Разработка технологического процесса детали втулка



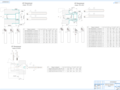
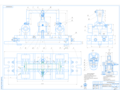
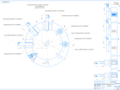
- Добавлен: 24.01.2023
- Размер: 3 MB
- Закачек: 0
Описание
Состав проекта
![]() |
![]() |
![]() ![]() ![]() |
![]() ![]() ![]() |
![]() ![]() ![]() |
![]() ![]() ![]() |
![]() ![]() ![]() |
![]() ![]() ![]() |
![]() ![]() ![]() |
![]() ![]() ![]() |
![]() ![]() ![]() |
![]() ![]() ![]() |
![]() ![]() |
![]() |
![]() |
![]() |
![]() ![]() ![]() ![]() |
![]() |
![]() ![]() ![]() ![]() |
![]() ![]() ![]() ![]() |
Дополнительная информация
+3.Заданная деталь.docx
Шероховатость поверхностей мкм
Дополнительная информация.doc
Револьверная головка BTP-63 Прагати
Инструментальный диск TD-VDI-S-63-8-20-240
Вспомогательный инструмент
+Приложение Б Технические характеристики станков.doc
Станок токарный с ЧПУ и автоматической сменой инструмента ТПК-125А1
Клас точности по ГОСТ 8-82
Наибольший диаметр устанавливаемой заготовки мм
Рекомендуемый диаметр обработки мм
Наибольшая длина обрабатываемой поверхности мм
Наибольшее перемещение суппорта по координате Z мм
Наибольшее перемещение суппорта по координате X мм
Пределы рабочих подач суппорта мммин
Скорость быстрых перемещений суппорта мммин
Дискретность задания перемещения суппорта мм
Нестабильность автоматического останова суппорта мм
Пределы частот вращения шпинделя обмин
Наибольшая высота резца устанавливаемая в резцедержателе мм
Количество инструментов устанавливаемых на станке шт.
Время смены позиции револьверной головки с
Класс точности резьбы нарезаемой резцом
Фланцевый конец шпинделя по ГОСТ 12595
Посадочный конус шпинделя
Шероховатость поверхности обрабатываемых образцов мкм
цветные сплавы (алмазным резцом)
Круглость образца-изделия не более мкм
Постоянство диаметров образца-изделия в продольном сечении мкм
Прямолинейность торцевой поверхности образца-изделия мкм
Мощность привода главного движения кВт
По особому заказу станок может комплектоваться: оснасткой для смазывающее - охлаждающей жидкости (СОЖ); агрегатом автоматизированной подачи прутка; механизмом приема детали; револьверной головкой с вращающимся инструментом ф. «Dup трехкулачковым патроном - SР125-26 с пневмоприводом; дополнительными резцовыми и инструментальными блоками; инструментом и оснасткой под техпроцесс заказчика.
Возможно оснащение станка: устройством лазерно-плазменного полирования; комплектом - БУФО (безабразивная ультразвуковая финишная обработка).
Стандартная комплектация ТПК-125А1:
Револьверная головка на 6 позиций с не вращающимся инструментом;
Цанговый патрон с набором цанг;
-х кулачковый патрон с ручным зажимом.
Вертикально консольно-фрезерный станок с ЧПУ и револьверной головкой 6Р13РФ3
Размеры рабочей поверхности стола мм:
Наибольшее перемещении стола мм:
продольное(по оси X)
поперечное(по оси Y)
продольная и поперечная
Скорость быстрого перемещения стола мммин:
продольного и поперечного
Перемещение гильзы со шпинделем
Наибольший угол поворота шпиндельной головки
Внутренний конус шпинделя (конусность 7:24)
Число скоростей шпинделя
Частота вращения шпинделя мин-1:
от оси шпинделя до вертикальных направляющих станины
от торца шпинделя до рабочей поверхности стола:
Мощность электродвигателя привода главного движения кВт
Общая мощность всех электродвигателей станка кВт
Число управляемых координат
Число одновременно управляемых координат
Дискретность отсчета координат мм
От плоскосности рабочей поверхности
От поралельности верхней поверхности его основанию
От перпендикулярности обработанных поверхностей при контурном фрезеровании цилиндрической поверхности
Масса (без выносного оборудования) кг
+Приложение В Спецификация.doc
Гидроцилиндр 7021-0171 ОСТ 2 Г21-2-87
Плита 7081-2072 ГОСТ 15187-70
Плита 7080-22 ГОСТ 15187-70
Призма 70033-121 ГОСТ 15275-70
Вилка АБВГ ХХХ. ХХХХХХ
Рычаг АБВГ ХХХ. ХХХХХХ
Шток АБВГ ХХХ. ХХХХХХ
Прижим АБВГ ХХХ. ХХХХХХ
Болт АБВГ ХХХ. ХХХХХХ
Ось 701 8-2053 ГОСТ 15407-70
Гайка 7003-2054 ГОСТ 15395-70
Гайка 7003-2003 ГОСТ 1539-70
Гайка М12-6Н.5 ГОСТ 5915-70
Гайка МТЗ-5915006 ГОСТ 5915-70
Приспособление для фрезерного станка
Шпилька 7009-20I26 ГОСТ 15389-70
Шпонка 7031-2001 ГОСТ 15344-70
Шпонка 7031-2075 ГОСТ 14737-69
Гайка М12-6Н.5 ГОСТ 5927-70
Винт 7002-2251 ГОСТ 153883-70
Винт 00027548 ГОСТ 17473-80
Шайба 7019-2003 ГОСТ 15401-70
Шайба 20 ГОСТ 22355-78
Болт пазовый 7002-2067 ГОСТ 15379-70
Болт пазовый 7002-2066 ГОСТ 15379-70
Винт A.M8 - 6g 73 ГОСТ 1491-80
+Приложение Г Комплект документов на ЕТП.docx
МЕХАНИЧЕСКОЙ ОБРАБОТКИ ВТУЛКИ
Отливка КЧ 50-5 ГОСТ 1215-79
Курсовое проектирование
Код наименование операции
Обозначение документа
Код наименование оборудования
1111 мод. ТПК – 125А1 3 15292 212 1Р 1 1 1 14 1 3645 496
1111 мод. ТПК – 125А1 3 15292 212 1Р 1 1 1 14 1 2235 479
1861 мод. 6Р13РФ3 3 15292 212 1Р 1 1 1 14 1 447 352
Стол контрольный 13063 312 1Р 1 1 1 14 1
Наименование операции
КЧ 50-5 ГОСТ 1215-79
Оборудование устройство ЧПУ
Обозначение программы
Токарный с ЧПУ мод. ТПК–125А1
-10% вод. раст. Экол-Б2
ТУ 0258-005-23693454-2003
мм мм ммоб мин-1 ммин мин мин
Установить и закрепить заготовку.
Патрон Ч 7100-00005 ГОСТ 2675-80.
Подрезать торец предварительно выдерживая размер 6585-074.
Резцедержатель 209.32.16. DIN 69880 Резец MWLNR1616Н06 ВК8 ТУ 2-035-892 – 82;
Штангенциркуль ШЦЦ-1-150-001ГОСТ 166-89.
Точить поверхность предварительно выдерживая размер ф846-074.
Резцедержатель 209.32.16. DIN 69880 Резец MTGNR-1616K16 ВК8 ТУ 19-4206-96–83;
Подрезать торец окончательно выдерживая размер 4.
Штангенциркуль ШЦЦ-1-150-001ГОСТ 166-89 Образцы шероховатости ГОСТ 9378-93.
Расточить поверхность предварительно выдерживая размеры ф302+0652 L=907+036
Резцедержатель 169.52.16. DIN 69880 Е2; Резец К.01.498.000-06 ВК8 ТУ 2-035-1040–86;
Штангенциркуль ШЦЦ-1-150-001ГОСТ 166-89
Расточить поверхность предварительно выдерживая размеры ф328+025 L=922+015
Точить поверхность предварительно выдерживая размер ф816-03.
Точить поверхность окончательно выдерживая размер 1
Резцедержатель 209.32.16. DIN 69880 Резец MTGNR-1616K16 ВК4 ТУ 19-4206-96–83;
Расточить поверхность предварительно выдерживая размеры ф344+016 L=971+012
Резцедержатель 169.52.16. DIN 69880 Е2; Резец К.01.498.000-06 ВК4 ТУ 2-035-1040–86;
Расточить поверхность окончательно выдерживая размеры 23
Контроль исполнителем.
мм мм ммоб мин-1 ммин мин мин
Патрон Ч 7100-00005 ГОСТ 2675-80
Подрезать торец предварительно выдерживая размер 6171-074.
Подрезать торец окончательно выдерживая размер 7.
Точить поверхность предварительно выдерживая размеры ф54-074 L=2895 +052
Резцедержатель 209.32.16. DIN 69880 Резец MTGNR-1616K16 ВК8 ТУ 19-4206-96–83;
Подрезать торцевую поверхность с последующим точением канавки выдерживая размер 1.
Резцедержатель 209.32.16. DIN 69880 Резец 035-2126-1177 ВК8 ОСТ 2И10-7–84;
Точить канавку предварительно подрезав торец выдерживая размеры 126.
Расточить поверхность предварительно выдерживая размеры ф268+052 L=902+036
Расточить поверхность предварительно выдерживая размеры ф288+052 L=962+015
асточить поверхность предварительно выдерживая размеры ф268+052 L=902+036
Расточить поверхность предварительно на проход выдерживая размеры ф208+052
Резцедержатель 169.52.16. DIN 69880 Е2; Резец К.01.4981.000-02 ВК8 ТУ 2-035-1040–86;
Расточить поверхность предварительно на проход выдерживая размеры ф228+021
Точить поверхность предварительно выдерживая размеры ф514-03 L=20-025
Расточить поверхность окончательно выдерживая размеры 3 5
Расточить поверхность окончательно на проход выдерживая размер 8
Точить поверхность окончательно выдерживая размер 4
Установить и закрепить заготовку.
Приспособление АБВГ. ХХХХХХ. ХХХ
Сверлить отверстие на проход выдерживая размеры L 5±0008; ф51+0.3
Патрон 1-50-6-90 ГОСТ 26539-85; . Сверло 035-2300-1225 Р6М5 ОСТ 2И20-1–80;
ШтангенциркульШЦЦ-1-150-001ГОСТ 166-89.
Развернуть отверстие на проход выдерживая размеры 14
Патрон 1-50-6-90 ГОСТ 26539-85; Развертка 2363-0062 Р6М5 Гост 1672-80 тип 1;
Фрезеровать паз выдерживая размеры 23
Оправка 6222-4017-100 ТУ2.00223728.013-93 Фреза 2240-0374 Р6М5 ГОСТ 3755-78
+5.отчет.docx
Выбор моделей станков4
Расчет режимов резания6
Расчет технической нормы времени311
Расчет погрешности установки заготовки в приспособление386
Расчет силы зажима40
Техническое задание на проектирование специального
Список использованной литературы433
Приложение А Размерный анализ
Приложение Б Технические характеристики станков
Приложение В Спецификация
Приложение Г Комплект документов на ЕТП
Приложение Д Чертеж детали
Приложение Е Чертежи к КП
В курсовом проекте должны быть умело использованы знания полученные в результате изучения общетеоретических общетехнических и специальных дисциплин учебного плана.
Основными задачами решаемыми в курсовом проекте разработки ЕТП изготовления втулки являются: разработка наиболее рационального с точки зрения экономичности и технологичности технологического процесса обеспечивающего получение годной детали при минимальных затратах труда времени материалов (т.е выбраны оптимальные условия труда) и минимальной стоимости получения детали. Главной задачей изготовления втулки является правильно составленная технология изготовления. От технологии зависит производительность и экономичность процесса. Также важно получение и закрепление навыков ведения самостоятельной инженерной работы.
Пересмотр метода изготовления втулки
Таблица 1 Квалитеты размеров
Таблица 2 Метод изготовления втулки
Методы ступеней обработки поверхностей
Квалитет достигаемой точности (IT)
Получистовая токарная
Черновое растачивание
Получистовое растачивание
Чистовое растачивание
Черновое фрезерование
Черновое развертывание
Выбор моделей станков
Токарные (точение растачивание зенкерование развертывание) операции
выполняем на токарном станке модели ТПК–125А1.
На станке установлена инструментальная головка ВТР-63 и инструментальный диск TD-VDI-S-63-8-20-240
Станок токарный с ЧПУ и автоматической сменой инструмента ТПК-125А1 предназначен для патронной обработки с высокой точностью малогабаритных деталей с большим количеством проходов и сложного профиля из различных конструкционных сталей и сплавов. На станке можно производить все виды токарной обработки. В конструкции станка ТПК-125А1 применены: базовые детали повышенной жесткости шпиндель выполнен на радиально-упорных подшипниках линейные роликовые направляющие с арочным профилем револьверная головка с пневмо-отжимом асинхронный двигатель с частотным регулированием в качестве привода главного движения сервоприводы Maxsine в качестве приводов координат. Наличие на станке револьверной головки и сервоприводов позволяет значительно расширить технологические возможности станка увеличить производительность повысить качество обрабатываемых деталей.
Фрезерно–сверлильную операцию выполняем на станке 6Р13РФ3.
Станок вертикальный консольно-фрезерный с ЧПУ и револьверной головкой предназначен для многооперационной обработки деталей сложной конфигурации из стали чугуна цветных и легких металлов а также других материалов. Наряду с фрезерными операциями на станке можно производить точное сверление растачивание зенкерование и развертывание отверстий.
Технические характеристики станков приведены в Приложении Б
Резец проходной подрезной с трехгранной пластиной ()из твердого сплава с :
Резец MWLNR1616Н06 ВК8 ТУ 2-035-892 – 82
Резец расточной с трехгранной пластиной из твердого сплава:
Резец К.01.4980.000-06 ВК8 ТУ 2-035-1040–86
Резец К.01.4980.000-06 ВК4 ТУ 2-035-1040–86
Резец проходной с с ромбической пластиной () из твердого сплава:
Резец MTGNR-1616K16 ВК8 ТУ 19-4206-96–83
Резец MTGNR-1616K16 ВК4 ТУ 19-4206-96–83
Резец токарный для обработки наружных канавок по стопорные кольца:
Резец 035-2126-1177 ВК8 ОСТ 2И10-7–84
Фреза дисковая трехгранная с радиусом закругления 016мм с предельным отклонением для паза по Р9:
Фреза 2240-0371 Р6М5 ГОСТ 3755–78
Сверло спиральное с коническим хвостовиком с 2φ = 118° и = 55°
Сверло 035-2300-1225 Р6М5 ОСТ 2И20-1–80
Развертка машинная с цилиндрическим хвостовиком и
Развертка 2363-0062 Р6М5 Гост 1672-80 тип 1
Расчет режимов резания
Произведем расчет режимов резания для обработки двух поверхностей (токарная обработка сверление) остальные назначим по справочнику с учетом поправочных коэффициентов.
Черновое точение цилиндрической поверхности 3
Токарная обработка: черновое точение. Резец проходной правый с трехгранной пластиной из твердого сплава ВК8 с φ=90º. Сечение державки 16 х 16 радиус скругления режущей кромки 0025 мм радиус вершины резца 10 мм. Стойкость Т = 45 мин.
Скорость резания ммин
где КV = Кmv·Кnv ·Кuv =10·085·083=0481 - коэффициент учитывающий качество обрабатываемого материала.
- поправочный коэффициент учитывающий влияние материала заготовки [5]
HB=150 MПа - предел прочности обрабатываемого материала при растяжении;
Кпv = 085 - поправочный коэффициент учитывающий состояние поверхностного слоя заготовки [5];
Кuv = 083 - поправочный коэффициент учитывающий влияние инструментального материала на скорость резания[5].
среднее значение стойкости инструмента;
поправочный коэффициент [5]
Постоянная СР и показатели степеней x y z для каждой составляющей силы резания приведены в таблице 2.1 [5]
Таблица 1 Коэфиценты и показатели степеней
Коэффициент и показатели степеней
КР =КМР·Кφр·Кλр·Кγр·Кrp - поправочный коэффициент учитывающий фактические условия резания
Поправочные коэффициенты (КМРКφрКλрКγрКrp) учитывающие влияние геометрических параметров на условия резания заносим в таблицу 2.2 [2]
- поправочный коэффициент учитывающий влияние качества обрабатываемого материала на силовые зависимости [2]
Таблица 2 Поправочные коэффиценты
Материал режущей части
Поправочные коэффициенты
Величина коэффициентов
Главный угол в плане
Радиус при вершине мм
Мощность резания (эффективная):
Расчет режимов резания на поверхность 10
Сверление отверстия
Инструмент: Сверло спиральное с коническим хвостовиком с 2φ = 118° и = 55°
Сверло 035-2300-1234 Р6М5 ОСТ 2И20-1–80
При сверлении глубина резания t = 05* D = 05*51 = 255 мм; где D – диаметр получаемого отверстия.
При сверлении отверстий без ограничивающих факторов берём максимально допустимую по прочности сверла подачу (табл. 25 стр 277[5])
Скорость резания. При сверлении скорость резания ммин равна:
Где С - поправочный коэффициент на скорость; Т – период стойкости; g m y – оказатели степени;
Кv= Кmv Кnv Кuv Kov=1*083*10*0.5=0415– общий поправочный коэффициент;
Км =1 – коэффициент на обрабатываемый материал;
Ки = 083 – коэффициент на инструментальный материал;
К = 10 – коэффициент учитывающий глубину сверления.
Где значения коэффициента Cv и показателей степени из таблицы 28 стр 278[5] а период стойкости Т- из таблицы 30 стр 279-280[1]
Cv=21.8; g=025; y=0125; m=055 Т=35мин;
Главная составляющая силы резания при сверлении - осевая сила Н
Где: Cр- поправочный коэффициент; Кр – коэффициент учитывающий фактические условия обработки.
Значение коэффициента Cр и показателей степени из табл. 32 поправочный коэффициент из табл. 9[5] .Cр=43.3; y=08; g=10; Кр=06
Мкр=10=10*0.021*5.10.2*013508*06=036 Н м
где См =0021– поправочный коэффициент; Кр =06– коэффициент учитывающий фактические условия обработки.
Мощность резания (эффективная) кВт
Режимы резания на остальные поверхности выбираем по справочнику [7]
Расчет режимов резания на поверхность 14
Содержание операции и стадии обработки: 1) черновая подрезка торца получистовая подрезка торца для поверхности 1 4.
Глубина резания для черновой стадии обработки на оби поверхности составляет ; для получистовой стадии обработки .
Для I стадии обработки глубина резания
Для черновой стадии обработки при подрезке терцев подачу выбирают по карте 3[2]. При глубине резания t до 2мм и диаметре детали до 180мм Для получистовой стадии обработки значения подач для данных поверхностей определяют по карте 4[2] аналогичным образом: при диаметре детали до 180мм и глубине резания до 15мм –
Выбранные значения подач корректируют по карте 5[2] для измененных условий в зависимости от:
инструментального материала ;
сечения державки резца;
прочности режущей части;
механических свойств обрабатываемого материала ;
схемы установи заготовки ;
состояния поверхности заготовки
геометрических параметров режущей части инструмента;
при получистовой обработке ковкого чугуна значение подачи умножаем на Ks=09
Окончательно значения подач для черновой и получистовой стадий обработки определяют по формуле
С учетом поправочных коэффициентов подачи принимают следующие значения:
для черновой стадии:
для поверхности 14 ;
для получистовой стадии :
для поверхности 14 .
Выбор скорости резания
Скорость резания для черновой и получистовой стадий обработки для поверхностей 1 4 выбирают по карте 21[2]. Черновой стадии обработке соответствует скорость резания для поверхностей 14 получистовой стадии обработки соответствует скорость резания для поверхности 14 .
По карте 23[2] выбирают поправочные коэффициенты на скорость резания для черновой и получистовой стадий обработки для измененных условий в зависимости от:
группы обрабатываемости материала
механических свойств обрабатываемого материала
геометрических параметров резца
периода стойкости (Т=30 мин) режущей части
Значение скорости для черновой и получистовой стадий обработки определяют по форме
С учетом поправочных коэффициентов у скоростей следующие значения:
На получистовой стадии
Частоту вращения шпинделя определяют по формуле .
Для черновой стадии обработки:
Принимаем частоту вращения для поверхности 14 тогда скорость резания
Для получистовой стадии обработки
для поверхности 14 Принимаем частоту для поверхности 14 .
Тогда скорость резания
Проверка выбранных режимов резания по мощности привода главного движения
Для черновой и получистовой стадий обработки мощность резания определяют по карте 21[2] аналогично выбору скорости и корректируют в зависимости от твердости обрабатываемого материала для черновой стадии обработки (карта 24[2]).
На черновой стадии обработки
На получистовой стадии обработки
Расчет режимов резания на поверхность 23
Базирование в патроне. Содержание операции – точить поверхность 23.
Выбор стадий обработки
Ведем в три стадии: черновое получистовое и чистовое точение.
Выбор глубины резания
По карте 2[2] определяют минимально необходимую глубину резания для получистовой стадии обработки.
При чистовой стадии обработки: для поверхности 2 диаметр которой соответствует интервалу размеров 30 50мм рекомендуется для поверхности 3 диаметр которой соответствует интервалу размеров 50 80мм рекомендуется .
При получистовой стадии обработки: для поверхности 2 диаметр которой соответствует интервалу размеров 30 50мм рекомендуется для поверхности 3 диаметр которой соответствует интервалу размеров 50 80мм рекомендуется .
Глубину резания на черновой операции определяют следующим образом
Для черновой стадии обработки подачу выбирают по карте 3[2]. Для поверхности 2 при точении детали диаметром до 180 мм с глубиной резания рекомендуется подача . Для поверхности 3 рекомендуется . По карте 3[2] определяют поправочные коэффициенты на подачу в зависимости от инструментального материала для поверхности .
Для получистовой стадии обработки значения подач определяют по карте 4[2] аналогично. Для поверхности 2 для поверхности 3 . Поправочные коэффициенты на подачу в зависимости от инструментального материала .
По карте 5 определяют поправочные коэффициенты на подачу для черновой и получистовой стадий обработки для измененных условий обработки в зависимости от:
Расчетные подачи для черновой стадии обработки проверяют по осевой и радиальной составляющим силы резания допустимым прочностью механизма подач станка.
Табличные значения составляющих силы резания при обработке поверхности 2 с глубиной резания 2мм и подачей а так же для поверхности 3 с глубиной резания 27мм и подачей определяют по карте 32[2]
для поверхности 3 . По карте 33[2] определяют поправочные коэффициенты на силы резания для измененных условий в зависимости от:
главного угла в плане
угла наклона режущей кромки
Значение составляющих силы резания определяют по формулам
Рассчитанные значения составляющих силы резания меньше допустимых механизмом подач станка в соответствующем направлении.
Для чистовой стадии обработки рекомендуемые значения подач выбираем по карте 6[2]. Для поверхности 2 для поверхности 3.
По карте 8 определяют поправочные коэффициенты на подачу для чистовой стадий обработки для измененных условий обработки в зависимости от:
радиуса вершины резца ;
квалитета обрабатываемой детали ;
кинематического угла в плане .
Окончательно подачу для чистовой обработки определяют :
Скорость резания для черновой и получистовой стадий обработки для поверхностей 2 3 выбирают по карте 21[2] для чистовой стадии по карте 22[2]. Черновой стадии обработке соответствует скорость резания для поверхностей 2 3 ; получистовой стадии обработки соответствует скорость резания для поверхности 2 3 ; чистовой стадии для поверхности 2 для поверхности 3 .
для поверхности 2 3 ;
Для черновой стадии обработки:
Принимаем частоту вращения для поверхности 2 тогда скорость резания
Принимаем частоту вращения для поверхности 3 тогда скорость резания
для поверхности 3 Принимаем частоту для поверхности 2 для поверхности 3 .
Для чистовой стадии обработки
Принимаем частоту для поверхности 2 для поверхности 3 .
Расчет режимов резания на поверхность 57
Содержание операции: 1) расточить поверхность 7; 2)расточить поверхность 5.
Стадии обработки: Для поверхности 7 черновое получистовое чистовое точение; для поверхности 5 черновое получистовое чистовое тонкое точение.
Выбор минимально необходимой глубины резания для II(получистовой) III(чистовой) и IV(тонкой) стадий осуществляется по карте 2 [2] в последовательности обратной обработке.
Для поверхности 7 (30Н12) диаметр детали входит в интервал размеров 18 30мм. Глубина резания для получистовой стадии обработки мм; для чистовой стадии обработки мм.
Для черновой стадии обработки глубина резания
Для поверхности 5 (35Н8) диаметр детали входит в интервал до 50мм. Глубина резания для тонкого чистового получистового точения ; ; .
Для черновой стадии обработки подачу выбирают по карте 9[2]. При растачивании резцом круглого сечения d=16мм для поверхности 7 при глубине резания 44мм и для поверхности 5 при глубине резания 61 мм при растачивании резцом с круглым сечением 16 мм . Для получистовой стадии обработки значения подач для поверхности 7 и 5 определяют по карте 10[2] аналогичным образом: для поверхности 7 – для поверхности 5 – .
Выбранные значения подач корректируют по карте 11[2] для измененных условий в зависимости от:
инструментального материала
геометрических параметров резца
Принятое значение подачи на черновой стадии обработки проверяют по осевой и радиальной составляющим силы резания допустимым прочностью механизма подач.
Табличные значения составляющих силы резания при обработке поверхности 7 с глубиной резания 44мм и подачей а так же для поверхности 5 с глубиной резания 61мм и подачей определяют по карте 32[2]
для поверхности 5 . По карте 33[2] определяют поправочные коэффициенты на силы резания для измененных условий в зависимости от:
Рекомендуемые значения подач:
для чистовой стадии обработки выбирают по карте 12[2]
для отделочной стадии обработки для поверхности 5 выбирают по карте 13[2]
По карте 14[2] определяют поправочные коэффициенты на подачу для чистовой и отделочной стадий обработки для изменений условий в зависимости от:
радиуса вершины резца;
квалитета обрабатываемой детали на чистовой стадии для на отделочной стадии ;
Окончательно значения подач для чистовой и отделочной стадий обработки определяют по формуле
для чистовой стадии ;
для отделочной стадии .
Скорость резания для черновой и получистовой стадий обработки для поверхностей 7 5 выбирают по карте 21[2]. Черновой стадии обработке соответствует скорость резания для поверхности 7 для поверхности 5 ; получистовой стадии обработки соответствует скорость резания для поверхности 7 для поверхности 5 . Скорость резания для чистовой и отделочной стадий обработки выбирают по карте 22[2]. Чистовой стадии обработки соответствует скорость резания для поверхности 7 для поверхности 5 ; отделочной стадии поверхности 5. По этой карте скорости резания корректируют с учетом инструментального материала .
для отделочной стадии обработки
для поверхности 5 Принимаем частоту для поверхности 7 для поверхности 5 .
тогда скорость резания
Для чистовой стадии обработки
для поверхности 7 Принимаем частоту для поверхности 7 .
для поверхности 5 Принимаем частоту для поверхности 5
Для отделочной стадии обработки
для поверхности 5 Принимаем частоту для поверхности 5 .
Расчет режимов резания на поверхность 6
Содержание операции: обработать отверстие 25+0052(Н9) мм длиной 40 мм с параметром шероховатости поверхности Ra=25 мкм.
Вариант маршрута обработки
Маршрут обработки включает в себя черновое растачивание получистовое растачивание чистовое растачивание.
Для поверхности 6 (25Н9) диаметр детали входит в интервал размеров 18 30мм. Глубина резания для получистовой стадии обработки мм; для чистовой стадии обработки мм.
Для черновой стадии обработки подачу выбирают по карте 9[2]. При растачивании резцом круглого сечения d=16мм для поверхности 6 при глубине резания 19мм . Для получистовой стадии обработки значения подач для поверхности 6 определяют по карте 10[2] аналогичным образом: .
Табличные значения составляющих силы резания при обработке поверхности 6 с глубиной резания 19мм и подачей определяют по карте 32[2]
По карте 33[2] определяют поправочные коэффициенты на силы резания для измененных условий в зависимости от:
Рекомендуемые значения подач для чистовой стадии обработки выбирают по карте 12[2]:
По карте 14[2] определяют поправочные коэффициенты на подачу для чистовой стадий обработки для изменений условий в зависимости от:
квалитета обрабатываемой детали на чистовой стадии для;
С учетом поправочных коэффициентов подачи принимают следующие значения ;
Скорость резания для черновой и получистовой стадий обработки для поверхности 6 выбирают по карте 21[2]. Черновой стадии обработке соответствует скорость резания ; получистовой стадии обработки соответствует скорость резания . Скорость резания для чистовой стадии обработки выбирают по карте 22[2]. Чистовой стадии обработки соответствует скорость резания .
Принимаем частоту тогда скорость резания
Принимаем частоту тогда скорость резания
Расчет режимов резания на поверхность 8
Содержание операции и стадии обработки: 1) точить канавку с предварительной подрезкой торца 8.
Расчет режимов на точение канавки.
При прорезании канавок подачу выбирают по карте 27[2] в зависимости от ширины режущей части резца и ограничиваются применяемой маркой инструментального материала. При ширине резца t до 5мм и диаметре детали до 150мм
Выбранные значения подач корректируют по карте 29[2] для измененных условий в зависимости от:
шероховатости обработанной поверхности
отношения конечного и начального диаметра обработки ;
С учетом поправочных коэффициентов подачи принимают следующие значения: ;
Скорость резания при прорезании канавок выбирают по карте 30[2] и ограничивают маркой инструментального материала. Скорость резания . По карте 21[2] выбирают поправочные коэффициенты в зависимости от инструментального материала .
По карте 31[2] выбирают поправочные коэффициенты на скорость резания при прорезании канавок для измененных условий в зависимости от:
периода стойкости (Т=30 мин) режущей части ;
наличия охлаждения ;
группы обрабатываемости материала ;
Значение скорости для получистовой стадий обработки определяют по форме
Принимаем частоту .
Расчет режимов на подрезку торца канавачным резцом.
Глубина резания для получистовой стадии обработки .
Для получистовой стадии обработки при подрезке торцев подачу выбирают по карте 4[2]. При глубине резания t до 3мм и диаметре детали до 180мм
Скорость резания для получистовой стадий обработки выбирают по карте 21[2]. Получистовой стадии обработки соответствует скорость резания . По карте 21[2] выбирают поправочные коэффициенты в зависимости от инструментального материала .
Для получистовой стадий обработки мощность резания определяют по карте 21[2] аналогично выбору скорости и корректируют в зависимости от твердости обрабатываемого материала (карта 24[2]).
Расчет режимов резания на поверхность 9
Содержание операции: фрезеровать паз выдерживая размеры h=3мм l=5мм (Н14) с параметром шероховатости поверхности Rz=40 мкм.
Охлаждение – эмульсия.
Глубина резания на фрезерование равна глубине паза 3мм t=3мм.
Фрезу выбирают по выбирают по ГОСТ3755–78. Форма заточки инструмента нормальная.
При фрезеровании дисковыми фрезами размеры зависят от геометрических параметров режущего инструмента.
При фрезеровании дисковыми двух-и трехсторонними фрезами подачу на зуб выбирают по карте 95[2] исходя из группы обрабатываемого материала диметра и числа зубьев фрезы глубины и ширины фрезерования.
Полученное значение подачи умножают на поправочные коэффициенты в зависимости от:
твердости обрабатываемого материала
отношение вылета оправки к диаметру оправки
фактического числа зубьев фрезы
формы обрабатываемой поверхности
Скорость и мощность резания выбирают по картам 96-98[2] исходя из диаметра фрезы глубны и ширины фрезерования подачу на зуб фрезы.
Полученные значения скорости и мощности резания умножают на поправочные коэффициенты в зависимости от:
твердости обрабатываемого материала;
материала режущей части фрезы;
периода стойкости режущей части фрезы ;
отношение фактической ширены фрезы к нормальной ;
отношения вылета оправки к диаметру оправки ;
формы обрабатываемой поверхности .
Частоту вращения шпинделя определяют п формуле
По паспорту станка принимают ближайшее значение
Фактическая скорость резания .
Содержание операции: обработать отверстие 6Н10 мм длиной 75 мм с параметром шероховатости поверхности Rz=40 мкм.
Маршрут обработки включает в себя сверление развертывание черновое.
Глубина резания на переходах развертывания определяют по карте 45[2] и корректируют с учетом последовательности переходов маршрута (поправочный коэффициент Кti).
Черновое развертывание t=018; Кti=24 окончательно t=018·24=043
Расчет диаметров обрабатываемого отверстия по переходам маршрута и выбор инструмента
Диаметры обрабатываемого отверстия по переходам находят по формуле
C учетом ранее определенных глубин резания диаметры отверстия находят для:
сверления D=6-2·043=514
С учетом округления принимают следующие размеры инструментов:
Сверло выбирают по ОСТ 2И20-1–80. Форма заточки инструмента нормальная.
Выбор подачи скорости мощности и осевой силы резания осуществляют по картам 46 51 [2] для ближайшего большего табличного значения диаметра инструмента.
В данном случае значения этих величин выбирают для:
сверления при диаметре D=51 мм отношения длины рабочей части сверла к диаметру lD=3. Для этих значений по карте 46 лист2 [2] определяют
чернового развертывания диаметру D=6мм соответствует ближайшее табличное значение DT=12мм; по карте [2 карта 49 лист1] определяют:
Значение частот вращения шпинделя для табличных значений скорости резания определяют по формуле
Табличные значения режимов резания корректируют в зависимости от измененных условий работы по формулам корректировки приведенным в карте 52[2]. Значения поправочных коэффициентов выбирают из карты 53[2].
В данном случаи для переходов:
Подачу корректируют по формуле (карта 52[2]).
Коэффициент выбирают по карте 53 лист 1[2].
Для ковкого чугуна (150 НВ)
С учетом коэффициента
Скорость редактируется по формуле
По карте 53 [2] выбирают коэффициенты:
( Для ковкого чугуна 150 НВ);
(для нормальной формы заточки инструмента);
(обработка с охлаждением);
(состояние обрабатываемой поверхности отливка без корки);
(материал инструмента – быстрорежущая сталь);
(сверло по ОСТ 2И20-1–80)
(инструментальный материал без покрытия)
Скорректированную частоту вращения шпинделя рассчитываем по формуле
Скорость резания определяется по формуле
По паспортным данным станка выбирают ближайшую имеющуюся у станка частоту вращения .
Окончательно принимают мин-1 мммин ммоб.
Фактическую скорость резания определяют по формуле
Чернового развертывания.
Подачу корректируем по формуле (карта 52)[2].
Скорость корректируем по формуле
По карте 53 [2] выбирают: ;
( обрабатываемая поверхность без корки);
( предшествующий переход был сверление);
(инструментальный материал без покрытия).
С учетом поправочных коэффициентов определяют значения подачи
скорости частоты вращения шпинделя и скорости подачи :
для чернового развертывания
С учетом паспортных данных станка фактические режимы резания выбирают: мин-1 мммин ммоб ;
Фактическая скорость резания
Корректировка табличных значений мощности резания и осевой силы
По карте 52[2] формулы для корректировки мощности резания и осевой силы имеют вид:
По карте 53[2] выбирают поправочные коэффициенты
С учетом определенных коэффициентов скорректированные значения мощности и осевой силы определяют по формулам:
для развертывания ; ;
Установленные режимы резания осуществимы на данном станке так как максимальная осевая сила максимальная мощность не превосходят допустимых значений станка.
Таблица 3. Режимы резания
Расчет технической нормы времени
Расчёт нормы штучно-калькуляционного времени.детали 0670кг производство единичное размер партии деталей – 1500 штук количество деталей в партии для одновременного запуска 146шт. Исходная заготовка прокат 65мм. Определим состав штучного времени на обработку детали для каждой из операций технологического процесса.
1 Расчет нормы времени для операции 005 программная
Расчет нормы штучно-калькуляционного времени для токарной операции выполняемой на станке с ЧПУ. Токарный станок модели ТПК-125А1.
Таблица: Расчёт подготовительно-заключительного времени
Карта позиция индекс
Наладка станка приспособлений инструмента программных устройств
Установить патрон трехкулачковый
Установить исх. режимы работы станка(число оборотов и подач)
Установить и снять инструментальный блок и РИ
Набрать программу и проверить её
Установить исх.координаты X и Z
Настроить устройство для подачи СОЖ
Карта 21 поз.31 Карта 21 поз.33
1.1 Норма подготовительно-заключительного времени
где норма времени на организационную подготовку; норма времени на наладку станка приспособления инструмента; норма времени на пробную обработку.
1.2 Штучное время обработки детали
где время на обсл. и отдых в % от операционного времени [6];
норма операционного времени мин
норма основного времени мин
длина обрабатываемой поверхности мм;
минутная подача мммин;
черновая подрезка торца №4;
черновое точение поверхности №3;
получистовая подрезка торца №4;
черновое растачивание поверхности №5;
получистовое точение поверхности №3;
получистовое растачивание поверхности №5;
чистовое точение поверхности №3;
чистовое растачивание поверхности №5;
тонкое растачивание поверхности №5.
норма вспомогательного времени мин.
Общее вспомогательное время на операцию
вспомогательное время на установку и снятие детали [7];
вспомогательное время по управлению станком [7 карта 14];
вспомогательное время на контрольное измерение [7карта 15].
Вспомогательное время на переходы
черновая подрезка торца;
черновое точение поверхности;
получистовая подрезка торца;
черновое растачивание поверхности;
получистовое точение поверхности;
получистовое растачивание поверхности;
чистовое точение поверхности;
чистовое растачивание поверхности;
тонкое растачивание поверхности.
Общее вспомогательное время по переходам: .
Вспомогательное время на всю операцию
2 Расчет нормы времени для операции 010 программная
Установить исх. режимы работы станка
(число оборотов и подач)
2.1 Норма подготовительно-заключительного времени
2.2 Штучное время обработки детали
где время на обсл. и отдых в % от операционного времени [6]
норма операционного времени мин.
черновая подрезка торца №1;
получистовая подрезка торца №1;
черновое точение поверхности №2;
черновое подрезка торцевой поверхности №8;
черновое растачивание поверхности №7;
получистовое растачивание поверхности №7; черновое растачивание поверхности №6;
получистовое растачивание поверхности №6;
получистовое точение поверхности №2; чистовое растачивание поверхности №7; чистовое растачивание поверхности №6;
чистовое точение поверхности №2.
норма вспомогательного времени мин
вспомогательное время на установку и снятие детали [7];
вспомогательное время по управлению станком [7 карта 14];
черновое точение поверхности;
черновая подрезка торцовой поверхности;
черновое точение канавки;
черновое растачивание поверхности;
получистовое растачивание поверхности
чистовое растачивание поверхности.
Общее вспомогательное время по переходам .
Вспомогательное время на всю операцию .
3 Расчет нормы времени для операции 015 программная
Расчет нормы штучно-калькуляционного времени для фрезерно-сверлильной операции выполняемой на станке с ЧПУ. Фрезерный станок модели 6P13PФ3.
Установить и снять приспособление в ручную
Подключить приспособление к гидросети
Переместить стол бабку шпиндель в зону удобную для наладки
Установить исходные режимы резанья
Ввести программу в память сис. с ЧПУ
Установить РИ и длину обработки
Для измерения поверхности по пл.
3.1 Норма подготовительно-заключительного времени
где норма времени на организационную подготовку;
норма времени на наладку станка приспособления инструмента;
норма времени на пробную обработку.
3.2 Штучное время обработки детали.
где время на обслуживание и отдых в % от операционного времени [6]
норма основного времени мин.
– фрезерование 4 пазов пов. 9;
– сверление 4 отверстий пов. 10;
– развертывание 4 отверстий пов. 10.
вспомогательное время на установку и снятие детали [7]
вспомогательное время по управлению станком; [7]
вспомогательное время на контрольное измерение [7]
Вспомогательное время непосредственно на обработку
Расчет погрешности установки заготовки в приспособление
Погрешность установки заготовки в приспособление равна сумме погрешностей базирования закрепления и положения заготовки .
1 Расчет погрешности базирования
Погрешность базирования - есть отклонение фактически достигнутого положения заготовки при базировании от требуемого положения.
Погрешность базирования размера А1 равна допуску на размер В
Погрешность базирования на размер А2 равна допуску на размер С
Погрешность базирования на размерравна нулю так как размер получается инструментом.
2 Расчет погрешности закрепления
Погрешность закрепления – это разность предельных смещений измерительной базы в направлении получаемого размера под действием силы зажима заготовки.
Погрешность закрепления рассчитывается по формуле:
где α- угол между направлением получаемого размера и направлением приложения силы зажима.
ymax ymin- предельные смещения измерительной базы в направлении получаемого размера.
т.к. α=90º а то погрешность закрепления равна нулю .
В погрешность размеравходит экстренсититет и рассчитывается по формуле
3 Расчет погрешности приспособления
Погрешность положения заготовки - это погрешность при изготовлении и сборке его установочных элементов износе последних и ошибках установки приспособления на станке.
Где ус- характеризует неточность положения установочных элементов ус = 0015мм; и характеризует износ установочных элементов приспособления и = 0; с -погрешность установки приспособления на станке с=001мм.
Подставим значения в формулу
Проектируемое приспособление удовлетворяет требуемой точности.
Зажимами называют механизмы устраняющие возможность вибрации или смещения заготовки относительно установочных элементов под действием собственного веса и сил возникающих в процессе обработки.
Расчет силы зажима сведен к решению задачи статики на равновесие твердого тела под действием внешних сил.
К заготовке с одной стороны приложена сила тяжести и силы возникающие в процессе обработки с другой - искомые зажимные силы и реакции опор.
Исходя из того что заготовка закреплена в призме с сила зажима рассчитывается по следующей формуле:
где составляющая силы резания стремящаяся вырвать деталь из приспособления; коэффициент запаса.
Коэффициент запаса находится по формуле:
где гарантированный коэффициент запаса;
коэффициент учитывающий однолезвийность инструмента;
коэффициент учитывающий многоместность приспособления;
коэффициент учитывающий внезапные факторы твёрдые включения в обрабатываемом материале выкрашивание режущей кромки инструмента;
коэффициент учитывающий наличие случайных неровностей на поверхности заготовки (чистовая обработка);
коэффициент учитывающий увеличение сил резания от прогрессирующего затупления режущего инструмента (фрезерование по стали);
коэффициент учитывающий увеличение силы резания при прерывистом резании;
коэффициент учитывающий стабильность силового привода (гидравлический привод);
коэффициент учитывающий удобство расположения рукояток в ручных
зажимных устройствах;
коэффициент учитывающий наличие моментов стремящихся повернуть заготовку;
коэффициенты трения детали с призмой.
Значение коэффициента Cр и показателей степени из табл. 41 стр291[5] поправочный коэффициент на качество обрабатываемого материала из табл. 9.
где усилие зажима; номинальное давление масла; КПД гидроцилиндра.
Принимаем стандартный диаметр цилиндра .
Для приспособления берем стандартный гидравлический цилиндр одностороннего действия.
Техническое задание на проектирование специального приспособления
Таблица 8.1 - Техническое задание на проектирование специального приспособления.
Наименование и область применения
Приспособление для сверления отверстия 6H10мм и фрезерования паза шириной 3мм глубиной 5мм.
Основания для разработки
Операционная карта технологического процесса механической обработки втулки.
Цель и назначение разработки
Проектируемое приспособление должно обеспечить:
точную установку и надежное закрепление заготовки втулки а также постоянное во времени положение заготовки относительно положения станка и режущего инструмента с целью получения необходимой точности размеров и их положения относительно поперечного паза; удобство установки закрепления и снятия заготовки.
Технические (тактико-технические требования)
Тип производства–единичное; программа выпуска-150год.
Регулирования конструкции приспособления не допускается. Время закрепления заготовки не более 069мин. Уровень унификации и стандартизации деталей приспособления 75%. Входные данные о заготовке: диаметр заготовки: 50-010 мм Rz 20 мкм;
Длина заготовки 60-040 мм шероховатость торцов заготовки Ra =2.5мкм.
Выходные данные операции:
Диаметр отверстия 6+0048мм; Глубина отверстия на проход; ширина паза 3+025мм; глубина паза 5+03мм. Характеристика режущих инструментов:
Сверло 035-2300-1225 Р6М5 ОСТ 2И20-1–80
Режимы резания штучное время на операцию приведены в операционной карте.
Список использованной литературы
Гузеев В. И. Режимы резания для токарных и сверлильно-фрезерно-расточных станков с числовым программным управлением: : справочник В. И. Гузеев В. А. Батуев И. В. Сурков. – 2-е изд. Под ред. В. И. Гузеева. М: Машиностроение 2007. – 368 с.
Режимы резания на работы выполняемые на шлифовальных и доводочных станках с ручным управлением и полуавтоматах : справочник Д. В. Ардашев [и др.]. – Челябинск: АТОКСО 2007. – 384 с.
Справочник технолога-машиностроителя. В 2-х т. Т. 1 Под ред. А. Г. Косиловой и Р. К. Мещерякова. – 4-е изд. перераб. и доп. – М.: Машиностроение 1986. – 656 с.: ил.
Справочник технолога-машиностроителя. В 2-х т. Т. 2 Под ред. А. Г. Косиловой и Р. К. Мещерякова. – 4-е изд. перераб. и доп. – М.: Машиностроение 1986. – 496 с.: ил.
Общемашиностроительные нормативы времени и режимов резания для нормирования работ выполняемых на универсальных и многоцелевых станках с числовым программным управлением: в 2 т. под общ. ред. С.Ю.Романова – М.: Экономика 1990. – Т.1. - 207с.
Общемашиностроительные нормативы времени и режимов резания для нормирования работ выполняемых на универсальных и многоцелевых станках с числовым программным управлением: в 2 т. под общ. ред. С.Ю.Романова – М.: Экономика 1990. – Т.2. - 472с.
Обработка металлов резаньем : Справочник технолога А.А. Панов [и др.]; под общ. ред. А.А. Панова – М.: Машиностроение 1988. – 736 с.: ил.
Кузнецов Ю. И. Оснастка для станков с ЧПУ : справочник Ю. И. Кузнецов А. Р. Маслов А. Н. Бойков. – 2-е изд. перераб. и доп. – М.: Машиностроение 1990. – 512 с.: ил.
Терликова Т.Ф. Основы конструирования приспособлений: учебное пособие для машиностроительных вузов. Т.Ф. Терликова А.С. Мельников В.И. Баталов. – М.: Машиностроение 1980. – 119с.: ил.
+1.Титульный лист.doc
Федеральное агентство по образованию
ИРКУТСКИЙ ГОСУДАРСТВЕННЫЙ ТЕХНИЧЕСКИЙ УНИВЕРСИТЕТ
Кафедра технологии машиностроения
РАЗРАБОТКА ЕТП ОБРАБОТКИ ДЕТАЛИ ТИПА ВТУЛКИ
ПОЯСНИТЕЛЬНАЯ ЗАПИСКА
к курсовой работе по дисциплине «Технология машиностроения»
Нормоконтролер Я. И. Солер
+2.Задание.docx
Федеральное агентство по образованию
ИРКУТСКИЙ ГОСУДАРСТВЕННЫЙ ТЕХНИЧЕСКИЙ УНИВЕРСИТЕТ
Кафедра технологии машиностроения
по дисциплине Технология машиностроения
Студента ФТиКМ группы ММ-07-1 Марчук Д.П. .
Тема курсовой работы: РАЗРАБОТКА ЕТП ОБРАБОТКИ ДЕТАЛИ ТИПА ВТУЛКИ
Годовая программа: N =150
Графический материал:
) Графическая технология изготовления втулки (А1 – 1 лист).
) Технологическая наладка (А1 – 1 лист).
) Приспособление для сверления отверстия 6H10мм и фрезерования паза b=5мм h=3мм (А1 – 1 лист).
Дата выдачи задания « » 2011г.
Срок выполнения курсовой работы « » 2011г.
Руководитель курсовой работы (Я. И.Солер)
Студент (Д. П. Марчук)
+4.Аннотация.docx
студента ФТиКМ гр. ММ-07-1 Д. П. Марчука
ПЗ на 43 стр. в том числе рисунки 3 листа чертежей приложения.
Иркутский государственный технический университет 2011г.
В курсовом проекте представлено: разработан маршрут изготовления втулки 1.012.00.00.00; выбраны режимы резания по справочнику и произведен их перерасчет ; выбор станков и приспособлений; расчет технической нормы времени; разработано ТЗ на изготовление специального приспособления расчет силы зажима; расчет точности приспособления; разработан ЕТП на изготовление втулки.
В конструкторской части работы на форматах А1 спроектировано приспособление для сверления отверстия и фрезерования паза выполнен чертёж графической технологии обработки детали и инструментальной наладки.
+Приложение А Размерный анализ.doc
Рассчитанные операционные размеры
Прииспособление для фрезерного станка3.cdw

Неуказанные предельные отклонения IT14(it14)
Острые кромки притупить.
Трущиеся поверхности смазать смазкой ЭРА.
Технические характеристики:
Усилие зажима на плунжере 12600Н
гидравлическом цилиндре - 10 МПа.
Номинальное рабочее давление гидропласта в
Объем заполняемый гидропластом в гидравлическом
Инструментальная наладка2.cdw

Резцедержатель 209.32.16. DIN 69880 B2
Резец MWLNR1616Н06 ВК8 ТУ 2-035-892 - 82
Резец MTGNR-1616K16 ВК8 ТУ 19-4206-96-83
Резец К.01.4980.000-02 ВК8 ТУ 2-035-1040-86
Резцедержатель 169.52.16. DIN 69880 Е2
Резец К.01.4980.000-02 ВК4 ТУ 2-035-1040-86
Резец MTGNR-1616K16 ВК4 ТУ 19-4206-96-83
Графическая техналогия механической обработки втулки1.cdw

Резец MTGNR-1616K16 BK8 ТУ 19-4206-96-83
Резец MWLNR1616H06 ВК8 ТУ2-035-892-82
Резец К.01.4980.000-02 ВК8 ТУ-035-1040-86
Резец MTGNR-1616K16 BK4 ТУ 19-4206-96-83
Резец К.01.4980.000-02 ВК4 ТУ-035-1040-86
Резец 035-2126-1177 ВК8 ОСТ 2И10-7-84
Сверло 035-2300-1225 Р6М5 ОСТ 2И20-1-80
Развертка 2363-0062 Р6М5 ГОСТ 1672-80
Фреза 2240-0374 Р6М5 ГОСТ 3755-78
Графическая технология
механической обработки
Рекомендуемые чертежи
- 24.01.2023