Разработка технологического процесса детали кронштейн




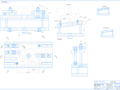
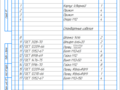
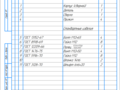
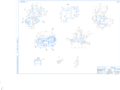
- Добавлен: 24.01.2023
- Размер: 1 MB
- Закачек: 0
Описание
Разработка технологического процесса детали кронштейн
Состав проекта
![]() |
![]() |
![]() ![]() ![]() ![]() |
![]() ![]() ![]() |
![]() ![]() ![]() |
![]() ![]() ![]() ![]() |
![]() ![]() ![]() ![]() |
![]() ![]() ![]() |
![]() ![]() ![]() |
![]() ![]() ![]() ![]() |
![]() ![]() ![]() ![]() |
![]() ![]() ![]() ![]() |
![]() ![]() ![]() ![]() |
![]() ![]() ![]() |
Дополнительная информация
Деталь.cdw

ЗАПИСКА.doc
Анализ технологичности детали.
Обоснования принятого в проекте метода изготовления заготовки. Проектирование заготовки технические требования к заготовке.
Разработка технологического процесса изготовления детали.
Проектирование приспособления.
Техника безопасности при механической обработке.
Список использованной литературы.
Машиностроение поставляет новую технику всем отраслям народного хозяйства определяет технический прогресс страны и оказывает решающее действие на создание материальной базы нового общества. Направление развития машиностроения предусматривают уменьшение сроков создания освоения и производства новой техники.
Если рассматривать современное состояние проектирования и изготовления машиностроительных изделий то можно отметить несколько направлений решения этой проблемы: развитие системы модульного проектирования на базе типизации унификации и стандартизации; широкое использование ЭВМ организация обмена опытом между различными отраслями машиностроения.
Творческая разработка и выполнение современных технических требований к технологической подготовке производства узлов и деталей машин сводится тщательному анализу служебного назначения и условий эксплуатации узла или детали на которые разрабатывается технологический процесс а так же себестоимость изготовления как основного показателя затрат общественного труда.
Если обобщить понятия детали то при разработке технологического процесса ее изготовления необходимо исходить из задачи обеспечения требуемой точности и взаимного расположения поверхностей детали и нельзя решать вопросы обработки отдельных поверхностей вне связи их с другими иначе разработанный технологический процесс приведет к изготовлению
детали не отвечающей своему служебному назначению в собранном узле и
приведет к бесполезным затратам труда.
В данном курсовом проекте разрабатывается технологический процесс изготовления детали «кронштейн».
В ходе выполнения курсового проекта используются знания полученные в результате изучения общетехнических и специальных дисциплин так же приобретаются навыки по разработке технологических процессов и заполнения технической документации пополняется опыт пользования справочной и нормативной литературой государственными и отраслевыми стандартами каталогами и другими материалами информационного характера.
Наименование детали - кронштейн. Кронштейн служит для крепления крыльев на самолете. Крылья крепятся к ним с помощью высокопрочных болтов диаметром 8мм с посадкой натяга р6.
Так как деталь находиться в крыле самолета и утяжеление нежелательно то деталь изготавливается из лёгкого алюминиевого сплава.
Алюминиевые сплавы отличаются малой плотностью хорошей коррозионной стойкостью сравнительно высокими электро и теплопроводностью. Из них можно отливать прогрессивным непрерывным методом круглые плоские и полые слитки практически любых необходимых размеров. Сплавы сравнительно легко поддаются горячей и холодной деформации прокатке ковке прессованию волочению гибки листовой штамповке.
Все алюминиевые сплавы можно сваривать точечной сваркой а специальные свариваемые — сваркой плавлением и другими видами сварки.
Алюминиевые сплавы легко обрабатываются резанием на них можно наносить защитные декоративные покрытия.
Литейный алюминиевый сплав АК6Т1 обладает хорошими литейными свойствами герметичный применяется для изготовления сложных штамповок. Технические условия на материал ГОСТ 21488-76 технические условия на штуку ОСТ 1.90073-85.
Химический состав сплава:
Т1-закаленные и искусственно состаренные.
Поковки из материала АК6Т1 предназначенные для изготовления ответственных и особо ответственных деталей должны поставляться на механическую обработку в термообработанном виде.
Технологичность детали - совокупность свойств и показателей определяющих возможность ее изготовления с наименьшими затратами при достижении требований и точности указанных в чертеже. Технологичность детали можно предварительно оценить сравнивая деталь с имеющимися аналогами. Окончательное решение о технологичности детали можно принять после разработки ТП и проведения технико-экономических расчетов.
Заготовка для данной детали «кронштейн» получена штамповкой.
Деталь имеет много фасонных поверхностей отверстий.
Деталь полностью обрабатывается на станке с ЧПУ за одну операцию что значительно повышает точность обработки т.к. не происходит смена баз.
Настроечной базой является два просверленных отверстия. Контактной базой является плоскость основания кронштейна. Упорной базой являются проушины кронштейна на которые устанавливаются прижимы.
Большой объем контрольных работ приводит к необходимости использования большой номенклатуры мерительного и специального инструмента.
Для изготовления деталей машин применяются заготовки пяти видов: заготовки из проката; поковки и штамповки; отливки; заготовки изготовленные комбинированным методом; заготовки из металлокерамики пластмасс и других неметаллических материалов. Выбор заготовки определяется рядом факторов: технологическими свойствами материала (литейных свойств штампуемости структурных изменений и т.д.); требуемой точностью выполнения заготовки и качеством ее поверхности; размерами детали и ее конструктивной формой; программой выпуска деталей; служебным назначением детали.
Заготовку из которой получают исходную деталь «кронштейн» рекомендуется изготовлять из штампованных поковок. Поскольку деталь работает в условиях значительного силового нагружения при знакопеременных или циклических нагрузках.
Поковки поставляются в термически обработанном состоянии. Они должны быть очищены от окалины травлением дробеструйным или иным методом. Допускаются местные дефекты в виде шлаковых включений закатов заковов а также трещин глубина которых не должна превышать половины номинального припуска на механическую обработку. Трещины должны быть удалены зачисткой.
Технические требования к заготовке:
Вид заготовки - поковка по ОСТ 1.90073-85
Группа контроля III.
Штамповочный уклон 5°
Неуказанные штамповочные радиусы 3мм.
Предельные отклонения размеров поковки по ОСТ1 41187-78
Класс точности отливки - 5.
Группа контроля качества термообработки поковки определяется в зависимости от ответственности детали и указывается в технических требованиях чертежа после технических условий на поковку. Для ТУ на поковку по ОСТ1 90073-85: группа контроля 3.
Составление технологического маршрута обработки.
Составление технологического маршрута обработки детали «кронштейн» начнем с того что в специальной части проекта мы внедряем станок с числовым программным управлением. Которое позволит нам за один установ обработать все необходимые нам поверхности. Тем самым мы добьемся высокой производительности и точности изготовления детали.
Разрабатываемую маршрутную карту включаем:
5 операция. Комбинированная ЧПУ.
0 операция. Контрольная.
Выбор технологических баз.
Технологические базы подразделяются на: контактные настроечные и проверочные. Выбор технологических баз и порядок их смены связан с точностью операционных размеров формой детали техническими требованиями на деталь видом станочного оборудования приспособления режущим и измерительным инструментами маршрутам обработки детали построением операции. Технологические базы определяют методы простановки и выполнения операционных размеров.
5 операция. В комбинированной ЧПУ настроечной базой является два просверленных отверстия. Контактной базой является основание кронштейна. Упорной базой являются проушины кронштейна на которые устанавливаются прижимы.
Правильный выбор для каждой операции и модели оборудования предполагает выполнение следующих условий:
-габариты и основные размеры станка должны соответствовать габаритным размерам детали;
-выбранная модель оборудования должна обеспечивать заданные требования по точности и качеству поверхности;
-мощность жесткость и кинематические возможности станка должны позволять вести обработку на оптимальных режимах резания;
-производительность станка должна соответствовать программе выпуска.
Основным принципом выбора станка является экономичность процесса обработки. Необходимо применять ту модель станка которая обеспечивает наименьшую трудоемкость и себестоимость обработки. Для выбора оборудования необходимо пользоваться паспортами станков каталогами или номенклатурными справочниками.
Для изготовления детали «кронштейн» выбираем следующее оборудование: многооперационный станок DMU 50V с вертикальным расположением шпинделя с системой ЧПУ HEIDENHAIN iTNC 426.
Применение станков с ЧПУ существенно уменьшает вспомогательное и основное время на обработку детали по сравнению с универсальными станками.
Техническая характеристика станка DMU 50V:
гидромеханический усилие зажима 12kH
асинхронный регулируемый цифровой интегрируемый шпиндель-двигатель
Диапазон чисел оборотов шпинделя: 1-8000 1мин
Крутящий момент: 130Hм
отдельные асинхронные регулируемые цифровые
Диапазон подач XYZ 1-10000 мммин
Быстрые хода XYZ 30 ммин
Усилие подачи XY 4000 Н
Направляющие: роликовые
Измерительные системы:
прямые фотоэлектрическое разрешение 0001мм
Максимальный диаметр инструмента 80-130мм
Количество инструмента 60 шт.
Максимальная длина инструмента 280 мм.
Максимальный вес инструмента 6 кг
Подвод воздуха 6 Бар
Напряжение 400В 50 Гц
Расход воздуха 7 куб мчас
Габариты 3000х3300х2400 мм
Расчет режимов резания.
Режимы резания для механической обработки определяются в следующей последовательности:
- Устанавливается глубина резания;
- Выбирается подача инструмента;
- Рассчитывается скорость резания;
- Проверяются режимы резания по мощности станка.
Расчёт режимов резания на развертывание. Операция 005.
Используемое оборудование: Станок c ЧПУ DMU 50V.
Инструмент: развертка диаметром 8мм.
При развертывании глубина резания:
При развертывании отверстий с точностью по 9-11му квалитетам подачу следует уменьшать на коэффициент=08. Принимаем подачу:
) Скорость резания. Скорость резания ммин при развертывании:
Значения коэффициента Cv и показателей степени периода стойкости Т:
Общий поправочный коэффициент на скорость резания учитывающий фактические условия резания
где - коэффициент учитывающий качество обрабатываемого материала;
- коэффициент учитывающий материал инструмента;
- коэффициент учитывающий глубину сверления.
) Сила резания. Осевая сила Н.
Значения коэффициента Ср и показателей степени. Коэффициент учитывающий фактические условия обработки в данном случае зависит только от материала обрабатываемой заготовки и определяется выражением .
для медных и алюминиевых сплавов:
) Крутящий момент на шпинделе .
Значения коэффициента См и показателей степени:
для медных и алюминиевых сплавов
) Частота вращения инструмента или заготовки обмин.
уточняем скорость резания
) Мощность резания (эффективная) кВт
Расчёт режимов резания на сверления. Операция 005.
Используемое оборудование: Станок с ЧПУ DMU-50V.
Инструмент: сверло диаметром 20мм.
При сверлении глубина резания:
При сверлении отверстий без ограничивающих факторов выбираем максимально допустимую по прочности сверла подачу. Принимаем подачу:
) Скорость резания. Скорость резания при сверлении ммин:
Значения коэффициента Cv и показателей степени периода стойкости Т.
) Сила резания. Осевая сила Н
Для медных и алюминиевых сплавов.
) Крутящий момент на шпинделе
Значения коэффициента См и показателей степени. Коэффициент учитывающий фактические условия обработки в данном случае зависит только от материала обрабатываемой заготовки и определяется выражением .
) Частота вращения инструмента или заготовки обмин
Расчёт режимов резания на фрезерование. Операция 005.
Используемое оборудование: Станок с ЧПУ DMU-50V.
Инструмент: фреза импортная ø25R3.
Фрезерование массива
) Глубина фрезерования t и ширина фрезерования B.
Во всех видах фрезерования за исключением торцевого t определяет продолжительность контакта зуба фрезы с заготовкой и измеряют в направлении перпендикулярном оси фрезы. Ширина фрезерования B определяет длину лезвия зуба фрезы участвующую в резании; B измеряют в направлении параллельном оси фрезы.
При фрезеровании различают подачу на один зуб sz подачу на один оборот фрезы s и подачу минутную sM мммин которые находятся в следующем соотношении:
где n - частота вращения фрезы обмин;
z - число зубьев фрезы.
Принимаем подачу sz = 008 ммзуб.
) Скорость резания - окружная скорость фрезы ммин:
- коэффициент учитывающий состояние поверхности заготовки;
- коэффициент учитывающий материал инструмента
) Сила резания главная составляющая силы резания при фрезеровании окружная сила Н:
где z — число зубьев фрезы участвующие в резании;
n — частота вращения фрезы обмин.
Значения коэффициента Ср и показателей степени поправочный коэффициент на качество обрабатываемого материала Кмр для медных и алюминиевых сплавов.
) Крутящий момент на шпинделе:
где D-диаметр фрезы мм.
Расчет припусков и операционных размеров.
Эскиз совмещенных переходов.
Первый шаг к выбору приспособления заключается в том что выясняют возможность обойтись без приспособления. Во многих случаях это удается. Однако форма и размеры детали требуемая точность обработки и нужная производительность могут требовать применения приспособления.
Технолог не разрабатывает конструкцию приспособления но он должен представить себе ее целесообразную схему ибо без этого нельзя правильно выбрать установочные базы. От него также требуется видеть возможные пути повышения производительности при помощи приспособления.
В первую очередь необходимо попытаться выбрать приспособления из имеющихся в цехе. Для станка с ЧПУ DMU 50V имеется фрезерно-расточное приспособление. Это приспособление состоит из: сварного корпуса на котором базируется заготовка; прижимов двух видов которые крепят заготовку; опор М12 которые удерживают прижимы от нежелательных поворотов.
Опоры зоны крепления число прижимов и их расположение должны выбираться тщательно. Правильный их выбор позволит:
Исключить смещение детали в процессе обработки от сил резания и от собственного веса;
Предупредить возникновение остаточных деформаций выходящих за пределы допускаемых;
Исключить по возможности переустановку прижимов в процессе выполнения операции;
Обеспечить перемещение инструментов с минимальной длиной холостых ходов.
Приспособление позволяет закрепить деталь с помощью усилия зажима соединения болт-гайка. Принцип действия приспособления заключается в следующем: установить деталь в приспособлении зафиксировав на пальцах. Рабочий прикладывает усилие с помощью ключа для завинчивания гайки и прижим зажимает деталь. Для смены прижимов и расфиксации детали рабочий прикладывает усилие для развинчивания гайки.
Для данного приспособления расчет усилия зажима выглядит следующим образом.
Расчет усилия зажима.
В нашем случае наихудшие условия резания возникают при сверлении отверстия ф20мм. При этом сила резания максимальная и заготовка зажата двумя прижимами. Сила резания Р стремится повернуть заготовку.
Чтобы не произошло сдвига заготовки необходимо выполнение условия .
М – момент возникающий от силы Р.
k - коэффициент запаса который вводят для обеспечения надежного закрепления заготовки;
k0 - коэффициент гарантированного запаса k0 = 15;
k1 - коэффициент который учитывает увеличение сил резания из-за случайных неровностей на обрабатываемых поверхностях k1 = 1 при чистовой обработке;
k2 - коэффициент который характеризует увеличение сил резания вследствие затупления режущего инструмента k2 = 16;
k3 - коэффициент который учитывает увеличение сил резания при прерывистом резании k3 = 1;
k4 - коэффициент который характеризует постоянство силы закрепления в зажимном механизме k4 = 12 если на силу закрепления влияют отклонения размеров заготовки;
k5 - коэффициент который характеризует эргономику ручных зажимных механизмов. При удобном расположении и малом угле поворота рукоятки k5=1;
k0 - коэффициент который учитывают только при наличии моментов стремящихся повернуть заготовку установленную плоской поверхностью на постоянные опоры. При установке заготовки на штыри К6 = 1;
- момент трения удерживающий заготовку от поворота.
f- коэффициент трения заготовки с зажимными и установочными элементами приспособления f=015;
Т.е. каждый прижим должен обеспечивать минимальное прижимное усилие равное W = 3267H.
Усилие Q создаваемое болтовым зажимом определяется из уравнения:
- кпд учитывающий потери на трение = 095;
- плечи = 35 мм. = 40 мм.;
Усилие создаваемое при зажиме гайкой вдоль оси болта определяется:
Определим по рассчитанному Q требуемую величину момента прикладываемого к гайке при зажиме заготовки:
dср - средний диаметр резьбы dср = 11.188 мм.
α - угол подъема резьбы;
φ - приведенный угол трения;
- приведенный коэффициент трения;
f - трение плоского контакта f = 01;
- половина угла профиля резьбы = 30º;
DT - наружный диаметр опорного торца гайки DT = 219мм;
d - внутренний диаметр опорного торца гайки d = 12мм;
- коэффициент трения на профиле гайки; = 0.12;
Для завинчивания гайки используем ключ с плечом l = 426мм. При этом усилие прикладываемое рабочим к ключу не должно превышать 24 Н.
Расчёт погрешности установки детали в фрезерно-расточное приспособление.
Базирование заготовки по двум цилиндрическим отверстиям
параллельными осями и плоскости перпендикулярные осям отверстий.
Эта схема базирование используется при обработке плит рам станин корпусных и других деталей. Она обеспечивает простую конструкцию приспособлений позволяет точно выдерживать принцип постоянства баз и дает возможность просто осуществлять передачу и фиксацию заготовок на автоматических линиях. Установочными элементами служат два пальца (жестких и выдвижных) и опорные планки. Плоскость и два отверстия заготовки всегда точные чистовые базы. Плоскость обрабатывается начисто на одной из первых операций отверстия как правило развертывают по 9-му квалитету. На плоскости располагаются три опорные точки на поверхности одного цилиндрического отверстия – две на поверхности другого цилиндрического отверстия – одна опорная точка.
Заготовка может базироваться на два цилиндрических пальца или один цилиндрический один ромбический палец. Сопряжение пальцев с отверстием осуществляется по посадке с гарантированным зазором.
В приспособление необходимо установить заготовку имеющую базовые отверстия и допуски на межцентровые расстояния
В первое отверстие устанавливаем палец с полем допуска g6 т.е. .
Зазор в сопряжении второго пальца и отверстия по сравнению с зазором в сопряжении первого пальца и отверстия увеличился на 0034 - 0005 = 0029мм. Это ведет к снижению точности установки. Значительно повысить точность удается если второй палец будет срезанным (ромбическим) а не цилиндрическим. При этом имеем следующее: в осевом направлении имеем зазоры и . Геометрические параметры таковы что . Поэтому положение заготовки в осевом направлении определяется цилиндрическим пальцем и отверстием. В то время когда зазор выбран цилиндрическим пальцем он не будет выбран ромбическим пальцем. Это позволяет увеличить допуск на Lo Lп что является положительным фактором. Установочные пальцы стандартизированы ромбические – по ГОСТ 12210-66. Ширина ленточки b зависит от диаметра цилиндрического пальца. Исходя из требуемой точности базирования можно было бы изготовить вместо ромбического пальца пластину шириной b но для придания ему большей жесткости задают ромб с размером B. При диаметре первого пальца размеры ромбического пальца будут b = 2 B = 7.
Определим диаметр второго пальца.
С учётом придельного отклонения . Минимальный зазор между ромбическим пальцем и отверстием в направлении перпендикулярном оси отверстий будет равен:
При наличие же цилиндрического пальца ранее было получено что
Таким образом использование ромбического пальца вместо цилиндрического значительно повышает точность базирования в направлении перпендикулярном оси отверстий.
В направлении оси отверстий получаем:
Ввиду наличия зазора существует возможность поворота заготовки относительно номинального положения. Максимальный угол поворота будет определяться из выражения:
Использование ромбического пальца положительно сказывается на базировании заготовки что позволяет увеличить допуск на Lo Lп.
Несчастные случаи в цехах механической обработки связаны с обслуживанием станков. Причины этого следующие:
Большее чем нужно количество оборотов рабочих шпинделей;
Внезапное отбрасывание обрабатываемого материала;
Очень частое применение ручной подачи;
Возникновение при обработке слишком большого количества стружек;
Отсутствие предохранительных приспособлений (ограждений).
Все работы должны производиться с максимальным применением соответствующей механизации и автоматизации и в соответствии с действующими стандартами нормами и правилами по охране труда к технике безопасности (приложение 1).
Оборудование инструмент и приспособления должны использоваться только но их прямому назначению находиться в доступном месте и быть в состоянии технической готовности.
Рабочее место должно быть удобным для проведения соответствующих операций. Отходы производства отработавшие продукты и т. п. должны своевременно удаляться с рабочего места.
Установка на рабочее место агрегатов деталей изделий массой более 20 кг должна быть механизирована.
После окончания работы (в перерывах) при ремонте и замене рабочих органов а также регулировочных работах (кроме специально оговоренных инструкцией завода-изготовителя) оборудование должно быть отключено от силовой сети.
Лица занятые на работах по ремонту автомобилей должны применять средства индивидуальной защиты (спецодежду спецобувь и др.) в соответствии с установленными нормами.
Андреев Г.Н. Новиков В.Ю. Проектирование технологической оснастки машиностроительного производства: Высш. Шк. 2001г.
Бурчаков Ш.А. Ухватов Н.Н. Технология машиностроения. Казань: Изд-во Казан. гос. ун-та 2003г.
Колесов И.М. Основы технологии машиностроения. 2001г.
Кузнецов Ю.И. Оснастка для станков с ЧПУ: справочник 1993г.
Ухватов Н.Н. Кувшинов П.И. Методические указания к изучению дисциплины «Проектирование станочных приспособлений». Казань: Изд-во Казан. гос. ун-та 2001г.
Справочник технолога-машиностроителя Под ред. А.Г.Косиловой Р.К.Мещерякова. – М.: Машиностроение 1985г. – Т. 1 Т. 2.
Станочные приспособления: Справочник Под ред. Б.Н.Вардашкина
А.А.Шатилова. – М.: Машиностроение 1984г. – Т. 1 Т. 2.
Обработка металлов резанием: Справочник технолога
А.А.Панов В.В.Аникин Н.Г.Бойм и др.; под общ. редакцией А.А.Панова
М.: Машиностроение 1988г.
Горошкин А.К. Приспособления для металлорежущих станков:
Справочник 7-е изд. перераб. и доп. М.: Машиностроение 1979г.
Барановский Ю.В. “Режимы резания” Справочник М. МС. 1972г.
moscow1.doc
Время прибытия в Казань
Время местное для каждого аэропорта
Чертеж опора.cdw

Чертеж заготовки.cdw

Штамповочный уклон 5
Неуказанные штамповочные радиусы 3мм.
Предельные отклонения размеров штамповки по ОСТ1 41187-78.
Разрешатеся изготавливать из поковки АК6Т1 ОСТ1 90073-85.
Маршрутная карта.doc
Код наименование операции
Обозначение документа
Код наименование оборудования
Многооперационный станок ЧПУ DMU 50V
Обеспечение безопасности технологических процессов добычи.doc
Потенциальная опасность технологических процессов добычи и транспортировки нефти обусловленная свойствами веществ обращающихся в производственном цикле требует реализации комплекса мер по обеспечению безаварийного функционирования среди которых одной из основных является применение автоматических систем пожарообнаружения контроля загазованности и пожаротушения. Программно-технические средства систем пожаробезопасности должны обладать высокой надежностью и эффективностью обеспечивать интеграцию этих систем в автоматизированные системы управления технологическими процессами и взаимосвязь с другими системами безопасности.
Оптический извещатель пламени ИПЭС-ИКУФ
Работа технологических объектов нефтяной и газовой промышленности предъявляет следующие требования к средствам обнаружения пожара которые связанны со спецификой работы указанных объектов: минимальное время (несколько секунд) обнаружение возгорания углеводородов большая контролируемая область высокая надежность работы при наличии нагретых и светящихся объектов в поле зрения несколько вариантов выходных сигналов (аналоговые цифровые дискретные) для возможности включения обнаружителей в различные системы АС пожаротушения и ВП наличие самотестирования для снижения затрат на эксплуатацию. Например в значительном по объему машинном зале современной автоматизированной нефтеперекачивающей станции нет постоянного присутствия персонала имеются сильно нагретые элементы технологического оборудования в случае загорания может иметь место как пламя с задымлением так и без него возможно очень быстрое распространение горения. В таких условиях датчики задымления и температурные датчики не обеспечивают с высокой надежностью срабатывание АС пожаротушения так как повышение температуры или задымленность в условиях больших объемов меняется медленно и слабо а в ряде ситуаций например при сильных сквозняках могут отсутствовать вовсе. Здесь для быстрого и надежного определения загорания требуются иные принципы чем анализ прозрачности атмосферы и изменение или достижение температурой определенного значения. Пожарные извещатели пламени (ИП) являются оптимальным видом сенсоров которые детектируют появление огня практически сразу после его возникновения. Это возможно потому что действие ИП основано на регистрации электромагнитного излучения. Известно что пламя горючих газов паров и жидкостей сопровождается электромагнитным излучением имеющим особенности в различных областях спектра и существенно отличающимся от спектров нагретых тел и солнечного света. Так как электромагнитное излучение распространяется с огромной скоростью то время срабатывания извещателей пламени определяется только временем необходимым на прием излучения выделение информативного сигнала и его обработку что занимает всего несколько секунд. Высокая чувствительность и низкий уровень шума современных фотоприемников в различных частях спектра: ультрафиолетовом (УФ) видимом ближнем и среднем инфракрасном (ИК) позволяет регистрировать и выделять излучение от пламени на большом расстоянии – 25 и более метров с большим углом обзора. Таким образом можно сделать заключение что для раннего обнаружения загораний на предприятиях нефтегазового комплекса целесообразно использовать в первую очередь извещатели пламени..
оптический многоспектральный
RS-4854-20мА «сухой контакт»
Непрерывный круглосуточный
Не менее 25м по ТП-5
Время срабатывания не более
До 5с ( с возможностью установки времени задержки от 0 до 5 с с шагом 1с)
Рабочий диапазон температур
От -600до+900 кратковременно до 1350с
ИПЭС изготавливаются следующих модификаций:
- ИПЭС-ИКУФ Состоит из оптических сенсоров УФ и ИК
- ИПЭС-ИК Состоит из двух оптических сенсоров ИК
- ИПЭС-УФ Состоит из оптического сенсора УФ излучения
Конструкция и характеристики делают ИПЭС уникальным и выгодно отличают его от приборов аналогичного назначения выпускаемых в нашей стране. Во-первых это достигается двухканальной оптической схемой построенной с учетом специфических свойств излучения пламени углеводородов. Во-вторых наличие различных вариантов выходных сигналов включая цифровой делают прибор встраиваемым практически в любую схему что особенно актуально в настоящее время при массовом использовании цифровой связи датчиков с системами различного уровня. В третьих жесткой надежной конструкцией корпуса извещателей имеющей взрывонепроницаемую оболочку 1ExdIICT4 по ГОСТ Р 51330.0. со степенью защиты IP66 по ГОСТ 14254-80 что обеспечивает надежную работу прибора в различных условиях. Конструкция ИПЭС обеспечивает также простоту эксплуатации прибора. Все датчики снабжены функцией автоматического контроля оптических цепей (оптической непрерывности). Нормальное функционирование детектора с помощью постоянного контроля чистоты оптики детектора чувствительности его датчиков состояния электронной схемы системы. Контроль оптической непрерывности осуществляется без использования внешнего источника УФ и ИК – излучения. При включении контрольных ламп проверки функции оптической непрерывности формируется откалиброванный контрольный луч который проходит сначала через смотровое окошко преломляется отражателем и направляется обратно. После этого электронная схема детектора анализирует возвращенный сигнал датчика и генерирует соответствующий выходной сигнал. Поскольку контрольный луч должен проходить через туже часть смотрового окошка что и излучение огня такая проверка способности детектора «видеть» пламя обеспечивает высокую степень надежности. Так наличие в ИПЭС встроенных источников излучения обеспечивающих сквозную проверку от приемников излучения до выходного сигнала и контроль степени запыленности окон исключают необходимость частой проверки функционирования извещателей при их эксплуатации при помощи открытого пламени или тестового источника излучения.
На рынке России предлагаются также различные извещатели пламени известных зарубежных фирм с одним или двумя УФ или ИК-каналами с УФ и ИК - каналами. Наиболее распространенные импортные приборы и ИПЭС имеют близкие основные технические характеристиками. Однако существенная разница в цене при одинаковых технических и ряде более гибких эксплуатационных характеристиках делают применение ИПЭС предпочтительным на отечественных предприятиях нефтяной и нефтехимической промышленности.
Безопасность оборудования и технологических процессов
Нормативным документом «ГОСТ 12.2.003-74 ССБТ. Оборудование производственное. Общие требования безопасности» установлено что безопасность обеспечивается:
· выбором более безопасного оборудования;
· применением в конструкции средств защиты механизации автоматизации и дистанционного управления;
· соблюдением эргономических требований.
Оборудование должно быть безопасным как при нормальных условиях так и при воздействии различных факторов окружающей среды (высоких и низких температур и влажности воздуха агрессивных веществ микроорганизмов грибков солнечной радиации и др.).
Используемое оборудование не должно загрязнять окружающую природную среду выше установленных норм быть пожаро- и взрывобезопасным.
Требования к производственному оборудованию обеспечивающие его безопасную эксплуатацию определены положением «ПОТ Р О-14000-002–98. Обеспечение безопасности производственного оборудования».
Безопасность производственных процессов определяется в соответствии с «ГОСТ 12.3.002-75 ССБТ. Процессы производственные. Общие требования безопасности» и обеспечивается:
· безопасностью производственного оборудования;
· выбором более безопасного технологического процесса;
· устранением непосредственного контакта работающих с исходными материалами заготовками полуфабрикатами готовой продукцией и отходами производства оказывающими вредное действие;
· выбором производственной площадки и производственных помещений;
· применением средств защиты работающих;
· профессиональным отбором инструктированием обучением и проверкой знаний по охране труда.
Безопасность должна обеспечиваться уже на стадиях составления технического задания при проектировании и разработке проекта.
Необходимо обеспечивать герметизацию оборудования применение дистанционного управления систем контроля и предупреждающей сигнализации при возникновении опасных ситуаций.
Производственные процессы должны быть пожаро- и взрывобезопасны не должны загрязнять окружающую природную среду.
При необходимости предъявляются дополнительные требования к персоналу: по возрасту; медицинскому осмотру; обучению и др.
Необходимо при производстве работ особенно повышенной опасности учитывать и требования «ГОСТ 12.2.012-89 ССБТ. Приспособления по обеспечению безопасного производства работ» определяющий требования к настилам ограждениям лестницам и др.
Копия Спецификация.cdw

ПРИСПОСОБЛЕНИЕ.cdw

Спецификация.cdw

Чертеж прижим.cdw

Технологический процесс.doc
Наименование операции
Оборудование устройство ЧПУ
Обозначение программы
Установить выверить закрепить
Поворот стола в позицию 1
поворотный стол прижимы
Фрезеровать поковку с 6ти сторон выдерживая размеры 123
фреза концевая 20 R5 Р6М5
Фрезеровать плоскость основания 1 выдерживая размер 4
фреза концевая 40 Р6М5
Сверлить отверстия 123456 на проход выдерживая размер 5678910
сверло спиральное 75 Р18
ГОСТ 3.1418-82 Форма 2а
Развернуть отверстия 123456 на проход выдерживая размер 5678910
Переустановить деталь
Поворот стола в позицию 2
импортная фреза 25 R3 Р6М5
Зенковать отверстия 12 выдерживая размер 11
спиральное сверло 22 Р6М5
Фрезеровать плоскость ушка 1 на зарезая контур основания
концевая фреза 40 Р6М5
Фрезеровать плоскость ушка 2 выдерживая размер 12
Фрезеровать плоскость ушка 3 не зарезая плоскость ребра
Фрезеровать плоскость ушка 4 выдерживая размер 13
Сверлить отверстие 7 на проход
сверло спиральное 20 Р6М5
Фрезеровать плоскость проушины 1 выдерживая размеры1415
концевая фреза 16 R5 Р6М5
Фрезеровать плоскость проушины 2 выдерживая размеры 1617
Фрезеровать плоскость проушины 3 выдерживая размеры 1819
Фрезеровать выборку 1 выдерживая размеры 202122
концевая фреза 20 R5 Р6М5
Фрезеровать выборку 2 выдерживая размеры 232425
Фрезеровать упоры 123 выдерживая размеры 2627
концевая фреза 20 R2 Р6М5
Дофрезеровать выборки 12 с R0.4
концевая фреза 20 R04 Р6М5
Фрезеровать поверхность 1 выдерживая размеры 2829
Фреза концевая 30 R5 Р6М5
Фрезеровать выборку 3 выдерживая размеры 3031
Дофрезеровать выборку 3 с R0.4
Поворот стола в позицию 3
Фрезеровать поверхность ушка 1 и толщину основания 1 выдерживая размеры 32
концевая фреза 16 R8 Р6М5
Фрезеровать поверхность 2 с R3
концевая фреза 8 R3 Р6М5
Фрезеровать контур ушка R25 выдерживая размер 3334
концевая фреза 20 R10 Р6М5
Фрезеровать контур ушка R20 выдерживая размер 3334
Фрезеровать скос ребра 1
Срезка технологического прилива
Сверлить отверстия 891011 на проход в ушках выдерживая размер 3536
сверло спиральное 22 Р6М5
Расточить отверстия 891011 на проход в ушках выдерживая размер 3536
сверло спиральное 24 Р6М5
Поворот стола в позицию 4
Поворотный стол прижимы
Окончательная срезка технологического прилива
Фрезеровать ребро 1 выдерживая размер в двух сторон 3738
Фрезеровать контур R50
концевая фреза 30 Р6М5
Сверлить отверстия 12 на проход в ушке выдерживая размер 39
сверло спиральное 17
Расточить отверстие 12 на проход в ушке выдерживая размер 39
сверло спиральное 19
Рекомендуемые чертежи
- 28.05.2016
- 18.10.2023
- 24.01.2023
- 13.12.2022
- 24.01.2023