Разработать технологию изготовления шевера дискового и оснастку




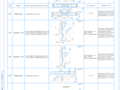
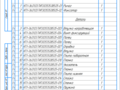
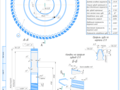
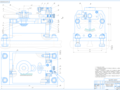
- Добавлен: 25.01.2023
- Размер: 5 MB
- Закачек: 0
Описание
Разработать технологию изготовления шевера дискового и оснастку
Состав проекта
![]() |
![]() ![]() ![]() |
![]() ![]() ![]() |
![]() ![]() ![]() ![]() |
![]() ![]() ![]() ![]() |
![]() ![]() ![]() ![]() |
![]() ![]() ![]() |
![]() ![]() ![]() ![]() |
![]() ![]() ![]() ![]() |
![]() ![]() ![]() |
![]() ![]() ![]() ![]() |
Дополнительная информация
курсач(исправление).doc
От качества надежности и работоспособности режущих инструментов применяемых в машиностроении в значительной степени зависит качество и точность детали ее шероховатость производительность и эффективность процесса обработки в особенности в наше время при использовании инструмента в автоматизированном производстве в условиях гибких производственных систем.
Значительно изменилась и технология изготовления самих режущих инструментов в связи с появлением новых технологических процессов а также конструктивными изменениями самих инструментов. Наиболее общими технологическими особенностями являются:
- широкое применение методов пластической деформации при получении заготовок инструментов (горячая экструзия продольно-винтовой прокат профильный прокат радиальная обжимка на машине с ЧПУ и др.);
- использование методов порошковой металлургии в том числе для получения биметаллического покрытия;
- использование абразивных инструментов из синтетических алмазов и нитрида бора позволяющее существенно снизить шероховатость режущих и присоединительных поверхностей и повысить их механические свойства;
- применение специальных высокоскоростных и высокопрочных абразивов в сочетании с эффективной высоконапорной системой обильного охлаждения и очистки охлаждающей жидкости создало возможность глубинного шлифования и вышлифовки стружечных канавок резьб и других элементов в цельных заготовках из твердых сплавов и инструментальных быстрорежущих сталей. Этот процесс по существу обеспечил возможность производства монолитного инструмента и коренным образом изменил технологию изготовления резьбообразующего инструмента;
- современное производство инструмента отличается широким использованием станков с ЧПУ и многокоординатных обрабатывающих центров что позволяет не только повысить производительность и точность но и осуществить целый ряд принципиально новых конструктивных решений.
НАЗНАЧЕНИЕ И КОНСТРУКЦИЯ ШЕВЕРА
Шевер применяется для окончательной обработки боковых поверхностей зубьев прямозубых и косозубых колес наружного внутреннего зацепления после предварительного их нарезания червячной фрезой или долбяком а также для чистовой обработки точных червячных колес. Дисковый шевер (см. рисунок 1б) представляет собой цилиндрическое колесо с винтовыми зубьями на боковых поверхностях которых прорезаны канавки и образованы режущие кромки.
Оси шевера и обрабатываемого зубчатого колеса являются скрещивающимися прямыми. При обработке шевер и колесо вводятся в беззазорное зацепление и образуют винтовую передачу. Шевер приводится во вращение и ведет обрабатываемое зубчатое колесо насаженное на оправку свободно установленную в центрах. Как известно винтовая пара характеризуется точечным контактом зубьев т. е мгновенным контактом между шевером и зубчатым колесом который будет происходить не по линии как при шевинговании рейкой а в одной точке. Точки контакта наблюдаемые в различные моменты времени образуют на поверхности зуба линию идущую на боковой поверхности от дна впадины до вершины зуба. Эта линия контакта и будет обработана шевером при неизменном взаимном расположении осей шевера и колеса. Поэтому чтобы обработать полностью боковую поверхность зубьев обрабатываемому колесу сообщают возвратно-поступательное движение вдоль своей оси. После каждого двойного хода колеса происходит радиальная подача т. е. оси шевера и колеса сближаются до тех пор пока толщина зубьев обрабатываемого колеса не будет равна требуемой (см рисунок 1а).
Рисунок 1 – Конструкция шевера дискового
Шевер при эксплуатации подвергается интенсивно изнашивается поэтому при изготовлении подвергается термической обработке. Целью термической обработки является получение заданных физико-механических свойств материала шевера под действием различных температур и скоростей охлаждения вследствие чего изменяется структура. Предварительная термическая обработка заготовок применяется для получения микроструктуры обеспечивающей оптимальную обрабатываемость при механической обработке. Шевер дисковый изготовляется из быстрорежущей инструментальной стали Р6М5 поэтому для улучшения обрабатываемости резанием подвергается отжигу при температуре 830°С. Для достижения необходимых механических свойств детали (прочность твердость вязкость) ее нужно подвергнуть окончательной термической обработки – это закалка при температуре 1230°С с охлаждением в масле и 3-х кратным отпуском при 550°С с охлаждением в воде потом на воздухе. При такой термической обработке достигаются необходимая твердость детали (63 66 HRC).
Химический состав и механические свойства материала детали стали Р6М5 ГОСТ 19265-73 сведены в таблицы 1 2 и 3. [1]
Таблица 1 – Химический состав %
Таблица 2 – Механические свойства (после отжига)
Таблица 3 – Механические свойства (после окончательной термообработки)
где 02 – предел текучести условный МПа;
В – временное сопротивление разрыву (предел прочности на растяжение) МПа;
5 – предел упругости МПа;
СЖ – предел прочности при сжатии МПа;
СЖ02 – предел текучести при сжатии МПа;
– относительное удлинение после разрыва %;
– относительное сужение %;
– относительная осадка при появлении первой трещины %;
к – предел прочности при кручении максимальное касательное напряжение МПа;
– относительный сдвиг %;
KCU – ударная вязкость определенная на образце с концентратором U Джсм2;
HB – твердость по Бринеллю;
HRC – твердость по Роквеллу шкала С.
АНАЛИЗ ТЕХНОЛОГИЧНОСТИ КОНСТРУКЦИИ ШЕВЕРА ДИСКОВОГО
Технологический анализ конструкции обеспечивает улучшение технико-экономических показателей разрабатываемого технологического процесса. Оценка технологичности конструкции может быть двух видов: качественной и количественной. Качественная оценка характеризует технологичность конструкции обобщенно на основании опыта исполнителя и допускается на всех стадиях проектирования как предварительная. Количественная оценка технологичности конструкции изделия выражается числовым показателем и рациональна в том случае если эти показатели существенно влияют на технологичность рассматриваемой конструкции.
1 Качественный анализ детали на технологичность
Шевер дисковый (рисунок 2) представляет собой косозубое цилиндрическое зубчатое колесо. Шевер имеет следующие конструктивные элементы: цилиндрические и конические поверхности (наружные и внутренние) шпоночный паз отверстия канавки зубья.
Шевер дисковый изготавливается из быстрорежущей стали Р6М5 ГОСТ 19265-73. В качестве легирующих элементов используются хром ванадий молибден и кобальт чтобы обеспечить высокую износостойкость теплостойкость хорошие режущие свойства прочность твердость. Данный материал широко применяется в машиностроении для изготовления режущих инструментов: сверл зенкеров разверток метчиков фрез напайных пластин для резцов и т.п.
Заготовка шевера изготавливается штамповкой и проходит термическую обработку (отжиг для снятия внутренних напряжений и повышение обрабатываемости резанием) что уменьшает внутренние напряжения увеличивает твердость прочность и износостойкость ответственных поверхностей а также имеет большое значение в отношении короблений возможных при нагревании и охлаждении детали. При штамповке контур заготовки приближен к контуру готовой детали что уменьшает припуски на обработку и снижает себестоимость изготовления детали.
Конструкция шевера позволяет обеспечить эффективное снятие припусков с большинства обрабатываемых поверхностей при токарной обработке за счет свободного подвода режущего инструмента и простоты обрабатываемых поверхностей. Деталь требует применения как универсального оборудования и станков с ЧПУ (для обработки цилиндрических и торцовых поверхностей) так и специального и специализированного оборудования (для обработки зубьев и канавок на поверхности зубьев). Имеется возможность надежного закрепления заготовки в приспособлениях на всех стадиях обработки т.к. имеются удобные технологические и конструкторские базы. Для контроля шевера применяется как универсальный мерительный инструмент (штангенциркуль нутромер микрометр) так и специальное измерительное оборудование (прибор для контроля параметров зубьев параметров биения поверхностей шевера).
Основная масса обрабатываемых поверхностей является наружными поверхностями что в свою очередь сказывается на технологичности обработки так как в процессе получения данных поверхностей облегчен доступ к ним режущего инструмента.
Такие конструктивные элементы шевера как зубья канавки на поверхности зубьев отверстия для выхода гребенки шпоночный паз снижают технологичность рассматриваемой детали.
Рабочий чертёж обрабатываемой детали содержит все необходимые сведения дающие полное представление о детали т.е. все проекции разрезы и сечения совершенно четко и однозначно объясняющие её конфигурацию и возможный способ получения заготовки. Все размеры на чертеже указаны с необходимыми отклонениями. Отметим правильную простановку размеров и шероховатости поверхностей: поверхности соответствующие более точным ответственным размерам имеют более низкие значения параметров шероховатости и наоборот.
Вывод: оценивая материал конструкцию предельные отклонения следует признать что данная деталь является не совсем технологичной. Но изменить конструкцию или какие-нибудь другие элементы невозможно так как конструкция шевера обусловлена его условиями работы – чистовая обработка зубчатых колес.
2 Количественный анализ детали на технологичность
При оценке детали на технологичность обязательными являются следующие дополнительные показатели:
Коэффициент унификации основных элементов детали:
где QУ.Э. = 5 – число унифицированных конструктивных элементов;
QЭ = 17 – число всех элементов.
Конструктивные элементы: фаски – 2 цилиндрические поверхности – 2 конические поверхности – 2 шпоночный паз – 1 зубья – 1 канавки на поверхности зубьев – 8 отверстия для выхода гребенки – 1. Неунифицированными элементами являются: шпоночный паз зубья канавки на поверхности зубьев поверхности 24017 и 635 т.к. не попадают в размерный ряд Ra40
Коэффициент применяемости стандартизованных обрабатываемых поверхностей
где DО.С.= 14 – число поверхностей детали обрабатываемых стандартным инструментом;
DМ.О.= 24 – число всех поверхностей детали подвергаемых механической обработке поверхностей.
К поверхностям обрабатываемым нестандартным инструментом относятся поверхности шпоночного паза зубьев канавок на поверхности зубьев. Данные поверхности требуют применения специального режущего инструмента для их обработки.
Коэффициент обработки поверхностей:
где DЭ = 24 – общее количество поверхностей детали.
Предельное значение квалитета ITmax14 и ITmin6.
Предельное значение параметров шероховатости обрабатываемых поверхностей Rаma
Вывод: таким образом проанализировав количественные показатели технологичности для данной детали следует сказать что к отрицательным показателям характеризующим деталь относятся: коэффициент унификации основных элементов (Ку.э.=029) и коэффициент применяемости стандартизированных обрабатываемых поверхностей. Минимальное значение квалитета обработки IT6 минимальное значение параметра шероховатости обрабатываемых поверхностей Ra025 мкм – деталь требует точной обработки. Коэффициент обработки поверхностей равен нулю что говорит о том что все поверхности детали подвергаются механической обработке.
Рисунок 2 – Эскиз шевера
ОПРЕДЕЛЕНИЕ ТИПА ПРОИЗВОДСТВА
В данном пункте курсового проекта я определю тип производства в котором работает предприятие. Это необходимо для того чтобы на основании типа производства предложить маршрут обработки данной детали – шевер а заодно произвести выбор и обоснование метода получения заготовки.
Исходные данные для расчета:
Годовая программа выпуска изделий N1=4000(по заданию);
Количество изделий в узле m = 1 шт;
Запасные части = 5%;
Режим работы предприятия – 2 смены.
Действительный годовой фонд времени работы оборудования FД = 4029 ч.
Для расчета составим таблицу в которую внесем данные по технологическому процессу а также результаты расчета.
Таблица 4 – Расчет типа производства
Наименование операции
Горизонтально-протяжная
Вертикально-сверлильная
Универсально-заточная
где Тшт(шт-к) – штучное (штучно-калькуляционное) время на операцию мин;
mР – количество станков шт;
Р – принятое число рабочих мест шт;
з.ф. – фактический коэффициент загрузки рабочего места;
О – количество операций выполняемых на рабочем месте шт.
Штучно-калькуляционное время на каждую операцию определим предварительно по формулам приведенным в [7] в приложении 1.
Тшт(шт-к) = φк·Tосн[7 c 147]
где Тосн – основное технологическое время мин; [7 c 146-147]
φк – коэффициент учитывающий вспомогательное и дополнительное время.[7 c 147]
5 операция (токарная с ЧПУ):
Тосн3=0.052(D2 – d2) =0.052(2402 – 632)=2788.8·10-3=2.79 мин;
Тосн4=0.052(D2 – d2) =0.052(1502 – 1102)=540.8·10-3=0.54 мин;
Тшт(шт-к) = 214·(0.34+0.28+2.79+0.54)=8.45 мин.
D-d – разность наибольшего и наименьшего диаметров обрабатываемого торца мм.
0 операция (токарная с ЧПУ):
Тосн2=0.052(D2 – d2) =0.052(2402 – 632)=2788.8·10-3=2.79 мин;
Тосн3=0.052(D2 – d2) =0.052(1502 – 1102)=540.8·10-3=0.54 мин;
Тшт(шт-к) = 214·(0.34+2.79+0.54)=7.85 мин.
0 операция (плоскошлифовальная):
Тшт(шт-к) = 21·(0.28+0.28)=118 мин.
5 операция (токарно-винторезная):
Тшт(шт-к) = 214·1.02=218 мин.
5 операция (горизонтально протяжная):
Тшт(шт-к) = 1.73·0.36=0.62 мин.
где lпр – длина протяжки мм.
5 операция (зубофрезерная):
Тосн=2.2Dзкbз=2.2·240·24.4=128832·10-3=1289 мин;
Тшт(шт-к) = 1.66·12.89 =21.40 мин.
где Dзк – диаметр зубчатого колеса мм;
0 операция (вертикально-сверлильная):
Тшт(шт-к) = 1.72·6.09 =10.45 мин.
где i – количество проходов.
5 операция (универсально-заточная):
Тшт(шт-к) = 2.1·3.9 =8.19 мин.
0 операция (зубошлифовальная):
Тосн=4.6zзbз=2.2·64·24.4=34355·10-3=344 мин;
Тшт(шт-к) = 1.66·3.44 =5.71 мин.
где zз – число зубьев зубчатого колеса.
5 операция (долбежная):
Тшт(шт-к) = 1.73·0.8 =1.38 мин.
где В – ширина обрабатываемой поверхности мм.
Тшт(шт-к) = 21·(0.28+0.28)=1.18 мин.
0 операция (внутришлифовальная):
Тшт(шт-к) = 21·2.38=5.00 мин.
5 операция (доводочная):
Тшт(шт-к) = 21·2.86=6.01 мин.
5 операция (зубошлифовальная):
5 операция (круглошлифовальная):
Тшт(шт-к) = 21·0.86=1.81 мин.
Количество станков определяется по формуле:
Значения mр для остальных операций сводим в таблицу 4.
Принятое число рабочих мест Р определяем округлением до ближайшего целого числа полученное значение mР. Результаты заносим в таблицу 4.
Фактический коэффициент загрузки рабочего места определяем по формуле:
Значения з.ф. для остальных операций сводим в таблицу 4.
Количества операций выполняемых на одном рабочем месте определяется по формуле:
Полученное значение округляется до большего целого числа.
Операция 025: принимаем О025 = 5.
Значения О для остальных операций сводим в таблицу 4.
Коэффициент закрепления операций:
Вывод: т.к коэффициент закрепления операций Кзо=1544 то тип производства среднесерийный. Он характеризуется небольшой номенклатурой выпускаемых изделий периодически повторяющимися средними партиями.
Количество деталей в партии для одновременного запуска:
где а – периодичность запуска в днях принимаем а = 6 дней;[7 c 23]
4 – количество рабочих дней в году.
Расчетное число смен на обработку всей партии деталей на основных рабочих местах:
где ТШТ-К ср – среднее штучно-калькуляционное время по основным операциям ТШТ-К ср = 928316 = 5.8 мин.
н.з. – нормативный коэффициент загрузки станков в серийном производстве н.з.=0.8[7 c 20]
6 – действительный фонд времени работы оборудования в смену мин.
принимаем сПР = 2 смены.
Определим число деталей в партии необходимых для загрузки оборудования на основных операциях в течение целого числа смен:
Вывод: в результате проведенных расчетов я определил что тип производства предприятия будет среднесерийным. Для обработки годовой программы деталей «Шевер» N=4200потребуется обработка партиями по n=131 деталей с периодичностью 6 дней. Партия будет обрабатываться за две смены.
ВЫБОР ЗАГОТОВКИ И МЕТОД ЕЕ ПОЛУЧЕНИЯ
В качестве заготовки для получения детали «Шевер» я предлагаю использовать поковку полученную методом горячей штамповки на ПШМ (пневматическом штамповочном молоте). При штамповке заготовка получает приближенный контур готовой детали. Это уменьшает время производственного цикла изготовления детали уменьшает затраты на дорогостоящий материал детали.
Расчет заготовки (поковки) получаемой штамповкой на ПШМ проводится по ГОСТ 7505-89 [6].
Исходные данные по операции:
Штамповочное оборудование – ПШМ.
Нагрев заготовки – индукционный
Исходные данные по детали:
Материал – сталь Р6М5 ГОСТ 19265-73
Масса детали – МД = 66 кг (рассчитана при помощи КОМПАС 3D)
Масса поковки расчетная – МР = 99 кг
Расчетный коэффициент КР = 15[6 таблица 20]
МР = МД · КР = 66·15 = 99 кг
Класс точности – Т4[6 таблица 19]
Группа стали – М3 (зависит от химсоства стали)[6 таблица 1]
Степень сложности – С1[6 с 30]
Размеры описывающей поковку фигуры (цилиндр):
Диаметр 24017·105 = 25218 мм
Высота 25·105 = 2625 мм
Масса описывающей фигуры (расчетная):
где D = 25218 мм – диаметр фигуры
Н = 2625 мм – высота фигуры
q = 0.00000785 кгмм3 – плотность материала.
Отношение массы поковки к массе фигуры:
следовательно степень сложности С1[6 с 30]
Конфигурация разъема штампа П (плоская)[6 таблица 1]
Исходный индекс – 14[6 таблица 2]
Припуски и кузнечные напуски:
Основные припуски на размеры мм:[6 таблица 3]
– толщина 25 и чистота поверхности Ra=04 мкм;
– диаметр 24017 и чистота поверхности Ra=125 мкм;
– диаметр 635 и чистота поверхности Ra=025 мкм;
Дополнительные припуски учитывающие:
смещение по поверхности разъема штампа – 03 мм;[6 таблица 4]
отклонение от плоскостности – 05 мм[6 таблица 5]
Штамповочные клоны:[6 таблица 18]
- на наружной поверхности – не более 7º принимаем 7º;
- на внутренних поверхностях – не более 10 º принимаем 10º.
Размеры поковки и их допускаемые отклонения:
толщина 25+(20+05)·2=30 принимаем 30 мм;
диаметр 24017+(27+03)·2=24617 принимаем 2465 мм;
диаметр 635-(22+03)·2=585 принимаем 585 мм;
Радиус закругления наружных углов – 25 мм (минимальный) принимаем 30 мм.[6 таблица 7]
Допускаемые отклонения мм:[6 таблица 8]
Неуказанные предельные отклонения размеров не указанных на чертеже поковки принимается равным 15 допуска соответствующего размера поковки с равными допускаемыми отклонениями.[6 с 16]
Неуказанные допуски на радиусы закруглений – 1 мм.[6 таблица 17]
Допускаемая величина остаточного облоя – 1 мм.[6 таблица 10]
Допускаемая отклонение от плоскостности – 08 мм.[6 таблица 13]
Допускаемое смещение по поверхности разъема штампа – 08 мм.
Допускаемая величина высоты заусенца – 5 мм.[6 с 21]
Допускаемое отклонение от концентричности пробитого отверстия относительно внешнего контура поковки – 15 мм. [6 таблица 12]
Выполняем чертеж заготовки (см. рисунок 3).
Рисунок 3 – Эскиз поковки шевера.
Масса заготовки (поковки) – МЗ = 108 кг.
Коэффициент использования материала –
Рассчитаем размеры заготовки для получения поковки.
Объем заготовки определим по формуле:
где V1 V2 V3 – объёмы поковки облоя и перемычки;
– потери металла на угар %.
Объем поковки V1=1377387.35 мм3
Потери на угар определяем в зависимости от метода нагрева заготовок: 03 10 % при нагреве в электронагревательных устройствах принимаем =07%
где k=05 – коэффициент заполнения металлом облойной канавки;
П – периметр поковки в плоскости разъема штампа;
Sк – площадь поперечного сечения облойной канавки штампа.
П=d2п=314·2465=77401 мм2
где d2п – наружный диаметр поковки d2п=2465 мм.
Определим высоту мостика облоя:
hк=0015d2п = 0015·246.5=37 мм[8 с 27]
Определяем номер канавки и площадь сечения Sк:
№ канавки – 4 площадь сечения Sк = 268 мм2. [8 с 28]
V2=0.5·77401·268=10371734 мм3
Исходя из объема заготовки определяем диаметр заготовки:
По ГОСТ 2590-88 принимаем диаметр заготовки D=90 мм.
Исходя из принятого диаметра определяем длину заготовки:
Определим размеры осаженной заготовки.
Диаметр заготовки после осадки находим по формуле:
Dоcd2п–10=246.5 - 10246 мм[8 с 29]
Высоту осаженной заготовки находим по формуле: [8 с 29]
Определим себестоимость полученной заготовки по методике изложенной в [7]. Цены на материал по состоянию на 1981 г. (в учебных целях).
Определим себестоимость изготовления заготовки для «Шевера» штамповкой на ПШМ.
kT – коэффициент зависящий от класса точности заготовки: kT = 1;
kС – коэффициент зависящий группы сложности заготовки: kС = 081;
kВ – коэффициент зависящий от массы заготовки: kВ = 08;
kМ – коэффициент зависящий от марки материала заготовки: kМ = 179;
kП – коэффициент зависящий от объема производства заготовки: kП = 1;
SОТХ – ценна 1 т. отходов: SОТХ = 27 руб.[7 с 32]
ВЫБОР ВАРИАНТА ТЕХНОЛОГИЧЕСКОГО МАРШРУТА И ЕГО ОБОСНОВАНИЕ
В данном пункте курсового проекта я проанализирую различные методики изготовления шевера и выберу наиболее оптимальную из всех (см. табл.5).
Для анализа и выбора метлики изготовления шевера я проанализирую методики изложенные в [3] [4] и [5]. Рассмотрим отдельные операции технологии изготовления шевера из этих источников.
На 025 операциях (см. табл. 5) можно применять следующее оборудование: токарно-винторезный токарно-револьверный станки и токарный станок с ЧПУ. Токарно-винторезный станок является самым дешевым из предложенных но процесс обработки на нем усложняется тем что обрабатываемая деталь (шевер) имеет ступенчатую форму а также высокие требования к точности что не в полной мере обеспечивает данный станок. Токарно-револьверный станок имеет большие возможности в сравнении с токарно-винторезным станком но станок имеет невысокую жесткость и мощность что необходимо для обработки инструментальной стали Р6М5 из которой изготовлен шевер. Всем требованиям по точности сложности обрабатываемых поверхностей твердости материала мощности резания удовлетворяет токарный станок с ЧПУ который я и принял в своей технологии (см. табл. 5).
На 055 операции можно использовать горизонтально-протяжной станок и вертикально-протяжной станок. Т.к. вертикально-протяжной станок имеет меньшую площадь в сравнении с горизонтально-протяжным станков то в своей технологии я принимаю вертикально-протяжной станок модели 7Б65.
Аналогичным образом анализируем и все остальные операции предложенных технологических процессов. Окончательный технологический процесс изготовления шевера приведен в таблице 5
Таблица 5 – Технологический процесс обработки шевера
Номер наименование и содержание операции
Оборудование приспособление инструмент
Отрезать заготовку выдерживая размер 1
Патрон самоцентрирующий;
Штамповать осаженную заготовку
Штангенциркуль радиусомер.
Точить поверхности выдерживая размеры 12358.
Точить поверхности выдерживая размеры 4 5 6.
Расточить отверстие выдерживая размеры 7 9
Резец; проходной подрезной расточной;
Продолжение таблицы 5
Точить поверхности выдерживая размеры 1 2368.
Точить поверхности выдерживая размеры 4567.
0 Плоскошлифовальная
Шлифовать торцы выдерживая размер 1
Шлифовать торцы выдерживая размер 2
5 Токарно-винторезная
Точить поверхность выдерживая размер 1
Оправка центра хомутик;
Штангенциркуль микрометр прибор для контроля биения.
5 Горизонтально-протяжная
Протянуть шпоночный паз выдерживая размеры 12
Зачистить заусенцы и снять фаски по шпоночной канавке
Фреза модульная червячная.
0 Вертикально-сверлильная
Сверлить 64 отверстия выдерживая размер 1
5 Универсально-заточная
Прорезать 64 перемычки выдерживая размер 1
Вулканитовый шлифовальный круг.
Предварительно шлифовать профиль зубьев
Долбить 8 канавок на боковых сторонах зубьев с двух сторон выдерживая размеры 12
Специальный долбежный станок;
Специальная гребенка;
Штангенциркуль калибр-пробка шаблон прибор для профиля зубьев.
Печь закалочная с баком
Прибор для размагничивания
0 Внутришлифовальная
Шлифовать отверстие выдерживая размер 1
Довести отверстие выдерживая размер 1
Микрометр калибр-пробка
Предварительно шлифовать профиль зубьев по эвольвенте с двух сторон
Шагомер эвальвентомер
5 Круглошлифовальная
Шлифовать по наружному диаметру выдерживая размер 1
Микрометр ролики зубомер
Микрометр ролики зубомер шагомер эвальвентомер нутромер.
ОПРЕДЕЛЕНИЕ ПРИПУСКОВ ДОПУСКОВ И РАЗМЕРЫ ЗАГОТОВКИ
В данном пункте курсового проекта я произведу расчет припусков на механическую обработку цилиндрических поверхностей 1 и 2детали (см. рисунок 4): 24017±0072(js9) с шероховатостью Ra125 мкм и 63.5+0.019 (H6) с шероховатостью Ra025 мкм.
Рисунок 4 – Фрагмент детали.
Поверхность 1 подвергается следующим видам механической обработки:
Обтачивание черновое – квалитет 13 = 072 мм Ra63 мкм;
Обтачивание чистовое – квалитет 11 = 029 мм Ra25мкм;
Термическая обработка (закалка и отпуск)
Шлифование черновое – квалитет 10 = 0185 мм Ra125мкм.
Шлифование чистовое – квалитет 9 = 0144 мм Ra125мкм.
Обтачивание черновое поверхности 1 производится в трехкулачковом самоцентрирующем патроне а чистовое точение и шлифование – при установке заготовке на оправку. Т.о. формула для расчета припуска будет иметь вид:
где Rz – средняя высота микронеровностей мкм;
Т – глубина дефектного поверхностного слоя мкм;
ρ – геометрическая сумма пространственных отклонений взаимосвязанных поверхностей мкм;
– погрешность установки на выполняемом переходе мкм.
Припуск на термообработку включает отклонение на коробление и кривизну ρкор=0.04·24017 =10 мкм [9 с 185]
Поверхность 2 подвергается следующим видам механической обработки:
Растачивание черновое – квалитет 12 = 03 мм Ra63 мкм;
Растачивание чистовое – квалитет 10 = 012 мм Ra25мкм;
Шлифование черновое – квалитет 8 = 0046 мм Ra125мкм;
Шлифование тонкое (доводка) – квалитет 6 = 0019 мм Ra025мкм.
Токарная обработка поверхности 2 производится при установке детали в самоцентрирующем трехкулачковом патроне шлифование предварительное – при установке на планшайбе а доводка – при установке на столе станка.
Припуск на термообработку включает отклонение на коробление и кривизну ρкор=0.04·63.5 =3 мкм [9 с 185]
Для расчета припуска составим таблицу 4 (для поверхности 1) и 5 (для поверхности 2).
Таблица 4 - Расчет припусков (поверхность 1).
Технологические переходы
Элементы припуска мкм
Расчетный припуск мкм
Таблица 5 – Расчет припусков (поверхность 2)
Необходимые значения элементов припуска для стадии «заготовка» берем из таблицы 4.3 [7 с 63] и заносим в таблицу 4 и 5. Для остальных технологических переходов элементы припуска берем из таблицы 4.5 [7 c 64-65].
Суммарное отклонение для стадии «заготовка» (для поверхностей 1 и 2) определяется по формуле:
где ρсм ρэкс – отклонение связанное со смещением одних участков поверхности относительно других в поперечном и продольном направлениях. В нашем случае он равно допустимому смещению по поверхности разъема штампа (п. 4) и равно ρэкс = ρсм = 08 мм.
Остаточное пространственное отклонение (поверхность 1): [7 c 73]
- после чернового точения: ;
- после чистового точения: .
- после шлифования чернового:
Остаточное пространственное отклонение (поверхность 2): [7 c 73]
- после чистового точения: ;
- после шлифования чернового: .
Погрешность установки определяется по формуле:
где б – погрешность базирования;
з – погрешность закрепления;
пр – погрешность положения заготовки в приспособлении пр = 0 т.к. имеет малое значение и ее включают в погрешность закрепления.
В результате формула примет вид:
Погрешность установки для поверхности 1:
б = 0 т.к. совпадают технологическая и установочная базы.
- шлифование черновое:
- шлифование чистовое:
Погрешность установки для поверхности 2:
- растачивание черновое:
- растачивание чистовое:
т.к. черновое и чистовое растачивание производятся за один установ то:
- шлифование тонкое (доводка):
Минимальный припуск для поверхности 1:
под точение черновое:
под точение чистовое:
под шлифование черновое:
под шлифование чистовое:
Минимальный припуск для поверхности 2:
под шлифование тонкое (доводку):
Расчетные размеры для поверхности 1:
Расчетные размеры для поверхности 2:
Наибольшие (наименьшие) предельные размеры вычисляем прибавлением (вычитанием) допуска к округленному наименьшему (наибольшему) размеру который равен расчетному размеру. Рассчитанные размеры заносим в таблицу 6 и 7.
Наибольшие предельные размеры для поверхности 1:
Наименьшие предельные размеры для поверхности 2:
Предельные значения припусков определяем как разность наибольших (наименьших) предельных размеров и - как разность наименьших (наибольших) предельных размеров предшествующего (выполняемого) и выполняемого (предшествующего) переходов. Рассчитанные значения заносим в таблицу 6 и 7.
Предельные значения припусков для поверхности 1:
Предельные значения припусков для поверхности 2:
Находим общий припуск суммированием промежуточных припусков. Рассчитанные значения внесем в таблицу 6 и 7.
Общий припуск для поверхности 1:
Общий припуск для поверхности 2:
Выполним проверку правильности произведенных расчетов:
Проверка для поверхности 1:
Проверка для поверхности 2:
84 – 0310 = 012 – 0046
13 – 0186 = 0046 – 0019
Таблица 6 - Предельные размеры и припуски (поверхность 1)
Технологический переход
Предельный размер мм
Предельные значения припусков мм
Таблица 7 - Предельные размеры и припуски (поверхность 2)
Шлифование тонкое (доводка)
Определим общий номинальный припуск:[7 c 62]
где НЗ – нижнее отклонение размера заготовки
НД – нижнее отклонение размера готовой детали
где ВЗ – верхнее отклонение размера заготовки
ВД – верхнее отклонение размера готовой детали
Номинальный размер заготовки для поверхности 1:
Номинальный размер заготовки для поверхности 2:
На остальные обрабатываемые поверхности детали припуски и допуски принимаем по ГОСТ 7505-89 (см. п. 4). Наносим припуски на деталь (см. рис. 5)
Рисунок 5 – Эскиз заготовки с назначенными припусками и допусками.
Строим схему графического расположения припусков и допусков на обработку поверхностей с размерами 240.17js9(±0.072) мм и 63.5H6(+0.019).
Рисунок 6 – Схема графического расположения припусков и допусков на обработку наружной поверхности шевера 240.17js9(±0.072)
Рисунок 7 – Схема графического расположения припусков и допусков на обработку отверстия шевера 63.5H6(+0.019)
ВЫБОР ОБОРУДОВАНИЯ И ОСНАСТКИ
В данном пункте курсового проекта я произведу выбор оборудования и оснастки по каждой операции механической обработки. Выбор оборудования зависит от размеров обрабатываемой заготовки и требований к обрабатываемой детали. Технологически процесс обработки шевера приведен в пункте 5 курсового проекта.
На 005 операции используется отрезной круглопильный автомат модели 8Б672. Данное оборудование позволяет отрезать круглые квадратные прямоугольные заготовки а также трубы различных профилей. Основные технические характеристики оборудования:
- диаметр и ширина пильного диска – 1010х6 мм
- наибольший диаметр обрабатываемой заготовки – 350 мм;
- наибольшая длина обрабатываемой заготовки – 25-1050 мм;
- мощность электродвигателя привода главного движения – 11 кВт;
- габаритные размеры (длинаширинавысота) – 310026502155 мм;
- масса станка – 7900 кг.
В качестве оснастки используется цанговый патрон с автоматической подачей заготовки.
На 025 и 030 операция используется токарный с ЧПУ станок модели 16М30Ф3. Данный станок предназначен для токарной обработки наружных и внутренних поверхностей деталей типа тел вращения со ступенчатым и криволинейным профилями в один или несколько проходов в замкнутом полуавтоматическом цикле а также для нарезания крепежных резьб обработки отверстий осевым инструментом. Основные технические характеристики:
- наибольший диаметр обрабатываемой заготовки: над станиной – 500 мм над суппортом – 320 мм;
- наибольшая длина обрабатываемой заготовки – 1500 мм;
- мощность привода главного движения – 30 кВт;
- габаритные размеры (длинаширинавысота) – 720036002130 мм;
- масса станка – 9000 кг.
В качестве оснастки на данных операциях используется патрон токарный самоцентрирующийся клиновой быстропереналаживаемый модели ПЗК-400Ф11.
На 040 и 100 операциях используется плоскошлифовальный станок модели 3П722. Данное оборудование предназначено для шлифования плоских поверхностей деталей периферией круга. Основные технические характеристики:
- наибольшие размеры обрабатываемой заготовки – 1600х320 мм;
- масса обрабатываемой заготовки – не более 1200 кг
- мощность электродвигателя главного движения – 15 кВт;
- габаритные размеры (длинаширинавысота) – 478021302360 мм;
- масса станка – 8900 кг.
В качестве оснастки используется магнитный стол самого станка с размерами 1600х320.
На 045 операции используется токарно-винторезный станок модели 16К25. Станок предназначен для выполнения разнообразных токарных работ: точение наружных цилиндрических конических и фасонных поверхностей растачивать цилиндрические и конические отверстия обрабатывать торцовые поверхности нарезать наружную и внутреннюю резьбы сверлить зенкеровать и развертывать отверстия производить отрезку подрезку и другие операции. Основные технические характеристики:
- наибольший диаметр обрабатываемой заготовки: над станиной – 500 мм над суппортом – 290 мм;
- наибольшая длина обрабатываемой заготовки – 710 мм;
- мощность электродвигателя главного движения – 11 кВт;
- габаритные размеры (длинаширинавысота) – 250512402500 мм;
- масса станка – 2925 кг.
В качестве оснастки применяется оправка (базирование по центральному отверстию) которая установлена в поводковом патроне с поджимом задним центром.
На 055 операции используется вертикально-протяжной станок модели 7Б65. Станок предназначен для точной обработки внутренних и наружных поверхностей различного профиля. Основные технические характеристики:
- наибольшая длина хода салазок – 1250 мм;
- размер рабочей поверхности плиты 450х450 мм;
- диаметр отверстия: в опорной плите под планшайбу – 160 мм в планшайбе – 125 мм;
- мощность электродвигателя главного движения – 22 кВт;
- габаритные размеры (длинаширинавысота) – 329213334540 мм;
- масса станка – 8080 кг.
В качестве оснастки используется адаптер самого станка куда устанавливаются обрабатываемые заготовки.
На 065 операции используется зубофрезерный станок модели 53А30П. Данный станок предназначен для нарезания зубьев цилиндрических и червячных колес методом обкатки. Основные технические характеристики:
- наибольший размеры обрабатываемой заготовки диаметр – 320 мм модуль – 6 мм длина зуба прямозубых колес – 220 мм;
- наибольший нарезаемый наклон зубьев – ±60°;
- мощность электродвигателя главного движения – 32 кВт;
- габаритные размеры (длинаширинавысота) – 230015001950 мм;
- масса станка – 6800 кг.
Обрабатываемые заготовки устанавливаются на оправку которая крепится в рабочей зоне станка за его присоединительные элементы.
На 070 операции используется вертикально-сверлильный станок модели 2Н135. Станок предназначен для сверления отверстий нарезания в них резьб метчиком растачивания и притирки отверстий вырезание дисков из листового материала и т.д. Основные технические характеристики:
- наибольший условный диаметр сверления в стали – 35 мм;
- рабочая поверхность стола – 450х500 мм;
- мощность электродвигателя главного движения – 4 кВт;
- габаритные размеры (длинаширинавысота) – 10308252535 мм;
- масса станка – 1200 кг.
Заготовка устанавливается и крепится в специальном поворотном кондукторе в котором также имеются втулки для направления сверла и устранения его увода при сверлении.
На 075 операции используется универсально-заточной станок модели 3М642. Данный станок позволяет прорезать перемычки оставшиеся от сверления отверстий на предыдущей операции шлифовальным кругом. Основные технические характеристики:
- наибольший размер обрабатываемой заготовки установленной в центрах: диаметр – 250 мм длина – 500 мм;
- размер рабочей поверхности стола – 140х800 мм;
- габаритные размеры (длинаширинавысота) – 165014701625 мм;
- масса станка – 1400 кг.
Заготовка устанавливается в специальном приспособлении которое позволяет прорезать перемычки вулканитовым шлифовальным кругом под углом.
На 080 используется зубошлифовальный станок модели 5В833. Данный станок предназначен для шлифования зубьев цилиндрических зубчатых колес методом обкатки. Основные технические характеристики:
- диаметр обрабатываемого зубчатого колеса – 40-320 мм;
- модуль обрабатываемого зубчатого колеса – 05-4 мм;
- наибольшая длина шлифуемого зуба прямозубого колеса – 150 мм;
- наибольший угол наклона шлифуемого зубчатого колеса – ±45°;
- шлифовальный круг – червячный;
- габаритные размеры (длинаширинавысота) – 240025002070 мм;
- масса станка – 7000 кг.
Обрабатываемая заготовка устанавливается на оправку и базируется в присоединительных элементах станка.
На 085 операции используется специальный долбежный станок. Данный станок предназначен для долбления канавок на поверхности зубьев шевера с помощью гребенки. Обрабатываемая заготовка (шевер) устанавливается в делительное устройство станка. Данный механизм совершает движения обкатки (гребенка по шеверу) что позволяет равномерно нарезать канавки на всей длине зуба шевера.
На 110 операции используется внутришлифовальный станок модели 3К227А. Станок применятся для шлифования отверстий в деталях которые можно закреплять в патроне и которым можно сообщать вращательное движение. Основные технические характеристики:
- наибольший диаметр: устанавливаемой заготовки – 400 мм устанавливаемой заготовки в кожухе – 250 мм;
- наибольшая длина: устанавливаемой заготовки при наибольшем диаметре отверстия – 125 мм шлифования – 125 мм;
- диаметр шлифуемых отверстий – 5-150 мм;
- габаритные размеры (длинаширинавысота) – 281519001750 мм;
- масса станка – 4300 кг.
Заготовка крепится на планшайбе станка с помощью прихватов.
На 115 операции используется доводочный станок модели 3К833. Станок предназначен для доводки отверстий в гильзах блоках шатунах двигателях внутреннего сгорания и других деталях. Основные технические характеристики:
- диаметр обрабатываемого отверстия – 30-125 мм;
- длина обрабатываемого отверстия – 20-400 мм;
- размер рабочей поверхности стола – 500х1000 мм;
- габаритные размеры (длинаширинавысота) – 129511452755 мм;
- масса станка – 1520 кг.
Заготовка устанавливается на столе станка и прижимается прихватами.
На 125 и 130 операциях используется зубошлифовальный станок модели 5891С. Станок предназначен для окончательной обработки эвольвентного профиля долбяков шеверов и измерительных колес. Основные технические характеристики:
- модуль обрабатываемого зубчатого колеса – 2-12 мм;
- наибольшая длина шлифуемого зуба прямозубого колеса – 56 мм;
- наибольший угол наклона шлифуемого зубчатого колеса – ±35°;
- шлифовальный круг – конический;
- габаритные размеры (длинаширинавысота) – 254517702190 мм;
- масса станка – 3500 кг.
Обрабатываемая заготовка устанавливается на переходную втулку и базируется в присоединительных элементах станка.
На 135 операции используется круглошлифовальный станок модели 3М161Е. Станок предназначен для наружного шлифования цилиндрических конических или торцовых поверхностей тел вращения. Основные технические характеристики:
- наибольший размер обрабатываемой заготовки: диаметр – 280 мм длина – 700 мм;
- мощность электродвигателя главного движения – 185 кВт;
- габаритные размеры (длинаширинавысота) – 348043452170 мм;
- масса станка – 8880 кг.
Обрабатываемая заготовка устанавливается на оправку которая базируется в поводковом патроне с поджимом задним центром.
ОПРЕДЕЛЕНИЕ РЕЖИМОВ РЕЗАНИЯ
В данном пункте курсового проекта я определю режимы резания на 025 операцию (токарная с ЧПУ станок 16М30Ф3) и на 135 операцию (круглошлифовальная станок 3М161Е) технологического процесса.
1 Определение режимов резания на 025 операцию
На 025 операции (токарная с ЧПУ) производится черновая (квалитет 12) обработка наружной цилиндрической поверхности черновая (12 квалитет) и чистовая (10 квалитет) торцовой поверхности черновая (12 квалитет) и чистовая (10 квалитет) обработка отверстия. Заготовка крепится в трехкулачковом самоцентрирующем патроне. Операционный эскиз на данную операцию показан на рисунке 8.
Рисунок 8 – Эскиз операционный на 025 операцию
Расчет режимов резания произведем по методике изложенной в [10].
- наименование – шевер (см. рисунок 2);
- материал – Р6М5 ГОСТ 19265-73 (226 269 НВ);
- точность обработки и параметр шероховатость см. на рисунке 8.
Исходные данные по заготовке:
- метод получения – штамповка IT16 (см рис 3);
- состояние поверхности – с коркой;
- масса заготовки – 108 кг;
- припуск на обработку поверхностей берутся из пункта 6 курсового проекта
Содержание операции:
А. Установить и закрепить заготовку.
Точить поверхность начерно и начисто выдерживая размеры 12358.
Точить поверхности начерно выдерживая размеры 56.
Расточить отверстие начерно и начисто выдерживая размеры 79.
Б. Открепить и снять деталь.
Выбор глубины резания:
Глубину резания берем из п. 6 курсового проекта и сводим в таблицу 8
Таблица 8 – Глубина резания
Глубина резания t мм
Выбор режущего инструмента и материала режущей части:
На станке 16М30Ф3 используются резцы с сечением державки 32х32 мм. Приложениям 15 [12] и исходя из условий обработки принимаем:
- для черновой и чистовой обработки поверхностей АБГ принимаем ромбическую пластину из твердого сплава СТ25;
- для черновой обработки поверхности В принимаем квадратную пластину из твердого сплава СТ25;
- для черновой и чистовой обработки поверхности Д принимаем ромбическую пластину из твердого сплава СТ25.
По приложению 7 [12] и исходя из условий обработки выбираем углы в плане: для обработки поверхностей АБГ – φ = 95° φ1 = 5°; для обработки поверхности В – φ = 45° φ1 = 45°; для обработки поверхности Д – φ = 75° φ1 = 15°.
Из приложения 8 [12] выбираем остальные геометрические параметры режущего инструмента:
Для черновой и чистовой стадий обработки поверхностей АБВГД:
- передний угол γ=10°;
- форма передней поверхности – плоская с фаской;
- ширина фаски главной режущей кромки – f = 06 мм;
- радиус скругления режущей кромки –ρ = 005 мм;
- радиус вершины резца – rв = 12 мм.
Нормативный период стойкости берем из каталога фирмы «Sandvik Coromant»: Тст=15 мин.
По каталогу фирмы «Sandvik Coromant» выбираем режущий инструмент и пластины согласно выше рассчитанным параметрам и заносим все в таблицу 9.
Таблица 9 – Выбор режущего инструмента
Подачу для черновой стадии обработки берем максимально допустимую по мощности оборудования жесткости системы СПИД прочности режущей пластины и прочности державки. Рекомендуемые значения для точения берем из таблицы 11 [10] а для чернового растачивания из таблицы 12 [10]. Подачи при чистовом точении выбирают в зависимости от требуемых параметров шероховатости обрабатываемой поверхности и радиуса при вершине резца по таблице 14 [10]. Значения подач сводим в таблицу 10.
Таблица 10 – Назначение подачи ммоб
Диапазон подач S0 ммоб
Выбор скорости резания:
При продольном поперечном точении и растачивании скорость резания определяется по эмпирической формуле:
где CV m x y – эмпирические параметры [10 с 269-270]
KV – поправочный коэффициент на скорость резания
Поправочный коэффициент KV учитывает влияние материала заготовки (KМV) состояние поверхности (KПV) материала инструмента (KИV).
где K1 – коэффициент характеризующий группу стали по обрабатываемости резанием K1=0.7[10 с 262]
n – показатель степени n=1[10 с 262]
В – предел прочности при растяжении В=850 МПа
- переход 1 черновая стадия:
- переход 1 чистовая стадия:
- переход 2 черновая стадия:
- переход 3 черновая стадия:
- переход 3 чистовая стадия:
Расчет частоты вращения
Частоту вращения определяем по формуле:
принимаем n=200 мин-1;
принимаем n=380 мин-1;
принимаем n=230 мин-1;
- переход 3 черновая стадия:
принимаем n=620 мин-1;
- переход 3 чистовая стадия:
принимаем n=880 мин-1;
Силы резания определяются по формуле:
где СP x y n – эмпирические параметры [10 с 273-274]
KP – поправочный коэффициент на силу резания. Данный коэффициент учитывает влияние различных факторов резания и определяется по формуле:
где KMP – поправочный коэффициент учитывающий влияние качества обрабатываемого материала. Определяется по формуле:
- поправочные коэффициенты учитывающие влияние геометрических параметров режущего инструмента[10 с 275]
KφP=0.89; KγP=1; KλP=1; KrP=1
KφP=1; KγP=1; KλP=1; KrP=1
Расчет мощности резания
Мощность резания определяется по формуле:
Окончательные значения показателей режимов резания сводим в таблицу 12.
Таблица 12 – Режимы резания.
Скорость резания Vт ммин
Мощность резания Nт кВт
2 Определение режимов резания на 135 операцию
На 135 операции производится круглое наружное шлифование шевера до диаметра 24017±0072 на длину 24 мм на круглошлифовальном станке модели 3М161Е. Расчет режимов резания будет произведен по методике изложенной в [10]. Операционный эскиз обработки показан на рисунке 9.
Шлифовальный круг выбираем по ГОСТ 2424-83. С учетом условий обработки (марка обрабатываемого материала вид обработки и т.п.) принимаем шлифовальный круг: 1450х32х203 24А 25 С1 8 К6 35мс А 1кл ГОСТ 2424-83
где 1 – тип круга (ПП – прямой профиль);
0х32х203 – размеры круга (наружный диаметр х ширина х внутренний диаметр);
А – абразивный материал (белый электрокорунд марки М24А);
С1 – степень твердости (средний);
– номер структуры (для шлифования вязких металлов с низким сопротивлением разрыву; внутреннее шлифование заточка инструментов плоское шлифование торцом круга);
К6 – марка керамической связки;
мс – рабочая скорость;
А – класс точности круга;
кл – первый класс неуравновешенности.
Припуск на шлифование составляет h=0.29 мм (см. пункт 6).
По таблице 55[10 с 301] принимаем режимы резания:
VК = 35 мс – скорость шлифовального круга;
VЗ = 40 ммин – скорость заготовки;
SР = (00025 0075) ммоб принимаем SР = 003 ммоб – радиальная подача круга.
Частота вращения заготовки:
Станок имеет бесступенчатое регулирование частоты вращения поэтому рассчитанное значение частоты вращения оставляем.
Эффективная мощность резания определяется по формуле:
где СN – коэффициент СN=014[10 с 303]
yrqz – показатели степени y=0.8 r=0.8 q=0.2 z=1.[10 с 303]
d – диаметр шлифования d=240.17 мм;
b – ширина шлифования b=24 мм.
Допустимая мощность по паспорту станка составляет NДОП=185 кВт что больше мощности резания NРЕЗ=1.6 кВт.
Рисунок 9 – Эскиз операционный на 135 операцию9 РАСЧЕТ ТЕХНИЧЕСКИХ НОРМ ВРЕМЕНИ
1 Расчет технических норм времени на 025 операцию.
Основное время на обработку определяется по формуле:
где L – длина рабочего хода инструмента мм. Она включает в себя длину врезания и перебега а также длину самого рабочего хода. Определяем ее из операционных эскизов.
L = 15+3+90+7=225 мм
- холостые ходу для перехода 1: ;
- холостые ходу для перехода 2: ;
- холостые ходу для перехода 3: .
Время на смену инструмента на одну позицию составляет Tсм=005 мин.
Окончательно получим время автоматической работы станка по программе:
Тц.а.=141+059+014+022+023+01+008+009+3·005=301 мин
Расчет норм времени заключается в определении штучно-калькуляционного времени ТШТ-К:
где ТШТ – штучное время на переход мин;
n = 131– количество деталей в партии;
ТП-З – подготовительно-заключительное время мин
где ТВ – вспомогательное время мин;
Ktв = 081– поправочный коэффициент[17 с 50]
аорг – время на организационное обслуживание рабочего места;
атех – время на техническое обслуживание рабочего места;
аотл – время на отдых и личные потребности.
аорг+ атех+ аотл=9% от оперативного времени[17 с 90]
где ТУ.С. = 023 мин – время на установку и снятие детали[17 с 52]
ТПЕР = 05 мин – время связанное с переходом мин.[17 с 79]
ТИЗ – время на измерение мин:[17 с 85]
ТИЗ = 03+023+018+026+026+018=141 мин.
Время на измерение не учитывается во вспомогательном времени т.к. перекрывается временем автоматической работы станка по программе.
ТП-З состоит из времени на наладку организационную подготовку (14 мин [17 с 96]) и времени на наладку станка приспособлений инструмента и программных устройств (149 мин [13 c 96-97]): ТП-З = 289 мин.
2 Расчет технических норм времени на 135 операцию.
Длина рабочего хода при врезном шлифовании состоит из срезаемого припуска и равна Lр.х. = 0.29 мм
Основное время на обработку:
Ktв = 1– поправочный коэффициент[16 с 31]
аобс = 9 % от оперативного времени – время на обслуживание рабочего места[16 с 130]
аотл = 7% от оперативного времени – время на отдых и личные потребности[16 с 203]
где ТУ.С. = 08 мин – время на установку и снятие детали[16 с 41]
ТПЕР =115 мин – время связанное с переходом;[16 с 129]
ТИЗМ = 022 мин – время на измерение.[16 с 187]
ТП-З состоит из времени на наладку станка инструмента и приспособлений (10 мин [16 с 130]) времени на дополнительные приемы (17 мин [16 c 130]) и времени на получение инструмента и приспособлений до начала и сдачи в конце работы (7 мин [16 с 131]): ТП-З = 34 мин.
ОПРЕДЕЛЕНИЕ ПОТРЕБНОГО КОЛИЧЕСТВА ОБОРУДОВАНИЯ И ЕГО ЗАГРУЗКИ
Расчет потребного количества оборудования был проведен в пункте 3 при определении типа производства. Также был рассчитан и коэффициент загрузки оборудования. Данные по расчету сведем в таблицу 13.
Таблица 13 – Количество оборудования и его загрузка.
Определим средний коэффициент загрузки оборудования з.ср.:
На основании данных таблицы 13 и среднего коэффициента загрузки оборудования з.ср. строим график загрузки оборудования (см. рисунок 10).
Рисунок 10 – График загрузки оборудования
ОПРЕДЕЛЕНИЕ ПОТРЕБНОГО КОЛИЧЕСТВА РАБОЧИХ
Проанализировав технологический процесс изготовления шевера изучив применяемые станки их расположение (по ходу технологического процесса) и количество можно объединить операции 025 030 (токарные с ЧПУ станок 16М30Ф3) и 125 130 (зубошлифовальные станок 5А893С) для многостаночного обслуживания. На этих парах операций используется одинаковое оборудования и в технологическом процессе они идут друг за другом а также время автоматической работы оборудования на операциях позволяет применить многостаночное обслуживание. Таким образом количество рабочих-станочников составит Чосн=14 чел.
Определим численность наладчиков необходимых для наладки всего оборудования применяемого в технологическом процессе:
где kсм – количество смен работы kсм = 2 смены;
Нoi – норма обслуживания по i-й профессии.[18 с 52]
kв – коэффициент учитывающий дополнительное время на обход рабочих мест kв = 12.[18 с 53]
Суммарное количество наладчиков составит:
ЧН=014·5+010·6+024·5=25 принимаем ЧН=3 чел.
ВЫБОР ОПИСАНИЕ КОНСТРУКЦИИ И РАСЧЕТ
ЭЛЕМЕНТОВ ПРИСПОСОБЛЕНИЯ
1 Описание конструкции и принцип действия приспособления
В качестве приспособления на 070 операции (вертикально-сверлильной) используется кондуктор для сверления отверстий у шевера. Конструкция приспособления представлена в графической части курсового проекта и на рисунке 11.
Рисунок 11 – Кондуктор для сверления отверстий у шевера.
В отверстие шевера вставляется втулка 8 которая отверстием надевается на оправку 7 и закрепляется болтом 18 с шайбой 17. Оправка установлена и закреплена гайкой 27 с шайбой 29 в окне плиты 9 вращающейся на пальцах 5 и 6 запрессованных в отверстия плиты. Один палец вращается в стойке 14 а второй в стенке 15. Стойка и стенка крепятся винтами к нижней плите 13. Плита 9 устанавливается под углом наклона зубьев шевера по шкале нанесенной на торце стенки 15 и указателю 11 закрепленному на пальце 6. Фиксация плиты в требуемом положении производится гайками 26. Сверление отверстий осуществляется через смещенную направляющую втулку 3 сидящую на планке 10 закрепленной на стенке 15 и планке 12 двумя винтами 22 и двумя штифтами 32. Установка шевера осуществляется с помощью пружинного фиксатора 2 и пружины 16 по впадине между зубьями шевера. Поворот шевера на окружной шаг зубьев производится вручную фиксатором с помощью рукоятки выводится из впадины зубьев рычагом 1. Оправка 7 с шевером устанавливается и закрепляется на плите 9 в зависимости от диаметра окружностей отверстий шевера. Риска на буртике оправки должна быть против градуировки соответствующего диаметра окружности отверстий шевера нанесенной на плите (от 100 до 250 мм).
2 Расчет режимов резания
Для определения усилия зажима и диаметра винта необходимо определить силу резания PZ и крутящий момент Мкр. Схема нагружения показана на рисунке 12.
В качестве режущего инструмента применяется сверло спиральное из быстрорежущей стали диаметром 75 мм. Глубина резания равна половине диаметра т.е. 375 мм. По таблице 25 [10 с 277] определяем табличное значение подачи S0т=007 ммоб. Поправочный коэффициент в зависимости от длины обрабатываемого отверстия KSl=0.9. Окончательное значение подачи: S0=0.07·0.9=0.06 ммоб.
Скорость резания определим по формуле:
где СV – коэффициент СV=3.5;[10 с 278]
myq – показатели степени m=0.12 y=0.45 q=0.5;[10 с 278]
KV – общий коэффициент на скорость резания;
D – диаметр сверления D=75 мм;
Т – стойкость сверла Т=8 мин.[10 c 279]
Общий коэффициент на скорость резания определяется по формуле:
где KMV – коэффициент на обрабатываемый материал;[10 с 261]
KИV – коэффициент на инструментальный материал KИV=03;
KlV – коэффициент учитывающий глубину сверления KlV=085.
где K1 – коэффициент характеризующий группу стали по обрабатываемости K1=0.6;[10 c262]
nV – показатель степени nV=09.[10 c262]
Определяем частоту вращения сверла и корректируем ее по паспорту станка:
По паспорту станка принимаем n=160 обмин
Фактическая скорость резания будет равна:
Крутящий момент определяем по формуле:
где СM – коэффициент СM=0041;[10 с 281]
yq – показатели степени y=0.7 q=2;[10 с 281]
KР – коэффициент учитывающий фактические условия обработки.
где n – показатель степени n=0.75[10 с 264]
Осевая сила определяется по формуле:
где СP – коэффициент СP=143;[10 с 281]
yq – показатели степени y=0.7 q=1;[10 с 281]
Определяем мощность резания:
3 Расчет усилий зажима
В данном пункте будет произведен расчет усилий зажима шевера при сверлении отверстий. Расчет режимов резания и необходимых усилий резания приведен выше. Схема нагружения представлена на рисунке 12.
Расчетная формула требуемой силы зажима определяется по формуле:
где K – коэффициент запаса;
f – коэффициент трения f=0.12;
d D – диаметры опоры (см. рисунок);
n – количество одновременно работающих инструментов n=1.
Рисунок 12 – Схема нагружения шевера при сверлении отверстий.
Коэффициент запаса определяется по формуле:
где K0 – гарантированный коэффициент запаса K0=1.5;[13 c 7]
K1 – коэффициент учитывающий состояние поверхности заготовки K1=1.0;[13 c 7]
K2 – коэффициент учитывающий увеличение сил резания от прогрессирующего затупления инструмента K2=1.0;[13 c 7]
K3 – коэффициент учитывающий увеличение силы резания при прерывистом резании K3 = 1.0;[13 c 7]
K4 – коэффициент учитывающий постоянство сил зажима развиваемой силовым приводом приспособления K4=1.3;[13 c 7]
K5 – коэффициент учитываемы только при наличии моментов стремящихся повернуть обрабатываемую деталь K5=1.[13 c 7]
Проверим требуемую силу зажима по силе зажима развиваемой винтом:
где Q – сила приложенная к гаечному ключу Q=300Н;
rср – средний радиус резьбы rср=75 мм;
α – угол подъема резьбы °.
φпр – приведенный угол трения °;
– коэффициент трения на плоском торце;
DН – наружный диаметр плоского торца DН=60 мм;
DВ – внутренний диаметр плоского торца DВ=40 мм.
Угол подъема резьбы определяется по формуле:
следовательно α=243°[13 c 18]
где S – шаг резьбы S=2 мм;
Приведенный угол трения определяется по формуле:
следовательно φпр = 789°[13 c 18]
где f – коэффициент трения при плоско контакте f=012;
– половина угла при вершине профиля резьбы =30°.
Как видно из расчета сила зажима развиваемая винтом (W=7964.6Н) больше требуемой силы зажима (W=16015Н). Следовательно принятый винт М16х2 подходит для данных условий работы.
ВЫБОР ОПИСАНИЕ И РАСЧЕТ РЕЖУЩИХ
ИНСТРУМЕНТОВ ВТОРОГО ПОРЯДКА
1 Выбор режущих инструментов второго порядка
В данном пункте курсового проекта я подберу режущий инструмент по каждой операции механической обработки шевера. Операционные эскизы и технологический процесс размещены в таблице 5.
На 005 операции (отрезная) используется отрезной станок модели 8Б672. На данной операции производится отрезка заготовки (прутка). В качестве режущего инструмента используется пильный диск станка диаметром 1010 мм.
На 025 операции (токарная с ЧПУ) используется токарный с ЧПУ станок 16М30Ф3. На данной операции производится обработка наружных торцовых и внутренних поверхностей шевера. В качестве режущего инструмента используются токарные резцы фирмы «Sandvik Coromant»:
- PCLNR 3232P19-X – токарный проходной упорный резец φ=95° φ1=5°.
- PSSNR 3232P19-X – токарный проходной резец φ=45° φ1=45°.
- S32U-PCLNR12-X - токарный расточной упорный φ=95° φ1=5°.
На 025 операции (токарная с ЧПУ) используется токарный с ЧПУ станок 16М30Ф3. На данной операции производится обработка наружных и торцовых поверхностей шевера. В качестве режущего инструмента используются токарные резцы фирмы «Sandvik Coromant»:
На 040 операции (плоскошлифовальная) используется плоскошлифовальный станок модели 3П722. На данной операции производится шлифование торцев шевера при базировании детали на магнитном столе станка. В качестве режущего инструмента используется шлифовальный круг типа 1 наружным диаметром 450 мм высотой 80 мм диаметром посадочного отверстия 203 мм из белого электрокорунда марки 25А зернистости 25 степени твердости С2 номером структуры 8 на керамической связи К6 с рабочей скоростью 35 мс класса точности А первого класса неуравновешенности – 1450х80х203 25А 25 С2 8 К6 35мс А 1кл ГОСТ2424-83.
На 045 операции (токарно-винторезная) используется токарно-винторезный станок модели 16К25. На данной операции производится обработка наружно поверхности шевера в пакете заготовок. В качестве режущего инструмента используется токарный проходной резец К.01.4979.000-02 ТУ 2-035-892-82 φ=45° φ1=45°.
На 055 операции (горизонтально-протяжная) используется горизонтально-протяжной станок модели 7Б55. На данной операции производится протягивание шпоночного паза в пакете заготовок. В качестве режущего инструмента используется шпоночная протяжка шириной 8 мм: Протяжка 2405-1061.I ГОСТ 18217-90.
На 065 операции (зубофрезерная) используется зубофрезерный станок модели 53А30П. На данной операции производится фрезерование зубьев шевера у пакета заготовок. В качестве режущего инструмента используется фреза модульная червячная м с модулем m=3.5 мм и класса точности АА: Фреза 2510-4083 АА ГОСТ 9324-80.
На 070 операции (вертикально-сверлильная) используется вертикально-сверлильный станок 2Н135. На данной операции производится сверление 64-х отверстий 75 у шевера для выхода гребенки. В качестве режущего инструмента используется сверло спиральное с коническим хвостовиком под конус Морзе: Сверло 035-2301-1007 ОСТ 2И20-2-80 2φ=118° =55°.
На 075 операции (универсально-заточная) используется станок универсально-прорезной модели 3М642. На данной операции производится прорезание 64-х перемычек во впадинах зубьев шевера. В качестве инструмента используется шлифовальный круг типа 1 наружным диаметром 200 мм высотой 8 мм диаметром посадочного отверстия 32 мм из белого электрокорунда марки 25А зернистости 25 степени твердости СМ1 номером структуры 8 на вулканитовой связи В5 с рабочей скоростью 35 мс класса точности А первого класса неуравновешенности – 1200х8х32 25А 25 СМ1 8 В5 35мс А 1кл ГОСТ2424-83.
На 080 операции (зубошлифовальная) используется зубошлифовальный станок модели 5В833. На данной операции производится предварительное шлифование профиля зубьев шевера. В качестве режущего инструмента используется шлифовальный круг типа 3 наружным диаметром 250 мм высотой 6 мм диаметром посадочного отверстия 76 мм из белого электрокорунда марки 25А зернистости 25 степени твердости М2 номером структуры 8 на керамической связи К6 с рабочей скоростью 35 мс класса точности А первого класса неуравновешенности – 3250х6х76 25А 25 М2 8 К6 35мс А 1кл ГОСТ 2424-83.
На 085 операции (долбежная) используется специальный долбежный станок. На данной операции производится долбление режущих канавок шириной 12 мм на поверхности зубьев шевера. В качестве режущего инструмента используется специальная гребенка для долбления канавок у шевера.
На 100 операции (плоскошлифовальная) используется плоскошлифовальный станок модели 3П722. На данной операции производится окончательное шлифование торцев шевера при базировании детали на магнитном столе станка. В качестве режущего инструмента используется шлифовальный круг типа 1 наружным диаметром 450 мм высотой 80 мм диаметром посадочного отверстия 203 мм из белого электрокорунда марки 25А зернистости 25 степени твердости С2 номером структуры 8 на керамической связи К6 с рабочей скоростью 35 мс класса точности А первого класса неуравновешенности – 1450х80х203 25А 25 С2 8 К6 35мс А 1кл ГОСТ 2424-83.
На 110 операции (внутришлифовальная) используется внутришлифовальный станок модели 3К227А. На данной операции производится шлифование посадочного отверстия у шевера. В качестве инструмента используется шлифовальный круг типа 1 наружным диаметром 50 мм высотой 16 мм диаметром посадочного отверстия 16 мм из белого электрокорунда марки 25А зернистости 25 степени твердости С2 номером структуры 8 на керамической связи К6 с рабочей скоростью 35 мс класса точности А первого класса неуравновешенности – 150х16х16 25А 25 С2 8 К6 35мс А 1кл ГОСТ 2424-83.
На 115 операции (доводочная) используется доводочный станок модели 3К833. На данной операции производится доводка посадочного отверстия. В качестве режущего инструмента используется чугунный притир и мелкозернистая абразивная паста или порошок.
На 125 операции (зубошлифовальная) используется зубошлифовальный станок модели 5А893С. На данной операции производится предварительное шлифование профиля зубьев шевера по эвольвенте с двух сторон. В качестве режущего инструмента используется шлифовальный круг типа 3 наружным диаметром 250 мм высотой 6 мм диаметром посадочного отверстия 76 мм из белого электрокорунда марки 25А зернистости 25 степени твердости М2 номером структуры 8 на керамической связи К6 с рабочей скоростью 35 мс класса точности А первого класса неуравновешенности – 3250х6х76 25А 25 М2 8 К6 35мс А 1кл ГОСТ 2424-83.
На 130 операции (зубошлифовальная) используется зубошлифовальный станок модели 5А893С. На данной операции производится окончательное шлифование профиля зубьев шевера по эвольвенте с двух сторон. В качестве режущего инструмента используется шлифовальный круг типа 3 наружным диаметром 250 мм высотой 6 мм диаметром посадочного отверстия 76 мм из белого электрокорунда марки 25А зернистости 25 степени твердости М2 номером структуры 8 на керамической связи К6 с рабочей скоростью 35 мс класса точности А первого класса неуравновешенности – 3250х6х76 25А 25 М2 8 К6 35мс А 1кл ГОСТ 2424-83.
На 135 операции (круглошлифовальная) используется круглошлифовальный станок 3М161Е. На данной операции производится шлифование шевера по наружному диаметру. В качестве режущего инструмента используется шлифовальный круг типа 1 наружным диаметром 450 мм высотой 32 мм диаметром посадочного отверстия 203 мм из белого электрокорунда марки 25А зернистости 25 степени твердости С2 номером структуры 8 на керамической связи К6 с рабочей скоростью 35 мс класса точности А первого класса неуравновешенности – 1 450х32х203 24А 25 С1 8 К6 35мс А 1кл ГОСТ 2424-83.
2 Расчет режущего инструмента второго порядка
Для расчета инструмента второго порядка я принимаю резец токарный проходной упорный используемый на 025 операции (токарная с ЧПУ) для обработки наружной цилиндрической и торцовой поверхности. Расчет будет произведен для наиболее нагруженных условий работу резца на данной операции. Расчет режимов резания был произведен в пункте 8.1 курсового проекта. В результате расчета осевая составляющая силы резани PZ=205 Н.
Также в пункте 8.1 были рассчитаны и геометрические параметры режущей части резца и выбрано сечение державки резца (32х32 мм):
Под данные параметры режущей части по каталогу фирмы «Sandvik Coromant» я подобрал пластину CNMG 190612-49 (рисунок 13а) из сплава СТ35:
где С – форма пластины (ромбическая с углом при вершине =80°);
N – параметр указывающий на величину заднего угла (α=0°);
М – класс точности пластины;
G – тип пластины (двухсторонняя пластина со стружколомающей канавкой и цилиндрическим центральным отверстием под крепление);
– ширина режущей кромки 19 мм;
– толщина пластины в 6 мм;
– радиус при вершине пластины 12 мм.
Выбираем метод крепления пластины винтом (рисунок 13б)
Рисунок 13 – Режущая пластина (а) и метод ее крепления (б)
Выбираем конструкцию державки резца сечением 32х32 (по паспорту станка 16М30Ф3) PCLNR 3232P19-X (рисунок) с углом в плане φ=95°. Высота державки резца 32 мм ширина – 32 мм. Длина резца в сборе – 170 мм ширина резца в сборе – 40 мм.
где Р – способ крепления пластины (см. рисунок 13б);
С – форма пластины (ромбическая с углом при вершине =80°);
L – тип резца по углу в плане (φ=95°);
N – задний угол (α=0°);
R – направление резания (правое);
32 – сечение державки 32х32 мм;
Р – длина резца 170 мм;
– длина режущей кромки пластины 19 мм.
Рисунок 14 – Резец проходной упорный
Выбираем материал резца: для корпуса – сталь 40Х по ГОСТ 4543-71 твердость 42 46 для пластины СТ35 фирмы «Sandv для винта – сталь 45 по ГОСТ 1050-88 твердость 32 37 для подложки – твердый сплав ВК6 оп ГОСТ 3882-74.
Технические требования на резец принимаем по ГОСТ 26611-85.
Произведем расчет резца на прочность.
Максимальная нагрузка допускаемая прочностью резца при известных размерах сечения корпуса резца:
ИД – предел прочности материала державки ИД=200 МПа
Максимальная нагрузка допускаемая жесткостью резца
Момент инерции прямоугольного сечения корпуса
Произведем проверку обладает ли резец достаточной прочностью и жесткостью. Для этого необходимо чтобы выполнялось условие
Условие выполняется значит наш резец обладает достаточными прочностью и жесткостью.
ВЫБОР ОПИСАНИЕ КОНСТРУКЦИИ ИЗМЕРИТЕЛЬНОГО ИНСТРУМЕНТА
Для контроля внутреннего диаметра 635+0019 мм используется нутромер 50-100 ГОСТ 9244-75 с ценой деления 0002 мм. Общий вид нутромера представлен на рисунке 15.
– отсчетное устройство; 2 – ручка; 3 – корпус; 4 – мостик.
Рисунок 15 – Нутромер
Нутромер – это измерительный инструмент который используется для точного определения внутренних линейных размеров деталей (пазов отверстий и т. д.) где замер рулеткой и линейкой не сможет дать точного результата. Измерения проводят как правило двумя наконечниками сферической формы которые расположены под углом 180 градусов друг к другу. У большей части нутромеров есть устройства для центрирования линии измерения в направлении контролируемого размера а также могут присутствовать и некие дополнительные механизмы которые передают передвижения от сферических наконечников на вычислительное устройство.
Данный нутромер по методу измерения относится к индикаторным и служит для измерения внутренних размеров деталей относительным методом. Нутромер состоит из устройства для измерения и индикаторной головки. Прибором для измерения выставляется расстояние в отверстии а индикатор отображает значение. Для совмещения линий измерения с диаметральной плоскостью нутромер снабжен центрирующим мостиком. Настройка нутромера на требуемый размер может производиться как по аттестованным кольцам так и по блокам концевых мер длины с боковинами. Нутромер с рычажной передачей он имеют предел измерений 50-100 мм. Цена деления шкалы нутромера - 0002 мм. Погрешность в измерении – 2 мкм по ГОСТ 9244-75. На инструменте расположены две шкалы. Большая шкала имеет цену деления 0002 мм и оборот стрелки 1 мм. Маленькая шкала показывает количество оборотов большой стрелки. Значение хода стержня головки - 10 мм. Размеры увеличиваются набором стержней.
При измерении детали регулируемый стержень нужной длины вставляется в нутромер. Нутромер в наклонном положении вводят в отверстие и устанавливают под углом 90 градусов легко покачивая инструмент. Затем отмечается степень отклонения стрелки. Отклонение стрелки влево означает что измеряемое отверстие больше настроенного размера если вправо - то меньше. Нутромер держат за деревянную ручку и не касаются штанги. От тепла руки металлическая часть станет длиннее а это приведет к ошибке в измерениях.
ОРГАНИЗАЦИЯ ИНСТРУМЕНТАЛЬНОГО ХОЗЯЙСТВА
Инструментообслуживание рабочего места в механических цехах серийного производства не требует больших постоянных наборов инструментария который имеется в единичном и мелкосерийном производстве. Система инструментообслуживания должна обеспечить подачу рабочему набора инструментария (или выдачу ему в ИРК) необходимого для обработки партии деталей. Если партия деталей обрабатывается в течение более чем одной смены то набор инструментария передается рабочему другой смены.
Замена изношенного и вышедшего из строя инструмента производится на рабочем месте по вызову рабочего (или самим рабочим в ИРК).
При данной системе инструментообслуживания в большинстве случаев отпадает необходимость оснащать рабочие места инструментальными тумбочками предназначенными для хранения довольно большого постоянного набора инструментария.
Рабочие места в серийном производстве следует оснащать приемными столиками с двумя или четырьмя инструментальными ящиками. Такого количества ящиков вполне достаточно для хранения инструмента предназначенного для обработки партии деталей а также для небольшого набора постоянно хранимых па рабочем месте средств по уходу за оборудованием (гаечных ключей универсального измерительного инструмента масленки и т. д.). Примеры инструментальных ящиков показаны на рисунке 16.
Рисунок 16 – Инструментальный ящик
Ящики столика (рисунок 16) используются для хранения инструмента а верхняя полка для размещения тары с деталями или для раскладки инструмента непосредственно необходимого в работе. Конструкция предусматривает установку двух или четырех инструментальных ящиков. При установке четырех ящиков два из них размещаются на подвеске с направляющими прикрепляемыми болтами и стойками. Ящики легко перемещаются и имеют ограничитель хода.
Для сокращения времени на наладку станка с ЧПУ настройку инструмента на размер осуществляют вне станка на приборе модели 2027. Данный прибор имеет базовые поверхности для крепления инструмента соответствующие аналогичным поверхностям на самом станке. Прибор мод. 2027 имеет индуктивные датчики линейного перемещения и устройство цифровой индикации Ф5291. Это позволяет с большой точностью и достаточно быстро настроить инструмент на размер. После настройки инструмента составляется карта наладки которая сопровождает настроенный инструмент вместе с остальной технологической документацией.
Весь режущий мерительный и вспомогательный инструмент хранится на инструментальном складе или в ИРК. Инструмент выдается мастеру участка механической обработки согласно техпроцессу и под роспись. Замена и сдача инструмента осуществляется так же мастером. Мастер в свою очередь передает инструмент рабочему и регистрирует этот момент.
Так же хранение и настройка режущего и вспомогательного инструмента осуществляется в инструментальном цеху. В этом же цеху осуществляется ремонт и сложная заточка режущего инструмента. Простой ремонт и заточка режущего инструмента осуществляется непосредственно в цеху на участке заточки. Инструмент из инструментального цеха поставляется в нужный цех по запросу.
ОРГАНИЗАЦИЯ РАБОЧЕГО МЕСТА СТАНОЧНИКА
При рациональной организации рабочее место в условиях серийного производства должно быть оснащено в соответствии с требованиями производственного процесса и условиями выполнения работы с соблюдением правил санитарной гигиены и техники безопасности.
Основными факторами влияющими на организацию рабочего места являются степень детализации технологического процесса и организация производства. Они определяют операции на рабочем месте систему обеспечения заданием технической и другой рабочей документацией систему обеспечения рабочего места материалами и заготовками порядок передачи готовых деталей после данной операции на следующее рабочее место систему сигнализации и связи.
Расположение оборудования на рабочем месте инвентаря производственной мебели тары стеллажей для заготовок и готовой продукции планируется с таким расчетом чтобы не создавалось стесненных условий работы лишних затрат времени на хождение и поиски.
Освещение рабочего места должно быть достаточным и правильным. Требуемая освещенность определяется в зависимости от характера и точности работы размеров объекта различения контраста рассматриваемого объекта с фоном и действующими санитарными нормами. При естественном и искусственном освещении рекомендуется так размещать рабочие места чтобы свет падал слева или спереди. При наличии местного освещения свет не должен слепить глаза тень не должна падать на обрабатываемую деталь.
Внешнее оформление рабочих мест и производственных помещений должно соответствовать требованиям технической эстетики.
Количество инструмента и приспособлений на рабочем месте должно быть минимально необходимым обеспечивающим бесперебойную работу в течение смены с наименьшими затратами времени на получение и замену их. В набор инструмента который постоянно хранится на рабочем месте должен включаться только нормализованный инструмент. Специальный инструмент хранится только во время пользования им. При определении набора инструмента предназначенного для постоянного храпения следует устанавливать не только минимально необходимое его количество но и максимально допустимое. Инструменты и приспособления должны располагаться на рабочем месте в определенном удобном для пользования порядке чтобы быстро без дополнительных потерь времени найти их взять установить и затем уложить после окончания работ.
Количество обрабатываемых деталей заготовок на рабочем месте определяется системой организации производства и должно обеспечивать непрерывную работу в течение смены. Не допускается загромождение рабочего места сверхнормативными запасами деталей заготовок.
Все обрабатываемые детали заготовки должны храниться на рабочем месте в таре.
Оснащение рабочих мест станочников оргоснасткой должно проводиться на основе типовых конструкций. Специальная оргоснастка проектируется в исключительных случаях если по тем или иным причинам не подходит типовая. Пример инструментального столика показан на рисунке 16 пример приемного столика – на рисунке 17.
Рисунок 17 – Столик приемный
На верхней полке столика (рисунок) размещается тара с обрабатываемыми деталями или сами обрабатываемые детали. При необходимости на нижней полке могут храниться приспособления и принадлежности. На отдельных рабочих местах столик может использоваться для раскладки на нем непосредственно в работе инструмента.
Ниже будут приведены примеры планировки отдельных рабочих мест станочников.
– столик приемный; 2 – столик приемный с инструментальными ящиками; 3 – решетка для ног
Рисунок 18 – Пример планировки рабочего места токаря (а) сверловщика (б) и шлифовщика
Рабочее место токаря сверловщика и шлифовщика оснащается двумя приемными столиками. Один из них имеет четыре инструментальных ящика. Тара с обрабатываемыми и готовыми деталями размещается на верхних полках приемных столиков а на нижних полках могут храниться принадлежности и приспособления.
– столик приемный с инструментальными ящиками; 2 – приемный столик; 3 – столик приемный к зубообрабатывающим станкам; 4 – решетка для ног
Рисунок 19 – Пример планировки рабочего места зубофрезеровщика
Рабочее место зубофрезеровщика обслуживающего три зубофрезерных станка оснащаются двумя приемными стоиками (один из них с инструментальными ящиками) и тремя столиками для установки тары с готовыми деталями. Особенностью этих столиков является отверстие в верхней полке для слива масла которое стекает с обработанных деталей. Показанная на планировке расстановка трех фрезерных станков обеспечивает их лучшее обслуживание. Рабочий находится между станками и его путь от одного станка к другому наименьший.
– станок 16М30Ф3; 3 – столик приемный с инструментальными ящиками; 4 – стол; 5 – решетка под ногами рабочего
Рисунок 20 – Пример планировки рабочего места оператора
титульник.doc
Белорусский Национальный технический университет
Кафедра «Металлорежущие станки и инструмент»
ПОЯСНИТЕЛЬНАЯ ЗАПИСКА
по дисциплине «Технология инструментального производства»
на тему «Разработать технологию и оснастку для изготовления шевера дискового»
Специальность1 – 36 01 03 «Технологическое оборудование машинострои-тельного производства»
Специализация 1 – 36 01 03 02 «Инструментальное производство»
тех процесс(шевер).cdw

мерительный инструмент
Станок отрезной круглопильный
выдерживая размеры 1 и 2.
Штамповать осаженную заготовку
Паровой штамповочный молот
Отжечь штампованную заготовку при t=830
Контролировать размеры 1-10
выдерживая размеры 1
выдерживая размеры 4
выдерживая размеры 7
Станок токарный с ЧПУ
Патрон самоцентрирующий
Угломер типа 4-10 ГОСТ 5378-65;
Набор радиусомеров ГОСТ 4126-82 №1
Набор радиусомеров ГОСТ 4126-82 №2
Резец токарный проходной упорный
PCLNR 3232P19-X Sandv
Резец токарный проходной
PSSNR 3232P19-X "Sandv
Резец токарный расточной
S32U-PCLNR12-X "Sandv
PCLNR 3232P19-X "Sandv
Контролировать размеры 1-7
Нутромер 50-100 ГОСТ 9244-75
Образец шероховатости 2
Станок плоскошлифовальный
Шлифовальный круг 1450х80х203 25А
С2 8 К635мс А 1кл ГОСТ2424-83
Микрометр МК50-1 ГОСТ 6507-90
Станок токарно-винторезный
К.01.4979.000-02 ТУ 2-035-892-82;
Контролировать размеры 1
Микрометр МК50-1 ГОСТ 6507-9
Образец шероховатости 1
Протянуть шпоночный паз
Станок горизонтально-
протяжной модели 7Б55;
Протяжка 2405-1061.I ГОСТ 18217-90;
Вертикально-сверлильная
Универсально-заточная
Зачистить заусенцы и снять фаски по
выдерживая размер 1
m=3.5 мм и делительный диаметр 227
Сверлить 64 отверстия
Прорезать 64 перемычки
Предварительно шлифовать профиль зубьев
модуль m=3.5 мм и делитель-
Долбить 8 канавок на боковых сторонах зубьев
Станок зубофрезерный
Станок вертикально-сверлильный
Станок универсально-заточной
Приспособление специальное
Станок зубошлифовальный
Станок для долбления канавок
Фреза шлицевая модульная
10-4083 АА ГОСТ9324-80
Угломер типа 4-10 ГОСТ 5278-65;
Шаблон для контроля профиля зубьев.
Сверло 035-2301-1007 ОСТ 2И20-2-80;
Вулканитовый шлифовальный круг
00х8х32 25А 25 СМ1 8 В5
мс А 1кл ГОСТ2424-83;
Шлифовальный круг 3 250х6х76 25А
М2 8 К6 35мс А 1кл ГОСТ 2424-83;
Шаблон для контроля профиля зубьев
Гребенка специальная;
Шаблон для контроля канавок.
Контролировать размеры 1-8
Прибор для контроля профиля зубьев
Калибр-пробка; шаблон;
Образец шероховатости 3
Закалка-подогрев предварительный 870
нагрев окончательный 1220
охлаждение на воздухе до 900
далее в масле до 300-400
окончательное охлаждение на воздухе.
Отпуск-трех кратный при 540-560
электрическая камерная печь
хлор-бариевая печь-ванна
выдерживая размер 1 и модуль m=3.5 мм
Шлифовать по наружному диаметру
Прибор для размагничивания
Станок внутришлифовальный
Станок доводочный модели 3К833;
Станок круглошлифовальный
Шлифовальный круг 1 50х16х16 25А 25
С2 8 К6 35мс А 1кл ГОСТ 2424-83.
Притир чугунный; мелкозернистая
Нутромер 50-100 ГОСТ 9244-75;
Микрометр МК50-1 ГОСТ 6507-90;
Образец шероховатости 0
Шлифовальный круг 1 450х32х203
А 25 С1 8 К6 35мс А 1кл ГОСТ 2424-83;
Микрометр МК250-1 ГОСТ 6507-90
Микрометр МК250-1 ГОСТ 6507-90;
Прибор для контроля биения;
КП.1-36.01.03.ТИП.303535.085.03
Технологический процесс
Маршрутно-операционный технологический процесс изготовления шевера
* Размер для справок
кондуктор_сп.spw

КП.1-36.01.03.ТИП.303535.085.05-01
КП.1-36.01.03.ТИП.303535.085.05-02
КП.1-36.01.03.ТИП.303535.085.05-003
КП.1-36.01.03.ТИП.303535.085.05-004
КП.1-36.01.03.ТИП.303535.085.05-005
КП.1-36.01.03.ТИП.303535.085.05-006
КП.1-36.01.03.ТИП.303535.085.05-007
КП.1-36.01.03.ТИП.303535.085.05-008
КП.1-36.01.03.ТИП.303535.085.05-009
КП.1-36.01.03.ТИП.303535.085.05-010
КП.1-36.01.03.ТИП.303535.085.05-011
КП.1-36.01.03.ТИП.303535.085.05-012
КП.1-36.01.03.ТИП.303535.085.05-013
КП.1-36.01.03.ТИП.303535.085.05-014
КП.1-36.01.03.ТИП.303535.085.05-015
КП.1-36.01.03.ТИП.303535.085.05-016
КП.1-36.01.03.ТИП.303535.085.05-017
Болт М16х30 ГОСТ 7805-70
Винт М4х14 ГОСТ 1491-80
Винт М5х8 ГОСТ Р 50385-92
Винт М6х12 ГОСТ 1491-80
Винт М8х25 ГОСТ 11738-84
Винт М10х25 ГОСТ 11738-84
Винт М16х40 ГОСТ 11738-84
Винт М16х50 ГОСТ 11738-84
Гайка М16 ГОСТ 15526-70
Гайка 2 М30х1.5 ГОСТ 11871-88
Шайба 16 ГОСТ 9065-75
Шайба 30 ГОСТ 9065-75
Шпилька М16х48 ГОСТ 22032-76
Штифт 2х10 ГОСТ 3128-70
Штифт 6х30 ГОСТ 3128-70
Штифт 8х30 ГОСТ 3128-70
Штифт 10х36 ГОСТ 3128-70
кондуктор.cdw

КП.1-36.01.03.ТИП.303535.085.05
* Размеры для справок.
** Установочные размеры для сверления отверстий у шевера
КП.136.01.03.ТИП.303535.085.01
Оправку 7 установить на размер 220. В отверстие шевера
которая отверстием надевается на оправку 7.
Поворотную плиту 9 повернуть на угол 10
гайками . Зафиксировать положение шевера с помощью фиксатора 2
и закрепить болтом с шайбой .
Кондуктор установить на стол станка Т-образными болтами 19
в пазах плиты стола станка
ЛИТЕРАТУРА.doc
Марочник сталей и сплавов В.Г. Сорокин А.В. Волосникова С.А. Вяткин и др.; Под общ. ред. В.Г. Сорокина. – М.: Машиностроение 1989. – 640 с.
Проектирование технологических процессов механической обработки в машиностроении: Учеб. Пособие В.В. Бабук В.А. Шкред Г.П. Кривко А.И. Медведев; Под ред. В.В. Бабука. – Мн.: Выш. шк. 1987. – 255 с.: ил.
Барсов А.И. Технология инструментального производства. Учебник для машиностроительных техникумов. Изд. 4 исправленное и дополненное. М.: Машиностроение 1975. – 272 с.: ил.
Палей М.М. Технология производства режущего инструмента. Учебное пособие для машиностроительных и факультетов. М.: Машгиз 1963. – 483 с.: ил.
Технология изготовления зуборезного инструмента П.Р. Родин В.И. Климов С.Б. Якубсон. – К.: Технiка 1982. – 208 с.: ил.
ГОСТ 7505-89 «Поковки стальные штампованные. Допуски припуски и кузнечные напуски»
Технология конструкционных материалов: Методические указания программа и практические задачи по курсу «Технология конструкционных материалов» для студентов машиностроительных специальностей. Составил: доцент к.т.н. Демченко Е.Б. – БНТУ 2006 – 30 с.
Справочник технолога-машиностроителя. В 2-х т. Т1. Под ред. А.Г. Касиловой и Р.К. Мещерякова. – 4-е изд. перераб. и дор. – М.: Машиностроение 1986 г. – 656 с. ил.
Справочник технолога-машиностроителя. В 2-х т. Т2. Под ред. А.Г. Касиловой и Р.К. Мещерякова. – 4-е изд. перераб. и дор. – М.: Машиностроение 1986 г. – 496 с. ил.
Кузнецов Ю.И. Маслов А.Р. Байков А.Н. Оснастка для станков с ЧПУ: Справочник. – 2-е изд. перераб. и доп. – М.: Машиностроение 1990. – 512 с.: ил.
Гузеев В.И. Батуев В.А.Сурков И.В. Режимы резания для токарных и сверлильно-фрезерно-расточных станков с числовым программным управлением: Справочник Под ред. В.И. Гузеева – М.: Машиностроение 2005 – 368 с.
Антонюк В.Е. Королев В.А. Башеев С.М. Справочник конструктора по расчету и проектированию станочных приспособлений. Минск «Беларусь» 1969 – 392 с.
Котельников В.К. Приспособления для изготовления металлорежущего инструмента. М. «Машиностроение» 1977 – 175 с.
ГОСТ 2424-83 «Круги шлифовальные. Технические условия»
Общемашиностроительные нормативы времени вспомогательного на обслуживание рабочего места и подготовительно-заключительного для технического нормирования станочных работ. Серийное производство. Издание второе уточненное и дополненное. – М: Машиностроение 1974 г. – 424 с.
Общемашиностроительные нормативы времени и режимов резания для нормирования работ выполняемых на универсальных и многоцелевых станках с числовым программным управлением. Часть 1 – нормативы времени. – М: Экономика 1990 г – 210 с.
И.С. Сачко И.М. Бабук Организация и планирование машиностроительного производства. Курсовое проектирование. Изд. третье перераб. и доп. – Мн.: УП «Технопринт» 2001 г – 108 с.
шевер.cdw

Диаметр основной окружности
Толщина зубьев нормальная по
дуге делительной окружности
Шаг зубьев нормальный
Угол наклона линии зуба
Направление линии зуба
Предельная погрешность
Накопленная погрешность
Погрешность направления зуба
Сталь Р6М5 ГОСТ 19265-73
КП.1-36.01.03.ТИП.303535.085.01
*Размер при нормальной толщине зуба
Технические требования по ГОСТ 8570-80
Маркировать: обозначение; m
знак завода изготовителя; год изготовления.
шевер(поковка).cdw

КП.1-36.01.03.ТИП.303535.085.02
точность изготовления Т4
исходный индекс 14 по ГОСТ 7505-89
Допускаемое смещение по поверхности разъема штампа не более
Допускаемая величина остаточного облоя не более 1 мм
Допускаемое отклонение от прямолинейности не более 0
Допускаемое отклонение от концентричности пробитого
отверстия относительно внешнего контура поковки не более 1
Допускаемая величина высоты заусенца не более 5 мм
Остальные технические требования по ГОСТ 7505-89
Содержание.doc
Выбор описание конструкции и расчет элементов приспособ-
Выбор описание и расчет режущих инструментов второго по-
наладка.cdw

1852007 ТУ 2-035-1110-87
1811027 ТУ 2-024-4586-76
1811004 ТУ 2-024-4586-76
Резец проходной упорный
- Наладочные размеры
КП.1-36.01.03.ТИП.303535.085.04
Инструментальная наладка
на токарный станок с ЧПУ