Редуктор червячно-цилиндрический двухступенчатый




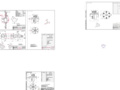
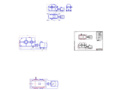
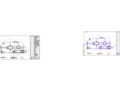
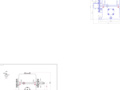
- Добавлен: 24.01.2023
- Размер: 6 MB
- Закачек: 0
Описание
Состав проекта
![]() |
![]() |
![]() ![]() ![]() ![]() |
![]() |
![]() |
![]() |
![]() |
![]() |
![]() |
![]() |
![]() ![]() ![]() |
![]() |
![]() ![]() ![]() ![]() |
![]() ![]() ![]() ![]() |
![]() ![]() ![]() |
![]() |
![]() ![]() ![]() ![]() |
![]() ![]() ![]() |
![]() |
![]() ![]() ![]() ![]() |
Дополнительная информация
Чертеж4.dwg

* Размер для справок. 2. Неуказанные предельные отклонения размеров: H14
h14 и IT . 3. Маркировать Ч и клеймить К на бирке.
содержание.doc
Выбор материалов и определение допускаемых напряжений для быстроходной передачи.
Выбор материалов и определение допускаемых напряжений
для зубчатых передач.
Проектный расчёт цилиндрической косозубой передачи.
Проектный расчет валов и эскизная компановка редуктора.
Расчетная схема нагружения валов определение реакций в опорах построение эпюр изгибающих и крутящих моментов.
Проверочный расчет подшипников качения по динамической грузоподъемности.
Проверочный расчет выходного вала на усталостную прочность.
Проверочный расчет выходного вала на статическую прочность при действии пиковой нагрузки.
Проверочный расчет шпоночных соединений.
Обоснование посадок в основных сопряжениях.
Выбор сорта масла и определение его количества.
Перечень использованных стандартов.
Список использованных литературных источников.
Чертеж2.dwg

Кольцо мазеудерживающие
ошибка: утолщить подошву на 5 мм.
* Размер для справок. 2. Неуказанные предельные отклонения размеров: H14
h14 и IT . 3. Маркировать Ч и клеймить К на бирке.
Чертеж1.dwg

Осевую игру подшипников поз. 1
и 4 обеспечить в пределах
мм прокладками поз. 53
Пятно контакта в червячном зацеплении обеспечить в пределах 70
Техническая характеристика
Общее передаточное отношение 71
Коэфициент полезного действия 0
Номинальная частота вращения выходного вала
Номинальный вращающий момент на ввыходном валу
Наименование и дополнительные указания
Подшипник214 ГОСТ 8338-75
Подшипник 36208 ГОСТ 831-75
Подшипник 36205 ГОСТ 831-75
M10 -8g x 45. 46. 05
M12 -8g x 85. 46. 05
Гайка М10 -7H. 5. 05 ГОСТ 5915-70
Шайба 10 65Г 05 ГОСТ 6402-70
Шайба 12.65Г.05 ГОСТ 11371-78
Шайба 10.65Г.05 ГОСТ 11371-78
Шайба 8 65Г 05 ГОСТ 6402-70
Шайба 8.65Г.05 ГОСТ 11371-78
Штифт 8 х 45 ГОСТ 3129-70
Шпонка 20 х 8 х 50 ГОСТ 23360-78
Шпонка 40 х 10 х 50 ГОСТ 23360-78
Шпонка 45 х 8 х 80 ГОСТ 23360-78
Шпонка 25 х 5 х 32 ГОСТ 23360-78
Мaнжета 1-50 х 95-1 ГОСТ 8752-79
Мaнжета 1-18 х 40-1 ГОСТ 8752-79
Вновь разрабатываемые детали
КПДМ. 250301. 000 ВО
червячно-цилиндрический
Сопряженные поверхности корпуса и крышек покрыть тонким
слоем герметика УТ-34 ГОСТ 24285-80
Необработанные наружные поверхности редуктора покрыть серой
В редуктор залить масла И-30А ГОСТ 20799-75.
Мaнжета 1-18х40-1 ГОСТ 8752-79
Мaнжета 1-50х95-1 ГОСТ 8752-79
Шпонка 6х6х26 ГОСТ 23360-78
Шпонка 14х9х50 ГОСТ 23360-78
Шпонка 14х9х50 ГОСТ23360-78
Шпонка 18х11х40 ГОСТ23360-78
Гайка М10-7H. 5. 05 ГОСТ 5915-70
Наименование и доп. указания
Кольцо мазеудерживающие
ошибка: вал не фисируется
* Размер для справок. 2. Неуказанные предельные отклонения размеров: H14
h14 и IT . 3. Маркировать Ч и клеймить К на бирке.
титул.docx
ГОУ ВПО Кубанский государственный технологический университет
Кафедра технической механики
ПОЯСНИТЕЛЬНАЯ ЗАПИСКА
Детали машин и основы конструирования
Проект привода общего назначения
Руководитель (нормоконтролер) работы:
Чертеж3.dwg

Общее передаточное отношение 71
Коэфициент полезного действия 0
Номинальная частота вращения выходного вала
Номинальный вращающий момент на ввыходном валу
КПДМ. 250301. 000 ВО
Наименование и дополнительные указания
Вновь разрабатываемые детали
Шайба 12.65Г.05 ГОСТ 11371-78
Шайба 8.65Г.05 ГОСТ 11371-78
M12 -8g x 85. 46. 05
* Размер для справок. 2. Неуказанные предельные отклонения размеров: H14
h14 и IT . 3. Маркировать Ч и клеймить К на бирке.
курсовой (пояснительная записка).docx
Назначение редуктора - понижение угловой скорости и соответственно повышение вращающего момента ведомого вала по сравнению с ведущим.
Редукторы классифицируют по следующим основным признакам: типу передачи (зубчатые червячные или зубчато-червячные); числу ступеней (одноступенчатые двухступенчатые и т.д.); типу зубчатых колес (цилиндрические конические коническо-цилиндрические и т.д.); относительному расположению валов редуктора в пространстве (горизонтальные вертикальные); особенностям кинематической схемы (развернутая соосная с раздвоенной ступенью и т.д.).
Червячные редукторы применяют для передачи движения между валами оси которых перекрещиваются.
По относительному положению червяка и червячного колеса различают три основные схемы червячных редукторов: с нижним верхним и боковым расположением червяка.
Искусственный обдув ребристых корпусов обеспечивает более благоприятный тепловой режим работы редуктора.
Выход вала колеса редуктора с боковым расположением червяка в зависимости от назначения и компоновки привода может быть сделан вверх или вниз.
При нижнем расположении червяка условия смазывания зацепления лучше при верхнем хуже но меньше вероятность попадания в зацепление металлических частиц - продуктов износа.
Выбор схемы редуктора обычно обусловлен удобством компоновки привода в целом: при окружных скоростях червяка до 4 - 6 мс предпочтительно нижнее расположение червяка; при больших скоростях возрастают потери на перемешивание масла и в этом случае следует располагать червяк над колесом. В редукторах с верхним расположением червяка при включении движение обычно начинается при недостаточной смазке (за время остановки при редких включениях масло успевает стечь с зубьев колеса).
Передаточные числа червячных редукторов обычно колеблются в пределах и=880 (см. ГОСТ 2144-76).
Так как КПД червячных редукторов невысок то для передачи больших мощностей и в установках работающих непрерывно проектировать их нецелесообразно. Практически червячные редукторы применяют для передачи мощности как правило до 45 кВт и в виде исключения до 150 кВт.
Курсовая работа содержит графическую часть и пояснительную записку выполненные в соответствии с ГОСТ 2.120-73 «Технический проект».
Объем графической части составляет 5 листов из них 4 листа формата А-1 1 лист формата А-2 2 листа формата А-3 по ГОСТ 2.301-68.
Пояснительная записка содержит 61 лист машинописного текста формата А4 включающего в себя:
Реферат (аннотация);
В расчетной части были выполнены: анализ схемы кинематический и силовой расчет привода выбор материалов и определение допускаемых напряжений для быстроходной передачи проектный расчет косозубых цилиндрических передач предварительный расчет валов и эскизная компоновка редуктора расчетные схемы нагружения валов определение реакций в опорах построение эпюр крутящих и изгибающих моментов проверочный расчет подшипников качения по динамической грузоподъемности проверочный расчет выходного вала на усталостную прочность проверочный расчет выходного вала на статическую прочность при действии пиковой нагрузки проверочный расчет шпоночных соединений обоснование посадок в основных сопряжениях в редукторе выбор сорта масла и определение его количества.
В графической части были выполнены чертежи общего вида редуктора рабочие чертежи сопрягаемых деталей.
Анализ схемы кинематический и силовой расчет привода.
Рис. 2.1 Кинематическая схема привода
Мощность на выходном валу кВт
Частота вращения выходного вала n мин-1
Коэффициент пиковой нагрузки КП
Коэффициент использования привода в течение года Кгод
2 Привод представленный на рис. 2.1 состоит из электродвигателя 1 упругой муфты 2 червячно-цилиндрического двухступенчатого редуктора 3 компенсирующей муфты 4 и приводного барабана транспортёра 5.
Силовой поток от электродвигателя идет последовательно через упругую муфту закрытую червячную и цилиндрическую косозубые передачи и далее через закрытую компенсирующую муфту на приводной барабан транспортёра.
Для упорядочения последующих расчетов на заданной кинематической схеме привода введем дополнительные обозначения по ходу силового потока т.е. в направлении от двигателя к выходному валу передаточного механизма нумеруем валы.
3 Поскольку в рассматриваемой кинематической схеме привода передаточный механизм состоит из последовательно соединенных червячной и цилиндрической (с раздвоенным силовым потоком) косозубой передач то с учетом потерь в упругой муфте и подшипниках качения коэффициент полезного действия передаточного механизма равен
где - общий коэффициент полезного действия упругой муфты;
- коэффициент полезного действия цилиндрической косозубой передачи;
- коэффициент полезного действия червячной передачи при двухвитковом червяке;
Примем значения КПД промежуточных звеньев привода по [1 с.14 табл.1П]:
КПД упругой муфты примем м=098;
КПД закрытой цилиндрической косозубой передачи работающей в масляной ванне примем ц =096;
Подставив значения общего КПД в формулу (2.1) получим
4 В соответствии с заданной мощностью на выходном валу привода и расчетным значением общего КПД передаточного механизма о вычисляем требуемую статическую мощность электродвигателя
5 Вычисляем среднеквадратическую мощность электродвигателя [1] полагая что частота вращения вала двигателя изменяется несущественно при изменении нагрузки
где коэффициент эквивалентности
Т – наибольший из длительно действующих моментов принимаемый за момент приведения;
tΣ – длительность цикла нагружения.
Таким образом по формуле (2.4) имеем
6 Располагая численным значением РКВ выберем по каталогу [1 с.15 табл. 2П] ориентируясь на номинальную мощность РД четыре возможных стандартных асинхронных двигателя которые при одном и том же значении РД отличаются номинальными частотами вращения валов nД.
При выборе двигателя соблюдаем условие
Возможные варианты типоразмеров асинхронных двигателей и их параметры представим в таблице 1.
Возможные варианты типоразмеров асинхронных двигателей
Тип электродвигателя
Номинальная мощность двигателя РДВ кВт
Номинальная частота вращения вала двигателя пДВ мин-1
Расчетное общее передаточное отношение передаточного механизма привода
7 Поскольку передаточный механизм привода состоит из одного червячно-цилиндрического двухступенчатого редуктора возможное ориентировочное значение общего передаточного отношения будет равно
где UОВ - ориентировочное значение общего передаточного отношения привода;
UР - среднее значение рекомендуемого передаточного отношения редуктора.
8 Из [ 1 с.20 табл. 6П] выберем стандартное ориентировочное значение общего передаточного отношения UОВ сопоставляя с расчетной величиной UОР представленной в табл. 1.
Таким образом окончательно выбираем электродвигатель типа 4А90L2У3
РДВ = 3.0 кВт пДВ =2840 мин-1; =064.
9 Для рассматриваемой кинематической схемы стандартное передаточное отношение
где UОС - стандартное передаточное отношение передаточного механизма
UР - передаточное отношение редуктора;
Uч - передаточное отношение червячной ступени редуктора;
Uц - передаточное отношение цилиндрической ступени редуктора;
Выполним разбивку передаточного отношения редуктора учитывая рекомендации
[1 с.19 табл. 5П] и [1 с.19 табл. 6П]
Назначим передаточное отношение второй червячной ступени редуктора
Передаточное отношение ступени редуктора
10 Определим номинальные частоты вращения валов с учетом выполненной разбивки общего передаточного отношения по ступеням передаточного механизма привода.
Частота вращения вала 1 (ведущего входного вала редуктора) мин-1
Частота вращения вала 2 (промежуточного вала редуктора) мин-1
Частота вращения вала 3 (выходного вала редуктора) мин-1
11 Определим номинальные вращающие моменты на валах редуктора.
На первом валу привода с учетом потерь в упругой муфте Н·мм
На втором (промежуточном) валу Н·мм
На третьем (выходном) валу Н·мм
12 Техническая характеристика привода
Номинальный вращающий момент на выходном валу T3
Номинальная частота вращения выходного вала n3 мин-1
Общее передаточное отношение UОС
Общий коэффициент полезного действия
Выбор материалов и определение допускаемых напряжений для быстроходной передачи
1 Исходные данные к определению допускаемых напряжений
Рис 3.1 Схема передачи
Номинальная частота вращения мин-1
номинальный вращающий момент на валу колеса
Срок службы передачи L лет
Коэффициент пиковой нагрузки Кп
2 Выбор материала червячной пары
Червяк изготавливаем из стали 18ХГТ упрочняющая химико-термическая обработка – цементация с закалкой до твёрдости HRCэ 56 63.
3 Для выбора материала червячного колеса определяем:
Скорость скольжения в зацеплении
Коэффициент эквивалентности при расчете по контактным напряжениям
Выбираем группу материалов. При 04 рекомендуются материалы гр. 1 а.
Назначаем для изготовления червячного колеса бронзу БрО.10Н1Ф1 ГОСТ 61379 способ получения заготовки – центробежное литьё.
Механические характеристики принятой бронзы
предел текучести Т=165Мпа (при растяжении)
предел прочности при растяжении В=285Мпа
твёрдость НВ 100120.
Ориентировочное значение коэффициента учитывающего износ зубьев червячного колеса в зависимости от скорости скольжения
Машинное время работы передачи часов согласно ТЗ
Фактическое число циклов нагружения зубьев червячного колеса за машинное время tz
Эквивалентное число циклов нагружения зубьев червячного колеса при расчете по контактным напряжениям за весь срок службы передачи.
Коэффициент долговечности при расчете по контактным напряжениям.
Принимаемое значение должно находиться в допустимых границах
3 Для материала червячного колеса определяем допускаемые напряжения
Допускаемые контактные напряжения
где СV = 0.869 – коэффициент учитывающий износ.
Коэффициент эквивалентности при расчёте на выносливость материала червячного колеса по напряжениям изгиба.
Для тяжёлого равновероятностного режима нагружения: КFE=0.2
Эквивалентное число циклов нагружения зубьев червячного колеса при расчёте по напряжениям изгиба
Коэффициент долговечности при расчёте по напряжениям изгиба
Допускаемое напряжение изгиба Мпа для материала червячного колеса при расчёте на выносливость
Предельные напряжения МПа для оценки статической прочности зубьев червячного колеса при действии пиковой нагрузки.
4 Проектный расчет червячной передачи
4.1 Предварительное значение межосевого расстояния червячной передачи из условия контактной прочности зубьев колеса
где - расчетный момент;
предварительное значение коэффициента нагрузки:
Коэффициент внешней динамической нагрузки при расчёте на усталостную прочность.
Принимаем стандартное значение межосевого расстояния аw = 100 мм.
4.2 Число зубьев колеса
4.3 Модуль зацепления
Принимаем стандартный модуль мм.
4.4 Коэффициент диаметра червяка
4.5 Коэффициент смещения в передаче
4.6 фактическое передаточное число
5 Проверяем фактические контактные напряжения
Коэффициент деформации червяка [1 табл.4 с.11] принимаем в зависимости от z1 и q.
– коэффициент учитывающий влияние режима нагружения передачи на приработку зубьев червячного колеса и витков червяка.
Уточненное значение коэффициента концентрации нагрузки по длине зубьев колеса
где =121 – коэффициент деформации червяка.
Окружная скорость мс на делительном диаметре колеса
Назначим 7-ю степень точности передачи с учётом назначения передачи и вида отделочных операций червяка.
Коэффициент динамичности нагрузки
(при 7 степени точности и V2=0.936 мс)
Для нахождения уточненного значения коэффициента нагрузки находим:
6 Действительные контактные напряжения в зацеплении МПа.
угол подъема витка червяка град на начальном диаметре
фактическая скорость скольжения в зацеплении
– уточнённое значение коэффициента
Уточняем значение допускаемого контактного напряжения МПа
Процент отклонения фактического контактного напряжения от допускаемого
Эквивалентное число зубьев червячного колеса
Коэффициент учитывающий форму зубьев червячного колеса определяют по рекомендациям таблицы
7 Условие выносливости зубьев червячного колеса по напряжениям изгиба
Проверка отсутствия пластической деформации зубьев колеса при действии пиковой нагрузки МПа. Значение коэффициента пиковой нагрузки Кп=22;
Проверка на отсутствие хрупкого излома зубьев колеса при действии пиковой нагрузки МПа. Величина допустимого напряжения
8 Основные геометрические параметры червяка с точностью 0.01 мм:
Делительный диаметр червяка
Начальный диаметр червяка
Диаметр вершин витков червяка
Делительный угол подъёма витка червяка град. γ = 841°
Диаметр впадин витков мм при эвольвентном профиле червяка.
Длина нарезанной части шлифованного червяка
Округляем расчётное значение линейного размера до стандартного b1=80.
9 Основные геометрические параметры червячного колеса с точностью до 0.01 мм
Делительный диаметр червячного колеса
Диаметр вершин зубьев червячного колеса
Диаметр впадин зубьев червячного колеса
Наибольший диаметр червячного колеса
Радиусы закругления червячного колеса
Ширина венца червячного колеса
Фактическое межосевое расстояние в червячной передаче
Приведённый угол трения град между червяком и колесом; в зависимости от ;
10 Уточнённое значение КПД передачи.
11 Усилия действующие в зацеплении червячной передачи Н.
Окружная сила на колесе равная по модулю осевой силе на червяке
Осевая сила на колесе равная окружной силе на червяке
Радиальная сила на колесе равная радиальной силе на червяке
Выбор материалов и определение допускаемых напряжений
для зубчатых передач
1 Исходные данные к определению допускаемых напряжений:
2 Выбираем материал сечения шестерни и колеса. Принимаем размер сечения заготовок S=100 мм и руководствуясь данными [3 с. 6 табл. 2]. Полученные данные заносим в таблицу 4.1.
Таблица 4.1 - Материалы и механические характеристики заготовок шестерни и колеса
Наименование параметра обозначение и размерность
Термическая обработка
Механические характеристики материалов
Твёрдость поверхности зуба
Предел текучести Т МПа
3 Определим наиболее вероятную (среднюю) твердость сердцевины
4 Определим наиболее вероятную (среднюю) твердость поверхности
5 Определим предел контактной выносливости материала Нlim МПа по данным [3 стр.6 табл. 2]
6 Определим базовое число циклов нагружения при расчете по контактным напряжениям; приближенные значения принимаем по данным [ 3 с. 16 рис. 4]
Точные значения базового числа NHG циклов нагружения при расчете по контактным напряжениям МПа рассчитаем по зависимостям
7 Определим суммарное машинное время работы (ресурс) передачи часов по зависимости
где L - cрок службы передачи лет;
ПВ - относительная продолжительность включения;
8 Определим фактическое число циклов перемены напряжений зубьев шестерни и колеса на заданный ресурс передачи по зависимостям
где NK1 и NK2 - фактическое число циклов перемены напряжений зубьев;
tΣ - суммарное машинное время работы (ресурс) передачи часов;
n1 и n2 – частота вращения шестерни и колеса соответственно мин-1;
СВ1 и С В2 – число вхождений в зацепление каждого зуба рассчитываемого колеса за один его оборот.
В соответствии с [ 3 стр. 20 рис. 7] принимаем
для шестерни СВ1 = 1
Подставив значения в формулы (4.14) и (4.15) получим
9 Определим коэффициент эквивалентности при расчете по контактным напряжениям по зависимости
где Н - коэффициент эквивалентности;
Ti - вращающие моменты которыми нагружается передача
соответственно в течение времени t
TН – номинальный вращающий момент Нмм.
10 Эквивалентные числа циклов перемены напряжений зубьев шестерни и колеса при расчете по контактным напряжениям
11 Коэффициент долговечности материалов шестерни и колеса при расчете по контактным напряжениям.
Поскольку эквивалентные числа циклов NHE1 и NHE2 больше соответствующих базовых значений NHG1 и NHG2 что указывает на работу материалов в зоне длительного предела выносливости поэтому коэффициент долговечности материалов при расчете по контактным напряжениям определим по зависимостям
12 Коэффициенты запаса прочности при расчете по контактным напряжениям выбираем по [3 стр.14 табл.3]
Для шестерни из стали 40ХН ГОСТ4543-71 улучшенной при вероятности неразрушения Р(t)=098 имеем SH1 =11.
Для колеса из стали 45 ГОСТ1050-88 улучшенной при вероятности неразрушения Р(t)=098 имеем SH2 =11.
13 Допускаемые контактные напряжения при расчете на выносливость активных поверхностей зубьев МПа вычисляем по зависимостям
14 Расчетное допускаемое контактное напряжение для проектного расчета передачи МПа.
Для данного типа термической обработки принимаем [H]= 4458 МПа 446 МПа
15 Максимальное допускаемое контактное напряжение для проверки прочности зубьев при кратковременных перегрузках МПа. Определим из зависимости
Т – предел текучести материала МПа.
Подставив значения Т в формулу (4.23) получим
16 Предел изгибной выносливости материалов МПа
17 Определим коэффициент учитывающий влияние способа получения заготовки по [3 стр.23 табл.6]
шестерня круглый прокат –
18 Определим коэффициент учитывающий влияние шероховатости переходной поверхности между смежными зубьями при расчете на их изгибную выносливость.
При окончательной механической обработке зубьев – шлифование рабочей и переходной поверхностей зубьев колес [3 стр.23 табл.6].
19 Определим коэффициент учитывающий влияние двухстороннего приложения нагрузки. Поскольку передача нереверсивная .
20 Определим коэффициент эквивалентности при расчете напряжениям изгиба
При режиме нагружения 1 и q=6 (4.30)
21 Эквивалентные числа циклов перемены напряжений зубьев шестерни и колеса при расчете по контактным напряжениям изгиба определяем по зависимостям
22 Коэффициенты запаса прочности при расчете по напряжениям изгиба при вероятности неразрушения P(t)=098
для шестерни SF1 = 1.75
для колеса SF2 = 1.75.
23 Допускаемые напряжения изгиба зубьев шестерни и колеса при расчете на выносливость МПа определим по зависимостям
24 Максимальные допускаемые напряжения изгиба для проверки прочности зубьев шестерни и колеса при кратковременных нагрузках[Fmax] МПа определим по зависимостям
25 Итоговые результаты определения допускаемых напряжений для быстроходной зубчатой передачи заносим в таблицу 4.2
Таблица 4.2 - Итоговые результаты определения допускаемых напряжений
Расчетное допускаемое контактное напряжение для проектного расчета передачи МПа
Допускаемое напряжение изгиба при расчете на выносливость МПа
Максимальное допускаемое контактное напряжение для проверки прочности зубьев при кратковременных перегрузках МПа
Максимальные допускаемые напряжения изгиба для проверки прочности зубьев при кратковременных нагрузках МПа
Проектный расчёт цилиндрической косозубой передачи
По результатам кинематического и силового расчета.
T3=456103Нмм – номинальный вращающий момент на ведомом валу проектируемой передачи;
U2=28 – передаточное число проектируемой передачи;
n2=1136 мин-1 – номинальная частота вращения ведущего вала проектируемой передачи;
n3=4057 мин-1 – номинальная частота вращения ведомого вала проектируемой передачи.
Схема передачи – по данным технического задания.
Механические характеристики и допускаемые напряжения для материалов зубчатой пары – итоговые результаты раздела «Выбор материалов и определения допускаемых напряжений для зубчатых передач».
Проектный расчет передачи
1 Предварительное значение межосевого расстояния а передачи из условия контактной выносливости рабочих поверхностей зубьев
где T3=456103 Нмм – номинальный вращающий момент на ведомом валу
проектируемой передачи;
U=28 – передаточное число проектируемой передачи;
[sН]=452 МПа - расчетное допускаемое контактное напряжение для
материалов зубчатой пары;
ba=02 – коэффициент ширины зубчатого колеса принимают из
стандартного ряда по рекомендациям;
КН = 12 – предварительное значение коэффициента нагрузки.
Принимаем межосевое расстояние а = 160 мм согласно ГОСТ 6636-69.
2 Назначаем нормальный модуль зацепления m.
Руководствуясь [4 с.5 табл.3] принимаем нормальный модуль зацепления .
3 Задаемся предварительным значением угла наклона линии зубьев для косозубой цилиндрической передачи.
4 Определяем суммарное число зубьев шестерни и колеса по зависимости
Принимаем суммарное число зубьев шестерни и колеса .
5 С учетом стандартных значений нормального модуля зацепления т межосевого расстояния а и принятого суммарного число зубьев шестерни и колеса находим действительный угол наклона линии зубьев на делительном цилиндре
6 Определяем ширину b2 u b1 зубчатого колеса и шестерни:
Принимаем b1=36 мм согласно ГОСТ 6636-69.
7 Находим коэффициент осевого и торцового перекрытия
8 Вычисляем числа зубьев шестерни Z1 и колеса Z2.
9 Фактическое передаточное отношение
10 Окружная скорость в зацеплении
где - делительный диаметр шестерни.
11 Степень точности 9 согласно ГОСТ 1643-81.
12 Фактическое значение коэффициента нагрузки при расчете по контактным напряжениям
где KHV=1+0022V=1+002205=1011 – коэффициент учитывающий внутреннюю динамическую нагрузку в передаче при расчете на прочность активных поверхностей зубьев;
КН= 109 – коэффициент учитывающий неравномерность распределения нагрузки по длине контактных линий зубьев при расчете на прочность их активных поверхностей;
КН= 11 – коэффициент учитывающий распределения нагрузки между зубьями при расчете на прочность их активных поверхностей.
13 Коэффициент Zм=190 Н 05мм учитывающий механические свойства сопряженных зубчатых колес принимают в зависимости от материалов.
14 Коэффициент ZН=26 учитывающий форму сопряженных поверхностей зубьев в полюсе зацепления.
15 Коэффициент Z=08 учитывающий суммарную длину контактных линий зубьев.
16 Действительные контактные напряжения на активных поверхностях зубьев при фактических параметрах передачи
где Ft – окружное усилие действующая в зубчатом зацеплении
17 Отклонение действительного контактного напряжения Н от допускаемого Н
18 Проверка контактной прочности зубьев при действии пиковой нагрузки
где КП =22 коэффициент пиковой нагрузки (по условию);
- максимальное допускаемое контактное напряжение для проверки прочности зубьев при кратковременных перегрузках.
19 Фактическое значение коэффициента нагрузки при расчете на прочность зубьев при изгибе
где KFV=1+0045V=1+004505=10225 – коэффициент учитывающий внутреннюю динамическую нагрузку;
КН= 12 – коэффициент учитывающий неравномерность распределения нагрузки по длине контактных линий зубьев при расчете на прочность их при изгибе;
КН= 10 – коэффициент учитывающий распределения нагрузки между зубьями при расчете их на изгибную прочность.
20 Проверяем усталостную прочность зубьев шестерни и колеса по напряжениям изгиба сопоставляя местные напряжения изгиба F1 u F2 в опасном сечении на переходной поверхности с допускаемыми напряжениями.
где YFS1=363 u YFS2=36 – коэффициенты учитывающие для шестерни и
колеса форму их зубьев и концентрацию напряжений;
Y=021 – коэффициент учитывающий наклон зубьев;
Y=057 – коэффициент учитывающий перекрытие зубьев.
21 Проверка изгибной прочности зубьев шестерни и колеса при действии пиковой нагрузки
22 Основные геометрические размеры зубчатой передачи
Делительные диаметры:
Диаметры вершин зубьев:
Диаметры впадин зубьев:
Ширина зубчатых венцов:
23 Усилия действующие в зацеплении косозубой цилиндрической передачи (составляющие силы нормального давления):
Окружное усилие . (5.30)
Осевое усилие (5.32)
Рисунок 5.1 Геометрические размеры зубчатой цилиндрической передачи.
Проектный расчет валов и эскизная компановка редуктора
Исходные данные для предварительного расчета валов и эскизной компоновки редуктора
Номинальный вращающий момент на первом валу T1 Н·мм
Номинальный вращающий момент на втором валу T2 Н·мм
Номинальный вращающий момент на третьем валу T3 Н·мм
Межосевое расстояние ступеней редуктора a мм
1 Определяем диаметры выходных участков валов
1.1 Назначаем диаметр выходного участка 1-го вала:
=15 допускаемое напряжение на кручение для валов из сталей 40 45 МПа.
Для удобства соединения входного вала редуктора dВ1 с валом электродвигателя dдв определим диаметр вала редуктора dВ1 мм исходя из соотношения
Полученное значение dВ мм округлим до нормального линейного размера по ГОСТ 663-69.
Выбираем МУВП типа 125-28-1-22-3-У3 ГОСТ21424-93 с расточками полумуфт под dдв=22 мм и dв1=18 мм.
1.2 Определяем наименьшие диаметры валов 2 и 3.
(6.3) где [2] = 18 МПа – допускаемое косательное напряжение;
Принимаем dв2 = 35 мм.
Принимаем dв3 = 50 мм.
Остальные размеры участков валов назначаем из ряда стандартных диаметров в сторону увеличения исходя из конструктивных и технологических соображений. Для быстроходного вала:
dy1=dП1 dв1+2t+118+22+1 23=25 мм -диаметр вала под уплотнение и подшипник. Необходимо учитывать что значение посадочного диаметра подшипника для диапазона кратно пяти. Также величина высоты t мм перехода диаметра вала по отношению к предыдущему диаметру должна быть больше или равна размеру фаски f мм.
Диаметр буртика для упора подшипника d1 мм вычислим по формуле
где t-значение высоты перехода
Окончательно выбираем d1=30 мм.
Величина высоты буртика больше величине радиуса закругления подшипника r мм что обеспечивает надежное осевое размещение подшипника на валу;
dfl da1 d1 - размеры червяка (пункт 3.8).
Для промежуточного вала:
Диаметр вала под уплотнение и подшипник:
dy2=dП2==35 мм (6.5)
Диаметры под червячное колесо
dк2 dП2+2 t235+235 42=42 мм (6.6)
и цилиндрическую шестерню
dк2 dП2+2 t235+215 38=38 мм (6.7)
Для тихоходного вала:
dy3=dП3=dВ3=50 мм (6.8)
Диаметр под зубчатые колеса:
dк4 dП3+2 t350+24 58=58 мм (6.9)
Диаметр буртика для упора колес: d3 58+235 65 мм (6.10)
2 Назначаем отдельные диаметры отдельных участков валов
2.1 Вал №1 – быстроходный вал.
d1 = 18 мм диаметр выходного участка 1-го вала.
dП1 = 25 мм. Диаметр вала под подшипники.
Рисунок 6.1 – Быстроходный вал.
2.2 Вал №2 – промежуточный вал.
d2К = 42 мм. Диаметр вала под червячное колесо.
d2Ш = 38 мм. Диаметр вала под цилиндрическую шестерню
Рисунок 6.2 – Промежуточный вал.
2.3 Вал №3 – выходной вал.
dВ3 = 50 мм d3П = 50 мм d3К = 58 мм.
Рисунок 6.3 – Выходной вал.
Длины участков валов определим после эскизной компоновки редуктора.
Схему установки валов №1№2№3 принимаем враспор. Используем однорядные шариковые подшипники типа 36000 ГОСТ 831-75.
3 Смазка подшипников и зацеплений
3.1 Смазывание подшипников вала №1 осуществляется через отверстия в крышке корпуса валов №2 и №3 осуществляется маслом из картера редуктора подшипники смазываются брызгами масла.
3.2 Передачи в редукторе смазываются путем заливки масла в корпус редуктора так чтобы венцы колес были в него погружены. Колеса при вращении увлекают масло разбрызгивая его внутри корпуса. Масло попадает на внутренние стенки корпуса откуда стекает в нижнюю его часть. Внутри корпуса образуется взвесь частиц масла в воздухе которая покрывает поверхность расположенных внутри корпуса деталей.
4 Конструктивные соотношения элементов корпуса
Корпусная деталь состоит из стенок ребер фланцев и других элементов соединенных в единое целое.
Исходя из габаритов корпуса принимаем толщину стенки
Для удобства сверления отверстий в редукторе делаем их сквозными.
Для увеличения жесткости корпуса редуктора на подшипниковых гнездах размещаем ребра жесткости шириной 63 мм.
Крепление крышки редуктора к корпусу осуществляем болтами М10.
Для фиксирования крышки редуктора относительно его корпуса в горизонтальной плоскости применяем два цилиндрических штифта. Это обеспечивает точную обработку боковых поверхностей редуктора.
Опорная часть корпуса выполняется сплошной поверхностью с отверстиями под крепежные болты M12.
Корпус и крышку редуктора выполняем из чугунного литья
Толщина стенки корпуса мм и крышки 1 мм должны быть не меньше 8 миллиметров.
Принимаем: = 1=10 мм.
Толщину верхнего фланца корпуса b мм и крышки b1 мм принимаем:
b= b1=15=1510=15 мм.
Толщину ребер корпуса мм и крышки мм определим согласно соотношению:
b=b1= (0.75 1) = 75 10 мм
Принимаем: b=b1=10 мм
Диаметр фундаментных болтов d1 принимаем:
Диаметр болтов крепящих крышку к корпусу
принимаем: d3= 10 мм
Длина lш b+b1+(5 6)=25 26 мм. Принимаем: lш = 25 мм
Шестерня может быть выполнена с валом как одна деталь (вал - шестерня) если выполняется следующее условие
где df - диаметр окружности впадин шестерни.
dк- диаметр вала под колёса.
Так как не выполняется условие 7795 16 38=608 то промежуточный вал не выполняются как вал-шестерня.
В редукторах применяют в основном подшипники качения. Выбор типа подшипника зависит от нагрузок действующих на вал. Так как на вал действуют осевая и радиальная силы то используем радиально-упорные подшипники.
Выбор его типоразмера зависит от диаметра вала под подшипник. Посадочный диаметр подшипника для быстроходного вала d=dП1 для промежуточного вала d=dП2 для тихоходного вала - d=dП3.
Входной вал: шариковый однорядный подшипник 36205 ГОСТ 831-75
Промежуточный вал: шариковый однорядный радиально-упорный подшипник 36207 ГОСТ 831-75.
Выходной вал: шариковый однорядный радиально-упорный подшипник 36210 ГОСТ 831-75.
Для герметизации подшипниковых узлов редуктора с осевой фиксацией подшипников применим закладные крышки. Они изготавливаются из чугуна СЧ 15 двух видов. Размеры крышек определяют в зависимости от диаметра наружного кольца подшипника D.
Во время работы привода происходит нагрев деталей и масла что приводит к линейному удлинению валов редуктора. Для компенсации этого расширения предусматривают осевой зазор в подшипниковых узлах а = 02 05 мм который на чертежах общего вида не показывается. Так как применили закладные крышки регулировка осевого зазора производится с помощью компенсирующих колец которые устанавливаются между торцами наружных колец подшипников и крышек.
Графическая часть эскизной компоновки проводим на бумаге формата А 1 в масштабе 1:1 и содержащей вид сверху редуктора с разрезом по осям валов и главного вида редуктора.
Выполнение эскизной компоновки проводим несколькими этапами.
На первом этапе откладываем межосевые расстояние и вычерчивается червячная и цилиндрическая передача.
На втором этапе прочерчиваем границы внутренней стенки редуктора на расстоянии X = 5 12 мм от элементов червячной и зубчатой цилиндрической передачи. Со стороны шестерни предварительное значение размера f мм назначим равным f =10 мм.
На третьем этапе вычерчиваем ступени валов на соответствующих осях по диаметральным размерам полученным в проектном расчете валов
(пункт 6). Длины участков валов получим из следующих рассуждений:
Длина участка вала под муфты которая равна:
где dв-диаметр выходного участка вала мм;
На четвертом этапе дорисовываются подшипники по своим габаритным размерам и определяем для валов размеры а и в мм которые являются плечами приложенных к валу сил.
Определение этих размеров позволяет провести проверочный расчет валов на прочность и расчет подшипников на долговечность.
Расчетная схема нагружения валов определение реакций в опорах построение эпюр изгибающих и крутящих моментов
1 РАСЧЕТ ПЕРВОГО (ЧЕРВЯЧНОГО) ВАЛА
1.1 Строим схему нагружения первого (червячного) вала
1.2 Определяем реакции опор первого (червячного) вала и Н
Суммарная реакция опоры А H:
Суммарная реакция опоры В H:
1.3 Определим изгибающие моменты в опасных сечениях M Н·мм.
По полученным значениям строим эпюру изгибающих моментов в плоскости XOZ.
По полученным значениям строим эпюру изгибающих моментов в плоскости YOZ.
1.4 Крутящий момент Т Н·мм действует в промежутке между сечениями
-1 и 2-2 будет равен моменту T1 Н·мм
2 РАСЧЕТ ТРЕТЬЕГО (ВЫХОДНОГО) ВАЛА
2.1 Строим схему нагружения третьего (выходного) вала
2.2 Определяем реакции опор третьего (выходного) вала и Н
2.3 Определим изгибающие моменты в опасных сечениях M Н·мм.
2.4 Определим крутящие моменты Т Н·мм действующие промежутках
Проверочный расчет подшипников качения по динамической грузоподъемности
Расчет на динамическую грузоподъемность сводится к расчету долговечности
С - динамическая грузоподъемность данного подшипника Н;
Статическая грузоподъёмность данного подшипника Н;
эквивалентная приведенная нагрузка Н;
частота вращения вала обмин.
показатель степени: для шариковых подшипников p=3.
1 Проведем расчет на динамическую грузоподъемность подшипников на первом (входном) валу.
1.1 Реакции опор R Н вала по формулам (7.1.7) и (7.1.8)
1.2 Опора А: подшипник шариковый радиально-упорный однорядный 36205 ГОСТ 831-75: C=167 кН; С0=91 кН; α=12º; n1=2840 мин-1.
Опора В: подшипник шариковый радиально-упорный однорядный 36205 ГОСТ 831-75: C=167 кН; С0=91 кН; α=12º; n1=2840 мин-1.
При С0=9100 Н; Fr=776
Из таблицы [4 c.81 табл.7.1] определяем Y=0; X=1.
Для опоры А расчетное значение отношения осевой нагрузки Fв1 кН к радиальной R1 кН меньше табличного эквивалентную нагрузку P кН определяем по формуле:
где Кб - коэффициент учитывающий нагрузку на подшипник;
КТ - температурный коэффициент.
Числовое значение коэффициента Кб выбираем из [4 c.84 табл.7.3] Кб = 1.
Числовое значение коэффициента КТ выбираем из [5 c.214 табл.9.20] КТ=105.
где V – коэффициент при вращающемся внутреннем кольце V=1;
е – предельное отношение осевой нагрузки к радиальной.
Из таблицы [4 c.81 табл.7.1] определяем Y=1.39; X=1.
1.4 Определяем эквивалентную нагрузку P кН.
Поскольку для опоры В расчетное значение отношения осевой нагрузки Fв1 кН к радиальной R1 кН больше табличного эквивалентную нагрузку P кН определяем по формуле:
Сдвоенные радиально-упорные шариковые подшипники рассчитывают как двухрядные. Если FBFR>e то в двухрядных подшипниках будет работать только 1 ряд тел качения следовательно более нагруженной является опора А.
расчет производится по более нагруженной опоре.
1.5 Определяем долговечность подшипников L часов по формуле (8.1):
где tΣ - суммарный ресурс работы редуктора часов.
ПРОВЕРОЧНЫЙ РАСЧЕТ ВЫХОДНОГО ВАЛА НА УСТАЛОСТНУЮ ПРОЧНОСТЬ
Проверочный расчет вала на усталостную прочность состоит в определении фактических значений коэффициента запаса прочности вала в различных сечениях.
1 Для расчета выберем выходной вал в сечении 1-1(см. рис. 6.3).. Концентрация напряжений обусловлена наличием шпоночного паза (см. рис. 9.1).
Рисунок 9.1-Размеры шпоночного паза.
пределы выносливости материала вала по нормальным и касательным напряжениям МПа;
эффективные коэффициенты концентрации нормальных и касательных напряжений;
масштабные факторы учитывающие отличие размеров проверяемого вала от диаметра образца для которого получено в;
коэффициент учитывающий влияние шероховатости поверхности
амплитуды циклов нормальных и касательных напряжений МПа;
средние напряжения нормальных и касательных напряжений МПа;
коэффициенты учитывающие чувствительность материала к ассиметрии цикла.
2 Материал вала сталь 45 ГОСТ 1050-71:
-1=043 ·640= 2752 МПа;
-1=058 ·2752= 220 МПа;
3 Определяем эффективные коэффициенты концентрации нормальных и касательных напряжений из [4 c.165 табл. 8.5].
4 Определяем масштабные факторы учитывающие отличие размеров проверяемого вала от диаметра образца для которого получено в.
Для вала диаметром 58 мм из углеродистой стали:
5 Определяем амплитуды циклов нормальных и касательных напряжений v МПа и v МПа по зависимостям:
суммарный изгибающий момент в сечении Н·мм;
осевой момент сопротивления изгибу мм3;
крутящий момент на валу Н·мм;
момент сопротивления кручению мм3;
Суммарный изгибающий момент в сечении Ми Н·мм определяется по формуле
максимальный изгибающий момент в плоскости XOZ Н·мм;
максимальный изгибающий момент в плоскости YOZ Н·мм.
Из формулы (6.2.10):
МYmax=1753712 кН·мм.
Осевой момент сопротивления изгибу W мм3 определяется по формуле
диаметр вала в сечении мм;
ширина шпоночного паза мм;
глубина шпоночного паза мм.
Подставляя полученные значения в формулу (9.6) определяем амплитуду циклов нормальных напряжений v МПа
Осевой момент сопротивления кручению WК мм3 определяется по формуле
Подставляя полученные значения в формулу (9.7) определяем амплитуду циклов касательных напряжений v МПа
Крутящий момент на валу Т3 Н·мм
6 Средние напряжения нормальных т МПа и касательных т МПа напряжений определяются по формуле
осевая сила действующая на вал Н.
7 Коэффициенты учитывающие чувствительность материала к ассиметрии цикла для углеродистой стали принимаем равными.
8 Определяем пределы выносливости материала вала по нормальным напряжениям -1 МПа по формуле (9.2)
9 Определяем пределы выносливости материала вала по касательным напряжениям -1 МПа по формуле (9.3)
10 Определяем фактическое значение коэффициента запаса прочности вала в расчетном сечении пределы s по формуле (9.1)
Условие прочности соблюдается.
Проверочный расчет выходного вала на статическую прочность при действии пиковой нагрузки
1 Для расчета выберем выходной вал в сечении 1-1.
Номинальное эквивалентное напряжение ЭП МПа в опасном сечении определяется по формуле
предел текучести материала вала МПа
коэффициент пиковой нагрузки.
Условие статической прочности удовлетворяется.
Проверочный расчет шпоночных соединений
1 Расчет шпоночного соединения на втором (промежуточном) валу.
Соединение червячного колеса с валом 2.
Шпонка 14×9×50 ГОСТ 23360-78 призматическая со скругленными торцами.
Материал шпонки – сталь 45.
Определяем напряжение смятия и условие прочности МПа по формуле (11.1)
глубина шпоночного паза на валу мм;
диаметр вала в месте соединения мм;
допускаемое напряжение смятия МПа
2 Расчет шпоночных соединений на выходном валу.
Соединение зубчатого колеса z3 с валом 3.
Шпонка 18×16×35 ГОСТ 10748-68 призматическая со скругленными торцами.
Определяем напряжение смятия и условие прочности МПа
Обоснование посадок в основных сопряжениях.
Посадки назначаем в соответствии с рекомендациями
[5 с.263 табл. 10.13].
Посадка червячного колеса z1 на вал 2 Н7p6 по ГОСТ 25347-82.
Посадка шестерни z2 на вал 2 Н7u7 по ГОСТ 25347-82.
Посадка зубчатого колеса z3 на вал 3 Н7p6 по ГОСТ 25347-82.
Шейки валов под подшипники выполняем с основным отклонением вала
k6. Отклонения отверстий в корпусе под наружные кольца подшипников
Для уменьшения потерь мощности на трение и снижения интенсивности износа трущихся поверхностей а также для предохранения их от заедания задиров коррозии и лучшего отвода теплоты трущиеся поверхности деталей должны иметь надежную смазку.
В настоящее время в машиностроении для смазывания передач широко применяют картерную систему. В корпус редуктора или коробки передач заливают масло так чтобы венцы колес были в него погружены. При их вращении масло увлекается зубьями разбрызгивается попадает на внутренние стенки корпуса откуда стекает в нижнюю его часть. Внутри корпуса образуется взвесь частиц масла в воздухе которая покрывает поверхность расположенных внутри корпуса деталей.
Картерную смазку применяют при окружной скорости зубчатых колес и червяков от 03 до 125 мс. При более высоких скоростях масло сбрасывается с зубьев центробежной силой и зацепление работает при недостаточной смазке. Кроме того заметно увеличиваются потери мощности на перемешивание масла и повышается его температура.
Выбор смазочного материала основан на опыте эксплуатации машин. Принцип назначения сорта масла следующий: чем выше окружная скорость колеса тем меньше должна быть вязкость масла чем выше контактные давления в зубьях тем большей вязкостью должно обладать масло. Поэтому требуемую вязкость масла определяют в зависимости от контактного напряжения и окружной скорости колес.
1 Определяем уровень масла hм мм.
При заданной компоновке редуктора для эффективного смазывания зубчатых передач необходимо погрузить шестерню z2 в масляную ванну на глубину не менее 3m 5m.
Исходя из размеров корпуса редуктора принимаем:
минимальный уровень масла hm
максимальный уровень масла hmax=52.
2 Вычисляем объем требуемого масла
площадь основания корпуса редуктора дм2.
3 По ранее рассчитанной окружной скорости в зацеплении V=0552 мс и при [H] = 189.6 МПа определяем требуемую кинематическую вязкость масла из [5 с.253 табл. 10.8 ] – 34 мм2с.
В соответствии с кинематической вязкостью назначаем из [4с.362табл.10.10] индустриальное масло И-30А ГОСТ 20799-75.
4 Полости подшипников заполняются пластичной смазкой ЦИАТИМ-201 ГОСТ6267-74.
Перечень использованных стандартов
ГОСТ 831-75 –«Шариковые радиально-упорные подшипники».
ГОСТ 7798-70 – «Болты с шестигранной головкой класса точности В».
ГОСТ 6402-70 – «Шайбы пружинные».
ГОСТ 3128-70 – «Штифты цилиндрические».
ГОСТ 23360-78 – «Шпонки призматические».
ГОСТ 13941-86 – «Кольца пружинные упорные плоские внутренние эксцентрические и канавки для них».
ГОСТ 8752-79 – «Манжеты резиновые армированные для валов».
ГОСТ 12080-66 – «Концы валов цилиндрические».
ГОСТ 19523-81 – «Двигатели трехфазные асинхронные серии 4А».
ГОСТ 1050-88 – «Сталь углеродистая качественная».
ГОСТ 20799-88 – «Жидкие смазочные материалы (масла) индустриальные: И-Г-А-32».
ГОСТ 2789-73 – «Параметры для нормирования шероховатости поверхности».
ГОСТ 24642-81 – «Отклонения и допуски формы цилиндрических поверхностей».
Конструирование узлов и деталей машин: Учеб. Пособие для техн. Спец. вузов П. Ф. Дунаев О. П. Леликов – 5-е изд. перераб. и доп. – М.: Высш. шк. 1998. – 447 с. ил.
Детали машин: Учеб. для студентов высш. техн. учеб. заведений М. Н. Иванов – 5-е изд. перераб. – М.: Высш. шк. 1991. – 383 с. ил.
Детали машин: Учеб. для вузов Л. А. Андриенко Б. А. Байков И. К. Ганулич и др.; Под ред. О.А. Ряховского. – М.: Изд-во МГТУ им. Н. Э. Баумана 2002. – 544 с.
Проектирование механических передач: Учебно-справочное пособие для вузов С. А. Чернавский Г. А. Снесарев Б. С. Козинцов и др. – 9-е изд. перераб. и доп. – М.: Машиностроение 2008. – 590 с. ил.
А.В. Пунтус. Методические указания к выполнению курсового проекта «Анализ схемы силовой и кинематический расчет привода» для студентов механических специальностей дневной и заочной форм обучения. Краснодар.: Изд. КубГТУ 2009. –20с.
А.В. Пунтус. Методические указания к выполнению курсового проекта «Проектный расчет косозубой цилиндрической передачи» для студентов механических специальностей дневной и заочной форм обучения. Краснодар.: Изд. КубГТУ 2009. –17с.
Чертеж6.dwg

Номальный исходный контур
Коэффициент смещения
Степень точности по ГОСТ 1643-81
Наибольшая окружная скорость
Обозначение чертежа сопряженного колеса
Овальность и конусообразность поверхности А
Техническая характеристика
Радиальное смещение валов 0
Угловое смещение валов 0
Осевое смещение валов 3 мм.
Наименование и доп. указания
Гайка М10-7Н.5.019 ГОСТ5915-70
Шайба 10 65Г 019 ГОСТ6402-70
Вновь разработанные изделия
Гайка М8-7Н.5.019 ГОСТ5915-70
Шайба 8 65Г 019 ГОСТ6402-70
КПДМ 24.01.00.002 ВО
Гайка М8-7Н.5.019 ГОСТ 5915-70
Шайба 8 65Г 019 ГОСТ 6402-70
Вновь разробатываемые изделия
Техническая характеристика:
ошибка: утолщить подошву на 5 мм.
* Размер для справок. 2. Неуказанные предельные отклонения размеров: H14
h14 и IT . 3. Маркировать Ч и клеймить К на бирке.
Рекомендуемые чертежи
- 16.03.2019