Разработка технологического процесса изготовления Гайки




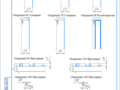
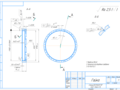

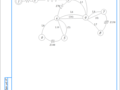
- Добавлен: 24.01.2023
- Размер: 338 KB
- Закачек: 1
Описание
Состав проекта
![]() |
![]() |
![]() |
![]() |
![]() ![]() ![]() ![]() |
![]() ![]() ![]() ![]() |
![]() ![]() ![]() ![]() |
![]() |
![]() ![]() ![]() ![]() |
![]() ![]() ![]() ![]() |
![]() ![]() ![]() ![]() |
![]() ![]() ![]() ![]() |
![]() ![]() ![]() ![]() |
![]() ![]() |
![]() ![]() ![]() |
Дополнительная информация
Граф-дерево.cdw

Деталь с поверхностями.cdw

Совмещенная схема.cdw

Заготовка.cdw

Резец.cdw

Гайка_задание.cdw

Фреза.cdw

Опепационные эскизы.cdw

Операция 10 Токарная
Операция 20 Токарная
Операция 50 Токарная
Операция 60 Токарная
Операция 70 Токарная
Операция 80 Резьбонарезая
Операция 90 Фрезерная
Операция 100 Фрезерная
Операция 130 Фрезерная
Операция 140 Фрезерная
Пояснительная записка.doc
РАЗРАБОТКА ОПЕРАЦИОННОЙ ТЕХНОЛОГИИ10
1 Выбор методов обработки поверхностей детали10
2 Установление этапов обработки поверхностей11
РАЗРАБОТКА МАРШРУТНОЙ ТЕХНОЛОГИИ12
1 Операции маршрутной технологии12
2 Операционные эскизы14
РАЗМЕРНЫЙ АНАЛИЗ ТЕХНОЛОГИЧЕСКОГО ПРОЦЕССА15
1 Совмещенная схема15
3 Размерный анализ16
РАСЧЕТ ОПЕРАЦИИ 50 ТОКАРНАЯ18
1 Выбор оборудования и режущих инструментов18
2 Расчет режимов резания19
3 Расчет норм времени21
4 Определение себестоимости выполнения операций22
РАСЧЕТ ОПЕРАЦИИ 130 ФРЕЗЕРНАЯ23
1 Выбор оборудования и режущих инструментов23
2 Расчет режимов резания24
3 Расчет норм времени25
4 Определение себестоимости выполнения операций26
СПИСОК ИСПОЛЬЗОВАННОЙ ЛИТЕРАТУРЫ28
Целью данного курсового проекта является разработка технологического процесса изготовления детали «Гайка».
Целью курсовой работы является не только закрепление углубление обобщение знаний по основным разделам и темам дисциплины “Технологии Машиностроения” но и разработка технологического процесса изготовления детали «Гайка».
В ходе выполнения курсового проекта необходимо:
oОпределить конструкцию данной детали материал химический состав и свойства материала;
oВыбрать вид заготовки и режущие инструменты;
oРассчитать технологические размеры;
oРассчитать режим обработки и нормы времени для технологических операций;
oТехнологическую себестоимость детали
Описание конструкции детали химический состав и свойства
Деталь «Гайка» изготовлена из Стали 10Х11Н23Т3НР (ГОСТ-5949-75). Сталь 10Х11Н20Т3Р относится к жаропрочным высоколегированным сталям.
Характеристика материала 10Х11Н20Т3Р
Сталь жаропрочная высоколегированная
турбинные диски кольцевые детали крепежные детали детали компрессора и рабочей части турбины с рабочей температурой до 700 град.
Химический состав в % материала 10Х11Н20Т3Р.
Механические свойства при Т=20oС материала 10Х11Н20Т3Р.
Закалка 1100oC воздух
Закалка 1100-1150oC воздух
Заготовку выбираем исходя из минимальной себестоимости готовой детали для заданного годового выпуска. Чем больше форма и размеры заготовки приближаются к форме и размерам готовой детали тем дороже она в изготовлении но тем проще и дешевле ее последующая механическая обработка и меньше расход материала.
При изготовлении детали «Гайка» наиболее целесообразным представляется применение заготовок получаемых с применением Трубного проката – стального бесшовного горячекатаного высокой точности ГОСТ 8732 – 78
mзаг = *(R2-r2)*ρст*b
где mзаг – масса заготовки; R – наружный радиус трубы; r – внутренний радиус трубы; ρст – плотность стали; b – ширина заготовки.
b = 14+2*2+2*05+2*01 = 172мм = 172см
R = 55+1+025 = 5625мм = 5625см
r = 505-1-025 = 4925мм = 4925см
mзаг = 314*(56252-49252)*78*172 = 0253кг
mдет = 314*(552-5052)*78*14 = 0163кг
где mдет – масса детали; R – наружный радиус детали; r – внутренний радиус детали; ρст – плотность стали; b – ширина детали.
Определим коэффициент использования материала (Ким):
Ким = mдетmзаг = 01630253 = 064
Коэффициент Ким должен стремиться к 1. Данная деталь имеет Ким=064 т.к. большое количество материала снимается в виде напуска при получении пазов но не смотря на это заготовка из трубного проката наиболее экономичная и приближается к форме и размерам готовой детали.
Себестоимость заготовки [2 стр.30] рассчитывается по формуле:
где М – затраты на материал заготовки руб; - технологическая себестоимость операций правки труб резки их на штучные заготовки:
где - приведенные затраты на рабочем месте коп.ч; - штучное или штучно-калькуляционное время выполнения заготовительной операции.
где Q – масса заготовки кг; S – цена 1 кг материала заготовки руб.; q – масса готовой детали кг; Sотх – цена 1 т отходов руб.
М = 0253*048-(0253-0163)*251000 = 011 руб.
Со.з. = 220*026000 = 0007руб.
Sзаг = 0007+011 = 0117руб.
Разработка операционной технологии
1 Выбор методов обработки поверхностей детали
Точение черновое + точение чистовое
тонкое точение + закалка
резьбонарезание + закалка
Фрезерование черновое + Фрезерование чистовое
2 Установление этапов обработки поверхностей
Фрезерование черновое
Фрезерование чистовое
Разработка маршрутной технологии
1 Операции маршрутной технологии
При разработке маршрутной технологии всю механическую обработку распределяют по операциям и таким образом выявляют последовательность выполнения операций и их число. В условиях конкретного производства для каждой операции выбирается оборудование и определяется конструкторская схема приспособления.
В маршрутной технологии также предусматривается контроль с целью технологического обеспечения заданных параметров качества обрабатываемой детали. При этом объект контроля и его место назначается после тех операций при которых точность обеспечивается наиболее трудно.
Маршрутная технология механической обработки гайки включает в себя следующие операции:
Операция 10 Токарная. На данной операции производится черновая обработка поверхностей 1 2 5.
Операция 20 Токарная. На данной операции производится черновая обработка поверхностей 3 2 4.
Операция 30 Промывка.
Операция 40 Контроль.
Операция 50 Токарная. На данной операции производится чистовая обработка поверхностей 1 2 5.
Операция 60 Токарная. На данной операции производится чистовая обработка поверхностей 3 2 4.
Операция 70 Токарная. На данной операции тонким точением производится обработка поверхности 1.
Операция 80 Резьбонарезная. На данной операции производится нарезание резьбы на поверхности 5.
Операция 90 Фрезерная. На данной операции производится черновое фрезерование поверхности 6.
Операция 100 Фрезерная. На данной операции производится черновое фрезерование поверхности 7.
Операция 110 Промывка.
Операция 120 Контроль.
Операция 130 Фрезерная. На данной операции производится чистовое фрезерование поверхности 6.
Операция 140 Фрезерная. На данной операции производится чистовое фрезерование поверхности 7.
Операция 150 Промывка.
Операция 160 Контроль.
Операция 170 Закалка. На данной операции производится термообработка закаливанием.
Операция 180 Промывка.
Операция 190 Окончательный контроль с целью технологического обеспечения заданных параметров качества детали.
=5. Размерный анализ технологического процесса
На основе совмещенной схемы и граф-дерева размеров составим таблицу системы уравнений размерной цепи и допусков на технологические размеры:
Допуски на технологические размеры мм
(012)T(5) ≥T L10(012)
(018)T(14)≥T L6(018)
(036)wZ≥T L2+TL1(018+018)
(024)wZ≥T L2+TL1(012+012)
По формуле Zmin=Rz+hc рассчитаем припуски:
Z10= (63 + 60) +0.36 мкм = 123+0.36 = 0.123+0.36 мм
Z20= (63 + 60) +0.36 мкм = 123+0.36 = 0.123+0.36 мм
Z50= (32 + 30)+0.36 мкм = 62+0.36 = 0.062+0.36 мм
Z60=(32 + 30)+0.36 мкм = 62+0.36 = 0.062+0.36 мм
Z70= 5+0.36мкм =0.005+0.36 мм
Z130= (40 + 50)+0.24 мкм = 90+0.24 = 0.09+0.24 мм
Z140= (40 + 50)+0.24 мкм = 90+0.24 = 0.09+0.24 мм
Решим систему уравнений размерной цепи:
L5 = 14-018+0005+036=14005+036-018-018+018 = 14005+018
L4 = 14005+018+0062+036 = 14067+054-018+018 =14067+036+018=14427-018
L3 = 14427-018+0062+036 = 14487+036-018-018+018=14487+018=14667-018=147-018
L2 = 147-018+0123+036 = 14823+036-018-018+018=14823+018=15003-018=15-018
L1 = 15-018+0123+036 = 15123+036-018-018+018=15123+018=15303-018=153-018
L7 = 4±006+009+024 = 409+030-006-006+006 = 409+024
L8 = 5±006+009+024 = 509+030-006-006+006 = 509+024
Расчет операции 50 Токарная
1 Выбор оборудования и режущих инструментов
Для операции 50 Токарная выбран токарно-револьверный станок 1365 по наибольшему диаметру обрабатываемой поверхности.
Режущий инструмент - резец с сечением h x b = 25x16 мм L = 140 мм оснащённый пластиной из твердого сплава марки Т15К6 (ГОСТ 18868 - 73). [1 с.119 т.2]
2 Расчет режимов резания
Глубина резания t: При чистовом точении припуск срезается за 2 прохода и более. На каждом последующем проходе следует назначать меньшую глубину резания чем на предыдущем. При параметре шероховатости обработанной поверхности Ra ≥08 мкм глубина резания
Назначаем t=04 мм при Ra = 25
Подача S: При чистовом точении выбирается в зависимости от требуемых параметров шероховатости и радиуса при вершине резца.
При Ra=25; t=04 мм; s= 0246мм об. [ 1 с. 268 таб. 14 т.2]
где Т - среднее значение стойкости; Т=60 мин
Cv = 420 при подаче до 03 ммоб
s – подача s = 0246 ммоб [1 с. 268 таб. 14 т. 2]
y = 02; m = 02 [1 с. 269 таб. 17 т. 2]
Kv = Kmv*Knv*Kuv = 1*0833*1 = 0833
где Kmv – коэффициент учитывающий влияние материала заготовки для стали 10Х11Н20Т2Р;
= 1*(750900)1 = 0833
Knv – коэффициент учитывающий материал инструмента Knv = 10
Kuv – коэффициент учитывающий состояние поверхности Kuv = 10
v = 420(6002*04015*024602)*0833 = 2343 ммин
Частота вращения инструмента: = 67834
Сила резания обычно раскладывается на составляющие силы направленные по осям координат станка (тангенциальную Pz радиальную Py и осевую Px). При наружном продольном и поперечном точении эти составляющие рассчитываются по формуле:
Значения коэффициента Cp и показателей степеней x y n [1с. 273 таб. 22 т.2]
Kp = KмpKφpKγpKλpKгр
Kмp = (900750)075 = 115
Pz Kφp = l0 Kγp=10 Kλp=l0 Krp=093
Py Kφp = 10 Kγp=l0 Kλp=l0 Krp=082
Px Kφp = -10 Kγp=10 Kλp=l0 Krp=l0
φ = 45° γ = 10° λ=0° r=l0 mm.
Pz = 10*300*041*0246075*2343-015*10695 = 19774Н
Py = 10*243*0409*024606*2343-03*0943 = 8426Н
Px= 10*339*041*024605*2343-04*115 = 872Н
Мощность резания: кВт
Nрез≤ Nэл.дв 0757кВт 13кВт станок подходит
3 Расчет норм времени
Штучное время обработки детали
где Тш-к – штучно-калькуляционнное время для обработки детали;
Тп-з –подготовительно-заключительное время мин;
n – количество деталей в настроечной партии;
Тшт – штучное время обработки детали
Тшт = То + Тв + Тo6.отд = 0154+0206+0009 = 0369 [2 с.101]
где То – основное время;
Тв – вспомогательное время;
Тоб – время на обслуживание рабочего места;
Тот – время на перерыв и отдых;
Тоб =Ттех +Торг [2 с.101]
Торг – время на организацию обслуживания;
Тв = Ту.с.+Тз.о.+Туп+Тиз = 007+0096+004 = 0206 мин [2 с.197 табл.51]
где Ту.с. – время на установку и снятие;
Тзо – время на закрепление и открепление;
Туп – время на управление;
Тиз – время на измерения;
То = 01*110*14 = 0154 мин
Туп = 001+0035+0016+0025+001 = 0096 мин
Тоб.отд = 0154*006 = 0009 мин
Тп-з = 6мин [1 с.605 т.1]
4 Определение себестоимости выполнения операций
Для расчета технологической себестоимости детали нормативным методом воспользуемся следующими данными:
- станкоемкость (То = 0154 мин) станко-минуты;
- трудоемкость (Тш-к = 0374 мин) нормо-минуты;
- разряд работы станочника - токарные работы выполняют рабочие 3 разряда
- сменность (2 смены);
- станок - одношпиндельный автомат продольного точения 1Б240П-8К;
- коэффициент машино-часа для токарно-револьверных станков 1365 при наибольшем диаметре обрабатываемой поверхности = 10
[1 с. 429 таб. 22 т.2];
- годовая программа (среднесерийное производство) = 1000Оптовая цена на заготовки
Ц = α – *lnm =50618 – 6536*In 0253 = 596 руб.т=0596 руб.кг
где α - эмпирические коэффициенты α = 50618; = 6536
[1 с. 421 таб. 7 т.2]
m - масса заготовки m = 0253 кг
Цзаг = gм*Ц*Кт-з= 0253*0596*104 = 0158 коп.
где gм - норма расхода на одну деталь;
kT-3 - коэффициент транспортно-заготовительных расходов.
- норматив заработной платы станочника с начислениями 3 разряда = 268 копмин [1 с. 429 таб. 21 т. 2]
- средние затраты на содержание и эксплуатацию оборудования в течение 1 минуты работы для групп оборудования с коэффициентом машино-часа равным 1 составляет 0594 копмин [1 с. 431 таб. 24 т. 2].
Расчет себестоимости
Зп станочника с начислениями коп.
Затраты на содерж. и экспл. оборудования коп.
Себестоимость обработки коп.
Себестоимость заготовки коп.
Технологическая себестоимость коп.
Расчет операции 130 Фрезерная
Для операции 130 Фрезерная выбран горизонтально-фрезерный универсальный консольный станок 6Р83.
Режущий инструмент – дисковая пазовая фреза(ГОСТ 3964-69)
число зубьев(z) = 18
Глубина фрезерования t и ширина фрезерования B - понятия связанные с размерами слоя заготовки срезаемого при фрезеровании. t измеряют в направлении перпендикулярном к оси фрезы. Ширина фрезерования B определяет длину лезвия зуба фрезы участвующую в резании; B измеряют в направлении параллельном оси фрезы.
Подача S: При чистовом фрезеровании исходной величиной подачи является величина ее на один оборот фрезы s по которой для дальнейшего использования вычисляют величину подачи на один зуб sz = sz
При Ra=25; s= 05 мм об. [ 1 с. 285 таб. 37 т.2]
sz = 03518 = 0019 ммзуб
где Т - среднее значение стойкости; Т=120 мин [1 с. 290 таб. 40 т. 2]
Cv = 1825 при подаче до 006 ммзуб [1 с. 286 таб. 39 т. 2]
s – подача s = 0019 ммзуб
Показатели степени: q = 02; y = 012; u = 01; p = 0; m = 035 [1 с. 269 таб. 17 т. 2]
Частота вращения инструмента:
Сила резания. Главная составляющая силы резания при фрезеровании – окружная сила Н
где z – число зубьев фрезы; n – частота вращения фрезы обмин
Значения коэффициента Cp = 261 и показателей степеней
y = 08; u = 11; q = 11; w = 01 [1с. 291 таб. 41 т.2]
Крутящий момент Н*м на шпинделе
Nрез≤ Nэл.дв 762кВт 11кВт станок подходит
Тшт = То + Тв + Тo6.отд = 0154+0251+0009 = 0414 [2 с.101]
Тв = Ту.с.+Тз.о.+Туп+Тиз = 007+0141+004 = 0251 мин [2 с.197 табл.51]
Туп = 002+0035+0016+004+003 = 0141 мин
- трудоемкость (Тш-к = 0419 мин) нормо-минуты;
- станок - горизонтально-фрезерный универсальный консольный станок 6Р83;
- коэффициент машино-часа для станков 1Б240П-8К при наибольшем диаметре обрабатываемой поверхности = 10 [1 с. 429 таб. 22 т.2];
Список использованной литературы
Справочник технолога-машиностроителя в 2 томах под ред. А.Г. Коси-ловой и Р.К. Мещерякова. М.: «Машиностроение» 1986.
Горбацевич А.Ф.Курсовое проектирование по технологии машиностроения: Учебное пособие. – Мн.:Выс.школа1983
Сборник задач по технологии авиадвигателестроения. Под ред. В.С. Мухина – Уфа: УАИ1987
Рекомендуемые чертежи
- 18.10.2023
- 24.01.2023
- 24.01.2023