снабженные двумя независимыми приспособлениями одно из которых - страховочное препятствующие самопроизвольному опусканию их рабочих органов в соответствии с требованиями государственного стандарта;
– оставлять АТС после окончания работ вывешенными на подъемниках;
– подкладывать под вывешенный автомобиль (прицеп полуприцеп) вместо козелков диски колес кирпичи и другие случайные предметы;
– снимать и ставить рессоры на автомобили (прицепы полуприцепы) всех конструкций и типов без предварительной разгрузки от массы кузова путем вывешивания кузова с установкой козелков под него или раму АТС;
– проводить техническое обслуживание и ремонт АТС при работающем двигателе за исключением отдельных видов работ технология проведения которых требует пуска двигателя;
– поднимать (вывешивать) АТС за буксирные приспособления (крюки) путем захвата за них тросами цепями или крюком подъемного механизма;
– поднимать (даже кратковременно) грузы масса которых превышает указанную на табличке подъемного механизма;
– снимать устанавливать и транспортировать агрегаты при зачаливании их стальными канатами или цепями при отсутствии специальных устройств;
– поднимать груз при косом натяжении тросов или цепей;
– работать на неисправном оборудовании а также с неисправными инструментами и приспособлениями;
– оставлять инструменты и детали на краях осмотровой канавы;
– работать с поврежденными или неправильно установленными упорами;
– пускать двигатель и перемещать АТС при поднятом кузове;
– производить ремонтные работы под поднятым кузовом автомобиля-самосвала самосвального прицепа без предварительного его освобождения от груза и установки дополнительного упора;
– проворачивать карданный вал при помощи лома или монтажной лопатки;
– сдувать пыль опилки стружку мелкие обрезки сжатым воздухом.
Перед снятием узлов и агрегатов систем питания охлаждения и смазки АТС когда возможно вытекание жидкости необходимо предварительно слить из них топливо масло и охлаждающую жидкость в специальную тару не допуская их проливания.
Автомобили-цистерны для перевозки легковоспламеняющихся взрывоопасных токсичных и т.п. грузов а также резервуары для их хранения перед ремонтом необходимо полностью очистить от остатков вышеуказанных продуктов.
Работник производящий очистку или ремонт внутри цистерны или резервуара (емкости) из-под этилированного бензина легковоспламеняющихся и ядовитых жидкостей должен быть обеспечен спецодеждой шланговым противогазом спасательным поясом со страховочным тросом; вне емкости должны находиться два специально проинструктированных помощника.
Шланг противогаза должен быть выведен наружу через люк (лаз) и закреплен с наветренной стороны.
К поясу работника внутри емкости прикрепляется страховочный трос свободный конец которого должен быть выведен через люк (лаз) наружу и надежно закреплен. Помощники находящиеся наверху должны наблюдать за работником держать страховочный трос страхуя работающего в емкости.
Ремонтировать топливные баки заправочные колонки резервуары насосы коммуникации и тару из-под легковоспламеняющихся и ядовитых жидкостей можно только после полного удаления их остатков и обезвреживания.
Работы по техническому обслуживанию и ремонту холодильных установок автомобилей-рефрижераторов должны выполняться в соответствии с инструкциями завода-изготовителя.
Для перегона АТС на посты проверки технического состояния обслуживания и ремонта включая посты проверки тормозов должен быть выделен специальный водитель (перегонщик) или другой работник назначаемый приказом по организации.
В зоне технического обслуживания и ремонта АТС не допускается:
– протирать АТС и мыть их агрегаты легковоспламеняющимися жидкостями (бензином растворителями и т.п.);
– хранить легковоспламеняющиеся жидкости и горючие материалы кислоты краски карбид кальция и т.д. в количествах превышающих сменную потребность;
– заправлять АТС топливом;
– хранить чистые обтирочные материалы вместе с использованными;
– загромождать проходы между осмотровыми канавами стеллажами и выходы из помещений материалами оборудованием тарой снятыми агрегатами и т.п.;
– хранить отработанное масло порожнюю тару из-под топлива и смазочных материалов.
Разлитое масло или топливо необходимо немедленно удалять с помощью песка или опилок которые после использования следует ссыпать в металлические ящики с крышками устанавливаемые вне помещения.
Использованные обтирочные материалы (промасленные концы ветошь и т.п.) должны немедленно убираться в металлические ящики с плотными крышками а по окончании рабочего дня удаляться из производственных помещений в специально отведенные места.
Настоящие Правила должны соблюдаться при техническом обслуживании или ремонте АТС проводимых вне организации.
Указание мер безопасности при подъемно-транспортировочных операциях агрегатов трансмиссии предлагаемым устройством.
К обслуживанию подъемно-транспортировочной тележки для обслуживания агрегатов трансмиссии допускаются лица прошедшие специальный инструктаж а так же ознакомившиеся с ее техническим описанием и требованиями по использованию вспомогательного подъемно-транспортного оборудования.
Необходимо соблюдать следующие требования:
Перед подъемно-транспортировочными операциями необходимо произвести мойку автомобиля в местах доступа к агрегатам трансмиссии.
Перед установкой двигателя на стенд необходимо проверить правильность расположения упоров.
Так как в конструкции стенда имеются вращающиеся части то необходимо держать руки стопы и одежду на безопасном расстоянии от движущихся частей.
При работе необходимо пользоваться перчатками.
Так как данный стенд работает и эксплуатируется в помещении необходимо произвести расчет искусственного освещения.
1 Расчет искусственного освещения.
Общая мощность освещения может быть определена по удельной мощности или по мощности светового потока.
Определим общую мощность освещения по удельной мощности для производственного корпуса АТП [21]:
где Po – общая мощность освещения Вт;
Py – удельная мощность освещения = 24 Втм2.
Po = 24 · 216 = 5184 Вт.
Определим количество ламп накаливания:
n = 5184 200 = 2592 шт.(4.2)
Для участков АТП значения сведем в таблицу 4.1.
Таблица 4.1 – Распределение электросветильников по участкам
Наименование производственных зон и участков
Дефектовочно-комплектовочный
Ремонта электрооборудования
Для производственных помещений принимаем площадь оконного проема равную 20 × 18 = 36 м2.
Должно выполняться следующее условие для производственных помещений [21]:
So Sn ³ 16 для остальных помещений So Sn ³ 18.
Расчет произведем на примере зоны ТО и ТР:
So = Sn 6 = 80 6 = 133 м2.(4.3)
Определим необходимое количество окон на данном участке:
Расчет для остальных участков сведем в таблицу.
Таблица 4.2 – Распределение окон по участкам
Наименование участка СПТО
2 Экологическая безопасность
Ключевыми проблемами обеспечения экологической безопасности в транспортных хозяйствах являются защита от загрязнения атмосферного воздуха водных объектов земельных ресурсов и недр защита от транспортного шума и вибраций предупреждение экологических последствий чрезвычайных ситуаций и катастроф обеспечение экологической безопасности населения снижение ущерба природным ресурсам в первую очередь биологическим сохранение качества природной среды обеспечивающее процессы саморегулирования и самоочищения от вредных для нее веществ.
Организационно-правовые мероприятия включают формирование нового эколого-правового мировоззрения эффективную реализацию государственной экологической политики создание современного экологического законодательства и нормативно-правовой базы экологической безопасности а также меры государственного административного и общественного контроля за выполнением функций по охране природы.
Архитектурно-планировочные мероприятия обеспечивают совершенствование планирования всех функциональных зон города (промышленной селитебной – предназначенной для жилья транспортной санитарно-защитной зоны отдыха и др.) с учетом инфраструктуры транспорта и дорожного движения разработку решений по рациональному землепользованию и застройке территорий сохранению природных ландшафтов озеленению и благоустройству.
Конструкторско-технические мероприятия позволяют внедрить современные инженерные санитарно-технические и технологические средства защиты окружающей среды от вредных воздействий на предприятиях и объектах транспорта технические новшества в конструкции подвижного состава.
Эксплуатационные мероприятия осуществляются в процессе эксплуатации транспортных средств и направлены на поддержание их состояния на уровне заданных экологических нормативов за счет технического контроля и высококачественного обслуживания.
Перечисленные группы мероприятий реализуются независимо друг от друга и позволяют достичь определенных результатов. Но комплексное их применение обеспечит максимальный эффект.
К настоящему времени в Российской Федерации создана основная правовая и нормативная база по вопросам экологии в транспортно-дорожном комплексе состоящая из правовых документов международного и общероссийского значения.
К основными отходами проектируемой зоны относятся: использованные технологические материалы (промывочная жидкость и масла) и бытовые отходы.
Масса отходов промывочной жидкости определяется по формуле:
где Мпр – общее количество промывочной жидкости Мпр=13 тг;
к – содержание донного осадка в промывочной жидкости к = 10%.
Определим объем отходов промывочной жидкости по формуле:
где g – объемный вес тм3
Определим массу отходов отработанных масел по формуле:
где к – норма расхода и применяемость смазочных масел к = 3120 л;
n – удельный показатель образования вторичного сырья n = 50%
Определим объем отходов отработанных масел:
где g – объемный вес равен 09 тм3
Определим массу бытовых отходов:
где N – количество человек работающих на предприятии за год;
n – норма накопления отходов на 1 человека кггод
Определим объем бытовых отходов:
Промышленные отходы полученные со всех участков ПТБ АТП такие как технические жидкости отработанные масла и т.д. необходимо тщательно собирать и хранить в металлической таре на специально оборудованной для этого площадке не допуская тем самым загрязнения ими ливневых вод и почвы. Их следует периодически вывозить в места утилизации или переработки вторичного сырья.
3 Безопасность жизнедеятельности в чрезвычайных ситуациях
Предприятие занимается перевозками разнообразных грузов используя имеющийся подвижной состав производит его техническое обслуживание и ремонт.
Подъездные пути к производственным подразделениям предприятия асфальтированные.
Электроснабжение осуществляется от электросетей с. Потодеево.
Водоснабжение обеспечивается из центрального водопровода.
Газоснабжение осуществляется по воздушному трубопроводу.
Из стихийных бедствий наблюдаемых на территории расположения предприятия могут иметь место: пожары ураганы сильные морозы.
От быстроты ликвидации и предупреждения последствий чрезвычайных ситуаций может зависеть не только производственно материальные аспекты но и здоровье работающего персонала. Поэтому предприятие работает в соответствии с программой Государственной системы предупреждения чрезвычайных ситуаций которая включает в себя:
обеспечение надежного контроля за состоянием потенциально опасных объектов;
создание резервных материально-технических средств медицинских средств и других материалов;
обеспечение высокой готовности органов управления сил и средств к действию в чрезвычайных ситуациях;
проведение аварийно-восстановительных и других работ по ликвидации последствий чрезвычайных ситуаций.
ЗАКЛЮЧЕНИЕ.doc
Технический проект в себя включает:
Технологический расчет участков производственного корпуса который позволил определить необходимые площади участков перечень необходимого оборудования и количество обслуживающего персонала.
Расчет мероприятий по модернизации стенда для разборки-сборки ДВС автомобилей которая заключается в оснащении стенда ручной лебедкой позволяющей проводить установку закрепление и ремонтные работы с максимально возможными удобствами и простотой что сказывается на производительности труда работников.
Технологический процесс на изготовление вала барабана лебедки модернизируемого стенда и рабочую документацию позволяющую изготовить детали стенда силами самого хозяйства.
Технико-экономическую оценку проекта которая показала что для реализации проекта необходимы дополнительные капитальные вложения на модернизацию стенда в размере 207 тыс. руб. При этом годовая экономия составит 237 млн. руб. а срок окупаемости дополнительных капитальных вложений – 087 года.
АХД.doc
Административно-хозяйственным центром является село Потодеево Наровчатского р-на которое удалено от областного центра города Пенза на 132 км. а от районного на 8 км.
Климат хозяйства умеренно-континентальный. Средняя годовая температура воздуха равна 350С. Наивысшая средняя температура наблюдается в июле +1990С наименьшая – в январе -120С. Продолжительность периода с температурой выше +50С составляет 142 дня. Средняя продолжительность безморозного периода составляет 122 дня продолжительность вегетационного периода – 133 дня. Общее количество осадков в районе 471 522 мм максимум осадков приходится на летние месяцы минимум осадков наблюдается в зимний период. Среднегодовая относительная влажность – 67%.
Хозяйство расположено в лесостепной зоне для которой характерно присутствие широколиственных лесов и лугово-степной растительности. Естественная травяная растительность характеризуется большим разнообразием.
В почвенном покрове преобладающее место занимают черноземные почвы тяжело- и среднесуглинистого механического состава. Почвы хозяйства в значительной степени подвержены водной и ветровой эрозии.
Таким образом природно-климатические условия в целом являются благоприятными для развития производства.
2 Анализ показателей производственно-технической
Согласно отчетной документации предприятие за 2007 2009 годы производственно-техническая деятельность соответствует специфике предприятия.
Таблица 1.1 - Основные производственные показатели
Отношение 2009 г. к 2007 г. %
Реализованная продукция тыс. руб.
Себестоимость всей реализованной продукции тыс. руб.
Общая земельная площадь га.
в т.ч. сельскохозяйственные угодья
Стоимость основных производственных средств на конец года тыс. руб.
Продолжение табл.1.1
Среднегодовая численность рабочих занятых в с.-х. производстве чел.
Данные таблицы 1.1 показывают что реализованная продукция в 2009 году по сравнению с 2007 г. увеличилась на 297% или на 7117 тыс. руб себестоимость реализованной продукции снизилась на 4% что в переводе на денежные средства составило 1836 тыс.руб.. В 2007 г. прибыль хозяйства составила 2533 тыс. руб а в 2009 г. была получена прибыль в 10507 тыс. руб. Стоимость основных производственных средств стремительно увеличиваясь составила в 2009 году 45895 тыс. рублей что на 2091 % больше чем в 2007 году. Это связано с привлечением новой дорогостоящей техники в хозяйство. Среднегодовая численность работников занятых в сельскохозяйственном производстве в 2009 году составила 81 человек то есть сократилась по сравнению с 2007 г. на 26 человек что обусловлено стабильной работой организации и рациональным использованием рабочей силы.
Успех производства во многом зависит от обеспеченности хозяйства основными ресурсами. По данным таблицы 1.2 оценим данные показатели.
Таблица 1.2 – Показатели работы автопарка предприятия
Среднесписочное число автомобилей шт.
Суммарный тоннаж автопарка т
Средняя грузоподъемность автомобиля т
Среднесуточный пробег км
Коэффициент выпуска на линию
Коэффициент использования пробега
Коэффициент технической готовности
Коэффициент использования грузоподъемности
Сменная выработка т·кмсмена
Производительность труда шофера т·кмч
Объем перевозок тыс. т
Годовой грузооборот т·км
Продолжение табл. 1.2
Общий пробег автомобилей тыс. км
Себестоимость транспортных работ руб.т·км
В отчетном году наметилась тенденция к увеличению таких показателей как коэффициент использования пробега который в 2009 году составил 089; коэффициент выпуска на линию – 05; коэффициент технической готовности – 094; коэффициент использования грузоподъемности – 085 что связано главным образом с приобретением в 2008 году трех автомобилей и увеличением сменной выработки.
Таблица 1.3 – Наличие энергетических ресурсов
Суммарная мощность двигателей кВт
Общая численность водителей чел.
Энерговооруженность труда кВтчел.
Средняя мощность двигателя кВт
Энергетические мощности за последний год выросли на 200 кВт. Среднегодовая численность рабочих также возросла за счет принятия в штат водителей на приобретенные автомобили. Энерговооруженность на предприятии увеличилась незначительно на 4 кВтчел.
Таблица 1.4 – Затраты на техническое обслуживание и ремонт машин
Затраты на содержание подвижного состава тыс. руб.
Затраты на текущий ремонт тыс. руб.
Затраты на ТО тыс. руб.
Анализируя предыдущие таблицы видно что подвижной состав работает с максимальной загрузкой. Поэтому в этих условиях для ремонта и обслуживания создана на предприятии соответствующая техническая база. На территории сформирован достаточно мощный технический центр в котором проводятся все виды обслуживания и ремонта техники. При этом немалое количество производственных процессов механизировано что положительно сказывается на эксплуатации автомобилей.
Таблица 1.5 – Уровень использования автопарка
Выполненный объем работ т·км
Выработка на 1 автомобиль т·км
Отработано нормо-смен на 1 автомобиль
Всего израсходовано топлива т
Расход топлива на 100 км кг
Анализируя данные таблицы 1.4 можно сделать вывод о том что в настоящее время производить капитальный и текущий ремонт автомобилей в необходимом объёме становится маловозможным из-за тяжелого материального положения. Однако на содержание и обслуживание имеющихся автомобилей осуществляется в достаточном количестве что обеспечивает их нормальную дальнейшую работоспособность.
Объем выполненных работ увеличивается и в отчетном году составляет 94107 т·км что на 76% больше чем в базовом. Как следствие происходит увеличение выработки в расчете на 1 автомобиль на 36% и соответственно увеличение расхода топлива.
Исходя из анализа хозяйственной деятельности следует отметить:
Количество подвижного состава незначительно увеличивается;
За последние 3 года годовой грузооборот возрос до 94107 т·км;
Затраты на техническое обслуживание и текущий ремонт составили на 2009 год 6055 и 665 тыс. руб. соответственно;
Коэффициент технической готовности составил в 2009 году k = 094;
ООО РАО «Наровчатское» это уверенно развивающееся предприятие. За рассматриваемый период по всем отраслям наблюдается положительная динамика роста. Стремительное развитие можно поддержать введением принципиально новых решений. В настоящее время хозяйствам следует следить за новыми инженерно техническими разработками и модернизировать существующую технику и оборудование.
Перспективным направлением является деятельность по проведению текущего и капитального ремонта силами самого хозяйства что значительно снизит затраты на восстановление работоспособности техники.
Поэтому для того чтобы повысить эффективность работы предприятия предлагается определить производственную программу проведения ТО и ремонтов произвести планировку производственного корпуса. Рассчитать площади производственных участков определить количество и виды необходимого оборудования количество рабочих модернизировать имеющийся стенд для разборки-сборки двигателей автомобилей для оптимизации работ связанных с разборкой-сборкой ДВС при проведении текущего и капитального ремонтов.
ЛИТЕРАТУРА.doc
Иванов А.С. Организация обеспечения работоспособности подвижного состава автотранспортного предприятия. Учебное пособие для студентов обучающихся по специальности 150200 – «Автомобили и автомобильное хозяйство» А.С. Иванов - Пенза: РИО ПГСХА. – 2001. – 166с.
Бабусенко С.М. Проектирование ремонтных предприятий С.М. Бабусенко. – М.: Колос 1981.
Черепанов С.С. Комплексная система технического обслуживания и ремонта машин в сельском хозяйстве С.С. Черепанов. – М.: 1985.
Смелов А.П. Курсовое и дипломное проектирование по ремонту машин А.П. Смелов. – М.: Колос 1984.
Расчет механизма подъема груза Под общей редакцией Н.Е. Курносова. – Пенза: РИО ПГУ 2006. – 30 с.
Александров М.П. Подъемно-транспортные машины М.П. Александров. – М.: Высшая школа 1985. – 504с.
Алексеев В.М. Расчет механизмов грузоподъемного оборудования В.М. Алексеев. – Улан-Удэ: Издательство ВСГТУ 2006. – 32 с.
Спицын И.А. Проектирование технологических процессов механической обработки деталей И.А. Спицын А.А. Орехов. - Пенза ВЦ ПГСХА 1999. – 100с.
Матвеев В.А. Техническое нормирование ремонтных работ в сельском хозяйстве В.А. Матвеев И.И. Пустовалов - М.: Колос1979. – 288с. ил.
Буралев Ю.В. Безопасность жизнедеятельности на транспорте: Учебник для вузов Ю.В. Буралев Е.И. Павлова – М.: Транспорт 1999. – 200с. ил.
Зотов Б.И. Безопасность жизнедеятельности на производстве Б.И. Зотов А.В. Курдюнов . – М.: Колос. 2003. – 432 с.
Дмитриева И.М. Гражданская оборона на объектах агропромышленного комплекса И. М. Дмитриева Г.Я. Курочкин О.В. Н.С. Николаева – М.: Агропромиздат 1990. - 351с.: ил.
Мельникова Ф.И. Методическое указание по экономическому обоснованию дипломного проекта по ремонту машин Ф.И. Мельникова. - Зерноград 1992.
Волкова Н.А. Экономическая оценка инженерных проектов: Учебное пособие Н.А. Волкова В.В. Коновалов И.А. Спицын А.С. Иванов – Пенза: РИО ПГСХА 2002 – 242с.
Конструкторская.doc
Разборка машин является важным этапом общего технологического процесса ремонта. Отсутствие необходимого оборудования и приспособлений или неправильное их использование приводят к повреждениям деталей в процессе разборки машин и их составных частей. Поэтому правильная организация и оснащение оборудованием и инструментом рабочих мест для разборки уменьшает расход запасных частей снижает стоимость и повышает качество ремонта машин.
Технологический процесс последовательность разборки объем разборочных работ при ремонте машины зависят от вида ремонта характера износов и повреждений типа ремонтного предприятия и принятой схемы производственного процесса.
При текущем ремонте в хозяйстве разборку машины производят после наружной очистки на эстакаде специальной площадке или в помещении. Машину разбирают только в тех пределах которые необходимы для выявления причин неисправностей и замены (ремонта) сборочных единиц или деталей утративших работоспособность. Сборочные единицы снимают с машины в том случае когда без этого невозможно устранить неисправность. Необоснованная разборка сборочных единиц нарушает приработку деталей и способствует увеличению их износа. Следовательно каждая разборка сокращает ресурс сборочной единицы за счет изменений в соединениях деталей что приводит к необходимости последующей приработки. Сведения о состоянии сборочной единицы и отдельных соединений деталей можно получить при тщательном их диагностировании.
Трудоемкость разборочно-сборочных работ при ремонте машин составляет более 50% от общей трудоемкости. Поэтому на предприятиях всех уровней для увеличения производительности труда повышают степень механизации разборочных и сборочных операций. Для разборки машин и сборочных единиц используют стенды прессы гайковерты съемники подъемно-транспортное оборудование.
Стенды используют в зависимости от конструктивных особенностей агрегатов их размеров массы и способа организации процесса. Конструкция стенда должна обеспечивать безопасность и удобство выполнения работ минимальные затраты времени на установку и снятие агрегата а также возможность поворота агрегата в требуемое удобное положение. При этом должны быть предусмотрены стопорные устройства исключающие самопроизвольный поворот агрегата.
По назначению стенды делят на универсальные и специализированные. Первые предназначены для установки на них однотипных агрегатов машин различных агрегатов машин различных моделей или разнотипных агрегатов одной модели. Вторые служат для разборки однотипных агрегатов машин определенной моделей. Их обычно применяют на специализированных ремонтных предприятиях с большой программой.
Рисунок 3.1 Схема стенда для разборки сборки двигателей
– платформа; 2 – стойка; 3 – плита; 4 – редуктор; 5 – рукоятка
К платформе 1 приварена стойка 2. Ремонтируемый двигатель крепят к плите 3 в которой имеются отверстия. Поворот двигателя на нужный угол осуществляют с помощью червячного редуктора. Привод вращения – ручной при помощи рукоятки 5.
Предприятие имеет достаточно большую программу ремонта (10356 чел.-ч. для моторного цеха) разномарочность подвижного состава. В условиях сельскохозяйственного производства необходимо чтобы время простоя техники в ремонте было минимальным. Для рассматриваемого хозяйства на наш взгляд стенд для разборки сборки должен иметь следующие технические и эксплуатационный характеристики:
Стенд должен быть универсальным обеспечивать возможность ремонта двигателей разных марок;
Стенд должен обеспечивать простоту установки и крепления ремонтируемых двигателей;
При работе на стенде необходимо обеспечить улавливание или отвод и масла грязи и других эксплуатационных жидкостей стекающих с внутренних деталей разбираемого двигателя;
Стенд должен иметь возможность изготовления в условиях собственной ремонтной базы предприятия (кроме редуктора лебедки и т.п.)
Имеющийся стенд не удовлетворяет этим требованиям поэтому в данном проекте рассматривается его модернизация. Для того чтобы провести ее наиболее рационально необходимо проанализировать имеющиеся конструкции стендов.
1 Обзор существующих конструкций стендов
для разборки-сборки двигателей
Из всего разнообразия известных стендов чаще всего на ремонтных предприятиях можно встретить стационарные стенды для ремонта определенной марки двигателя. Эти стенды зачастую изготавливаются собственными силами этих предприятий так как массовое производство универсальных стендов для ремонта двигателей в нашей стране слабо развито. Это делало необходимым иметь на крупных ремонтных предприятиях большое количество разборочных стендов ориентированных на определенную марку двигателей.
В последние годы крупные производители автотракторных двигателей такие как ЯМЗ КамАЗ ЗИЛ начали выпускать двигатели с универсальными привалочными плоскостями и ремонтными отверстиями. Это сделало возможным разработку и изготовление ремонтных стендов на которых можно производить ремонт двигателей различных марок.
Стенд ОПТ-5557-ГОСНИТИ предназначен для кантования двигателей: тракторных – Д-50 Д-240 СМД-14 и его модификаций А-41 -01М и автомобильных – ГАЗ-53 ЗИЛ-130. Применяется при разборке и сборке двигателей на ремонтных предприятиях.
Составные части стенда: пульт для размещения силовой и аппаратуры управления защиты и сигнализации; грузовая подвеска для установки двигателя и выравнивания его в горизонтальной плоскости; кантователь два ящика для хранения инструмента и мелких деталей крестовина служащая опорой стенда трубопроводы для подвода проводов.
Рисунок 3.2 – Стенд ОПТ-5557-ГОСНИТИ для разборки и сборки двигателей
Таблица 3.1 – Техническая характеристика стенда ОПТ-5557-ГОСНИТИ
Мощность электропривода кВт
Максимальная грузоподъемность кг
Угол поворота двигателя град
Габаритные размеры мм
Наличие электромеханического привода;
Большая грузоподъемность.
Невозможность ремонта двигателей КамАЗ ЯМЗ;
Нет емкости для сбора стекающего масла грязи и других эксплутационных жидкостей;
Пульт управления расположен вне корпуса стенда;
Ограниченный угол поворота двигателя.
Стенд Р-660 с электромеханическим приводом поворотного устройства двигателя изображен на рисунке 3.3. Данный стенд предназначен для проведения сборочно-разборочных операций с двигателями КамАЗ ЯМЗ.
Конструкция стенда состоит из сварной рамы двух стоек одна из которых фиксируется в двух положениях. Первое положение – подвижная стойка установлена на максимальный размер для двигателя ЯМЗ второе положение – для двигателя КамАЗ. На неподвижной стойке установлен червячный редуктор приводимый во вращение от реверсного асинхронного электродвигателя переменного тока через клиноременную передачу. В верхней части передвижной стойки смонтирована подшипниковая опора. На выходном валу редуктора и на валу подшипниковой опоры смонтированы две траверсы трубчатого сечения. В них с обеих сторон запрессованы втулки и входят телескопические раздвижные опоры на концах которых смонтированы штыри.
Рисунок 3.3 – Cтенд Р 660 для ремонта двигателей КамАЗ ЯМЗ
Во время работы на стенде в зависимости от марки устанавливаемого двигателя передвижную стойку перемещают по траверсе на необходимую величину. Для установки двигателей КамАЗ-740 и КамАЗ-741 передвижную стойку сдвигают до упора со стационарной а для установки двигателей ЯМЗ-236 или ЯМЗ-238 – отодвигают от стационарной и крепят фиксатором.
Раздвижные опоры устанавливают также в зависимости от марки двигателя. Для крепления двигателей ЯМЗ-236 или ЯМЗ-238 оси штырей должны располагаться перпендикулярно оси поворота двигателя при этом для установки двигателя ЯМЗ-236 опоры сдвигают а для установки двигателя ЯМЗ-238 – раздвигают.
Для крепления двигателей КамАЗ-740 или КамАЗ-741 оси штырей должны располагаться под углом 45° к оси поворота двигателя при этом для установки двигателя КамАЗ-740 опоры сдвигают а для установки двигателя КамАЗ-741 – раздвигают. Затем опоры закрепляют фиксатором.
Двигатель устанавливают на стенд при помощи грузоподъемного устройства вводят штыри в отверстия в блоке цилиндров двигателя. Затем при помощи специального устройства поворачивают двигатель в положение удобное для работы. Снимают двигатель со стенда в обратном порядке.
Привод стенда закрыт металлическим кожухом на лицевой части которого расположены кнопки управления реверсной прокрутки механизма поворота двигателя. На раме двигателя установлено съемная емкость для сбора стекающего масла грязи и других эксплутационных жидкостей.
Основные технические характеристики данного стенда приведены в таблице 3.2.
Таблица 3.2 –Техническая характеристика стенда Р-660
Напряжение питания В
Возможность перемещения одной опорной стойки относительно другой;
Возможность использования различных траверс для навески двигателя.
Большая мощность электродвигателя
Стенд Р642 (рисунок 3.4) предназначен для сборки и разборки V-образных карбюраторных двигателей ЗМЗ-53 и ЗИЛ-130.
Стенд состоит из стойки 1 основания 2 кронштейна крепления двигателя 3 подпорки 4 и поддона 5.
Стойка и основание крепятся к фундаменту болтами. В стойке смонтирован электромеханический привод поворота состоящий из электродвигателя и червячного редуктора.
На выходном валу редуктора закреплен кронштейн с опорными цапфами на котором крепится ремонтируемый двигатель.
Двигатель установленный на стенде поворачивается в наиболее удобное для работы положение вокруг параллельной оси коленчатого вала и надежно фиксируется самотормозящим редуктором. Поворот двигателя осуществляется при нажатии кнопки управления.
Рисунок 3.4 – Стенд Р642 для разборки и сборки двигателей:
– стойка 2 – основание 3 – кронштейн 4 – подпорка 5 – поддон для масла
Таблица 3.3 –Техническая характеристика стенда Р 642
Наличие электромеханического привода.
Небольшая грузоподъемность.
Стенд 6501-72 для подразборки двигателя предназначен для разборки-сборки двигателя ЗИЛ-130 на одном рабочем посту.
Рисунок 3.5 – Стенд 6501-72 для подразборки и разборки двигателя
Внутри станины 6 стенда разметен электромеханический самотормозящий привод для поворота вилки 5 вокруг горизонтальной оси. Опорное кольцо 2 может поворачиваться в подшипниках 3 на концах вилки. Опорное кольцо 2 состоит из двух частей одна из которых (неподвижная) имеет цапфы входящие в подшипники вилки а другая часть 1 (подвижная) может поворачиваться вручную внутри неподвижной вокруг их общей оси и стопорится ручным стопором. Двигатель крепится к подвижной части опорного кольца быстродействующим ручным зажимом байонетного типа и может в процессе разборки поворачиваться вокруг трех взаимно перпендикулярных осей. Консоль 4 для подвески инструмента может поворачиваться вокруг вертикальной оси для удобства установки двигателя на стенд. Схема стенда 6501-72 приведена на рисунке 3.5.
Таблица 3.4 – Техническая характеристика стенда 6501-72
Время поворота двигателя на 180° с
Возможность вращения двигателя в трех плоскостях.
Ремонт двигателей одной марки;
Большая масса стенда.
Применение дополнительного механизма фиксации стенда в любом положении с установленным двигателем;
Предусмотреть в конструкции стенда ручную лебедку для возможности легкой и быстрой установки на стенд ремонтируемых двигателей.
2 Устройство и принцип работы модернизируемого стенда для разборки и сборки двигателей
Стенд (рисунок 3.6) предназначен для разборки и сборки двигателей КамАЗ-740 -741 ЯМЗ-236 -238 Д-240 а также карбюраторных двигателей грузовых автомобилей ЗИЛ-130 ГАЗ-53.
Рисунок 3.6 – Стенд для разборки-сборки двигателей:
- рама 2 – колесо 3 – червячный редуктор 4 – рукоятка 5 – плита крепления двигателя 6 – домкрат гидравлический 7 – стоика лебедки 8 – лебедка ручная.
Стенд имеет рамную сварную конструкцию. К платформе 1 приварена стойка 7. Ремонтируемый двигатель крепят к плите 5 в которой имеются отверстия. Поворот двигателя на нужный угол осуществляют с помощью червячного редуктора 3. Привод вращения – ручной при помощи рукоятки 4.
В конструкции стенда присутствует гидравлический домкрат 6 с помощью которого производится изменение положения оси вращения ремонтируемого двигателя по вертикали.
В зависимости от типа ремонтируемого двигателя к установочной плите 5 крепятся различные сменные кронштейны с отверстиями.
На стойках 7 в верхней части смонтирована ручная лебедка 8 с помощью которой осуществляется подъем ремонтируемого двигателя для закрепления его на установочной плите.
На раме стенда установлены колеса причем задние колеса являются поворотными что позволяет транспортировать стенд к ремонтируемому двигателю для дальнейшего его закрепления.
Разработанный стенд отвечает выдвинутым требованиям: имеется ручная лебедка для подъема двигателей обеспечена универсальность. Универсальность стенда обеспечивается применением сменных кронштейнов для крепления двигателей различных марок.
3 Расчет ручной лебедки
Согласно рекомендациям ВНИИПТМаш [1] при малых грузоподъёмностях (до 3 тонн) груз может подвешиваться без полиспаста.
В качестве рабочего тягового органа лебедки применяется стальной канат выбираемый исходя из условия [2]
Fp – разрывное усилие каната Н;
s – запас прочности каната.
Согласно Правилам Госгортехнадзора стальные канаты рассчитывают на растяжение при запасе прочности s = 4 6 принимаем s = 5 [3].
Нагрузка на одну ветвь каната определится как суммарная сила тяжести действующая на поднимаемый двигатель
Суммарная сила тяжести определяется из выражения
где m – масса поднимаемого двигателя m = 800 кг.
Fg = 981 · 800 = 7200 Н.
Fр = 5 ·7848 = 39240 Н.
Выбираем стальной канат типа ЛК-РО 6×36 (1+7+77+14)+1 о.с.
ГОСТ 7668-80 dк = 81 мм при = 1770 МПа с разрушающим усилием
Чтобы ограничить напряжения изгиба и достичь определенной долговечности каната рекомендуется наименьшие диаметры барабана и блока определять по формуле [3]
Dб ≥ (e 1) · dк(3.4)
где е – коэффициент зависящий от типа грузоподъемника и режима эксплуатации e = 25 [3]
Dб = (25 – 1) 81 = 1944 мм
Рабочая поверхность барабана выполняется с винтовой канавкой для направленной навивки стального каната. Многослойная навивка допустима только на гладкие барабаны но она приводит к повышенному износу каната.
Основные размеры барабана круглого полого сечения. Различают номинальный (расчетный) Dб определяемый по формуле (5) наружный D и внутренний Dв диаметры.
Наружный диаметр измеряемый по дну канавок [1]
D = Dб – dк = 1944 – 81 = 1863 мм(3.5)
Внутренний диаметр барабана [1]
где – толщина стенки барабана [3] мм.
= 002 · Dб + (6 10) = 002 · 1944 + 6 = 99(3.7)
Dв = 1863 – 2 · 99 = 1665 мм
Рисунок 3.7 – Эскиз барабана
Длина каната при однослойном наматывании на один барабан [2]
где Н – высота подъема или длина перемещения груза Н = 2000 мм;
z – число ветвей подвеса или тяги;
zн – число ветвей наматываемых на барабан.
Lо = 2000 1 1= 2000 мм
Число рабочих витков на барабане [2]
где 15 2 – запасные витки рекомендуемые Правилами Госгортехнадзора для разгрузки крепления каната на барабане.
zв – число рабочих витков;
l1 – длина концевой части барабана l1 = 14 мм.
4 Расчет стопорного устройства
Стопорные устройства или остановы применяют в механизмах с ручным приводом работающих с небольшими скоростями. В качестве такого устройства нами используется храповой останов. Остановы данной конструкции надежны в работе и более распространены. Их чаще всего монтируют на валу рукоятки (привода) получая менее громоздкую конструкцию. Храповые колеса изготавливают из стали реже из чугуна с внешним или внутренним зацеплением.
Основные размеры профиля зуба и храповика 1 (рисунок 3.8) принимают в зависимости от модуля m = 6 30 мм и числа зубьев z = 10 30 [2]:
DK = m z; р = т; h = (075 08) m; а = 155 m; b1 = b + (2 3) мм;
kb = b m так для стали 45 – kb = 1 2; для стали 35Л – kb = 15 4; для СЧ-15 – kb = 2 6.
Исходя из данных условий выбираем храповое колесо из стали 35Л с числом зубьев z = 10 и модулем m = 10.
DK = 10 10 = 100 мм; р = 314 10 = 314 мм; h = (075 08) 10 = 8 мм;
а = 155 10 = 155 мм; b = 25 · 10 = 25 мм; b1 = 25 + 2 3 = 28 мм;
Рисунок 3.8 – Останов храповой
– храповик; 2 - защелка; 3 – пружина
Из расчета зуба на изгиб определим необходимое значение модуля по выражению [2]:
где Tс – статический момент на валу барабана
у – коэффициент формы зуба для внешнего зацепления у = 0375 [2];
[]и – допускаемое напряжение изгиба для зуба для стали
[]и = 60 70 МПа [2].
Статический момент на валу барабана определится по формуле:
Тс = 05 · g · mo · Dб Нм(3.13)
где mо = m + mг – общая масса груза и грузозахватного органа;
Dб – диаметр барабана м.
Тс = 05 · 981 · 800 · 1944 · 10–3 = 7628 Н·м.
При проверке кромки зуба на смятие линейная нагрузка [2]
где [р] – допускаемая нагрузка на единицу ширины кромки зуба с учетом динамического характера нагружения [р] = 300 400 Нмм [2].
Линейная нагрузка р = 3158 Нмм укладывается в интервал допускаемой нагрузки – [р] = 300 400 Нмм таким образом условие прочности выполняется.
Расчет на прочность барабана лебедки сводится к определению напряжений сжатия изгиба и кручения действующих на барабан.
Для проверки барабана на прочность должно выполняться условие [2]
где [] – допускаемое напряжение для барабана [] = 230 МПа (для материала барабана) [2].
Условие прочности выполняется.
5 Расчет устойчивости стенда
Во время работы грузоподъемные машины (ГПМ) подвергаются действию различных сил которые стремятся изменить их нормальное рабочее положение. К таким силам относятся: масса консольно расположенных частей ветровая нагрузка масса поднимаемого груза динамические нагрузки возникающие при резком пуске и торможении механизмов и при движении ГПМ по неровному пути и др. [4]
Устойчивость рассчитывается для следующих случаев: при действии груза (рисунок 3.9) при отсутствии груза при внезапном снятии нагрузки на крюке при монтаже или демонтаже ГПМ.
Рисунок 3.9 – Схема определения грузовой устойчивости стенда
В соответствии с ГОСТ 13994-81 проверяется устойчивость [4]:
где Мо Мнwр Мнwн – опрокидывающие моменты относительно ребра опрокидывания соответственно от массы груза динамических нагрузок и от ветровой нагрузки рабочего и нерабочего состояния Н·м;
Муд – удерживающий момент относительно ребра опрокидывания от силы тяжести ГПМ Н·м;
Fg – нормативная составляющая массы груза Fg = 7200 Н по (3.3);
bFg – расстояние от точки подвеса груза до вертикальной плоскости проходящей через ребро опрокидывания м;
Go – нормативная составляющая массы ГПМ кг;
bк – расстояние от центра масс частей ГПМ до вертикальной плоскости проходящей через ребро опрокидывания м.
где то – масса стенда то = 150 кг;
g – ускорение свободного падения g = 981 мс2.
Go = 150 · 981 = 14715 Н
Так как эксплуатация стенда предполагается внутри производственного помещения то опрокидывающими моментами относительно ребра опрокидывания от ветровой нагрузки рабочего Мнwр и нерабочего Мнwн состояния можно пренебречь.
Мо = 7200 · 0066 = 4752 Н·м.
Опрокидывающий момент от массы поднимаемого ГПМ груза тем больше чем больше масса груза и вылет крюка от ребра опрокидывания. Под ребром опрокидывания р-р понимается грань опорного контура относительно которой силы стремятся опрокинуть ГПМ.
Коэффициент устойчивости К представляет собой отношение удерживающего момента к опрокидывающему [4]
Условие устойчивости выполняется.
Введение.doc
Постоянно растущая потребность в ремонтах автомобилей и их агрегатов изменения их конструкций и конструкции технологического оборудования а также постоянное совершенствование технологии ремонта машин требуют непрерывного совершенствования ремонтной базы строительства новых и реконструкции существующих ремонтных предприятий. Система проектирования ремонтных предприятий призвана исключить возможность применения неэффективных технологий строительства экономически неэффективных предприятий и обеспечить строгое обоснование организационных технических и технологических параметров ремонтных предприятий.
Улучшение качества ремонтных работ можно добиться увеличением объемов работ применением современного оборудования современной технологии высококвалифицированных работников а так же путем модернизации устаревшего ремонтно-технологического оборудования улучшение организации труда лучшей компоновкой участков и организации рабочих мест строгим соблюдение прогрессивных технологий ремонта.
Мы предлагаем технический проект совершенствования ПТБ этого хозяйства с модернизацией стенда для разборки-сборки двигателей автомобилей.
Перспективным направлением является деятельность по проведению текущего и капитального ремонта силами самого хозяйства что значительно снизит затраты на восстановление работоспособности техники.
Для выполнения поставленной цели были сформулированы следующие задачи:
Определить производственную программу проведения ТО и ремонтов произвести планировку производственного корпуса. Рассчитать площади производственных участков определить количество и виды необходимого оборудования количество рабочих.
Повысить эффективность работы ремонтно-монтажного участка путем модернизации имеющегося стенда для разборки-сборки двигателей автомобилей. Разработать конструкцию позволяющую произвести модернизацию силами самого хозяйства выполнить необходимые расчеты.
Разработать мероприятия по БЖД при работе в ремонтной мастерской в целом и на модернизированном стенде в частности.
Провести оценку экономической эффективности модернизируемого стенда для разборки-сборки двигателей автомобилей.
Рекомендуемые чертежи
- 01.04.2015
- 09.07.2014
- 07.03.2016
- 29.07.2014
- 04.06.2014
- 25.01.2023