Редуктор цилиндрический косозубый одноступенчатый горизонтальная компоновка




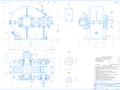
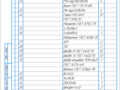

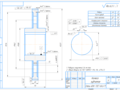
- Добавлен: 24.01.2023
- Размер: 798 KB
- Закачек: 2
Описание
Редуктор цилиндрический косозубый одноступенчатый горизонтальная компоновка
Состав проекта
![]() |
![]() |
![]() |
![]() |
![]() ![]() ![]() |
![]() ![]() ![]() ![]() |
![]() ![]() ![]() ![]() |
![]() ![]() ![]() ![]() |
![]() ![]() ![]() ![]() |
![]() ![]() ![]() |
![]() ![]() ![]() ![]() |
Дополнительная информация
ш пояснительная2.docx
Требуемую мощность электродвигателя определяют на основании исходных данных. Потребляемую мощность (кВт) привода (мощность на выходе) определяют по формуле
где - момент на тихоходном валу 320; - частота вращения тихоходного вала n2 = 300; - коэффициент полезного действия (КПД) привода в общем случае равный произведению частных КПД ступеней редуктора:
где - КПД подшипников ; - КПД цилиндрической зубчатой передачи (см. табл. 1.1).
Требуемая мощность электродвигателя .
Таблица 1.1 Средние значения КПД механических передач
закрытая червячная при числе заходов червяка:
2 Определение частоты вращения вала электродвигателя
Требуемая частота вращения вала электродвигателя () определяется по формуле:
где - передаточное отношение привода.
В дальнейших расчётах вместо передаточного отношения применяют передаточное число
где - число зубьев шестерни; - число зубьев колеса .
Применение u вместо i связано только с принятой формой расчётных зависимостей для контактных напряжений значения которых не зависят от того какое из зубчатых колёс является ведущим.
Руководствуясь рекомендациями по выбору значений передаточных чисел в соответствии с заданным типом передачи в редукторе (см. табл. 1.2) определяем возможный диапазон частот вращения вала электродвигателя:
Таблица 1.2 Рекомендуемые значения
передаточных чисел одноступенчатого редуктора
Допускаемые отклонения
зубчатая цилиндрическая
зубчатая коническая
По рассчитанной мощности и диапазону из табл. 1.3 выбираем электродвигатель таким образом чтобы его номинальная мощность а номинальная частота вращения вала была самой близкой (из возможных вариантов) к большему значению диапазона . В этом случае размеры и стоимость электродвигателя будут наименьшими.
Электродвигатель – 4A132M4У3 кВт n ном = 1460.
По выбранному электродвигателю определяем расчётное передаточное число зубчатой передачи редуктора:
Номинальная мощность кВт
Синхронная частота вращения обмин
Таблица 1.3 Двигатели асинхронные короткозамкнутые серии 4A общепромышленного применения; закрытые обдуваемые. Технические данные
Примечание: Структура обозначения типоразмера двигателя (расшифровывается слева направо): 4 - порядковый номер серии; А - вид двигателя - асинхронный; А - станина и щиты двигателя алюминиевые (отсутствие знака означает что станина и щиты чугунные или стальные); двух - или трёхзначное число - высота оси вращения ротора; А В - длина сердечника статора; L S М - установочный размер по длине станины; 2 4 6 8 - число полюсов; УЗ - климатическое исполнение и категория размещения (для работы в зонах с умеренным климатом) по ГОСТ 15150-69.
Расчёт зубчатой передачи
1 Выбор материалов зубчатых передач и вида термообработки
При выборе материала зубчатых колёс следует учитывать назначение проектируемой передачи условия эксплуатации требования к габаритным размерам и возможную технологию изготовления колёс. Основным материалом для изготовления зубчатых колёс является сталь. Необходимую твёрдость в сочетании с другими механическими характеристиками (а следовательно желаемые габариты и массу передачи) можно получить за счет назначения соответствующей термической или химико-термической обработки стали.
В условиях индивидуального и мелкосерийного производства в мало- и средненагруженных передачах а также в передачах с большими габаритами колёс (когда термическая обработка их затруднена) обычно применяют стали с твёрдостью не более 350 НВ которая обеспечивается нормализацией или термоулучшением материала. При этом возможно чистовое нарезание зубьев непосредственно после термообработки с высокой точностью изготовления а при работе передачи обеспечивается хорошая прирабатываемость зубьев без хрупкого разрушения их при динамических нагрузках.
Для равномерного изнашивания зубьев и лучшей их прирабатываемости твёрдость шестерни рекомендуют назначать больше твердости колеса не менее чем на (10 15) НВ.
Основные механические характеристики выбранных материалов приведены в табл. 2.1.
Таблица 2.1 Механические характеристики сталей
2. Расчёт допускаемых напряжений
Допускаемые контактные напряжения. Допускаемое контактное напряжение (МПа) рассчитывают для каждого зубчатого колеса передачи по формуле:
где (МПа) - предел контактной выносливости - коэффициент безопасности - коэффициент долговечности.
Предел контактной выносливости вычисляют по эмпирическим формулам в зависимости от материала и способа термической обработки зубчатого колеса и средней твердости ( или ) на поверхности зубьев (см. табл. 2.2). Коэффициент безопасности рекомендуют назначать при нормализации термоулучшении или объемной закалке зубьев (при однородной структуре материала по всему объему); при поверхностной закалке цементации азотировании (при неоднородной структуре материала по объему зуба).
Таблица 2.2 Твердость на поверхности зубьев
Коэффициент долговечности вычисляется по формуле
где - базовое число циклов перемены напряжений; - расчётное число циклов напряжений.
Коэффициент учитывает возможность повышения допускаемых напряжений для кратковременно работающих передач ().
Расчёт числа циклов перемены напряжений выполняют с учетом режима нагружения передачи. Различают режимы постоянной и переменной нагрузки. При постоянном режиме нагрузки расчётное число циклов напряжений вычисляют по формуле
где - число зацеплений зуба за один оборот (для проектируемого редуктора ); - частота вращения того зубчатого колеса по материалу которого определяют допускаемые напряжения n1 = 1460 обмин; - время работы передачи (ресурс) в часах t = Lh = 10000 часов.
N h1 = 60*1*1460*10000 = 0.876*.
N h2 = 60*1*300*10000 = 1.8*.
Постоянный режим нагрузки является наиболее тяжёлым для передачи поэтому его принимают за расчетный также в случае неопределенного (незадаваемого) режима нагружения.
Режим работы передачи с переменной нагрузкой при расчёте допускаемых контактных напряжений заменяют некоторым постоянным режимом эквивалентным по усталостному воздействию. При этом в формулах расчётное число циклов перемены напряжений заменяют эквивалентным числом циклов до разрушения при расчетном контактном напряжении
где - коэффициент эквивалентности режим 0 (см. табл. 2.3).
N he1 = 1*0.876* = 0.876*.
N he2 = 1*1.8* = 1.8*.
Таблица 2.3 Коэффициент эквивалентности для типовых режимов
Расчет на изгибную усталость
Термическая обработка
закалка объемная поверхностная цементация
Базовое число циклов перемены напряжений соответствующее пределу контактной выносливости рассчитывают по эмпирическим следующим зависимостям:
Если то следует принимать .
Из двух полученных значений за расчётное допускаемое контактное напряжение принимают для косозубых (цилиндрических и конических) передач - меньшее из двух значений и то есть МПа.
Допускаемые напряжения изгиба. Расчёт зубьев на изгибную выносливость выполняют отдельно для зубьев шестерни и колеса для которых вычисляют допускаемые напряжения изгиба по формуле
где (МПа) - предел выносливости зубьев по напряжениям изгиба (см. табл. 2.2); - коэффициент учитывающий влияние двустороннего приложения нагрузки при односторонней нагрузке ; - коэффициент долговечности; - коэффициент безопасности .
Методика расчёта коэффициента долговечности аналогична расчету .
Базовое число циклов перемены напряжений рекомендуют принимать для всех сталей .
При постоянном режиме нагружения передачи расчётное число циклов напряжений вычисляют по формуле
N fe1 = N h1 = 60*1*1460*10000 = 0.876*.
N fe2 = N h2 = 60*1*300*10000 = 1.8*.
При переменных режимах нагрузки подчиняющихся типовым режимам нагружения
где - коэффициент эквивалентности = 1 (см. табл. 2.3).
N fe1 = * N f1 = 1*0.876* = 0.876*.
N fe2 = * N f2 = 1*1.8* = 1.8*.
При следует принимать .
3 Проектный расчёт закрытой цилиндрической зубчатой передачи
При проектном расчёте прежде всего определяют главный параметр цилиндрической передачи - межосевое расстояние в мм. Для косозубой передачи межосевое расстояние определяют по следующей формуле
где ; - коэффициент неравномерности нагрузки по длине контакта (см. табл. 2.4); - приведенный модуль упругости для стали МПа; - относительная ширина колес (см. табл. 2.5).
Полученное значение межосевого расстояния округляем до ближайшего большего значения по ряду нормальных линейных размеров.
В дальнейшем в расчетах может встретиться относительная ширина колес которую рассчитывают с учётом зависимости
Таблица 2.4 - Коэффициент нагрузки
Расположение шестерни относительно опор
Твердость на поверхности зубьев колеса HB
и в зависимости от коэффициента
Консольное опоры - шарикоподшипники
Консольное опоры - роликоподшипники
Таблица 2.5 Относительная ширина колёс
Схема расположения колёс относительно опор
Твёрдость рабочих поверхностей зубьев
4 Геометрический расчёт закрытой цилиндрической передачи
Определяем модуль зацепления из соотношения . Полученное значение модуля необходимо округлить до стандартного значения по 1-му ряду модулей: 10; 125; 15; 2; 25; 3; 4; 5; 6; 8; 10 мм.
mn = (0.01 0.02)*140 = 1.4 2.8 = 2 мм.
Для косозубой передачи угол наклона линии зуба назначаем в пределах = 8 20. Примем = 14.
Определяем суммарное число зубьев шестерни и колеса
zΣ = z1 + z2 = 135.8136.
Определяем число зубьев шестерни
Определяем число зубьев колеса
z2 = zΣ – z1 = 136 - 23 = 113.
Определяем фактическое значение передаточного числа передачи
Определяем фактическое межосевое расстояние
Для косозубой передачи уточняем значение фактического угла наклона линии зуба .
Рабочая ширина зубчатого венца колеса
Рабочую ширину зубчатого венца колеса округляем до ближайшего большего значения по ряду нормальных линейных размеров bw = 56 мм тогда ширина зубчатого венца колеса b2 = bw = 56 мм.
Ширина зуба шестерни: b1 = b2+ (2 5) = 56+4 = 60 мм.
Делительные диаметры рассчитывают по формуле .
Начальный диаметр шестерни
Начальный диаметр колеса передачи
dw2 = = = 232.622 мм.
Диаметры вершин зубьев колес рассчитывают по формуле .
da1 = d1 +2*m = 47.5+2*2 = 51.5мм.
da2 = d2 +2*m = 233+2*2 = 237 мм.
Диаметры впадин зубьев колес рассчитывают по формуле .
df1 = d1 – 2.5*m = 47.5-2.5*2 = 42.5 мм.
df2 = d2 – 2.5*m = 233-2.5*2 = 228 мм.
Угол зацепления передачи принимают равным углу профиля исходного контура: .
5 Проверочный расчёт закрытой цилиндрической передачи
Проверка контактной выносливости рабочих поверхностей зубьев колёс. Расчётом должна быть проверена справедливость соблюдения следующего неравенства
где - коэффициент повышения прочности косозубых передач по контактным напряжениям; () - вращающий момент на шестерне проверяемой передачи; - коэффициент внутренней динамической нагрузки.
Величину вращающего момента на шестерне проверяемой передачи рассчитывают по формуле
где - КПД передачи он учитывает потери мощности в зубчатой передаче .
Коэффициент повышения прочности косозубых передач по контактным напряжениям рассчитывают по формуле
где - коэффициент торцового перекрытия зубчатой передачи.
Коэффициент торцового перекрытия зубчатой передачи рассчитывают по формуле
y = a где = b * sin ( * m) = 56 * sin 14 (3.14 * 2) = 2.157
y = 1.661 + 2.157 = 3.818
Для определения коэффициента внутренней динамической нагрузки необходимо по табл. 2.6 назначить степень точности передачи в зависимости от окружной скорости () в зацеплении
Таблица 2.6 Степени точности зубчатых передач
Окружные скорости вращения колёс V мс
При окружной скорости вращения колёс для косозубых передач V степень точности равна 9. Затем по табл. 2.7 для рассчитываемой передачи находим значение коэффициента = 1.05.
В косозубой передаче теоретически зацепляется одновременно не менее двух пар зубьев. На практике ошибки нарезания зубьев могут устранить двухпарное зацепление и при контакте одной пары между зубьями второй пары может быть небольшой зазор который устраняется под нагрузкой вследствие упругих деформаций зубьев. Однако первая пара зубьев нагружена больше чем вторая на размер усилия необходимого для устранения зазора. Это учитывают коэффициентом KH назначаемым из табл. 2.8 KH=1.13.
Зная KH рассчитаем коэффициент повышения прочности косозубых передач по контактным напряжениям
В результате проверки выявилась недогрузка
С целью более полного использования возможностей материалов зубчатых колёс возможна корректировка рабочей ширины зубчатого венца по соотношению.
Рабочую ширину зубчатого венца колеса округляем до ближайшего большего значения по ряду нормальных линейных размеров bw =20 мм тогда ширина зубчатого венца колеса b2 = bw = 20 мм.
Ширина зуба шестерни: b1 = b2 + (2 5) = 20+4 = 24 мм.
Теперь в результате проверки существенная недогрузка (свыше 10%) не выявилась и корректировка рабочей ширины зубчатого венца не требуется.
Таблица 2.7 Значения коэффициентов KНV и KFV
Твердость поверхностей зубьев
Окружная скорость V мс
Верхние цифры относятся к прямым зубьям нижние к косым зубьям.
Таблица 2.8 Значения коэффициентов KH и KF
Проверка прочности зубьев по напряжениям изгиба. Расчёт выполняют отдельно для шестерни и для зубчатого колеса передачи после уточнения нагрузок на зубчатые колёса и их геометрических параметров.
Проверяют справедливость соотношения расчётных напряжений изгиба и допускаемых напряжений по следующему неравенству
где (H) - окружная сила в зацеплении колёс; - коэффициент неравномерности распределения нагрузки по длине линии контакта = 1.14 (см. табл. 2.4); -коэффициент внутренней динамической нагрузки= 1.14 (см. табл. 2.7); - коэффициент формы зуба 1 = 3.982 = 3.6 (см. табл. 2.9).
Окружное усилие в зацеплении колёс рассчитывают по формуле
Таблица 2.8 Коэффициент формы зуба YF
6 Расчёт открытой цилиндрической зубчатой передачи
Для проектного расчёта открытых передач по напряжениям изгиба определяют модуль зацепления из выражения
где z3 число зубьев шестерни открытой передачи (см. исходные данные);
коэффициент ширины зубчатого венца колеса относительно начального диаметра шестерни рекомендуют назначать для открытых передач bd = 01 20; [F1] допускаемое напряжение изгиба зубьев шестерни Нмм2 определяют в соответствии с п. 2.2. («Расчет допускаемых напряжений»).
Полученное значение модуля округлим в большую сторону до значения из стандартного ряда модулей .
Зная значение модуля определяем геометрические размеры шестерни.
Делительный диаметр – d3 = m*z3 = 3*22 = 66 мм.
Диаметр вершин зубьев – da3 = d3 +2*m = 66+2*3 = 72 мм.
Диаметр впадин зубьев – df3 = d3 -2.5*m = 66-2.5*3 = 58.5 мм.
где - коэффициент ширины зубчатого венца колеса относительно модуля рекомендуют назначать для открытых передач .
b3 = 12*3+3 = 40 мм.
Проектный расчёт валов и опорных конструкций
Основными критериями работоспособности проектируемых редукторных валов являются прочность и выносливость. Они испытывают сложную деформацию - совместное действие кручения изгиба и растяжения (сжатия). Но так как напряжения в валах от растяжения небольшие то их обычно не учитывают.
Расчет редукторных валов производится в два этапа:
-й - проектный (приближённый) расчёт валов на чистое кручение;
-й - проверочный (уточнённый) расчёт валов на выносливость по напряжениям изгиба и кручения.
1 Выбор материала валов
Основными материалами для валов служат углеродистые и легированные стали. Механические характеристики выбранного материала 40XH приведены в табл. 3.1.
Таблица 3.1 Механические характеристики стали
2 Выбор допускаемых напряжений на кручение
Проектный расчёт валов редуктора выполняют только по напряжениям кручения (как при чистом кручении) то есть при этом не учитывают напряжений изгиба концентрации напряжений и переменность напряжений во времени (циклы напряжений). Для компенсации этого значения допускаемых напряжений на кручение выбирают заниженными в пределах . Меньшие значения - для быстроходных валов большие значения - для тихоходных валов.
3 Определение геометрических параметров ступеней валов
Редукторный вал представляет собой ступенчатое цилиндрическое тело количество и размеры ступеней которого зависят от количества и размеров установленных на вал деталей. На рис. 3.1 и рис. 3.2 приведены типовые конструкции быстроходного и тихоходного валов одноступенчатых редукторов.
Проектный расчёт ставит целью определить ориентировочно геометрические размеры каждой ступени вала: её диаметр d и длину l. Значения высоты буртика t ориентировочные величины фаски ступицы f и радиусы скругления r определяются в зависимости от диаметра ступени d (см. табл. 3.2).
I под элемент открытой передачи или полумуфту.
По ряду нормальных линейных размеров d1 = 28 мм.
l1 = (1.0 1.5)*d1 = 1.25*d1 = 1.25*28 = 35 мм.
II под уплотнение крышки с отверстием и подшипник.
d2 = d1+2*t = 28+2*3.5 = 35мм.
Диаметр d2 под подшипник округляем до ближайшего стандартного диаметра внутреннего кольца подшипника мм.
По ряду нормальных линейных размеров мм.
определить графически на эскизной компоновке.
V упорная или под резьбу
d5 = d3 +3*f = 70+3*2 = 75 мм.
Таблиц 3.2 Высота буртика фаски радиус скругления
4 Предварительный выбор подшипников качения
Выбор наиболее рационального типа подшипника для данных условий работы редуктора весьма сложен и зависит от целого ряда факторов передаваемой мощности редуктора типа передачи соотношения сил в зацеплении частоты вращения внутреннего кольца подшипника требуемого срока службы приемлемой стоимости схемы установки.
Для опор валов цилиндрических прямозубых колёс редукторов применяют шариковые или роликовые радиальные подшипники рис. 3.3. Первоначально назначают подшипники лёгкой серии. Если при последующем расчёте грузоподъёмность подшипника окажется недостаточной то принимают подшипники средней серии.
Типоразмер подшипников выбирают пo величине диаметра внутреннего кольца подшипника равного диаметру второй и четвёртой ступеней вала под подшипники. Из таблицы 3.3 назначаем подшипники лёгкой серии:
Таблица 3.3 Подшипники радиальные однорядные (ГОСТ 8338-75)
5 Эскизная компоновка редуктора
Эскизная компоновка устанавливает положение шестерни и колёса закрытой зубчатой передачи шестерни открытой передачи и муфты относительно стенок корпуса редуктора и подшипниковых опор определяет расстояния lБ и lТ между точками приложения реакций подшипников быстроходного и тихоходного валов а также точки приложения сил давления от шестерни открытой передачи и муфты на расстоянии lоп и lм от точки приложения реакции ближнего подшипника.
При необходимости эскизная компоновка выполняется в соответствии с требованиями ЕСКД на миллиметровой бумаге формата А2 или А1 карандашом в контурных линиях в масштабе 1:1 и должна содержать эскизное изображение редуктора в двух проекциях основную надпись.
Эскизную компоновку редуктора рекомендуется выполнять в такой последовательности:
Намечают расположение проекций компоновки в соответствии с кинематической схемой привода и наибольшими размерами колёс.
Проводят оси проекций и осевые линии валов.
В цилиндрическом редукторе оси валов проводят на межосевом расстоянии параллельно друг другу.
Вычерчивают зубчатую передачу в соответствии с геометрическими параметрами шестерни и колеса полученными в результате проектного расчёта. Места зацепления колёс показывают в соответствии с рис. 3.4.
Для предотвращения задевания поверхностей вращающихся колёс за внутренние стенки корпуса контур стенок проводят с зазором = 8 10 мм. Расстояние hM между дном корпуса и поверхностью вершин зубьев колёс для всех типов редукторов принимают hM 4 (с целью обеспечения зоны отстоя масла).
Действительный контур корпуса редуктора зависит от его кинематической схемы размеров деталей передач способа транспортировки смазки и тому подобного и определяется при разработке конструктивной компоновки.
Вычерчивают ступени вала на соответствующих осях в соответствии с геометрическими размерами d и l полученными в проектном расчёте валов и графическим определением конструкции валов для цилиндрического редуктора. Ступени валов вычерчивают в последовательности от 3-й к 1-й. При этом длина 3-й ступени l3 получается конструктивно как расстояние между противоположными стенками редуктора или равное длине ступицы колеса.
На 2-й и 4-й ступенях вычерчивают контуры подшипников по размерам d D B (T С) в соответствии со схемой их установки.
Контуры подшипников проводят основными линиями.
Определяют расстояния lБ и lТ между точками приложения реакций подшипников быстроходного и тихоходного валов.
Радиальную реакцию подшипника считают приложенной в точке пересечения нормали к середине поверхности контакта наружного кольца и тела качения подшипника с осью вала.
Проставляют на проекциях эскизной компоновки необходимые размеры.
В одноступенчатом цилиндрическом редукторе обычно применяют зубчатое колесо с симметричной ступицей и располагают его на равных расстояниях от опор.
В индивидуальном и мелкосерийном производствах валы изготовляют ступенчатыми снабжая буртами для упора колёс и подшипников. Во всех вариантах конструкций подшипники устанавливают "враспор". Регулировка подшипников выходного вала как и подшипников входного вала осуществляется установкой набора тонких металлических прокладок под фланец привертной крышки а в конструкциях с закладной крышкой установкой компенсаторного кольца при использовании радиального шарикоподшипника или нажимного винта при использовании конических роликоподшипников.
6 Проверочный расчёт валов на выносливость
На практике установлено что для валов основным видом разрушения является усталостное разрушение. Статическое разрушение происходящее под действием случайных кратковременных перегрузок наблюдается значительно реже. Поэтому для валов расчёт на выносливость (сопротивление усталости) является основным и заключается в определении расчётных коэффициентов запаса усталостной прочности в потенциально опасных сечениях предварительно намеченных в соответствии с эпюрами моментов и наличием на валу концентраторов напряжений.
Составим расчётную схему по чертежу выходного вала и определим опорные реакции (см. рис. 3.6). При составлении расчётной схемы валы рассматривают как прямые брусья лежащие на шарнирных опорах. Подшипники качения воспринимающие радиальные и осевые силы рассматривают как шарнирно неподвижные опоры а подшипники воспринимающие только радиальные силы как шарнирно-подвижные.
Определим расстояния между точками приложения внешних сил к валу:
Определим внешние силы действующие на вал:
Ft2 = 2*T2d2 = 2*320*100233 = 2746 H; Fr2 = Ft2 * tgα = 999.746 H;
Ft3 = 2*T2d3 = 2*T2(m*z3)= 2*320*1000(3*22)= 9696 H; Fr3 = Ft3*tgα =3529 H.
Построение эпюр изгибающих моментов в двух взаимно перпендикулярных плоскостях и эпюры крутящих моментов проводят в следующей последовательности.
Определяют реакции в опорах из условия равновесия вала составляя уравнения статики
Правильность определения реакций и проверяют с помощью уравнения .
Определяют внутренние изгибающие моменты в поперечных сечениях на каждом участке вала методом сечений составляя уравнения равновесия:
Определим опорные реакции и в горизонтальной плоскости XOY:
Rвг = = 20505.676 H;
; Rаг+Ft2-Rвг+Ft3 = 8063.285+2746-20505.676+9696 = 0.
Реакции определены правильно.
Построим эпюру изгибающих моментов в горизонтальной плоскости (рис. 3.6):
в точке С: Мг = Rаг*a = 8063.285*56* = 451.543;
= (8063.285*(56+56)+2746*56)* = 1056.863;
Определим опорные реакции и в вертикальной плоскости XOZ:
; Rав-Fr2-Rвв+Fr3 = 3934.346-999.746-6463.6+3529 = 0.
Построим эпюру изгибающих моментов в вертикальной плоскости (рис. 3.6):
в точке С: Мв = Rав *а = 3934346*56* = 220323;
в точке B: Мв = Rав *(а+b)-Fr2*b = (3934.346*(56+56)-999.746*56)* =
В соответствии с размерами вала и эпюрами и предположительно опасными сечениями вала подлежащими проверке на сопротивление усталости являются сечения I-I и II-II в которых возникают наибольшие моменты и имеются концентраторы напряжений (рис. 3.6).
Определим суммарные изгибающие моменты в сечениях:
Наиболее опасным сечением для вала подлежащим проверке на сопротивление усталости является сечение II-II и Mu = Mu2 = 1124.687 .
Для установленного опасного сечения запас усталостной прочности определяют по формуле
где и - коэффициенты запаса сопротивления усталости по изгибу и кручению определяемые по зависимостям
Здесь и - амплитуды напряжений цикла; и - средние напряжения; и - коэффициенты чувствительности к асимметрии цикла напряжений для рассматриваемого сечения.
В расчётах валов принимают что нормальные напряжения изменяются по симметричному циклу: и а касательные напряжения – по отнулевому циклу: и .
Напряжения в опасных сечениях вычисляют по формулам
где и - моменты сопротивления сечения вала при изгибе и кручении .
Моменты сопротивления при изгибе при кручении вычисляют по нетто-сечению:
Напряжения в опасных сечениях:
Пределы выносливости вала в рассматриваемом сечении определяют по формулам
где и - пределы выносливости гладких образцов при симметричном цикле изгиба и кручения МПа МПа (см. табл. 3.1); и - коэффициенты снижения предела выносливости.
Значения и вычисляют по зависимостям
где и - эффективные коэффициенты концентрации напряжений; и - коэффициенты влияния абсолютных размеров поперечного сечения (табл. 3.4); и - коэффициенты влияния качества поверхности (табл. 3.5); - коэффициент влияния поверхностного упрочнения (табл. 3.6).
Таблица 3.4 Коэффициенты влияния абсолютных размеров поперечного сечения
Напряжённое состояние и материал
при диаметре вала d мм
Изгиб для углеродистой стали
Изгиб для легированной стали
Кручение для всех видов сталей
Таблица 3.5 Коэффициенты влияния качества поверхности
Вид механической обработки
Параметр шероховатости мкм
Обтачивание чистовое
Таблица 3.6 Коэффициент влияния поверхностного упрочнения
Вид упрочнения поверхности вала
Дробеструйный наклёп
Значения коэффициентов и для ступенчатого перехода с галтелью (рис. 3.2) берут из табл. 3.7.: МПа МПа.
Коэффициент влияния асимметрии цикла для рассматриваемого сечения вала
где - коэффициент чувствительности материла к ассиметрии цикла напряжений ( см. табл. 3.1).
Таблица 3.7 Эффективные коэффициенты концентрации напряжений
Прочность вала в сечении II-II обеспечивается.
7 Проверка правильности подбора подшипников качения
Выбранный в ходе проектирования узла вала типоразмер подшипника должен быть проверен на работоспособность по динамической грузоподъёмности. Проверка правильности выбора подшипников может быть проведена двумя способами:
) по сравнению требуемой Сr треб и паспортной Сr пасп динамической грузоподъемности подшипника когда должно выполняться условие Сr треб Сr пасп;
) по обеспечению заданной долговечности подшипника то есть где с учетом режима нагрузки . (см. табл. 2.3).
Фактический срок работы подшипника рассчитывают по формуле
где - коэффициент надежности обычно принимают при 90% надежности; - обобщенный коэффициент совместного влияния качества металла деталей подшипника и условий его эксплуатации для обычных условий эксплуатации назначают = 0.6 (для роликоподшипников);
Величина эквивалентной динамической нагрузки на проверяемый подшипник рассчитывается в общем случае по формуле
где Frn и Fan – соответственно радиальная и осевая силы в опоре ;
V - коэффициент вращения зависящий от того какое кольцо подшипника вращается при вращении внутреннего кольца V=1; kб - коэффициент безопасности учитывающий характер нагрузки при умеренных толчках kб=13 15=14; kt -температурный коэффициент для температуры подшипникового узла ; X и Y – коэффициенты соответственно радиальной и осевой нагрузок на подшипник ; - показатель степени .
Lhe зад =1*10000 = 10000 ч.
Frn = Rв = = 21500.2 H.
Pr = (0.6*1*20505.676+0.5*0)*1.4*1 = 18060.212 H.
В связи с режимом нагрузки 0 шариковые подшипники 312 и 412 по предварительному подсчету не подошли выбираем роликовый подшипник 2312 (N312)
Lh факт = 1*0.6*(* 10530 ч
Так как фактический срок работы подшипника больше заданного (10530) то предварительно назначенный подшипник средней серии 2312 (N312) ГОСТ 8338-75 пригоден.
Конструирование зубчатых колёс
1 Цилиндрические зубчатые колеса внешнего зацепления
Форма зубчатого колеса может быть плоской или с выступающей ступицей. В одноступенчатых редукторах колёса делают со ступицей выступающей в обе стороны. При отсутствии в техническом задании на курсовое проектирование указаний о серийности производства редукторов его можно задать отдавая предпочтение индивидуальному и мелкосерийному производству.
На рис. 4.1 показана простейшая форма колёс изготовляемых в единичном и мелкосерийном производстве. При небольших диаметрах колес их изготавливают из прутка а при больших заготовки колёс получают свободной ковкой с последующей токарной обработкой. Чтобы уменьшить объём точной обработки резанием на дисках колес выполняют выточки (см. рис. 4.1).
Длину посадочного отверстия колеса желательно принимать равной или больше ширины зубчатого венца колеса. Длину ступицы согласуют также с расчетами соединения (шпоночного шлицевого или с натягом) выбранного для передачи вращающего момента с колеса на вал (или с вала на колесо) и с диаметром посадочного отверстия : обычно .
Диаметр ступицы назначают в зависимости от материала колеса для стали - . Меньшие значения принимают для шлицевого соединения вала с колесом большие - для шпоночного соединения с натягом.
dст = 1.5*d = 1.5*70 = 108 мм.
Ширину S торцов зубчатого венца принимают .
На торцах зубчатого венца выполняют фаски: которые округляют до стандартного значения (см. табл. 4.1).
Острые кромки на торцах ступицы также притупляют фасками размеры которых принимают по табл. 4.1.
Принципиально возможны два конструктивных исполнения шестерен зубчатых передач: заодно с валом (вал - шестерня) и отдельно от вала (насадная шестерня). Качество вала - шестерни (жесткость точности зацепления и т.п.) оказывается выше а стоимость изготовления ниже чем вала с насадной шестерней поэтому все шестерни редукторов как правило выполняют заодно с валом.
На рис. 4.2 конструкция шестерни обеспечивает нарезание зубьев со свободным выходом зуборезного инструмента (червячной фрезы или долбяка).
Проектный расчёт соединений
1 Шпоночные соединения
Для передачи вращающего момента чаще всего применяют призматические и сегментные шпонки.
Призматические шпонки имеют прямоугольное сечение; концы скругленные или плоские. Стандарт предусматривает для каждого диаметра вала определённые размеры поперечного сечения шпонки (рис. 5.1 табл. 5.1). Длину шпонки со скруглёнными или с плоскими торцами выбирают из стандартного ряда. Длину ступицы назначают на 8 10 мм больше длины шпонки. Если по результатам расчёта шпоночного соединения получают длину ступицы то вместо шпоночного целесообразнее применить шлицевое соединение или соединение с натягом.
I шпонка – под элемент открытой передачи на вале-шестерне.
Диаметр вала d = 28 мм. Сечение шпонки: мм мм.
Глубина паза мм мм. Длина мм.
II шпонка – под колесо.
Диаметр вала мм. Сечение шпонки: мм мм.
III шпонка – под элемент открытой передачи на вале-колесе.
Таблица 5.1 Шпонки призматические (ГОСТ 23360-78)
Примечания. 1. Длину l (мм) призматической шпонки выбирают из ряда 10 12 14 16 18 20 22 25 28 32 36 40 45 50 56 63 70 80 90 100 110 125 140 160 180 200 220 250 280. 2. Пример обозначения шпонки с размерами b=18 мм h=11 мм l=80 мм: «Шпонка 18×11×80 ГОСТ 23360-78»
2 Проверочный расчёт шпоночного соединения
Проверочный расчёт шпоночного соединения осуществляют обычно на напряжение смятия.
Для призматической шпонки (рис. 5.1)
Для стальной шпонки при нагрузке принимаем допускаемое напряжение смятия: МПа.
МПа. Условие для шпоночного соединения под элемент открытой передачи на вале-шестерне выполняется.
МПа. Условие для шпоночного соединения под колесо выполняется.
МПа. Условие для шпоночного соединения под элемент открытой передачи на вале-колесе выполняется.
Выбор смазочных материалов и системы смазывания
1 Смазывание зубчатых передач
Для уменьшения потерь мощности на трение снижения интенсивности изнашивания трущихся поверхностей их охлаждения и очистки от продуктов износа а также для предохранения от заедания задиров коррозии должно быть обеспечено надёжное смазывание трущихся поверхностей.
Для смазывания передач широко применяют картерную систему. В корпус редуктора или коробки передач заливают масло так чтобы венцы колес были в него погружены. Колеса при вращении увлекают масло разбрызгивая его внутри корпуса. Масло попадает на внутренние стенки корпуса откуда стекает в нижнюю его часть. Внутри корпуса образуется взвесь частиц масла в воздухе которая покрывает поверхность расположенных внутри корпуса деталей.
Картерное смазывание применяют при окружной скорости зубчатых колес и червяков до . При более высоких скоростях масло сбрасывает с зубьев центробежная сила и зацепление работает при недостаточном смазывании. Кроме того заметно возрастают потери мощности на перемешивании масла повышается его температура.
Выбор смазочного материала основан на опыте эксплуатации машин.
Преимущественное применение имеют масла. Принцип назначения сорта масла следующий: чем выше окружная скорость колеса тем меньше должна быть вязкость масла и чем выше контактные давления в зацеплении тем большей вязкостью должно обладать масло. Поэтому требуемую вязкость масла определяем в зависимости от контактного напряжения и окружной скорости колес (табл. 6.1).
Таблица 6.1 Вязкость масла
Контактные напряжения МПа
Рекомендуемая кинематическая вязкость при окружной скорости мс
Для зубчатых передач при С
При окружной скорости V = 3.619 и контактном напряжении МПа рекомендуемая кинематическая вязкость 28 . По табл. 6.2 выбираем марку масла для смазывания зубчатой передачи.
Марка масла – И-Г-А-32.
Обозначение индустриальных масел состоит из четырёх знаков каждый из которых обозначает: первый (И) – индустриальное второй – принадлежности группе по назначению (Г – для гидравлических систем) третий – принадлежность к группе по эксплуатационным свойствам (А - масло без присадок) четвёртый (число) – класс кинематической вязкости.
Таблица 6.2 Характеристики марок масла
Кинематическая вязкость
Допустимые уровни погружения колёс цилиндрического редуктора в масляную ванну (рис. 6.1): но не менее 10 мм. Наибольшая допустимая глубина погружения зависит от окружной скорости колеса. Чем медленнее вращение колеса тем на большую глубину оно может быть погружено.
hм = (2*m+0.25*d2)2 = (2*2+0.25*233)2 = 31.1 мм.
При работе передач продукты изнашивания постепенно загрязняют масло. С течением времени оно стареет свойства его ухудшаются. Браковочными признаками служат увеличенное кислотное число повышенное содержание воды и наличие механических примесей. Поэтому масло залитое в корпус редуктора периодически меняют. Для замены масла в корпусе предусматривают сливное отверстие закрываемое пробкой с цилиндрической резьбой (рис. 6.2).
Берём следующий размер пробки с цилиндрической резьбой:
Цилиндрическая резьба не создаёт надёжного уплотнения. Поэтому под пробку с цилиндрической резьбой ставят уплотняющие прокладки из фибры алюминия паронита. Для этой цели применяют также кольца из маслобензостойкой резины которые помещают в канавки глубиной чтобы они не выдавливались пробкой при её завинчивании (рис. 6.3).
3 Манжетные уплотнения
Манжетные уплотнения применяют для предохранения от вытекания смазочного материала из подшипниковых узлов а также для защиты их от попадания извне пыли и влаги. Манжета (рис. 6.4) состоит из корпуса 1 изготовленного из маслобензостойкой резины каркаса 2 представляющего собой стальное кольцо Г-образного сечения и браслетной пружины 3. Каркас придаёт манжете жёсткость и обеспечивает её плотную посадку в корпусную деталь без дополнительного крепления. Браслетная пружина стягивает уплотняющую часть манжеты вследствие чего образуется рабочая кромка. Манжету обычно устанавливают открытой стороной внутрь корпуса.
Конструирование элементов корпуса редуктора
Корпус редуктора служит для размещения и координации деталей передачи защиты их от загрязнения организации системы смазки а также воспринятая сил возникающих в зацеплении редукторной пары подшипниках открытой передаче. Корпус редуктора изготавливают из серого чугуна марки СЧ15.
В проектируемых одноступенчатых редукторах принята в основном конструкция разъёмного корпуса состоящего из крышки и основания. Корпуса вертикальных цилиндрических редукторов могут иметь в отдельных случаях два разъёма что определяет ещё одну часть корпуса - среднюю. Несмотря на разнообразие форм корпусов они имеют одинаковые конструктивные элементы - подшипниковые бобышки фланцы рёбра соединённые стенками в единое целое и их конструирование подчиняется некоторым общим правилам.
1 Конструктивное оформление внутреннего контура редуктора
В малонагруженных редукторах () толщины стенок крышки и основания корпуса принимают одинаковыми: мм.
Плоскости стенок встречающиеся под прямым углом или тупым углом сопрягают дугами радиусом и (рис. 7.1 а). Если стенки встречаются под острым углом рекомендуют их соединять короткой вертикальной стенкой. (рис. 7.1 б). В обоих случаях принимают: .
2 Крепление крышки редуктора к корпусу
По всему контуру корпуса и крышки делают специальные фланцы в которых размещают крепёжные болты. Диаметры болтов для крепления крышки к корпусу и диаметры отверстий (рис. 7.3) на проход в зависимости от межосевого расстояния можно выбрать из табл. 7.1.
Таблица 7.1 Зависимость болтов и соеденительных отверстий от межосевого расстояния
Главный геометрический параметр
где каждый диаметр относится к следующим фланцевым соединениям:
- фундаментный основания корпуса;
- подшипниковый бобышки основания и крышки корпуса;
- соединительный основания и крышки корпуса;
- крышки подшипникового узла;
- крышки смотрового люка.
Болты для крепления крышки редуктора к корпусу располагают по всему периметру корпуса примерно на одинаковом расстоянии один от другого с шагом .
Ширину фланца выбирают такой чтобы на нём свободно размещалась гайка или шестигранная головка болта и можно было повернуть гаечный ключ на угол не менее .
При креплении болтами (рис. 7.3) .
Оси болтов размещают на расстоянии от кромки. Толщину фланцев принимают (рис. 7.3) .
3 Конструктивное оформление приливов для подшипниковых гнёзд
Приливы в которых располагаются подшипники конструктивно оформляют по рис. 7.4. Диаметр прилива для закладной крышки принимают.
Болты крепления крышки корпуса расположенные у подшипниковых гнёзд стремятся максимально приблизить к отверстию для увеличения жёсткости и уменьшения размеров приливов.
Для вала колеса: мм.
4 Фиксирование крышки относительно корпуса
При сборке редуктора во время затяжки болтов соединяющих корпус с крышкой возможно некоторое смещение крышки относительно корпуса что вызовет деформирование наружных колец подшипников имеющих малую жёсткость. Кроме того торцы приливов у подшипниковых гнёзд на крышке редуктора и корпусе могут не совпасть что повлечёт перекос крышек подшипников и наружных колец самих подшипников. Следовательно при сборке редуктора нужно точно фиксировать положение крышки относительно корпуса. Необходимую точность фиксирования достигают штифтами которые располагают на возможно большем расстоянии друг от друга. Диаметр штифтов
где - диаметр крепёжного болта.
Кроме фиксирования штифты предохраняют крышку и корпус от сдвига при растачивании подшипниковых отверстий. Обычно применяют два конических штифта которые устанавливают по срезам углов крышки (рис. 7.5).
Из ГОСТ 3129-70 (штифты конические) выбираем параметры штифта (рис. 7.6).
5 Конструктивное оформление опорной части корпуса
Опорная поверхность фланца выполняется в виде двух длинных параллельно расположенных платиков (рис. 7.7). Места крепления располагают на возможно большем (но в пределах корпуса) расстоянии друг от друга . Длина опорной поверхности платиков ; ширина ; высота .
6 Оформление отверстий под маслоуказателъ и сливную пробку
Oба отверстия (рис.7.8) желательно располагать рядом на одной стороне основания корпуса в доступных местах. Нижняя кромка сливного отверстия должна быть на уровне днища или несколько ниже его.
Дно желательно делать с уклоном 1 20 в сторону отверстия. У самого отверстия в отливке основания корпуса выполняют местное углубление для стока масла и отстоявшейся грязи. Отверстие под маслоуказателъ должно располагаться на высоте достаточной для точного замера верхнего и нижнего уровней масла. Форма и размер отверстий зависят от типа выбранных маслоуказателя и сливной пробки. Наружные стороны отверстий оформляют опорными платиками. При установке маслоуказателя и сливной пробки с цилиндрической резьбой обязательно применяют уплотнительные прокладки из паронита или резиновое кольцо. Пробка с конической резьбой не требует уплотнения.
7 Оформление прочих конструктивных элементов корпусных деталей
Для подъёма и транспортирования крышки корпуса и редуктора в сборке применяют проушины отливая их заодно с крышкой. По варианту рис. 7.9 проушина выполнена в виде ребра с отверстием. Выбор конструкции проушины зависит от размеров и формы крышки корпуса.
Служит для контроля сборки и осмотра редуктора при эксплуатации. Для удобства осмотра его располагают на верхней крышке корпуса что позволяет также использовать люк для заливки масла. Смотровой люк делают прямоугольной или (реже) круглой формы максимально возможных размеров. Люк закрывают крышкой. Широко применяют стальные крышки из листов толщиной k 2 мм (см. рис. 7.10 а). Для того чтобы внутрь корпуса извне не засасывалась пыль под крышку ставят уплотняющие прокладки из картона (толщиной 1 15 мм) или полоски из резины (толщиной 2 3 мм). Если с такой крышкой совмещена пробка-отдушина то её приваривают к ней или прикрепляют развальцовкой (рис. 7.10 б).
На рис. 7.10 в приведена крышка совмещённая с фильтром и отдушиной. Внутренняя крышка окантована с двух сторон вулканизированной резиной. Наружная крышка плоская вдоль длинной её стороны выдавлены 2 3 гофра через которые внутренняя полость редуктора соединена с внешней средой. Пространство между крышками заполнено фильтром из тонкой медной проволоки или другого материала. Крышки крепятся к корпусу винтами с полукруглой или полупотайной головкой.
Если смотровой люк отсутствует или расположен в боковой стенке корпуса то в верхней плоскости крышки корпуса предусматривают отверстие под отдушину. Иногда по конструктивным соображениям контроль уровня смазки зацепления осуществляют жезловым маслоуказателем установленным в крышке корпуса для чего предусматривается специальное отверстие. Эти отверстия можно использовать и для заливки масла. Используем б.
Список используемой литературы
Федосеев В. И. «Сопротивление материалов» М. Наука 1986г.
Детали машин: Учебник для машиностроительных специальностей вузов 12-е изд. Испр. М.Н. Иванов В.А. Финогенов. – М.:Высш. Шк. 2008. – 408с.
Чернавский С. А. «Проектирование механических передач» М. Машиностроение 1984г.
Дунаев П. Ф. Лёликов О. П. «Конструирование узлов и деталей машин» учебное пособие для машиностроительных ВУЗов изд.5 М. Высшая
Расчет и конструирование одноступенчатого зубчатого редуктора: Учеб. пособие М. Ш. Мигранов С.М. Минигалеев О. Ф. Ноготков А. А. Сидоренко Л. Ш. Шустер – М.: Изд-во МАИ 2008. – 125 с.
1404._2.cdw

Подшипник ГОСТ 8338-75
Шайба 8 ГОСТ 6402.70
Шайба концевая 7019-0623
Шайба 12 ГОСТ 6402.70
Шпонка ГОСТ 23360-78
Чертеж колесо.cdw

Сталь 40ХН ГОСТ 4543-71
Радиусы скруглений 1
Общие допуски по ГОСТ 30893
Вал.cdw

Сталь 40ХН ГОСТ 1050-88
9 302 HB кроме места
*Размер обеспеч. инстр.
Общие допуски по ГОСТ 30893
1404..cdw

Пояснительная записка.
Компенсаторное кольцо
Маслоотражательная шайба.
Кольцо уплотнительное
содержание.doc
1 ОПРЕДЕЛЕНИЕ ТРЕБУЕМОЙ МОЩНОСТИ ЭЛЕКТРОДВИГАТЕЛЯ 4
2 ОПРЕДЕЛЕНИЕ ЧАСТОТЫ ВРАЩЕНИЯ ВАЛА
ЭЛЕКТРОДВИГАТЕЛЯ ..4
РАСЧЁТ ЗУБЧАТОЙ ПЕРЕДАЧИ . ..7
1 ВЫБОР МАТЕРИАЛОВ ЗУБЧАТЫХ ПЕРЕДАЧ И ВИДА
2. РАСЧЁТ ДОПУСКАЕМЫХ НАПРЯЖЕНИЙ .7
3 ПРОЕКТНЫЙ РАСЧЁТ ЗАКРЫТОЙ ЦИЛИНДРИЧЕСКОЙ ЗУБЧАТОЙ ПЕРЕДАЧИ 10
4 ГЕОМЕТРИЧЕСКИЙ РАСЧЁТ ЗАКРЫТОЙ ЦИЛИНДРИЧЕСКОЙ
5 ПРОВЕРОЧНЫЙ РАСЧЁТ ЗАКРЫТОЙ ЦИЛИНДРИЧЕСКОЙ
6 РАСЧЁТ ОТКРЫТОЙ ЦИЛИНДРИЧЕСКОЙ ЗУБЧАТОЙ
ПРОЕКТНЫЙ РАСЧЁТ ВАЛОВ И ОПОРНЫХ КОНСТРУКЦИЙ 19
1 ВЫБОР МАТЕРИАЛА ВАЛОВ 19
2 ВЫБОР ДОПУСКАЕМЫХ НАПРЯЖЕНИЙ НА КРУЧЕНИЕ .19
3 ОПРЕДЕЛЕНИЕ ГЕОМЕТРИЧЕСКИХ ПАРАМЕТРОВ СТУПЕНЕЙ ВАЛОВ ..19
4 ПРЕДВАРИТЕЛЬНЫЙ ВЫБОР ПОДШИПНИКОВ КАЧЕНИЯ .22
5 ЭСКИЗНАЯ КОМПОНОВКА РЕДУКТОРА ..23
6 ПРОВЕРОЧНЫЙ РАСЧЁТ ВАЛОВ НА ВЫНОСЛИВОСТЬ 26
7 ПРОВЕРКА ПРАВИЛЬНОСТИ ПОДБОРА ПОДШИПНИКОВ
КОНСТРУИРОВАНИЕ ЗУБЧАТЫХ КОЛЁС 33
1 ЦИЛИНДРИЧЕСКИЕ ЗУБЧАТЫЕ КОЛЕСА ВНЕШНЕГО
2 ВАЛ – ШЕСТЕРНЯ . 34
ПРОЕКТНЫЙ РАСЧЁТ СОЕДИНЕНИЙ 35
1 ШПОНОЧНЫЕ СОЕДИНЕНИЯ ..35
2 ПРОВЕРОЧНЫЙ РАСЧЁТ ШПОНОЧНОГО СОЕДИНЕНИЯ .36
ВЫБОР СМАЗОЧНЫХ МАТЕРИАЛОВ И СИСТЕМЫ СМАЗЫВАНИЯ.37
1 СМАЗЫВАНИЕ ЗУБЧАТЫХ ПЕРЕДАЧ 37
2 СЛИВНОЕ ОТВЕРСТИЕ ..38
3 МАНЖЕТНЫЕ УПЛОТНЕНИЯ .40
КОНСТРУИРОВАНИЕ ЭЛЕМЕНТОВ КОРПУСА РЕДУКТОРА .41
1 КОНСТРУКТИВНОЕ ОФОРМЛЕНИЕ ВНУТРЕННЕГО КОНТУРА
2 КРЕПЛЕНИЕ КРЫШКИ РЕДУКТОРА К КОРПУСУ 41
3 КОНСТРУКТИВНОЕ ОФОРМЛЕНИЕ ПРИЛИВОВ ДЛЯ
ПОДШИПНИКОВЫХ ГНЁЗД .42
4 ФИКСИРОВАНИЕ КРЫШКИ ОТНОСИТЕЛЬНО КОРПУСА 43
5 КОНСТРУКТИВНОЕ ОФОРМЛЕНИЕ ОПОРНОЙ ЧАСТИ
6 ОФОРМЛЕНИЕ ОТВЕРСТИЙ ПОД МАСЛОУКАЗАТЕЛЪ И СЛИВНУЮ ПРОБКУ 44
7 ОФОРМЛЕНИЕ ПРОЧИХ КОНСТРУКТИВНЫХ ЭЛЕМЕНТОВ
КОРПУСНЫХ ДЕТАЛЕЙ .45
СПИСОК ИСПОЛЬЗУЕМОЙ ЛИТЕРАТУРЫ 48
Косозубый редуктор.cdw

косозубый одноступенчатый
Техническая характеристика
Вращающий момент на тихоходном валу
Частота вращения тихоходного вала
Передаточное число 4.9
Число зубьев шестерен z1 23
Тип передачи - цилиндрическая косозубая
Технические требовония.
Необработанные поверхности литых деталей
красить маслостойкой краснай эмалью.
Наружные поверхности корпуса красить серой эмалью ПФ-155
Перед сборкой детали промыть диз. топливом
Подшипники освободить от консервации
Залить Масло И-Г-А-32
Перед окончательной сборкой редуктора крышку установить
на герметик УТ-34 ГОСТ 24285-80.
Проверить в ручную плавность вращения валов.
Редуктор обкатать без нагрузки при частоте вращения
быстроходного вала 1432 обмин в течение 2 часов.
После обкатки масло в редукторе заменить.