Широкоуниверсальный фрезерный станок мод.6Б76ПФ2




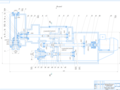
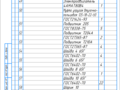
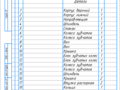
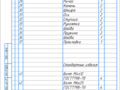
- Добавлен: 25.01.2023
- Размер: 575 KB
- Закачек: 1
Описание
Широкоуниверсальный фрезерный станок мод.6Б76ПФ2
Состав проекта
![]() |
![]() |
![]() |
![]() ![]() ![]() ![]() |
![]() ![]() ![]() ![]() |
![]() ![]() ![]() ![]() |
![]() ![]() ![]() ![]() |
![]() ![]() ![]() ![]() |
![]() ![]() ![]() ![]() |
![]() |
![]() ![]() ![]() ![]() |
![]() ![]() ![]() |
Дополнительная информация
МРС специф лист4.cdw

МРС специф лист1.cdw

МРС специф лист2.cdw

МРС специф лист3.cdw

МРС лист3.cdw

МРС лист1.cdw

горизонтальный вариант - XZOYB
вертикальный вариант - XZOYC
Кинематическая схема
МРС лист2 140508.cdw

Введение.doc
Расчет режимов резания6
Кинематическая структура станка 19
Варианты компоновки станка 205 Кинематический расчет привода главного движения 20
Расчет чисел зубьев 23
Расчет модулей зубчатых передач 24
Размеры зубчатых колес 28
Определение крутящих моментов на валах привода 30
Выбор подшипников проектирующего узла 32Список литературы 34
Темпы развития станкостроения количественный и качественный состав станочного парка во многом определяют промышленный потенциал любой страны и характеризует уровень ее машиностроения.
Станки занимают особое место среди таких машин орудий как текстильные транспортные машины легкой промышленности полиграфические и др. потому что они предназначены для изготовления деталей машин т.е. для производства средств производства. Поэтому станкостроение часто называют сердцевиной машиностроения.
Современные металлорежущие станки – это весьма развитые машины включающие большое число механизмов и использующие механические электрические гидравлические и другие методы осуществления движений и управления циклом.
По конструкции и назначению трудно найти более разнообразные машины чес металлорежущие станки. На них обрабатывают всевозможные детали – мельчайших осей шестеренок и рычажков для часов и приборов до громадных деталей размеры которых достигают многих метров. Поэтому и габариты станков весьма различны.
Уточнение служебного назначения станка
Широкоуниверсальный фрезерный станок предназначен для горизонтального фрезерования различных изделий сравнительно небольших размеров цилиндрическими дисковыми и фасонными резцами. Для вертикального фрезерования торцовыми концевыми и шпоночными фрезами а также для выполнения различных сложных инструментальных работ.
Наличие горизонтального шпинделя и поворотной головки с вертикальным шпинделем а также ряд дополнительных приспособлений (углового универсального стола делительной головки круглого делительного стола и др.) обеспечивает станку широкую универсальность. Его целесообразно применять для работы в инструментальных и экспериментальных цехах при изготовлении приспособлений штампов пуансонов пресс-форм различных инструментов и т.д. На станке могут быть установлены долбежная головка и копировальное устройство.
Техническая характеристика станка приведена в таблице1.
Рабочая поверхность стола (ширина х длина) в мм
Наибольший ход стола в мм:
Наибольшее вертикальное перемещение вертикального шпинделя в мм
Наибольшее перемещение шпиндельной бабки в мм
Набольший угол поворота вертикального шпинделя в град
Количество скоростей подач стола
Пределы скоростей продольных и вертикальных подач стола в мммин
Мощность электродвигателя кВт
Основные узлы станка:
– поворотная головка;
– шпиндельная бабка;
– станина с коробкой скоростей и коробкой подач;
Нормы точности и жесткости.
Проверка точности станка:
Проверка 1.1 Плоскостность рабочей поверхности стола – осуществляется при помощи линейки и индикатора. Индикатор устанавливают на столе так чтобы его наконечник касался рабочей поверхности линейки. Индикатор перемещают вдоль линейки и определяют прямолинейность формы профиля поверхности.
Проверка 1.2 Перекосы рабочей поверхности стола при его продольном и поперечном перемещении.
Проверка 1.3 Прямолинейность перемещения стола в горизонтальных плоскостях при его перемещении в продольном и поперечном направлениях.
Проверка 1.4 Параллельность траектории продольного перемещения стола его рабочей поверхности.
Проверка 1.5 Параллельность траектории поперечного перемещения стола его рабочей поверхности.
Проверка 1.6 Перпендикулярность направлений продольного и поперечного перемещения стола в горизонтальной плоскости.
Проверка 1.7 Перпендикулярность направления вертикального перемещения шпиндельной бабки к рабочей поверхности стола в продольном и поперечном направлениях.
Проверка 1.8 Перпендикулярность оси вращения шпинделя к рабочей поверхности стола в продольном и поперечном направлениях.
Проверка 1.9 Осевое биение шпинделя.
Проверка 1.10 Торцовое биение опорного торца шпинделя.
Проверка 1.11 Радиальное биение конического отверстия шпинделя.
Проверка 1.12 Точность установки стола с помощью имеющихся на станке механизмов отсчета перемещения в продольном и поперечном направлениях.
Проверка 1.13 Перпендикулярность направления вертикального перемещения гильзы к рабочей поверхности стола в продольном и поперечном направлениях.
Проверка станка в работе.
Проверка жесткости станка:
Проверка 3.1 Перемещение под нагрузкой стола относительно оправки закрепленной на шпинделе или в отверстии шпинделя.
Расчет режимов резания
1 Фрезерование торцовой фрезой
где - ширина стола станка
коэффициент 04 берем учитывая небольшие габариты станка.
По таблице 94 [1 с . 187] определяем
Глубина и ширина фрезерования:
Подача. При фрезеровании различают подачу на один зуб SZ подачу на один оборот фрезы S и подачу минутную SМ которые находятся в соотношении:
Где n – частота вращения фрезы
z - число зубьев фрезы.
Определяем SZ по таблице 34 [1 с. 283]
Скорость резания – окружная скорость фрезы:
Значение коэффициента и показателей степени приведены в таблице 39 [1 с. 286] а период стойкости Т – в таблице 40 [1 с. 290]
Коэффициент является произведением коэффициентов учитывающих влияние материала заготовки (определяется по таблицам 1-4 [1 с.261-263]) состояния поверхности (по таблицам 5 [1 с.263]) материала инструмента (по таблицам 6 [9 с.263]).
Сила резания. Главная составляющая силы резания при фрезеровании – окружная сила:
Значение коэффициента и показателей степени приведены в таблице 41 [1 стр. 291] поправочный коэффициент на качество обрабатываемого материала в таблице 9 [1 с. 264].
Величины остальных составляющих сил определяются по таблице 42 [1 с. 292].Расположение сил показано на рисунке 1.
2 Фрезерование дисковой фрезой
Величины остальных составляющих сил определяются по таблице 42 [1 с. 292].
3 Фрезерование концевой фрезой
По таблице 94 [1 с. 187] определяем
Значение коэффициента и показателей степени приведены в таблице 41 [1 с. 291] поправочный коэффициент на качество обрабатываемого материала в таблице 9 [1 с. 264].
4 Сверление сверлом 5 мм
Глубина резания. При сверлении глубина резания
Подача. При сверлении отверстий без ограничивающих факторов выбираем максимально допустимую по прочности сверла подачу по таблице 25 [1 с. 277].
Значения коэффициентов и показателей степеней приведены в таблице 28 [1 с. 278].
Общий поправочный коэффициент на скорость резания учитывающий фактические условия резания:
- коэффициент на обрабатываемый материал определяется по таблицам 1-4 [1 с. 261-263]. - коэффициент на инструментальный материал определяется по таблице 6 [1 с. 263]. - коэффициент учитывающий глубину сверления определяется по таблице 31 [1 с. 280].
Крутящий момент и осевую силу рассчитываем по формуле:
Значение коэффициентов и показателей степеней приведены в таблице 32 [1 с. 281].
Коэффициент учитывающий фактические условия обработки в данном случае зависит только от материала заготовки и определяется выражением:
4 Сверление сверлом 20 мм
Кинематическая структура станка
Варианты компоновки станка
Горизонтальный вариант XZOYBh
Вертикальный вариант XZOY
Кинематический расчет привода главного движения
Варианты кинематических схем с геометрических рядом чисел оборотов связаны двух основных задач привода: настройки чисел оборотов в пределах заданного диагноза Д уменьшения (редукций или увлечения ) (мультипликаций) числа оборотов шпинделя.
При проектирований привода станка необходимо строится чтобы при заданном числе Z ступеней частоты вращения шпинделя и заданном диапазоне регулирования привод имел:
)минимальные число всех передач;
)минимальные число групп передач;
)минимальные габариты;
Зная частоты вращения шпинделей в каждой позиции обработки проектируем кинематическую схему многошпиндельной коробки. Главное требование к кинематическим цепям – максимально возможно обеспечить совпадение расчетных частот вращения с частотами вращения полученными в результате подбора передаточных отношений. Передаточные отношения (числа зубьев ведущего и ведомого колес) подбираются согласно графикам частот вращения.
Для вычерчивания кинематической схемы принимаем конструктивно модуль для всех зубчатых колес мм знаменатель ряда частот вращения .
По известным значениям наибольшей и наименьшей частоты вращения определяем диапазон регулирования:
Определяем диапазон регулирования коробки скоростей:
Число ступеней скорости шпинделя определяем по формуле:
Принимаем коробку скоростей:
Структурная формула коробки передач будет иметь вид:
Рассчитаем все частоты вращения:
Для построения графика чисел оборотов необходимо в каждом из соотношений выбрать одно передаточное число; тогда определяются и все остальные значения. График чисел оборотов строим также в логарифмическом масштабе. Каждому валу отвечаем вертикальная линия графика. Горизонтальные линий имеют отметки чисел оборотов соответствующего вала или шпинделя в пределах от минимального да максимального числа оборотов. Передаточные отношения передач выражаются лучами. Для ускорительной передачи передаточное отношение и луч направляем вверх для за медлительной передачи передаточных отношений и луч направляем вниз. При передаточном отношении луч направляется горизонтально.
Выбор передаточных отношений i следует производить так чтобы их значения не выходили за допускаемые пределы.
Ограничения передаточных отношений предельными значениями применяется во избежание чрезмерно больших диаметров ведомых колес и увеличения по этой причине радиальных габаритов привод
На рисунке 5 представлен график частот вращения.
По графику частот вращения определяем передаточные отношения:
Расчет чисел зубьев
Число чисел зубьев колес групповых передач обуславливается межцентровым расстояние а которое остается постоянным для данной группы.
Сумму чисел зубьев определяем по таблице 4.5 [2 с. 101].
Учитывая передаточные отношения находим числа зубьев каждого колеса по таблице 4.5 [2 с. 101]:
Расчет модулей зубчатых передач
При расчете на прочность зубьев зубчатых колес рассчитываются модули по контактным напряжениям и по напряжениям изгиба.
Расчет зубчатых передач для коробок скоростей ведут для модуля исходя из прочности по напряжениям изгиба и контактным напряжениям по формулам:
Модуль по контактным напряжениям:
Z – число зубьев меньшего зубчатого колеса в группе передач
- наименьшая частота вращения вала при которой передается наибольшая установленная мощность
- ширина зубчатого колеса
- модуль (предварительно берем значение модуля равного 2)
-допускаемое напряжение по изгибу определяем по таблице 2.2 [3 с. 12]:
-допускаемое напряжение по усталости поверхностных слоев определяем по таблице 2.2 [3 с. 12]:
- коэффициент формы зуба
- динамический коэффициент учитывает дополнительные нагрузки возникающие при входе зубьев в зацепление которые возникают в результате удара.
- окружная скорость зубчатого колеса.
- межосевое расстояние
- погрешность окружного шага определяется в зависимости от степени точности.
- коэффициент концентрации учитывает распределение эпюры давлений по длине зуба.
- коэффициент режима работы учитывает то обстоятельство что коробка скоростей работает не только при номинальной нагрузке но и на других режимах.
Тогда рассчитываем модули:
Рассчитываем диаметры валов:
- допускаемое напряжение при кручении для валов из среднеуглеродистой стали.
Проверочный расчет зубчатого зацепления
При проектировании коробки предварительно были приняты модуль зубчатого зацепления мм и делительные диаметры зубчатых колес. Ширина зубчатого венца принимается в пределах . Ширину зубчатого венца окончательно принимаем
Для зубчатых колес принимаем материал сталь 40Х. Вид термической обработки – улучшение. Твердость 240 НВ.
Размеры зубчатых колес
Размеры зубчатого колеса
Делительный диаметр зубчатого колеса
Диаметр окружности вершин зубьев зубчатого колеса
Диаметр окружности впадин зубьев зубчатого колеса
Делительный диаметр зубчатого колеса мм
Определение крутящих моментов на валах привода
Крутящий момент на валу электродвигателя определяем по формуле
где NH – номинальная мощность электродвигателя привода (NH = 22 кВт);
nH – номинальное число оборотов в минуту электродвигателя (nH = 500мин-1).
Крутящий момент на валах привода определяем по формуле
где nI – число оборотов в минуту первого вала привода (nI = 640 мин-1);
- К. П. Д. передач от электродвигателя до первого вала.
- К. П. Д. муфты (= 095);
- К. П. Д. пары подшипников качения (= 099).
Подставляя найденные значения получаем
Крутящий момент на втором валу привода определяем по формуле
где nII – число оборотов в минуту второго вала (nII = 640мин -1);
- К. П. Д. коробки от первого вала до второго вала включая зубчатую передачу
- К. П. Д. зубчатой передачи (=097).
Подставляя найденные значения B (4.4) получаем
Крутящий момент на третьем валу привода определяем по формуле
где nIII – число оборотов в минуту третьего вала привода ( nIII = 250
- К. П. Д. коробки от первого до третьего вала.
Подставляя найденные значения в получаем
Крутящий момент на четвертом валу привода определяем по формуле
где nIV – число оборотов в минуту третьего вала привода (nIV = 160
- К. П. Д. коробки от третьего до четвертого вала
Подставляя найденные значения получаем
Выбор подшипников проектирующего узла
В коробках скоростей и подач станков общего назначения в качестве опор валов применяются подшипники значения так как они лучше воспринимают различные нагрузки в широком диапазоне скоростей и при частого пусках и остановках. При воздействий на узел только радикальной нагрузки то есть когда вал передает крутящий момент при помощи прямозубых колес применяют радикальные подшипники.
Исходные данные = 30 мм – диаметр под подшипник R1=1176 H R2 = 837Hn = 250 мин режим напряжения – ( 90.83)
Находим эквивалентные нагрузки
Где - коэффициент эквивалентности (Кt=08 [9 с. 8])
)Предварительные шариковый радикальный подшипник мягкой серий №206
)Для этих подшипников из табл. 24.10 находим что базовая динамическая грузоподъемность Cr=153 kH а базовая статическая грузоподъемность Cor=102kH
)Находим эквивалентную динамическую радикальную нагрузку
Где V – коэффициент вращения (V = 1[9 c. 83])
X – коэффициент (X=1 [9 c. 84])
Y – коэффициент (y=0 [9 c. 83])
– коэффициент безопасности
KT – температурный коэффициент (КТ=1 [9 c. 84])
)Определяем требуемую динамическую грузоподъемность подшипника
где - время работы станка ч
где L – время работы станка в годах (L=10 [9 c. 11])
- коэффициент суточной загрузки (Kr =09 [9 c. 12])
- коэффициент годовой загрузки (Kc=03)
)Так как Стр Cr (831815300H)то предварительно выбранной подшипник подходит
Смазка обеспечивается циркуляционной системой. Циркуляционной системой осуществляются смазки коробки скоростей корпус которой является резервуаром для массы от плунжерного насоса через обратных клапаны.
Масло указатели и показывают наличия масла в резервуаре. Плунжерный насос крепится к нижней плите корпуса коробки скоростей и приводится в действия эксцентричном закрепленном на валу коробки скоростей. Поддаваемое насосом масло поступает через прорезки в трубах на зубчатые колеса сверлильной головки затем стекает обратно в масляном резервуаре 6.Для глазка станка используется индустриальное масло 20А ГОСТ 20799 – 75
Список использованных источников
А.Г. Косилова Р.К. Мещеряков. Справочник технолога-машиностроителя том 2. М.: Машиностроение 1986. – 495с.
Дунаев П.Ф.Леликов О.П. Конструирование узлов и деталей машин М Высшая школа 1985 416с
Балабанов А.Н. Краткий справочник технолого – машиностроителя М Издательство сотрудников 1992 463с.
Прожиков А.С. Расчет и констрирование металлорежущих станков М Высшая школа.1967 431 с
Кочергин Ю.Н. Конструирование и расчет маталлорежущих станков и станочных комплексов Минин Высшая школа 1976 590 с
Сварщевский А.Ш.Макейчин Н.Н. Расчет и констрирование коробок скоростей и подач МинскВысшая школа 1976 59с
Рабинович А.Смилянский В.Милевский Э. Коробки скоростей металлорежущих станков ЛьвовИздательство Львовского университета 1968 376с
Тарабановский В.М.Дудак Н.С. Методические указания к выполнению курсового проекта по металлорежущим станкам часть 2 Алма – ата 1980 39с
Тарабановский В.М.Дудан Н.С. «Методика указания к выполнению курсового проекта по металлорежущим станкам» Алма – Ата1980 56с.
Металлорежущие станки под ред. Ажеркана Н.С. ММашиностроение 1965том 1 757 с.