Ректификационная установка непрерывного действия для разделения бинарной смеси бензол-анилин



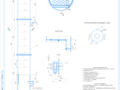
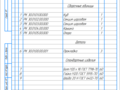
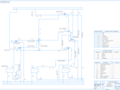
- Добавлен: 25.01.2023
- Размер: 3 MB
- Закачек: 0
Описание
Ректификационная установка непрерывного действия для разделения бинарной смеси бензол-анилин
Состав проекта
![]() |
![]() ![]() ![]() |
![]() ![]() ![]() |
![]() ![]() ![]() |
![]() ![]() ![]() |
![]() ![]() ![]() |
![]() ![]() ![]() |
![]() ![]() ![]() |
![]() ![]() ![]() |
![]() ![]() ![]() |
![]() |
![]() ![]() ![]() ![]() |
![]() ![]() ![]() ![]() |
![]() ![]() ![]() ![]() |
![]() ![]() ![]() |
![]() ![]() ![]() |
![]() ![]() ![]() |
Дополнительная информация
8. Библиографический список.doc
Коган В.Е.Фридман В.Н. Кафаров В.В. Равновесие между жидкостью и паром: справочник. – М.: Наука 1966.
Павлов К.Ф. Романков П.Г. Носков А.А. Примеры и задачи по курсу процессов и аппаратов химической технологии. Ленинград: Химия 1981. – 560 с.
Рамм В.М. Абсорбция газов. М.: Химия 1976.
Савельев Н.И. и др. Расчёт и конструирование ректификационных колонн с использованием ЭВМ. Казань: Наири 1983. – 48с.
Расчёт основных процессов и аппаратов нефтепереработки. Справочник Под. ред. Судакова. М.: Химия 1979. – 568с.
Вредные вещества в промышленности. Справочник. Т 12. Органические веществаПод ред. Н.В. Лазарева. Л.: Химия 1976. – 538с.
Дытнерский Ю.И. Основные процессы и аппараты химической технологии: пособие по проектированию. М.: Химия 1991 – 496с.
Справочник химика. Том II. Основные свойства неорганических и органических соединений. Л. М.: Химия. 1964. – 1168 с.
Лащинский А.А. Толчинский А.Р. Основы конструирования и расчет химической аппаратуры. Справочник. Л.: Машиностроение 1970-752с
Варгафтик Н.Б. Справочник по теплофизическим свойствам газов и жидкостей. М.: Физматгаз 1963-708с.
Перри Дж. Справочник инженера-химика. Т.I . Л.: Химия. 1969-640с.
Лащинский А.А. Конструирование сварных химических аппаратов. Справочни. Л.: Машиностроение1981.-382.
6.подбор.DOC
Днище элептическое отбортованное
Днище является одним из основных элементов химических аппаратов.
Цилиндрические цельносварные корпусы как горизонтальных так и вертикальных аппаратов с обеих сторон ограничиваются днищами. Формы днищ бывают элептические полушаровые в виде сферического сегмента конические и цилиндрические. Наиболее распространенной формой является элептическая. Они изготавливаются горячей штамповкой из плоских круглых заготовок состоящих из одной или нескольких частей сваренных между собой.
Диаметр аппарата D = 600 мм. Размеры элептических отбортованных днищ с внутренними базовыми диаметрами по таблице 7.2. [12 с. 116] ГОСТ 6533-78 выбираем днище и крышку.
Конструкция стандартной цилиндрической опоры для стальных сварных
аппаратов с местными косынками.
По диаметру выбираем опору. Основные размеры цилиндрических опор для колонных аппаратов ОСТ 26-467-78 [12 с. 288].
Фланцы соединяющие колонну с трубопроводами.
В химических аппаратах для разъемного соединения стальных корпусов и отдельных частей применяются фланцевые соединения преимущественно круглой формы. На фланце присоединяются к аппаратам трубы арматуры и т.д. Фланцевые соединения должны быть прочными жесткими герметичными доступными для сборки разборки и ремонта.
Фланцы для аппаратов стальные плоские приварные ОСТ 26-426-79. Ру = 06 Мпа таблица 13.7 [15 с. 233].
Фланцевые соединения стандартизованы для труб и трубной арматуры и отдельно для аппаратов.
Фланцы для труб и трубной арматуры стальные плоские приварные с соединительным выступом ГОСТ 1255-67 [12 с. 212].
Фланцы арматуры соединительных частей и трубопроводов из черных металлов цельные. ГОСТ 1255-67. РУ = 06 Мпа.
Выход пара из колонны
Выход жидкости из куба
Для выхода кубового остатка
Вход парожидкостной смеси
Вход пара в подогрев питания
Вход пара в кипятильник
Вход воды в дефлегматор
Вход воды в холодильник дистиллята
Вход воды в холодильник кубового остатка
5.Расчетная часть.doc
Пусть GD и GW – массовые расходы дистиллята и кубового остатка кгчас.
Уравнение материального баланса:
Из системы уравнений материального баланса определяем GD и GW:
GD = 18065 кгч GW = 41935 кгч.
Сделаем перерасчёт концентраций из массовых долей в мольные. МНК и МВК – мольные массы НК и ВК.
Кубовый остаток: (5)
Находим по диаграмме состав – состав (x – y) которую строю по данным о фазовом равновесии разделяемой бинарной системы [1 с.632] – мольная доля НК в паре равновесном с жидкостью питания.
Вычисляем минимальное флегмовое число:
Рабочее флегмовое число: R = 13Rmin + 03(7)
R = 130044+ 03 = 03576
Находим число питания: (8)
Составляем уравнения рабочих линий [2 с. 320]:
а) для верхней (укрепляющей) части колонны:
б) для нижней (исчерпывающей) части колонны:
2 Определение скорости пара и диаметра колонны.
Средние концентрации жидкости:
а) верх колонны (11)
Средние концентрации пара (по уравнениям рабочих линий):
а) верх колонны: (13)
б) низ колонны: (14)
Находим средние температуры пара и по диаграмме «температура – состав состав» (t – которую строим по равновесным данным [1 с.632]:
Средние мольные массы пара:
Определим средние плотности пара:
Средняя плотность пара в колонне:
Находим температуры флегмы и кубовой жидкости по диаграмме t – x y при xD и xW.По справочникам определяем:
а) плотность жидкого НК при tВ
б) плотность жидкого ВК при tН
Средняя плотность жидкости в колонне:
Максимально допустимую скорость пара в колонне определяем по формуле [2 с.322]:
Коэффициент вычисляем по формуле [3 с. 515]:
где H = 035 – межтарельчатое расстояние;
q = q0 = 25 м2ч – линейная плотность орошения т.е. отношение объёмного расхода к периметру слива П (длине сливной планки);
k1 = 115 k2 = 1 при атмосферном и повышенном давлениях k3 = 03410-3.
Вычисляем по формуле (21):
Определяем мольную массу дистиллята:
Средняя температура пара в колонне:
Объёмный расход пара в колонне:
Вычисляем диаметр колонны:
Из каталога “Колонные аппараты” выбираем ближайший диаметр колонны.
Периметр слива П можно определить также решением системы уравнений [2 с. 354]:
где R – радиус колонны.
Определяем по формуле:
- определяют по формуле (выведенной из системы уравнений[2 с. 354]):
Определяем среднюю мольную массу жидкости в верхней части колонны:
Объёмный расход в верхней части колонны:
Линейная плотность орошения в верхней части колонны
Сравниваем q1 c ранее принятым значением. Разность между ними небольшая значит принимаем q =15 м2ч.
3 Определение числа тарелок и высоты колонны.
Строим рабочую диаграмму процесса ректификации y- .
Находим по справочным данным коэффициент отклонения летучести компонентов и коэффициент динамической вязкости жидкой смеси [Па·с] при средней температуре в колонне:
РНК =2973 мм.рт.ст.
РВК =15866 мм.рт.ст. [2 с. 565]
Находим среднюю концентрацию жидкости в колонне:
Вязкость жидкой смеси находим по формуле:
Вычисляем произведение α:
α = 1870029= 538 (мПас)
Находим по рис. 7.4 [2 с.323] средний КПД тарелок ср= 032
Длина пути жидкости на тарелке l = D – 2b
l = 06 - 2009= 043 (м)
Так как l 09 то Δ = 0 следовательно средний КПД тарелок равен
Общее число тарелок в колонне: n = 4+7=11
Вычислим число действительных тарелок в верхней и нижней частях колонны с запасом 15 %:
Тарелка питания: nП = 7 115 = 8058. Значит тарелка питания имеет 8-й номер.
Высота тарельчатой части колонны:
HT = (13– 1)035 = 42 (м)
4 Гидравлический расчёт колонны.
4.1. Гидравлическое сопротивление тарелки равно сумме потерь напора на сухой тарелке и в слое жидкости:
а) верхняя часть колонны
Потеря напора на неорошаемой тарелке
– коэффициент сопротивления; для клапанной тарелки при полностью открытом клапане = 363
– скорость пара в отверстии:
где f – доля свободного сечения тарелки для клапанных тарелок с диаметром
D = 600 мм принимаем f = 009;
– средняя плотность пара в верхней части колонны.
Потеря напора в слое жидкости:
– высота сливной планки ориентировочно принимаем 60 мм(006м).
– подпор жидкости над сливной планкой. Подпор жидкости при прямой сливной планке:
где – объёмный расход жидкости в верхней части колонны м3ч.
H – межтарельчатое расстояние;
hn – высота сливной планки;
b – максимальная ширина сливного кармана;
y – вылет ниспадающей струи;
– градиент уровня жидкости;
h – подпор жидкости над планкой;
h – высота слоя невспененной жидкости.
– средняя плотность жидкости.
Определяем сопротивление орошаемой тарелки
б) нижняя часть колонны
Сопротивление сухой тарелки:
где – средняя плотность пара в нижней части колонны.
Средняя мольная масса жидкости в нижней части колонны:
Средняя мольная масса питания:
Объёмный расход жидкости в нижней части колонны:
Подпор жидкости над сливной планкой:
Сопротивление слоя жидкости на тарелке:
Сопротивление орошаемой тарелки:
Суммарное сопротивление всех тарелок:
4.2.Проверка работоспособности тарелок
Она проводится по величине межтарельчатого уноса жидкости или по пропускной способности переливного устройства.
Тарелка работает устойчиво при
– высота слоя вспененной жидкости в переливном кармане м.
y – вылет ниспадающей струи м.
b – стрелка сегмента (максимальная ширина переливного кармана)
где – высота слоя невспененной жидкости в сливном устройстве м.
– относительная плотность вспененной жидкости.
Высота слоя светлой жидкости:
где - подпор жидкости над сливной планкой в нижней части колонны;
– сопротивление тарелки в нижней части колонны;
Δ – градиент уровня жидкости на тарелке м. Для клапанных тарелок можно принять Δ = 0005.
– сопротивление движению жидкости в перетоке [5 с. 273]:
где – скорость жидкости в минимальном сечении переливного кармана: (56)
kж = 085 для среднепенящихся жидкостей;
* – скорость всплывания пузырей грибообразной формы:
– средний коэффициент поверхностного натяжения жидкости при средней температуре в колонне Нм.[10 c.282] [1 c.527]
Условие (51) выполняется.
Вылет струи [6 с. 199]
Условие (52) выполняется.
Рабочая скорость пара в отверстии тарелки не должна быть меньше минимальной скорости пара в отверстии тарелки обеспечивающей беспровальную работу клапанной тарелки [5 с. 285]:
беспровальная работа клапанной тарелки.
5 Тепловой расчёт установки.
5.1.Расход тепла отдаваемого парами воде при конденсации в дефлегматоре:
– теплота конденсации паров Джкг.
при [10 с.280] [2542]
5.2.Расход тепла получаемого кубовой жидкостью от греющего пара в кипятильнике:
СD и СW при tВ и tН СF при tF.
при [10 с.281] [2с.562]
5.3.Расход тепла в паровом подогревателе питания:
СF – принята при средней температуре
tнач – температура до подогревателя принимаемая равной 18°С.
5.4.Расход тепла отдаваемого дистиллятом воде в холодильнике:
– принята при средней температуре
tкон – температура после холодильника принимаемая равной 25°С.
5.5.Расход тепла принимаемого водой от кубового остатка в холодильнике
Расход греющего пара с давлением и степенью сухостью x =95%.
где - удельная массовая теплота конденсации греющего пара при давлении 4ат Джкг.
б) в подогревателе питания:
Всего пара: 01662 + 02691 = 04353 кгс или 15671 тч.
Расход охлаждающей воды при нагреве на 20°С.
Св – теплоёмкость воды при 20°С
б) в холодильнике дистиллята:
б) в холодильнике кубового остатка
Всего воды 20787 + 06138+ 51206=7813 кгс или 2813 тч.
6 Определение диаметров штуцеров
Диаметры штуцеров определяем из объёмного расхода и максимально допустимой скорости потока жидкости (газа) в штуцерах.
Скорость выбираем из таблицы 1.1 [2 с.17]. Поток жидкости при движении самотёком: = 01÷05 мс. Принимаем 03 мс для флегмы жидкости выходящей из куба в кипятильник и кубового остатка. Поток жидкости в напорных трубопроводах: = 15÷25 мс. Принимаем 2 мс для исходной смеси. Газы при атмосферном или близком к нему давлении: = 20÷40 мс. Принимаем = 35 мс для выходящих из колонны паров. Для парожидкостной смеси выходящей из кипятильника: = 20÷40 мс. Принимаем = 35 мс.
6.1.Диаметр штуцера ввода в колонну питания:
м3с – объёмный расход питания.(75)
при [2 с.512] [10 с.281]
= 2 мс – скорость жидкости в штуцере при питании.
Штуцер стандартного диаметра:
6.2.Диаметр штуцера подачи флегмы:
м3с – объёмный расход флегмы. (77)
= 03 мс – скорость флегмы в штуцере.
6.3.Диаметр штуцера вывода паров из колонны:
Массовый расход паров:
Gп= (R+1)GD= (039+1) 18065 3600= 0695 кгс
– объёмный расход паров из колонны;
= 35 мс – скорость паров в штуцере
Выбираем диаметр штуцера по ближайшим стандартным диаметрам таблица 10.2. [15с.175] d = 100 мм.
6.4.Диаметр штуцера вывода жидкости из куба:
Мольный расход флегмы:
Мольный расход питания:
Мольный расход кубовой жидкости:
Плотность кубовой жидкости примерно равна ρВК при tH: ρВК =89786кгм3
Объёмный расход кубовой жидкости :
= 03 мс – скорость в штуцере.
6.5.Диаметр штуцера вывода кубового остатка:
м3с – объёмный расход кубовой жидкости.(81)
= 03 мс – скорость жидкости в штуцере вывода кубовой жидкости.
6.6.Диаметр штуцера для ввода парожидкостной смеси:
м3с – объёмный расход флегмы.(82)
где Pн = Pб+P=101325+1897847=12030347 Па
Pб – барометрическое давление (101325 Па) тогда
кгм3 – плотность пара в колонне.
= 35 мс – скорость парожидкостной смеси в штуцере.
6.7.Диаметр штуцера для подогревателя питания:
плотность пара при абсолютном давлении
м3с – расход пара в подогреве питания.
6.8.Диаметр штуцера для кипятильника:
– объемный расход пара в кипятильнике.
6.9.Диаметр штуцера для дефлегматора:
м3с – расход воды в дефлегматоре
6.10.Диаметр штуцера для холодильника дистиллята:
м3с – расход воды в холодильнике дистиллята.
6.11.Диаметр для холодильника кубового остатка:
м3с – расход воды в холодильнике кубового остатка.
6.12.Диаметр штуцера для вывода дистиллята:
– объемный расход вывода дистиллята.
= 03 мс – скорость дистиллята в штуцере.
Штуцер стандартного диаметра: d = 50 мм.
7.Общие сведения.DOC
Бензол -органическое соединение C6H6 простейший ароматический углеводород; подвижная бесцветная летучая жидкость со своеобразным нерезким запахом; tnл55°C; tkип801°С; плотность 8791кг м3(08791гсм3) при 20°С;n20D15011. С воздухом в объёмной концентрации 15—8% бензол образует взрывоопасные смеси. Бензол смешивается во всех соотношениях с эфиром бензином и др. органическими растворителями; в 100г бензола при 26°С растворяется 0054гводы; с водой образует азеотропную (постоянно кипящую) смесь (912% бензола по массе) сtkип6925°С.
Бензол содержится в продуктах сухой перегонки каменного угля (коксовом газе) и небольшое количество — в коксовой смоле. Значительные количества бензола получают также каталитической циклизацией алифатических углеводородов нефти. Бензол — важнейшее сырьё химической промышленности. При действии азотной кислоты на бензол образуется нитробензолС6Н5NО2 который может быть восстановлен в анилин C6H5NH2— исходный продукт в производстве многих красителей. При взаимодействии бензола с серной кислотой получается бензолсульфокислота C6H5SO2OH щелочное плавление солей которой — один из основных методов производствафенола. При алкилировании бензола этиленом в присутствии хлористого алюминия получается этилбензол каталитическое дегидрирование которого представляет собой основной способ производствастиролаC6H5CH=CH2. Аналогично из бензола и пропилена образуется изопропилбензол C6H5CH (CH3)2— исходный продукт для получения фенола иацетонав промышленном масштабе. Широко применяют и галогенопроизводные бензола. Так хлорбензол омыляется в фенол; из хлорбензола и магния Гриньяра реакциейполучают фенилмагнийхлорид C6H5MgCI при реакции которого с окисью этилена образуется b-фенилэтиловый спирт C6H5CH2CH2OH используемый в парфюмерии как искусственное розовое масло. При каталитическом гидрировании бензол превращается в циклогексан — исходный продукт в одном из способов производства капролактама полимеризацией которого получают синтетическое волокно "капрон". При облучении бензол присоединяет 3 моля хлора с образованием смеси стереоизомерных гексахлорциклогексанов один из которых (гексахлоран) обладает сильными инсектицидными свойствами. Бензол применяют в производстве взрывчатых веществ а также как растворитель и экстрагирующее средство в производстве лаков красок и др.
Действие на организм. Бензол может вызывать острые и хронические отравления. Проникает в организм главным образом через органы дыхания может всасываться и через неповрежденную кожу. Предельно допустимая концентрация паров бензола в воздухе рабочих помещений 20 мгм3. Выводится через лёгкие и с мочой. Острые отравления происходят обычно при авариях; их наиболее характерные признаки: головная боль головокружение тошнота рвота возбуждение сменяющееся угнетённым состоянием частый пульс падение кровяного давления в тяжёлых случаях — судороги потеря сознания. Хроническое отравление бензолом проявляется изменением крови (нарушение функции костного мозга) головокружением общей слабостью расстройством сна быстрой утомляемостью; у женщин — нарушением менструальной функции. Надёжная мера против отравлений парами бензола — хорошая вентиляция производственных помещений.
Лечение при острых отравлениях: покой тепло бромистые препараты сердечно-сосудистые средства; при хронических отравлениях с выраженной анемией: переливание эритроцитарной массы витамин B12 препараты железа.
Анилин(франц. an впервые анилин был получен изиндиго) аминобензол фениламин C6H5NH2 простейший ароматический амин; бесцветная жидкость со слабым запахом; tnл—615°С;tkип1844°C; плотность при 20°C 1027кгм3 показатель преломления
Анилин растворим в воде (34гв 100гводы при 20°C) смешивается во всех соотношениях со спиртом эфиром бензолом; с рядом металлов (К Na Ca Mg и др.) образует металлические производные например C6H5NHNa. Анилин обладает основными свойствами более слабо выраженными чем у алифатических аминов (константа диссоциацииК= 45·10-10). С минеральными кислотами анилин образует соли например солянокислый анилин C6H5NH3Cl применяемый в ситцепечатании.
Основной метод производства анилин восстановление нитробензола нагреванием с чугунной стружкой в присутствии небольшого количества соляной кислоты:
Применяют также и другие методы: восстановление нитробензола (катализатор — карбонат меди) аммонолиз хлорбензола и др. Анилин был открыт несколькими химиками независимо друг от друга; синтетически впервые получен Н. Н.Зининымв 1842 восстановлением нитробензола сернистым аммонием.
Вредное действие анилина и техника безопасности. Анилин ядовит действует на центральную нервную систему вызывает в крови образование метгемоглобина и дегенеративные изменения эритроцитовгемолиз следствием чего является кислородное голодание организма. Анилин проникает в организм через органы дыхания в виде паров а также при всасывании через кожу и слизистые оболочки которое особенно усиливается при повышении температуры воздуха и приёме алкоголя. Возможны острые и хронические (анилизм) отравления анилином. При лёгком отравлении анилином наблюдаются слабость головокружение головная боль синюшность губ ушных раковин ногтей. При отравлениях средней тяжести присоединяется тошнота иногда рвота появляется шатающаяся походка; пульс учащён. Тяжёлые случаи отравления встречаются крайне редко. При хронических отравлениях — токсическийгепатит нервно-психические нарушения расстройство сна снижение памяти и т. д.
Первая помощь — удаление пострадавшего из очага отравления обмывание тёплой (не горячей!) водой вдыхание кислорода с карбогеном; применяют кровопускание введение антидотов (метиленовая синь) сердечно-сосудистые средства покой.
Профилактика — механизация и герметизация производственных процессов вентиляция строгое соблюдение правил техники безопасности и промышленной санитарии. Предельно допустимая концентрация анилина в воздухе рабочей зоны 3мгм3. Средства индивидуальной защиты: фильтрующий противогаз марки "А" непроницаемая для анилина спецодежда душ и смена одежды после работы. Обязательны периодические медицинские осмотры работающих с анилином. Предельно допустимая концентрация анилина в водоёмах (при их промышленном загрязнении) 01мгл(100мгм3).
Техника безопасности ведения процесса.
Одно из основных условий безопасной эксплуатации ректификационных колонн – обеспечение их герметичности.
Причинами нарушения герметичности могут быть:
– повышение давления в аппарате сверх допустимого;
– недостаточная компенсация увеличения линейных размеров при температурных нагрузках;
– коррозия и эрозия корпуса;
– механические повреждения;
– наиболее опасной причиной резкого повышения давления в колонне могут быть
попадание в нее воды.
Мгновенное испарение воды вызывает столь быстрое парообразование и повышения давления что предохранительные клапаны в силу своей инерционности не успевают сработать и может произойти взрыв стенок аппарата. Для исключения попадания воды в колонну необходимо следить за целостностью трубок в подогревателе куба в оросительных холодильниках. Повышение давления в колонне может произойти так же вследствие нарушения температурного режима процесса ректификации и превышения пропускной способности колонны по сырью.
При входе сырья в колонны его парожидкостная струя имеет большие скорости что может вызвать эрозию стенок аппарата. Для защиты корпуса аппарата сырье вводят в полость специального устройства- улиты которая снабжена отбойным местом принимающим удар струи и защитной гильзой занимаемой по мере износа.
Одной из причин механического повреждения колонны является вибрация вызываемая неудовлетворительным креплением корпуса к фундаменту и неправильным присоединением обвязывающих трубопроводов. Вибрацию вызывают ветровые потоки пульсирующая подача продукта поршневыми насосами и компрессорами. [7 c.317]
3.Введение.DOC
Для разделения смесей жидкостей и сжиженных газов в промышленности применяют следующие способы: простую перегонку (дистилляцию) перегонку под вакуумом и с водяным паром молекулярную перегонку и ректификацию.
Ректификацию широко используют в промышленности для полного разделения смесей летучих жидкостей частично или целиком растворимых одна в другой.
Сущность процесса ректификации сводится к выделению из смеси двух или нескольких жидкостей с различными температурами кипения в более или менее чистом виде. Это достигается нагреванием и испарением такой смеси с последующим многократным тепло- и массообменном между жидкой и паровой фазами. В результате часть легколетучего компонента переходит из жидкой фазы в паровую а часть менее летучего компонента – из паровой фазы в жидкую
Таким образом ректификация – разделение жидких бинарных или многокомпонентных смесей и сжиженных газов на отдельные компоненты или фракции многократным контактом неравновесных восходящей паровой и нисходящей жидкой фаз.
При ректификации исходная смесь делится на две части:
часть обогащённую легколетучим компонентом (ЛЛК) – дистиллят (НК);
часть обеднённую легколетучим компонентом – кубовый остаток (ВК).
Процесс ректификации может протекать при атмосферном давлении а также при давлениях выше и ниже атмосферного. Под вакуумом ректификацию про-
водят когда разделению подлежат высококипящие жидкости. Повышение дав-ления применяют для разделения смесей находящихся в газообразном состоянии при более низком давлении.
Степень разделения смеси жидкостей на составные компоненты и чистота получаемого дистиллята и кубового остатка зависят от того насколько развита поверхность фазового контакта а следовательно от количества орошающей жидкости (флегмы) и устройства ректификационной колонны.
В промышленности применяют колпачковые ситчатые насадочные плёночные трубчатые колонны и центробежные плёночные ректификаторы. Они различаются конструкцией внутреннего устройства аппарата назначение которого – обеспечение взаимодействия жидкости и пара. Это взаимодействие происходит при барботировании пара через слой жидкости на тарелках (колпачковых или ситчатых) либо при поверхностном контакте пара или жидкости на насадке или поверхности жидкости стекающей тонкой плёнкой.
При использовании ректификационных колонн с клапанными тарелками они показали высокую эффективность при значительных интервалах нагрузок благодаря возможности саморегулирования. В зависимости от нагрузки клапан перемещается вертикально изменяя площадь живого сечения для прохода пара причём максимальное сечение определяется высотой устройства ограничивающего подъём. Клапаны изготовляют в виде пластин круглого или прямоугольного сечения с верхним или нижним ограничителем подъёма.
Процесс ректификации может осуществляться по периодической и непрерывной схемам. В нефтеперерабатывающей промышленности в основном применяют ректификационные колонны непрерывного действия. Для разделения бинарной смеси обычно достаточно одной простой колонны.
Основными рабочими параметрами процесса ректификации является давление и температура в системе соотношение потоков жидкости и пара и число контактных ступеней.
При соответствующем выборе этих параметров обеспечивается разделение исходной смеси на фракции удовлетворяющие определённым требованиям.
Титульник.doc
Федерального государственного образовательного учреждения
Высшего профессионального образования
«Казанский национальный исследовательский технологический университет»
Ректификационная колонна
Пояснительная записка и расчёты к курсовому проекту
РК 30. 01. 00. 00. 000 ПЗ
Руководитель:Гарипов М.Г.
Бензол.doc
Бензол содержится в продуктах сухой перегонки каменного угля (коксовом газе) и небольшое количество — в коксовой смоле. Значительные количества бензола получают также каталитической циклизацией алифатических углеводородов нефти. Бензол — важнейшее сырьё химической промышленности. При действии азотной кислоты на бензол образуется нитробензолС6Н5NО2 который может быть восстановлен в анилин C6H5NH2— исходный продукт в производстве многих красителей. При взаимодействии бензола с серной кислотой получается бензолсульфокислота C6H5SO2OH щелочное плавление солей которой — один из основных методов производствафенола. При алкилировании бензола этиленом в присутствии хлористого алюминия получается этилбензол каталитическое дегидрирование которого представляет собой основной способ производствастиролаC6H5CH=CH2. Аналогично из бензола и пропилена образуется изопропилбензол C6H5CH (CH3)2— исходный продукт для получения фенола иацетонав промышленном масштабе. Широко применяют и галогенопроизводные бензола. Так хлорбензол омыляется в фенол; из хлорбензола и магния Гриньяра реакциейполучают фенилмагнийхлорид C6H5MgCI при реакции которого с окисью этилена образуется b-фенилэтиловый спирт C6H5CH2CH2OH используемый в парфюмерии как искусственное розовое масло. При каталитическом гидрировании бензол превращается в циклогексан — исходный продукт в одном из способов производства капролактама полимеризацией которого получают синтетическое волокно "капрон". При облучении бензол присоединяет 3 моля хлора с образованием смеси стереоизомерных гексахлорциклогексанов один из которых (гексахлоран) обладает сильными инсектицидными свойствами. Бензол применяют в производстве взрывчатых веществ а также как растворитель и экстрагирующее средство в производстве лаков красок и др.
Действие на организм. Бензол может вызывать острые и хронические отравления. Проникает в организм главным образом через органы дыхания может всасываться и через неповрежденную кожу. Предельно допустимая концентрация паров бензола в воздухе рабочих помещений 20 мгм3. Выводится через лёгкие и с мочой. Острые отравления происходят обычно при авариях; их наиболее характерные признаки: головная боль головокружение тошнота рвота возбуждение сменяющееся угнетённым состоянием частый пульс падение кровяного давления в тяжёлых случаях — судороги потеря сознания. Хроническое отравление бензолом проявляется изменением крови (нарушение функции костного мозга) головокружением общей слабостью расстройством сна быстрой утомляемостью; у женщин — нарушением менструальной функции. Надёжная мера против отравлений парами бензола — хорошая вентиляция производственных помещений.
Лечение при острых отравлениях: покой тепло бромистые препараты сердечно-сосудистые средства; при хронических отравлениях с выраженной анемией: переливание эритроцитарной массы витамин B12 препараты железа.
Анилин(франц. an впервые анилин был получен изиндиго) аминобензол фениламин C6H5NH2 простейший ароматический амин; бесцветная жидкость со слабым запахом; tnл—615°С;tkип1844°C; плотность при 20°C 1027кгм3 показатель преломления
Анилин растворим в воде (34гв 100гводы при 20°C) смешивается во всех соотношениях со спиртом эфиром бензолом; с рядом металлов (К Na Ca Mg и др.) образует металлические производные например C6H5NHNa. Анилин обладает основными свойствами более слабо выраженными чем у алифатических аминов (константа диссоциацииК= 45·10-10). С минеральными кислотами анилин образует соли например солянокислый анилин C6H5NH3Cl применяемый в ситцепечатании.
Основной метод производства анилин восстановление нитробензола нагреванием с чугунной стружкой в присутствии небольшого количества соляной кислоты:
Применяют также и другие методы: восстановление нитробензола (катализатор — карбонат меди) аммонолиз хлорбензола и др. Анилин был открыт несколькими химиками независимо друг от друга; синтетически впервые получен Н. Н.Зининымв 1842 восстановлением нитробензола сернистым аммонием.
Вредное действие анилина и техника безопасности. Анилин ядовит действует на центральную нервную систему вызывает в крови образование метгемоглобина и дегенеративные изменения эритроцитовгемолиз следствием чего является кислородное голодание организма. Анилин проникает в организм через органы дыхания в виде паров а также при всасывании через кожу и слизистые оболочки которое особенно усиливается при повышении температуры воздуха и приёме алкоголя. Возможны острые и хронические (анилизм) отравления анилином. При лёгком отравлении анилином наблюдаются слабость головокружение головная боль синюшность губ ушных раковин ногтей. При отравлениях средней тяжести присоединяется тошнота иногда рвота появляется шатающаяся походка; пульс учащён. Тяжёлые случаи отравления встречаются крайне редко. При хронических отравлениях — токсическийгепатит нервно-психические нарушения расстройство сна снижение памяти и т. д.
Первая помощь — удаление пострадавшего из очага отравления обмывание тёплой (не горячей!) водой вдыхание кислорода с карбогеном; применяют кровопускание введение антидотов (метиленовая синь) сердечно-сосудистые средства покой.
Профилактика — механизация и герметизация производственных процессов вентиляция строгое соблюдение правил техники безопасности и промышленной санитарии. Предельно допустимая концентрация анилина в воздухе рабочей зоны 3мгм3. Средства индивидуальной защиты: фильтрующий противогаз марки "А" непроницаемая для анилина спецодежда душ и смена одежды после работы. Обязательны периодические медицинские осмотры работающих с анилином. Предельно допустимая концентрация анилина в водоёмах (при их промышленном загрязнении) 01мгл(100мгм3).
Предназначаются фланцы стальные для герметичного и надежного соединения трубопроводной арматуры и самих трубопроводов.doc
В соответствии с российскими стандартами выпускаются следующие фланцы стальные:
- фланцы стальные плоские приварные;
- фланцы воротниковые;
- фланцы стальные свободные на приварном кольце.
Первый тип - фланцы стальные плоские приварные производятся в соответствии с требованиями ГОСТ 12820-80; фланцы стальные плоские предназначены для эксплуатации при температуре от -70 до 450 °С.
Второй тип - фланцы воротниковые которые привариваются встык производятся в соответствии с ГОСТом 12821-80; фланцы стальные воротниковые используются при температуре от -253 до 600 °С.
Третий тип – стальные фланцы приварные на специальном кольце также выпускаются по ГОСТу 12822-80 и такие фланцы приварные на кольце имеют отличия выраженные в удобстве монтажа. Поэтому область применения фланцев с приварным кольцом – это проведение регулярного ремонта или труднодоступные места трубопровода.
o2.2Электродуговая сварка
2.1Сварка неплавящимся электродом
2.2Сварка плавящимся электродом
2.2.1Ручная дуговая сварка
2.3Сварка под флюсом
o2.3Газопламенная сварка
o2.4Электрошлаковая сварка
o2.5Плазменная сварка
o2.6Электронно-лучевая сварка
o2.8Контактная стыковая сварка оплавлением
o2.9Сварка с закладными нагревателями
Термомеханический класс
o3.1Контактная сварка
o3.2Диффузионная сварка
o3.3Кузнечная сварка
o3.4Сварка высокочастотными токами
o4.2Ультразвуковая сварка металлов
4.Схема рект.установки.doc
Рис.1 Принципиальная схема ректификационной установки:
- ёмкость для исходной смеси; 29-насосы; 3-теплообменник-подогреватель; 4- кипятильник; 5-ректификационная колонна; 6-дефлегматор; 7-холодильник дистиллята; 8-Ёмкость для сбора дистиллята; 10-холодильник кубовой жидкости; 11-ёмкость для кубовой жидкости.
Принцип действия. Исходная смесь в жидком виде после подогрева в подогревателе питания обычно до температуры кипения поступает в колонну на тарелку питания. Затем питание смешивается с жидкостным потоком флегмы.
Образовавшаяся жидкая смесь самотеком стекает в нижнюю (кубовую) часть колонны. Часть кубовой жидкости отбирается в количестве GW в виде готового продукта (кубового остатка). Другая часть после испарения в кипятильнике обычно в паро-жидкостном виде возвращается в кубовую часть колонны.
Паровая фаза поднимается через все тарелки в верхнюю часть колонны затем она поступает в дефлегматор где частично или полностью конденсируется. Часть конденсата в количестве GR возвращается на верхнюю тарелку колонны для ее жидкостного орошения. Цель возвращения флегмы- повышение четкости разделения смеси за счет дополнительного контакта паровой и жидкой фаз. Другая часть конденсата отбирается в виде готового продукта- дистиллята.
Назначение гидрозатвора- не допущение паров конденсата минуя дефлегматор.
колонна 600.cdw

Аппарат предназначен для разделения смеси бензол - анилин с
Емкость номинальная 2
Производительность 6000 кгч
Давление в колонне 0
Температура в кубе 166
Среда в аппарате токсичная
Тип тарелок - клапанный.
Технические требования.
испытании и поставке аппарата должны
выполняться требования:
3 - 76 " Оборудование производственное. Общие
требования безопасности ".
б) ОСТ 26 - 291 - 79 "Сосуды и аппараты стальные сварные.
Технические требования".
Материал тарелок и частей колонны соприкасающиеся с
разделяемыми жидкостями или их парами из стали 12Х18Н10Т ГОСТ
остальные элементы колонны - из стали СТ 3. ГОСТ
Аппарат испытать на прочность гидравлически:
а) в горизонтальном положении - давлением 0
б) в вертикальном положении - наливом.
Сборные соединения должны соответствовать требованиям ОН
-01-71-68 "Сварка в химическом машиностроении". Сварку
производить электродами марки АНО-5-4
Сборочные швы в объеме 100% контролировать
рентгенопросвечиванием.
Действительное расположение штуцеров и цапф смотри на
Размеры для справок
Вход парожидкостной смеси
Выход жидкости из куба
Для выхода кубового остатка
Схема расположения штуцеров и цапф
Спецификация.cdw

РК 30.01.00.00.000 ПЗ
РК 30.01.00.00.000 ТС
Пояснительная записка
Технологическая схема
Гайка М20 ГОСТ 5915-70
Шайба 20 Н ГОСТ 6402-70
Болт М20 х 90 ГОСТ 7798-70
Схема.cdw

Наименование среды в трубопроводе
Паро - жидкостная эмульсия
Точка замера и контроля
Контролируемый параметр
Колонна ректификационная
Вентиль регулирующий
РК 30.01.00.00.000 ТС
Технологическая схема
Приложение.doc
Диаграмма «состав – состав» для бинарной смеси «бензол - анилин» при атмосферном давлении ( Р=760 мм.рт.ст.).
Диаграмма «температура – состав состав» для бинарной смеси «бензол - анилин» при атмосферном давлении ( Р=760 мм.рт.ст.).
2.Содержание.doc
Схема ректификационной установки. Принцип действия.
1.Материальный баланс.
2.Определение скорости пара и диаметра колонны.
3.Определение числа тарелок и высоты колонны.
4.Гидравлический расчет колонны.
5.Тепловой расчет установки.
6.Расчет диаметров штуцеров.
Подбор стандартных изделий.
Общие сведения о компонентах смеси и техника безопасности
1.Задание.doc
= 96 % (масс.) = 3 % (масс.).
Рекомендуемые чертежи
- 24.01.2023
- 15.04.2023
- 25.01.2023
- 25.01.2023
- 25.01.2023